成型各工序工艺要求
流延成型的工艺要求
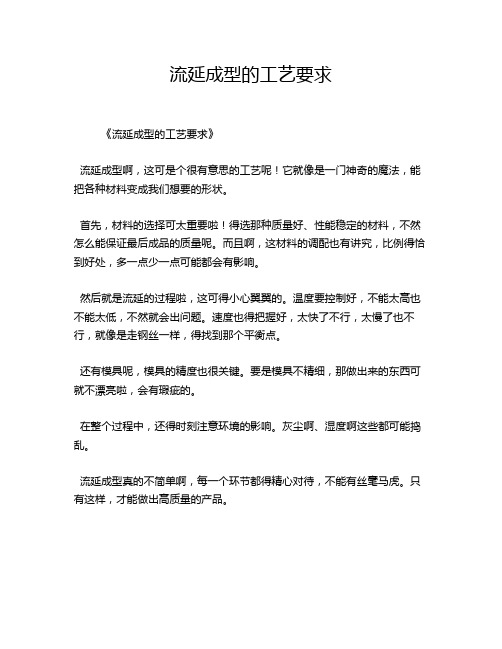
流延成型的工艺要求
《流延成型的工艺要求》
流延成型啊,这可是个很有意思的工艺呢!它就像是一门神奇的魔法,能把各种材料变成我们想要的形状。
首先,材料的选择可太重要啦!得选那种质量好、性能稳定的材料,不然怎么能保证最后成品的质量呢。
而且啊,这材料的调配也有讲究,比例得恰到好处,多一点少一点可能都会有影响。
然后就是流延的过程啦,这可得小心翼翼的。
温度要控制好,不能太高也不能太低,不然就会出问题。
速度也得把握好,太快了不行,太慢了也不行,就像是走钢丝一样,得找到那个平衡点。
还有模具呢,模具的精度也很关键。
要是模具不精细,那做出来的东西可就不漂亮啦,会有瑕疵的。
在整个过程中,还得时刻注意环境的影响。
灰尘啊、湿度啊这些都可能捣乱。
流延成型真的不简单啊,每一个环节都得精心对待,不能有丝毫马虎。
只有这样,才能做出高质量的产品。
橡胶模压成型工艺要求

橡胶模压成型工艺要求
在制造橡胶制品的过程中,橡胶模压成型是一种常用的工艺方法。
橡胶模压成型工艺要求严格,需要注意多个方面以确保产品质量和生产效率。
首先,选择合适的橡胶材料至关重要。
橡胶材料应该符合产品设计的要求,如耐磨、耐油、耐高温等性能。
同时,橡胶材料的硬度、粘度、流动性等参数也需要考虑到模压成型的实际情况。
其次,模具设计是影响产品质量的重要因素之一。
模具应该具有良好的设计,使得产品可以顺利脱模,避免气泡和瑕疵的产生。
模具的材质和表面处理也需要考虑到橡胶材料的特性,以确保成型后产品的表面光滑度和尺寸精度。
在橡胶模压成型的过程中,温度、压力和时间是关键的参数。
温度过高或过低都会影响橡胶材料的流动性和硬度,导致产品质量不稳定。
压力的控制要均匀,以确保橡胶材料能够填充模具的所有细节,避免出现空洞和变形。
成型时间的控制也需要精准,过长或过短都会对产品的性能产生影响。
另外,模具的维护和保养也是至关重要的。
定期清洁模具,检查有无损坏和磨损,确保模具表面平整度和精度。
及时更换老化的模具以避免对产品质量造成影响。
最后,对成型后的产品进行质量检验也是必不可少的环节。
检查产品的尺寸、外观和性能,确保符合设计要求。
如果发现产品有质量问题,需要及时调整模具和工艺参数,避免批量生产出现质量问题。
总的来说,橡胶模压成型工艺是一个需要综合考虑材料、模具设计、工艺参数、维护保养等多个方面因素的复杂过程。
只有严格按照要求操作,才能生产出高质量的橡胶制品。
1。
模压成型工艺条件要求有哪些
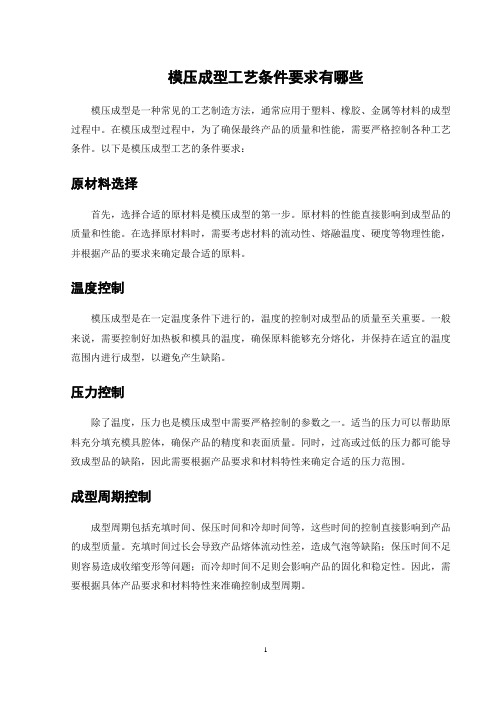
模压成型工艺条件要求有哪些模压成型是一种常见的工艺制造方法,通常应用于塑料、橡胶、金属等材料的成型过程中。
在模压成型过程中,为了确保最终产品的质量和性能,需要严格控制各种工艺条件。
以下是模压成型工艺的条件要求:原材料选择首先,选择合适的原材料是模压成型的第一步。
原材料的性能直接影响到成型品的质量和性能。
在选择原材料时,需要考虑材料的流动性、熔融温度、硬度等物理性能,并根据产品的要求来确定最合适的原料。
温度控制模压成型是在一定温度条件下进行的,温度的控制对成型品的质量至关重要。
一般来说,需要控制好加热板和模具的温度,确保原料能够充分熔化,并保持在适宜的温度范围内进行成型,以避免产生缺陷。
压力控制除了温度,压力也是模压成型中需要严格控制的参数之一。
适当的压力可以帮助原料充分填充模具腔体,确保产品的精度和表面质量。
同时,过高或过低的压力都可能导致成型品的缺陷,因此需要根据产品要求和材料特性来确定合适的压力范围。
成型周期控制成型周期包括充填时间、保压时间和冷却时间等,这些时间的控制直接影响到产品的成型质量。
充填时间过长会导致产品熔体流动性差,造成气泡等缺陷;保压时间不足则容易造成收缩变形等问题;而冷却时间不足则会影响产品的固化和稳定性。
因此,需要根据具体产品要求和材料特性来准确控制成型周期。
模具设计模具设计是模压成型中至关重要的一环。
合理的模具结构可以有效地避免产品缺陷的产生,保证产品的精度和表面质量。
在模具设计中,需要考虑成型品的结构、收缩率、流道设计等因素,确保原料能够充分填充模具,并在成型过程中保持稳定的形状。
