Update-on-PDA-TR22-Revisions-for-Aseptic-Process-Simulations
TAP-213系列产品的固件更新说明书
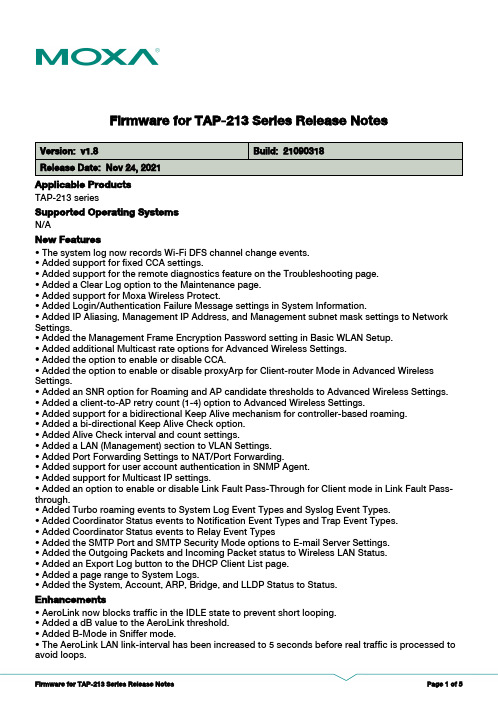
Firmware for TAP-213 Series Release NotesSupported Operating SystemsApplicable Products• AeroLink now blocks traffic in the IDLE state to prevent short looping.• Added a dB value to the AeroLink threshold.• Added B-Mode in Sniffer mode.• The AeroLink LAN link-interval has been increased to 5 seconds before real traffic is processed to avoid loops.EnhancementsN/ATAP-213 series• The system log now records Wi-Fi DFS channel change events.• Added support for fixed CCA settings.• Added support for the remote diagnostics feature on the Troubleshooting page.• Added a Clear Log option to the Maintenance page.• Added support for Moxa Wireless Protect.• Added Login/Authentication Failure Message settings in System Information.• Added IP Aliasing, Management IP Address, and Management subnet mask settings to Network Settings.• Added the Management Frame Encryption Password setting in Basic WLAN Setup.• Added additional Multicast rate options for Advanced Wireless Settings.• Added the option to enable or disable CCA.• Added the option to enable or disable proxyArp for Client-router Mode in Advanced Wireless Settings.• Added an SNR option for Roaming and AP candidate thresholds to Advanced Wireless Settings.• Added a client-to-AP retry count (1-4) option to Advanced Wireless Settings.• Added support for a bidirectional Keep Alive mechanism for controller-based roaming.• Added a bi-directional Keep Alive Check option.• Added Alive Check interval and count settings.• Added a LAN (Management) section to VLAN Settings.• Added Port Forwarding Settings to NAT/Port Forwarding.• Added support for user account authentication in SNMP Agent.• Added support for Multicast IP settings.• Added an option to enable or disable Link Fault Pass-Through for Client mode in Link Fault Pass-through.• Added Turbo roaming events to System Log Event Types and Syslog Event Types.• Added Coordinator Status events to Notification Event Types and Trap Event Types.• Added Coordinator Status events to Relay Event Types • Added the SMTP Port and SMTP Security Mode options to E-mail Server Settings.• Added the Outgoing Packets and Incoming Packet status to Wireless LAN Status.• Added an Export Log button to the DHCP Client List page.• Added a page range to System Logs.• Added the System, Account, ARP, Bridge, and LLDP Status to Status.New FeaturesBugs Fixed• Added a null SSID check.• Added auto/manual refresh on the RSTP status page.• Adjusted the accuracy of the transmission (tx) rate to the second decimal.• Increased the number of Port Forwarding rule entries from 16 to 32.• Increased the number of MAC Filter, IP Protocol Filter, and TCP/UDP Port Filter entries from 8 to 32.• Cybersecurity enhancements.• Enhanced the group check logic for WLAN, 50 ms roaming, security mode, and WAC settings.• Network information (including IP, subnet mask, and gateway) has been added to the “Reboot” and “Save Configuration and Restart” pages to show the expected network settings after performing these tasks.• Added support for individual policies for MAC Filter, IP protocol Filter, and TCP/UDP Port Filter rule entries.• Added an ARP filter option for IP Protocol Filter entries.• Wireless clients are sometimes unable to connect to the AP during startup.• Wireless clients time out during authentication if using WEP encryption,• Setting a null configuration triggers a false configuration change.• The power saving status of wireless clients is not handled correctly by the AP during roaming.• Changing IP address settings does not trigger the system to restart.• Some tx power values for N mode are inaccurate.• AeroLink sometimes reinitializes unexpectedly.• Failed SSH login does not trigger an event log.• No response when using the Wireless Search Utility to configure IP settings.• RSSI report handoff messages are in an incorrect format.• Web browsers will redirect users to a wrong address If changes to IP settings are not saved.• The DHCP maximum numbers of users setting is not applied correctly.• The order of txpower settings is incorrect.• The DHCP status would appear incorrect in the Wireless Search utility.• The rate tables for A/G are incorrect.• SNMP does not return a “N/A” response if certain wireless status parameters values are blank.• Wireless clients are unable to reauthorize after being disconnected in enterprise mode during controller-based roaming.• The device may reboot automatically while upgrading the firmware.• Wireless clients do not leave an AP after receiving a DEAUTH message.• The system log cannot be exported when using the Firefox browser.• The name of the wlanSignal SNMP node is incorrect.• Language errors on the Turbo Chain status page.• ARP Request messages in Client-mode are in an incorrect format.NotesChanges• Changed the default device name to “Model name_xx:yy:zz”, where xx:yy:zz are the last 3 bytes of the device’s MAC address.• Changed the RF type default value from “B/G/N Mixed” to “2.4G N”.• Changed the Wireless default state on the Operation Mode page from “enabled” to “disabled”.• Changed the default value of the Client lease time for the DHCP server from 5 days to 14400 min.• Changed the default state of HTTP and Telnet on the Console Settings page from “enabled” to “disabled“.• Renamed “Multicast rate” to “Multicast and broadcast rate” in the web interface.• Removed the ability to press Enter to trigger the ping function.N/ASupported Operating SystemsNotesChangesApplicable ProductsBugs FixedN/A• KRACK (Key Reinstallation Attack) WPA2, [CVE-2017-13077]: Issue Descriptions: Wi-Fi Protected Access (WPA and WPA2) allows reinstallation of the Pairwise Transient Key (PTK) and Temporal Key (TK) during the four-way handshake, allowing an attacker within radio range to replay, decrypt, or spoof frames.• KRACK (Key Reinstallation Attack) WPA2, [CVE-2017-13078]: Issue Descriptions: Wi-Fi Protected Access (WPA and WPA2) allows reinstallation of the Group Temporal Key (GTK) during the four-way handshake, allowing an attacker within radio range to replay frames from access points to clients.• KRACK (Key Reinstallation Attack) WPA2, [CVE-2017-13080]: Issue Descriptions: Wi-Fi Protected Access (WPA and WPA2) allows reinstallation of the Group Temporal Key (GTK) during the group key handshake, allowing an attacker within radio range to replay frames from access points to clients.EnhancementsN/ATAP-213-EU-CT-T, TAP-213-JP-CT-T, TAP-213-US-CT-TN/ANew FeaturesN/AN/ASupported Operating SystemsNotesChangesApplicable ProductsBugs FixedN/AN/AEnhancementsN/ATAP-213-EU-CT-T, TAP-213-JP-CT-T, TAP-213-US-CT-T • First release.New FeaturesN/AN/A。
oracle常用维护命令和技巧

常用维护命令与技巧目录操作系统命令 (3)通用操作系统命令 (3)LINUX (3)AIX (4)HPUX (6)Solaris (10)Oracle组件选项命令 (12)CRS (12)ASM (13)配置使用logminer (13)Oracle常用SQL语句 (16)SGA (16)UNDO管理 (16)dba_segments 和 dba_extents (17)查找LOB字段的信息 (18)Index (18)expdp impdp (18)怎么发现transaction table 竞争 (18)查找非缺省的参数(Non default parameter) (18)Determining Which Segments Have Many Buffers in the Pool (18)查询所有的PGA的大小 (19)CURSOR (19)compact Table space (19)Session (20)tablespace (20)ADDM (20)等待事件(wait event) (21)查询当前正在运行的SQL语句(current sql_text) (21)session sid and process sid (22)设置初始化参数 (22)操作系统命令通用操作系统命令DUMP磁盘的头部信息dd if=/dev/rhdisk28 bs=8192|od –c怎么使用truss或则trace查看运行脚本的输出:sh –x < program >debug我们要执行的程序或者命令:truss -o /tmp/mytruss <program> <any arguments>或者trace -o /tmp/mytruss <program> <any arguments> debug 子进程:truss -o /tmp/mytruss -fae <program> <any arguments> debug 一个已经运行了的进程:truss -o /tmp/mytruss -p <pid of process>或者trace -o /tmp/mytruss -p <pid of process>debug 一个已经运行了的进程的子进程truss -o /tmp/mytruss -fae -p <pid of process> LINUX检查机器内存的大小:# grep MemTotal /proc/meminfo检查机器SWAP的大小# grep SwapTotal /proc/meminfo检查可用的内存和SWAP大小# free检查可用的共享内存大小# df -k /dev/shm/检查系统的结构uname –m确定linux属于哪个厂商的那个版本# cat /proc/version确定Linux的核心# uname –r查询安装了的包# rpm -q <package_name>检查网络的流量/usr/bin/sar –n DEVAIX检查机器内存的大小:# /usr/sbin/lsattr -E -l sys0 -a realmem#svmon –G --检查内存使用情况#svmon -P -t 10 //查看最耗内存的10个进程,里面会有每个进程的详细信息。
Viavi OneAdvisor ONA-800 软件更新指南说明书

Viavi OneAdvisor ONA-800Software Update InstructionsMay 1, 2020Table of ContentsScope (2)work Upgrade (2)2. USB Upgrade (8)3. Stratasync Upgrade (13)ScopeThe ONA-800 platform base software includes software for the ONA-800 base and all supported modules. There are three methods to update ONA-800 software:work upgrade - Use this method to update your ONA-800 via an Internet connection.B upgrade - Use this method to update your ONA-800 with a USB thumb drive.3.StrataSync upgrade - Use this method if your ONA-800 is managed using Viavi’s StrataSync AssetManagement system and your company has elected to deploy software via this method.The ONA must be connected to AC Power, regardless of update method. Please note that network upgrades are NOT supported over WiFi.work UpgradeStep Action Details1.Power On Press and release the ON/OFF button to turn on the ONA-800.2.AC Power Connect the AC power adapter to thepower connector on the top of the mainframe.N Connection Connect the Ethernet ManagementPort, on the top of the mainframe,to a network connection with internetaccess, using CAT 5E or better cable.4.System Press the System icon, , at the left of the HOME screen, to display theSystem Menu.work Settings Press the Network icon,, to display LAN Settings. Set IP Mode to“DHCP” for automatic IP address assignment or “Static” for manual input.If using a static address, be sure to configure the DNS server for an accurateaddress or the upgrade will fail to locate the upgrade server.the System Menu.6. Upgrade Press the Upgrade icon,, to display upgrade methods.settings. Press Reset to Default to ensure the server address name is correct.8.Connect Press to showthe upgrade versions available at .9.Start UpgradePress , and pressto initiate the upgrade.B UpgradeStep Action Details Using an internet browser on your PC or laptop, go to /2.ONA-800 Click on theto display the OneAdvisor ONA-800 upgrade page.3.Download Click on the icon for the desired server to start the download from that server.There are icons for three servers: EMEA, NORTH AMERICA or APACserver. For example, North America . Click to downloadthe current software revision from that server, if prompted. Do NOT save thedownload directly to the USB stick. Save to your PC and wait for thedownload to complete.B Stick Insert a USB thumb drive into the USB port on your PC or laptop.5.Extract Open and run the downloaded file, enter the path of the USB stick, and pressto extract files.6.Eject Once the extract has completed, safely eject the USB drive from your PC orLaptop.7.Power on ONA Press and release the ON/OFF button to turn on the ONA-800.8.AC Power Connect the AC power adapter to the power connector on the top of theONA-800 mainframe.B Connect the USB Thumb Drive to one of the USB ports on the ONA-800mainframe. An 8GB or smaller drive is recommended.10.System Press the System icon, , at the left of the HOME screen, to display theSystem Menu.11. Upgrade Press the Upgrade icon,, to display upgrade methods.12.Select USB Press to display upgrade versionsavailable on the USB stick.13.Start Upgrade Press . Press to initiate the upgrade.3.StrataSyncStep Action Details1.Power On Press and release the ON/OFF button to turn on the ONA-800.2.AC Power Connect the AC power adapter to thepower connector on the top of the ONA-800.N Connection Connect the Ethernet ManagementPort on the top of ONA-800to a network connection with internetaccess, using CAT 5E or better cable.4.System Press the System icon, , at the left of the HOME screen, to display theSystem Menu.work Settings Press the Network icon,, to display LAN Settings. Set IP Mode to“DHCP”for automatic IP address assignment or “Static” for manual input.If configuring a static address, be sure to include an accurate DNS address orthe unit will fail to locate the Stratasync server.After configuring LAN settings, press the System icon, , to redisplay the System Menu.6.StrataSync Press the StrataSync icon,, to display StrataSync Settings. Ensurethat Account ID and Technician ID match those of your StrataSync account.7.Sync Press to sync your ONA-800 and initiate upgrades that have beenassigned by your company’s StrataSync Administrator.。
Covaris E220 DNA Shearing Quick Guide

Quick Guide:This Quick Guide provides DNA Shearing protocols when using microTUBE-130, microTUBE-50, microTUBE-15, microTUBE-500, or miniTUBE and a Covaris E220 Focused-ultrasonicator.Revision History010308 K 1/17 Format Changes; Addition of microTUBE-500 AFA Fiber Screw-Capprotocols; update ‘Additional Accessories’; update Appendix B 010308 L 2/17 Changes to 8 microTUBE-50 Strip V2 protocols; addition of 8 microTUBE-15AFA Beads H Slit Strip V2 and 8 microTUBE-50 AFA Fiber H Slit Strip V2010308 M 5/17 Addition of 96 microTUBE-50 AFA Fiber Plate Thin Foil (PN 520232) and 130ul 96 microTUBE AFA Fiber Plate Thin Foil (PN 520230)010308 N 7/17 Add the names of the well plates definition for 520230 & 520232. Changedyear for Rev M Date.Values mentioned in this Quick Guide are nominal values. The tolerances are as follows: -Temperature +/-2°C-Sample volumeo microTUBE-15: from 15 to 20 µl, +/- 1 µlo microTUBE-50: 55 µl, +/- 2.5 µlo microTUBE Plate, Strip, Snap and Crimp Cap: 130 µl, +/- 5 µlo microTUBE-500: 500 µl, +/- 10 µl or 320 µl, +/- 10 µlo miniTUBE: 200 µl, +/- 10 µl-Water Level +/- 1Sample guidelines-DNA input: up to 5 µg purified DNA (1 µg for the microTUBE-15; minimum 320 ng for the microTUBE-500) -Buffer: Tris-EDTA, pH 8.0-DNA quality: Genomic DNA (> 10 kb). For lower quality DNA, Covaris recommends setting up a time dose response experiment for determining appropriate treatment times.-DO NOT use the microTUBE or miniTUBE for storage. Samples should be transferred after processing. Instrument setup-Refer to the instrument manual for complete setup.-microTUBE and miniTUBE have specific holders or racks associated with them.-E220 and E220 evolution may require the Intensifier (PN 500141). Refer to Appendix C for instructions.-E220 and E220 evolution may require Y-dithering. Refer to Appendix A for instructions.Instrument settings-Recommended settings are subject to change without notice.-Mean DNA fragment size distributions are based on electropherograms generated from the Agilent Bioanalyzer with the DNA 12000 Kit (cat# 5067-1509), with the exception of the 320 µl microTUBE-500 protocol (HighSensitivity DNA Kit, cat# 5067-4626). DNA fragment representation will vary with analytical systems, please carry out a time course experiment based on settings provided in this document to reach desired fragment sizedistribution.See /wp-content/uploads/pn_010308.pdf for updates to this document.130 µl sample volume - from 150 to 1,500 bpVessel microTUBEAFA FiberSnap-Cap(PN 520045)microTUBEAFA FiberCrimp-Cap(PN 520052)8 microTUBEStrip(PN 520053)96 microTUBEPlate(PN 520078)96 microTUBEAFA Fiber PlateThin Foil(PN 520230)Sample Volume 130 µlE220RacksRack 24 PlacemicroTUBESnap-Cap (PN500111)Rack 96 PlacemicroTUBECrimp-Cap(PN 500282)Rack 12 Place 8microTUBE Strip(PN 500191)No Rack needed Plate Definitions“500111 24microTUBEsnap +4mmoffset”“E220_500282Rack 96 PlacemicroTUBE-6mm offset”“E220_500191 8microTUBE stripPlate -6mmoffset”“E220_52007896 microTUBEPlate -6mmoffset”“E220_52023096 microTUBEPlate Thin Foil -6mm offset”Water Level 6Intensifier (PN 500141) YesY-dithering NoE220 evolutionRacks Rack E220e 8 Place microTUBECrimp and Snap Cap (PN 500433)Rack E220e 8microTUBE Strip(PN 500430)Non Compatible Plate Definitions“500433 E220e 8 microTUBECrimp and Snap Cap -3.7mmoffset”“500430 E220e 8microTUBE Strip-6mm offset”N/A Water Level 6Intensifier (PN 500141) YesY-dithering NoAllTemperature (°C) 7Target BP (Peak) 150 200 300 400 500 800 1,000 1,500 Peak Incident Power (W) 175 175 140 140 105 105 105 140 Duty Factor 10% 10% 10% 10% 5% 5% 5% 2% Cycles per Burst 200 200 200 200 200 200 200 200 Treatment Time (s) 430 180 80 55 80 50 40 15Vessel microTUBE-50Screw-Cap (PN 520166)8 microTUBE-50 AFA FiberStrip V2 (PN 520174)8 microTUBE-50 AFA Fiber HSlit Strip V2 (PN 520240)96 microTUBE-50AFA Fiber Plate(PN 520168)96 microTUBE-50AFA Fiber Plate ThinFoil (PN 520232) Sample Volume 55 µlE220RacksRack 24 PlacemicroTUBE Screw-Cap (PN 500308)Rack 12 Place 8 microTUBEStrip (PN 500444) No Rack needed Plate Definitions“E220_500308 Rack24 Place microTUBE-50 Screw-Cap+6.5mm offset”“E220_500444 Rack 12 Place 8microTUBE-50 Strip V2-10mm offset”“E220_520168 96microTUBE-50 Plate-10.5mm offset”“E220_520232 96microTUBE-50 PlateThin Foil -10.5mmoffset”E220evolutionRacksRack E220e 4 PlacemicroTUBE ScrewCap (PN 500432)Rack E220e 8 microTUBE StripV2 (PN 500437) Non Compatible Plate Definitions“500432 E220e 4microTUBE-50 ScrewCap -8.32mm offset”“500437 E220e 8 microTUBE-50 Strip V2 -10mm offset” N/AAllTemperature (°C) 7Water Level 6 -2 0 Intensifier (PN 500141) Yes Yes YesY-dithering No No Yes (0.5mm Y-dither at10mm/s) Target BP (Peak) 150 200 250 300 350 400 550Screw-CapPeak Incident Power(W) 100 75 75 75 75 75 30Duty Factor 30% 20% 20% 20% 20% 10% 10%Cycles per Burst 1000 1000 1000 1000 1000 1000 1000Treatment Time (s) 130 95 62 40 30 50 708-StripPeak Incident Power (W) 75 75 75 75 75 75 50Duty Factor 15% 15% 20% 20% 20% 10% 10%Cycles per Burst 500 500 1000 1000 1000 1000 1000Treatment Time (s) 360 155 75 45 35 52 50 PlatePeak Incident Power (W) 100 100 75 75 75 75 75Duty Factor 30% 30% 20% 20% 20% 10% 10%Cycles per Burst 1000 1000 1000 1000 1000 1000 1000Treatment Time (s) 145 90 70 49 34 50 32 The Y-dithering function is required for shearing with 96 microTUBE-50 plate (PN 520168). This function is only available on SonoLab versions 7.3 and up. Please see Appendix A for detailed instructions.Vessel microTUBE-15 