第四章 表面淬火10 1
合集下载
4 表面淬火
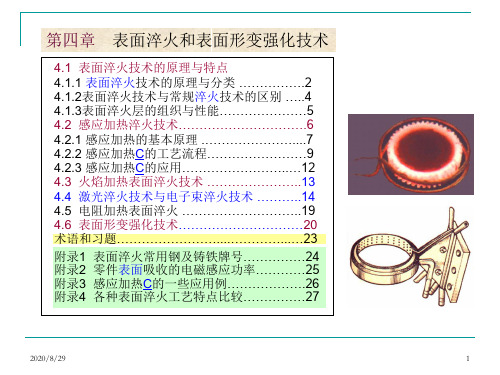
10
6
℃/s以硬上化; 层
过渡区
图图T::r拉4a5n丝钢sf模Bor的JmCaJt相区io变n金硬相Ha化组rd淬织en硬in层g 深度<1mm
•组淬织硬为区隐厚针度M约,兼0.有4m含m碳;硬量度低约的7板0激0条光HVM束
•过渡组区织厚为度正约火0.珠4m光m体;6类00组~2织50H模V,具
工件 通过控制火焰大小/喷嘴 与工件相对位置以及相对 运动速度获得不同硬化层
固定火 焰喷嘴
旋转的工件
硬化层 齿根以上(左)和齿根以下(右)的硬化层
例:几种典型零件火焰加热B/29
12
4.3 火焰加热BC技术(续1)
•零件内部 C
•平面 C 火焰喷嘴与喷水管可同时推进对整个平面进行C
表:轴类零件B 比功率的选择
电流频率 淬硬层深度
比功率 kW / cm2
(kHz)
(mm)
低值
最佳值
高值
500 =较速低度10频效..14率果~~+:1较2.较.13高高频比率功+率10较..15低比功率10..68
1.9 1.2
1.5~2.3
1.2
1.6
2.5
10
2.3 ~ 3.0
0.8
1.6
2.3
200
14
28
8
16
2.7
5.4
1.1
2.2
2020/8/29
8
4.2.2 感应加热C的工艺流程
①预先调质处理 保证心部具有较高的力学性能;容易获得均匀A
② 按工件要求选择比功率
心部要求不高时,可采用正火
••按频工率件确直定比径后功,确率淬定太硬工小层件将深单导度位致与面电积不流上足频的,率比的层功关深率系度选k增W择加设/ c,过备m渡2频区率增大
第四章 钢的表面淬
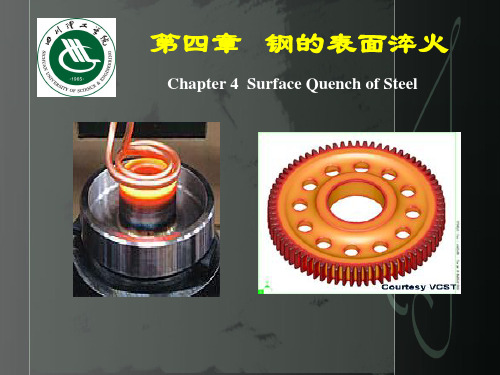
感应加热的物理过程
• 透入式加热 •冷态:加热开始:室温 透入深度小 •过渡态:温度升高 透入深度增大
•温度超过磁性转变点后,该层变为顺磁体,在此顺磁体与相邻 铁磁体之间,涡流强度增大、磁力线密集,铁磁体电流密度剧 增,被迅速加热
•热态:当变成顺磁体的高温层厚度超过热态电流透入深 度后,涡流不再向内部推移 • 传导式加热:继续加热,热态电流透入层温度升高,热传 导方式对内部加热。
感应加热表面淬火工艺
2)淬火工艺选择: 根据零件尺寸及硬化层深度的要求,合理选 择设备。 I.设备频率的选择(frequency):主要根据硬化层深度 来选择。 II.比功率的选择:比功率是指感应加热时工件单位面 积上所吸收的电功率(kW/cm2)。 比功率的选择主要取决于频率和要求的硬化层深度。
1.表面淬火的目的、分类及应用
三、表面淬火的应用(Application) • 零件在复杂的交变应力作用下工作 – 传动轴、传动齿轮
• 要求表面硬度高、强度高、耐磨性好,同时 心部又要有足够的韧性和塑性 • 表面淬火可以仅对钢的表面加热、冷却而不 改变其成分
2.表面淬火工艺原理
表面淬火最基本条件: 高能量集中表面 表面有足够快的速度升温 心部仍保持原有组织状态
过程:正火或调质处理---表面淬火---低温回火
感应加热表面淬火工艺
1)适用钢种: 一般选用中碳钢或中碳低合金钢,例如45、40Cr、 40MnB、42CrMo钢等 高碳钢也可表面淬火,主要用于较小冲击和交变载荷的 工具、量具等,并可采用自回火方法,以提高生产效率, 节约能源,但要注意:应防止过热的产生 表面感应加热淬火的预处理一般采用正火或调质,经感 应加热淬火和回火后心部仍保持较高的综合机械性能,而 表面具有高的硬度和耐磨性
表面淬火课件
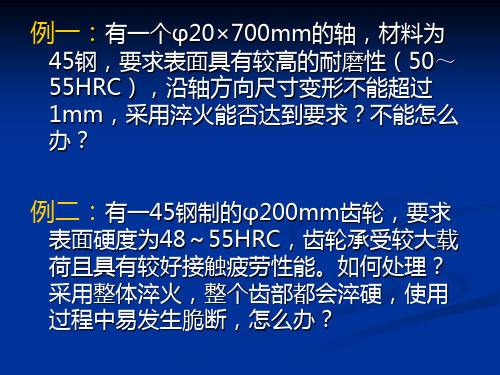
例一:有一个φ20×700mm的轴,材料为45
钢,要求表面具有较高的耐磨性(50~ 55HRC),沿轴方向尺寸变形不能超过1mm, 采用淬火能否达到要求?不能怎么办?
例二:有一45钢制的φ200mm齿轮,要求表
面硬度为48~55HRC,齿轮承受较大载荷且 具有较好接触疲劳性能。如何处理?采用 整体淬火,整个齿部都会淬硬,使用过程 中易发生脆断,怎么办?
1、感应加热表面淬火(Induction hardening) 2、火焰加热淬火(Flame / Torch hardening) 3、电接触表面加热淬火(Contact hardening) 4、激光表面加热淬火(Laser hardening) 5、电子束表面加热淬火等(Electron-beam hardening )
●残余应力与沿硬化层深度的硬度分布有关。 过渡区硬度降落愈陡,表面压应力虽较大, 但紧靠过渡区的张应力峰值也最大;过渡区 硬度降得愈平缓,过渡区愈宽,张应力峰值 内移且减少,表面的残余压应力也减少。
●残余应力的分布和钢中的含碳量有关。含碳 量愈高,残余压应力愈大
§4-3:表面淬火方法
一、感应加热表面淬火 工件在交变磁场作用下产生了较高的感
应电势并在表面形成涡流,利用感应电流 在零件表面产生的热效应而使零件加热称 为感应加热;将感应加热后的零件快速冷 却的淬火工艺称为感应加热淬火。
根据设备输出频率高低,感应加热的种类如下表所示:
加热方法
工频 中频 高频、超音频 超高频脉冲
频率(KHz)
50 <10 20~1000 27120
功率密度 (102W×cm-2)
● 极限硬度(HV)HL(即规定硬度)是零部件所要
求最小表面硬度的函数: (HV)HL =0.8 (HV)HS
钢,要求表面具有较高的耐磨性(50~ 55HRC),沿轴方向尺寸变形不能超过1mm, 采用淬火能否达到要求?不能怎么办?
例二:有一45钢制的φ200mm齿轮,要求表
面硬度为48~55HRC,齿轮承受较大载荷且 具有较好接触疲劳性能。如何处理?采用 整体淬火,整个齿部都会淬硬,使用过程 中易发生脆断,怎么办?
