课设说明书
课程设计说明书【范本模板】
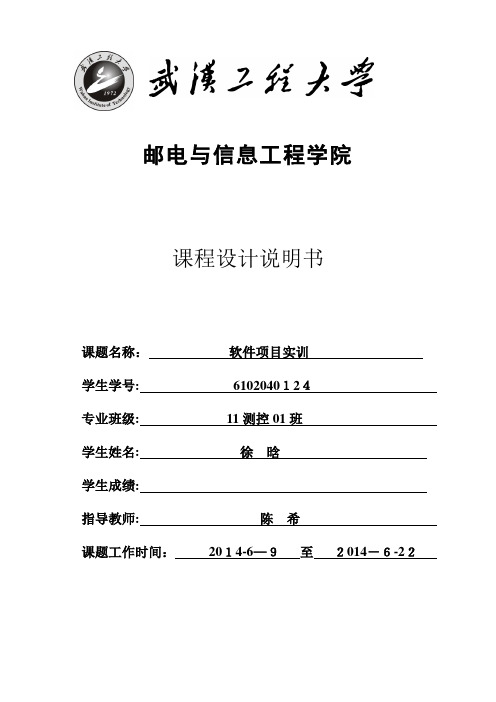
邮电与信息工程学院课程设计说明书课题名称:软件项目实训学生学号:6102040124专业班级:11测控01班学生姓名: 徐晗学生成绩:指导教师:陈希课题工作时间:2014-6—9至2014-6-22一、课程设计任务的基本要求:(1)课程设计目的:1.全面理解程序的顺序结构、选择结构、循环结构,掌握结构化程序设计的自顶向下,逐步细化,模块化的设计原则。
2.掌握C语言基础知识,灵活应用函数、指针、数组、结构体等知识进行程序设计。
3.掌握利用C语言进行程序设计的方法和技巧,提高学生综合分析和调试程序的能力.(2)课程设计总体要求:1。
采用模块化程序设计方法。
2.主菜单设计界面如下:3.子菜单界面如下:选择结构子菜单:循环结构子菜单:4。
在对应模块下完成如下功能: (1)单选择if语句:(2)双选择if语句:(3)多选择if语句:(4)switch语句(5)while循环语句(6)do—while循环语句(7)for循环语句(8)循环嵌套例如:switch语句案例界面:(3)论文部分1、学生应提交的资料:纸质《课程设计说明书》1份;课程设计报告1份。
2、课程设计报告的内容附在《课程设计说明书》后,内容包括:一、设计目的1。
全面理解程序的顺序结构、选择结构、循环结构,掌握结构化程序设计的自顶而下,逐步细化,模块化的原则。
2。
掌握C语言的基础知识,灵活应用函数、指针、数组、结构体等知识进行程序设计。
3。
掌握利用C语言进行程序设计的方法和技巧,提高学生综合分析和调试程序的能力.二、系统功能模块图(略)三、设计函数列表在C语言中每一个功能模块都对应一个函数,即由函数来实现各功能模块的具体功能,也就是建立功能模块与函数之间一一对应的关系,在编写程序时可以减少不课程设计报告一、设计目的1. 全面理解程序的顺序结构、选择结构、循环结构,掌握结构化程序设计的自顶而下,逐步细化,模块化的原则。
2. 掌握C语言的基础知识,灵活应用函数、指针、数组、结构体等知识进行程序设计.3.掌握利用C语言进行程序设计的方法和技巧,提高学生综合分析和调试程序的能力。
课程设计说明书模板

课程设计说明书模板课程设计说明书1. 课程名称:[填写课程名称]2. 课程设计目的:[填写课程设计的主要目的和需求]3. 课程设计目标:[填写课程设计的具体目标]4. 课程大纲:[填写课程的大纲,包括每个单元的主题、教学目标、教学内容、教学方法、评价方式等]5. 教学资源:[列举所需的教学资源,如教科书、参考书、多媒体设备等]6. 教学活动:[列举每个单元的教学活动,包括课堂讲解、实验、讨论、小组活动等]7. 评估方式:[说明课程的评估方式,包括考试、作业、项目等]8. 教学团队:[介绍教学团队的成员,包括主讲教师、助教等]9. 课程进度安排:[设置每个单元的教学时间,包括预计的课程开始和结束日期]10. 教学参考文献:[列举可供参考的教学资料和文献]11. 补充说明:[如有任何额外的补充说明,请在此处填写]以上是一个简单的课程设计说明书模板,具体的内容根据课程的实际需求进行填写和修改。
12. 课程设计背景:[解释为什么设计此课程,背景资料和理由等]13. 教学目标细化:[具体阐述每个单元的教学目标,并且可分为知识、技能和态度等层面]14. 教学方法和策略:[详细描述采用的教学方法和策略,如讲授、案例分析、小组合作等]15. 教学评估标准:[明确课程评估的标准和要点,例如针对知识理解的测验、技能表现的评估等]16. 教学资源准备:[具体说明所需的教学材料、设备、实验器具等,以及相关的采购和准备工作]17. 学习支持与辅助:[列举可提供给学生的学习支持和辅助资源,如电子教学平台、辅导手册等]18. 教学组织和管理:[描述课堂组织和管理的方式,包括上课时间、课堂纪律、小组分工等]19. 教学团队角色职责:[详细说明教学团队中各成员的角色职责,包括主讲教师、助教、辅导员等]20. 课程进度和时间安排:[具体列出每个单元的教学时间安排,包括每周课时数、教学时间分配等]这些补充内容可以根据课程的具体要求和设计者的个人情况进行修改和适应,以更好地满足教学需求和目标。
课程设计说明书范文格式
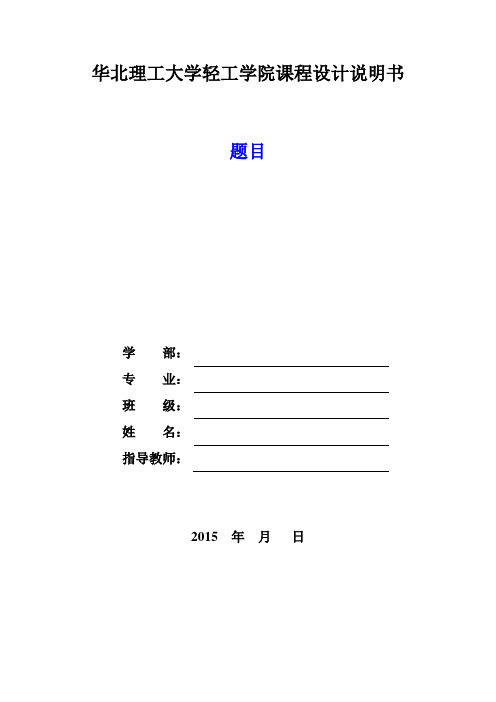
华北理工大学轻工学院课程设计说明书题目学部:专业:班级:姓名:指导教师:2015 年月日第1章绪论 (1)1.1在线考试的现状 (1)1.1.1 在线考试在国外的发展状况 (1)1.1.2 在线考试在国内的发展状况 (1)1.1.3 当前在线考试系统的特征 (1)1.2组卷算法的现状 (2)1.3.本课题的来源 (2)1.4本文主要内容 (2)第2章组卷算法与题库的研究 (3)2.1组卷算法理论 (3)2.1.1随机选取法和回溯试探法 (3)2.1.2 遗传算法 (3)2.2在线考试系统的组卷算法 (3)2.2.1 组卷算法的确定 (3)2.2.2组卷参数定义 (4)2.2.3 基于遗传算法的组卷算法设计 (4)2.3题库基础理论 (5)2.3.1 题库发展 (5)2.3.2 题库的概念 (5)2.3.3 题库的特征 (5)2.3.4 题库的建设理论 (5)2.3.5题库建设步骤 (5)2.4在线考试系统的题库建设方案 (5)2.4.1 在线考试系统的题库建设步骤 (6)2.4.2 题库管理系统框架 (6)2.4.3 题库管理设计方案 (6)第3章在线考试系统的需求分析和设计 (7)3.1系统需求分析 (7)3.1.1 系统功能分析 (7)3.1.2系统的数据流图 (7)3.2系统概要设计 (7)3.2.1 系统功能模块的划分 (7)3.2.2 在线考试系统的主流程图 (7)3.2.3数据库设计 (7)3.3系统详细设计 (8)结论 (9)参考文献 (10)第1章绪论1.1 在线考试的现状1.1.1 在线考试在国外的发展状况大约1997年初,国外开始出现支持网上教学的系统和平台,近年来层出不穷。
国外大多数系统侧重于网上的课程开发、课程管理、学生历史记录等方面,对教学过程提供全面有效但是比较基础的支持,也有一些系统重视教学活动的设计,如提供对不同教学模式的教学实施方便性的支持。
美国的NTU英国的pen College都是十分典型的网络教育示例。
课程设计说明书的格式是怎样的?

