双色注塑模具设计36条经典经验分享
双(多)色塑料注射成型4.
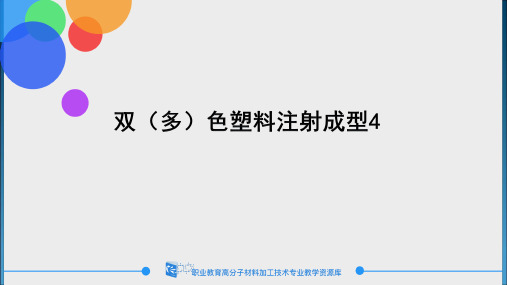
2、双色注射模结构设计 (3)成型零件结构设计 选材:因生产批量大,塑件外观要求高,成型零件的加 工要求较高,宜选用性能良好的预硬钢P20制造镶块,并 预硬化处理至35~37HRC。 结构:塑件外表面由动、定模大镶块整体成型,而内孔 部分采用局部镶拼结构,以利于内孔成型镶块表面加工。 在定、动模镶块的四角设置锁扣精定位结构,可提高动、 定模镶块的合模精度,并有利于模具制造时动、定模镶块 在模外的修配。
2、双色注射模结构设计 (2)模具浇注系统设计 浇口数量选择:因第一色塑件的4个内面板两两相连, 内面板之间仅由2.5mm宽、0.3mm厚的薄片与梯形凸台连 接,塑料熔体充模较困难,宜采用四点浇口进料,以保证 各型腔达到较好的流动平衡。 第二色塑件结构与第一色塑件有类似的特点,所以也采 用四点浇口进料。 浇注系统尺寸确定 • 因塑件的注塑量较小,浇口尺寸不宜太大,依经验选用 点浇口的内浇口尺寸为φ1.0mm,分流道截面为梯形,最 大宽度4mm,深度3mm,侧面斜度取8°。
2、双色注射模结构设计 (1)分型面与型腔数确定 1)分型面选择
2、双色注射模结构设计 (1)分型面与型腔数确定 2)型腔数的选择 因塑件生产批量较大,且为中小型件,塑件结构较为简 单,可选用一模多腔成型。 但模腔数太多将造成冷却管路连接困难,且模具尺寸受 注射机装模空间限制,不宜太大;所以确定采用一模两腔 的成型方案。
四、双(多)色塑料注射成型模具设计实例
2、双色注射模结构设计 双色注射模因生产所使用的双色注射机类型和半成品件 的换位方式的不同,其模具的浇注系统和各部分的结构会 不同,设计时应注意模具与设备的匹配问题。 (1)分型面与型腔数确定 1)分型面选择 控制开关面板塑件为扁平件,其分型面位置通常选在塑 件最大轮廓面的边界上。 由于双色塑件第一色注射成型的半成品塑件需在下一次 注射前旋转换位至第二色注射工位,它要求两种颜色塑件 的分型面应一致,故分型面应选择在二者的公共面上。
干货分享-双色模具设计经验总结
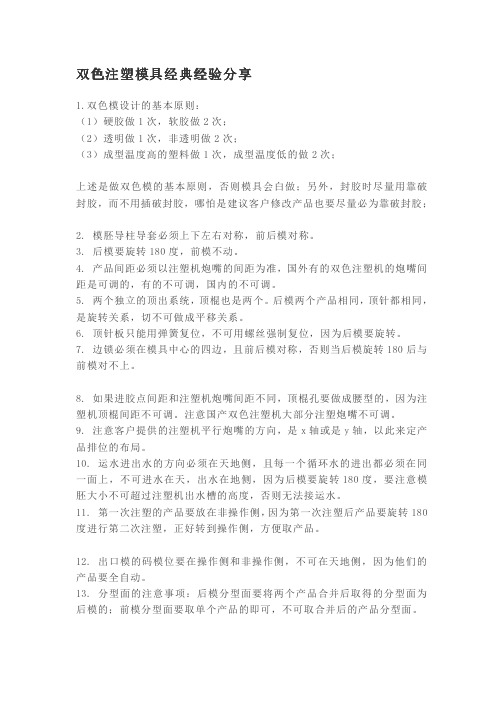
双色注塑模具经典经验分享1.双色模设计的基本原则:(1)硬胶做1次,软胶做2次;(2)透明做1次,非透明做2次;(3)成型温度高的塑料做1次,成型温度低的做2次;上述是做双色模的基本原则,否则模具会白做;另外,封胶时尽量用靠破封胶,而不用插破封胶,哪怕是建议客户修改产品也要尽量必为靠破封胶;2.模胚导柱导套必须上下左右对称,前后模对称。
3.后模要旋转180度,前模不动。
4.产品间距必须以注塑机炮嘴的间距为准,国外有的双色注塑机的炮嘴间距是可调的,有的不可调,国内的不可调。
5.两个独立的顶出系统,顶棍也是两个。
后模两个产品相同,顶针都相同,是旋转关系,切不可做成平移关系。
6.顶针板只能用弹簧复位,不可用螺丝强制复位,因为后模要旋转。
7.边锁必须在模具中心的四边,且前后模对称,否则当后模旋转180后与前模对不上。
8.如果进胶点间距和注塑机炮嘴间距不同,顶棍孔要做成腰型的,因为注塑机顶棍间距不可调。
注意国产双色注塑机大部分注塑炮嘴不可调。
9.注意客户提供的注塑机平行炮嘴的方向,是x轴或是y轴,以此来定产品排位的布局。
10.运水进出水的方向必须在天地侧,且每一个循环水的进出都必须在同一面上,不可进水在天,出水在地侧,因为后模要旋转180度,要注意模胚大小不可超过注塑机出水槽的高度,否则无法接运水。
11.第一次注塑的产品要放在非操作侧,因为第一次注塑后产品要旋转180度进行第二次注塑,正好转到操作侧,方便取产品。
12.出口模的码模位要在操作侧和非操作侧,不可在天地侧,因为他们的产品要全自动。
13.分型面的注意事项:后模分型面要将两个产品合并后取得的分型面为后模的;前模分型面要取单个产品的即可,不可取合并后的产品分型面。
14.前后法兰的公差为负0.05mm,两法兰间距公差为正负0.02mm,顶棍与顶棍孔的间隙单边为0.1mm,前后模导套导柱的中心距公差为正负0.01,模框四边和深度都要加公差,否则当后模旋转180度后,因高低不一致而产生批锋。
双色注射模具设计10个实例(经典案例)

双⾊注射模具设计10个实例(经典案例)这是⼀款⼿机护套,如下图产品分析:此款为某品牌⼿机的外圈护套,由⼆种塑料(PC+TPE)组成。
由于要求外形美观光滑,分模线必须做在内侧圆弧切点,所以外模要四⾯滑开,再看内侧,四周全部是内扣的,必须全⽅位内抽芯,也就是俗称的“爆炸芯”。
关于“爆炸芯”的模具结构,假如是普通的注塑模具,已经有⾮常经典的机构,我下⾯将有详细的介绍。
现在问题是双⾊模具,有⼆组动模和⼆组定模,⼆组动模的所有部件是完全⼀致的,要在双⾊注塑机的转盘上进⾏180度旋转,⼆种不同的塑料分别射进模腔,注射硬胶(PC)时动模的顶出机构和抽芯机构不动作,再注射软胶(TPE)并开模后,对准软胶料筒的⼀侧的动模的抽芯机构和顶出机构才开始动作,将完整的双⾊制品顶出。
由于动模旋转后,交换⼜合模后的浇⼝必须在同⼀位置,所以软胶和硬胶的浇⼝的处理显得令⼈困惑。
由于模具必须四周都要进⾏“内外同抽”,内、外滑块怎样排列,轨道设置在哪⾥?这个问题同样有被逼⼊墙⾓的感觉。
且不谈模具滑块机构的复杂性,我们从双⾊模具的基本原理来考虑,硬胶部分的成型和内外同抽机构是⼀定要设置在定模⼀侧的,软胶部分的成型机构也要设置在定模。
⽽且这个部分是由内外同抽的机构组成的凸起插⼊到动模的凹槽中。
转盘旋转180度后,这组凸起刚好插⼊到另外⼀个动模的凹槽中。
也就是说,⼆个定模上的由内外同抽滑块组成的凸起的外部形状和尺⼨是完全相同的。
仅仅是成型软胶和硬胶的型⾯不同⽽已。
问题的难点是,这个凸起会分成上下⼆层,⼀层向外移动,另⼀层向内移动,也就是俗称的“内外同抽”,合成的凸起的侧⾯是⼀个统⼀的斜⾯,但是,传统的滑块必须要有滑动轨道等必要的条件,怎样设置轨道?这便成了本案例的核⼼问题。
我是这样设置动模部分的凹槽和定模部分凸起的。
动模的凹槽是这样的。
下⾯我们来探讨定模部分的设计1.01定模内外同抽的设计基本机构是这样的当A板和定模底板分开35mm后拨块拨动内滑块,同时通过齿轮的传动,外滑块向外移动。
双色模具设计及双色注塑成型的36条经验

双色模具设计及双色注塑成型的36条经验:1.双色模设计的基本原则:(1.)硬胶做1次,软胶做2次;(2.)透明做1次,非透明做2次;(3.)成型温度高的塑料做1次,成型温度低的做2次;上述是做双色模的基本原则,否则模具会白做;另外,封胶时尽量用靠破封胶,而不用插破封胶,哪怕是建议客户修改产品也要尽量必为靠破封胶;2.模胚导柱导套必须上下左右对称,前后模对称。
3.后模要旋转180度,前模不动。
4. 产品间距必须以注塑机炮嘴的间距为准,国外有的双色注塑机的炮嘴间距是可调的,有的不可调,国内的不可调。
5. 两个独立的顶出系统,顶棍也是两个。
后模两个产品相同,顶针都相同,是旋转关系,切不可做成平移关系。
6. 顶针板只能用弹簧复位,不可用螺丝强制复位,因为后模要旋转。
7. 边锁必须在模具中心的四边,且前后模对称,否则当后模旋转180后与前模对不上。
8. 如果进胶点间距和注塑机炮嘴间距不同,顶棍孔要做成腰型的,因为注塑机顶棍间距不可调。
