30×2100×5000(Q215) 中厚板生产规程设计
某中厚板厂车间设计与生产工艺流程的制定
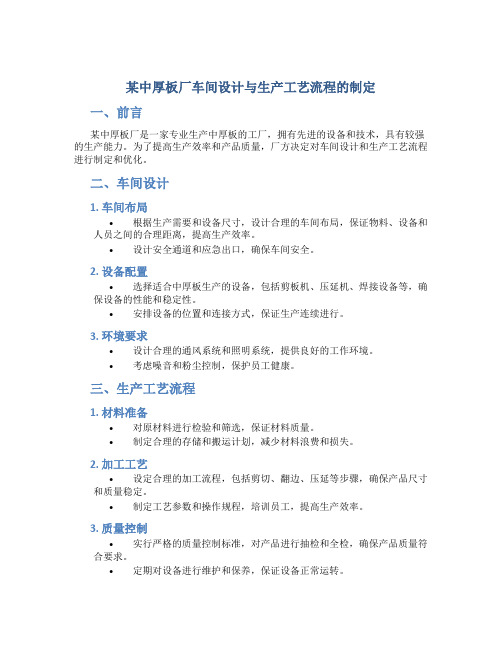
某中厚板厂车间设计与生产工艺流程的制定一、前言某中厚板厂是一家专业生产中厚板的工厂,拥有先进的设备和技术,具有较强的生产能力。
为了提高生产效率和产品质量,厂方决定对车间设计和生产工艺流程进行制定和优化。
二、车间设计1. 车间布局•根据生产需要和设备尺寸,设计合理的车间布局,保证物料、设备和人员之间的合理距离,提高生产效率。
•设计安全通道和应急出口,确保车间安全。
2. 设备配置•选择适合中厚板生产的设备,包括剪板机、压延机、焊接设备等,确保设备的性能和稳定性。
•安排设备的位置和连接方式,保证生产连续进行。
3. 环境要求•设计合理的通风系统和照明系统,提供良好的工作环境。
•考虑噪音和粉尘控制,保护员工健康。
三、生产工艺流程1. 材料准备•对原材料进行检验和筛选,保证材料质量。
•制定合理的存储和搬运计划,减少材料浪费和损失。
2. 加工工艺•设定合理的加工流程,包括剪切、翻边、压延等步骤,确保产品尺寸和质量稳定。
•制定工艺参数和操作规程,培训员工,提高生产效率。
3. 质量控制•实行严格的质量控制标准,对产品进行抽检和全检,确保产品质量符合要求。
•定期对设备进行维护和保养,保证设备正常运转。
四、总结某中厚板厂车间设计和生产工艺流程的制定,是为了提高生产效率和产品质量,确保工厂的可持续发展。
通过合理的车间设计和生产工艺流程制定,可以实现生产流程的规范化和标准化,提高生产效率和产品质量,满足市场需求。
最后,希望厂方能根据本文档提供的建议和指导,不断优化和改进车间设计和生产工艺流程,使中厚板产品更具竞争力。
中厚板轧制规程设计方法39页PPT

23、一切节省,归根到底都归结为时间的节省。——马克思 24、意志命运往往背道而驰,决心到最后会全部推倒。——莎士比亚
中厚板轧制规程设计方法
26、机遇对于有准备的头脑有特别的 亲和力 。 27、自信是人格的核心。
28、目标的坚定是性格中最必要的力 量泉源 之一, 也是成 功的利 器之一 。没有 它,天 才也会 在矛盾 无定的 迷径中 ,徒劳 无功。- -查士 德斐尔 爵士。 29、困难就是机遇。--温斯顿.丘吉 尔。 30、我奋斗,所以我快乐。--格林斯 潘。
中厚板热处理工艺设计技术规程
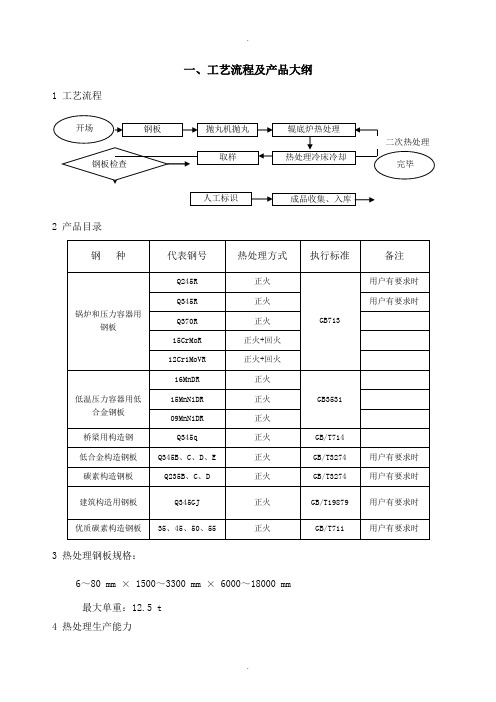
一、工艺流程及产品大纲1 工艺流程2 产品目录3 热处理钢板规格:6~80 mm × 1500~3300 mm × 6000~18000 mm最大单重:12.5 t4 热处理生产能力钢板的正火或钢板的高温回火,年处理量20.5万吨,其中正火钢板19万吨/年;回火钢板1.5万吨/年。
二抛丸清理区域工艺技术操作规程1、抛丸清理区域主要设备及性能1.1 抛丸清理机总体性能参数1.2 抛丸清理机前上料、机后输送辊道:1.3 抛丸室输送辊道:1.4 抛丸除锈系统1.5 丸料清扫系统对钢板的清理采用二级清扫加二级风吹的方式:一级滚扫采用传统的高强度尼龙滚刷+收丸螺旋的方式;二级横扫采用钢丝侧刷+压轮方式,清扫大量弹丸;一级风吹采用高压风机在清扫室内吹丸。
二级风吹采用高压空气在清扫室进展吹丸。
1.6 丸料循环系统1.7抛丸器1.8 除尘系统1.9 气控系统1.10 起重设备2 抛丸清理机的工艺操作规程2.1抛丸清理运行方式的选择运行方式分为自动和手动两种方式。
自动方式为总操作台上"自动/手动〞转换开关位于"自动〞位置,按压自动起动按钮后,抛丸机按PC内预定程序顺序起动。
在进展完毕时,按压自动停顿按钮后,抛丸机的电气设备将顺序关机。
手动方式为"自动/手动〞转换开关位于"手动〞位置,操作人员可按照预处理的要求,分别按压相关的起动停顿按钮,来控制电气设备的工作状态。
如从"手动〞转为"自动〞运行时,要保证抛丸机和辊道上没有钢板,然后将转换开关扳向"自动〞位置,进入启动自动开机程序。
在"手动〞和"自动〞方式中,操作人员均可通过观察模拟屏上设备的运行状态的显示,来判断抛丸机的工作状况。
2.2 钢板抛丸清理工艺规定2.2.1 按炉〔批〕进展钢板抛丸清理,严禁混炉混号。
2.2.2 钢板的摆放吊板放在抛丸机前上料辊道上一定要放正,使其摆放在上料辊道的中间位置。
中厚板厂安全操作规程内容
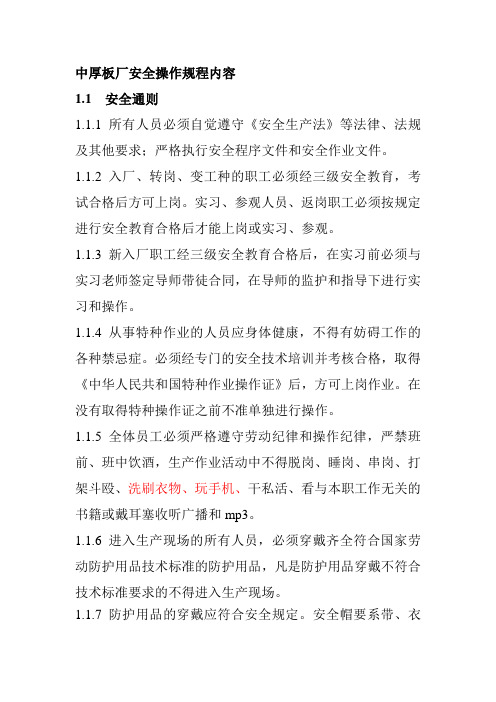
中厚板厂安全操作规程内容1.1 安全通则1.1.1 所有人员必须自觉遵守《安全生产法》等法律、法规及其他要求;严格执行安全程序文件和安全作业文件。
1.1.2 入厂、转岗、变工种的职工必须经三级安全教育,考试合格后方可上岗。
实习、参观人员、返岗职工必须按规定进行安全教育合格后才能上岗或实习、参观。
1.1.3 新入厂职工经三级安全教育合格后,在实习前必须与实习老师签定导师带徒合同,在导师的监护和指导下进行实习和操作。
1.1.4 从事特种作业的人员应身体健康,不得有妨碍工作的各种禁忌症。
必须经专门的安全技术培训并考核合格,取得《中华人民共和国特种作业操作证》后,方可上岗作业。
在没有取得特种操作证之前不准单独进行操作。
1.1.5 全体员工必须严格遵守劳动纪律和操作纪律,严禁班前、班中饮酒,生产作业活动中不得脱岗、睡岗、串岗、打架斗殴、洗刷衣物、玩手机、干私活、看与本职工作无关的书籍或戴耳塞收听广播和mp3。
1.1.6 进入生产现场的所有人员,必须穿戴齐全符合国家劳动防护用品技术标准的防护用品,凡是防护用品穿戴不符合技术标准要求的不得进入生产现场。
