膜片弹簧的力学性能分析.
汽车膜片弹簧分析

位移云图
5.结果提取
节点504590 节点480181 位移d与内缘点Ty位移的关系 (内缘点位移为3mm介于INCR5和INCR6之间)
5.结果提取
变形关系曲线图
位移d(0≤d≤5)与零件3 的任意一内缘点的变形的曲线图
内缘点Ty位移
5.结果提取
总力大小
midas NFX
汽车膜片弹簧分析
汇报内容
1. 简介
2.技术难点
3.模型的建立
4.边界条件和工况
5.结果提取
1.意义及题目简述
膜片弹簧简介
通过合理地选择构参数, 膜片弹簧可以在简化汽车 离合器构件的同时提供适 宜的非线性弹性特性。 利用有限元的方法研究膜 片弹簧的弹性特性。 考虑膜片弹簧与压盘和支 承环之间的接触、摩擦等 实际因素,建立膜片弹簧大 端受载的有限元模型,分析 得到膜片弹簧的载荷-位移 特性和 载荷-应变特性。
2.题目简述及意义
某产品的有限元分析
模型说明: 材料: 不锈钢304 边界: 零件1 和 2 固定 载荷: 零件 4(共 12 个) 施加位移 d,方向垂直于 外表面,并使零件 4 压 紧零件3 。 接触:各零部件之间均为 接触关系 模型文件:analysis.stp
结果分析:
3.模型的简化和分网
网格划分的探索
延伸:不适用于曲面 填充:上下表面有相等数量的网格 扫描:不适用于多个变截面 投影:投影面只能是一个 偏移:适用于曲面
延伸
填充
扫描
零件3特点:等厚度 平面与曲面结合 投影
偏移
3.模型的建立
网格模型
零件3
零件1,零件2
整体模型 零件4
3.模型的建立
弹簧系统的力学性质与振动频率分析
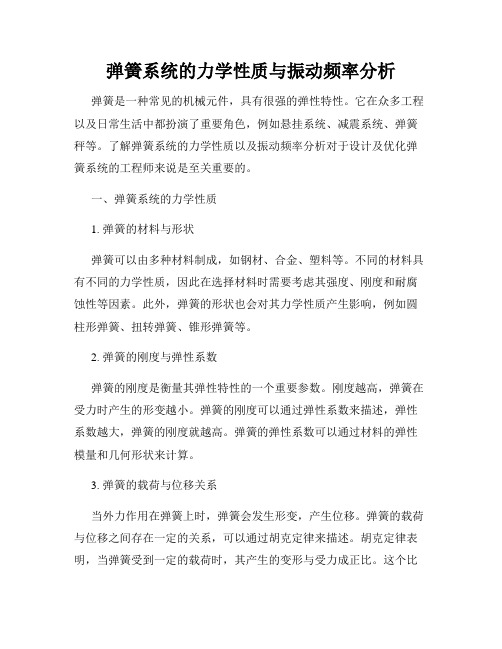
弹簧系统的力学性质与振动频率分析弹簧是一种常见的机械元件,具有很强的弹性特性。
它在众多工程以及日常生活中都扮演了重要角色,例如悬挂系统、减震系统、弹簧秤等。
了解弹簧系统的力学性质以及振动频率分析对于设计及优化弹簧系统的工程师来说是至关重要的。
一、弹簧系统的力学性质1. 弹簧的材料与形状弹簧可以由多种材料制成,如钢材、合金、塑料等。
不同的材料具有不同的力学性质,因此在选择材料时需要考虑其强度、刚度和耐腐蚀性等因素。
此外,弹簧的形状也会对其力学性质产生影响,例如圆柱形弹簧、扭转弹簧、锥形弹簧等。
2. 弹簧的刚度与弹性系数弹簧的刚度是衡量其弹性特性的一个重要参数。
刚度越高,弹簧在受力时产生的形变越小。
弹簧的刚度可以通过弹性系数来描述,弹性系数越大,弹簧的刚度就越高。
弹簧的弹性系数可以通过材料的弹性模量和几何形状来计算。
3. 弹簧的载荷与位移关系当外力作用在弹簧上时,弹簧会发生形变,产生位移。
弹簧的载荷与位移之间存在一定的关系,可以通过胡克定律来描述。
胡克定律表明,当弹簧受到一定的载荷时,其产生的变形与受力成正比。
这个比例关系可以用公式F = kx 来表示,其中F 是弹簧受力,k 是弹性系数,x 是弹簧的位移。
二、弹簧系统的振动频率分析1. 自由振动与强迫振动弹簧系统可以发生自由振动和强迫振动。
自由振动是指在没有外力作用下,弹簧系统由于初始扰动而产生的振动。
而强迫振动是指在外力的作用下,弹簧系统受迫振动而产生的振动。
要了解弹簧系统的振动频率,需要对其进行分析并求解其固有频率。
2. 振动频率的影响因素弹簧系统的振动频率受到多个因素的影响,包括弹簧的刚度、质量、几何形状以及受力方式等。
刚度越高,振动频率越高;质量越大,振动频率越低;几何形状的改变也会对振动频率造成影响。
此外,弹簧的振动频率还会受到外界激励频率的影响。
3. 振动频率的计算方法弹簧系统的振动频率可以通过分析其动力学方程来求解。
对于简谐振动的弹簧系统,可以使用以下公式计算其固有频率:f = 1/(2π) * √(k/m)其中,f 为振动频率,k 是弹簧的弹性系数,m 是弹簧的质量。
膜片弹簧力学特性CAE分析

