球铁微量元素
球铁450-10的标准成分

球铁450-10的标准成分球墨铸铁450-10是一种高强度、高韧性的铸铁材料,其标准成分具有严格的控制范围。
在全球范围内,球墨铸铁450-10的标准得到了广泛的应用,尤其在汽车、建筑、机械等领域。
本文将对球墨铸铁450-10的标准成分及其应用进行详细解析。
一、球墨铸铁450-10标准的背景介绍球墨铸铁450-10的标准起源于20世纪50年代,经过多年的发展与完善,现已成为全球铸铁行业的重要参考标准。
我国参照国际标准,结合国内生产实际,制定了一系列球墨铸铁450-10的产品标准。
二、球墨铸铁450-10的标准成分概述球墨铸铁450-10的标准成分主要包括:碳(C)含量为2.8%-3.2%,硅(Si)含量为1.8%-3.2%,锰(Mn)含量为0.3%-0.8%,磷(P)含量小于0.1%,硫(S)含量小于0.025%,镁(Mg)含量为0.05%-0.15%,稀土(Re)含量为0.025%-0.1%。
此外,球墨铸铁450-10还含有少量的镍(Ni)、铜(Cu)等元素。
三、球墨铸铁450-10的主要性能特点球墨铸铁450-10具有以下主要性能特点:1.高强度:经过适当的热处理,球墨铸铁450-10的抗拉强度可达到450MPa以上。
2.高韧性:球墨铸铁450-10具有良好的韧性和延展性,其冲击韧度AK值大于6J/cm。
3.良好的耐磨性:球墨铸铁450-10的耐磨性优于普通铸铁,可提高零件的使用寿命。
4.良好的铸造性能:球墨铸铁450-10的流动性好,收缩率低,可获得复杂零件的铸件。
四、球墨铸铁450-10的应用领域球墨铸铁450-10广泛应用于以下领域:1.汽车:球墨铸铁450-10适用于制造汽车发动机、变速器、车架等关键部件。
2.建筑:球墨铸铁450-10用于制造各类建筑五金件、管道、水泵等。
3.机械:球墨铸铁450-10适用于制造重型机械、工程机械、石油化工设备等。
4.电力:球墨铸铁450-10用于制造发电厂、变电站等高压电力设备。
微量元素偏析对厚大断面球铁石墨形态的影响
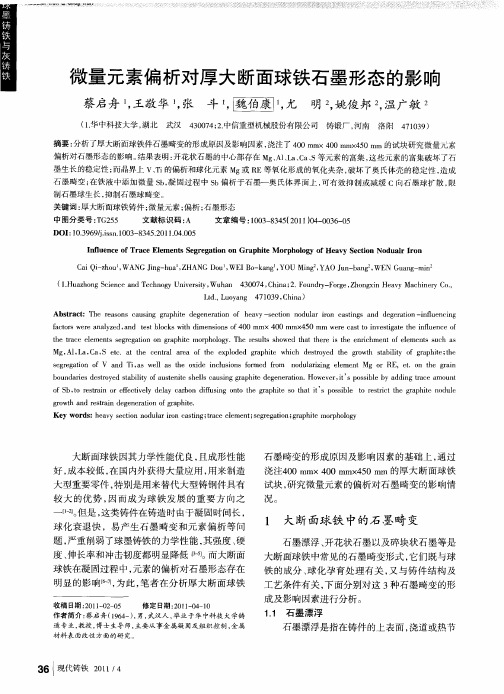
C i izo WA G J g h a,H N o WE o kn Y U Mig, AOJn b n2WE un — i a Q—hu, N n— u A G D u, I — a g, O n Y u— ag, N G a g m n i Z B
( . u z o gS i c n e h o yU ies y Wu a 4 0 7 , hn ; . o n r— og , h n x e v c ieyCo. 1 a h n c n ea dT c n g nvri , h n 3 0 4 C i 2 F u dy F re Z o g i H a yMa hn r H e t a n .
墨生长的稳定性 ; 晶界 上 V、i 而 T 的偏 析和球化元 素 M g或 R E等氧化形成的氧化夹杂 , 破坏 了奥氏体壳 的稳 定性 , 造成 石 墨畸变 ; 在铁液 中添加微量 s , 固过程 中 s 析于石墨一 奥氏体界面上 , b凝 b偏 可有效抑制 或减缓 C向石墨球扩 散 , 限 制石墨球生长 , 抑制石墨球畸变。 关键词 : 大断 面球铁铸件 ; 厚 微量元素 ; 偏析 ; 墨形态 石
一
ห้องสมุดไป่ตู้.
? _ ∞ l
_ t
一
j 譬。 t
罅l 冀 。
微 量元素偏析对厚大 断面球铁石 墨形态 的影 响
蔡启舟 , 敬华1 斗 , 王 , 张 团
( . 中科技大学 , 1 华 湖北 武汉
, 明z 俊邦z 广敏z 尤 , 姚 , 温
洛 阳 4 13 ) 7 0 9
b un re sr y d sa lt fa se ie s el a i ap ie d e r to .H o v r i ’ si l y a i r c m o t o da isde to e tbiiyo u t n t h lsc usnggr h t eg ne ai n we e ,t Spo sb e b ddng ta e a un
球铁的金相组织
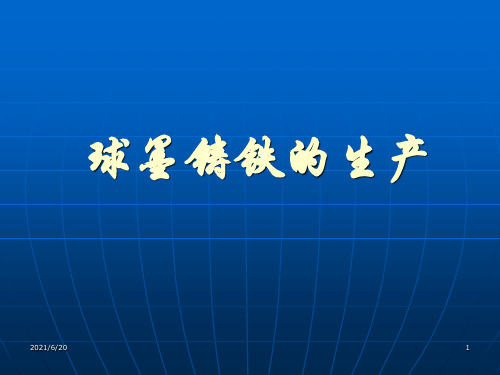
对于退火铁素体球铁,允许的Si、Mn含量范围较宽,Si的质量 分数可从2.0%到2.7%,对原材料的纯净度(干扰球化元素含 量)要求可适当放宽。
最小值 400(40.80) 250(25.50) 400(40.80) 250(25.50) 450(45.90) 310(31.60) 500(51.00) 320(32.65) 600(61.20) 370(37.75) 700(71.40) 420(42.85) 800(81.60) 480(48.98) 900(91.80) 600(61.20)
2021/6/20
13
(3) 磷
磷在球墨铸铁中有严重的偏析倾向,易在晶界处形成磷共 晶,严重降低球墨铸铁的韧性。
磷还增大球墨铸铁的缩松倾向。 当要求球墨铸铁有高韧性时,应将含磷量控制
0.04%~0.06%以下,对于寒冷地区使用的铸件,宜采 用下限的含磷量。 如球墨铸铁中有钼存在时,更应注意控制磷的含量,因此 时易在晶界处形成脆性的磷钼四元化合物。
9
7
铸态 3.5~3. 2.5~3. ≤0.3
9
0
低温用 3.5~3. 1.4~2. ≤0.2
9
0
2021/6/20
P
≤0.0 7
≤0.0 7
≤0.0 4
S
≤0.0 2
≤0.0 2
≤0.0 1
Mg
0.03~0. 06
0.03~0. 06
0.04~0. 06
RE 0.02~0.
