氯乙烯合成工艺设计
化工PVC各工段工艺流程
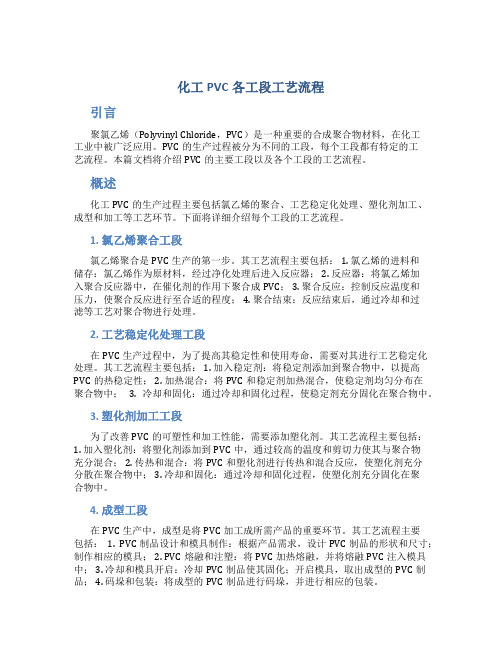
化工PVC各工段工艺流程引言聚氯乙烯(Polyvinyl Chloride,PVC)是一种重要的合成聚合物材料,在化工工业中被广泛应用。
PVC的生产过程被分为不同的工段,每个工段都有特定的工艺流程。
本篇文档将介绍PVC的主要工段以及各个工段的工艺流程。
概述化工PVC的生产过程主要包括氯乙烯的聚合、工艺稳定化处理、塑化剂加工、成型和加工等工艺环节。
下面将详细介绍每个工段的工艺流程。
1. 氯乙烯聚合工段氯乙烯聚合是PVC生产的第一步。
其工艺流程主要包括: 1. 氯乙烯的进料和储存:氯乙烯作为原材料,经过净化处理后进入反应器; 2. 反应器:将氯乙烯加入聚合反应器中,在催化剂的作用下聚合成PVC; 3. 聚合反应:控制反应温度和压力,使聚合反应进行至合适的程度; 4. 聚合结束:反应结束后,通过冷却和过滤等工艺对聚合物进行处理。
2. 工艺稳定化处理工段在PVC生产过程中,为了提高其稳定性和使用寿命,需要对其进行工艺稳定化处理。
其工艺流程主要包括: 1. 加入稳定剂:将稳定剂添加到聚合物中,以提高PVC的热稳定性; 2. 加热混合:将PVC和稳定剂加热混合,使稳定剂均匀分布在聚合物中; 3. 冷却和固化:通过冷却和固化过程,使稳定剂充分固化在聚合物中。
3. 塑化剂加工工段为了改善PVC的可塑性和加工性能,需要添加塑化剂。
其工艺流程主要包括:1. 加入塑化剂:将塑化剂添加到PVC中,通过较高的温度和剪切力使其与聚合物充分混合; 2. 传热和混合:将PVC和塑化剂进行传热和混合反应,使塑化剂充分分散在聚合物中; 3. 冷却和固化:通过冷却和固化过程,使塑化剂充分固化在聚合物中。
4. 成型工段在PVC生产中,成型是将PVC加工成所需产品的重要环节。
其工艺流程主要包括:1. PVC制品设计和模具制作:根据产品需求,设计PVC制品的形状和尺寸;制作相应的模具; 2. PVC熔融和注塑:将PVC加热熔融,并将熔融PVC注入模具中; 3. 冷却和模具开启:冷却PVC制品使其固化;开启模具,取出成型的PVC制品; 4. 码垛和包装:将成型的PVC制品进行码垛,并进行相应的包装。
年产10万吨氯乙烯工艺设计项目设计方案

设计方案项目背景:氯乙烯是一种重要的有机化工原料,广泛应用于塑料、橡胶、涂料、农药等多个领域。
我国是全球最大的氯乙烯生产和消费国家之一,但生产设备老化、能耗高等问题制约了其可持续发展。
因此,本设计方案旨在设计一套年产量为10万吨的氯乙烯工艺,利用先进的技术和设备,提高产能和能源利用效率。
设计方案:1.原料准备:该工艺采用乙烯和氯气为原料,通过氯化反应生成氯乙烯。
乙烯和氯气作为主要原料需要在储罐中储存,并通过气体管道输送至反应箱进行反应。
为确保原料的供给稳定和安全,需要设计合适的储存和输送系统,并设置相应的自动控制和安全设备。
2.反应过程:该工艺采用常压氯化法进行氯化反应。
乙烯和氯气通过催化剂在反应箱中进行氯化反应生成氯乙烯。
为提高反应效率和选择性,需要选择合适的催化剂和反应条件,并设计适当的反应器结构和控制系统。
同时,需要考虑废气处理和安全措施,避免有毒气体泄漏和环境污染。
3.分离和提纯:反应产生的气体混合物需要经过分离和提纯才能得到纯净的氯乙烯产品。
首先通过冷凝和压缩将气体混合物转化为液体,然后采用分离技术如蒸馏、吸附等进行分离和提纯。
分离后的氯乙烯产品需要经过后续的脱水、脱色等工艺步骤,得到满足市场要求的产品。
4.能源回收利用:为提高能源利用效率,该工艺设计考虑了能源回收利用系统。
具体包括废热回收、废气回收等。
废热回收可以通过余热锅炉进行,将废热转化为蒸汽等能源进行再利用;废气回收可以通过气体分离和净化系统,将有价值的气体组分进行回收利用。
5.自动控制系统:为确保生产过程的稳定和安全,该工艺设计采用自动控制系统进行全面控制。
通过传感器和仪表对关键工艺参数进行监测和控制,自动化地调节反应条件、制备工艺等,提高生产效率和产品质量。
同时,系统还需要具备报警、故障诊断等功能,保证生产的安全和可靠性。
6.安全环保措施:该工艺设计重点考虑安全和环保问题。
针对反应过程中有毒气体的泄漏和排放,需要设计相应的密封装置和废气处理系统,降低对环境和人体的影响。
年产10万吨氯乙烯工艺设计项目设计方案

年产10万吨氯乙烯工艺设计项目设计方案第一章绪论1.1聚氯乙烯1.1.1聚氯乙烯性质和用途⑴常温常压下,氯乙烯(vinyl chloride ,CH2=CHCI是无色气体,具有微甜气味,微溶于水,溶于烃类,醇,醚,氯化溶剂和丙酮等有机溶剂中,氯乙烯沸点-13.9 C,易聚合,并能与乙烯、丙烯、醋酸乙烯酯,偏二氯乙烯、丙烯腊、丙烯酸酯等单体共聚,而制得各种性能的树脂,加工成管材、面膜、塑料地板、各种压塑制品、建筑材料、涂料和合成纤维等。
近年来世界和中国聚氯乙烯树脂消耗比例分别见表 1.1和表1.2。
表1.1近年来世界聚氯乙烯树脂消耗比例品种比例/% 品种比例/%管材33 薄膜片材13 PVC 护墙板8 PVC 地板地砖 3硬薄膜和片材8 软合成皮革 3制吹塑制品 5 制电线电缆8品其他 6 品其他13合计60 合计40表1.2近年来中国聚氯乙烯树脂消耗比例品种比例/% 品种比例/%管材14 薄膜片材11 PVC 护墙板18 PVC 地板地砖8硬薄膜和片材15 软合成皮革7制吹塑制品 5 制电线电缆 4品其他 5 品其他13合计57 合计431.2 氯乙烯VC1.2.1 氯乙烯在国民经济中的地位和作用自1835 年法国化学家V.Regnault 首先发现了氯乙烯,于1838年他又观察到聚合体,这就是最早的聚氯乙烯。