模型导入 将hypermesh中生成的网格模型导入 到abaqus。设置膜片弹簧三角形单元类型 为STRI65,四边形单元类型为S8R,均为 二次单元。材料为60Si2Mn,弹性模量 E=206000MPa,泊松比为0.29。支承环与 压盘单元类型为C3D4, 材料为碳素钢,弹 性模量210000MPa,泊松比为0.27。
三、分析结果
将数据导入matlab中处理,得到膜片弹簧压紧过程的弹性特性 曲线,其中x轴为支承环的位移,y轴为支承环与膜片弹簧之间沿 膜片弹簧轴向方向的接触力大小。
通过A-L法理论计算得到的弹性特性曲线:
两种方法得到的弹性特性曲线的对比: (如图,峰值大的是CAE分析曲线,峰值小的是理论计算曲线 )
接触条件 建立支承环与膜片弹簧之间的面接触, 建立膜片弹簧与压盘之间的面接触,两个接 触为库伦摩擦,摩擦系数为0.18。
施加位移载荷 位移载荷分两个分析步施加,两个分析 步均设置为非线性。第一个分析步使RP-2在 膜片弹簧轴向方向下压0.02mm(将膜片弹 簧压平),这样是为了先让两对接触面的接 触关系平稳的建立起来,这个分析步中时间 增量步设为1。第二个分析步使RP-2在膜片 弹簧轴向方向下压6mm,分20个时间增量步 进行加载,即每个增量步中支承环下压 0.3mm。
边界条件 约束压盘全部节点的所有自由度。在A 处建立局部坐标系,以在膜片弹簧平面内并 垂直于A边方向为Y方向,以轴向方向为X方 向。同理在B处也建立局部坐标系,以在膜 片弹簧平面内并垂直于B边方向为Y方向,以 轴向方向为X方向。在局部坐标系中约束膜片 弹簧A、B处所有节点的U2(Y方向)、UR1 (X方向转动)、UR3(Z方向转动)三个自 由度。将参考点RP-2与支承环所有节点刚性 耦合,约束RP-2除膜片弹簧轴向方向外的其 余五个自由度。
膜片弹簧最大应力点位置

膜片弹簧最大应力点位置你知道吗,膜片弹簧其实是一种看起来不起眼,但却能承载巨大压力的小东西,应用广泛,像汽车、家电这些地方都少不了它。
膜片弹簧的工作原理呢,其实就是通过材料的弹性,来吸收和释放力,就像你揉一团橡皮泥,越用力,它就越挤压,松开后又恢复原样。
可是啊,这个东西最关键的地方在于它的“最大应力点”,也就是那一刻,膜片弹簧最脆弱的地方。
简单来说,最容易坏掉的地方,伤不起啊!所以,找准这个点,就能延长膜片弹簧的使用寿命,避免它突然“罢工”,给你带来不必要的麻烦。
要说膜片弹簧的最大应力点在哪,首先我们得知道一个事情,弹簧的应力不是均匀分布的。
你看,弹簧受力时,内部不同部位的变形是有差异的。
最简单的道理就是,弹簧中间部分的受力最大,因为离支撑点更近,形变也更明显,就像你坐在沙发中间,承受的重量比靠边缘要重多了。
膜片弹簧也是如此,离中心越近的地方,受的力越大。
这个最大应力点,基本上就在膜片的圆心位置,那里压力最大,最容易出现塑性变形。
你可以想象一下,膜片弹簧像个纸盘子,盘子中心处一受到重压,就会下凹,外边缘倒还好。
膜片的形状和受力的分布类似,就是那块“心脏”地带,不太抗压。
你得考虑材料的强度。
不同材料做的膜片弹簧,最大应力点的分布也不一样。
有些材料抗压能力强,能把应力分散开;有些则不行,容易变形。
咱们常见的膜片弹簧,通常是用钢板或者不锈钢做的,但如果你换成一些高分子材料,弹性可能就不够,容易产生应力集中,变得脆弱。
材料好坏对膜片弹簧的使用寿命有很大影响。
所以,买膜片弹簧时,选对材料也至关重要。
你可能还会问,这个最大应力点不就很简单,找个中心点不就行了?说实话,这事儿可没那么简单。
膜片弹簧的形状、大小、受力情况,都会影响最大应力点的位置。
如果是环形膜片弹簧,受力分布比较均匀,最大应力点可能就会在中心。
如果是异形的弹簧,比如说椭圆形或是带有孔洞的,那就不一定了,可能会在离中心稍微偏一点的地方。
所以,想精确找到最大应力点,除了依赖经验之外,还得有一些高精度的测试手段。
毕设膜片弹簧离合器设计

毕设膜片弹簧离合器设计膜片弹簧离合器是一种常见的机械传动装置,广泛应用于汽车和工程机械等领域。
它通过操纵离合器踏板来实现发动机和传动系统的分离和连接。
本文将从设计原理、材料选择、结构设计和制造工艺等方面进行详细阐述。
首先,膜片弹簧离合器的设计原理基于膜片弹簧的力学特性。
膜片弹簧是一种平面弹簧,具有较大的变形能力和较小的刚度。
当施加外力时,膜片弹簧会发生弹性变形,从而产生恢复力。
利用这种力学特性,可以实现离合器的分离和连接。
其次,材料的选择对于膜片弹簧离合器的设计至关重要。
由于膜片弹簧在工作过程中需要承受较大的压力和变形,因此材料的强度和韧性是关键考虑因素。
常用的膜片弹簧材料有合金钢、不锈钢和铝合金等。
根据具体要求和工作环境选择合适的材料。
接下来是结构设计。
膜片弹簧离合器的结构包括主动盘、从动盘、膜片和压盘等组成部分。
主动盘与发动机相连,从动盘与传动系统相连。
膜片被夹在主动盘与从动盘之间,通过与压盘的接触实现传递动力。
为了提高离合器的传递效率和使用寿命,结构设计应考虑传递能力、热稳定性、振动和噪声控制等因素。
最后是制造工艺。
膜片弹簧的制造主要包括材料切割、冷冲压和热处理等工艺。
材料切割可以采用激光切割或机械切割,确保膜片弹簧的尺寸和形状精确。
冷冲压工艺是将切割好的膜片进行冷变形,形成所需的结构和形状。
热处理可以提高膜片弹簧的硬度和韧性,并消除内部应力,改善材料的机械性能。
综上所述,膜片弹簧离合器的设计考虑了力学特性、材料选择、结构设计和制造工艺等方面。
通过合理设计和优化,可以获得性能稳定、安全可靠的离合器产品。
对于长时间运行的汽车和工程机械等设备来说,膜片弹簧离合器的设计是非常重要的。
膜片弹簧最大磨损压紧力会

