复杂曲面精密加工的发展现状和趋势
复杂曲面零件的加工与测量技术
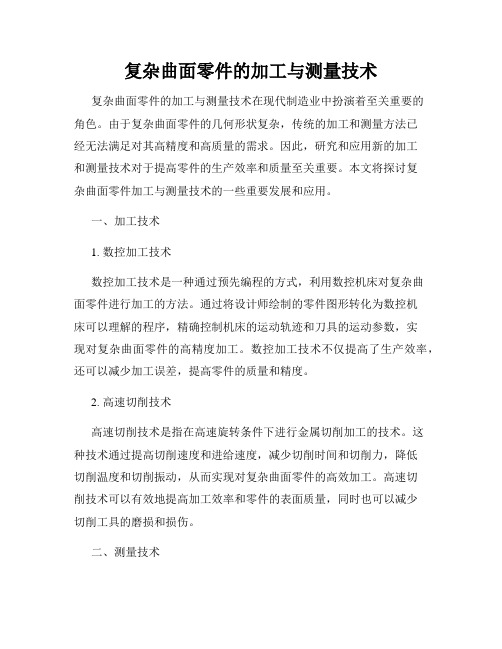
复杂曲面零件的加工与测量技术复杂曲面零件的加工与测量技术在现代制造业中扮演着至关重要的角色。
由于复杂曲面零件的几何形状复杂,传统的加工和测量方法已经无法满足对其高精度和高质量的需求。
因此,研究和应用新的加工和测量技术对于提高零件的生产效率和质量至关重要。
本文将探讨复杂曲面零件加工与测量技术的一些重要发展和应用。
一、加工技术1. 数控加工技术数控加工技术是一种通过预先编程的方式,利用数控机床对复杂曲面零件进行加工的方法。
通过将设计师绘制的零件图形转化为数控机床可以理解的程序,精确控制机床的运动轨迹和刀具的运动参数,实现对复杂曲面零件的高精度加工。
数控加工技术不仅提高了生产效率,还可以减少加工误差,提高零件的质量和精度。
2. 高速切削技术高速切削技术是指在高速旋转条件下进行金属切削加工的技术。
这种技术通过提高切削速度和进给速度,减少切削时间和切削力,降低切削温度和切削振动,从而实现对复杂曲面零件的高效加工。
高速切削技术可以有效地提高加工效率和零件的表面质量,同时也可以减少切削工具的磨损和损伤。
二、测量技术1. 光学测量技术光学测量技术是利用光学原理对复杂曲面零件进行测量的方法。
常用的光学测量技术包括激光测量、视觉测量和相机测量等。
这些技术可以非接触地获取零件的三维形貌和尺寸信息,并通过计算机处理和分析,得到零件的测量结果。
光学测量技术具有高精度、高效率和非接触等优点,广泛应用于复杂曲面零件的测量领域。
2. 接触式测量技术接触式测量技术是指通过接触传感器对复杂曲面零件进行测量的方法。
常用的接触式测量技术包括坐标测量、形状测量和表面测量等。
这些技术通过在零件表面接触传感器进行测量,获取零件的形状、尺寸和表面粗糙度等信息。
接触式测量技术具有高精度和可靠性的特点,适用于对复杂曲面零件的几何形状和尺寸进行测量。
三、加工与测量技术的应用1. 航空航天工业在航空航天工业中,复杂曲面零件的加工和测量技术对飞机和宇宙飞船的制造具有重要意义。
精密和超精密加工现状与发展趋势
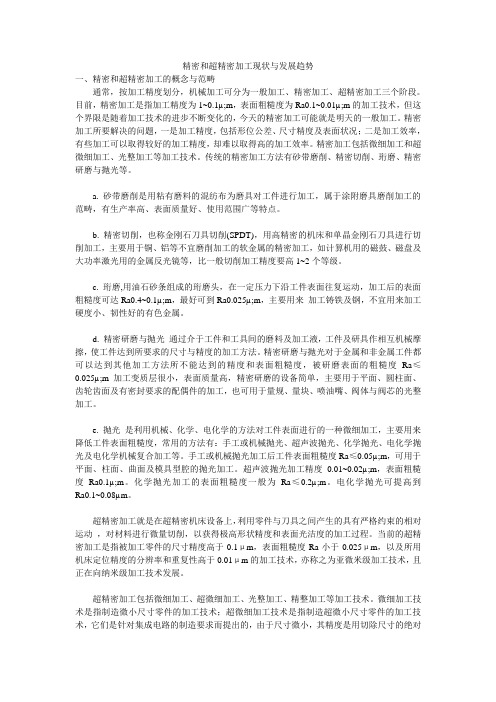
精密和超精密加工现状与发展趋势一、精密和超精密加工的概念与范畴通常,按加工精度划分,机械加工可分为一般加工、精密加工、超精密加工三个阶段。
目前,精密加工是指加工精度为1~0.1µ;m,表面粗糙度为Ra0.1~0.01µ;m的加工技术,但这个界限是随着加工技术的进步不断变化的,今天的精密加工可能就是明天的一般加工。
精密加工所要解决的问题,一是加工精度,包括形位公差、尺寸精度及表面状况;二是加工效率,有些加工可以取得较好的加工精度,却难以取得高的加工效率。
精密加工包括微细加工和超微细加工、光整加工等加工技术。
传统的精密加工方法有砂带磨削、精密切削、珩磨、精密研磨与抛光等。
a. 砂带磨削是用粘有磨料的混纺布为磨具对工件进行加工,属于涂附磨具磨削加工的范畴,有生产率高、表面质量好、使用范围广等特点。
b. 精密切削,也称金刚石刀具切削(SPDT),用高精密的机床和单晶金刚石刀具进行切削加工,主要用于铜、铝等不宜磨削加工的软金属的精密加工,如计算机用的磁鼓、磁盘及大功率激光用的金属反光镜等,比一般切削加工精度要高1~2个等级。
c. 珩磨,用油石砂条组成的珩磨头,在一定压力下沿工件表面往复运动,加工后的表面粗糙度可达Ra0.4~0.1µ;m,最好可到Ra0.025µ;m,主要用来加工铸铁及钢,不宜用来加工硬度小、韧性好的有色金属。
d. 精密研磨与抛光通过介于工件和工具间的磨料及加工液,工件及研具作相互机械摩擦,使工件达到所要求的尺寸与精度的加工方法。
精密研磨与抛光对于金属和非金属工件都可以达到其他加工方法所不能达到的精度和表面粗糙度,被研磨表面的粗糙度Ra≤0.025µ;m加工变质层很小,表面质量高,精密研磨的设备简单,主要用于平面、圆柱面、齿轮齿面及有密封要求的配偶件的加工,也可用于量规、量块、喷油嘴、阀体与阀芯的光整加工。
e. 抛光是利用机械、化学、电化学的方法对工件表面进行的一种微细加工,主要用来降低工件表面粗糙度,常用的方法有:手工或机械抛光、超声波抛光、化学抛光、电化学抛光及电化学机械复合加工等。
数控加工中心五轴复杂曲面零件加工技术研究及加工精度控制

数控加工中心五轴复杂曲面零件加工技术研究及加工精度控制摘要:随着社会经济的不断发展,各行各业对产品制造精度的要求越来越高。
而数控加工中心是一种高效率、高精度、多功能的加工设备,已成为现代制造业必不可少的工具。
为了满足现代制造业对于高精度、高效率及多样化的加工需求,数控加工中心五轴复杂曲面零件加工技术得到广泛关注。
本文研究该领域中的加工过程和加工精度控制,并提出一种基于机器学习的方法用于优化加工参数,显著地提高了加工效率和精度。
关键词:数控加工中心;五轴复杂曲面;加工技术;精度控制;机器学习一、数控加工中心和五轴复杂曲面零件的特点和加工难点数控加工中心和五轴复杂曲面零件是现代制造业中的重要设备和关键部件。
数控加工中心以其高效、高精度和多功能等特点,成为现代制造业不可或缺的加工工具,而五轴复杂曲面零件则由于其异常复杂的形状和表面几何变化,难以通过常规方式进行加工,因此充满挑战性,也因此引起了广泛的关注。
在加工过程中,数控加工中心一般采用立式刀库,能够根据需要调整角度和位置,实现多种加工操作。
五轴复杂曲面零件的特点则在于它们所具有的极端复杂的几何形状和表面设计,包括向外突出的棱和边、开口孔和内部各种壁面,而这些都需要经过精密的加工才能达到标准。
然而,在面对加工复杂曲面零件时,存在着以下几大加工难点:几何参数测量:针对五轴复杂曲面零件,必须完全了解这样一个元件形状中的复杂性质并产生命令来摆放该物体进行加工;工具路径规划:为了处理复杂曲面上的不同加工区域,需要寻找合适的、高效率的轨迹以用来掌控工件在加工期间机器终端上的运动;剪力和热源问题:五轴复杂曲面零件的特殊形态给剪力和热源性能带来了挑战。
较大的压力会导致断屑、撕裂,并影响表面质量;同时温度过高也会导致损坏。
加工精度控制:由于其表面几何变化比较大,需要高精度的控制方案才能够确保正常完成任务。
二、数控加工中心和五轴复杂曲面零件在现代制造业中的重要性数控加工中心和五轴复杂曲面零件在现代制造业中具有极为重要的地位。
五轴数控技术发展有哪些困难和阻力?