聚氯乙烯自工业化问世至今,六十多年来仍处不衰之势。
占目前塑料消费总量的29%以上。
到上世纪末,聚氯乙烯树脂大约以3%的速度增长。
这首先是由于新技术不断采用,产品性能亦不断地得到改进,品种及牌号的增加,促进用途及市场的拓宽。
其次是制造原料来源广、制造工艺简单。
产品质量好。
在耐燃性、透明性及耐化学药品性能方面均较其它塑料优异。
又它是氯碱行业耗“氯”的大户,对氯碱平衡起着举足轻重的作用。
从目前世界主要聚氯乙烯生产国来说:一般耗用量占其总量的20〜30%。
特别是60 年代以来,由于石油化工的发展,为聚氯乙烯工业提供廉价的乙烯资源,引起了人们极大的注意,因而促使氯乙烯合成原料路线的转换和新制法以及聚合技术不断地更新,使聚氯乙烯工业获得迅猛的发展。
氯乙烯合成工艺设计
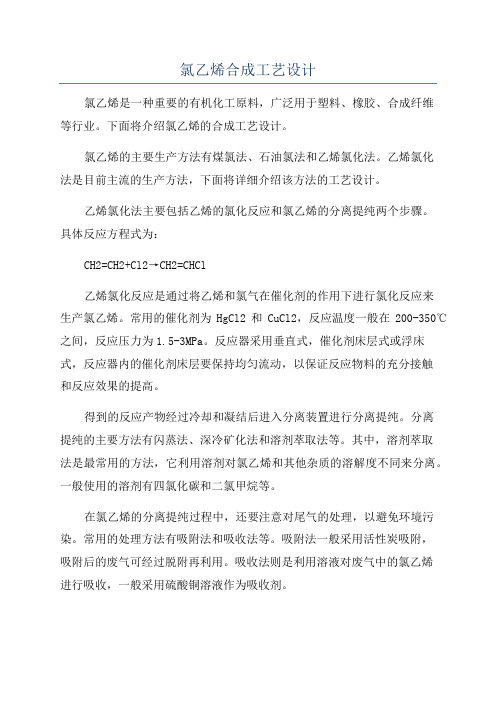
氯乙烯合成工艺设计氯乙烯是一种重要的有机化工原料,广泛用于塑料、橡胶、合成纤维等行业。
下面将介绍氯乙烯的合成工艺设计。
氯乙烯的主要生产方法有煤氯法、石油氯法和乙烯氯化法。
乙烯氯化法是目前主流的生产方法,下面将详细介绍该方法的工艺设计。
乙烯氯化法主要包括乙烯的氯化反应和氯乙烯的分离提纯两个步骤。
具体反应方程式为:CH2=CH2+Cl2→CH2=CHCl乙烯氯化反应是通过将乙烯和氯气在催化剂的作用下进行氯化反应来生产氯乙烯。
常用的催化剂为HgCl2和CuCl2,反应温度一般在200-350℃之间,反应压力为1.5-3MPa。
反应器采用垂直式,催化剂床层式或浮床式,反应器内的催化剂床层要保持均匀流动,以保证反应物料的充分接触和反应效果的提高。
得到的反应产物经过冷却和凝结后进入分离装置进行分离提纯。
分离提纯的主要方法有闪蒸法、深冷矿化法和溶剂萃取法等。
其中,溶剂萃取法是最常用的方法,它利用溶剂对氯乙烯和其他杂质的溶解度不同来分离。
一般使用的溶剂有四氯化碳和二氯甲烷等。
在氯乙烯的分离提纯过程中,还要注意对尾气的处理,以避免环境污染。
常用的处理方法有吸附法和吸收法等。
吸附法一般采用活性炭吸附,吸附后的废气可经过脱附再利用。
吸收法则是利用溶液对废气中的氯乙烯进行吸收,一般采用硫酸铜溶液作为吸收剂。
除了反应和分离提纯步骤外,还要对生产过程中产生的废水、废热等进行处理利用,以达到资源综合利用和环境保护的目的。
总结起来,氯乙烯的合成工艺设计主要包括乙烯氯化反应和氯乙烯的分离提纯两个步骤,其中乙烯氯化反应通过催化剂的作用将乙烯和氯气进行氯化反应,分离提纯则通过溶剂萃取法将氯乙烯和其他杂质进行分离。
在生产过程中还要注意对废气、废水和废热的处理利用。
正确设计和优化各个环节的操作条件和流程,能够提高产量、品质和能源利用率,降低生产成本和环境污染,实现可持续发展。
年产16万吨氯乙烯合成工艺设计

年产16万吨氯乙烯合成工艺设计1. 引言氯乙烯是一种重要的有机化工原料,广泛应用于塑料、合成橡胶、溶剂等行业。
本文旨在设计一种年产16万吨氯乙烯的合成工艺,以满足市场需求并提高生产效率。
2. 工艺概述合成工艺的概述如下:1.原料准备:主要原料包括乙烯、氯气和催化剂。
2.反应装置:采用流动床反应器,具有较高的热传导和负载能力。
3.反应步骤:氯气与乙烯在催化剂作用下发生氯化反应,生成氯乙烯。
4.分离纯化:通过多级凝馏和萃取等工艺对氯乙烯进行纯化。
5.产品储存和包装:将纯化后的氯乙烯储存于贮罐中,并进行相应的包装以便于运输和销售。
3. 反应装置设计3.1 流动床反应器流动床反应器是当前工业生产中常用的反应器类型之一,由于其具有优良的热传导和负载能力,适用于氯乙烯的合成反应。
流动床反应器的设计要点如下:•反应器材料:选择耐腐蚀性能好、热传导性能高的不锈钢。
•反应器结构:采用垂直式结构,方便气体和液体的流动,并且易于维护和清洗。
•热交换器:在反应器内部设置热交换器,提高反应器的热效率,减少能量损失。
•自动控制系统:采用先进的自动控制系统,实时监测反应器的温度、压力等参数,保证反应的稳定进行。
4. 反应步骤与工艺条件4.1 氯化反应氯化反应是合成氯乙烯的关键步骤,该反应基于氯气与乙烯的化学反应。
反应方程式如下:C2H4 + Cl2 -> C2H3Cl + HCl氯化反应的工艺条件如下:•温度:反应温度为300-500摄氏度。
•压力:反应压力为1-5兆帕。
•催化剂:采用氯化汞作为催化剂,具有较高的活性和选择性。
4.2 分离纯化分离纯化工艺的目的是将氯乙烯从反应产物中分离出来,以提高氯乙烯的纯度和质量。
分离纯化工艺包括多级凝馏和萃取等步骤:•多级凝馏:通过不同的温度和压力条件,将乙烯、氯乙烯和其他杂质分离出来。
•萃取:采用特定的溶剂将残留的杂质进一步去除,提高氯乙烯的纯度。
5. 安全防护措施在氯乙烯合成工艺中,涉及到氯气和高温高压条件,因此必须采取必要的安全防护措施,以防止事故发生,保证生产安全。
年产10万吨聚氯乙烯生产工艺设计

聚氯乙烯(Polyvinyl Chloride,简称PVC)是一种用途广泛的塑料材料,其年产量也相对较大。
本文将对年产10万吨聚氯乙烯的生产工艺进行设计,并将工艺步骤进行详细介绍。
1.原料准备2.氯乙烯制备利用氯气和乙烯进行反应,生成氯乙烯。