注意国产双色注塑机大部分注塑炮嘴不可调。
9. 注意客户提供的注塑机平行炮嘴的方向,是X轴或是Y轴,以此来定产品排位的布局。
10. 运水进出水的方向必须在天地侧,且每一个循环水的进出都必须在同一面上,不可进水在天,出水在地侧,因为后模要旋转180度,要注意模胚大小不可超过注塑机出水槽的高度,否则无法接运水。
11. 第一次注塑的产品要放在非操作侧,因为第一次注塑后产品要旋转180度进行第二次注塑,正好转到操作侧,方便取产品。
12. 出口模的码模位要在操作侧和非操作侧,不可在天地侧,因为他们的产品要全自动。
13. 分型面的注意事项:后模分型面要将两个产品合并后取得的分型面为后模的;前模分型面要取单个产品的即可,不可取合并后的产品分型面。
14. 前后法兰的公差为负0.05mm,两法兰间距公差为正负0.02mm,顶棍与顶棍孔的间隙单边为 0.1mm,前后模导套导柱的中心距公差为正负0.01,模框四边和深度都要加公差,否则当后模旋转180度后,因高低不一致而产生批锋。
一种新型双色注塑模具结构的制作方法

一种新型双色注塑模具结构的制作方法引言在注塑模具制作领域,双色注塑模具被广泛应用于生产各种产品,包括汽车零件、电子设备外壳以及家电产品等。
为了提高生产效率和产品质量,在模具结构和制作方法方面持续进行创新和改进。
本文介绍了一种新型双色注塑模具结构的制作方法,该方法通过引入特殊的切换机构和优化设计,提高了模具的生产效率和稳定性。
1. 模具结构设计1.1 外模设计外模是双色注塑模具中的主要构件,它负责注塑料成型的外层。
设计外模时,需要考虑产品形状、尺寸和注塑工艺等因素。
1.1.1 产品形状和尺寸要求根据实际产品的外形要求和尺寸,设计外模的结构和几何形状。
通常情况下,外模应具备一定的强度和刚度,以保证注塑过程中的准确性和稳定性。
1.1.2 注塑工艺要求考虑注塑工艺参数,如注塑料的熔融温度、注射速度和压力等,设计出适合的冷却系统和流道结构。
优化冷却系统可以有效降低注塑过程中的温度变化和应力集中。
1.2 内模设计内模是双色注塑模具中的另一个重要构件,它负责注塑料成型的内层。
内模的设计需要考虑与外模之间的配合以及内层注塑料的粘附性。
1.2.1 配合设计内模的几何形状应与外模密切配合,以确保成型产品的精度和质量。
在配合设计过程中,需要考虑两种不同材料的热胀冷缩系数,以及模具在使用过程中的磨损和热变形。
1.2.2 表面处理内模的表面应经过特殊处理,以减少注塑过程中内层材料的粘附性。
常用的表面处理方法包括喷涂覆盖层、电火花处理和抛光等。
2. 模具制作工艺2.1 材料选择模具的材料选择对制作工艺和模具寿命有着重要影响。
根据模具的使用要求和预计生产数量,选择适合的模具材料。
常用的模具材料包括钢材和铝合金等。
2.2 制模过程制作新型双色注塑模具的制模过程包括以下步骤:2.2.1 设计和加工外模根据外模的设计图纸,选择合适的工艺设备和工具进行加工和制造。
2.2.2 设计和加工内模根据内模的设计图纸,选择合适的工艺设备和工具进行加工和制造。
双色注塑模具设计及双色注塑成型注意事项与经验 共三十六条

双色注塑模具设计及双色注塑成型注意事项与经验共三十六条1.双色注塑模具设计的基本原则:(1.)硬胶做1次,软胶做2次;(2.)透明做1次,非透明做2次;(3.)注塑成型温度高的塑料做1次,成型温度低的做2次;上述是做双色注塑模具的基本原则,否则注塑模具会白做;另外,封胶时尽量用靠破封胶,而不用插破封胶,哪怕是建议客户修改产品也要尽量必为靠破封胶;2.模胚导柱导套必须上下左右对称,前后模对称。
3.后模要旋转180度,前模不动。
4. 产品间距必须以注塑机炮嘴的间距为准,国外有的双色注塑机的炮嘴间距是可调的,有的不可调,国内的不可调。
5. 两个独立的顶出系统,顶棍也是两个。
后模两个产品相同,顶针都相同,是旋转关系,切不可做成平移关系。
6. 顶针板只能用弹簧复位,不可用螺丝强制复位,因为后模要旋转。
7. 边锁必须在模具中心的四边,且前后模对称,否则当后模旋转180后与前模对不上。
8. 如果进胶点间距和注塑机炮嘴间距不同,顶棍孔要做成腰型的,因为注塑机顶棍间距不可调。
注意国产双色注塑机大部分注塑炮嘴不可调。
9. 注意客户提供的注塑机平行炮嘴的方向,是X轴或是Y轴,以此来定产品排位的布局。
10. 运水进出水的方向必须在天地侧,且每一个循环水的进出都必须在同一面上,不可进水在天,出水在地侧,因为后模要旋转180度,要注意模胚大小不可超过注塑机出水槽的高度,否则无法接运水。
11. 第一次注塑的产品要放在非操作侧,因为第一次注塑后产品要旋转180度进行第二次注塑,正好转到操作侧,方便取产品。
12. 出口模的码模位要在操作侧和非操作侧,不可在天地侧,因为他们的产品要全自动。
13. 分型面的注意事项:后模分型面要将两个产品合并后取得的分型面为后模的;前模分型面要取单个产品的即可,不可取合并后的产品分型面。
14. 前后法兰的公差为负0.05mm,两法兰间距公差为正负0.02mm,顶棍与顶棍孔的间隙单边为0.1mm,前后模导套导柱的中心距公差为正负0.01,模框四边和深度都要加公差,否则当后模旋转180度后,因高低不一致而产生批锋。
双色模具的设计及注塑成型
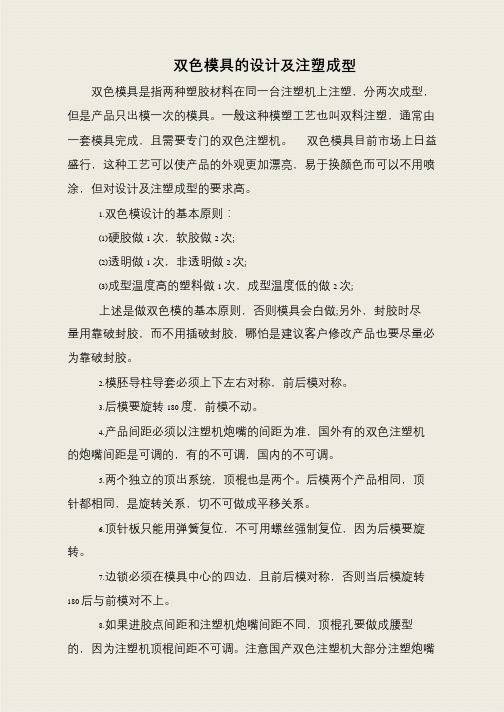
双色模具的设计及注塑成型
双色模具是指两种塑胶材料在同一台注塑机上注塑,分两次成型,但是产品只出模一次的模具。
一般这种模塑工艺也叫双料注塑,通常由一套模具完成,且需要专门的双色注塑机。
双色模具目前市场上日益盛行,这种工艺可以使产品的外观更加漂亮,易于换颜色而可以不用喷涂,但对设计及注塑成型的要求高。
1.双色模设计的基本原则:
(1)硬胶做1 次,软胶做2 次;
(2)透明做1 次,非透明做2 次;
(3)成型温度高的塑料做1 次,成型温度低的做2 次;
上述是做双色模的基本原则,否则模具会白做;另外,封胶时尽
量用靠破封胶,而不用插破封胶,哪怕是建议客户修改产品也要尽量必为靠破封胶。
2.模胚导柱导套必须上下左右对称,前后模对称。
3.后模要旋转180 度,前模不动。
4.产品间距必须以注塑机炮嘴的间距为准,国外有的双色注塑机的炮嘴间距是可调的,有的不可调,国内的不可调。
5.两个独立的顶出系统,顶棍也是两个。
后模两个产品相同,顶针都相同,是旋转关系,切不可做成平移关系。
6.顶针板只能用弹簧复位,不可用螺丝强制复位,因为后模要旋转。
7.边锁必须在模具中心的四边,且前后模对称,否则当后模旋转180 后与前模对不上。
8.如果进胶点间距和注塑机炮嘴间距不同,顶棍孔要做成腰型的,因为注塑机顶棍间距不可调。
注意国产双色注塑机大部分注塑炮嘴。
图文详解双色注塑技术-20200609
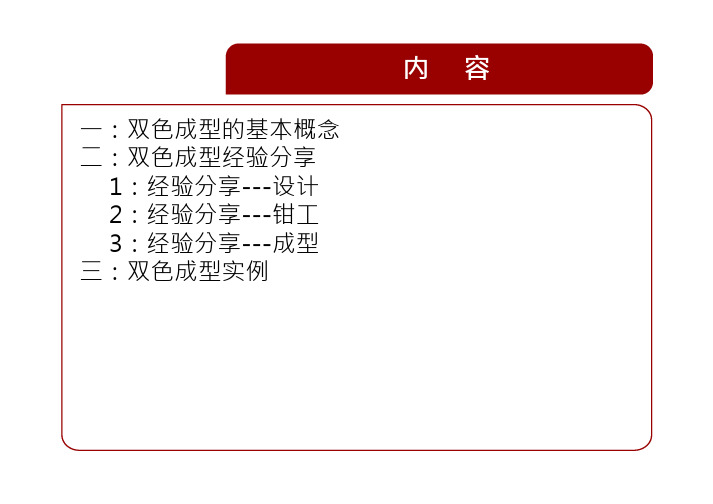
2.双色单模
3.抽芯式双色模
4.混料成型双色
模
5.双料夹层双色模
混色射枪(单一模)
材料混成的亲和性
第一射成型
第二射成型公模互换取第一射料头
首先注射第一种材质,再通过第二色型腔完成双色成型
二色进料口
一色进料口
顶针板
两块顶出
结构分别
脱模一模二
穴型腔,
不一样,
分别成
型一/二
色材料
Shot2射台
Shot1射台转盘
转盘
变形
变形
PC材质热变形130度.Shot2硅胶在通过浇口进入模腔时的温度已超200度.a处在此种状况下,所能承受的力是极有限的.