AFA BeadsScrew-Cap (PN 520145)8 microTUBE-15 AFA BeadsStrip V2 (PN 520159)8 microTUBE-15 AFA BeadsH Slit Strip V2 (PN 520241)Sample Volume 15 µlE220Racks Rack 24 Place microTUBEScrew-Cap (PN 500308)Rack 12 Place 8 microTUBEStrip V2 (PN 500444) Plate Definitions“E220_500308 Rack 24 PlacemicroTUBE-15 Screw-Cap+15mm offset”“E220_500444 Rack 12 Place 8microTUBE-15 Strip V2 -1.5mmoffset”Water Level 10 6Intensifier (PN 500141) NoY-dithering NoE220evolutionRacks Rack E220e 4 Place microTUBEScrew Cap (PN 500432)Rack E220e 8 microTUBE StripV2 (PN 500437)Plate Definitions ”500432 E220e 4 microTUBE-15Screw Cap 0.18mm offset”“500437 E220e 8 microTUBE-15Strip V2 -1.58mm offset”Water Level 10 6Intensifier (PN 500141) NoY-dithering NoAllTemperature (°C) 20Target BP (Peak) 150 200 250 350 550Peak Incident Power (W) 18 18 18 18 18Duty Factor 20% 20% 20% 20% 20%Cycles per Burst 50 50 50 50 50Treatment Time (s) 300 120 80 45 22To ensure reproducible DNA shearing, it is required to centrifuge samples before processing DNA in amicroTUBE-15. Please see Appendix B for instructions.Please note that microTUBE-15 requires removal of the Intensifier (PN 500141) from the E220 focused-ultrasonicator. Please see Appendix C for instructions.200 µl sample - 2,000; 3,000 and 5,000 bpVesselminiTUBE Clear(PN 520064)Blue(PN 520065)Red(PN 520066) Sample Volume 200 µlE220Racks Rack 24 Place miniTUBE (PN 500205)Plate Definition “500205 24 miniTUBE +15mm offset”Water Level 11Intensifier (PN 500141) NoY-dithering NoE220evolutionRacks Rack E220e 4 Place miniTUBE (PN 500434)Plate definition “500434 E220e 4 miniTUBE 4.9mm offset”Water Level 11Intensifier (PN 500141) NoY-dithering NoAllTemperature (°C) 7 20 20 Target BP (Peak) 2,000 3,000 5,000miniTUBE Clear Blue RedPeak Incident Power (W) 3 3 25Duty Factor 20% 20% 20%Cycles per Burst 1000 1000 1000Treatment Time (s) 900 600 600Please note that miniTUBE requires removal of the Intensifier (PN 500141) from the E220 focused-ultrasonicator. Please see Appendix C for instructions.320 µl and 500 µl sample volume – from 150 to 600 bpVesselmicroTUBE-500 AFA Fiber Screw-Cap(PN 520185)Sample Volume320 µl 500 µlE220Rack Rack, 24 microTUBE-500 Screw-Cap (PN 500452)Plate Definition “E220_500452 Rack 24 Place microTUBE-500 Screw-Cap +6mmoffset” Water Level6 Intensifier (PN 500141)Yes Y-dithering NoE220 evolutionRackRack E220e 4 microTUBE-500 Screw-Cap (PN 500484) Plate Definition “500484 E220e 4 microTUBE-500 Screw-Cap -9.9mm offset”Water Level6 Intensifier (PN 500141)Yes Y-ditheringNo AllTemperature (°C)7Target BP (Peak)500 - 600150200350550Peak Incident Power (W) 75 175 175 175 175 Duty Factor 25% 20% 20% 20% 5% Cycles per Burst 200 200 200 200 200 Treatment Time (s)7540018055110To fragment DNA to sizes larger than 5 kb, Covaris offers the g-TUBE: a single-use device that shears genomic DNA into selected fragments sizes ranging from 6 kb to 20 kb. The only equipment needed is a compatible bench-top centrifuge.Additional AccessoriesPart Number Preparation stationsmicroTUBE Prep Station Snap & Screw Cap 500330 microTUBE-500 Screw-Cap Prep Station 500510 miniTUBE loading and unloading station 500207 8 microTUBE Strip Prep Station500327 Centrifuge and Heat Block microTUBE Screw-Cap Adapter Fits microTUBE Screw-Caps into bench top microcentrifuges500406 Centrifuge 8 microTUBE Strip V2 Adapter Fits the 8 microTUBE Strip into a Thermo Scientific TM mySPIN TM 12 mini centrifuge 500541 g-TUBEg-TUBEs (10) and prep station520079Appendix A – Using Y-dithering with SonoLab 7.3 and upA Y-dithering step is required for DNA shearing with the 96 microTUBE-50 Plate-This feature is only available on SonoLab versions 7.3 and up.-To obtain a copy of the SonoLab 7.3 and the Plate Definition installers, please employ the Registered Users Login on the Covaris website, -For any assistance in this process, please contact your local representative, or Covaris Global Technical Services at ***********************.Use the following steps to include Y-dithering in sample treatment1.Go into the Method Editor2.Select ‘Add Step’ and enter the treatment settings for the desired fragment sizea.Note: The following steps must be done for each individual treatment3.Select the Motion tab4.Enter the following values into the ‘X-Y Dithering Box’a.Y Dither (mm): 0.5b.X-Y Dither Speed (mm/sec): 10.0c.Both X Dither (mm) and X-Y Dwell (sec) should be set to 0Appendix B – microTUBE-15 centrifugation before DNA Shearing1.Sample loading and centrifugationmicroTUBE-15 AFA Beads Screw-CapLoad and centrifuge microTUBE-15 Screw-Cap as described before placing the tubes in the rack.If some of the sample splashes onto the wall of the microTUBE while removing from centrifuge or placing into rack, repeat centrifuge step. All liquid should be at the bottom of the microTUBE-15 before starting the AFA treatment.8 microTUBE-15 AFA Beads Strip V2The 8 microTUBE-15 AFA Beads Strip V2 will fit into the Covaris Centrifuge 8 microTUBE Strip V2 Adapter (PN 500541) for the Thermo Scientific TM mySPIN TM 12 mini centrifuge. Place the strip in the adapter and spin for a minimum of 1 minute.2.Sample processingUse settings provided in page 4.3.Sample recoveryRepeat the centrifuge step before recovering sample from microTUBE-15.Appendix C – Removing or Installing the Intensifier (Covaris PN 500141) from an E System The 500141 Intensifier is a small inverted stainless steel cone centered over the E Series transducer by four stainless wires. The wires are held by in a black plastic ring pressed into the transducer well.If an AFA protocol requires “no intensifier”, please remove the Intensifier, using the following steps:1.Empty the water bath. Start the E System and start the SonoLab software.2.Wait for the homing sequence to complete (the transducer will be lowered with the rack holder at it home position,allowing easy access to the Intensifier).3.Grasp opposite sides of plastic ring and gently pull the entire assembly out of the transducer well. Do not pull on the steelcone or the wires. The ring is a friction fit in the well – no hardware is used to hold it in place.The 500141 Intensifier (left) shown installed in the E System transducer well and (right) removed.Note the “UP” marking at the center of the Intensifier.If a protocol requires the Intensifier to be present, simply reverse this process:1.Align the black plastic ring with the perimeter of the transducer well. Note that the flat side of the center cone (marked UP)should be facing up (away from the transducer).2.Gently press each section of the ring into the well until the ring is seated uniformly in contact with the transducer, withapproximately 2 mm of the ring evenly exposed above the transducer assembly. Do not press on the cone or wires. The rotation of the ring relative to the transducer assembly is not important.3.Refill the tank. Degas and chill the water before proceeding.Technical Assistance•By telephone (+1 781 932 3959) during the hours of 9:00am to 5:00pm, Monday through Friday, United States Eastern Standard Time (EST) or Greenwich Mean Time (GMT) minus 05:00 hours•By e-mail at ***********************。
Exos AP-BV-1存储装置固件升级说明书
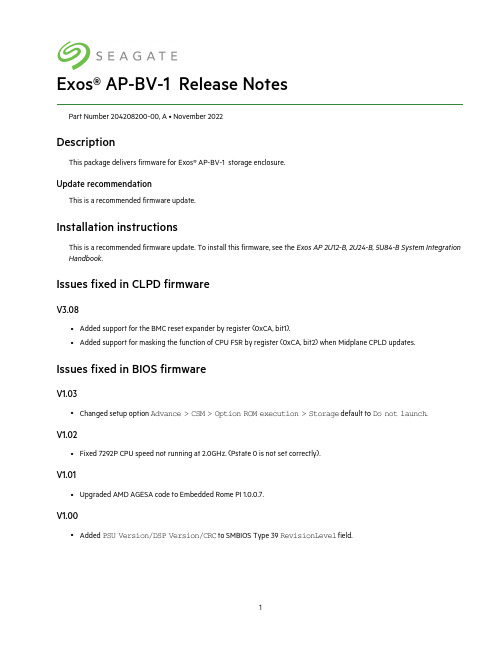
Exos®AP-BV-1Release NotesPart Number204208200-00,A•November2022DescriptionThis package delivers firmware for Exos®AP-BV-1storage enclosure.Update recommendationThis is a recommended firmware update.Installation instructionsThis is a recommended firmware update.To install this firmware,see the Exos AP2U12-B,2U24-B,5U84-B System Integration Handbook.Issues fixed in CLPD firmwareV3.08l Added support for the BMC reset expander by register(0xCA,bit1).l Added support for masking the function of CPU FSR by register(0xCA,bit2)when Midplane CPLD updates. Issues fixed in BIOS firmwareV1.03l Changed setup option Advance>CSM>Option ROM execution>Storage default to Do not launch.V1.02l Fixed7292P CPU speed not running at2.0GHz.(Pstate0is not set correctly).V1.01l Upgraded AMD AGESA code to Embedded Rome PI1.0.0.7.V1.00l Added PSU Version/DSP Version/CRC to SMBIOS Type39RevisionLevel field.l Fixed Redfish conformance test failure.V0.08l Fixed the issue where the virtual CD-ROM couldn’t be used in legacy mode.l Fixed the issue where BIOS v0.07couldn’t detect TPM.l Deleted the Redfish mapping ID IPMI800-IPMI812.V0.07l Fixed a hot swap issue where sometimes the IOM1has PCI PERR in sel log and PCI-e error in dmesg after IOM0hot removal followed by IOM0hot insertion.l Fixed an issue where,after successfully upgrading BIOS firmware,the system automatically rebooted with default boot priority but then hung at task Downloading NBP file.l Changed the NTB port(C0:03.1)register PCIE_CORR_ERR_MASK bit12REPLAY_TIMER_TIMEOUT_MASK from0to1.l Changed the default value of IPV6PXE support to disabled.l Removed UEFI:PXE IP4/IP6American Megatrends Inc.from boot order list.l Changed the default boot order settings.V0.06l Updated RTL8111UNDI driver to v2.056.l When the motherboard is Production Verification Test(PVT)(Mainboard ID=x02)or later,set the BIOS SPI bus to Quad mode.l Set FRB2timer default to Enabled.V0.05l Fixed and issue where the chassis information did not sync between Redfish command and dmidecode.l Changed SMBIOS type3and39information from MP(Midplane)and PSU FRU data.l Updated CRB version from5.14_AESRome_0ACPQ002to5.14_AESRome_0ACPQ003.l Hid BIOS setup item AMD PBS Options>RAS>CCIX GHES Corrected Err Notify Type.l Reduced the BIOS setting items.(Hid unused items and blank pages.)l Changed the default value of the BIOS setup item Secure Device Support Trusted Platform Module(TPM)to enable. Issues fixed in BMC firmwareV0.52l Fixed an issue where uninitialized fan data led to the IPMI stack being terminated.l Extended the IPMI OEM command(0x92)CPLD Refresh with additional options.l Changed the major version string of PCM MCU/DSP firmware from DEC to HEX in/redfish/v1/Chassis/Self/Power.l Changed AUX voltage sensors to monitor on standby.l Changed5U fan sensors to monitor on standby.V0.50l Updated the BIOS version by parsing the version string in the BIOS flash when finishing the update BIOS via BMC.l Re-arranged the entity IDs and entity instances for sensors and set some sensors to monitor on standby state.l Improved the PCM FW update flow.l Changed the minor version string of PCM MCU/DSP firmware from DEC to HEX in/redfish/v1/Chassis/Self/Power.V0.49l Fixed an issue with the single IOM mode judgment with IOM0(slot-0)that activates the FAULT LED.l Changed the minor version to have a leading zero of two digits for the FAN module.l Added IPMI OEM command to switch the BMC mode to secondary.l Added IPMI OEM command to switch the other BMC mode to slave.l Added IPMI OEM command to get PCM version.l Updated the IPMI OEM command usage of Check PCM update command.l Added failed message to Redfish task for PCM update.V0.48l Fixed wrong high bit value of SKU ID.(Netfn0x30,Cmd0x03).V0.47l Added support for Malibu Midplane CPLD firmware update.l Added IPMI OEM command to reset SAS controller(GEM)via CPLD.l Added IPMI OEM command to enable/disable NVDIMM support via CPLD.l Added IPMI OEM command to enable/disable NVDIMM support including another IOM which is based on the OEM command0x9B via IPMB.l Fixed premature reporting of PCM update where the response was reporting as a false-negative before the update was actually finished.l Added IPMI OEM command to preserve NVRAM area for BIOS update.l Added new parameter of PreserveNVRAM for the header of OemParameters when updating BIOS via Redfish /redfish/v1/UpdateService/upload.l Added a sensor of BMC_Covery with sensor type of2Bh(Version Change)with05h(invalid or unsupported firmware)to indicate that BMC secure boot check failed with recovery.l Set SSDP(Simple Service Discovery Protocol)disabled as default.l Fixed the Redfish@odate.id vpd instance from Fru to FruArea.l Added an OEM attribute of PsuStatus on/redfish/v1/Chassis/Self/Power to indicate a PSU alert which maps to CPLD register of C0h/C1h.l Added IPMI OEM command to reset Redfish server.l Added IPMI OEM command to reset Redis and Redfish server.l Changed IOM and OPS Fault LED behavior to support single and dual canister use cases.The determination of single or dual canister is based on another canister presence during BMC initialization.l Added initialization flash timeout for flash update.l Extend the zone mode value of the Set SAS Zone Mode command to00h-03h.l Changed the IPMI OEM command of Get Board ID command(03h)to support get SKU ID.l Added the OEM attribute of SkuId in/redfish/v1/Systems/Self and/redfish/v1/Managers/Self.V0.46l Added support for FLEX PSU PCM MCU and DSP firmware update.V0.45l Fixed an issue where two BMC images in shared memory might run out of space.Instead,only uploaded the BMC image to update BMC firmware,but did not copy another one for update.l Fixed an issue where NCSI kernel debug messages contiued to display when NCSI wasn't being used.V0.44l Fixed wrong EEPROM type of PCM VPD on2U.l Changed the PCM FW version string to have a leading zero for minor version of two digits.(Major version number has no leading zero.)l Added IPMI OEM command to get Midplane/PCM/FAN VPD CRC.l Added VPD CRC information,VpdCrc,in the corresponding Redfish VPD instance URL.l Displayed PCM DSP firmware information in/redfish/v1/Chassis/Self/Power.l Changed the threshold value of the PVDDQ_GH voltage sensor.l Corrected the sensor reading source(ADC channel)for PVDDQ_CD and PVDDQ_GH.V0.43l Fixed wrong default disabled VLAN.l Added IPMI OEM command to get GEM-related version from SES page07:Netfn0x30,Cmd0x2F.l Added support to preserve configuration with/UpdateService via Redfish.[Preserve configuration via/UpdateService] l Added IPMI OEM command to send command line to GEM console and receive the result.l Added Redfish API to read/write FRU binary data for FRU ID1-9.Note that the FRU ID0is not supported.l Added IPMI OEM command to get platform type command.V0.42l Added IPMI OEM command to get PSU/fan code version.l Support get Fan code version via/redfish/v1/Chassis/Self/Oem/FanInventor.Note:Only the primary BMC can get the fan version.l Removed unsupported SNMP trap version options v2and v3from the web management interface.l Fixed incorrect behavior of system power-on after using Redfish to update BIOS.V0.41l Redfish support midplane CPLD update.Update MP CPLD via/UpdateService/Actions/Oem/CPLDFWUpdate.l Support GEM Download Microcode of SES page0Eh via/redfish/v1/UpdateService/upload.l Enabled circular SEL for2U/5U platform.l Added task and audit log update status checking for PSMI FW Redfish update.V0.40l Restored the delay time between MDIO commands to prevent EEPROM data corrupted.l Moved the blocking MDIO operations in VLAN related commands(0x13and0x1F)to another task.l Added IPMI OEM command to get the progress of two VLAN related commands(0x13or0x1F).V0.39l Fixed Status Indicator not mapping to some failure conditions of SES page02.l Fixed VLAN initialization issue.l Remove unnecessary security mode configuration of port4.l Show flush EEPROM messages.l Added return value on MDIO read command and error handling for MDIO access failure.V0.38l Added secure boot feature.l Removed disable virtual device after post complete.l Changed total size of flash from0x8000000to0x4000000.l Enabled setting EncID at power off.l Added Actions/Drive.l Changed Reset to POWERControl for SAS drives in Redfish drive.l Changed the enum string(OK or Fail)of StatusIndicator to match Redfish drive schema.l Updated the StatusIndicator to include IN CRIT ARRAY,IN FAILED ARRAY,REBUILD/REMAP and R/R ABORT of SES page02h.l When updating BMC,BIOS,and IOM CPLD via Redfish,disable STONITH.l Changed behavior of IOM CPLD FW update.l Don't send refresh command to CPLD after finishing an IOM CPLD FW update.l Don't power on the system after finishing an IOM CPLD FW update.l Added a new OEM command(0x300x92)to send refresh command to refresh CPLD.l Upgraded IOM CPLD recovery FW version from v03.06to v03.07.l Changed NCSI configuration in bootloader when an add-in card was installed that didn't support NCSI.V0.37l When executing yafuflash update BMC/BIOS/CPLD,inform the other IOM to stop STONITH.l To restart STONITH after updating:l Start IOM-2STONITHl ipmitool-t0x32-b0x6raw0x300x980x0l Update IOM-1STONITHl ipmitool-t0x30-b0x6raw0x300x980x0l Upgraded IOM CPLD recovery FW version from v02.04to v03.06.l Added Other Module event to5U.l Disabled setting Enc ID by front panel button at system power off.V0.36l Disabled set fan to full speed when IOM is removed.l Disabled dual image feature.l Added Fan Present sensor for5U.l Fixed an issue where SEL did not keep records when unplugging FAN modules.V0.35l Redfish corrected URI typo for PSMIUpdate.l Redfish support IOM CPLD updated/UpdateService/Actions/Oem/CPLDFWUpdate.(Only support IOM CPLD updated via Redfish.)l Fixed issue where SEL did not keep records in time for unplugging FAN modules.l Fixed incorrect data type of PowerCapacityWatts for PowerSupplies(RTP).V0.34l Enabled BMC MAC0(NCSI)with dual image.l Removed unused OEM Redfish APIs.V0.33l Fixed an issue where the2U/5U fan speed sensor reading was incorrect after unplugging the fan module.l Configured NCSI from manual switch to auto fail over.l Enabled dual image feature.l Added workaround to prevent BMC reset which is caused by kernel null pointer exception during AC cycle stress test.l Fixed an issue where the CPLD update in the BMC WEB UI should be absent from the BMC web UI.l Fixed an issue where the SEL did not keep records in time for unplugging FAN modules.©2022Seagate Technology LLC or its affiliates.All rights reserved.Seagate,Seagate Technology,and the Spiral logo are registered trademarks of Seagate Technology LLC in the United States and/or other countries.Exos is either a trademark or a registered trademark of Seagate Technology LLC or one of its affiliated companies in the United States and/or other countries.All other trademarks or registered trademarks are the property of their respective owners.When referring to disk capacity,one gigabyte(GB)equals one billion bytes,one terabyte(TB)equals one trillion bytes,and one petabyte(PB)equals one thousand terabytes.Your computer's operating system may use a different standard of measurement and report a lower capacity.In addition,some of the listed capacity is used for formatting and other functions,and thus will not be available for data storage.Actual data rates may vary depending on operating environment and other factors,such as chosen interface and disk capacity.The export or re-export of Seagate hardware or software is regulated by the U.S.Department of Commerce, Bureau of Industry and Security(for more information,visit ),and may be controlled for export,import and use in other countries.All coded instruction and program statements contained herein remain copyrighted works and confidential proprietary and trade secret information of Seagate Technology LLC or its affiliates.Any use,derivation,disassembly,reverse engineering,dissemination,reproduction,or any attempt to modify,prepare derivative works, reproduce,distribute,disclose copyrighted material of Seagate Technology LLC,for any reason,in any manner,medium,or form,in whole or in part,if not expressly authorized,is strictly prohibited.Seagate reserves the right to change,without notice,product offerings or specifications.Regulatory and compliance informationFor the latest regulatory and compliance information see /support.Scroll down to the Compliance,Safety and Disposal Guide link.Open source third-party licenses and codeSeagate storage products use open source software components.To view information about open source software licenses and open source code used in Seagate storage products,see /support.。