这一步需要精确控制反应的温度、压力和氯乙烯生成的速率,以确保反应的高效性和安全性。
3.聚合反应将氯乙烯和引发剂引入聚合反应器中进行聚合反应。
聚合反应器需要具备良好的搅拌和加热功能,以确保反应均匀进行且能高效完成。
聚合反应的时间和温度控制至关重要,以确保所得的聚合物的分子量和物性符合要求。
4.分离和净化将聚合反应产生的混合物进行分离和净化。
这一步主要包括聚合物的沉淀、过滤、洗涤等操作,以去除杂质和未反应的原料。
5.干燥和造粒将净化后的聚合物颗粒进行干燥处理,以去除水分和挥发性杂质,同时将其熔融并通过造粒机构成颗粒状的聚氯乙烯。
颗粒的大小和形状对后续的加工工艺和产品质量有关联。
6.真空除气将造粒后的聚氯乙烯通过真空除气设备进行处理,去除颗粒中的气体和挥发性成分,以确保产品的稳定性。
7.制品加工将除气处理后的聚氯乙烯颗粒进行制品加工。
常见的制品加工方式包括挤出、注塑、吹塑等。
通过这些加工方式,可以将聚氯乙烯颗粒制成板材、管材、型材等不同形状和尺寸的产品。
8.产品测试和质量控制对最终产品进行测试,检查其物理、力学、热学等性能指标,确保产品质量达到要求。
并建立质量控制体系,对每批产品进行检验和记录,以便进行溯源和质量追踪。
9.废弃物处理对生产过程中产生的废弃物进行处理和回收利用。
这些废弃物包括回收的聚氯乙烯颗粒、废水、废气等,应根据地方环保要求进行合理的处理。
综上所述,年产10万吨聚氯乙烯的生产工艺设计包括原料准备、氯乙烯制备、聚合反应、分离和净化、干燥和造粒、真空除气、制品加工、产品测试和质量控制以及废弃物处理等主要步骤。
在每一步骤中,都需要精确控制工艺参数、确保产品质量和安全性。
氯乙烯生产工艺介绍
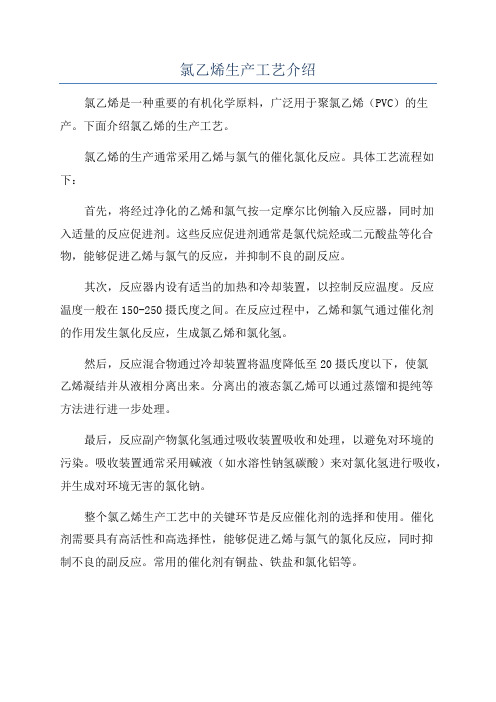
氯乙烯生产工艺介绍氯乙烯是一种重要的有机化学原料,广泛用于聚氯乙烯(PVC)的生产。
下面介绍氯乙烯的生产工艺。
氯乙烯的生产通常采用乙烯与氯气的催化氯化反应。
具体工艺流程如下:首先,将经过净化的乙烯和氯气按一定摩尔比例输入反应器,同时加入适量的反应促进剂。
这些反应促进剂通常是氯代烷烃或二元酸盐等化合物,能够促进乙烯与氯气的反应,并抑制不良的副反应。
其次,反应器内设有适当的加热和冷却装置,以控制反应温度。
反应温度一般在150-250摄氏度之间。
在反应过程中,乙烯和氯气通过催化剂的作用发生氯化反应,生成氯乙烯和氯化氢。
然后,反应混合物通过冷却装置将温度降低至20摄氏度以下,使氯乙烯凝结并从液相分离出来。
分离出的液态氯乙烯可以通过蒸馏和提纯等方法进行进一步处理。
最后,反应副产物氯化氢通过吸收装置吸收和处理,以避免对环境的污染。
吸收装置通常采用碱液(如水溶性钠氢碳酸)来对氯化氢进行吸收,并生成对环境无害的氯化钠。
整个氯乙烯生产工艺中的关键环节是反应催化剂的选择和使用。
催化剂需要具有高活性和高选择性,能够促进乙烯与氯气的氯化反应,同时抑制不良的副反应。
常用的催化剂有铜盐、铁盐和氯化铝等。
此外,工艺中还需要注意安全问题。
氯乙烯是一种具有毒性和高燃烧性的物质,对工人的生命和健康构成一定的威胁。
因此,在生产过程中需要严格控制反应温度和压力,保证设备和操作的安全性。
综上所述,氯乙烯的生产工艺主要包括乙烯与氯气的催化氯化反应、冷却和凝析、分离和提纯以及氯化氢的吸收和处理等环节。
工艺的主要挑战是催化剂的选择和使用,以及安全控制。
通过科学合理的工艺设计和严格的操作管理,可以实现高效、安全、环保的氯乙烯生产。
氯乙烯工艺设计范文

氯乙烯工艺设计范文氯乙烯是一种非常重要的有机化学原料,广泛应用于塑料制品、橡胶制品、合成纤维、涂料、医药和农药等领域。
本文将探讨氯乙烯的工艺设计及其工艺流程。
氯乙烯的工艺设计主要包括原料选择、反应器设计、分离装置设计以及工艺流程优化等方面。
首先,原料选择。
氯乙烯的主要原料是乙烯和氯气。
乙烯是一种广泛存在于石油和天然气中的重要烃类化合物,而氯气则可通过电解食盐水或电解氯化钠来制备。
在原料选择时,需要考虑乙烯和氯气的纯度以及供应的可靠性和成本因素。
其次,反应器设计。
氯乙烯的主要制备方法是通过氯化乙烯反应。
该反应通常是在高温下进行,并利用催化剂促进反应速率。
反应器的设计要考虑到反应速率、温度和压力的控制以及产物的分离等因素。
分离装置设计是氯乙烯工艺设计的关键一步。
氯乙烯的主要杂质是氯化乙烯和1,2-二氯乙烷。
分离装置的设计要考虑到这些杂质的物理性质和沸点,并采取合适的分离方法,如精馏、冷凝和吸收等。
最后,对氯乙烯的工艺流程进行优化是提高生产效率和产品质量的关键。
在工艺流程中,可以采用节能措施和改进操作条件来减少能耗和排放。
此外,还可以进行废气处理和废水处理,以减少对环境的污染。
总的来说,氯乙烯工艺设计是一个复杂而关键的过程。
通过合理选择原料、合适的反应器设计、优化的分离装置和工艺流程,可以实现高效生产氯乙烯,并提高产品质量和减少环境污染。
在实际应用中,还需要与相关部门合作,遵守相关法规和标准,确保工艺的安全和可持续发展。
年产5万吨PVC的氯乙烯合成工段的工艺设计

氯乙烯是一种重要的有机化工原料,广泛应用于塑料、橡胶、涂料等行业。
为了满足年产5万吨PVC的生产需求,需要进行氯乙烯的合成工艺设计。
本文将从原料选择、反应条件、催化剂选择、分离工艺、产品纯化和废水处理等方面进行详细讨论。
首先,氯乙烯的合成主要通过乙烯进行氯化反应得到。
乙烯可以采用石油轻烃或乙烷气相氯化的方法进行制备,其中后者是最常用的方法。
乙烯和氯气在加热的条件下进入氯化炉,通过氯化剂进行反应。