1、感应加热表面淬火(Induction hardening) 2、火焰加热淬火(Flame / Torch hardening) 3、电接触表面加热淬火(Contact hardening) 4、激光表面加热淬火(Laser hardening) 5、电子束表面加热淬火等(Electron-beam hardening )
●残余应力与沿硬化层深度的硬度分布有关。 过渡区硬度降落愈陡,表面压应力虽较大, 但紧靠过渡区的张应力峰值也最大;过渡区 硬度降得愈平缓,过渡区愈宽,张应力峰值 内移且减少,表面的残余压应力也减少。
●残余应力的分布和钢中的含碳量有关。含碳 量愈高,残余压应力愈大
§4-3:表面淬火方法
一、感应加热表面淬火 工件在交变磁场作用下产生了较高的感
应电势并在表面形成涡流,利用感应电流 在零件表面产生的热效应而使零件加热称 为感应加热;将感应加热后的零件快速冷 却的淬火工艺称为感应加热淬火。
根据设备输出频率高低,感应加热的种类如下表所示:
加热方法
工频 中频 高频、超音频 超高频脉冲
频率(KHz)
50 <10 20~1000 27120
功率密度 (102W×cm-2)
● 极限硬度(HV)HL(即规定硬度)是零部件所要
求最小表面硬度的函数: (HV)HL =0.8 (HV)HS
第4~5章表面淬火
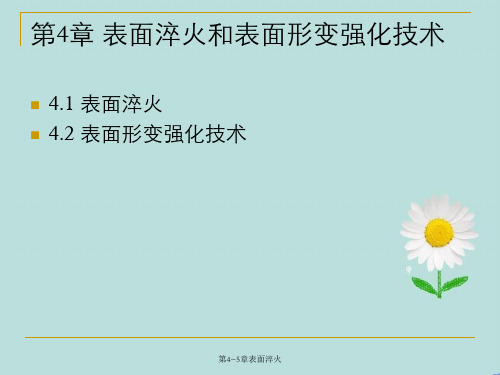
中,当感应线圈通以交流 电后,线圈内即形成交流 磁场,在零件中引起闭合 电流即涡流,并由于集肤 效应而集中分布于工件表 面,使工件表面温度迅速 加热到钢的相变临界温度 以上,然后在冷却介质中 快速冷却,使工件表面获 得马氏体。 演示录像1
第4~5章表面淬火
1-加热淬火层 2-间隙 3-工件 4-加热感应圈 5-淬火喷水套
4.1 表面淬火
感应加热淬火的优缺点 工件表面氧化、脱碳小,变形小,质量稳
定;加热速度快,热效率高,生产率高;易实 现机械化和自动化。
成本较高;尖角效应;对一些形状复杂的 零件而言,难以保证得到均匀的表面淬火层。
第4~5章表面淬火
4.1 表面淬火
感应加热广泛用于齿轮、轴、曲轴、凸轮、轧 辊等工件的表面淬火,目的是提高这些工件的 耐磨性和抗疲劳破断的能力。汽车后半轴采用 感应加热表面淬火,设计载荷下的疲劳循环次 数比用调质处理约提高10倍。
4.1 表面淬火
• 感应加热淬火机床的主要作用是使工件定位并 进行必要的运动。
• 感应加热淬火机床还应附有提供淬火介质的装 置。淬火机床可分为标准机床和专用机床,前 者适用于一般工件,后者适用于大量生产的复 杂工件。
第4~5章表面淬火
4.1 表面淬火
进行感应加热热处理时,为保证热处理质量和 提高热效率,必须根据工件的形状和要求,设 计制造结构适当的感应器。常用的感应器有外 表面加热感应器、内孔加热感应器、平面加热 感应器等。
孔10mm~30mm的孔喷射冷却介质 承圈等直径大表面窄的
(如图4-6b)
工件
工件以一定速度旋转,喷嘴轴向配合 获得螺旋状淬硬层 运动,得螺旋状淬硬层
一个或几个喷嘴沿旋转工件定速移动, 用于轴、锤杆和轧轮 加热和冷却工件表面
第4~5章表面淬火
1-加热淬火层 2-间隙 3-工件 4-加热感应圈 5-淬火喷水套
4.1 表面淬火
感应加热淬火的优缺点 工件表面氧化、脱碳小,变形小,质量稳
定;加热速度快,热效率高,生产率高;易实 现机械化和自动化。
成本较高;尖角效应;对一些形状复杂的 零件而言,难以保证得到均匀的表面淬火层。
第4~5章表面淬火
4.1 表面淬火
感应加热广泛用于齿轮、轴、曲轴、凸轮、轧 辊等工件的表面淬火,目的是提高这些工件的 耐磨性和抗疲劳破断的能力。汽车后半轴采用 感应加热表面淬火,设计载荷下的疲劳循环次 数比用调质处理约提高10倍。
4.1 表面淬火
• 感应加热淬火机床的主要作用是使工件定位并 进行必要的运动。
• 感应加热淬火机床还应附有提供淬火介质的装 置。淬火机床可分为标准机床和专用机床,前 者适用于一般工件,后者适用于大量生产的复 杂工件。
第4~5章表面淬火
4.1 表面淬火
进行感应加热热处理时,为保证热处理质量和 提高热效率,必须根据工件的形状和要求,设 计制造结构适当的感应器。常用的感应器有外 表面加热感应器、内孔加热感应器、平面加热 感应器等。
孔10mm~30mm的孔喷射冷却介质 承圈等直径大表面窄的
(如图4-6b)
工件
工件以一定速度旋转,喷嘴轴向配合 获得螺旋状淬硬层 运动,得螺旋状淬硬层
一个或几个喷嘴沿旋转工件定速移动, 用于轴、锤杆和轧轮 加热和冷却工件表面
表面淬火
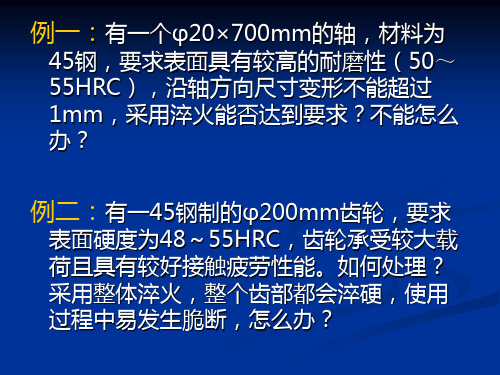
2、对奥氏体晶粒度影响
提高相变区加热速度使奥氏体起始晶粒度显著细化。 原因: ◆奥氏体形核不仅在铁素体与碳化物相界,而且在α 相亚结构边界形核;晶核尺寸仅为亚结构边界宽度 1/10—1/5,形成极细的起始晶粒。 ◆在高速加热条件下,起始晶粒度不易长大,从而细 化晶粒。 ◆所形成的奥氏体晶粒内部受热应力和组织应力的作 用,形成许多位错胞。
▲感应圈形状与结构 感应圈的几何形状主要根据工件硬化部位 感应圈的几何形状主要根据工件硬化部位 的几何形状、尺寸及选择的加热方式来确定。 的几何形状、尺寸及选择的加热方式来确定。 设计时应注意以下几种效应: ▲临近效应:(采用旋转加热方法) 临近效应: ▲环状效应:(有利于圆柱体外表面) 环状效应:(有利于圆柱体外表面) ▲尖角效应:(调节线圈与零件间的间隙或改 尖角效应:(调节线圈与零件间的间隙或改 进感应圈的结构来改善)
透入式加热与传导式加热相比较有如下特点: 透入式加热与传导式加热相比较有如下特点: ●表面的温度超过A2点以后,最大密度的涡流 表面的温度超过A 移向内层,表层加热速度开始变慢,不易过 热,而传导式加热随着加热时间的延长,表 面继续加热容易过热; ●加热迅速,热损失小,热效率高; ●热量分布较陡,淬火后过渡层较窄,使表面 压应力提高
求最小表面硬度的函数: HV) (HV)HL =0.8 (HV)HS HV) 式中(HV) 式中(HV)HS为零件要求最小表面硬度。