04 0.02~0.
04 —
稀土元素如铈、镧、钍、钇等皆有不同程度的中和干扰球化元素的 作用,加入RE0.01%~0.02%即能中和这些元素的有害作用。稀土 元素的存在可放宽反球化元素的最大允许量。
知识篇——球铁中的Mg含量
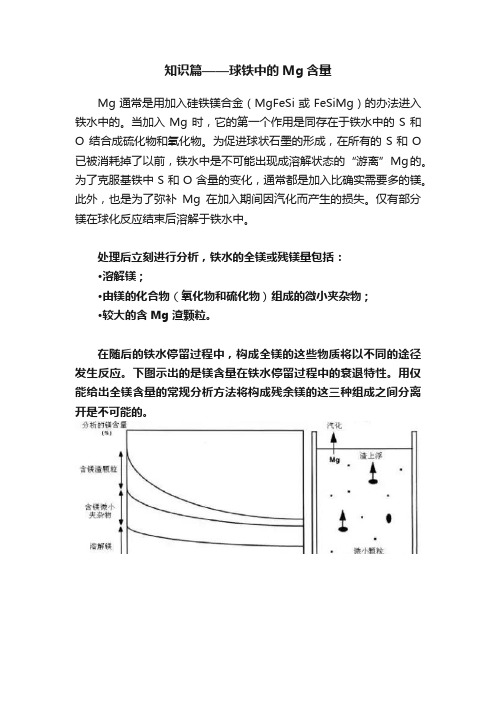
知识篇——球铁中的Mg含量Mg通常是用加入硅铁镁合金(MgFeSi或FeSiMg)的办法进入铁水中的。
当加入Mg时,它的第一个作用是同存在于铁水中的S和O 结合成硫化物和氧化物。
为促进球状石墨的形成,在所有的S和O 已被消耗掉了以前,铁水中是不可能出现成溶解状态的“游离”Mg的。
为了克服基铁中S和O含量的变化,通常都是加入比确实需要多的镁。
此外,也是为了弥补Mg在加入期间因汽化而产生的损失。
仅有部分镁在球化反应结束后溶解于铁水中。
处理后立刻进行分析,铁水的全镁或残镁量包括:·溶解镁;·由镁的化合物(氧化物和硫化物)组成的微小夹杂物;·较大的含Mg渣颗粒。
在随后的铁水停留过程中,构成全镁的这些物质将以不同的途径发生反应。
下图示出的是镁含量在铁水停留过程中的衰退特性。
用仅能给出全镁含量的常规分析方法将构成残余镁的这三种组成之间分离开是不可能的。
石墨球化率随时间衰退的示意图。
第二次加入孕育剂可再次获得充分球化的石墨组织,尽管分析镁含量还在继续下降Mg含量和Mg衰退随停留时间变化的重要特点·分球铁析出来的总残镁量不是溶解镁含量;·Mg含量随处理过的铁水的停留时间的衰退可能是渣分离、夹杂物上浮和溶解镁的汽化损失的结果。
在有些情况下,Mg衰退可以对铁水的洁净度和免除渣的夹带产生好的作用,这是由于有害的渣粒将随铁水的停留而上浮到熔池表面,并因此可以被去除;·采用常规的分析方法只能分析出试样中的全镁含量(渣+微小夹杂物+溶解Mg);·已经表明:铁水溶解镁随停留时间的损失一般都很小,常常归罪于Mg衰退的球状石墨组织的恶化实际上是孕育衰退造成的。
通过最后加入少量孕育剂常常可以再次获得充分球化的石墨组织。
铁水的取样从铁水取样时,通常是用取样勺将铁水浇入激冷铸模中,这样就可以保证供分析用的试样是同一标样的。
从铁水中得到一个有代表性的试样并不是如此简单的,因为就微量元素和合金化元素的浓度而言,从其取样的大多数铁水是不均匀的。
微量元素铋对厚断面球铁组织及性能的影响

龙源期刊网 微量元素铋对厚断面球铁组织及性能的影响作者:高文理岑鸽等来源:《湖南大学学报·自然科学版》2013年第06期摘要:通过添加不同质量分数的微量Bi和调整残余稀土量,研究其对厚断面球铁组织、抗拉强度、伸长率、硬度和-40 ℃低温冲击韧度的影响.结果表明,对于180 mm × 180 mm ×200 mm试块,添加0.012%Bi可以明显消除其碎块石墨;而对于250 mm × 250 mm × 300 mm 试块,加Bi只能在一定程度上抑制碎块石墨产生,随着Bi量的增加,其抑制作用呈先增强后减弱的趋势,加入Bi的质量分数最佳值为0.010%~0.012%,此时抗拉强度达337 MPa,伸长率为10.4%,-40 ℃低温冲击功可达到10.5 J.适当降低残余稀土量,调整wRE /wBi加=1.3~1.5,可以进一步抑制碎块石墨和改善综合力学性能.关键词:球墨铸铁;铋;微观组织;力学性能中图分类号:TG255 文献标识码:A厚断面球墨铸铁(简称球铁)由于冷却速度缓慢,共晶凝固时间长,易导致球化衰退和孕育衰退,使得铸件中尤其是厚壁中心或热节处出现球化不良、石墨畸变、球数减少、球径增大、成分偏析、晶间碳化物增多及缩松缩孔等等缺陷,特别是碎块石墨的出现,严重影响了铸件的综合性能[1-3].