Removed_调整杠杆说明书()
10K Lowrise LR10000 杠杆抬高机器人说明书
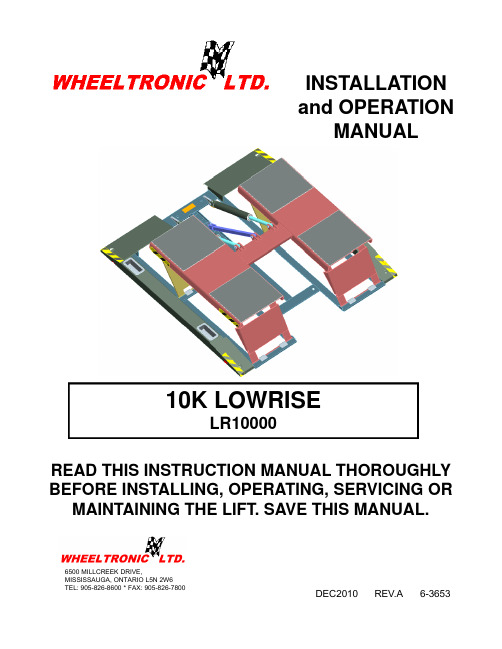
INSTALLATIONd OPERATIONand OPERATION MANUAL10K LOWRISE READ THIS INSTRUCTION MANUAL THOROUGHLY 10K LOWRISELR10000READ THIS INSTRUCTION MANUAL THOROUGHLY BEFORE INSTALLING, OPERATING, SERVICING OR MAINTAINING THE LIFT. SAVE THIS MANUAL.DEC2010 REV.A 6-36536500 MILLCREEK DRIVE,MISSISSAUGA, ONTARIO L5N 2W6TEL: 905-826-8600 * FAX: 905-826-7800TABLE OF CONTENTSTABLE OF CONTENTS (2)1.0 SAFETY AND OPERATING INSTRUCTIONS (3)2.0 SAFETY WARNING DECALS (6)3.0 GENERAL SPECIFICATIONS (8)Figure 1 - Overall Specifications (9)4.0 SHIPPING CONTENTS (10)5.0 TOOLS REQUIRED FOR INSTALLATION (10)6.0 INSTALLATION INSTRUCTIONS (11)6.1 BAY LAYOUT – SURFACE MOUNT (12)Figure 2 - Bay Layout – Surface Mount (12)6.2 UNPACKING THE LIFT (13)7.0 HYDRAULIC CONNECTIONS (13)7.1 ANCHORING PROCEDURES (13)Figure 3 - Anchoring Steps (14)8.0 BLEEDING PROCEDURE (15)8.1 FINAL CHECK OF ASSEMBLED LIST (15)8.2 OPERATION TEST WITH VEHICLE (16)9.0 LIFT OPERATION (16)Before Lifting: (16)Raising the Lift: (16)Lowering the Lift: (16)After Lowering: (17)10.0 RECOMMENDED MAINTANANCE (17)Inspect Regularly for: (17)10.1 MAINTANANCE SCHEDULE (17)11.0 TROUBLE SHOOTING (18)12.0 LIFT ASSEMBLY (19)12.1 LIFT PARTS LIST (19)13.0 POWER PACK ASSEMBLY (20)13.1 POWER PACK PARTS LIST (20)14.0 AVAILABLE ACCESSORIES (22)Figure 4 – Square Rubber Pad, Part No. 6-2776 (Set of 4) (22)Figure 5 – Pump Stand Assembly, Part No. 22573 (22)Figure 6 – Pump Stand Bolt Down 84”, Part No. 3-1027 (23)1.0 SAFETY AND OPERATING INSTRUCTIONS IMPORTANT SAFETY INSTRUCTIONSWhen using your garage equipment , basic safety precautions should always be followed, including the following:1. Read all instructions2. Care must be taken as burns can occur from touching hot parts3. Do not operate equipment with a damaged cord or if the equipment has beendropped or damaged – until it has been examined by a qualified person.4. Do not let a cord hang over the edge of the table, bench , or counter or come incontact with hot manifolds or moving fan blades.5. If an extension cord is necessary, a cord with a current rating equal to or morethan that of the equipment should be used. Cord rated for less current that theequipment may pverheat. Care should be taken to arrange the cord so that it will not be tripped over or pulled.6. Always unplug equipment from electrical outlet when not in use. Never use thecord to pull the plug from the outlet. Grasp plug and pull to disconnect.7. Let the equipment cool completely before putting away. Loop cord loosely aroundequipment when storing.8. To reduce the risk of fire, do not operate equipment in the vicinity of opencontainers of flammable liquids ( gasoline).9. Adequate ventilation should be provided when working on operating internalcombustion engines.10. K eep hair, loose clothing , fingers, and all parts of body away from moving parts.11. T o reduce the risk of electric shock, do not ise on wet surfaces or expose to rain.12. U se only as described in this manual. Use only manufacturer’s recommendedattachments.13. A LWAYS WEAR SAFETY GLASSES. Everyday eye glasses only have impactresistant lenses, they are not safety glasses.SAVE THESE INSTRUCTIONSWhen using this lift, basic safety precautions should always be followed, including the following:1. Thoroughly read all instructions in this manual and on the lift before installing,operating, servicing or maintaining the lift.2. Inspect the lift daily. Do not operate lift if it malfunctions or if problems have beenencountered.3. Never attempt to overload the lift. The manufacturer’s rated capacity is shown onthe identification label. Do not override the operating controls or the warranty will be void.4. Only trained and authorized personnel should operate the lift. Do not allowcustomers or bystanders to operate the lift or be in the lift area.5. Caution! Never work under the lift unless the mechanical safety locks areengaged.6. Always keep the lift area free of obstruction and debris. Grease and oil spillsshould always be cleaned up immediately.7. Never lift a vehicle with passengers inside.8. Before lowering the lift check the area for any obstructions.9. To protect against risk of fire, do not operate lift in the vicinity of open containersof flammable liquids.10. Adequate ventilation should be provided when working on internal combustionengines.11. Do not remove hydraulic fittings while under pressure.12. Only replace parts with genuine lift manufacturer supplied parts.SAVE THESE INSTRUCTIONSFor additional safety instructions regarding lifting, lift types, warning labels, preparing to lift, vehicle spotting, vehicle lifting, maintaining load stability, emergency stop procedures, vehicle lowering, lift limitations, lift maintenance, good shop practices, installation, operator training, and owner/employer responsibilities, please refer to “Lifting It Right” (ALI/SM) “Safety Tips” (ALI/ST) and vehicle lift points for service garage lifting SAE J2184.For additional instructions on general requirements for lift operation, please refer to “Automotive Lift-Safety Requirements For Operation, Inspection and Maintenance” (ANSI/ALI ALOIM).Installation shall be performed in accordance with ANSO/ALI ALIS, SafetyRequirements for Installation and Service of Automotive Lifts.ATTENTION! This lift is intended for indoor installation only. It is prohibited to install this product outdoors. Operating environment temperature range should be 41 – 104 °F (5 – 40 °C). Failure to adhere will result in desertification, loss of warranty, and possible damage to the equipment.2.0 SAFETY WARNING DECALSBe sure the operator is aware and understands all safety warning labels and followsthem accordingly.CAUTION TAPE LOCATIONSNOTE: CAUTION TAPE IDENTIFIES POSSIBLE TRIP HAZARDS WHEN THE LIFT IS LOWERED AND NOT IN USE. ENSURE THAT THIS TAPE IS REPLACED WHEN WORN ORREMOVED.3.0 GENERAL SPECIFICATIONSCapacity: 10000 lbs. 4536 kg Overall Width: 85” 2159 mm Overall Length: 83” 2108 mm Lowered Height: 3-7/8” 98 mm Raised Height: 21½” 546 mm Power Requirements:115 Volts AC, 1 Ph., 60 Hz.Figure 1 - Overall Specifications4.0 SHIPPING CONTENTSOverall Weight: 900lb / 408kg1 – Lifting frame assembly with cylinders attached1 – Pump box including:1 – Pumping unit assembly4 - 1/4” x 1 bolts with nuts & washers (Pump Mount)8 – ¾” x 5 ½” anchor bolts with nuts & washers (Frame Mount)1 – Tee fitting1 – Automotive lift safety tips1 – ALI manual “Lifting it Right”1 – Installation and Operation manual1 – Parts box including:4 – Height adapters4 – Height extensions2 – ¼”x29” hydraulic hose1 – 3/8” x 20’hydralic hose1 – Pumping unit mounting standMissing PartsIt is important to notify the delivery carrier immediately if any parts are damages or missing from shipment.5.0 TOOLS REQUIRED FOR INSTALLATION•16ft. Measuring Tape• Chalk Line•Rotary Hammer Drill•3/4” diameter Masonry Drill Bit• Hammer•SAE Wrenches and Ratchet Set• 2ft. Level• 4ft. Level• Crow Bar•12ft. Step Ladder• Side Cutters• Screwdrivers•4” x 4” Wooden Blocks (for unpacking)6.0 INSTALLATION INSTRUCTIONSWhen the lift arrives on site, please read the owner’s manual completely and make sure the installation instructions are fully understood. Check the contents of the hardware and accessory boxes to make sure no parts are missing and no freight damages exist before starting installation. Gather all the tools listed above and make sure the installation instructions are fully understood before commencing with the installation. IMPORTANT:It is the user’s responsibility to provide a satisfactory installation area for the lift. Lifts should only be installed on level concrete floors with a minimum thickness of five 4 1/4” or 115 mm. Concrete must have a steel reinforcing with a minimum strength of 3000 psi or 21 MPa and should be aged thirty (30) days prior to installation. Maximum slope must not exceed 1/16” per foot.Always pay special attention to the condition of the concrete such as age, cracking, chipping, and levelness. Please consult the architect, contractor or engineer if doubt exists as to the strength and feasibility of the floor to enable proper lift installation and operation.It is the user’s responsibility to provide all wiring for electrical hook-up prior to installation and to insure that the electrical installation conforms to local building codes. Where required, it is the user’s responsibility to provide an electrical isolation switch located in close proximity to the lift that will enable emergency stop capability and isolate electrical power from the lift for any servicing requirements.6.1 BAY LAYOUT – SURFACE MOUNTFigure 2 - Bay Layout – Surface MountNOTE: LAYOUT SHOWN WITH OPTION LINE COVER KIT EAK0299T13A6.2 UNPACKING THE LIFTRemove the metal strapping from the main structure package and slide the liftshipping skid. Open the accessory box and check the contents of the box.1. Position unit on a flat floor allowing a minimum of 6 feet from center of lift to sideobstructions and 12 feet from center of lift to front or rear obstructions. (Lift cylinder is on front end of lift.) Recommended overhead clearance is a minimum97 inches ceiling providing 25 inches for the maximum lift height and 6 feet forthe supported vehicle. For vehicles taller than 6 feet it is recommended that the user provides additional overhead clearance or a shut off mechanism to stop the lift from raising the vehicle too high.2. Remove pumping unit from box and install on pump stand.7.0 HYDRAULIC CONNECTIONSNOTE: When working with hydraulics it is important to keep all components clean.1. Select a position best suited for the power pack.2. Remove the breather filler cap and fill with 11 liters / 3 Gal. of ISO 32 10 weighthydraulic oil.3. Reinstall the breather filler cap onto the Power Unit.4. Connect the 90° elbow fitting (9/16” JIC-M, 3/8” JIC-M) with ‘O’ ring, to thehydraulic outlet port on the valve assembly of the power pack. The 90° elbow fitting is located in a hardware kit.5. Connect 11' (3353 mm) long hydraulic hose (female end) to the opposite end ofthe 90° elbow fitting.6. Locate the opposite (male) end of the 11' (3353 mm) long hydraulic hose.Connect to the central end of the swivel tee.7. Connect the male ends from both 29” long hydraulic hoses to the swivel tee sideends. Locate the opposite (female) ends of both 29” long hydraulic hoses and connect them to the inlet ports of the lift, which are located on the corresponding hydraulic cylinders.8. Tighten the hydraulic line in place so that it runs along the floor giving it a lowprofile.7.1 ANCHORING PROCEDURESNOTE: Check operation of lift (up/down) before anchoring the lift.1. Using a rotary hammer drill and a 3/4” concrete bit, drill through the floor at eachanchor bolt location. Make sure that the 3/4” concrete drill bit is in good condition.2. Clean out the drilling dust from the holes3. Assemble the nut and washer onto the supplied ¾” x 5 ½” long wedge anchorbolts. A minimum of six threads must be visible below the surface of the nut.4. Hammer in the anchors until they make contact with the base plate. Handtighten all anchor bolts. Remove any bolt assembly that does not grip concrete firmly and open expansion sleeve before reinstalling.5. Inspect to make certain lift sits firmly on floor. There should be no twisting orrocking motion in the base unit.6. Torque all anchor bolts to 75 ft-lbs.7. Position the power pack in the final desired location. Using a rotary hammer drilland a 1/4” concrete bit, drill four (4) holes and anchor the power pack stand to the floor using anchor bolts located in the hardware kit.8. Install the optional line covers to protect hydraulic hoses, refer to section 7.29. With all anchor bolts torqued as specified operate the lift checking its fulloperation.If anchor bolts do not tighten to 75 ft-lbs OR project more than 2 ¼” above the concrete surface, the concrete should be replaced by an appropriate concrete pad.(Consult Product Manufacturer / Supplier for further details.)Figure 3 - Anchoring Steps7.2 LINE COVER INSTALLATION (OPTIONAL)NOTE: FLOOR COVERS ARE DESIGNED TO SUPPORT FOOT TRAFFICAND TOOL BOXES UNDER 300LBS. ANY VEHICLE TRAFFIC WILL CAUSE DAMAGE TO THE LINE COVERS.1. Position the power pack in the location shown in the Bay layout Figure 22. Use the combination of straight (2-2736) and angled (2-2734 and 2-2733) linecovers provided in the options line cover kit EAK0299T13 to cover the hosesfrom the structure to the power pack. Any excess hydraulic hose should be coiled and zip tied to the power pack stand to avoid trip hazards.3. The angled line covers 2-2733 and 2-2734 will need to be cut at the cut lineshown in figure 2.4. Using a ¼” concrete drill bit, drill and fasten the line covers to the floor using the¼” x 1” long nail in anchors provided. The number beside the line coversrepresent the quantity of fasteners required to secure that side. Ensure that theline covers are sitting securely on the floor.NOTE: If the lift is shimmed to a point where the line covers do not sit flush due to interference with hoses, the line covers can be heated with a heat gun and then placed over the hoses for a cleaner look.8.0 BLEEDING PROCEDURE1. Press the up control button and raise the lift 10” (254mm) above the ground.2. Lower the lift to the ground and hold the down button until lift fully reaches theground.3. Repeat these steps 3-4 times to completely bleed the system of air. Check the liftfor hydraulic leaks at all connections.4. After bleeding, it is recommended that the filter assembly fitting (between thehydraulic hose and the power pack be cleaned. Place the fitting on a workbench and use an air gun to blow through the filter in the opposite direction to flow from the lift.8.1 FINAL CHECK OF ASSEMBLED LIFT1. Check for hydraulic leaks. ____2. Ensure all safety lock mechanisms are working correctly. ____3. Re-check level of decks. ____4. Check all fasteners, tighten if necessary. ____5. Operate lift to full stroke then lower to ground while checkingfor proper functionality. ____6. Ensure Customer Care Kit is complete and given to operator. ____a. Operation Manual____b. ANSI / ALI Lift It Right Manual ____c. ANSI / ALI Safety Tip CARD ____d. ANSI / ALI ALIS safety Requirements for Installationand Service of Automotive Lifts ____e. ANDI / ALI Quick Reference Guide ____7. Train end user on operation of the lift. ____8.2 OPERATION TEST WITH VEHICLE1. Lower lift to ground.2. Drive vehicle on to lift such that the lift’s contact frame is properly aligned with themanufacturer’s recommended lifting points for that vehicle.3. Raise lift to and lower onto first, second, and third lock positions during full rise toensure all locks are working correctly.4. Check lowering speed and smooth decent rate.5. Lower lift to ground and drive vehicle off lift.If any problems occur during the final checkout or operation of the lift please contact customer service at 1-800-268-7959.9.0 LIFT OPERATIONOperators of this lift should be trained by authorized personnel.Before Lifting:1. After making certain lift is in the fully lowered position, drive the vehicle into thebay and position it with the wheel in front of the superstructure.NOTE: The center of gravity of the vehicle should be centered on the liftingstructure. Refer to the "Lifting it Right" and "Vehicle lifting points quick referenceGuide" ALI/LP Guide provided. SAE J2184DO NOT TURN STEERING WHEEL WHILE TIRES ARE CROSSING2. Check to make certain car is fairly well centered left to right on lift.Raising the Lift:1. Hold toggle switch on pumping unit in “ON” position until locking leg drops ontoone of the three lifting height locking positions.2. Rock vehicle to check for stability.3. Lower the vehicle onto the mechanical locks.Lowering the Lift:1. After making certain lifting area is clear of people, electric cords, hoses, etc.,raise lift past next the safety lock to full height to disengage locking device.2. Press the lowering handle slowly until the lift is in its fully collapsed position..After Lowering:1. Drive car off lift without turning steering wheel while tires are crossing the lift.10.0 RECOMMENDED MAINTANANCEInspect Regularly for:a. Overload cracks in welds and metal fatigue.b. Misalignment of working parts.c. Hydraulic leaks.d. Low fluid level in pump reservoir. DO NOT use automatic transmission fluid.Use only petroleum based ISO 32-10 weight hydraulic oil.e. Lubricate all moving parts.f. Check locking latch for smooth and proper operation.10.1 MAINTANANCE SCHEDULEDaily:1. Check all hydraulic lines and fittings for pinch points , damage , cracks or leaks2. Check all electrical wiring for pinch points , cracks or damage3. Check all moving parts for uneven or excessive wear4. Repair or replace all damaged, defective, worn or broken componentsimmediately.5. Check the telescopic arms for movement. Clean any grease or oil from the liftingadapters.6. Raise and lower the lift at the beginning of each shift, without a vehicle on, toverify the lift is leveled and operating properly.7. Check the operation of the mechanical safety lock and release mechanism. If anydamage or malfunction is found, discontinue using the lift until repair isperformed.Weekly:1. Check and adjust hydraulic level.Every Two Months:1. Clean and re-grease hinge pins.Every Year:Inspect lift as per Automotive Lift Operation, Inspection and Maintenance(ALOIM).Every Two Years:Change hydraulic fluid.LUBRICATION:Where grease is required multi-purpose lithium grease.Where lubricating oil is required > multi-purpose SAE 30 lubricating oil.Where hydraulic oil is required > ISO 32 10W - non detergent hydraulic oil.11.0 TROUBLE SHOOTING1) Motor does not run:A. Breaker tripped or fuse blown.B. Motor thermal overload tripped. Wait for overload to cool.C. Defective control switch. Replace switch.D. Faulty wiring connections. Call electrician.2) Motor runs but the lift will not hold a load.A. A foreign object under check valve. Push handle down and push “raise”switch. Foreign matter should release under pressure.B. Remove check valve. Clean ball and seat and replace the nut.C. Oil level low, check oil reservoir. With lift cylinder (cylinders) in the downposition, pump reservoir should be full.3) Motor runs but the lift picks up partial load only.A. Lift is overloaded. Check capacity of lift and weight of vehicle.B. Relief valve setting is too low. Remove back hex cap on pump and adjustvalve clockwise.C. Hydraulic seals damaged (call customer service for instructions 1-800-266-7959)..4) Lift makes groaning sound when raising or lowering.A. Bleed cylinder manually.B. Add an ounce of oil to the air side of the piston.12.0 LIFT ASSEMBLYNOTE: Only replace parts with genuine lift manufacturers supplied parts12.1 LIFT PARTS LISTItem Part No. Description QTY.1 1-3368 3/8” x 19” x 22-1/2” Rubber Pad 42 2-2569HeightExtension Adapter 44”Height Extension Adapter 43 2-25704-1/2”4 6-1379 3/4” x 5-1/2” Anchor Bolt 45 1-3806 7/8” x 2-3/4” Piston Top Axle 26 2-2561 1/4” x 29” Hydraulic Hose M-F 2Assembly 2Cylinder7 3-10688 6-3516 F Pipe x F Pipe Swivel Tee 6-4-4 19 1-3374 Plastic Lug Nut Box 4restrictor 210 6-4018Flow11 1-3805 3/4” x 2-7/16” Pin 212 3-1066 Lock Leg Assembly 114 2-2566 11' High Pressure Hose 13-1026 Pump Stand Bolt Down Standard 1* Not shown in figure.13.0 POWER PACK ASSEMBLYNOTE: Only replace parts with genuine lift manufacturer’s supplied parts13.1 POWER PACK PARTS LISTAssembly No. Part No. Description1 6-2298 BOLT, 5/16” - 24” X 2-3/4” LG2 6-0774 COUPLING (4 POST POWER PACK)3 6-2157 PLUMBING PLUG 5/16” SAE4 6-2158 SEAL SHAFT 0.5X1X.25.338X.625X.065 6-2159WASHER6 62300 CORDSET 16/3 SJO 8FT 115V PLUG7 6-2156 WIRING ASSEMBLY AC 1PH FENNER8 6-2301 PACKAGE PLUG 9/16” SAE9 6-2157 PLUMBING PLUG 9/16 SAEMAGNET10 6-2162PLUMBING11 6-2302 ELECTRICAL STAKON NUT12 6-2164 SCREW TAPTITE TORX13 6-2165 COVER ASY SUCTIONINLETCLAMPHOSESEADJ.14 6-216615 6-2303 ELECTRIC CORD GRIP 3/4"NPT3/4"PIPENUTELECTRIC16 6-230417 6-1087 VALVE CARTRIDGE CHECK18 6-2305 VALVE LOAD DELAY19 6-2167 NUT 3/4”-16x1” HEX .2520 6-2168 WASHER 3/4” INT TOOTH21 6-1108 RELEASE HANDLE ASS’Y22 6-3782 END HEAD UNIV.23 6-2311 ELECT. REDUCER WASHER.35MMM6X124 6-2169SHCS,25 6-2170 WASHER 1/4 LC HI-COLLRMOTOR(2781-BC)115/230V,1PH,1HP26 6-2600RESERVOIRSCREW27 6-1091BREATHERFILLER28 6-137629 6-0884 INLET HOSE/FILTER ASS'Y30 6-1089 RELIEF VALVE CAP31 6-3783 TANK 2.0 GAL WHITE32 6-1846 CABLE TIE 8” LONG WHITERV1933 6-131934 6-2153 COMPRESSION TUBE NUT35 6-2154 COMP. TUBE SLEEVE36 6-3786 RETURN TUBE 1/2 OD 90 DEGO-RING37 6-0875RESERVOIR38 6-2306 PUMP ASS’Y 0.8 SHORT SPLINE.48X.063X.4239 6-2151SPRING40 6-0880 VALVE CARTRIGE RELEASE MANUAL41 6-2156 MICROSWITCH W/SNAP LID W-20042 6-2161 PLUMB. PLUG 3/8NPT43 6-3466 GROUNDING SCREW, #8-32 X 1/2"DECAL44 6-399614.0 AVAILABLE ACCESSORIESFigure 4 – Square Rubber Pad, Part No. 6-2776 (Set of 4)Figure 5 – Pump Stand Assembly, Part No. 22573Figure 6 – Pump Stand Bolt Down 84”, Part No. 3-1027EAK0299T13A Line Coverkit。
杠杆表使用作业指导书

1.0 目的指导和规范使用人员正确使用和维护杠杆表,确保使用时输出的结果准确有效,达到测量的准确度。
2.0 适用范围适用于公司所有使用杠杆表的岗位。
3.0 定义杠杆表是利用杠杆-齿轮传动机构,将尺寸变化为指针角位移,并指示出长度尺度数值的计量器具,用于测量工件几何形状误差和相互位置正确性。
