粉末冶金学复习资料第三章
第三章粉末冶金
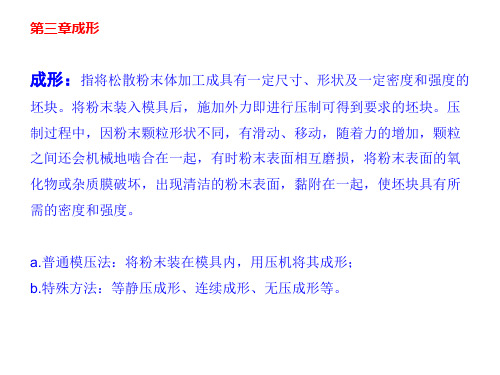
第三章成形 d.弹性后效
加载(或卸载)后经过一段时间应变才增加(或减小)到一定数值的 现象。压制过程中,当卸掉压制力并把坯块从模具内取出后,由于弹性 内应力的作用,坯块发生弹性膨胀,这种现象称为弹性后效。
a.粉末颗粒发生位移,填充孔隙,施加压力,密度增加很快; b.密度达到一定值后,粉末体出现一定压缩阻力,由于位移大大减少, 而变形尚未开始,压力增加,但密度增加很少; c.当压力超过粉末颗粒的临界应力时,粉末颗粒开始变形,使坯块密度 继续增大。
图3-10坯块密度的变化规律
第三章成形
(5)压制压力与坯块相对密度的关系 相对密度指物质的密度与参考物质的密度在各自规定的条件下之比,
第三章成形
退火温度: T退 (0.5 ~ 0.6)T熔
退火气氛: a.还原性气氛(氢、离解氨、转化天然气或煤气) b.惰性气氛 c.真空退火
第三章成形
(2)混合 a.混合:将两种或两种以上不同成分的粉末混合 b. 将相同成分而粒度不同的粉末混合(合批) 混合方法:机械法(干混、湿混)和化学法 机械法:干混用于生产铁基制品;湿混用于生产硬质合金。混料设备有
a.普通模压法:将粉末装在模具内,用压机将其成形; b.特殊方法:等静压成形、连续成形、无压成形等。
第三章成形
1.成形前原料准备 (1)退火
将金属缓慢加热到一定温度,保持足够时间,然后以适宜速度冷却(通 常是缓慢冷却,有时是控制冷却)的一种金属热处理工艺。
金属粉末退火的目的: a.氧化物还原,降低碳和其它杂质的含量,提高粉末的纯度; b.消除粉末的加工硬化,稳定粉末的晶体结构; c.防止超细粉末自燃,将其表面钝化。 加工产品退火的目的: a.降低硬度,改善切削加工性; b.消除残余应力,稳定尺寸,减少变形与裂纹倾向; c.细化晶粒,调整组织,消除组织缺陷。
《粉末冶金原理》复习题教案资料
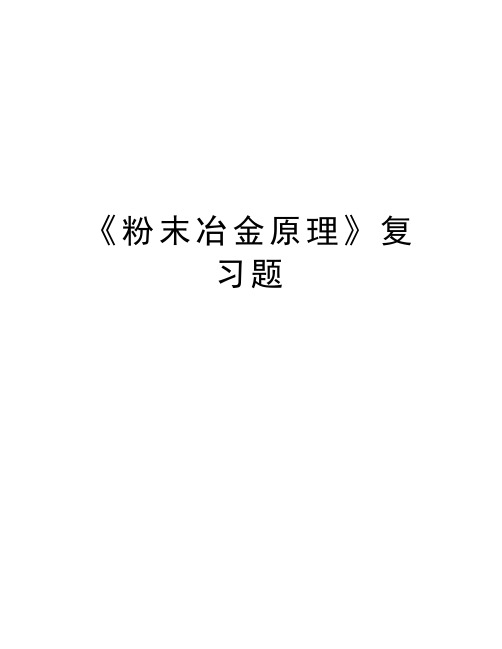
《粉末冶金原理》复习题名词解释临界转速机械研磨时,使球磨筒内小球沿筒壁运动能够正好经过顶点位置而不发生抛落时,筒体的转动速度比表面积单位质量或单位体积粉末具有的表面积(一克质量或一定体积的粉末所具有的表面积与其质量或体积的比值称为比表面积)二次颗粒由多个一次颗粒在没有冶金键合而结合成粉末颗粒称为二次颗粒离解压每种金属氧化物都有离解的趋势,而且随温度提高,氧离解的趋势越大,离解后的氧形成氧分压越大,离解压即是此氧分压。
电化当量这是表述电解过程输入电量与粉末产出的定量关系,表达为每 96500库仑应该有一克当量的物质经电解析出气相迁移细小金属氧化物粉末颗粒由于较大的蒸气压,在高温经挥发进入气相,被还原后沉降在大颗粒上,导致颗粒长大的过程真密度颗粒质量用除去开孔和闭孔的颗粒体积除得的商值。
真密度实际上就是粉末的固体密度似密度又叫有效密度,颗粒质量用包括闭孔在内的颗粒体积去除得的相对密度粉末或压坯密度与对应材料理论密度的比值百分数松装密度粉末在规定条件下自然填充容器时,单位体积内的粉末质量,单位为g/cm3比形状因子将粉末颗粒面积因子与体积因子之比称为比形状因子压坯密度压坯质量与压坯体积的比值相对体积粉末体的相对密度(d=ρ/ρ理)的倒数称为相对体积,用β=1/d表示粒度分布将粉末样品分成若干粒径,并以这些粒径的粉末质量(颗粒数量、粉末体积)占粉末样品总质量(总颗粒数量、总粉末体积)的百分数对粒径作图,即为粒度分布;(一定体积或一定重量(一定数量)粉末中各种粒径粉末体积(重量、数量)占粉末总量的百分数的表达称为粒度分布)粉末加工硬化金属粉末在研磨过程中由于晶格畸变和位错密度增加,导致粉末硬度增加,变形困难的现象称为加工硬化雾化法利用高速气流或高速液流将金属流(其它物质流)击碎制造粉末的方法.二流雾化由雾化介质流体与金属液流构成的雾化体系称为二流雾化快速冷凝将金属或合金的熔液快速冷却(冷却速度>105℃/s),保持高温相、获得性能奇异性能的粉末和合金(如非晶、准晶、微晶)的技术,是传统雾化技术的重要发展假合金两种或两种以上金属元素因不是根据相图规律、不经形成固溶体或化合物而构成的合金体系,假合金实际是混合物保护气氛为防止粉末或压坯在高温处理过程发生氧化而向体系加入还原性气体或真空条件称为保护气氛压制性粉末压缩性与成形性的总称成形性粉末在经模压之后保持形状的能力,一般用压坯强度表示压缩性粉末在模具中被压缩的能力称为压缩性,一般用压坯密度表示粉末粒度一定质量(一定体积)或一定数量的粉末的平均颗粒尺寸成为粉末粒度粉末流动性 50 克粉末流经标准漏斗所需要的时间称为粉末流动性。
粉末冶金复习资料
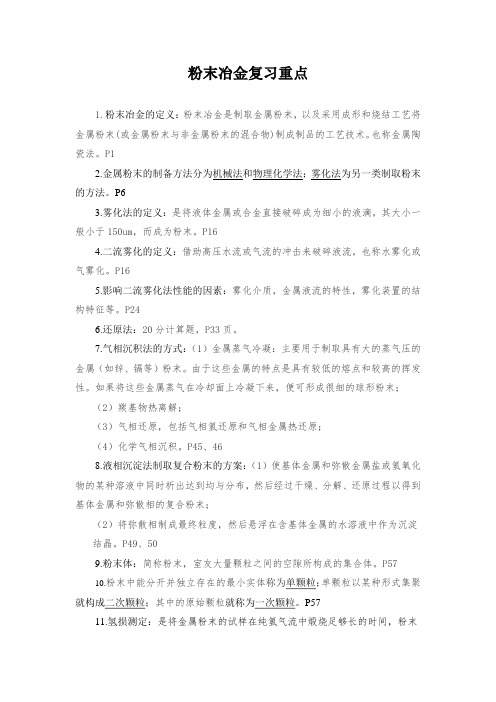
粉末冶金复习重点1.粉末冶金的定义:粉末冶金是制取金属粉末,以及采用成形和烧结工艺将金属粉末(或金属粉末与非金属粉末的混合物)制成制品的工艺技术。
也称金属陶瓷法。
P12.金属粉末的制备方法分为机械法和物理化学法;雾化法为另一类制取粉末的方法。
P63.雾化法的定义:是将液体金属或合金直接破碎成为细小的液滴,其大小一般小于150um,而成为粉末。
P164.二流雾化的定义:借助高压水流或气流的冲击来破碎液流,也称水雾化或气雾化。
P165.影响二流雾化法性能的因素:雾化介质,金属液流的特性,雾化装置的结构特征等。
P246.还原法:20分计算题,P33页。
7.气相沉积法的方式:(1)金属蒸气冷凝:主要用于制取具有大的蒸气压的金属(如锌、镉等)粉末。
由于这些金属的特点是具有较低的熔点和较高的挥发性。
如果将这些金属蒸气在冷却面上冷凝下来,便可形成很细的球形粉末;(2)羰基物热离解;(3)气相还原,包括气相氢还原和气相金属热还原;(4)化学气相沉积。
