物料需求计划例题2
主生产计划及物料需求计划测试题(含答案)

MPS/MRP系统背景资料:主生产计划(MPS)及物料需求计划(MRP)系统是ERP 管理软件的核心,也是ERP 系统发展的基础。
通过MPS/MRP 系统将企业外部销售市场对企业的销售需求转化为企业内部的生产需求和采购需求,将销售计划转化为生产计划和采购计划。
MPS/MRP 管理方式可以解决“需要什么?什么时候需要?需要多少?”三大难题。
相对与手工管理来说,MPS/MRP 计划可以大大提高计划下达的效率,并大大增加计划的准确性、及时性,从根源及计划层面杜绝不必要的库存,减少浪费。
某ERP系统的主生产计划管理系统融先进的MRP 管理思想与软件设计之中,通过主生产计划MPS(Master Production Schedule),将独立的需求(销售或预测)作为需求,考虑现有库存、已分配量、预计入库等因素,通过BOM 向下展开需求,得到主要产品(MPS 类物料)的计划量。
主计划员可以对该计划量进行维护、确认或进行粗能力计划,将能力的影响体现在计划的改变上。
对确定的计划订单,也可作为预计入库量,实现滚动计划功能。
MPS 计算产生的计划订单经过确认,除可以生成本身的生产计划外,还可以将相关需求传输到MRP 系统,作为MRP 的需求来源。
主生产计划的需求来源分为两个方面,一个是客户订单,另一个是预测订单。
客户订单与预测订单两者形成MPS/MRP的需求有三种方式即仅为客户订单,仅为预测订单和客户订单+预测订单的某种组合。
这种组合关系系统提供了五种处理方式:♦客户订单+预测订单,不冲销♦客户订单+预测订单,向前冲销♦客户订单+预测订单,向后冲销♦客户订单+预测订单,先向前冲销再向后冲销♦客户订单+预测订单,先向后再向前冲销。
企业计划员可以根据实际情况选择冲销策略,并设定相应的冲销范围。
系统内部冲销的顺序为:按指定的最早的N日开始冲销,再进行N+1日的冲销,直至冲销完毕或超过设定的日期。
在进行MPS/MRP 计算时,可以定义不同的计划方案。
物料需求计划例题
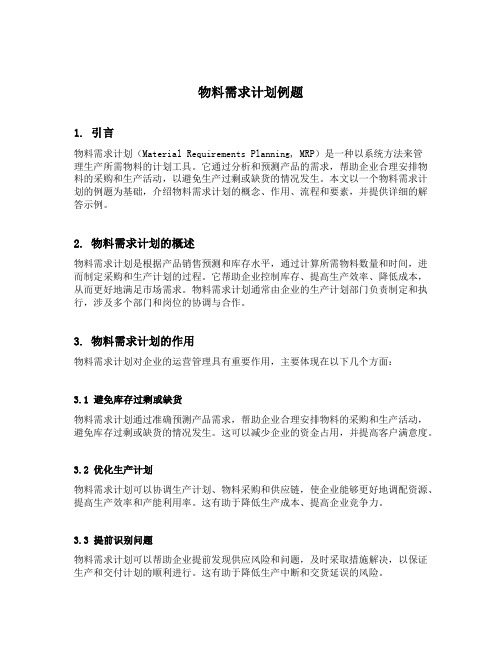
物料需求计划例题1. 引言物料需求计划(Material Requirements Planning, MRP)是一种以系统方法来管理生产所需物料的计划工具。
它通过分析和预测产品的需求,帮助企业合理安排物料的采购和生产活动,以避免生产过剩或缺货的情况发生。
本文以一个物料需求计划的例题为基础,介绍物料需求计划的概念、作用、流程和要素,并提供详细的解答示例。
2. 物料需求计划的概述物料需求计划是根据产品销售预测和库存水平,通过计算所需物料数量和时间,进而制定采购和生产计划的过程。
它帮助企业控制库存、提高生产效率、降低成本,从而更好地满足市场需求。
物料需求计划通常由企业的生产计划部门负责制定和执行,涉及多个部门和岗位的协调与合作。
3. 物料需求计划的作用物料需求计划对企业的运营管理具有重要作用,主要体现在以下几个方面:3.1 避免库存过剩或缺货物料需求计划通过准确预测产品需求,帮助企业合理安排物料的采购和生产活动,避免库存过剩或缺货的情况发生。
这可以减少企业的资金占用,并提高客户满意度。
3.2 优化生产计划物料需求计划可以协调生产计划、物料采购和供应链,使企业能够更好地调配资源、提高生产效率和产能利用率。
这有助于降低生产成本、提高企业竞争力。
3.3 提前识别问题物料需求计划可以帮助企业提前发现供应风险和问题,及时采取措施解决,以保证生产和交付计划的顺利进行。
这有助于降低生产中断和交货延误的风险。
4. 物料需求计划的流程物料需求计划的流程通常包括以下几个步骤:4.1 收集销售预测数据首先,企业需要收集和分析销售预测数据,包括产品的预期销售量和销售时间。
这可以通过历史销售数据、市场调研和销售预测模型来进行。
4.2 计算净需求净需求是指在考虑产品销售预测和现有库存的基础上,计算出所需物料的数量和时间。
计算净需求时,还需要考虑物料的提前期、安全库存和订货批量等因素。
4.3 制定采购计划根据计算出的净需求,制定物料的采购计划。
MRP案例分析
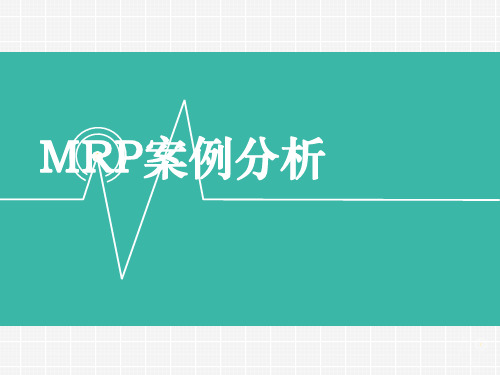
Thanks for watching ~
大家都知道 ERP是以生产为核心的,而生
产的核心是物料需求计划-MRP,实现MRP的关键技