国内外有众多研究者发现,当球铁中某些微量元素(如Bi)与稀土元素以适当比例共存时,则会消除变异石墨,改善球铁性能[2,4-5].但该技术还不够成熟,国内多数铸造企业又没有掌握关键技术,如果直接用于生产,则会存在一定风险.本文制定了严格而合适的化学成分和实验工艺,通过添加不同质量分数的微量Bi和调整残余稀土量,研究了其对球铁心部碎块石墨的抑制作用以及对球铁组织和综合力学性能的影响,从而为获得更好的球铁组织和性能提供依据,为同行提供参考.1实验方法11化学成分原铁液纯净度要高,尽可能排除杂质等干扰因素.遵循高碳,低硅,低锰、磷、硫的原则[6],球铁主要化学成分范围见表1,其中碳质量分数为原铁水成分要求,其余为处理后要求.采用300 kg 中频电炉熔炼,树脂砂造型,原材料采用本溪Q10生铁和废钢混合配比.熔炼过程中通过浇注白口试样进行光谱分析,并调整原铁液C和Si成分分别为:C 3.70±0.05%,Si。
高质量球墨铸铁微量元素和合金元素的选择与控制
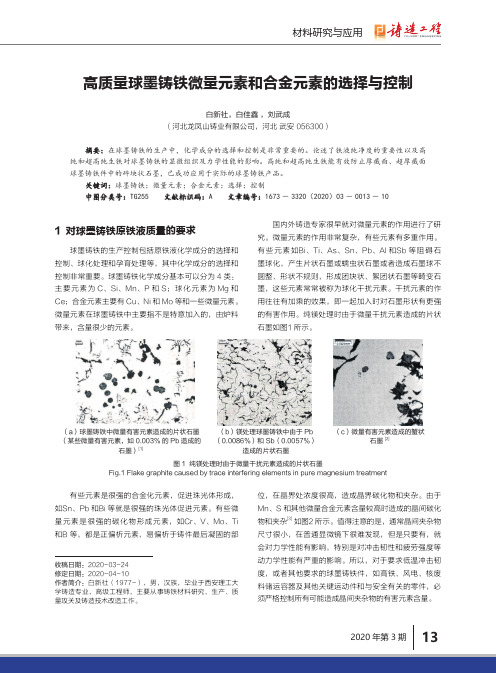
高质量球墨铸铁微量元素和合金元素的选择与控制1 对球墨铸铁原铁液质量的要求球墨铸铁的生产控制包括原铁液化学成分的选择和控制、球化处理和孕育处理等,其中化学成分的选择和控制非常重要。
球墨铸铁化学成分基本可以分为4类:主要元素为C、Si、Mn、P和S;球化元素为Mg和Ce;合金元素主要有Cu、Ni和Mo等和一些微量元素。
微量元素在球墨铸铁中主要指不是特意加入的,由炉料带来,含量很少的元素。
国内外铸造专家很早就对微量元素的作用进行了研究。
微量元素的作用非常复杂,有些元素有多重作用。
有些元素如Bi、Ti、As、Sn、Pb、Al和Sb等阻碍石墨球化,产生片状石墨或蠕虫状石墨或者造成石墨球不圆整、形状不规则,形成团块状、絮团状石墨等畸变石墨,这些元素常常被称为球化干扰元素。
干扰元素的作用往往有加乘的效果,即一起加入时对石墨形状有更强的有害作用。
纯镁处理时由于微量干扰元素造成的片状石墨如图1所示。
有些元素是很强的合金化元素,促进珠光体形成,如Sn、Pb和Bi等就是很强的珠光体促进元素。
有些微量元素是很强的碳化物形成元素,如Cr、V、Mo、Ti和B 等,都是正偏析元素,易偏析于铸件最后凝固的部位,在晶界处浓度很高,造成晶界碳化物和夹杂。
由于Mn、S 和其他微量合金元素含量较高时造成的晶间碳化物和夹杂[3]如图2所示。
值得注意的是,通常晶间夹杂物尺寸很小,在普通显微镜下很难发现,但是只要有,就会对力学性能有影响,特别是对冲击韧性和疲劳强度等动力学性能有严重的影响。
所以,对于要求低温冲击韧度,或者其他要求的球墨铸铁件,如高铁、风电、核废料储运容器及其他关键运动件和与安全有关的零件,必须严格控制所有可能造成晶间夹杂物的有害元素含量。
白新社,白佳鑫 ,刘武成(河北龙凤山铸业有限公司,河北 武安 056300)摘要:摘要:在球墨铸铁的生产中,化学成分的选择和控制是非常重要的。
论述了铁液纯净度的重要性以及高纯和超高纯生铁对球墨铸铁的显微组织及力学性能的影响。
各种少量-微量元素在铸铁中作用
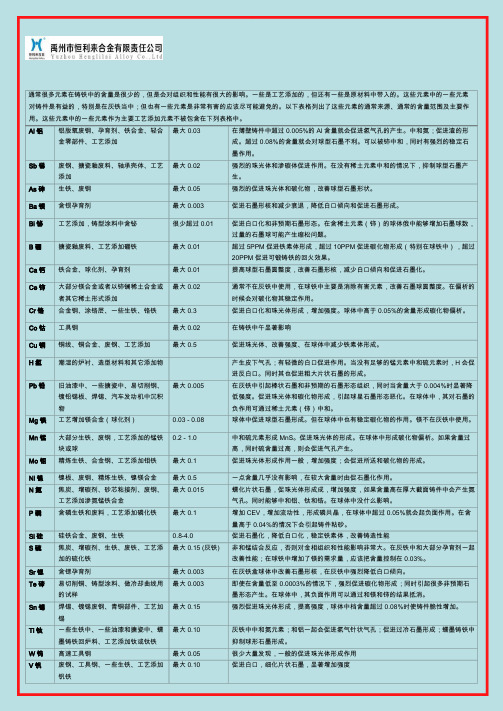
通常很多元素在铸铁中的含量是很少的,但是会对组织和性能有很大的影响。
一些是工艺添加的,但还有一些是原材料中带入的。
这些元素中的一些元素对铸件是有益的,特别是在灰铁当中;但也有一些元素是非常有害的应该尽可能避免的。
以下表格列出了这些元素的通常来源、通常的含量范围及主要作用。
这些元素中的一些元素作为主要工艺添加元素不被包含在下列表格中。