3、表面淬火后性能 ◆表面硬度:快速加热,激冷淬火的工件表面 表面硬度:快速加热,激冷淬火的工件表面 硬度往往比普通淬火高2 硬度往往比普通淬火高2~5个百分点 ◆耐磨性:快速加热表面淬火后工件的耐磨性 耐磨性:快速加热表面淬火后工件的耐磨性 优于普通淬火 ◆疲劳强度:采用正确的表面淬火工艺可以显 疲劳强度:采用正确的表面淬火工艺可以显 著提高零件的抗疲劳性能 ◆残余应力分布:表面淬火后的残余应力大小 残余应力分布:表面淬火后的残余应力大小 和分布与钢种、零件尺寸、硬化层深度及加 热冷却等多种因素有关
四、表面淬火

二、表面淬火的条件
快速加热: 要在工件表面有限深度内达到相变点以上的温度, 必须给工件表面以极高的能量密度来加热,使工件表面的热量来 不及向心部传导,以造成极大的温差。
-
2
三、表面淬火的分类: 表面淬火常以供给表面能量的形式不同而命名及分类。目前表
面淬火可以分成以下几类: 1.感应加热表面淬火 2.火焰淬火 3.电接触加热表面淬火 4.电解液加热表面淬火 5.激光加热表面淬火 6.电子束加热表面淬火
-
4
2. 奥氏体成分不均匀性随着加热速度的增加而增大 如前所述,随着加热速度的增大,转变温度提高,转变温度范
围扩大. 随着转变温度的升高,与铁素体相平衡的奥氏体碳浓度 降低,而与渗碳体相平衡的奥氏体碳浓度增大. 因此,与铁素体 相毗邻的奥氏体碳浓度将和与渗碳体相毗邻的奥氏体中碳浓度有 很大差异。由于加热速度快,加热时间短,碳及合金元素来不及 扩散,将造成奥氏体中成分的不均匀,且随着加热速度的提高, 奥氏体成分的不均匀性增大。例如0.4%C碳钢,当以130℃/s 的加热速度加热至900℃时,奥氏体中存在着1.6%C的碳浓度区. 显然,快速加热时,钢种、原始组织对奥氏体成分的均匀性有很 大影响. 对热传导系数小,碳化物粗大且溶解困难的高合金钢采 用快速加热是有困难的。
快速加热使奥氏体成分不均匀及晶粒细化,减小了过冷奥氏体 的稳定性,使c曲线左移. 由于奥氏体成分的不均匀性,特别是亚 共析钢,还会出现二种成分不均匀性现象。在珠光体区域,原渗 碳体片区与原铁素体片区之间存在着成分的不均匀性,这种区域 很傲小,即在微小体积内的不均匀性. 而在原珠光体区与原先共 析铁素体块区也存在着成分的不均匀性,这是大体积范围内的不 均匀性. 由于存在这种成分的大体积不均匀性,将使这二区域的 马氏体转变点不同,马氏体形态不同. 即相当于原铁素体区出现 低碳马氏体,原珠光体区出现高碳马氏体. 由于快速加热奥氏体 成分的不均匀性,淬火后马氏体成分也不均匀,所以,尽管淬火 后硬度较高,但回火时硬度下降较快,因此回火温度应比普通加 热淬火的略低。
快速加热: 要在工件表面有限深度内达到相变点以上的温度, 必须给工件表面以极高的能量密度来加热,使工件表面的热量来 不及向心部传导,以造成极大的温差。
-
2
三、表面淬火的分类: 表面淬火常以供给表面能量的形式不同而命名及分类。目前表
面淬火可以分成以下几类: 1.感应加热表面淬火 2.火焰淬火 3.电接触加热表面淬火 4.电解液加热表面淬火 5.激光加热表面淬火 6.电子束加热表面淬火
-
4
2. 奥氏体成分不均匀性随着加热速度的增加而增大 如前所述,随着加热速度的增大,转变温度提高,转变温度范
围扩大. 随着转变温度的升高,与铁素体相平衡的奥氏体碳浓度 降低,而与渗碳体相平衡的奥氏体碳浓度增大. 因此,与铁素体 相毗邻的奥氏体碳浓度将和与渗碳体相毗邻的奥氏体中碳浓度有 很大差异。由于加热速度快,加热时间短,碳及合金元素来不及 扩散,将造成奥氏体中成分的不均匀,且随着加热速度的提高, 奥氏体成分的不均匀性增大。例如0.4%C碳钢,当以130℃/s 的加热速度加热至900℃时,奥氏体中存在着1.6%C的碳浓度区. 显然,快速加热时,钢种、原始组织对奥氏体成分的均匀性有很 大影响. 对热传导系数小,碳化物粗大且溶解困难的高合金钢采 用快速加热是有困难的。
快速加热使奥氏体成分不均匀及晶粒细化,减小了过冷奥氏体 的稳定性,使c曲线左移. 由于奥氏体成分的不均匀性,特别是亚 共析钢,还会出现二种成分不均匀性现象。在珠光体区域,原渗 碳体片区与原铁素体片区之间存在着成分的不均匀性,这种区域 很傲小,即在微小体积内的不均匀性. 而在原珠光体区与原先共 析铁素体块区也存在着成分的不均匀性,这是大体积范围内的不 均匀性. 由于存在这种成分的大体积不均匀性,将使这二区域的 马氏体转变点不同,马氏体形态不同. 即相当于原铁素体区出现 低碳马氏体,原珠光体区出现高碳马氏体. 由于快速加热奥氏体 成分的不均匀性,淬火后马氏体成分也不均匀,所以,尽管淬火 后硬度较高,但回火时硬度下降较快,因此回火温度应比普通加 热淬火的略低。
表面淬火技术
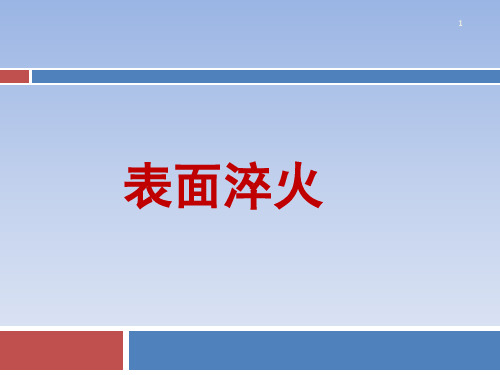
仅仅表面加热,工件淬火变形小。 设备紧凑,操作简单,易于实现机械化自
动化生产,可放置在生产线上,,生产效 率高。
10.4.1 感应加热的基本原理
28
1.电磁感应
当感应线圈通以交流电时,在感应线圈的内部和 周围同时产生与电流频率相同的交变磁场,将工 件置于高频感应线圈内,受电流交变磁场的作用, 在工件内相应地产生感应电流,这种感应电流在 金属工件内自行闭合,称为涡流。其感应电动势 瞬时值为:
e
e
If
Z
R2 XL2
31
2.表面效应(集肤效应) 涡流强度If随高频电磁场强度由工件表面向
内层逐渐减小而相应减小的规律称为表面 效应或集肤效应。离表面x处的涡流强度:
x
Ix I0 e
式中,I0-表面最大的涡流强度;x-到工件表 面的距离;Δ-与工件材料物理性质有关的 系数。
32
所以,当x=0时,Ix = I0 当x>0时,Ix<I0
激光加热表面淬火是一种新的淬火工艺,与常规 表面淬火相比,具有如下优点:由于能量密度高, 加热速度极快,无氧化脱碳,热变形极小;冷却速 度也很快,可自淬火而无需冷却介质;表面光洁度 高,不需要再 进行表面精加工,可作为最后一道 工序;表面硬度高,一般不需回火;适合对于形状 复杂的工件(如带有盲孔、小孔、小槽、薄壁工件) 进行局部表面淬火。
因此,表面是零件的薄弱位置,是引起零 件失效的策源地。
4
10.1 表面淬火工艺分类
5
实现表面淬火的基本条件