a
流道强度小
流痕。
双色模设计要求及经验总结

编写:胡明辉
•定义:此文件适应于誉铭新公司双色模具设计
•注:双色模具有很多种类,此处仅为后模及后模模架整体旋转的双色模具。
•誉铭新双色机台规格有两种,1.120T的双色机台 常用模架FCI2327/FCI2530(唧嘴要偏心) • • 2.250T的双色机台
•电子档位置:\\server\gmn1\标准化文件\标准库\2D 相关\誉铭新 双色注塑机 规格.dwg
B.双色模的进浇
1.软胶的水口勾针与一般模具不一样,如右图 2.软胶对模具竖浇道及点入水流道的出模斜度与一般模具不一样,
常规模具的水口做单边1度即可, 软胶水口部分的出模斜度需做到单边3度(同时注意,大端尺寸不可大 于6mm)。 3.软胶竖浇道的小端尺寸应为2.5~3.0,大端尺寸不可大于6mm 4.较胶的流道系统均不可抛光,应使用粗纹(24号以上火花纹), 以防止真空产生吸附力。
唧嘴顶棍孔一并偏心之所以要偏心20是因为如果不偏心20则不能采用120t的机台生产模架为2530的的模侧250t机台的最小模厚为250最大模厚为560最大开模尺寸为1120当2530模架仅能在250t的注塑机时模架不偏心20唧嘴顶棍孔不偏心如模具过厚中兴r750项目的n75247529的模厚即不可用于120t的注塑机250t机台的最小模厚为250最大模厚为56010最大开模尺寸为1120103
以下章节为双色模具设计 需注意的问题,
A.模架与锁模
1. 2327模架时,采用120T的注塑机台,锁模螺丝位置如下图
操 作 侧
120T机台的最小模厚为177, 最大模厚为334-10, 最大开模尺寸为620-10 10mm为装在注塑机上的隔热板厚度
2. 2530模架时,同时采用120T或250T时,锁模螺丝位置如下图,注意:模架订购图中锁模螺丝要偏心。 唧嘴/顶棍孔一并偏心(之所以要偏心20是因为如果不偏心20则不能采用120T的机台生产模架为2530的的模具 注意:一般情况下,锁模螺丝孔相对唧嘴中心应是对称的
双色模具设计及双色注塑成型的36条经验

双色模具设计及双色注塑成型的36条经验1.双色模具设计要考虑产品的结构和使用功能,合理设计产品的内外形状,确保产品在注塑成型时能够顺利分离并达到预期效果。
2.双色模具设计中要注意两种颜色的材料流动和混色问题,避免颜色交叉污染。
3.在双色注塑过程中,要控制两种颜色的注射压力和速度,以避免色块儿不均匀或颜色混合不好的问题。
4.双色模具设计要合理设置副模和主模的开关位置和开关顺序,确保两种颜色的注塑成型能够同时进行。
5.在双色注塑过程中,需要合理设置两种颜色的熔体温度和熔体流率,以确保两种颜色能够顺利融合。
6.双色模具设计中要考虑产品的尺寸收缩和变形问题,确保产品的尺寸和外观质量。
7.双色注塑时要注意注塑机的射胶量和压力,以确保两种颜色注塑料能够充满整个模具腔体。
8.双色模具设计要考虑产品的冷却和固化时间,以避免产品变形和缩水的问题。
9.双色注塑时要注意两种颜色注塑料的开合模时间和速度,以确保产品分离顺利。
10.双色模具设计中要考虑产品的镂空和细节处理,确保产品的复杂结构能够正确注塑。
11.双色注塑时要注意产品的填充速度和压力,以避免产品出现短充或气泡等缺陷。
12.双色模具设计要考虑模具的损耗问题,合理选择模具材料和加工工艺,延长模具的使用寿命。
13.双色注塑时要注意熔体温度的控制,避免产品出现烧焦和热分解等问题。
14.双色模具设计要考虑产品的注塑料和色母的选择,确保颜色稳定和耐磨性能。
15.双色注塑时要注意产品的射胶位置和射胶方式,以确保两种颜色注塑料能够充分融合。
16.双色模具设计中要考虑产品的模胚和射胶道的设计,确保产品的流畅性和充满性。
17.双色注塑时要注意注塑成型周期和循环时间,以提高生产效率和降低成本。
18.双色模具设计要考虑产品的特殊要求和辅助工艺,如压纹、喷漆等,提高产品的附加值。
19.双色注塑时要注意产品的表面光洁度和质量要求,以满足消费者对产品外观的要求。
20.双色模具设计要考虑产品的组装和拆卸问题,以方便产品的维修和更换。
双色注塑知识点总结
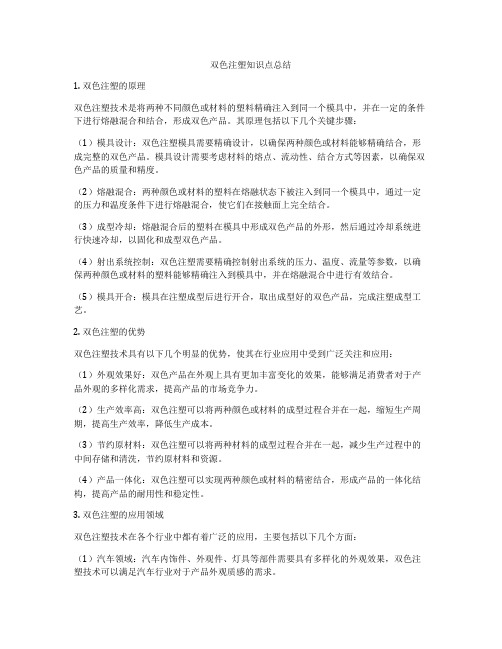
双色注塑知识点总结1. 双色注塑的原理双色注塑技术是将两种不同颜色或材料的塑料精确注入到同一个模具中,并在一定的条件下进行熔融混合和结合,形成双色产品。
其原理包括以下几个关键步骤:(1)模具设计:双色注塑模具需要精确设计,以确保两种颜色或材料能够精确结合,形成完整的双色产品。
模具设计需要考虑材料的熔点、流动性、结合方式等因素,以确保双色产品的质量和精度。
(2)熔融混合:两种颜色或材料的塑料在熔融状态下被注入到同一个模具中,通过一定的压力和温度条件下进行熔融混合,使它们在接触面上完全结合。
(3)成型冷却:熔融混合后的塑料在模具中形成双色产品的外形,然后通过冷却系统进行快速冷却,以固化和成型双色产品。
(4)射出系统控制:双色注塑需要精确控制射出系统的压力、温度、流量等参数,以确保两种颜色或材料的塑料能够精确注入到模具中,并在熔融混合中进行有效结合。
(5)模具开合:模具在注塑成型后进行开合,取出成型好的双色产品,完成注塑成型工艺。
2. 双色注塑的优势双色注塑技术具有以下几个明显的优势,使其在行业应用中受到广泛关注和应用:(1)外观效果好:双色产品在外观上具有更加丰富变化的效果,能够满足消费者对于产品外观的多样化需求,提高产品的市场竞争力。
(2)生产效率高:双色注塑可以将两种颜色或材料的成型过程合并在一起,缩短生产周期,提高生产效率,降低生产成本。
(3)节约原材料:双色注塑可以将两种材料的成型过程合并在一起,减少生产过程中的中间存储和清洗,节约原材料和资源。
(4)产品一体化:双色注塑可以实现两种颜色或材料的精密结合,形成产品的一体化结构,提高产品的耐用性和稳定性。
3. 双色注塑的应用领域双色注塑技术在各个行业中都有着广泛的应用,主要包括以下几个方面:(1)汽车领域:汽车内饰件、外观件、灯具等部件需要具有多样化的外观效果,双色注塑技术可以满足汽车行业对于产品外观质感的需求。
(2)电子领域:手机壳、电脑外壳、家电外壳等产品需要具有精美的外观效果,双色注塑技术可以实现产品的多彩外观变化。
吐血奉献,多年的注塑模具设计经验总结,绝对转载
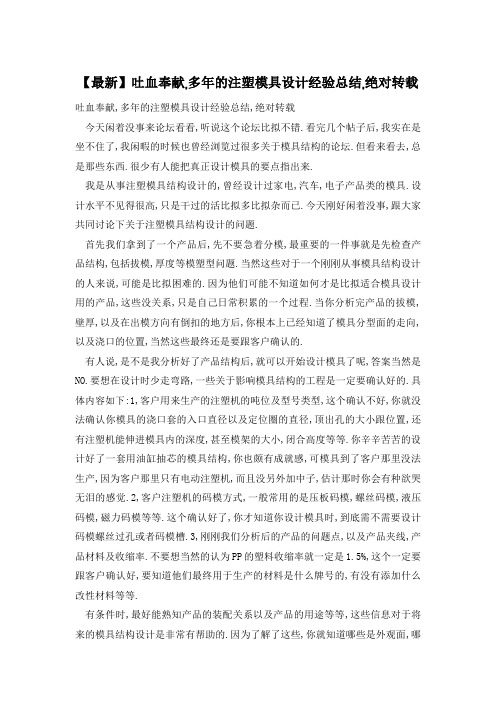
【最新】吐血奉献,多年的注塑模具设计经验总结,绝对转载吐血奉献,多年的注塑模具设计经验总结,绝对转载今天闲着没事来论坛看看,听说这个论坛比拟不错.看完几个帖子后,我实在是坐不住了,我闲暇的时候也曾经浏览过很多关于模具结构的论坛.但看来看去,总是那些东西.很少有人能把真正设计模具的要点指出来.我是从事注塑模具结构设计的,曾经设计过家电,汽车,电子产品类的模具.设计水平不见得很高,只是干过的活比拟多比拟杂而已.今天刚好闲着没事,跟大家共同讨论下关于注塑模具结构设计的问题.首先我们拿到了一个产品后,先不要急着分模,最重要的一件事就是先检查产品结构,包括拔模,厚度等模塑型问题.当然这些对于一个刚刚从事模具结构设计的人来说,可能是比拟困难的.因为他们可能不知道如何才是比拟适合模具设计用的产品,这些没关系,只是自己日常积累的一个过程.当你分析完产品的拔模,壁厚,以及在出模方向有倒扣的地方后,你根本上已经知道了模具分型面的走向,以及浇口的位置,当然这些最终还是要跟客户确认的.有人说,是不是我分析好了产品结构后,就可以开始设计模具了呢,答案当然是NO.要想在设计时少走弯路,一些关于影响模具结构的工程是一定要确认好的.具体内容如下:1,客户用来生产的注塑机的吨位及型号类型,这个确认不好,你就没法确认你模具的浇口套的入口直径以及定位圈的直径,顶出孔的大小跟位置,还有注塑机能伸进模具内的深度,甚至模架的大小,闭合高度等等.你辛辛苦苦的设计好了一套用油缸抽芯的模具结构,你也颇有成就感,可模具到了客户那里没法生产,因为客户那里只有电动注塑机,而且没另外加中子,估计那时你会有种欲哭无泪的感觉.2,客户注塑机的码模方式,一般常用的是压板码模,螺丝码模,液压码模,磁力码模等等.这个确认好了,你才知道你设计模具时,到底需不需要设计码模螺丝过孔或者码模槽.3,刚刚我们分析后的产品的问题点,以及产品夹线,产品材料及收缩率.