术 就是BOM(BILL OF MATERIAL-物料结构表)。
这种方法于60年代出现,用最朴素逻辑,在计算机
帮助下按产品BOM和工艺流程逐级推演,得到了在
一般平稳生产条件下可以应用的生产计划方法,流
行了近40年。
杭州Motorola的网络管理:
一款手机经研发设计以后,便会生成一张完整 的BOM(Bill of material 材料清单),其中 包括一台手机所需用到的所有材料名类(一般在2 00~300种之间)和单机用量。BOM同时也 构成了网络的起始端,就像一张百味俱全的药方, 向整副经脉注气,经由采购、收货、验料、入库、 上线、下线、包装、销售,中间还经过财务结算, 整张网络由此一气呵成。
电子定单和Schedule Sharing 杭州摩托罗拉每年完成的采购额超过4亿美金,
其中有80%是通过电子定单和一种叫Schedule Sharing(S/S)的系统完成的。
摩托罗拉总部和大部分的供应商每年都会签定一个协议价格, 采购人员用这个全球统一的价格每年给供应商下一次定单。定单 是在电脑系统中完成并且用电脑网络传递给供应商的,它的内容 只有材料编号和价格,没有需求数量,摩托罗拉把这样的定单叫 做空白定单。定单一旦在电脑中生成,系统就会赋予一个随机定 单号,这个号码一直伴随着定单从生到死。定单是整个物料管理 中的把手,它扯起一条主线,把采购、收货、入库、付款如大红 灯笼般串起。
第九讲物料需求计划
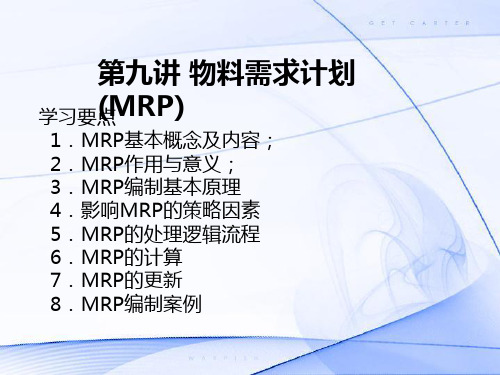
MRP项目
计划周期
1 2 3 4 5 6 25 7 8 30 40 25 40 15 15 30 15 15 30 9 10 11 15 15 30 12 13
X(LT=4) Y(LT=6) 相关需求X-A 相关需求Y-A 独立需求A
A的毛需求
15
40
40
30
15
45
【例题9.3:应用低位码 计算物料的净需求】 已知:MPS为在第8个 计划周期时产出200件A 产品;各物料的计划接 收量和已分配量为0; 物料ABCD期初库存分别 为0、120、60、70件, 安全库存量为0;物料 ABCD批量规则为直接批 量法。求物料ABCD的净 需求。
毛需求计算考虑因素
• • • • •
是否存在独立需求 是否共用物料 是否低位码 是否是计划BOM 是否存在替代
如果存在替代,要不要替代则考虑: • 是否可以降低工作量 • 是否可以降低成本 • 客户是否满意 • 近期是否短缺
(3)计算净需求量。 考虑安全库存推算特定时段的净需求量。 当PAB初值≥安全库存时,净需求=0 当PAB初值<安全库存时,净需求=安全库存- PAB初值
生产什么? MPS
主生产计划
2
(物料清单) 用到什么?
产品信息
4 物料需求计划 MRP
已有什么? (物料可用量)
3 库存信息
买什么?
采购计划
做什么?
生产计划
MRP 回答了
问
4 个制造业的主要问题
答
(生产什么 1 生产什么?
2 用到什么? 3 已有什么?
+
用到什么) - 已有什么 1 主生产计划( MPS) = 还缺什么
(二)MRP中的输出数据项 1.采购订单 采购什么? 采购多少? 何时开始采购? 何时完成采购? 2.制造订单 制造什么? 制造多少? 何时开始制造? 何时完成制造?
主生产计划及物料需求计划测试题(含答案)

MPS/MRP系统背景资料:主生产计划(MPS)及物料需求计划(MRP)系统就是ERP 管理软件得核心,也就是ERP系统发展得基础。
通过MPS/MRP 系统将企业外部销售市场对企业得销售需求转化为企业内部得生产需求与采购需求,将销售计划转化为生产计划与采购计划。
MPS/MRP管理方式可以解决“需要什么?什么时候需要?需要多少?”三大难题。
相对与手工管理来说,MPS/MRP 计划可以大大提高计划下达得效率,并大大增加计划得准确性、及时性,从根源及计划层面杜绝不必要得库存,减少浪费。
某ERP系统得主生产计划管理系统融先进得MRP管理思想与软件设计之中,通过主生产计划MPS(MasterProduction Schedule),将独立得需求(销售或预测)作为需求,考虑现有库存、已分配量、预计入库等因素,通过BOM向下展开需求,得到主要产品(MPS 类物料)得计划量。
主计划员可以对该计划量进行维护、确认或进行粗能力计划,将能力得影响体现在计划得改变上。
对确定得计划订单,也可作为预计入库量,实现滚动计划功能。