五轴数控技术发展有哪些困难和阻力?五轴数控加工是数控技术中难度最大、应用最广泛的技术。
它集计算机控制、高性能伺服驱动、精密加工技术于一体,用于复杂曲面的高效、精密、自动化加工。
与三轴CNC加工相比,从工艺和编程的角度来看,复杂曲面的五轴CNC加工具有以下优势:1.提高加工质量和效率2.扩大工艺范围迎接复合材料发展的新方向但是,由于加工空间中刀具的干涉和位置控制,五轴数控加工的数控编程、数控系统、机床结构都比三轴机床复杂得多。
因此,真正实现五轴加工很难,更难操作和使用好。
真假五轴加工说起五轴加工,就不得不说真假五轴加工。
真假五轴加工的主要区别在于是否具有RTCP功能。
RTCP是“旋转工具中心点”的缩写。
只有带RTCP 功能的五轴加工才是真正的五轴加工。
不具备RTCP功能的五轴机床和数控系统必须依靠CAM编程和后处理,提前规划好刀具路径。
对于同一个零件,如果换了机床,或者刀具改变了,必须重新进行CAM编程和后处理,所以只能称为假五轴加工。
简而言之,真五轴加工就是五轴五联动,而假五轴加工可能是五轴三联动,另外两轴只起定位作用。
五轴数控技术发展的难点和阻力虽然我们都知道五轴数控技术的优越性和重要性。
但五轴数控技术的应用还仅限于一些规模比较大的企业,还存在一些未解决的问题。
下面详述了一些困难和阻力。
1、五轴CNC编程抽象,操作难度大这是每一个传统CNC程序员都深感难解的问题。
三轴机床只有直线坐标轴,而五轴数控机床结构多样。
相同的NC代码在不同的三轴数控机床上可以达到同样的加工效果,但五轴机床的NC代码不能适用于所有类型的五轴机床。
CNC编程除了直线运动外,还必须坐标旋转运动的相关计算,如旋转角度行程检查、非线性误差检查、刀具旋转计算等。
处理的信息量非常大,CNC编程极其抽象。
五轴数控加工的操作与编程技巧息息相关。
如果用户在机床上增加特殊功能,编程和操作会更加复杂。
只有反复练习,编程和操作人员才能掌握必要的知识和技能。
2023年全国职业院校技能大赛高职组复杂部件数控多轴联动加工技术数控多轴加工技术

2023年全国职业院校技能大赛高职组复杂部件数控多轴联动加工技术数控多轴加工技术。
2023年全国职业院校技能大赛高职组复杂部件数控多轴联动加工技术数控多轴加工技术序在2023年全国职业院校技能大赛高职组中,复杂部件数控多轴联动加工技术和数控多轴加工技术将成为备受关注的主题。
这两项技术在制造业中具有重要意义,尤其在高端装备制造领域有着广泛的应用。
本文将从深度和广度两方面对这两项技术进行全面评估,并探讨其在现代制造业中的意义和挑战。
1. 复杂部件数控多轴联动加工技术的意义复杂部件数控多轴联动加工技术是一种高精度、高效率的加工技术,它可以实现对复杂零部件的精密加工和加工效率的提升。
在工业制造中,很多复杂部件都需要经过精密加工才能满足产品的质量要求,而数控多轴联动加工技术正是为了解决这一难题而应运而生的。
通过多轴联动加工,可以实现对复杂曲面的加工,大大提高了生产效率和产品质量。
2. 数控多轴加工技术的应用另数控多轴加工技术也具有重要意义。
它是一种通过多轴协同工作来完成加工任务的技术,可以实现对多种复杂形状的加工。
在汽车、航空航天、船舶等行业中,很多零部件都需要经过数控多轴加工才能满足产品的要求。
这项技术的应用不仅提高了加工精度,还大大缩短了加工周期,降低了生产成本。
3. 技术挑战和发展趋势然而,复杂部件数控多轴联动加工技术和数控多轴加工技术也面临着一些挑战。
技术本身的复杂性和高度要求需要操作人员具备较高的技能和经验,这对于技术人才提出了更高的要求。
随着制造业的发展,对于产品精度和加工效率的要求也在不断提高,这就需要技术不断创新和提升。
4. 个人观点和总结从我个人的观点来看,复杂部件数控多轴联动加工技术和数控多轴加工技术是现代制造业不可或缺的重要技术。
它们不仅可以提高产品的质量和生产效率,还可以降低生产成本,提高企业竞争力。
然而,要想在这两项技术领域取得突破,我们需要不断加强技术研发和人才培养,促进技术的应用和创新。
精密和超精密加工技术的发展
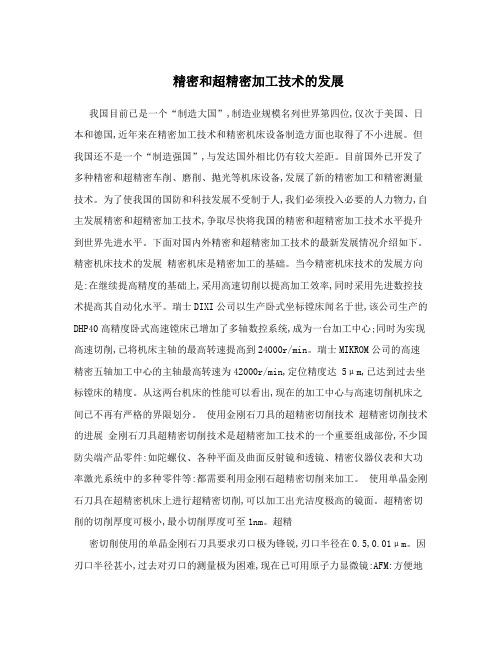
精密和超精密加工技术的发展我国目前已是一个“制造大国”,制造业规模名列世界第四位,仅次于美国、日本和德国,近年来在精密加工技术和精密机床设备制造方面也取得了不小进展。
但我国还不是一个“制造强国”,与发达国外相比仍有较大差距。
目前国外已开发了多种精密和超精密车削、磨削、抛光等机床设备,发展了新的精密加工和精密测量技术。
为了使我国的国防和科技发展不受制于人,我们必须投入必要的人力物力,自主发展精密和超精密加工技术,争取尽快将我国的精密和超精密加工技术水平提升到世界先进水平。
下面对国内外精密和超精密加工技术的最新发展情况介绍如下。
精密机床技术的发展精密机床是精密加工的基础。
当今精密机床技术的发展方向是:在继续提高精度的基础上,采用高速切削以提高加工效率,同时采用先进数控技术提高其自动化水平。
瑞士DIXI公司以生产卧式坐标镗床闻名于世,该公司生产的DHP40高精度卧式高速镗床已增加了多轴数控系统,成为一台加工中心;同时为实现高速切削,已将机床主轴的最高转速提高到24000r/min。
瑞士MIKROM公司的高速精密五轴加工中心的主轴最高转速为42000r/min,定位精度达5μm,已达到过去坐标镗床的精度。
从这两台机床的性能可以看出,现在的加工中心与高速切削机床之间已不再有严格的界限划分。
使用金刚石刀具的超精密切削技术超精密切削技术的进展金刚石刀具超精密切削技术是超精密加工技术的一个重要组成部份,不少国防尖端产品零件:如陀螺仪、各种平面及曲面反射镜和透镜、精密仪器仪表和大功率激光系统中的多种零件等:都需要利用金刚石超精密切削来加工。
使用单晶金刚石刀具在超精密机床上进行超精密切削,可以加工出光洁度极高的镜面。
超精密切削的切削厚度可极小,最小切削厚度可至1nm。
超精密切削使用的单晶金刚石刀具要求刃口极为锋锐,刃口半径在0.5,0.01μm。
因刃口半径甚小,过去对刃口的测量极为困难,现在已可用原子力显微镜:AFM:方便地进行测量。
精密和超精密加工机床的现状及发展对策

工作台尺寸 (宽×长) 800 mm×1 500 mm
最大加工高度
500 mm
最大通过宽度
1 100 mm
工作台进给速度
0.01~30 m/min
砂轮尺寸 (外径×宽) Φ510 mm×100 mm
砂轮转速
1 000~4 000 r/min
砂轮最小进刀量
0.2 μm
在高精度加工的范畴内, 根据精度水平的不 同, 分为 3 个档次:
2
Oct. 2010
第27卷 第10期 Vol.27 No.10
精 度 为 0.3~3 μm, 粗 糙 度 为 0.03~0.3 μm 的 为 精密加工;
精 度 为 0.03~0.3 μm, 粗 糙 度 为 0.005~0.03 μm 的称作超精密加工, 或亚微米加工;
