硅钢基础知识
硅钢片普及知识

硅钢(silicon steel)含硅量0.5%~4.8%的铁硅合金。
是电工领域广泛使用的一种软磁材料。
电工用硅钢常轧制成标准尺寸的大张板材或带材使用,俗称硅钢片,广泛用于电动机、发电机、变压器、电磁机构、继电器电子器件及测量仪表中。
硅是钢的良好脱氧剂,它与氧结合,使氧转变为稳定的不为碳还原的SiO2,避免了因氧原子掺杂而使铁的晶格畸变。
硅在α铁中成为固溶体后使电阻率增加,同时有助于将有害杂质碳分离出来。
因此,一般含杂质的铁加入硅后能提高磁导率、降低矫顽力和铁损。
但含硅量增加又会使材料变硬变脆,导热性和韧性下降,对散热和机械加工不利,故一般硅钢片的含硅量不超过4.5%。
硅钢片分冷轧、热轧两种,使用较多的是冷轧硅钢片。
冷轧硅钢片沿轧制方向有优良的磁性能,不仅在强磁场中具有高饱和磁通密度和低铁损,而且在弱磁场中也有良好的磁性(初始磁导率大)。
这是由于冷轧工艺过程使钢片中杂质含量降低,并在钢片中造成粗大晶粒,致使磁导率增大,磁滞损耗减小。
硅钢片的主要品质特性有铁损值、磁通密度、硬度、平坦度、厚度均匀性、涂膜种类及冲片性等。
以下针对各项品质特性加以说明。
1.铁损值硅钢片在某一特定频率的交流磁场下,磁化到特定的磁通密度时,每单位重量之硅钢片所损失的能量,称为铁损值。
通常所用的交流磁场频率为50或60赫兹,而所达到的磁通密度通常为1.5或1.7特斯拉。
常用的铁损值单位是每公斤或每磅硅钢片所损失的瓦特值,用Watt/kg或Watt/lb 表示。
硅钢片的铁损值来源包括磁滞损、涡电流损和异常涡电流损三部份。
硅钢片在磁化的过程中,会产生磁滞的现象。
磁滞损即为B-H磁滞曲线所包涵的面积。
硅钢片的涡电流损起源于在交流变化的磁场,因法拉第定理的影响,硅钢片内部产生诱导电压,依照奥姆定律,电压在硅钢片内部引起诱导电流,进而造成硅钢片的焦耳热,这项能源损失称为涡电流损。
根据古典电磁学理论,涡电流损和钢片的厚度、电阻系数、磁通密度和频率有关。
电磁钢板(硅钢)知识
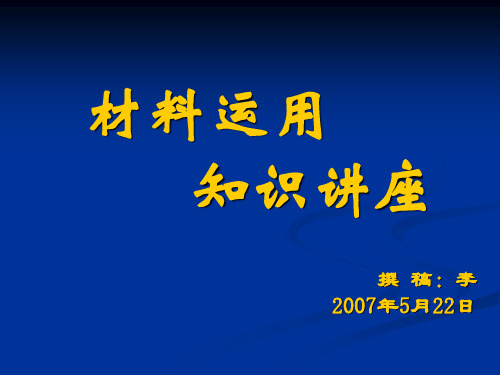
(2)冷轧取向硅钢带由公称厚度(扩大100倍的值)+代号G: 表示普通材料,P:表示高取向性材料+铁损保证值(将频率50HZ, 最大磁通密度为1.7T时的铁损值扩大100倍后的值)。如30G130 表示厚度为0.3mm,铁损保证值为≤1.3的冷轧取向硅钢带。 注:我司常用材料实际表示中,一般以钢厂名称的英文或中 文首写字母代替通用代号,如中钢表示为CS,如35CS440,宝钢 表示为B如50B470等,较特殊的新日铁取向硅钢表示为Z,如 35Z155,30Z120
深圳春源钢铁工业有限公司 材料运用知识
三、材料厚度
50CS1300*1200材质厚度测量曲线图
说明:1.AC、DB段宽度各为50mm;每隔5mm测一点; CD段每隔50mm测一点; 2.测量时采用精度为0.001mm之外千分尺(编号为M-178); 3.测量点距边约20mm; 4.测量者封中华,测量日期为2007年5月16日。
品质特性项目 1、低铁损值
2、高磁通密度 3、低磁性时效性 4、硬度\强度
质量的最重要指标,世界 各国都以铁损值划分牌号, 铁损越低,牌号越高,质 量也高 在相同磁场下能获得较高 磁感的硅钢片,用它制造 电机或变压器铁芯的体积 和重量较小,相对而言可 节约硅钢片、铜线和绝缘 材料等
所影响之使用特性 磁气性质
类别 序号
50JN1300 50CS1300 50B1000
50AW1000 50AW800
A 品
1 2 3 4 5 平均
49.2 50.3 50.9 48.2 48.7 49.5
53.6 53.8 53.5 53.4 53.5 53.6
55.7 55.8 55.8 53.5 54.7 55.1
53.5 54.0 54.3 53.9 53.0 53.7
冷轧硅钢基础知识1
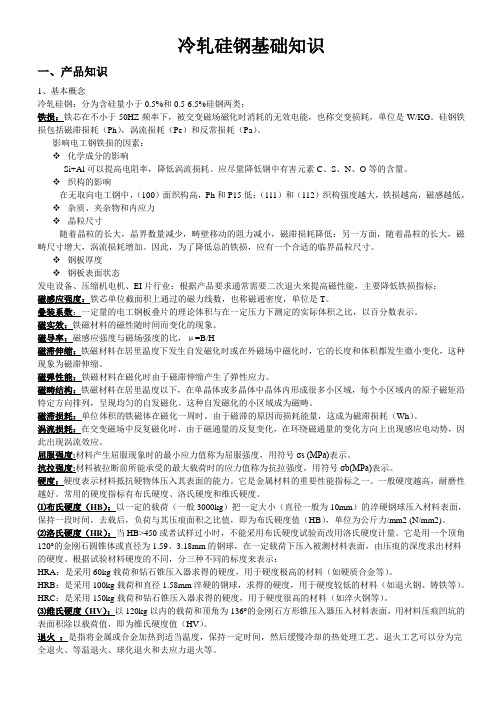
冷轧硅钢基础知识一、产品知识1、基本概念冷轧硅钢:分为含硅量小于0.5%和0.5-6.5%硅钢两类;铁损:铁芯在不小于50HZ频率下,被交变磁场磁化时消耗的无效电能,也称交变损耗,单位是W/KG。
硅钢铁损包括磁滞损耗(Ph),涡流损耗(Pe)和反常损耗(Pa)。
影响电工钢铁损的因素:化学成分的影响Si+Al可以提高电阻率,降低涡流损耗。
应尽量降低钢中有害元素C、S、N、O等的含量。
织构的影响在无取向电工钢中,(100)面织构高,Ph和P15低;(111)和(112)织构强度越大,铁损越高,磁感越低。
杂质、夹杂物和内应力晶粒尺寸随着晶粒的长大,晶界数量减少,畴壁移动的阻力减小,磁滞损耗降低;另一方面,随着晶粒的长大,磁畴尺寸增大,涡流损耗增加。
因此,为了降低总的铁损,应有一个合适的临界晶粒尺寸。
钢板厚度钢板表面状态发电设备、压缩机电机、EI片行业:根据产品要求通常需要二次退火来提高磁性能,主要降低铁损指标;磁感应强度:铁芯单位截面积上通过的磁力线数,也称磁通密度,单位是T。
叠装系数:一定量的电工钢板叠片的理论体积与在一定压力下测定的实际体积之比,以百分数表示。
磁实效:铁磁材料的磁性随时间而变化的现象。
磁导率:磁感应强度与磁场强度的比,μ=B/H磁滞伸缩:铁磁材料在居里温度下发生自发磁化时或在外磁场中磁化时,它的长度和体积都发生微小变化,这种现象为磁滞伸缩。
磁弹性能:铁磁材料在磁化时由于磁滞伸缩产生了弹性应力。