1.1.7 防护用品的穿戴应符合安全规定。
安全帽要系带、衣服扣紧各部位钮扣、不准穿着化纤服装、女员工不准穿高跟鞋、长头发的女员工应将头发盘入安全帽内、坐通勤车员工不准穿拖鞋。
1.1.8 进入高温、噪声作业区域的人员(参观、检查、临时通过的人员执行相关方管理规定),必须佩戴防高温面罩和防噪声耳塞。
1.1.9 工作前应认真检查自己使用的工具、仪器、材料及所需物件,确认无缺陷、无损坏、无异常后方可使用。
1.1.10 生产工作场所、人行通道的上方都应设有足够的照明,作业中上下走梯、进行平台作业,环境不熟悉区域作业时脚要站稳、手要抓牢,不准进入视线不清的地段。
1.1.11 非本岗位人员不准随便触动各种操作手柄、按钮、操作键、电气开关及各种阀门。
1.1.12 设备在运转过程中(包括机械设备、电气设备、煤气设备、压力容器等),不得靠近、清扫、检查、修理、人工调整或测量。
中厚板设计

1 产品方案与坯料的选择1.1 产品方案的主要内容产品方案是设计任务书的主要内容之一,是进行车间设计时制定产品生产工艺过程中,确定轧机组成和选择各项设备的主要依据。
制定产品方案的主要原则:(1)满足国民经济发展对轧制产品的需求,特别是根据市场信息解决某些短缺产品的供应和优先保证国民经济重要部门对与钢材的需要。
(2)考虑各类产品的平衡,尤其是地区之间产品的平衡。
要正确处理长远与当前,局部和整体的关系。
做到供应适合,品种平衡。
产销对路,布局合理,要防止不顾轧机特点,不顾车间具体工艺设备条件一哄而上,一哄而下的倾向。
(3)考虑轧机生产能力的充分利用和建厂地区的合理分工。
有条件的要争取轧机的专业化和产品系列化的发展,以利于提高轧机生产技术水平。
(4)考虑建厂地区资源及环境条件,物资和材料等道路运输情况,逐步完善和配套起我国自己的独立的轧钢生产体系。
(5)要逐步解决产品品种和规格老化问题要适应当前对外开放,对内搞活新的经济形式的需要,要根据车间工业设备的情况,力争做到产品结构和产品标准的现代化,有条件的考虑生产一些出口产品,走向国际市场。
产品方案的主要内容包括:(1)车间生产的钢种和生产的规模;(2)各类产品的品种和规格(3)种类产品的数量和其在总量中所占的比例。
各种产品的品种和规格及种类产品的数量和其在总量中所占的比例如表所示表1-1中厚板产品方案(典型产品:1.2金属平衡表成品率的倒数即为金属的消耗系数。
它表示轧制一吨成品需要多少吨原料。
所以成品的数量乘以1金属消耗系数就是金属的需要量。
即:原料需要量=金属消耗系数×成品数量为分析轧钢生产中金属的损失,寻找降低损失的途径。
须编制金属平衡表按本次设计要求。
本设计只列出典型产品的金属平衡表。
单位(万t)表1-2金属平衡表1.3坯料的技术条件1.3.1中厚板的坯料选用中厚板生产采用的原料有扁锭、初扎坯、连铸坯、三种。
中厚板生产压下规程设计
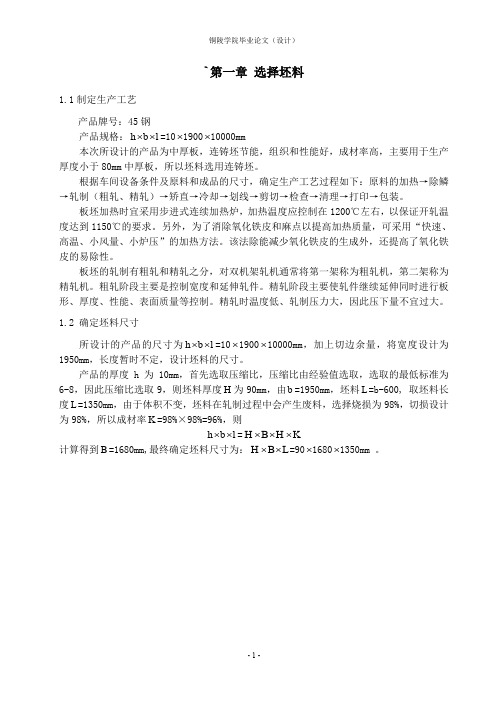
`第一章选择坯料1.1制定生产工艺产品牌号:45钢产品规格:l⨯=10⨯1900⨯10000mmbh⨯本次所设计的产品为中厚板,连铸坯节能,组织和性能好,成材率高,主要用于生产厚度小于80mm中厚板,所以坯料选用连铸坯。
根据车间设备条件及原料和成品的尺寸,确定生产工艺过程如下:原料的加热→除鳞→轧制(粗轧、精轧)→矫直→冷却→划线→剪切→检查→清理→打印→包装。
板坯加热时宜采用步进式连续加热炉,加热温度应控制在1200℃左右,以保证开轧温度达到1150℃的要求。
另外,为了消除氧化铁皮和麻点以提高加热质量,可采用“快速、高温、小风量、小炉压”的加热方法。
该法除能减少氧化铁皮的生成外,还提高了氧化铁皮的易除性。
板坯的轧制有粗轧和精轧之分,对双机架轧机通常将第一架称为粗轧机,第二架称为精轧机。
粗轧阶段主要是控制宽度和延伸轧件。
精轧阶段主要使轧件继续延伸同时进行板形、厚度、性能、表面质量等控制。
精轧时温度低、轧制压力大,因此压下量不宜过大。
1.2 确定坯料尺寸所设计的产品的尺寸为l⨯=10⨯1900⨯10000mm,加上切边余量,将宽度设计为bh⨯1950mm,长度暂时不定,设计坯料的尺寸。
产品的厚度h为10mm,首先选取压缩比,压缩比由经验值选取,选取的最低标准为6-8,因此压缩比选取9,则坯料厚度H为90mm,由b=1950mm,坯料L=b-600, 取坯料长度L=1350mm,由于体积不变,坯料在轧制过程中会产生废料,选择烧损为98%,切损设计为98%,所以成材率K=98%×98%=96%,则h⨯⨯=KblH⨯⨯⨯HB计算得到B=1680mm,最终确定坯料尺寸为:L⨯=90⨯1680⨯1350mm 。
H⨯B第二章变形量分配2.1 确定轧制方法先经过二辊轧机纵轧一道,在不考虑切边的情况下,使板坯长度等于成品宽度,然后转90°横轧到所需规格。
2.2 确定道次压下量坯料尺寸:LBH⨯⨯ =90⨯1680⨯1350mm,则总的压下量为90-10=80mm。
中厚板轧制规程设计方法
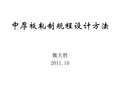
• 2.在采用控轧控冷时,要根据工艺要求, 结合温度制度、速度制度合理的安排压下 量。 • 3.双机架轧制时,要均衡分配道次和轧制 负荷,提高作业率。
三.设计步骤
• 1.根据原料尺寸和生产的钢板品种规格,在满足 轧件顺利咬入的条件下,确定轧制道次,分配各 道次的压下量和压下率。 • 2.制定速度制度,计算轧制时间和各道次的温度。 • 3.按上述确定的参数计算轧制力、轧制力矩和主 电机功率。 • 4.校核轧辊强度、传动系统强度、主电机功率。 • 5.对不合适的部分进行修正,得到合理的压下规 程。 • 中厚板轧制规程的制定流程图如下:
• 4.计算用主要数学模型 • (1)温度模型 • 轧钢生产中温度起着重要的作用,它会影响到材 料的变形抗力、工作辊热凸度等,最终影响到钢 材的性能和产品尺寸精度。因此必须计算不同阶 段的轧件温度。 • 轧钢生产时轧件的温度随着时间会发生变化: 有热量损失:如热辐射;热对流;水冷却;工作 辊间的热传导等,导致钢材温度降低。 有热量增加:如机械塑性加工热;钢板和工作辊 间的摩擦热等,导致钢材温度上升。 • 为了方便计算可以做如下假设: 宽度方向和轧制方向的热流量可以忽略,只考虑 厚度方向的热流量; 轧件的长度方向温度是光滑的变量;
• 1.轧制过程分为三个阶段 • ⑴成形阶段。 压下量主要考虑坯料纵横轧 制比 对坯料成形的矩形化影响;为横轧提供尺寸精度 的保证;轧制长度要考虑能转钢。 • ⑵展宽阶段。 压下量主要考虑宽度控制;考虑性 能控制,在可能情况下,尽量采用大压下量。 • ⑶伸长阶段 • ①前半道次。在设备能力允许的条件下,采 用大压下量。 • ②后半道次。考虑板形和厚度精度,一般采 用恒比例凸度优先的原则控制压下量;采用液压 弯辊时,可根据弯辊的能力设定压下量。
二.轧制规程设计原则
中厚板生产压下规程课程设计(DOC)

《塑性成型工艺(轧制)》课程设计说明书课题名称12×1800×10000mm轧制规程设计指导教师张金标. 专业小组10材控第3设计小组.小组成员x x x 101012101xx x x 101012101xx x x 101012101xx x x 101012101xx x x 101012101xx x x 101012101x2013年06月05日《塑性成型工艺(轧制)》课程设计任务书10级材料成型与控制工程专业设计小组:第 3 小组成员:x x x x x x x x xx x x x x x x设计课题:中厚板轧制规程设计指导教师:张金标一、设计产品设计小组学生学号产品牌号产品规格/mm1 24,1,2,3,4,5 Q235 10×2000×90002 6,7,8,9,10,11 45 10×1900×100003 12,13,14,15,16,17 12CrNi3A 12×1800×100004 18,19,20,21,22,24 4Cr13 13×1700×90005 25,26,27,28,29,30 Q235 12×2100×120006 31,32,33,34,35,36 45 8×1800×130007 37,38,39,40,41,42 12CrNi3A 14×2000×90008 43,44,45,46,47,48 4Cr13 12×2000×80009 49,50,51,52,53,55 Q235 9×2050×1200010 56,57,58,59,60,62 45 10×2300×1200011 63,64,65,66,67,68 12CrNi3A 13×1900×1200012 69,70,146,147,148,149,150 4Cr13 15×2100×9000二、设计条件机组:双机架串列式可逆机组(二辊可逆轧机粗轧,四辊可逆轧机精轧)。
中厚板压下规程设计

一.制定生产工艺及工艺制度1.生产工艺:选择坯料——原料清理——加热——除鳞——纵轧一道(使宽度接近成品宽度)——转90˚横轧到底——矫直——冷却——表面检查——切边——定尺——表面尺寸形状检查——力学性能试验——标记——入库——发货2.工艺制度:在保证压缩比的条件下,坯料尺寸尽量小。
加热时出炉温度应在1120˚—1150˚,温度不要过高,以免发生过热或过烧现象;用高压水去除表面的氧化铁皮,矫直时选用辊式矫直机矫直,开始冷却温度一般要尽量接近终轧温度,轧后快冷到相变温度以下,冷却速度大多选用5—10˚C或稍高一些。
切边用圆盘式剪切机进行纵剪,然后用飞剪定尺。
二.选择坯料1.根据生产经验和实践,目前生产中厚板选择连铸坯已成为主流,所以选择连铸坯2.坯料尺寸的确定坯。
(1)坯料厚度的确定:根据经验,压缩比在6—10之间较好,本设计取10,由成品厚度h=13mm知H=10h=130mm。
(2)坯料宽度的确定假设先轧两道,压下量分别为20mm和10mm,且设两道轧后其长度等于宽度。
假设轧后金属烧损不计,考虑切头尾,切边。
在我国切头尾一般为500mm—2500mm取Δl=500mm,切边Δb=100mm,由体积不变定理得Bˊ×Lˊ×[H-(20+10)]=(l+2×500)×(b+2×100)×13因为Bˊ=Lˊ所以Bˊ=Lˊ=(9000+2×500)(1900+2×100)×13/[130-(20+10)]=1650mm(3)坯料长度的确定由H,B,Bˊ,Lˊ由体积不变定理得H×B×L=Hˊ×Bˊ×Lˊ得L=1270mm三.变形量分配1.根据经验,中厚板压下量在Δh=12mm左右,这里取Δh=12mm2.分配各道次压下量,计算各道次变形程度,轧件尺寸及轧制道次(1)由H=130mm,h=13mm,取轧制道次n=12(二辊7道四辊五道)(2)第一道,先用展宽轧制把坯料的宽度B轧成b(或接近b)且不考虑长度变化由体积不变定理得B×L×H=B×L×(H-Δh1)得Δh1=17mm则变形程度ε1=Δh/H×100%=13.08%轧后轧件尺寸为113×1900×1270mm同理其余道次压下量分配,变形程度,轧件尺寸如下表所示四.设计变形工具1.设计二辊(1)辊身长度L:由L=bmax+a bmax=1900mm 当b=1000-2500mm a=150-200mm 取a=200mm所以L=1900+200=2100mm(2)辊径尺寸中厚板轧机L/D=2.2-2.8 取L/D=2.6 得D=808mm 取810mm(3)辊颈尺寸查表3-5 取d/D=0.75(轧钢机械邹家祥主编) 得d=608mm取d=600mm辊颈长度l 取d/l=1 得l=600mm(3)辊头设计因为对于中厚板轧机来说轧辊调整行程比较大,倾角在8˚-12˚间所以应选择万向辊头。