4.0 职责:4.1 品质部:4.1.1 测量中心:负责量/检具回厂后的验收、领用登记造册、内外校计划的制定及周期检定/校准的执行、坏损量具和检具内部维修、报废判定及统计,监督各使用部门正确使用量具和检具等;4.1.2 各部品管:负责本部门领用的量/检具的日常点检保养、送校等;负责监督稽核量/检具使用保养是否规范;4.2 采购部:负责量/检具采购、退货及对接量/检具专业外校、维修厂商等;4.3 各使用部门:负责本部领用的量/检具的日常使用、点检维护、送校。
5.0 工作流程:5.1 杠杆表结构图5.2 常见杠杆表5.3 杠杆表的使用方法5.3.1使用前的准备工作5.3.1.1杠杆表使用前必须做好检查工作,当有其中一条不能满足时都必须进行更换;A.检查杠杆表的稳定性,取一块表,目视表盘,用手指轻推表的测杆,观察表针读数是否稳定。
B.旋转表盘使“0”位对准指针。
C.检查杠杆表的准确度,用手指反复轻推测杆,检查指针是否能回到“0”位。
5.3.1.2根据所选表架适合规格的轴套,并将其牢固拧在表体上,否则松动易造成表的损坏。
5.3.1.3检查表架各部分功能;A.检查表架上的两个联接螺母是否能拧紧。
B.检查磁力表座的锁紧开关是否能正常工作,可靠。
5.3.2 杠杆表装在表架上的夹持部位应尽量靠近连接销的根部,同时不能影响表盘旋转。
5.4 测量5.4.1 平面测量:调整杠杆表测量的角度以及表架杆的长度和角度,使表的测杆轴线应尽可能垂直工件尺寸变动的方向,在该方向与被测要素接触,接触时指针的压缩量一般为0.02-0.05mm;测量时,测杆轴线尽可能与被测量平面平行,如下图1所示,若出现下图2所示的做法,则会出现不可避免的测量误差,该测量误差Δ=A(1-cosa)[其中A为杠杆表的读数,α为测杆轴线与测量平面之间的夹角],α角度越小误差也相对越小,通用情况下α≤15°为宜,当测量一些特殊工件α角度较大时按下表1换算得出实际测量结果。
海港自由工具 1.5 吨重量限制杠杆斧头说明书
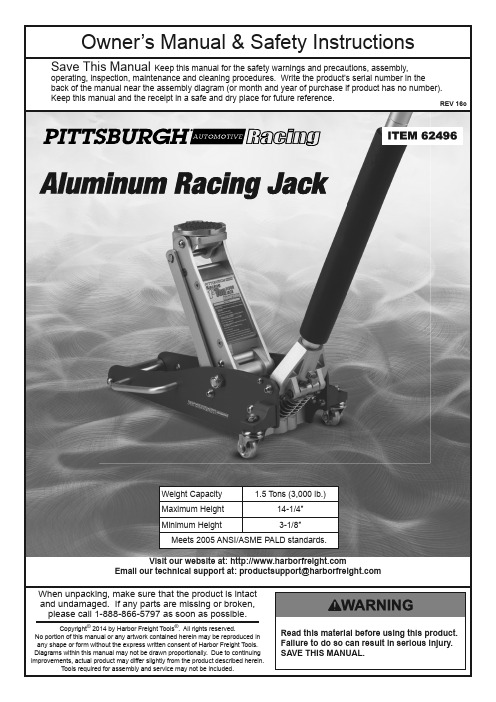
Visit our website at: Emailourtechnicalsupportat:********************************Weight Capacity 1.5 Tons (3,000 lb.)Maximum Height 14-1/4″Minimum Height3-1/8″Meets 2005 ANSI/ASME PALD standards.When unpacking, make sure that the product is intact and undamaged. If any parts are missing or broken, please call 1-888-866-5797 as soon as possible.Copyright © 2014 by Harbor Freight T ools ®. All rights reserved.No portion of this manual or any artwork contained herein may be reproduced in any shape or form without the express written consent of Harbor Freight T ools. Diagrams within this manual may not be drawn proportionally. Due to continuing improvements, actual product may differ slightly from the product described herein.T ools required for assembly and service may not be included.Read this material before using this product.Failure to do so can result in serious injury.SAVE THIS MANUAL.IMPORTANT SAFETY INFORMATION1. Study, understand, and follow all instructionsbefore operating this device.2. Do not exceed rated capacity.3. Use only on hard, level surfaces.4. Lifting device only. Immediately after lifting,support the vehicle with appropriate means.5. Do not move or dolly the vehicle while on the jack.6. Failure to heed these markings may result inpersonal injury and/or property damage.7. Lift only areas of the vehicle as specifiedby the vehicle manufacturer.8. No alterations shall be made to this product.9. Never work on, under or around a loadsupported only by this device.10. Do not adjust safety valve.11. Wear ANSI-approved safety goggles andheavy-duty work gloves during use.12. Keep clear of load while lifting and lowering.13. Lower load slowly.14. Apply parking brake and chocktires before lifting vehicle.15. Lift vehicle only at manufacturerrecommended locations. 16. Inspect before every use; do not useif parts are loose or damaged.17. Do not use for aircraft purposes.18. The warnings, precautions, and instructionsdiscussed in this manual cannot cover allpossible conditions and situations that may occur.The operator must understand that common sense and caution are factors, which cannot be built into this product, but must be supplied by the operator.19. WARNING: The brass components of this productcontain lead, a chemical known to the Stateof California to cause cancer and birth defectsor other reproductive harm. (California Health& Safety Code § 25249.5, et seq.)20. WARNING: This product contains di (2-ethylhexyl)phthalate (DEHP), a chemical known to the Stateof California to cause cancer and birth defectsor other reproductive harm. (California Health& Safety Code § 25249.5, et seq.) IMPORTANT! Before first use:Check hydraulic oil level and fill to 1/4″ below theFill Plug hole as needed as stated on page 4. Thoroughly test the Jack for proper operation.If it does not work properly, bleed air from its hydraulic system as stated on page 4.SAVE THESE INSTRUCTIONS.Page 2For technical questions, please call 1-888-866-5797.Item 62496Page 3For technical questions, please call 1-888-866-5797.Item 62496manual including all text under subheadings therein before set up or use of this product.Note: For additional information regarding the parts listed in the following pages, refer to Parts Lists and Assembly Diagram on page .FunctionsSaddle PadSaddleHandleHandleSocketLifting ArmRear CasterCarry HandleFigure AFill PlugCover Screw for Safety Valve. Do not open or adjust.Figure B: Hydraulic Unitmanual including all text under subheadings therein before set up or use of this product. Tool Set UpAttaching the Handle1. Fasten the Upper Handle to the Lower Handle.2. Loosen the Set Screw and insert theassembled Handle into the Handle Socket.3. Tighten the Set Screw.Bleeding1. Remove the Fill Plug.2. Insert the Handle into the Handle Socketto operate the Release Valve.3. Turn the Handle counterclockwise to open the valve.4. Pump the Handle up and down quickly severaltimes to purge air from the system.5. Replace the Fill Plug.Adding Oil1. Remove Fill Plug. See Figure B: Hydraulic Unit.2. Add high grade hydraulic fluid into the Fill Plughole slowly until the oil is 1/4″ below the fill hole.Note: Do not touch the Handle when adding the hydraulic oil.3. Replace the Fill Plug.Page 4For technical questions, please call 1-888-866-5797.Item 62496General Operating InstructionsLiftingPark vehicle on a flat, level, solid, surface safely away from oncoming traffic. Turn off the vehicle’s engine. Place the vehicle’s transmission in “PARK” (if automatic) or in its lowest gear (if manual). Set the vehicle’s emergency brake. Then, chock the wheels that are not being lifted.1. Turn the Handle counterclockwise to lower the Jack.Once the Jack is fully lowered, turn theHandle firmly clockwise to close it.2. Carefully position the Saddle of the Jack underthe vehicle manufacturer’s recommended liftingpoint. (See vehicle manufacturer’s owner’smanual for location of frame lifting point.)3. Pump the Handle until the top of the Jack’s Saddlehas nearly reached the vehicle lifting point. Positionthe Saddle directly under the vehicle’s lifting point. 4. To lift the vehicle, pump the Handle ofthe Jack. Use smooth, full strokes.5. Once the vehicle is raised, slide a jack stand ofappropriate capacity (not included) under a properlifting point referred to in the vehicle owner’smanual. Always use two jack stands, position themat the same point on each side of the vehicle.WARNING! The rated capacity of jack stands is per pair, not the individual capacities combined unless specifically noted on the product by the jack stand manufacturer. Do not exceed rated jack stand capacity. Ensure that the vehicle support points are fully seatedin the saddle of both jack stands. Use a matched pairof jack stands per vehicle to support one end only. Failure to do so may result in the load suddenly falling, which may cause personal injury and/or property damage.6. Center the vehicle’s lifting point(s) on the saddle ofthe jack stand(s). Set the jack stand(s) to the same height according to the manufacturer’s instructions,making sure that they lock securely into position.7. Slowly turn the Handle counterclockwise to lowerthe vehicle onto the saddle(s) of the jack stand(s).Then, turn the Handle firmly clockwise to close it.Lowering1. Carefully remove all tools, parts, etc.from under the vehicle.2. Position the Saddle under the lifting point.Turn the Handle firmly clockwise and raise load high enough to clear the jack stands,then carefully remove jack stands.3. Slowly turn the Handle counterclockwise(never more than 1/2 full turn) to lowerthe vehicle onto the ground.4. Lower the Jack completely. Then, store in asafe, dry location out of reach of children.5. To prevent accidents, turn off the tool anddisconnect its power supply after use. Clean, then store the tool indoors out of children’s reach.Page 5For technical questions, please call 1-888-866-5797. Item 62496Procedures not specifically explained in this manual mustbe performed only by a qualified technician.TO PREVENT SERIOUS INJURY FROM TOOL FAILURE:Do not use damaged equipment. If abnormal noise or vibration occurs, have the problem corrected before further use. Cleaning, Maintenance, and Lubrication1. Before each use, inspect the general conditionof the Jack. Check for broken, cracked, or bentparts, loose or missing parts, and any conditionthat may affect the proper operation of the product.If a problem occurs, have the problem correctedbefore further use.Do not use damaged equipment.2. Before each use, thoroughly test the Jackfor proper operation prior to its actual use.If the Jack appears not to be working properly,follow Bleeding instructions on page 4.3. Wipe dry with a clean cloth. Then, store theJack in a safe, dry location out of reach ofchildren and other non-authorized people.4. Change the hydraulic oil at leastonce every three years:A. With the Jack fully lowered, remove theFill Plug on the top of the Ram.B. Tip the Jack to allow the old hydraulic oilto drain out of the Housing completely,and dispose of the old hydraulic oil inaccordance with local regulations.C. With the Jack upright, completely fill the Ramwith a high quality hydraulic oil (not included)until the oil is 1/4″ below the fill hole.D. Open the valve by turning the Handlecounterclockwise and pump the Handleto bleed air from the system.E. Recheck oil level and re-fill as needed.F. Reinstall the Fill Plug.Page 6For technical questions, please call 1-888-866-5797.Item 62496Page 7For technical questions, please call 1-888-866-5797.Item 62496Record Product’s Serial Number Here:Note: If product has no serial number, record month and year of purchase instead.Note: Replacement parts are not available for this item.TroubleshootingTO PREVENT SERIOUS INJURY:Use caution when troubleshooting a malfunctioning jack. Stay well clear of the supported load.Completely resolve all problems before use. If the solutions presented in the Troubleshooting guide do not solve the problem, have a qualified technician inspect and repair the jack before use.After the jack is repaired: Test it carefully without a load by raising and lowering it fully, checking for proper operation, BEFORE RETURNING THE JACK TO OPERATION.DO NOT USE A DAMAGED OR MALFUNCTIONING JACK!POSSIBLE SYMPTOMSPROBABLE SOLUTION (Make certain that the jack is not supporting a load while attempting a solution.)Jack will not lift at its weight capacitySaddle lowers under loadPump stroke feels spongySaddle will not lift all the wayHandlemoves up when jack is under loadOil leakingfrom Fill Plug X X Check that Release Valve is fully closed. Bleed air from the system.X XXValves may be blocked and may not close fully. To flush the valves:1. Lower the Saddle and securely close the Release Valve.2. Manually lift the saddle several inches.3. Open the release valve and force the saddle down as quickly as possible.XXXJack may be low on oil. Check the oil level and refill if needed.Jack may require bleeding - see instructions on page Bleeding on page 4.XUnit may have too much hydraulic oil inside, check fluid level and adjust if needed.Harbor Freight Tools Co. makes every effort to assure that its products meet high quality and durability standards, and warrants to the original purchaser that this product is free from defects in materials and workmanship for the period of 90 days from the date of purchase. This warranty does not apply to damage due directly or indirectly,to misuse, abuse, negligence or accidents, repairs or alterations outside our facilities, criminal activity, improper installation, normal wear and tear, or to lack of maintenance. We shall in no event be liable for death, injuriesto persons or property, or for incidental, contingent, special or consequential damages arising from the use ofour product. Some states do not allow the exclusion or limitation of incidental or consequential damages, so the above limitation of exclusion may not apply to you. THIS WARRANTY IS EXPRESSLY IN LIEU OF ALL OTHER WARRANTIES, EXPRESS OR IMPLIED, INCLUDING THE WARRANTIES OF MERCHANTABILITY AND FITNESS. To take advantage of this warranty, the product or part must be returned to us with transportation charges prepaid. Proof of purchase date and an explanation of the complaint must accompany the merchandise.If our inspection verifies the defect, we will either repair or replace the product at our election or we mayelect to refund the purchase price if we cannot readily and quickly provide you with a replacement. We willreturn repaired products at our expense, but if we determine there is no defect, or that the defect resultedfrom causes not within the scope of our warranty, then you must bear the cost of returning the product.This warranty gives you specific legal rights and you may also have other rights which vary from state to state.3491 Mission Oaks Blvd. • PO Box 6009 • Camarillo, CA 93011 • 1-888-866-5797。
海港自由工具3-4吨杠杆汽油搬运机说明书

Visit our website at: Emailourtechnicalsupportat:********************************Read this material before using this product.Failure to do so can result in serious injury.SAVE THIS MANUAL.ITEM Rated LoadMax.HeightMin.HeightBase TypeRam PinHole64535 3 Tons (6,000 lb.)44-1⁄4″24-3⁄4″5⁄8″ Round Pin Holes5⁄8″640398 Tons (16,000 lb.)43-3⁄4″25″5⁄8″ Round Pin Holes5⁄8″64006 3 Tons (6,000 lb.)42-5⁄8″23-1⁄4″4″ x 4-1⁄2″ Flat5⁄8″640078 Tons (16,000 lb.)42-1⁄5″23″4-3⁄8″ x 5-1⁄4″ Flat5⁄8″Page 2For technical questions, please call 1-888-866-5797.Long Ram JackRead all safety warnings and instructions. Failure to follow the warnings and instructions may result in serious injury and DEATH from sudden failure of Jack or device. Save all warnings and instructions for future reference.1. Study, understand, and follow allinstructions before operating this device.2. Install ONLY on device designedfor a Jack with the same rating:• A device designed for a Jack witha higher rating may damage the Jackor cause it to suddenly fail under load.• A device designed for a Jack witha lower rating may be damagedor may suddenly fail under load.3. Mount properly as partof a device designed forthis type of Jack before use.Mounting points, maximum length,and rating must be IDENTICAL.Do not mount on different device oruse while not mounted properly.4. Do not use upside-down.5. Do not adjust safety valve.6. Wear ANSI-approved safety gogglesand heavy-duty work gloves during use.7. Keep clear of load whilelifting and lowering.8. Lower load slowly.9. Do not use for aircraft purposes.10. Inspect before every use;do not use if parts loose or damaged. 11. Keep your work area clean and well lit.Cluttered work areas invite accidents.12. Keep bystanders, children, andvisitors away while operating Jack.13. Stay alert. Watch what you aredoing, and use common sense whenoperating a Jack. Do not use a Jackwhile tired or under the influenceof drugs, alcohol, or medication.14. Jack service must be performed only byqualified repair personnel. Service ormaintenance performed by unqualifiedpersonnel could result in a risk of injury.15. When servicing a Jack, use onlyidentical replacement parts.Follow instructions in the “Inspection,Maintenance, and Cleaning” sectionof this manual. Use of unauthorizedparts or failure to follow maintenanceinstructions may create a risk of injury.16. Maintain labels andnameplates on the Jack.These carry important information.If unreadable or missing, contactHarbor Freight Tools for a replacement.17. Industrial applications mustfollow OSHA requirements.18. The warnings, precautions, andinstructions discussed in this manualcannot cover all possible conditionsand situations that may occur.The operator must understand thatcommon sense and caution are factors,which cannot be built into this product,but must be supplied by the operator.SAVE THESE INSTRUCTIONS.Page 3 For technical questions, please call 1-888-866-5797.Long Ram JackRead the ENTIRE IMPORTANT SAFETY INFORMATION section at thebeginning of this document including all text under subheadings thereinbefore set up or use of this product.MountingWARNING! TO PREVENT SERIOUS INJURY: Install ONLY on device designed for a Jack with the same rating:• A device designed for a Jack witha higher rating may damage the Jackor cause it to suddenly fail under load.• A device designed for a Jack witha lower rating may be damagedor may suddenly fail under load. WARNING! TO PREVENT SERIOUS INJURY: Mount properly aspart of a device designed forthis type of Jack before use.Mounting points, maximum length,and rating must be IDENTICAL.Do not mount on different device oruse while not mounted properly.Note: Do not mount upside-down.Note: Jack must have loadon Piston to retract.WARNING! TO PREVENT SERIOUS INJURY: Only use pins that arecapable of supporting the rated load,and ensure that the pins are properly secured before use. Make sure thepins’ diameters are a push fit with just enough clearance so they move freely.1. Secure the Base to the device:a. Round Base:Insert a pin (not included) throughthe holes in the Round Base and inthe device, properly securing it.b. Flat Base:Secure Flat Base tothe device according todevice supplier’s instructions.2. Insert another pin (not included)through the device and Ram Pin Hole.3. Secure pins in place with appropriateretaining rings or cotter pins(both sold separately).HolePage 4For technical questions, please call 1-888-866-5797.Long Ram JackBleedingIMPORTANT! Before first use, check for proper hydraulic oil level in the Jack. Then thoroughly test the Jack forproper operation prior to its actual use. If the Jack appears not to be working properly, it may be necessary to bleedits hydraulic system of excess air.1. Remove the Oil Fill Plug.2. Turn the Release Valvecounterclockwise.3. Insert the Handle into theHandle Socket.4. Apply pressure to the lifting point, andpump the Handle quickly several times.5. Check the Oil Fill Hole and, if necessary,top off the Oil Fill Hole with hydraulic oil.6. Replace the Oil Fill Plug.7. Test the Jack several times for properoperation before attempting to lift a load.If, after purging, the Jack stilldoes not appear to be workingproperly, do not use the Jackuntil it has been repaired by aqualified service technician.Plug HolePage 5For technical questions, please call 1-888-866-5797. Long Ram Jackoperation instructions before use.The following general Jack instructionsdo not cover necessary device-specificoperation warnings and instructions.1. Before each use, thoroughly test theJack for proper operation prior toits actual use. If the Jack appearsnot to be working properly, followBleeding instructions on page 5.2. Clear area near device and Jack.3. Turn the Release Valve firmly clockwise.4. Insert the Handle into theHandle Socket. Pump the Handleto extend the Jack. Use smooth,full strokes for best results.Note: Lower the Jack completely after use.Page 6For technical questions, please call 1-888-866-5797.Long Ram Jackoperation instructions before use.The following general Jack instructionsdo not cover necessary device-specificoperation warnings and instructions.Note: Jack must have loadon Piston to retract.1. Clear area near device and Jack.2. Slowly turn the Release Valvecounterclockwise(never more than two full turns)to allow the Jack to retract.Note: Lower the Jack completely after use.Long Ram JackPage 7 For technical questions, please call 1-888-866-5797.Procedures not specifically explained in this manualmust be performed only by a qualified technician.TO PREVENT SERIOUS INJURY FROM ACCIDENTAL OPERATION: Do not use damaged equipment. If abnormal noise or vibration occurs, have the problem corrected before further use. Cleaning, Maintenance, and Lubrication1. BEFORE EACH USE, inspectthe general condition of the Jack.Check for:• loose hardware,• misalignment or bindingof moving parts,• cracked, bent, or broken parts, and• any other condition that mayaffect its safe operation.2. Before each use, thoroughly test theJack for proper operation prior toits actual use. If the Jack appearsnot to be working properly, followBleeding instructions on page 5.3. Change the hydraulic oil atleast once every three years:a. With the Jack fully lowered,remove the Oil Fill Plug on the side.b. Tip the Jack to allow the oldhydraulic oil to drain out completely,and dispose of the old hydraulic oilin accordance with local regulations.c. With the Jack upright, completelyfill the Reservoir with a highquality hydraulic oil (not included)until the oil just begins to runout of the Oil Fill Hole.d. Then, reinstall the Oil Fill Plug.4. Clean with a clean cloth witha detergent or mild solvent.Then, store the Jack in a safe,dry location out of reach of childrenand other non-authorized people.Page 8For technical questions, please call 1-888-866-5797.Long Ram JackPage 9For technical questions, please call 1-888-866-5797.Long Ram Jack TroubleshootingTO PREVENT SERIOUS INJURY:Use caution when troubleshooting a malfunctioning Jack.Stay well clear of the supported load. Completely resolve all problems before use. If the solutions presented in the Troubleshooting guide do not solve the problem, have a qualified technician inspect and repair the Jack before use. After the Jack is repaired:Test it carefully without a load by raising it and lowering it fully,checking for proper