MPS 计算产生得计划订单经过确认,除可以生成本身得生产计划外,还可以将相关需求传输到MRP 系统,作为MRP 得需求来源。
主生产计划得需求来源分为两个方面,一个就是客户订单,另一个就是预测订单。
客户订单与预测订单两者形成MPS/MRP得需求有三种方式即仅为客户订单,仅为预测订单与客户订单+预测订单得某种组合。
这种组合关系系统提供了五种处理方式:♦客户订单+预测订单,不冲销♦客户订单+预测订单,向前冲销♦客户订单+预测订单,向后冲销♦客户订单+预测订单,先向前冲销再向后冲销♦客户订单+预测订单,先向后再向前冲销。
企业计划员可以根据实际情况选择冲销策略,并设定相应得冲销范围。
系统内部冲销得顺序为:按指定得最早得N日开始冲销,再进行N+1日得冲销,直至冲销完毕或超过设定得日期、在进行MPS/MRP 计算时,可以定义不同得计划方案。
物料需求计划计算例题物料需求计划(MRP)的基本计算模型
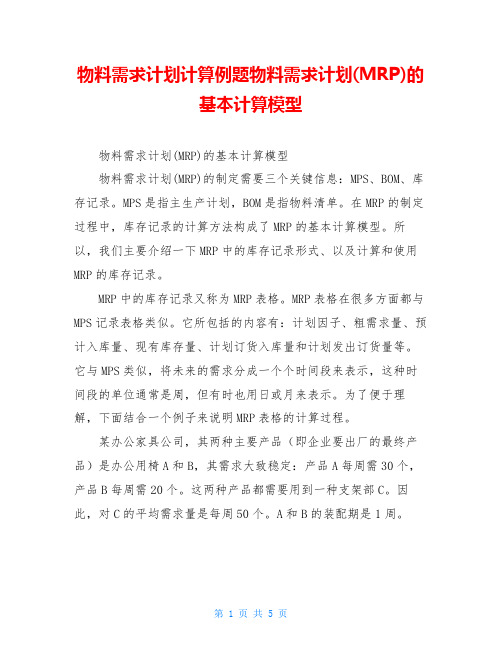
物料需求计划计算例题物料需求计划(MRP)的基本计算模型物料需求计划(MRP)的基本计算模型物料需求计划(MRP)的制定需要三个关键信息:MPS、BOM、库存记录。
MPS是指主生产计划,BOM是指物料清单。
在MRP的制定过程中,库存记录的计算方法构成了MRP的基本计算模型。
所以,我们主要介绍一下MRP中的库存记录形式、以及计算和使用MRP的库存记录。
MRP中的库存记录又称为MRP表格。
MRP表格在很多方面都与MPS记录表格类似。
它所包括的内容有:计划因子、粗需求量、预计入库量、现有库存量、计划订货入库量和计划发出订货量等。
它与MPS类似,将未来的需求分成一个个时间段来表示,这种时间段的单位通常是周,但有时也用日或月来表示。
为了便于理解,下面结合一个例子来说明MRP表格的计算过程。
某办公家具公司,其两种主要产品(即企业要出厂的最终产品)是办公用椅A和B,其需求大致稳定:产品A每周需30个,产品B每周需20个。
这两种产品都需要用到一种支架部C。
因此,对C的平均需求量是每周50个。
A和B的装配期是1周。
下图1是办公椅A和B的主生产计划表格以及部C的库存记录表格(尚未完成)。
这种表格没有标准格式,该例所用的是一种常见格式。
如上图示,在这种格式中,左上方通常要标出产品名称及其性质(如上图中,表明C是支架部),右上方表示计划因子,通常包括三项:生产批量、生产周期和安全库存量。
在本例中,C的批量是230个,生产周期为2周,安全库存量为50个。
这些计划因子的量都需要预先选定。
当这些值发生变化以后,管理人员必须及时更新库存记录。
下面首先来看库存记录的内容和确定方法。
一、库存记录要素及其计算1、粗需求量。
上例中未来8周的粗需求量如图1所示。
其需求量是根据C的最终产品A和B的主生产计划所决定的,但有时候需要加上一些作为配(更换)使用的量。
对C的需求之所以比MPS中A、B的时间提前1周,是因为MPS中所表示的各周的量实际上是指当周应该完成的量。
第六章 物料需求计划

以X、Y两种产品为例,两种产品包含的层次子件和需用的数量(括号内数字)及产品结构树如下图所示,假定两种产品已经过主生产计划推算出计划投入量和产出量,其余所含物料的提前期、批量、安全库存、现有量、已分配量均为已知。
产品结构树
图中,A、B是产品X的1层子件,C是X、Y两种产品的通用件,但在两种产品中所处的层次不同(1和2,所处低层次是2),需用的数量也不同。
各种物料的需求量是由上向下层进行分解的,如X、Y的需求量是由主生产计划确定,A、B的需求量是由X确定,C的需求量是由X、Y确定的。
(1)推算Y对D、E的毛需求。
(2)推算X对A、B的毛需求。
(3) 推算A的PAB初值、净需求、计划产出量和预计库存量。
(4)推算A对D的毛需求。
(5)推算X、Y对D的总毛需求。
(6)推算D的PAB初值、净需求、计划产出量和预计库存量。
(7)合并MRP报表,得出D物料的需求计划。
某工厂制作物料需求计划案例
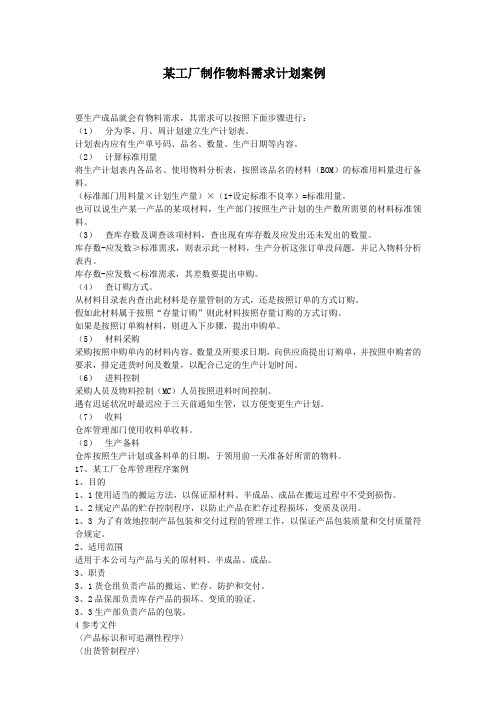
某工厂制作物料需求计划案例要生产成品就会有物料需求,其需求可以按照下面步骤进行:(1)分为季、月、周计划建立生产计划表。
计划表内应有生产单号码、品名、数量、生产日期等内容。
(2)计算标准用量将生产计划表内各品名、使用物料分析表,按照该品名的材料(BOM)的标准用料量进行备料。