中厚板生产工艺流程

中厚板生产工艺流程
(石灰石)(铁矿石)加热炉定尺剪
(烧结)(焦炭)高压水除磷打包
高炉开坯成品
脱硫轧制
精炼炉层流冷却
转炉矫直
板坯连铸机冷床
板坯切边
3月15日,集团唐钢公司700吨加硼中厚板材在京唐港装船
出港,销往韩国。
今年以来,唐钢已有1.75万吨加硼中厚板材登陆韩国市场,价格高于同期内贸300-500元,累计出口创汇458万美元,在增创效益的同时,有力提升了唐钢高端产品在国际市场的知名度。
唐钢加硼中厚板板材主要以SS400和Q235B品种为主,具备较高的创效能力。
加硼板材在生产过程中容易出现边裂问题,直接影响产品的合格率,是保证质量的难点所在。
唐钢中厚板公司积极开展质量攻关,实施全过程的质量控制。
以提升铸坯质量为重点,在强化连铸机的点检、维护的基础上,有针对性地调整连铸机冷却制度,并针对含硼钢生产定制专用保护渣,以满足工艺要求。
在保证质量的前提下,以效益最大化为原则,对成分进行优化设计,成本降低了10元/吨。
对加硼板材的轧制工艺成功调整,有效缩短了生产周期,提高了合同兑现率。
同时,加强售后服务工作,建立了客户信息反馈"快速响应"制度,为生产及质量提升提供指导,充分满足客户需求,使国内外客户对唐钢加硼中厚板材的信任度日益提高。
中厚板生产压下规程设计
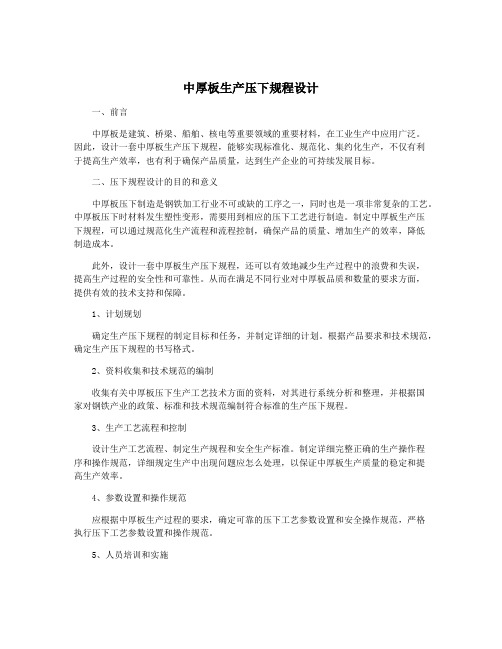
中厚板生产压下规程设计一、前言中厚板是建筑、桥梁、船舶、核电等重要领域的重要材料,在工业生产中应用广泛。
因此,设计一套中厚板生产压下规程,能够实现标准化、规范化、集约化生产,不仅有利于提高生产效率,也有利于确保产品质量,达到生产企业的可持续发展目标。
二、压下规程设计的目的和意义中厚板压下制造是钢铁加工行业不可或缺的工序之一,同时也是一项非常复杂的工艺。
中厚板压下时材料发生塑性变形,需要用到相应的压下工艺进行制造。
制定中厚板生产压下规程,可以通过规范化生产流程和流程控制,确保产品的质量、增加生产的效率,降低制造成本。
此外,设计一套中厚板生产压下规程,还可以有效地减少生产过程中的浪费和失误,提高生产过程的安全性和可靠性。
从而在满足不同行业对中厚板品质和数量的要求方面,提供有效的技术支持和保障。
1、计划规划确定生产压下规程的制定目标和任务,并制定详细的计划。
根据产品要求和技术规范,确定生产压下规程的书写格式。
2、资料收集和技术规范的编制收集有关中厚板压下生产工艺技术方面的资料,对其进行系统分析和整理,并根据国家对钢铁产业的政策、标准和技术规范编制符合标准的生产压下规程。
3、生产工艺流程和控制设计生产工艺流程、制定生产规程和安全生产标准。
制定详细完整正确的生产操作程序和操作规范,详细规定生产中出现问题应怎么处理,以保证中厚板生产质量的稳定和提高生产效率。
4、参数设置和操作规范应根据中厚板生产过程的要求,确定可靠的压下工艺参数设置和安全操作规范,严格执行压下工艺参数设置和操作规范。
5、人员培训和实施对管理人员和操作人员进行生产压下规程培训,宣传和推广生产压下规程;制定全员参加的生产压下规程宣传计划,方便所有员工能够逐步规范化生产压下工艺操作,从而提高工作效益,生产高质量的中厚板。
四、总结本文通过制定中厚板生产压下规程的步骤和意义、可以在工业生产中采用规范化和科学化的方法,规避不良产生,并为保证产品质量和生产效率提供技术支持和保障。
中厚板生产课程设计
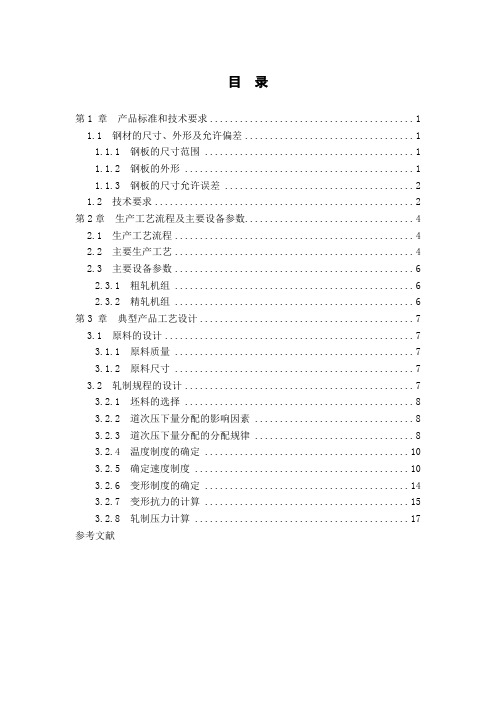
目录第1 章产品标准和技术要求 (1)1.1 钢材的尺寸、外形及允许偏差 (1)1.1.1 钢板的尺寸范围 (1)1.1.2 钢板的外形 (1)1.1.3 钢板的尺寸允许误差 (2)1.2 技术要求 (2)第2章生产工艺流程及主要设备参数 (4)2.1 生产工艺流程 (4)2.2 主要生产工艺 (4)2.3 主要设备参数 (6)2.3.1 粗轧机组 (6)2.3.2 精轧机组 (6)第3 章典型产品工艺设计 (7)3.1 原料的设计 (7)3.1.1 原料质量 (7)3.1.2 原料尺寸 (7)3.2 轧制规程的设计 (7)3.2.1 坯料的选择 (8)3.2.2 道次压下量分配的影响因素 (8)3.2.3 道次压下量分配的分配规律 (8)3.2.4 温度制度的确定 (10)3.2.5 确定速度制度 (10)3.2.6 变形制度的确定 (14)3.2.7 变形抗力的计算 (15)3.2.8 轧制压力计算 (17)参考文献第1 章产品标准和技术要求1.1 钢材的尺寸、外形及允许偏差钢板和钢带的尺寸、外形及允许偏差见国标GBT/709-2006《热轧钢板和钢带的尺寸、外形、重量及允许偏差》如下所示:1.1.1 钢板的尺寸范围钢板公称厚度:4mm~400mm钢板公称宽度:600mm~4800mm钢板公称长度(包括剪切钢板):2000mm~20000mm1.1.2 钢板的外形1.1.2.1 不平度的规定表1.1 剪切钢板的不平度1.1.2.2 镰刀弯的规定表1.2 剪切钢板的镰刀弯1.1.2.3 切斜的规定钢板的切斜应不大于实际宽度的1%1.1.2.4 塔形的规定表1.3 塔形高度1.1.3 钢板的尺寸允许误差1.1.3.1 钢板的厚度允许偏差表1.4 钢板的厚度允许偏差1.1.3.2 钢板的宽度允许偏差表1.5 切边钢板的宽度允许偏差1.1.3.3 钢板的长度允许偏差的规定表1.6 剪切钢板的长度允许偏差1.2 技术要求合金牌号和化学成分可查国标,如碳素结构钢可查GB/T700-2006,低合金结构钢可查GB/T1591,优质碳素结构钢 GB/T 699-1999等另外,技术要求可查找GB 3524-2005《碳素结构钢和低合金结构钢热轧钢带》,GB/T4237-2007《不锈钢热轧钢板和钢带》,GB/T8749-2008《优质碳素结构热轧钢带》等。