膜片弹簧最大磨损压紧力会一、引言膜片弹簧作为离合器的重要组成部分,其性能对离合器的使用效果具有重大影响。
其中,膜片弹簧的最大磨损压紧力是一项关键参数,直接关系到离合器的使用寿命和驾驶性能。
本篇文档将对膜片弹簧的最大磨损压紧力进行详细分析。
二、膜片弹簧的结构与工作原理膜片弹簧采用碟形设计,通过圆锥形的弹性变形实现压紧力。
当离合器结合时,膜片弹簧将压盘压向从动盘,从而实现动力的传递。
膜片弹簧的优点在于其结构简单、压紧力稳定且重量轻。
三、膜片弹簧最大磨损压紧力的影响因素1.材料质量:膜片弹簧的材料决定了其耐磨性和耐久性。
高品质的材料能够提高膜片弹簧的最大磨损压紧力,从而延长离合器的使用寿命。
2.制造工艺:制造过程中的热处理、表面处理等工艺对膜片弹簧的性能有重要影响。
合理的工艺控制可以提高膜片弹簧的硬度和耐磨损性能,从而提高其最大磨损压紧力。
3.使用环境:使用环境中的温度、湿度、污染物等因素都会对膜片弹簧的磨损产生影响。
高温、高湿度和污染物会增加膜片弹簧的磨损速度,降低其最大磨损压紧力。
四、提高膜片弹簧最大磨损压紧力的措施1.选用优质材料:采用高强度、耐磨性好的材料,如特殊合金钢或钛合金等,能够显著提高膜片弹簧的最大磨损压紧力。
2.优化制造工艺:通过优化热处理和表面处理工艺,提高膜片弹簧的硬度和耐磨损性能,从而提高其最大磨损压紧力。
3.加强使用维护:定期更换润滑油和清洗离合器,保持使用环境的清洁,可以有效减缓膜片弹簧的磨损速度,延长离合器的使用寿命。
五、结论通过对膜片弹簧最大磨损压紧力的分析,我们可以了解其影响因素和优化措施。
在实际应用中,应综合考虑材料质量、制造工艺和使用环境等多个因素,以提高膜片弹簧的最大磨损压紧力,从而延长离合器的使用寿命并保障驾驶性能。
未来,随着新材料和新工艺的发展,膜片弹簧的性能将得到进一步提升,为离合器的优化提供更多可能性。
膜片弹簧

3.2.2 R 及R/r 确定比值R/r 对弹簧的载荷及应力特性都有影响,从材料利用率的角度,比值在1.8~2.0时,碟形弹簧储存弹性的能力为最大,就是说弹簧的质量利用率和好。
因此设计用来缓和冲击,吸收振动等需要储存大量弹性能时的碟簧时选用。
对于汽车离合器的膜片弹簧,设计上并不需要储存大量的弹性能,而是根据结构布置与分离的需要来决定,一般R/r 取值为1.2~1.3.对于R,膜片弹簧大端外径R 应满足结构上的要求和摩擦片的外径相适应,大于摩擦片内径,近于摩擦片外径。
此外,当H ,h 及R/r 等不变时,增加R 有利于膜片弹簧应力的下降。
初步确定R/r=5.82108=1.313.2.3 膜片弹簧起始圆锥底角汽车膜片弹簧一般起始圆锥底角α在10°~14°之间,α≈)(r R H -代入数值计算可得:α=11°15′3.2.4 膜片弹簧小端半径及分离轴承的作用半径r f 的值主要由结构决定,最小值应大于变速器第一轴花键外径,分离轴承作用半径r p 大于 r f因为花键外径D=32㎜要使2 r f >D ,所以取r f =25㎜,r p =28㎜3.2.5 分离指数目、切槽宽、窗孔槽宽、及半径汽车离合器膜片弹簧的分离指数目n >12,一般在18左右,采用偶数,便于制造时模具分度切槽宽1δ≈4㎜,2δ≈12㎜,窗孔半径r e 一般情况下由(r -r e )≈(0.8~1.4) 2δ,所以取r -r e =12δ=12㎜ 可取得n=18, 1δ≈4㎜,2δ≈12㎜, r e =70.53.2.6 承环的作用半径和膜片与压盘接触半径由于采用推式膜片弹簧,l ,L 的大小将影响膜片弹簧的刚度,一般来说,l 值应尽量靠近r 而略大与r 。
L 应接近R 略小于R 。
可选择:l=84㎜,L=108㎜3.2.7 膜片弹簧材料制造膜片弹簧用的材料,应具有高的弹性极限和屈服极限,高的静力强度及疲劳强度,高的冲击强度,同时应具有足够大的塑性变形性能。
膜片弹簧载荷变形特性有限元分析