operation, BEFORE RETURNING THE JACk TO OPERATION.DO NOT USE A DAMAGED OR MALFUNCTIONING JACk!POSSIBLE SYMPTOMSPROBABLE SOLUTION (Make certain that the Jack is not supporting a load whileattempting a solution.)Jack will not lift at its weight capacitySaddle lowers under loadPump stroke feels spongySaddle will not lift all the wayHandlemoves upwhen Jack is under loadOil leaking from fillerplugX XCheck that Release Valveis closed fully.X X XValves may be blocked and may not close fully. To flush the valves:1. Lower the Saddle and securelyclose the Release Valve.2. Manually lift the saddleseveral inches.3. Open the release valveand force the saddle down as quickly as possible.XX XJack may be low on oil.Check the oil level and refill if needed.Jack may require bleeding - see instructions on page 5.XUnit may have too muchhydraulic oil inside, check fluid level and adjust if needed.PLEASE READ THE FOLLOWING CAREFULLYTHE MANUFACTURER AND/OR DISTRIBUTOR HAS PROVIDED THE PARTS LIST AND ASSEMBLY DIAGRAM IN THIS DOCUMENT AS A REFERENCE TOOL ONLY. NEITHER THE MANUFACTURER OR DISTRIBUTOR MAKES ANY REPRESENTATION OR WARRANTY OF ANY KIND TO THE BUYER THAT HE OR SHE IS QUALIFIED TO MAKE ANY REPAIRS TO THE PRODUCT, ORTHAT HE OR SHE IS QUALIFIED TO REPLACE ANY PARTS OF THE PRODUCT. IN FACT, THE MANUFACTURER AND/OR DISTRIBUTOR EXPRESSLY STATES THAT ALL REPAIRS AND PARTS REPLACEMENTS SHOULD BE UNDERTAKEN BY CERTIFIED AND LICENSED TECHNICIANS, AND NOT BY THE BUYER. THE BUYER ASSUMES ALL RISK AND LIABILITY ARISING OUT OF HIS OR HER REPAIRS TO THE ORIGINAL PRODUCT OR REPLACEMENT PARTS THERETO,OR ARISING OUT OF HIS OR HER INSTALLATION OF REPLACEMENT PARTS THERETO.Parts ListPart Description Qty 1Top Nut1 2O-Ring1 3Sealing Gasket1 4Reservoir1 5Oil Plug1 6T-Ring1 7Ram1 8Retaining-Ring1 9O-Ring1 10Cylinder1 11Washer1 12Steel Ball3 13a Round Base (64535 / 64039 only)1 13b Flat Base (64006 / 64007 only)Part Description Qty 14Cotter Pin3 15Handle Socket1 16Pin3 17Pump Piston1 18O-Ring1 19Back Up-Ring1 20U-Cup1 21Pump1 22Washer1 23Handle1 24Square Ring1 25Release Valve1 26Guide Ring (64535 / 64006 only)1 27Retaining Ring (64535 / 64006 only)1Record Serial Number Here:Note: If product has no serial number, record month and year of purchase instead.Note: Some parts are listed and shown for illustration purposes only,and are not available individually as replacement parts. Parts maynot be interchangeable. Specify UPC number when ordering:3-Ton Round: 1931753547168-Ton Round: 1931753547543-Ton Flat: 1931753547308-Ton Flat: 193175354778Page 10For technical questions, please call 1-888-866-5797.Long Ram JackPage 11For technical questions, please call 1-888-866-5797.Long Ram Jack Assembly Diagram123461418192122122313a/13b1224251211109826277151617205Harbor Freight Tools Co. makes every effort to assure that its products meet high qualityand durability standards, and warrants to the original purchaser that this product is free from defects in materials and workmanship for the period of 90 days from the date of purchase.This warranty does not apply to damage due directly or indirectly, to misuse, abuse, negligence or accidents, repairs or alterations outside our facilities, criminal activity, improper installation, normal wear and tear, or to lack of maintenance. We shall in no event be liable for death, injuries to persons or property, or for incidental, contingent, special or consequential damages arising from the use of our product. Some states do not allow the exclusion or limitation of incidental or consequential damages, so the above limitation of exclusion may not apply to you. THIS WARRANTY IS EXPRESSLY IN LIEU OF ALL OTHER WARRANTIES, EXPRESS OR IMPLIED, INCLUDING THE WARRANTIES OF MERCHANTABILITY AND FITNESS.To take advantage of this warranty, the product or part must be returned to us with transportation charges prepaid. Proof of purchase date and an explanation of the complaint must accompany the merchandise. If our inspection verifies the defect, we will either repair or replacethe product at our election or we may elect to refund the purchase price if we cannot readilyand quickly provide you with a replacement. We will return repaired products at our expense, but if we determine there is no defect, or that the defect resulted from causes not withinthe scope of our warranty, then you must bear the cost of returning the product.This warranty gives you specific legal rights and you may alsohave other rights which vary from state to state.26541 Agoura Road • Calabasas, CA 91302 • 1-888-866-5797。
Q015 杠杆指示表操作作业指导书
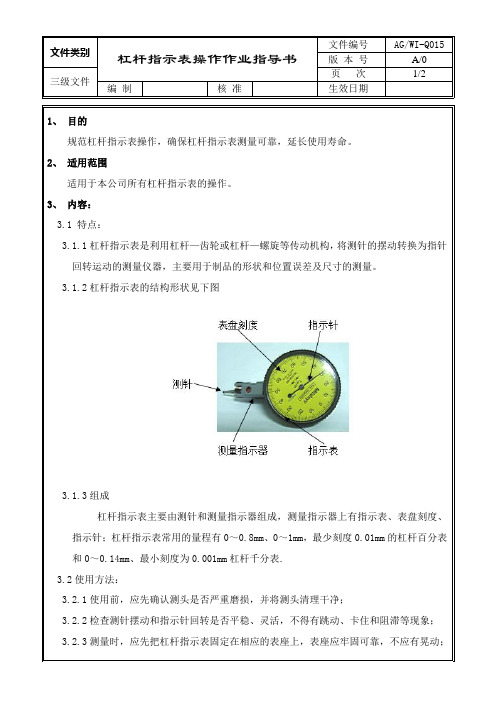
杠杆指示表主要由测针和测量指示器组成,测量指示器上有指示表、表盘刻度、指示针;杠杆指示表常用的量程有0~0.8mm、0~1mm,最少刻度0.01mm的杠杆百分表和0~0.14mm、最小刻度为0.001mm杠杆千分表.
3.2使用方法:
3.2.1使用前,应先确认测头是否严重磨损,并将测头清理干净;
4、注意事项:
4.1保持杠杆指示表清洁、防止碰撞,以免降低测量精度。
4.2当测头磨损时,应及时更换相应长度的测针,并进行确认精度是否有影响。
4.3使用时应尽量让杠杆指示表少接触油污,避免阳光照射,清洁杠杆ห้องสมุดไป่ตู้示表时,应用软布擦拭,以延长杠杆指示表的使用寿命和确保测量时的精度。
3.2.2检查测针摆动和指示针回转是否平稳、灵活,不得有跳动、卡住和阻滞等现象;
3.2.3测量时,应先把杠杆指示表固定在相应的表座上,表座应牢固可靠,不应有晃动;然后将测头缓慢的靠向被测制品的表面(尽量使被测面与测针垂直或平行),给测针施加一定的力度,让指示针适当的转动,接着转动表盘刻度,使指示针指向零位,最后根据测量的需要调整杠杆指示表或被测制品,并进行相应的读数。
1、目的
规范杠杆指示表操作,确保杠杆指示表测量可靠,延长使用寿命。
2、适用范围
适用于本公司所有杠杆指示表的操作。
3、内容:
3.1特点:
3.1.1杠杆指示表是利用杠杆—齿轮或杠杆—螺旋等传动机构,将测针的摆动转换为指针回转运动的测量仪器,主要用于制品的形状和位置误差及尺寸的测量。
3.1.2杠杆指示表的结构形状见下图
chrome DLX 杠杆式婴儿车舱面板说明书
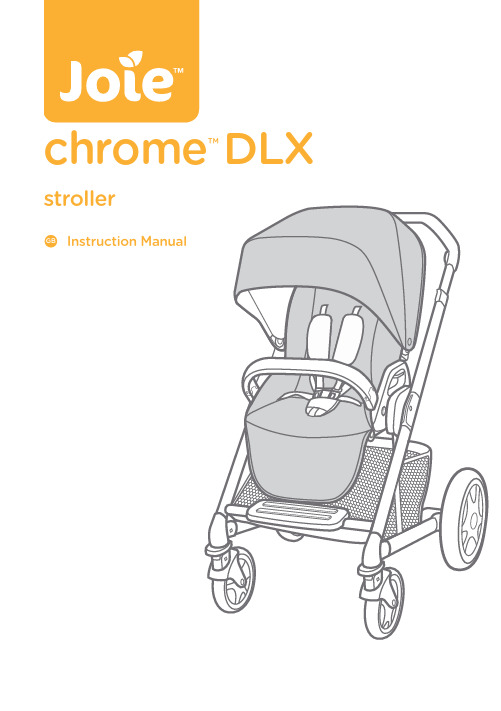
Instruction Manualchrome ™DLXstrollerF IG U R E 29 - 34F IG U R E 41 - 4535 40F IG U R E 51 ~ 5646 5057 61NOTEGBContentsFigures 1-11 WARNING 15 Stroller Assembly18Open Stroller 18 Assemble Front Wheels 18 Assemble Rear Wheels 18 Assemble Armbar 18 Assemble Canopy 19 Stroller Operation 19 Use Canopy19 Switch Seat 19 Adjust Recline 19 Use Buckle 20 Use Shoulder & Waist Harnesses 20 Adjust Calf Support 21 Use Front Swivel Lock 21 Use Brake 21 Adjust Handle 21 Tether Strap 21 Fold Stroller 21 Use Shoulder Harness Pad Cover and Crotch Harness Pad Cover22Use Accessories 23 Care and Maintenance 26EmergencyIn case of emergency or accident, it is most important to have your child taken care of with first aid and medical treatment immediately.ARNINGFOLLOW THE MANUFACTURER’S INSTRUCTIONS.PUT ON ALL THE BRAKES WHENEVER YOU PARK THE PRAM/STROLLER.DO NOT LEAVE CHILDREN UNATTENDED.DO NOT CARRY EXTRA CHILDREN OR BAGS ON THIS PRAM/STROLLER.MAKE SURE CHILDREN ARE CLEAR OF ANY MOVING PARTS IF YOU ADJUST THE PRAM/STROLLER. OTHERWISE THEY MAY BE INJURED.ALWAYS KEEP CHILD IN VIEW WHILE IN PRAM/ STROLLER.DO NOT USE THE SEAT WITH ANY OTHER MODELS OF PRAM/STROLLER.SECURE THE CHILD IN THE HARNESS AT ALL TIMES. USE THIS HARNESS AT ALL TIMES.ALWAYS USE THE CROTCH COMBINATION WITH THE WAIST BELT. IT IS SUGGESTED THAT THE SHOULDER HARNESSES BE USED AS WELL.TO AVOID SERIOUS INJURY FROM FALLING OR SLIDING OUT, ALWAYS USE SEAT BELT.USE THIS TETHER STRAP TO STOP THE PRAM/ STROLLER ROLLING AWAY.DO NOT USE THIS BASSINET ONCE THE CHILD CAN SIT UP UNAIDED.DO NOT USE FOR UNSUPERVISED SLEEPING.Ensure that all the locking devices are engaged before use.Do not let your child play with this product.Never leave the harness buckled when not fitted to a child in the stroller because the harness can form loops which may pose a strangulation hazard.The use of accessories not approved by the vehicle manufacturer is unsafe.Adult assembly required.PLEASE TRANSPORT THE FOLDED STROLLER SAFEL e of this stroller with a child weighing more than 22 kg will cause excessive wear, and stress on the stroller, and could create an unstable condition. Use the stroller with only one child at a time.T o prevent a hazardous, unstable condition, do not place more than 4.5 kg in the storage basket before use. Overloading, folding incorrectly, or using component parts from other manufacturers may cause the pram/ stroller to be damaged﹐ broken or unsafe. Please read the instruction manual carefully.Please read all the instructions in the manual before using the product. Please save instruction manual for future use. Failure to follow these warnings and instructions may result in serious injury or death.Safety belts and restraint system must be used correctly. Child may slip into leg openings and be strangled if the harness is not used.Never use pram/stroller on stairs or escalators.The pram/stroller is not to be used near an open fire or exposed flame.Never allow your child to stand on the pram/stroller orsit in the pram/stroller with head toward front of pram/ stroller.Never place the pram/stroller on roads or dangerous area. The vehicle is designed for use on flat or gently sloping surfaces and may be unstable on higher sloping and uneven surfaces, resulting in the possibility of the vehicle tipping over.Do make sure all parts are assembled and fastened properly before using the pram/stroller.T o avoid strangulation, do not place items with a string around your child’s neck, suspend strings from this product, or attach strings to toys.T o prevent tipping, do not put anything on the handle. Always lift the child in and out of the pram/stroller.Do not lift pram/stroller while child is in stroller.Do not use storage basket as a child carrier.The rear-facing position is suitable for children under 2 years or less.T o prevent tipping, never let child climb the pram/stroller.T o avoid finger entrapment or injury to the body, use care when folding and unfolding the pram/stroller.Be sure the stroller is fully open or folded before allowing child near the pram/stroller.Check that the infant child restraint attachment device is correctly engaged before use.T o avoid strangulation, do make sure your child is clear from the canopy.Discontinue using your pram/stroller if it is damaged or broken.Pram/stroller to be used only at walking speed. This product is not intended for use while jogging.T o avoid suffocation, remove plastic bag and packaging materials before using this product. The plastic bag and packaging materials should then be kept away from babies and children.This product is not suitable for running or skating.Stroller designed to be used from birth shall recommend the use of the most reclined position for new born babies. The parking device must be engaged when placing and removing children.Bassinet is only suitable for a child who cannot sit up unaided, roll over and cannot push itself up on its hands and knees. Maximum weight of the child: 9kg.Bassinet is not to be used for long term sleeping.Do not use or add any mattress other than the one supplied with the bassinet.Please ensure that the storage latch has been properly locked, before lifting or moving the vehicle.The vehicle is not to be used as an unsupervised sleeping environment.The brakes must always be applied when the pram/stroller is not moving.For infant child restraint used in conjunction with a chassis, this vehicle does not replace a cot or a bed. Should your child need to sleep, then it should be placed in a suitable pram body, cot or bed.Stroller AssemblyPlease read all the instructions in this manual before assembling and using this product.Open StrollerSeparate storage latch from storage latch mount 1, and then lift the handle upwards 2, a click sound means the stroller is open completely. Press the recline handle on the back of backrest to rotate the backrest to vertical position. 3! Check that the stroller is completely open before continuing.Assemble Front WheelsAssemble front wheels to front legs. Check that wheels are securely attached by pulling on wheel assemblies. 4To disassemble front wheel, detach front wheel from front leg 5- 2 while pressing the release button. 5- 1Assemble Rear WheelsAssemble brake assembly to rear legs 6, assemble rear wheels to brake assembly 7. Pull the basket tube backward and wrap the connecting tube of rear legs with the flap of the storage basket, and then snap the three buttons 8- 1.! Check that wheels are securely attached by pulling on wheel assemblies. To disassemble rear wheel, detach rear wheel from rear wheel mount 7- 2 while pressing the release button. 7- 1Assemble ArmbarAlign the armbar ends with the armbar mounts, and then insert to lock. 9 To disassemble armbar, press armbar release button 10- 1, and then pull out the armbar. 10- 2Assemble CanopyTo assemble canopy, insert clips into mount 12, then attach 2 pairs of buttons. 11i. Engage the canopy webbing with recline buttons first. 11- 1ii. Then engage the softgood with canopy webbing and buttons. 11 - 2 The completely assembled stroller is shown as 13Stroller OperationUse CanopyOpen the zipper, then push the canopy forwards to open the canopy. 14 ! Please adjust the backrest to upright position before opening the canopy if it is convenient. 15! Please press the backrest before opening the canopy if it is not conve-nient to adjust the backrest to upright position. 16To fold the canopy, pull canopy toward back.! The canopy is NOT removable.Switch SeatThe seat can be switched, which makes mother and child can face to face with each.Squeeze the seat release buttons while lifting the seat. 17Turn the seat to reverse direction, and then insert the seat to seat mounts. 18Adjust ReclineThere are 5 positions for the backrest.To recline the backrest, squeeze the adjustment button 19- 1, and then adjust the backrest to a desired angle. 19- 2 To raise the backrest, push up.!Make sure the recline is set properly for e BuckleRelease BucklePress the center button to release the buckle. 20Lock BuckleMatch the waist belt buckle with the shoulder buckle 21- 1, and click into the center buckle. 21- 2 A “click” sound means the buckle is locked completely. 21- 3! To avoid serious injury from falling or sliding out, always secure your child with harness.! Make sure your child is snugly secured. The space between the child and the shoulder harness is about the thickness of one hand.! Do not cross the shoulder belts. This will cause pressure on child’s neck.Use Shoulder & Waist Harnesses! In order to protect your child from falling out, after your child is placed into the seat, check whether the shoulder and waist harnesses are at proper height and length.22- 1Shoulder harness anchor A22- 2Shoulder harness anchor B22- 3Slide adjusterFor larger child, use shoulder harness anchor A and the highest shoulder slots. For smaller child, use shoulder harness anchor B and the lowest shoulder slots.To adjust the position of the shoulder harness anchor, turn the anchor to be level with the side facing forward. Thread it through the shoulder harness slot from back to front. 23Rethread it through the slot that is closest to child's shoulder height. 24Use slide adjuster to change the harness length. 25- 1Press the button 25- 2, while pulling the waist harness to proper length. 25- 31920Press the recline handle on the back of backrest to rotate the backrest to horizontal position. 31Lift the folding button , step the folding pedal downwards, push the stroller forward to fold. 31The storage latch will automatically hook onto the storage mount, then the stroller is folded and locked completely. 32Use Shoulder Harness Pad Cover and Crotch Harness Pad CoverThe shoulder harness pad cover or crotch harness pad cover can be removed from the webbing. Simply reverse these steps to re-assemble shoulder harness and crotch harness pad cover.Use AccessoriesAccessories may be sold separately or may not be available depending on region.2122Adjust Calf SupportThe calf support has 2 positions.Raise Calf SupportTo raise the calf support, just push it upwards.Lower Calf SupportPress the adjustment buttons on both sides of the calf support 26 - 1, and rotate the calf support downwards. 26 - 2Use Front Swivel LockPush up the front swivel locks to maintain the moving direction. 27 It is recommended to use swivel locks on uneven surfaces.Use BrakeTo lock wheels, step the brake lever downwards. 28 To release wheels, just lift the brake lever upwards. 29 Always apply brake when stroller is in stopped position.Adjust HandleThe handle has 3 positions.To adjust the height of the handle, pull the handle upward or downward 30 - 2 while pressing the handle adjustment button. 30 - 1T ether StrapUse the tether strap to prevent the stroller inadvertently rolling away. Check that when your hand is through the loop, it allows you to easily control the stroller.Fold Stroller! Please fold the canopy before folding the stroller.Use with Joie Child RestraintWhen using with Joie child restraint gemm, i-Gemm please refer to the following instructions.1. To attach adapter, place adapter onto mounts as show 33, A “click”sound means the adapter is locked completely. 342. To attach child restraint, place child restraint onto adapter as show 35,A "click" sound means the child restraint is locked completely. 363. To remove child restraint, lift the child restraint upwards 37- 2 whilepressing the two stroller fix release buttons A. 37- 1!If you have any problems about using the stroller and the adapter, please refer to their own instruction manuals.!To remove adapter, lift the adapter upwards 38- 2 while pressing the two release buttons. 38- 1!Remove the adapter show as 39!Please don’t fold stroller when attaching the child restraint.Use BassinetYou can use this bassinet with the chrome DLX (S1201) stroller. Bassinet Assembly1. Please ensure the 2 support mounts are securely attached.4041! To release the support mounts, please see image 412. Please ensure that both attachment mounts, located on the sides, are securely attached. 4243! To release the attachment mounts, please see image 43- 23. Place the inner mattress and zip the zipper. 44454. Pull up the canopy as illustrated while pressing the buttons on bothsides. 46- 3Check to make sure the handle is secure before placing the child in the bassinet. 46- 1! Please make sure that the handle is in the correct position of usebefore carrying or lifting.5. Attach the loop and hook fasteners on the bottom of bassinet. 47A storage compartment is inside of the bassinet.47- 1! Always use the mattress when using the bassinet. 48! Mattress cover can easily be removed.6. Place the apron onto the top of the bassinet, and attach at the loopand fasteners. 49! Using the apron in cold weather will help give baby a more warm and comfortable environment.7. The completely assembled bassinet is shown as 50! To disassemble the bassinet simply reverse the steps above.8. Place the bassinet directly down until it latches into place. 519. The bassinet is securely attached with a positive “click”. 52! Always remove the seat before using the bassinet.! Please don’t fold the stroller when the bassinet is still attached.! The bassinet can be used with chrome DLX.10. Remove BassinetPress each release side button as shown 53- 1, whilst lifting up the handle simultaneously. 53- 211. Unzip the zipper to remove the canopy soft goods. 542324Use Footmuff ApronThe soft footmuff apron can provide your child with a warm and comfortable environment.Assemble the footmuff apron by following these steps.1. Adjust the calf support and backrest to level position and reclineposition respectively before assembling footmuff apron. 552. Cover the calf support with footmuff apron. 56The assembled footmuff apron is shown as 57.Use Rain CoverTo assemble the rain cover, place it over the stroller. 58!Before using the rain cover, to be make sure the seat has been fas-tened.!When using the rain cover, please always check its ventilation.!When not in use, please check that the rain cover has been cleaned and dried before folding.!Do not fold the stroller after assembling the rain cover.!Do not place your child into the stroller assembled with rain cover dur-ing hot weather.!To be used under adult supervision. Do not use on a stroller without a canopy.Use Seat Linersee images59Use Storage Bagsee images60The maximum load of Storage Bag is 0.45kg.Care and MaintenanceBassinet!Remove mattress from bassinet and mattress pad from liner. Clean liner and mattress with a damp cloth and dry flat.!CLEANING: After removing mattress pad from liner, hand wash,drip dry, NO BLEACH. Only use a damp cloth to clean the mattress pad. Never iron.!Removable seat pad may be washed in cold water and drip-dried. No bleach.!Excessive exposure to sun or heat could cause fading or warping of parts.Stroller!Removable seat pad may be washed in cold water and drip-dried. No bleach.!To clean stroller frame, use only household soap and warm water. No bleach or detergent.!From time to time, check your stroller for loose screws, worn parts,torn material or stitching. Replace or repair the parts as needed.!Excessive exposure to sun or heat could cause fading or warping of parts.!If stroller becomes wet, open hood and allow to dry thoroughly before storing.!If wheels squeak, use a light oil (e.g., Silicon Spray, antirust oil, or sewing machine oil). It is important to get the oil into the axle and wheel assembly. 61!When using your stroller at the beach, completely clean your stroller after use to remove sand and salt from mechanisms and wheel assemblies.2526Nuna Baby Australia Pty Ltd.Unit 1, 35 Lyn Parade Prestons,NSW Australia 2170Share the joy at joie IM-001147E。
福特竞速配件:高性能铝制杠杆臂指示书说明书

No cylinder head pedestal machining or additional components such as guide plates and rocker studs are required.