AOC-TBT-DSL5320 用户手册说明书

USER GUIDE Revision 1.0aAOC-TBT-DSL5320User Guide: Revision 1.0aRelease Date: October 12, 2015Unless you request and receive written permission from Super Micro Computer, Inc., you may not copy any part of this document.Information in this document is subject to change without notice. Other products and companies referred to herein are trademarks or registered trademarks of their respective companies or mark holders.Copyright © 2015 by Super Micro Computer, Inc.All rights reserved. Printed in the United States of AmericaThe information in this user guide has been carefully reviewed and is believed to be accurate. The vendor assumes no responsibility for any inaccuracies that may be contained in this document, and makes no commitment to update or to keep current the information in this user guide, or to notify any person or organization of the updates. Please note: For the most up-to-date version of this user guide, please see our web site at .Super Micro Computer, Inc. ("Supermicro") reserves the right to make changes to the product described in this user guide at any time and without notice. This product, including software and documentation, is the property of Supermicro and/or its licensors, and is supplied only under a license. Any use or reproduction of this product is not allowed, except as expressly permitted by the terms of said license.IN NO EVENT WILL SUPER MICRO COMPUTER, INC. BE LIABLE FOR DIRECT, INDIRECT, SPECIAL, INCIDENTAL, SPECULATIVE OR CONSEQUENTIAL DAMAGES ARISING FROM THE USE OR INABILITY TO USE THIS PRODUCT OR DOCUMENTATION, EVEN IF ADVISED OF THE POSSIBILITY OF SUCH DAMAGES. IN PARTICULAR, SUPER MICRO COMPUTER, INC. SHALL NOT HAVE LIABILITY FOR ANY HARDWARE, SOFTWARE, OR DATA STORED OR USED WITH THE PRODUCT, INCLUDING THE COSTS OF REPAIRING, REPLACING, INTEGRATING, INSTALLING OR RECOVERING SUCH HARDWARE, SOFTWARE, OR DATA.Any disputes arising between the manufacturer and the customer shall be governed by the laws of Santa Clara County in the State of California, USA. The State of California, County of Santa Clara shall be the exclusive venue for the resolution of any such disputes. Supermicro's total liability for all claims will not exceed the price paid for the hardware product.FCC Statement: This equipment has been tested and found to comply with the limits for a ClassA digital device pursuant to Part 15 of the FCC Rules. These limits are designed to provide reasonable protection against harmful interference when the equipment is operated in a commercial environment. This equipment generates, uses, and can radiate radio frequency energy and, if not installed and used in accordance with the manufacturer’s instruction manual, may cause harmful interference with radio communications. Operation of this equipment in a residential area is likely to cause harmful interference, in which case you will be required to correct the interference at your own expense.California Best Management Practices Regulations for Perchlorate Materials: This Perchlorate warning applies only to products containing CR (Manganese Dioxide) Lithium coin cells. “Perchlorate Material-special handling may apply. See /hazardouswaste/perchlorate”.WARNING: Handling of lead solder materials used in this product may expose you to lead, a chemical known to the State of California to cause birth defects and other reproductive harm.PrefaceAbout This User GuideThis user guide is written for system integrators, PC technicians and knowledgeable end users. It provides information for the installation and use of the AOC-TBT-DSL5320 add-on card with your Supermicro motherboard.An Important Note to the UserAll images and layouts shown in this user guide are based upon the latest PCB revision available at the time of publishing. The card you have received may or may not look exactly the same as the graphics shown in this user guide.Returning Merchandise for ServiceA receipt or copy of your invoice marked with the date of purchase is required before any warranty service will be rendered. You can obtain service by calling your ven-dor for a Returned Merchandise Authorization (RMA) number. When returning the motherboard to the manufacturer, the RMA number should be prominently displayed on the outside of the shipping carton, and the shipping package is mailed prepaid or hand-carried. Shipping and handling charges will be applied for all orders that must be mailed when service is complete. For faster service, You can also request a RMA authorization online (/RmaForm/).This warranty only covers normal consumer use and does not cover damages in-curred in shipping or from failure due to the alternation, misuse, abuse or improper maintenance of products.During the warranty period, contact your distributor first for any product problems. Conventions Used in This User GuidePay special attention to the following symbols for proper system installation and to prevent damage to the system or injury to yourself:Note: Additional information given to differentiate between various models or provides information for correct system setup. PrefaceContacting SupermicroHeadquartersAddress:Super Micro Computer, Inc.980 Rock Ave.San Jose, CA 95131 U.S.A.Tel:+1 (408) 503-8000Fax:+1 (408) 503-8008Email:************************(GeneralInformation)**********************(TechnicalSupport) Web Site:EuropeAddress:Super Micro Computer B.V.Het Sterrenbeeld 28, 5215 ML's-Hertogenbosch, The NetherlandsTel:+31 (0) 73-6400390Fax:+31 (0) 73-6416525Email:*******************(GeneralInformation)*********************(TechnicalSupport)*****************(CustomerSupport) Web Site:www.supermicro.nlAsia-PacificAddress:Super Micro Computer, Inc.3F, No. 150, Jian 1st Rd.Zhonghe Dist., New Taipei City 235Taiwan (R.O.C)Tel:+886-(2) 8226-3990Fax:+886-(2) 8226-3992Email:**********************.twWeb Site:PrefaceTable of ContentsPrefaceChapter 1 Overview1-1 Overview ..............................................................................................................1-1 1-2 Introduction to Intel® Thunderbolt™ Technology ................................................1-1 1-3 Why Use Thunderbolt Technology? .....................................................................1-2 1-4 Key Features ........................................................................................................1-2 1-5 Specifications .......................................................................................................1-3 1-6 Product Use .........................................................................................................1-4 Chapter 2 Installation Instructions and Procedures2-1 Add-On Card Image and Layout ..........................................................................2-1 2-2 Thunderbolt AOC Installation ...............................................................................2-2 2-3 Thunderbolt AOC in BIOS ....................................................................................2-3 2-4 Installing the Thunderbolt Drivers ........................................................................2-6 2-5 Connecting Thunderbolt Devices .......................................................................2-10 Chapter 3 Frequently Asked Questions (FAQs)NotesChapter 1: OverviewChapter 1Overview1-1 OverviewCongratulations on purchasing your add-on card from an acknowledged leader in the industry. Supermicro products are designed with the utmost attention to detail to provide you with the highest standards in quality and performance. For product support and updates, please refer to our website at: / products/nfo/Thunderbolt.cfmIn addition to the add-on card, several important parts that are included with the card are listed below. If anything listed is damaged or missing, please contact your retailer.1-2 Introduction to Intel® Thunderbolt™ TechnologyThunderbolt is Intel's breakthrough Input/Output (IO) technology, providing the fast-est and most versatile connection to your computer.A Thunderbolt connection is the amalgam of the PCI Express (PCIe) and DisplayPortI/Os into one super connection. This singular port offers increased data transfer speeds and ability for superior audio and video output.Thunderbolt also allows for the hot-plugging of devices and the daisy chaining of various peripherals, without the loss of performance or speed.Supermicro has created an add-on card (AOC-TBT-DSL5320) to enable the addition of Thunderbolt functionality to your existing Supermicro workstation motherboard.Note: AOC is Supermicro's terminology for Add-On Card. TBT is short forThunderbolt. This language may be used throughout this manual.1-3 Why Use Thunderbolt Technology?Thunderbolt technology simplifies the attachment of peripheral devices to your system. Now multiple storage, audio, and video devices can be connected to your system through one high quality connector. Additionally, data transfer speeds both to and from the computer are increased due to the utilization of both the PCIe and DisplayPort avenues.Thunderbolt 2 has taken this advanced technology even a step further. While the first iteration of Thunderbolt offered download and upload speeds of 10 Gbps, Thunderbolt 2 offers 20 Gbps.The increased data transfer speed and hot-plugging capability saves Systems Administrators, graphics/video enthusiasts, and savvy end users time, as well as decreasing the number of connectors that they need. Furthermore, users can enjoy the latest technology in high definition video output without concerning themselves about loss of quality.Supermicro's add-on card will give you access to all of these great features.1-4 Key Features• PCIe 2.0 x 4 connection• Thunderbolt SPI ROM chip• DisplayPort chip• Display Converter chip• One (1) Thunderbolt connector• One (1) DisplayPort connector• One (1) General Purpose Input/Output header (GPIO)Chapter 1: Overview 1-5 SpecificationsMechanical Specifications• Dimensions: 3.71" length x 2.99" height• Must be inserted into the PCIe slot that is connected to the PCH. Refer to your Supermicro motherboard manual to determine which PCIe slot is connected to the PCH chipset.Note: Some motherboard models may denote this slot with the Thunder-bolt symbol.Supported Platforms• Must be used with a compatible Supermicro motherboard model.Note: At the time of this manual's publication, the supported models are:X10DAX, X10DAC, X10DAi, X10DRG-Q, and X10DAL-i.• Computers must be running Windows 7 32-bit, Windows 7 64-bit, or Windows8.1 64-bit.• Supports DisplayPort 1.2Power• Low power consumption of 4.1W max.Speed• Thunderbolt bandwidth of 20 GbpsCompliance/Operating EnvironmentThe add-on card is compliant with the following environmental regulations:• RoHS Compliant 6/6, Pb Free1-6 Product UseTo connect a device to a Thunderbolt port, use a Thunderbolt cable. Thunderbolt cable ends are the same as Mini DisplayPort ends.For displays that do not have Thunderbolt connections built into them, adapters can be used. Storage devices must be Thunderbolt capable to work.Up to six (6) devices may be daisy-chained via one Thunderbolt connector.Note: It is important to note that non-Thunderbolt capable devices or cablesthat are connected via an adapter will not be able to utilize Thunderboltspeeds. Non-Thunderbolt capable devices should be connected as thelast devices on any daisy chains to ensure that the Thunderbolt capabledevices in the chain can maintain optimal performance.Chapter 2: Installation Instructions and ProceduresChapter 2Installation Instructions and Procedures2-1 Add-On Card Image and Layout4AOC-TBT-DSL5320Thunderbolt SPI ROMThunderbolt 2 Controller GPIO HeaderFORCE SLP_S3FORCE PWRFORCE SLP_S5SW1SW 2SW 3PCIe 2.0 x 430”u Gold PS181 Display ConverterCBTD06DP213For DisplayPortDisplayPort 30”u Gold Thunderbolt Port 30”u Gold2-2 Thunderbolt AOC Installation1. Identify which PCIe slot is connected to the PCH on your motherboard. Usingboth hands, carefully insert the AOC into the appropriate PCIe slot.2. Connect one end of an SGPIO cable to the GPIO header on the AOC. Con-nect the other end to the GPIO header JBT1 on the motherboard.next to JBT1.3. Connect one end of a DisplayPort cable to the DisplayPort input connectoron the AOC (on the back of the metal bracket). Connect the other end to theDisplayPort output connector on the graphics card (GPU) attached to themotherboard.SGPIO CableDisplayPortInputPCIe Slot 6Chapter 2: Installation Instructions and ProceduresAOC-TBT-DSL5320 / Motherboard Layout2-3 Thunderbolt AOC in BIOSAfter you have physically installed the AOC, you should verify that Thunderbolt is enabled in the BIOS.Note : The default settings for the AOC should enable immediate function-ality. This process is just to perform a verification check.1. On system boot-up, press the Delete key to enter the BIOS.2. The Maintab of the BIOS opens.3. Press the right arrow key to navigate to the Advanced tab.4. Press the down arrow key to navigate to the Intel(R) Thunderbolt option.Press the Enter key.Chapter 2: Installation Instructions and Procedures 5. Verify that Intel Thunderbolt Technology is set to [Enabled].6. When you are finished, press the Esc key. If you made changes, use theright arrow key to navigate to the Save & Exit tab and down to the Save Changes option. Press the Enter key to save any configuration changes that you made.2-4 Installing the Thunderbolt DriversNow that you have verified that Thunderbolt is set up in the BIOS, you will need to download and install the drivers from the Intel web site.Note: A Windows 7 computer was used to capture the following screen-shots. If you are running a different OS, your screens may look different.Google Chrome was the web browser used for the purposes of this sec-tion. If you are running a different browser, you may be presented withdifferent options.1. In your Internet browser, go to https:///Detail_Desc.aspx?DwnldID=23742 to access the Intel Thunderbolt driver.2. Double-click the File name link TBT_Win7_32_64_Win8.1_64_2.0.4.250.zip. The Intel Software License Agreement dialog box appears. Review theagreement and if you accept, click the I accept the terms in the licenseagreement button. If you do not accept, you will not be able to continue.3. After you have accepted the license agreement, download and save the driv-ers to a folder of your choice.Chapter 2: Installation Instructions and Procedures4. Open the zip file, then open either the Win32 or Win64 folder depending on ifyour operating system (OS) is 32-bit or 64-bit. Click Thunderbolt Software to start the installation process.Note: If you do not know if your OS is 32 or 64-bit, you can find this informa-tion by navigating to Start > Computer > System Properties > System type.5. The Thunderbolt(TM) Software Setup dialog box and license agreementopens. Review the agreement and if you agree to it, check the I accept the terms in the License Agreement box and click the Install button. If you do not accept the terms, you will not be able to continue.6. When the installation is finished a dialog box will appear to notify you that youmay connect Thunderbolt devices to your system. Click the OK button.Chapter 2: Installation Instructions and Procedures2-5 Connecting Thunderbolt DevicesNow that your AOC has been installed, you can begin connecting Thunderbolt devices to your system. If your Thunderbolt device is not working you can check to see if the system recognizes it.To do this:1. Open the Start menu and open the All Programs directory. Navigate to theThunderbolt (TM) Software folder, open it, and click Thunderbolt (TM) Soft-ware.2. The Thunderbolt icon now appears in your System Tray. Click on it.3. A list of your Thunderbolt connected devices appears.Chapter 3: FAQsChapter 3Frequently Asked Questions (FAQs)Q: What do I need to do to get my AOC working?A: You will need to do three things:1. Physically install the AOC (see page 2-2 for instructions)2. Verify that Thunderbolt is enabled in the BIOS (see pages 2-3 to 2-5)3. Install and run the drivers (see pages 2-6 to 2-8)Q: What do I do if the AOC is not being recognized by my system?A: You will need to perform a series of checks on your hardware and software. Hardware• Verify it is the Supermicro add-on card model AOC-TBT-DSL5320. You cannot add Thunderbolt functionality to your Supermicro motherboard with any other brand or model of add-on card.