膜片弹簧载荷变形特性有限元分析付建蓉 1,王青春 1,牛浩龙 1,王玉鑫 1(1.北京林业大学工学院,北京 100083摘要:本文通过实验研究、理论计算和有限元方法对膜片弹簧载荷变形进行了研究。
首先进行了膜片弹簧大端加载时的载荷变形实验,然后根据 A-L 理论公式进行了计算,最后根据实验工况利用 MSC.MARC 进行了有限元计算。
将理论计算所得的膜片弹簧大端载荷变形曲线、有限元模拟分析所得的膜片弹簧大端载荷变形曲线与实验所得的膜片弹簧大端载荷变形曲线进行比较,分析膜片弹簧几个关键大端位移处的载荷与实验对应值的误差。
通过对比,得出采用有限元模拟计算所得计算结果与实验值更为接近的结论。
关键词:膜片弹簧;非线性;有限元分析;载荷变形曲线Load Deformation Characteristics of Diaphragm SpringBased on Finite Element AnalysisFU Jian-rong1, WANG Qing-chun1, NIU Hao-long1, WANG Yu-xin1(1.School of Technology, Beijing Forestry University, Beijing 100083, ChinaAbstract: In this article, experimental research 、 theoretical calculation and finite element method have been used to analyze the load deformation characteristics of diaphragm spring. First, an experiment of diaphragm spring load deformation has been done, and then a calculation based on the A-L theoretical formula has been done, finally, according to the experimental conditions by using the finite element methodMSC.MARC to do a calculation. We compare the load deformation cure of A-L and FEA to the one figured out by experiment, analysis the errors which compare to the experiment of several key big end diaphragm spring load and displacement values. Bycontrast, the finite element simulation results are quite closer to the experimental results. Key words: diaphragm spring; nonlinear; finite element analysis; load deformation curve1 引言膜片弹簧离合器采用膜片弹簧为压紧弹簧, 与采用圆柱弹簧为压紧弹簧的离合器相比突出的优越性是膜片弹簧具有更理想的非线性弹性特性。
弹簧的力学性能分析与设计优化
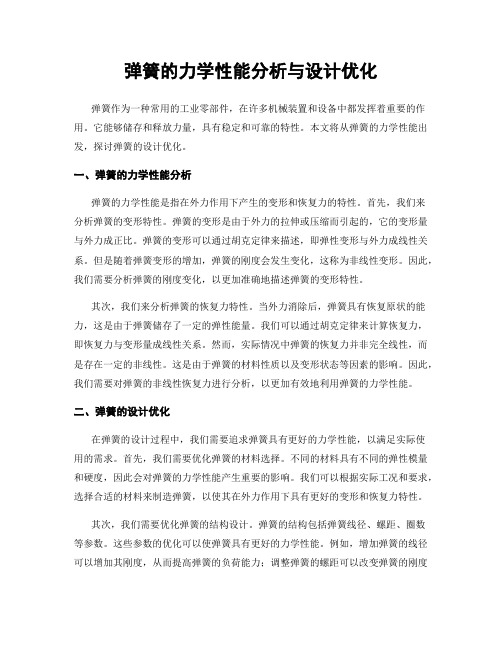
弹簧的力学性能分析与设计优化弹簧作为一种常用的工业零部件,在许多机械装置和设备中都发挥着重要的作用。
它能够储存和释放力量,具有稳定和可靠的特性。
本文将从弹簧的力学性能出发,探讨弹簧的设计优化。
一、弹簧的力学性能分析弹簧的力学性能是指在外力作用下产生的变形和恢复力的特性。
首先,我们来分析弹簧的变形特性。
弹簧的变形是由于外力的拉伸或压缩而引起的,它的变形量与外力成正比。
弹簧的变形可以通过胡克定律来描述,即弹性变形与外力成线性关系。
但是随着弹簧变形的增加,弹簧的刚度会发生变化,这称为非线性变形。
因此,我们需要分析弹簧的刚度变化,以更加准确地描述弹簧的变形特性。
其次,我们来分析弹簧的恢复力特性。
当外力消除后,弹簧具有恢复原状的能力,这是由于弹簧储存了一定的弹性能量。
我们可以通过胡克定律来计算恢复力,即恢复力与变形量成线性关系。
然而,实际情况中弹簧的恢复力并非完全线性,而是存在一定的非线性。
这是由于弹簧的材料性质以及变形状态等因素的影响。
因此,我们需要对弹簧的非线性恢复力进行分析,以更加有效地利用弹簧的力学性能。
二、弹簧的设计优化在弹簧的设计过程中,我们需要追求弹簧具有更好的力学性能,以满足实际使用的需求。
首先,我们需要优化弹簧的材料选择。
不同的材料具有不同的弹性模量和硬度,因此会对弹簧的力学性能产生重要的影响。
我们可以根据实际工况和要求,选择合适的材料来制造弹簧,以使其在外力作用下具有更好的变形和恢复力特性。
其次,我们需要优化弹簧的结构设计。
弹簧的结构包括弹簧线径、螺距、圈数等参数。
这些参数的优化可以使弹簧具有更好的力学性能。
例如,增加弹簧的线径可以增加其刚度,从而提高弹簧的负荷能力;调整弹簧的螺距可以改变弹簧的刚度和变形范围等。
因此,在设计弹簧时,我们需要考虑这些参数的优化,以使弹簧能够更好地满足实际应用要求。
最后,我们还可以通过优化弹簧的加工工艺来改善其力学性能。
例如,采用热处理技术可以提高弹簧的强度和韧性,使其具有更好的负荷能力和耐久性。
强化处理工艺影响膜片弹簧载荷变形关系的分析