P45、468.液相沉淀法制取复合粉末的方案:(1)使基体金属和弥散金属盐或氢氧化物的某种溶液中同时析出达到均与分布,然后经过干燥、分解、还原过程以得到基体金属和弥散相的复合粉末;(2)将弥散相制成最终粒度,然后悬浮在含基体金属的水溶液中作为沉淀结晶。
P49、509.粉末体:简称粉末,室友大量颗粒之间的空隙所构成的集合体。
P57 10.粉末中能分开并独立存在的最小实体称为单颗粒;单颗粒以某种形式集聚就构成二次颗粒;其中的原始颗粒就称为一次颗粒。
P5711.氢损测定:是将金属粉末的试样在纯氢气流中煅烧足够长的时间,粉末中的氧被还原生成水蒸气,某些元素与氢生成挥发性化合物,与挥发性金属一同排除,测得试样粉末的质量损失称为氢损。
P62%100⨯--=CA B A 氢损值 式中 A ——粉末试样加烧舟的质量B ——氢中煅烧后残留物加烧舟的质量C ——烧舟质量12.酸不溶物法:粉末试样用某种无机酸溶解,将不溶物沉淀并过滤出来,煅烧后称重,再按下式计算酸不溶物含量。
粉末冶金期末复习.
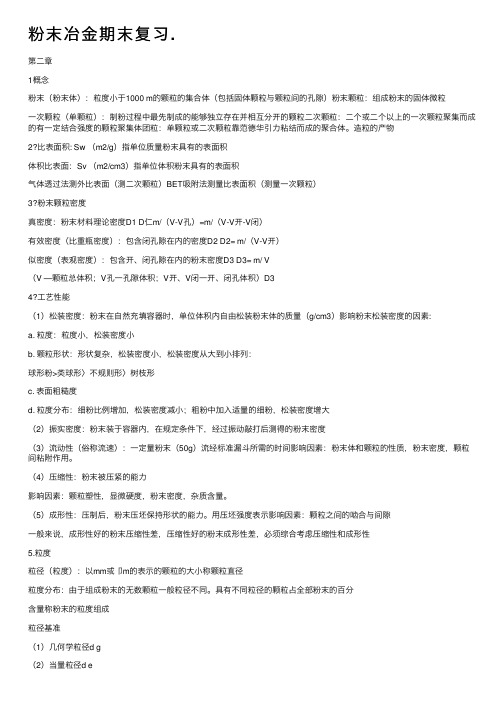
粉末冶⾦期末复习.第⼆章1概念粉末(粉末体):粒度⼩于1000 m的颗粒的集合体(包括固体颗粒与颗粒间的孔隙)粉末颗粒:组成粉末的固体微粒⼀次颗粒(单颗粒):制粉过程中最先制成的能够独⽴存在并相互分开的颗粒⼆次颗粒:⼆个或⼆个以上的⼀次颗粒聚集⽽成的有⼀定结合强度的颗粒聚集体团粒:单颗粒或⼆次颗粒靠范德华引⼒粘结⽽成的聚合体。
造粒的产物2?⽐表⾯积: Sw (m2/g)指单位质量粉末具有的表⾯积体积⽐表⾯:Sv (m2/cm3)指单位体积粉末具有的表⾯积⽓体透过法测外⽐表⾯(测⼆次颗粒)BET吸附法测量⽐表⾯积(测量⼀次颗粒)3?粉末颗粒密度真密度:粉末材料理论密度D1 D仁m/(V-V孔)=m/(V-V开-V闭)有效密度(⽐重瓶密度):包含闭孔隙在内的密度D2 D2= m/(V-V开)似密度(表观密度):包含开、闭孔隙在内的粉末密度D3 D3= m/ V(V —颗粒总体积;V孔⼀孔隙体积;V开、V闭⼀开、闭孔体积)D34?⼯艺性能(1)松装密度:粉末在⾃然充填容器时,单位体积内⾃由松装粉末体的质量(g/cm3)影响粉末松装密度的因素:a. 粒度:粒度⼩,松装密度⼩b. 颗粒形状:形状复杂,松装密度⼩,松装密度从⼤到⼩排列:球形粉>类球形〉不规则形〉树枝形c. 表⾯粗糙度d. 粒度分布:细粉⽐例增加,松装密度减⼩;粗粉中加⼊适量的细粉,松装密度增⼤(2)振实密度:粉末装于容器内,在规定条件下,经过振动敲打后测得的粉末密度(3)流动性(俗称流速):⼀定量粉末(50g)流经标准漏⽃所需的时间影响因素:粉末体和颗粒的性质,粉末密度,颗粒间粘附作⽤。
(4)压缩性:粉末被压紧的能⼒影响因素:颗粒塑性,显微硬度,粉末密度,杂质含量。
(5)成形性:压制后,粉末压坯保持形状的能⼒。
⽤压坯强度表⽰影响因素:颗粒之间的啮合与间隙⼀般来说,成形性好的粉末压缩性差,压缩性好的粉末成形性差,必须综合考虑压缩性和成形性5.粒度粒径(粒度):以mm或⼙m的表⽰的颗粒的⼤⼩称颗粒直径粒度分布:由于组成粉末的⽆数颗粒⼀般粒径不同。
粉末冶金学复习资料

第一章粉末的制取一.粉末制取的方法:机械粉碎法、雾化法、还原法、气相沉积法、液相沉积法、电解法、水热法、纳米及超细粉末的制备技术二.机械粉碎法●固态金属的机械粉碎既可以是一种独立的制粉方法,又可以是其他方法的补充。
●机械粉碎是靠压碎、击碎和磨削等作用,将块状金属、合金或化合物机械地粉碎为粉末的。
●物料最终的粉碎程度:粗碎、细碎✓压碎:碾碎、辊轧、鄂式破碎✓击碎:锤磨✓击碎和磨削多方面作用:球磨、棒磨等机械研磨比较适用于脆性材料,涡旋研磨、冷气流粉碎多用于制取塑性金属或合金的粉末。
1.机械研磨法●研磨的任务(作用)包括:减小或增大粉末粒度;合金化;固态混料;改善、转变或改变材料的性能等。
●研磨后的金属粉末会有加工硬化、形状不规则以及出现流动性变坏和团块等特征。
(1)研磨规律●研磨是粉末冶金工艺中耗时最长、生产效率最低的一个工序。
研磨过程中作用在颗粒材料上的力:冲击、磨耗、剪切以及压缩✓冲击:是一个颗粒体被另一个颗粒体瞬时撞击,这时,两个颗粒体可能都在运动,或者一个颗粒体是静止的。
✓磨耗:由于两物体间的摩擦作用产生磨损碎屑或颗粒。
(较脆弱材料和耐磨性极低的材料)✓剪切:用切断法将颗粒断裂成单个颗粒,而同时产生很少的细屑。
压缩:缓慢施加压力于颗粒体上,压碎或挤压颗粒材料。
(2)影响球磨的因素●决定因素:装料比、球磨筒尺寸、球磨机转速、研磨时间、球磨体与被研磨物料的比例、研磨介质、球体直径等。
●球磨筒尺寸的影响:球筒直径D与长度L之比D/L:D/L>3 硬而脆的材料D/L<3 塑性材料2.介质的影响:物料除可以在空气介质中干磨外,还可以在液体介质中进行湿磨。
✓液体介质:水、酒精、汽油、丙酮等。
✓湿磨的特点:①可减少金属的氧化;②防止金属颗粒的再聚集长大;③减少物料的成分偏析;④防止粉末飞扬,改善劳动环境;⑤湿磨会增加辅助工序,如过滤、干燥等。
3.球体大小对物料的粉碎有很大的影响。
一般是把大小不同的球配合使用。
粉末冶金学

产品性能不同
P.M可生产特殊性能产品,例:高熔点金属、多孔材料、摩擦材料、
磁性或电性能材料;
F.M只能生产普通产品。
4.粉末冶金与熔化冶金的区别
生产工艺不同
P.M工艺
a.传统方法:金属→化学法、物理法、机械法→不同形状、粒度的粉 末→混合→压制→烧结→制品→后处理
b. 先进技术:热固结——压制和烧结同时进行(热压、热挤压、热等
e.旋涡环形喷射:压缩气体从切想方向进入喷嘴内腔,然后以高速喷
出形成一封闭的锥体,金属流在锥底被击碎。
第一章粉末的制取
图2-5二流雾化形式
第一章粉末的制取
图2-7V形水喷射形式