年度 2000 2003 2006 2007
表1 我国机床进出口情况 (亿 美元)
产值 21.97 23.80 64.00 111.9
出口 2.99 3.80 11.90 16.50
进口 18.90 41.60 72.40 70.70
消费 37.88 67.00 131.10 166.10
由于国外对我们封锁禁运一些重要的高精度机 床设备和仪器, 而这些精密设备仪器正是国防和尖 端技术发展所迫切需要的, 因此, 我们必须投入必 要的人力物力, 自主发展精密和超精密加工机床, 使我国的国防和科技发展不会受制于人。
磨头0 mm/min
磨头的横向进给速度 1~4 000 mm/min
砂轮轴驱动电机
11 kW (4P)
机床尺寸 (宽×长×高) 约3 600 mm×5 800 mm×3 700 mm
精密复杂曲面零件多轴数控加工技术研究

精密复杂曲面零件多轴数控加工技术研究摘要:随着时代发展的推动,各行各业的发展与改革也在不断向前推进,在现代工业领域,多轴数控加工技术已经成为了该领域的标志性加工技术,在我国的运载工具、国防、能源、航空航天、动力等领域的关键零部件加工中,多轴数控加工技术均发挥着重要的作用。
而伴随着各个领域对于装备性能的要求在不断提升,精密复杂曲面零件随之产生,该零件本身具备性能指标要求苛刻、加工难度大等特点,关于精密复杂曲面零件的加工,已经从原有的形位精度要求,转变成为性能指标与形位并重的高性能加工要求,这种转变的产生,给传统精密复杂曲面零件技术的革新带来了契机。
本文将针对精密复杂曲面零件的多轴数控加工技术进行分析与研究。
关键词:精密复杂曲面零件;多轴数控加工;技术研究随着我国综合国力的增强以及科学技术水平的不断提升,我国的制造业领域也在不断发展和拓展,在这其中,一批精密复杂曲面零件不断涌现出来,例如,航空发动机的叶片和机匣、大型航空运载工具的天线罩以及精密壳体等都属于精密复杂曲面零件。
因为此类零件的超常规使役环境,在进行制造的过程中,主要制造要求就要以气动特性、透波、导流以及抗疲劳性等的性能指标为主。
而为了进一步满足相关性能指标的要求,该类软件的结构以及形状发展的愈发复杂,一般具有极端大尺度比以及薄壁悬挂等显著特点。
1多轴数控加工的相关概述数控加工的过程是经过模型曲面上的加工路径直接进行驱动的,所以,高效的加工路径设计方法是保证零件表面形成精度以及加工效率提升的关键所在。
但是,传统的路径规划方法具有拘泥于几何层面进行离散调整以及逐点进行路径设计的特点,这种特点的具备从切割特性层面以及运动学角度考虑,能够将加工路径拓扑成几何形状的方法较少,无法将曲面几何的物理特性进行兼顾,也难以实现关于路径的整体性调控,十分不利于加工生产工作的进行。
在进行复杂曲面的数控加工过程中,运动规划也是非常重要的,特别是在复杂曲面零件的高精度高速加工过程中,关于适应性进给率定制加工技术的使用,是保证加工效率、保证加工精度的有效措施[1]。
发展精密和超精密加工技术的重要性

发展精密和超精密加工技术的重要性精密和超精密加工代表了加工精度发展的不同阶段,通常,按加工精度划分,可将机械加工分为一般加工,精密加工,超精密加工三个阶段精密加工;加工精度在0.1 -1um,讲表面粗糙度在Ra 0.02-0.1um之间的加工方法称为精密加工超精密加工;加工精度高于0.1um,加工表面粗糙度小于Ra 0.01um的加工方法称为超精密加工。
(微细加工、超微细加工、光整加工、精整加工等)二提高加工精度的原因提高制造精度后可提高产品的性能和质量,提高产品稳定性和可靠性;促进产品小型化;增强零件的互换性,提高装配生产率,并促进自动化装配。
三发展超精密加工的重要性1 超精密加工是国家制造工业水平的重要标志之一超精密加工所能达到的精度、表面粗糙度、加工尺寸范围和几何形状是一个国家制造技术水平的重要标志之一。
金刚石刀具切削刃钝圆半径的大小是金刚石刀具超精密切削的一个关键技术参数,日本声称已达到2nm,而我国尚处于亚微米水平,相差一个数量级(国际上公认0.1nm~100nm为纳米尺度空间,100nm~1000nm为亚微米体系,小于1个纳米为原子团簇);金刚石微粉砂轮超精密磨削在日本已用于生产,使制造水平有了大幅度提高,突出地解决了超精密磨削磨料加工效率低的问题。
2 精密和超精密加工是先进制造技术的基础和关键计算机工业的发展不仅要在软件上,还要在硬件上,即在集成电路芯片上有很强的能力,我国集成电路的制造水平约束了计算机工业的发展。
美国制造工程研究者提出的汽车制造业的“两毫米工程”(车身尺寸变动量控制在2mm以内)使汽车质量赶上欧、日水平,其中的举措都是实实在在的制造技术。
3 国防工业上的需求陀螺仪的加工涉及多项超精密加工,导弹系统的陀螺仪质量直接影响其命中率,1kg的陀螺转子,其质量中心偏离其对称轴0.0005μm,则会引起100m的射程误差和50m的轨道误差。
大型天体望远镜的透镜、直径达 2.4m,形状精度为0.01μm,如著名的哈勃太空望远镜,能观察140亿光年的天体(六轴CNC研磨抛光机)(图)。
国内外数控技术的发展现状与趋势

国内外数控技术的发展现状与趋势一、本文概述数控技术,即数控加工编程技术,是现代制造业的核心技术之一,它涉及到计算机编程、机械设计、自动控制等多个领域。
随着科技的飞速发展,数控技术在国内外都取得了显著的进步,广泛应用于航空航天、汽车制造、模具加工等各个行业。
本文将对国内外数控技术的发展现状与趋势进行深入探讨,以期了解数控技术的最新发展动态,为相关领域的从业者提供有益的参考。
本文将回顾数控技术的起源与发展历程,从最初的简单数控系统到现在的高度智能化、网络化数控系统,阐述数控技术在国内外的发展历程和主要成就。
接着,本文将重点分析国内外数控技术的现状,包括数控系统、数控机床、数控编程软件等方面的发展情况,以及数控技术在各个行业的应用现状。
同时,本文还将探讨数控技术发展中的关键问题,如精度与效率、智能化与自动化、开放性与标准化等。
在趋势分析方面,本文将关注数控技术的前沿动态,探讨数控技术的未来发展方向。
随着、大数据、云计算等新一代信息技术的快速发展,数控技术将如何实现与这些技术的深度融合,提高加工精度、效率和智能化水平,将是本文关注的重点。
本文还将分析数控技术在绿色制造、智能制造等领域的应用前景,以及国内外数控技术市场竞争格局的变化趋势。
本文旨在全面梳理国内外数控技术的发展现状与趋势,为相关领域的从业者提供有价值的参考信息,推动数控技术的持续创新与发展。
二、数控技术的历史回顾数控技术,即数字控制技术,其发展历程可以追溯到20世纪40年代末。
初期的数控技术主要应用于军事工业,例如美国为了制造飞机叶片而研发的数控铣床。
随着计算机技术的飞速发展和普及,数控技术也逐步实现了电子化、信息化和智能化。
20世纪50年代,数控技术开始进入商业应用领域,主要用于机床加工和自动化生产线。