综上所述,模压成型工艺条件的要求包括原材料选择、温度控制、压力控制、成型周期控制和模具设计等多个方面。
只有在严格控制这些条件的前提下,才能生产出质量优良的模压成型产品,满足客户的需求并提升企业的竞争力。
密封条成型工艺及生产工序简介

密封条成型工艺及生产工序简介密封条成型工艺及生产工序是指将原材料制成密封条产品的一系列工艺和过程。
下面是该过程的简介。
1. 原材料准备:选择适合的密封材料,如橡胶、硅胶或塑料,并进行初步加工,如切割成条状或片状。
2. 配方调制:根据产品要求,调配出合适的原材料配方,包括添加剂和填充材料,以提高密封条的性能和使用寿命。
3. 混炼:将原材料和配方中的添加剂混合,通过搅拌和热处理等方法,使原料充分混合,确保配方均匀。
4. 挤出成型:将混合好的原材料导入挤出机,通过挤压和模具形成带有密封条形状的连续胶条。
在挤出过程中可以加入压纹、纹理和标记等特殊要求。
5. 切割成型:将挤出的连续胶条切割成固定长度的密封条,可以采用刀切割或拉伸断裂等方法。
6. 成品检验:对切割好的密封条进行外观质量、尺寸精度和物理性能等方面的检验,确保产品符合要求。
7. 包装和存储:将合格的密封条进行包装,并标明产品信息、生产日期和储存条件等,以便运输和存储。
以上是密封条成型工艺及生产工序的简介。
在实际生产中,还需要根据不同产品要求和工艺可行性,进行材料采购、模具制造和设备调试等前期准备工作,以确保产品的质量和效率。
密封条成型工艺及生产工序是密封条生产过程中极为关键的环节,直接关系到产品的质量和性能。
下面将更详细地介绍密封条成型工艺及生产工序的相关内容,以及一些常见的技术要点和注意事项。
1. 原材料准备:在密封条的生产过程中,常用的材料有橡胶、硅胶和塑料。
橡胶密封条具有耐磨损、耐油、耐高温等特点,常用于汽车、机械设备等领域。
硅胶密封条具有耐高温、耐酸碱、耐腐蚀等特点,适用于电子、医疗器械等领域。
塑料密封条具有耐腐蚀、阻燃性好等特点,适用于建筑、家居等领域。
在制备原材料时,首先需要选择合适的材料类型,并根据产品要求进行初步加工。
例如,对于橡胶密封条,可以进行胶片切割或拉伸成条状,以供后续工序使用。
2. 配方调制:密封条在使用过程中需要具备优异的性能,如抗拉伸性、耐热性、耐腐蚀性等。
成型作业指导书

成型作业指导书
1.目的:为规范成型操作,确保本工序产品符合要求。
2.范围:适应本公司裁断,成型工序。
3.职责:在生产技术厂长领导下,成型车间负责本过程的控制,操
作工人按操作规程严格工艺操作。
4.裁断:质量标准
裁断公差宽度为5mm,角度为0.5度。
帘布必须摆放平整,无折子、无杂质、无劈缝,无胶豆等质量问题。
操作工必须按照施工标准严格操作角度宽度要符合施工标准。
5.成型:
(1)工艺条件:风压0.4-0.8Mpa
(2)质量标准:成型筒宽度,项点周长务必正确,内面胶贴附不得折皱,对正中心,帘子线贴符对齐标线,确保帘线无折子,
无漏白,无杂物,无断线,无胶豆等问题,各层方向相反,
接头无脱开,接头压线为5-7根,钢丝圈放上下左右必须对
正并压实,帘线接头一定要错开。
胎面胶贴符对正中心线。
胎面接头要接平不要过大或过小并压实,把成好的胎胚挂在
架车上不得落地。
热压成型工艺流程

热压成型工艺流程热压成型是一种常用的塑料加工工艺,其工艺流程主要包括原材料准备、预热、热压、冷却和后处理等步骤。
下面将详细介绍各个步骤的具体内容。
首先是原材料准备。
热压成型通常使用的原材料是塑料颗粒或者塑料片材。
在进行热压成型之前,需要根据产品的要求选择合适的原材料,并按照一定的比例将其混合均匀,以确保产品的性能和质量。
接下来是预热。
预热是为了提高塑料的流动性和降低成型时间。
在预热的过程中,需要将混合好的塑料原料加热至一定的温度,通常为塑料的熔化温度。
预热温度的确立需要根据不同的塑料材料来确定。
第三步是热压。
在热压过程中,将预热好的塑料原料放置于加热板之间,然后施加一定的压力。
同时,加热板会继续为塑料原料提供热量,使其保持在熔化状态。
塑料原料在热压的过程中会流动,填满热压模具的腔体,形成所需的产品形状。
第四步是冷却。
冷却是为了使热压成型后的塑料产品固化并保持其形状。
