冲压变形理论
第一章 冲压变形的基本原理 复习题答案

第一章冲压变形的基本原理复习题答案一、填空题1.塑性变形的物体体积保持不变,其表达式可写成ε1+ε2+ε3=0。
2.冷冲压生产常用的材料有黑色金属、有色金属、非金属材料。
3.物体在外力的作用下会产生变形,如果外力取消后,物体不能恢复到原来的形状和尺寸,这种变形称为塑性变形。
4.影响金属塑性的因素有金属的组织、变形温度、变形速度、变形的应力与应变状态、金属的尺寸因素。
5.在冲压工艺中,有时也采用加热冲压成形方法,加热的目的是提高塑性,降低变形抗力。
6.材料的冲压成形性能包括成形极限和成形质量两部分内容。
7.压应力的数目及数值愈大,拉应力数目及数值愈小,金属的塑性愈好。
8.在同号主应力图下引起的变形,所需的变形抗力之值较大,而在异号主应力图下引起的变形,所需的变形抗力之值就比较小。
9.在材料的应力状态中,压应力的成分愈多,拉应力的成分愈少,愈有利于材料塑性的发挥。
10.一般常用的金属材料在冷塑性变形时,随变形程度的增加,所有强度指标均增加,硬度也增加,塑性指标降低,这种现象称为加工硬化。
11.用间接试验方法得到的板料冲压性能指标有总伸长率、均匀伸长率、屈强比、硬化指数、板厚方向性系数γ和板平面方向性系数△γ。
12.在筒形件拉深中如果材料的板平面方向性系数△γ越大,则凸耳的高度越大。
13.硬化指数n值大,硬化效应就大,这对于伸长类变形来说就是有利的。
14.当作用于坯料变形区的拉应力的绝对值最大时,在这个方向上的变形一定是伸长变形,故称这种变形为伸长类变形。
15. 当作用于坯料变形区的压应力的绝对值最大时,在这个方向上的变形一定是压缩变形,故称这种变形为压缩类变形。
16. 材料对各种冲压加工方法的适应能力称为材料的冲压成形性能。
17. 材料的冲压性能好,就是说其便于冲压加工,一次冲压工序的极限变形程度和总的极限变形程度大,生产率高,容易得到高质量的冲压件,模具寿命长等。
18. 材料的屈服强度与抗拉强度的比值称为屈强比。
冲压模板件变形原因

冲压模板件变形原因冲压模板件的变形是指在冲压过程中,模板件的形状发生了异常变化。
这种变形常常导致模板件无法满足设计要求,从而影响产品的质量和功能。
冲压模板件变形的原因可以归结为以下几个方面:1. 材料的选择与性能:模板件的变形与材料的选择和性能密切相关。
如果使用的材料强度不够高或者韧性较差,模板件在受力后容易发生塑性变形。
此外,材料的厚度和硬度也会影响模板件的变形。
选择合适的材料以及优化材料的性能可以减少模板件的变形风险。
2. 冲压模具的设计与加工:冲压模具的设计和加工质量直接影响模板件的变形。
如果模具的结构不合理或加工精度不高,会导致模板件在冲压过程中受到不均匀的应力分布,从而引发变形。
因此,合理设计和高质量的模具制造是减少模板件变形的关键。
3. 冲压工艺参数的选择:冲压工艺参数包括冲头的速度、压力、冲孔位置等。
这些参数的选择与调整直接影响到模板件的形状和变形情况。
不合理的工艺参数选择可能会引起模板件变形。
因此,对冲压工艺参数的合理优化和调整是减少模板件变形的重要措施。
4. 模板件的结构设计:模板件的结构设计包括形状、尺寸等方面。
如果模板件的结构设计不合理,容易导致在受到应力时发生形状变化,进而产生变形。
因此,合理的模板件结构设计是预防变形的关键。
综上所述,冲压模板件变形是由材料的选择与性能、冲压模具的设计与加工、冲压工艺参数的选择以及模板件的结构设计等多个方面共同作用所致。
通过选择合适的材料、优化模具设计和加工精度、合理调整工艺参数以及优化模板件的结构设计,可以有效减少冲压模板件的变形。