表面淬火是利用金属固态相变,通过快 速加热的方法对工件表面进行淬火。其目 的是在工件表面一定深度内获得马氏体组 织,而其心部依然保持淬火前的原始组织 (调质或正火态),以获得表面高的强度、 硬度及耐磨性,同时保持心部大的塑性和 韧性。
动化生产,可放置在生产线上,,生产效 率高。
10.4.1 感应加热的基本原理
28
1.电磁感应
当感应线圈通以交流电时,在感应线圈的内部和 周围同时产生与电流频率相同的交变磁场,将工 件置于高频感应线圈内,受电流交变磁场的作用, 在工件内相应地产生感应电流,这种感应电流在 金属工件内自行闭合,称为涡流。其感应电动势 瞬时值为:
e
e
If
Z
R2 XL2
31
2.表面效应(集肤效应) 涡流强度If随高频电磁场强度由工件表面向
内层逐渐减小而相应减小的规律称为表面 效应或集肤效应。离表面x处的涡流强度:
x
Ix I0 e
式中,I0-表面最大的涡流强度;x-到工件表 面的距离;Δ-与工件材料物理性质有关的 系数。
32
所以,当x=0时,Ix = I0 当x>0时,Ix<I0
激光加热表面淬火是一种新的淬火工艺,与常规 表面淬火相比,具有如下优点:由于能量密度高, 加热速度极快,无氧化脱碳,热变形极小;冷却速 度也很快,可自淬火而无需冷却介质;表面光洁度 高,不需要再 进行表面精加工,可作为最后一道 工序;表面硬度高,一般不需回火;适合对于形状 复杂的工件(如带有盲孔、小孔、小槽、薄壁工件) 进行局部表面淬火。
因此,表面是零件的薄弱位置,是引起零 件失效的策源地。
4
10.1 表面淬火工艺分类
5
实现表面淬火的基本条件
表面淬火是利用金属固态相变,通过快 速加热的方法对工件表面进行淬火。其目 的是在工件表面一定深度内获得马氏体组 织,而其心部依然保持淬火前的原始组织 (调质或正火态),以获得表面高的强度、 硬度及耐磨性,同时保持心部大的塑性和 韧性。
四表面淬火.优秀精选PPT
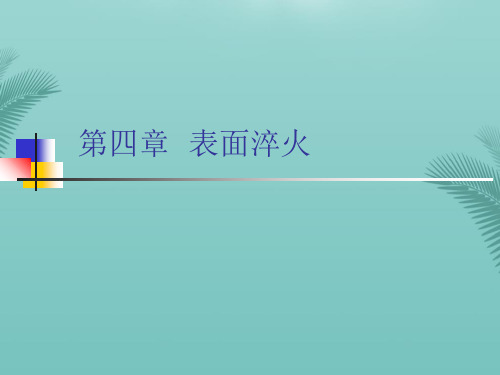
快速加热:要在工件表面有限深度内达到相变点以上的温度, 必须给工件表面以极高的能量密度来加热,使工件表面的热量来 不及向心部传导,以造成极大的温差。
三、表面淬火的分类: 表面淬火常以供给表面能量的形式不同而命名及分类。目前表
面淬火可以分成以下几类: 1.感应加热表面淬火 2.火焰淬火 3.电接触加热表面淬火 4.电解液加热表面淬火 5.激光加热表面淬火 6.电子束加热表面淬火
交流电时,其内外将产生频率相同的交变磁场。 冷却水
若将工件放人感应圈内,在交变磁场作用下,
工件内就会产生与感应圈中的电流频率相同而
感应线圈
方向相反的感应电流。由于感应电流沿工件表
淬火喷水套
面形成封闭回路,故称为涡流。
电
涡流在被加热工件中的分布由表面至心部呈
流 密 度
加热淬火层
指数规律衰减,因此,涡流主要分布于工件表
4.2 表面淬火工艺原理
一、钢在非平衡加热时的相变特点 钢在表面淬火时,其基本条件是有足够的能量密度提供表面加
热,使表面有足够快的速度达到相变点以上的温度。因此,表面 淬火时,钢处于非平衡加热。 钢在非平衡加热时有如下特点: 1.在一定的加热速度范围内,临界点随加热速度的增加而提高。
在快速加热时均随着加热速度的增加而向高温移动。但当加热 速度大到某一范围时,所有亚共析钢的转变温度均相同。加热速 度愈快,奥氏体形成温度范围愈宽,但形成速度快;形成时间 短.加热速度对奥氏体开始形成温度影响不大,但随着加热速度 的提高,显著提高了形成终了温度.原始组织愈不均匀,最终形 成温度提得愈高。
感应加热淬火后一般只进行低温回火。
2又由表于面加淬热火时工2间艺.极原短理奥,奥氏氏体体晶成粒来分不不及长均大.匀当性用超随快速着加加热时热,可速获度得超的细化增晶加粒。而增大 由1、于感感应应加电热流基沿本工如原件理表前:面所形成述封闭,回随路,着故称加为热涡流速。度的增大,转变温度提高,转变温度范 3.提高加热围速度扩可显大著.细化随奥氏着体转晶粒变. 温度的升高,与铁素体相平衡的奥氏体碳浓度 因二此、, 表从面加淬热火降角的度组低考织,虑与,性而表能面与淬渗火仅碳是在体工相件表平面有衡限的深度奥范围氏内体加热碳到相浓变度点以增上。大.因此,与铁素体 的表热面效 淬应火,常使以相工供件给毗表表邻面面局能的部量加的奥热形氏,式继不体之同快而碳速命浓冷名却及度,分以类将获。和与渗碳体相毗邻的奥氏体中碳浓度有 感应加热就是很利用大电差磁感异应和。集由肤效于应,加通热过表速面强度大快电流,的热加效热应把时工件间表短面迅,速加碳热到及淬合火温金度的元。素来不及 表快面速淬 加火热常使以奥扩供氏给体散表成,面分能不将量均的匀造形及成式晶不粒奥同细而化氏命,体名减及小中分了类过成。冷分奥氏的体的不稳均定性匀,使,c曲且线左随移着.由加于奥热氏速体成度分的的不提均匀高性,,特别是亚共析钢, 还感会应出 加现热二淬种火奥成后分一氏不般体均只匀进成性行现低分象温。回的火不。 均匀性增大。例如0.4%C碳钢,当以130℃/s 得马氏体组织的的工加艺热。 速度加热至900℃时,奥氏体中存在着1.6%C的碳浓度 喷射冷却法即区当感.应显加热然终了,时快把工速件置加于热喷射时器之,中钢,向种工件、喷原射淬始火介组质织进行对淬火奥冷氏却。体成分的均匀性
三、表面淬火的分类: 表面淬火常以供给表面能量的形式不同而命名及分类。目前表
面淬火可以分成以下几类: 1.感应加热表面淬火 2.火焰淬火 3.电接触加热表面淬火 4.电解液加热表面淬火 5.激光加热表面淬火 6.电子束加热表面淬火
交流电时,其内外将产生频率相同的交变磁场。 冷却水
若将工件放人感应圈内,在交变磁场作用下,
工件内就会产生与感应圈中的电流频率相同而
感应线圈
方向相反的感应电流。由于感应电流沿工件表
淬火喷水套
面形成封闭回路,故称为涡流。
电
涡流在被加热工件中的分布由表面至心部呈
流 密 度
加热淬火层
指数规律衰减,因此,涡流主要分布于工件表
4.2 表面淬火工艺原理
一、钢在非平衡加热时的相变特点 钢在表面淬火时,其基本条件是有足够的能量密度提供表面加
热,使表面有足够快的速度达到相变点以上的温度。因此,表面 淬火时,钢处于非平衡加热。 钢在非平衡加热时有如下特点: 1.在一定的加热速度范围内,临界点随加热速度的增加而提高。