冷却的方法主要有自然冷却和水冷却两种。
在自然冷却的情况下,塑料产品会通过自身散热而进行冷却。
而在水冷却的情况下,可以将塑料产品放置于水中进行快速冷却,以提高生产效率。
最后是后处理。
后处理一般包括产品的修整、清洁和质量检查等步骤。
修整是为了将产品表面的毛刺和余料去除。
清洁是为了将产品表面的杂质和污染物清除。
质量检查是为了确保产品的尺寸和质量满足要求。
根据产品的要求,可能还需要对产品进行表面处理和组装等工序。
热压成型工艺流程的每个步骤都非常重要,任何一个环节的问题都可能导致产品的质量下降。
因此,在实际操作中需要严格控制每个步骤的工艺参数,并进行充分的工艺试验和质量检查,以确保产品能够满足客户的要求。
同时,还需要对每个步骤进行维护和保养,以确保设备的正常运行,提高生产效率和产品质量。
成型车间制作流程

工序:刷中底、帮脚白胶无钉夹包,要求楦头部、中底头部、刷少量白胶,宽度不得超过15mm,若过多会影响脱楦;中底板刷胶一圈宽度15-18mm,不可遗漏或堆胶;鞋帮包脚刷胶宽度10-12mm均匀到位,若里布未修到位,需退上道工序重修,不得流入下道工序,分清左右脚、码号,成双作业。
工序:抹里布、粘中底、前帮手前帮手要求检查每只鞋帮需符合上述要求,同楦号、码号一致再操作,操作过程中参照生产确认样,注意头帮高低、机心圆顺、前后中心点同楦对齐;前撑两侧鞋帮搭地,左右平行,内侧允许向前1-3mm,脚背贴楦,包头平整,包脚内外侧基本一致,头部支口平整,不可有花角。
工艺操作说明工序:拉中帮首先检查上道工序是否符合第八点的要求才可操作,否则退回上道工序一律不予操作;操作过程中,内里、支跟、拉贴楦同帮面平顺;必须先拉内腰,再拉外腰,后支跟、内外边脚长短是否一致,内腰允长2-3mm,后帮严格按照鞋楦定位点及后帮包脚大小;注意脚背、腰档必须贴楦;后跟小割线平顺、接缝不可歪斜,后上口、内外基本平行,一般允许内脚高1-2mm;特别注意,内外包脚大小基本一致,腰档搭地,装饰物内外基本平行;支口平整,后帮处内外拉中帮时,稍往头部带一些,便利后帮操作,成双作业。
工艺操作说明工序:后帮机、锤鞋后帮手根据不同楦型,首先调节好角度,符合操作基本要求,后帮高度严格按照定位线要求作业,保证后帮支口平整,不可有花角;成双配对作业流到下道工序。
锤鞋为半成品验收:其职责主要是检查以上工序(第五—十条)操作要求。
帮面贴楦、高低一致、支口平整、机心圆顺,前、中、后三点一线,不可歪斜,成双作业。
工序:画线、打磨根据底型,由组长做好相应的垫片,注意同双高底一致,不要歪斜,前后包脚拉磨打平,面料支口不可磨断,轮机上打磨,会发生安全事故。
工艺操作说明工序:底处理、面处理底、面处理按组长指导,根据不同材料用相对应的处理剂;帮面要先清理灰尘,再刷处理剂;按底型画线位,不可外溢到帮面上;TPR材料鞋底刷处理剂时,务必均匀到位不可漏刷,更不可有处理剂堆在上面,外侧底边若刷到处理剂应及时处理掉,处理不掉的应作废品处理,绝对不可流到下道工序。
鞋厂成型各工序工艺要求
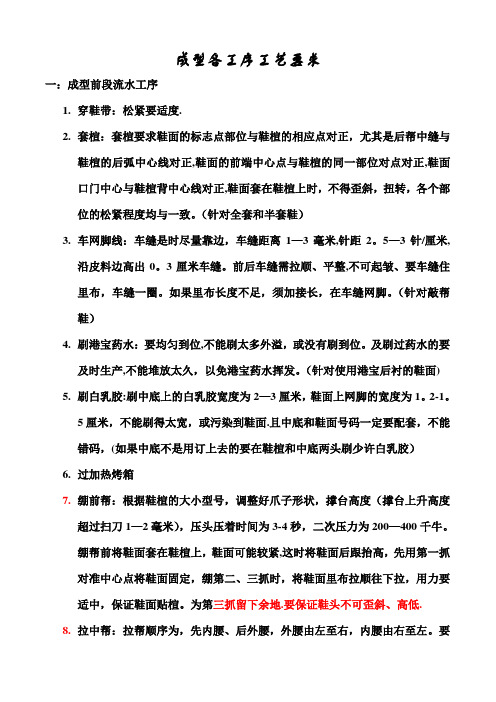
成型各工序工艺要求一:成型前段流水工序1.穿鞋带:松紧要适度.2.套楦:套楦要求鞋面的标志点部位与鞋楦的相应点对正,尤其是后帮中缝与鞋楦的后弧中心线对正,鞋面的前端中心点与鞋楦的同一部位对点对正,鞋面口门中心与鞋楦背中心线对正,鞋面套在鞋楦上时,不得歪斜,扭转,各个部位的松紧程度均与一致。
(针对全套和半套鞋)3.车网脚线:车缝是时尽量靠边,车缝距离1—3毫米,针距2。
5—3针/厘米,沿皮料边高出0。
3厘米车缝。
前后车缝需拉顺、平整,不可起皱、要车缝住里布,车缝一圈。
如果里布长度不足,须加接长,在车缝网脚。
(针对敲帮鞋)4.刷港宝药水:要均匀到位,不能刷太多外溢,或没有刷到位。
及刷过药水的要及时生产,不能堆放太久,以免港宝药水挥发。
(针对使用港宝后衬的鞋面)5.刷白乳胶:刷中底上的白乳胶宽度为2—3厘米,鞋面上网脚的宽度为1。
2-1。
5厘米,不能刷得太宽,或污染到鞋面.且中底和鞋面号码一定要配套,不能错码,(如果中底不是用订上去的要在鞋楦和中底两头刷少许白乳胶)6.过加热烤箱7.绷前帮:根据鞋楦的大小型号,调整好爪子形状,撑台高度(撑台上升高度超过扫刀1—2毫米),压头压着时间为3-4秒,二次压力为200—400千牛。