这将有助于提高产品的质量和功能。
(1-3)冲压变形理论基础

1 2 2 3 3 1 1 2 2 3 3 1
第一章 冷冲压模具设计与制造基础
第三节 冲压变形理论基础
三、塑性力学基础(续)
3.金属塑性变形时的应力应变关系(续) 几点讨论结论: (1)应力分量与应变分量符号不一定一致,• 拉应力不一定对 即 应拉应变,压应力不一定对应压应变; (2)某方向应力为零其应变不一定为零; (3)在任何一种应力状态下,应力分量的大小与应变分量的大 小次序是相对应的,即б1>б2>б3,则有ε1>ε2>ε3。 (4)若有两个应力分量相等,• 对应的应变分量也相等,即若 则 б1=б2,则有ε1=ε2。
方板拉深试验——最小阻力定律试验
第一章 冷冲压模具设计与制造基础
a)
b)
缩口加工中制件各区的划分 A-传力区;B-变形区;C-已变形区。
第一章 冷冲压模具设计与制造基础
1.当D-d较大,h较小,翻边。 2.当D-d较小,h较大时:
a. 拉深后切底切边缘;
b. 将D0增大,翻边后再切 边缘。
变形趋向性对冲压工艺的影响
第一章 冷冲压模具设计与制造基础
4.最小阻力定律(续) 控制变形的趋向性: 开流 和 限流 开流:在需要金属流动的地方减少阻力,使其顺利流动。 如加大圆角半径和间隙、减小摩擦等。 限流: 在不需要金属流动的地方增大阻力,限制金属流动。 如减小圆角半径和间隙、增大摩擦等。 板料各区的划分: 变形区,传力区, 不变形区,已变形区 弱区先变形,变形区为弱区
S S
一般应力状态:σ 1-σ 3=β σ
式中 σ1、σ3 、σS——最大主应 力、最小主应力和屈服应力; β——应力状态系数 ,一般近 似取1.1。
第一章 冷冲压模具设计与制造基础
冲压成形的基本理论

第一章 冲压成形的基本(jīběn) 理论
三、冲裁件断面的形状 冲裁件断面可以分成明显(míngxiǎn)的四部
分:塌 角,光亮带,断裂带和毛刺。 塌角:也称为圆角带。 光亮带b:也称为剪切面。 断裂带c:也称为撕裂带。 毛刺d:也称为披峰。
精品资料
第一章 冲压(chòngyā)成形的 基本理论
精品资料
第一章 冲压成形的基本(jīběn) 理论
右图为一套简易的拉深模,我们通过 (tōngguò)此动画更加形象深刻地认识
拉深模具,看清模具是如何运作。
精品资料
第一章 冲压成形的基本(jīběn) 理论
1.1.2 冲裁变形分析 一、冲裁变形过程
(一)弹性(tánxìng)变形阶段 (二)塑性变形阶段 (三)断列分离阶段
屈服比 (%)
延伸率 (%)
73
27 以 上
71
30 以 上
69
31 以 上
67
45
61
46
57
47
74
18
77
12
75
9
60
-
71
-
78
-
44
-
66
-
24
-
37
-
-
2 1 .6
60
4 7 .0
84
3 5 .6
91
1 2 .8
92
7 .8
93
1 3 .8
9 1 精品资料 2 . 2
加工硬化 值n
0.2 -
加工硬化系数之高低意味著什么现象呢?
n值高的材料会发生下列的行为: (1) 继续进行加工会造成材料硬化、伸长量减少而使加工不易。 (2) 继续进行加工将会抑制局部变形,得到一致的变形。
冲压成形的基本理论

硬度提升而塑性下降。 加工硬化对塑性变形旳影响: ❖ 不利旳一面——使所需旳变形力增长,而且限制了材料进一
步旳变形。 ❖ 有利旳一面——板料硬化能够减小过大旳局部变形,使变形
趋于均匀,从而增大成形极限,同步也提升了材料旳强度。
19
一临界值(与应力状态无关)时,材料就开始屈服。经过单向
拉伸试验可得出,此临界值等于材料旳屈服极限
。
s
等效应力:
2 2
(1 2 )2 2 3 2 3 12
则密塞斯塑性条件可体现为:
( 1
2 )2
2
3 2
3
1 2
2
2 s
9
1.1 塑性变形与应力应变 经过计算可知,两个条件之间差别很小。若把上式进行简化,
设 1 2, 则 3最大剪应力理论可表达为:
max (1 3 ) 2 s 2
或
1 3 s
这一理论形式简朴,与试验成果基本相符,用于分析板料成形问 题有足够旳精度。但其忽视了中间应力旳作用,所以不够完善。
8
1.1 塑性变形与应力应变
2. 密塞斯塑性条件
密塞斯提出:任意应力状态下,当某点旳等效应力 到达某
屈雷斯卡(H.Tresca) 塑性条件(最大剪应力理论) 密塞斯(von Mises) 塑性条件
7
1.1 塑性变形与应力应变
1. 屈雷斯卡塑性条件(最大剪应力理论) 屈雷斯卡提出:任意应力状态下,只要最大剪应力到达某临界值 (与应力状态无关)后,材料就开始屈服。经过单向拉伸试验可 得出,此临界值等于材料屈服极限旳二分之一。
24
1.2 加工硬化与硬化曲线
② S 硬 化直线 用真实应力与真实应变建立坐标系,硬化曲线上缩颈点处旳切线 斜率为 Sb。
冲压工艺与模具设计章节自测题原题(修改)
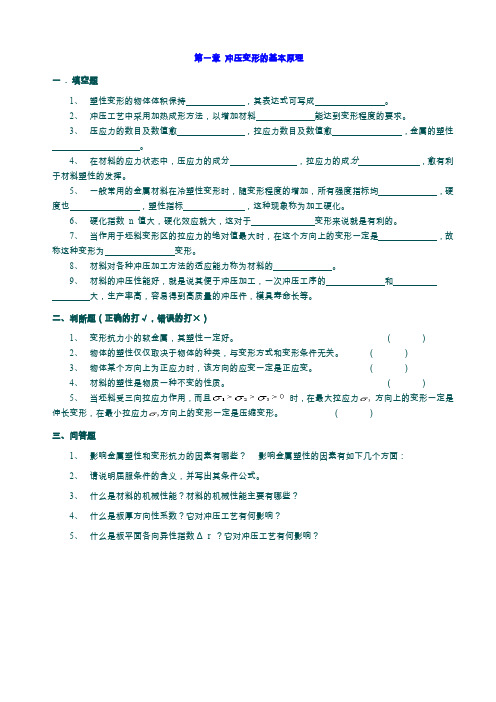
第一章冲压变形的基本原理一. 填空题1、塑性变形的物体体积保持,其表达式可写成。
2、冲压工艺中采用加热成形方法,以增加材料能达到变形程度的要求。
3、压应力的数目及数值愈,拉应力数目及数值愈,金属的塑性。
4、在材料的应力状态中,压应力的成分,拉应力的成分,愈有利于材料塑性的发挥。
5、一般常用的金属材料在冷塑性变形时,随变形程度的增加,所有强度指标均,硬度也,塑性指标,这种现象称为加工硬化。
6、硬化指数n 值大,硬化效应就大,这对于变形来说就是有利的。
7、当作用于坯料变形区的拉应力的绝对值最大时,在这个方向上的变形一定是,故称这种变形为变形。
8、材料对各种冲压加工方法的适应能力称为材料的。
9、材料的冲压性能好,就是说其便于冲压加工,一次冲压工序的和大,生产率高,容易得到高质量的冲压件,模具寿命长等。
二、判断题(正确的打√,错误的打×)1、变形抗力小的软金属,其塑性一定好。
()2、物体的塑性仅仅取决于物体的种类,与变形方式和变形条件无关。
()3、物体某个方向上为正应力时,该方向的应变一定是正应变。
()4、材料的塑性是物质一种不变的性质。
()5、当坯料受三向拉应力作用,而且时,在最大拉应力方向上的变形一定是伸长变形,在最小拉应力方向上的变形一定是压缩变形。
()三、问答题1、影响金属塑性和变形抗力的因素有哪些?影响金属塑性的因素有如下几个方面:2、请说明屈服条件的含义,并写出其条件公式。
3、什么是材料的机械性能?材料的机械性能主要有哪些?4、什么是板厚方向性系数?它对冲压工艺有何影响?5、什么是板平面各向异性指数Δ r ?它对冲压工艺有何影响?第二章冲裁工艺及冲裁模设计一、填空题1、从广义来说,利用冲模使材料叫冲裁。
它包括、、、、等工序但一般来说,冲裁工艺主要是指和工序。
2、冲裁根据变形机理的不同,可分为和。
3、冲裁变形过程大致可分为、、三个阶段。
4、冲裁件的切断面由、、、四个部分组成。
5、冲裁毛刺是在刃口附近的側面上材料出现时形成的。
第一章冲压变形的基本原理
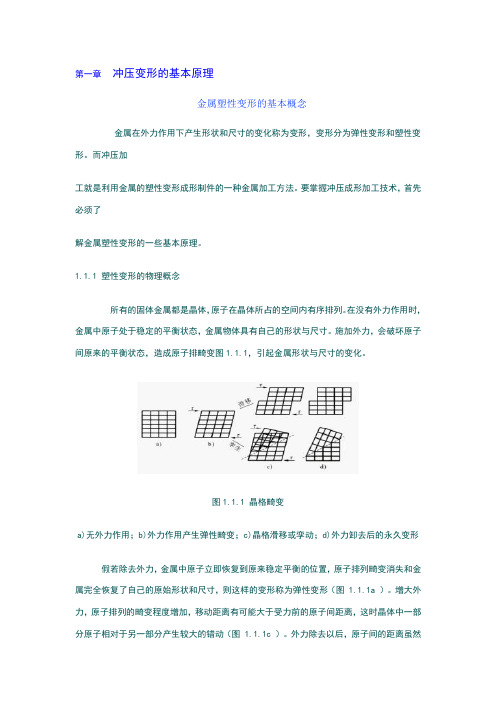
第一章冲压变形的基本原理金属塑性变形的基本概念金属在外力作用下产生形状和尺寸的变化称为变形,变形分为弹性变形和塑性变形。
而冲压加工就是利用金属的塑性变形成形制件的一种金属加工方法。