此时,数控系统多为硬件连线式,编程复杂,灵活性差。
进入60年代,随着计算机软件技术的发展,数控系统开始采用软件编程,大大提高了编程的灵活性和效率。
浅谈数控技术在数控铣床中的应用

浅谈数控技术在数控铣床中的应用一、数控技术在数控铣床中的基本原理数控技术是指利用数控系统对机床进行自动控制,实现工件的加工。
数控系统包括硬件和软件两部分,硬件包括数控装置、伺服系统、执行机构等,软件则包括数控编程、数控操作等内容。
数控铣床通过数控系统控制刀具在不同方向上进行运动,实现对工件的精密加工。
数控铣床的数控系统利用计算机进行控制,可以实现对工件的各种加工操作。
数控系统通过数学模型进行计算,确定刀具的运动轨迹和加工路径,然后通过控制系统实现刀具的精确控制。
数控系统还可以实现对加工参数的精确调节,确保加工的精度和表面质量。
二、数控技术在数控铣床中的应用1. 高精度加工数控技术可以实现对刀具的高精度控制,可以在工件上进行微小的切削,实现对工件的高精度加工。
数控铣床可以实现对各种复杂曲面的加工,可以加工出精密的零件和模具。
2. 多轴联动加工数控系统可以实现对多轴的联动控制,可以同时控制数个刀具进行加工。
这样可以大大提高加工效率和精度,实现复杂零件的加工。
3. 自动化生产数控系统可以实现对整个加工过程的自动化控制,包括送料、定位、加工、卸料等操作。
可以实现对批量零件的高效加工,提高生产效率。
4. 灵活的加工方式数控系统可以实现对不同工件的灵活加工,可以根据工件的要求进行编程,实现加工过程的灵活控制。
可以实现对不同形状、不同尺寸的工件进行高效加工。
5. 实时监控和调整数控系统可以实时监控加工过程中的各种参数,可以根据实际情况对加工参数进行实时调整,确保加工的质量和效率。
三、数控技术在数控铣床中的发展趋势1. 高速加工随着数控系统的发展,数控铣床可以实现对工件的高速加工,大大提高了加工效率。
高速加工可以提高生产效率,减少加工成本,是未来数控铣床发展的一个重要方向。
2. 智能化控制未来数控系统将会更加智能化,可以通过人工智能技术实现对加工过程的智能监控和自动调整,大大提高了生产效率和品质稳定性。
3. 精密加工未来数控铣床将会更加注重对零件的精密加工,可以实现对微小尺寸零件的加工和精密模具的加工,满足高精度加工的需求。
精密和超精密加工现状与发展趋势.doc

精密和超精密加工现状与发展趋势核心提示:当前精密和超精密加工精度从微米到亚微米,乃至纳米,在汽车、家电、IT电子信息高技术领域和军用、民用工业有广泛应用。
同时,精密和超精密加工技术的发展也促进了机械、模具、液压、电子、半导体、光学、传感器和测量技术及金属加工工业的发展。
一、精密和超精密加工的概念与范畴通常,按加工精度划分,机械加工可分为一般加工、精密加工、超精密加工三个阶段。
目前,精密加工是指加工精度为1~0.1μm,表面粗糙度为Ra0.1~0.01μm的加工技术,但这个界限是随着加工技术的进步不断变化的,今天的精密加工可能就是明天的一般加工。
精密加工所要解决的问题,一是加工精度,包括形位公差、尺寸精度及表面状况;二是加工效率,有些加工可以取得较好的加工精度,却难以取得高的加工效率。
精密加工包括微细加工和超微细加工、光整加工等加工技术。
传统的精密加工方法有砂带磨削、精密切削、珩磨、精密研磨与抛光等。
a. 砂带磨削是用粘有磨料的混纺布为磨具对工件进行加工,属于涂附磨具磨削加工的范畴,有生产率高、表面质量好、使用范围广等特点。
b. 精密切削,也称金刚石刀具切削(SPDT),用高精密的机床和单晶金刚石刀具进行切削加工,主要用于铜、铝等不宜磨削加工的软金属的精密加工,如计算机用的磁鼓、磁盘及大功率激光用的金属反光镜等,比一般切削加工精度要高1~2个等级。
c. 珩磨,用油石砂条组成的珩磨头,在一定压力下沿工件表面往复运动,加工后的表面粗糙度可达Ra0.4~0.1μm,最好可到Ra0.025μm,主要用来加工铸铁及钢,不宜用来加工硬度小、韧性好的有色金属。
d. 精密研磨与抛光通过介于工件和工具间的磨料及加工液,工件及研具作相互机械摩擦,使工件达到所要求的尺寸与精度的加工方法。
精密研磨与抛光对于金属和非金属工件都可以达到其他加工方法所不能达到的精度和表面粗糙度,被研磨表面的粗糙度Ra≤0.025μm加工变质层很小,表面质量高,精密研磨的设备简单,主要用于平面、圆柱面、齿轮齿面及有密封要求的配偶件的加工,也可用于量规、量块、喷油嘴、阀体与阀芯的光整加工。
超精密加工技术的发展现状
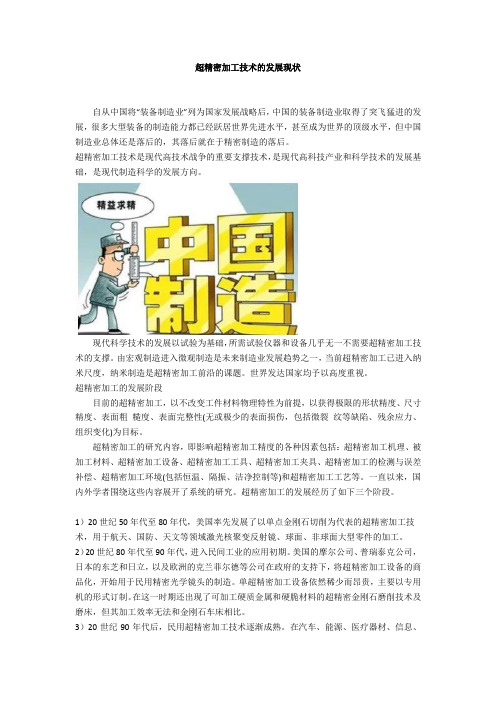
超精密加工技术的发展现状自从中国将“装备制造业”列为国家发展战略后,中国的装备制造业取得了突飞猛进的发展,很多大型装备的制造能力都已经跃居世界先进水平,甚至成为世界的顶级水平,但中国制造业总体还是落后的,其落后就在于精密制造的落后。
超精密加工技术是现代高技术战争的重要支撑技术,是现代高科技产业和科学技术的发展基础,是现代制造科学的发展方向。
现代科学技术的发展以试验为基础,所需试验仪器和设备几乎无一不需要超精密加工技术的支撑。
由宏观制造进入微观制造是未来制造业发展趋势之一,当前超精密加工已进入纳米尺度,纳米制造是超精密加工前沿的课题。
世界发达国家均予以高度重视。
超精密加工的发展阶段目前的超精密加工,以不改变工件材料物理特性为前提,以获得极限的形状精度、尺寸精度、表面粗糙度、表面完整性(无或极少的表面损伤,包括微裂纹等缺陷、残余应力、组织变化)为目标。
超精密加工的研究内容,即影响超精密加工精度的各种因素包括:超精密加工机理、被加工材料、超精密加工设备、超精密加工工具、超精密加工夹具、超精密加工的检测与误差补偿、超精密加工环境(包括恒温、隔振、洁净控制等)和超精密加工工艺等。
一直以来,国内外学者围绕这些内容展开了系统的研究。
超精密加工的发展经历了如下三个阶段。
1)20世纪50年代至80年代,美国率先发展了以单点金刚石切削为代表的超精密加工技术,用于航天、国防、天文等领域激光核聚变反射镜、球面、非球面大型零件的加工。
2)20世纪80年代至90年代,进入民间工业的应用初期。
美国的摩尔公司、普瑞泰克公司,日本的东芝和日立,以及欧洲的克兰菲尔德等公司在政府的支持下,将超精密加工设备的商品化,开始用于民用精密光学镜头的制造。
单超精密加工设备依然稀少而昂贵,主要以专用机的形式订制。
在这一时期还出现了可加工硬质金属和硬脆材料的超精密金刚石磨削技术及磨床,但其加工效率无法和金刚石车床相比。
3)20世纪90年代后,民用超精密加工技术逐渐成熟。
精密复杂曲面零件多轴数控加工技术研究进展
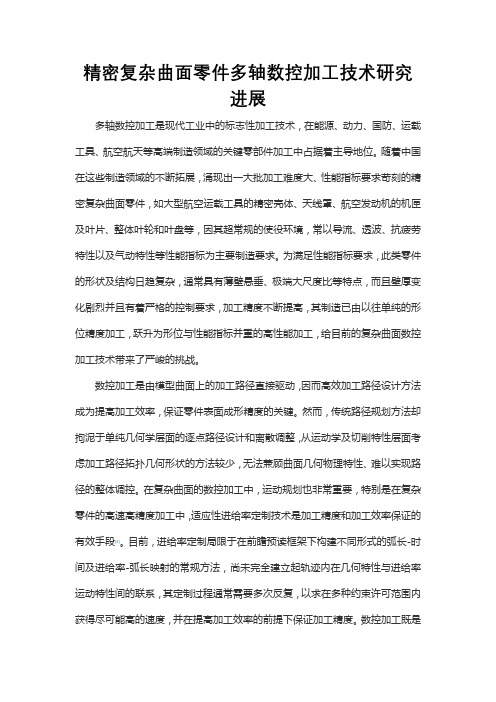
精密复杂曲面零件多轴数控加工技术研究进展多轴数控加工是现代工业中的标志性加工技术,在能源、动力、国防、运载工具、航空航天等高端制造领域的关键零部件加工中占据着主导地位。