第一章粉末的制取
(2)二流雾化喷嘴
作用:使雾化介质获得高能量、高速度,稳定雾化效率和雾化过程。
图2-6二流雾化喷嘴结构 α—气流与金属流间的交角;A—喷口与金属流轴间的距离; D—喷射宽度;P——漏嘴突出喷嘴部分
7.粉末冶金的发展史
锻压铂(wrought platinum)
熔点:1772℃ 时间:1750~1850年 生产方法:自然铂→清洗干净→压制成形→烧结→热锻→ 锻压铂 生产国家:西班牙、英国、前苏联 发展状况:随着科技的发展,合适的炉子和耐火材料出现。 P.M生产锻压铂的工艺消失,现在采用F.M法。
5.粉末冶金的优缺点
缺点 1.昂贵的粉末 要控制粉末形状、粒度、粒度分布等。 2.昂贵的模具 要承受更大的压力。 3.压机 吨位要足够大。
6.粉末的应用
直接应用 颜料、油墨、试剂、炸药、燃料、食品添加剂; 结构件
烧结铁基零件、不锈钢零件,烧结铜、铝及其合金零件
特殊材料及制品
多孔、磁性、超导材料,自润滑轴承,金属陶瓷,电极,
粉末冶金复习资料
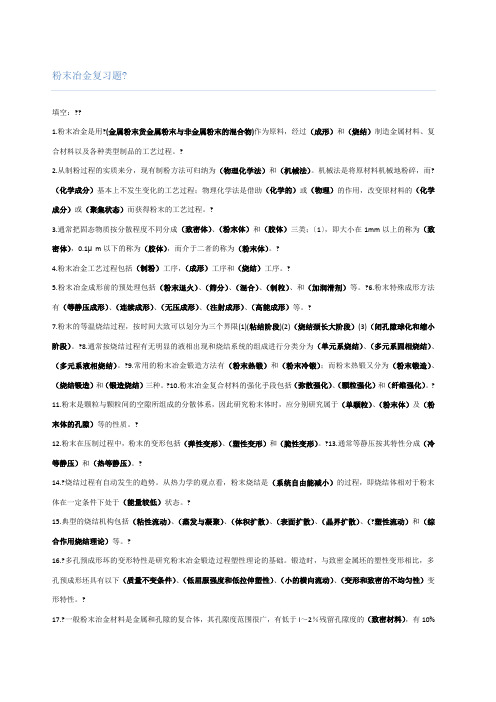
粉末冶金复习题?填空:??1.粉末冶金是用?(金属粉末货金属粉末与非金属粉末的混合物)作为原料,经过(成形)和(烧结)制造金属材料、复合材料以及各种类型制品的工艺过程。
?2.从制粉过程的实质来分,现有制粉方法可归纳为(物理化学法)和(机械法)。
机械法是将原材料机械地粉碎,而?(化学成分)基本上不发生变化的工艺过程;物理化学法是借助(化学的)或(物理)的作用,改变原材料的(化学成分)或(聚集状态)而获得粉末的工艺过程。
?3.通常把固态物质按分散程度不同分成(致密体)、(粉末体)和(胶体)三类;〔1〕,即大小在1mm以上的称为(致密体),0.1μm以下的称为(胶体),而介于二者的称为(粉末体)。
?4.粉末冶金工艺过程包括(制粉)工序,(成形)工序和(烧结)工序。
?5.粉末冶金成形前的预处理包括(粉末退火)、(筛分)、(混合)、(制粒)、和(加润滑剂)等。
?6.粉末特殊成形方法有(等静压成形)、(连续成形)、(无压成形)、(注射成形)、(高能成形)等。
?7.粉末的等温烧结过程,按时间大致可以划分为三个界限(1)(粘结阶段)(2)(烧结颈长大阶段)(3)(闭孔隙球化和缩小阶段)。
?8.通常按烧结过程有无明显的液相出现和烧结系统的组成进行分类分为(单元系烧结)、(多元系固相烧结)、(多元系液相烧结)。
?9.常用的粉末冶金锻造方法有(粉末热锻)和(粉末冷锻);而粉末热锻又分为(粉末锻造)、(烧结锻造)和(锻造烧结)三种。
?10.粉末冶金复合材料的强化手段包括(弥散强化)、(颗粒强化)和(纤维强化)。
?11.粉末是颗粒与颗粒间的空隙所组成的分散体系,因此研究粉末体时,应分别研究属于(单颗粒)、(粉末体)及(粉末体的孔隙)等的性质。
?12.粉末在压制过程中,粉末的变形包括(弹性变形)、(塑性变形)和(脆性变形)。
?13.通常等静压按其特性分成(冷等静压)和(热等静压)。
?14.?烧结过程有自动发生的趋势。
从热力学的观点看,粉末烧结是(系统自由能减小)的过程,即烧结体相对于粉末体在一定条件下处于(能量较低)状态。
第三章 粉末冶金原理粉末概念微观结构性能(合)总结
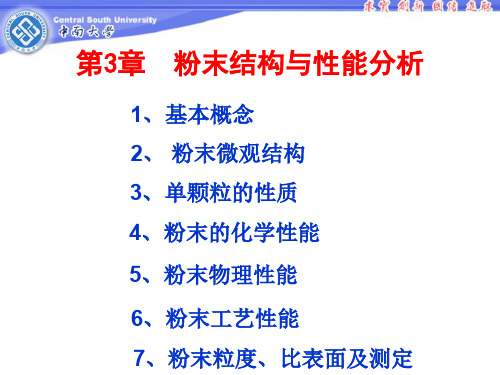
制粉工艺中带入的杂质。如水溶液电解粉末中的氢、气体还
原粉末中溶解的碳、氮等
原材料或生产过程中带入机械夹杂,如SiO2、 Al2O3、硅酸盐、难熔金属等 机械夹杂物一般提高颗粒硬度,降低粉末压制性 能,对材料韧性,特别是冲击韧性影响显著。
活性。
TB5 钛合金beta相热加 工后淬火的金相图片
(2)颗粒表面状态 :
一般来说凹凸不平
外表面:包括颗粒表面所有宏观的凸起和凹进的 部分及宽度大于深度的裂纹。 内表面:包括深度超过宽度的裂纹、微缝及颗粒 外表面连通的孔隙等,但不包括封闭在颗粒内的 闭孔。 多孔性颗粒内表面远比外表面复杂、丰富。 粉末发达的表面积储藏着高的表面能 故在加热时一定要保护气氛。
总孔隙体积、颗粒间的孔隙体积、孔隙数量、分布、形状等 d、粉末体的性质
颗粒性质、平均粒度、颗粒组成、比表面积、松装密度、振实密 度、流动性、颗粒间摩擦状态等
4、化学性能
原材料成分与组成,纯度标准,粉末国家及部级标准GB 、 ISO、BB(包装)
形成合金的加入元素-形成固溶体,化合物合金的生成元素,
S=fD2
V=kD3
f:表面形状因子, k体积形状因子, 二者之比
m=f/k
比形状因子
如规则的球形体: S=D2, V=(1/6)D3 因此,规则球形颗粒的 表面形状因子为π,
体积形状因子等于π/6,
比形状因子等于6. m=6; 边长为a的规则正方体,表面积等于6a2,体积等 于a3,f=6,k=1,m=6;
粉末冶金复习资料
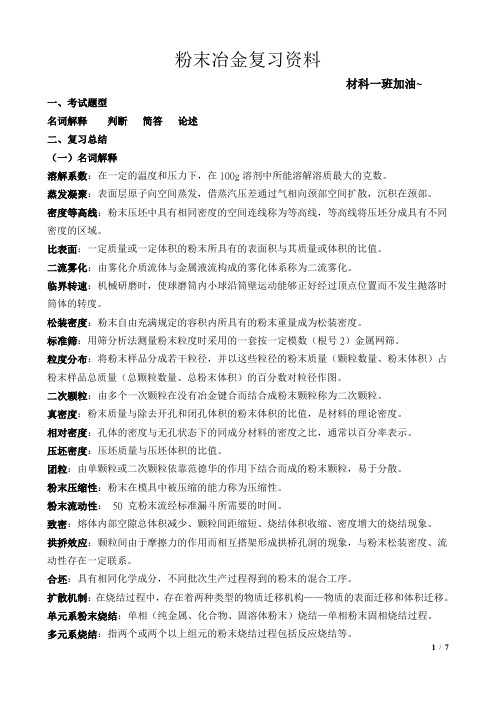
粉末冶金复习资料材科一班加油~一、考试题型名词解释判断简答论述二、复习总结(一)名词解释溶解系数:在一定的温度和压力下,在100g溶剂中所能溶解溶质最大的克数。
蒸发凝聚:表面层原子向空间蒸发,借蒸汽压差通过气相向颈部空间扩散,沉积在颈部。
密度等高线:粉末压坯中具有相同密度的空间连线称为等高线,等高线将压坯分成具有不同密度的区域。
比表面:一定质量或一定体积的粉末所具有的表面积与其质量或体积的比值。
二流雾化:由雾化介质流体与金属液流构成的雾化体系称为二流雾化。
临界转速:机械研磨时,使球磨筒内小球沿筒壁运动能够正好经过顶点位置而不发生抛落时筒体的转度。
松装密度:粉末自由充满规定的容积内所具有的粉末重量成为松装密度。
标准筛:用筛分析法测量粉末粒度时采用的一套按一定模数(根号2)金属网筛。