强化处理工艺影响膜片弹簧载荷变形关系的分析膜片弹簧是机械弹簧的一种,由多个平面的弹性金属薄片组成,具有高载荷、小变形、耐疲劳等特点,广泛应用于各种机械、汽车、航空航天等领域。
而膜片弹簧的弹性性能和载荷变形关系受到强化处理工艺的影响。
本文将对强化处理工艺对膜片弹簧载荷变形关系的影响进行分析。
首先,强化处理工艺可以提高薄片的强度和硬度,从而提高弹簧的载荷能力。
常见的强化处理方法包括热处理、表面处理和化学处理等。
热处理是将薄片加热到一定温度,并保温一段时间,使薄片内部的组织结构发生改变,从而提高其强度和硬度。
表面处理是在薄片表面涂覆一层硬化剂或进行表面改性,从而形成一层硬度高的表面层。
化学处理是将薄片浸泡在含有特定化学物质的溶液中,通过化学反应改变其组织结构和性能。
其次,强化处理工艺还可以改善薄片的疲劳性能,从而延长弹簧的使用寿命。
疲劳是弹簧在反复加载和卸载过程中发生的变形和断裂现象,是弹簧失效的主要原因之一。
强化处理可以提高薄片的抗疲劳性能,使其在反复加载和卸载过程中出现的裂纹和缺陷减少或消失,从而延长弹簧的寿命。
同时,强化处理工艺还可以影响弹簧的变形特性,从而影响其载荷变形关系。
在弹簧的设计和制造过程中,载荷变形关系是一个重要的性能指标,它反映弹簧在载荷作用下的变形量和应力分布。
强化处理可以改变薄片的材料特性和组织结构,从而影响弹簧的变形特性。
例如,热处理可以降低薄片的弯曲刚度,使其在相同载荷下发生更大的弯曲变形;表面处理和化学处理可以增加薄片的摩擦系数,从而增加弹簧的摩擦阻力和阻尼性能。
综上所述,强化处理工艺对膜片弹簧的载荷变形关系有着重要的影响。
强化处理可以提高薄片的强度、硬度和抗疲劳性能,延长弹簧的使用寿命;同时,也可以改变弹簧的变形特性和应力分布,从而影响其载荷变形关系。
在弹簧的设计和制造中,应根据具体应用需求选择适当的强化处理工艺,以达到更好的性能和效果。
除了上述提到的强化处理工艺外,还有一些细节处理也会影响膜片弹簧的载荷变形关系。
基于ANSYS的膜片弹簧分析

基于ANSYS的膜片弹簧分析通过Proe建立三维模型,导入至ansys中,模型为对称模型,固只取四分之一模型进行分析研究,几何模型如下所示单元类型采用solid185,材料属性取弹性模量2.1e5MPa,泊松比为0.3进行网格划分,采用六面体网格对结构进行划分,为保证计算精度,厚度方向上划分了两层单元。
约束膜片弹簧上表面与支撑环接触的圆周区域。
因为在结构后处理中需要提取支反合力与位移的曲线,所以此处再约束膜片弹簧时候,先将其与支撑环接触的区域耦合到某一个新建的节点上,然后约束该节点的所有自由度,节点和膜片弹簧之间设置为刚性连接。
则后处理时候提取该节点的支反力,即为总支反力。
在膜片弹簧下表面与压盖接触的区域施加Z向的强制位移,模拟膜片弹簧压平过程。
位移加载14mm因为此处只取四分之一模型,所以截面上需要施加对称约束。
所有约束情况如下所示打开大变形,设置好载荷子步进行非线性求解。
提取应力位移曲线,可以采用如下命令提取/POST26FILE,'file','rst','.'/UI,COLL,1NUMVAR,200SOLU,191,NCMITSTORE,MERGEFILLDATA,191,,,,1,1REALVAR,191,191!*NSOL,2,4261,U,Z, UZ_2,STORE,MERGEFORCE,TOTAL!*ANSOL,3,2305,S,Z,SZ_3STORE,MERGEXVAR,2PLVAR,3,其中2305为所提取应力的节点编号,如果你要提取其他节点,只要改这个编号,然后用上面这段命令就可以这段命令是提取Z向应力的如果要提取等效应力的,ANSOL,3,2305,S,EQV,SEQV_4提取结果如下如果要提取负荷特性曲线,即论文中的图5 /POST26NUMVAR,200FILLDATA,191,,,,1,1REALVAR,191,191!*NSOL,2,4261,U,Z, UZ_2,STORE,MERGE!*RFORCE,3,7279,F,Z, FZ_3STORE,MERGEFILLDATA,192,,,,0,0FILLDATA,193,,,,1,0FILLDATA,194,,,,-1,0FILLDATA,195,,,,1,1VARNAME,195,NSET!! Name: F! ID: 4! Function: abs({FZ_3})ABS,4,3,,,F!STORE,MERGEXVAR,2PLVAR,4,提取弹簧片的变化过程,就是提取不同时刻下的位移云图/POST1SET,LIST,999SET,,, ,,, ,4!*/EFACET,1PLNSOL, U,SUM, 0,1.0修改4就是不同时刻,对应如下0.1s 最终。
膜片弹簧标准
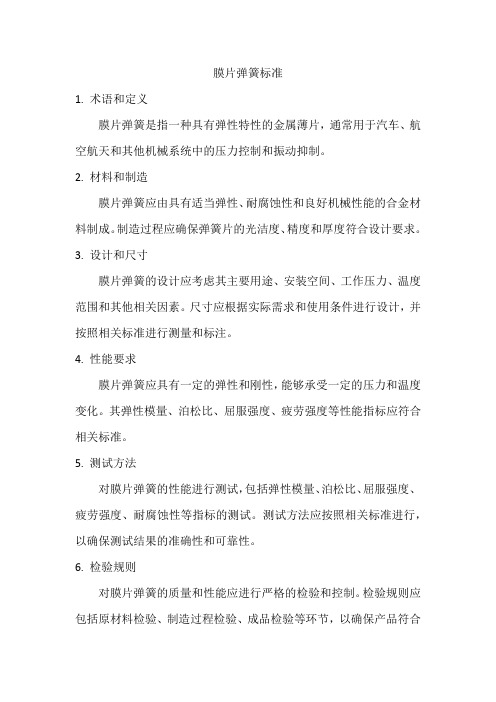
膜片弹簧标准
1. 术语和定义
膜片弹簧是指一种具有弹性特性的金属薄片,通常用于汽车、航空航天和其他机械系统中的压力控制和振动抑制。
2. 材料和制造
膜片弹簧应由具有适当弹性、耐腐蚀性和良好机械性能的合金材料制成。
制造过程应确保弹簧片的光洁度、精度和厚度符合设计要求。
3. 设计和尺寸
膜片弹簧的设计应考虑其主要用途、安装空间、工作压力、温度范围和其他相关因素。
尺寸应根据实际需求和使用条件进行设计,并按照相关标准进行测量和标注。
4. 性能要求
膜片弹簧应具有一定的弹性和刚性,能够承受一定的压力和温度变化。
其弹性模量、泊松比、屈服强度、疲劳强度等性能指标应符合相关标准。
5. 测试方法
对膜片弹簧的性能进行测试,包括弹性模量、泊松比、屈服强度、疲劳强度、耐腐蚀性等指标的测试。
测试方法应按照相关标准进行,以确保测试结果的准确性和可靠性。
6. 检验规则
对膜片弹簧的质量和性能应进行严格的检验和控制。
检验规则应包括原材料检验、制造过程检验、成品检验等环节,以确保产品符合
设计要求和客户期望。
7. 包装、标志和贮存
膜片弹簧在包装、标志和贮存方面应按照相关规定进行。
包装应确保产品在运输过程中不受损坏,标志应清晰、易读,并包括产品名称、型号、规格等信息。
贮存环境应干燥、无尘、无腐蚀,以确保产品的质量和使用寿命。
8. 使用要求和安全注意事项
在使用膜片弹簧时,应遵循使用说明书或相关规定,确保安装正确、使用得当。
同时,应注意安全事项,如避免过度加载、避免金属疲劳等,以确保产品的安全使用和延长使用寿命。
膜片弹簧的结构特点