随着中国在这些制造领域的不断拓展,涌现出一大批加工难度大、性能指标要求苛刻的精密复杂曲面零件,如大型航空运载工具的精密壳体、天线罩、航空发动机的机匣及叶片、整体叶轮和叶盘等,因其超常规的使役环境,常以导流、透波、抗疲劳特性以及气动特性等性能指标为主要制造要求。
为满足性能指标要求,此类零件的形状及结构日趋复杂,通常具有薄壁悬垂、极端大尺度比等特点,而且壁厚变化剧烈并且有着严格的控制要求,加工精度不断提高,其制造已由以往单纯的形位精度加工,跃升为形位与性能指标并重的高性能加工,给目前的复杂曲面数控加工技术带来了严峻的挑战。
数控加工是由模型曲面上的加工路径直接驱动,因而高效加工路径设计方法成为提高加工效率,保证零件表面成形精度的关键。
然而,传统路径规划方法却拘泥于单纯几何学层面的逐点路径设计和离散调整,从运动学及切削特性层面考虑加工路径拓扑几何形状的方法较少,无法兼顾曲面几何物理特性、难以实现路径的整体调控。
在复杂曲面的数控加工中,运动规划也非常重要,特别是在复杂零件的高速高精度加工中,适应性进给率定制技术是加工精度和加工效率保证的有效手段[4]。
目前,进给率定制局限于在前瞻预读框架下构建不同形式的弧长-时间及进给率-弧长映射的常规方法,尚未完全建立起轨迹内在几何特性与进给率运动特性间的联系,其定制过程通常需要多次反复,以求在多种约束许可范围内获得尽可能高的速度,并在提高加工效率的前提下保证加工精度。
数控加工既是一个零件的几何成形过程,也是一个复杂的动态物理切削过程,特别是随着高档数控机床切削速度不断提高,对数控加工技术的研究不能仅关注常规几何学层面的走刀路径设计和运动学层面的运动规划,必须转向实际的物理加工过程,解决大进给量、高转速所带来的刀具负载波动、变形、破损失效,特别是解决加工过程中由于切削力变化所引起的切削系统的不稳定等问题。
五轴激光曲面加工工艺
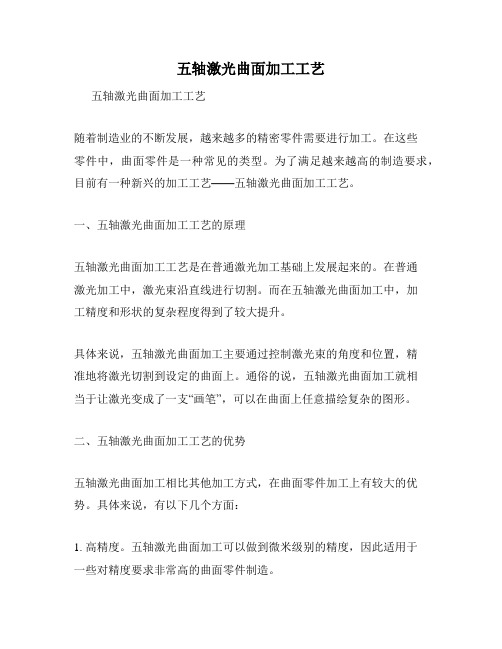
五轴激光曲面加工工艺五轴激光曲面加工工艺随着制造业的不断发展,越来越多的精密零件需要进行加工。
在这些零件中,曲面零件是一种常见的类型。
为了满足越来越高的制造要求,目前有一种新兴的加工工艺——五轴激光曲面加工工艺。
一、五轴激光曲面加工工艺的原理五轴激光曲面加工工艺是在普通激光加工基础上发展起来的。
在普通激光加工中,激光束沿直线进行切割。
而在五轴激光曲面加工中,加工精度和形状的复杂程度得到了较大提升。
具体来说,五轴激光曲面加工主要通过控制激光束的角度和位置,精准地将激光切割到设定的曲面上。
通俗的说,五轴激光曲面加工就相当于让激光变成了一支“画笔”,可以在曲面上任意描绘复杂的图形。
二、五轴激光曲面加工工艺的优势五轴激光曲面加工相比其他加工方式,在曲面零件加工上有较大的优势。
具体来说,有以下几个方面:1. 高精度。
五轴激光曲面加工可以做到微米级别的精度,因此适用于一些对精度要求非常高的曲面零件制造。
2. 微小变形。
由于五轴激光曲面加工是通过激光束切割而非机械切割,会产生较少的内部应力,因此不容易产生形变。
3. 制造灵活性。
五轴激光曲面加工不受复杂曲面的限制,并且可以在各种曲面上进行加工,从而提高了制造的灵活性。
三、五轴激光曲面加工的应用领域五轴激光曲面加工工艺在一些特定领域中得到了广泛的应用。
下面列举了几个具体的应用领域:1. 航空航天制造。
航空航天制造需要零件的精度高、形状复杂,而五轴激光曲面加工可以满足这些要求。
2. 电子制造。
五轴激光曲面加工可以用于制造电子组件外壳,特别是那些需要紧凑、细密的结构。
3. 医疗器械制造。
五轴激光曲面加工可以用于制造医疗器械中的一些精细零件,比如人工关节、牙齿修复器等。
四、五轴激光曲面加工的未来发展随着制造技术的不断提升,五轴激光曲面加工工艺还有很大的发展空间。
具体来说,可以从以下几个方面进一步发展:1. 加工精度再提升。
可以通过提升设备和材料、加强控制等方面进一步提升五轴激光曲面加工的加工精度。
复杂曲面零件数控加工的关键问题——解读《复杂曲面零件五轴数控加工理论与技术》

1五轴数控加工简介复杂曲面零件作为数字化制造的主要研究对象之一,在航空、航天、能源和国防等领域中有着广泛的应用,其制造水平代表着一个国家制造业的核心竞争力。
复杂曲面零件往往具有形状和结构复杂、质量要求高等难点,是五轴数控加工的典型研究对象。
当前,复杂曲面零件主要包括轮盘类零件、航空结构件以及火箭贮箱壁板等,如图1所示。
轮盘类零件是发动机完成对气体的压缩和膨胀的关键部件,主要包括整体叶盘类零件和叶片类零件。
整体叶盘类零件的叶展长、叶片薄且扭曲度大,叶片间的通道深且窄,开敞性差,零件材料多为钛合金、高温合金等难加工材料,因此零件加工制造困难。
叶片是一种特殊的零件,数量多、形状复杂、要求高、加工难度大且故障多发,一图1复杂曲面零件直以来都是各发动机厂生产的关键。
航空整体结构件由整块大型毛坯直接加工而成,在刚度、抗疲劳强度以及各种失稳临界值等方面均比铆接结构胜出一筹,但由于其具有尺寸大、材料去除率大、结构复杂、刚性差等缺点,因此加工后会产生弯扭组合等加工变形。
随着新一代大型运载火箭设计要求的提高,为保证火箭的可靠性,并减轻结构质量,提高有效载荷,对火箭贮箱壁板网格壁厚精度和根部圆弧过渡尺寸都提出了更严格的要求。
五轴数控铣削加工具有高可达性、高效率和高精度等优势,是加工大型与异型复杂零件的重要手段。
五轴数控机床在3个平动轴的基础上增加了2个转动轴,不但可以使刀具相对于工件的位置任意可控,而且刀具轴线相对于工件的方向也在一定的范围内任意可控。
五轴数控加工的主要优势包括:①提高刀具可达性。
通过改变刀具方向可以提高刀具可达性,实现叶轮、叶片和螺旋桨等复杂曲面零件的数控加工。
②缩短刀具悬伸长度。
通过选择合理刀具方向可以在避开干涉的同时使用更短的刀具,提高铣削系统的刚度,改善数控加工中的动态特性,提高加工效率和加工质量。
③可用高效加工刀具。
通过调整刀轴方向能够更好地匹配刀具与工件曲面,增加有效切宽,实现零件的高效加工。
研磨加工中的复杂曲面加工技术

研磨加工中的复杂曲面加工技术工业生产中,加工工艺一直是一个重要的话题。
随着科技的发展和应用不断深入,加工工艺也在不断的进步和发展。
其中,研磨加工技术是一项非常重要的技术,它可以对工件表面进行微米级的加工,使得工件的精度和表面质量能够得到保证。
而针对一些复杂的曲面加工,研磨加工技术也有着非常重要的应用。
一、研磨加工概述研磨加工是一种高效的精密加工方式,通常被用来制造金属、陶瓷、塑料和玻璃等硬质材料的表面。
在研磨加工过程中,磨粒切入工件表面,去除表面材料,从而实现对工件的加工。
研磨加工操作简便,可以实现对工件表面的加工,保证加工后的工件光洁度和表面平整度符合要求。
二、复杂曲面加工对于一些外形复杂、曲面复杂的工件加工,传统的研磨加工技术已经远远不能满足要求。