粒度分布:将粉末样品分成若干粒径,并以这些粒径的粉末质量(颗粒数量、粉末体积)占粉末样品总质量(总颗粒数量、总粉末体积)的百分数对粒径作图。
二次颗粒:由多个一次颗粒在没有冶金键合而结合成粉末颗粒称为二次颗粒。
真密度:粉末质量与除去开孔和闭孔体积的粉末体积的比值,是材料的理论密度。
相对密度:孔体的密度与无孔状态下的同成分材料的密度之比,通常以百分率表示。
压坯密度:压坯质量与压坯体积的比值。
团粒:由单颗粒或二次颗粒依靠范德华的作用下结合而成的粉末颗粒,易于分散。
粉末压缩性:粉末在模具中被压缩的能力称为压缩性。
粉末流动性:50 克粉末流经标准漏斗所需要的时间。
致密:熔体内部空隙总体积减少、颗粒间距缩短、烧结体积收缩、密度增大的烧结现象。
拱挢效应:颗粒间由于摩擦力的作用而相互搭架形成拱桥孔洞的现象,与粉末松装密度、流动性存在一定联系。
合坯:具有相同化学成分,不同批次生产过程得到的粉末的混合工序。
扩散机制:在烧结过程中,存在着两种类型的物质迁移机构——物质的表面迁移和体积迁移。
单元系粉末烧结:单相(纯金属、化合物、固溶体粉末)烧结—单相粉末固相烧结过程。
粉末冶金材料学复习内容五篇范文

粉末冶金材料学复习内容五篇范文第一篇:粉末冶金材料学复习内容“粉末冶金材料学”复习内容一、粉末冶金材料学概述1.简介粉末冶金的特点粉末冶金技术:是以金属粉末或非金属粉末或其混合物为原料,经过成形和烧结,制造金属材料、复合材料以及各种类型制品的工艺技术。
粉末冶金材料:是用粉末冶金技术制得的近全致密或多孔材料(包括制品)特点:1)技术多样性;粉末制备技术, 成形技术, 烧结技术2)工艺复杂性;制粉,制备金属粉末、合金粉末、金属化合物粉末以及包覆粉末;成形,分加压成形和无压成形两类, 其他加压成形方法有等静压成形、粉末轧制、粉末挤压等;烧结, 单元系烧结和多元系烧结,其烧结温度都比所含金属与合金的熔点要低。
烧结后处理, 有精整、熔浸、机加工、热处理(淬火、回火和化学处理)和电镀等.3)性能优越性;材料具有特殊结构和性能, 能制造性能更优的材料(与熔炼法比)粉末高速钢、粉末超合金可避免成分的偏析,保证合金具有均匀组织和稳定性能,同时,这种合金具有细晶粒组织使热加工性大为改善4)零件复杂性;零件的孔隙度可控, 零件的形状、结构复杂5)手段先进性;6)规模扩大性;7)成本低廉性。
2.粉末冶金发展趋势与学科前沿发展趋势① 辐射领域越来越广(研制新材料、开发新应用);② 新技术层出不穷(如喷射成形、注射成形等);③ 多学科交叉(材料、化学、化工、冶金、物理、机械等);④ 高致密化、高性能化、集成化和低成本化;⑤ 非平衡及超细材料和制品的制备,如非晶、微晶、纳米晶、准晶等;⑥ 具有独特组分的复合材料设计与制备。
学科前沿① 粉末制取新技术、新工艺及其过程理论。
向超细、超纯、粉末特性可控方向发展。
② 建立以“近净成形”技术为中心的各种新型固结技术及其过程模拟理论,如粉末注射成形、挤压成形、喷射成形、温压成形、粉末锻造等。
③ 建立以“全致密化”为主要目标的新型固结技术及其过程模拟技术。
如热等静压、微波烧结、高能成形等。
粉末冶金知识讲义(ppt 48页)
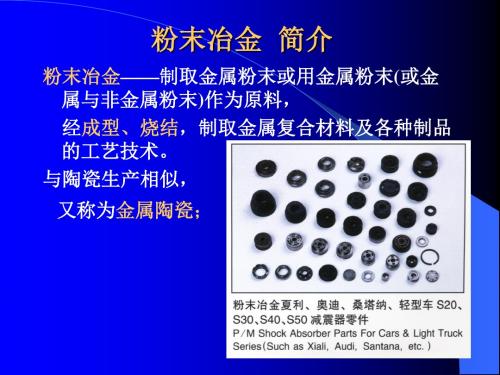
5、粉末性能及测定 成分-
金属粉末、合金粉末、金属化合物粉末;
聚集状态 单颗粒、 二次颗粒; 2-1
外形-球形、多角形、树枝形 2-4;
粒度: 粗粉-150~500微米; 中粉-40~150微米, 细粉-10~40微米; 极细粉-0.5~10微米 超细粉-0.5微米以下; 纳米粉-100纳米及以下;
粉末压坯,在适当的温度和气氛中, 所发生的物理化学变化, 由粉末颗粒的聚集体→晶粒的聚集体; 颗粒之间发生粘结、强度↑,多数情况下密度也↑ 粉末有自动粘结的倾向(比表面积大,能量高), 特别是极细粉末;
烧结是制品达到所要求的性能-关键;
烧结的热力学过程 -5-1 ①烧结初期: 颗粒之间接触点或面 →晶体结合, 经过形核长大→烧结颈;即颗粒界面→晶粒界面, 烧结体不收缩,密度↑极小,强度、导电性明显↑
粉末冶金 简介
粉末冶金——制取金属粉末或用金属粉末(或金 属与非金属粉末)作为原料, 经成型、烧结,制取金属复合材料及各种制品 的工艺技术。
与陶瓷生产相似,
又称为金属陶瓷;
一、发展历史 公元前3000年,古埃及人用C还原氧化铁
制成海绵状的铁, 经高温锻造成致密块状的Fe, 再制出铁器; 本世纪初,电灯W丝问世(爱迪生发明), 使粉末冶金得以迅速发展;
分类和牌号 YG类(钨钴类)
—Y、G:硬、钴,其后数字代表钴含量。 牌号后面的“C”表示为粗晶粒合金,
“X”表示细晶粒合金。 YT类(钛钨类)-除WC、Co外,
还有硬度比WC更高的TiC粉末。 耐磨性高但强度和韧性低。 YW类-新发展起来的硬质合金, 含有TaC,红硬性提高。 用来切削耐热钢、不锈钢、
2、多孔材料 含油轴承:Fe粉+石墨粉+硬脂酸锌=混合、
粉末冶金复习资料全
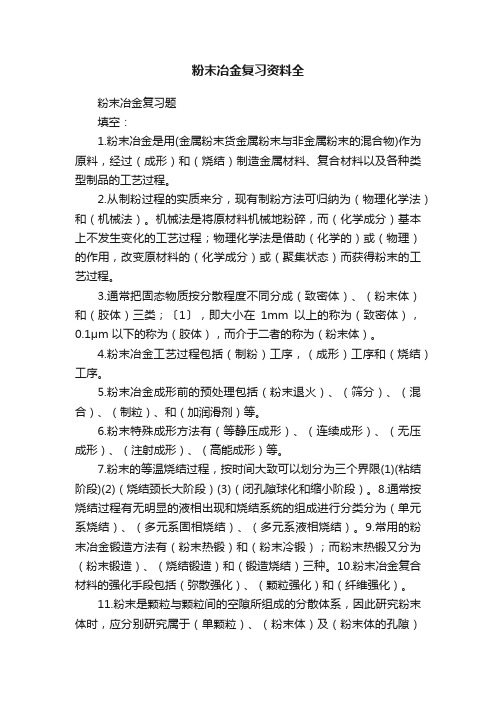
粉末冶金复习资料全粉末冶金复习题填空:1.粉末冶金是用(金属粉末货金属粉末与非金属粉末的混合物)作为原料,经过(成形)和(烧结)制造金属材料、复合材料以及各种类型制品的工艺过程。
2.从制粉过程的实质来分,现有制粉方法可归纳为(物理化学法)和(机械法)。
机械法是将原材料机械地粉碎,而(化学成分)基本上不发生变化的工艺过程;物理化学法是借助(化学的)或(物理)的作用,改变原材料的(化学成分)或(聚集状态)而获得粉末的工艺过程。
3.通常把固态物质按分散程度不同分成(致密体)、(粉末体)和(胶体)三类;〔1〕,即大小在1mm以上的称为(致密体),0.1μm 以下的称为(胶体),而介于二者的称为(粉末体)。