Al铝铝脱氧废钢、孕育剂、铁合金、轻合金零部件、工艺添加最大 0.03 在薄壁铸件中超过0.005%的Al含量就会促进氢气孔的产生。
中和氮;促进渣的形成。
超过0.08%的含量就会对球型石墨不利。
可以被铈中和,同时有强烈的稳定石墨作用。
Sb锑废钢、搪瓷釉废料、轴承壳体、工艺添加最大0.02 强烈的珠光体和渗碳体促进作用。
在没有稀土元素中和的情况下,抑制球型石墨产生。
As砷生铁、废钢最大0.05 强烈的促进珠光体和碳化物,改善球型石墨形状。
Ba钡含钡孕育剂最大0.003 促进石墨形核和减少衰退,降低白口倾向和促进石墨形成。
Bi铋工艺添加,铸型涂料中含铋很少超过0.01 促进白口化和非预期石墨形态。
在含稀土元素(铈)的球体俄中能够增加石墨球数,过量的石墨球可能产生缩松问题。
B硼搪瓷釉废料、工艺添加硼铁最大0.01 超过5PPM促进铁素体形成,超过10PPM促进碳化物形成(特别在球铁中),超过20PPM促进可锻铸铁的回火效果。
Ca钙铁合金、球化剂、孕育剂最大0.01 提高球型石墨圆整度,改善石墨形核,减少白口倾向和促进石墨化。
Ce铈大部分镁合金或者以铈镧稀土合金或者其它稀土形式添加最大0.02 通常不在灰铁中使用,在球铁中主要是消除有害元素,改善石墨球圆整度。
在偏析的时候会对碳化物其稳定作用。
Cr铬合金钢、涂铬层、一些生铁、铬铁最大0.3 促进白口化和珠光体形成,增加强度。
球体中高于0.05%的含量形成碳化物偏析。
Co钴工具钢最大0.02 在铸铁中午显著影响Cu铜铜线、铜合金、废钢、工艺添加最大0.5 促进珠光体、改善强度、在球体中减少铁素体形成。
球铁的金相组织
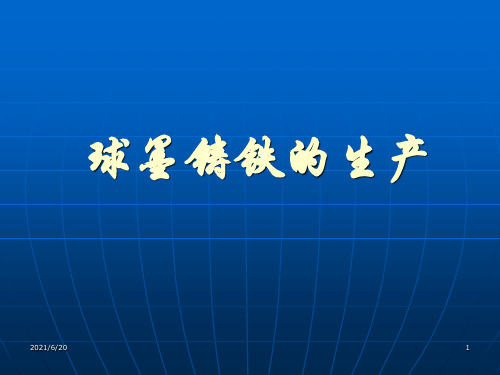
2021/6/20
10
1.1基本元素
(1) 碳和硅
由于球状石墨对基体的削弱作用很小,故球墨铸铁 中石墨数量多少,对力学性能的影响不显著,当含碳量在 3.2%~3.8%范围内变化时,实际上对球墨铸铁的力学性 能无明显影响。确定球墨铸铁的含碳量时,主要从保证铸 造性能考虑,为此将碳当量选择在共晶成分左右。
(5) 锑
锑是强烈稳定珠光体元素,当其含量在 0.006%~0.008%时,就能有效的提高球铁基体中珠光 体的百分率。
在生产铸态珠光体球铁时,用微量锑代替铜,在经济上更 为合理。
但锑有干扰石墨球化的作用,当Sb>0.01%时,即会明 显地使石墨形状恶化,故对球墨铸铁的含锑量应严格控制 在0.006%~0.008%以下,使用时还应注意积累问题。
(1)球化级别1~6级,一般要求1~3级。 (2)石墨大小3~8级,一般要求石墨直径6~8级。 (3)珠光体的粗细和数量。 ➢ 珠光体粗细度分为:粗片状珠光体、片状珠光体、细片状珠光体。 ➢ 一般要求为细片状珠光体。 ➢ 对于高韧性球铁,珠光体要少,特别是QT400-18,不允许有珠光体,
或其量<1%,其余为铁素体。 (4)高韧性球铁中不允许出现磷共晶和碳化物。
球铁力学性能的验收依据,主要为抗拉强度(σb)和伸长 率(δ),如用户有特殊需要,冲击韧性、屈服点、硬度 也可作为附加的验收依据,必要时还应对金相组织进行检 验。
在特殊情况下,经供需双方同意,允许根据铸件本体所测 得的硬度值规定球铁的硬度牌号,见GB1348-88。
2021/6/20
3
2.金相组织
2021/6/20
18
(3) 镍
镍常作为强化元素使用,其作用和铜相似。在国内由于其 价格较贵,因而用得较少。
球铁的主要微量元素,它们的作用是什么?
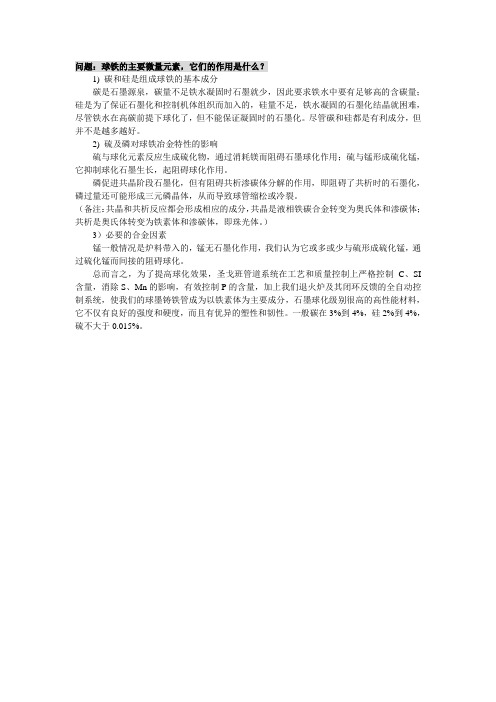
问题:球铁的主要微量元素,它们的作用是什么?