在快速加热时均随着加热速度的增加而向高温移动。但当加热 速度大到某一范围时,所有亚共析钢的转变温度均相同。加热速 度愈快,奥氏体形成温度范围愈宽,但形成速度快;形成时间 短.加热速度对奥氏体开始形成温度影响不大,但随着加热速度 的提高,显著提高了形成终了温度.原始组织愈不均匀,最终形 成温度提得愈高。
感应加热淬火后一般只进行低温回火。
2又由表于面加淬热火时工2间艺.极原短理奥,奥氏氏体体晶成粒来分不不及长均大.匀当性用超随快速着加加热时热,可速获度得超的细化增晶加粒。而增大 由1、于感感应应加电热流基沿本工如原件理表前:面所形成述封闭,回随路,着故称加为热涡流速。度的增大,转变温度提高,转变温度范 3.提高加热围速度扩可显大著.细化随奥氏着体转晶粒变. 温度的升高,与铁素体相平衡的奥氏体碳浓度 因二此、, 表从面加淬热火降角的度组低考织,虑与,性而表能面与淬渗火仅碳是在体工相件表平面有衡限的深度奥范围氏内体加热碳到相浓变度点以增上。大.因此,与铁素体 的表热面效 淬应火,常使以相工供件给毗表表邻面面局能的部量加的奥热形氏,式继不体之同快而碳速命浓冷名却及度,分以类将获。和与渗碳体相毗邻的奥氏体中碳浓度有 感应加热就是很利用大电差磁感异应和。集由肤效于应,加通热过表速面强度大快电流,的热加效热应把时工件间表短面迅,速加碳热到及淬合火温金度的元。素来不及 表快面速淬 加火热常使以奥扩供氏给体散表成,面分能不将量均的匀造形及成式晶不粒奥同细而化氏命,体名减及小中分了类过成。冷分奥氏的体的不稳均定性匀,使,c曲且线左随移着.由加于奥热氏速体成度分的的不提均匀高性,,特别是亚共析钢, 还感会应出 加现热二淬种火奥成后分一氏不般体均只匀进成性行现低分象温。回的火不。 均匀性增大。例如0.4%C碳钢,当以130℃/s 得马氏体组织的的工加艺热。 速度加热至900℃时,奥氏体中存在着1.6%C的碳浓度 喷射冷却法即区当感.应显加热然终了,时快把工速件置加于热喷射时器之,中钢,向种工件、喷原射淬始火介组质织进行对淬火奥冷氏却。体成分的均匀性
表面淬火专题知识专业知识讲座

▲可见,频率愈高,电流透入深度愈浅;频率不变时, 温度超过居里点以后,电流透入深度显著增加。
(C) 热传导
本文档所提供的信息仅供参考之用,不能作为科学依据,请勿模仿。文档如有不
(2)感应加当之热处的,请过联系程本人或网站删除。 如右图为工件在感
应加热时涡流在工件表 面分布变化的曲线和感 应加热时冷态和热态的 涡流分布曲线。 透入式加热 概念: 特点:P86 (与传导式加热区别)
2 f
本文档所提供的信息仅供参考之用,不能作为科学依据,请勿模仿。文档如有不
3、奥氏体成分当之均处,匀请化联系影本响人或网站删除。
奥氏体成分不均匀性随着加热速度的增加而增加 原因:
◆快速加热条件下形成的奥氏体,其含 C量随加热速
度提高而偏离其平衡成分
◆大部分合金元素在碳化物中富集,从而使合金元素
在快速加热时更难固溶于奥氏体并不易均匀化
根据设备输出频率高低,感应加热的种类如下表所示:
加热方法
工频 中频 高频、超音频 超高频脉冲
频率(KHz)
50 <10 20~1000 27120
功率密度 (102W×cm-2)
0.1~1
<5 2~10 100~300
本文档所提供的信息仅供参考之用,不能作为科学依据,请勿模仿。文档如有不
1、感应加热基本原当之理处,请联系本人或网站删除。 (1)感应加热的物理基础 (a)电磁感应:当工件放在通有交变电流的感应圈中时,受到
本文档所提供的信息仅供参考之用,不能作为科学依据,请勿模仿。文档如有不 当之处,请联系本人或网站删除。
本文档所提供的信息仅供参考之用,不能作为科学依据,请勿模仿。文档如有不 当之处,请联系本人或网站删除。
2、对奥氏体晶粒度影响
第四章表面热处理
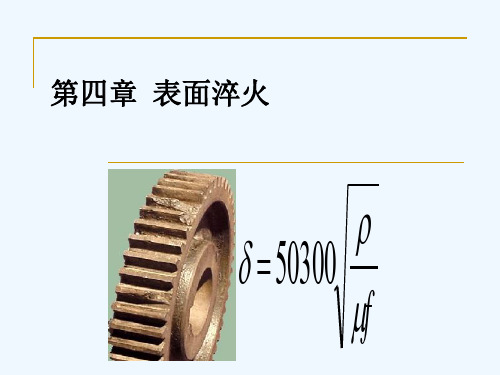
第四章 表面淬火
50300 f
火焰表面淬火.swf
什么是表面淬火
将工件快速加热到淬火温度,然后迅速冷却,仅使 表面层获得淬火组织的热处理方法。
表面淬火有何特点
不改变表面化学成分,只改变表面组织
表面淬火主要解决哪些问题
表面-心部不同性能要求,高效率生产
火焰表面淬火.swf
• 工艺要点:用快速加热法,使零件表面层很快地达到淬火温 度(A化),在热量传至内部之前,立即冷却使表 面层淬硬。 • 材料:中碳钢及中碳合金钢,如40、45、40Cr。
3、45钢曲轴,调质后进行表面淬火,处理后从表面到心部的 组织如何变化?
火焰表面淬火.swf
火焰表面淬火.swf
2、分类(按电源频率)
工频:50Hz,功率密度0.1~100W/cm2; δ = 10~15mm 中频:<10kHz,功率密度< 5 W/cm2;
δ >2mm
高频、超高频:20 ~1000kHz,功率密度2 ~10 W/cm2;
δ = 0.5~2mm
一般地:淬火硬化层厚度随感应加热器频率↗而↘; 但感应电流随感应加热器频率↗而↗ ,即表面加热热效率高 (易过热)。
应根据工件尺寸和要求的淬硬层深度选择合理的电流频率。
火焰表面淬火.swf
3、高频应加热表面淬火后的组织和性能
快速加热时钢的相变特点
1)临界温度升高,转变在较宽的温度范围内完成 2)奥氏体晶粒较细 3)奥氏体成分不均匀
高频感应淬火后的组织
M →M+F →原始组织
高频感应淬火后的性能 硬度比普通淬火高2~3HRC 疲劳强度提高 强度提高
热量,硬化层较深,不易淬裂,淬火硬度不高。 适用于中碳钢(调质钢、工具钢、模具钢等)和铸铁 零件表面淬火; 适用于大型零件,不适用于薄壁零件。 加热温度不易控制、工件表面易过热、 淬火质量不够稳定。
50300 f
火焰表面淬火.swf
什么是表面淬火
将工件快速加热到淬火温度,然后迅速冷却,仅使 表面层获得淬火组织的热处理方法。
表面淬火有何特点
不改变表面化学成分,只改变表面组织
表面淬火主要解决哪些问题
表面-心部不同性能要求,高效率生产
火焰表面淬火.swf
• 工艺要点:用快速加热法,使零件表面层很快地达到淬火温 度(A化),在热量传至内部之前,立即冷却使表 面层淬硬。 • 材料:中碳钢及中碳合金钢,如40、45、40Cr。
3、45钢曲轴,调质后进行表面淬火,处理后从表面到心部的 组织如何变化?