课程设计说明书的格式是怎样的?课程设计说明书撰写格式为了保证课程设计质量,特制定本规范。
设计说明书要求按统一格式打印,其版面要求:A4纸,页边距:上2cm,下2cm,左2.5cm、右2cm;字体:正文宋体、小四号;行距:固定值20;页码:底部居中。
一份完整的设计说明书应包括以下几个方面:一、封面(包括题目、院系、学生班级、设计组号、学生组员姓名、指导教师姓名等)(见附1)。
二、目录居中打印目录二字,(四号黑体,段后1行),字间空一字符;章、节、小节及其开始页码(字体均为小四号宋体)。
节向右缩进两个字符,小节及以后标题均向右缩进四个字符。
目录中应包含正文及其后面部分的条目。
目录的最后一项是无序号的“参考文献资料”。
三、正文(一)正文内容一般应包括:1、设计任务和要求:说明本课题应解决的主要问题及应达到的技术要求;简述本设计的指导思想。
2、设计依据和设计原则。
3、方案论证:阐明为什么要选择这个设计方案以及所采用方案的特点。
4、设计论述:对设计工作的详细表述(包括设计计算)。
要求层次分明、表达确切。
5、结论或总结:对整个设计工作进行归纳和综合。
(二)正文要求:(1)计算正确,论述清楚,文字简练通顺,插图简明,书写整洁。
文中图、表按制图要求绘制。
(2)段落及层次要求:每节标题以四号黑体左起打印(段前段后各0.5行),节下为小节,以小四号黑体左起打印(段前段后各0.5行)。
换行后以小四号宋体打印正文。
节、小节分别以1、1.1、1.1.1依次标出,空一字符后接各部分的标题。
当论文结构复杂,小节以下的标题,左起顶格书写,编号依次用(1)、(2)……或1)、2)……顺序表示。
字体为小四号宋体。
对条文内容采用分行并叙时,其编号用(a)、(b)……或a)、b)……顺序表示,如果编号及其后内容新起一个段落,则编号前空两个中文字符。
(3)图纸要求:图面整洁,布局合理,线条粗细均匀,圆弧连接光滑,尺寸标注规范,使用计算机绘图。
课程设计课程设计说明书

课程设计课程设计说明书一、教学目标本课程的教学目标是使学生掌握XX学科的基本概念、原理和方法,培养学生运用XX知识解决实际问题的能力。
具体来说,知识目标包括:1.掌握XX学科的基本概念、原理和方法;2.了解XX学科的发展趋势和应用领域。
技能目标包括:1.能够运用XX知识解决实际问题;2.具备XX学科的基本实验技能。
情感态度价值观目标包括:1.培养学生对XX学科的兴趣和热情;2.培养学生团队合作、创新思维和科学精神。
二、教学内容根据课程目标,本课程的教学内容主要包括XX学科的基本概念、原理和方法,以及实际应用案例。
具体安排如下:第一章:XX学科概述1.1 XX学科的定义和发展历程1.2 XX学科的应用领域和前景第二章:XX基本原理2.1 XX原理的提出和证明2.2 XX原理的应用案例第三章:XX方法与应用3.1 XX方法的原理和步骤3.2 XX方法在实际问题中的应用第四章:XX学科的发展趋势4.1 XX学科的最新研究成果4.2 XX学科的未来发展方向三、教学方法为了实现课程目标,本课程将采用多种教学方法,如讲授法、讨论法、案例分析法和实验法等。
具体安排如下:1.讲授法:通过教师的讲解,使学生掌握XX学科的基本概念、原理和方法;2.讨论法:引导学生针对实际问题进行思考和讨论,培养学生的创新思维和解决问题的能力;3.案例分析法:通过分析具体案例,使学生了解XX方法在实际问题中的应用;4.实验法:让学生亲自动手进行实验,培养学生的实验技能和科学精神。
四、教学资源为了支持教学内容和教学方法的实施,本课程将利用多种教学资源,包括教材、参考书、多媒体资料和实验设备等。
具体安排如下:1.教材:选用国内权威出版的XX学科教材,为学生提供系统、科学的学习资料;2.参考书:推荐学生阅读相关领域的经典著作和最新研究论文,拓展知识面;3.多媒体资料:利用课件、视频等多媒体资源,丰富教学手段,提高学生的学习兴趣;4.实验设备:配备必要的实验设备,为学生提供动手实践的机会,培养实验技能。
课程设计说明书格式及要求

西华大学电气信息学院课程设计说明书格式及要求一份完整的课程设计说明书应包括:封面、摘要、目录、正文(前言、总体方案设计、…、结论、总结与体会、谢辞等)、参考文献、附录等。
一、封面:单独1页(见样件)二、摘要、关键词:中文(150~200字)、英文;单独1页摘要应高度概括题目的内容、方法和观点,以及取得的成果和结论。
应反映出整个内容的精华。
中文摘要在200字以内为宜,同时要求写出外文摘要,以200个实词为宜。
并要求写出中文、外文的关键词。
①用精炼、概括的语言表达,每项内容不宜展开论证和说明;②要客观陈述,不宜加主观评价;③成果和结论性字句是摘要的重点,论述上要多些,以加深读者的印象;④要独立成文,选词用语要避免与全文尤其是前言和结论部份雷同;⑤既要简短扼要,又要表达清晰,结构合理。
摘要用中、英文对照编写;“摘要”两字加粗,字体用楷体四号字,第一行行头缩进四格,行尾缩进两格,选用小四号宋体字。
关键词一般为3~8个,在摘要后另起一行排,各关键词之间用“,”号分隔。
关键词的字体和排版与“摘要”的相同;关键词与摘要之间不空行。
(见样件)三、目录:内容必要对应页码号“目录”的字体采用三号宋体加粗;目录中的标题不宜超过三级。
一级标题用四号宋体加粗;二级及其以后的标题用四号字,不加粗。
四、设计说明书正文:正文的标题可分为章(一级)、节(二级)、小节(三级)等。
一级标题用小三号字,编号用1级阿拉伯数字(如:2总体方案设计),字体选用宋体加粗;二级标题用四号字,编号用2级阿拉伯数字(如:2.1),字体选用宋体加粗;三级标题及其以后的标题用小四号字,三级标题编号用3级阿拉伯数字(如:2.1.3),字体选用宋体加粗。
标题的排列按:①一~三级标题文字均居左顶排,标题与标题间不空行,标题与前段正文之间空一行;②各一级标题之间要换页;③在两级标题连排的情况下,标题间应间隔一行;④在有副标题的情况下,应注意主标题与副标题的关系与比例。
课程设计说明书