• Is your motherboard supported? It must be a Supermicro motherboard, and must be a supported model. At the time of this manual's publication the supported models are: X10DAX, X10DAC, X10DAi, X10DRG-Q, and X10DAL-i.• Is your AOC installed in the appropriate PCIe slot? It must be installed in the PCIe slot that is connected to the PCH or your AOC will not work. Please refer to your Supermicro motherboard manual to determine which PCIe slot is con-nected to the PCH chipset.• Are the appropriate cables connected? In other words, are the SGPIO cable and the DisplayPort cable connected to the AOC and the motherboard? (See pages 2-2 and 2-3 for more information).• See also section 1-6 Product Use (page 1-4) and verify that the products you are using are supported and connected correctly.Software• Is your computer running one of the supported OS types? They are Windows7 32-bit, Windows 7 64-bit, and Windows 8.1 64-bit. If your computer is notrunning one of these, the AOC will not work.• Is the AOC properly set up in the BIOS? The default BIOS settings should have been sufficient to run your AOC (see pages 2-3 to 2-5 for more information).• Have you installed the drivers properly? (See pages 2-6 to 2-9 for more in-formation).If you have checked all of these things and everything is in order, please contact Supermicro to receive technical support (see page iv in the Preface section).Q: I see three sets of jumpers on the right side of my AOC (page 2-1). What do I do with those?A: Nothing. Those are configuration straps and should not be adjusted unless advised by Supermicro technical support.Q: My AOC is detected by my system and all set up. How do I begin using Thunderbolt devices?A: You will need to plug in a Thunderbolt cable to the Thunderbolt port (see dia-gram on page 2-1 for location of Thunderbolt port).From there, you can begin utilizing the Thunderbolt functionality. See section 1-6 Product Use on page 1-4 and verify that the products you are using are supported and connected correctly.3-2(Disclaimer Continued)The products sold by Supermicro are not intended for and will not be used in life support systems, medical equipment, nuclear facilities or systems, aircraft, aircraft devices, aircraft/emergency com-munication devices or other critical systems whose failure to perform be reasonably expected to result in significant injury or loss of life or catastrophic property damage. Accordingly, Supermicro disclaims any and all liability, and should buyer use or sell such products for use in such ultra-hazardous ap-plications, it does so entirely at its own risk. Furthermore, buyer agrees to fully indemnify, defend and hold Supermicro harmless for and against any and all claims, demands, actions, litigation, and proceedings of any kind arising out of or related to such ultra-hazardous use or sale.。
RF扫描枪刷中文系统步骤

本机连接RF枪一、在本地安装“ActiveSyncsetupchs.msi”程序,用数据线将RF枪底座和本地电脑进行连接,弹出页面,显示“已连接”,点击红框选项开始进行各项设置,如下图:英文系统刷中文系统一、本地连接RF枪,RF枪底座连接电源,将本地文件夹“OSUpdate”拷贝到RF枪的根磁盘的“Temp”文件夹中,RF枪屏幕双击“我的设备”找到“Temp”文件夹打开OSUPDATE文件夹内的3100c60Bcp_TEMP.lnk,开始刷机,等PDA屏幕左上角出现}}}符号表示刷机成功注:在刷机过程切勿切断电源,否则会导致刷机失败,无法修复RF枪安装带UTF-8字符集的Wave-link TelnetCE一、在本机安装“WLTE_MOT_MC3100_CE6_LANG_7_0_159_AS.exe”程序,打开应用程序页面,如下图:二、点击红线框中按钮,弹出页面,如下图:注:在RF枪屏幕安装“Wavelink TelnetCE”前先关闭已经打开的“Wavelink TelnetCE”程序三、点击红框中按钮,等待安装完成,回到RF枪屏幕,如下图:四、点击红框中按钮,等待安装完成检验RF枪是否成功安装带UTF-8字符集的Wave-link TelnetCE 一、双击RF枪屏幕红框中图标,如下图:二、在弹出页面中的菜单中选择红框中选项,如下图:三、在弹出页面输入框中输入“system”,点击“ok”,如下图:四、在弹出页面点击红框中按钮,如下图:五、在弹出页面将Emulation选项的值置为红框中的值后点击“Config”按钮,如下图:六、查看Language菜单中Server选项的属性值下拉框中是否存在“UTF-8 Unicode”,如不存在则重新安装带UTF-8字符集的Wave-link TelnetCE。
Guardmaster 440C-CR30 Safety Relay 版本11 目录号440C-CR

Release NotesOriginal InstructionsGuardmaster 440C-CR30 Safety Relay, Revision 11Catalog Number 440C-CR30-22BBBSummary of ChangesThis publication contains the following new or updated information. This list includes substantive updates only and is not intended to reflect all changes.About This PublicationThese release notes supplement the existing documentation supplied with your product. Read this document before using Guardmaster® 440C-CR30 safety relays.Firmware Revision HistoryAvailability of Enhancements and Anomaly FixesEnhancements are available in the safety relay only if it is at the required firmware revision or higher and the Connected Components Workbench™ or Studio 5000 Logix Designer® project contains a safety relay that is configured with the required firmware revision or higher. If the project contains a safety relay revision that is lower than the required revision for an enhancement, then the project is still valid but the enhancement will not be available until the project is upgraded to the minimum supported revision.Fixes for firmware anomalies are available as long as the safety relay firmware revision is at the minimum revision or higher. The configured safety relay revision must be of the same major revision.The following tables provide a list of enhancements, known anomalies, and corrected anomalies for the CR30 safety relay firmware revisions.EnhancementsTopicPage Updated Firmware Revision History 1Updated Table 22Updated image in step 23Revision Description6.004First revision release [safety firmware 0A.01]6.006Minor revision release [safety firmware 0A.02]7.006Major revision release [safety firmware 0A.02]8.013Major revision release [safety firmware 0A.02]9.004Major revision release [safety firmware 0A.02]10.004Major revision release [safety firmware 0A.03]10.009Minor revision release [safety firmware 0A.03]10.010Minor revision release [safety firmware 0A.03]10.011Minor revision release [safety firmware 0A.03]Table 1 - EnhancementsEnhancement (1)DescriptionAvailable From Firmware RevisionLock control function support New Lock Control function is now supported forissuing an unlock request to a safety gate withguard locking.10.004Mode selection function support New Mode Selection Safety Monitoring Function is now supported.10.004Mute function enhancements New Muting function block has been enhanced to support a mute enable input, a mute fault manual monitored reset and now offers a secondary output based on the override status.10.004Status function supportNew Status functions for monitoring andannunciating function block faults or ‘waiting for reset’ conditions.10.004Reusable feedback supportNew ability to apply feedback inputs to multiple Safety Output Functions.10.004Single input And withRestartenhancement New ability for the And with Restart logic function to support one input.10.004PanelView Plus Tag browsing support With release 8.00 of FactoryTalk® View Studio, PanelView™ Plus can communicate to CR30 safety relays using EDS parameter browsing over EtherNet/IP™.9.004Nesting of Logic Level Function blocksNew ability to use the output state of a logic block immediately above another logic block as an input condition.9.004Inverting of Logic Level Inputs/Outputs New ability to invert (logical NOT) of inputs and outputs of Logic Level function blocks.9.004Output Loop Safety Monitoring Function support New Output Loop Safety Monitoring Function that allows the logical state of a Safety Output Function to be used as an input condition.9.004RS Flip-Flop Logic Function support New RS Flip-Flop Logic function is now supported in the Logic level columns of the Logic Editor.9.004440C-ENET plug-in supportThe EtherNet/IP plug-in provides both I/O messaging and explicit messaging. The safety relay can now be configured over EtherNet/IP using either Connected Component Workbench or an Add-on Profile (AOP) in Studio 5000 Logix Designer application.8.013Standard Signal Safety Monitoring Function support New Standard Signal Safety Monitoring Function that allows the use of standard control signals from digital plug-ins or communication ports to be used in the logic of the safety relay.8.013Project Upgrade featureProjects developed for earlier versions of firmware can be automatically converted into the latest version of firmware supported.8.0132080-MEMBAK-RTC plug-in support Project backup and restore are supported on CR30 safety relays through the 2080-MEMBAK-RTC module.7.0062080-IQ4 plug-in supportThe 2080-IQ4 digital input plug-in provides 4-pt standard rated 12/24V DC digital input expansion. It can be used in slot 1 and/or slot 2 module bays.7.0062Rockwell Automation Publication 440C-RN001H-EN-P - December 2020Guardmaster 440C-CR30 Safety Relay, Revision 11 Release NotesAnomalies2080-OB4 plug-in support The 2080-OB4 digital output plug-in provides 4-pt standard rated 12/24V DC sourcing output expansion. It can be used in slot 1 and/or slot 2 module bays.7.0062080-OW4I plug-in supportThe 2080-OW4I relay output plug-in provides 4-pt standard rated relay output, individually isolated, 2A expansion. It can be used in slot 1 and/or slot 2 module bays.7.006Unique function block name supportUnique names can be assigned to the Safety Monitoring Function blocks and the Safety Output Function blocks. These names are stored in the project that is loaded to the safety relay and can be recovered by an upload.7.006Password protection Software connections including Upload, Download,and Connect can be restricted through passwordprotection.7.006(1)For more information, see publication 440C-UM001.Table 2 - Known and Corrected AnomaliesAnomalyDescriptionAffected Firmware Revisions Corrected Firmware Revision Discrepancy Fault on Power-upDevices with pulse testing outputs would sometimes cause a discrepancy fault in the CR30 safety relay upon power-up. On power-up, the Channel Test during the first logic scan when transitioning from self-test to run mode has been removed to help prevent the discrepancy fault.See publication 440C-UM001 for details.6.0046.0067.0068.0139.00410.00410.00910.01010.011Memory Module Incompatibility Safety relay fails to recognize 2080-MEMBAK-RTC memory modules that are manufactured on or after 2016/02/11.APBC000280011 6.0046.0067.0068.0139.00410.00410.00910.010Memory Module Update When updating a safety relay from a previous firmware revision to firmware 10 using thememory module the restore operation must be performed twice (the first process updates thefirmware, the second process restores the user configuration). 6.004 6.0067.0068.0139.004Configuration loss on power cycleDuring specific power down conditions, the safety relay could be interrupted while writing a fault condition to its nonvolatile memory. On power up, the memory is evaluated as corrupted and the user configuration is discarded.APBC00026898 6.0046.0067.0068.0139.00410.00410.009Connection failure with Add-on Profile (AOP) major revision 1The safety relay rejects an I/O connection that originates from the safety relay AOP (versions 1.013 and versions 1.014) when Compatible Keying and Major Revision 8 or later is configured.APBC000271569.00410.004Download faultA download could result in a major fault on the safety relay, Type 06, Code 20 – Configuration Fault.APBC000251087.0068.0139.00410.004Download over Ethernet faultA download over Ethernet to the safety relay could result in a Type 05, Code 00 – Internal Safety Synch Fault.APBC000236608.0139.00410.004Unexpected disconnect from safety relay Occasionally Connected ComponentsWorkbench software would unexpectedly disconnect while connected to a password protected safety relay.APBC000248668.0139.004Table 1 - Enhancements (Continued)Enhancement (1)DescriptionAvailable From Firmware RevisionLocked by another connection error Attempts to connect to the safety relay arerejected and erroneously reports “CR30 has been locked by another, new connection is not allowed.”APBC000248678.0139.004No reconfiguration after EEPROM fault After the safety relay experiences a memory fault (Type 5 Code 00), the safety relay does not accept a new download.APBC00024866 6.0046.0067.0068.0139.004Muting L-Type reports incorrect fault description Under specific configuration conditions, the Muting T Type function block incorrectly reports a mute sensor timing fault when actually a sequence fault occurred.APBC000237318.0139.004Network address changes require power cycle Changes to the 440C-ENET Ethernet portsettings, duplicate IP address detection, and DHCP vs. static IP address settings may require a power cycle to take effect.APBC000241338.0139.004Power-up faultVariations in 24V DC supply power to the CR30 safety relay during power-up could lead to power fault: Type 04, Code 01.APBC000244266.0046.0067.0068.013Discrepancy fault after power-upVariations in 24V DC supply power to the CR30 safety relay during power-up could lead to adiscrepancy fault on any dual channel Safety Monitoring Function: “One channel open after reset” 6.0046.0067.0068.013Empty fault logModbus reporting of the fault log always returns 0, indicating no fault, even if faults are present in the log.APBC00025011 6.0046.0067.0068.013Incorrect Mode The safety relay will return to Run Mode after downloading a valid configuration to a unit that has experienced a nonrecoverable fault.APBC000257716.0046.0067.0068.013Modbus fault state cleared in Program Mode The safety relay does not report faultinformation over Modbus once the safety relay is placed in Program Mode.6.0046.0067.0068.013Memory module firmware update failure The memory module is unable to upgrade a firmware revision 7 safety relay to version 8 or later 7.006L-Type muting override conditionOverride for L-Type muting cannot be initiated when only the light curtain is interrupted (no mute sensors).6.0046.0067.006Two Hand Control at power up Two Hand Control does not fault at power up if buttons are pressed. 6.0046.0067.006Override conditionsFor muting applications, mute sensor interrupted or timing faults should be only conditions that allow override to be initiated.6.0046.0067.006Serial port doesnot shutdownWhen the serial port is configured as shutdown,it still responds to Modbus messages.APBC00020590 6.0046.0067.006Input filters greater than 200 ms create nonrecoverable fault When an input filter of greater than 200 ms is configured on any Safety Monitoring function, a nonrecoverable fault is generated when the configuration is downloaded to the safety relay.APBC00020589 6.0046.0067.006Missing plug-in slot 1 without fault log entry A missing plug-in module configured in slot 1 and not actually present results in a fault but no fault log entry is created.APBC00018493 6.0046.0067.006Plug-inmismatch with duplicate fault log entriesA mismatch between the plug-in present on slot 1 and the actual plug-in present results in duplicate entries in the fault log.APBC000205086.0046.0067.006Plug-in outputs fail to configure When Plug-in outputs terminals are selected asoutputs for Safety Output Functions, they fail toturn on when the corresponding Safety OutputFunction turns on.APBC000201036.004 6.006Table 2 - Known and Corrected Anomalies (Continued)AnomalyDescriptionAffected Firmware Revisions Corrected Firmware RevisionRockwell Automation Publication 440C-RN001H-EN-P - December 20203Guardmaster 440C-CR30 Safety Relay, Revision 11 Release NotesUse DMK FilesFirmware for the CR30 safety relay beginning with firmware revision 10.009 uses a new file format called *.DMK. These files are named for easy identification, for example: 440C-CR30-22BBB_10.009.dmk.ControlFLASH™ software, version 13 or later, supports the format. ControlFLASH software is automatically installed as part of Studio 5000 Logix Designer application installation, version 28 or later. You can download ControlFLASH software from the Rockwell Automation Product Compatibility and Download Center (PCDC - rok.auto/pcdc ) separately, if necessary.You are not required to install the new firmware file format. When you download *.DMK files from the Rockwell Automation PCDC, ControlFLASH softwareautomatically saves the folder location where the *.DMK files were downloaded. As a result, ControlFLASH software can easily locate *.DMK files.You can use the Browse option to access and configure the folders that ControlFLASH software monitors as shown:Upgrade Safety Relay FirmwareThis procedure shows you how to update the firmware in a CR30 safety relay using ControlFLASH. To download the latest CR30 safety relay firmware revision, go to the PCDC (PCDC - rok.auto/pcdc ) and select your desired revision.On CR30 safety relays, you can upgrade your safety relays through the Ethernet port on the 440C-ENET plug-in module and the USB.Through USB1.Verify successful RSLinx® Classic communications with you CR30 safety relay by USB using RSWho. The CR30 safety relay uses the AB_VBP-x driver.2.Start ControlFLASH (Start > All Programs > FLASH Programming Tools > ControlFlash) and click Next >.3.Select the catalog number of the CR30 safety relay (440C-CR30-22BBB) that you are updating and click Next >.4.Select the safety relay in the browse window and click OK.Communication fault without fault log entryIf the host microprocessor within the CR30safety relay loses communication with the safety processors a fault is generated but no fault log entry is createdAPBC00020302 6.0046.006Fault log index changes after power cycleAfter a power cycle of the safety relay,previously detected faults index by one within the fault log.APBC000186376.004 6.006Inverted image of downloadprogram notcompared After performing a download, the inverted datais sent back from the safety relay to Connected Components Workbench software but not compared as an additional diagnostic check.APBC00020430 6.004 6.006Download through virtual image failsDownload of a program to the safety relay occasionally fails due to connection timeout when downloading through a virtual image.6.004 6.006ATTENTION: All Ethernet settings are reverted to factory default after a ControlFLASH firmware update.Table 2 - Known and Corrected Anomalies (Continued)AnomalyDescriptionAffected Firmware Revisions Corrected Firmware Revision IMPORTANTTo update your safety relay successfully, it must be in Program Mode or BOOT Loader mode. The safety relay can be placed into Program Mode from the Graphic Overview screen in Connected Component Workbench software, the Logic Configuration tab in the Logix Designer module profile or placed in BOOT Loader mode by holding the MEM/ID button located below the USB port on the safety relay during power-up.Publication 440C-RN001H-EN-P - December 2020 | Supersedes Publication 440C-RN001G-EN-P - April 2016Copyright © 2020 Rockwell Automation, Inc. All rights reserved. Printed in the U.S.A.Rockwell Otomasyon Ticaret A.Ş. Kar Plaza İş Merkezi E Blok Kat:6 34752 İçerenköy, İstanbul, Tel: +90 (216) 5698400 EEE Yönetmeliğine UygundurAllen-Bradley, Connected Components Workbench, ControlFLASH, expanding human possibility, FactoryTalk, Guardmaster, PanelView,Rockwell Automation, RSLinx, and Studio 5000 Logix Designer are trademarks of Rockwell Automation, Inc.EtherNet/IP is a trademark of ODVA, Inc.Trademarks not belonging to Rockwell Automation are property of their respective companies.Your comments help us serve your documentation needs better. If you have any suggestions on how to improve our content, complete the form at rok.auto/docfeedback .For technical support, visit rok.auto/support.Waste Electrical and Electronic Equipment (WEEE)Rockwell Automation maintains current product environmental compliance information on its website at rok.auto/pec .At the end of life, this equipment should be collected separately from any unsorted municipal waste.5.Verify the revision, and click Next > to continue.6.Click Finish.7.Click Yes to initiate the update.The next screen shows the download progress.If you see the following error message, verify that the safety relay is in Run mode. If so, change to Program or BOOT Loader mode by pressing theMEM/ID switch during power-up of the CR30 safety relay, click OK, and try again.When the update is complete, you see a screen similar to the following.Click OK to complete the update.。