磁畴结构:铁磁材料在居里温度以下,在单晶体或多晶体中晶体内形成很多小区域,每个小区域内的原子磁矩沿特定方向排列,呈现均匀的自发磁化。
这种自发磁化的小区域成为磁畴。
磁滞损耗:单位体积的铁磁体在磁化一周时,由于磁滞的原因而损耗能量,这成为磁滞损耗(Wh)。
涡流损耗:在交变磁场中反复磁化时,由于磁通量的反复变化,在环绕磁通量的变化方向上出现感应电动势,因此出现涡流效应。
屈服强度:材料产生屈服现象时的最小应力值称为屈服强度,用符号σs (MPa)表示。
硅钢片基本知识

五金知识:矽钢片--------------------------------------------------------------------------------来源: 发布日期:电工用硅钢薄板俗称矽钢片或硅钢片。
顾名思义,它是含硅高达0.8%-4.8%的电工硅钢,经热、冷轧制成。
一般厚度在1mm以下,故称薄板。
硅钢片广义讲属板材类,由于它的特殊用途而独立一分支。
电工用硅钢薄板具有优良的电磁性能,是电力、电讯和仪表工业中不可缺少的重要磁性材料。
(1)硅钢片的分类A、硅钢片按其含硅量不同可分为低硅和高硅两种。
低硅片含硅2.8%以下,它具有一定机械强度,主要用于制造电机,俗称电机硅钢片;高硅片含硅量为 2.8%-4.8%,它具有磁性好,但较脆,主要用于制造变压器铁芯,俗称变压器硅钢片。
两者在实际使用中并无严格界限,常用高硅片制造大型电机。
B、按生产加工工艺可分热轧和冷轧两种,冷轧又可分晶粒无取向和晶粒取向两种。
冷轧片厚度均匀、表面质量好、磁性较高,因此,随着工业发展,热轧片有被冷轧片取代之趋势(我国已经明确要求停止使用热轧硅钢片,也就是前期所说的"以冷代热")。
(2)硅钢片性能指标A、铁损低。
质量的最重要指标,世界各国都以铁损值划分牌号,铁损越低,牌号越高,质量也高。
B、磁感应强度高。
在相同磁场下能获得较高磁感的硅钢片,用它制造的电机或变压器铁芯的体积和重量较小,相对而言可节省硅钢片、铜线和绝缘材料等。
C、叠装系数高。
硅钢片表面光滑,平整和厚度均匀,制造铁芯的叠装系数提高。
D、冲片性好。
对制造小型、微型电机铁芯,这点更重要。
E、表面对绝缘膜的附着性和焊接性良好。
F、磁时效G、硅钢片须经退火和酸洗后交货。
(一)电工用热轧硅钢薄板(GB5212-85)电工用热轧硅钢薄板以含碳损低的硅铁软磁合金作材质,经热轧成厚度小于1mm的薄板。
电工用热轧硅钢薄板也称热轧硅钢片。
热轧硅钢片按其合硅量可分为低硅(Si≤2.8%)和高硅(Si≤4.8%)两种钢片。
硅钢片的介绍(普及知识)

关于硅钢的常识硅钢(silicon steel)含硅量0.5%~4.8%的铁硅合金。
是电工领域广泛使用的一种软磁材料。
电工用硅钢常轧制成标准尺寸的大张板材或带材使用,俗称硅钢片,广泛用于电动机、发电机、变压器、电磁机构、继电器电子器件及测量仪表中。
硅是钢的良好脱氧剂,它与氧结合,使氧转变为稳定的不为碳还原的SiO2,避免了因氧原子掺杂而使铁的晶格畸变。
硅在α铁中成为固溶体后使电阻率增加,同时有助于将有害杂质碳分离出来。
因此,一般含杂质的铁加入硅后能提高磁导率、降低矫顽力和铁损。
但含硅量增加又会使材料变硬变脆,导热性和韧性下降,对散热和机械加工不利,故一般硅钢片的含硅量不超过4.5%。
硅钢片分冷轧、热轧两种,使用较多的是冷轧硅钢片。
冷轧硅钢片沿轧制方向有优良的磁性能,不仅在强磁场中具有高饱和磁通密度和低铁损,而且在弱磁场中也有良好的磁性(初始磁导率大)。
这是由于冷轧工艺过程使钢片中杂质含量降低,并在钢片中造成粗大晶粒,致使磁导率增大,磁滞损耗减小。
硅钢片的主要品质特性有铁损值、磁通密度、硬度、平坦度、厚度均匀性、涂膜种类及冲片性等。
以下针对各项品质特性加以说明。
1.铁损值硅钢片在某一特定频率的交流磁场下,磁化到特定的磁通密度时,每单位重量之硅钢片所损失的能量,称为铁损值。
通常所用的交流磁场频率为50或60赫兹,而所达到的磁通密度通常为1.5或1.7特斯拉。
常用的铁损值单位是每公斤或每磅硅钢片所损失的瓦特值,用Watt/kg或Watt/lb表示。
硅钢片的铁损值来源包括磁滞损、涡电流损和异常涡电流损三部份。
硅钢片在磁化的过程中,会产生磁滞的现象。
磁滞损即为B-H磁滞曲线所包涵的面积。
硅钢片的涡电流损起源于在交流变化的磁场,因法拉第定理的影响,硅钢片内部产生诱导电压,依照奥姆定律,电压在硅钢片内部引起诱导电流,进而造成硅钢片的焦耳热,这项能源损失称为涡电流损。
根据古典电磁学理论,涡电流损和钢片的厚度、电阻系数、磁通密度和频率有关。
硅钢片基本知识

五金知识:矽钢片--------------------------------------------------------------------------------来源: 发布日期:电工用硅钢薄板俗称矽钢片或硅钢片。
顾名思义,它是含硅高达0.8%-4.8%的电工硅钢,经热、冷轧制成。
一般厚度在1mm以下,故称薄板。
硅钢片广义讲属板材类,由于它的特殊用途而独立一分支。
电工用硅钢薄板具有优良的电磁性能,是电力、电讯和仪表工业中不可缺少的重要磁性材料。
(1)硅钢片的分类A、硅钢片按其含硅量不同可分为低硅和高硅两种。
低硅片含硅2.8%以下,它具有一定机械强度,主要用于制造电机,俗称电机硅钢片;高硅片含硅量为 2.8%-4.8%,它具有磁性好,但较脆,主要用于制造变压器铁芯,俗称变压器硅钢片。