4.粉末冶金工艺过程包括(制粉)工序,(成形)工序和(烧结)工序。
5.粉末冶金成形前的预处理包括(粉末退火)、(筛分)、(混合)、(制粒)、和(加润滑剂)等。
6.粉末特殊成形方法有(等静压成形)、(连续成形)、(无压成形)、(注射成形)、(高能成形)等。
7.粉末的等温烧结过程,按时间大致可以划分为三个界限(1)(粘结阶段)(2)(烧结颈长大阶段)(3)(闭孔隙球化和缩小阶段)。
8.通常按烧结过程有无明显的液相出现和烧结系统的组成进行分类分为(单元系烧结)、(多元系固相烧结)、(多元系液相烧结)。
9.常用的粉末冶金锻造方法有(粉末热锻)和(粉末冷锻);而粉末热锻又分为(粉末锻造)、(烧结锻造)和(锻造烧结)三种。
10.粉末冶金复合材料的强化手段包括(弥散强化)、(颗粒强化)和(纤维强化)。
11.粉末是颗粒与颗粒间的空隙所组成的分散体系,因此研究粉末体时,应分别研究属于(单颗粒)、(粉末体)及(粉末体的孔隙)等的性质。
12.粉末在压制过程中,粉末的变形包括(弹性变形)、(塑性变形)和(脆性变形)。
13.通常等静压按其特性分成(冷等静压)和(热等静压)。
14.烧结过程有自动发生的趋势。
从热力学的观点看,粉末烧结是(系统自由能减小)的过程,即烧结体相对于粉末体在一定条件下处于(能量较低)状态。
哈工大粉末冶金考试复习提纲
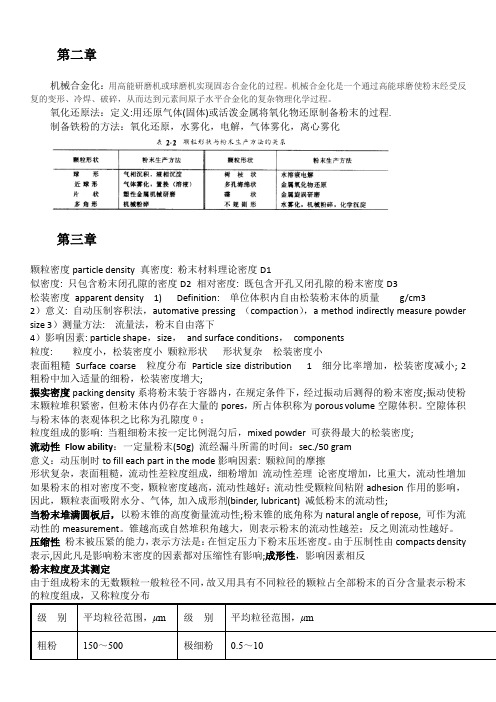
第二章机械合金化:用高能研磨机或球磨机实现固态合金化的过程。
机械合金化是一个通过高能球磨使粉末经受反复的变形、冷焊、破碎,从而达到元素间原子水平合金化的复杂物理化学过程。
氧化还原法:定义:用还原气体(固体)或活泼金属将氧化物还原制备粉末的过程.制备铁粉的方法:氧化还原,水雾化,电解,气体雾化,离心雾化第三章颗粒密度particle density 真密度: 粉末材料理论密度D1似密度: 只包含粉末闭孔隙的密度D2 相对密度: 既包含开孔又闭孔隙的粉末密度D3松装密度apparent density 1) Definition: 单位体积内自由松装粉末体的质量g/cm32)意义: 自动压制容积法,automative pressing (compaction),a method indirectly measure powder size 3)测量方法: 流量法,粉末自由落下4)影响因素: particle shape,size,and surface conditions,components粒度: 粒度小,松装密度小颗粒形状形状复杂松装密度小表面粗糙Surface coarse 粒度分布Particle size distribution 1 细分比率增加,松装密度减小; 2 粗粉中加入适量的细粉,松装密度增大;振实密度packing density系将粉末装于容器内,在规定条件下,经过振动后测得的粉末密度;振动使粉末颗粒堆积紧密,但粉末体内仍存在大量的pores,所占体积称为porous volume空隙体积。
空隙体积与粉末体的表观体积之比称为孔隙度θ;粒度组成的影响: 当粗细粉末按一定比例混匀后,mixed powder 可获得最大的松装密度;流动性Flow ability:一定量粉末(50g) 流经漏斗所需的时间:sec./50 gram意义:动压制时to fill each part in the mode影响因素: 颗粒间的摩擦形状复杂,表面粗糙,流动性差粒度组成,细粉增加流动性差理论密度增加,比重大,流动性增加如果粉末的相对密度不变,颗粒密度越高,流动性越好;流动性受颗粒间粘附adhesion作用的影响,因此,颗粒表面吸附水分、气体, 加入成形剂(binder, lubricant) 减低粉末的流动性;当粉末堆满圆板后,以粉末锥的高度衡量流动性;粉末锥的底角称为natural angle of repose, 可作为流动性的measurement。
粉末冶金知识点

1.粉末冶金定义:由粉末制备、粉末成形、高温烧结以及加工热处理等重要过程组成的材料制备和生产的工程技术。
2.工艺过程:粉末的制备、粉末的加工成形、粉末的烧结以及烧结后处理四个工序。
3.特点:能耗低、材料利用率高以及低成本等优点;与普通熔炼方法相比,有如下特点:1)粉末冶金能生产用普通熔炼无法生产的具有特殊性能的材料。
a.能控制制品的孔隙度b.能利用金属和金属、金属和非金属的组合效果,生产具有各种特殊性能的材料c.能生产各种复合材料2)粉末冶金生产的材料,与普通熔炼相比,性能优越。
a.高合金元素含量粉末冶金材料的性能比熔炼法生产的合金材料要好。
b.粉末冶金法还可用来生产难熔金属材料或制品。
c.在制造机械零件方面,粉末冶金法是一种少切削或无切削的新工艺,可以大大减少机加工量,节约金属材料,提高劳动生产率。
缺点:粉末冶金法成本高,制品的大小和形状受到一定的限制,烧结零件的韧性较差。
第二章.粉体制备的原理与技术1.粉体制备是粉末冶金的第一个重要步骤。
2.方法:1)在固态下制备粉末的方法:机械粉碎法和电化学腐蚀法、还原法、还原-化合法、高温反应合成法2)在液态下制备粉末的方法:雾化法、置换法、溶液氢还原法、水溶液电解法、熔盐电解法3)在气态下:蒸汽冷凝法、热离解法、气相氢还原法、化学气相沉积法3.机械粉碎是靠压碎、碰撞、击碎和磨削等作用,将粗颗粒金属或合金机械的粉碎成粉末的过程。
4.球磨的三种情况:1)球磨机转速慢时,球和物料沿筒体上升至坡度角,然后滚下,称为泻落。
此时物料粉碎主要靠球的磨擦作用2)球磨转速较高时,球在离心力作用下,随着筒体上升至比第一种情况更高的高度,然后在重力作用下掉下来,称为抛落。
这时物料不仅靠球与球之间的磨擦作用,主要靠球落下时的冲击作用被粉碎,其效果最好3)继续增加球磨机的转速,当离心力超过球体的重力时,紧靠球磨筒内衬板的球不脱离筒壁而与筒体一起回转,此时物料的粉碎作用停止。