Engines with non-standard components, particularly performance camshafts, may need additional minimal machining or grinding of the pedestal inserts or different length push rods.
ALUMINUM ROLLER-TIP NEEDLE BEARING ROCKER ARMS STUD-MOUNTED TYPE AND BOLT-ON TYPE Instruction Sheet
NO PART OF THIS DOCUMENT MAY BE REPRODUCED WITHOUT PRIOR AGREEMENT AND WRITTEN PERMISSION OF FORD RACING PERFORMANCE PARTS.
TAPPET NOISE
Engines with standard components should run quietly without tappet noise. If engine operation was not noisy before installation of the rocker arms but is now, simple corrective action is necessary. See instructions below.
Factory Ford shop manuals are available from Helm Publications, 1-800-782-4356
嘉盛调整杠杆填表范本

嘉盛调整杠杆填表范本嘉盛调整杠杆填表范本随着经济全球化的加深与金融市场的日益发达,投资者们对于杠杆调整的需求也越来越迫切。
嘉盛作为一家知名的金融服务提供商,一直以来都在帮助客户实现财务目标。
在这篇文章中,我将为您详细介绍嘉盛调整杠杆的填表范本,并分享我对这个主题的个人观点和理解。
1. 背景和意义杠杆调整是指根据投资者的风险和回报需求,对投资组合进行重新配置,以达到投资目标的过程。
正确调整杠杆可以帮助投资者在风险可控的情况下实现更高的收益。
嘉盛提供的填表范本,旨在帮助投资者全面了解自身风险承受能力,并根据个人情况进行合理的杠杆调整。
2. 嘉盛调整杠杆填表范本的使用方法为了让您更好地理解和运用嘉盛调整杠杆填表范本,我将从以下几个方面进行详细说明:2.1 填表范本的基本使用方法嘉盛调整杠杆填表范本通常由几个主要部分组成:资产配置、持仓比例、风险偏好、风险因子等。
投资者可以根据自身情况填写这些表格,并根据填写结果进行杠杆调整。
2.2 资产配置的意义资产配置是指将资金分配到不同类型资产之间的过程。
在嘉盛调整杠杆填表范本中,投资者需要根据自己的投资目标和风险承受能力来确定资产配置比例。
对于风险承受能力较高的投资者,可以适度增加股票、期货等高风险资产的比例。
2.3 持仓比例的考虑因素持仓比例是指投资者在资产配置中各个资产类别的比例。
投资者在填写嘉盛调整杠杆填表范本时,需要根据自身情况进行持仓比例的评估。
对于投资者而言,应考虑到资产的流动性、风险收益特征等因素,合理分配不同资产类别的比例。
2.4 风险偏好的重要性风险偏好是指投资者在决策中对风险的态度和偏好。
填写嘉盛调整杠杆填表范本时,投资者需要清楚地了解自己对风险的容忍度和承受能力。
对于风险承受能力较低的投资者,应适度减少高风险资产的比例,以防止过于冒险的投资行为。
3. 个人观点和理解在我个人的观点和理解方面,嘉盛调整杠杆填表范本是一个非常实用的工具。
它能够帮助投资者全面了解自身的风险承受能力,并根据个人情况进行合理的杠杆调整。
LD-2010杠杆设备产品目录说明书

Li f t i n g D ev i c e s2Lifting BeamsEconomicalAdjustable Spreader/Lifting Beam(ASLB16) ............................................. 4 Adjustable Lifting Beam (ALB17) .............. 4 Fixed Spread Lifting Beam (FSLB19) ....... 5 Basket Sling Lifting Beam (BSLB18) ........5 I ndustrialLow Headroom Multiple Spread Lifting Beam (LHLB20) ....................6, 7 Heavy Duty Twin Basket Sling Lifting Beam (HDLB22) ..................................8 Twin Hoist Lifting Beam (THLB25) ...........9 SpreaderFixed Spreader Beam (FSB30) ...............10 Adjustable Spreader Beam (ASB32) .......11 Modular Spreader Beam (MSB14) . (12)Coil LifterD ixon Coil Hook with Pivoting Wedge (DCH80) .....................................13 H eavy Duty Coil Hook (HDCH82) .. (13)Construction ToolsBeam/Girder ClampsBeam Flange Clamp (BFC) (14)Girder Clamp (GC)..................................14 Beam Grab (F) ........................................15 Pipe & Manhole Lifting Pipe Grab (C/S) ......................................16 Pipe Tongs (PLT) ....................................17 Concrete Manhole Lifter (MHL) ..............18 Manhole Sleeve Lifter (MCL) .................19 Tea Cup Pipe Carrier (TC) .....................20 Tea Cup Sling (TCS) ..............................20 Pipe Pick (CPP)......................................21 Barrier Grab (BRG74) . (22)TABLE OF CONTENTSFork Lift AccessoriesBooms F ixed Fork Lift Booms (FFLB) ........................23 S ingle Fork Hook (SFH) .................................23 T elescoping Fork Lift Booms (TFLB) ..............24 D ouble Fork Beam (DFB) ...............................24 P ivoting Fork Lift Booms (PFLB) .. (25)Specialty ProductsFiberglass Battery Lifting Beam (BLB) .............26 Battery Lifting Beam, Low Headroom(BLBLHA) ......................................................27 Adjust-A-Link ....................................................28 Adjust-A-Leg .. (29)Gantry CranesFixed Steel (H90) .......................................30, 31 Adjustable Steel (K90) ................................32, 33Fixed Aluminum (HA90) ...................................34 Adjustable Aluminum (KA90) . (35)3 Quality Engineered ProductsAll of the products in this catalog have beenengineered and produced to the highest qualitystandards and meet or exceed all applicable U.S.government standards including OSHA andASME B30.20 AND B30.9. Random proof testingis standard. Proof testing with certification isavailable upon request for a nominal charge.Product OverviewLifting BeamsPRODUCT INFORMATIONAllow for multiple pick points ofthe load for balance or supportissues. Spreader Beams havea top rigging that add stability tothe lift. Available in 9 standardstyles.Beam/Girder ClampsFor use in lifting and positioningstructural beams. Two stylesmay also be hung from loadbearing beams to suspendhoists or other lifting devices.Coil LiftersUse to lift, manipulate andreposition coils. Requiresminimum aisle space equal toLifter arm length. Available in 2standard styles.Gantry CranesThese portable cranes allow forthe pick up and transport of aload wherever you have asmooth and level floor. Availablein either steel or aluminum, fixedor adjustable height.Pipe & Manhole LiftingFor the lifting and positioningof steel, iron and concrete pipes.Pipe Grabs are for metal pipes.Pipe Picks and Tea Cups forconcrete pipes.Barrier GrabsScissor style grab is the easyway to lift and move concreteroad barriers. Auto-latch forhands-off operation.Forklift AccessoriesThree styles of booms andtwo hook devices provideadded lifting capabilities toyour forklift trucks.Battery Beams provide a non-conductive lifting method forindustrial batteries. (i.e.-forkliftbatteries)Adjust-A-Leg slings allowcontrolled lifting of loads wherelift points are not equidistantfrom the load’s center of gravity.Specialty Products4FEATURES• Use for 2, 3 or 4 point lifting or as spreader beam (add top rigging)• Adjustable lifting points • Good for unbalanced loads • Low headroom • Shackles included • 6" spread adjustments • 4" bail adjustments OPTIONS• Pair of swivel hooks - Code S*• Top chain rigging - Code CFEATURES• Adjust bail for unbalanced load • 6" spread adjustments • Shackles includedOPTIONS• Pair of swivel hooks - Code S*ECONOMICAL LIFTING BEAMSAdjustable Spreader/Lifting Beam (ASLB16)* For Optional Swivel Hooks, add an “S” to part No. Contact Lift-All for added cost.Adjustable Lifting Beam (ALB17)Bail Adjustment forUnbalanced LoadsLift Point Adjustment for Load Length5ECONOMICAL LIFTING BEAMSFEATURES• Fixed spread lifting • Eye hooks with latches• Sealed construction for cleaner beamFixed Spread Lifting Beam (FSLB19)Basket Sling Lifting Beam (BSLB18)FEATURES• Best beam for low headroom applications • Fixed spread lifting• Bent bar hooks allow for 2" wide sling eyes - One set for 3' & 4' spreads - Two sets for 6' - 12' spreads •Spread 2 is 1/2 of Spread 16FEATURES• Great for low headroomapplications• Swivel hooks with latchesstandard•3' & 4' beams have 2 spreads•6' & longer beams have 3 spreads(Inner spread lengths are shorterthan outer spreads by 1' increments•Additional or repositioned holesavailable INDUSTRIAL LIFTING BEAMSLow Headroom Multiple Spread Lifting Beam (LHLB20)7Extra Holes Allows for extra hook positions in addition to the standard holes.Specify number and spread.Low Headroom Multiple Spread Lifting Beam (Continued)Options:Extra HooksAllows for multiple pick points.Saves time from having to move hooks.FasPinsAllows for easy repositioning of hooks.Recommended for frequent hookposition changes.8FEATURES• For use with slings in a basket hitch • Latch hooks designed to minimize sling eye damage• Two sets of fixed hooks are standard for all lengths over 4'• Inner spread is 1/2 of outer spread • Extra spreads available upon requestINDUSTRIAL LIFTING BEAMSHeavy Duty Twin Basket Sling Lifting Beam (HDLB22)9FEATURES• For use with two hoists to increase lift capacity• Swivel hook with latch standardTwin Hoist Lifting Beam (THLB25)INDUSTRIAL LIFTING BEAMSCenter hook offset to accommodate hoists of unequal capacities.Custom pick points for both top and bottom.Center bail and extra pair ofhooks for maximum versatility.10FEATURES• Adds stability to lift where headroom is not limited• Chain rigging standard, wire rope rigging availableFixed Spreader Beam (FSB30)SPREADER BEAMS* Add a "W" for Wire Rope RIggingAdd an "A" for Adjust-A-Link Rigging11SPREADER BEAMSAdjustable Spreader Beam (ASB32)FEATURES• Great versatility and stability where headroom is not limited• Chain rigging standard, wire rope rigging available• Telescoping spread adjusts in 1 in. increments* Add a "W" for Wire Rope RIggingSpread12SPREADER BEAMSModular Spreader Beam (MSB14)FEATURES• Designed to accommodate spreads from 10' to 22'• Capacities in 1 and 2 tons • Lightweight• Faspin with lanyard allows for quick adjustment of spread in 1' increments• Hair pin cotter to rigging attachment • Designed and manufactured to ASME standardsRecommended Optional Top Rigging (Add "R" to Part Number)2 Sets of 2-Leg Tuflex Roundslings per BeamOuter TubeInner Tube - each system contains (2)Short TubeLifting Eye Dimensions13COIL LIFTERSDixon Coil Hook with Pivoting Wedge (DCH80)Heavy Duty Coil Hook (HDCH82)FEATURES• For easy upending of coils from horizontal to vertical• Pivoting wedge great for lifting coils that have been stacked • Wedge also acts as a coil retainer• Excels in use with small, lightweight coils • Good for limited overhead clearance•Standard handle for easier coil positioningFEATURES• Designed for heavy duty applications• High tensile alloy steel plate reduces physical size and weight • Counter balanced to hang level when empty • Inside radius on hooks avoid coil edge contact • Guide handles for ease of hook positioning • Handles a wide range of coil widths•Available with optional padding for additional coil protectionHeadroom14FEATURES• Light weight, portable design• Jaw opening adjusts to a wide range of beam types and flange widths• Built in suspension pin for minimum headroom • Opposing thread screw spindles for rapid operation• Large Bail option available for large crane hooksCONSTRUCTION TOOLSBeam Flange Clamp (BFC)Great for the lifting of or suspension from I-BeamsFEATURES• Heavy duty design for lifting wide range of flange beams and plate girders• Screw-spindle design ensures positive grip • Opposing thread screw spindles for rapid operation• Simple design for minimum maintenanceGirder Clamp (GC)Designed for the lifting of or suspension from large girders and I-BeamsLarge Bail OptionAPBH15FEATURES• Heavy duty design for lifting wide flange beams and plate girders• Recessed base accepts studs in beam surface• Eliminates need for slings, chokers and spreader barsCONSTRUCTION TOOLSBeam Grab (F)(For vertical lifting only, not suspension)Operation:1.Lower grab onto beam.2. Lift arms, if necessary, to slide under beam flange.3. As beam is lifted, pressure forces arms together to secure beam.4. The heavier the beam, the greater the clamping force.W16FEATURES• Automatically clamps to pipe when lowered onto it • Moveable outriggers stabilize the pipe during lift • No blocking required• Quick and efficient handling of properly balanced pipeCONSTRUCTION TOOLSPipe Grab (C OR S)(For cast iron or steel pipe only)Operation:1. Lower grab onto approximate center of pipe. Grab will open and seat on pipe.2. Lift slowly to check for pipe balance. Never exceed a 15° angle.3. If angle exceeds 15°, lower pipe and reposition grab.17FEATURES• Pipe Tongs are made of sturdy construction to handle pipe, round bars, castings, etc• Tongs are provided with bare steel curved gripping arms• Optional replaceable urethane pads available to protect smooth or polished surfaces• Load must be balanced and controlled when lifting • May be used in pairs with a lifting beam for added stabilityCONSTRUCTION TOOLSPipe Tongs (PLT)(For vertical lifting only, not suspension)Decreasing the load by bumping or substantial imbalance can, under certain circumstances loosen the grip.Do not use in diameters other than those specified on nameplate.Specifications - Fixed DiameterSpecifications - Adjustable DiameterFixedAdjustable18FEATURES• Designed for 4"-6" concrete wall thickness• Will not damage concrete seat • Legs can be quickly positioned to balance load• 2 and 3 leg models available • Conforms to ASME B30.9 & B30.20Note: Constant tension required to maintain positive load contact.CONSTRUCTION TOOLSConcrete Manhole Housing Lifter (MHL)2 Leg Model3 Leg Model19TWO LEG LIFTERSTHREE LEG LIFTERSFEATURES• Easy to attach and release from sleeve • The quick and easy way to place cast manhole sleeves• 2 or 3 leg models availableManhole Sleeve Lifter (MCL)Note: Flange diameter range 12"-30".CONSTRUCTION TOOLS20FEATURES• Efficiently handles concrete water and sewer pipes • Three sizes available to lift up to 18 tons • Standard hand grip for ease of installation• Optional spoon handle available to assist Tea Cup placement (Model TC66 only) in small diameter pipesCONSTRUCTION TOOLSTea Cup Pipe Carrier (TC)Tea Cup Sling(TCS)For use with Tea Cup Carriers• 5 ft. standard lengthOPERATION1. Drop TCS Slingdown through hole in pipe2. Align and insert Tea Cup Pipe Carrier onto sling3. Lift pipeModel TC66Tea Cup Spoon Handle (TCSH)(Includes Bolt-on Lip)21FEATURES• Simple and fast• No need to reach inside the pipe• Worker remains above the pipe at all times • Use to easily join length of pipeCONSTRUCTION TOOLSPipe Pick (PP)(For concrete pipe only)Lift arm counter-weighted for easy removal22FEATURES• Labor saving, quick and easy hands-off operation•No slings or chains to attach•Reduces damage to barrier due to moving•Replaceable polyurethane lifting pads for unpaintedbarriers•Replaceable steel "Dog Point" lifting pads for paintedbarriers (typical in coastal areas) CONSTRUCTION TOOLSBarrier Grab (BRG74)The Barrier Grab isdesigned to handle 6"-12"nominal widths at thebarrier top (W)1. Grab in openposition is placedonto barrier. Autolatchwill disengage whenhoist line becomesslack.2. Raising cranehook will thencause pads toengage barrier.3. Lower barrierinto position.4. Slack in hoistline will engageauto-latch, holdinggrab open for removaland placement of nextbarrier.23FEATURES• Easy attachment - no tools required • Welded construction for durability • Promotes versatility of fork lift trucks • 3,000 lb. rated capacityFEATURES• Fixed length beam design• Restraining chain with grab hook FORK LIFT ACCESSORIESFixed Fork Lift Booms (FFLB)Note: Fixed hook shown, swivel hook also available.FFLB-15 Single Pick Point• Use with 1" or 2" wide web sling • Optional swivel hook availableFFLB-40 Multiple Pick Points• 5 alternate hook positions at 1 foot intervals • Fixed or swivel hooks availableSingle Fork Hook (SFH)24FEATURES• Telescoping boom for versatility • T-Pin locks boom into position • Handle on end for easy extension of boom• Swivel hooks with latch are standard• Restraining chain with grab hook standard• 12 ft. maximum horizontal reachFORK LIFT ACCESSORIESTelescoping Fork Lift Booms (TFLB)FEATURES• Easy attachment - no tools required• Welded construction for durability• Promotes versatility of forklift trucksDouble Fork Beams (DFB)Note: Swivel hook shown, fixed hook also available.25FEATURES• Vertical adjustability in 5 increments up to 40°, 6' 4" maximum height• Telescoping boom for versability • T-Pin locks boom into position • Handle on end for easy extension of boom• Swivel hooks with latch are standard• Restraining chain with grab hook standard reachFORK LIFT ACCESSORIESPivoting Fork Lift Booms (PFLB)26FEATURES• Non-conductive for lifting industrial size fork lift or similar batteries• Up to 70% lighter than other beams• Available for single or multiple size batteries• Heavy duty capacities of 4,800 lbs. and 7,000 lbs.• Acid resistant coated polyester straps and hooks • 36" standard spread - custom lengths available • Swivel hooks standardFORK LIFT ACCESSORIESFiberglass Battery Lifting Beam (BLB)Fixed Length (BLBF)Adjustable (BLBA)Optional J HooksAvailable in place of swivel hooksNote: Maximum spread range is 12"* Add a "J" to Part No. for Optional J Hooks27FEATURES• Low Headroom, 18.3"• Adjustable to handle batteries of different lengths • Non-conductive beam• Acid-resistant, coated polyester straps with either swivel or J-hookSPECIALTY BEAMSBattery Lifting Beam (BLBLHA)Low Headroom, AdjustableJ Hooks StandardSwivel Hooks Available28FEATURES• Chain cannot be removed from the master control plate, assuring the capacity rating will not be compromised• Alloy steel master control plate for strength and reliability • Each assembly serialized for traceability• Complies with OSHA - proof tested and certified• Grade 100 chain provides approximately 25% higher capacities than our previous Adjust-A-Links - replaces larger, more expensive slings• New angled plate design reduces bending torque on chain and plate - reduces wear and extends sling life• Wider top bearing surface reduces wear to both plate and crane hook• Versatile - one sling does many jobs• Using two Adjust-A-Links on the same crane hook eliminates the need for expensive triples and quads• Heat treated alloy steel construction for long sling life• Yellow powder coating on master plate and hooks prevents rust – extends sling life• More compact plate design fits larger hooks for easier rigging • Less bulky than typical double adjustable chain slings • High visibility yellow fittings make assembly easy to spot• Easily adjustable to accommodate a wide range of applications • No time wasted searching for just the right slingSPECIALTY SLINGSAdjust-A-LinkThe adjustable, two leg chain slingSingleDoubleBasketNever exceed rated capacities.Chain must be seated at the base of adjusting slot of the Master Control Link.29FEATURES• Easily adjust the legs for a level lift of unbalanced and non-symetrical loads• Can be locked in place for repetitive lifts • Use in pairs for 4 point lifts• Can be used as top rigging for spreader beams • Great as rigging to move machinerySPECIALTY SLINGSAdjust-A-LegThe adjustable, two leg wire rope sling* Reach should be a length of 70% or greater of the distance between pick up points.Level lifting of non-symetrical loads where lift points are not equidistant from center of gravity.Operation:For a level lift, adjust the leg lengths so that the master plate is above the approximate center of gravity. Test position by lifting only until one end of the load is raised. Lower and reposition master plate and legs for another test. Repeat until load raises without tilting. Adjust-A-Leg must be loaded to at least 10% of rated capacity before legs will fully lock into place.Level lifting of symetrical loads where lift points are not equidistant from center of load.Lifting of any load at an angle.Typical Applications30FEATURES• Balanced design allows for easyrolling, even under load•Simple bolt together construction•Includes 4 steel swivel casters• Easy set-up and maintenance GANTRY CRANESFixed Steel (H90)3132FEATURES• Balanced design allows for easy rolling, even under load• Simple bolt together construction • Includes 4 steel swivel casters • Easy set-up and maintenance• Height adjustable in 1 ft. incrementsGANTRY CRANESAdjustable Steel (K90)3334FEATURES•Light-weight Aluminum construction•Balanced design allows for easy rolling,even under load•Simple bolt together construction•Includes 4 poly-coated swivel casters•Easy set-up and maintenance GANTRY CRANESFixed Aluminum (HA90)35FEATURES• Light-weight Aluminum construction • Balanced design allows for easy rolling, even under load• Simple bolt together construction • Includes 4 poly-coated swivel casters • Easy set-up and maintenance• Height adjustable in 6 in. incrementsGANTRY CRANESAdjustable Aluminum (KA90)Manufacturing and Warehousing in:AtlantaChicago Houston Las VegasHeadquarters, Customer Service & Manufacturing:1909 McFarland Dr.Landisville, PA 17538-1810800-909-1964FAX: 717-898-1215E-Mail:*********************CustomerService:****************************Cat. LD-2010 Integra 10M 110LIFTING DEVICES RETURN POLICY1. Items to be returned MUST BE UNUSED and in like new condition.2. An RGA number must be obtained from our Customer Service Agents. No unauthorized returns will be accepted.3. Freight for returns must be prepaid by the customer to the location designated by our Customer Service Agents.4. Requests for returns must be made within 30 days of the original shipment date.5. A 25% restocking charge will apply to all authorized returns.6. Credit will be issued after receipt, inspection and acceptance.7.Custom ordered or modified items may not be returned.。