两者在实际使用中并无严格界限,常用高硅片制造大型电机。
B、按生产加工工艺可分热轧和冷轧两种,冷轧又可分晶粒无取向和晶粒取向两种。
冷轧片厚度均匀、表面质量好、磁性较高,因此,随着工业发展,热轧片有被冷轧片取代之趋势(我国已经明确要求停止使用热轧硅钢片,也就是前期所说的"以冷代热")。
(2)硅钢片性能指标A、铁损低。
质量的最重要指标,世界各国都以铁损值划分牌号,铁损越低,牌号越高,质量也高。
B、磁感应强度高。
在相同磁场下能获得较高磁感的硅钢片,用它制造的电机或变压器铁芯的体积和重量较小,相对而言可节省硅钢片、铜线和绝缘材料等。
C、叠装系数高。
硅钢片表面光滑,平整和厚度均匀,制造铁芯的叠装系数提高。
D、冲片性好。
对制造小型、微型电机铁芯,这点更重要。
E、表面对绝缘膜的附着性和焊接性良好。
F、磁时效G、硅钢片须经退火和酸洗后交货。
(一)电工用热轧硅钢薄板(GB5212-85)电工用热轧硅钢薄板以含碳损低的硅铁软磁合金作材质,经热轧成厚度小于1mm的薄板。
电工用热轧硅钢薄板也称热轧硅钢片。
热轧硅钢片按其合硅量可分为低硅(Si≤2.8%)和高硅(Si≤4.8%)两种钢片。
硅钢基础知识(含义、分类、牌号表示方法、涂层)
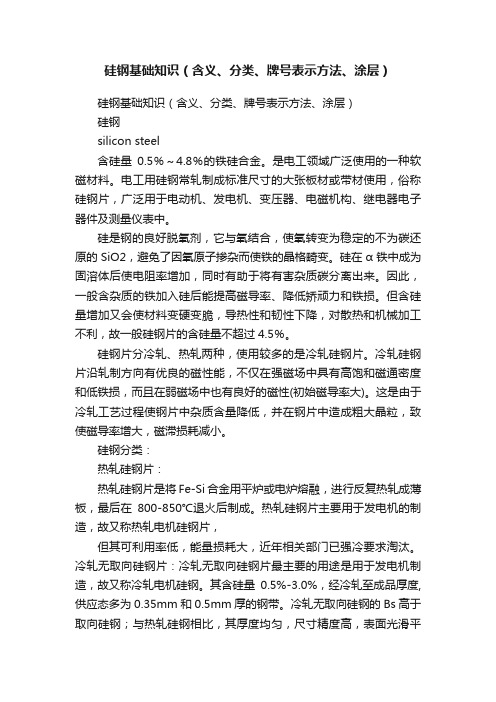
硅钢基础知识(含义、分类、牌号表示方法、涂层)硅钢基础知识(含义、分类、牌号表示方法、涂层)硅钢silicon steel含硅量0.5%~4.8%的铁硅合金。
是电工领域广泛使用的一种软磁材料。
电工用硅钢常轧制成标准尺寸的大张板材或带材使用,俗称硅钢片,广泛用于电动机、发电机、变压器、电磁机构、继电器电子器件及测量仪表中。
硅是钢的良好脱氧剂,它与氧结合,使氧转变为稳定的不为碳还原的SiO2,避免了因氧原子掺杂而使铁的晶格畸变。
硅在α铁中成为固溶体后使电阻率增加,同时有助于将有害杂质碳分离出来。
因此,一般含杂质的铁加入硅后能提高磁导率、降低矫顽力和铁损。
但含硅量增加又会使材料变硬变脆,导热性和韧性下降,对散热和机械加工不利,故一般硅钢片的含硅量不超过4.5%。
硅钢片分冷轧、热轧两种,使用较多的是冷轧硅钢片。
冷轧硅钢片沿轧制方向有优良的磁性能,不仅在强磁场中具有高饱和磁通密度和低铁损,而且在弱磁场中也有良好的磁性(初始磁导率大)。
这是由于冷轧工艺过程使钢片中杂质含量降低,并在钢片中造成粗大晶粒,致使磁导率增大,磁滞损耗减小。
硅钢分类:热轧硅钢片:热轧硅钢片是将Fe-Si合金用平炉或电炉熔融,进行反复热轧成薄板,最后在800-850℃退火后制成。
热轧硅钢片主要用于发电机的制造,故又称热轧电机硅钢片,但其可利用率低,能量损耗大,近年相关部门已强冷要求淘汰。
冷轧无取向硅钢片:冷轧无取向硅钢片最主要的用途是用于发电机制造,故又称冷轧电机硅钢。
其含硅量0.5%-3.0%,经冷轧至成品厚度,供应态多为0.35mm和0.5mm厚的钢带。
冷轧无取向硅钢的Bs高于取向硅钢;与热轧硅钢相比,其厚度均匀,尺寸精度高,表面光滑平整,从而提高了填充系数和材料的磁性能。
冷轧取向硅钢片:冷轧取向硅钢带最主要的用途是用于变压器制造,所以又称冷轧变压器硅钢。
与冷轧无取向硅钢相比,取向硅钢的磁性具有强烈的方向性;在易磁化的轧制方向上具有优越的高磁导率与低损耗特性。
常用的硅钢
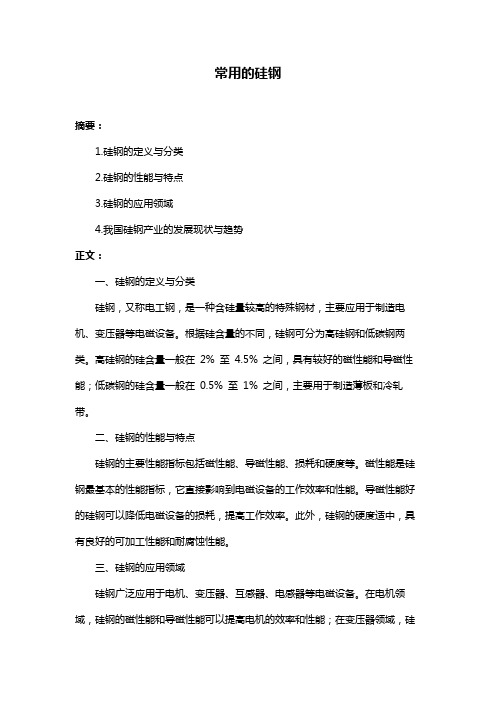
常用的硅钢
摘要:
1.硅钢的定义与分类
2.硅钢的性能与特点
3.硅钢的应用领域
4.我国硅钢产业的发展现状与趋势
正文:
一、硅钢的定义与分类
硅钢,又称电工钢,是一种含硅量较高的特殊钢材,主要应用于制造电机、变压器等电磁设备。
根据硅含量的不同,硅钢可分为高硅钢和低碳钢两类。
高硅钢的硅含量一般在2% 至4.5% 之间,具有较好的磁性能和导磁性能;低碳钢的硅含量一般在0.5% 至1% 之间,主要用于制造薄板和冷轧带。
二、硅钢的性能与特点
硅钢的主要性能指标包括磁性能、导磁性能、损耗和硬度等。
磁性能是硅钢最基本的性能指标,它直接影响到电磁设备的工作效率和性能。
导磁性能好的硅钢可以降低电磁设备的损耗,提高工作效率。
此外,硅钢的硬度适中,具有良好的可加工性能和耐腐蚀性能。
三、硅钢的应用领域
硅钢广泛应用于电机、变压器、互感器、电感器等电磁设备。
在电机领域,硅钢的磁性能和导磁性能可以提高电机的效率和性能;在变压器领域,硅
钢的损耗性能可以降低变压器的运行损耗,提高其工作效率。
此外,硅钢还应用于磁悬浮列车、风力发电、新能源汽车等领域,为我国的节能减排和绿色发展做出了重要贡献。
四、我国硅钢产业的发展现状与趋势
我国是世界上最大的硅钢生产和消费国。
近年来,我国硅钢产业在产量、品种、质量和应用领域等方面取得了显著的成果。
随着国家对硅钢产业的支持力度加大,硅钢产业的技术水平和产品质量得到了显著提高。
硅钢最新知识

30XQ120及30Q130适用于S9 ,S10,S11A,S11B(必要结构调整),适用种类为干式变压器,油浸变压器。
同板差是指在一块钢板上厚度的偏差,是指测厚仪测量一块钢板的实际厚度值与实际厚度平均值的差,英文简称In bar。
同板差是指在一块钢板上厚度的偏差,指在同一张钢板上任意两点之间的厚度差的最大值。
同板差就是根据纵向厚度和横向厚度两种检验结果确定的。
它是检验同一张钢板上厚度差是否符合公差标准要求的一项指标。
在生产中板带钢的厚度是根据其中心点处的厚度波动加以控制的,出厂时也只作纵向厚度检验。