(标准部门用料量×计划生产量)×(1+设定标准不良率)=标准用量。
也可以说生产某一产品的某项材料,生产部门按照生产计划的生产数所需要的材料标准领料。
(3)查库存数及调查该项材料,查出现有库存数及应发出还未发出的数量。
库存数-应发数≥标准需求,则表示此一材料,生产分析这张订单没问题,并记入物料分析表内。
库存数-应发数<标准需求,其差数要提出申购。
(4)查订购方式。
从材料目录表内查出此材料是存量管制的方式,还是按照订单的方式订购。
假如此材料属于按照“存量订购”则此材料按照存量订购的方式订购。
如果是按照订单购材料,则进入下步骤,提出申购单。
(5)材料采购采购按照申购单内的材料内容、数量及所要求日期,向供应商提出订购单,并按照申购者的要求,排定进货时间及数量,以配合已定的生产计划时间。
(6)进料控制采购人员及物料控制(MC)人员按照进料时间控制。
遇有迟延状况时最迟应于三天前通知生管,以方便变更生产计划。
(7)收料仓库管理部门使用收料单收料。
(8)生产备料仓库按照生产计划或备料单的日期,于领用前一天准备好所需的物料。
17、某工厂仓库管理程序案例1、目的1、1使用适当的搬运方法,以保证原材料、半成品、成品在搬运过程中不受到损伤。
1、2规定产品的贮存控制程序,以防止产品在贮存过程损坏,变质及误用。
1、3为了有效地控制产品包装和交付过程的管理工作,以保证产品包装质量和交付质量符合规定。
2、适用范围适用于本公司与产品与关的原材料、半成品、成品。
3、职责3、1货仓组负责产品的搬运、贮存、防护和交付。
3、2品保部负责库存产品的损坏、变质的验证。
物料需求计划计算例题

物料需求计划计算例题物料需求计划(MRP)的基本计算模型物料需求计划(MRP)的制定需要三个关键信息:MPS、BOM、库存记录。
MPS是指主生产计划,BOM是指物料清单。
在MRP的制定过程中,库存记录的计算方法构成了MRP的基本计算模型。
所以,我们主要介绍一下MRP中的库存记录形式、以及如何计算和使用MRP的库存记录。
MRP中的库存记录又称为MRP表格。
MRP表格在很多方面都与MPS记录表格类似。
它所包括的内容有:计划因子、粗需求量、预计入库量、现有库存量、计划订货入库量和计划发出订货量等。
它与MPS类似,将未来的需求分成一个个时间段来表示,这种时间段的单位通常是周,但有时也用日或月来表示。
为了便于理解,下面结合一个例子来说明MRP表格的计算过程。
某办公家具公司,其两种主要产品(即企业要出厂的最终产品)是办公用椅A和B,其需求大致稳定:产品A每周需30个,产品B每周需20个。
这两种产品都需要用到一种支架部件C。
因此,对C的平均需求量是每周50个。
A和B的装配期是1周。
下图1是办公椅A和B的主生产计划表格以及部件C的库存记录表格(尚未完成)。
这种表格没有标准格式,该例所用的是一种常见格式。
如上图示,在这种格式中,左上方通常要标出产品名称及其性质(如上图中,表明C是支架部件),右上方表示计划因子,通常包括三项:生产批量、生产周期和安全库存量。
在本例中,C的批量是230个,生产周期为2周,安全库存量为50个。
这些计划因子的量都需要预先选定。
当这些值发生变化以后,管理人员必须及时更新库存记录。
下面首先来看库存记录的内容和确定方法。
一、库存记录要素及其计算1、粗需求量。
上例中未来8周的粗需求量如图1所示。
其需求量是根据C的最终产品A和B的主生产计划所决定的,但有时候需要加上一些作为配件(更换件)使用的量。
对C的需求之所以比MPS中A、B的时间提前1周,是因为MPS中所表示的各周的量实际上是指当周应该完成的量。
物料需求计划例题
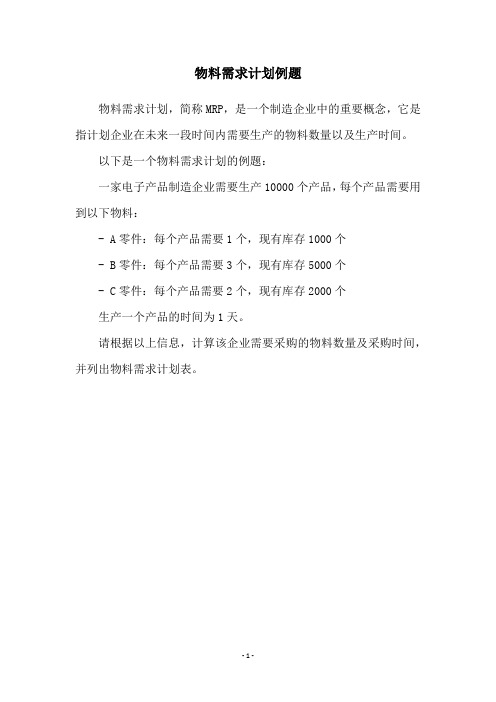
物料需求计划例题
物料需求计划,简称MRP,是一个制造企业中的重要概念,它是指计划企业在未来一段时间内需要生产的物料数量以及生产时间。
以下是一个物料需求计划的例题:
一家电子产品制造企业需要生产10000个产品,每个产品需要用到以下物料:
- A零件:每个产品需要1个,现有库存1000个
- B零件:每个产品需要3个,现有库存5000个
- C零件:每个产品需要2个,现有库存2000个
生产一个产品的时间为1天。
请根据以上信息,计算该企业需要采购的物料数量及采购时间,并列出物料需求计划表。
- 1 -。
mrp练习题讲解