绷帮前将鞋面套在鞋楦上,鞋面可能较紧,这时将鞋面后跟抬高,先用第一抓对准中心点将鞋面固定,绷第二、三抓时,将鞋面里布拉顺往下拉,用力要适中,保证鞋面贴楦。
为第三抓留下余地.要保证鞋头不可歪斜、高低.8.拉中帮:拉帮顺序为,先内腰、后外腰,外腰由左至右,内腰由右至左。
要到贴楦,内外腰高低一致.9.绷后帮:后帮机压着时间为3秒,压着力为350-400千牛,后跟高低要一致,里布不能有起皱现象。
10.定点:用圆规等工具在鞋头或后跟上规定的高度标记画线,确保同一双鞋的高度统一。
11.画线:根据每款鞋的型体配置各种鞋底画线模,左右两台画线机的压力要一致,鞋面上的画线要清晰,要与大底弧度一致,同双鞋鞋头后跟高度要一致。
鞋厂成型各工序工艺要求
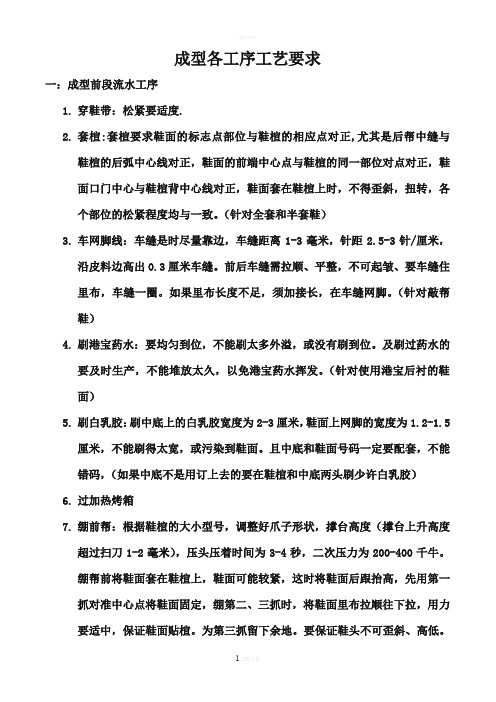
成型各工序工艺要求一:成型前段流水工序1.穿鞋带:松紧要适度.2.套楦:套楦要求鞋面的标志点部位与鞋楦的相应点对正,尤其是后帮中缝与鞋楦的后弧中心线对正,鞋面的前端中心点与鞋楦的同一部位对点对正,鞋面口门中心与鞋楦背中心线对正,鞋面套在鞋楦上时,不得歪斜,扭转,各个部位的松紧程度均与一致。
(针对全套和半套鞋)3.车网脚线:车缝是时尽量靠边,车缝距离1-3毫米,针距2.5-3针/厘米,沿皮料边高出0.3厘米车缝。
前后车缝需拉顺、平整,不可起皱、要车缝住里布,车缝一圈。
如果里布长度不足,须加接长,在车缝网脚。
(针对敲帮鞋)4.刷港宝药水:要均匀到位,不能刷太多外溢,或没有刷到位。
及刷过药水的要及时生产,不能堆放太久,以免港宝药水挥发。
(针对使用港宝后衬的鞋面)5.刷白乳胶:刷中底上的白乳胶宽度为2-3厘米,鞋面上网脚的宽度为1.2-1.5厘米,不能刷得太宽,或污染到鞋面。
且中底和鞋面号码一定要配套,不能错码,(如果中底不是用订上去的要在鞋楦和中底两头刷少许白乳胶)6.过加热烤箱7.绷前帮:根据鞋楦的大小型号,调整好爪子形状,撑台高度(撑台上升高度超过扫刀1-2毫米),压头压着时间为3-4秒,二次压力为200-400千牛。
绷帮前将鞋面套在鞋楦上,鞋面可能较紧,这时将鞋面后跟抬高,先用第一抓对准中心点将鞋面固定,绷第二、三抓时,将鞋面里布拉顺往下拉,用力要适中,保证鞋面贴楦。
为第三抓留下余地。
要保证鞋头不可歪斜、高低。
8.拉中帮:拉帮顺序为,先内腰、后外腰,外腰由左至右,内腰由右至左。
要到贴楦,内外腰高低一致。
9.绷后帮:后帮机压着时间为3秒,压着力为350-400千牛,后跟高低要一致,里布不能有起皱现象。
10.定点:用圆规等工具在鞋头或后跟上规定的高度标记画线,确保同一双鞋的高度统一。
11.画线:根据每款鞋的型体配置各种鞋底画线模,左右两台画线机的压力要一致,鞋面上的画线要清晰,要与大底弧度一致,同双鞋鞋头后跟高度要一致。
塑料压铸成型的工艺和流程

三、塑料制品成型阶段
在进行塑料制品成型之前,需要准备好塑料原料和成型设备。
通过上述的流程,就可以完成塑料压铸成型的制造过程。塑料压铸成型具有成本低、生产效率高、制品精度高等优点,在各个行业中得到了广泛应用。
塑料压铸成型的工艺和流程
下载温馨提示:该文档是我店铺精心编制而成,希望大家下载以后,能够帮助大家解决实际的问题。文档下载后可定制随意修改,请根据实际需要进行相应的调整和使用,谢谢!
并且,本店铺为大家提供各种各样类型的实用资料,如教育随笔、日记赏析、句子摘抄、古诗大全、经典美文、话题作文、工作总结、词语解析、文案摘录、其他资料等等,如想了解不同资料格式和写法,敬请关注!
Download tips: This document is carefully compiled by theeditor. I hope that after you download them,they can help yousolve practical problems. The document can be customized andmodified after downloading,please adjust and use it according toactual needs,thank you!