中厚板轧制规程设计课程设计

前言板钢轧制制度的确定要求充分发挥设备潜力、提高产量、保证制度,并且操作方便、设备安全。
合理的轧制规程设计必须满足下列原则和要求:在设备允许的条件下尽量提高产量,充分发挥设备潜力提高产量的途径不外是提高压下量、减少轧制道次、确定合理速度规程、缩短轧制周期、提高作业率、合理选择原料增加坯重等。
在保证操作稳定的条件下提高质量,为保证钢板操作的稳定,要求工作辊缝成凸型,而且凸型值愈大操作愈稳定。
压下规程是钢板轧制制度中最基本的核心内容,它直接关系着轧机的产量和产品的质量。
轧制制度中得其他内容如温度制度、速度制度都是以压下制度为核心展开的。
反过来,温度制度、速度制度也影响到压下速度。
目录1·制定生产工艺和工艺制度…………………………………………………………1·1制定生产工艺流程……………………………………………………………1·2制定生产工艺制度……………………………………………………………2·压下规程制定……………………………………………………………………2·1坯料的选择………………………………………………………………………2·2确定轧制方法……………………………………………………………………2·3轧制道次的确定,分配各道次压下量…………………………………………2·4咬入能力的校核…………………………………………………………………3·速度制度确定…………………………………………………………………………4·温度制度确定…………………………………………………………………………5·压下规程表的制定……………………………………………………………………6·各道次变形程度和变形速率的制定…………………………………………………6.1 变形程度的确定…………………………………………………………………6.2 变形速率的确定…………………………………………………………………7·轧制压力的制定…………………………………………………………………………7.1 变形抗力的确定…………………………………………………………………7.2 平面变形抗力的确定……………………………………………………………7.3 计算平均压力p…………………………………………………………………7.4 轧制压力的确定…………………………………………………………………8·电机输出力矩的制定…………………………………………………………8.1 传动力矩的计算………………………………………………………8.2 附加摩擦力矩的确定…………………………………………………8.3 空转力矩的计算………………………………………………………8.4 动力矩的计算…………………………………………………………8.5 电机输出力矩的计算…………………………………………………8.6 电机额定力矩的计算…………………………………………………9·电机的校核…………………………………………………………………9.1 主电机能力的限制…………………………………………………9.2 各机架电机输出力矩等效力矩的计算……………………………9.3 校核各机架的电机输出力矩………………………………………9.4 校核各机架的电机输出力矩………………………………………10·电机输出负荷图……………………………………………………………10.1 速度制度图………………………………………………………10.2 电机负荷图………………………………………………………参考文献…………………………………………………………………………………1·制定生产工艺和工艺制度1·1制定生产工艺选择坯料→原料清理→加热→除磷→纵轧到底→矫直→冷却→表面检查→切边→定尺→表面尺寸形状检查→力学性能检测→标记→入库→发货。
30mm×2100mm×5000mm中厚板生产规程设计

典型产品生产规程设计1 制定生产工艺1.1制定生产工艺选择坯料→原料清理→加热→除磷→横轧两道次(使宽度接近成品宽度)→转90°纵轧到底→矫直→冷却→表面检查→切边→定尺→表面尺寸形状检查→力学性能检测→标记→入库→发货。
1.2制定工艺制度在保证压缩比的情况下,坯料尺寸尽量小,加热时出炉温度应在1120-1300℃,温度不要过高,以免发生过热或过烧现象;用高压水去除表面的氧化铁皮;矫直时采用辊式矫直机矫直,开使冷却温度一般要接近纵轧温度,轧后快冷到相变温度以下,冷却速度大都选用5-10°或稍高一些,切边时用圆盘式剪切机进行纵剪,然后用飞剪定尺。
2 制定压下规程2.1原料设计2.1.1原料的质量按成品钢板的质量和计划成材率计算出原料的质量。
计划成材率指的是在设计原料尺寸时的成材率,计算成材率可以按下面的公式计算。