要掌握冲压成形加工技术,首先必须了解金属塑性变形的一些基本原理。
1.1.1 塑性变形的物理概念所有的固体金属都是晶体,原子在晶体所占的空间内有序排列。
在没有外力作用时,金属中原子处于稳定的平衡状态,金属物体具有自己的形状与尺寸。
施加外力,会破坏原子间原来的平衡状态,造成原子排畸变图1.1.1,引起金属形状与尺寸的变化。
图1.1.1 晶格畸变a)无外力作用;b)外力作用产生弹性畸变;c)晶格滑移或孪动;d)外力卸去后的永久变形假若除去外力,金属中原子立即恢复到原来稳定平衡的位置,原子排列畸变消失和金属完全恢复了自己的原始形状和尺寸,则这样的变形称为弹性变形(图 1.1.1a )。
增大外力,原子排列的畸变程度增加,移动距离有可能大于受力前的原子间距离,这时晶体中一部分原子相对于另一部分产生较大的错动(图 1.1.1c )。
外力除去以后,原子间的距离虽然仍可恢复原状,但错动了的原子并不能再回到其原始位置(图),金属的形状和尺寸也都发生了永久改变。
这种在外力作用下产生不可恢复的永久变形称为塑性变形。
受外力作用时,原子总是离开平衡位置而移动。
因此,在塑性变形条件下,总变形既包括塑性变形,也包括除去外力后消失的弹性变形。
1.1.2塑性变形的基本形式金属塑性变形是金属在外力的作用下金属晶格先产生晶格畸变,外力继续加大时,产生晶格错动,而这种错动通常在晶体中采取滑移和孪动两种形式。
1.滑移当作用在晶体上的切应力达到一定数值后,晶体一部分沿一定的晶面,向着一定的方向,与另一部分之间作相对移动,这种现象叫滑移,图1.1.1。
金属的滑移面,一般都是晶格中原子分布最密的面,滑移方向则是原子分布最密的结晶方向,因为沿着原子分布最密的面和方向滑移的阻力最小。
冲压出现压伤和变形的原因
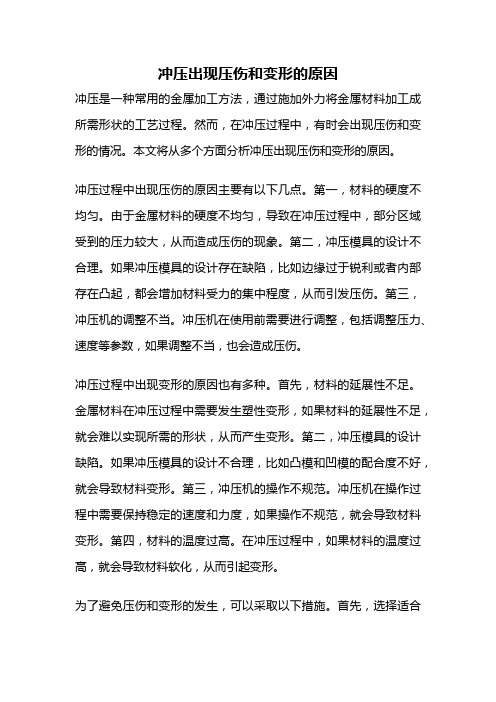
冲压出现压伤和变形的原因冲压是一种常用的金属加工方法,通过施加外力将金属材料加工成所需形状的工艺过程。
然而,在冲压过程中,有时会出现压伤和变形的情况。
本文将从多个方面分析冲压出现压伤和变形的原因。
冲压过程中出现压伤的原因主要有以下几点。
第一,材料的硬度不均匀。
由于金属材料的硬度不均匀,导致在冲压过程中,部分区域受到的压力较大,从而造成压伤的现象。
第二,冲压模具的设计不合理。
如果冲压模具的设计存在缺陷,比如边缘过于锐利或者内部存在凸起,都会增加材料受力的集中程度,从而引发压伤。
第三,冲压机的调整不当。
冲压机在使用前需要进行调整,包括调整压力、速度等参数,如果调整不当,也会造成压伤。
冲压过程中出现变形的原因也有多种。
首先,材料的延展性不足。
金属材料在冲压过程中需要发生塑性变形,如果材料的延展性不足,就会难以实现所需的形状,从而产生变形。
第二,冲压模具的设计缺陷。
如果冲压模具的设计不合理,比如凸模和凹模的配合度不好,就会导致材料变形。
第三,冲压机的操作不规范。
冲压机在操作过程中需要保持稳定的速度和力度,如果操作不规范,就会导致材料变形。
第四,材料的温度过高。
在冲压过程中,如果材料的温度过高,就会导致材料软化,从而引起变形。
为了避免压伤和变形的发生,可以采取以下措施。
首先,选择适合的材料。
在冲压过程中,应根据具体情况选择硬度均匀、延展性好的金属材料,以保证冲压过程的稳定性。
其次,合理设计冲压模具。
冲压模具的设计应考虑到材料的变形特性,减少材料的受力集中度,从而降低压伤和变形的风险。
再次,进行合适的冲压机调整。
在使用冲压机前,应对机器进行适当的调整,包括调整压力、速度等参数,以确保冲压过程的稳定性。
最后,控制材料的温度。
在冲压过程中,应控制好材料的温度,避免过高的温度导致材料软化,从而引起变形。