这种转速称为临界转速。
粉末冶金原理总复习题2011详解
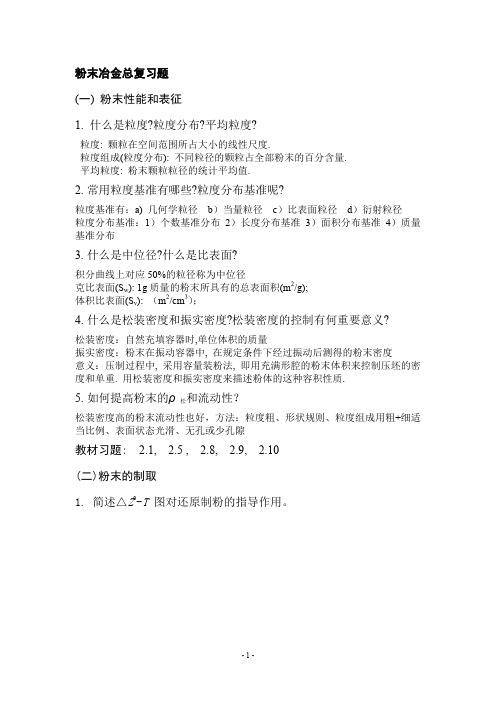
粉末冶金总复习题(一) 粉末性能和表征1. 什么是粒度?粒度分布?平均粒度?粒度: 颗粒在空间范围所占大小的线性尺度.粒度组成(粒度分布): 不同粒径的颗粒占全部粉末的百分含量.平均粒度: 粉末颗粒粒径的统计平均值.2.常用粒度基准有哪些?粒度分布基准呢?粒度基准有:a) 几何学粒径b)当量粒径c)比表面粒径d)衍射粒径粒度分布基准:1)个数基准分布2)长度分布基准3)面积分布基准4)质量基准分布3.什么是中位径?什么是比表面?积分曲线上对应50%的粒径称为中位径克比表面(S w): 1g质量的粉末所具有的总表面积(m2/g);体积比表面(S v): (m2/cm3);4.什么是松装密度和振实密度?松装密度的控制有何重要意义?松装密度:自然充填容器时,单位体积的质量振实密度:粉末在振动容器中, 在规定条件下经过振动后测得的粉末密度意义:压制过程中, 采用容量装粉法, 即用充满形腔的粉末体积来控制压坯的密度和单重. 用松装密度和振实密度来描述粉体的这种容积性质.5.如何提高粉末的ρ松和流动性?松装密度高的粉末流动性也好,方法:粒度粗、形状规则、粒度组成用粗+细适当比例、表面状态光滑、无孔或少孔隙教材习题: 2.1, 2.5 , 2.8, 2.9, 2.10(二)粉末的制取1. 简述△Z0-T图对还原制粉的指导作用。
3. 欲得细W 粉,应如何控制各种因素?(1) 采用两阶段还原法,并控制WO 2的粒度细; (2)减少WO 3的含水量和杂质含量; (3)H 2入炉前应充分干燥脱水以减少炉内水蒸气的浓度; (4)增大H 2流量(有利于反应向还原方向进行,有利于排除水蒸气使WO 3在低温充分还原,从而可得细W 粉); (5)采用顺流通H 2法; (6)减小炉子加热带的温度梯度; (7)减小推舟速度和舟中料层的厚度; (8)WO3中混入添加剂(如重铬酸氨的水溶液);4. 用雾化法制取金属粉末有哪些优点?优点: ① 易合金化 — 可制得预合金粉末(因需熔化), 但完全预合金化后, 又易使压缩性下降. 一般采用部分预合金.② 在一定程度上, 粒度、形状易控制.③ 化学成分均匀、偏析小, 且化学成分较还原粉为纯.④ 生产规模大.5. 简述水雾化和气体雾化法的基本原理。
粉末冶金学

Ⅰ还原法
用还原剂还原金属氧化物及盐类来生产金 属粉末是一种最广泛采用的制粉方法。 MeO(金属氧化物)+X(还原剂)=Me+XO 那么到底哪些物质能做哪些氧化物的还原 剂呢?这可由金属氧化物的标准生成自由 能图中得出:
氧化物的标准生成自由能-温度图
氧化物的标准生成自由能-温度图的说明
随温度升高,△G°增大,各种金属的氧化反应愈难进 行,由于随温度升高,金属对氧的亲和力减小。因此, 还原金属氧化物通常要在高温下进行 △G°-T关系线在相变温度处,特别是在沸点处发生明 显的转折,这是由于系统的熵在相变时发生了变化。 CO生成的△G°-T关于系统得走向是向下的;即CO的 △G°随温度升高而减小。即这条线与很多金属氧化物 的△G°相交。这说明在一定温度下碳能还原很多金属 氧化物。如Fe、W的氧化物。 2H2+O2=2H2O的△G°-T关系线在Cu、Fe、Ni、Co、 W等氧化物的关系线以下,说明在一定条件下氢可以还 原Cu、Fe、Ni、Co、W等氧化物 位于图中最下面的几条关系线所代表的金属如Ca、Mg 等与氧的金和力最大。所以Ti、Zr、Th、U等氧化物要 用Ca、Mg作还原剂,这就是所谓的金属热还原。 在同一温度下,图中位置愈低的氧化物,其稳定性愈大, 即该元素对氧的亲和力愈大。
晶粒
各种粉末实物图
锌粉
铁粉
合成金刚石粉
不锈钢粉
粉末实物照片
纯钨粉
a)
b
Al2O3和C粉
1mm
粉末颗粒的形状
球形、近球形、片状、多角形、树枝状、多孔海绵状、碟状、不规则形
§2-2 粉末的性能
1、化学成分:主要金属的含量和杂质的含 量 2、物理性能 :颗粒密度,显微硬度 ,颗粒大 小,粒度组成,比表面积 3、工艺性能:包括松装密度、摇实密度、 流动性、压缩性和成型性。
西华大学粉末冶金复习题

第一章粉末的制取一.名词解释1.粉末冶金: 粉末冶金是用金属粉末(或者金属粉末与非金属粉末的混合物)作为原料,经过成形和烧结制成金属材料、复合材料以及各种类型制品的工艺过程。
2.雾化法:利用高速气流、液流或者通过离心力将金属流(其他物质)击碎并冷却凝固制造粉末的方法。
3.化学气相沉积:气相沉积是通过某种形式的能量输入,使气相物质发生气-固相变或者气相化学反应,生成金属或陶瓷粉末。
二.填空题1.机械粉碎是靠压碎、击碎和磨削等作用,将块状金属或合金机械地粉碎成粉末的。
2.机械制粉的本质是将动能转变为表面能,机械制粉适合脆性材料。
3.球磨制粉的基本原则是提高磨球的动能,提高磨球的有效碰撞几率。
4.冷气流粉碎法利用高速高压的气流带着较粗的颗粒通过喷嘴轰击于击碎室的靶子上,压力立刻从高压降到 0.1 MPa,发生绝热膨胀,产生加速效应和冷却效应,造成颗粒的破碎。
5.机械粉碎法是借机械作用破坏固体金属原子的结合,雾化法是克服液体金属原子间的结合使之分散成粉末,所以雾化法所消耗的外力比机械粉碎法小得多。
6.金属液流在气流作用下分为负压紊流区、原始液滴形成区、有效雾化区和冷却凝固区四个区域。
7. 物理蒸发冷凝制粉是一种制备超微金属粉末的重要方法,采用不同的输入方式,使金属汽化,然后再在冷凝壁上沉积从而获得金属粉末。
8.化学气相沉积制粉包含化学反应、均相形核、晶粒长大和团聚四个过程。
9.羰基物热离解法中的羰基物是易挥发的液体或易升华的固体,这些羰基化合物很容易分解生成金属粉末和 CO 。