在反应条件方面,首先需要控制反应温度和压力。
一般来说,氯乙烯的合成反应需要在高温条件下进行,可以选择在300-400℃之间的温度范围内进行反应。
压力方面,一般选择在1-3 atm之间。
此外,还需要控制乙烯和氯气的摩尔比,通常选择1:1的比例。
催化剂选择是氯乙烯合成的重要环节。
常用的催化剂有氧化铜、氯化铜和氯化铁等。
其中,氧化铜催化剂广泛应用于工业氯乙烯的合成中,因其催化活性高,选择速度快,具有良好的经济效益。
在分离工艺方面,主要是将合成氯乙烯和催化剂进行分离。
可以采用蒸馏或萃取等方法,将氯乙烯从反应混合物中分离出来。
蒸馏是一种常用的分离方法,通过控制温度和压力,将氯乙烯从混合物中分离出来。
此外,也可以采用萃取的方法,选择适当的溶剂将氯乙烯从混合物中提取出来。
在产品纯化方面,需要对分离得到的氯乙烯进行纯化处理,以提高产品质量。
可以采用氧化、脱色、脱酸等方法进行纯化处理。
其中,氧化是一种常用的方法,通过氯气的氧化作用,将杂质气体、不饱和物质和酸性物质等进行氧化,提高产品纯度。
最后,需要对废水进行处理,以满足环保要求。
合成氯乙烯的过程中会产生含有盐酸和氯化物等的废水,需要进行中和处理和固液分离等工艺,以达到排放标准。
综上所述,年产5万吨PVC的氯乙烯合成工段的工艺设计,需要从原料选择、反应条件、催化剂选择、分离工艺、产品纯化和废水处理等方面进行综合考虑。
通过合理的工艺设计和操作控制,可以实现高效、稳定的氯乙烯合成过程,满足PVC生产的需求。
年产10万吨氯乙烯工艺设计
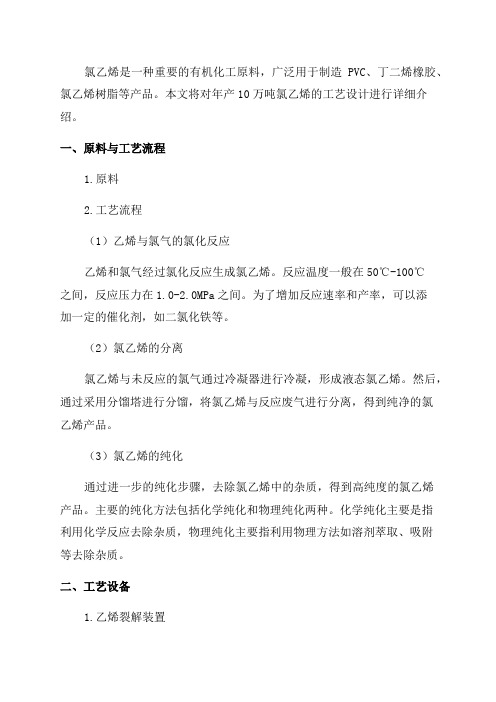
氯乙烯是一种重要的有机化工原料,广泛用于制造PVC、丁二烯橡胶、氯乙烯树脂等产品。
本文将对年产10万吨氯乙烯的工艺设计进行详细介绍。
一、原料与工艺流程1.原料2.工艺流程(1)乙烯与氯气的氯化反应乙烯和氯气经过氯化反应生成氯乙烯。
反应温度一般在50℃-100℃之间,反应压力在1.0-2.0MPa之间。
为了增加反应速率和产率,可以添加一定的催化剂,如二氯化铁等。
(2)氯乙烯的分离氯乙烯与未反应的氯气通过冷凝器进行冷凝,形成液态氯乙烯。
然后,通过采用分馏塔进行分馏,将氯乙烯与反应废气进行分离,得到纯净的氯乙烯产品。
(3)氯乙烯的纯化通过进一步的纯化步骤,去除氯乙烯中的杂质,得到高纯度的氯乙烯产品。
主要的纯化方法包括化学纯化和物理纯化两种。
化学纯化主要是指利用化学反应去除杂质,物理纯化主要指利用物理方法如溶剂萃取、吸附等去除杂质。
二、工艺设备1.乙烯裂解装置乙烯裂解装置是将较重的石脑油等原料在适宜的温度下进行裂解,生成乙烯。
2.电解氯化钠装置电解氯化钠装置将氯化钠电解产生氯气。
3.盐酸制备装置盐酸制备装置通过反应制备盐酸。
4.氯化反应釜氯化反应釜是进行乙烯与氯气的氯化反应的设备,通过控制反应温度和压力,实现氯乙烯的产生。
5.冷凝器冷凝器通过冷凝氯乙烯和氯气混合物,将其分离出液态氯乙烯。
6.分馏塔分馏塔通过分馏氯乙烯和反应废气,将纯净的氯乙烯产品分离出来。
三、工艺设计1.反应温度和压力的选择反应温度和压力的选择会影响氯化反应的速率和产率。
合理选择反应温度和压力可以提高氯乙烯的产率,并且减少副反应的产生。
2.催化剂的选择和适量添加适量添加一定的催化剂可以提高氯化反应速度和产率,促进反应的进行。
常用的催化剂有二氯化铁等。
3.设备选型和工艺流程优化选用适当的设备和优化工艺流程可以提高工艺的效率和产品质量,同时降低能耗和成本。
4.废气处理废气处理也是工艺设计中的重要环节,通过合适的废气处理方法,减少对环境的污染。
年产20万吨氯乙烯工艺设计

氯乙烯是一种重要的有机化工原料,广泛应用于塑料制品、合成橡胶、建筑材料和溶剂等领域。
在工业生产中,氯乙烯的工艺设计对于提高生产效率和产品质量具有重要的意义。
本文将对年产20万吨氯乙烯工艺设计进行详细的介绍。
首先,了解氯乙烯的制备原理是进行工艺设计的基础。
氯乙烯的主要生产方法有氯乙烯法和氧化法两种。
在氯乙烯法中,通过乙烯与氯气反应得到氯乙烯;而在氧化法中,通过氯乙烯的氯化得到氯乙烯。
根据产品数量和质量的需求,选择合适的制备方法是工艺设计的第一步。
接下来,确定反应器的类型和工艺条件。
反应器的选择和设计对于氯乙烯的产率和质量有着重要的影响。
目前,氯乙烯的制备主要使用的是氯乙烯法,其中常见的反应器有氯化塔和热式氯化器。
在工艺设计中,需要考虑反应温度、压力、氯乙烯的流量和催化剂的使用量等参数,以实现最佳的反应条件和产量。
在氯乙烯制备过程中,生成的氯乙烯需要通过分离和纯化来获得高纯度的产品。
分离和纯化的工艺流程包括吸附、蒸馏、吸收、冷凝等步骤。
各个步骤的选择和操作条件要根据产品要求进行设计,以避免杂质和不纯物质的混入。
此外,在工艺设计中还需要考虑废弃物的处理和环保要求。
氯乙烯的制备过程中会产生一定数量的废弃物和排放物,如副产盐酸、氯化氢等。
为了保护环境和减少污染,需要对废弃物进行妥善处理和处置。
最后,要进行工艺设计的经济评估和计算。
针对年产20万吨氯乙烯的工艺设计,需要进行原料成本分析、设备投资和运营成本等方面的计算,以评估项目的可行性和经济效益。
总结而言,年产20万吨氯乙烯的工艺设计包括制备原理的选择、原料的选择和准备、反应器的类型和工艺条件的确定、分离和纯化的工艺流程设计、废弃物处理和环保要求的考虑以及经济评估和计算等方面。
通过科学的工艺设计和优化,可以提高生产效率和产品质量,实现可持续发展和经济效益。