此时,研磨加工技术需要与计算机辅助设计和制造技术相结合,才能完成这种复杂曲面的加工。
目前,这种复杂曲面加工都采用了三轴和五轴CNC数控研磨技术。
这种技术通过计算机CAD三维软件进行三维建模,并将模型输入到CNC数控机床中,自动化、智能化地完成复杂曲面零件的加工。
五轴CNC数控研磨技术,相对于三轴CNC数控研磨技术,能够更加精细地进行切削,对工件表面的形状和精度的控制也更加准确。
三、研磨加工中的技术难点研磨加工中有许多技术难点。
当进行复杂曲面加工时,研磨加工技术的难度更大。
首先,研磨轮的选型非常重要。
研磨轮的硬度和耐磨性必须符合工件材料的性质,同时研磨轮的尺寸也需符合工件加工的要求。
其次,为了提高研磨加工的效率和精度,必须控制研磨加工过程中的参数。
例如,应该控制研磨轮的进给速度、研磨轮和工件的接触强度、研磨轮的压力等。
最后,研磨加工时所产生的摩擦热量,也是一个需要解决的问题。
摩擦热量过大会引起工件表面的变形、热裂纹和残留应力,甚至导致工件的损坏。
因此,研磨加工时必须采取适当的降温措施,同时也需要选择适当的研磨液和研磨液的淋喷方式。
四、结语研磨加工技术是一项重要的高精度加工技术,对于一些表面加工的需求,都有着重要的应用。
超精密加工的发展和展望

超精密加工的发展和展望精密和超精密制造工程是适应前沿高技术发展需求而发展起来的。
它是一个国家重要经济和技术实力的体现,是其它高新技术实施的基础。
超精密制造技术是当前各个工业国家发展的核心技术之一,各技术先进国家在高技术领域(如国防工业、集成电路、信息技术产业等)之所以一直领先,与这些国家高度重视和发展超精密制造技术有极其重要的关系。
超精密制造技术是随着测量技术的发展而发展的。
Renishaw、Heidenhain及SONY等公司发展了分辨率均可以达到1nm的测量元件;美国HP公司、英国Taylor、美国zygo等公司的测量仪器均可以满足纳米测量的需求。
超精密制造技术在国际上已经得到广泛应用。
与国防工业有关的如人造卫星用的姿态轴承和遥测部件、被送入太空的哈勃望远镜(HST)、飞机发动机转子叶片等;与集成电路(IC)有关的硅片加工(要求硅片的加工表面粗糙度Ra一般小于2nm,精度要求达0.1nm);此外光刻设备和硅片加工设备的精度要求到亚微米和纳米级。
仪表的精度、激光陀螺仪的平面反射镜的精度、红外制导的反射镜等,其表面粗糙度均要求达到纳米级。
另外,光学非球曲面零件面形制造精度要求已达λ/(30—50),表面粗糙度要求≤0.5nm。
1、超精密制造技术的发展状况1962年美国Union Carbide公司研制出首台超精密车床。
在美国能源部支持下,LLI实验室和Y—12工厂合作,与1983年成功地研制出大型超精密金刚石车床(DTM—3型)。
该机床可加工直径¢2100mm,多路激光干涉测量系统分辨率为2.5nm。
1984年,LLL实验室成功地研制出LODTM大型金刚石车床。
该机床可加工的最大直径为¢1625mm x500mm,重量1360kg。
采用的双频激光测量系统分辨率为0.7nm,其主轴静态精度为:径向跳动≤25nm,轴向窜动≤51nm。
LLL实验室这两台机床是目前公认的国际上水平最高的超精密机床。
CUPE(Cranfield Unit for Precision Engineering)研制的Nanocenter超精密车床已批量生产,其主轴精度≤50nm,加工工件的面形精度≤0.1μm。
精密和超精密加工技术现状和发展趋势

精密和超精密加工技术现状和发展趋势1.引言国际上在超精密加工技术方面处于领先地位的国家有美国、德国和日本发达国家中,美国、日本、德国等在高技术领域(如国防工业、集成电路、信息技术产业等)之所以一直领先,与这些国家高度重视和发展精密、超精密制造技术有极其重要的关系。
由于加工技术水平的发展,精密和超精密加工划分的界限逐渐向前推移,但在具体数值上没有确切的定义。
被加工零件的尺寸精度在 1.0~0.1μm,表面粗糙度Ra在0.1~0.03μm之间的加工方法称为精密加工。
超精密加工当前是指被加工零件的尺寸精度高于0.1μm,表面粗糙度Ra小于0.025μm,以及所用机床定位精度的分辨率和重复性高于0.01μm的加工技术,亦称之为亚微米级加工技术,且正在向纳米级加工技术发展超精密加工技术主要包括:超精密加工的机理,超精密加工的设备制造技术,超精密加工工具及刃磨技术,超精密测量技术和误差补偿技术,超精密加工工作环境条件。
2.发展现状美国是开展研究最早的国家,也是迄今处于世界领先地位的国家。
早在50年代末,由于航天等尖端技术发展的需要,美国首先发展了金刚石刀具的超精密切削技术,并发展了相应的空气轴承主轴的超精密机床,用于加工激光核聚变反射镜、战术导弹及载人飞船用球面、非球面大型零件。
20世纪80年代后期,美国通过能源部“激光核聚变项目”和陆、海、空三军“先进制造技术开发计划”,对超精密金刚石切削机床的开发研究,投入了巨额资金和大量人力,实现了大型零件的微英寸超精密加工。
如美国劳伦斯利弗莫尔国家实验室已经研制出一台大型光学金刚石车床(Large Op tics Diam ond Turn ing Machine, LODTM ), 是一台最大加工直径为1.63m的立式车床,定位精度可达28nm,借助在线误差补偿能力,它已实现了距离超过1m而直线度误差只有±25nm 的加工。
在美国能源部支持下,LLI实验室和Y-12工厂合作,与1983年成功地研制出大型超精密金刚石车床(DTM—3型)。
- 1、下载文档前请自行甄别文档内容的完整性,平台不提供额外的编辑、内容补充、找答案等附加服务。
- 2、"仅部分预览"的文档,不可在线预览部分如存在完整性等问题,可反馈申请退款(可完整预览的文档不适用该条件!)。
- 3、如文档侵犯您的权益,请联系客服反馈,我们会尽快为您处理(人工客服工作时间:9:00-18:30)。
复杂曲面精密加工的发展现状和趋势摘要:随着高新技术的发展,人们对外观美学效果的需要,复杂曲面的应用也越来越广泛。
但是复杂曲面的应用在应用方面仍然需要取决于力学特性和功能的需要和满足人们对产品外形的需求。
复杂曲面的发展和实现,又取决于复杂曲面的设计技术和制造技术。
所以我们从3个方面分别阐述它们的研究现状与发展趋势:复杂曲面设计技术,复杂曲面加工技术,复杂曲面加工设备。
指出复杂曲面设计技术、加工技术及加工设备发展存在的主要问题,对其发展趋势进行科学预测。
关键词:复杂曲面精密加工装备现状趋势一前言随着全球经济的发展,市场竞争日趋激烈,具有复杂曲面的产品越来越多,广泛应用于模具、工具、能源、交通、航空航天、航海等领域。
复杂曲面的复杂性主要体现在:许多边缘学科、高科技产品领域对产品涉及的曲面造型有很高的精度要求,以达到某些数学特征的高精度为目的;现代社会中,人们在注重产品功能的同时,对产品的外观造型提出了越来越高的要求,以追求美学效果或功能要求为目的。