火焰表面淬火.swf
火焰表面淬火.swf
2、分类(按电源频率)
工频:50Hz,功率密度0.1~100W/cm2; δ = 10~15mm 中频:<10kHz,功率密度< 5 W/cm2;
δ >2mm
高频、超高频:20 ~1000kHz,功率密度2 ~10 W/cm2;
δ = 0.5~2mm
一般地:淬火硬化层厚度随感应加热器频率↗而↘; 但感应电流随感应加热器频率↗而↗ ,即表面加热热效率高 (易过热)。
应根据工件尺寸和要求的淬硬层深度选择合理的电流频率。
火焰表面淬火.swf
3、高频应加热表面淬火后的组织和性能
快速加热时钢的相变特点
1)临界温度升高,转变在较宽的温度范围内完成 2)奥氏体晶粒较细 3)奥氏体成分不均匀
高频感应淬火后的组织
M →M+F →原始组织
高频感应淬火后的性能 硬度比普通淬火高2~3HRC 疲劳强度提高 强度提高
热量,硬化层较深,不易淬裂,淬火硬度不高。 适用于中碳钢(调质钢、工具钢、模具钢等)和铸铁 零件表面淬火; 适用于大型零件,不适用于薄壁零件。 加热温度不易控制、工件表面易过热、 淬火质量不够稳定。
第四章表面淬火设备
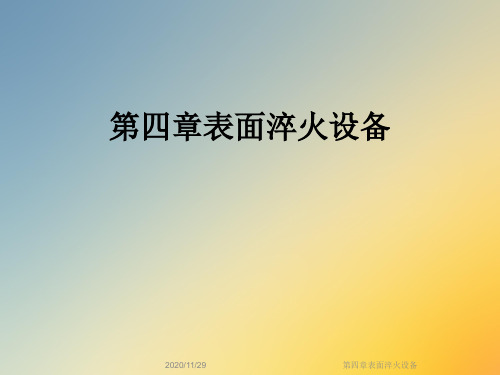
• 高频电流较小,不需要很高的机械强度,可用薄壁纯铜管绕制而 成,也可用薄铜片焊接而成。
• 中频电压较低,电流大,线圈有足够的强度抵抗电磁力的作用, 要用厚的铜板和铜管制造。
第四章表面淬火设备
2 结构
第四章表面淬火设备
(2)铜管成形 步骤如下 • 先将铜管退火软化(加热至650~700℃,然后水冷) • 用锤子敲击成长方形或方形截面;ϕ10mm铜管经过三道模拉制
第四章表面淬火设备
常用喷嘴的形状有以下几种:
(3)环形 适用于滚轮、轴类及其他外圆表面淬火加热时用,另一种 是内圆表面淬火加热之用。
第四章表面淬火设备
(4)角形 (5)钳形
常用喷嘴的形状有以下几种:
适用于机床、导轨等角形工件的表面淬火加热之用。 专门用于加热齿轮及类似形状的零件。第四章表Βιβλιοθήκη 淬火设备第四章表面淬火设备
晶闸管中频电源缺点:主要是由于受晶闸管元件过电流和过电压 能力的限制,晶闸管中频电源的过载能力较差,因此整个设备的保 护系统较复杂。
第四章表面淬火设备
二、晶闸管中频加热装置的规格及选用
第四章表面淬火设备
第四章表面淬火设备
第四章表面淬火设备
四 感应热处理辅助设备
感应热处理的优点:机械化、自动化程度较高,产品热处理质量 的均匀性和一致性好,同时减轻体力劳动并改善劳动条件。 感应加热用热处理设备主要指淬火机床、感应器以及各种专用的感 应加热调质、退火、淬火生产流水线等。
第四章表面淬火设备
2020/11/29
第四章表面淬火设备
• 表面淬火方法:感应淬火,火焰淬火, 接触电阻加热淬火等。
第四章表面淬火设备
§4.1 感应淬火
感应加热就是利用电磁感应在工件内产生涡流而将工件进 行加热。感应加热表面淬火与普通淬火比具有如下优点:
• 中频电压较低,电流大,线圈有足够的强度抵抗电磁力的作用, 要用厚的铜板和铜管制造。
第四章表面淬火设备
2 结构
第四章表面淬火设备
(2)铜管成形 步骤如下 • 先将铜管退火软化(加热至650~700℃,然后水冷) • 用锤子敲击成长方形或方形截面;ϕ10mm铜管经过三道模拉制
第四章表面淬火设备
常用喷嘴的形状有以下几种:
(3)环形 适用于滚轮、轴类及其他外圆表面淬火加热时用,另一种 是内圆表面淬火加热之用。
第四章表面淬火设备
(4)角形 (5)钳形
常用喷嘴的形状有以下几种:
适用于机床、导轨等角形工件的表面淬火加热之用。 专门用于加热齿轮及类似形状的零件。第四章表Βιβλιοθήκη 淬火设备第四章表面淬火设备
晶闸管中频电源缺点:主要是由于受晶闸管元件过电流和过电压 能力的限制,晶闸管中频电源的过载能力较差,因此整个设备的保 护系统较复杂。
第四章表面淬火设备
二、晶闸管中频加热装置的规格及选用
第四章表面淬火设备
第四章表面淬火设备
第四章表面淬火设备
四 感应热处理辅助设备
感应热处理的优点:机械化、自动化程度较高,产品热处理质量 的均匀性和一致性好,同时减轻体力劳动并改善劳动条件。 感应加热用热处理设备主要指淬火机床、感应器以及各种专用的感 应加热调质、退火、淬火生产流水线等。
第四章表面淬火设备
2020/11/29
第四章表面淬火设备
• 表面淬火方法:感应淬火,火焰淬火, 接触电阻加热淬火等。
第四章表面淬火设备
§4.1 感应淬火
感应加热就是利用电磁感应在工件内产生涡流而将工件进 行加热。感应加热表面淬火与普通淬火比具有如下优点:
- 1、下载文档前请自行甄别文档内容的完整性,平台不提供额外的编辑、内容补充、找答案等附加服务。
- 2、"仅部分预览"的文档,不可在线预览部分如存在完整性等问题,可反馈申请退款(可完整预览的文档不适用该条件!)。
- 3、如文档侵犯您的权益,请联系客服反馈,我们会尽快为您处理(人工客服工作时间:9:00-18:30)。
150 2500 f 2 2 x x
(b)比功率的选择:
f 最佳
600 2 x
比功率是指感应加热时工件单位表面积上所吸收的 电功率。比功率选择主要决定于频率和要求硬化层 深度 设备比功率 :设备输出功率与零件同时被加热的面 积比
P P A
P P工 P A
实验表明:
●在工件直径一定的情况下,随着硬化层深度 的增厚,表面残余压应力先增大,达到一定 值后,继续增加硬化层厚度,表面残余压应 力反而减少。 ●残余应力与沿硬化层深度的硬度分布有关。 过渡区硬度降落愈陡,表面压应力虽较大, 但紧靠过渡区的张应力峰值也最大;过渡区 硬度降得愈平缓,过渡区愈宽,张应力峰值 内移且减少,表面的残余压应力也减少。 ●残余应力的分布和钢中的含碳量有关。含碳 量愈高,残余压应力愈大
§4-3:表面淬火方法
一、感应加热表面淬火
工件在交变磁场作用下产生了较高的感
应电势并在表面形成涡流,利用感应电流
在零件表面产生的热效应而使零件加热称 为感应加热;将感应加热后的零件快速冷 却的淬火工艺称为感应加热淬火。
根据设备输出频率高低,感应加热的种类如下表所示:
加热方法 工频 中频 高频、超音频 超高频脉冲
流条;冷却装置等
▲感应圈形状与结构
感应圈的几何形状主要根据工件硬化部位 的几何形状、尺寸及选择的加热方式来确定。 设计时应注意以下几种效应:
▲临近效应:(采用旋转加热方法)
▲环状效应:(有利于圆柱体外表面)
▲尖角效应:(调节线圈与零件间的间隙或改 进感应圈的结构来改善)
▲感应圈尺寸的确定
感应圈管壁厚度应略大于高频电流穿透厚度。
67 / f (mm) 4、感应加热时的驱流和屏蔽
▲导磁体的驱流作用:在感应圈上卡上导磁体后, 磁力线走向发生变化,即由原来圆环效应作用电流 沿着圆环内侧流过变为沿着导磁体缺口流动。
高频导磁体用铁淦氧制成;中频采用硅钢片叠成。
▲屏蔽方法:铜环屏蔽;磁短路
5、高频装置的工作原理 电子管变频装置
M
P+ M P
M +F
M + F+ P
M
F+ P
离表面距离 共析钢表面淬火沿截面温度分布 及淬火后金相组织
离表面距离 45钢表面淬火沿截面温度分布 及淬火后金相组织
2、表面淬火后有效硬化层深度测定 国际上统一采用ISO3754标准 我国制订国标GB5617-85 标准规定:在感应加热或火焰加热后有效硬 化层深度(DS)从零件表面到维氏硬度(HV) 等于规定的硬度值的那一层之间的距离。硬 度测量是在9.8N的负荷下进行。 ● 极限硬度(HV)HL(即规定硬度)是零部件所要
§4-1:表面淬火目的及分类
一、表面淬火目的 在工件表面一定深度范围内获得马氏 体组织,而心部仍保持表面淬火前的组织 状态(调质或正火状态)以获得表面层硬 而耐磨,心部又有足够塑性、韧性的工件。
二、表面淬火分类
要实现表面加热必须给工件以极高的能量密度来加热,使工 件表面的热量来不及向心部传导,造成极大温差。一般认为 若加热装置能提供≥102W/CM2能量密度就可实现表面加热。 (按加热装置不同可分为)
对钢而言简化为: uf 由式可见:电流透入深度随着工件材料电阻 率的增加而增加,随材料的导磁率及电流频 率的增加而减小。 频率越高,电流透入深度越浅;当频率不 变时,温度超过居理点以后,电流透入深度 显著增加。
50300
生产上可简化为: ▲ 20℃时
▲ 800 ℃时
20 20 / f 冷态电流透入深度
2、对奥氏体晶粒度影响
提高相变区加热速度使奥氏体起始晶粒度显著细化。 原因: ◆奥氏体形核不仅在铁素体与碳化物相界,而且在α 相亚结构边界形核;晶核尺寸仅为亚结构边界宽度 1/10—1/5,形成极细的起始晶粒。 ◆在高速加热条件下,起始晶粒度不易长大,从而细 化晶粒。 ◆所形成的奥氏体晶粒内部受热应力和组织应力的作 用,形成许多位错胞。
例一:有一个φ20×700mm的轴,材料为45
钢,要求表面具有较高的耐磨性(50~ 55HRC),沿轴方向尺寸变形不能超过1mm, 采用淬火能否达到要求?不能怎么办?