年产10万吨氯乙烯工艺设计

一、总体技术方案
1.1产品和质量要求
本工艺设计是针对每年产10万吨氯乙烯的,氯乙烯工艺流程采用芳
烃炔反应法生产,氯乙烯产品的质量指标应符合GB1408-93的质量标准,
即重量分析:99.6%以上;含醚:≤0.1%;酸值:≤0.1%;氯代烷烃:
≤0.3%;芳香族烃:≤0.2%;苯、邻苯和对苯二甲酸盐:≤0.05%;其
他不溶物:≤0.05%。
1.2主要工艺装置
本工艺设计中,主要工艺装置有芳烃炔反应塔(精炼装置)、精馏装置、蒸发装置、精分装置、气液混合装置、冷凝装置、蒸馏装置、再精馏
装置、萃取装置、汽油装置、热交换装置、分离装置、调节装置等。
1.3工艺流程
(1)芳烃炔反应:用氢气与乙炔反应在芳烃炔反应塔(精炼装置)内,产生氯乙烯油和稀释气,氯乙烯油经过精馏和蒸发进行净化,获得氯
乙烯产品;
(2)水蒸馏:将氯乙烯油送入蒸发器,加入混合物,经过精分后进
入气液混合装置,使稀释混合物加热混合,然后经过冷凝器,进入蒸馏器,经过混合,蒸发内循环,使氯乙烯油升温进行深度蒸馏,从而获得氯乙烯
产品;。
年产20万吨氯乙烯工艺设计
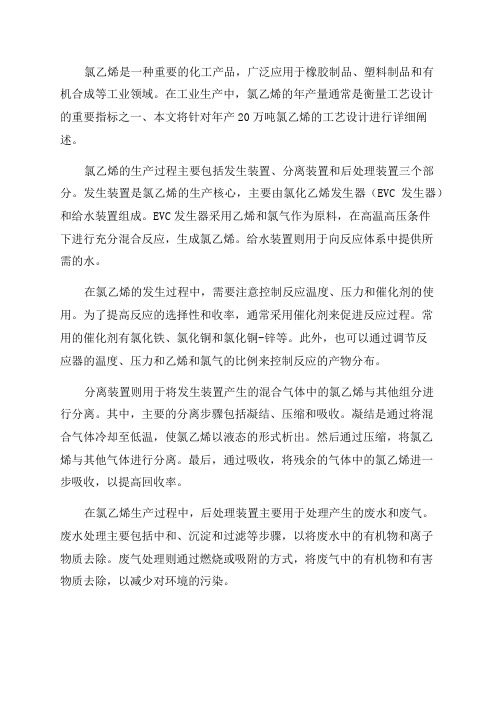
氯乙烯是一种重要的化工产品,广泛应用于橡胶制品、塑料制品和有机合成等工业领域。
在工业生产中,氯乙烯的年产量通常是衡量工艺设计的重要指标之一、本文将针对年产20万吨氯乙烯的工艺设计进行详细阐述。
氯乙烯的生产过程主要包括发生装置、分离装置和后处理装置三个部分。
发生装置是氯乙烯的生产核心,主要由氯化乙烯发生器(EVC发生器)和给水装置组成。
EVC发生器采用乙烯和氯气作为原料,在高温高压条件下进行充分混合反应,生成氯乙烯。
给水装置则用于向反应体系中提供所需的水。
在氯乙烯的发生过程中,需要注意控制反应温度、压力和催化剂的使用。
为了提高反应的选择性和收率,通常采用催化剂来促进反应过程。
常用的催化剂有氯化铁、氯化铜和氯化铜-锌等。
此外,也可以通过调节反应器的温度、压力和乙烯和氯气的比例来控制反应的产物分布。
分离装置则用于将发生装置产生的混合气体中的氯乙烯与其他组分进行分离。
其中,主要的分离步骤包括凝结、压缩和吸收。
凝结是通过将混合气体冷却至低温,使氯乙烯以液态的形式析出。
然后通过压缩,将氯乙烯与其他气体进行分离。
最后,通过吸收,将残余的气体中的氯乙烯进一步吸收,以提高回收率。
在氯乙烯生产过程中,后处理装置主要用于处理产生的废水和废气。
废水处理主要包括中和、沉淀和过滤等步骤,以将废水中的有机物和离子物质去除。
废气处理则通过燃烧或吸附的方式,将废气中的有机物和有害物质去除,以减少对环境的污染。
在工艺设计过程中,还需要考虑原料的质量、能耗和产品质量等因素。
优化原料的选择和处理过程,可以提高反应的效率和选择性;降低能耗,可以减少生产成本;控制产品质量,可以满足市场需求。
综上所述,年产20万吨氯乙烯的工艺设计主要包括发生装置、分离装置和后处理装置三个部分。
通过合理选择催化剂、控制反应条件和优化分离和后处理过程,可以实现高效、稳定、环保的氯乙烯生产。
年产20万吨PVC氯乙烯单体合成工序工艺设计

(年 月本科毕业设计说明书 学校代码: 学 号:题 目:年产20万吨PVC 氯乙烯单体合成工序工艺设计 学生姓名: 学 院: 系 别: 专 业:化学反应工程与工艺 班 级: 指导教师:摘要Abstract目录引言 (1)第一章绪论 (2)1.1聚氯乙烯工业的发展概况 (2)1.1.1聚氯乙烯工业 (2)1.1.2国外聚氯乙烯工业的发展 (2)1.1.3聚氯乙烯的性质与性能 (3)1.2中国的聚氯乙烯工业 (5)1.3聚氯乙烯的分类 (5)1.4聚氯乙烯工业在国民中经济中的重要意义 (6)1.5厂址的选择 (6)第二章聚氯乙烯生产过程 (8)2.1氯乙烯的生产方法及方案的确定 (8)2.1.1电石乙炔法 (8)2.1.2联合法 (8)2.1.3乙烯法 (9)2.1.4乙烯氧氯化法 (10)2.1.5烯炔法 (11)2.2氯乙烯单体的聚合 (11)2.2.1氯乙烯悬浮聚合法 (12)2.2.2本体聚合 (13)2.2.3乳液聚合 (13)2.2.4微悬浮聚合及微悬浮种子聚合法 (14)2.3生产流程及特点 (14)2.3.1氯化氢的制备 (14)2.3.2乙炔的制备 (16)2.3.3氯乙烯的制备 (17)2.3.4氯乙烯的精馏 (21)第三章物料衡算 (24)3.1生产条件 (24)3.2原料气的物料衡算 (24)3.3混合器的物料衡算 (25)3.4石墨冷凝器的物料衡算 (26)3.5转化器的物料衡算 (27)3.6水洗塔的物料衡算 (29)3.7碱洗塔的物料衡算 (30)3.8低沸塔的物料衡算 (31)3.9高沸塔的物料衡算 (32)第四章热量衡算 (34)4.1石墨冷凝器的热量衡算 (34)4.2转化器的热量衡算 (35)4.2.1反应热Q反 (36)4.2.2原料气带入热Q入 (36)4.2.3出料带出热Q出 (37)4.2.4热损失Q损 (37)4.2.5热载体所需量 (38)4.3高沸塔的热量衡算 (38)4.3.1热量衡算 (39)4.3.2再沸器所需GH及冷凝器所需冷冻盐水量GC的计算 (41)第五章设备型计算 (44)5.1石墨冷凝器的造型计算 (44)5.1.1求取平均温度差 (44)5.1.2确定传热面积和传热系数 (44)5.1.3利用给热系数验算K值 (45)5.1.4最后确定K值和传热面积 (49)5.2转化器的选型计算 (49)5.2.1传热面积的计算 (49)5.2.2催化剂的装填量 (50)第六章车间厂房布置设计 (52)6.1厂房布置设计的条件加依据 (52)6.1.1常用的设计规范和规定 (52)6.1.2厂房布置设计的基本条件 (52)6.1.3厂房布置设计的基本依据 (52)6.2车间厂房的布置设计 (53)6.2.1厂房的平面布置 (53)6.2.2厂房的空间布置 (54)6.2.3厂房布置设计时须注意的问题 (55)结论参考文献 (56)参考文献 (57)谢辞 (58)引言第一章绪论1.1聚氯乙烯工业的发展概况1.1.1聚氯乙烯工业乙烯早在1835年就为法国V.勒尼奥发现,用日光照射聚乙烯时生成一种白色固体,即聚氯乙烯。