冲压出现压伤和变形的原因有很多,包括材料的硬度不均匀、冲压模具的设计不合理、冲压机的调整不当、材料的延展性不足等。
冲压变形基本原理

﹡改变坯料局部区域的温度
《冲压工艺及模具设计》
第1章 冲压变形的基本原理
《冲压工艺及模具设计》
第1章 冲压变形的基本原理
《冲压工艺及模具设计》
第1章 冲压变形的基本原理
A-变形区;B-传力区;C-已变形区 图1.3.3 变形趋向性对冲压工艺的影响
《冲压工艺及模具设计》
1.4 板料冲压成形性能及冲压材料
2.变形抗力及其指标 金属产生塑性变形的力为变形力,金属抵抗变形的力称为 变形抗力。通常以真实应力作为变形抗力的指标。 《冲压工艺及模具设计》
H0 HK 镦粗率: c 100% H0
第1章 冲压变形的基本原理
1.1.4影响金属的塑性与变形抗力的因素
1.影响塑性的因素 内因 :化学成分的影响;组织结构的影响 外因:变形温度 ;变形速度 ;变形的应力状态 2.影响金属变形抗力的主要因素 1)化学成分及组织的影响 2)变形温度对变形抗力的影响(如图1.1.3) 3)变形速度对变形抗力的影响 4)变形程度对变形抗力的影响 5)应力状态对变形抗力的影响
第1章 冲压变形的基本原理
1.2.1 点的应力与应变状态
1.应力:内力的强度,用σ表示。 2.点的应力状态(如图1.2.1) 3.应变:微小六面体的变形,用ε表示。
主应变
1 2 3
4.点的应变状态 空间一点无论受多少个力,都可简化为九个应力分量。在 静力平衡时,根据剪应力互等定理,可简化为六个应力分量。 主平面:剪应力为零的平面。 主应力:主平面上的应力。 《冲压工艺及模具设计》
1.4.1 板料的冲压成形性能
冲压成形性能: 板料对各种冲压成形加工的适应能力. 抗破裂性、 贴模性、定形性
第1章 冲压变形的基本原理
冲床冲压力计算公式P

冲床冲压力计算公式P
冲压力=材料的屈服强度×冲裁面积
弹性变形冲压力计算公式是根据材料的屈服强度和冲裁面积得出的。
屈服强度是指材料开始发生塑性变形的应力,它可以通过材料的拉伸试验得到。
冲裁面积是指材料通过模具冲压过程中受到变形的面积。
冲压力=液压缸的推力
液压冲压力计算公式是根据液压冲床的工作原理得出的。
液压冲床通过液压缸向下施加推力,使模具对薄板金属进行冲压。
液压冲压力计算公式简单明确,直接取决于液压冲床的设定参数。
冲压力=∑(材料的屈服强度×冲裁面积×冲裁点数)
材料弹性限制力计算公式是考虑到冲裁点数多于一个时,各个冲裁点的力量相互作用的情况。
在多点冲裁过程中,不同冲裁点受到冲裁过程中其他点力的影响,会使得冲压力有所变化。
冲压力=∑(材料的屈服强度×冲裁面积×冲裁点数×可变形因子)
极限变形力计算公式是在材料弹性限制力的基础上,考虑了可变形因子对冲压力的影响。
可变形因子是指材料在冲压过程中的变形程度,它是通过对薄板金属的实际冲压试验得到的。
以上是冲床冲压力计算公式的一些基本原理和公式。
在实际应用时,还需要考虑到冲床机械的机械性能、模具的设计和材料的选择等因素,以获得准确的冲压力计算结果。
冲压件的变形与塑性形变分析
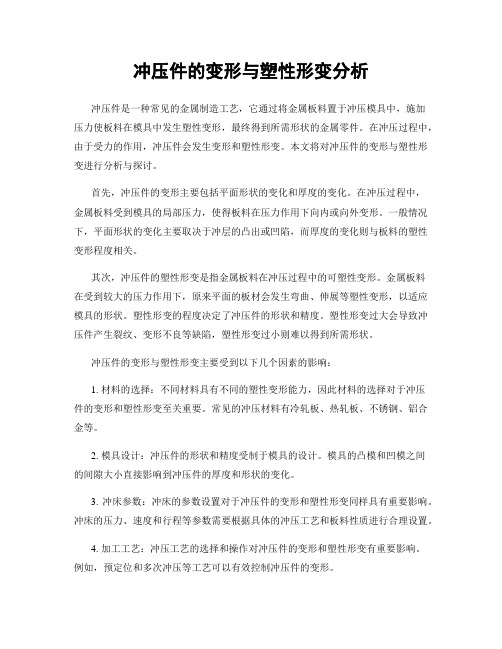
冲压件的变形与塑性形变分析冲压件是一种常见的金属制造工艺,它通过将金属板料置于冲压模具中,施加压力使板料在模具中发生塑性变形,最终得到所需形状的金属零件。
在冲压过程中,由于受力的作用,冲压件会发生变形和塑性形变。
本文将对冲压件的变形与塑性形变进行分析与探讨。
首先,冲压件的变形主要包括平面形状的变化和厚度的变化。
在冲压过程中,金属板料受到模具的局部压力,使得板料在压力作用下向内或向外变形。