约翰逊电力有限公司:通用耦合杠杆耐用指南说明书

JOHNSON POWER LTD.& MAINTENANCE GUIDEIMPORTANT - Read CarefullyThese instructions are provided to aid in the properhandling, installation and maintenance of Johnson Power universal joint shafting. They should be carefully read and followed. Failure to do so may result in unsatisfactory service as well as serious personal injury or property damage.IF THERE ARE ANY QUESTIONS CONCERNING PROPER INSTALLATION, MAINTENANCE ORSTORAGE, CONTACT JOHNSON POWER BEFORE PROCEEDING.HANDLING & STORAGE:Examine all shafting and related material upon arrival and note any damage or shortage on bill of lading. Such damage is the responsibility of the freight carrier. All transportation and storage should be in a horizontal position only.Balance weights should not be removed. Unbalance will cause vibrations and premature wear of shafting and the bearings of the connected units.Shocks, bumps and mishandling must be avoided to assure proper performance. Abuse could result inbending the driveshaft, causing whipping and unbalance problems. Damage of this nature will VOID the warranty.FOR SPECIAL LONG TERM STORAGEINSTRUCTIONS CONTACT JOHNSON POWER. Shafts that have been stored for a long time, should be re-greased in the working position prior to start up. See Lubrication section.REPAIR SHOULD ONLY BE DONE BY THOSE WITH EXPERIENCE IN APPLYING, INSTALLING, SERVICING AND REBUILDING INDUSTRIAL UNIVERSAL JOINT TYPE DRIVESHAFTS.EQUIPMENT ALIGNMENT:The defection angles (β°1 & β°2) of both joints must also be equal to one another within ±1°. This can be achieved by either Parallel offset or Angular misalignment. The maximum joint operating angle of 3° is recommended for optimum bearing life. While, in theory, shafts should be offset slightly, to initiate bearing rotation, experience indicates that there is sufficient deviation in mostapplications for essential bearing rotation. The preferred angle is ½° to 1°, unless the driver or driven produces torque spikes, such as a reciprocating engine or compressor, then an operating angle of 2° to 3° is desirable.Parallel offsetshaft series and operating speed, consult Johnson Power or our master catalog.FOUNDATIONS / SUPPORTING STRUCTURES:1. Foundations for all installations must be adequate.The appropriate steel beams and/ or concrete foundation, with hold down bolts, are necessary to maintain alignment and to eliminate damaging vibrations.2. Steady bearing supports must be rigid enough tosustain steady bearing forces and natural frequency requirements. The following guidelines must be observed:A. Keep spans as short as possible.B. End connections must be rigid.C. Position channel and I - Beams for their greateststrength advantage. The natural frequency of the bearing supports should be a minimum of four times running speed (RPM) forcing frequency, in all direction perpendicular and parallel to shafting centerline.INADEQUATE FOUNDATIONS OR STEADY BEARING SUPPORTS WILL VOID THE JOHNSON POWER UNIVERSAL JOINT COUPLING WARRANTY.INSTALLATION:Check flange bores and shaft diameters for proper fit. All mating surfaces, bores and faces must be clean and free from grease, oil, dirt, nicks and other contaminates to insure a proper fit and function of mating parts. The shaft should not extend beyond the flange face.Stock bored flanges are bored to +.001 / -.000 tolerance. This allows the flange to be gently tapped onto the driving and driven shafts. One set screw is provided to lock the flange into position.An additional set screw at 90 degree, is supplied for vertical installations. In vertical applications where theu-joint shafting weight exceeds 300 lbs., we recommend an interference fit, split ring key or jam nut to support the weight.For light interference or shrink fits heat the flange uniformly (preferably submerged in oil not exceeding 350° F)to expand the bore. Align the keyways in both the shaft and flange, slide flange onto shaft and allow to cool. CAUTION: Do not attempt to hammer an undersized flange on without heat.Some VB U-joint couplings are provided with a taper bored flange, which is secured in place, with the steady bearing installed. See table 1, for the jam nut torque specifications. The larger VB shafts use straight bored flanges, with two set screws and a locking plate.After installing companion flanges, check the run-out of the flange face and pilot diameter (.005 T.I.R. maximum permissible).TABLE 1VB Torque Specifications31 - 37 3/4" - 16 100 lb-ft41 - 48 1.00" - 20 230 lb-ft55 - 61 - 71 1 1/4" - 18 450 lb-ft81 1 2" - 18 550 lb-ft88 2.00" - 12 800 lb-ftNOTE: Above torque based on lightly oiled threads.Splined telescoping assemblies should not be disassembled to avoid misalignment and unbalance. Shaft yokes must be aligned in phase. Check the match markings.For fixed length shafts, one companion flange must be free to move to allow slight length variation due to temperature changes, etc.To insure long life and trouble free operation, units should be regularly inspected to insure that bolts are tight, mating flanges are secure and lubrication seals and zerk fittings are intact.Any unusual sound or vibration should be located and corrected immediately. WHEREVER PEOPLE OR EQUIPMENT CAN BE ENDANGERED BY ROTATING UNIVERSAL SHAFTS, SAFETY DEVICES MUST BE PROVIDED BY USER!TABLE 2Companion Flange Torque Specifications31,61,71 3/8 - 24 8 30 lbs. ft. 37,41,81 7/16 - 20 8 50 lbs. ft. 48,55 1/2 - 20 8 75 lbs. ft.88 5/8 - 18 8 210 lbs. ft.75 M6 10.9 10 lbs. ft. 90, 100 M8 10.9 25 lbs. ft.120 M10 10.9 50 lbs. ft.150 M12 10.9 90 lbs. ft.180-8 M14 10.9 140 lbs. ft. 180-10, 225 M16 10.9 218 lbs. ft. 250 M18 10.9 298 lbs. ft. 285 M20 10.9 428 lbs. ft. 315, 350 M22 10.9 575 lbs. ft. 390 M24 10.9 738 lbs. ft. 435 M27 10.9 1106 lbs. ft.NOTE: Torque values based on lightly oiled threads. Once components are properly seated, graduate up to final torque value.INSTALLATION OF UNIVERSAL JOINT COUPLING HORIZONTAL APPLICATION (Single & Multiple Section)Lower compressed U-Joint Coupling into position and extend ends so that the pilot is seated firmly into matingtorque indicated in Table 2.VERTICAL APPLICATION: (Single Section)Additional protection must be provided to eliminate the possibility of the drive shaft from coming apart at the splined section (Fig1). Compress the slip joint with care to preventdamaging the dust cap or spline seal. Position the universal joint shaft at the top, making sure that the pilots are seated firmly into mating companion flange and that the bolt holes are aligned. Then extend the slip joint and secure at the bottom, making sure to check that the slip joint is not completely extended or bottomed out to insure that there is adequate length adjustment for the application requirements. Torque the companion bolts/studs to the value, shown in table 2.VERTICAL APPLICATION: (Multiple Section)Match marking is used to insure that the shafting isreassembled as it was manufactured and balanced. Start with the upper-most VB section, universal joint end of shafting (FIG 2), making sure that the pilot is seated into mating companion flange or B-Flange and that the bolt holes are aligned. Insert bolts/studs and tighten specified torque indicated in Table 2.Allow the shafting to hang plumb, and secure the steady bearing housing to the support structures. Steadybearings supplied by Johnson Power are designed for 1.5 degrees maximum misalignment capability. Shim the bearing as required to minimize the universal joint operating angle and steady bearing alignment, asrequired. On steady bearings using set screws to friction hold inner race to "B" stub (small to medium duty series), TIGHTEN EACH SET SCREW ON STEADY BEARING RACE alternately until they stop and the socket wrench starts to spring. When both sets screws are tightened the bearing is seated. On large series shafting, positiongrease zerk fitting on the steady bearings so that the zerk is up (opposing gravity). For floating or expansion bearings, position housing at bearing mid- float before securing to the support or "B" stub. Other intermediate VB sections are installed in the same manner, follow match marking and FIG 2.The lower VA section is installed, the same as the single section vertical. Making sure to install the slip section towards the driven unit.ALIGNMENT MARKSON SHAFTINGALIGNMENT MARKSON SHAFTINGPREFERED METHODVAVBVBTOP FLANGEBOTTOM FLANGESLIPCOMPRESSEDROPE OR CHAINFigure 1Figure 2LUBRICATION:more frequent lubrication.TROUBLE SHOOTING GUIDEP ROBLEM C AUSE S OLUTIONV IBRATIONS 1. Operating near critical or half critical speed resonance. Change speed, multiple shafting, rework using different tube size.2. Operating at or near driver or driven equipment natural frequency.Consult with equipment manufacture.3. Non-rigid foundations, floors or steady bearing beams.Reinforce and/or perform structural analysis.4. Driver or driven components out of balance.Consult with equipment manufacturer.5. Bent shafting during installation or balancing required.Return for straightening and/or balancing.6. Pump noise.Consult pump manufacturer.7. Ears not in phase Disassemble and align yoke.(Fig 1 or 2)8. Flange faces not seated.Check for burrs or grit and reseat.9. Operating speed within a torsional vibration mode.Perform torsional analysis. Consult Johnson Power.10. Driver and driven shafts/Companion flange not parallel within 1°.Align and adjust, shim structure if necessary.11. Driver and driven shaft run-out Consult Component Manufactures.12. Flange face or pilot run-out exceeding .005" TIR.Check fit, if exceeds consult manufacturer.13. Steady bearing inner race not secured to shafting.Tighten set screw.14. Steady bearing not self aligning, failure or binding.Shim bearing or replace.15. Bearings elsewhere in the system failed or binding.Replace or consult equipment manufacturer.16. Exceeding maximum joint acceleration (consult cat.Reduce angle and/or speed.17. Dry or brinelled (needle bearing indentations) Universal Joint Replace defective joints / Check lubrication section / Review operating parameters18. System resonance/vibration Vibration analysis preformed.19. Excessive radial movement at the slip yoke or binding movement Lack of lubrication, overload, condition, consult manufacturer.20. Companion flange, other U-Joint or steady bearing fastener loose.Secure fastener / Check for vibrations21. Slip assembly bottomed out (especially under heavy axial load).Revise installation.1. Set screw tightened improperly.Tighten set screw.F LANGE S LIPPINGO FF S HAFT 2. Exceeding weight limitations for stock bored flanges/shaft diameterundersize.Add additional set screw or replace with interference fit bore flange/locking collar. SAFETY and WARRANTY“We recommend the use of safety guards to protect personnel from contact with rotating universal joint couplings. Johnson Power agrees to repair or replace without charge, F.O.B. our factory, or at our option allow credit for, any portion of a product which proves to be defective in material or workmanship within a period of 180 days from the date the product is placed in service. Products claimed to be defective in material or workmanship within a period of 180 days from the date the product is placed in service. Products claimed to be defective must be held for our shipping instructions and no claim will be allowed unless we have a reasonable opportunity to examine the products. WE MAKE NO WARRANTY AS TO MERCHANTABILITY OR AS TO FITNESS OF PRODUCTS FOR A PARTICULAR PURPOSE OR AS TO THE RESULT TO BE OBTAINED FROM THEIR USE BY PURCHASER OR OTHERS. We make no warranties, express or implied, statutory or otherwise.”These instructions have been complied with best of our knowledge and belief. We cannot accept responsibility for possible errors herein.。
Swift Lift 服务杠杆抬升机说明书

This is the safety alert symbol. It is used to alert you to potential personal injury hazards. Obey all safety messages that follow this symbol to avoid possible injury or death.Swift Lift Service JackModel number Operating Instructions & Parts Manualcapacity Atd Tools Inc.160 Enterprise Drive, Wentzville, MO 63385PreParatiOnassembly1. Assemble the 2-piece handle with provided bolt .2. Insert handle into the handle fork. Tighten the bolt on handle fork to prevent accidental removal of handle while in use.Before Use1. Verify that the product and application are compatible, if in doubt call ATD Tools Technical Service line (636)327-9050.2. Before using this product, read the operator's manual completely and familiarize yourself thoroughly with the product, its components and recognize the hazards associated with its use.3. To familiarize yourself with basic operation, locate and turn the release valve (handle):a. Clockwise until firm resistance is felt to further turning. This is the ‘cLOSed ’ release valve position used to raise the saddle.b. Counter-clockwise, but no more than 1/2 turn from the closed position. This is the ‘OPen ’ release valve position used to lower the saddle.4. With saddle fully lowered, remove the vent screw. Pump 6 to 8 full strokes. This will help release any pressurized air which may be trapped within the reservoir. Check oil level. Proper oil level will vary from just covering the ram cylinder to 3/16” above it as seen from the oil filler hole. Reinstall vent screw.5. Ensure that jack rolls freely. Raise and lower the unloaded saddle throughout the lifting range before putting into service to ensure the pump operates smoothly. Replace worn or damaged parts and assemblies with ATD Tools authorized replacement parts only.SaFetY and GeneraL inFOrMatiOnSave these instructions. For your safety, read, understand, and follow the information provided with and on this jack before using. The owner and operator of this equipment shall have an understanding of this jack and safe operating procedures before attempting to use it. The owner and operator shall be aware that use and repair of this product may require special skills and knowledge. Instructions and safety information shall be conveyed in the operator's native language before use of this jack is authorized. If any doubt exists as to the safe and proper use of this jack, remove from service immediately.inspect before each use. Do not use if broken, bent, cracked or damaged parts are noted. Any jack that appears damaged in any way, or operates abnormally shall be removed from service immediately. If the jack has been or suspected to have been subjected to a shock load (a load dropped suddenly, unexpectedly upon it), immediately discontinue use until jack has been checked by a factory authorized service center (contact distributor or manufacturer for list of authorized service centers). It is recommended that an annual inspection be done by qualified personnel. Labels and Operator's Manuals are available from the manufacturer.PrOdUct deScriPtiOnThis Service Jack is designed to lift, but not support, one end of a vehicle. Immediately after lifting, loads must be supported by a pair of appropriately rated jack stands. This Swift Lift service jack has a unique feature that provides fast, no load lifts to the jacking point, at which time it lifts in approximately 0.75~0.2" increments.NEVER use hydraulic jack as stand-alone device. After lifting, immediately support the lifted vehicle withSPeciFicatiOnSModel Capacity Jack Size (L x W x H)Min. HeightMax. Height Saddle Dia.Atd-73323-1/2 Ton30-7/8" x 14-7/8" x 7-1/4"4"21-5/8"4-3/4"OPeratiOnLifting Only attachments and/or adapters supplied by the manufacturer shall be used. Lift only on area of the1. Follow the vehicle manufacturer’s recommended guidelines for lifting. Engage the emergency brake and chock each unlifted wheel in both directions to prevent inadvertent vehicle movement.2. Close the release valve by turning the handle clockwise until firm resistance is felt.3. Refer to the vehicle manufacturer owner’s manual to locate approved lifting points on the vehicle. Center jack saddle under lift point.4. Verify lift point, pump handle to contact lift point. To lift, pump handle until load reaches desired height.5. Transfer the load immediately to appropriately rated jack stands.NEVER use hydraulic jack as a stand alone device! ALWAYS transfer the lifted load IMMEDIATELY to apair of appropriately rated jack stands. Use one pair of jack stands per vehicle. Rated capacity is per pair only! Do not exceed rated capacity.LoweringBe sure all tools and personnel are clear before lowering load. Slowly open the release valve! The more you turn the handle counter-clockwise, the faster the load will come down. Maintain control of the rate of speed at which the load lowers at all times!1. Raise load high enough to clear the jack stands.2. Remove jack stands carefully.3. Slowlyturn the handle counter-clockwise, but no more than 1/2 full turn. If the load fails to lower: a. Use another jack to raise the vehicle high enough to reinstall jack stands. b. Remove the malfunctioning jack and then the jack stands. c. Use the functioning jack to lower the vehicle.4. After removing jack from under the vehicle, fully lower the saddle to reduce ram exposure to rust and contamination.Figure 1 - Typical Jack NomenclatureMaintenancenOte: Use only good grade hydraulic jack oil. Avoid mixing different types of fluid and NEVER use brake fluid, turbine oil, transmission fluid, motor oil or glycerin. Improper fluid can cause premature failure of the jack and the potential for sudden and immediate loss of load. We recommends Mobil DTE 13M or equivalent.adding oil1. With saddle fully lowered set jack in its upright, level position. Remove vent screw.2. Fill with oil until ~3/16" above the inner cylinder as seen from the oil filler hole. Reinstall vent screw. changing oilFor best performance and longest life, replace the complete fluid supply at least once per year.1. With saddle fully lowered, remove vent screw.2. Lay the jack on its side and drain the fluid into a suitable container.note. Dispose of