年产30万吨氯乙烯工艺设计

氯乙烯(VCM)是一种重要的有机化工原料,在塑料、橡胶、涂料和溶剂等方面具有广泛的应用。
为了满足市场需求,需要进行年产30万吨氯乙烯的工艺设计。
氯乙烯的生产一般是通过乙烯与氯气在催化剂的作用下发生氯化反应得到的。
在工艺设计中,需要考虑以下几个方面:原料选择,反应条件和催化剂的选择。
对于原料选择来说,乙烯和氯气是氯乙烯生产的两个主要原料。
乙烯是石化工业中非常重要的化工原料,可以通过石化企业的乙烯装置进行采购。
而氯气则需要通过电解盐水或一些工艺方法得到。
通过分析市场需求和具体情况,可以选择合适的供应商和生产工艺路线来获取乙烯和氯气。
在反应条件方面,乙烯与氯气的氯化反应需要在一定的温度和压力下进行。
通常情况下,氯乙烯的氯化反应温度在100-200°C之间,压力在0.5-3MPa之间。
同时,还需要考虑反应物的进料速度、混合程度等因素,以及对反应产物的处理方式等。
对于催化剂的选择,氯乙烯的氯化反应需要选择合适的催化剂。
常用的催化剂有氯化铁、氯化铝和氯化销等,这些催化剂对反应速率和产物选择性有一定的影响。
选择合适的催化剂可以提高化学反应的效果,减少副反应的发生,从而提高氯乙烯的产率。
在工艺设计中,还需要考虑反应过程中的能量平衡和废气处理等问题。
氯乙烯的生产通常是一个能量密集型过程,需要考虑能源的供应和利用,以及废气处理的设备和工艺。
综上所述,年产30万吨氯乙烯的工艺设计需要考虑原料选择、反应条件、催化剂选择、能量平衡和废气处理等方面的问题。
通过合理的工艺设计,可以实现高效的氯乙烯生产,满足市场需求。
化工PVC各工段工艺流程

化工PVC各工段工艺流程一、概述聚氯乙烯(PVC)是一种重要的化工原料,广泛应用于建筑、包装、医疗等领域。
PVC的生产工艺通常包括原料制备、聚合、塑化、挤出、成型等多个工段,每个工段的工艺流程和操作步骤都至关重要。
二、原料制备工艺流程PVC的原料主要包括乙烯、氯气等,原料制备工艺流程如下:1.乙烯制备:乙烯是PVC的主要原料之一,通过乙烯裂解或乙烯蒸馏等工艺获得。
2.氯气制备:氯气是PVC的另一重要原料,通常通过盐水电解等方式获得。
3.氯乙烯合成:将乙烯和氯气在催化剂作用下进行氯化反应,生成氯乙烯。
三、聚合工艺流程聚合是PVC生产的核心工艺之一,通过聚合可以将氯乙烯聚合成PVC树脂,常见的聚合工艺流程如下:1.聚合反应:将氯乙烯溶于溶剂中,加入引发剂和稳定剂,控制温度和压力进行聚合反应。
2.精滤:将聚合得到的PVC树脂溶液进行过滤,去除杂质。
3.干燥:将精滤后的PVC树脂溶液进行干燥,得到PVC树脂粉末。
四、塑化工艺流程PVC树脂需要进行塑化处理,以增加其适应性和加工性,常见的塑化工艺流程如下:1.加热混合:将PVC树脂和增塑剂等混合物加热至一定温度,使其软化。
2.冷却混合:冷却加热混合物,使其形成均匀的PVC塑料熟料。
3.颗粒化:将塑化好的PVC熟料经过颗粒机或挤出机进行颗粒化。
五、挤出成型工艺流程挤出是PVC制品生产的重要工艺环节,通过挤出机将PVC颗粒挤出成型,常见的挤出成型工艺流程如下:1.挤出:将PVC颗粒加热至熔化状态,通过螺杆挤出机挤出成型。
2.卷取:将挤出好的PVC制品通过卷取机卷取成卷状,便于后续加工和使用。
3.冷却:对挤出成型后的PVC制品进行冷却处理,使其达到设计要求的硬度和形状。
六、总结PVC的生产工艺包括原料制备、聚合、塑化、挤出、成型等多个工段,每个工段都有其独特的工艺流程和操作要点。
只有严格按照工艺流程进行操作,控制温度、压力和时间等关键参数,才能生产出优质的PVC制品。
氯乙烯生产工艺流程设计与安全评价

氯乙烯生产工艺流程设计与安全评价氯乙烯是一种广泛应用于塑料、橡胶、助剂等行业的重要化工产品。
本文将就氯乙烯的生产工艺流程设计和安全评价进行探讨,为相关工程设计和生产管理提供有益参考。
一、氯乙烯的生产工艺流程设计氯乙烯的生产主要通过乙烯与氯气在催化剂的作用下发生氯化反应得到。
下面将按照先后顺序描述氯乙烯的生产工艺流程设计:1. 乙烯的净化与储存:这一步骤主要是通过分离和净化来提高乙烯的纯度,通常采用冷凝技术和吸附剂的使用。
2. 氯气的净化与储存:与乙烯相似,氯气也需要经过净化处理,主要是去除杂质和水分。
3. 氯化反应:将经过净化处理的乙烯与氯气按照一定比例进入氯化炉中,在催化剂的作用下发生氯化反应生成氯乙烯。
4. 氯乙烯的分离与净化:通过采用蒸馏、浓缩、洗涤等工艺,将氯乙烯与杂质分离,提高氯乙烯的纯度。
5. 尾气处理:氯乙烯生产过程中会产生大量尾气,其中包含的氯气、乙烯、氯乙烯等有机物和杂质需要进行处理,以减少对环境的污染。
二、氯乙烯生产工艺流程的安全评价在氯乙烯的生产过程中,安全问题一直备受关注。