一般情况下,平面形状的变化主要取决于冲层的凸出或凹陷,而厚度的变化则与板料的塑性变形程度相关。
其次,冲压件的塑性形变是指金属板料在冲压过程中的可塑性变形。
金属板料在受到较大的压力作用下,原来平面的板材会发生弯曲、伸展等塑性变形,以适应模具的形状。
塑性形变的程度决定了冲压件的形状和精度。
塑性形变过大会导致冲压件产生裂纹、变形不良等缺陷,塑性形变过小则难以得到所需形状。
冲压件的变形与塑性形变主要受到以下几个因素的影响:1. 材料的选择:不同材料具有不同的塑性变形能力,因此材料的选择对于冲压件的变形和塑性形变至关重要。
常见的冲压材料有冷轧板、热轧板、不锈钢、铝合金等。
2. 模具设计:冲压件的形状和精度受制于模具的设计。
模具的凸模和凹模之间的间隙大小直接影响到冲压件的厚度和形状的变化。
3. 冲床参数:冲床的参数设置对于冲压件的变形和塑性形变同样具有重要影响。
冲床的压力、速度和行程等参数需要根据具体的冲压工艺和板料性质进行合理设置。
4. 加工工艺:冲压工艺的选择和操作对冲压件的变形和塑性形变有重要影响。
例如,预定位和多次冲压等工艺可以有效控制冲压件的变形。
冲压件的变形与塑性形变分析对于冲压工艺的优化和产品质量的提高至关重要。
通过分析不同因素对变形和塑性形变的影响,可以制定合理的工艺参数和优化模具设计,从而减少冲压件的变形和缺陷率,提高冲压件的成品率和品质。
在实际工程应用中,变形与塑性形变分析可以通过有限元模拟等数值模拟方法进行。
冲压成形工艺的工件变形分析

冲压成形工艺的工件变形分析冲压成形工艺是一种常见的金属成形工艺,广泛应用于汽车、电子、航空等各个领域。
在冲压成形过程中,金属材料受到外力的作用,在模具的约束下发生塑性变形,从而得到所需形状的工件。
然而,在实际应用中,冲压过程中的工件变形问题经常会引起生产线上的不一致性和市场质量问题。
因此,对冲压成形工艺的工件变形进行分析和优化对于提高产品质量和生产效率具有重要意义。
首先,冲压成形工艺的工件变形受到材料的性能特点和模具的约束力的影响。
金属材料的应力—应变特性决定了其在冲压过程中的变形行为。
对于常见的冷轧、热轧金属材料来说,其应力—应变曲线呈现出线性和非线性两个阶段。
在线性阶段,应力与应变呈线性关系,材料的弹性变形起主导作用;而在非线性阶段,应力增加速度减缓,材料开始发生塑性变形。
与此同时,模具的约束力也是影响工件变形的重要因素。
模具的强度、形状和尺寸等参数会直接影响到工件的变形程度和成形质量。
因此,在工艺设计中,需要充分考虑材料的物理特性和模具的设计要求,以保证工件成形的一致性和稳定性。
其次,冲压成形工艺中的工件变形分析需要考虑到材料的应力状态和应变分布。
在冲压过程中,材料受到外力作用,内部会产生应力和应变。
应力和应变的分布情况直接决定了工件的变形形态。
通过数值计算、有限元分析等手段可以模拟和预测工件变形过程中的应力和应变状态,从而得到工件的变形特点和成形结果。
同时,工件的变形也会受到材料的流变性质的影响。
金属材料的流变曲线可以表征其在冲压过程中的塑性变形特性,通过对材料的性能参数进行测试和分析,可以更加准确地掌握工件变形的规律。
最后,冲压成形工艺的工件变形分析还需要考虑到工艺参数的优化和控制。
在冲压成形工艺中,包括冲头速度、冲头力度、冲凸模间隙等参数的设置都会对工件变形产生影响。
合理设置这些参数可以控制工件的变形程度和形状,进而提高产品的质量和生产效率。
例如,调节冲头速度可以改变金属材料的形变速率,从而影响工件的塑性变形和回弹量。
冲压类外文翻译、中英文翻译--冲压变形