课程设计说明书1. 引言课程设计是现代教育教学改革的重要组成部分,它旨在培养学生的创新思维和实践能力。
本文档旨在为课程设计提供详细的说明和指导,帮助教师和学生有效地进行课程设计工作。
2. 设计目标课程设计的目标是提供一个学习框架,使学生能够充分理解和掌握所学课程的关键概念和技能。
具体目标包括:- 培养学生的分析和解决问题的能力;- 培养学生的团队合作和沟通能力;- 激发学生的创新和创造力;- 提高学生的实践能力;- 促进学生的自主学习和自我管理能力。
3. 课程设计步骤3.1 确定课程目标和学习内容在设计课程之前,首先需要明确课程的目标和学习内容。
课程目标应与学生的学习需求和教学要求相一致,并具有明确的可测量性。
学习内容应包括基本概念、原理和应用。
3.2 制定教学计划和学习活动根据课程目标和学习内容,制定详细的教学计划和学习活动。
教学计划应包括教学目标、教学方法、评价方法和学习资源等。
学习活动应设计成富有创意和挑战的,能够培养学生的实践和创新能力。
3.3 开展学习和实践活动在课程设计实施过程中,教师应引导学生积极参与学习和实践活动。
通过小组讨论、实验、实习等方式,培养学生的团队合作、沟通和解决问题的能力。
3.4 进行评估和反馈课程设计结束后,教师应及时进行评估和反馈。
评估可以包括学生的作业、项目成果、实习报告等。
根据评估结果,教师可以为学生提供个性化的指导和建议,帮助他们改进学习。
4. 教学方法为了有效实施课程设计,教师可以采用多种教学方法,包括: - 授课讲解:教师将重点理论知识讲解给学生,并进行互动讨论和思考;- 实践体验:学生通过实验、实习等实际操作来巩固所学知识;- 小组合作:学生分组合作完成项目任务,培养团队合作和沟通能力;- 个性化指导:教师根据学生的学习进展,提供个性化的学习指导和反馈。
5. 课程评价课程评价是课程设计的重要环节。
为了全面评价学生的学习情况,教师可以采用多种评价方法,包括:- 作业/project成果评价:根据学生交付的作业和项目成果,评估其理解和应用能力;- 考试评价:通过考试对学生的知识掌握程度进行评估;- 口头表现评价:通过学生的展示、演讲等口头表现,评估其沟通和表达能力。
课程设计说明书范文
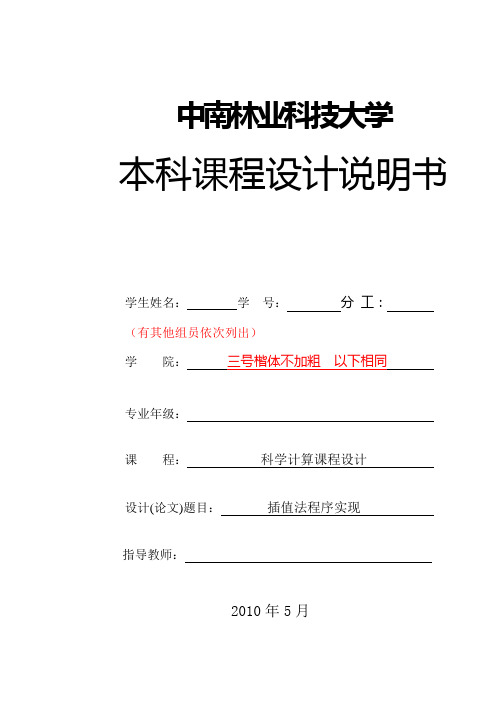
中南林业科技大学本科课程设计说明书学生姓名:学号:分工:(有其他组员依次列出)学院:三号楷体不加粗以下相同专业年级:课程:科学计算课程设计设计(论文)题目:插值法程序实现指导教师:2010年5月中文摘要(空1行)主要内容,研究的目的、方法、结果和结论等(小4号宋体,1.5倍行距)××××××××××××××××××××××××××××××××××××××。
(要求150~300字)(空2行)关键词×××,×××,×××,×××(小4号宋体,3~8个)英文摘要(和中文摘要对应)引言引言的内容可包括研究的目的、意义、主要方法、范围和背景等。
应开门见山,言简意赅。
正文部分1、XXX1.1X X X第 1.1的内容1.2X X X第 1.2的内容……2、XXX第2部分的内容结论/讨论结论是文章的主要结果、论点的提炼与概括,应准确、简明、完整、有条理。
参考文献:例如:1 胡曰利、吴晓芙,林木生长与养分动态模型研究V杉木林曲线[1]、中南林学院,1999,19(4):1-72 华罗庚,王元.论一致分布与近似分析.中国科学,1973(4):339~3573 Borko H,Bernier C L.Indexing concepts and methods .New York:Academic Pr,1978指导评阅人签名:。
教学课程设计说明书模板

教学课程设计说明书模板一、项目概述本教学课程设计说明书模板旨在为教师在设计课程时提供指导和参考。
通过本模板,教师可以详细说明课程的目标、内容、教学方法、评估方式等关键要素,为教学活动的顺利进行提供指导。
二、项目目标本项目的主要目标是设计一门符合教学要求的课程,以达到培养学生综合素质和提高学习能力的目标。
通过科学合理的教学课程设计,提高学生的学习兴趣和主动性,培养学生的创新思维和实践能力,使学生能够灵活地运用所学知识解决实际问题。
三、课程内容1. 课程介绍:简要介绍课程的背景和意义,引起学生的兴趣和学习动机。
2. 教学目标:明确课程的教学目标,包括知识、能力和素养的培养目标。
3. 课程大纲:详细列出课程的各个单元或模块,每个单元或模块包括的主题、目标、内容和学时等。
确保课程设计合理有序,能够覆盖所需的知识点和技能。
4. 教学方法:结合具体的课程内容和教学目标,选择适合的教学方法,如讲授、示范、讨论、实验、小组活动等,以促进学生的积极参与和主动探究。
5. 教学资源:列举所需的教具、实验器材、参考书籍等教学资源,确保教学过程顺利进行。
6. 评估方式:明确课程的评估方式,包括作业、考试、实验报告等。
要求评估方式与课程目标相匹配,能够全面、准确地评价学生的学习成果。
四、教学安排1. 课程周期:确定课程的教学周期,包括总学时和每周学时。
2. 教学进度:安排具体的教学进度表,每个单元或模块的学时安排和重点内容。
3. 课堂活动:设计每堂课的教学活动和教学方法,保证活动的多样性和趣味性,增加学生的参与度。
4. 作业布置:根据课程内容和学生能力水平,合理布置各类作业,以巩固和拓展学生的学习成果。
五、教学评价1. 评价标准:明确课程的评价标准,包括知识理解、能力应用、思维发展、实践操作等方面。
2. 评价方法:选择合适的评价方法,如考试、实验报告、项目展示等,以客观、公正、全面地评价学生的学习效果。
3. 评价周期:确定课程的评价周期,包括阶段性评价和总结性评价。
《课程设计说明书》word版