例二:有一45钢制的φ200mm齿轮,要求表
面硬度为48~55HRC,齿轮承受较大载荷且 具有较好接触疲劳性能。如何处理?采用 整体淬火,整个齿部都会淬硬,使用过程 中易发生脆断,怎么办?
η-设备总效率0.4~0.6
◆感应加热的其他条件及感应器确定后,比功率的
调整依靠感音加热装置的电参数来调整,如:阳极 电压、阳极电流、栅极电流和槽路电压。
(2)淬火加热温度和方式的选择 淬火加热温度应根据材料原始组织、零件 的要求来确定;一般比普通淬火温度高30~ 200℃加热。 ◆常用的加热方式有两种:
第四章:表面淬火
● 表面淬火作为强化金属零件的手段之一,具有以下 特点: 1、经表面处理零件不仅提高表面硬度和耐磨性,而且 与适当预先处理的心部组织相结合,可以获得高的 疲劳强度和强韧性。 2、表面淬火工艺简单,强化效果显著,热处理后变形 小。 3、生产过程易于自动化,生产效率高。
主要内容
1、表面淬火目的 2、表面淬火基本条件 3、快速加热时组织转变特点及 组织结构与性能关系 4、几种表面淬火方法
求最小表面硬度的函数: (HV)HL =0.8 (HV)HS 式中(HV)HS为零件要求最小表面硬度。
3、表面淬火后性能 ◆表面硬度:快速加热,激冷淬火的工件表面 硬度往往比普通淬火高2~5个百分点 ◆耐磨性:快速加热表面淬火后工件的耐磨性 优于普通淬火 ◆疲劳强度:采用正确的表面淬火工艺可以显 著提高零件的抗疲劳性能 ◆残余应力分布:表面淬火后的残余应力大小 和分布与钢种、零件尺寸、硬化层深度及加 热冷却等多种因素有关
残余应力和脆性,又不致降低硬度,
●一般采用的回火方式有炉中回火、自回火和感应
加热回火。
3、感应器设计简介
感应器是将高频电流转化为高频磁场对工件实行 感应加热的能量转换器。 ▲材料
感应器中电流密度可达6000A/m㎡,故所用的
材料的电阻率必须尽可能小,一般采用电解铜,通 常用紫铜制作。 ▲组成: 有效线圈(又称施感导体);汇流接线板;汇
三、激光热处理
1、激光热处理基本原理 为解决吸收率低的问题,可在需硬化表 面涂敷一层能吸收远红外线的涂层,这种 工艺叫“表面黑化”处理。 2、激光热处理工艺 由于激光束光斑尺寸很小,工件表面淬 火时必须靠激光束在淬火工件表面的扫描 运动来实现,目前扫描有三种方法: (1)散焦激光束单程扫描;(2)散焦激光 束交叠扫描;(3)摆动激光束加热。
1、感应加热表面淬火(Induction hardening) 2、火焰加热淬火(Flame / Torch hardening) 3、电接触表面加热淬火(Contact hardening) 4、激光表面加热淬火(Laser hardening) 5、电子束表面加热淬火等(Electron-beam hardening )
频率(KHz) 50×10-3 <10 20~1000 27120
功率密度 (102W×cm-2) 0.1~1 <5 2~10 100~300
1、感应加热基本原理 (1)感应加热的物理基础 (a)电磁感应:当工件放在通有交变电流的感应圈中时,受到 交变磁场作用,其表面产生感应电动势: d e K dt 涡流——零件在感应电势的作用下产生的电流。
3、奥氏体成分均匀化影响
奥氏体成分不均匀性随着加热速度的增加而增加 原因:
◆快速加热条件下形成的奥氏体,其含C量随加热速
度提高而偏离其平衡成分
◆大部分合金元素在碳化物中富集,从而使合金元素
在快速加热时更难固溶于奥氏体并不易均匀化
◆原始组织对奥氏体均匀化有很大影响 4、对过冷奥氏体转变及回火的影响
热态电流透入深度 ▲可见,频率愈高,电流透入深度愈浅;频率不变时, 温度超过居里点以后,电流透入深度显著增加。
800 500/ f
(C) 热传导
(2)感应加热的过程 如右图为工件在感 应加热时涡流在工件表 面分布变化的曲线和感 应加热时冷态和热态的 涡流分布曲线。 透入式加热 概念: 特点:P86 (与传导式加热区别)
If
e e 2 Z R2 X L
Q 0.24I f R t
2
(b)表面效应(集肤效应) 定义:涡流强度随高频电磁场强度由零件表面向内层逐渐减小 而相应减小的规律。
离表面x处的涡流强度为:
x
I x I 0e
式中 Io——表面最大的涡流强度(A)
x——到零件表面的距离(cm)
同时加热法
连续加热法
(3)冷却方式和冷却介质的选择 ●最常用的冷却方式是喷射冷却和浸液冷却法。 ●对于细、薄工件或合金钢齿轮,为减少变形、开
裂,可将感应器与工件同时放于油槽中加热,断电 后冷却,这种加热方法称为埋油淬火法。
●常用的冷却介质有水、油、乳化液等。 (4)回火工艺 ●感应加热一般只进行低温回火,目的是为了降低
c 2 p f
x=I0 x >0时,Ix<I0 x=Δ时, Ix=I0/e=0.368I0 工程上规定:当涡流强度从表面向内层降低到表面
最大涡流强度的36.8%即I0/e时,该处到表面的距离
Δ称为电流透入深度,用δ表示。
δ的大小与金属的电阻率(ρ),相对磁导 率Ur=u/u0和电流频率(f)有关: 2 u0u
3、激光热处理的特点 (1)加热速度快,淬火不用冷却剂 (2)可以进行局部、选择性淬火 (3)几乎没有变形
四、电子束加热表面淬火、 电解液加热表面淬火、 电接触加热表面淬火
●升压变压器:将50HZ、380V电升到高压10KV
●直流整流:将高压工频电流(50HZ)整流为高压直流
(b)比功率的选择:
f 最佳
600 2 x
比功率是指感应加热时工件单位表面积上所吸收的 电功率。比功率选择主要决定于频率和要求硬化层 深度 设备比功率 :设备输出功率与零件同时被加热的面 积比
P P A
P P工 P A
实验表明:
●在工件直径一定的情况下,随着硬化层深度 的增厚,表面残余压应力先增大,达到一定 值后,继续增加硬化层厚度,表面残余压应 力反而减少。 ●残余应力与沿硬化层深度的硬度分布有关。 过渡区硬度降落愈陡,表面压应力虽较大, 但紧靠过渡区的张应力峰值也最大;过渡区 硬度降得愈平缓,过渡区愈宽,张应力峰值 内移且减少,表面的残余压应力也减少。 ●残余应力的分布和钢中的含碳量有关。含碳 量愈高,残余压应力愈大
§4-3:表面淬火方法
一、感应加热表面淬火
工件在交变磁场作用下产生了较高的感
应电势并在表面形成涡流,利用感应电流
在零件表面产生的热效应而使零件加热称 为感应加热;将感应加热后的零件快速冷 却的淬火工艺称为感应加热淬火。
根据设备输出频率高低,感应加热的种类如下表所示:
加热方法 工频 中频 高频、超音频 超高频脉冲
流条;冷却装置等
▲感应圈形状与结构
感应圈的几何形状主要根据工件硬化部位 的几何形状、尺寸及选择的加热方式来确定。 设计时应注意以下几种效应:
▲临近效应:(采用旋转加热方法)
▲环状效应:(有利于圆柱体外表面)
▲尖角效应:(调节线圈与零件间的间隙或改 进感应圈的结构来改善)
▲感应圈尺寸的确定
感应圈管壁厚度应略大于高频电流穿透厚度。
67 / f (mm) 4、感应加热时的驱流和屏蔽
▲导磁体的驱流作用:在感应圈上卡上导磁体后, 磁力线走向发生变化,即由原来圆环效应作用电流 沿着圆环内侧流过变为沿着导磁体缺口流动。
高频导磁体用铁淦氧制成;中频采用硅钢片叠成。
▲屏蔽方法:铜环屏蔽;磁短路
5、高频装置的工作原理 电子管变频装置
M
P+ M P
M +F
M + F+ P
M
F+ P
离表面距离 共析钢表面淬火沿截面温度分布 及淬火后金相组织
离表面距离 45钢表面淬火沿截面温度分布 及淬火后金相组织
2、表面淬火后有效硬化层深度测定 国际上统一采用ISO3754标准 我国制订国标GB5617-85 标准规定:在感应加热或火焰加热后有效硬 化层深度(DS)从零件表面到维氏硬度(HV) 等于规定的硬度值的那一层之间的距离。硬 度测量是在9.8N的负荷下进行。 ● 极限硬度(HV)HL(即规定硬度)是零部件所要
§4-1:表面淬火目的及分类
一、表面淬火目的 在工件表面一定深度范围内获得马氏 体组织,而心部仍保持表面淬火前的组织 状态(调质或正火状态)以获得表面层硬 而耐磨,心部又有足够塑性、韧性的工件。
二、表面淬火分类
要实现表面加热必须给工件以极高的能量密度来加热,使工 件表面的热量来不及向心部传导,造成极大温差。一般认为 若加热装置能提供≥102W/CM2能量密度就可实现表面加热。 (按加热装置不同可分为)
对钢而言简化为: uf 由式可见:电流透入深度随着工件材料电阻 率的增加而增加,随材料的导磁率及电流频 率的增加而减小。 频率越高,电流透入深度越浅;当频率不 变时,温度超过居理点以后,电流透入深度 显著增加。
50300
生产上可简化为: ▲ 20℃时
▲ 800 ℃时
20 20 / f 冷态电流透入深度
2、对奥氏体晶粒度影响
提高相变区加热速度使奥氏体起始晶粒度显著细化。 原因: ◆奥氏体形核不仅在铁素体与碳化物相界,而且在α 相亚结构边界形核;晶核尺寸仅为亚结构边界宽度 1/10—1/5,形成极细的起始晶粒。 ◆在高速加热条件下,起始晶粒度不易长大,从而细 化晶粒。 ◆所形成的奥氏体晶粒内部受热应力和组织应力的作 用,形成许多位错胞。
例一:有一个φ20×700mm的轴,材料为45
钢,要求表面具有较高的耐磨性(50~ 55HRC),沿轴方向尺寸变形不能超过1mm, 采用淬火能否达到要求?不能怎么办?