不要想当然的认为PP的塑料收缩率就一定是1.5%,这个一定要跟客户确认好,要知道他们最终用于生产的材料是什么牌号的,有没有添加什么改性材料等等.有条件时,最好能熟知产品的装配关系以及产品的用途等等,这些信息对于将来的模具结构设计是非常有帮助的.因为了解了这些,你就知道哪些是外观面,哪些是非外观,哪些地方的拔模角度是可以随便加大的,哪些地方是不能改的.甚至包括一些产品的结构,如果你了解了产品的实际装配关系以及用途,你就知道哪些倒扣结构是可以取消或改成另外一种简单形式的.一定要牢记,做模具的过程就是把复杂问题简单化的过程.常看到一些人以做了一套多么多么复杂的结构而感到骄傲自豪,我觉得那是非常得无知.因为很多产品工程师可能会由于自身的经验问题,设计了一些不太合理的结构,如果作为下游工序,不能帮他们指正的话,他们可能永远都觉得那样设计是没问题的.那我们产品工程师的进步就会非常的缓慢.4,模具水路外接参数,油路外接参数,电路外接参数,气路外接参数.只有在设计之前了解了客户这些要求之后,你才能有预见性的设计水路油路气路,别到时辛辛苦苦设计好了模具,后来发现客户需要在模具内部串联油路,那时你再改动,估计会累个半死,因为你水路,顶杆,螺钉什么的都好不容易排好了位.像这四路的设计顺序一般是先保证油路,因为油路要分布平衡,特指需要油缸顶出的模具结构,如果油路不平衡的话,油缸顶出的动作就会有先后,容易顶出不平衡.当然也可以采用齿轮分油器,但那样就更复杂了.其次是水路,因为水路要保证冷却效果,分布不均会影响产品质量及模具寿命.最后才是气路跟电路.在模具上的放置顺序是,最靠近TOP方向的是电路,然后是水路,气路,最下面的是油路接头.5,其它未尽事项.掌握了这些信息后,我们就可以着手设计模具了.首先是分模,这个过程估计是大家都比拟喜欢的过程.因为分出模来有成就感.拉分型面的原那么就是简单即好,能拉伸出来的坚决不扫描,或者用其它高级命令.其次拉分型面时要有大局观,尽量简化分型面,不要搞的七七八八的,如果不是精密模具,那些0.1~0.5的插穿位能防止的就要防止.另外分型面还要遵循一个原那么,就是尽量顺着产品趋势做.那样做出来的分型面才会beautiful.串插一句题外话,在学习三维软件时,一定要切记,每个命令的原理都弄明白,那你就知道在什么时候能用到那个命令.很多时候重要的不是你不会用软件,而是你不会活学活用软件.同样一个命令,有经验的人会有很多种灵活的用法,这点表达在UG上是最明显的.一句话,重要的是思路,而不是工具本身.在做分型面的时候,只需要知道,插穿面的角度能大就大,碰穿面的面积能大就大,拉出来的枕位能宽就宽.要充分考虑你现在手上拉的这个分型面将来实际模具做出来后,人家车间负责飞模的师傅会不会骂你就行了.如果你觉得不会挨骂,那就OK,继续进行,当将来你真的被骂了,这些就是你的经验.在做分型面的同时肯定是要考虑滑块跟斜顶的排布的,因为那些也要涉及到分型面的改动.典型滑块结构就是三角函数关系,这个没事自己多算算就行,但要保证斜导柱的角度不要太大,尽量做到30度以下.斜导柱选用的原那么就是能粗就粗,别太小气,因为斜导柱是要受力的.另外滑块也分很多变异的结构,例如,上坡滑块,下坡滑块,内抽滑块,油缸抽,前模滑块,滑块带滑块,滑块带反顶,滑块带斜顶,等等,这些特殊结构都是充分利用了三角函数关系式,目的就是为了实现产品倒扣的脱模,及模具的正常开合模动作.滑块的计算公式各大论坛都有详细的介绍,我就不在此赘述了.其次是斜顶,斜顶比拟灵活,但典型斜顶的角度也不要太大,尽量不要超过15度,当然你非要做20度也行,但寿命就很难保证了,而且动作也会很不顺畅,具体原理参照三角函数与理论力学.斜顶的形状有很多演化形式,例如,上坡斜顶,下坡斜顶,歪脖子斜顶,镶拼斜顶杆的大斜顶,镶拼圆杆的大斜顶,镶拼挂台的小斜顶,顶块下面走斜顶的,滑块上走斜顶的,斜顶上走斜顶的,斜顶上带反顶的,等等,这些所有的结构都是一个目的,利用三角函数把产品的倒扣做出来.由此可见,学好三角函数是多麽的重要啊!所以至于各种特殊的结构,都是人想出来的,你大可以充分发挥你的想象力,不管什么样的结构都可以去随便想,想好了,就去大胆的设计,搞不好你就有新创造呢,但设计完后,一定要验证下三角函数的关系,就是实际模拟下模具的开合模动作,以及考虑下在注塑时会不会有问题等等.说着说着,我们分模分好了.接下来就是模具结构的排位了,这些内容都是事先要理清头绪的,根据产品的实际情况,选用不同类型的模具结构,例如,两板模,三板模,热流道,IMD,IML,双色,叠模等等.所有的模具结构类型都是为了能很好的实现产品的量产而效劳的.在选用模架时,我们就要充分考虑刚刚提到的那4点考前须知了.选好了模架我们就要考虑模具的镶拼了,镶拼的原那么就是简化加工,节省材料,利于产品成型,比方排气等等.你觉得模具上存在特别薄的地方,一定要单独镶拼出来,易于将来更换.在镶拼的时候要充分考虑镶件的强度,加工性,以及将来水路的可设计性.镶拼完了后,就要加标准件了.加标准件的原那么就是先重点后局部,尽量布置平衡对称.一般都是要先加顶杆的,加顶杆时一定要考虑水路的排布.一般情况下,要优先考虑顶杆的排布,然后大体设计水路,然后再根据实际情况调整水路顶杆,使两者到达平衡.加顶出的原那么就是抱紧力大的地方,另外要加在产品的楞,台,边等强度结构比拟好的地方,以免顶白或顶出不平衡.排水路的原那么就是加顶出的原那么,因为一般来讲,产品抱紧力大的地方也就是产品的热点,需要加强冷却的部位,这个矛盾需要调节好.至于到底是用顶杆还是用顶块或者推板,就需要具体问题具体分析了.这个要结合产品的结构特点来分析,比方产品容易粘前模,就要考虑要不要后模加倒扣,或者前模加顶出,这些都是自然而然的事情,但很多朋友都不会想全面是什么原因呢,那还是因为没有对产品结构分析充分,没有实际考虑下产品在注塑过程中的状态.这是问题的关键.顶杆水路加完了,剩下的就是那些乱七八糟的标准件了,大家在加的时候尽量考虑对称平衡就是了.整套模具设计完成后,一定要做以下几项检查,首先是镶块的拔模分析,看看有没有倒扣的地方,其次是模具各零件的干预检查,重中之重.现在的三维软件都有这项功能,方便的很.然后就是模具开合模动作的模拟,再简单的模具只要自己不是太清晰,就一定要实际模拟下,另外就是模具各零件的可加工性以及模具的装配过程,别辛辛苦苦设计出来了个巧妙的结构,理论计算也没问题,加工完了,结果装不进去,或者不好装配.至此,可以恭喜你了,大体的流程都已经结束了.其实模具设计是个充满着矛盾的事情.想设计完美些,模具费用就高了,想设计简单一些,可能产品就要改或者模具的强度,使用寿命都会有影响.所以模具设计没有绝对的.只要寻好了那个平衡点,你设计的模具就是成功的.所以,别人设计的结构未必都适合你.只要遵循了以上的模具设计要点,估计大家都能设计出比拟合理的模具结构来.由于时间紧张,讲的有些地方词不达意,并且本人水平有限,有些地方可能有点偏颇,希望大家都能讨论下.如果有朋友对模具结构有兴趣,也可能跟我共同讨论下,大家互相学习,共同进步!今天先大体讲下,有时间再进一步拓展下.扩展阅读:多年的注塑模具设计经验总结我是从事注塑模具结构设计的,曾经设计过家电,汽车,电子产品类的模具.设计水平不见得很高,只是干过的活比拟多比拟杂而已.今天刚好闲着没事,跟大家共同讨论下关于注塑模具结构设计的问题.首先我们拿到了一个产品后,先不要急着分模,最重要的一件事就是先检查产品结构,包括拔模,厚度等模塑型问题.当然这些对于一个刚刚从事模具结构设计的人来说,可能是比拟困难的.因为他们可能不知道如何才是比拟适合模具设计用的产品,这些没关系,只是自己日常积累的一个过程.当你分析完产品的拔模,壁厚,以及在出模方向有倒扣的地方后,你根本上已经知道了模具分型面的走向,以及浇口的位置,当然这些最终还是要跟客户确认的.有人说,是不是我分析好了产品结构后,就可以开始设计模具了呢,答案当然是NO.要想在设计时少走弯路,一些关于影响模具结构的工程是一定要确认好的.具体内容如下:1,客户用来生产的注塑机的吨位及型号类型,这个确认不好,你就没法确认你模具的浇口套的入口直径以及定位圈的直径,顶出孔的大小跟位置,还有注塑机能伸进模具内的深度,甚至模架的大小,闭合高度等等.你辛辛苦苦的设计好了一套用油缸抽芯的模具结构,你也颇有成就感,可模具到了客户那里没法生产,因为客户那里只有电动注塑机,而且没另外加中子,估计那时你会有种欲哭无泪的感觉.2,客户注塑机的码模方式,一般常用的是压板码模,螺丝码模,液压码模,磁力码模等等.