以下是对氯乙烯生产工艺流程的安全评价的一些建议和注意事项:1. 设备安全:在氯乙烯的生产过程中,各种设备的安全是首要考虑的问题。
包括氯化炉、分离塔、蒸馏设备等,需要符合相应的安全标准,并定期进行检修和维护,确保设备的正常运行。
2. 原料储存和供应系统的安全:乙烯和氯气作为重要原料,储存和供应系统的安全是保证生产过程稳定的重要环节。
需要采取安全措施,避免泄漏和事故发生。
3. 废气处理系统的安全:废气处理对环境保护至关重要,需要进行规范的设计和操作,确保废气的处理达到相关标准。
4. 防火防爆措施:氯乙烯属于易燃易爆物质,需要在生产过程中采取相应的防火防爆措施,减少火灾和爆炸的风险。
5. 操作员培训和安全意识提升:对从事氯乙烯生产工作的操作员进行专业培训,提高其安全意识和应急处置能力,减少事故的发生。
综上所述,氯乙烯的生产工艺流程设计和安全评价是关乎生产安全和环境保护的重要内容。
乙烯氯化制氯乙烯工艺流程设计与安全性评价

乙烯氯化制氯乙烯工艺流程设计与安全性评价一、概述在化工领域,乙烯氯化制氯乙烯是一种重要的工艺过程。
它是通过将乙烯和氯气进行氯化反应,生成氯乙烯。
本文将从工艺流程设计和安全性评价两个方面探讨乙烯氯化制氯乙烯过程。
二、工艺流程设计1. 原料准备首先,需要准备乙烯和氯气作为反应的原料。
乙烯通常通过蒸馏分离纯化得到,而氯气则需要经过脱水和脱硫等预处理步骤。
2. 氯化反应将乙烯和氯气按照一定的比例引入氯化反应器中,加热至适当的温度,并施加适当的压力。
在反应器中,乙烯与氯气发生氯化反应,生成氯乙烯。
3. 分离和净化经过氯化反应后,产生的氯乙烯与副产物和未反应的乙烯、氯气等混合物需要进行分离和净化。
这一步骤通常包括凝固、升华、吸附等工艺操作,以得到纯度较高的氯乙烯产品。
4. 氯化副产物处理在乙烯氯化过程中,还会产生一些氯化副产物,如氯化氢和四氯化碳等。
这些副产物需要进行处理,以避免对环境和人体健康造成影响。
三、安全性评价1. 压力控制在乙烯氯化制氯乙烯过程中,反应器的内部压力是一个关键参数。
合理控制反应器的压力,可以确保反应过程稳定安全。
过高的压力可能导致反应器爆炸,而过低的压力则可能影响反应速率和产品质量。
2. 温度控制乙烯氯化反应需要在适当的温度条件下进行。
过高或过低的温度都会对反应速率和产品质量产生不利影响,甚至引发危险情况。
因此,对反应器的温度进行精确控制,可以提高工艺的安全性和稳定性。
3. 废气处理乙烯氯化制氯乙烯过程中会产生大量废气,其中包含有毒有害的气体和颗粒物。
必须对这些废气进行有效处理,以减少对环境的污染和对人体健康的损害。
通常采用吸附、吹扫、冷凝等处理方法。
4. 库存管理由于乙烯氯化工艺存在一定的危险性,需要对原料和产物进行严格的库存管理。
防止事故和泄漏的发生,并确保工艺的持续运行。
五、结论乙烯氯化制氯乙烯工艺流程的设计与安全性评价是保证工艺运行安全和高效的重要环节。
通过合理控制参数、处理废气和库存管理等措施,可以最大程度地提高工艺的安全性和稳定性。
- 1、下载文档前请自行甄别文档内容的完整性,平台不提供额外的编辑、内容补充、找答案等附加服务。
- 2、"仅部分预览"的文档,不可在线预览部分如存在完整性等问题,可反馈申请退款(可完整预览的文档不适用该条件!)。
- 3、如文档侵犯您的权益,请联系客服反馈,我们会尽快为您处理(人工客服工作时间:9:00-18:30)。
前言氯乙烯单体(VCM)几乎全部(98%以上)都用来生产聚氯乙烯(PVC)。
余下的则用于生产聚氯乙烯氯化物和氯化溶剂。
传统工艺的电石法精馏氯乙烯质量已不能满足PVC 树脂的生产要求,受其工艺流程及精馏塔塔型的限制,原氯乙烯精馏装置规模小,产品质量较差,尾气放空量大,造成氯乙烯、乙炔流失量大,导致生产成本较高,环境污染严重。
最初的氯乙烯生产全部以乙炔为原料。
60年代后期,随着乙烯装置大型化及乙烯氧氯化技术的成熟,乙烯法在经济和环保等方面占有明显的优势,在世界范围内乙炔法迅速被乙烯法取代。
迄今为止,全世界氯乙烯装置93%以上采用乙烯法,在工业发达国家如日本,以全部淘汰了乙炔法,仅在我国及其它发展中国家仍占有相当比重。
目前国内比较先进而又经济可行的成熟工艺技术是电石乙炔法本设计用美国ChemStations公司开发的流程模拟软件ChemCAD软件对电石乙炔法制备VCM进行了工艺模拟设计与计算,计算主要包括物料衡算和热量衡算,用计算所得到的相关数据对此工艺中所涉及到的设备进行选型,主要包括塔的选型、换热器的选型、泵的选型等,然后用PDSOFT三维软件对车间设备进行布置,为工业生产提供参考。
11 总论1.1 概述1.1.1 意义与作用氯乙烯(简称VCM),是无色的、易液化的气体。
易聚合,也能与丁二烯、乙烯、丙烯、丙烯睛、酷酸乙烯、丙烯酸醋和马来酸醋等共聚。
主要用于制备PVC,也用于制备偏二氯乙烯、冷冻剂等。
氯乙烯单体几乎全部(98%以上)都用来生产聚氯乙烯。
余下的则用于生产聚氯乙烯氯化物和氯化溶剂。
通过对二氯乙烷(EDC)裂解后脱除HCL,以及干燥精制可获得制造PVC级的VCM。
由于资源结构的特点,世界上只有我国的氯碱行业有电石法生产PVC,其他国家都是通过乙烯法生产PVC,即乙烯直接氯化、氧氯化生产EDC,进而裂解生产VCM制造PVC。
其中96%VCM均用于生产PVC。
聚氯乙烯(简称PVC)是五大热塑性合成树脂之一,以其价廉物美的特点,占合成树脂总消费量的29%左右,仅次于聚乙烯居第二位。