四、后处理阶段
在塑料制品成型完成后,还需要进行一些后处理工作,以保证产品质量和外观。
1.去除余料:成型完成后,需要将塑料制品从模具中取出,并去除余料和毛刺等不良部位。
泥人工艺学12 成型

第五章成型成型工艺是生产制作泥人的重要步骤,成型的方法目前有三种:印制成型、手捏成型和浇注成型,而印制成型是最古老也是最普遍的制作工艺,至今为止仍然占据着主要地位。
成型后产品坯体的质量好坏,直接影响到最终产品的品质和艺术效果,因此,成型工艺是制作泥人重要的基本功和工艺技术。
第一节印制成型印制成型是泥人批量生产普遍采用的工艺,将制备好的泥料通过石膏模型重复印制泥人坯体。
本章节除了介绍它的工艺过程和操作方法外,并且还要了解模型与泥坯制作的协调关系,以及修坯、揩坯的基本知识和操作方法。
一、工艺流程:它的工艺流程分为:揉泥→擀泥皮→印坯→合模→封底→脱模→修坯→揩坯1、揉泥:将泥料切成团,在操作台上用手揉压。
通过手的揉压、混锻使泥分子和水分子更加紧密混合一致,排出空气,让泥团颗粒逐步均匀柔软,最后将泥团搓成园柱型,放于密封的容器内备用。
通过一段时间的存放,在微生物的作用下,使泥土更加滋润,结合力更好,可塑性更强,这样印制出来的坯体,干燥后它的致密度和光洁度会更好,表皮细腻而不开裂。
操作方法:按需要将泥分块揉压。
揉泥时要借助身体的重量前倾和手掌协调用力,用一个手的手掌根部压住泥巴,用另一只手压住这个手的手背,双手同时向下用力揉压,不断反复多次。
在手感泥料已经达到需要的柔韧度和可塑性时结束。
结束后搓成圆柱型装入塑料包装袋,放入避光、不透风的容器中备用。
2、擀泥皮:为了印坯方便,保证坯体通体厚薄均匀和泥料质量的一致性,一般泥料都需先压擀成泥皮子,或者用木锤、拍板拍按需要的尺寸打成泥皮,再用整张泥皮来印制泥坯。
操作方法:按模型尺寸大小,用泥拉弓割出所需体积的泥块,用手搓成条子或园饼状,先用手掌压薄,再用擀子擀压成和模具形状相同的皮子。
皮子的尺寸应略大于模型,皮子的厚度应考虑模型面积的大小和型腔的深度。
皮子要平整、厚度要均匀。
3、印坯:将泥片按模型的外型匀称地平放入石膏模中,使泥片在石膏模的造型上成型。
操作方法:一般泥模由前后二个大爿组成,先将前部(脸部)的泥模型腔朝上,将泥皮盖在模型上边。
拉胚成型工艺
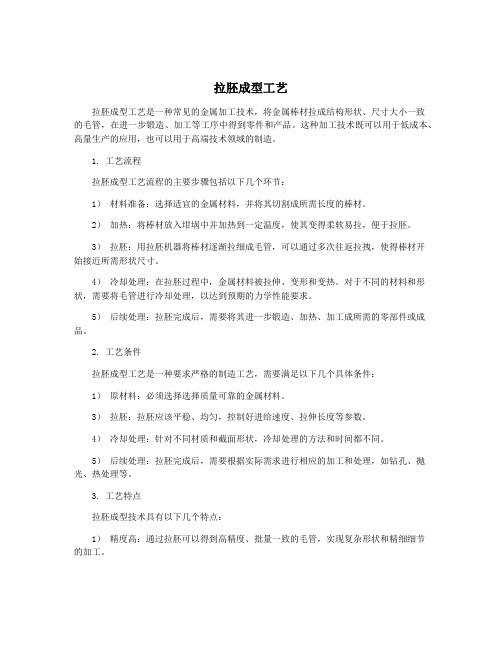
拉胚成型工艺拉胚成型工艺是一种常见的金属加工技术,将金属棒材拉成结构形状、尺寸大小一致的毛管,在进一步锻造、加工等工序中得到零件和产品。
这种加工技术既可以用于低成本、高量生产的应用,也可以用于高端技术领域的制造。
1. 工艺流程拉胚成型工艺流程的主要步骤包括以下几个环节:1)材料准备:选择适宜的金属材料,并将其切割成所需长度的棒材。
2)加热:将棒材放入坩埚中并加热到一定温度,使其变得柔软易拉,便于拉胚。
3)拉胚:用拉胚机器将棒材逐渐拉细成毛管,可以通过多次往返拉拽,使得棒材开始接近所需形状尺寸。
4)冷却处理:在拉胚过程中,金属材料被拉伸、变形和变热。
对于不同的材料和形状,需要将毛管进行冷却处理,以达到预期的力学性能要求。
5)后续处理:拉胚完成后,需要将其进一步锻造、加热、加工成所需的零部件或成品。
2. 工艺条件拉胚成型工艺是一种要求严格的制造工艺,需要满足以下几个具体条件:1)原材料:必须选择选择质量可靠的金属材料。
3)拉胚:拉胚应该平稳、均匀,控制好进给速度、拉伸长度等参数。
4)冷却处理:针对不同材质和截面形状,冷却处理的方法和时间都不同。
5)后续处理:拉胚完成后,需要根据实际需求进行相应的加工和处理,如钻孔、抛光、热处理等。
3. 工艺特点拉胚成型技术具有以下几个特点:1)精度高:通过拉胚可以得到高精度、批量一致的毛管,实现复杂形状和精细细节的加工。
2)金属利用率高:与其他加工技术相比,拉胚可以更有效利用原材料,降低耗材成本。
3)工序简单:相对于其他加工工艺,拉胚成型的制造工序相对简单,便于自动化流程控制。
4)应用广泛:拉胚适用于多种金属材料和截面形状的加工,领域包括汽车零配件、航天航空、建筑装饰、家居装饰等。
拉胚成型工艺是一种广泛应用于金属加工领域的技术,具有高精度、高效率、低成本等优点,而且能够应用于多种金属材料和形状的加工需求。
虽然该工艺仍面临许多挑战和技术难关,但在不断推进技术革新的进程中,其应用前景仍然十分广阔。
浇注成型工艺流程是什么样的

浇注成型工艺流程是什么样的在现代工业生产中,浇注成型工艺是一种常见且关键的制造技术,旨在生产出具有特定形状和结构的零件或产品。
浇注成型工艺流程通常包括原料准备、模具制备、浇注、固化、脱模等多个步骤,每一步都至关重要。
首先,浇注成型的第一步是原料准备。
根据所需产品的特性和要求,选择合适的原材料,对原料进行精确的配比和加工处理。
原料的选择和准备直接影响到最终产品的质量和性能,因此这一步需要高度重视。
接着,在模具制备阶段,根据产品的设计要求制造模具。
模具的设计应考虑到产品的形状、尺寸和表面质量,以保证最终产品的精度和外观。
制备好的模具应具有良好的耐磨性和导热性,以确保生产过程中的稳定性和效率。
随后是浇注这一关键步骤。
在浇注过程中,将预熔的原料倒入准备好的模具中,确保原料充分填满模具的每一个角落,并消除气泡和缺陷。
浇注时需要控制好温度、压力和流速等参数,以保证产品的均匀性和密实性。
固化是浇注成型工艺中的另一个重要环节。
在浇注完成后,待产品冷却固化至一定程度后,可以使产品具有必要的强度和硬度。
固化的时间和温度会根据原料的性质和产品的要求而有所不同,需要经过研究和试验来确定最佳的固化条件。
最后是脱模。
在产品完全固化后,将其从模具中取出,进行后续的整形、修磨和表面处理工序。