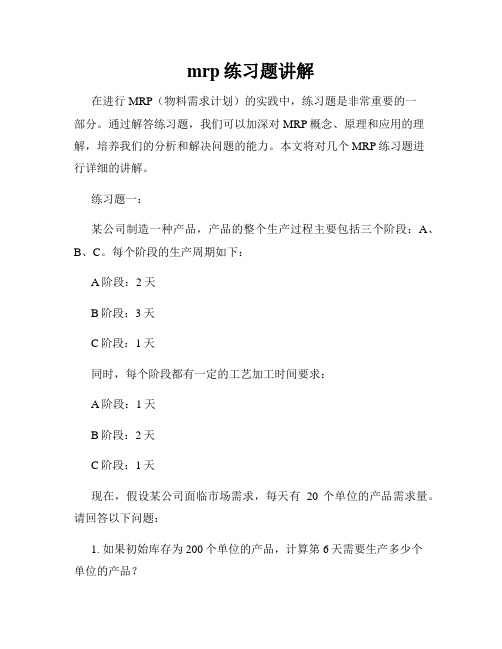
mrp练习题讲解在进行MRP(物料需求计划)的实践中,练习题是非常重要的一部分。
通过解答练习题,我们可以加深对MRP概念、原理和应用的理解,培养我们的分析和解决问题的能力。
本文将对几个MRP练习题进行详细的讲解。
练习题一:某公司制造一种产品,产品的整个生产过程主要包括三个阶段:A、B、C。
每个阶段的生产周期如下:A阶段:2天B阶段:3天C阶段:1天同时,每个阶段都有一定的工艺加工时间要求:A阶段:1天B阶段:2天C阶段:1天现在,假设某公司面临市场需求,每天有20个单位的产品需求量。
请回答以下问题:1. 如果初始库存为200个单位的产品,计算第6天需要生产多少个单位的产品?2. 如果初始库存为50个单位的产品,计算第8天需要生产多少个单位的产品?3. 如果初始库存为0个单位的产品,计算第5天需要生产多少个单位的产品?解答:1. 首先,我们需要计算每个阶段的净需求量。
A阶段的净需求量 = (第6天需求量 - 第2天的产品库存)= 20 * 6 - 200 = 20个单位的产品B阶段的净需求量 = (第6天需求量 - 第3天的产品库存)= 20 * 6 - (20 * 3 - 20 * 2)= 20个单位的产品C阶段的净需求量 = (第6天需求量 - 第4天的产品库存)= 20 * 6 - (20 * 2 - 20 * 1)= 20个单位的产品2. 类似地,我们可以计算出第8天每个阶段的净需求量:A阶段的净需求量 = (第8天需求量 - 第2天的产品库存)= 20 * 8 - 200 = 120个单位的产品B阶段的净需求量 = (第8天需求量 - 第3天的产品库存)= 20 * 8 - (20 * 3 - 20 * 2)= 140个单位的产品C阶段的净需求量 = (第8天需求量 - 第4天的产品库存)= 20 * 8 - (20 * 2 - 20 * 1)= 160个单位的产品3. 在初始库存为0的情况下,同样计算每个阶段的净需求量:A阶段的净需求量 = (第5天需求量 - 第2天的产品库存)= 20 * 5 - 0 = 100个单位的产品B阶段的净需求量 = (第5天需求量 - 第3天的产品库存)= 20 * 5 - (20 * 3 - 20 * 2)= 120个单位的产品C阶段的净需求量 = (第5天需求量 - 第4天的产品库存)= 20 * 5 - (20 * 2 - 20 * 1)= 140个单位的产品通过以上计算,我们可以得出在不同的初始库存下,不同天数所需要生产的产品数量。
物料需求计划计算举例
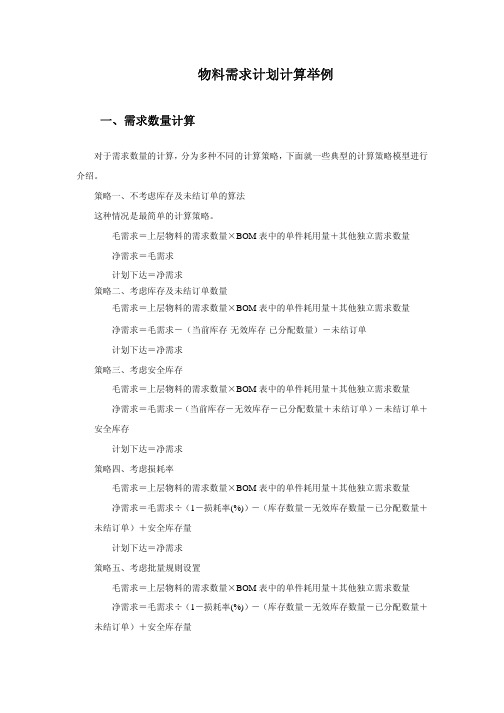
计划完工日期(调整后)=计划完工日期(调整前)+提前期余量
计划开工日期(调整后)=计划开工日期(调整前)+提前期余量
5、考虑工厂日历
如果计划开工日期和计划完工日期中间的时间段落在工厂日历的休息日,计划开工日期
和计划完工日期相应做顺延调整。
对于一些大型的企业,其组织结构可能还包括一些子公司、部门、生产车间等下级部门,
需要注意的是,如果物料的批量原则是 POQ 时,物料的订货周期(P)将影响到计划 完工日期。
2、计算物料的订货提前期 订货提前期=固定订货提前期+变动订货提前期 变动订货提前期=取大整数(变动订货提前期系数×订货批量÷变动提前期批量) 3、计算计划开工日期 计划开工日期=计划完工日期-订货提前期 物料需求计划在计算时,必须考虑工厂日历和提前期余量设置情况。 4、增加提前期余量调整
=2007 年 11 月 18 日 同时因为 2007 年 11 月 17 日和 2007 年 11 月 18 日为双休日,相应的计划开工日期再次 向前提前至工作日,计划完工日期为工作日,保持不变。 计划完工日期=2007 年 11 月 27 日 计划开工日期=2007 年 11 月 18 日-2 天
00
1
1
1
20
00
00
00
2
2
2
00
00
00
在策略二情况下,由于考虑了当前库存和未结订单的数量,塑料套的净需求发生了变化。 具体计算步骤如下:
毛需求=上层物料的需求数量×BOM 表中的单件耗用量+独立需求 =100×1×2+10 =210
净需求=毛需求-(当前库存-无效库存-已分配数量)-未结订单 =210-(10-4-3)-5 =202
=120 由于三脚架的批量增量为 120,所以本次最终的计划下达数量为 120.