1) 碳和硅是组成球铁的基本成分
碳是石墨源泉,碳量不足铁水凝固时石墨就少,因此要求铁水中要有足够高的含碳量;硅是为了保证石墨化和控制机体组织而加入的,硅量不足,铁水凝固的石墨化结晶就困难,尽管铁水在高碳前提下球化了,但不能保证凝固时的石墨化。
尽管碳和硅都是有利成分,但并不是越多越好。
2) 硫及磷对球铁冶金特性的影响
硫与球化元素反应生成硫化物,通过消耗镁而阻碍石墨球化作用;硫与锰形成硫化锰,它抑制球化石墨生长,起阻碍球化作用。
磷促进共晶阶段石墨化,但有阻碍共析渗碳体分解的作用,即阻碍了共析时的石墨化,磷过量还可能形成三元磷晶体,从而导致球管缩松或冷裂。
(备注:共晶和共析反应都会形成相应的成分,共晶是液相铁碳合金转变为奥氏体和渗碳体;共析是奥氏体转变为铁素体和渗碳体,即珠光体。
)
3)必要的合金因素
锰一般情况是炉料带入的,锰无石墨化作用,我们认为它或多或少与硫形成硫化锰,通过硫化锰而间接的阻碍球化。
总而言之,为了提高球化效果,圣戈班管道系统在工艺和质量控制上严格控制C、SI 含量,消除S、Mn的影响,有效控制P的含量,加上我们退火炉及其闭环反馈的全自动控制系统,使我们的球墨铸铁管成为以铁素体为主要成分,石墨球化级别很高的高性能材料,它不仅有良好的强度和硬度,而且有优异的塑性和韧性。
一般碳在3%到4%,硅2%到4%,硫不大于0.015%。
X射线光谱法分析球铁微量元素的探讨
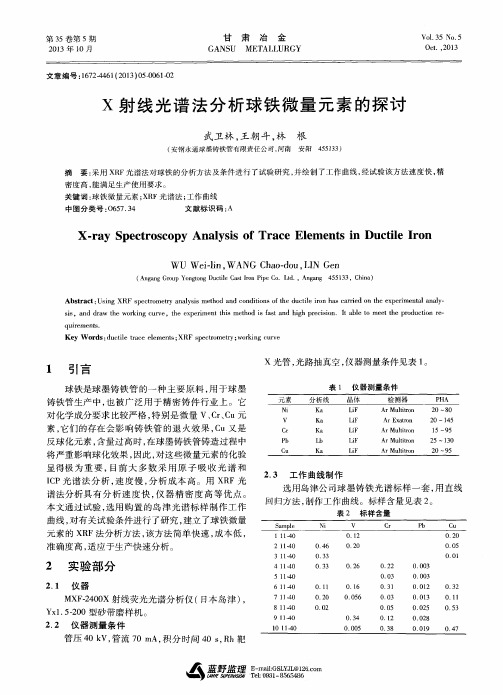
x光管, 光路抽真空, 仪器测量条件见表 。
表1 仪 器 测 量 条 件
显 得极 为 重 要 , 目前 大 多 数 采 用 原 子 吸 收 光 谱 和 I C P光 谱 法 分 析 , 速度慢 , 分 析 成 本 高 。用 X R F光 谱 法 分析 具 有 分 析 速 度 快 , 仪器 精密度高 等优点。 本 文 通过试 验 , 选 用 购 置 的 岛 津光 谱 标 样 制 作 工 作 曲线 , 对有 关 试验 条件 进行 了研 究 , 建立 了球 铁微 量
E- ma i I : GS L YJ L @1 2 6 1 c 0 I l I ㈣ 8 6
—
6 2 2 . 4 样 品分析 测量
甘
肃
冶
金
表4 准 确 度 试 验 结 果/w%
第3 5卷
取 铁水 于制样 磨 具 中 , 制成 蘑菇 状分 析样 片 , 待 冷 却后 在砂 带磨 样 机上 打磨 成 表 面 光 洁平 整 、 纹 路
第3 5卷第 5期
2 0 1 3年 1 0月
甘
肃
冶
金
Vo 1 . 3 5 No . 5
Oc t .. 201 3
Байду номын сангаас
GANS U METAL LURGY
文章编号 : 1 6 7 2 4 4 6 1 ( 2 0 1 3 ) 0 5 - 0 0 6 1 - 0 2
X射 线光 谱 法 分 析 球 铁 微 量 元 素 的探 讨
一
致 的样片 , 然后 用 仪 器 在设 定 条 件 下 进 行 强 度 测
量, 最后 在工 作 曲线上 求 出对应 各元 素含 量 。
球铁800化学成分

球铁800化学成分全文共四篇示例,供读者参考第一篇示例:球铁800是石墨球铁的一种,其主要成分为铁、碳、硅和锰等元素。
球铁800的化学成分是经过精心设计和调配的,以满足特定的使用要求。
球铁800具有优异的机械性能和耐磨性,适用于各种高要求的工程应用。
铁是球铁800的主要成分,占比超过90%,铁是球铁的基础元素,它提供了球铁800的强度和韧性。
碳是另一个重要的成分,通常占比在2%-4%之间,碳的含量影响球铁的硬度和磨损性能。
硅是球铁800中的另一种重要元素,硅的含量通常在1%-3%之间,硅可以提高球铁的热稳定性和耐热性。
锰是球铁800的另一种关键元素,锰的含量通常在0.5%-1%之间,锰可以提高球铁的硬度和抗疲劳性能。
除了上述主要成分外,球铁800还含有少量的其他元素,如磷、硫、铬等。
磷和硫是常见的杂质元素,它们的含量会影响球铁的冷脆性和疲劳性能。
铬是一种有益的合金元素,它可以提高球铁的耐磨性和抗腐蚀性能。
球铁800的化学成分是经过精确设计和控制的,以确保其符合特定的标准和要求。
制造球铁800的关键是精确控制各种元素的含量和比例,以达到所需的性能。
球铁800通常通过熔炼、浇铸和热处理等工艺来制备,确保其结构和性能达到设计要求。
在工程应用中,球铁800具有一些显著的优点。
球铁800具有优异的机械性能,包括高强度、高硬度和良好的韧性。
球铁800具有优异的耐磨性能,适用于各种高磨损的环境。
球铁800还具有良好的耐热性和热稳定性,适用于高温环境下的使用。
球铁800是一种优秀的工程材料,其化学成分经过精心设计和调配,具有优异的机械性能和耐磨性。
在各种高要求的工程应用中,球铁800都能够发挥出色的性能,受到广泛的应用和认可。
在未来,随着技术的不断发展和进步,球铁800也将继续不断优化和升级,为更广泛的应用领域提供更好的解决方案。
第二篇示例:球铁800是一种热处理球化铁的品种,根据化学成分的不同可以分为球铁800-2和球铁800-3。
微量元素对球铁影响