对于轧后还要进行焊接或继续加工的钢板,如造船、锅炉、桥梁及冲压用钢板等,除了作纵向厚度检验外,还要作横向厚度检验。
1同一张钢板上任意两点之间的厚度差的最大值使用测厚仪测几个点后(点的数量越多当然越精确),用最大值减去最小值得出的差值1.》硅钢基础知识(含义、分类、牌号表示方法、涂层)硅钢silicon steel含硅量0.5%~4.8%的铁硅合金。
是电工领域广泛使用的一种软磁材料。
电工用硅钢常轧制成标准尺寸的大张板材或带材使用,俗称硅钢片,广泛用于电动机、发电机、变压器、电磁机构、继电器电子器件及测量仪表中。
硅是钢的良好脱氧剂,它与氧结合,使氧转变为稳定的不为碳还原的SiO2,避免了因氧原子掺杂而使铁的晶格畸变。
硅在α铁中成为固溶体后使电阻率增加,同时有助于将有害杂质碳分离出来。
因此,一般含杂质的铁加入硅后能提高磁导率、降低矫顽力和铁损。
但含硅量增加又会使材料变硬变脆,导热性和韧性下降,对散热和机械加工不利,故一般硅钢片的含硅量不超过4.5%。
硅钢片分冷轧、热轧两种,使用较多的是冷轧硅钢片。
冷轧硅钢片沿轧制方向有优良的磁性能,不仅在强磁场中具有高饱和磁通密度和低铁损,而且在弱磁场中也有良好的磁性(初始磁导率大)。
这是由于冷轧工艺过程使钢片中杂质含量降低,并在钢片中造成粗大晶粒,致使磁导率增大,磁滞损耗减小。
硅钢片的介绍(普及知识)

关于硅钢的常识硅钢(silicon steel)含硅量0.5%~4.8%的铁硅合金。
是电工领域广泛使用的一种软磁材料。
电工用硅钢常轧制成标准尺寸的大张板材或带材使用,俗称硅钢片,广泛用于电动机、发电机、变压器、电磁机构、继电器电子器件及测量仪表中。
硅是钢的良好脱氧剂,它与氧结合,使氧转变为稳定的不为碳还原的SiO2,避免了因氧原子掺杂而使铁的晶格畸变。
硅在α铁中成为固溶体后使电阻率增加,同时有助于将有害杂质碳分离出来。
因此,一般含杂质的铁加入硅后能提高磁导率、降低矫顽力和铁损。
但含硅量增加又会使材料变硬变脆,导热性和韧性下降,对散热和机械加工不利,故一般硅钢片的含硅量不超过4.5%。
硅钢片分冷轧、热轧两种,使用较多的是冷轧硅钢片。
冷轧硅钢片沿轧制方向有优良的磁性能,不仅在强磁场中具有高饱和磁通密度和低铁损,而且在弱磁场中也有良好的磁性(初始磁导率大)。
这是由于冷轧工艺过程使钢片中杂质含量降低,并在钢片中造成粗大晶粒,致使磁导率增大,磁滞损耗减小。
硅钢片的主要品质特性有铁损值、磁通密度、硬度、平坦度、厚度均匀性、涂膜种类及冲片性等。
以下针对各项品质特性加以说明。
1.铁损值硅钢片在某一特定频率的交流磁场下,磁化到特定的磁通密度时,每单位重量之硅钢片所损失的能量,称为铁损值。
通常所用的交流磁场频率为50或60赫兹,而所达到的磁通密度通常为1.5或1.7特斯拉。
常用的铁损值单位是每公斤或每磅硅钢片所损失的瓦特值,用Watt/kg或Watt/lb表示。
硅钢片的铁损值来源包括磁滞损、涡电流损和异常涡电流损三部份。
硅钢片在磁化的过程中,会产生磁滞的现象。
磁滞损即为B-H磁滞曲线所包涵的面积。
硅钢片的涡电流损起源于在交流变化的磁场,因法拉第定理的影响,硅钢片内部产生诱导电压,依照奥姆定律,电压在硅钢片内部引起诱导电流,进而造成硅钢片的焦耳热,这项能源损失称为涡电流损。
根据古典电磁学理论,涡电流损和钢片的厚度、电阻系数、磁通密度和频率有关。
硅钢产品知识

μm 颜色 层间电阻钢种 涂层类别涂层膜厚(T 2) 1.5~3.0灰色>30(GB2522-2007) 850(T 4) 0.8~1.2(GB2522-2007) 750透明 >20(HW )0.8~1.2 (GB2522-2007) 750 涂层(C 5) 0.5~4灰白>20(GB2522-2007) 800(C 6) 2~7 (ASTMA717-6) 不宜退火性环保型涂层 3~8 灰白—不宜退火家用电器用热轧硅钢薄板的牌号用 JDR+铁损值+厚度值来表示,如 JDR540- 50。
2. 日本牌号表示方法:2.1 冷轧无取向硅钢带由公称厚度(扩大 100 倍的值)+代号 A+铁损保证值(将频 率 50HZ ,最大磁通密度为 1.5T 时的铁损值扩大 100 倍后的值)。
如 50A470 表 示厚度为 0.5mm ,铁损保证值为≤4.7 的冷轧无取向硅钢带。
2.2 冷轧取向硅钢带由公称厚度(扩大 100 倍的值)+代号 G :表示普通材料,P : 表示高取向性材料+铁损保证值(将频率 50HZ ,最大磁通密度为 1.7T 时的铁损值 扩大 100 倍后的值)。
如 30G130 表示厚度为 0.3mm ,铁损保证值为≤1.3 的冷 轧取向硅钢带。
3. 美国牌号有M15_24G,M15_26G,M19_24G,M19_26G,M19_29,M22_24G,M22_26G,M22_ 29G 等等,这些牌号都是美国标准。
4. 永磁体选择国产牌号4.1 铁氧体永磁体牌号:Y10T,Y15,Y15H,Y20,Y20H 等等类似牌号都是的。
4.2 稀土钴永磁体牌号:XG112/96,XG128/120,XG144/120 等等类似牌号。
4.3 钐钴永磁体牌号:SmCo24,SmCo28 两种。
4.4 钕铁硼永磁体牌号:NdFe35,NdFe30 两种。