这个确认好了,你才知道你设计模具时,到底需不需要设计码模螺丝过孔或者码模槽.3,刚刚我们分析后的产品的问题点,以及产品夹线,产品材料及收缩率.不要想当然的认为PP的塑料收缩率就一定是1.5%,这个一定要跟客户确认好,要知道他们最终用于生产的材料是什么牌号的,有没有添加什么改性材料等等.有条件时,最好能熟知产品的装配关系以及产品的用途等等,这些信息对于将来的模具结构设计是非常有帮助的.因为了解了这些,你就知道哪些是外观面,哪些是非外观,哪些地方的拔模角度是可以随便加大的,哪些地方是不能改的.甚至包括一些产品的结构,如果你了解了产品的实际装配关系以及用途,你就知道哪些倒扣结构是可以取消或改成另外一种简单形式的.一定要牢记,做模具的过程就是把复杂问题简单化的过程.常看到一些人以做了一套多么多么复杂的结构而感到骄傲自豪,我觉得那是非常的无知.因为很多产品工程师可能会由于自身的经验问题,设计了一些不太合理的结构,如果作为下游工序,不能帮他们指正的话,他们可能永远都觉得那样设计是没问题的.那我们产品工程师的进步就会非常的缓慢.〔作为主管的一种经验,让所有的参与者共同进步!〕4,模具水路外接参数,油路外接参数,电路外接参数,气路外接参数.只有在设计之前了解了客户这些要求之后,你才能有预见性的设计水路油路气路,别到时辛辛苦苦设计好了模具,后来发现客户需要在模具内部串联油路,那时你再改动,估计会累个半死,因为你水路,顶杆,螺钉什么的都好不容易排好了位.像这四路的设计顺序一般是先保证油路,因为油路要分布平衡,特指需要油缸顶出的模具结构,如果油路不平衡的话,油缸顶出的动作就会有先后,容易顶出不平衡.当然也可以采用齿轮分油器,但那样就更复杂了.其次是水路,因为水路要保证冷却效果,分布不均会影响产品质量及模具寿命.最后才是气路跟电路.在模具上的放置顺序是,最靠近TOP方向的是电路,然后是水路,气路,最下面的是油路接头.5,其它未尽事项.掌握了这些信息后,我们就可以着手设计模具了.首先是分模,这个过程估计是大家都比拟喜欢的过程.因为分出模来有成就感.分型面的原那么就是简单即好,能拉伸出来的坚决不扫描,或者用其它高级命令.其次拉分型面时要有大局观,尽量简化分型面,不要搞的七七八八的,如果不是精密模具,那些0.1~0.5的插穿位能防止的就要防止.另外分型面还要遵循一个原那么,就是尽量顺着产品趋势做.那样做出来的分型面才会beautiful.串插一句题外话,在学习三维软件时,一定要切记,每个命令的原理都弄明白,那你就知道在什么时候能用到那个命令.很多时候重要的不是你不会用软件,而是你不会活学活用软件.同样一个命令,有经验的人会有很多种灵活的用法,这点表达在UG上是最明显的.一句话,重要的是思路,而不是工具本身.在做分型面的时候,只需要知道,插穿面的角度能大就大,碰穿面的面积能大就大,拉出来的枕位能宽就宽.要充分考虑你现在手上拉的这个分型面将来实际模具做出来后,人家车间负责飞模〔飞模就是合模,模具的分模面及滑块面等经过机加工或放电加工后,要用红丹着色来确认面同面的接触是否良好,如接触不很理想就加以钳工修正,这个过程就叫飞模,也叫合模或配模.〕的师傅会不会骂你就行了.如果你觉得不会挨骂,那就OK,继续进行,当将来你真的被骂了,这些就是你的经验.在做分型面的同时肯定是要考虑滑块跟斜顶的排布的,因为那些也要涉及到分型面的改动.典型滑块结构就是三角函数关系,这个没事自己多算算就行,但要保证斜导柱的角度不要太大,尽量做到30度以下.斜导柱选用的原那么就是能粗就粗,别太小气,因为斜导柱是要受力的.另外滑块也分很多变异的结构,例如,上坡滑块,下坡滑块,内抽滑块,油缸抽,前模滑块,滑块带滑块,滑块带反顶,滑块带斜顶,等等,这些特殊结构都是充分利用了三角函数关系式,目的就是为了实现产品倒扣的脱模,及模具的正常开合模动作.滑块的计算公式各大论坛都有详细的介绍,我就不在此赘述了.其次是斜顶,斜顶比拟灵活,但典型斜顶的角度也不要太大,尽量不要超过15度,当然你非要做20度也行,但寿命就很难保证了,而且动作也会很不顺畅,具体原理参照三角函数与理论力学.斜顶的形状有很多演化形式,例如,上坡斜顶,下坡斜顶,歪脖子斜顶,镶拼斜顶杆的大斜顶,镶拼圆杆的大斜顶,镶拼挂台的小斜顶,顶块下面走斜顶的,滑块上走斜顶的,斜顶上走斜顶的,斜顶上带反顶的,等等,这些所有的结构都是一个目的,利用三角函数把产品的倒扣做出来.由此可见,学好三角函数是多麽的重要啊!所以至于各种特殊的结构,都是人想出来的,你大可以充分发挥你的想象力,不管什么样的结构都可以去随便想,想好了,就去大胆的设计,搞不好你就有新创造呢,但设计完后,一定要验证下三角函数的关系,就是实际模拟下模具的开合模动作,以及考虑下在注塑时会不会有问题等等.说着说着,我们分模分好了.接下来就是模具结构的排位了,这些内容都是事先要理清头绪的,根据产品的实际情况,选用不同类型的模具结构,例如,两板模,三板模,热流道,IMD,IML,双色,叠模等等.所有的模具结构类型都是为了能很好的实现产品的量产而效劳的.在选用模架时,我们就要充分考虑刚刚提到的那4点考前须知了.选好了模架我们就要考虑模具的镶拼了,镶拼的原那么就是简化加工,节省材料,利于产品成型,比方排气等等.你觉得模具上存在特别薄的地方,一定要单独镶拼出来,易于将来更换.在镶拼的时候要充分考虑镶件的强度,加工性,以及将来水路的可设计性.镶拼完了后,就要加标准件了.加标准件的原那么就是先重点后局部,尽量布置平衡对称.一般都是要先加顶杆的,加顶杆时一定要考虑水路的排布.一般情况下,要优先考虑顶杆的排布,然后大体设计水路,然后再根据实际情况调整水路顶杆,使两者到达平衡.加顶出的原那么就是抱紧力大的地方,另外要加在产品的楞,台,边等强度结构比拟好的地方,以免顶白或顶出不平衡.排水路的原那么就是加顶出的原那么,因为一般来讲,产品抱紧力大的地方也就是产品的热点,需要加强冷却的部位,这个矛盾需要调节好.至于到底是用顶杆还是用顶块或者推板,就需要具体问题具体分析了.这个要结合产品的结构特点来分析,比方产品容易粘前模,就要考虑要不要后模加倒扣,或者前模加顶出,这些都是自然而然的事情,但很多朋友都不会想全面是什么原因呢,那还是因为没有对产品结构分析充分,没有实际考虑下产品在注塑过程中的状态.这是问题的关键.顶杆水路加完了,剩下的就是那些乱七八糟的标准件了,大家在加的时候尽量考虑对称平衡就是了.整套模具设计完成后,一定要做以下几项检查,首先是镶块的拔模分析,看看有没有倒扣的地方,其次是模具各零件的干预检查,重中之重.现在的三维软件都有这项功能,方便的很.然后就是模具开合模动作的模拟,再简单的模具只要自己不是太清晰,就一定要实际模拟下,另外就是模具各零件的可加工性以及模具的装配过程,别辛辛苦苦设计出来了个巧妙的结构,理论计算也没问题,加工完了,结果装不进去,或者不好装配.至此,可以恭喜你了,大体的流程都已经结束了.其实模具设计是个充满着矛盾的事情.想设计完美些,模具费用就高了,想设计简单一些,可能产品就要改或者模具的强度,使用寿命都会有影响.所以模具设计没有绝对的.只要寻好了那个平衡点,你设计的模具就是成功的.所以,别人设计的结构未必都适合你.只要遵循了以上的模具设计要点,估计大家都能设计出比拟合理的模具结构来.由于时间紧张,讲的有些地方词不达意,并且本人水平有限,有些地方可能有点偏颇,希望大家都能讨论下.如果有朋友对模具结构有兴趣,也可能跟我共同讨论下,大家互相学习,共同进步!今天先大体讲下,有时间再进一步拓展下.。
双色模具设计经验免费分享

现在进行实际的模具设计阶段
而不具须 下统的具 的一两有对 设。套相于 计可模同用 方以具的作 法通在基双 来过制准色 完在作坐模 成组生标具 。立产系的 模时,的 块不以两 下会确个 采出保产 用 现双品 由基色, 上准模必
分别对两个产品进行收缩率设置
设 置
这 是 第 二 次 注 塑 产 品 收 缩 率 的
昱卓模具厂收集整理
首先要确认客人制品的所有要求 其次要明确通过何种方式来完成双色注塑 最后来确定模具结构
如图示产品,先要了该制品通过双色成型后的最终结果
1ST
2ND
Production
1、首先来了解一下何谓双色(射)成型
双射成型主要以双射成型机兩只料管配合兩套模具按先后次序经兩次成型制成双射產 品.