组织
力学性能
使用性能
工艺性能
耐磨性
耐热性
耐蚀性
可切削性
铸造性能
C
3.5-3.8%
4.0-4.3%缩松、缩孔倾向最小;
含碳量过高,降低缩松的作用不明显,反而会出现石墨漂浮。
Ni
0.5~2.0常与Cr、Cu、Mo合用
促进石墨化,消除白口和游离渗碳体;细化石墨;稳定且细化珠光体,促成索氏体
提高强度、硬度、冲击韧度
显著提高强度、硬度、冲击韧度、疲劳强度、高温(<550℃)性能,大断面性能
显著提高
提高
稍改善
改善
减少收缩,改善热处理性能
V
0.1~0.4常与Ti合加
阻碍石墨化;细化、均化石墨;细化珠光体;强烈促成碳化物;消除大断面的铁素体合枝晶组织
少量V,可显著提高强度、硬度,提高冲击韧性
显著提高。与Cu、Ti
合用更好
提高
提高
提高
优于同硬度和强度的非合金铸铁
减少缩松,提高铸件致密性。断面壁厚差大时尤有效
Cu
0.5~2.0常与Ni、Cr、Mo、V合用
弱石墨化;细化且珠光体和石墨;减少薄断面白口,改善大断面组织敏感性
提高强度、硬度、韧度。低碳铸铁尤显著
提高
提高
提高
尤耐弱酸和大气腐蚀
改善
改善流动性提高铸件致密度
Cr
0.2~1.0常与Cu、Mo、Ni合用
强阻碍石墨化,促成碳化物;细化石墨;细化且稳定珠光体;促成白口
提高强度、硬度;Cr约>0.5%,降低塑性、韧性显著
提高,与Cu、Mo、Ni合用更好
提高。铬越多越显著
提高。铬越多越显著
降低。少量影响不大
球铁
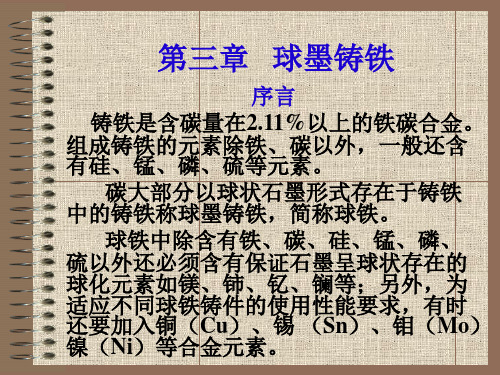
• 在球铁生产中遇到一些微量元素和合金元素是 起干扰球化作用的。归纳起来这些元素及其在 球铁中的临界含量见表3.2。 • 消耗型:硫(S)氧(O)硒(Se)碲(Te)是
在球化处理时优先与球化元素起反应,消耗一部分球 化剂,剩余部分球化剂才能去起到球化作用,促成蠕 虫状、片状石墨; 晶界偏析型:钛(Ti)砷(As)铝(Al)锑(Sb)锡 (Sn)等元素是富集在共晶团边界,形成畸变石墨; 混合型:铅(Pb)铋(Bi)镉(Cd)锌(Zn)是即消 耗球化剂,又可产生共晶团晶界偏析。 值得关注的是,上述干扰元素(除钛以外)对采用 高度净化的铁水浇注打断面球铁铸件时,在有适量稀 土的情况下,适量加入反而起到圆整石墨防止畸变石 墨、增加球墨数量的好作用。加入量限于: 锑0.002~0.01%、铋≤0.01%、铅≤0.01%。千万不能过 量。 另外,国外已开发应用了含氧硫总量0.1%的氧硫孕育 剂,用于厚大球铁铸件生产获得良好效果。
球铁与其他材料机械性能对比表
材料 类别
铸态铁素体 球铁 铸态珠光体 球铁 正火珠光体 球铁
抗拉强度 σb MPa
400~600 600~800 600~900
屈服强度 延伸率 硬度 冲击韧性 σsMPa (%) (HB)(J/cm2)
280~420 320~420 420~600 8~22 2~4 2~8 130~ 190 180~ 230 230~ 302 5~15 1.5~3.5 2~4
第一节 球墨铸铁的组织和性能
一、球墨铸铁的石墨组织及球化剂 1. 石墨形成机理
• 石墨是碳(C)的一种同素异 构体,属六方晶系。石墨的晶 体结构如图3.1。石墨的密度为 2.25g/cm3,比重比铁轻得多, 铁的密度是7.68g/cm3,所以铸 铁凝固时析出石墨会使铸件体 积膨胀。石墨晶体中的碳原子 是层状排列的,在同层原子之 间是以共价键结合,其结合力 较强;而层与层之间是以极性 键结合,其结合力较弱。因此, 石墨极易分层剥落,强度极低。 由于石墨具有这样的结构特点, 因此在铁液中长大时应该是沿 基面择优生长,最后形成片状。
球铁典型铸造缺陷极其防止

球铁典型铸造缺陷极其防止1、球化不良与球化衰退(1)球化不良:球化不良是指球化处理没有达到预期的球化效果。
球化不良的金相组织为:集中分布的厚片状石墨和少量球状、团状石墨;有时还有水草状石墨。
随着球化不良的程度的加剧,集中分布的厚片状石墨的数量逐渐增多、面积增大,球化不良将使球墨铸铁的力学性能达不到响应牌号要求的指标。
关于球化不良产生的原因极其防止措施分述如下:1、原铁液含硫高 硫是主要反球化元素,含硫高会严重影响球化,一般原铁液的硫的质量分数要小于等于0.06%。
为保证球化,当原铁液含硫量偏高时,必须响应地提高球化剂的加入量,含硫量越高,则球化剂的消耗量也越多。
2、球化元素残留量低 为使石墨球化良好,球铁中必须含有一定量的残余镁和稀土,在我国现今生产条件下,残余镁量的质量分数不得小于0.03%,残余稀土量的质量分数不得小于0.02%。
3、铁液氧化 原材料中铁锈、污染以及铁液在熔化与过热中的氧化,导致铁液中的FeO 含量增多,因而在球化过程中要消耗更多的镁,致使残余镁量过低。
4、炉料含有反球化元素 当反球化元素超出允许范围时,就会影响球化效果,要注意废钢中可能含有钛,还要注意电镀材料、铝销、铅系涂料进入冲天炉。
稀土有中和反球化元素的能力,根据我国原生铁中含有较多的反球化元素的情况,我国球铁中的残余稀土量比国外的要多。
5、 孕育效果差 由于孕育效果差,或者孕育衰退,均会造成石墨球数量少,使得石墨球不圆整。