表面涂层绝缘特点Ω/平方米适用退火温度 ℃取向硅钢 半有机薄涂层NGO 半有机薄涂层浅绿 >15无取向硅钢 NGO 半有机薄涂层NGO 水溶性NGO 水溶性涂层灰白 >1500主 要NGO 自粘接1. 武汉钢铁股份有限公司2. 宝山钢铁股份有限公司钢薄规格取向硅钢高牌号无取向硅钢无取向硅钢低牌号HiB钢一般取向硅、0.350.15、0.200.35、0.50、0.650.35、0.500.50、0.65变压器★★变压器★★★变压器★★和磁放大器★★★★变压器★★★变压器★★★★★器,而110及以上牌号的取向硅钢可用于500kV和更高电压等级的变压器。
硅钢知识简介

目录关于硅钢的类型及性能←一、关于硅钢的类型及性能←二、硅钢板主要用语说明三我国硅钢片牌号表示方法(无取向)←三、我国硅钢片牌号表示方法(无取向)四、我厂的硅钢线的简易的工艺流程及简图和生产规规格←五、退火炉段←六、炉喉←七、炉内保护气体吹扫←八、炉压与脱碳的关系(对炉压差要有整体认识)←九、设备运行的视频←十、硅钢检验一、关于硅钢的类型及性能一关于硅钢的类型及性能←1、电工钢板的类别)无取向硅钢结晶不带方向性←(1)、无取向硅钢结晶不带方向性.自由排列的产品。
对所有的磁性特性致自由排列的产品。
对所有的磁性特性一致机机转机材所以用在发电机、电动机等旋转机铁芯材料及电源变压器、稳压器、小型静止电气上使用。
←(2)、取向硅钢通过特殊制作工艺结晶用个方向轧制方向排列大幅结晶用一个方向(轧制方向)排列,大幅提高特性。
←取向性硅钢板的用途轧制方向的磁性特性好,但轧制方向以外的磁性特性相对差最大限度体现轧制方向特性的各种变压器,磁放大器等和静止电气铁芯材料来使用.大型旋转机也有使用的时候。
大型旋转机也有使用的时候(3)、晶向)晶向硅钢板取向无取向硅钢板◈轧制方向磁性好◈所有方向磁性均匀、硅钢的性能要求2硅钢的性能要求←A、铁损低。
质量的最重要指标,世界各国都以铁损值划分牌号铁损越低牌号越高质量也高损值划分牌号,铁损越低,牌号越高,质量也高。
←B、磁感应强度高。
在相同磁场下能获得较高磁感片用制机或变压器铁体积的硅钢片,用它制造的电机或变压器铁芯的体积和重量较小,相对而言可节省硅钢片、铜线和绝缘材料等。
叠装系数高矽钢片表面光滑平整和厚度均←C、叠装系数高。
矽钢片表面光滑,平整和厚度均匀,制造铁芯的叠装系数提高。
←D、冲片性好。
对制造小型、微型电机铁芯,这点更重要。
←E、表面对绝缘膜的附着性和焊接性良好。
二、硅钢板主要用语说明铁损←1、铁损)硅钢板呈现产品特性重要的尺度在铁芯磁化过←1) 硅钢板呈现产品特性重要的尺度。
硅钢基础知识讲座
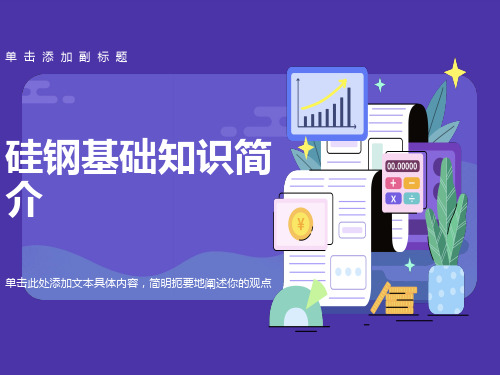
晶粒无取向 晶粒取向
2.3 热轧、冷轧的区别
2.4 主要用途
第二部分 硅钢的主要性能
主要性能 1磁性能:
铁损曲线
取向硅钢 30RK100
磁化曲线
取向硅钢 30RK100
铁损(P):单位重量的铁芯在交变磁场中磁化到一定磁感应强度所耗用的能量,这部分能量以热的形式放出。它包含磁滞损耗( Ph)、 涡流损耗( Pe)和附加损耗( Pa)。 P=Ph+Pe+Pa
用户无要求的执行国标或武钢企标
用户有要求的执行双方签定的技术协议或采购规范
质量保证依据给用户开具的《产品质量证明书》
四、武钢产品交货标准
4.1 武钢无取向硅钢磁性标准
*
*
4.2 武钢无取向硅钢尺寸公差标准
4.3 无取向硅钢机械性能标准
4.4 取向硅钢磁性能(常用牌号)
4.5 取向硅钢尺寸及允许偏差
■与硅钢片比非晶合金的特点及使用要求: (1)与S7 配电变压器相比,空载损耗下降75-80%,负载损耗下降23-27%。与S9 配电变压器相比,空载损耗下降74-77%,负载损耗基本相近; (2)非晶变压器空载功率因数为0.35,是硅钢片铁芯配电变压器的8倍以上; (3)硅钢片铁芯配电变压器的铁损随电压平方变化;而非晶变的铁损不随电压的变化而变化;
退火气氛:退火气氛的选择以冲片不氧化、不渗碳和磁性钢带表面绝缘涂层无明显恶化为原则。最好选用含氢2~10%的氮氢混合气体,加入少量的氢可保冲片不氧化。保护气体中的露点一般应在0℃以下。
严防渗碳和氧化:硅钢产品出厂含碳量小于0.003%(<30ppm)。因此铁芯片在消除应力退火时,必须严防渗碳,以免恶化磁性。炉用材料,如炉罩、底板应选用低碳钢。铁芯片表面的残余油脂应在退火前清除。防止铁芯片氧化是消除应力效果的重要措施。除合理选用退火气氛外,在操作时首先要确认炉膛密封是否完好,在送电升温前,先通入氮气或惰性气体进行炉内清扫。
硅钢片基础知识全集

硅钢片基础知识全集/ 13 冷轧晶粒取向、无取向磁性钢带标准 1、范围本标准规定了晶粒取向、无取向磁性钢带(片)的牌号、磁特性、尺寸、外形、力学性能、工艺特性和检验方法等。
本标准适用于磁路结构中使用的、带有绝缘涂层的全工艺冷轧取向和无取向磁性钢带(片)。
2、引用标准下列标准包含的条文,通过在本标准中引用而构成为本标准的条文。
在标准出版时,所示版本均为有效。
所有标准都会修订,使用本标准和各方应探讨使用下列标准最新版本的可能性。