=()()()()rp twlt t w w l l l s +∆+∆++计划成材率式中t —成品板厚度 W —成品板宽度 L —成品板长度t t +∆—轧制平均厚度 w w +∆—轧制平均宽度rp l —试样长度S —烧损 △t —宽度余量 △w —厚度余量2.1.2原料的尺寸由计算出的原料质量和连铸坯或初轧坯,钢锭的规格范围,考虑到压缩比,横轧时轧机送钢的最小长度,轧机允许最大轧制长度,加热炉允许装入长度等因素,决定原料的厚度、宽度和长度。
在选择原料尺寸时应注意尽可能采用倍尺轧制,即当计算出原料质量小于最大允许原料质量的一半时,应按倍尺轧制考虑选用厚度尺寸。
由于厚板特别是较厚板的订货坯料一般不大,甚至几家用户订货的钢板需要编组在一起进行轧制,因此在选择厚板原料的计算中需要考虑的因素很复杂,而且这些因素互相影响,互相制约。
选择成品尺寸为h ×b ×l=30mm ×2100mm ×5000mm 坯料尺寸:H=220mm B=1600mm取切边为30mm ∆=,切头、尾为50mm δ=,每块板坯轧成n 块成品,n=4 根据体积不变原理有:(b +2∆)×(l ×n +2δ)×h=H ×B ×L 代入数据求得:L=3700mm2.2轧制规程的设计2.2.1坯料的选择中厚板的原料的主体是连铸坯,为了确保成品钢板的综合性能,连铸坯与成品钢板间的最小压缩比保持在6:1以上。
中厚板轧制规程设计方法PPT文档39页

71、既然我已经踏上这条道路,那么,任何东西都不应妨碍我沿着这条路走下去。——康德 72、家庭成为快乐的种子在外也不致成为障碍物但在旅行之际却是夜间的伴侣。——西塞罗 73、坚持意志伟大的事业需要始终不渝的精神。——伏尔泰 74、路漫漫其修道远,吾将上下而求索。——屈原 75、内外相应,言行相称。——韩非
中厚板轧制规程设计方法
51、山气日夕佳,飞鸟相与还。 52、木欣欣以向荣,泉涓涓而始流。
53、富贵非吾愿,帝乡不可期。 54、雄发指危冠,猛气冲长缨。 55、土地平旷,屋舍俨然,有良田美 池桑竹 之属, 阡陌交 通,鸡 犬相闻 。
谢谢你的阅读
中厚板压下规程设计.docx李1.docx123

粗轧 t1=n1/a=20/40=0.5s 精轧 t1=n1/a=30/40=0.75s 纯轧制时间 T=t2+t3+t4 n 1 2 3 4 5 6 7 8 9 10 11 12 13 14 t1 0.50 0.50 0.50 0.50 0.50 0.50 0.50 0.75 0.75 0.75 0.75 0.75 0.75 0.75 t2 0.25 0.25 25 0.25 0.25 0.25 0.25 0.25 0.25
T 2.5 2.5 2.5 6 6 6 6 6 4 4 4 4 4 4
tj
12.32 14.77
二、校核轧机
(1).计算各道次的轧制温度
运用二辊轧机对钢号为 16Mn 的钢坯轧制时,根据所给定的板坯入辊温度为 1160℃.即为 粗轧开轧温度,精轧开轧温度为 960℃。 用恰古诺夫公式:∆t=(t1-400)(Z/h1)/16 (Z 为各道次间隙时间与纯轧制时间之和)
3. 确定轧制速度制度 目前,可逆式中厚板轧机粗轧的轧辊咬入和抛钢转速一般在 10-20r/min 和 1525r/min 范围内选择,精轧机的轧辊咬入和抛出速度一般在 20-60r/min 和 2030r/min 范围内选择。 而且轧制时时低速咬入和抛出。 即二辊轧机上轧制时,取咬入转速 n1=10r/min n2<nh ① 即四辊轧机上轧制时,取咬入转速 n1=20r/min n2<nh ② 现代化轧机启动加速度 a=30-80r/min.s 速度 b=60-120r/min.s ③ 课程下达的机组规格尺寸如下: 粗轧轧辊辊径(工作直径)ø=960mm 支撑辊直径 ø=1600mm 精轧轧辊辊径(工作直径)ø=820mm 支撑辊直径 ø=1550mm 由①、③可知 : 粗轧转速:n1=20rpm n2=30rpm n3=20rpm 精轧转速:n1=30rpm n2=40rpm n3=30rpm a=40r/min.s b=60r/min.s
中厚板厂通用安全操作规程
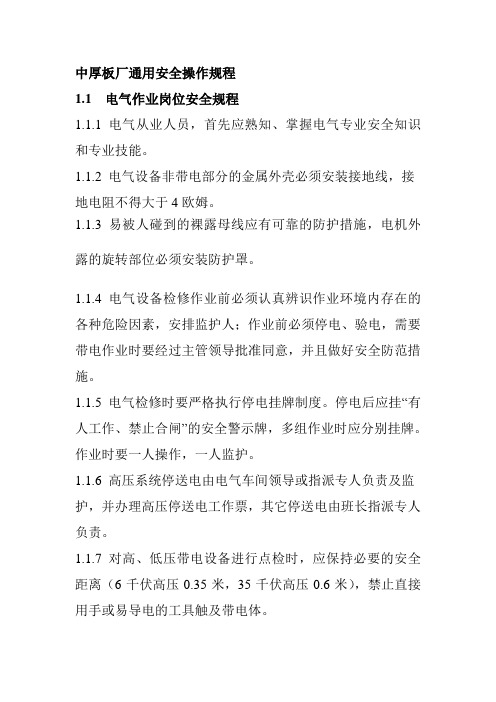
中厚板厂通用安全操作规程1.1 电气作业岗位安全规程1.1.1 电气从业人员,首先应熟知、掌握电气专业安全知识和专业技能。
1.1.2 电气设备非带电部分的金属外壳必须安装接地线,接地电阻不得大于4欧姆。
1.1.3 易被人碰到的裸露母线应有可靠的防护措施,电机外露的旋转部位必须安装防护罩。
1.1.4 电气设备检修作业前必须认真辨识作业环境内存在的各种危险因素,安排监护人;作业前必须停电、验电,需要带电作业时要经过主管领导批准同意,并且做好安全防范措施。
1.1.5 电气检修时要严格执行停电挂牌制度。
停电后应挂“有人工作、禁止合闸”的安全警示牌,多组作业时应分别挂牌。
作业时要一人操作,一人监护。
1.1.6 高压系统停送电由电气车间领导或指派专人负责及监护,并办理高压停送电工作票,其它停送电由班长指派专人负责。
1.1.7 对高、低压带电设备进行点检时,应保持必要的安全距离(6千伏高压0.35米,35千伏高压0.6米),禁止直接用手或易导电的工具触及带电体。
1.1.8 高压电气设备检修时,凭工作票按下列步骤和程序进行:-停电:首先停高压断路器,摇出高压断路器小车;-验电:使用经过试验、安全性能良好的高压验电笔对停电设备进行验电。
-接地装置:确认无电后,合上接地开关,并挂“有人工作、禁止合闸”的安全警示牌;-检修作业人员只能在指定的地点和设备上进行作业,防止发生触电事故;-送电:送电由作业负责人组织,在确认送电安全的情况下进行,要严格执行谁停电、谁送电的原则,检查好开关位置,断开接地开关,送电时先摇进高压断路器小车,后合高压断路器。