膜片弹簧的结构特点膜片弹簧是一种常见的弹性元件,具有以下结构特点:1. 结构简单:膜片弹簧由一片或多片薄膜组成,每片膜片呈弧形或波浪形,通过连接在一起形成弹簧的结构。
相比于传统的螺旋弹簧,膜片弹簧的结构更为简单,易于制造和安装。
2. 轴向刚度高:膜片弹簧的薄膜通常采用高强度的金属材料制成,例如不锈钢或合金钢。
这些薄膜具有较高的轴向刚度,即在垂直于弹簧轴向的压缩或拉伸力下,能够提供较大的恢复力。
3. 轴向柔度可调:膜片弹簧的轴向柔度可通过改变薄膜的数量、形状和材料来调节。
增加薄膜的数量或改变形状可以增加弹簧的柔度,而更换不同材料的薄膜可以改变弹簧的刚度。
这使得膜片弹簧能够满足不同应用场景下的需求。
4. 体积小巧:由于膜片弹簧采用薄膜的结构,相比于传统的螺旋弹簧,其体积更小巧。
这使得膜片弹簧在空间有限的应用场景中具有较大的优势,例如微型仪器、电子设备等。
5. 耐腐蚀性好:膜片弹簧通常采用不锈钢或合金钢等耐腐蚀材料制成,具有良好的耐腐蚀性。
这使得膜片弹簧能够在恶劣的环境条件下使用,如潮湿、酸碱等腐蚀性介质中。
6. 负荷承载能力高:膜片弹簧的薄膜结构能够在受到轴向力的作用下产生较大的弹性变形,从而提供较大的负荷承载能力。
这使得膜片弹簧能够在工程领域中承担较大的压缩或拉伸负荷,如汽车悬挂系统、工业机械等。
7. 阻尼性能好:膜片弹簧具有较好的阻尼性能,能够吸收和减缓外部振动或冲击产生的能量。
这使得膜片弹簧广泛应用于减震、缓冲和隔振等领域,如汽车减震器、工业机械隔振系统等。
膜片弹簧具有结构简单、轴向刚度高、轴向柔度可调、体积小巧、耐腐蚀性好、负荷承载能力高和阻尼性能好等特点。
这些特点使得膜片弹簧在各个领域都具有广泛的应用前景。
膜片弹簧载荷变形特性的试验研究的开题报告

膜片弹簧载荷变形特性的试验研究的开题报告一、选题背景与意义膜片弹簧作为一种重要的载荷元件,广泛应用于工业生产中的诸多领域,如汽车工业、机械工业、电子工业等。
它具有高负荷、长寿命、稳定性好、尺寸小、重量轻等特点,因此备受青睐。
然而,由于缺乏对膜片弹簧载荷变形特性的深入研究,难以实现其超负荷量级的应用,且难以解决不同应用场合下膜片弹簧的性能差异问题,因此有必要进行试验研究,以了解其载荷变形特性,进而完善其应用,提高其性能。
二、研究内容、目的和方法本研究旨在通过试验研究的方法,了解膜片弹簧的载荷变形特性,掌握其压缩弹性模量、回弹率、疲劳寿命等方面的变化规律,为其应用提供科学依据。
具体内容包括:1. 设计并制作符合国际标准的膜片弹簧试验装置,并进行初始负荷测试,确定试验参数;2. 采用静态加载法和动态加载法,分别载荷不同程度下,测量膜片弹簧毫米级应变值和变形量,建立载荷和变形之间的关系曲线;3. 在疲劳试验机上进行膜片弹簧的疲劳寿命试验,研究其寿命受到载荷循环次数、强度和形状等因素的影响;4. 进一步分析试验数据,揭示膜片弹簧的载荷变形特性,为其在不同应用场合下的设计和使用提供依据。
三、预期结果和意义通过本研究的试验研究,可以得到膜片弹簧载荷变形特性的数据,从而揭示其性能瓶颈,为膜片弹簧的设计和使用提供科学依据。
具体预期结果和意义如下:1. 得到膜片弹簧的压缩弹性模量和回弹率等关键参数,为其应用提供依据;2. 揭示载荷和变形之间的关系曲线,对设计膜片弹簧的结构和形状提供参考;3. 研究膜片弹簧的疲劳寿命规律,为其性能的进一步提高提供基础及参考。
四、研究进度安排预计研究的时间为半年,主要进度安排如下:1. 第1-2个月:查阅文献资料,确定研究方案,制定试验计划;2. 第3-4个月:搭建试验装置并进行试验,测量相关数据;3. 第5-6个月:分析试验数据,撰写论文并进行修改。
五、研究难点与解决途径研究过程中主要涉及如何合理设计试验装置,确保测量数据的准确性,以及如何处理多组试验数据进行分析,得出正确结论。
案例2-离合器膜片弹簧的有限元分析