GB/T228-87 金属拉伸试验方法GB/T235-88 金属反复弯曲试验方法(厚度等于或小于3mm薄板及带材)GB/T247-87 钢板和钢带验收、包装、标志及质量证明书的一般规定GB/T2522-88 电工钢片(带)层间电阻、涂层附着性、迭装系数测试方法GB/T3076-82 金属薄板(带)拉伸试验方法GB/T3655-92 电工钢片(带)磁、电和物理性能测量方法GB/T6397-86 金属拉伸试验试样GB/T13789-92 单片电工钢片(带)磁性能测量方法 3、定义和牌号表示方法 3.1定义 3.1.1标准比总铁损当磁感应强度随时间按正弦规律变化,其峰值为某一标定值,变化频率为某一标定频率时,单位质量的铁芯在温度20℃时所有消耗的功率定为标准比总铁损(简称标准铁损或铁损),单位为W/kg 3.1.2标准磁感应强度温度为20℃,铁芯试样从退磁状态,在标定频率下磁感应强度按正弦规律变化,当交流磁场的峰值达到某一标定值时,铁芯试样磁感的峰值为标准磁感强度(简称磁感应强度或磁感),单位为T 3.1.3弯曲次数弯曲次数是用肉眼观察到基体金属上第一次出现裂纹前反复弯曲的次数,它代表了材料的延展性。
3.2牌号表示方法 4、分类本标准中的磁性钢带(片)分为取向和无取向两大类,每类按最大铁损和材料的公称厚度分成不同牌号。
/ 13 5、技术要求 5.1磁特性 5.1.1磁感取向钢在800A/m交变磁场(峰值),频率为50HZ时,规定的最小磁感值B800(峰值)应符合表1的规定无取向钢在5000A/m交变磁场(峰值),频率为50HZ时,规定的最小磁感值B5000(峰值)应符合表2的规定 5.1.2铁损取向钢在磁感为1.7T、频率为50HZ时,规定的最大铁损P1.7应符合表1的规定。
硅钢基础知识讲座
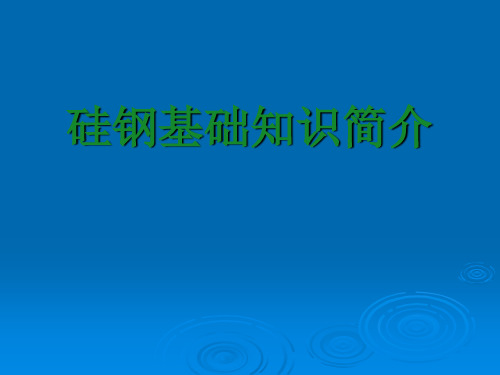
2.1.2各项性能检测执行标准
类别 磁性能 性能 铁损 磁感 强度 延伸率 反弯 硬度 涂层 层间电阻 叠装系数 执行标准 GB/T3655-2008 GB/T228-2002 GB/T235-1999 GB/T4340.1-1999 GB/T2522-2007 GB/T19289-2003
力学性能
煤
焦炉
酸洗常化
轧制
脱碳退火
高温退火
拉伸退火及涂层
激光刻痕
精整分卷
成品
二、硅钢产品的检验
硅钢产品的磁性及厚度是通过成 品机组在线连续检测,记录整卷性能
曲线,并在机组出侧取卷头、尾样或
剪切机组重取样送检,根据检测结果, 比照在线连续检测曲线,进行硅钢产 品的牌号判定。
连续在线检测铁损和厚度记录曲线
冷轧硅钢片各项性能检验表:
不宜进行消除应力退火
晶粒无取向硅钢
晶粒无取向硅钢
晶粒无取向硅钢
在无氧化气氛中,能经 在无氧化气氛中,能经 在无氧化气氛中,能经 在无氧化气氛中,能经 受700~750℃消除应力 受800℃的消除应力退火 受800℃的消除应力退火 受750℃的消除应力退火 退火
对于绝缘油漆、机器油和制冷介质均有较高的抗蚀性能
二、其它性能
为了增大电机铁心叠片间的绝缘,减 小叠片中的涡流损耗,同时改善电工钢片 的焊接、冲剪性能,电工钢片表面都要求 有一层绝缘层。 对绝缘层的基本要求是:绝缘电阻高、 化学稳定性好、机械强度高、不粘结、耐 腐蚀,同时要求绝缘层薄而平整,以提高 叠片的叠片系数。
2.1 涂层的种类及作用
高级晶粒取向硅钢 钢种 一般晶粒取向硅钢 一般晶粒取向硅钢 涂层种类 成分 颜色 涂层厚度μm 层间电阻Ω·cm 2 /片 附着性 冲片性 防锈性 耐热性 耐蚀性 良 良 T1 无机质 灰色 3 ≥30 B-E级 T2 无机质 灰色 3 ≥30 B-E级 T3 无机质 透明 1.5 >3 B-C级 一般 一般 T4 半有机 淡褐色 1~2 >3 A-B级 优 优 T5 有机 淡褐色 3 >5 A-B级 优 优
硅钢片的介绍(普及知识)

硅钢(silicon steel)含硅量0.5%~4.8%的铁硅合金。
是电工领域广泛使用的一种软磁材料。
电工用硅钢常轧制成标准尺寸的大张板材或带材使用,俗称硅钢片,广泛用于电动机、发电机、变压器、电磁机构、继电器电子器件及测量仪表中。
硅是钢的良好脱氧剂,它与氧结合,使氧转变为稳定的不为碳还原的SiO2,避免了因氧原子掺杂而使铁的晶格畸变。
硅在α铁中成为固溶体后使电阻率增加,同时有助于将有害杂质碳分离出来。
因此,一般含杂质的铁加入硅后能提高磁导率、降低矫顽力和铁损。
但含硅量增加又会使材料变硬变脆,导热性和韧性下降,对散热和机械加工不利,故一般硅钢片的含硅量不超过4.5%。
硅钢片分冷轧、热轧两种,使用较多的是冷轧硅钢片。
冷轧硅钢片沿轧制方向有优良的磁性能,不仅在强磁场中具有高饱和磁通密度和低铁损,而且在弱磁场中也有良好的磁性(初始磁导率大)。
这是由于冷轧工艺过程使钢片中杂质含量降低,并在钢片中造成粗大晶粒,致使磁导率增大,磁滞损耗减小。
硅钢片的主要品质特性有铁损值、磁通密度、硬度、平坦度、厚度均匀性、涂膜种类及冲片性等。
以下针对各项品质特性加以说明。
1.铁损值硅钢片在某一特定频率的交流磁场下,磁化到特定的磁通密度时,每单位重量之硅钢片所损失的能量,称为铁损值。
通常所用的交流磁场频率为50或60赫兹,而所达到的磁通密度通常为1.5或1.7特斯拉。
常用的铁损值单位是每公斤或每磅硅钢片所损失的瓦特值,用Watt/kg或Watt/lb表示。
硅钢片的铁损值来源包括磁滞损、涡电流损和异常涡电流损三部份。
硅钢片在磁化的过程中,会产生磁滞的现象。
磁滞损即为B-H磁滞曲线所包涵的面积。
硅钢片的涡电流损起源于在交流变化的磁场,因法拉第定理的影响,硅钢片内部产生诱导电压,依照奥姆定律,电压在硅钢片内部引起诱导电流,进而造成硅钢片的焦耳热,这项能源损失称为涡电流损。
根据古典电磁学理论,涡电流损和钢片的厚度、电阻系数、磁通密度和频率有关。
- 1、下载文档前请自行甄别文档内容的完整性,平台不提供额外的编辑、内容补充、找答案等附加服务。