因此,进一步提高复杂曲面的设计和加工水平成了国内外竞相研究的焦点。
二主题1 复杂曲面设计与加工技术的发展1.1 复杂曲面造型技术的发展及现状复杂曲面造型技术是计算机辅助设计和计算机图形学中最为活跃、同时也是最为关键的学科分支之一,它随着CAD/CAM技术的发展而不断完善,渐趋成熟。
它主要研究在计算机图像系统的环境下对曲面的表示、设计、显示和分析,肇源于飞机、船舶的外形放样工艺。
从研究领域来看,曲面造型技术已从传统的曲面表示、曲面求交和曲面拼接,扩充到曲面变形、曲面重建、曲面简化、曲面转换和曲面等距性。
此外,随着工业生产的发展和需要,其他学科的技术方法被引进到计算机图形学中来,形成一种融合的趋势,出现了许多新造型方法的研究:如基于物理模型优化的曲面造型方法、基于力密度方法的曲线曲面的造型方法等。
1.2复杂曲面反求技术的发展和现状反求技术,也称逆向技术、反向技术,是指用一定的测量手段对实物或模型进行测量,根据测量数据通过三维几何建模方法重构实物的CAD模型的过程,是一个从样品生成产品数字化信息模型,并在此基础上进行产品设计开发及生产的全过程。
随着计算机、数控和激光测量技术的飞速发展,反求技术不再是对己有产品进行简单的“复制”,其内涵与外延都发生了深刻变化,成为家电、汽车、玩具、轻工、建筑、医疗、航空、航天、兵器等行业最重要的产品设计方法之一,是工程技术人员通过实物样件、图样等快速获取工程设计概念和设计模型的重要手段。
复杂曲面反求技术是20 世纪80 年代初分别由美国明尼苏达采矿制造公司、日本名古屋工业研究所以及美国思博明仪器设备有限公司提出并研制开发成功的。
目前,已有一些高等学校和企业正致力于这方面的研究。
如浙江大学、西北工业大学、南京航空航天大学、西安交通大学、清华大学、上海交通大学、华中科技大学等先后开展了复杂曲面反求工程CAD问题的研究。
1.3光学自由曲面加工技术的发展加工高精度复杂曲面光学零件代表了超精密加工技术的最高水平。
由于对光学自由曲面零件的形状精度要求达到微米、亚微米级,表面粗糙度达到纳米、亚纳米级,必然使得光学自由曲面加工的复杂程度远比传统球面和非球面要高得多。
但是,由于光学自由曲面零件在工业上应用广泛,使得其成为复杂曲面加工技术的重要研究领域。
由于曲面光学零件属于难加工的硬脆材料,且自由曲面有较大的曲率变化和多变的曲率中心,该领域除了采用超精密磨削、研磨及抛光技术外,还多采用计算机控制光学表面成形等技术实现光学自由曲面的加工。
国内外学者对各种硬脆材料的磨削机理、加工工艺、加工设备、磨削力、磨削热、砂轮磨损等问题进行了广泛而深入的研究,相继研发出了高速磨削、缓进给磨削、镜面磨削、恒压力磨削和延性域磨削等高效磨削工艺,对光学自由曲面加工需要多轴联动的超精密数控机床,例如,美国摩尔公司的超精密五轴数控车床Nanotech500FG,Precitech 公司的Freeform700A 超精密五轴机床等采用单点金刚石车削或铣削等加工技术实现自由曲面的加工。
2 复杂曲面加工设备的发展和现状近年来,复杂曲面零件的加工技术由于多轴联动数控加工中心的应用得到了突破。
国外多轴数控切削技术发展很快,CNC 机床已经从三轴发展到十轴。
日本研制的五面加工机床采用复合主轴头,可实现4 个垂直平面、任意角度的倾斜面和倒锥孔的加工。
德国德马吉公司生产的DMUVoution 系列加工中心可由CNC 系统控制、CAD/CAM 直接或间接控制,在一次装夹下完成五面加工。
另外,随着数字化光电技术的高速发展,精密多轴曲面磨床的技术性能得到改善。
瑞士的罗诺曼迪克有限公司研究开发的高精度NC600Xplus 六轴工具磨削中心配装了光学装夹,每个磨削砂轮的位置在机床上都可以在线测量。
近年来,我国在多轴数控机床的研制方面也取得了很大的发展。
沈阳机床厂研制生产的GMB25505x龙门式五轴镗铣加工中心应用于大型叶轮等复杂曲面高速、精密加工。
济南二机床集团有限公司研制生产的XKV2740 型五轴联动定梁龙门(双龙门)移动数控镗铣床,可以完成对多种叶片、螺旋桨、金属模具等大型复杂曲面的精密加工。
北京机电院与东方汽轮机厂联合开发了五轴联动大型叶片加工中心,可一次装夹完成60 MW 汽轮机首末级叶片的加工。
齐齐哈尔二机床厂、清华大学和哈尔滨电机厂有限责任公司联合研制了新型龙门式五轴联动混合机床,实现了三维立体曲面的高速切削,成功加工出三峡工程左岸水轮发电机组特大型水泵叶片。
3 国内存在的问题进入 21 世纪以来,复杂曲面加工技术领域作为机械制造的重要组成部分,在我国虽然已经取得了长足的进展,但是与国际先进水平仍然存在很大差距,主要表现在以下几个方面。
(1) 高档多轴数控机床主要依赖于进口。
复杂零件曲面结构的多样化、复杂化及高精度化需要依靠多轴数控切削加工来实现。
我国对多轴数控机床的研究与开发起步较晚,虽然已经开发了一些多轴数控机床,但在质量、功能和性能等方面还有待提高,其中一些关键零部件、特别是支承系统、驱动系统和控制系统、在线检测系统主要还是依赖进口。
(2) 复杂型面数控加工软件有待进一步开发。
近年来虽然在复杂型面建模和切削加工方面的研究取得了一定的成果,但在复杂型面数控切削软件的开发方面仍需要努力。
有的机床公司虽然开发了多轴数控机床,但在开发数控加工软件方面显得力量不够,数控加工软件问题没有彻底解决,使得整机的应用受到严重影响,针对工具机床的研究较多,但很少从多轴联动复杂型面加工路径生成的角度去研究问题。
(3)复杂型面检测技术及仪器设备的研究有待加强。
复杂型面的加工虽然是按照零件设计中所描述的结构特征及结构尺寸进行的,但由于加工过程中复杂型面的特征表面的形成过程非常复杂,且往往会出现干涉现象。
由于复杂形状的零件具有形状复杂的功能表面,在检测与这些功能表面有关的零件结构参数时,传统的检测方法难以实现,只能采取间接测量的方式,但必须得到零件在法剖面及端截面内的截形,按照这样的方法实际操作起来十分困难,一些高档的检测设备仍然依赖进口。
因此,需要探讨更有效的检测方法,研制高档的检测仪器设备。
三总结(1) 复杂曲面广泛应用于航空、航天、航海、模具、工具、能源、交通等领域,它作为机械制造的重要组成部分,在我国虽然已经取得了长足的进展,但是与国际先进水平仍然存在很大差距,其发展对提高我国机械设计与制造水平具有重要的理论意义和应用价值。
(2) 近年来,随着计算机技术、自动控制技术的发展,特别是多轴数控加工技术在复杂曲面加工中的广泛应用,从曲面造型、反求技术等的复杂曲面设计到光学自由曲面、复杂刀具等的曲面加工技术,复杂曲面设计和加工技术有了突破性的发展。
(3) 对复杂曲面质量的要求带动了复杂曲面加工设备的进一步发展,复杂曲面多轴联动加工技术也日趋成熟。
我国对多轴数控机床的研究与开发起步较晚,虽然已经开发了一些多轴数控机床,但是,还应该加强对机床关键零部件等功能部件、配备智能化技术和高性能数控系统的多轴数控机床的研究和开发。