西北工业大学课程设计班级:05010903姓名:焦健指导教师:康永刚蒋建军完成日期:2012.9设计任务书一、设计内容1、模具的图样设计1)了解制品的工艺性2)了解制品的生产批量3)了解制品所选用的冲压设备2、确定模具设计方案2)确定模具设计的基本结构3)确定模具所选用的标准件类型4)确定模具中凸凹模的尺寸5)完成模具图样的设计三、进度安排1、第一周:熟悉任务,消化图纸,收集相关资料,做好前期准备2、第二周:对零件进行工艺性分析,拟定设计方案3、第三周:设计模具,绘制图纸4、第四周:编写说明书,做好答辩准备摘要模具设计是上学年课程《飞机钣金成形工艺与原理》的应用延伸。
设计过程从零件的工艺分析开始的,根据工艺要求来确定设计的大体思路。
其开始是确定该模具类型为落料-拉深复合模,计算毛坯尺寸,确定拉深次数,作工艺计算,计算出冲裁时的冲压力、卸料力、推件力,以及拉深时的拉深力和压边力,确定模具的压力中心,选择压力机和确定冲模的闭合高度,最后根据前面所计算出的内容确定模具的凸、凹模尺寸和形状。
设计出挡料销、卸料板、推件装置、弹簧、导柱、导套和模柄等模具的主要零部件,从而完成整个模具的设计工作。
其中模具主要零部件结构设计是这次设计的主要内容,其内容包含了凹模结构设计、凸模结构设计、凸凹模结构设计、定位零件、弹性卸料装置、钢性推件装置、弹簧的选用、导柱与导套、模柄与模架的选取等重要零部件的设计加工方法和加工注意要点。
这样更有利于加工人员的一线操作,使其通俗易懂加工方便。
本次设计不仅让我熟悉了课本所学的知识,而且让我做到所学的运用到实践当中,更让我了解了冲压模具设计的全过程和加工实践中应注意的要点。
在此次真正的感受到去设计一个模具的整个过程中,去体会知识与实际、理论与实际的结合,获益良多。
关键词:落料拉深冲压力冲模闭合高度拉深力1 冷冲压工艺规程的编制1.1工艺分析该零件为旋转体零件。
属于大批量生产,是一个不带凸缘的圆筒形零件,且其形状简单、对称,有利于合理排样、减小废料,直线、曲线的连接处为圆角过渡。
课程设计设计说明书格式规范

课程设计设计说明书格式标准一、课程设计设计说明书格式标准装订成册的书面说明书和完整电子文档各一份,说明书统一采用A4纸打印,说明书格式如下,顺序为:〔一〕封面〔二〕索命数正文,包括:1、摘要〔包括中文摘要和英文摘要〕:分别为300字左右,应包括:工作目的、内容、结论、关键词2、目录以上部分以I、II……编制页码。
以下部分根据章节编写序号和页码。
3、主体部分〔不少于12000字,按要求设定页眉页角,要求居中〕主要包括引言或绪论、正文、结论、致谢,采用全角符号,英文和数字半角。
每页28行、每行32-35个汉字,倍行间距3.1格式:主体部分的编写格式由引言(绪论)开始,以结论结束。
主体部分必须由1页开始。
一级标题之间换页,二级标题之间空行。
3.2序号3.2.1毕业说明书各章应有序号,序号用阿拉伯数字编码,层次格式为:1××××〔三号黑体,居中〕××××××××××××××××××××××××××〔小三号黑体,居左〕×××××××××××××××××××××××××〔四号黑体,居左〕××××××××××××××××××××〔内容用小四号宋体〕。
《Java课程设计》说明书

《Java课程设计》说明书
课程设计报告书目录
一、设计课题
二、设计目的
三、操作环境
四、设计场所(机房号、机器号或自己机器)
五、设计过程(设计内容及及各源代码板块)
六、本次设计中用到的课程知识点(列出主要知识点)
七、设计过程中遇到的问题及解决办法
八、设计心得总结
2.总体设计
本程序是为了实现计算器的基本功能的运行。
利用监听器去实现计算器的基本功能。
3.科学计算器界面截图:
1)功能描述
1、打开计算器。
首先是标准型的计算器,具有基本的加减乘除,开方等
基本功能。
同时,在标准型的计算器中还可以存储文本框中的内容。
如图1所示:
图1标准型计算器界面
2、在标准型的计算器界面中,进行的运算--加法运算。
如计算
2+3=5.0。
如图2
图2加法功能
3、实现减法运算.如计算:4-2=2.0 如图3
图3 减法运算
4、实现取余运算.如计算 12%20=12.0 如图4
图4取余计算
4.程序整体设计说明
【1】程序中所用到的变量
count、line1、line2、leng、input、input1 【2】代码列表:
import java.awt.FlowLayout;。
课程设计说明书的内容及文本格式标准

课程设计说明书的内容及文本格式标准1、课程设计说明书要求用A4纸排版,单面打印,并装订成册,其内容包括:(1)封面(按教研室统一排版标准),姓名部分手签;(2)设计任务书(整体采用宋体小四号字体);(3)目录(单独编写,不与正文编号连在一起,一般采用罗马数字表示页码);(4)中文摘要(另起一页);(5)正文;(绪论、产品工艺介绍,工艺设计的计算,工艺流程示意图,章节的符号说明等内容)(6)结论(设计结果总汇一般以表格的形式);(7)结束语或致谢;(8)参考文献(9)主要符号说明(以表格的形式给出);(10)附录(计算机程序、附图等)。
2、课程设计说明书正文参考字数不少于3000字。
3、设计任务书格式。
4、目录格式:(1)标题“目录”(三号、黑体、居中);(2)章标题(四号、黑体、居左);(3)节标题(小四、宋体、居左)(4)页码(小四号、宋体、居右)整个页眉居中印有吉林化工学院食品工艺学课程设计的字样(楷体五号字)上边距2.3cm。
5、正文格式(1)页边距:上2.54cm,下2.54cm,左2.09cm,右1.59cm,页眉1.5cm,页脚1.75cm,装订线位置左;(2)字体:正文全部用宋体、小四号字;(3)行距:固定值18;(4)页码:底部居中,五号字,宋体;页眉:上部居中,小五号字,楷体;(5)数据表格全部采用五号字,宋体;(6)公式全部用公式编辑器来编辑(12号字宋体)。
6、参考文献格式:(1)标题:“参考文献”小四,黑体,居中(2)示例:(五号,宋体)图书类:(序号)作者1,作者2……作者n,书名,出版地点,出版社,出版年,页次。
期刊类:(序号)作者1,作者2……作者n,文章名,期刊名(版本),出版年,卷次(期次),页次食品科学与工程系教研室2011年5月课程设计教师评分表注:按优(90-100分)、良(80-89分)、中(70-79分)、及格(60-69分)、不及格(60分以下)五级评定成绩。