- 2、"仅部分预览"的文档,不可在线预览部分如存在完整性等问题,可反馈申请退款(可完整预览的文档不适用该条件!)。
- 3、如文档侵犯您的权益,请联系客服反馈,我们会尽快为您处理(人工客服工作时间:9:00-18:30)。
硅钢带的生产1903年美国和德国首先生产了热轧硅钢。
美国阿姆柯钢公司于1935年开始生产冷轧取向硅钢,20世纪40年代初生产无取向硅钢。
50年代主要工业发达国家陆续引进阿姆柯技术专利。
70年代前,世界约80%取向硅钢都按此专利生产。
1968年日本新日铁正式生产高磁感取向硅钢(Hi-B钢)。
从1971年开始,美国等6个国家引进了日本Hi—B钢专利。
从1968年开始,日本在冷轧电工钢产品质量、制造技术和装备、开发新产品和新技术、科研和测试技术各方面都远超过美国,处于领先地位。
我国太原钢铁(集团)公司于1954年首先生产热轧硅钢。
1957年钢铁研究总院研制成功冷轧取向硅钢,到1973年已掌握阿姆柯技术专利要点。
1974年武汉钢铁(集团)公司从日本新日铁引进冷轧硅钢制造装备和专利,1979年正式生产11个牌号的冷轧取向及无取向硅钢。
4.1 电工钢的分类及性能4.1.1 电工钢的分类电工钢按其成分分为低碳低硅(碳含量很低,硅的质量分数小于0.5%)电工钢和硅钢两类;按最终加工成形的方法分为热轧硅钢和冷轧硅钢两大类;按其磁各向异性分为取向电工钢和无取向电工钢。
热轧硅钢板均系无取向硅钢,硅钢的磁各向异性是在冷轧后通过二次再结晶过程发展而成的,因此只有冷轧电工钢才有取向与无取向之分。
由于产品的用途不同对磁各向异性的要求不同。
在旋转状态下工作的电机要求电工钢磁各向同性,用无取向电工钢制造;变压器在静止状态下工作,要求沿一个方向磁化(轧制方向),用冷轧取向硅钢制造,因此取向硅钢又称变压器钢。
我国电工用热轧硅钢薄板的国家标准号为GB5212—85;从20世纪60年代开始,主要工业发达国家陆续停止了热轧硅钢板的生产。
我国冷轧晶粒取向、无取向磁性钢带(片)的国家标准号为GB2521—1996。
标准中的牌号表示方法为:以字母W表示无取向钢带(片);以字母Q表示取向钢带(片);以字母G表示取向钢中的高磁感材料。
在一些资料、书籍中,称普通取向硅钢为GO钢,高磁感取向硅钢为Hi-B钢,电工钢分类见表3—1。
4.1.2 电工钢的性能要求4.1.2.1 磁性能电工钢是以其铁损和磁感应强度作为产品磁性保证值的。
用户对电工钢的磁性能要求如下:(1) 低的铁损。
铁损(尸t)是由磁滞损耗(Ph)、涡流损耗(Pe)和反常损耗(Pa)三部分组成的。
铁损低可节省大量电力、延长电机和变压器工作时间并简化冷却装置。
因电工钢的铁损造成的电量损失占一个国家年发电量的2.5%一4.5%,其中变压器约占50%,小电机占30%,镇流器占15%。
因此,各国生产电工钢板总是千方百计地降低铁损,并以铁损作为考核产品磁性能的最重要的指标,按铁损值作为划分牌号的依据。
(2) 高的磁感应强度。
磁感应强度高,铁芯激磁电流(空载电流)降低,导线电阻引起的铜损和铁芯铁损降低,可节省电能。
当电机或变压器容量不变时,磁感应强度高可使铁芯体积缩小和质量减轻,节省电工钢板、导线等的用量,并使铁芯铁损和制造成本降低,有利于制造、安装和运输。
(3) 对磁各向异性的要求。
硅钢是体心立方晶体结构,其晶轴不同,磁化特性也不同。
三个主轴方向的磁性,[100]方向为易磁化轴,[110]方向为次易磁化轴,[111]方向为难磁化轴。
这种磁化特性称为磁各向异性。
电工钢的用途不同,要求磁各向异性不同。
电机在旋转状态下工作,要求电工钢磁各向同性,用无取向电工钢制造;变压器在静止状态下工作,要求磁各向异性,用冷轧取向硅钢制造。
(4) 磁时效小。
铁芯的磁性随使用时间而变化的现象叫磁时效。
磁时效主要是由于过饱和碳和氮析出微小碳化物和氮化物而引起的。
所以要求电工钢产品中碳含量(质量分数) 和氮含量(质量分数)分别小于0.0035%和0.005%。
4.1.2.2 加工性能由于电工钢还需要进一步加工成形,用户对电工钢的加工性能也有一定的要求:(1) 好的冲片性。
电工钢成形的冲剪工作量很大,特别是微、小电机,所以要求电工钢板的冲片性好。
冲片性好能够提高冲剪片的尺寸精度,延长冲剪工具的使用寿命。
(2) 表面光滑平整,厚度偏差小和均匀。
这项要求主要是为了提高产品的叠片系数(铁芯有效利用空间),保证冲剪片尺寸精度和便于铁芯装配。
电工钢板的叠片系数降低1%,相当于铁损增高2%和磁感强度降低1%。
4.1.2.3 好的绝缘膜.冷轧电工钢产品表面涂有无机盐或半有机盐绝缘薄膜,以防止铁芯叠片间发生短路而增高涡流损耗。
对绝缘膜的要求是:(1)耐热性好;(2)膜薄且均匀;(3)层间电阻高;(4)附着性好;(5)冲片性好;(6)耐腐蚀性和防锈性好。
高磁感取向硅钢表面涂以应力涂层,使钢板中产生拉应力,通过细化磁畴使铁损和磁致伸缩明显降低。
不同用途的电工钢,对磁性、冲片性和绝缘性有不同的要求。
不同的最终加工成形方法,对磁性和加工性有不同影响。
冷轧电工钢比热轧电工钢具有如下优点:(1)磁性高,可节省大量电能;(2)表面光滑,叠片系数高;(3)冲片性好;(4)表面涂绝缘膜,便于使用;(5)成卷供应,适用于高速冲床,利用率高。
4.1.3 影响电工钢性能的因素磁感应强度和铁损是电工钢磁性的根本特性。
4.1.3.1 影响磁感应强度的因素影响磁感应强度的因素有:(1) 无取向电工钢的磁感应强度主要与硅含量和晶体织构有关。
硅含量提高,磁感应强度月50值降低。