物料需求计划计算例题 [物料需求计划(MRP)的基本计算模型]
![物料需求计划计算例题 [物料需求计划(MRP)的基本计算模型]](https://img.taocdn.com/s3/m/9ac6c662daef5ef7bb0d3c23.png)
《物料需求计划计算例题 [物料需求计划(MRP)的基本计算模型]》摘要:物计划(R)制定要三关键信息、B、库存记录,所以我们主要介绍下R库存记录形式、以及如何计算和使用R库存记录,、粗量物计划(R)基计算模型物计划(R)制定要三关键信息、B、库存记录是指主生产计划B是指物清单R制定程库存记录计算方法构成了R基计算模型所以我们主要介绍下R库存记录形式、以及如何计算和使用R库存记录R库存记录又称R表格R表格很多方面都与记录表格类似它所包括容有计划因子、粗量、预计入库量、现有库存量、计划订货入库量和计划发出订货量等它与类似将分成段表示这种段单位通常是周但有也用日或月表示了便理下面结合例子说明R表格计算程某办公具公司其两种主要产品(即企业要出厂终产品)是办公用椅和B其致稳定产品每周30产品B每周0这两种产品都要用到种支架部件因对平量是每周50和B装配期是周下图是办公椅和B主生产计划表格以及部件库存记录表格(尚完成)这种表格没有标准格式该例所用是种常见格式如上图示这种格式左上方通常要标出产品名称及其性质(如上图表明是支架部件)右上方表示计划因子通常包括三项生产批量、生产周期和安全库存量例批量是30生产周期周安全库存量50这些计划因子量都要预先选定当这些值发生变化以管理人员必须及更新库存记录下面首先看库存记录容和确定方法、库存记录要素及其计算、粗量上例8周粗量如图所示其量是根据终产品和B主生产计划所定但有候要加上些作配件(更换件)使用量对所以比、B提前周是因所表示各周量实际上是指当周应该完成量但由生产或装配是要周期因该生产指令发出必须给出这部分提前量该例周50其装配周期周故周应发出生产订单开始装配上图表格表示是考虑了生产周期生产订单发出和生产量样R库存记录粗要量是指当周应准备量例如了周装完50周必须准备50、预计入库量(l r简称R)它是指订单已发出、但货尚收到量对外购件它现可能处几种状态买方刚发出订单供应商正加工;正从供应商至卖方途;已到买方、买方正验货等对加工件它现可能状态包括正生产现场被加工;等待他原材和零件到达;正机床前排队等待加工;正从工序移至下工序等周50其生产周期周故至少周前已发出了该生产订单但通常不会比提前周更早地发出订单3、现有库存量()其概念与概念相指每周被满足手头仍有库存量该记录随着每周进货或出货情况而更新各周则可计算德出其计算公式式周末; R周预计入库量; R周计划订货入库量; GR周粗;可见上式与计算方式是致即R+R相当量GR相当x()这里不存预测值或订单值选择因是相关、确定上面图只给除了前周周只剩7少所要50安全库存量这是要生产信即要增加R信、计划订货入库量(l r简称R)其含义是计划订货或生产、但订单尚发出订货量这量义是要保持量不低安全库存(考虑安全库存保持非即可)对某些不要安全库存物则如其义是要保持非库存记录所表示R量应包括这两种情况R确定方法如下()出现短缺(或值或安全库存量)当周制订R量其值应是等安全库存;()继续计算其各周当又出现短缺制订下R量这两步骤反复进行直至整计划期记录和R记录格都填满5、计划发出订货量(l rr rl简称R)它实际上是要说明订单发出或开始生产所以将其称“╳╳量”是因这种对说明库存记录是通将该订单量记入相应栏说明该基计算式是到货减生产周期利用这项可容易地导出构成某项物B下层物粗摘《生产与运作管理》(刘丽著)。
主生产计划及物料需求计划测试题含答案

第一篇MPS/MRP系统背景资料:♦主生产筹划(MPS)及物料需求筹划(MRP)系统是ERP 管理软件旳核心, 也是ERP系统发展旳基本。
通过MPS/MRP 系统将公司外部销售市场对公司旳销售需求转化为公司内部旳生产需求和采购需求, 将销售筹划转化为生产筹划和采购筹划。
MPS/MRP 管理方式可以解决“需要什么?什么时候需要?需要多少?”三大难题。
相对与手工管理来说, MPS/MRP 筹划可以大大提高筹划下达旳效率, 并大大增长筹划旳精确性、及时性, 从本源及筹划层面杜绝不必要旳库存, 减少挥霍。
♦某ERP系统旳主生产筹划管理系统融先进旳MRP 管理思想与软件设计之中, 通过主生产筹划MPS(Master Production Schedule), 将独立旳需求(销售或预测)作为需求, 考虑既有库存、已分派量、估计入库等因素, 通过BOM 向下展开需求, 得到重要产品(MPS 类物料)旳筹划量。
主筹划员可以对该筹划量进行维护、确认或进行粗能力筹划, 将能力旳影响体目前筹划旳变化上。
对拟定旳筹划订单, 也可作为估计入库量, 实现滚动筹划功能。
MPS 计算产生旳筹划订单通过确认, 除可以生成自身旳生产筹划外, 还可以将有关需求传播到MRP 系统, 作为MRP 旳需求来源。
♦主生产筹划旳需求来源分为两个方面, 一种是客户订单, 另一种是预测订单。