例二:有一45钢制的φ200mm齿轮,要求表
面硬度为48~55HRC,齿轮承受较大载荷且 具有较好接触疲劳性能。如何处理?采用 整体淬火,整个齿部都会淬硬,使用过程 中易发生脆断,怎么办?
η-设备总效率0.4~0.6
◆感应加热的其他条件及感应器确定后,比功率的
调整依靠感音加热装置的电参数来调整,如:阳极 电压、阳极电流、栅极电流和槽路电压。
(2)淬火加热温度和方式的选择 淬火加热温度应根据材料原始组织、零件 的要求来确定;一般比普通淬火温度高30~ 200℃加热。 ◆常用的加热方式有两种:
第四章:表面淬火
● 表面淬火作为强化金属零件的手段之一,具有以下 特点: 1、经表面处理零件不仅提高表面硬度和耐磨性,而且 与适当预先处理的心部组织相结合,可以获得高的 疲劳强度和强韧性。 2、表面淬火工艺简单,强化效果显著,热处理后变形 小。 3、生产过程易于自动化,生产效率高。
主要内容
1、表面淬火目的 2、表面淬火基本条件 3、快速加热时组织转变特点及 组织结构与性能关系 4、几种表面淬火方法
求最小表面硬度的函数: (HV)HL =0.8 (HV)HS 式中(HV)HS为零件要求最小表面硬度。
3、表面淬火后性能 ◆表面硬度:快速加热,激冷淬火的工件表面 硬度往往比普通淬火高2~5个百分点 ◆耐磨性:快速加热表面淬火后工件的耐磨性 优于普通淬火 ◆疲劳强度:采用正确的表面淬火工艺可以显 著提高零件的抗疲劳性能 ◆残余应力分布:表面淬火后的残余应力大小 和分布与钢种、零件尺寸、硬化层深度及加 热冷却等多种因素有关
残余应力和脆性,又不致降低硬度,
●一般采用的回火方式有炉中回火、自回火和感应
加热回火。
3、感应器设计简介
感应器是将高频电流转化为高频磁场对工件实行 感应加热的能量转换器。 ▲材料
感应器中电流密度可达6000A/m㎡,故所用的
材料的电阻率必须尽可能小,一般采用电解铜,通 常用紫铜制作。 ▲组成: 有效线圈(又称施感导体);汇流接线板;汇
三、激光热处理
1、激光热处理基本原理 为解决吸收率低的问题,可在需硬化表 面涂敷一层能吸收远红外线的涂层,这种 工艺叫“表面黑化”处理。 2、激光热处理工艺 由于激光束光斑尺寸很小,工件表面淬 火时必须靠激光束在淬火工件表面的扫描 运动来实现,目前扫描有三种方法: (1)散焦激光束单程扫描;(2)散焦激光 束交叠扫描;(3)摆动激光束加热。
1、感应加热表面淬火(Induction hardening) 2、火焰加热淬火(Flame / Torch hardening) 3、电接触表面加热淬火(Contact hardening) 4、激光表面加热淬火(Laser hardening) 5、电子束表面加热淬火等(Electron-beam hardening )
频率(KHz) 50×10-3 <10 20~1000 27120
功率密度 (102W×cm-2) 0.1~1 <5 2~10 100~300
1、感应加热基本原理 (1)感应加热的物理基础 (a)电磁感应:当工件放在通有交变电流的感应圈中时,受到 交变磁场作用,其表面产生感应电动势: d e K dt 涡流——零件在感应电势的作用下产生的电流。
3、奥氏体成分均匀化影响
奥氏体成分不均匀性随着加热速度的增加而增加 原因:
◆快速加热条件下形成的奥氏体,其含C量随加热速
度提高而偏离其平衡成分
◆大部分合金元素在碳化物中富集,从而使合金元素
在快速加热时更难固溶于奥氏体并不易均匀化
◆原始组织对奥氏体均匀化有很大影响 4、对过冷奥氏体转变及回火的影响
热态电流透入深度 ▲可见,频率愈高,电流透入深度愈浅;频率不变时, 温度超过居里点以后,电流透入深度显著增加。
800 500/ f
(C) 热传导
(2)感应加热的过程 如右图为工件在感 应加热时涡流在工件表 面分布变化的曲线和感 应加热时冷态和热态的 涡流分布曲线。 透入式加热 概念: 特点:P86 (与传导式加热区别)
If
e e 2 Z R2 X L
Q 0.24I f R t
2
(b)表面效应(集肤效应) 定义:涡流强度随高频电磁场强度由零件表面向内层逐渐减小 而相应减小的规律。
离表面x处的涡流强度为:
x
I x I 0e
式中 Io——表面最大的涡流强度(A)
x——到零件表面的距离(cm)
同时加热法
连续加热法
(3)冷却方式和冷却介质的选择 ●最常用的冷却方式是喷射冷却和浸液冷却法。 ●对于细、薄工件或合金钢齿轮,为减少变形、开
裂,可将感应器与工件同时放于油槽中加热,断电 后冷却,这种加热方法称为埋油淬火法。
●常用的冷却介质有水、油、乳化液等。 (4)回火工艺 ●感应加热一般只进行低温回火,目的是为了降低
c 2 p f
x=I0 x >0时,Ix<I0 x=Δ时, Ix=I0/e=0.368I0 工程上规定:当涡流强度从表面向内层降低到表面
最大涡流强度的36.8%即I0/e时,该处到表面的距离
Δ称为电流透入深度,用δ表示。
δ的大小与金属的电阻率(ρ),相对磁导 率Ur=u/u0和电流频率(f)有关: 2 u0u
3、激光热处理的特点 (1)加热速度快,淬火不用冷却剂 (2)可以进行局部、选择性淬火 (3)几乎没有变形
四、电子束加热表面淬火、 电解液加热表面淬火、 电接触加热表面淬火
●升压变压器:将50HZ、380V电升到高压10KV
●直流整流:将高压工频电流(50HZ)整流为高压直流