〖汽车理论与设计〗精品课程建设精品课程建设 福州大学机械工程及自动化学院车辆工程系图1 膜片弹簧的基本结构膜片弹簧的基本结构 案例二、离合器膜片弹簧的有限元分析 在工程技术领域,对于许多力学问题和物理问题,人们已经得到了它们应遵循的基本方程和相应的定解条件,程和相应的定解条件,但对于其中的大多数问题,但对于其中的大多数问题,但对于其中的大多数问题,由于方程某些特性的非线性性质,由于方程某些特性的非线性性质,由于方程某些特性的非线性性质,或由于或由于求解区域的几何形状比较复杂,求解区域的几何形状比较复杂,不能求得解析解。
不能求得解析解。
不能求得解析解。
对于这类问题,对于这类问题,对于这类问题,以前常常通过引入简化条以前常常通过引入简化条件,进行简化状态下的解答,进行简化状态下的解答,但过多的简化可能导致误差很大甚至是错误。
但过多的简化可能导致误差很大甚至是错误。
但过多的简化可能导致误差很大甚至是错误。
二十世纪六十年二十世纪六十年代以来,随着计算机的飞速发展和广泛应用,数值分析方法已经成为求解这类问题的主要工具,其中,有限单元法(Finite Element Method )在工程实践中已得到了广泛的认可。
)在工程实践中已得到了广泛的认可。
)在工程实践中已得到了广泛的认可。
有限单元法的基本思路是将复杂的结构视为由有限的、有限单元法的基本思路是将复杂的结构视为由有限的、简单的基本单元所组成。
简单的基本单元所组成。
这种基于离散化的数值计算方法,借助于矩阵方法与计算机相结合,几乎适用于求解所有的连续介质和场问题。
对于有限元法的原理,大家可到图书馆参阅相关书籍[1]。
在汽车设计中,与固体力学、流体力学、热力学、声学、电磁学等相关的问题都可以应用有限元法求解,并且在很多问题上已经成为汽车研发流程中重要的环节。
很多问题上已经成为汽车研发流程中重要的环节。
在下面的例子中,应用有限元法分析了离合器膜片弹簧的弹性特性。
膜片弹簧大端载荷_变形特性的研究

它们之间的误差列于表 2 。
表1 膜片弹簧大端载荷 —变形 ( F1 - λ1 ) 特性试验结果 N
大端
大端载荷
位移
170
232
240
267
330
(mm) 7 # 9 # 1 # 2 # 4 # 3 # 5 # 1 # 3 # 5 # 1 # 2 #
0. 0 0 0 0 0 0 0 0 0 0 0 0 0
本文通过对现有不同规格的膜片弹簧 ( 170 , 232 , 240 , 267 , 330 等) 的大端加载的试验研究 , 再 根 据 试 验 结 果 的 分 析 , 并 与 相 应 弹 簧 用 Al2 me n-L a szlo 近似公式的计算值对比 , 分析了膜片弹簧 结构参数与误差大小的关系 , 找出它们的共性 , 进而提 出了较为符合实际的修正公式 。
3. 5 1620 1944 5982 6531 6324 5315 5520 8828 8757 8680 10741 11369
4. 0 1350 1646 5567 6189 5850 5041 5230 8710 8621 84 5036 5600 5270 4657 4816 8279 8222 8023 10051 10796
数据见表 1 ,绘制的试验曲线见图 2~13 。将根据膜片弹 簧的尺寸参数用 Al me n--L a szlo 公式计算出的大端载 荷 —变形 ( F1 —λ1 ) 数据亦绘于图 2~13 中 。可以看出 , 在同样的大端变形λ1 下 , 实测的大端载荷 F1 与用 Al2 me n-L a szlo 公式计算的理论值存在一定的差别 , 各种 膜片弹簧在峰点和谷点处实测载荷与理论载荷值以及
膜片弹簧在不同工作状态时的作用力及变形情况