1.1.9 对电感、电容性电气设备检修时,停电作业前,一定要对其进行放电,确认无电后方可作业。
1.1.10 严禁带负荷操作(合、分)动力开关(高、低压断路器小车、空气开关)等。
1.1.11 电气设备试车时,应由专人负责联系和指挥。
送电前,首先要对电气设备进行全面检查,经确认无误后方可送电试车,送电时一人操作、一人监护。
- 1、下载文档前请自行甄别文档内容的完整性,平台不提供额外的编辑、内容补充、找答案等附加服务。
- 2、"仅部分预览"的文档,不可在线预览部分如存在完整性等问题,可反馈申请退款(可完整预览的文档不适用该条件!)。
- 3、如文档侵犯您的权益,请联系客服反馈,我们会尽快为您处理(人工客服工作时间:9:00-18:30)。
湖南工业大学课程设计资料袋冶金工程学院(系、部)2012 ~ 2013 学年第 1 学期课程名称金属材料专业课程设计2 指导教师王生朝职称副教授学生姓名xxx 专业金属材料工程班级金属材料093 学号0xxx题目30×2100×5000(Q215)中厚板生产规程设计成绩起止日期2013 年 1 月7 日~2013 年1 月18 日目录清单金属材料专业课程设计2设计说明书30×2100×5000(Q215)中厚板生产规程设计起止日期:2013 年 1 月7 日至2013 年 1 月18 日学生姓名xxx班级金属材料093班学号xxxx成绩指导教师(签字)冶金工程学院2013年1月17 日湖南工业大学课程设计任务书2012 — 2013 学年第 1 学期冶金工程学院金属材料工程专业金属材料093 班级课程名称:金属材料专业课程设计2设计题目:30×2100×5000(Q215)中厚板生产规程设计完成期限:自2013 年 1 月7 日至2013 年 1 月17 日共两周指导教师(签字):王生朝2013年 1 月7 日系主任(签字):王生朝2013年1 月7 日冶金工程学院课程设计指导教师评阅表冶金工程学院课程设计答辩及最终成绩评定表说明:采用百分制计分,最终评定成绩=答辩评分(20%)+指导教师评分(80%),根据综合分值给出相应等级。
目录1 制定生产工艺...................................... 错误!未定义书签。
1.1制定生产工艺................................. 错误!未定义书签。
1.2制定工艺制度................................. 错误!未定义书签。
2 制定压下规程...................................... 错误!未定义书签。
2.1原料设计...................................... 错误!未定义书签。
2.1.1原料的质量 ............................... 错误!未定义书签。
2.1.2原料的尺寸 ............................... 错误!未定义书签。
2.2轧制规程的设计................................ 错误!未定义书签。
2.2.1坯料的选择 ............................... 错误!未定义书签。
2.2.2道次压下量分配的影响因素 ................. 错误!未定义书签。
2.2.3道次压下量的分配规律 ..................... 错误!未定义书签。
2.3轧制速度制度.................................. 错误!未定义书签。
2.3.1轧辊的咬入和抛出转速及轧辊加速度的确定 ... 错误!未定义书签。
2.3.2最大轧制转速及最大轧制速度的确定 ......... 错误!未定义书签。
2.3.3纯轧时间及间隙时间的确定 ................. 错误!未定义书签。
2.4温度制度的确定................................ 错误!未定义书签。
2.5变形制度的确定................................ 错误!未定义书签。
2.5.1变形程度的计算 ........................... 错误!未定义书签。
2.5.2平均变形速度 ............................. 错误!未定义书签。
2.5.3变形抗力的计算 ........................... 错误!未定义书签。
2.6轧制力能参数计算.............................. 错误!未定义书签。
2.6.1轧制压力的计算 ........................... 错误!未定义书签。
2.6.2计算各道传动力矩 ......................... 错误!未定义书签。
典型产品生产规程设计1 制定生产工艺1.1制定生产工艺选择坯料→原料清理→加热→除磷→横轧两道次(使宽度接近成品宽度)→转90°纵轧到底→矫直→冷却→表面检查→切边→定尺→表面尺寸形状检查→力学性能检测→标记→入库→发货。
1.2制定工艺制度在保证压缩比的情况下,坯料尺寸尽量小,加热时出炉温度应在1120-1300℃,温度不要过高,以免发生过热或过烧现象;用高压水去除表面的氧化铁皮;矫直时采用辊式矫直机矫直,开使冷却温度一般要接近纵轧温度,轧后快冷到相变温度以下,冷却速度大都选用5-10°或稍高一些,切边时用圆盘式剪切机进行纵剪,然后用飞剪定尺。