因此在模具设计时,必须要同时设计两套模具,通常是两个 型腔不同的前模和两个型腔相同的后模; 在注塑生产时,两套模具同时进行生产,第一次注塑完成后 后模旋转180度后与第二型腔的前模构成一套完整的模具完志第二 次注塑!
3、双色模具的几个特点
a、具有两套相同的后模; b、有两套分别用于成型第一色和第二色的两个前模, 两套前模虽然型腔不同、结构允许有差异(如某些情况下可能会一 套需要行位来完成,而另一套不需要)之外,其余的数据大多要求 保持完全相同(后续特别说明) c、用来制作双色模的两套模架,分中尺寸一定要求完全一致,导柱 孔的位置也必须一致,要求两套模架的前、后模能够自由互换,同 时两套模架的总高也要相同,还要两套前和两套后分别等高(这 一点在购定模架时就需要作特别说明! d、由于双色模具生产目前尚未形成规模,双色机的数量目前还是比 较有限,所以在进行双色模具设计前一定要清楚将要使多大吨位的 塑机来生产,而且双色的锁模孔等参数均不同常规塑机,所以也必 须注意塑机的参数!
双(多)色塑料注射成型3.
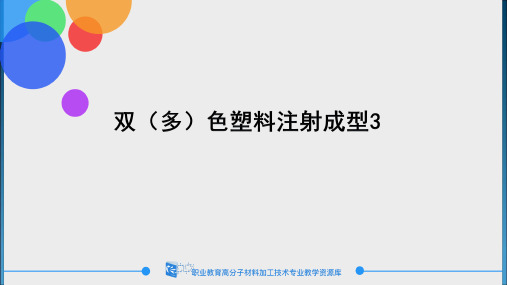
2、双色注射模推出机构的设计 采用分流阀或型芯运动工艺的双色注射模,推出机构与 常规注射模相同。 采用旋转换位工艺的双色注射模 • 当第一色料的浇注系统采用点浇口时,模具的推出机构 仍可按常规注射模一样设计。 • 若第一色料的浇注系统采用潜伏式浇口时,须将推出浇 道凝料和推出塑件的推出机构分为两部分,在第一色料注 射位置,只允许推出浇道凝料,而在第二色料注射位置, 则必须将浇道凝料和双色塑件同时推出,且二者必须能够 联动。
2、双换位机构的设计 (1)平面转盘换位装置 这类双色注射模的模腔换位由注射机提供,模具上无需 设置专门的模腔换位机构。 (2)托芯转盘换位装置 这类双色注射模上必须设计有模腔换位机构,并能与注 射机的托芯装置可靠连接,可随注射机的托芯杆顶升、旋 转及下降复位,同时应保证托芯镶块随换位装置运动过程 中不与模具的顶杆发生干涉。
1、双色注射模浇注系统的设计 (2)浇注系统受其脱模方式的影响 双色注射模第一色料注射完成后,开模时只顶出浇注系 统凝料,而半成品塑件不顶出,并且随动模旋转换位,这 就要求第一色料的浇注系统必须与塑件能自动分离。 通常第一色料的浇注系统宜选用点浇口或潜伏式浇口, 为简化模具结构,第一色料和第二色料的浇注系统类型往 往选用同一种类型为宜。 对于采用分流阀或型芯运动工艺注射成型的双色注射模 的浇注系统则不受此条件限制。
三、双(多)色塑料注射成型模具设计 模具结构设计思路与常规塑料注射模相同,只是在浇注 系统、推出机构和模具型腔换位机构的设计方面存在差异, 需要根据双色塑件所使用的注射成型工艺方法和设备的不 同,进行相应的模具结构设计。
1、双色注射模浇注系统的设计 双色注射模的浇注系统类型、浇注系统结构和浇口位置 的选择,受双色注射机的结构类型影响,同时也受浇注系 统脱模因素的影响。 (1)不同双色注射机对浇注系统形式的影响 V型、L型双色注射机上使用的双色注射模浇注系统一个 垂直于模具分型面,另一个则平行于模具分型面。
双色注塑工艺(3篇)
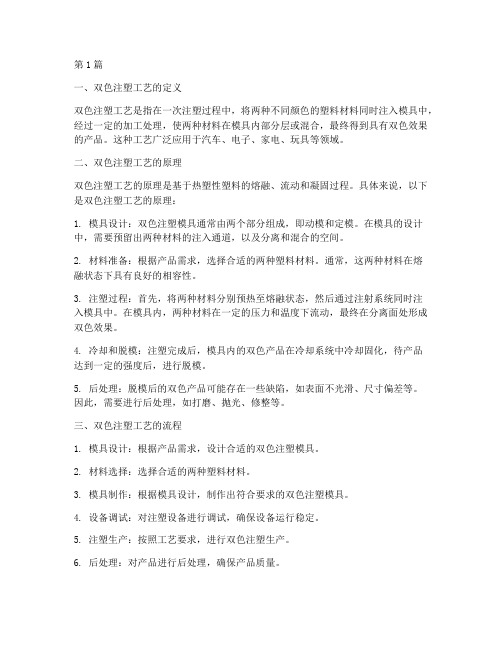
第1篇一、双色注塑工艺的定义双色注塑工艺是指在一次注塑过程中,将两种不同颜色的塑料材料同时注入模具中,经过一定的加工处理,使两种材料在模具内部分层或混合,最终得到具有双色效果的产品。
这种工艺广泛应用于汽车、电子、家电、玩具等领域。
二、双色注塑工艺的原理双色注塑工艺的原理是基于热塑性塑料的熔融、流动和凝固过程。
具体来说,以下是双色注塑工艺的原理:1. 模具设计:双色注塑模具通常由两个部分组成,即动模和定模。
在模具的设计中,需要预留出两种材料的注入通道,以及分离和混合的空间。
2. 材料准备:根据产品需求,选择合适的两种塑料材料。
通常,这两种材料在熔融状态下具有良好的相容性。
3. 注塑过程:首先,将两种材料分别预热至熔融状态,然后通过注射系统同时注入模具中。
在模具内,两种材料在一定的压力和温度下流动,最终在分离面处形成双色效果。
4. 冷却和脱模:注塑完成后,模具内的双色产品在冷却系统中冷却固化,待产品达到一定的强度后,进行脱模。
5. 后处理:脱模后的双色产品可能存在一些缺陷,如表面不光滑、尺寸偏差等。
因此,需要进行后处理,如打磨、抛光、修整等。
三、双色注塑工艺的流程1. 模具设计:根据产品需求,设计合适的双色注塑模具。
2. 材料选择:选择合适的两种塑料材料。
3. 模具制作:根据模具设计,制作出符合要求的双色注塑模具。
4. 设备调试:对注塑设备进行调试,确保设备运行稳定。
5. 注塑生产:按照工艺要求,进行双色注塑生产。
6. 后处理:对产品进行后处理,确保产品质量。
四、双色注塑工艺的应用领域1. 汽车行业:汽车零部件、内饰件等。
2. 电子行业:手机、电脑、电视等电子产品的外壳。
3. 家电行业:冰箱、洗衣机、空调等家电产品的外壳。
4. 玩具行业:玩具、模型等。
5. 医疗器械:医疗器械的外壳等。
五、双色注塑工艺的注意事项1. 模具设计:双色注塑模具的设计要合理,确保两种材料在模具内部分层或混合均匀。
2. 材料选择:选择具有良好相容性的两种塑料材料,确保双色效果。
双色模具设计入门资料
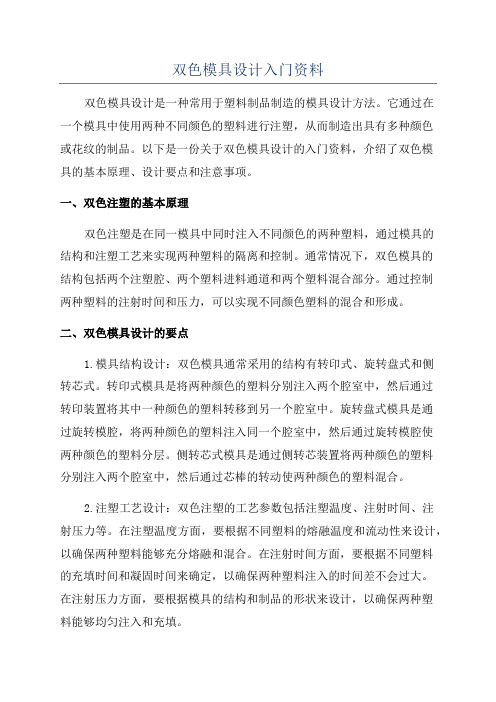
双色模具设计入门资料双色模具设计是一种常用于塑料制品制造的模具设计方法。
它通过在一个模具中使用两种不同颜色的塑料进行注塑,从而制造出具有多种颜色或花纹的制品。
以下是一份关于双色模具设计的入门资料,介绍了双色模具的基本原理、设计要点和注意事项。
一、双色注塑的基本原理双色注塑是在同一模具中同时注入不同颜色的两种塑料,通过模具的结构和注塑工艺来实现两种塑料的隔离和控制。
通常情况下,双色模具的结构包括两个注塑腔、两个塑料进料通道和两个塑料混合部分。
通过控制两种塑料的注射时间和压力,可以实现不同颜色塑料的混合和形成。
二、双色模具设计的要点1.模具结构设计:双色模具通常采用的结构有转印式、旋转盘式和侧转芯式。
转印式模具是将两种颜色的塑料分别注入两个腔室中,然后通过转印装置将其中一种颜色的塑料转移到另一个腔室中。
旋转盘式模具是通过旋转模腔,将两种颜色的塑料注入同一个腔室中,然后通过旋转模腔使两种颜色的塑料分层。
侧转芯式模具是通过侧转芯装置将两种颜色的塑料分别注入两个腔室中,然后通过芯棒的转动使两种颜色的塑料混合。
2.注塑工艺设计:双色注塑的工艺参数包括注塑温度、注射时间、注射压力等。
在注塑温度方面,要根据不同塑料的熔融温度和流动性来设计,以确保两种塑料能够充分熔融和混合。
在注射时间方面,要根据不同塑料的充填时间和凝固时间来确定,以确保两种塑料注入的时间差不会过大。
在注射压力方面,要根据模具的结构和制品的形状来设计,以确保两种塑料能够均匀注入和充填。
三、双色模具设计的注意事项1.模具材料选择:由于双色模具需要承受高温和高压的工作环境,所以模具材料要选择具有良好耐热性、耐腐蚀性和耐磨性的材料,常见的有铝合金、钢等。