脱模过程中需要小心谨慎,避免损坏产品或模具,同时保证产品的形状和尺寸符合要求。
综上所述,浇注成型工艺流程是一个复杂而精细的制造过程,每一个步骤都需要严格控制和管理,以确保最终产品的质量和性能达到预期。
只有在每个环节都注重细节和质量,才能生产出优质的零件和产品,满足市场和客户的需求。
1。
成型工艺要求

线路产品成型车间成型工艺要求
一、合格品的判定:
1、坯件表面应无裂纹、缺损、变形等缺陷;
2、坯件表面应光滑、无刀痕、波纹等不符合半成品规范的
缺陷;
3、坯件表面应无子屑、线纹、手印、余泥等缺陷;
4、坯件内孔应光滑、无余泥、绞坏等缺陷;
5、坯件头部抿坯应圆整,符合图纸要求。
二、过程操作工艺要求
压坯人员:
1、泥段冲模时,应将泥段垂直放在模内;
2、旋坯:分为两次旋坯,第一次快到位时,将刀提起,抹去刀心上余泥后,再用板刀将坯件旋好;
3、首件应用规板进行自检;
4、翻模时应注意不能将托板上杂质带入泥料内。
修坯人员:
1、将合格毛坯放入石膏模座的过程,应不使毛坯的棱边损
坏;
2、修坯时进刀均匀,坯件旋转时平稳,且接口部位圆整;
3、必须在坯车停稳后取坯,并应轻拿轻放;
4、首件应用规板进行自检;
5、合格坯件上架须遵循从上到下的原则。
复合材料成型工艺以及设备要求

生产中建立起来的成型方法有:
• 8. 模压成型 9. 注射成型
10. 挤出成型 11. 纤维缠绕成型 12. 拉挤成型 13. 连续板材成型 14. 层压或卷制成型 15. 热塑性片状模塑料热冲压成型 16. 离心浇铸成型 其中,9,10,15为热塑性树脂基复合材 料成型工艺
复合材料成型工艺以及设备要求
• 3) 其它影响因素 : 胶液体积 、环境温度与湿度 、制品
厚度与表面积大小 、交联剂蒸发损失 、 抑制聚合反应的助剂、填料加入量。 • 4) 配制方法
按配方比例先将引发剂等助剂和树脂 混合均匀备用,操作前再加入促进剂搅 拌均匀。加入引发剂的树脂胶液,贮存 期不能过长。一次配胶量不要过多。
3. 色料:改变制品外观。一般不使用有机颜料和 碳黑
复合材料成型工艺以及设备要求
3) 增强材料
1).玻璃纤维 A一玻璃纤维 E一玻璃纤维 (无碱) S一高强玻璃纤维 M一高弹玻 璃纤维和L一防辐射玻璃纤维 ,c-中碱 玻璃纤维 玻璃纤维制品 无捻粗纱、短切纤维毡 、 无捻粗纱布 、 玻璃纤维细布 、 单向 织物
• 2). 碳纤维聚丙烯睛(PAN)纤维、沥 青纤维和粘胶纤
• 3). Kevlar纤维
复合材料成型工艺以及设备要求
6.2.2 手糊成型模具与脱模剂
• 6.2.2.1 模具结构与材料 1) 模具结构 --单模和对模两类 2) 成整体式或拼装式
复合材料成型工艺以及设备要求
6.2.2.2. 模具材料
复合材料成型工艺以及设备要求
复合材料成型工艺以及设备要求
6.2 手糊成型工艺及设备
• 手糊成型又称接触成型。是用纤维增强 材料和树脂胶液在模具上铺敷成型,在室 温或加热无压(或低压)条件下固化,脱 模成制品的工艺方法。
型材成型流程范文

型材成型流程范文第一步:材料准备在进行型材成型之前,首先需要准备所需的材料。
根据具体的需要,可以选择不同种类的金属或其他材料,并根据型材的使用环境和要求选择材料的物理和化学性能。
第二步:原材料切割通常情况下,原材料会准备成一定长度的棒状或板状。
在型材成型之前,需要根据所需尺寸将原材料进行切割。
切割可以使用机械切割工具,如剪切机,也可以使用激光切割机等高精度切割设备。
第三步:热处理有些金属材料在成型之前需要进行热处理,以改变材料的晶体结构和性能。
比如,热处理可以加强材料的硬度、强度和韧性,或者消除材料内部的应力和缺陷。
常见的热处理方法包括退火、淬火和回火。
第四步:型材成型型材成型是整个流程的核心步骤。
型材成型可以通过多种方式进行,常见的方式包括挤压、拉伸、滚轧、锻造和压铸等。
-挤压:将金属材料放入挤压机中,在一定的压力和温度条件下,通过挤出口挤出成型。
挤压可用于制造各种横截面形状的型材。
-拉伸:将金属材料加热至一定温度后,通过外力使其在塑性状态下,逐渐拉长成型。
拉伸可用于制造细长型材,如线材和钢丝。
-滚轧:将金属材料放入滚轧机中,通过多个辊轧制成型。
滚轧广泛用于制造板材、带材和型钢等。
-锻造:将金属材料放入锻造机中,在一定的压力和温度条件下,通过锻打和成型工具对金属进行加工。
锻造可用于制造各种形状的型材,对材料的内部结构有较大的影响。
-压铸:将金属材料加热至液态后,通过高压注入模具中进行成型。
压铸通常用于制造复杂形状的小型型材。
第五步:表面处理在型材成型完成后,通常需要对其表面进行一些处理,以提高外观和性能。
常见的表面处理方式包括抛光、喷涂和电镀等。
第六步:检验和质量控制在成型完成后,需要对型材进行检验和质量控制,以确保其符合要求。
检验可以通过目视检查、专用仪器或无损检测等方法进行,质量控制可以通过制定和遵守相关标准和规范来完成。
最后,经过以上几个步骤,型材成型的流程就基本完成了。
具体的型材成型流程会根据不同的材料和型材形状的要求而有所差异,但以上步骤是成型过程的主要内容。
模压成型的工艺过程有哪些内容
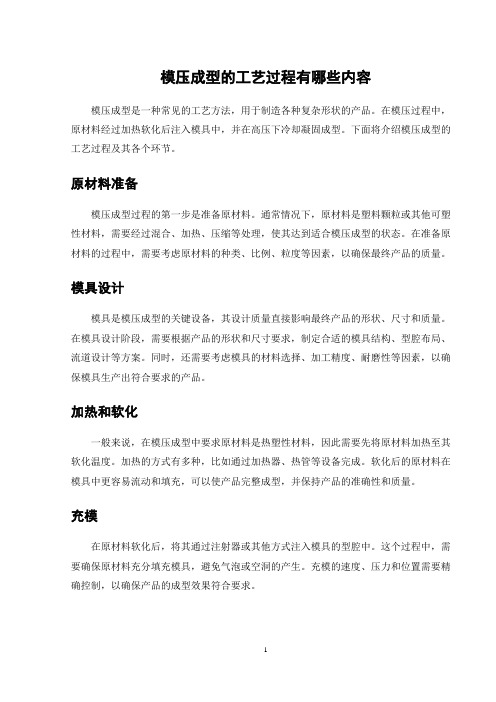
模压成型的工艺过程有哪些内容模压成型是一种常见的工艺方法,用于制造各种复杂形状的产品。
在模压过程中,原材料经过加热软化后注入模具中,并在高压下冷却凝固成型。
下面将介绍模压成型的工艺过程及其各个环节。
原材料准备模压成型过程的第一步是准备原材料。
通常情况下,原材料是塑料颗粒或其他可塑性材料,需要经过混合、加热、压缩等处理,使其达到适合模压成型的状态。
在准备原材料的过程中,需要考虑原材料的种类、比例、粒度等因素,以确保最终产品的质量。