无取向电工钢基本为混乱织构,但调整成分和改善制造工艺,可使织构中(100)和(110) 位向组分加强,(111)组分减弱,Bso值提高钢中杂质和夹杂物含量增高,以及成品晶粒尺寸增大,也使B.so值降低。
(2) 冷轧取向硅钢的硅含量(质量分数)基本不变(在2.9%一3.5%Sl的范围内变化),所以磁感应强度只随(110)[001]晶粒取向度提高或(110)[001]位向偏离角减小而增高。
4.1.3.2 影响铁损的因素影响铁损Pt的因素多且复杂,因为影响组成Pt的磁滞损耗Ph涡流损耗Pe和反常损耗Pa的因素各不相同,而且其中一些因素对这三种铁损组分具有完全相反的影响,只能最终看表现在Pt值上的综合效果。
无取向电工钢铁损Pt中,Ph占60%一80%,主要是降低Ph。
取向硅钢铁损Pt中,Ph仅占大约30%,Pe十Pa约占70%,而Pa又比Pe大1~2倍,因此降低铁损主要应降低Pa和Pe,特别是Pa。
A 影响磁致损耗Ph的因素影响几的因素就是影响磁畴壁移动的因素,它们是:(1) 晶体织构。
取向硅钢(110)[001)取向度提高或无取向电工钢中(100)位向组分增高,则Ph降低。
(2) 杂质、夹杂物和内应力。
它们使晶格发生畸变,位错密度增高,阻碍磁畴壁移动,所以Ph增高。
(3) 晶粒尺寸。
晶界的晶格是畸变的,晶体缺陷多,使磁畴壁移动阻力增大,所以晶粒小晶界面大,Ph增高。
(4) 板厚。
成品厚度减薄,表面自由磁极能量(静磁能)增大,磁畴壁移动阻力增加,Ph 增高。
(5) 表面状态。
钢板表面平滑,表面自由磁极减少,磁畴壁移动阻力减小,Ph降低。
B 影响涡流损耗Pe和反常损耗Pa的因素Pe与电工钢的电阻率 (取决于硅含量)成反比关系;与板厚t的平方成正比关系。
Pa与电工钢的磁畴结构有关。
日本近十年降低取向硅钢铁损的三个主要措施(提高硅含量、减薄成品厚度和细化磁畴)就是以此理论为依据的。
影响磁畴尺寸的主要因素是:(1) 晶粒尺寸。
晶粒粗大,磁畴尺寸增大,畴壁移动速度加快,而Pa与畴壁移动速度平方成正比关系,所以Pa增大。
(2) (110)[001]位向偏离角。
取向硅钢[001]位向对轧制面的倾角时,1800主磁畴尺寸减小,Pa降低。
(3) 拉应力效应。
沿轧制方向加拉应力,1800磁畴细化和900亚磁畴减少,Pa减低。
应力涂层就是据此效应开发的。
(4) 刻痕效应。
取向硅钢表面沿横向刻度可使磁畴细化,降低Pa。
但刻度使钢板表面不平和叠片系数降低,故无实用价值。
4.1.3.3 硅的作用硅是影响电工钢磁性、力学性能最基本的因素。
在电工钢中加硅主要是提高电阻率,降低涡流损耗,同时使矫顽力和磁滞损耗也降低,从而使铁损下降,但磁感应强度和饱和磁感应强度也降低,随着硅含量增高,钢的屈服强度和抗拉强度明显提高,但硅含量(质量分数)大于3.5%时的屈服强度和硅含量(质量分数) 大于4.0%时的抗拉强度又迅速降低,随着硅含量增高,伸长率显著降低,硬度迅速增高。
因此,热轧硅钢的硅含量(质量分数)上限约为4.5%,冷轧硅钢约为4.5%,随着硅含量增高,钢的热导率下降,铸造晶粒粗大。
4.2硅钢生产工艺4.2.1 生产硅钢的理论依据在冶金生产过程中,影响磁性能的冶金因素是制定各类磁性锅合理生产工艺的主要依据。
3.2.1.1 取向硅钢生产的理论依据硅钢和铁一样都是体心立方晶体结构,其晶轴不同,磁化特性不同。
图3•1为体心立方晶格结构示意图,[100]方向为易磁化轴晶格结构示意图,(100)方向为易磁化轴,(110)方向为次易磁化轴,(111)方向为难化轴。
这种磁化特性称为磁各向异性。
取向硅钢就是利用这种磁各向异性原理制造出来的。
图3—2为取向硅钢的晶粒位向示意图。
[100]轴平行轧向(即钢板的长度方向),(110)面平行轧面(即钢板表面),这种位向称为高斯织构,表示为(110)(001)。
高斯织构是通过二次再结晶过程发展面成的。
为了获得优良的高斯织构必须具备三个条件。
(1) 热轧板中必须存在(110)(001)晶粒(2) 基体中必须含有细小并且均匀弥散分布的第二相质点,也称抑制剂(如MnS、AIN 等)。
二次再结晶的驱动力是晶界能,抑制剂的作用是阻碍初次再结晶晶粒长大,促进二次再结晶发展,使(110)(001)位向的初次晶敞通过二次再结晶吞食其他位向的初次晶粒而迅速长大。
抑制初次再结晶晶粒长大的能力,与抑制剂质点尺寸成反比关系,与抑制剂质点数量成正比关系。
(3) 要求初次晶粒均匀细小因此,在钢水成分、热轧工艺、冷轧及热处理工艺等方面均需保证上述条件的实现。
取向硅钢根据机理及生产工艺不取向硅钢有普通取向硅钢(GO钢)和高磁感取向硅钢(Hi-B钢)之分。
普通取向硅钢以MnS作为抑制剂,采用二次冷轧工艺生产,进行一次中间退火,产品易磁化轴[001]偏离轧制方向的平均角在70左右;晶粒尺寸平均为3—5mm。
高磁感取向硅钢以MnS+AlN作为抑制剂。
采用一次冷轧工艺生产,产品易磁化轴[001]偏离轧制方向的平均角在30以内,因此磁感应强度更高(Hi-B名由此而来),而铁损更低,晶粒尺寸平均为10mm一20mm。
4.2.1.2 无取向硅钢的生产特点无取向硅钢有普通无取向硅钢和高级无取向硅钢之分。
普通无取向硅钢,w(Si)<1.5%,生产牌号相当于50W540、50W600;高级无取向硅钢w(Si)>2.0%除控制硅含量外,为达到产品性能的要求,锰和铝的含量也是无取向硅钢炼钢时要严格控制的,而碳、硫、氮等有害元素含量要尽量低。