四参考文献[1] 孙大涌. 先进制造技术[M]. 北京:机械工业出版社,1999.SUN Dayong. Advanced manufacturing technology[M].Beijing:China Machine Press,1999.[2] 刘雄伟. 数控加工理论与编程技术[M]. 北京:机械工业出版社,1994.LIU Xiongwei. CNC machining theory and programmingtechnology[M]. Beijing:China Machine Press,1994.[3] 周建忠,张永康. 激光加工技术在汽车车身制造中的应用[J]. 电加工与模具,2000(4):32 -36.ZHOU Jianzhong,ZHANG Yongkang. Laser processingtechnology applicated in automobile body manufacturing[J]. Electromachining & Mould,2000(4):32-36.[4] 焦向东,贾永田. 基于快速原型技术的金属模具制造发展现况[J]. 制造技术与机床,2000(7):8-9.JIAO Xiangdong,JIA Yongtian. Development of metaldie manufacturing based on rapid prototypingtechnology[J] Manufacturing Technology & MachineTool,2000(7):8-9.[5] 赵玉刚,周锦进. 新型的复杂曲面磁粒光整加工机床[J].机械工程学报,2000,36(3):100-103.ZHAO Yugang , ZHOU Jinjin. Magnetic abrasivefinishing machine tool on the new complex surface[J].Chinese Journal of Mechanical Engineering,2000,36(3):100-103.[6] LEE S,WALBERG G,SHIN S Y.Scattered datainterpolation with multilevel B-splines[J].IEEE Trans. onVisualization and Computer Graphics, 1997,3(3):228-244.[7] THOMAS F,TUMBULL C,ROS L,et al. Computingsigned distance between free-form objects[C]//Proceeding of the 2000 IEEE International Conference on Roboticsand Automation,April 24-28,2000,San Francisco,CA,USA. Piscataway,NJ. USA:IEEE,2000:3 713-3 718.[8] PAGE F,GUIBAULT F. Collision detection algorithmfor NURBS surfaces in interactive applications[C]//Canadian Conference on Electrical and Computer Engineering,May 4-7, 2003,Montreal,Que.,Canada.Piscataway,NJ. USA:IEEE,2003:1 417-1 420.[9] 刘浩. NURBS 曲面间的最短距离[D]. 南京:南京航空航天大学,2002.LIU Hao. The shortest distance between NURBS surfaces[D]. Nanjing:Nanjing University of Aeronautics andAstronautics,2002.[10] 潘俊. PH 曲线及有理PH 曲线插值及其应用[D]. 上海:复旦大学,2006.PAN Jun. PH curves and rational PH curves interpolation and its application[D]. Shanghai:Fudan University,2006.[11] 吴宗敏. 径向基函数、散乱数据拟合与无网格偏微分方程数值解[J]. 工程数学学报,2002(5):1-11.WU Zongmin. Radial basis functions, scattered data fitting with the non-grid numerical solution of partial differential equations[J]. Journal of Engineering Mathematics,2002(5):1-11.[12] 陈发来. 双二次Bézier 曲面的正性与凸性[J]. 高校应用数学学报,1996(12):467-476.CHEN Falai. Positive nature and protruding nature of two repeated Bézier curved surface[J]. Applied Mathematics Journal of Chinese Universities,1996(12):467-476.[13] 范树迁. 反求工程中自由形状模型的美化技术[D]. 杭州:浙江大学,2006.FAN Shuqian. Landscaping techniques of free-formmodel in reverse engineering[D]. Hangzhou:Zhejiang University. 2006.[14] 朱永强,鲁聪达. 自由曲线曲面造型技术的综述[J]. 中国制造业信息化,2003,32(5):110-113.ZHU Yongqiang,LU Congda. Overview on free curve and curved surface model technology[J]. Manufacture Information Engineering of China,2003,32(5):110-113.[15] 柳晓燕,冯峰. 基于能量优化的NURBS 曲面几何特征修改[J]. 计算机工程与应用,2008,44(26):41-44.LIU Xiaoyan,FENG Feng. Geometric features modification of NURBS surfaces via energy optimization[J].Computer Engineering and Applications,2008,44(26):41-44.。