课程设计说明书撰写格式规范

课程设计说明书撰写格式规范一、课程设计说明书打印页面设置1、页面设置纸张大小:A4,单页打印。
页边距及行间距:上2.54厘米,下2.54厘米,左2.5厘米,右2.5厘米,左侧装订,页眉1.5厘米,页脚1.75厘米。
除一、二级标题及特别注明外,正文统一为1.5倍行距。
二、课程设计说明书内容构成及格式要求1、封面页:独立一页(具体见格式模板)2、目录页:独立一页。
目录页中正文部分的内容只列到二级标题为止。
除“目录”用黑体三号居中、中间空4个字距外,其他统一用宋体小四号,1.5倍行距。
论文目录及页码部分由正文中定义的标题自动生成。
在完成论文正文文字录入后,按下述步骤排版:(1)点击菜单“格式”中“样式与格式”,打开“样式与格式”窗口。
(2)选中文中相应的标题行,点击“样式与格式”窗口中的“标题1”定义“一级标题”,“标题2”定义“二级标题”…。
并按对各级标题的格式要求修改标题格式(如字体、字号、段前、段后行距等)。
(3)选中已定义好的标题。
双击格式刷,将格式刷到其它同类标题上。
(4)所有各级标题定义完毕后,编辑点移至准备插入目录的地方,再点击主菜单中“插入”→“引用”→“索引和目录”即可生成自动生成目录。
目录页中只生成至二级标题。
(5)为了使页码编号只从正文开始,建议整个文档分为3节,方法是:在第2节论文正文开始处点击“插入”→“分隔符”→“分节符类型”→“下一页”。
在第2节内,点击“插入”→“页码”→“格式”→选“起始页码”。
这样,第1节(封面等)可不编页码,只从第2节开始插入页码。
4、中英文摘要页本页主要由以下内容构成。
(1)论文标题:原则上控制在30个汉字以内,黑体小二号居中,段前2行,段后1行;如限定范围,可以借副标题予以补充,臵于标题下,前加破折号,用黑体四号居中。
(2)作者名、导师及学院信息:用宋体小四号居中, 1.5倍行距,分两行设臵。
(3)中文摘要:是指对论文内容不加任何评论的简短陈述及要点摘录,限200-300字,中文摘要后加上冒号用黑体五号,左对齐;相应具体内容紧接冒号之后,用宋体五号, 1.5倍行距。
课程设计说明书内容及格式要求
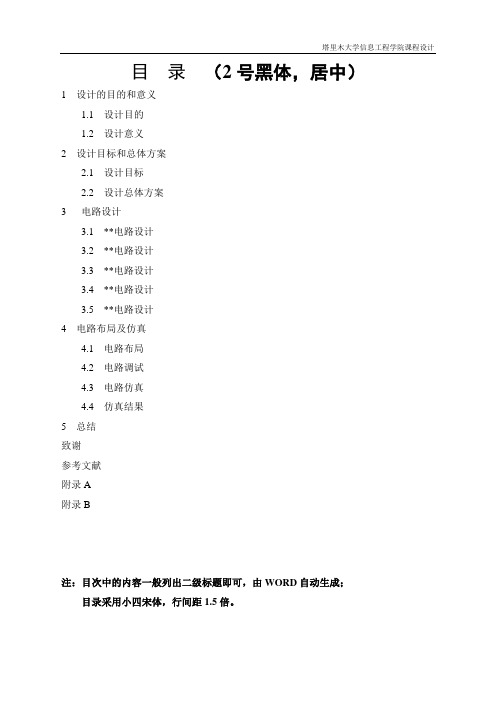
目录(2号黑体,居中)1 设计的目的和意义1.1 设计目的1.2 设计意义2 设计目标和总体方案2.1 设计目标2.2 设计总体方案3 电路设计3.1 **电路设计3.2 **电路设计3.3 **电路设计3.4 **电路设计3.5 **电路设计4 电路布局及仿真4.1 电路布局4.2 电路调试4.3 电路仿真4.4 仿真结果5 总结致谢参考文献附录A附录B注:目次中的内容一般列出二级标题即可,由WORD自动生成;目录采用小四宋体,行间距1.5倍。
题目(2号字,宋体加粗,居中。
)摘要:×××××××××(宋体小四段前后间距 0行左右缩进0字符首行缩进0字符,行距1.5倍)。
此处大概200-300字,大致内容为:以某某为研究背景,利用了某某软件和某某技术设计了某某作品,实现了某某功能,具有某某价值或者具有某某意义。
关键词:此处是本设计的重要核心词,词和词之间用分号或者空格间隔1××××××(作为1级标题,4号字体,楷体_GB2312,左右缩进0字符,首行缩进0字符,段前段后间距0行,行间距1.5倍行距。
)×××××××××(小四号字宋体段前后间距0行左右缩进0字符首行缩进2字符,行距1.5倍。
)1.1 ××××(作为2级标题,小4号字,黑体,段前后间距0行,左右缩进0字符,首行缩进0字符,行距1.5倍。
)×××××××××(小四号字宋体段前后间距0行左右缩进0字符首行缩进2字符,行距1.5倍。
)1.2 ×××××××××××××××1.3×××××××××××××2××××××(作为1级标题,4号字体,楷体_GB2312,左右缩进0字符,首行缩进0字符,段前段后间距0行,行间距1.5倍行距。
课程设计说明书
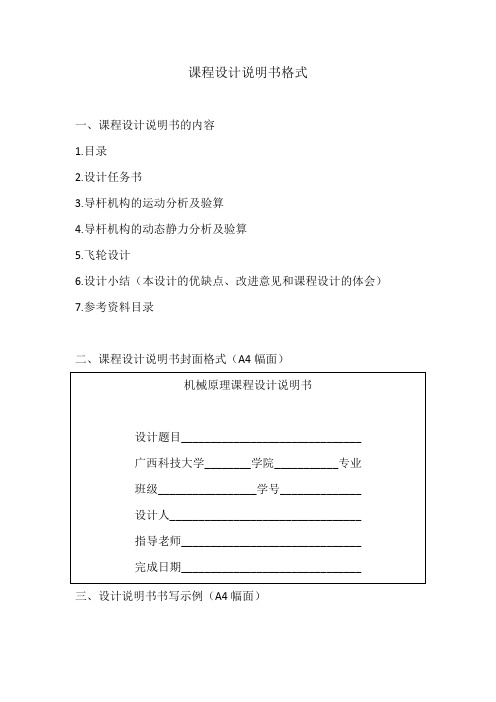
课程设计说明书格式
一、课程设计说明书的内容
1.目录
2.设计任务书
3.导杆机构的运动分析及验算
4.导杆机构的动态静力分析及验算
5.飞轮设计
6.设计小结(本设计的优缺点、改进意见和课程设计的体会)
7.参考资料目录
二、课程设计说明书封面格式(A4幅面)
三、设计说明书书写示例(A4幅面)
四、其他要求
1.设计说明书要求论述清楚,文字精炼,计算准确,书写工整。
2.设计说明书用黑色或蓝色墨水笔按一定格式书写,采用统一格式的封面,装订成册
3.设计说明书其他格式要求,自行参考《机械原理课程设计指导书》。
课程设计说明书
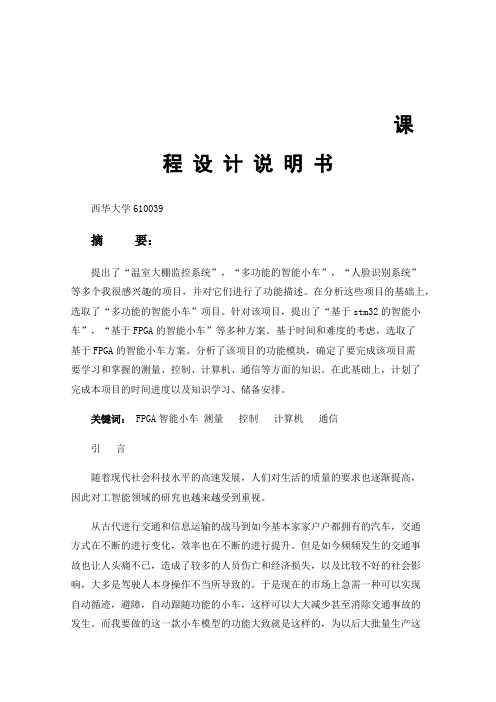
课程设计说明书西华大学610039摘要:提出了“温室大棚监控系统”,“多功能的智能小车”,“人脸识别系统”等多个我很感兴趣的项目,并对它们进行了功能描述。
在分析这些项目的基础上,选取了“多功能的智能小车”项目。
针对该项目,提出了“基于stm32的智能小车”,“基于FPGA的智能小车”等多种方案。
基于时间和难度的考虑,选取了基于FPGA的智能小车方案。
分析了该项目的功能模块,确定了要完成该项目需要学习和掌握的测量、控制、计算机、通信等方面的知识。
在此基础上,计划了完成本项目的时间进度以及知识学习、储备安排。
关键词: FPGA智能小车测量控制计算机通信引言随着现代社会科技水平的高速发展,人们对生活的质量的要求也逐渐提高,因此对工智能领域的研究也越来越受到重视。
从古代进行交通和信息运输的战马到如今基本家家户户都拥有的汽车,交通方式在不断的进行变化,效率也在不断的进行提升。
但是如今频频发生的交通事故也让人头痛不已,造成了较多的人员伤亡和经济损失,以及比较不好的社会影响,大多是驾驶人本身操作不当所导致的。