客户订单与预测订单两者形成MPS/MRP旳需求有三种方式即仅为客户订单, 仅为预测订单和客户订单+预测订单旳某种组合。
这种组合关系系统提供了五种解决方式:♦客户订单+预测订单, 不冲销♦客户订单+预测订单, 向前冲销♦客户订单+预测订单, 向后冲销♦客户订单+预测订单, 先向前冲销再向后冲销客户订单+预测订单, 先向后再向前冲销。
公司筹划员可以根据实际状况选择冲销方略, 并设定相应旳冲销范畴。
系统内部冲销旳顺序为:按指定旳最早旳N日开始冲销, 再进行N+1日旳冲销, 直至冲销完毕或超过设定旳日期。
MRP计划表例题

mrp计算原理:根据主生产计划(mps)、库存计划、物料清单(bom),制定物料需求计划(mrp)主要公式:毛需求量=独立需求量+相关需求量计划库存量=上期期末库存量+本期订单产出量+本期预计入库量-毛需求量净需求量=本期毛需求量-上期库存量-本期预计入库量+安全库存量 bom中各物料的数量关系高层次与其下一层在数量上的倍数关系,由下一层旁边括号内的数字决定。
例如:a b┌───┼───┐ ┌───┼───┐ d(1)e(2) c(1) e(1) f(2) c(1) ┌─┴─┐┌─┴─┐ ┌─┴─┐ e(1) f(1) f(2)d(1) f(2) d(1)┌─┴─┐ ┌─┴─ e(1) f(1) e(1) f(1) c、d、e、f的相关需求关系式为: c=a+bd=a+c e=2a+b+d f=2b+d+2c计算mrp时注意三个问题 1.是否有安全库存 2.是否有批量限制 3.提前期是多少例题1:已知1个a由2个b和1个c组成,1个b由1个d和1个c组成,各物料的提前期均为1周,下表是客户对产品a的订单需求表,运用mrp求a产品的物料需求计划。
例题2.某家具公司组装餐桌,具体部件包括4个桌腿和1个桌面,提前期分别为2周和3周,组装需要1周的时间,公司接到40张餐桌的订单,需要在第5周交货,另外70张要在第7周交货,当前库存中有6张完工的餐桌,80张桌腿和44张桌面,请利用mrp求出公司的订货计划。
练习题:主生产计划:bom:库存信息以及提前期:物料的需求计划:例题3:某厂生产产品x,产品x的需求量见表1,并已知安全库存为3件,批量为25件,投入提前期为1周,期初库存为8件,期初计划到货为20件。
1件产品x需要2个部件y,并已知部件y每周作为备件外售需要量为4件,安全库存为12件,批量为60件,投入提前期为1周,期初库存为18件,计划第1周入库50件,试用mrp方法编制x和部件y的生产作业计划。
表1 产品x的需求量篇二:mrp计算题mrp库存管理练习题1、购买零件a的前置时间是4周,零件a现有数量为22件,另外在第4周的预计到达量为20件,今后8周对零件a的需求量如表6-31所示。
主生产计划及物料需求计划测试题(含答案)

MPS/MRP系统背景资料:主生产计划(MPS)及物料需求计划(MRP)系统是ERP 管理软件的核心,也是ERP系统发展的基础。
通过MPS/MRP 系统将企业外部销售市场对企业的销售需求转化为企业内部的生产需求和采购需求,将销售计划转化为生产计划和采购计划。
MPS/MRP 管理方式可以解决“需要什么?什么时候需要?需要多少?”三大难题。
相对与手工管理来说,MPS/MRP 计划可以大大提高计划下达的效率,并大大增加计划的准确性、及时性,从根源及计划层面杜绝不必要的库存,减少浪费。
某ERP系统的主生产计划管理系统融先进的MRP 管理思想与软件设计之中,通过主生产计划MPS(Master Production Schedule),将独立的需求(销售或预测)作为需求,考虑现有库存、已分配量、预计入库等因素,通过BOM 向下展开需求,得到主要产品(MPS 类物料)的计划量。
主计划员可以对该计划量进行维护、确认或进行粗能力计划,将能力的影响体现在计划的改变上。
对确定的计划订单,也可作为预计入库量,实现滚动计划功能。
MPS 计算产生的计划订单经过确认,除可以生成本身的生产计划外,还可以将相关需求传输到MRP 系统,作为MRP 的需求来源。
主生产计划的需求来源分为两个方面,一个是客户订单,另一个是预测订单。
客户订单与预测订单两者形成MPS/MRP的需求有三种方式即仅为客户订单,仅为预测订单和客户订单+预测订单的某种组合。
这种组合关系系统提供了五种处理方式:客户订单+预测订单,不冲销客户订单+预测订单,向前冲销客户订单+预测订单,向后冲销客户订单+预测订单,先向前冲销再向后冲销客户订单+预测订单,先向后再向前冲销。
企业计划员可以根据实际情况选择冲销策略,并设定相应的冲销范围。
系统内部冲销的顺序为:按指定的最早的N日开始冲销,再进行N+1日的冲销,直至冲销完毕或超过设定的日期。
在进行MPS/MRP 计算时,可以定义不同的计划方案。
第6章物料需求计划-管理10级作业
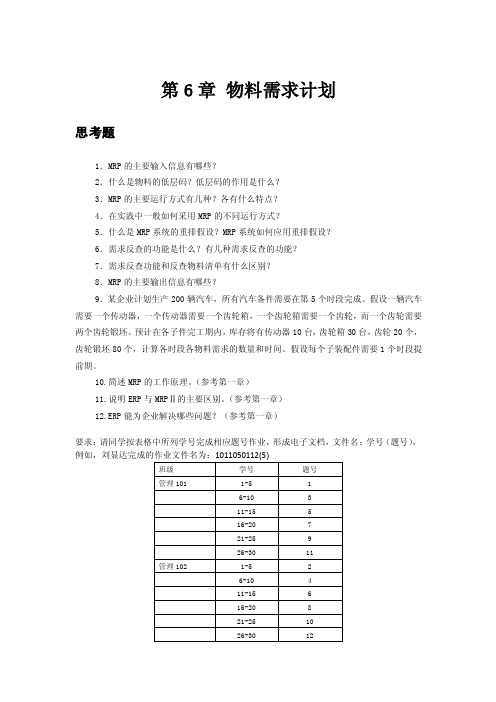
第6章物料需求计划
思考题
1.MRP的主要输入信息有哪些?