利用羰基物热离解法可以对金属进行提纯、制备合金粉末和包覆粉末。
10.球磨法的四个基本要素是磨球、球磨筒、研磨物料和研磨介质。
11.雾化制粉包括雾化、聚并和凝固三个过程,提高雾化制粉效率的两大准则是能量交换准则和快速冷凝准则。
12.二流雾化是利用高速气流、高速液流将金属流(其他物质流)击碎并冷却凝固制造粉末的方法。
三.简答题1.机械制粉时湿磨的优点有哪些?(1)可以减少金属氧化(2)防止金属颗粒的再聚集和长大(3)可减少物料的成分偏析并有利于成型剂的均匀分布(4)浇入表面活性物质时可促进粉碎作用(5)可减少粉尘飞扬,改善劳动条件2.冷气流粉碎法的基本原理是什么?利用高速高压气流带着较粗大的颗粒通过喷嘴轰击在靶子上,压力立即从高压降到0.1MPa,发生绝热膨胀,使金属靶和击碎室温度降到室温下甚至零下以下,冷却了的颗粒就被粉粹。
- 1、下载文档前请自行甄别文档内容的完整性,平台不提供额外的编辑、内容补充、找答案等附加服务。
- 2、"仅部分预览"的文档,不可在线预览部分如存在完整性等问题,可反馈申请退款(可完整预览的文档不适用该条件!)。
- 3、如文档侵犯您的权益,请联系客服反馈,我们会尽快为您处理(人工客服工作时间:9:00-18:30)。
第三章粉末成形技术§3.1 成形前的粉末冶金§3.2 模压成形技术§3.3 等静压成形§3.4 粉末连续成形§3.5 粉浆浇注§3.6 粉末注射成形第一节成形前的粉末冶金(成形料准备)目的:准备具有一定组成和物理工艺性能的成形混合料一、对成形料的要求(以铁基粉末冶金为例)(一)成分要求1. 主要元素:Fe -符合一定标准2. 合金元素:种类很多•作用:提高力学、物理性能、控制尺寸稳定性•加入方式:元素混合、预合金状态比较(下页图)!•注意:石墨-特殊的合金元素、多功能性!3. 成形剂和润滑剂•Fe基常用:硬脂酸、硬脂酸锌(锂)、石墨、硫磺、机油等•比较:S在粉末烧结钢与铸钢中的不同作用!•机油的作用: 1)防止比重偏析2)减少粉尘 3)严重降低粉末流动性:用量严格控制!(二)成形料粒度和松装比重的调整1. 成形料粒度和粒度组成的调整(1)原料粒度影响制品性能(2)根据制品性能要求来确定粒度和粒度组成•高强度结构件:细粉,范围宽•含油轴承:稍粗、范围窄(一般 -80~100目2. 成形料松装密度的调整松装密度是最重要的工艺性能之一!如何调整:(1)粉末筛粉分级后根据要求合批;(2)粉末中加入机油,显著降低松装密度;(3)粉末退火后球磨,松装密度随球磨时间变化二、原料金属粉末的还原、退火(Reduction or annealing)✓作用:1.降低氧碳含量,提高纯度2.消除加工硬化,改善粉末压制性能(前者亦然)3.消除长期放置所吸附气体等✓注意:此项工作绝大多数由粉末生产厂家完成三、分级•分级:将粉末按粒度大小分成若干等级。
•常用分级方法:✓筛分分级:Screening by screens of various mesh sizes.✓旋风分级、离心分级、沉降分级等。
✓粉末的粒度及粒度组成不同,影响压制和烧结工艺,且对产品的最终性能也有重要影响!采用细颗粒粉末制成的产品,其强度较粗颗粒的高韧性也好四、合批与混合(blending,mixing)合批:同质、不同粒度粉末混和均匀过程;混合:将不同成分(材质)的粉末混和均匀过程(一)合批和混合的目的1. 不同成分混合均匀;2. 消除运输过程中产生的偏析或生产过程中不同批号粉末之间的性能差异3. 混入合金元素4. 调整松装密度和流动性5. 混入润滑剂、成形剂等(二)影响混合的因素1.粉末特性: 比重、粒度及组成、相对含量等2.装料量、球料比、研磨体的尺寸及其搭配 3.混合机的结构与转速 4. 混合方式(1)机械法混合:多种原料粉末在混料机中混合均匀得到混合料。
机械混合分为:干混、湿混干混:在空气或惰性气体中混合,铁基及其它粉末冶金零件的生产(多不采用磨介);湿磨混合法:在液体介质中混合,多同时加入磨介(球)。
广泛应用于硬质合金、含易氧化组分材料;例如:WC与Co粉之间除产生一般的混合均匀效果,还发生显著的细化效果,一般采用工业酒精作为研磨介质湿磨的主要优点:a.有利于环境保护b.无粉尘飞扬和减轻噪音c.提高破碎效率,有利于粉末颗粒的细化d.保护粉末不氧化(2)化学法混合:多在溶液中,通过反应同时生成均匀混合的产物(或前驱体),或包覆粉末。
混合较机械法更为均匀,可以实现原子尺度的混合•例:A. W-Cu-Ni包覆粉末的制造工艺:• W粉+Ni(NO3)2溶液→混合→热解还原(700- 750℃)→ W-Ni包覆粉 + 溶液→混合→热解还原(400-450℃)→W-Cu-Ni包覆粉末CuCl2• B. Cu-Al2O3复合包覆粉末的制备:•Cu(NO3)2+Ni(NO3)2溶液→加氨水(pH)→过滤、洗涤、干燥、煅烧→CuO+Al2O3→ H2还原→Cu-Al2O3复合粉末五、造粒(制粒)✓目的——获得团粒:a.改善细小颗粒或硬质粉末的成形性;b.添加粘结剂、改善流动性;c.进行自动压制或压制形状较复杂的大型P/M制品; d.减小颗粒间的摩擦力,大幅度降低颗粒运动时的摩擦面积✓原理:借助于聚合物的粘结作用将若干细小颗粒形成团粒✓制粒方法: a.擦筛制粒—传统硬质合金生产b.旋转盘制粒c.挤压制粒d.喷雾干燥—最先进的制粒方法之一第二节模压成形技术(Compaction Technique)一、概述模压成形是将金属粉末或粉末混合料装入钢制压模(阴模)中,通过模冲对粉末加压,卸压后脱模,得到压坯的过程。
(一)模压成形的特点1.效率高;2. 成本较低;3. 工序少;4. 应用受限(压坯尺寸、形状、密度等)(二)模压成形的发展方向•高强度、高精度、复杂形状结构零件的生产(三)模压成形工序:二、称料和装粉(一)称料称料量通常称为压坯的单重(允许一定的误差)。