于是现在的市场上急需一种可以实现自动循迹,避障,自动跟随功能的小车,这样可以大大减少甚至消除交通事故的发生。
而我要做的这一款小车模型的功能大致就是这样的,为以后大批量生产这种智能汽车打下研发和制造的基础。
相信在不久的将来这种智能汽车会在大众之间普及!1 选题随着社会的高速发展,人们的交通方式也在发生着显著的变化,从古时候的战马,到近代的自行车,以及到21世纪的汽车,使得交通运输和信息传递的效率显著提升。
而为了减少甚至避免交通事故的发生,一种能实现自动避障,循迹,跟随功能的智能小车想法应运而生。
主要可以分为基于stm32的智能小车和基于FPGA的智能小车。
1.1 项目描述●基于stm32的智能小车由ST(意法半导体)公司使用arm公司的cortex-M3为核心生产的32位的单片机,由于单片机的内部资源较为丰富,因此可以实现较多功能。
课程设计说明书封面及撰写格式
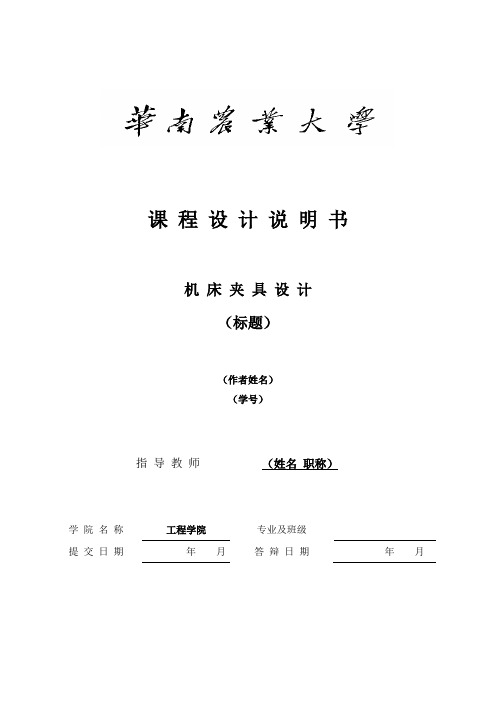
课程设计说明书机床夹具设计(标题)(作者姓名)(学号)指导教师(姓名职称)学院名称工程学院专业及班级提交日期年月答辩日期年月一、排版与装订1、页面设置:页边距上下左右各用2.4cm。
2、行距:全部采用1.5倍行距。
3、页码:每页下端居中,全部采用阿拉伯数字排序,如1,2,3等,不要写“第1页”或“-1-”等。
4、页眉:全部不加页眉。
5、分页:摘要、目录、正文、致谢、参考文献等各部分都应分页。
6、页面大小:全部采用A4纸。
7、封面用230克浅蓝色虎纹纸。
8、装订:一律左侧装订。
二、目录1、目录置于摘要之后,“目录”两字用黑体4号字居中,字与字之间空4个字距。
2、目录中之中文全部用宋体小4号字。
3、目录中各层次标题与正文层次标题同,一律用阿拉伯数字排序,不同层次的数字之间用圆点“.”相隔,如22.12.1.12.1.1.1一般不要超过4级层次。
4、层次标题序号一律左对齐,页码右对齐,中间用小黑点连接。
三、正文1、正文层次标题应简短明确,以不超过15字为宜,题末不加标点符号。
各层次一律用阿拉伯字连续编号,如:“1”,“2.1”,“3.1.2”,一律左顶格,后空一字距写标题。
一级标题从前言起编,一律用黑体4号字,左顶格。
2、二级标题用黑体小4号字,左顶格。
3、三级标题用楷体小4号字,左顶格。
4、正文其他部分全部用宋体小4号字。
5、各级标题与段落之间不留空行。
6、图、表与正文之间上下各空一行。
7、图应有图题,放图下方居中,用阿拉伯数字编号,如:图1,图号后不加任何符号,空1个字距写图题。
8、表应有表题,放表上方居中,用阿拉伯数字编号,如:表1,表号后不加任何符号,空1个字距写表题。
9、表一律采用三线表。
10、图题、表题与图、表之间不留空行。
11、试验数据的统计分析,如果是应用计算机软件的,尽可能用公开发行的程序。
如果是自编的,应在文体后的附录中列出程序。
在数表中各试验数据的平均数之后应列出平均数的标准误(S.E.),而不应列出标准差(S.D.)。
课程设计说明书模板
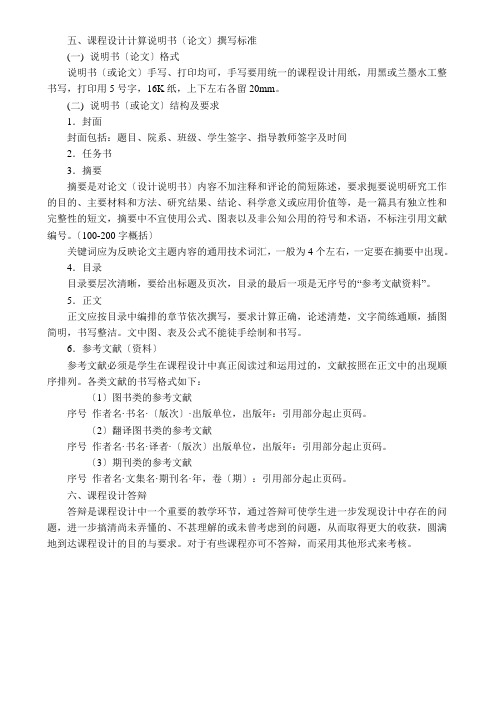
五、课程设计计算说明书〔论文〕撰写标准(一)说明书〔论文〕格式说明书〔或论文〕手写、打印均可,手写要用统一的课程设计用纸,用黑或兰墨水工整书写,打印用5号字,16K纸,上下左右各留20mm。
(二)说明书〔或论文〕结构及要求1.封面封面包括:题目、院系、班级、学生签字、指导教师签字及时间2.任务书3.摘要摘要是对论文〔设计说明书〕内容不加注释和评论的简短陈述,要求扼要说明研究工作的目的、主要材料和方法、研究结果、结论、科学意义或应用价值等,是一篇具有独立性和完整性的短文,摘要中不宜使用公式、图表以及非公知公用的符号和术语,不标注引用文献编号。
〔100-200字概括〕关键词应为反映论文主题内容的通用技术词汇,一般为4个左右,一定要在摘要中出现。
4.目录目录要层次清晰,要给出标题及页次,目录的最后一项是无序号的“参考文献资料”。
5.正文正文应按目录中编排的章节依次撰写,要求计算正确,论述清楚,文字简练通顺,插图简明,书写整洁。
文中图、表及公式不能徒手绘制和书写。
6.参考文献〔资料〕参考文献必须是学生在课程设计中真正阅读过和运用过的,文献按照在正文中的出现顺序排列。
各类文献的书写格式如下:〔1〕图书类的参考文献序号作者名·书名·〔版次〕·出版单位,出版年:引用部分起止页码。
〔2〕翻译图书类的参考文献序号作者名·书名·译者·〔版次〕出版单位,出版年:引用部分起止页码。
〔3〕期刊类的参考文献序号作者名·文集名·期刊名·年,卷〔期〕:引用部分起止页码。
六、课程设计答辩答辩是课程设计中一个重要的教学环节,通过答辩可使学生进一步发现设计中存在的问题,进一步搞清尚未弄懂的、不甚理解的或未曾考虑到的问题,从而取得更大的收获,圆满地到达课程设计的目的与要求。
对于有些课程亦可不答辩,而采用其他形式来考核。
附课程设计参考模板课程设计〔学年论文〕说明书课题名称:学生学号:专业班级:学生:学生成绩:指导教师:课题工作时间:至黄山学院教务处制课程设计评审标准〔指导教师用〕黄山学院****设计课程设计说明书目录一、************ (2)二、************ (2)三、****************************** (3)四、********************** (3)五、六、七、八、九、十、设计小结 (17)参考资料 (17)【摘要】【关键词】〔正文部分:论文正文部分包括:绪论〔或前言、序言〕、论文主体及结论。
- 1、下载文档前请自行甄别文档内容的完整性,平台不提供额外的编辑、内容补充、找答案等附加服务。
- 2、"仅部分预览"的文档,不可在线预览部分如存在完整性等问题,可反馈申请退款(可完整预览的文档不适用该条件!)。
- 3、如文档侵犯您的权益,请联系客服反馈,我们会尽快为您处理(人工客服工作时间:9:00-18:30)。