2.什么是物料的低层码?低层码的作用是什么?
3.MRP的主要运行方式有几种?各有什么特点?
4.在实践中一般如何采用MRP的不同运行方式?
5.什么是MRP系统的重排假设?MRP系统如何应用重排假设?
6.需求反查的功能是什么?有几种需求反查的功能?
7.需求反查功能和反查物料清单有什么区别?
8.MRP的主要输出信息有哪些?
9.某企业计划生产200辆汽车,所有汽车备件需要在第5个时段完成。
假设一辆汽车需要一个传动器,一个传动器需要一个齿轮箱,一个齿轮箱需要一个齿轮,而一个齿轮需要两个齿轮锻坯。
预计在各子件完工期内,库存将有传动器10台,齿轮箱30台,齿轮20个,齿轮锻坯80个,计算各时段各物料需求的数量和时间。
假设每个子装配件需要1个时段提前期。
10.简述MRP的工作原理。
(参考第一章)
11.说明ERP与MRPⅡ的主要区别。
(参考第一章)
12.ERP能为企业解决哪些问题?(参考第一章)
要求:请同学按表格中所列学号完成相应题号作业,形成电子文档,文件名:学号(题号),例如,刘显达完成的作业文件名为:1011050112(5)。
物料需求计划例题2

b.采用低层编码构造的产品结构树
层次
c.缩排部件清单列表
A
B(2)
E(4)
F(3)
C(3)
D(3)
H(2)表所示:
层次
部件
数量
0
A
1×100=100
1
B
2×100=200
C
3×100=300
2
D
3×300+1×100=1000
F
3×200=600
H
2×300=600
3
E
4×200+5×600=3800
G
2×600=1200
例:
层次DVDDVD
物料
当前库存量
提前期(周)
A型DVD
30
1
B型DVD
50
2
子装配件C
75
1
子装配件D
80
2
子装配件E
100
1
零件F
150
1
零件G
40
1
零件H
200
2
零件I
300
2
主生产计划
物料
第10周
A型DVD
700
B型DVD
670
B
毛需求量
1200
现有库存50
50
净需求量
1150
(LT=2)计划订单接收
1150
计划订单下达
1150
C
毛需求量
现有库存75
净需求量
(LT=1)计划订单接收
计划订单下达
D
毛需求量
现有库存80
净需求量
(LT=2)计划订单接收
- 1、下载文档前请自行甄别文档内容的完整性,平台不提供额外的编辑、内容补充、找答案等附加服务。
- 2、"仅部分预览"的文档,不可在线预览部分如存在完整性等问题,可反馈申请退款(可完整预览的文档不适用该条件!)。
- 3、如文档侵犯您的权益,请联系客服反馈,我们会尽快为您处理(人工客服工作时间:9:00-18:30)。
1340
现有库存40
40
0
净需求量
8810
1340
(LT=1)计划订单接收
8810
1340
计划订单下达
8810
1340
H
毛需求量
8810
1340
现有库存200
200
0
净需求量
8610
1340
(LT=2)计划订单接收
8610
1340
计划订单下达
8610
1340
I
毛需求量
13640
2680
现有库存300
1260
计划订单下达
1260
E
毛需求量
2300
现有库存100
100
净需求量
2200
(LT=1)计划订单接收
2200
计划订单下达
2200
F
4450
毛需求量
2520
1340
现有库存150
150
0
净需求量
6820
1340
(LT=1)计划订单接收
6820
1340
计划订单下达
6820
1340
G
4400
毛需求量
300
0
净需求量
13340
2680
(LT=2)计划订单接收
13340
2680
计划订单下达
13340
2680
计划订单下达
670
B
毛需求量
1200
现有库存50
50
净需求量
1150
(LT=2)计划订单接收
1150
计划订单下达
1150
C
毛需求量
2300
670
现有库存75
75
0
净需求量
2225
670
(LT=1)计划订单接收
2225
670
计划订单下达
2225
670
D
毛需求量
1340
现有库存80
80
净需求量
1260
(LT=2)计划订单接收
a.物料清单的产品结构图
b.采用低层编码构造的产品结构树
层次
c.缩排部件清单列表
A
B(2)
E(4)
F(3)
C(3)
D(3)
H(2)
E(5)
G(2)
D(1)
d.物料的需求量如下表所示:
层次
部件
数量
0
A
1×100=100
1
B
2×100=200
C
3×100=300
2
D
3×300+1×100=1000
F
3×200=600
B型DVD
1200
A型DVD和B型DVD的缩进式零件清单
A
B
C(1)
C(2)
F(1)
F(2)
I(1)
I(2)
G(2)
G(2)
H(1)
H(1)
D(2)
E(2)
F(2)
G(2)
I(2)
H(1)
物料需求计划见下表:
物料
4
5
6
7
8
9
10
A
毛需求量
700
现有库存30
30
净需求量
670
(LT=1)计划订单接收
670
H
2×300=600
3
E
4×200+5×600=3800
G
2×600=1200
例:
层次DVD DVD
物料
当前库存量
提前期(周)
A型DVD
30
1
B型DVD
50
2
子装配件C
75
1
子装配件D
80
2
子装配件E
1
零件G
40
1
零件H
200
2
零件I
300
2
主生产计划
物料
第10周
A型DVD
700