hydraulic fluid in accordance with local regulations.3. Fill with oil until ~3/16" above the inner cylinder as seen from the oil filler hole. Reinstall vent screw. LubricationA periodic coating of light lubricating oil to pivot points, axles and hinges will help to prevent rust and assure that wheels, casters and pump assemblies move freely.cleaningPeriodically check the pump piston and ram for signs of rust or corrosion. Clean as needed and wipe with an oily cloth.note: Never use sandpaper or abrasive material on these surfaces!StorageWhen not in use, store the jack with saddle fully lowered.Symptom Possible causes corrective actionJack will not lift load• Release valve not tightly closed• Load is too heavy • Ensure release valve tightly closed • Consider higher capacity jackJack will lift, but not maintain pressure •Release valve not tightly closed• Hydraulic unit malfunction•Ensure release valve tightly closed• Discontinue use, contact ATD Toolstechnical serviceJack will not lower after unloading• Reservoir overfilled• Linkages binding• Fluid level low • Drain fluid to proper level• Clean and lubricate moving parts • Ensure proper fluid levelPoor lift performance• Fluid level low•Hydraulic unit malfunction • Ensure proper fluid level •Discontinue use, contact ATD Tools technical serviceWill not lift to full extension• Fluid level low• Ensure proper fluid level trOUBLeSHOOtinGrePLaceMent PartSAvailable Parts: Please refer to the Parts drawing when ordering parts. Not all components of this kit are replace-ment items, but are illustrated as a convenient reference of location and position in the assembly sequence. When ordering parts, give Model number, serial number and description below. Call or write for current pricing:Atd Tools Inc. 160 Enterprise Drive, Wentzville, MO 63385 Tel:(636)327-9050 Fax:(636)327-9046One Year LiMited WarrantYFor a period of one (1) year from date of purchase, atd tools inc. will repair or replace, at its option, without charge, any of its products which fails due to a defect in material or workmanship, or which fails to conform to any implied warranty not excluded hereby.Performance of any obligation under this warranty may be obtained by returning the warranted product, freight prepaid, to atd tools inc. Warranty Service Department, 160 Enterprise Drive, Wentzville, MO 63385.Except where such limitations and exclusions are specifically prohibited by applicable law, (1) the CONSUMER'S SOLE AND EXCLUSIVE REMEDY SHALL BE THE REPAIR OR REPLACEMENT OF DEFECTIVE PRODUCTS AS DESCRIBED ABOVE, and (2) atd tools inc. SHALL NOT BE LIABLE FOR ANY CONSEQUENTIAL OR INCIDEN-TAL DAMAGE OR LOSS WHATSOEVER, and (3) THE DURATION OF ANY AND ALL EXPRESSED AND IMPLIED WARRANTIES, INCLUDING WITHOUT LIMITATION, ANY WARRANTIES OF MERCHANTABILITY AND FITNESS FOR A PARTICULAR PURPOSE, IS LIMITED TO A PERIOD OF ONE (1) YEAR FROM DATE OF PURCHASE. Some states do not allow limitations on how long an implied warranty lasts, so the above limitation may not apply to you. Some states do not allow the exclusion or limitation of incidental or consequential damages, so the above limitation or exclusion may not apply to you. This warranty gives you specific legal rights, and you may also have other rights which vary from state to state.replacement Parts illustration for model atd-7332:87145618122313141019171516JKHHGF E D C B N JW Q P A M N L A MN L VUTS9R 11** Replacement requires special skills, knowledge, and equipment. Only authorized service center may perform the repair and/or replacement of these items.replacement Parts for model atd-7332:Item Part No. DescriptionQty 1G730-04000-000Hydraulic Power Unit 12G730-90009-K01Front Wheel Assy.23G520-90026-K02Rear Caster Assy.24G730-00004-000Saddle15G62S-03300-200Vent Screw Assy.16G730-90009-K04U-joint Assy.17G730-90009-K02 Handle (2 pc.)18G933-00001-000Handle Grip195102-08018-000Handle Retaining Bolt, M8*18110G931-00009-000Spring, Handle Fork (Right)111G931-00003-000Spring, Lift Arm 212G610-03005-000Spring, Pump 113G610-00009-000Bolt1145303-00020-000Lock Washer, M20215G62S-00008-000Bolt, M124165303-00012-000Lock Washer, M12417G730-00005-000Cover118G730-90009-K03Pump Piston Assembly 119G62S-05000-000Handle Fork 1**G6122S-120Repair Kit-Item DescriptionQty A O-ring, D7.8x2.654B Back-up Ring 1C O-ring, D15x2.651D U-cup1E Back-up Ring 1F O-ring, D44.5x2.41G Back-up Ring 1H O-ring, D63x2.652J O-ring, D8.2x2.42K O-ring, D31.6x3.51L Back-up Ring 2M Steel Ball, D9.522N Steel Ball, D6.355P Back-up Ring 1Q O-ring, D6x31R O-ring, D7.2x2.651S Back-up Ring 2T O-ring, D17.6x2.52U Back-up Ring 1V O-ring, D25x2.651W Steel Ball, D6.741(in #5)O-ring, D8.8x1.91Repair Kit Contentsatd tools inc.160 Enterprise Drive, Wentzville, MO 63385Tel: (636)327-9050 Fax: (636)327-9046 Notes。
CSEVS22T 22吨杠杆抬杆说明书

Manufactured to comply with the OPERATING MANUAL • WARNING INFORMATION • PARTS LISTASME PASE-2019 Safety StandardThis is the safety alert symbol . It is used to alert youto potential personal injury hazards . Obey all safetymessages that follow this symbol to avoid possibleinjury or death .IMPORTANT: READ THESE INSTRUCTIONS BEFORE OPERATINGTHE NATURE OF HAZARDOUS SITUATIONSMETHODS TO AVOID HAZARDOUS SITUATIONSBEFORE USING THIS DEVICE, READ THIS MANUAL COMPLETELY AND THOROUGHLY, UNDERSTAND ITS OPERATING PROCEDURES, SAFETY WARNINGS AND MAINTENANCE REQUIREMENTS.It is the responsibility of the owner to make sure all personnel read this manual prior to using the device. It is also the responsi-bility of the device owner to keep this manual intact and in a convenient location for all to see and read. If the manual or product labels are lost or not legible, contact Cornwell for replacements. If the operator is not fluent in English, the product and safety instructions shall be read to and discussed with the operator in the operator's native language by the purchaser/owner or his designee, making sure that the operator comprehends its contents.The use of portable automotive supporting devices are subject to certain hazards that cannot be prevented by mechanical means, but only by the exercise of intelligence, care, and common sense. It is therefore essential to have owners and personnel involved in the use and operation of the equipment who are careful, competent, trained, and qualified in the safe operation of the equipment and its proper use. Examples of hazards are dropping, tipping or slipping of loads caused primarily by improp-erly securing loads, overloading, off-centered loads, use on other than hard level surfaces, and using equipment for a purpose for which it was not designed.• Read, study, understand and follow all instructions before operating this device• User and bystanders must wear eye protection that meets ANSI Z87.1 and OSHA standards• Inspect the jack stands before each use. Do not use if damaged, altered, modified, in poor condition or unstable due to loose or missing hardware or parts. Make corrections before using the stands• Use as a matched pair only• Use only on a hard level surface capable of supporting the load• Stands are to be used in matched pairs to support one end of the vehicle only. Do not simultaneously support both ends or one side of the vehicle.• Center load on saddle. Do not use saddle lugs to support the load• Do not use jack stands beyond its rated capacity. Do not shock load• Maximum load capacity per matched pair shall not exceed the rated capacity of the individual stand• Apply the emergency brake and put the gear shift lever in park or in gear if a manual shift transmission, and chock the tires that will not be lifted off the ground• Check the stands for solid contact with the ground and vehicle• Make sure the stand's locking pins are fully engaging the stand on both sides and the support column saddle is making contact with a vehicle support surface that can support the load• Ensure both stands are set at same height and locking pins are fully engaged• Do not crawl under vehicle when placing/removing stands• Consult the vehicle manufacturer for the proper frame support locations• No alterations shall be made to these stands• Never use the stand's lower support plate (if so equipped) as a load bearing surface for the locking pin• Failure to heed these warnings may result in serious or fatal personal injury and/or property damageWARNING: Indicates a hazardous situationwhich, if not avoided, could result in deathor serious injury .WARNING: This product can expose you to chemicals including nickel, which is known to the State of California to cause cancer andSETUPOPERATIONPREVENTATIVE MAINTENANCE1. Install the support column in the stand where the locking holes in the column are facing toward the stand's locking pin attachment location.2. Most pin type jack stands are designed with a support column that can always be removed from the stand; therefore do not attempt to move or lift the stand by pulling up on the column or its saddle.3. Some stands are equipped with a storage holder for the locking pin. Locking pins connected to the stand by way of a tether orlanyard should not be stored in the stand's support column receiver hole.This is the safety alert symbol used for the PREVENTATIVE MAINTENANCE section of this manual to alert you to potential personal injury hazards. Obey all instructions to avoid possible injury or death.1. Always store the jacks stands in a well protected area where they will not be exposed to inclement weather, corrosive vapors, abrasive dust, or any other harmful elements. The stands must be cleaned of water, snow, sand, grit, oil, grease or other foreign matter before using.2. Every jack stand owner is responsible for keeping the stand labels clean and readable. Use a mild soap solution to wash external surfaces of the stand. Contact Cornwell Tools for a replacement label if your stand's label is not readable.3. Inspect the stands before each use. Do not use the stands if any component is cracked, broken or bent. Do not use the stand if it has loose ormissing hardware or components, or is modified in any way. Take corrective action before using the stand again. Premature wearing or damage to components caused by loose or missing hardware is not eligible for warranty consideration.This is the safety alert symbol used for the OPERATING INSTRUCTIONS section of this manual to alert you to potentialpersonal injury hazards. Obey all instructions to avoid possible injury or death. IMPORTANT: Before attempting to raise any vehicle, check vehicle service manual for recommended lifting surfaces.1. Make sure the work floor is clean and free of debris and obstacles.2. Chock the vehicle's tires that will not be lifted. Make sure the emergency brake is on and the vehicle's transmission is either in the park mode or in gear if a manual transmission.3. Raise the vehicle to a safe working height and make sure the jack and vehicle setup are stable before positioning the jack stands. DO NOT CRAWL UNDER THE VEHICLE TO POSITION OR REMOVE STANDS.4. Position the jack stands right below the areas of the vehicle support points as specified by the vehicle manufacturer.5. Lift the support columns as close to the vehicle as possible without the saddles on the columns coming in contact with the vehicle. Make sure the support columns' teeth are engaged with the locking pawls.6. Slowly and carefully lower the vehicle on the jack stands. Shock loads or loads dropped abruptly on stands can cause premature metal fatigue or even stand failure depending on the weight of the vehicle and the speed of descent that impacts the stands' support columns. The load should be supported in the center of the support column saddles, not the locating lugs of the saddles.7. Check the load for stability. If the load is not stable, lift the load off the stands and correctly reposition the stands. 8. When work is completed, raise the vehicle high enough off the stands where the stands can be easily removed.CONSEQUENCES OF NOT AVOIDING HAZARDOUS SITUATIONSFailure to read this manual completely and thoroughly, understand its OPERATING INSTRUCTIONS, SAFETY WARNINGS,MAINTENANCE INSTRUCTIONS and not comply with them, and neglecting the METHODS TO AVOID HAZARDOUS SITUATIONS could cause accidents resulting in serious or fatal personal injury and/or property damage.WARRANTY COVERAGECornwell Quality Tools Company (“Cornwell”) warrants against defects on this product for a period of TWO (2) YEARS from the date of original retail purchase. Subject to the conditions and limitations set forth below, Cornwell will, at its option, either repair or replace anypart of the product(s) that proves defective by reason of improper workmanship or materials.This warranty does not cover any damage to this product that results from accident, abuse, misuse, natural or personal disaster, or any unauthorized disassembly, repair, or modification. Repairs, disassembly and modification are only authorized to be made by Cornwell ora warranty service center approved by Cornwell.WARRANTY SERVICETo obtain warranty service, contact your Cornwell dealer.EXCLUSIONS AND LIMITATIONSTHIS WARRANTY AND THE REMEDIES SET FORTH ABOVE ARE EXCLUSIVE AND IN LIEU OF ALL OTHER WARRANTIES, REMEDIES AND CONDITIONS, WHETHER ORAL OR WRITTEN, EXPRESS OR IMPLIED. CORNWELL SPECIFICALLY DISCLAIMS ANY AND ALL IMPLIED WARRANTIES, INCLUDING, TO THE EXTENT PERMITTED BY APPLICABLE LAW, ANY WARRANTIESOF MERCHANTABILITY AND FITNESS FOR A PARTICULAR PURPOSE. IF CORNWELL CANNOT LAWFULLY DISCLAIM IMPLIED WARRANTIES UNDER THIS LIMITED WARRANTY, ALL SUCH IMPLIED WARRANTIES ARE LIMITED IN DURATION TO THE DURATION OF THIS WARRANTY. IN NO EVENT SHALL CORNWELL BE LIABLE TO THE PURCHASER OR TO THE USER OFA CORNWELL PRODUCT FOR ANY SPECIAL, INCIDENTAL OR CONSEQUENTIAL DAMAGES BASED UPON BREACH OF WARRANTY, BREACH OF CONTRACT, NEGLIGENCE, TORT, OR ANY OTHER LEGAL THEORY. SUCH DAMAGES INCLUDE, WITHOUT LIMITATION, EXPENSES, LOST REVENUES, LOST SAVINGS, LOST PROFITS, OR ANY OTHER INCIDENTAL OR CONSEQUENTIAL DAMAGES ARISING FROM THE PURCHASE, USE OR INABILITY TO USE THE CORNWELL PRODUCT.Some states do not allow the exclusion or limitation of incidental or consequential damages or exclusions or limitation on the duration of implied warranties or conditions, so the above limitations or exclusions may not apply to you. This warranty gives you specific legal rights, and you may also have other rights that vary by state.Repair kits and replacement parts are available for many Cornwell products, regardless of whether or not the product is still covered by a warranty plan.PARTS LISTDue to safety precautions, the only replaceable part is RS152201, locking pins with wire. Product label kits are also available as: RSCSEVS22TPLK - 1 pair of labels SupportColumnBaseLocking Pinwith Wire:RS152201。
杰克 H5 系列产品使用说明书

H5系列产品使用说明书H5series product instruction manual使用说明和零件样本下载地址:PLEASE DOWNLOAD THE MANUAL AND SPARE PARTS FROM THE FOLLOWING WEBSITE: ÇäŇÌÇÁ Èfåêä ãÊêÈ ÇäÈÙäêåÇÈ èâXÙ ÇāÈĖÏêä åæ ÇäåèâÛÇäÊÇāé:POR FAVOR DESCARGAR EL MANUAL Y LIBRO DE PARTES Y REPUESTOS LO SIGUIENTE ENSITIO WEB:Пожалуйста,загрузитеинструкциюпоэксплуатацииидеталировку(списокзапасныхчастей ) соследующеrовебсайта:产品标准代号:Q/T K001-2017Standard code of the products: Q/T K001-2017杰克缝纫机JACK SEWING MACHINE杰克科技股份有限公司JACK TECHNOLOGY CO.,LTD.●公司地址(Address of Company):中国浙江省台州市椒江区三甲东海大道东段1008号NO.1008,DONGHAI AVENUE EAST,JIAOJIANG DISTRICT,TAIZHOU CITY,ZHEJIANG邮编:318000●国内销售部(Domestic Trade Department):电话(TEL):0086-0576-881177788 88177789传真(FAX):0086-0576-881177758●国贸部(International Trade Department):电话(TEL):0086-0576-881177782 88177774传真(FAX):0086-0576-881177787●免费售后服务电话:400-8876858●资料如有更改,恕不另行通知,以实物为准。
Removed_桥梁课程设计书54

桥梁工程课程设计装配式预应力混凝土简支T型梁姓名:余将学号:1252010721班级:路桥一班专业:土木工程(道路与桥梁方向)指导老师:沈明燕目录设计资料桥梁跨径及桥宽 3 设计荷载 3桥面铺装 3材料及施工工艺 3材料性能参数 3设计依据 3计算方法 4设计任务横断面布置 4主梁内力计算 4设计过程主梁间距与主梁片数 5主梁跨中截面主要尺寸及主梁截面细部尺寸拟定 5 截面几何特性 6截面效率指标 6横截面沿跨长的变化 6横隔梁的设置 6恒载内力计算 7活载内力计算 7内力组合 16装配式钢筋混凝土简支T形梁桥设计资料1.桥梁跨径及桥宽标准跨径:40.9m主梁全长:40.72m计算跨径:40.5m桥面净宽:(0.5+1+14+1+0.5)m=17m(防撞栏+人行道+四车道+人行道+防撞栏)桥面横坡:2.0%2.设计荷载:公路Ⅰ级,人群荷载3.0KN/m23.桥面铺装沥青表面处治2cm(重力密度为kN/m2),混凝土垫层厚6~12cm(重力密度为24kN/m2),T梁的重力密度为25kN/m24.材料及施工工艺混凝土:采用C40混凝土。
预应力钢筋采用1*7(7股)钢绞线,标准强度f pk=1860Mpa;普通钢筋采用HRB335级和R235级钢筋;钢板:锚头下支撑垫板,支座垫板等均采用普通A3碳素钢。
按后张法施工工艺制作主梁,采用70mm的波纹管和OVM锚具。
5.材料性能参数(1)混凝土强度等级为C40,主要强度指标:强度标准值:f ck=26.8Mpa,f tk=2.4Mpa强度设计值:fcd=18.4Mpa,ftd=1.65Mpa弹性模量:Ec=3.25*104Mpa(2)预应力钢筋采用1*7标准型15.2-1860-Ⅱ-GB/T 5224-1995钢绞线抗拉强度标准值:fpk=1860Mpa,抗拉强度设计值:fpd=1260Mpa弹性模量:Ep=1.95*105Mpa相对界限受压区高度:ζa=0.4,ζpu=0.2563(3)普通钢筋a.纵向抗拉及构造普通钢筋采用HRB335.其强度指标抗拉强度指标:fsk=335Mpa 抗拉强度设计值:fsd=280Mpa弹性模量:Es=2.0*105Mpab.采用的R235钢筋,其强度指标抗拉强度指标:fsk=235Mpa 抗拉强度设计值:fsd=195Mpa弹性模量:Es=2.1*105Mpa6.设计依据(1)交通部颁《公路桥涵设计通用规范》JTG D60-2004 简称“规范”;(2)交通部颁《公路钢筋混凝土及预应力混凝土桥涵设计规范》 JTG D62-2004简称“公预规”;(3)交通部颁《公路桥涵地基与基础设计规范》 JTJ 024-85.7.计算方法:极限状态法装配式钢筋混凝土简支T形梁桥设计任务1、横断面布置(1)用AUTOCAD绘制桥梁平、纵、横断面图,并绘制中梁与边梁的结构图;(2)主梁间距与主梁片数;(3)主梁跨中截面主要尺寸拟定;(4)主梁截面细部尺寸;(5)计算截面几何特性;(6)计算截面效率指标p(要求p在0.5以上);(7)横断面沿跨长的变化;(8)横隔梁设置;2、主梁内力计算(1)恒载内力计算A. 一期恒载集度;B. 二期恒载集度;C. 恒载内力。
Equity 电子工作台及键盘杠杆说明书
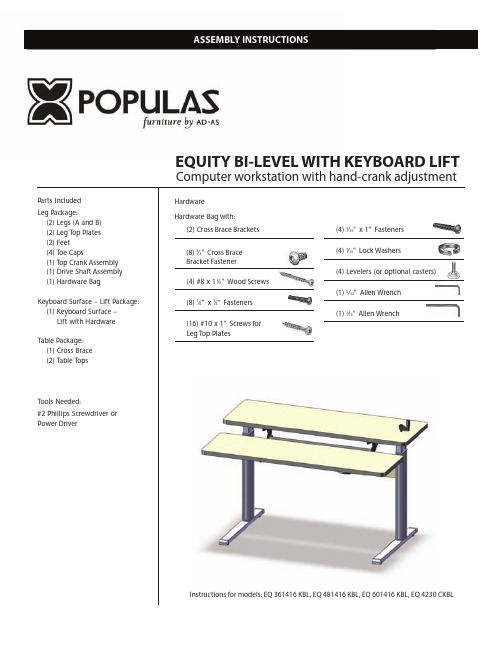
P arts IncludedLeg Package:(2) Legs (A and B)(2) Leg Top Plates(2) Feet(4) Toe Caps(1) Top Crank Assembly(1) Drive Shaft Assembly(1) Hardware Bag Keyboard Surface –Lift Package:(1) Keyboard Surface –Lift with Hardware Table Package:(1) Cross Brace (2) Table TopsHardware Bag with:(2) Cross Brace Brackets (8)3⁄8" Cross Brace (4) #8 x 13⁄4" Wood Screws(8) 1⁄4" x 3⁄4" Fasteners(16) #10 x 1" Screws for Leg Top Plates(4) 5⁄16" x 1" Fasteners (4) 5⁄16" Lock Washers(4) Levelers (or optional casters)(1) 5⁄32" Allen Wrench(1) 3⁄16" Allen WrenchHardwareTools Needed:#2 Phillips Screwdriver or Power DriverComputer workstation with hand-crank adjustmentEQUITY BI-LEVEL WITH KEYBOARD LIFTASSEMBLY INSTRUCTIONSBracket FastenerInstructions for models: EQ 361416 KBL, EQ 481416 KBL, EQ 601416 KBL, EQ 4230 CKBLUnpack and identify all parts.Place table tops upside down on padded surface and identify front edge.STEP TWOIdentify the legs (A and B) and their orientation as shown in the diagram.Look at the bottom of the leg to identify the leg letter (A or B).Legs must be positioned in correct orientation to operate. Shaft couplers face inward..STEP FOURAttach feet to legs using two 5⁄16" button head fasteners and lock washers per foot. Insert toe caps and levelers.Feet are offset to the front of the table.STEP THREEAttach leg top plates to legs using four ¼" button head fastener per plate as shown.Leg BAttach cross brace bracket to cross brace using four #8 13⁄4" screws as shown.Attach cross brace bracket to legsas shown.Attach mounting plates to tabletops using #10 x 1" screws.Attach Keyboard Surface-Lift using #10 x 1" screws as shown.with front lever. Tilt adjustment is made with a knob.Clean with soft cloth and mild cleaners suitable for furniture.。
堪倪公司浮动和杠杆值房子说明书
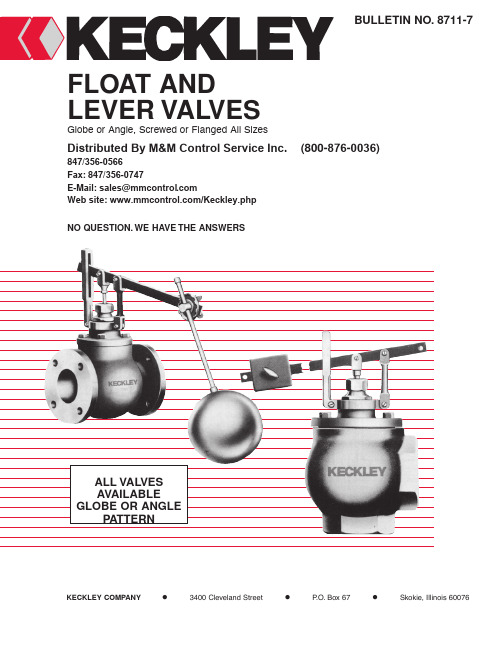