DeviceNet Adapter 22-COMM-D 固件 v1.011 发布说明书
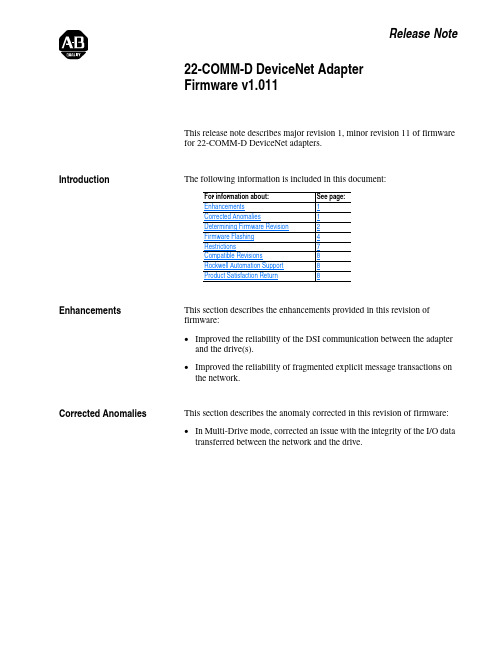
Release Note22-COMM-D DeviceNet Adapter Firmware v1.011This release note describes major revision 1, minor revision 11 of firmware for 22-COMM-D DeviceNet adapters.IntroductionThe following information is included in this document: EnhancementsThis section describes the enhancements provided in this revision of firmware:•Improved the reliability of the DSI communication between the adapter and the drive(s).•Improved the reliability of fragmented explicit message transactions on the network.Corrected AnomaliesThis section describes the anomaly corrected in this revision of firmware:•In Multi-Drive mode, corrected an issue with the integrity of the I/O data transferred between the network and the drive.For information about:See page:Enhancements 1Corrected Anomalies 1Determining Firmware Revision 2Firmware Flashing 4Restrictions 7Compatible Revisions 8Rockwell Automation Support 8Product Satisfaction Return 8222-COMM-D DeviceNet Adapter Firmware v1.011Determining Firmware Revision This section describes procedures to determine the firmware revision of your 22-COMM-D DeviceNet adapter.Using the Optional, External LCD HIM (22-HIM-**)22-COMM-D DeviceNet Adapter Firmware v1.0113Using DriveExplorer Lite/Fullunch DriveExplorer and go online (via 1203-USB or 22-SCM-232converter) with the drive that is connected to the adapter.2.In the DriveExplorer treeview, click on 22-COMM-D DeviceNetModule as shown in Figure 1.3.Click the information icon to display the adapter’s properties screen.4.The “Revision:” field shows the present revision (for example, 1.010) ofthe adapter firmware.Figure 1 Information Icon in DriveExplorer WindowTIP: When clicking on the 22-COMM-D adapter using version 5.01 orhigher DriveExplorer Lite/Full, the adapter firmware revision is also shownin the right pane of the DriveExplorer window.Step 4422-COMM-D DeviceNet Adapter Firmware v1.011Using DriveExecutive unch DriveExecutive and go online with the drive that is connected to the adapter.2.In the DriveExecutive treeview, click on 22-COMM-D as shown in Figure 2.3.Click the information icon to display the adapter’s Properties screen.4.The “Revision:” field shows the present revision (for example, 1.010) of the adapter firmware.Figure 2 Information Icon in DriveExecutive Window Firmware FlashingThis section describes procedures to flash upgrade your adapter firmware. Flash kits for drives, communications adapters, and peripherals are provided on the Allen-Bradley Web Updates site located at /support/abdrives/webupdate . Flashing can only be performed using a 1203-USB or 22-SCM-232 converter. For information about how to connect to your drive, please refer to the 1203-USB or 22-SCM-232 User Manual. They can be viewed/downloaded on the Literature Library web site located at .Step 4ATTENTION: Risk of permanent equipment damage exists. Once a flash update has been started, do not remove power from the drive (or the 22-XCOMM-DC-BASE External Comms Kit, if used) until after the download has completed and the adapter MOD status indicator starts FLASHING GREEN. If power is removed before this occurs, the adapter may be permanently damaged. An adapter that has been damaged in this22-COMM-D DeviceNet Adapter Firmware v1.0115Installing the Flash Kit1.Install the flash kit utility from the Allen-Bradley Web Updates site forthe 22-COMM-D adapter. (This also automatically installs theControlFLASH utility and deploys the firmware files for use withHyperTerminal on your computer.)2.You are now ready to use DriveExplorer, DriveExecutive,ControlFLASH or HyperTerminal to update the adapter. Refer to the respective section below and follow the instructions.Using DriveExplorer Lite/Full to Flash Update1.With the Flash Kit installed (see Installing the Flash Kit), launchDriveExplorer and go online (via a 1203-USB or 22-SCM-232converter) with the drive that is connected to the adapter.2.In the DriveExplorer treeview, click on 22-COMM-D DeviceNetModule. Then click the information icon as shown in Figure 1 todisplay the adapter’s Properties screen.3.On the 22-COMM-D Properties screen, click the Details tab.Important:This update may cause the adapter parameters to revert to their default values. You may want to save yourconfiguration using DriveExplorer or the HIM CopyCatfeature before upgrading.4.To start the flash update, click the Flash Update… button. Then select“v1.011.xx Full” from the list of available updates and click Next >.Follow the remaining screen prompts until the flash update procedure completes and displays the new firmware version (v1.011).Using DriveExecutive to Flash Update1.With the Flash Kit installed (see Installing the Flash Kit), launchDriveExecutive and go online (via a 1203-USB or 22-SCM-232converter) with the drive that is connected to the adapter.2.In the DriveExecutive treeview, click on 22-COMM-D adapter. Thenclick the information icon as shown in Figure 2 to display the adapter’s Properties screen.3.On the 22-COMM-D Properties screen, click the Component Detailstab.Important:This update may cause the adapter parameters to revert to their default values. You may want to save yourconfiguration using DriveExecutive or the HIM CopyCatfeature before upgrading.4.To start the flash update, click the Flash Update button. Then select the22-COMM-D from the list of available devices and click Next >.622-COMM-D DeviceNet Adapter Firmware v1.0115.Select “v1.011.xx Full” from the list of available updates and clickNext >. Follow the remaining screen prompts until the flash updateprocedure completes and displays the new firmware version (v1.011).Using ControlFLASH to Flash Update1.With the Flash Kit installed (see Installing the Flash Kit on page5),launch ControlFLASH by selecting Start > (All) Programs > FlashProgramming Tools > ControlFLASH.2.On the ControlFLASH Welcome screen, click Next >.3.Choose the appropriate 22-COMM-D update from the list of availableupdates and click Next >.Important:This update may cause the adapter parameters to revert totheir default values. You may want to save yourconfiguration using the HIM CopyCat feature,DriveExplorer or DriveExecutive before upgrading.4.Expand the treeview for the communication path you are using, andselect the drive icon that represents the drive with the 22-COMM-Dadapter you are updating. Then click OK.5.With the Multiple Assemblies Found window displayed, select“Port X - 22-COMM-D” from the list and click OK.6.With the Firmware Revision window displayed, select “1.011.xx Full”from the list of available updates and click Next >. Follow theremaining screen prompts until the flash procedure completes anddisplays the new firmware revision (v1.011).Using HyperTerminal to Flash Update1.Verify that adapter jumper J2 is set to Single operating mode.2.With the Flash Kit installed (see Installing the Flash Kit on page5),launch HyperTerminal and go online (via a 1203-USB or 22-SCM-232converter) with the powered drive that is connected to the adapter.3.Press the Enter key until the main menu (Figure 3) appears.Figure 3 Main MenuMain Menu - Enter Number for Selection1> Display Setup Parameters2> Display Event Queue3> Flash Upgrade4.In the main menu, press 3 to flash upgrade. Then press the number keythat corresponds to the “22-COMM-D” in the list, and press Y (for Yes)to update the flash code. The terminal program will start displaying theletter “C”. This signals the XMODEM protocol that the download mayproceed. You then have one minute to start the transfer.22-COMM-D DeviceNet Adapter Firmware v1.01175.Select Transfer > Send File to display the Send File screen (Figure 4).6.Click Browse and navigate to the flash file located in:C:\ Program Files\ControlFLASH\0001\0079\8100Figure 4 Send File Screen7.In the Select File to Send window list, click on the “22-COMM-D_1_011_01_Full.bin” file. Then click Open . This file name now appears in the Filename box in the Send File screen.8.In the Protocol box, select “Xmodem.”9.Click Send . A dialog box appears and reports the progress of the update. When it is complete, the message “Flash Complete” appears. Press any key to continue.Important:Keep the device powered for 15 seconds after the operation has completed or until the adapter MOD status indicator starts flashing green. 10.Press the Enter key to return to the main menu.11.After the flash successfully completes, set adapter jumper J2 to the desired Single or Multi-Drive operating mode position.RestrictionsNo restrictions apply to this revision of firmware.ATTENTION: Risk of injury or equipment damage exists. When you perform a flash update, the drive will fault if it is receiving control I/O from the adapter. Verify that the drive has stopped safely or is receiving controlI/O from an alternate source before beginning a flash update.TIP: To cancel the flash update at any time, press CTRL-X .U.S.Allen-BradleyDrivesTechnicalSupport-Tel:(1)262.512.8176,Fax:(1)262.512.2222,Email:*****************,Online:/support/abdrivesCompatible Revisions To use this revision of firmware, update your system tools as follows:Rockwell AutomationSupport Rockwell Automation provides technical information on the web to assist you in using our products. At , youcan find technical manuals, a knowledge base of Frequently AskedQuestions (FAQs), technical and application notes, sample code and links tosoftware service packs, and a MySupport feature that you can customize tomake the best use of these tools.Rockwell Automation also provides complimentary phone support fordrives, communication adapters, and peripherals. If you experience aproblem with the adapter, please review the information in its User Manual.For further help in getting your adapter operational, contact a CustomerSupport representative:For an additional level of technical phone support for installation, configuration and troubleshooting, we offer TechConnect Support programs. For more information, contact your local distributor or Rockwell Automation representative, or visit . Product Satisfaction Return Rockwell Automation tests all products to ensure that they are fully operational when shipped from the manufacturing facility. However, if your product is not functioning and needs to be returned: Update this:To this version or later:DriveExplorer Lite/Full4.01DriveExecutive3.01PowerFlex 4-Class Driveall versions compatible External LCD HIM (22-HIM-**)all versions compatible RSLinx Classic 2.43United States (1) 262.512.8176Monday – Friday, 7am – 6pm CSTOutside United States Please contact your local Rockwell Automationrepresentative for any technical support issues.United States Contact your distributor. You must provide a Customer Support case number (see phone number above to obtain one) to your distributor to complete the return process.Outside United States Please contact your local Rockwell Automation representative for return procedure.。
ATTO Configuration Tool 用户指南说明书

Product Release Notes1. General Release InformationThe ATTO Configuration Tool helps you customize the settings of your ATTO storage Controller to maximize the performance of your storage connection. While the factory settings on your host adapter should provide excellent performance for a wide range of applications, some specialized applications may benefit from modification of the adapter settings to tune the adapter for a specific performance range.These product release notes define the new features, changes, known issues and release details that apply to the ATTO Configuration Tool v4.09 that was released on November 29, 2012. This information pertains to the Microsoft® Windows OS including Windows XP, Vista, 7, 8, Server 2003, 2008, 2008 R2 and 2012.2. Changes∙Version 4.09 (Released 11/29/12)o The following apply to changes made from v4.08 to v4.09. You must use the latest product drivers for your specific adapter whenever updating the ATTO Configuration Tool version. Thelatest driver sets can be accessed via the ATTO website.o New Features, Enhancements and Changes▪ A new tab has been added to manage NPIV settings▪The ConfigTool now supports NPIV on windows platforms only▪Celerity 16Gb support to the Windows and Linux diagnostic scripts▪Devices can be added/removed in a rapid fashion without consequence▪The adapter buzzer now sounds for non-Thunderbolt adapters when clicking thenotification test button∙Version 4.08 (Released 11/08/12)o The following apply to changes made from v4.07 to v4.08. You must use the latest product drivers for your specific adapter whenever updating the ATTO Configuration Tool version. Thelatest driver sets can be accessed via the ATTO website.o New Features, Enhancements and Changes▪Added process power management events from the ESASRAID driver▪Activated the on-board buzzer on the adapter that triggered a buzzer event only▪Added detect mute button events from ThunderStream products▪Resolved a timing related crash on shutdown if SNMP is enabled▪Resolved a crash when committing the Notifications Plane contents with an emailpassword▪Resolved conflict with StorNext▪Made changes to the operating system display for Window 8∙Version 4.07 (Released 09/28/12)o The following apply to changes made from v4.05 to v4.07. You must use the latest product drivers for your specific adapter whenever updating the ATTO Configuration Tool version. Thelatest driver sets can be accessed via the ATTO website.o New Features, Enhancements and Changes▪Removed the discovery mode option in the NVRAM panel for a 16Gb Celerity FCadapter.∙Version 4.05 (Released 08/13/12)o The following apply to changes made from v4.03 to v4.05. You must use the latest product drivers for your specific adapter whenever updating the ATTO Configuration Tool version. Thelatest driver sets can be accessed via the ATTO website.o New Features, Enhancements and Changes▪Added support for OEM branding.▪Added support for time-stamped log messages from a RIAD device.∙Version 4.03 (Released 04/23/12)o The following apply to changes made from v4.02 to v4.03. You must use the latest product drivers for your specific adapter whenever updating the ATTO Configuration Tool version. Thelatest driver sets can be accessed via the ATTO website.o New Features, Enhancements and Changes▪The installer now makes the application available to all users.▪Several freezes in the system service have been resolved.▪Several crashes related to the auto discovery system were resolved.∙Version 4.02 (Released 02/14/12)o The following apply to changes made from v4.01 to v4.02. You must use the latest product drivers for your specific adapter whenever updating the ATTO Configuration Tool version. Thelatest driver sets can be accessed via the ATTO website.o New Features, Enhancements and Changes▪SNMP support has been added.▪Help menu now features a ‘Run Diagnostics’ option for troubleshooting purposes, which displaces the former option to save logs under the Notifications panel. RAIDlogging has also been improved.▪Support for FastFrame CT and NT adapter series has been added.▪Gen 3 PCIe transfer rate support has been added.▪Hot spares can now be assignable to RAID groups via CLI.▪Support for sounding the buzzer on buzzer-equipped hardware, controllable by the Notification Application.