2.模具可行性分析:在设计双色模具之前,需要进行模具可行性分析,评估模具结构的可行性和制造成本。
这包括对模具的注塑效果、生产周期和模具维护等方面的评估,以确保设计出的模具能够满足制品的要求和生产的需要。
双色注塑模具设计36条经典经验分享精编版
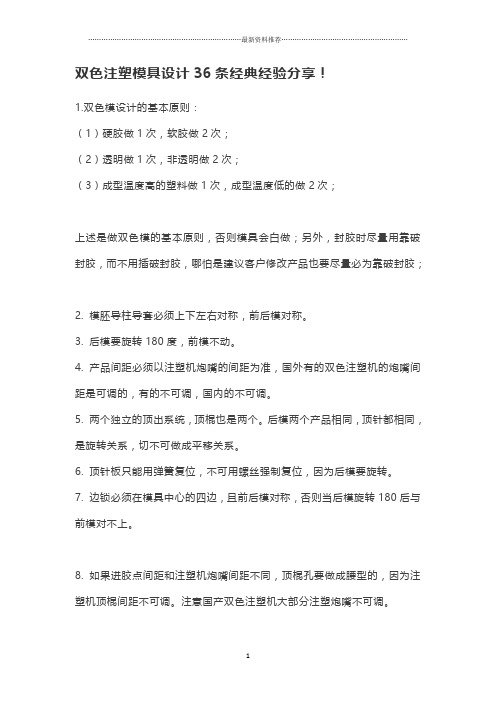
双色注塑模具设计36条经典经验分享!1.双色模设计的基本原则:(1)硬胶做1次,软胶做2次;(2)透明做1次,非透明做2次;(3)成型温度高的塑料做1次,成型温度低的做2次;上述是做双色模的基本原则,否则模具会白做;另外,封胶时尽量用靠破封胶,而不用插破封胶,哪怕是建议客户修改产品也要尽量必为靠破封胶;2. 模胚导柱导套必须上下左右对称,前后模对称。
3. 后模要旋转180度,前模不动。
4. 产品间距必须以注塑机炮嘴的间距为准,国外有的双色注塑机的炮嘴间距是可调的,有的不可调,国内的不可调。
5. 两个独立的顶出系统,顶棍也是两个。
后模两个产品相同,顶针都相同,是旋转关系,切不可做成平移关系。
6. 顶针板只能用弹簧复位,不可用螺丝强制复位,因为后模要旋转。
7. 边锁必须在模具中心的四边,且前后模对称,否则当后模旋转180后与前模对不上。
8. 如果进胶点间距和注塑机炮嘴间距不同,顶棍孔要做成腰型的,因为注塑机顶棍间距不可调。
注意国产双色注塑机大部分注塑炮嘴不可调。
9. 注意客户提供的注塑机平行炮嘴的方向,是x轴或是y轴,以此来定产品排位的布局。
10. 运水进出水的方向必须在天地侧,且每一个循环水的进出都必须在同一面上,不可进水在天,出水在地侧,因为后模要旋转180度,要注意模胚大小不可超过注塑机出水槽的高度,否则无法接运水。
11. 第一次注塑的产品要放在非操作侧,因为第一次注塑后产品要旋转180度进行第二次注塑,正好转到操作侧,方便取产品。
12. 出口模的码模位要在操作侧和非操作侧,不可在天地侧,因为他们的产品要全自动。
13. 分型面的注意事项:后模分型面要将两个产品合并后取得的分型面为后模的;前模分型面要取单个产品的即可,不可取合并后的产品分型面。
14. 前后法兰的公差为负0.05mm,两法兰间距公差为正负0.02mm,顶棍与顶棍孔的间隙单边为0.1mm,前后模导套导柱的中心距公差为正负0.01,模框四边和深度都要加公差,否则当后模旋转180度后,因高低不一致而产生批锋。
双色模具的基本原理和要点

双色模具的基本原理和要点1.引言1.1 概述双色模具是一种用于制造双色产品的模具,它可以同时注塑两种不同颜色的塑料材料,使得最终产品具有丰富的颜色层次感和视觉效果。
通过采用双色模具,生产厂商可以在一次注塑成型过程中完成多种颜色的组合,大大提高了生产效率和产品质量。
双色模具的基本原理是通过在注塑机上安装两个或多个注射装置,并利用旋转或滑动结构使得两种颜色的塑料材料在模具腔内交替注入,最终形成双色产品。
在注射过程中,不同颜色的塑料材料通过熔融状态下的混合和交织,在模具腔内逐渐固化成型,从而实现了双色产品的制造。
在双色模具的设计和制造过程中,需要注意一些要点。
首先,模具的结构设计要合理,能够实现不同颜色塑料材料的分层注入和良好的分子交融,以确保双色产品的色彩过渡自然、层次清晰。
其次,双色模具的注射装置和运动结构要稳定可靠,以确保双色注射过程的准确性和可控性。
此外,模具的材料选择和表面处理也需要考虑,以满足双色产品的质量要求和模具的使用寿命。
总之,双色模具通过注塑机的操作和结构设计,实现了双色产品的快速制造。
它不仅为制造业带来了生产效率和产品质量的提升,也为消费者提供了更加丰富多样的产品选择。
随着技术的不断进步和创新,双色模具在未来的发展前景将更加广阔,有望在各个领域得到更广泛的应用。
1.2 文章结构文章结构部分的内容可以如下所示:文章结构是指文章整体上按照某种逻辑次序组织的方式,由不同的部分组成,每个部分都有其独特的功能和承担的任务。
本文将通过以下几个部分来展开介绍双色模具的基本原理和要点:1. 引言部分:在这一部分中,我们将对双色模具进行概述,介绍其基本概念和应用领域。
同时,我们将给出本文的结构和目的,以便读者能对接下来的内容有一个整体的了解。
2. 正文部分:在这一部分中,我们将详细介绍双色模具的基本原理。
包括双色模具的结构和工作原理等方面的内容,帮助读者全面了解双色模具的基本工作机制。
3. 正文部分:接着我们将进一步介绍双色模具的要点。
双色注塑模具设计36条经典经验分享
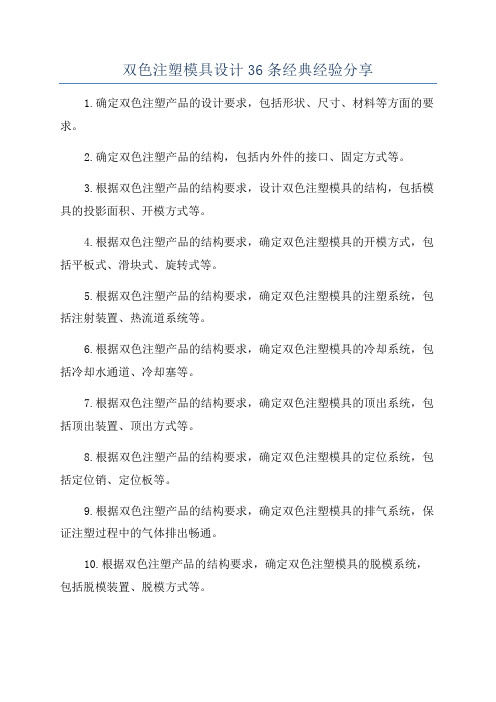
双色注塑模具设计36条经典经验分享1.确定双色注塑产品的设计要求,包括形状、尺寸、材料等方面的要求。
2.确定双色注塑产品的结构,包括内外件的接口、固定方式等。
3.根据双色注塑产品的结构要求,设计双色注塑模具的结构,包括模具的投影面积、开模方式等。
4.根据双色注塑产品的结构要求,确定双色注塑模具的开模方式,包括平板式、滑块式、旋转式等。
5.根据双色注塑产品的结构要求,确定双色注塑模具的注塑系统,包括注射装置、热流道系统等。
6.根据双色注塑产品的结构要求,确定双色注塑模具的冷却系统,包括冷却水通道、冷却塞等。
7.根据双色注塑产品的结构要求,确定双色注塑模具的顶出系统,包括顶出装置、顶出方式等。
8.根据双色注塑产品的结构要求,确定双色注塑模具的定位系统,包括定位销、定位板等。
9.根据双色注塑产品的结构要求,确定双色注塑模具的排气系统,保证注塑过程中的气体排出畅通。
10.根据双色注塑产品的结构要求,确定双色注塑模具的脱模系统,包括脱模装置、脱模方式等。
11.选择合适的模具材料,根据双色注塑产品的要求和生产环境的温度、压力等因素进行选择。
12.根据双色注塑产品的形状和尺寸要求,确定双色注塑模具的尺寸和结构。
13.优化双色注塑模具的结构,减少材料消耗和模具重量。
14.避免双色注塑模具的设计与生产工艺的冲突,确保模具能够顺利生产。
15.使用CAD软件进行双色注塑模具的设计,提高设计效率和准确性。
16.合理设置模具的开模速度和顶出速度,确保双色注塑产品的质量和生产效率。
17.设计模具的冷却系统,以提高生产效率和降低能源消耗。
18.选择合适的注射装置,以提高双色注塑产品的质量和生产效率。
19.设计合适的热流道系统,以提高双色注塑产品的质量和生产效率。
20.设计合适的顶出系统,以提高双色注塑产品的质量和生产效率。
21.设计合适的脱模系统,以提高双色注塑产品的质量和生产效率。
22.合理选择材料和热处理工艺,提高模具的硬度和耐磨性。
- 1、下载文档前请自行甄别文档内容的完整性,平台不提供额外的编辑、内容补充、找答案等附加服务。
- 2、"仅部分预览"的文档,不可在线预览部分如存在完整性等问题,可反馈申请退款(可完整预览的文档不适用该条件!)。
- 3、如文档侵犯您的权益,请联系客服反馈,我们会尽快为您处理(人工客服工作时间:9:00-18:30)。
双色注塑模具设计36条经典经验分享!