BULLETIN NO.8711-7FLOAT AND LEVER VALVESGlobe or Angle, Screwed or Flanged All SizesDistributed By M&M Control Service Inc. (800-876-0036)847/356-0566F ax :847/356-0747E-M ail : sales @mmcontrol .comW eb site : www.mmcontrol .com/Keckley.php NO QUESTION.WE HAVE THE ANSWERSKECKLEY COMPANY•3400 Cleveland Street•P .O.Box 67•Skokie, Illinois 60076ALL VALVES AVAILABLE GLOBE OR ANGLEPATTERNSince 1914, Keckley engineering and manufacturing has been working for industry and commercial building installations worldwide.Keckley Float and Lever Valves excel in their construction and performance.With the purchase of Klipfel Valves Inc.in 1962, there was a combining of engineering talents and features of both valve companies resulting today in this complete line.Float Valves are actuated Lever Valves designed to control the level of liquids.Lever Valves are designed to control the flow of liquids, gases or steam.This can be done by manual operation, float boxes or mechanisms, electric motors or other actuators through linkage to the lever of the valve.2KECKLEY COMPANY• 3400 Cleveland Street • P .O.Box 67• Skokie, Illinois 60076Open or closed Feed water storage tanks heaters Vats Condensate Process tanks tanks Cooling towers Reservoirs Basins Sprinkler Standpipes services Receivers Swimming pools All valves can be used on filling control (close on level rise) ordrainage control (open on level rise)applications.Floats — all materials, sizes and connectionsFloat Rods — brass, stainless steel or galvanized pipeSwivel Adaptor — vertical operation of float rod;replaces rosette and joins the lever and float rodTrim — main valve and seat can be brass or stainless steel Discs and Cups — T eflon fortemperatures exceeding 125°F to maximum of 350°F .1)Valve size2)Keckley type number 3)Connections(screwed or flanged)4)Globe or angle pattern 5)Media6)Maximum operating pressure 7)Discharge pressure of valveif other than atmosphere 8)Maximum temperatureAny additional information to help us insure a correct selection.Typical InstallationsTypesFloat Valve#27 #7#77Lever Valve#62 #73#773Sizes1⁄2" - 12" 1⁄2" - 2"2" - 12"How Operated Direct Internal Internalt o l i Pt o l i PDouble Seated/X ——Not Tight ClosingSingle Seated/— X XTight ClosingInner Valve Bronze Neoprene NeopreneDisc DiscConstruction (Body)Standard Bronze 1⁄4" - 11⁄2"Cast Iron 2"—LargerSpecial Consult FactoryBronze, Cast Iron, Cast Stainless Steel — Available in Most SizesConnections Screwed 1⁄2" - 3"Flanged 2" & LargerMax.T emperature (Std.)406°F 125°F125°FConsult factory for high temperature trim.e b o l GXXXAngle-side Inlet X X—Angle-bottom Inlet——XFloat Size1⁄2" - 2" Valves 7" Diameter Type 304 Stainless SteelStandard21⁄2" - 4" Valves 8" Diameter T ype 304 Stainless Steel5" - 8" Valves 10" Diameter Type 304 Stainless Steel10" - 12" Valves 12" Diameter Type 304 Stainless SteelOther Float Materials - Consult FactoryAllowable Pressure Low-Med.Low-Med.Low-HighDropMax.Working Varies Varies250 psie r u s s e r Pe z i S r e Pe z i S r e PSee Bulletin Page4-6 7-97-9Level ControllersUsed to Operate the Above Lever ValvesTypes20 Float Box For Valve Sizes 1⁄2" - 6" Cast Iron Body Screwed or Std.Flanged See Bulletin Page 10KECKLEY COMPANY •3400 Cleveland Street•P.O.Box 67•Skokie, Illinois 600763Balanced Double Seated (not tight closing)Globe or AngleBRONZE CAST IRON STAINLESS STEEL BODYNO.27 GLOBENO.62 GLOBEThe No.27double seated float valve is the typemost widely used for the automaticcontrol of the supply of liquids to anopen tank where dead-end closing isnot essential and valve inletpressures are normal.Manythousands are in use on large andsmall water, oil and chemicalstorage tanks in all types ofindustries.Where a drop-tight closing floatvalve, or a valve for higher thanordinary pressure is required, one ofthe single seated valves, describedon the following pages, should beselected.The maximum inletpressures for the sizes of the No.27valve are shown in the table on theopposite page.The No.62lever valve is the samevalve minus the float, float rod androsette.It may be operated by a floatinside a closed tank or float cage;byhand or electric solenoid as a quickopening valve;and wherever adouble seated sliding stem valve isrequired.These valves are allmetal, simple in operation, sturdy inconstruction and of the bestmaterials and workmanship.Adouble seated inner valve, asillustrated, is standard.Both angleand globe pattern bodies areavailable in all the sizes.Thestandard valve can be adapted tonearly any installation.The swivel yoke, which supports thelever, can be turned and secured atany angle.The length and angle ofthe float rod can be adjusted at therosette so that the valve can beeasily adapted to various locations.In sizes 11⁄2inch andsmaller, the No.27 and No.62 valveshave bronze bodies and trim withintegral seats.In sizes 2 inches andlarger, the standard bodies are castiron with bronze trim and removableseats.Stainless steel trim can alsobe supplied.All iron, all bronze andall stainless steel valves can besupplied at extra cost in many sizes.As ordinarily assembledand used as a filling controller, theinner valve in the No.27 rises andopens as the float drops with thewater level.With the lever reversed,the float and inner valve move in thesame direction so that the valve willopen on level rise and can be usedas a drainage controller.In the same manner, the No.62valve may be assembled for eitherdirect or reverse movement.4 KECKLEY COMPANY•3400 Cleveland Street•P.O.Box 67•Skokie, Illinois 600765KECKLEY COMPANY• 3400 Cleveland Street • P .O.Box 67• Skokie, Illinois 60076Balanced Double Seated (not tight closing)Globe or AngleBRONZECAST IRONSTAINLESS STEEL BODYNO.27 GLOBEA float valve when usedon a water tank installation is best located near the surface of the water with the float where it will be least disturbed by waves.The discharge pipe extending below the surface helps to prevent waves.Wheresanitary regulations forbid the use of such a discharge pipe because of the possibility of siphoning out of the tank, the discharge may flow into a funnel and perforated pipe.The angle pattern will avoid the need for an elbowNote that the inlet of the No.27valve is at the side of the angle pattern body.The valve stem should be vertical to avoid friction and wear on the inner valve sliding on its side.The valve will operate just as well if in-verted, but the lever must be re-versed.If space limitations require the valve to be installed with stem horizontal in a vertical pipe, a lever bent 90°can be supplied.The valve may be submerged, if desired.BodyInner ValveSeat Bushings Valve Stem Stem ClevisPacking Box CoverSwivel Guide Yoke Guide Arm LeverFloatFloat RodFloat Rod Bolt and Nut Rosette{upper lower NO.27—DIMENSIONS—WEIGHTS (approximate)y t i c a p a C t a o l F eb o l G d n a e l g n A s e hc n I -e c a F o t e c a F s e h c n I —B s e h c n I —A .x a M r o t c a F s b L -t h g i e W g n i p p i h S -m a i D se h c n I n r e t t a P e b o l G n r e t t a P e l g n A n r e t t a P e l g n A t e l n I e e S .y v H .x E .d t S .d t S r e t e .y v H .x E .d t S .d t S .y v H .x E d t S .d t S .y v H .x E d t S d t S Scr.Flg.Flg.Scr.Flg.Flg.Scr Flg.Flg.CDEFGInches Scr.Flg.Flg.Page 11 Pressure 1⁄22——2——41⁄8——85⁄8115⁄161311⁄16165710 ——.041503⁄42——2——41⁄8——85⁄8115⁄161311⁄16165710 ——.15150121⁄8——21⁄8——43⁄8——83⁄4115⁄161311⁄161653⁄16713——.2415011⁄421⁄4——21⁄4——41⁄2——87⁄8115⁄161311⁄161651⁄4714 ——.4012011⁄221⁄4——21⁄4——41⁄2——87⁄8115⁄161311⁄161651⁄4714 ——.57100241⁄441⁄441⁄231⁄431⁄431⁄261⁄261⁄27123⁄42173⁄81681⁄27293842 1.4 7521⁄251⁄457⁄863⁄16315⁄1641⁄1643⁄877⁄883⁄16813⁄16133⁄42173⁄81891⁄4845 6575 1.7 60353⁄453⁄461⁄845⁄845⁄8591⁄491⁄410141⁄42173⁄81895⁄886786100 2.3 504—615⁄1671⁄4— 53⁄8511⁄16—103⁄4113⁄8141⁄22177⁄818105⁄88— 120137 4.4 355—65⁄871⁄16—65⁄871⁄16—12127⁄81921⁄2201⁄224121⁄210— 1681907.5 306—87⁄1687⁄8—61⁄2615⁄16—13137⁄8193⁄421⁄2201⁄2241310— 19422910.2258—83⁄887⁄8—83⁄887⁄8—163⁄4173⁄4257⁄832830163⁄810— 34240915.7 2010—101⁄41015⁄16—101⁄41015⁄16—201⁄4215⁄8293⁄434130181⁄212—48057225.01512—117⁄8125⁄8—117⁄8125⁄8—225⁄8241⁄832341302012—71585340.012Certified Dimensional Sheets AvailableSizeInches NO.27 ANGLE (SIDE INLET)6KECKLEY COMPANY• 3400 Cleveland Street • P .O.Box 67• Skokie, Illinois 60076Balanced Double Seated (not tight closing)Globe or AngleBRONZECAST IRONSTAINLESS STEEL BODYNO.62 ANGLENO.62 GLOBEThe No.62Lever Valve is adapted for manual control of steam, water and air lines wherever a quick acting double seated valve is required, but where perfectly tight closing is not essential.It is widely used on feed water heaters and on open and closed tanks and operated by an internal float such as the No.20, shown on page 10.It may also be operated by an electric solenoid, diaphragm motor,or hydraulic cylinder.All sizes are fittedwith swivel yokes, so that the lever can be turned to any desireddirection.The lever can be reversedto close the valve when the longer end is lifted.The counterweight is used on either end to balance levers or rods which may form part of the operating mechanism.Standardconstruction includes double seated inner valve not designed for tight closing applications.BodyInner Valve Seat Bushings Valve StemStem Clevis Packing Box CoverSwivel Guide YokeGuide ArmLever Weight{upper lowerNO.62—DIMENSIONS—WEIGHTS (approximate)A—Inches Face to Face-Inches B—Inches Globe and Angle—Inches Shipping Weight-Lbs.Capacity.x a M ro t c a F e d o c r e t t e l 5 e g a p e t o N nr e t t a P e l g n A nr e t t a P e b o l G n r e t t a P e l g n A t e l n I e e S .y v H .x E .d t S .d t S .y v H .x E .d t S .d t S .y v H .x E d t S .d t S .y v H .x E d t S d t S Scr.Flg.Flg.Scr.Flg.Flg.Scr Flg.Flg.CDEFGScr.Flg.Flg.Page 15Pressure 1⁄22——41⁄8——2——81⁄8115⁄16113⁄465⁄16510 ——.041503⁄42——41⁄8——2——81⁄8115⁄16113⁄465⁄16510 ——.15150121⁄8——43⁄8——21⁄8——85⁄16115⁄16113⁄465⁄1653⁄1611——.2415011⁄421⁄4——41⁄2——21⁄4——81⁄2115⁄16113⁄465⁄1651⁄411 ——.4012011⁄221⁄4——41⁄2——21⁄4——81⁄2115⁄16113⁄465⁄1651⁄412 ——.57100241⁄441⁄441⁄261⁄261⁄2731⁄431⁄431⁄2131⁄42153⁄865⁄881⁄2263640 1.40 7521⁄251⁄457⁄863⁄1677⁄883⁄16813⁄16315⁄1641⁄843⁄8131⁄22153⁄865⁄891⁄453 6470 1.70 60353⁄453⁄461⁄891⁄491⁄41045⁄845⁄85142153⁄865⁄895⁄8738397 2.30 504—615⁄1671⁄4—103⁄4113⁄8—53⁄8511⁄16141⁄82153⁄865⁄8105⁄8— 117134 4.40 355—65⁄871⁄16—12127⁄8—65⁄871⁄16191⁄221⁄2163⁄49121⁄2— 1631857.50 306—87⁄1687⁄8—13137⁄8—61⁄2615⁄16201⁄421⁄2163⁄4913— 18822310.20258—83⁄887⁄8—163⁄4173⁄4—83⁄887⁄8227⁄831913163⁄8— 33540215.70 2010—101⁄41015⁄16—201⁄4215⁄8—101⁄41015⁄16243⁄431913181⁄2—47256425.001512—117⁄8125⁄8—225⁄8241⁄8—117⁄8125⁄8265⁄83191320—70884640.0012Certified Dimensional Sheets AvailableSizeInchesSingle Seated, Dead End Service (tight closing)Globe or AngleBRONZE CAST IRON STAINLESS STEEL BODYNO.77 GLOBEThe No.7 and 77 pilot controlled float valves are recommended when tight closing is essential.They are commonly used to maintain a water level in an open tank.They are best suited for clean liquids not injurious to neoprene, leather or brass parts.Standard design temperature is 125°F.For higher temperatures up to 350°F, the neoprene disc in the No.7 or neoprene disc and leather cup in the No.77 are replaced by teflon parts.Referring to the sectional views on page 8, the inner valve consists of a hollow bronze piston, somewhat larger in diameter than the seat bore, and carrying the disc holder.The composition disc may be replaced when worn.The soft disc will accommodate itself to grit and wear and still close tight where a metal to metal construction would leak.The piston slides in a stationary bronze cylinder attached to the cover or body.The pilot port is opened and closed by the end of the stem which is moved by the lever.A pin through the stem at its lower end permits the inner valve to be lifted by the stem.The guide yoke, with the lever andfloat, can be turned and secured atany angle.The angle and length offloat rod can be adjusted at therosette.In the No.7 valve, madein sizes 2 inches and smaller, waterfrom the inlet enters the spaceabove the piston through a smallhole in the piston head.While thepilot port is open, this water escapesfreely through the hollow valve postto the outlet.The excess pressureunder the piston, in relation to thepressure above it, and the weight ofthe float hold the valve open.On closing the pilot port, the waterpressure above the piston quicklyrises to equal and balance the inletpressure under the piston.There-upon the inlet pressure above thedisc holder closes the valve.Noleather cup is required.The disc closes in the direction ofthe flow through the No.7 valve.Inthe larger valves and for the higherpressures, the “pull”of the water inpassing through the valve seat maycause the valve to close suddenlyfrom a nearly closed position.Forthis reason, this valve is not made insizes above 2 inches.In the No.77 valve, made in sizes 2inches and larger, the inlet pressureis under the disc.Water enters thechamber above the piston throughthe strainer and the central anddiagonal passages.If the pilot port isopen, this water escapes freely tothe valve outlet, so that the inletpressure under the disc opens thevalve.When the pilot port is closed,the water pressure above the pistonquickly rises to equal the inletpressure under the disc and, due tothe larger piston area, the innervalve is moved toward the seat.The disc closes against the inletpressure and sudden closing cannotoccur in the No.77.However, thisvalve requires the piston to be fittedwith a leather cup, the friction ofwhich may cause sluggishness onlow inlet pressures.Maximum inlet pressures for boththe No.7 and No.77 are shown inthe table on the next page.7KECKLEY COMPANY •3400 Cleveland Street•P.O.Box 67•Skokie, Illinois 600768KECKLEY COMPANY• 3400 Cleveland Street • P .O.Box 67• Skokie, Illinois 60076Internal Pilot Control, Single Seated,Dead End Service, Globe or AngleBRONZECAST IRONSTAINLESS STEEL BODY1—Body 12—Guide Arm 2—Cover*13—Lever 3—Inner Valve 14—Float Rod 4—Cylinder*15—Rosette 5—Seat Bushing*16—Float Rod Bolt 6—Composition 17—Float Valve Disc 18—Disc Plate 7—Port Stud* 19—Disc Plate Screw*8—Packing Box +20—Strainer*9—Valve Stem +21—Leather Cup*10—Stem Clevis +22—Lock Nut*11—SwivelGuide Yoke*Parts used only in sizes 2" and larger.+ Used in No.77 only.No.7 valves in sizes 11⁄2inchand smaller have bronze bodies and integral seats, screwed ends only.The 2 inch No.7 and all sizes of the No.77 have cast iron bodies, with renewable seats, screwed or flanged ends in sizes 2 inch to 3 inch inclusive,flanged ends only above 3 inch.All sizes of both valves have bronze trim and renewable composition discs.NOS.7 and 77—DIMENSIONS—WEIGHTS (approximate).s b L -t h g i e W g n i p p i h S —n r e t t a P e l g n A se h c n I —e c a F o t e c a F s e h c n I —B r o A **.x a M y t i c a p a C n r e t t a P e b o l Gs e h c n I n r e t t a P e b o l G n r e t t a P e l g n A t e l n I r o t c a F .y v H .x E .d t S .d t S .y v H .x E d t S .d t S .y v H .x E d t S dt S Scr.Flg.Flg.Scr.Flg.Flg.C D E F G H Scr.Flg.Flg.Page 11 Pressure1⁄2& 3⁄42——41⁄4——87⁄16115⁄161311⁄161653⁄1665⁄16711——.17130121⁄16——5——83⁄4115⁄161311⁄161651⁄265⁄8713——.3510011⁄421⁄8——51⁄8——83⁄4115⁄161311⁄161651⁄265⁄8714——.508011⁄221⁄2——51⁄4——9115⁄161311⁄161653⁄467⁄8714——.8065237⁄1641⁄843⁄879⁄1681⁄483⁄4123⁄8115⁄16173⁄8168101⁄87354560 1.650237⁄1641⁄843⁄879⁄1681⁄483⁄4123⁄8115⁄16173⁄8168101⁄87354560 1.625021⁄2315⁄1643⁄451⁄1683⁄491⁄2101⁄8123⁄4115⁄16173⁄81881⁄2105⁄88556872 2.5250341⁄251⁄455⁄893⁄4101⁄2111⁄4131⁄8115⁄16173⁄81891⁄8111⁄487180115 3.52504—61⁄867⁄16—121⁄4127⁄8135⁄8115⁄16173⁄81893⁄8111⁄28—140145 6.52505—71⁄4711⁄16—141⁄2153⁄8181⁄221⁄2201⁄224111⁄4141⁄410—23519510.02506—81⁄889⁄16—161⁄4171⁄8193⁄421⁄2201⁄224121⁄2155⁄810—23524014.02508—91⁄895⁄8—191⁄8201⁄82532830161⁄42110—39544526.025010globe pattern only ——201⁄8211⁄23654130293512—65070041.0250**The absolute minimum operating pressure for the #77 Float Valve is 5 psi for sizes 2" through 6" and 10 psi for sizes 8" and 10".The neck of the globe body is slightly longer than the neck of the angle body.Therefore dimensions G,H,and C are slightly greater than those shown above.Certified Dimensional Sheets Available.SizeInches Float Diam-eter Inches NO.7 GLOBENO.7 ANGLE (SIDE INLET)NO.77 GLOBENO.77 ANGLE (BOTTOM INLET)N O .7N O .779KECKLEY COMPANY• 3400 Cleveland Street • P .O. Box 67 • Skokie, Illinois 60076Internal Pilot Control, Single Seated, Dead End Service, Globe or AngleBRONZECAST IRONST AINLESS STEEL BODYNOS. 73 and 773—DIMENSIONS—WEIGHTS (approximate)A or B—Inches Face to Face—InchesAngle Pattern—Shipping Weight-Lbs.Angle Pattern Globe Pattern InchesGlobe PatternCapacityMax.