▪Performance, stability and logging improvements.∙Version 4.01 (Released 09/06/11)o The following apply to changes made from v4.0 to v4.01. You must use the latest product drivers for your specific adapter whenever updating the ATTO Configuration Tool version. Thelatest driver sets can be accessed via the ATTO website.o New Features, Enhancements and Changes▪The integrated help text features new icons for the buttons the user can click as well as manipulate in the table of contents.▪This release offers improved support and functionality with 3Gb RAID adapters.▪Rare instances of system hangs have been resolved.∙Version 4.0 (Released 08/17/11)o The following apply to changes made from v3.38 to v4.0. You must use the latest product drivers for your specific adapter whenever updating the ATTO Configuration Tool version. Thelatest driver sets can be accessed via the ATTO website.o New Features, Enhancements and Changes▪Support for ExpressSAS H6F0GT.▪This release represents a major update to the GUI interface and capabilities. Whereas previous versions contained a single application, this release provides a GUIapplication and system service. Refer to the product manual for more information onthe setup and operation of these components.▪This release offers the ability to set-up, manage and optimize storage connected locally and remotely to ATTO storage controllers. This includes the ability to remotely accessand update NVRAM settings, updating system firmware and drivers, as well asretrieving system event logs.▪Only one instance of the ConfigTool can be installed on a host at any one time (i.e.either v3.38 or v4.0, but not both).This version does not have SNMP enabled. Use an earlier version of the ATTOConfigTool if you require SNMP.3. Known Issues/Advisements∙Windows XP x64 and Windows 2003 machines do not display a message when the system is prompted to shut down via the ConfigTool.∙The Notifications tab can be viewed and changed without logging into a host. Additionally, the Notifications tab doesn’t detect if a connected host has disconnected, and thus the informationdisplayed may become stale.∙The audible and visual notifications only work with the system service on the local machine (not remotely).∙Drives may not disappear in the ConfigTool if a cable is pulled with no IO.∙The ConfigTool client doesn’t detect when it has been disconnected from a daemon.∙Manually entered IP addresses or hostnames are not saved.∙Installer extraction process does not automatically start the installation process on Windows.∙If many notifications pop-up, the Notification Application may stop responding.4. Affected ProductsATTO ConfigTool for the following ATTO products:ATTO ExpressSAS H6F0GT, H6F0, H60F, H680, H608, H644, H30F, H380, H308ATTO ExpressSAS RAID Adapters R30F, R380, R348, R60F, R680, R608, R644ATTO Celerity FC-162E, FC-161E, FC-84EN, FC-81EN, FC-82EN, FC-44ES, FC-42ES, FC-41ES,FC-42XS, FC-41XSATTO ExpressPCI UL5D Low-Profile, ExpressPCI UL5D, ExpressPCI UL4DATTO FastFrame Network Adapters CS14, CS12, CS11, NS14, NS12, NS11, NT12, NT11ATTO ThunderStream SC 3808ATTO ThunderLink FC1082, SH1068, NT1102, NS11015. Contacting ATTO SupportATTO Technology, Inc. is renowned for its technical support services. ATTO’s goal is to provide you the quickest response possible for your technical support needs, and is available Monday-Friday, 8:00 AM to 6:00 PM EST (except holidays).ATTO Technical Support can be contacted via phone or email:∙Phone: 716.691.1999 ext. 242∙E-Mail: ************************。
PDA TR 80《制药实验室数据完整性管理体系》(中英文对照版)

PDA TR 80《制药实验室数据完整性管理体系》(中英文对照版)PDA TR 80《制药实验室数据完整性管理体系》现已全文翻译完毕,大家可以点击文末“阅读原文”链接下载中英文对照版全文。
由于微信篇幅关系,这里只放出微生物实验室数据完整性的内容:5.0 Data Integrity in the Pharmaceutical Microbiology Laboratory5.0 微生物实验室的数据完整性5.1 General Considerations and Risks一般原则及风险The approaches used to investigate the occurrence of suspected data integrity issues that h recently occurred in a pharmaceutical microbiology laboratory can be challenging and, in some cases, may bevery different than those used to evaluate similar occurrences in an analytical chemistry laboratory, Many microbiological methods are performed manually;subsequently, the recorded results are often based on the visual observations by an individual scientist performing the tests.制药企业微生物实验室对可疑数据完整性问题的调查方法,越来越成为一个挑战,并且在一些情况下,与同样发生可疑数据的化学分析实验室的调查方法完全不同。
很多微生物测试方法都是手动操作,以及所有的测试结果都由微生物测试人员人工检查并记录。
NDP的各种报文

Change in IPv6
New value of 6 Removed Traffic Class field Payload Length field Removed to Fragment header Removed to Fragment header Removed to Fragment header Hop Limit field Next Header field Removed Same, new 128-bit length Same, new 128-bit length Removed (extension headers)
介绍:该字段由传送路径上的每个节点和路由器读取并处理
用途:主要用于巨型数据包(RFC2675)和路由器警报(RFC 2711),
e.g :RSVP,MLD report etc) 报文格式: Next Header(8-bit):标识下一个包头 Hdr ext Len(8-bit):Hop-by-hop option的长度,不统计前1个字节
IPv6 NDP
1.相关模块:
Router/Prefix Discovery Address Autoconfigration Duplicate Address Detection Address Resolution Host Sending algorithm (for host) Neighbor Unreachability Detection Redirect
2.需要用到的地址类型:
节点组播地址(FF02::1) 节点组播地址 路由器组播地址(FF02::2) 路由器组播地址 被请求节点组播地址(FF02::1:FFXX:XXXX) 被请求节点组播地址 本地链路地址(FE80::/10) 本地链路地址 未指定地址(::) 未指定地址
PDA TR29(1998)中英文对照版[1]
![PDA TR29(1998)中英文对照版[1]](https://img.taocdn.com/s3/m/a7cef87f02768e9951e738ca.png)
3.5 Cleaning Agent Groupings 清洁剂分类
4. Residues and Residue Removal 残留物与残留物的清除
4.1 Types of Residue 残留物的类别
4.2 Cleaning Agents
蒲公英论坛首发。Eleven 制作,未经许可请勿在其他网站和论坛发布。
Our goal had always been to outline cleaning validation practices across a range of equipment, process, and product applications and the inclusion of this flexibility was certainly a factor in the length of time it took to complete this effort. During the course of assembling this document, we recognized the commonality of certain themes, issues, and concerns relative to cleaning and cleaning validation across the industry. We also realized that in order to apply the principles in different operating settings, that some narrowing of the document would be necessary. As a result, we have included perspectives on the application of the guidance in various areas: finished pharmaceuticals, bulk pharmaceutical chemicals, biopharmaceuticals and clinical products. Inclusion of biopharmaceuticals in this effort is not intended to replace the more comprehensive coverage provided by our partner committee, but rather to provide greater insight regarding the broad application of the guidance provided herein. 我们的目标一直都是着眼于如何描述清洁验证的操作,以适应一系列设备、工艺及产品 的应用,另外,在完成本工作之前耗时不少,是以运作的弹性度也自然的进行了考虑。 在编制本文件的过程中,我们了解工业界在清洁方法与清洁验证方面若干共同的主题、 争议及关注点。我们也知道如要讲相关的原则用于不同的现状,本文件中有些部分涉及 的内容有必要加以量化的必要。基于这些原因,我们对本文件在各种领域方面的应用, 如一般制剂、原料药、生物制剂及临床有关产品等,分别加以研究描述。生物药学制剂 的列入,目的不在于取代我们的队友已提供的较为广泛而深入的资料,而在于本资料更 能令人深入了解,以使其广泛的应用。
AT-Patch用户手册说明书

AT-PatchUser ManualMODEL: ATP-C130ContentsProduct Descriptions (4)Intended Purpose (4)Components (5)Instructions for Use (7)CAUTIONS (8)Contraindications (8)Warnings (8)Measuring device (ATP-C130) and the App (AT-Note) (9)Conditions for Use and Storage (10)How to Use the Device (ATP-C130) (11)Instructions for Operating and Attaching the Device (ATP-C130) (11)Instructions for Installing the App (AT-Note) (15)Specifications (17)Product Disposal (18)Labeling and Packaging (19)Labeling (19)Packaging (21)How to Use the AT-Note App (22)Screen with the App (AT-Note) Icon & Initial Run Screen (22)Connect to Device Window (23)Main Screen (24)LIVE Display Screen (25)RECORD Screen (27)Symptom Note Entry Screen (28)Symptom Note Details Screen (30)Symptom Note Revision Screen (32)Viewing Recorded Data (34)AT-Patch User Manual︱34︱AT-Patch User Manual Product DescriptionsThis product (ATP-C130) is a patch-type ECG device that measures thepotential differences transmitted to the surface of the body from the actionpotential generated from the activated myocardium. By attaching electrodes oncertain sites, it displays, stores, and records the measured ECG data.Intended Purpose► ATP-C130 is intended to measure, analyze, and report electrocardiogram (ECG) information forlong-term monitoring (up to 14 days) by attaching to the skin surface. It is used for patients withheart disease such as arrhythmia or patients with suspected heart disease. Reported ECG metrics include single lead analysis in beats, heart rate measurement and rhythm analysis. Used bypatients as prescribed by physician or medical personnel.► Target Treatment group• asymptomatic or who may suffer from transient symptoms such as palpitations, shortness ofbreath, dizziness, light-headedness, pre-syncope, syncope, fatigue, or anxiety and patients who are asymptomatic► Target User • physician or medical personnelClassification : Electrocardiographic Holter AnalysisProduct Name (Model Number): AT-Patch (ATP-C130)Manufacturer : ATsens Co., Ltd.Head Office : (13558) KINS TOWER 301, 8, Seongnam-daero331beon-gil, Bundang-gu, Seongnam-si, Gyeonggi-do, Republic ofKoreaFactory : (13637) Point Town 803, 11, Gumi-ro, Bundang-gu,Seongnam-si, Gyeonggi-do, Republic of KoreaContact : Tel. +82-70-5220-0220/Fax. +82-70-8270-0738Authorized Representative• Name: CMC Medical Devices & Drug S.L.• Address: C/Horacio Lengo n18 C.P 29006 Málaga-Spain• Tel.: +34 951 214 054• E-mail:**************************Product Descriptions ︱ComponentsAT-Patch User Manual ︱5Components■ Device Components► Basic Components AT-Patch (ATP-C130) Pad Paper Sealing Bag Quick GuideSymptom NoteGift BoxFigure 1.1 AT-Patch Basic ComponentsProduct Descriptions ︱Components6︱AT-Patch User Manual► Accessories & PC S/W (AT-Report) – Separate saleAccessory. Dedicated USBcable PC S/W(AT-Report) USB Memory BLE DongleOur dedicated cable thatconnects the device with PC S/W for the purpose oftransmitting the ECG datarecorded in the device toPC S/W. It is connected viathe USB Port located onthe side of the device.A USB memory stick for storing the PC S/W installation file to be provided to the users. A product with a test report or a certificate issued by national or accredited offices is used. A dedicated BLE dongle used when connecting thedevice with PC S/Wthrough BLE connection. A product with a test report ora certificate issued by national or accredited offices is used.■ AppFor Android™ users : Google play™ (https:///store )For iPhone ® users: App Store SM (https:///ios/app-store/)► Please search "AT-Note", "ATsens" in Google Play™ Store or App Store SM .► Download the App.► Perform the registration step, then start using the App.Supports: Android 5.0 or later / iOS 11.0 or laterProduct Descriptions︱Instructions for Use■PC S/W►USB provided: Storage size of 4 GB or greater►Minimum requirements (PC)Instructions for Use►ATP-C130 is a device that measures, records, and stores the data from one ECG channel, and transmits the measured data using wireless communication (Bluetooth) to be displayed on the App and the PC S/W.►Data to be recorded•ECG Signal•3-axis Data•Temperature data of Device•Heart rateAT-Patch User Manual︱7CAUTIONSContraindications►DO NOT use if you have current symptoms or medical history of skin cancer, rash, dermatosis, keloids, wounds, etc.Warnings►This product is for single use only. Reuse is prohibited. Reusing it may lead to malfunction and inaccurate results.►DO NOT attach to any other place than the recommended bodily location of application.►Only authorized technicians are allowed to repair or disassemble ATP-C130.►Make sure to be fully aware of how to use the product, through sufficient training, before using it.►Avoid use at locations where wireless communication interference may occur (e.g., places where metallic hardware or electronic devices are frequently found).►This product cannot be simultaneously used with a defibrillator.►DO NOT expose to strong electromagnetic fields.►Product disposalDisposal of ATP-C130 and battery must comply with local waste disposal regulations. Non-compliance with waste disposal regulations may result in environmental pollution.NOTE: The data stored within the device must be taken care of before disposal.8︱AT-Patch User ManualCAUTIONS ︱Measuring device (ATP-C130) and the App (AT-Note)AT-Patch User Manual ︱9Measuring device (ATP-C130) and the App (AT-Note)■ Precautions► Since improper application and use of the sensor may result in inaccurate measurements, pleaseavoid:• Excessive movement on the patient's part• Application outside the recommended bodily locations• To prevent signal abnormalities due to the state of the patient's skin, sufficient notice of use froma medical specialist must be obtained before use.► The following persons should consult a physician before using the device.• Patients with sensitive skin or skin allergy• Patients with wounds on the skin that contact the device• Pregnant women, breastfeeding mothers, infants or children• Patients with pacemakers, defibrillators, or other implantable electronic devices► Take caution to avoid getting liquid in the device, and also avoid the following:(Dustproof and waterproof grade IP57)• Long-term exposure to water such as baths, swimming, etc.► Avoid letting the device come into contact with organic compounds like thinners or benzene. ► Beware of strong shocks and vibrations.► Once the product is detached from the body, do not reattach it.► The smartphone on which the App is run must be one with a test report or a certificate issued bynational or accredited offices.CAUTIONS︱Conditions for Use and StorageConditions for Use and Storage■Conditions for Use►Temperature range: 10℃ ~ 45℃►Relative humidity range: 10% ~ 95%, non-condensing ►Atmospheric range: 700hPa ~ 1060hPa►Dustproof and waterproof grade: IP57■Conditions for Storage►Temperature range: -20℃ ~ 55℃►Relative humidity range: 0% ~ 95%, non-condensing ►Atmospheric range: 700hPa ~ 1060hPa10︱AT-Patch User ManualHow to Use the Device (ATP-C130)Instructions for Operating and Attaching the Device (ATP-C130)Figure 1.2 External appearance of the device, USBTable 1.1 Table describing the external appearance of the device (ATP-C130)How to Use the Device (ATP-C130)︱Instructions for Operating and Attaching the Device (ATP-C130)■Instructions for Operating the Device (ATP-C130)①The device (ATP-C130) is initially packaged in Sleep Mode and delivered to the customer. Patientwho wishes to attach the device should press the Power Button, #❸ in [Figure 1.2], for 3 seconds, upon which the green LED blinks twice and a long “beep” sound occurs once. The device is now in Active Mode.②Once the device (ATP-C130) is attached and connected to the App (AT-Note), it begins storingmeasured ECG signals in the internal memory. The device continues to store the ECG signals for the duration of use, and automatically goes into Sleep Mode after use. NOTE: If there is no App or AT-Report (PC S/W) Hookup connection for about 8 minutes after Active Mode is on, then thedevice goes into Sleep Mode following a single red LED blink and three “beep-- bebeep--” sounds.•During the initial connection process, the connection between the device (ATP-C130) and AT-Report (PC S/W) Hookup or the App must be established at least once. Otherwise, the connection process is terminated as described in ②, and the device will not operate normally. After the initial connection is established, ECG measurement is performed normally even if AT-Report (PC S/W) Hookup or the Bluetooth paring for the App is terminated for some reasons.- The device cannot be used with a PC or smartphone that does not support Bluetooth.•The working status of the device (ATP-C130) can only be confirmed through the App's real-time live monitoring or AT-Report (PC S/W) Hookup.•Once the initial one-time connection is confirmed, ATP-C130 is not terminated for the duration of use (14 days).- Physically turning the power off is not possible. Automatic Power-Off will occur after the duration of use (14 days) has elapsed.