膜片弹簧在不同工作状态时的作用力及变形情况一、引言膜片弹簧作为一种重要的弹性元件,广泛应用于各种机械设备中。
它具有体积小、弹性系数大、变形稳定等特点,在不同工作状态下能够发挥不同的作用力和变形情况。
本文将从膜片弹簧的结构特点入手,深入探讨其在不同工作状态下的作用力和变形情况,以期为读者对膜片弹簧的特性有更深入的了解。
二、膜片弹簧的结构特点膜片弹簧通常由多层薄片叠合而成,呈圆形或椭圆形。
在受力时,薄片会发生弯曲变形,从而产生作用力。
膜片弹簧的变形特点主要包括轴向变形和径向变形两种情况。
(一)轴向变形当膜片弹簧受到轴向载荷作用时,薄片会呈现出轴向挤压或拉伸的变形情况。
这种变形状态下,薄片的叠合层数也会发生相对的位移,从而产生作用力。
(二)径向变形在径向载荷作用下,膜片弹簧的薄片会发生径向挤压或拉伸的变形情况。
这种变形状态下,薄片的内外直径也会产生相对的变化,从而产生不同的作用力。
三、膜片弹簧在不同工作状态下的作用力及变形情况(一)静态工作状态在膜片弹簧处于静态工作状态时,即受到恒定的轴向或径向载荷作用时,其作用力主要取决于载荷大小和弹簧的刚度。
此时,膜片弹簧的变形情况相对稳定,可以通过简单的力学模型进行分析和计算。
(二)动态工作状态在膜片弹簧处于动态工作状态时,即受到交变的轴向或径向载荷作用时,其作用力和变形情况会随载荷的变化而发生相应的变化。
这时,薄片的弯曲变形将产生频率响应,可能会出现疲劳破坏的情况。
四、总结与展望通过对膜片弹簧在不同工作状态下的作用力和变形情况的分析,我们可以看出膜片弹簧具有较为稳定的变形特性,能够根据不同的工作状态发挥不同的作用力。
但在动态工作状态下,需要特别注意其疲劳破坏问题,以保证设备的安全运行。
对于膜片弹簧的进一步研究,可以针对其动态工作状态下的疲劳特性展开深入的研究,以期能够改进设计和制造工艺,提高弹簧的使用寿命和可靠性。
个人观点:作为一种重要的弹性元件,膜片弹簧在机械设备中起着不可替代的作用。
膜片弹簧在不同工作状态时的作用力及变形情况

膜片弹簧在不同工作状态时的作用力及变形情况膜片弹簧是一种特殊的弹簧结构,由圆形薄片密排而组成。
它具有良好的弹性和弹力恢复性能,被广泛应用于各种机械设备和工业领域。
膜片弹簧的作用力和变形情况在不同的工作状态下会有所不同。
本文将从以下几个方面逐步探讨膜片弹簧的作用力和变形情况。
第一部分:膜片弹簧的结构和工作原理首先,我们要了解膜片弹簧的基本结构和工作原理。
膜片弹簧由多个圆形薄片叠加而成,通过薄片之间的摩擦力保持弹簧的形状和稳定性。
当受到外力作用时,薄片会发生相对的位移,产生弹性变形,从而吸收和释放能量。
第二部分:膜片弹簧在静态工作状态下的作用力和变形情况在静态工作状态下,膜片弹簧受到外力后会产生相应的位移和变形。
根据胡克定律,弹簧的变形与施加在其上的力成正比。
因此,膜片弹簧的变形量可以用力和弹性系数之间的关系进行描述。
同时,膜片弹簧的背弯半径和受力分布也会影响其变形情况。
第三部分:膜片弹簧在动态工作状态下的作用力和变形情况在动态工作状态下,膜片弹簧的变形和作用力会随着外力的大小和频率而变化。
当外力作用频率较低时,膜片弹簧的变形和位移会较慢,弹簧会有足够的时间进行能量的吸收和释放。
而当外力频率较高时,膜片弹簧的变形和位移会加速,可能会导致共振和失效现象。
第四部分:膜片弹簧在不同工作状态下的应用案例最后,我们将以实际应用案例来阐述膜片弹簧在不同工作状态下的作用力和变形情况。
例如,当膜片弹簧用于减震器时,在静态状态下,弹簧可以吸收和分散车辆行驶中的颠簸和冲击力,提高乘坐舒适性。
而在动态状态下,弹簧可以根据路面的不平度进行相应的变形,实现良好的减震效果。
通过以上几个部分的介绍,我们可以全面了解膜片弹簧在不同工作状态下的作用力和变形情况。
这有助于我们更好地理解和应用膜片弹簧,提高机械设备的性能和效率。
- 1、下载文档前请自行甄别文档内容的完整性,平台不提供额外的编辑、内容补充、找答案等附加服务。
- 2、"仅部分预览"的文档,不可在线预览部分如存在完整性等问题,可反馈申请退款(可完整预览的文档不适用该条件!)。
- 3、如文档侵犯您的权益,请联系客服反馈,我们会尽快为您处理(人工客服工作时间:9:00-18:30)。
膜片弹簧的力学性能分析
膜片弹簧是膜片弹簧离合器的关键零件,其设计质量的优劣不仅直接影响离合器的使用性能和使用寿命,而且还影响离合器与整车的匹配。
因此在设计膜片弹簧离合器时,精确计算膜片弹簧的负载特性是非常重要的。
目前,膜片弹簧的设计仍普遍采用美国人J.o.Almen和Laszlo所提出的近似公式(简称A-L
公式),但工程人员在设计制造膜片弹簧的实践中发现,根据A-L公式设计的膜片弹簧,在膜片弹簧试制后的试验中,其大端载荷、升程等均不能完全符合设计要求,往往需要修改膜片弹簧尺寸参数,再进行试验。
这样,既延长了试制周期,又增加了成本。
因此,有必要寻找一种更有效的计算方法。
本文以膜片弹簧为研究对象,首先介绍了传统的A-L计算方法和膜片弹簧的基本特性。
然后,采用有限元的方法对膜片弹簧进行力学性能的仿真分析研究。
利用ANSYS参数化设计语言APDL,建立膜片弹簧自由状态下的三维参数化模型,大大简化了复杂繁琐的建模过程;通过适当的方法,对三维模型进行映射网格划分,确定相应的边界条件,建立起膜片弹簧的有限元模型。
模拟加载过程,计算得到膜片弹簧负载特性曲线,通过实验结果的比较,验证了有限元模型的正确性。
在膜片弹簧有限元分析的基础上,建立膜片弹簧负载特性的数学回归模型,对A-L公式系数进行了修正,提高了其计算的精度。
通过对应力分布的分析和膜片弹簧失效的特点,确定了其疲劳危险区域,利用材料的σ-N曲线,采用ANSYS疲劳分析模块估算了膜片弹簧的疲劳寿命。
最后,建立了膜片弹簧的优化模型,对其进行结构优化,取得了较好的结果。