**Std Std Ex. Hvy. Std. Std Ex. Hvy. Std. Std. Ex. Hvy. Factor Inlet Scr.Flg. Flg.Scr.Flg. Flg.CDEFGHScr. Flg.Flg. Page 11 Pressure 1⁄2 & 3⁄4 2—— 41⁄4 ——715⁄16 115⁄16 113⁄4 65⁄16 53⁄16 65⁄16 10 — — .17 130121⁄16 —— 5 — — 81⁄4 115⁄16 113⁄4 65⁄16 51⁄2 65⁄8 12 — — .35 10011⁄4 21⁄8 —— 51⁄8 —— 81⁄4 115⁄16 113⁄4 65⁄16 51⁄2 65⁄8 13 — — .50 8011⁄2 21⁄2 —— 51⁄4—— 81⁄2 115⁄16 113⁄4 65⁄16 53⁄4 67⁄8 14 — — .80 65237⁄16 41⁄8 43⁄8 79⁄16 81⁄4 83⁄4 12 115⁄16 153⁄8 65⁄8 8101⁄8 30 48 56 1.6 50237⁄16 41⁄8 43⁄8 79⁄16 81⁄4 83⁄4 12 115⁄16 153⁄8 65⁄8 8101⁄8 34 48 56 1.6 25021⁄2 315⁄16 43⁄4 51⁄16 83⁄4 91⁄2 101⁄8 123⁄8 115⁄16 153⁄8 65⁄8 81⁄2 105⁄8 53 65 72 2.5 250341⁄2 51⁄455⁄8 93⁄4 101⁄2 111⁄4 123⁄4 115⁄16 153⁄8 65⁄8 91⁄8 111⁄4 73 105 110 3.5 250443⁄4 61⁄8 67⁄16 —121⁄4 127⁄8 131⁄4 115⁄16 153⁄8 65⁄8 93⁄8 111⁄2 — 135 140 6.5 2505—71⁄4 711⁄16 —141⁄2 153⁄8 183⁄4 21⁄2 163⁄4 81⁄4 111⁄4 141⁄4 — 170 195 10.0 2506—81⁄8 89⁄16 —161⁄4 171⁄8 203⁄4 21⁄2 163⁄4 81⁄4 121⁄2 155⁄8 — 230 240 14.0 2508—91⁄895⁄8 —191⁄8 201⁄8 23 3 19 13 161⁄4 21 — 395 445 26.0 25010 globe pattern only ——201⁄8211⁄240 541131⁄229 35—65070041.0250**The absolute minimum operating pressure for the #77 Float Valve is 5 psi for sizes 2" through 6" and 10 psi for sizes 8" and 10".The neck of the globe body is slightly longer than the neck of the angle body.Therefore dimensions G, H, and C are slightly greater than those shown above.Certified Dimensional Sheets Available.Size InchesThese singleseated, internal pilot type levervalves are adapted for operation by an enclosed float (page 10)or by hand, solenoid, diaphragm motor, or other means, wherever a tight-closing, quick-acting, easily operated valve is required.The lever valves on thispage have the same internal construction and operate in the same manner as the float valves described on pages 7 and 8.They are also adapted to the same pres-sure and temperature conditions as the corresponding float valves.No.73 valve in sizes 11⁄2inch and smaller have bronzebodies and integral seats, screwed ends only.The 2 inch No.73 and all sizes of the No.773 have cast iron bodies, with renewable seats,screwed or flanged ends in sizes 2 inch to 3 inch inclusive, flanged ends only above 3 inch.All sizes of both valves have bronze trim and renewable composition discs.They are suitable for water andother ordinary liquids.The operating rod may be attached to either end of the lever with the counterweight located as required.The No.73 Single Seated Lever Valve is the same as No.7, shown and described on pages 7 and 8, minus float, float rod and rosette, and plus a counterweight.The No.773 Single Seated Lever Valve is the same as No.77, shown and described on pages 7 and 8, minus float, float rod and rosette, and plus a counterweight.N O .73N O .77310KECKLEY COMPANY• 3400 Cleveland Street • P .O.Box 67• Skokie, Illinois 600766" or 8" FloatsCast Iron Body With Ball Bearing Stuffing BoxFloat Boxesare used in connection with closed tanks where fluctuation of the liquid level in the tank is thegoverning factor in the control of the lever valve, signal switch,motor or other equipment.The entire unit is mounted outside the tank where it can be easilyinstalled, adjusted, inspected and serviced.By placing the Box in the same horizontal plane as the tank liquid level with equalizing connections above and below the level and the valve suitably linked to the Box,the tank level may be auto-matically maintained whether the flow is into or out of the tank.Typical applications are with a No.62, 73 or 773 lever valve used as a level controller for hot or cold water.The packing boxhas outboard ball bearing with bolted gland reducing friction and wear to a minimum, the rotary stem is stainless steel.The float rod is brass when used with a 6inch float and galvanized pipe when used with an 8 inch float.A gauge glass and bracketed lever and counterweight completes the Unit.Equalizing pipe connections are 1" screwed on the Box with the 6" float, 11⁄2" standard flanged or screwed connections on the 8"Box.Cast iron Float Boxes are suitable for pressures up to 250psi and maximum temperatures of 406°F .Various types of switchesavailable are mercury tube switch,single pole snap switch and the explosion proof mercury tubeswitch.Rating of all switches is 10amperes at 110 volts or 5amperes at 220 volts AC or DC.NO.20 FLOAT BOXSize of Lever Valve 1⁄23⁄4111⁄411⁄2221⁄2345688888886666ta o l F f o e z i S Approximate Shipping Weight10010010010019019019019019019019011KECKLEY COMPANY• 3400 Cleveland Street • P .O.Box 67• Skokie, Illinois 60076The maximum capacity of a float or lever valve depends on its size and on the pressure difference — or drop — between the inlet and outlet when the valve is wide open.It is recommended that a valve beselected having 50% to 100% morecapacity than the normal demand.For example, if the normal require-ment is 100 gallons per minute, a valve having 150 to 200 G.P .M.capacity should be selected.This will result in less variation in water level, and provide reserve capacityin case of low water pressure or unusual demand.The maximum capacity is the product of the flow per square inch of port area (Orifice Capacity) multiplied by theequivalent port area of the valve (Capacity Factor).MAXIMUM CAPACITIES OF NOS.27 FLOAT AND 62 LEVER VALVES U.S.GALLONS PER MINUTE OF WATERPressure Drop between Inlet and Outlet in Pounds per Square InchSize Capacity Inches 1 3510 15 20 25 3035 40 45 50 60 70 80 90 100Factor 1⁄2" 1.5 2.6 3 5 6 7 7 8 9 10 10 11 12 13 14 14 15 .04 3⁄4" 5.7 10 13 18 22 25 28 31 34 36 38 40 44 48 51 54 57 .15 1" 9.1 16 20 29 35 40 46 50 54 58 61 64 70 76 81 86 91 .2411⁄4" 15 26 34 48 58 68 76 83 90 97 102 108 118 127 136 144 152 .40 11⁄2" 22 38 48 68 83 97 108 118 128 138 145 154 168 181 194 205 216 .572" 53 92 119 168 204 236 266 290 314 339 357 377 412 446 447 —— 1.421⁄2" 64 111 144 204 248 287 323 352 382 410 433 458 500 ———— 1.73" 87 150 196 276 335 389 437 476 518 556 586 620————— 2.34" 167 290 374 528 642 743 846 910 990———————— 4.45" 285 493 637 900 1095 1270 1425 1550 —————————7.56" 388 672 867 1225 1490 1725 1940——————————10.28" 596 1030 1335 1885 2290 2655———————————15.710" 950 1645 2125 3000 3650————————————2504———————03850084004303620251"211 sq.in.Orifice 38 66 85 120 147 170 190 208 225240255269294318340360 3801Capac.For other liquids divide above G.P.M.by √specific gravity of the liquid.Capacities are in U.S.Gallons.The Imperial Gallon = 1.2 U.S.Gallons.MAXIMUM CAPACITIES OF NOS.7,77 FLOAT AND 73,773 LEVER VALVES U.S.GALLONS PER MINUTE OF WATERPressure Drop between Inlet and Outlet in Pounds per Square InchSize Capacity Inches 1 3510 15 20 25 30 35 40 45 50 60 70 80 90 100Factor 3⁄4" 6.5 11 14 20 25 29 32 35 38 41 43 46 50 54 58 61 65 .17 1" 13 23 30 42 52 50 66 73 79 84 89 94 103111 119 126 133 .3511⁄4"19 33 42 60 73 85 95 104 112 120 127 134 147 159 170 180 190 .50 11⁄2"30 53 68 96 118 136 152 166 180 192 204 215 235 254 272 288 304 .802" 61 106 136 192 235 272 304 333 360 384 408 430 470508 544 576608 1.621⁄2"95 165 212 300 368 425 475 520 562 600 638 672 735 795850900950 2.53" 133 231 297 420 514 595 665 728 786 840 892 94010301110119012601330 3.54" 247 429 552 780 955 1105 1235 1353 146015601660175019102070221023402470 6.55" 380 660 850 1200 1470 1700 1900 2080 22502400255026802940318034003600380010.06" 532 923 11921680 2060 2380 2660291031503360357037604110445047605030532014.08" 987 1720 2215 3120 3820 44204930540058506230653069807630826088309350987026.01 sq.in.Orifice 38 66 85 120 147 170 190 208 225 240 255 269 294 318340360380Capac.For other liquids divide above G.P.M.by √specific gravity of the liquid.Capacities are in U.S.Gallons.The Imperial Gallon = 1.2 U.S.Gallons.Orifice Capacity:Bottom line of tables shows the G.P .M of water which will flow through a standard orifice of 1 sq.in.area at the given pressure drop.These quantities are calculated by the formula:G.P .M.per Sq.In.= 38 √Pressure Drop in p.s.i.= 25 √Pressure Drop in feetFor other liquids, divide the above G.P .M.by√specific gravity of liquid.Capacity Factor:The last column at the right in the tables shows the equivalent square inches of port area of each size of Nos.27, 62, 7,77, 73 and 773 valves.Thesecapacity factors are obtained by test,not by measurement of the ports.Capacity Factors for other types of valves are listed in the last column of each table on the following pages.Distributed By: M&M Control Service, Inc. /Keckley.php 800-876-0036 847-356-0566。
分离杠杆高度的调整

分离杠杆高度的调整
1. 找到分离杠杆的位置:分离杠杆通常位于发动机舱内,可以通过查阅车辆手册或询问专业技师来确定其位置。
2. 固定分离杠杆:使用扳手或钳子等工具松开分离杠杆上的螺丝,调整高度后再拧紧螺丝。
3. 测试调整效果:在空地上进行加速测试,或者在高速公路上进行测试,观察汽车的加速性能和燃油经济性是否有所改善。
需要注意的是,调整分离杠杆高度需要一定的技巧和经验。
如果你不确定如何进行操作,建议咨询专业技师或前往汽车维修店进行维修。
汽车杠杆扶手说明书

HEAVY DUTYLOW PROFILE FLOOR JACK Model: RFJ-5000HD2.5 TON CAPACITYSHIPPING DAMAGE CLAIMSWhen this equipment is shipped, title passes to the purchaser upon receipt from the carrier. Consequently, claims for the material damaged in shipment must be made by the purchaser against the transportation company at the time shipment is received.BE SAFERanger™ Floor Jacks are designed and built with safety in mind. However, proper training and thought-ful operation on the part of the user can increase your overall safety. DO NOT operate or repair this tool without reading this manual and the important safety instructions shown inside.1645 Lemonwood Dr.Santa Paula, CA. 93060, USA Toll Free: 1-800-253-2363Tel: 1-805-933-9970Fax: PLEASE READ THE ENTIRE CONTENTS OF THIS MANUAL PRIOR TO INSTALLATION AND OPERATION. BY PROCEEDING YOU AGREE THAT YOU FULLY UNDERSTAND AND COMPREHEND THE FULL CONTENTS OF THIS MANUAL. FORWARD THIS MANUAL TO ALL OPERATORS. FAILURE TO USE THIS EQUIPMENT AS DIRECTED MAY CAUSE INJURY OR DEATH.REV A 12-31-2015P/N 5900964Keep this operation manual near the machine at all times. Make sure that ALL USERS read this manual.THIS OPERATING MANUAL CONTAINS IMPORTANT DETAILS CONCERNING THE SAFE OPERATION OF THIS TOOL THE USER MUST READ AND UNDERSTAND THESE DETAILS BEFORE ANY USE OF THE TOOL. THIS MANUAL MUST BE RETAINEDFOR FUTURE REFERENCE. OWNER/OPERATOR RESPONSIBILITY:The owner and/or operator shall study the product instructions and retain them for future reference. The owner and/or operator shall have an understanding of the product operating instructions and warnings beforeoperating the jack. Warning information shall be emphasized and understood. If the operator is not fluent in English, the product instructions and warnings shall be read to and discussed with the operator in the operator’s native language by the purchaser/ owner or his designee, making sure that the operator comprehends its contents.INSPECTIONVisual inspection should be made before each use of the jack. This inspection should check for abnormalconditions such as cracked welds, leaks, and damaged, loose or missing parts.Any jack that appears to be damaged in any way, is found to be worn or operated abnormally, must be removed from service immediately.Any jack that operates abnormally shall be removed from service until repaired by a qualified repair service center. If the jack is accidentally subjected to an abnormal load or shock, it must be taken out of service immediately and be inspected by a qualified repair or service center. It is recommended that an annual inspection is performed on the jack and that any damaged or worn parts, decals or warning labels be replaced with manufacturer’s specified parts.ALTERATIONSBecause of potential hazards associated with this type of equipment, no alterations shall be made to the product. FOR YOUR SAFETY AND TO PREVENT INJURY:Use Service Jack for lifting purposes ONLY . Always support vehicle with jack stands.T HIS IS A LIFTING DEVICE ONLY. DO NOT MOVE ORDOLLY THE VEHICLE WHILE ON THE JACK. IMMEDIATELY AFTER LIFTING, SUPPORT THEVEHICLE WITH APPROPRIATE MEANS.DO NOT EXCEED RATED CAPACITY. OVERLOADING CAN CAUSE DAMAGE TOOR FAILURE OF THE JACK. LIFT ONLY ON AREAS OF THE VEHICLE AS SPECIFIED BY THE VEHICLE MANUFACTURER. CENTER LOAD ON SADDLE PRIOR TO LIFTING. OFF-CENTER LOADS MAY CAUSE DAMAGE TO JACK, LOSS OF LOAD, PROPERTY DAMAGE,PERSONAL OR FATAL INJURY. THIS JACK IS DESIGNED FOR USE ONLY ON HARD LEVEL SURFACES CAPABLE OF SUSTAINING THELOAD. USE ON OTHER THAN HARD LEVELSURFACES CAN RESULT IN JACK INSTABILITY ANDPOSSIBLE LOSS OF LOAD. NO ALTERATIONS TO THE JACK SHALL BE MADE. READ, STUDY AND UNDERSTAND THE OPERATINGMANUAL PACKED WITH THIS JACK BEFOREOPERATING. FAILURE TO HEED THESE WARNINGS MAY RESULT IN LOSS OF LOAD, DAMAGE TO JACK, AND/OR FAILURE RESULTING IN PROPERTY DAMAGE,PERSONAL OR FATAL INJURY.ASSEMBLY INSTRUCTIONS1. Remove 2-piece handle from box. Insert narrow portion of top section (41) into bottom section (39) and secure with bolt (42) provided.2. Then, slightly press down on the handle yoke assembly to release pressure on the handle yoke assembly retainer and remove retainer. This will allow handle yoke to be raised to operating position.3. Grease handle receptacle and insert slotted end of handle into place. Tighten set screw (35) to secure handle.OPERATING INSTRUCTIONSBEFORE USE:Air may become trapped in the hydraulic system during transit. To purge air:1. Open release valve by turning handle counterclock-wise.2. Pump handle rapidly 4 full strokes. This will expel air that may have entered oil passages during transit.3. Close release valve by rotating handle clockwise and pump handle.4. If lift arm is raised, jack is ready for use. If not, repeat this procedure.IMPORTANT:Before attempting to raise any vehicle, checkvehicle service manual for recommended lifting surfaces.OPERATION:1. To Raise Load: Close release valve tightly (by turning handle clockwise). DO NOT OVERTIGHTEN. Position jack under load so that saddle will contact load firmly and load is centered so it cannot slip. Operate jack handle un-til saddle approaches the load. Once again, check to see that saddle is correctly positioned. Raise load to desired height. Place jack stands of appropriate capacity under the vehicle. DO NOT CRAWL UNDER VEHICLE WHILE LIFTING VEHICLE OR PLACING OR REMOVING JACK STANDS!Place jack stands at vehicle manufacturer’s recommend-ed lift areas that provide stable support for the raised Vehicle. Once jack stands are positioned, open the release valve VERY SLOWLY (by turning the handle counterclockwise).Lower the load to rest on the jack stands. Then, make sure that the release valve on the jack is closed tightly (by turning the handle clockwise).2. To lower load:Re-check to make sure release valve is tightly closed. Then, operate the jack handle until the load is raised enough to remove the jack stands.DO NOT CRAWL UNDER VEHICLE WHILE LIFTING VEHICLE OR REMOVING THE JACK STANDS! Once jack stands are removed, open release valve very slowly to lower the vehicle. Lower jack completely so that the vehicle is securely resting on the ground and that jack no longer makes contact with vehicle.Keep hands or feet away from the hinge mechanism of the jack.MAINTENANCEWhen adding or replacing hydraulic fluid, always use a quality hydraulic fluid. DO NOT use brake fluid, alcohol, detergent motor oil, dirty oil or any fluid other than quality hydraulic fluid. Improper fluids can cause internal dam -age to the jack and improper or unsafe operation. Adding Hydraulic FluidWith the saddle fully lowered and the jack on level ground, remove the filler screw. Hydraulic fluid should be filled to the level of the filler screw hole. If the level is below this hole, add hydraulic fluid as needed.LUBRICATIONAll moving joints require lubrication often. Lightly grease saddle post and saddle bottom. Remove handle and grease the lower end of handle where it rotates in the handle socket. Using a grease gun, grease the lift arm pivot shaft grease fitting until grease appears at the end of the shaft. Oil all lift arm linkages, front wheels and rear casters.SPECIFICATIONSRated Load Capacity: 5000 lbs. (2268 kg.)Minimum Height: 3” (76mm)High height 20” (508mm)Front Overall Width 10-1/2” (267mm)Rear OVerall Width 14” (356mm)Shipping Weight 74lbs. (34 kg.)FEATURESTROUBLESHOOTINGPROBLEMACTION1. Unit will not lift loadPurge air from hydraulic system by following procedure under OPERATING INSTRUCTIONS.2. Unit will not sustain load or feels “spongy” under load.Purge air from hydraulic system as above.3. Unit will not lift to full height.Purge air from hydraulic system as above. Check to be sure oil level is not too high or low.4. Unit will not lower completely.Check oil level. Make sure not overfilled.5. Handle tends to raise up while the unit is under load. Pump the handle rapidly several times to push oil past ball valves in power unit.6. Unit still does not operate.Contact Parts & Warranty Department.WARRANTY NOTICEThis Floor Jack from Ranger Products™ is covered under a 1 year warranty when used as recommended. Many parts are available, as shown in parts breakdown on pages: 5 - 6. For assistance with the operation or the availability ofreplacement parts contact our Customer Service Department at 1-800-253-2363. Please have available a copy of your receipt, the model number of the product, and specific details regarding your question.WARRANTY INFORMATIONWe want to know if you have any cooncerns with Ranger Products. If so, please call us toll-free for immediate assistance: 1-800-879-7316 or 1-805-933-9970For more information about our warranty, please visit:/support/warrantyWARRANTYLow profile chassis accommodates low groundclearance vehicles.Swivel Casters for easy mobility“Quick-pump” feature for fater lifting speed. Professional model designed for heavy use. Universal-joint, pressure release system.Roller-cam, dual plunger pump assembly.Heavy steel construction for maximum durability. Double-sealed hydraulics for longer service life. Sealed hydraulic unit prevents contamination. Safety-overload system.Flanged side plates for increased strength.____________________________________________________________________ ____________________________________________________________________ ____________________________________________________________________ ____________________________________________________________________ ____________________________________________________________________ ____________________________________________________________________ ____________________________________________________________________ ____________________________________________________________________ ____________________________________________________________________ ____________________________________________________________________ ____________________________________________________________________ ____________________________________________________________________ ____________________________________________________________________ ____________________________________________________________________ ____________________________________________________________________ ____________________________________________________________________ ____________________________________________________________________ ____________________________________________________________________ ____________________________________________________________________ ____________________________________________________________________。
- 1、下载文档前请自行甄别文档内容的完整性,平台不提供额外的编辑、内容补充、找答案等附加服务。
- 2、"仅部分预览"的文档,不可在线预览部分如存在完整性等问题,可反馈申请退款(可完整预览的文档不适用该条件!)。
- 3、如文档侵犯您的权益,请联系客服反馈,我们会尽快为您处理(人工客服工作时间:9:00-18:30)。
图 1-1.1
图 1-1.1 为零件实体图 2.零件工艺分析 通过对该零件的重新绘制,知道原图样的视图基本正确,完整尺寸,公差及技术要求 齐全。但下表面的精度较高。要进行精铣才能达到粗糙度要求。
该零件属于杆类零件,它的侧面都是直接锻造出来的,在加工时很方便,但要同 时保证孔的平行度和垂直度比较困难,但毛坯基本确定位置,所以简单了许多 3.零件的生产类型 依设计题目知:Q=2000 台/年,n=1 件/台;结合生产实际,备品率 α 和废品率 β 分 别取 10%和 1%。代入公式 N=Qn(1+α)(1+β)得该零件生产纲领
:50 45. 44. 43. by 42.41.— 4—0.— 3—9.—3—8.by37@.—— 36.35. —34—. ——33.312. 1.2.3.34.0.5.6—.—29.by28.by@27.26.—— 25. 24. 23. 22. by 21.20. — 1—9.by:18.by:17.— 1—6.— 1—5.—1—4.—— 13. 12. 111.0“. ”by: 9M.“OOOKN”b8y.:——7.——6.——5.——4.——3.——2.——1.——
参考资料以及说明: (1)崇凯.机械制造技术基础课程设计指南[M].北京:化学工业出版社,2010 (2)吕明.机械制造技术基础(第二版)[M].武汉:武汉理工大学出版社,2010 (3)陈宏钧.实用机械加工工艺手册[M].北京:机械工业出版社,2003 (4)符炜.实用切削加工手册[M].长沙:湖南科学技术出版社,2003
零件的工艺分析及生产类型确定 零件的作用
题目所给的零件是调速杠杆,主要作用是用于连接调速器,对侧面加工要求低, 对下孔的的加工精度要求比较高,尤其是 φ12mm 的孔有粗糙度的要求高,加工有困难。
:50 45. 44. 43. by 42.41.— 4—0.— 3—9.—3—8.by37@.—— 36.35. —34—. ——33.312. 1.2.3.34.0.5.6—.—29.by28.by@27.26.—— 25. 24. 23. 22. by 21.20. — 1—9.by:18.by:17.— 1—6.— 1—5.—1—4.—— 13. 12. 111.0“. ”by: 9M.“OOOKN”b8y.:——7.——6.——5.——4.——3.——2.——1.——
○2 锻件质量 m f
根据零件成品质量 0.25Kg ,估算为 m f
0.39Kg
。
○3 锻件形状复杂系数 S
S mf / mN
该锻件为非圆形锻件,长158.5mm ,宽 29mm ,假设最大厚度 53mm ,则由公式(5-
5)
mN lbhp 158.5 29 54 7.85 106 1.912Kg S m f / mN 0.39 /1.912 0.204
○5 零件的表面粗糙度 由于该零件图可知,该零件各加工表面为 Ra 1.6m 。
3.确定机械加工余量 根据锻件质量、零件表面粗糙度、形状复杂系数查表 5-9,由此查得单边余量在厚
2.机械制造技术基础课程设计指南》(崇凯 主编,李楠 副主编 2010 版)第五章
第一节,钢质模锻件的公差及机械加工余量按 GB/T 12362-2003 确定。要确定毛坯的
尺寸公差及机械加工余量,应先确定如下各项因素。 ○1 锻件公差等级 由该零件的功用和技术要求,确定其锻件公差等级为普通级。
N=2000 1 (1+10%) (1+1%)=2222 件/年
零件质量为 0.25kg,查表 2-1 得其属轻型零件,生产类型为中批生产。 选择毛坯及热处理、确定毛坯尺寸、设计毛坯图 选择毛坯 该零件的材料为 30 钢,考虑到零件的强度要求较高、形状比较简单,因此应该采用锻 件,以使金属纤维尽量不被切断,保证零件工作可靠。由于零件年产量为 2222 件,属 批量生产,而且零件的轮廓尺寸不大,故可采用模锻成型。这从提高生产率,保证加 工精度上考虑,也是应该的。
课程设计任务书 兹发给 2010 级机械 X 班 班学生 张 XX 课程设计任务书,内容如下:
设计题目: “135 调速器调速杠杆”零件机械加工工艺规程设计 应完成的项目: (1)原始资料:该零件图样,Q=2000 台/年,n=1 件/台,每日 1 班 (2)零件图 1 张,毛坯图 1 张; (3)机械加工工艺过程卡片 1 张; (4)机械加工工序卡片 1 套; (5)课程设计说明书 1 份。
本设计任务书于 2013 年 6 月 3 日发出,应于 2013 年 6 月 14 日前完成,然后进行答 辩。 目录
序言 机械制造技术基础课程设计是在学完了机械制造技术基础和大部分专业课,并进行了 生产实习的基础上进行的又一个实践性教学环节。这次设计使我们能综和运用机械制 造技术基础中的基本理论,并结合生产实习中学到的实践知识,独立的分析和解决了 零件机械制造工艺问题,设计了机床专用夹具这一典型的工艺装备,提高了结构设计 能力,为今后的毕业设计及未来从事的工作打下了良好的基础。 由于能力所限,经验不足,设计中还有很多不足之处,希望各位老师多加指教。
由于 0.204 介于 0.16 和 0.32 之间,故该零件的形状复杂系数 S 属于 S3 级。 ○4 锻件材质系数 M 由于该零件材料为 30 钢,是碳的质量分数小于 0.65% 的碳素钢, 故该锻件的材质系数属于 M 1 级
:50 45. 44. 43. by 42.41.— 4—0.— 3—9.—3—8.by37@.—— 36.35. —34—. ——33.312. 1.2.3.34.0.5.6—.—29.by28.by@27.26.—— 25. 24. 23. 22. by 21.20. — 1—9.by:18.by:17.— 1—6.— 1—5.—1—4.—— 13. 12. 111.0“. ”by: 9M.“OOOKN”b8y.:——7.——6.——5.——4.——3.——2.——1.——