2 制定压下规程2.1原料设计2.1.1原料的质量按成品钢板的质量和计划成材率计算出原料的质量。
计划成材率指的是在设计原料尺寸时的成材率,计算成材率可以按下面的公式计算。
=()()()()rp twlt t w w l l l s +∆+∆++计划成材率式中t —成品板厚度 W —成品板宽度 L —成品板长度t t +∆—轧制平均厚度w w +∆—轧制平均宽度rp l —试样长度S —烧损 △t —宽度余量 △w —厚度余量2.1.2原料的尺寸由计算出的原料质量和连铸坯或初轧坯,钢锭的规格范围,考虑到压缩比,横轧时轧机送钢的最小长度,轧机允许最大轧制长度,加热炉允许装入长度等因素,决定原料的厚度、宽度和长度。
在选择原料尺寸时应注意尽可能采用倍尺轧制,即当计算出原料质量小于最大允许原料质量的一半时,应按倍尺轧制考虑选用厚度尺寸。
由于厚板特别是较厚板的订货坯料一般不大,甚至几家用户订货的钢板需要编组在一起进行轧制,因此在选择厚板原料的计算中需要考虑的因素很复杂,而且这些因素互相影响,互相制约。
选择成品尺寸为h ×b ×l=30mm ×2100mm ×5000mm 坯料尺寸:H=220mm B=1600mm取切边为30mm ∆=,切头、尾为50mm δ=,每块板坯轧成n 块成品,n=4 根据体积不变原理有:(b +2∆)×(l ×n +2δ)×h=H ×B ×L 代入数据求得:L=3700mm2.2轧制规程的设计2.2.1坯料的选择中厚板的原料的主体是连铸坯,为了确保成品钢板的综合性能,连铸坯与成品钢板间的最小压缩比保持在6:1以上。
2.2.2道次压下量分配的影响因素道次压下量分配轧制总道次数应根据从坯料到成品钢板厚度上的压下量和平均压下量,参照类似的轧制规程来确定,对于单机架、总道次数应为奇数,对于双机架应为偶数,并且要考虑两架轧机的轧制节奏要大致平衡。
道次压下量的分配要考虑以下因素: 2.2.2.1咬入条件成形轧制阶段由于板坯的厚度大、温度高、轧制速度低、道次压下量大,所以咬入条件可能成为限制压下量因素。
每道次的压下量应该小于由最大咬入角所确定的最大压下量。
(1cos )(1mas mas h D a D ∆=-=-式中D ——轧辊直径,mm F ——摩擦系数。
二辊和四辊可逆式中厚板轧机的轧制厚度可调,因此可以采用低速咬入,所以实际的最大咬入角可以达到22°到25°。
在这类轧机中厚板,咬入条件将不是限制压下量的主要因素,在实际生产中,热轧钢板时,咬入角一般为15°到22°,低速咬入可取为20°。
2.2.2.2主电机的能力限制新建中厚板轧机的主电机不应成为一个限制最大压下量的因素,主电机能力限制是指电机语序温升和过载能力的直接关系,因此,必须通过设定的道次压下量来计算出轧制力和力矩,然后再来校核电机温升条件过载能力。
2.2.2.3轧辊及辊颈的强度条件中厚板轧制过程中,轧辊辊身的轻度经常是限制压下量的重要因素,尤其是二辊轧机轧制宽厚板时更为突出。
因此道次压下量的分配除考虑咬入条件之外,还要考虑轧辊本身的强度条件。
2.2.3道次压下量的分配规律轧机采用连铸坯作为原料时,除鳞道次之后可以采用大压下量轧制,中间道次为了充分利用钢坯温度高,变形抗力低的优势,采用较大压下量。
然后随着钢坯温度降低,压下量逐渐减少,最后1~2道次为了保持板形和温度精度也要采用较小压下量。
总压下量:000010086.36H hHε∑-=⨯= 粗轧压下量:一般在总压下量的75%以上,取85% 则:=85%=73.41%εε∑⨯二辊 又 00100H h Hε-=⨯二辊二辊 则:=58.5mm h 二辊根据分配规律分配道次压下量如下: 粗轧:第1道次整形:110h mm ∆=第2、3、4道次展宽:225h mm ∆= 315h mm ∆= 47h mm ∆= 第5~9道次延长:530h mm ∆= 625h mm ∆= 720h mm ∆=820h mm ∆= 99.5h mm ∆=精轧:第10~14道次:108h mm ∆= 118h mm ∆= 126h mm ∆= 134h mm ∆= 14 2.5h mm ∆=由上可得:根据体积不变定律,有H×B×L=h×b×l 可得出表格:2.3轧制速度制度在选好速度图的基础上,确定轧制速度制度的内容包括轧辊咬入和抛出速度,计算轧辊最大转速和纯轧时间以及确定间隙时间三项内容。
2.3.1轧辊的咬入和抛出转速及轧辊加速度的确定轧辊咬入和抛出转速确定的原则:获得较短的道次轧制节奏时间,保证轧件顺利咬入,便于操作和适合与电机的合理调速范围。
咬入和抛出不仅会影响到本道次的纯轧时间,而且还会影响到两道次间的间隙时间。
在保持转速曲线下面积相等的原则下,采用高速咬入、抛出会使本道次纯轧时间缩短,而使其间隙时间增加,因此,咬入和抛出转速的选择应兼顾上述两个因素。
目前,可逆式中厚板轧机粗轧机的轧辊轧辊咬入和抛出速度一般在10~20r/min 和15~25r/min 范围内选择。
精轧机的轧辊咬入和抛出速度一般在20~60r/min 和20~30r/min 范围内选择。
在该次设计中粗轧过程:咬入速度20/min y n r = 抛出速度20/min p n r =轧辊加速时的加速度40/a rpm s = 轧辊减速时的加速度60/b rpm s = 精轧过程:咬入速度40/min y n r = 抛出速度20/min p n r =轧辊加速时的加速度40/a rpm s = 轧辊减速时的加速度60/b rpm s = 2.3.2最大轧制转速及最大轧制速度的确定最大转速计算公式为:d n =式中a,b ——轧辊加速与减速时的加速度。