6、型砂水分高、含硫量高 由于界面反应,铁液中的镁与铸型表面中的氧、硫发生作用,致使铸件表面的残余镁量不足,形成一薄层的片状石墨。
解决的措施就是提高残余镁量,减少型砂含水量,型砂硫的质量分数应小于0.1%,或采用能获得还原性气氛的涂料。
在使用含硫硬化剂的树脂砂铸型中,可采用含有MgO 、CaO 的涂料。
2、球化衰退球化衰退的特点时:炉前球化良好,在铸件上球化不好;或者同一浇包的铁液,先浇注的铸件球化良好,后浇注的铸件球化不好。
微量铋、锑元素对大断面球墨铸铁的影响

收稿日期:2013-08-28稿件编号:1308-326作者简介:曹伟康(1962-),男,高级技师,从事铸造生产工作1概况随着球墨铸铁件的广泛应用,对球铁的理化性能要求也越来越高,除常规的强度、硬度、球化等级等指标外,也提出了如单位面积的石墨球个数、单一基体的纯净度、低温冲击等特殊性能要求。
而其中的大断面球墨铸铁件,由于生产成本低廉,可以替代以往的钢件或铜件,使得其在各个领域的应用越来越广泛。
但这类球铁铸件,由于冷却缓慢,凝固时间长,若存在过量干扰元素或缺乏石墨核心时,在其心部极易出现球化和孕育的衰退现象,使球铁组织中出现团片状、蠕虫状、碎块状等变异石墨,导致球铁力学性能下降。
通过研究,在实际生产中以适当的比例加入某些微量元素(如Bi 、Sb 、Pb 、Sn ),在采用稀土镁硅合金作为球化剂时,控制稀土元素和微量铋、锑元素的比例,就可消除变异石墨,改善基体组织,满足一些特殊性能要求。
关于球铁石墨变异的原因,有很多说法,其中比较一致的看法是:主要在共晶凝固初期,缺乏石墨的异质形核核心所致。
而含有稀土和Bi 、Sb 的高熔点复杂化合物能作为石墨的结晶核心,数量众多,且比只含有稀土元素的核心更加稳定,如此就能促使石墨球数增加,形状更加圆整,变异石墨基本消失。
通过实践,球铁中加入Bi 、Sb 元素,含量控制在某一范围内时,表现出上述的有益作用,而过量时,则体现出对石墨形态的危害。
同时研究也表明,铁液中适量的稀土元素不仅能大大扩大Bi 、Sb 元素的加入范围,而且还和Bi 、Sb 元素共同产生作用,使得效果比单一加入Bi 、Sb 元素更好,但稀土元素和Bi 、Sb 元素之间应有一个合适的比例,否则也无法取得预期的效果。
对于镁球铁,有研究报道,在25mm 厚基尔试块的检验结果中,当Bi 元素的加入量超过0.003%时,就可能产生片状石墨,当Bi 元素加入量达0.006%时,球状石墨完全消失。
在一定范围内,随着球铁凝固时间的缩短,Bi 元素的加入量可适当增加。
球铁的金相组织
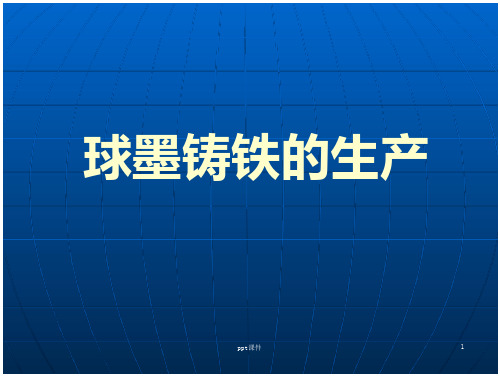
球墨铸铁的生产过程包含以下几个环节:熔炼合格的铁液,球化处理,孕育处理,炉前检查,浇注铸件,清理及热处理,铸件质量检查。在上述各个环节中,熔炼优质铁液和进行有效的球化—孕育处理是生产的关键。
1. 化学成分的选定
选择适当化学成分是保证铸铁获得良好的组织状态和高性能的基本条件,化学成分的选择既要有利于石墨的球化和获得满意的基体,以期获得所要求的性能,又要使铸铁有较好的铸造性能。
生产铸态珠光体球铁要遵循以下原则:
严格控制炉料(生铁与废钢),避免含有强烈形成碳化物元素如Cr、V、Mo、Te等,含锰量取下限,以防止铸态下形成游离渗碳体。适量孕育,一方面防止形成碳化物,另一方面还要防止因强化孕育导致出现大量的铁素体。根据铸件壁厚的性能要求,添加稳定珠光体,但又不形成碳化物的元素如Cu、Ni、Sn等,其中,添加铜的效果显著,成本较低(与添加镍相比),而且也无副作用(与添加锡相比)。在生产高强度珠光体球墨铸铁(抗拉强度要求超过700MPa)时,应采用纯净炉料、严格控制形成碳化物元素、干扰元素以及P、S等有害杂质元素的含量,必要时,还应添加适量的铜和钼。
1.4.3 铁素体-珠光体球墨铸铁
生产牌号QT500-7这种铁素体和珠光体混合基体的球铁时,可参考铁素体、珠光体球铁生产所必须遵循的原则。采用热处理生产铁素体-珠光体球铁时,参考生产退火铁素体球铁 所要求的化学成分,此时,可不必添加铜,只是在石墨化退火第二阶段,缩短保温时间,令其中的部分珠光体转变成铁素体,其余部分则保留下 来,组成混合基体。视所要求的铁素体与珠光体的相对含量,决定缩短 第二阶段的保温时间,要求的铁素体越多,则要缩短的保温时间就越短。采用铸态生产铁素体-珠光体球铁时,参考生产铸态铁素体球铁要遵循的原则。在此基础上,通过控制添加铜的数量,以获得铁素体与珠光体的混合基体,随加铜量的增多,珠光体量增加。
球铁生产中的几项技术处理

球铁生产中的几项技术处理球铁生产中的几项技术处理炉料选择球铁的炉料由回炉料、废钢、生铁、铁合金和增碳剂等组成。
以下就生铁和增碳剂谈谈个人的看法。
2.1生铁我国现有铸造生铁、炼钢生铁、球墨铸铁用生铁、含钒生铁和铸造用磷铜钛低合金耐磨生铁等五个国标。
球铁常用的生铁牌号为Z14、(Z18)、(L08)、L10、Q10、Q12和Q16。
选定生铁时,首先要根据球铁的基体要求及回炉料用量来确定生铁的硅量(定牌号)。