目录1、零件的分析 (1)1.1挺杆零件图的分析 (1)1.1.1作用 (1)1.1.2技术要求 (1)1.2传动轴的结构工艺性分析 (2)2.绘制零件图 (2)3.生养类型:中批量生产 (2)4.毛坯的确定 (2)4.1确定毛坯类型 (2)4.2确定毛坯表面加工余量及公差 (3)4.2.1毛坯直径余量的确定 (3)4.2.2毛坯长度L的确定 (3)4.3绘制毛坯图 (3)5.工艺规程设计 (3)5.1选择定位基准 (4)5.2制订工艺路线 (4)5.2.1确定各表面加工方法 (4)5.2.2加工顺序,加工阶段的划分 (4)5.2.3热处理工序安排 (4)5.2.4拟定工艺路线 (5)5.3选择加工设备及工艺装备 (5)6.工序设计 (5)6.1确定工序尺寸 (5)6.2确定切削用量 (6)6.3顶尖孔尺寸 (8)7.填写工艺文件 (8)8.参考文献 (8)1.零件的分析1.1挺杆零件图的分析1.1.1作用:挺杆是内燃机中一个重要的零件。
Ф30端面与凸轮轴接触,轴向运动传动,它承受高速、较强烈的冲击和受磨损条件下工作。
20Cr经渗碳淬火,使零件表面具有较高的硬度和耐磨性,而心部具有较高的强度和冲击韧性。
它的作用是将凸轮推力传递给气门。
1.1.2技术要求:材料:20Cr;渗碳层深度为0.7—0.8;用头部为Ф30的标准螺栓拧入M10×1螺孔,并用标准螺母拧紧,Ф30平面边缘对Ф16轴线的端跳为0.03;1.1.3零件的工艺分析:(1)毛坯材料20Cr的含碳量为0.2%,故锻件成型后安排了正火处理,以适当地提高材料的强度和硬度,减少内应力,避免切削时产生的粘刀现象。
(2)渗碳后,安排车Ф16端面及钻孔Ф8.5×80,有如下作用:车去端面碳层,使端面淬火后还能车削;也能保证端面与孔Ф8.5的垂直度。
(3)粗磨Ф16外圆后作为定位基准,一次装夹下:车端面、镗孔、攻丝。
并要保证M10×1内螺纹与外圆Ф16的同轴度和M10×1与端面的垂直度,以达到技术条件的第一条要求。
(4)在M7120A型平面磨床上Ф30的左端面时,工件在专业夹具上竖直安置,底部用弹簧做辅助支撑,一般是多件装夹,故用一根平行于电磁吸盘的圆柱压在所有工件的端面上,同时用V形夹块加紧Ф16外圆,此时圆柱即可离开工件端面。
这种装夹方法,可保证Ф30的端面相对Ф16圆柱面轴线的端跳在0.025mm公差范围内。
(5)Ф8.5小孔深度为80mm,使用过程有效长度为25mm,主要作用是提高挺杆该处的刚度以及减轻重量。
修磨Ф8.5钻头的两条主切削刃时,有意识磨成不对称,约相差0.1mm左右,以利于排屑,提高钻头的耐用度。
2.绘制零件图(见A3挺杆零件图)3.生产类型:大批量生产4.毛坯的确定4.1确定毛坯类型材料为20Cr钢,要求强度较高,要承受较大的循环载荷等,所以毛坯形式采用锻件,其晶粒细小,较均匀,致密,可以保证零件的工作可靠,由于零件为大批生产,为了提高生产率,保证加工质量,故采用模锻成型。
4.2查有关手册确定毛坯表面加工余量及公差用查表法分别确定各加工表面的机械加工余量、工序尺寸及毛坯尺寸。
为简化模锻毛坯的外形,取直径为φ16段的毛坯尺寸与φ30相同。
4.2.1毛坯直径余量的确定毛坯直径的确定:工件直径φ30,公差为0.20,机械加工总余量为:2X(0.7+0.25+0.05)=2mm;查询资料可知,毛坯直径加工余量为2-4mm;所以取毛坯尺寸为φ34mm。
4.2.2毛坯长度L的确定查表可知:粗车端面加工余量为2;粗车后调质后半精加工,端面的加工余量为0.45;则总长至少为124+2x(2+0.45)=129.8则取毛坯总长度为130mm。
4.3绘制毛坯图(见A3传动轴毛坯零件图)5.工艺规程设计5.1选择定位基准基面的选择是工艺规程设计中的重要工作之一,基准选择的正确与合理,可以使加工质量得到保证,生产效率得以提高。
否则,加工工艺过程中会出问题,甚至造成零件的大批报废,使生产无法进行。
(1)粗基准的选择本零件是带螺孔的杆类零件。
参照资料可知,应选择Ф30的圆柱表面(即余量最小处)作为粗基准。
(2)精基准的选择本零件的设计基准是螺孔,为避免由于基准不重合而产生的误差,应选螺孔为定位基准,即遵守“基准重合”原则,即选择M10×1螺孔及其端面作为精基准。
5.2制订工艺路线5.2.1确定各表面加工方法轴类在进行外圆加工时,会因切除大量金属后引起残余应力重新分布而变形。
应将粗精加工分开,先粗加工,再进行半精加工和精加工。
主要表面精加工放在最后进行。
传动轴大多是回转面,主要是采用车削和外圆磨削。
由于该零件的各段公差等级较高,表面粗糙度值较小,精加工时应采用磨削加工。
所有外圆均采用粗车、半精车、磨加工的方案。
在侧槽处则需进行铣加工。
5.2.2加工顺序,加工阶段的划分外圆表面加工顺序应为:应加工大直径外圆,然后再加工小直径外圆,以免一开始就降低了工件的刚度。
螺纹一般有较高的精度,其加工应安排在工件局部淬火之前进行,避免因淬火后产生的变形而影响螺纹的精度。
定位精基准面中心孔应在粗加工之前加工。
拟定零件的工艺过程时,在考虑主要表面加工的同时,还要考虑次要表面的加工。
在半精加工φ30mm,φ16mm外圆时,应车到图样规定的尺寸,同时加工出各圆角、倒角和螺纹;侧槽应在半精车后以及磨削之前铣削加工出来,这样可保证铣槽时有较精确的定位基准,又可避免在精磨后铣键槽时破坏已精加工的外圆表面。
该传动轴加工划分为三个阶段:粗车:粗车外圆,钻中心孔等;半精车:半精车各处外圆等;粗磨,半精磨。
各阶段划分大致以热处理为界。
5.2.3热处理工序安排:轴的热处理要根据其材料和使用要求确定。
该传动轴材料为20Cr,需进行正火处理,并安排在粗车各外圆之前。
同时根据技术要求,需要渗碳处理,且安排在半精车后,钻孔前。
为了便于加工并提高材料性能,在磨削前需要进行热处理,及淬火和低温回火。
5.2.4拟定工艺路线下料-正火-粗车Ф30外圆-车Ф16右端面,钻中心孔-半精车各外圆,倒角,圆角-渗碳-打螺纹孔-车螺纹-铣槽-热处理-磨削-检验。