1.双色模设计的基本原则:
(1)硬胶做1次,软胶做2次;
(2)透明做1次,非透明做2次;
(3)成型温度高的塑料做1次,成型温度低的做2次;
上述是做双色模的基本原则,否则模具会白做;另外,封胶时尽量用靠破封胶,而不用插破封胶,哪怕是建议客户修改产品也要尽量必为靠破封胶;
2. 模胚导柱导套必须上下左右对称,前后模对称。
3. 后模要旋转180度,前模不动。
4. 产品间距必须以注塑机炮嘴的间距为准,国外有的双色注塑机的炮嘴间距是可调的,有的不可调,国内的不可调。
5. 两个独立的顶出系统,顶棍也是两个。
后模两个产品相同,顶针都相同,是旋转关系,切不可做成平移关系。
6. 顶针板只能用弹簧复位,不可用螺丝强制复位,因为后模要旋转。
7. 边锁必须在模具中心的四边,且前后模对称,否则当后模旋转180后与前模对不上。
8. 如果进胶点间距和注塑机炮嘴间距不同,顶棍孔要做成腰型的,因为注塑机顶棍间距不可调。
注意国产双色注塑机大部分注塑炮嘴不可调。
9. 注意客户提供的注塑机平行炮嘴的方向,是x轴或是y轴,以此来定产品排位的布局。
10. 运水进出水的方向必须在天地侧,且每一个循环水的进出都必须在同一面上,不可进水在天,出水在地侧,因为后模要旋转180度,要注意模胚大小不可超过注塑机出水槽的高度,否则无法接运水。
11. 第一次注塑的产品要放在非操作侧,因为第一次注塑后产品要旋转180度进行第二次注塑,正好转到操作侧,方便取产品。
12. 出口模的码模位要在操作侧和非操作侧,不可在天地侧,因为他们的产品要全自动。
13. 分型面的注意事项:后模分型面要将两个产品合并后取得的分型面为后模的;前模分型面要取单个产品的即可,不可取合并后的产品分型面。
14. 前后法兰的公差为负0.05mm,两法兰间距公差为正负0.02mm,顶棍与顶棍孔的间隙单边为0.1mm,前后模导套导柱的中心距公差为正负0.01,模框四边和深度都要加公差,否则当后模旋转180度后,因高低不一致而产生批锋。
框深公差为负0.02mm。
15. 如果在模胚厂已经将模胚加工完,本厂要加工唧嘴和顶棍孔时,要以4个导柱导套孔的间距中心为基准取数,否则偏差太多,容易卡死模。
订模胚时要注明是双色模胚,四个导柱导套和框对称,后模旋转180度后能与前模匹配。
16. 如果是后模旋转的双色话就简单多了,两个前模芯一样,一边注塑好硬胶后.旋转180度(注意产品转的时候不能掉落,浇口可以自动分离) , 转到另外一边后再注塑软胶,注塑硬胶无需布置顶针,只需布置在软胶这边模芯即可,另外缩水要注意,如果软胶完全把硬胶缠住,则只需放硬胶的缩水,如果是轮廓相接则硬胶软胶都要放缩水。
17. 如果是一套模具的双色模具的话,那就是一个直炮筒,一个90度的炮筒射胶,不需要旋转,只需一个模芯,软胶与硬胶的分离方法靠行位封胶。
18. cavity的两个外形是不同的,分别成型1种产品。
而core的两个外形完好一样。
19. 模具的前、后模以中心旋转180°后,必需吻合。
设计时必需做这个检查动作。
20. 留意顶针孔的位置,最小间隔210mm。
大的模具须恰当增加顶棍孔的数量。
并且,由于注塑机本身附带的顶针不够长,所以我们的模具中必需设计加长顶针,顶针长出模胚底板150mm左右。
21. 后模底板上必需设计2个定位圈。
22. 前模面板加a板的总厚度不能少于170mm。
请认真查看这种型号的注塑机的其它参考数据,比方,最大容模厚度、最小容模厚度、顶棍孔间隔等。
23. 前侧sprue的深度不要超越65mm。
上侧(大水口)sprue的顶部到模胚中心的间隔不小于150mm。
24. 在设计第二次注塑的cavity时,为了防止cavity插(或擦)伤第一次曾经成型好的产品胶位,可以设计一局部避空。
但是必需慎重思索每一处封胶位的强度,即:在注塑中,能否会有在大的注塑压力下,塑胶发作变形,招致第二次注塑可能会有批锋产生的可能;
25. 注塑时,第一次注塑成型的产品尺寸可以略大,以使它在第二次成型时能与另一个cavity压得更紧,以到达封胶的作用。
26. 在a、b板合模前,要留意前模slider或lifter能否会先复位而压坏产品?如此,必需想方法使在a、b板先合模,之后前模的slider或lifet才干复位。
27. 两cavity和core的运水布置尽量充分,并且平衡、一样。
28. 99%的情况是先注塑产品的硬胶局部,再注塑产品的软胶局部。
由于软胶易变形。
29. 留意在第二次注塑时,塑胶的活动能否会冲动第一次曾经成型好的产品,使其胶位变形?假设有这个可能,一定要想方法改善。
30. 双色模具一定要谨慎选择浇口位置。
一次产品最好选择潜伏式进胶,这样产品和流道可以自动切断。
当无法采用潜伏式进胶时,可以考虑三板模或者热流道模具。
一次料如果是点浇口,要做波仔,避免因一次进点残留而碰穿二次料。
31. 双色注塑模具常采用旋转注塑模。
旋转注塑模两个位置上的凸模/凹模要求尺寸、精度一致,且与凹模/凸模配合良好。
当无法利用双色注塑机上的顶出脱模机构时,回转台上必须要设置液压顶出脱模机构。
32. 双色模具注塑成型通常选用不同颜色的同一种塑料,也可以是两种不同的塑料原料,这个时候就要考虑两种材料的界面作用、收缩率差异、加工工艺参数等方面了。
双色注塑制品一般以abs、pc等硬塑料配合tpe软塑料为主,由于成本或应用的关系,要充分考虑采用的两种物料之间可能没有良好的粘合性和融合性,两种料之间结合处的模具处理(一般都会有压花纹路的现象或者需要做封模槽)还有料厚的厚度等很多问题!为了使两种塑胶“粘”得更紧,要思索材料之间的“粘性”以及模具外表的粗糙度。
双色注塑有专用的tpu 材料;而模具外表越光滑,它们“粘得越紧。
33. 一般来说,双色模具的缩水率取决于一次材料。
因为一次材料已经把塑料制品的轮廓撑住了,二次材料不会收缩更多。
至于如何确定一次材料
和二次材料,这有许多要考虑到的因素,比如原料流动性,塑料制品形状等等。
34. 留意前后模的定位;一切插穿、靠破面的斜度落差尽量大些,要0.1mm 以上。
35. abs/pc,abs/pc+abs,abs/pmma双色注塑时,需要先注塑温度较高的pc,pc+abs或者pmma。
如果是透明面壳模具时大部分采用倒装模具结构。
36. 透明的大的双色注塑对于结构设计而言是需要注意的地方:
a. 浇口位置的预留,必须和模具厂预先达成一致;
b. 材料厚度推荐使用透明的0.8mm以上,非透明的0.7mm以上,非透明的尽量采用浅色,有led灯时候注意遮光;
c. 透明件分模面和孔的地方宽度一致,宽度推荐0.5mm,曲面接顺,避免侧面看,能透过很远,不美观,尽量减少孔;
d. 非透明件的厚度有限,上面筋条等结构尽量是在0.5-0.6mm之间,避免缩水;
e. 就目前而言不推荐做带主镜片的双色注塑,模具和产品成本太高,对模具厂家的设备和技术水平有相当的要求,做的话,需要对方给出整个一个流程的解决详细方案供评估,针对中间的环节都需要审查;
f. 对于大面积的双色注塑件,两个关键的测试是跌落和冷热冲击,在这两个测试里面,透明件和非透明件容易脱开。
冷热冲击-40 -65,时间48小时。
g. 双色件上结构尽量简化,复杂的做到配合件上面,非透明件的筋条宽度尽量在0.5-0.6,避免缩水。