压坯的单重可按以下公式计算: Q = V× d× K•式中:Q--单件压坯的称料量(单重),kg;V--制品的体积(由制品图算出),m3;d--制品要求密度,kg/m3;K--重量损失系数。
•称料方法有两种:(1)重量法;(2)容量法。
(二)装料(粉)•将所称量的粉末装入模具中时,要求粉末在模腔内分布均匀、平整,以保证压坯各部分压缩比一致。
1.装粉要求:保证各高度(料腔)处装填系数相同!2. 基本方法:(1)手工装粉—重量法➢要求:☆保证粉料重量在允许误差范围内;☆装料均匀,尤注意边角处的充填;☆不能过分振动阴模,防止比重轻的组元上浮产生偏析☆多台阶压坯,要严格控制各料腔的装填高度。
•(2)自动装粉—容量法装于料仓中的粉末,通过送料器自动地送入阴模模腔中。
自动装料是自动压制的一个重要的工艺步骤!常用的装料方式有:●落入(下)法、吸入法、多余装料法、超满装料法、零腔装料法、不满装料法(图)三、压制(一)压制行程1.定义:为得到一定密度压坯,模冲压制粉末时必须移动的最小距离。
压制行程等于粉料在阴模中的松装高度与压坯高度之差。
2.控制方法:(1)模冲行程控制法:采用高度限位块、行程开关等;✓高度精度高,但密度误差可能大,应严格控制装粉量!(2)压制压力控制法•根据密度-压力关系,控制压机压力(压力表读数)各压坯密度较一致,但高度误差可能较大,应严格控制装粉量,压力表精度要高!实际生产中:两种方法结合使用(二)压制方式及其选择(三)压制压力、保压时间、压制速度的选择1. 压制压力➢根据密度-单位压制压力关系(经验公式或曲线)→确定单位压制压力→计算总压制压力→选择压机吨位2.保压时间 ;根据压坯材质和结构形状复杂程度而定3.压制速度(后述)四、脱模(一)脱模的基本方式1.顶出式脱模:阴模固定不动,通过上下模冲的运动将压坯从阴模中脱出。
又分:下顶出——手动压制中常用;上顶出——自动压制中常用2. 拉下式脱模:上模冲撤回,阴模向下阴模拉动,使压坯脱出。
(二)脱模的基本原则• 1. 速度快、连续平稳;2. 对侧向加压压坯,先撤垂直压力,后撤侧向压力 3. 合理选择脱模方式:a.柱状压坯,可顶出或拉下式 b.带发兰压坯多拉下式c.强动压制多拉下式(拉下式脱模速度快,更适合大规模生产)五、模压成形新技术(一)粉末高速压制成形(High velocity compaction,HVC)压制压力600-1000MPa、压制速度2-30m/s下对粉末进行高能锤击:●可将压坯密度提高0.3g/cm3以上;结合模壁润滑,生坯密度可达7.6g/cm3以上;结合模壁润滑加温压,生坯密度可达7.7g/cm3。
高速压制(HVC—High Velocity Compaction)✓以足够的冲击能量,瞬时作用于模腔内已预除气体的粉末体,使颗粒快速移动和变形,实现高致密和稳态动压成形。
✓特有的“绝热压制”特征,高冷态压制密度,低静摩擦系数和弹性后效值;作为常规模压技术极限外延,具有“高密度、高强度、高精度、低成本”优势。
✓瑞典Hydropulsor专利技术,兼具动态压制的高能量冲击和传统压制的高速平稳双重特征,适用于金属、陶瓷和聚合物的成形。
✓与高致密成形(复压、复烧、热压、热等静压、温压)相比,具有密度、效率和形状等优势;与动压成形(冲击、爆炸、模锻)相比,具有高速、平稳和精密等优势。
(二)粉末温压成形(Warm compaction pressing)1. 概述(1)定义:添加专门粘结剂的粉末与模具被加热到较低温度(一般≤150℃)后进行的刚模压制。
☆除粉末与模具需加热以外,与常规模压几乎相同;☆与热压不同,温压加热温度低(热压温度高于主要组分的再结晶温度)。
(2)温压技术开发的原动力✓汽车特别是轿车工业急需低成本、高性能的铁基PM零部件。
• A. 高致密度压坯烧结可以获得高密度高性能零部件;• B. 材质调整和后处理也可改善铁基PM零部件力学性能,但:潜力已几乎发挥到极限。
•提高铁基P/M零部件密度的技术途径☆复压-复烧工艺:密度92%左右,形状复杂程度有限,成本较高☆浸铜(熔渗):密度大于95%,表面较粗糙,形状、成分设计有限,成本高☆液相烧结:密度可达93%,变形较大,零件精度低,尺寸控制困难,成分设计有限☆粉末锻造:全致密,但尺寸精度低,形状受限,成本昂贵(3)温压的特点☆低成本制造高性能P/M零部件相对成本:若WP=1.0,则1P1S0.8;2P2S=1.3;CI(浸铜)=1.5;PF=1.8( 工序少,模具寿命长,零件形状复杂程度提高)☆压坯密度高相对密度提高0.02-0.06,即孔隙度降低2-6%☆便于制造形状复杂的零部件低脱模压力:↓30%;高压坯强度,↑25-100%;弹性后效小:↓50%;密度分布均匀,密度差:↓0.1-0.2g/cm3零件强度高(同质、同密度)极限抗拉强度↑10%,烧结态达1200MPa;疲劳强度↑10%若经适度复压,与粉末锻件相当☆零件表面质量高精度提高2个IT级,模具寿命长(模具磨损少)☆压制压力降低同压坯密度时,压力降低140MPa,提高压机容量☐温压保持了传统模压的高效、高精度优势☐提高了铁基零部件的性能和服役可靠性☐拓宽了部件的应用范围是“导致铁基粉末冶金技术革命的新技术2. 温压工艺粉末原料(扩散粘结铁粉+新型润滑剂)↓粉末加热(130℃)↓阴模装粉(130-150℃)↓温压↓温压压坯↓烧结↓温压零部件3. 温压加热系统阴模加热:多采用电阻加热●粉末加热:★热油循环加热:温控稳定性好,不易过热★微波加热:加热速度快,但存在过热和微波;外泄(安全)问题★感应加热:与微波相似★电阻加热:加热速度较快,存在过热问题4. 温压过程的实质(1)塑性变形得以充分进行加工硬化速度和程度降低(2)减小粉末与模壁间的摩擦、降低粉末颗粒间的内摩擦,便于颗粒间的相互填充和颗粒重排颗粒的塑性变形进一步促进颗粒重排,成为后期的主导致密化机理。