其次,根据韧性要求和热处理与否限定锰量(定分组)。
生铁中的磷硫量则越少越好。
磷的分级和硫的分类,各种生铁的界定量不太一样。
球铁用生铁有特级磷(P≤0.05%)和特类硫(S≤0.02%)。
炼钢生铁有特类硫(S≤0.02%),但磷一般较高。
铸造生铁没有特级磷和特类硫,其一级磷和一类硫分别为≤0.06%和≤0.03%。
因铁矿来源的不同,生铁中常含有Cu、Cr、Mo、Ti、Sn、Al、Pb、Bi、Te、Cd、Zn、As和Sb等微量元素。
其中As、Pb、Zn、Ti、Bi、Sb、Cd和Te等超过一定含量,或干扰球化,或生晶界脆性相,或生硬质点,从而影响着球化成败、球铁的韧性和切削加工性。
这些干扰元素的作用很复杂,它们共存时,有倍增效应或抵消作用,机理有待进一步研究。
为了控制干扰元素,需对生铁中微量元素总量(∑T)加以限制。
例如德国规定∑T≤0.0745%,日本规定为∑T≤0.089%,其中Ti不大于50%∑T。
我国目前一般约定为∑T≤0.1%,其中Ti≤0.045%。
从微量元素含量考察,本溪生铁最好(某组数据为∑T≤0.1%,Ti<0.055%,有的数据Ti为0.027%);其它生铁Ti均高于控制值。
若精选矿源,在高炉配料上想些办法,可将Ti降至控制值以下,例如林州某生铁可由Ti0.09%降至0.033%。
Sorelmetal(QIT)生铁是国际著名的高纯生铁,其S≤0.025%(实际S≤0.01%),P≤0.04%,∑T≤0.07%,其中Ti≤0.01%,而Mn≤0.05%,国外广泛使用于汽车铸件。
海门球墨铸铁参数
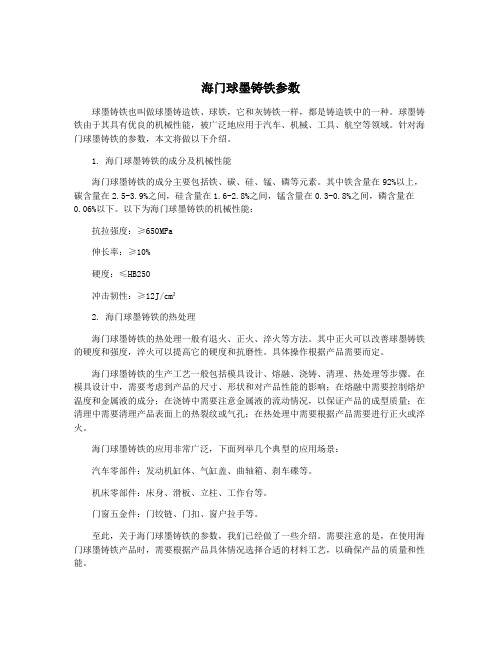
海门球墨铸铁参数球墨铸铁也叫做球墨铸造铁、球铁,它和灰铸铁一样,都是铸造铁中的一种。
球墨铸铁由于其具有优良的机械性能,被广泛地应用于汽车、机械、工具、航空等领域。
针对海门球墨铸铁的参数,本文将做以下介绍。
1. 海门球墨铸铁的成分及机械性能海门球墨铸铁的成分主要包括铁、碳、硅、锰、磷等元素。
其中铁含量在92%以上,碳含量在2.5-3.9%之间,硅含量在1.6-2.8%之间,锰含量在0.3-0.8%之间,磷含量在0.06%以下。
以下为海门球墨铸铁的机械性能:抗拉强度:≥650MPa伸长率:≥10%硬度:≤HB250冲击韧性:≥12J/cm²2. 海门球墨铸铁的热处理海门球墨铸铁的热处理一般有退火、正火、淬火等方法。
其中正火可以改善球墨铸铁的硬度和强度,淬火可以提高它的硬度和抗磨性。
具体操作根据产品需要而定。
海门球墨铸铁的生产工艺一般包括模具设计、熔融、浇铸、清理、热处理等步骤。
在模具设计中,需要考虑到产品的尺寸、形状和对产品性能的影响;在熔融中需要控制熔炉温度和金属液的成分;在浇铸中需要注意金属液的流动情况,以保证产品的成型质量;在清理中需要清理产品表面上的热裂纹或气孔;在热处理中需要根据产品需要进行正火或淬火。
海门球墨铸铁的应用非常广泛,下面列举几个典型的应用场景:汽车零部件:发动机缸体、气缸盖、曲轴箱、刹车碟等。
机床零部件:床身、滑板、立柱、工作台等。
门窗五金件:门铰链、门扣、窗户拉手等。
至此,关于海门球墨铸铁的参数,我们已经做了一些介绍。
需要注意的是,在使用海门球墨铸铁产品时,需要根据产品具体情况选择合适的材料工艺,以确保产品的质量和性能。
- 1、下载文档前请自行甄别文档内容的完整性,平台不提供额外的编辑、内容补充、找答案等附加服务。
- 2、"仅部分预览"的文档,不可在线预览部分如存在完整性等问题,可反馈申请退款(可完整预览的文档不适用该条件!)。
- 3、如文档侵犯您的权益,请联系客服反馈,我们会尽快为您处理(人工客服工作时间:9:00-18:30)。
问题:球铁的主要微量元素,它们的作用是什么?
1) 碳和硅是组成球铁的基本成分
碳是石墨源泉,碳量不足铁水凝固时石墨就少,因此要求铁水中要有足够高的含碳量;硅是为了保证石墨化和控制机体组织而加入的,硅量不足,铁水凝固的石墨化结晶就困难,尽管铁水在高碳前提下球化了,但不能保证凝固时的石墨化。
尽管碳和硅都是有利成分,但并不是越多越好。
2) 硫及磷对球铁冶金特性的影响
硫与球化元素反应生成硫化物,通过消耗镁而阻碍石墨球化作用;硫与锰形成硫化锰,它抑制球化石墨生长,起阻碍球化作用。
磷促进共晶阶段石墨化,但有阻碍共析渗碳体分解的作用,即阻碍了共析时的石墨化,磷过量还可能形成三元磷晶体,从而导致球管缩松或冷裂。
(备注:共晶和共析反应都会形成相应的成分,共晶是液相铁碳合金转变为奥氏体和渗碳体;共析是奥氏体转变为铁素体和渗碳体,即珠光体。
)
3)必要的合金因素
锰一般情况是炉料带入的,锰无石墨化作用,我们认为它或多或少与硫形成硫化锰,通过硫化锰而间接的阻碍球化。
总而言之,为了提高球化效果,圣戈班管道系统在工艺和质量控制上严格控制C、SI 含量,消除S、Mn的影响,有效控制P的含量,加上我们退火炉及其闭环反馈的全自动控制系统,使我们的球墨铸铁管成为以铁素体为主要成分,石墨球化级别很高的高性能材料,它不仅有良好的强度和硬度,而且有优异的塑性和韧性。
一般碳在3%到4%,硅2%到4%,硫不大于0.015%。