- In case the buzzer or the Red LED blink was missed after ATP-C130's duration of use has passed, the App or AT-Report (PC S/W) Hookup can be used for confirmation.How to Use the Device (ATP-C130)︱Instructions for Operating and Attaching the Device (ATP-C130)■ Instructions for Attaching the Device on the Body (ATP-C130)► State of the skin before attachmentAn area larger than the device (ATP-C130) attachment area needs to be cleaned on the patient's skin. If body hair is abundant in the attachment area, shaving will be required to remove the hair. NOTE: If a wound or bleeding occurs when removing body hair, the device should be attached after the bleeding stops.As demonstrated in the "confirm patchattachment site" figure ❶, place the end ofthe patch about a finger's distance below theclavicle, and confirm the attachment site at a45-degree angle. If necessary, remove possible obstructions like hair using a razor, etc. as shown in the "shave the patch attachment site" figure ❷.Figure 1.3 Attachment preparation step– Confirming attachment siteTo produce the accurate ECG signals, clean the attachment area using alcohol swabs to remove any possible obstructions such as dead skin cells, etc. from the skin surface. Then, fully dry the skin for at least one minute before attaching the device (ATP-C130).Cleansing the patch attachment site with alcoholAs illustrated in Figure ❸, cleanse the attachment site to remove dead skin cells and possible obstructions by wiping horizontally, vertically and diagonally with alcohol cottons or swabs. Then, fully dry for at least one minute to make sure no alcohol is left on the surface.Figure 1.4 Attachment preparation step – Removing possible obstructions from the attachment siteHow to Use the Device (ATP-C130)︱Instructions for Operating and Attaching the Device (ATP-C130)►Attaching the device to the bodyAfter pressing the device (ATP-C130) Power Button, attach as followsFigure 1.5 How to attach ATP-C1301. As shown in [Figure 1.5] ❶, remove the tape designed to protect the patch side. Once theprotective tape is removed, attach the device to the body.2. As shown in [Figure 1.5] ❷, attach the device so that it is tilted toward the left nipple area, usingthe line in the middle between the two clavicles as the center. However, if the patient has a fullerchest or if diagonally attaching the device is difficult, the part directed toward the nipple should beraised a bit higher and then attached.3. As shown in [Figure 1.5] ❸, remove the bottom protective tape from the ECG Patch, then applyeven pressure on the attached the ECG Patch.How to Use the Device (ATP-C130)︱Instructions for Installing the App (AT-Note) Instructions for Installing the App (AT-Note)►Android™ users can download App (AT-Note) from Google play™ (https:///store) on Android™ Market. [Figure 1.6] demonstrates the installation steps.Figure 1.6 Installing the App – Android1. As shown in [Figure 1.6] ❶, search for either AT-Note, ATsens, AT-Patch in the Android™ marketGoogle Play™ (https:///store) search field.2. As shown in [Figure 1.6] ❷, click Install to download and install the App once the search result hasreturned AT-Note.3. As shown in [Figure 1.6] ❸, click Open to run the App when the installation is completed.4. Once the AT-Note icon appears on the smartphone screen as shown in [Figure 1.6] ❹, theinstallation has been successfully completed.5. After installation, use according to How to Use the AT-Note App.How to Use the Device (ATP-C130)︱Instructions for Installing the App (AT-Note)►For iPhone users (iPhone®), App (AT-Note) can be downloaded from App Store SM (https:///ios/app-store/) in the iOS Store. [Figure 1.7] demonstrates the installation steps.Figure 1.7 Installing the App – iOS1. As shown in [Figure 1.7] ❶, search either AT-Note or ATsens in the iOS App Store SM(https:///ios/app-store/) search field.2. As shown in [Figure 1.7] ❷, click Install to download and install the App once the search result hasreturned AT-Note.3. As shown in [Figure 1.7] ❸, click Open to run the App when the installation is completed.4. Once the AT-Note icon appears on the smartphone screen as shown in [Figure 1.7] ❹, theinstallation has been successfully completed.5. After installation, use according to How to Use the AT-Note App.How to Use the Device (ATP-C130)︱Specifications Specifications■ATP-C130 SpecificationsApp (AT-Note) / PC S/W (AT-Report): The smartphone and PC used must be one with a test report or a certificate issued by national or accredited offices.Product Disposal►This product is a medical device for single use only. Reuse is prohibited.►Disposal of ATP-C130 and battery must comply with local waste disposal regulations. Non-compliance with waste disposal regulations may result in environmental pollution.Labeling and PackagingLabeling■Package Label■Explanation of Visual Symbols of LabelLabeling and Packaging︱Packaging Packaging■Basic Components■PC S/W & AccessoriesHow to Use the AT-Note App︱Screen with the App (AT-Note) Icon & Initial Run ScreenHow to Use the AT-Note AppAT-Note is a smartphone APP (Android / iOS) that controls AT-Patch wirelessly (Bluetooth) and provides ECG data output transmitted from AT-Patch in real time. The 3-axis sensor measures and records rapid movements of the patient or user. The 3-axis sensor checks the magnitude of the movements by detecting speed changes in the X, Y, and Z axes measured through a single acceleration sensor, and displays the measured data in a two-dimensional form.Screen with the App (AT-Note) Icon & Initial Run ScreenFigure 1.8 AT-Note_App icon installed & intro screenTable 1.2How to Use the AT-Note App︱Connect to Device Window Connect to Device WindowFigure 1.9 Initial & in-progress screen for connecting to the deviceTable 1.3How to Use the AT-Note App︱Main ScreenMain ScreenFigure 1.10 AT-Note initial Main ScreenTable 1.4How to Use the AT-Note App︱LIVE Display Screen LIVE Display ScreenFigure 1.11 Live display screen (left) & zoomed in ECG graph section (top right) &zoomed in 3-axis data graph section (bottom right)How to Use the AT-Note App︱LIVE Display ScreenTable 1.5How to Use the AT-Note App︱RECORD Screen RECORD ScreenFigure 1.12 Screen displayed after the Record button is clickedUpon tapping the Record icon in the left screen of the [Figure 1.12] above, the Record icon is replaced with the Stop icon and recording begins, with the recording time displayed to the right of the Stop icon.How to Use the AT-Note App︱Symptom Note Entry ScreenSymptom Note Entry Screen■Making Symptom Note Entries Using the App (AT-Note) The screens in [Figure 1.13] shows the steps of making Symptom Note entries using the App in order.Upon tapping the Make Symptom Note Entry icon on the lower right side in the Main Screen (i.e. the first screen on the far left in [Figure 1.13]), the initial screen for Symptom Note entry is displayed. TheSymptom Note entry is entered in the order of: date, time of occurrence of given symptom, type of symptom, activity status, and other opinions. Once a Symptom Note entry is made, the list of Symptom Note entered is displayed in the main page.Figure 1.13 Screen Showing the Process for Making Symptom Note entries using the AppTable 1.6How to Use the AT-Note App︱Symptom Note Entry Screen■Making Symptom Note Entries Using the Device (AT-Patch) Below [Figure 1.14] is the symptom note registration screen using the device. Once the Power icon on the device is pressed for about 0.2 seconds, the relevant information is transmitted wirelessly (viaBluetooth) to the App, and the App receives the event information from the device. As shown in the screen on the right, a dialog box is displayed to ask whether to record the symptoms immediately in a pop-up window. If the Later icon is tapped, the Symptom Note entry count on the main page increases, but no new screen shows up. Once "Write symptoms" is tapped, the first screen for making Symptom Note entry is displayed.Press for about 0.2 secondsFigure 1.14 Making Symptom Note entries using the device (AT-Patch)How to Use the AT-Note App︱Symptom Note Details ScreenSymptom Note Details Screen■Viewing Details for Symptom Note Entries Made Using the App (AT-Note)By tapping the registered Symptom Note details icon in the Main Screen, the screen listing the registered Symptom Note for a Day number of using the App is displayed as shown in [Figure 1.15]. The registered Symptom Note entry list for a Day number of using the App is briefly displayed, as seen in the redrectangular section. Once the red rectangular section is tapped, the details screen for one case of the Symptom Note shows up.Figure 1.15 Details screen for Symptom Note entries made using the AppTable 1-7How to Use the AT-Note App︱Symptom Note Details Screen ■Viewing Details for Symptom Note Entries Made Using the Device (AT-Patch)When Symptom Note entry is made using the device, the time of the event, as seen in the redrectangular section in [Figure 1.16], is displayed with only the symptom start time. All other content hasn't been set yet. Because the Symptom Note entry is incomplete, the Symptom Note entry completion status is displayed in black. By tapping on the red rectangular section, other items excluding the symptom start time can be confirmed.Figure 1.16 Details screen for Symptom Note entries made using the device (AT-Patch)AT-Patch User Manual︱31How to Use the AT-Note App︱Symptom Note Revision ScreenSymptom Note Revision ScreenThe top left screen from the [Figure 1.17] below shows the details screen for a single entry of Symptom Note, with the revision icon or revision icon area for each item indicated. Upon tapping each revision icon or revision icon area, the previously selected values for the items are displayed on the screen. Since there are no values set for each of the items except for the symptom occurrence start time regarding entries registered in the Symptom Note through the device, they have to be entered by tapping the revision icon or revision icon area.Figure 1.17 Symptom Note revision screen32︱AT-Patch User ManualHow to Use the AT-Note App︱Symptom Note Revision ScreenTable 1.8AT-Patch User Manual︱33How to Use the AT-Note App︱Viewing Recorded DataViewing Recorded DataAs shown in the red rectangular section, the recording data can be accessed through the screen that lists the registered Symptom Note entries for a Day number of using the App. The ECG recording data does not include Symptom Note contents, only ECG data. The ECG recording data viewing screen is displayed upon tapping the red rectangular section.Figure 1.18 ECG and 3-axis recording data viewing screen34︱AT-Patch User ManualHow to Use the AT-Note App ︱Viewing Recorded DataAT-Patch User Manual ︱35Table 1.936︱AT-Patch User Manual。
Storage Center Drive 固件更新.pdf_1701111535.6345294说明
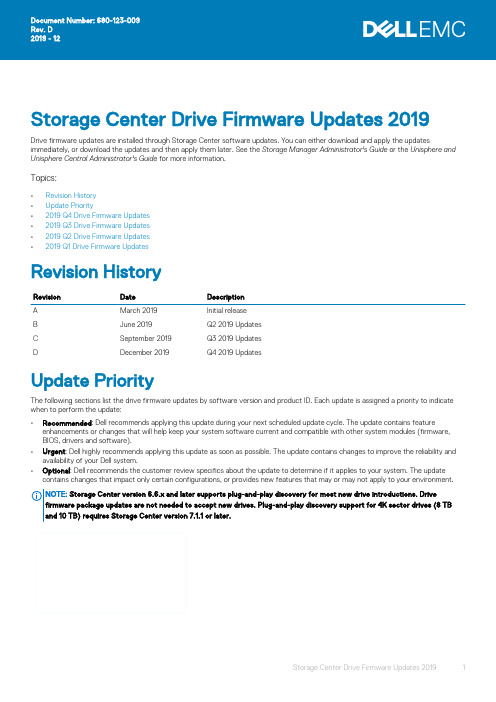
Storage Center Drive Firmware Updates 2019Drive firmware updates are installed through Storage Center software updates. You can either download and apply the updates immediately, or download the updates and then apply them later. See the Storage Manager Administrator's Guide or the Unisphere and Unisphere Central Administrator's Guide for more information.Topics:•Revision History•Update Priority•2019 Q4 Drive Firmware Updates•2019 Q3 Drive Firmware Updates•2019 Q2 Drive Firmware Updates•2019 Q1 Drive Firmware UpdatesRevision HistoryRevision Date DescriptionA March 2019Initial releaseB June 2019Q2 2019 UpdatesC September 2019Q3 2019 UpdatesD December 2019Q4 2019 UpdatesUpdate PriorityThe following sections list the drive firmware updates by software version and product ID. Each update is assigned a priority to indicate when to perform the update:•Recommended: Dell recommends applying this update during your next scheduled update cycle. The update contains feature enhancements or changes that will help keep your system software current and compatible with other system modules (firmware, BIOS, drivers and software).•Urgent: Dell highly recommends applying this update as soon as possible. The update contains changes to improve the reliability and availability of your Dell system.•Optional: Dell recommends the customer review specifics about the update to determine if it applies to your system. The update contains changes that impact only certain configurations, or provides new features that may or may not apply to your environment.Storage Center version 6.6.x and later supports plug-and-play discovery for most new drive introductions. DriveThe 2019 Q4 firmware update package contains drive firmware updates for the following versions of Storage Center:•Version 7.4.2•Version 7.3.20•Version 7.2.51Drive Firmware UpdatesThe following table lists the drive firmware updates for this software release. These updates represent Dell’s latest qualification versions.Product ID (SAS Drives)Existing FirmwareVersionNew FirmwareVersionPriority CommentsHUS728T8TAL4204RF01RF03Recommended Ongoing firmware improvements HUS726T6TAL5204PF02PF03Recommended Ongoing firmware improvements ST900MP0136KP74KP79Recommended Ongoing firmware improvements ST900MP0166KMT4KMT9Recommended Ongoing firmware improvements ST600MP0006KL34KL37Recommended Ongoing firmware improvements ST300MP0006ST600MP0026KPC4KPC7Recommended Ongoing firmware improvements ST2400MM0159SF73SF78Recommended Ongoing firmware improvements ST2400MM0149SF13SF18Recommended Ongoing firmware improvements DL1800MM0129SE23SE28Recommended Ongoing firmware improvements ST1800MM0149SEE3SEE8Recommended Ongoing firmware improvements ST600MM0009SE03SE06Recommended Ongoing firmware improvements ST1200MM0009ST1200MM0069SEC3SEC6RecommendedOngoing firmware improvementsMZILT960HAHQ0D4CSF8CSFARecommendedOngoing firmware improvementsMZILT1T9HAJQ0D4MZILT3T8HALS0D4MZILT7T6HMLA0D4MZILT15THMLA0D4ST6000NM0285DEE4DEE5Recommended Ongoing firmware improvements ST10000NM0598N/A REN6Optional New product release ST12000NM0158ST10000NM0608N/AREH6OptionalNew product releaseThe 2019 Q3 firmware update package contains drive firmware updates for the following versions of Storage Center:•Version 7.4.2•Version 7.3.20•Version 7.2.51Drive Firmware UpdatesThe following table lists the drive firmware updates for this software release. These updates represent Dell’s latest qualification versions.Product ID (SAS Drives)Existing FirmwareVersionNew FirmwareVersionPriorityCommentsWUSTM3240ASS200F927F953RecommendedOngoing firmware improvementsWUSTM3280ASS200WUSTM3216ASS200WUSTR1548ASS200WUSTR1596ASS200WUSTR1519ASS200WUSTR1538ASS200ST1000NX0453NE03NE05RecommendedOngoing firmware improvementsST1200MM0027IEF9IEFA ST300MP0025VECB VECC Recommended Ongoing firmware improvements ST600MP0025ST1800MM0078TEEATEEBRecommendedOngoing firmware improvementsKPM5XMUG400G B11AB11CRecommendedOngoing firmware improvementsKPM5XMUG800G KPM5XMUG1T60KPM5XRUG480G KPM5XRUG960G KPM5XRUG1T92KPM5XRUG3T84KPM5WMUG1T60KPM5WRUG1T92KPM5WRUG3T84KPM5WMUG1T60B412B414RecommendedOngoing firmware improvementsKPM5WMUG1T92KPM5WMUG3T84ST8000NM0065PE45PE47RecommendedOngoing firmware improvementsST2000NM0045DE05DE07RecommendedOngoing firmware improvementsST3000NM0025ST4000NM0025Product ID (SAS Drives)Existing FirmwareVersionNew FirmwareVersionPriority CommentsST6000NM0095DE24DE26Recommended Ongoing firmware improvements ST4000NM0005ME05ME07Recommended Ongoing firmware improvements ST6000NM0034ME2C ME2D Recommended Ongoing firmware improvements HUH721008AL4204LF12LF17Recommended Ongoing firmware improvements HUH721010AL4200LR12LX17Recommended Ongoing firmware improvements HUH721212AL4N/ANR05OptionalNew product release2019 Q2 Drive Firmware UpdatesThe 2019 Q2 firmware update package contains drive firmware updates for the following versions of Storage Center:•Version 7.3.11•Version 7.2.51Drive Firmware UpdatesThe following table lists the drive firmware updates for this software release. These updates represent Dell’s latest qualification versions.Product ID (SAS Drives)Existing FirmwareVersionNew FirmwareVersionPriorityCommentsHUS726020ALS214KE31KE40Recommended Ongoing firmware improvements HUS726040ALS214HUS726060AL5214KF37KX40RecommendedOngoing firmware improvementsHUC101860CSS204FE39FE40RecommendedOngoing firmware improvementsHUC101890CSS204HUC101812CSS204HUC101818CS4204FF39FF40Recommended Ongoing firmware improvements HUC156030CSS204EE39EE40RecommendedOngoing firmware improvementsHUC156060CSS204ST300MP0005VE0CVE0ERecommendedOngoing firmware improvementsST450MP0005ST600MP0005ST600MM0006LE0B LE0D Recommended Ongoing firmware improvements ST900MM0006ST1200MM0108TEC9TECARecommendedOngoing firmware improvementsPX05SRB048Y AU09AU0BRecommendedOngoing firmware improvementsPX05SRB096Y PX05SRB192Y PX05SRB384Y PX05SMB040Y PX05SMB080Y PX05SMB160Y2019 Q1 Drive Firmware UpdatesThe 2019 Q1 firmware update package contains drive firmware updates for the following versions of Storage Center software:•Version 7.3.6•Version 7.2.51•Version 6.7.50Drive Firmware UpdatesThe following table lists the drive firmware updates for this software release. These updates represent Dell’s latest qualification versions,and are general firmware updates (including ongoing improvements) unless otherwise noted in the comments.Product ID (SAS Drives)Existing FirmwareVersionNew FirmwareVersionPriorityCommentsKPM5XMUG400G N/AB11AOptionalNew product releaseKPM5XMUG800G KPM5XMUG1T60KPM5XRUG480G KPM5XRUG960G KPM5XRUG1T92KPM5XRUG3T84KPM5WMUG1T60N/AB412OptionalNew product releaseKPM5WRUG1T92KPM5WRUG3T84WUSTM3240ASS200N/AF927OptionalNew product releaseWUSTM3280ASS200WUSTM3216ASS200WUSTR1548ASS200WUSTR1596ASS200WUSTR1519ASS200WUSTR1538ASS200MZILT960HAHQ0D4CSF7CSF8RecommendedOngoing firmware improvementsMZILT1T9HAJQ0D4MZILT3T8HALS0D4MZILT7T6HMLA0D4MZILT15THMLA0D4ST600MM0088TE0CTE0DRecommendedOngoing firmware improvementsST900MM0168ST1200MM0088ST1800MM0018TE2B TE2C Recommended Ongoing firmware improvements ST91000640SS AE11AE13Recommended Ongoing firmware improvements PX05SMQ160B AY06AY08RecommendedOngoing firmware improvementsPX05SRQ384BProduct ID (SAS Drives)Existing FirmwareVersion New FirmwareVersion Priority CommentsST1200MM0007IE07IE09Recommended Ongoing firmware improvements ST9146853SSYE0F YE0H Recommended Ongoing firmware improvements ST9300653SS© 2018 - 2019 Dell Inc. or its subsidiaries. All rights reserved. Dell, EMC, and other trademarks are trademarks of Dell Inc. or its subsidiaries. Other trademarks may be trademarks of their respective owners.。
AC升级 、AP升级及形态切换

作业:1.AP5030DN由FIT形态切换到FAT形态。
2.AP5130DN升级(AC模式)。
3.AC6605由升级到AC6605V200R006C10SPC103TB701验证升级成功后再会退到FIT形态切换到FAT形态以AP5030DN使用命令行切换形态为例1.使用串口线将AP的串口和PC的串口相连,使用“超级终端”等软件,进入命令行界面。
2.升级前可执行命令display version查看当前AP版本。
3.执行命令ap-mode-switch prepare,准备形态切换。
AP切换到image A文件启动<Huawei> system-view[Huawei] ap-mode-switch prepare[Huawei] display imageImage Status Version==============================================================Image A (Active) AP5X30XN V200R005C00SPC100B023(FIT)Image B (Backup) AP5X30XN V200R005C00SPC100B020(FIT)==============================================================[Huawei] ap-mode-switch checkInfo: Ap-mode-switch check ok.4.执行命令ap-mode-switch check,确认形态切换已准备完成。
5.FTP方式升级[ftp] binary200 Type is Image (Binary)[ftp] ap-mode-switch ftp FatAP5X30XN_V200R006C10SPC800.bin 192.168.10.11 admin admin123 #Warning: Do Not Power-off.........Info: Upgrade upgrade-assistant-package successfully!Warning: System will reboot, if you want to switch to upgrade-assistant-package.Are you sure to execute these operations ? [Y/N]: y6.AP自动重启并升级。
自动升级工具(AUT)发布说明 December 2012 v9.3.2说明书