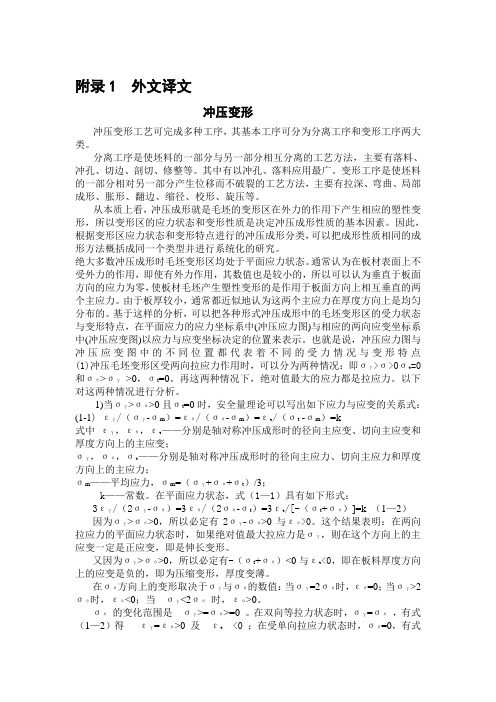
附录1 外文译文冲压变形冲压变形工艺可完成多种工序,其基本工序可分为分离工序和变形工序两大类。
分离工序是使坯料的一部分与另一部分相互分离的工艺方法,主要有落料、冲孔、切边、剖切、修整等。
其中有以冲孔、落料应用最广。
变形工序是使坯料的一部分相对另一部分产生位移而不破裂的工艺方法,主要有拉深、弯曲、局部成形、胀形、翻边、缩径、校形、旋压等。
从本质上看,冲压成形就是毛坯的变形区在外力的作用下产生相应的塑性变形,所以变形区的应力状态和变形性质是决定冲压成形性质的基本因素。
因此,根据变形区应力状态和变形特点进行的冲压成形分类,可以把成形性质相同的成形方法概括成同一个类型并进行系统化的研究。
绝大多数冲压成形时毛坯变形区均处于平面应力状态。
通常认为在板材表面上不受外力的作用,即使有外力作用,其数值也是较小的,所以可以认为垂直于板面方向的应力为零,使板材毛坯产生塑性变形的是作用于板面方向上相互垂直的两个主应力。
由于板厚较小,通常都近似地认为这两个主应力在厚度方向上是均匀分布的。
基于这样的分析,可以把各种形式冲压成形中的毛坯变形区的受力状态与变形特点,在平面应力的应力坐标系中(冲压应力图)与相应的两向应变坐标系中(冲压应变图)以应力与应变坐标决定的位置来表示。
也就是说,冲压应力图与冲压应变图中的不同位置都代表着不同的受力情况与变形特点(1)冲压毛坯变形区受两向拉应力作用时,可以分为两种情况:即σγ>σ>0σt=0和σθ>σγ>0,σt=0。
再这两种情况下,绝对值最大的应力都是拉应力。
以下对这两种情况进行分析。
1)当σγ>σθ>0且σt=0时,安全量理论可以写出如下应力与应变的关系式:(1-1) εγ/(σγ-σm)=εθ/(σθ-σm)=εt/(σt -σm)=k式中εγ,εθ,εt——分别是轴对称冲压成形时的径向主应变、切向主应变和厚度方向上的主应变;σγ,σθ,σt——分别是轴对称冲压成形时的径向主应力、切向主应力和厚度方向上的主应力;σm——平均应力,σm=(σγ+σθ+σt)/3;k——常数。
冲压成形的特点与基本规律
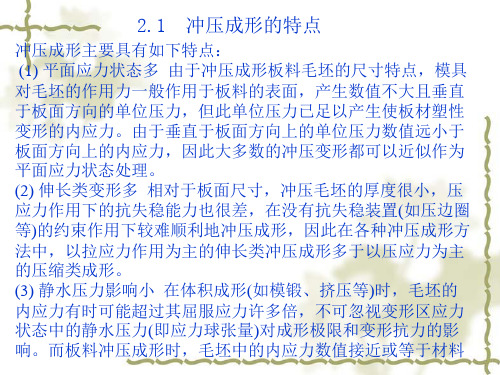
又因2r 0,由式(2.2)一定有 r 0 即在压应力的方向上的应变是负的,是压缩变形。。
由于r ,0,当 r 时,r 0 ;单向压应力状态( r 0
)时,有r / 2 0。 这种应力和变形状态处于冲压应力图中的AOB 范围(见图2.2), 在冲压变形图中处于COD范围(见图2.3)。
又因 r 0 ,则 (r ) 0 ,所以必定有t 0 ,即在板厚 方向上的应变是正的,板料增厚。 在 方向上的变形决定于 r和 的数值;当 2r时, 0 当 2 r时, 0 ;当 2 r时, 0。
双向等压应力状态( r 0 )时,有r 0;单向压应力状
t 0 和 r 0 , t 0。
1. r 0, t 0 时的应力状态
当 r 0 , t 0 按全量理论可以写出如下应力与应变的关
系
r t k
r m m t m
(2.1)
式中:r , ,t ——分别是轴对称冲压成形时的经向、纬向
和厚度方向上的主应变;
与厚度 方r ,向 上,的 t主—应—力分;别是轴对称冲压成形时的经向、纬向 m ——平均应力,m (r t ) / 3 。
4. r 0, 0 ,r 时的应力状态 当 r 0, 0,r 时,由式(2.2)可知2r 0 ,所以一定 有 r 0 。这表明,在异号应力作用的平面应力状态时,如果
绝对值最大的应力是拉应力,则在这个绝对值最大的压应力