模具设计模具是模压成型的关键设备,其设计质量直接影响最终产品的形状、尺寸和质量。
在模具设计阶段,需要根据产品的形状和尺寸要求,制定合适的模具结构、型腔布局、流道设计等方案。
同时,还需要考虑模具的材料选择、加工精度、耐磨性等因素,以确保模具生产出符合要求的产品。
加热和软化一般来说,在模压成型中要求原材料是热塑性材料,因此需要先将原材料加热至其软化温度。
加热的方式有多种,比如通过加热器、热管等设备完成。
软化后的原材料在模具中更容易流动和填充,可以使产品完整成型,并保持产品的准确性和质量。
充模在原材料软化后,将其通过注射器或其他方式注入模具的型腔中。
这个过程中,需要确保原材料充分填充模具,避免气泡或空洞的产生。
充模的速度、压力和位置需要精确控制,以确保产品的成型效果符合要求。
施加压力一旦原材料充分注入模具,就需要施加高压力使其充分填充模具型腔,并保持一定时间以确保原材料的冷却凝固。
施加的压力大小需要根据产品的形状、尺寸和要求来确定,过高或过低都可能导致产品出现瑕疵。
冷却固化在原材料充分填充模具并施加压力后,需要等待一定时间让原材料冷却固化。
冷却的速度和时间取决于原材料的种类和厚度,一般情况下需要精确控制以确保产品质量。
在冷却固化的过程中,模具温度、环境温度和湿度等因素都会对产品的质量产生影响。
脱模当原材料冷却固化后,就可以进行脱模操作。
脱模时需要小心翼翼地分离模具和产品,避免产品损坏或形状不规则。
模压成型工艺条件要求标准

模压成型工艺条件要求标准在模压成型工艺中,制定合适的工艺条件要求标准对于产品质量的提高和生产效率的保障至关重要。
下面将介绍模压成型工艺条件要求标准的相关内容。
材料选用首先,在模压成型工艺中,选用合适的原材料非常重要。
通常情况下,要求选用熔点适中、流动性好、熔聚指数适中的原料。
同时,材料的颜色、添加剂的含量等也需要满足产品的要求。
模具设计模具的设计与工艺条件密切相关。
模具应设计合理,结构坚固,表面光洁度高。
模具的温度控制也是关键,需要根据产品要求来确定合适的温度范围。
温度控制在进行模压成型时,温度的控制是至关重要的。
通常情况下,需要控制模具温度、料筒温度、压力头温度等多个方面的温度。
确保温度稳定可以提高产品质量。
压力控制除了温度外,压力的控制也是必不可少的。
合适的压力可以确保产品成型的完整性和密实度。
压力过大或过小都会影响成型质量,因此需要根据具体产品要求来合理调节压力。
时间控制模压成型的时间控制也是非常重要的一环。
时间太短会导致产品未完全成型,时间太长则会造成能耗浪费。
因此,在工艺条件要求标准中,需要明确规定成型时间的范围。
冷却方式在模压成型过程中,产品成型后需要进行适当的冷却。
冷却方式可以通过自然冷却或者水冷却等方式进行。
正确的冷却方式可以保证产品尺寸稳定和形状完整。
检测要求最后一步,模压成型工艺的条件要求标准还包括对产品的检测要求。
需要确保产品的密实性、尺寸精确性、表面光洁度等符合标准要求。
通过以上对模压成型工艺条件要求标准的介绍,可以看出在生产过程中,对各项工艺条件的合理控制非常重要。
只有严格按照标准要求执行,才能生产出高质量的模压成型产品。
这也是保障产品质量和生产效率的关键所在。
模压成型工艺条件有哪些要求
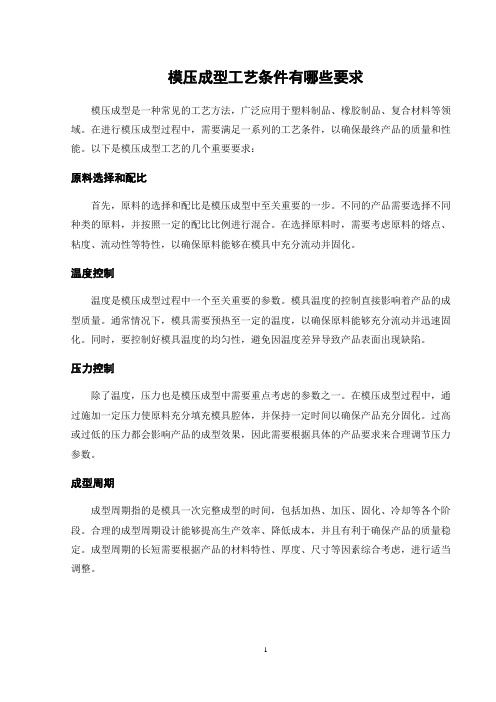
模压成型工艺条件有哪些要求模压成型是一种常见的工艺方法,广泛应用于塑料制品、橡胶制品、复合材料等领域。
在进行模压成型过程中,需要满足一系列的工艺条件,以确保最终产品的质量和性能。
以下是模压成型工艺的几个重要要求:原料选择和配比首先,原料的选择和配比是模压成型中至关重要的一步。
不同的产品需要选择不同种类的原料,并按照一定的配比比例进行混合。
在选择原料时,需要考虑原料的熔点、粘度、流动性等特性,以确保原料能够在模具中充分流动并固化。
温度控制温度是模压成型过程中一个至关重要的参数。
模具温度的控制直接影响着产品的成型质量。
通常情况下,模具需要预热至一定的温度,以确保原料能够充分流动并迅速固化。
同时,要控制好模具温度的均匀性,避免因温度差异导致产品表面出现缺陷。
压力控制除了温度,压力也是模压成型中需要重点考虑的参数之一。
在模压成型过程中,通过施加一定压力使原料充分填充模具腔体,并保持一定时间以确保产品充分固化。
过高或过低的压力都会影响产品的成型效果,因此需要根据具体的产品要求来合理调节压力参数。
成型周期成型周期指的是模具一次完整成型的时间,包括加热、加压、固化、冷却等各个阶段。
合理的成型周期设计能够提高生产效率、降低成本,并且有利于确保产品的质量稳定。
成型周期的长短需要根据产品的材料特性、厚度、尺寸等因素综合考虑,进行适当调整。
模具设计和制造最后,模具的设计和制造也是模压成型中至关重要的一环。
合理的模具结构设计能够保证产品的成型精度和表面质量,降低生产过程中的浪费。
同时,模具的制造质量、表面处理等也会直接影响产品的最终质量和外观。
综上所述,模压成型工艺需要满足原料选择和配比、温度控制、压力控制、成型周期、模具设计和制造等多个方面的要求。
只有在这些关键工艺条件得到合理控制和保障的情况下,才能生产出质量稳定、性能优良的模压制品。
- 1、下载文档前请自行甄别文档内容的完整性,平台不提供额外的编辑、内容补充、找答案等附加服务。
- 2、"仅部分预览"的文档,不可在线预览部分如存在完整性等问题,可反馈申请退款(可完整预览的文档不适用该条件!)。
- 3、如文档侵犯您的权益,请联系客服反馈,我们会尽快为您处理(人工客服工作时间:9:00-18:30)。
成型各工序工艺要求
一:成型前段流水工序
1. 穿鞋带:松紧要适度.