Automated Upgrade ToolAUT Release Notesv9.3.2Part No. E28708-01December 2012Copyright and TrademarksCopyright © 1995, 2012, Oracle and/or its affiliates. All rights reserved.This software and related documentation are provided under a license agreement containing restrictions on use and disclosure and are protected by intellectual property laws. Except as expressly permitted in your license agreement or allowed by law, you may not use, copy, reproduce, translate, broadcast, modify, license, transmit, distribute, exhibit, perform, publish or display any part, in any form, or by any means. Reverse engineering, disassembly, or decompilation of this software, unless required by law for interoperability, is prohibited.The information contained herein is subject to change without notice and is not warranted to be error-free. If you find any errors, please report them to us in writing.If this software or related documentation is delivered to the U.S. Government or anyone licensing it on behalf of the U.S. Government, the following notice is applicable:U.S. GOVERNMENT RIGHTSPrograms, software, databases, and related documentation and technical data delivered to U.S. Government customers are "commercial computer software" or "commercial technical data" pursuant to the applicable Federal Acquisition Regulation and agency-specific supplemental regulations. As such, the use, duplication, disclosure, modification, and adaptation shall be subject to the restrictions and license terms set forth in the applicable Government contract, and, to the extent applicable by the terms of the Government contract, the additional rights set forth in FAR 52.227-19, Commercial Computer Software License (December 2007). Oracle USA, Inc., 500 Oracle Parkway, Redwood City, CA 94065.This software is developed for general use in a variety of information management applications. It is not developed or intended for use in any inherently dangerous applications, including applications which may create a risk of personal injury. If you use this software in dangerous applications, then you shall be responsible to take all appropriate fail-safe, backup, redundancy and other measures to ensure the safe use of this software. Oracle Corporation and its affiliates disclaim any liability for any damages caused by use of this software in dangerous applications.Oracle and Java are registered trademarks of Oracle Corporation and/or its affiliates. Other names may be trademarks of their respective owners.This software and documentation may provide access to or information on content, products and services from third parties. Oracle Corporation and its affiliates are not responsible for and expressly disclaim all warranties of any kind with respect to third party content, products and services. Oracle Corporation and its affiliates will not be responsible for any loss, costs, or damages incurred due to your access to or use of third party content, products or services. The RMW product includes software developed by the Visigoth Software Society.C ONTENTSCopyright and Trademarks (2)Chapter 1 Agile PLM Automated Upgrade Tool (1)Downloading the Software (1)Maintenance and Updates (2)Chapter 2 What's New (1)Supported Agile PLM Upgrade Paths (1)Merged Hotfixes (2)Supported Agile Advantage Upgrade Paths (3)Resolved Issues (3)Known Issues (3)Check Snap Material Views Utility Runs Twice (3)Existing Dashboards No Longer Work (3)Upgrade Criteria Contains All Is Changed to Contains Any (3)Markup Restrictions Not Retained on Upgrade (3)Performance Issue - Delete SQL for Notification fields (3)AUT Throws Error if Destination Version is 9.2 or 9.2.x (4)PrefaceOracle's Agile PLM documentation set includes Adobe® Acrobat PDF files. The Oracle Technology Network (OTN) Web site /technetwork/documentation/agile-085940.html contains the latest versions of the Agile PLM PDF files. You can view or download these manuals from the Web site, or you can ask your Agile administrator if there is an Agile PLM Documentation folder available on your network from which you can access the Agile PLM documentation (PDF) files.Note To read the PDF files, you must use the free Adobe Acrobat Reader version 9.0 or later.This program can be downloaded from the Adobe Web site .The Oracle Technology Network (OTN) Web site/technetwork/documentation/agile-085940.html can be accessed through Help > Manuals in both Agile Web Client and Agile Java Client. If you need additional assistance or information, please contact My Oracle Support (https://) for assistance.Note Before calling Oracle Support about a problem with an Agile PLM manual, please have the full part number, which is located on the title page.TTY Access to Oracle Support ServicesOracle provides dedicated Text Telephone (TTY) access to Oracle Support Services within the United States of America 24 hours a day, 7 days a week. For TTY support, call 800.446.2398. Outside the United States, call +1.407.458.2479.ReadmeAny last-minute information about Agile PLM can be found in the Readme file on the Oracle Technology Network (OTN) Web site /technetwork/documentation/agile-085940.html.Agile Training AidsGo to the Oracle University Web page/education/chooser/selectcountry_new.html for more information on Agile Training offerings.Accessibility of Code Examples in DocumentationScreen readers may not always correctly read the code examples in this document. The conventions for writing code require that closing braces should appear on an otherwise empty line; however, some screen readers may not always read a line of text that consists solely of a bracket or brace.This documentation may contain links to Web sites of other companies or organizations that Oracle does not own or control. Oracle neither evaluates nor makes any representations regarding the accessibility of these Web sites.Chapter 1 Agile PLM Automated Upgrade Tool This chapter includes the following:▪Downloading the Software (1)▪Maintenance and Updates (2)▪What's New (1)▪Resolved Issues (3)▪Known Issues (3)The Automated Upgrade Tool (AUT) upgrades your Agile PLM database using the inputs you provide in a property file. It completes the upgrade using your existing database as the source database, and the newly created database as the destination database. For detailed information on the upgrade process using the AUT, refer to the Agile PLM Database Upgrade Guide. Downloading the SoftwareThe Automated Upgrade Tool is distributed with each Agile major release and subsequent service pack releases. The software can be downloaded from Oracle Software Delivery Cloud, or My Oracle Support.To download the software from Oracle Software Delivery Cloud():1. On the Oracle Software Delivery Cloud Welcome page, choose your language and clickContinue.2. Enter required information on the Export Validation screen and click Continue.3. On the Search screen, select Oracle Agile Applications in the Select a Product Pack drop-down listbox. Select a platform value. Click Go.4. Links to applicable Agile release downloads display. Select the appropriate link. Click Continue.5. The Download screen displays release parts that can be downloaded, including customerguides. Click Download for the appropriate media pack.6. Extract the contents of the media pack. The Agile PLM Database Installer is included with theAgile PLM software.7. To download the database installer, navigate to the DB_Installer folder. DB installers for allplatforms are made available within the DB_Installer folder, regardless of the operating system on which you have chosen to install Agile PLM.8. To download the AUT software, navigate to the AUT folder within the Deployment_Tools folder.From the AUT folder, extract the contents of the AUT.zip file to your destination database server.After the AUT is extracted, all of the files are located in an AUT directory on the local drive. In this document, this directory is referred to as the AUT_HOME.AUT Release NotesTo download only the AUT software from My Oracle Support (https://):1. Log in to My Oracle Support.2. Under Patches & Updates, click Product or Family (Advanced Search).1. Select the Include all products in a family checkbox.2. Enter the following search parameters:▪Product : Oracle Agile Applications▪Release : Agile PLM Tools 9▪Platform : Select the appropriate platform, for example, Microsoft Windows (32-bit).3. Click Search.4. Links to Averify and AUT are displayed in the search results.5. Select the Patch ID and click Download.3. From the Patchset zip file, extract the contents of the AUT.zip file to your destination databaseserver. After the AUT is extracted, all of the files are located in an AUT directory on the local drive. In this document, this directory is referred to as the AUT_HOME.Maintenance and UpdatesBefore you upgrade your database, you should always make sure you are using the latest version of the AUT. Changes to scripts such as averify may occur after the initial version has been released. To ensure your database is correctly upgraded, always check the My Oracle Support (https://) web site for updates.Chapter 2 What's NewThis chapter includes the following:▪Supported Agile PLM Upgrade Paths (1)▪Supported Agile Advantage Upgrade Paths (3)This chapter introduces additional upgrade paths and enhancements in release 9.3.2. Supported Agile PLM Upgrade PathsUpgrade of your Agile PLM database to version 9.3.2 is supported from any of the earlier versions listed below:▫Agile 9.3.1.2▫Agile 9.3.1.1▫Agile 9.3.1▫Agile 9.3.0.2▫Agile 9.3.0.1▫Agile 9.3▫Agile 9.2.2.7▫Agile 9.2.2.6▫Agile 9.2.2.5▫Agile 9.2.2.4▫Agile 9.2.2.3▫Agile 9.2.2.2▫Agile 9.2.2.1▫Agile 9.2.2▫Agile 9.2.1.6▫Agile 9.2.1.5▫Agile 9.2.1.4▫Agile 9.2.1.3▫Agile 9.2.1.1▫Agile 9.2.1▫Agile 9.2.0.2AUT Release Notes▫Agile 9.2.0.1▫Agile 9.2▫Agile 9.1 SP1-SP4▫Agile 9.0 SP1-SP7▫Program Execution 8.5 SP2▫Product Service and Improvement 8.5 SP1-SP7▫Product Cost Management 8.5 SP1▫Product Collaboration 8.5 SP1-SP7Merged HotfixesUpgrade is supported from any of the hotfixes merged to 9.3.2 listed here: 9302HF1269302HF149931HF63931HF66931HF69931HF73931HF74931HF759311HF959311HF1069311HF1079311HF1179311HF1379311HF1389311HF1399311HF1539311HF1569311HF1629311HF1779311HF1789312HF49312HF69312HF7Chapter 2: Agile PLM Automated Upgrade Tool9312HF89312HF109312HF329312HF42Supported Agile Advantage Upgrade PathsUpgrade of your Agile Advantage (AA) database to version 9.3.2 is supported from the following version only:AA 2006Resolved IssuesThe list of service requests (SRs) resolved in this release is provided here for your reference. Known IssuesThe list of known issues as of this release is provided here for your reference, along with workarounds, if any.Check Snap Material Views Utility Runs TwiceWhen you upgrade with SourceEqualsDestination parameter set to FALSE, the Check Snap Material Views Utility runs twice.Existing Dashboards No Longer WorkWhen upgrading to Agile PLM 9.3.1.2, rows in CRITERIA, QUERY and SELECT_LIST tables associated with dashboard queries are deleted.Resolution: Do not delete dashboard query rows during the upgrade.Upgrade Criteria Contains All Is Changed to Contains AnyCorrect all schema change errors to fix this issue.Markup Restrictions Not Retained on UpgradeMarkup restrictions that were enforced through privileges are not retained when you upgrade. With the new security model implemented in 9.2.2.2, Markup is a subclass under the File Folders class and all markup privileges are automatically enabled. To prevent users from viewing or modifying the existing markups, you must disable blanket privileges at File Folders class level in Java Client and enable Markup privilege for relevant users only.Performance Issue - Delete SQL for Notification fieldsThe SQL script to clean up deleted notifications takes too long to run on very large databases.AUT Release NotesAUT Throws Error if Destination Version is 9.2 or 9.2.xIf you select 9.2, 9.2.1 or 9.2.2 as the destination version for the upgrade, the database upgrades successfully but Averify may not run, and the log file may report the following error "Source database version and selected upgrade destination versions are same. Please change thedest.version in aut.properties file."You can ignore the error as it does not affect the upgrade. Run Averify manually to check for other errors.。
清洁验证状态维护(PDA TR 49内容节选 中英文版)

清洁验证状态维护(PDA TR 49内容节选中英文版)8.0 maintenance of Validated state8.0 验证状态维护A key part of the validation life cycle for any system is maintenance of the validated state. This section deals with activities after the cleaning process has been designed and developed and after the formal validation protocols have been successfully executed. This is critical for cleaning validation, because a lapse in the validated state has the potential to adversely impact the quality, safety and purity of subsequent batches of the same or different products. The main tools for ensuring the continued maintenance of the validated state are change control, risk-based periodic monitoring and data trending review. Additionally, training and retraining are important areas of control for manual cleaning processes, as they are the primary mechanisms for controlling the cleaning cycle. In each of these three areas, knowledge of the design space (see Section 3.8) should be applied.验证状态维护是任何系统的验证生命周期的一个关键组成部分。
- 1、下载文档前请自行甄别文档内容的完整性,平台不提供额外的编辑、内容补充、找答案等附加服务。
- 2、"仅部分预览"的文档,不可在线预览部分如存在完整性等问题,可反馈申请退款(可完整预览的文档不适用该条件!)。
- 3、如文档侵犯您的权益,请联系客服反馈,我们会尽快为您处理(人工客服工作时间:9:00-18:30)。
What’s Changing – Section 6 ELEMENTS OF PROCESS SIMULATION TESTS
•Created Section 7 to discuss intervention identification and management • Recommend that the frequency of intervention during APS be related to the frequency of occurrence in production. •Recommend that the APS duration be long enough to stress the process, the supporting environment and the operators •Recommend that the number of units filled during each manual process simulation study represent the maximum production lot size. •Incubate for a minimum of 14 days unless supported by a validated approved alternative method (Rapid Methods)
8
What’s Changing – Section 2 RISK ASSESSMENT ADDITION
•A risk assessment may be performed to determine, identify, and rate the aseptic process steps and interventions, which can potentially adversely affect the sterility assurance of the product. •These process impacting steps and interventions should be included in the process simulation study. •Other steps and interventions which do not affect the sterility assurance of the product may be included in the study at the discretion of the company.
3
Definition of TR22
•Initial version published in 1996, replaces: •Technical Monograph No. 2, Validation of Aseptic Filling for Solution Drug Products, 1980; •Technical Report No. 6, Validation of Aseptic Drug Powder Filling Processes, 1984 •Provide a valuable guide to industry in the area of process simulation testing •Addresses the validation of aseptic processing during formulation and filling activities •An APS is a simulation of the entire aseptic formulation and filling process, which substitutes a microbiological growth medium for a sterile product.
• Interventions must be the focus of the discussion, because contamination is largely associated with them. • Aseptic process simulation, is not just media filling.
Байду номын сангаас
6
Purpose of the APS
•Demonstrate as part of an overall process validation approach, the capability of the aseptic process to produce sterile drug products. •Evaluate proficiency of aseptic processing personnel. •Comply with current Good Manufacturing Practice requirements. •Confirm the appropriateness of operating practices used in support of aseptic processing.
5
Important Points to Consider
• APS demonstrates capability, does not determine an SAL. • Interventions are either:
– Inherent – a integral part of the process – Corrective – performed to fix problems
11
What’s Changing – Section 6 ELEMENTS OF PROCESS SIMULATION TESTS
•Added Section for Unit Accountability and Reconciliation •Recommend an accurate count of integral media-filled containers be performed •An accurate unit count may be obtained by one of the following methods: •Use of a calibrated counter with demonstrated accuracy •A nested or divided tray configuration •A verified physical count •Complete unit accountability of the APS is the goal
PDA: A Global Association
1
Update on PDA TR22 Revisions for Aseptic Process Simulations
Anthony Pavell Associate Director, APP Pharmaceuticals
2
Agenda
•Definition TR22 •Why the revision •What’s Changing •Conclusions •Acknowledgements
7
What’s Changing – Section 2 PROCESS SIMULATION CONCEPTS AND PRINCIPLES
•No change to typical six month interval •Providing clarity around worst case conditions •Present a reasonable challenge to the system without forcing unintentional failure •Duration is equal to a maximum production run including •Shifts •Room/equipment time •Extremes of container sizes and rates
9
What’s Changing – Section 3 PROCESS SIMULATION TEST DOCUMENTATION
•Media fills do not support the filtration validation of the product / process being simulated, so differences in filtration area, filter media, etc are acceptable •Expanded content for aseptic compounding steps and recommend that processes requiring the addition of sterile powders employ an acceptable placebo material in containers identical to those utilized in the process being evaluated •Anaerobic media would be appropriate where strict anaerobic conditions are present •NOTE: The aseptic production of sterile bulk pharmaceuticals is addressed in PDA’s TR #28
4
Why the Revision
•Periodic Review – originally published in 1996 •Develop a modest revision / expansion of PDA TR#22, •Update / clarify coverage of interventions. •Address personnel participation in a meaningful and coherent fashion. •Include an accountability discussion. •Clarify application to aseptic steps in the drug compounding process. •Outline execution practice in greater detail. •Maintain consistency with regulatory guidance (especially FDA’s 2004 AP guide).