5.3选择加工设备及工艺装备刀具的选择:20Cr经正火后,综合力学性能较高,故选用硬质合金刀具进行粗、精车,可选用牌号为YT15。
有90度刀,90度度偏刀,90度偏刀R=5,切断刀;铣刀用硬质合金柱铣刀YG8;磨具使用普通平面砂轮。
量具的选择:游标卡尺,螺旋测微器,轴用双头卡规。
机床的选择:车轴上各外圆用通用车床,CA6140;铣键槽用立式铣床X52K;粗、精磨用外圆磨床M7120A。
6.工序设计6.1确定工序尺寸外圆,加工长度为5mm,与其联结的非加工外圆表面直径为φ16,为简化Φ300.20锻件毛坯的外形,考虑其作为定位基准尺寸,有径向圆跳动公差要求,因此,其工序尺寸和加工余量为:粗车:φ34mm ,加工至φ32mm;半精车:φ32mm ,2Z=1.4,加工至φ30.6mm;粗磨:φ30.6mm ,2Z=0.5,加工至φ30.1mm;半精磨:φ30.1mm ,2Z=0.1,加工至φ30mm。
Ф160.04外圆,加工长度为109mm,与其联结的加工外圆表面直径为φ30,为简化-0.06锻件毛坯的外形,考虑其加工工序及精度要求,因此,其工序尺寸和加工余量为:粗车:φ32mm ,加工至φ18mm;半精车:φ18mm ,2Z=1.4,加工至φ16.6mm;粗磨:φ16.6mm ,2Z=0.5,加工至φ16.1mm;半精磨:φ16.1mm ,2Z=0.1,加工至φ16mm。
6.2确定切削用量粗车,Ra值为40um~10um,切削速度>50m/min,进给量为0.30~0.50mm/r。
查表,可取进给量f为0.5mm/r;背吃刀量ap为3~5mm6.2.1.车φ30左端面取机床转速为n=330r/min,则:车端面,加工余量为2mm;切削速度为v=πdn/1000=π30X330/1000=31.1m/min6.2.2.车φ16左端面及打中心孔取机床转速为n=330r/min,则:车端面,加工余量为2mm;钻φ30mm左端面,切削速度为v=πdn/1000=π30X330/1000=31.1m/min6.2.2.将毛坯外圆φ34mm车至φ30mm,长度为128mm粗车(1)背吃刀量单边余量Z=3mm,可一次切除;(2)进给量查表,可选用f=0.5mm/r;(3)切削速度查表,切削速度的计算公式为v=Cvkv/(T0.2ap0.15fy v)其中,切削速度的修正系数kv =kMvkKrvktvksv =0.87x0.81x1.0x0.8=0.56376,f<0.7mm/r,则Cv=242,y v=0.35,T=60所以v=242X0.56376/(600.230.150.50.35)=65.0m/min确定机床主轴转速:ns=1000vc/(πdw)=1000X65.0/(πX34)=608.5r/min,按机床选取560r/min所以实际切削速度为v=πdn/1000=π34X560/1000=59.8m/min6.2.3.将毛坯外圆φ32mm车至φ18mm,长度为119mm粗车(1)背吃刀量单边余量Z=3mm,可3次切除;(2)进给量查表,可选用f=0.5mm/r;(3)切削速度查表,切削速度的计算公式为v=Cvkv/(T0.2ap0.15fyv)其中,切削速度的修正系数kv =kMvkKrvktvksv =0.87x0.81x1.0x0.8=0.56376,f<0.7mm/r,则Cv=242,yv=0.35,T=60所以v=242X0.56376/(600.230.150.50.35)=65.0m/min确定机床主轴转速:ns=1000vc/(πdw)=1000X65.0/(πX32)=646.6r/min,按机床选取710r/min 所以实际切削速度为v=πdn/1000=π32X710/1000=71.4m/min6.2.4.半精车φ16mm端面,长度达图,留0.016mm余量取机床转速为n=330r/min,则:车端面,加工余量为2mm;切削速度为v=πdn/1000=π18X330/1000=18.7m/min6.2.5半精车φ16mm外圆及圆弧面,留余量0.2mm,倒角达图(1)背吃刀量单边余量Z=0.9mm,可一次切除;(2)进给量查表,可选用f=0.5mm/r;(3)切削速度查表,切削速度的计算公式为v=Cvkv/(T0.2ap0.15fyv)其中,切削速度的修正系数kv =kMvkKrvktvksv =0.87x0.81x1.0x0.8=0.56376,f<0.7mm/r,则Cv=242,yv=0.35,T=60所以v=242X0.56376/(600.2*0.90.15*0.50.35)=78.3m/min确定机床主轴转速:ns=1000vc/(πdw)=1000X78.3/(πX18)=1385.3r/min,按机床选取1400r/min所以实际切削速度为v=πdn/1000=π18X1400/1000=79.1m/min6.2.6.半精车φ30端面达图,半精车φ30外圆,倒圆角达图,倒圆角达图,倒角取机床转速为n=330r/min,则:车端面,保证总长为124mm;半精车(1)背吃刀量单边余量Z=2mm,可一次切除;(2)进给量查表,可选用f=0.5mm/r;(3)切削速度查表,切削速度的计算公式为v=Cvkv/(T0.2ap0.15fyv)其中,切削速度的修正系数kv =kMvkKrvktvksv =0.87x0.81x1.0x0.8=0.56376,f<0.7mm/r,则Cv=242,yv=0.35,T=60所以v=242X0.56376/(600.2*20.15*0.50.35)=69.5m/min确定机床主轴转速:ns=1000vc/(πdw)=1000X69.5/(πX32)=690.9r/min,按机床选取710r/min所以实际切削速度为v=πdn/1000=π32X710/1000=71.4m/min6.2.7. ;将毛坯外圆φ16.2mm粗磨至φ16.016mm,长度为102mm,ap=0.05,单行程为4;砂轮主轴转速n砂=1755r/min,v砂=35m/s。