2. 套楦:套楦要求鞋面的标志点部位与鞋楦的相应点对正,尤其是后帮中缝与鞋楦的后弧中心线对正,鞋面的前端中心点与鞋楦的同一部位对点对正,鞋面口门中心与鞋楦背中心线对正,鞋面套在鞋楦上时,不得歪斜,扭转,各个部位的松紧程度均与一致。
(针对全套和半套鞋)
3. 车网脚线:车缝是时尽量靠边,车缝距离1-3毫米,针距2.5-3针/厘米,沿皮料边高出0.3厘米车缝。
前后车缝需拉顺、平整,不可起皱、要车缝住里布,车缝一圈。
如果里布长度不足,须加接长,在车缝网脚。
(针对敲帮鞋)
4. 刷港宝药水:要均匀到位,不能刷太多外溢,或没有刷到位。
及刷过药水的要及时生产,不能堆放太久,以免港宝药水挥发。
(针对使用港宝后衬的鞋面)
5. 刷白乳胶:刷中底上的白乳胶宽度为2-3厘米,鞋面上网脚的宽度为1.2-1.5厘米,不能刷得太宽,或污染到鞋面。
且中底和鞋面号码一定要配套,不能错码,(如果中底不是用订上去的要在鞋楦和中底两头刷少许白乳胶)
6. 过加热烤箱
7. 绷前帮:根据鞋楦的大小型号,调整好爪子形状,撑台高度(撑台上升高度超过扫刀1-2毫米),压头压着时间为3-4秒,二次压力为200-400千牛。
绷帮前将鞋面套在鞋楦上,鞋面可能较紧,这时将鞋面后跟抬高,先用第一抓对准中心点将鞋面固定,绷第二、三抓时,将鞋面里布拉顺往下拉,用力要适中,保证鞋面贴楦。
为第三抓留下余地。
要保证鞋头不可歪斜、高低。
8. 拉中帮:拉帮顺序为,先内腰、后外腰,外腰由左至右,内腰由右至左。
要划伤、车线爆开一律返工。
6. 鞋面任何部位花角、发角、折皱不平顺,一律返工。
7. 鞋头高低误差1.5㎜以上者一律返工。
8. 后跟歪斜误差2㎜以上者一律返工。
9. 鞋头绷帮大小需符合工艺说明要求,左右脚大小统一,高低误差1.5㎜内配双。
10. 针车脱线、跳针、浮线以及裁断皮革缺陷或者装饰配件松动脱落等不良现象应返修。
11. 中底不可超出鞋楦边缘1.5㎜,中底走位,卷折一律返工。
二:成型中段流水工艺要求
1. 配双:同双的半成品,左右脚号码一致、配色必须一致。
检查鞋头大小;后跟高度是否一致,如有问题必须及时调整更改,并向管理人员反映。
2. 配底:检查鞋底品质,如有不良应剔除。
同一双鞋底左右脚号码必须一致,且鞋底号码必须与鞋面号码配对。
检查鞋面号码与鞋楦号码是否一致,有无同边,单脚,将同号码的楦、底配双成对放入流水线。
3. 刷鞋面和鞋底处理剂:鞋面/大底处理按不同材质正确使用处理剂,刷鞋面时必须按画线来刷,不能超过画线标记。
刷完边侧,底部也需回刷。
刷鞋底时不能把处理剂漏到大底边或凝结在大底上,且各个部位药水都要全部刷到位。
4. 刷鞋面和鞋底胶:1. 刷鞋面胶按照定位线从鞋后跟外侧刷起,经鞋头绕鞋一圈,不能出现积胶、欠胶、溢胶、接缝处回胶现象。
胶水要刷均匀且薄,不要使刷胶部位的胶水粘到不该刷得地方。
不要使胶水凝结在皮料的连接处。
周围刷胶不可超出画线及没有刷到画线处。
二次刷胶和第一次刷法一样,就是不能未刷到或超过一次胶。
2. 刷大底胶第一遍要稀一些,使胶水能够充分侵润被粘物的表面,有利于胶水被粘物内部的扩散和渗透。
刷胶方法是往复推刷,因为单向刷胶时,被粘物表面上被磨起的绒毛会向一侧倾倒,产出绒毛上部有胶、下部无胶的结果。
而双向往复刷胶则可使胶水充分侵润被粘物的表面。
第二遍刷胶的浓度要高于头遍胶,二遍胶对提高剥离强度起着决定性的作用。
头遍胶对黏合强度的提高几乎不起作用,但由于头遍胶的作用是侵润被粘物的表面,并扩散、渗透到被粘去的内部,以便形成胶粘过度层,为二遍胶发挥作用打好基础。
刷胶方法是单向推刷,这样可以避免胶水产生堆积,胶膜的厚薄也比较均匀,刷胶时应用力适中,每次刷胶完后都必须干。