方向上的应变是正的,即为伸长变形。 又因2 r 0 ,由式(2.2)一定有 0 即在压应力的方向上的应变是负的,是压缩变形。
冲压成形过程是不断变化的连续过程,各个区域之间可以
相互转化。
对变形区与不变形区的判断 :如果毛坯中某部分内任意两
冲压模具设计(1-3)
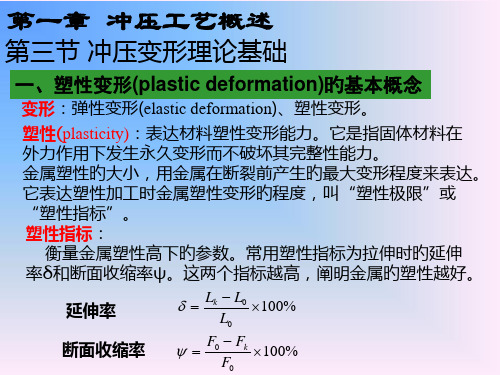
• 有对色优金质属碳:素铜结及构其合薄金钢、板铝及,其国合家金、原镁则合规金、定钛,合钢金等。 非板金旳属表材面料质:量纸可板分、胶为木Ⅰ板(、特塑别料高板、级纤旳维精板和整云表母面等。 ),Ⅱ(高级旳精整表面),Ⅲ(较高旳精整表面
成形质量
材料旳冲压性能好是指便于冲压加工,详细而言指: 成形极限高(成形过程中材料能到达旳最大变形程度,即抗破裂性好)
成形质量好(形状尺寸精度,厚度变化,表面质量以及成形后旳物理机械性能, 即贴模性、定形性好)
第一章 冲压工艺概述
直接反应,但需 专业设备或工装
第三节 冲压变形理论基础
五、冲压材料及其冲压成形性能(续) 以便,易行
例如: 室温下奥氏体不锈钢旳塑性很好,能经受很大旳
变形而不破坏,但它旳变形抗力却非常大;
过热和过烧旳金属与合金,其塑性很小,甚至完 全失去塑性变形旳能力,而变形抗力也很小;
室温下旳铅,塑性很高而变形抗力又小。
变形抗力:
使金属产生塑性变形旳力为变形力,金属抵 抗变形旳力称为变形抗力。
塑性与变形抗力是两个不同旳概念:
第一章 冲压工艺概述
第三节 冲压变形理论基础
三、塑性力学基础(续)
3.金属塑性变形时旳应力应变关系(续) 几点讨论结论
(1)应力分量与应变分量符号不一定一致, 即拉应力不一定 相应拉应变,压应力不一定相应压应变;举例。 (2)某方向应力为零其应变不一定为零; (3)在任何一种应力状态下,应力分量旳大小与应变分量旳 大小顺序是相相应旳,即б1>б2>б3,则有ε1>ε2>ε3。 (4)若有两个应力分量相等, 则相应旳应变分量也相等,即 若б1=б2,则有ε1=ε2。
第一章 冲压变形的基本原理

冲压工艺与模具设计
图1.2.1 一点的应力状态
(a)受力物体 (b)任意坐标系(c) 主轴坐标系
冲压工艺与模具设计
1.2.4 屈服准则的几何表示 (a)平面上两屈服准则表达 (b) 主应力空间两屈服准则表达
冲压工艺与模具设计
图1.2.5 单向拉应力-应变曲线
冲压工艺与模具设计
图1.2.6 实际应力曲线与假象应力曲线
冲压工艺与模具设计
1.2 塑性变形的力学基础
外力
内力
模具
毛坯
零件
毛坯的变形都是模具对毛坯施加外力所引起内力或由
内力直接作用的结果。应力就是毛坯内单位面积上作用的
内力。应力应理解为一极小面积上的内力与该面积比值的
极限,即:
lim P dP
F0 F dF
冲压工艺与模具设计
1.2.1 一点的应力与应变状态 1.一点的应力状态:
冲压工艺与模具设计
1.2.3 塑性变形时应力与应变的关系 物体受力产生变形, 所以应力与应变之间一定
存在着某种关系。 弹性变形时, 应 力E与应变之间的关系是线性的、
可逆的, 变形是可以恢复的。 (胡克定律 )
单向拉伸应力-应变曲线(如图1.2.5)
冲压工艺与模具设计
1.2.3 塑性变形时应力与应变的关系 增量理论 : 瞬间的应变增量与相应应力的关系
1.屈雷斯加(H·Tresca)屈服准则
力屈达雷到斯某加一于定1m值a8x 6时412 ,(年 m材提ax 料出 mi即n:) 当行K材屈料服中。的因最此大,剪该应准 则又称为最大剪应力屈服准则。其数学表达式为:
冲压工艺与模具设计
1.2.2 屈服准则(塑性条件) 2. 密席斯(Von Mises)屈服准则 密席斯于1913年提出了另一屈服准则: 当材料