由于PVC树脂具有优良的耐化学腐蚀性、电绝缘性、阻燃性、质轻、强度高且易加工、成本又低,因而PVC制品广泛用于工业、农业、建筑、电子电器及人们生活中的各个领域。
PVC硬质制品可代替金属制成各种工业型材、门窗、管道、阀门、绝缘板及防腐材料等,还可作收音机、电话、蓄电池外壳及家俱、玩具等。
PVC软质品可制成薄膜做雨披、台布、包装材料及农用薄膜,还可制成人造革、电线、电缆的绝缘层。
另外,PVC树脂作为氯碱工业最大的有机耗氯产品,对氯碱工业的碱、氯平衡和发展起到重要的作用。
PVC主要用于建筑业,制造管材、门窗和墙板等。
作为第一大用户,建筑业约占聚氯乙烯消费总量的76%。
其它方面的用量相对较少。
包装薄膜和容器约占消费总量的6%,电气配件、电线电缆包皮约占消费总量的4%,涂料和粘合剂约占消费总量的4%,其他约占消费总量的10%。
1.1.2 氯乙烯生产的国内外现状及发展前景(1)国外发展概况氯乙烯(VCM)的合成始于1835年,由法国化学家Regnault用氢氧化钾的乙醇溶液将二氯乙烷脱氯化氢制得,并于1838年观察到了它的聚合体,这次的发现被认为是PVC 的开端。
1902年,Biltz将1,2-二氯乙烷进行热分解也制得氯乙烯,但当时由于聚合物的科学和生产技术尚不成熟,他的发现没有导致工业生产的结束。
Klatte于1912年通过乙炔与氯化氢的催化加成反应制得了氯乙烯,成为工业上氯乙烯合成的最初工艺,但在沿用将近30多年后,由于乙炔生产的高能耗而逐渐趋于淘汰。
从1940年起,氯乙烯的生产原料,乙炔开始被乙烯部分取代,首先将乙烯直接氯化成1,2-二氯乙烷(EDC),再加以热裂解制得氯乙烯,裂解产生的氯化氢仍被用在乙炔-氯化氢法中。
混合气体法制备氯乙烯采用石脑油作原料,将石脑油用燃烧气体裂解后,制成含乙炔和乙烯的混合气体,该混合气体先后与氯化氢和氯气反应,制成易分离的氯乙烯和1,2-二氯乙烷经热裂解制成氯乙烯,日本吴羽化学公司将其工业化生产。
将该法中的原料从石脑油换成石油,则成为原油裂解法,可得到高浓度的乙炔、乙烯的混合气体,而且可从副产物的芳香族的焦油、沥青的物质中制造热煤油或碳纤维等物质,具有综合的经济效益。
1955-1958年,美国的化学公司研究的大规模乙烯氧氯化法制备1,2-二氯乙烷取得成功。
至此以后,乙烷全部取代乙炔成为制备氯乙烯的原料。
至目前为止,大多数工厂都采用乙烯直接氯化(DC)和乙烯氧氯化(OXY)制备1,2-二氯乙烷(EDC),再将EDC加以热裂解得到氯乙烯单体(VCM)的联合切平衡的DC-EDC-OXY-EDC-VCM法来制备氯乙烯。
联合平衡法充分利用廉价的原料,基本上不生成副产物,目前西方世界90%以上的氯乙烯产量是用该法生产的。
近年来,世界VCM的生产稳步发展。
2004年全世界VCM的总生产能力为3392.0万吨,2009年增加到4422.8万吨,生产主要集中在亚洲、北美和西欧3个地区,2009年这3个地区的生产能力合计达到3864.9万吨,约占世界总生产能力的87.38%。
其中亚洲地区的生产能力为2296.9万吨,约占世界总生产能力的51.93%;西欧地区的生产能力为657.0万吨,约占总生产能力的14.55%;北美地区的生产能力为911.0万吨,约占总生产能力的20.60%;非洲地区的生产能力为46.0万吨,约占总生产能力的1.04%;中东欧地区的生产能力为256.1万吨,约占总生产能力的5.79%;中东地区的生产能力为129.8万吨,约占总生产能力的2.93%;中南美洲地区的生产能力为126.0万吨/年,约占总生产能力的2.85%。
Formosa Plastics Group公司是目前世界上最大的VCM生产厂家,生产能力为309.7万吨/年,约占世界VCM总生产能力的7.00%;其次是Occidental Petroleum公司,生产能力为260.9万吨/年,约占总生产能力的5.90%;再次是Dow Chemical公司,生产能力为207.0万吨/年,约占总生产能力的4.68%。
其中采用乙炔法工艺路线的生产能力为1074.6万吨/年,约占总生产能力的24.30%;采用二氯乙烷高温分解工艺的生产能力为2731.1万吨/年,约占总生产能力的61.75%;采用乙烯和二氯乙烷工艺路线的生产能力为617.1万吨/年,约占总生产能力的13.95%。
预计2009-2014年,世界VCM的生产能力将以年均约2.1%的速度增长,到2014年总生产能力将超过4918.0万吨。
(2)国内发展概况1954年,沈阳化工研究院开始聚氯乙烯的研究。
1958年,锦西化工厂(现锦化化工集团公司)建成了第一套年产3000吨规模的生产装置,紧接着北京、天津、上海等地也相继又建成四套年产6000吨的装置。
60年代各省市又陆续新建了一批,聚氯乙烯工业得到了较快速的发展,1987年聚氯乙烯生产能力已达到64.54万吨,1990年产量77.7万吨,2001年生产能力约为360万吨/年,2005年我国大约有聚氯乙烯生产厂79家,2009年增加到1307.7吨,约占世界总生产能力的29.57%。
2004-2009年生产能力的年均增长率约为21.06%。
随着韩华(宁波)、甘肃新川、陕西金泰、宁夏英力特等多套新建或扩建装置的建成投产,预计到2014年,我国VCM的总生产能力将达到约1508.7万吨。
九十年代中期以前,原料氯乙烯单体主要采用电石乙炔法制得。
七十年代中期,随着3我国石油化工的迅速发展,国内开始建设乙烯氧氯化法制氯乙烯装置。
1976年10月,北京化工二厂引进的年产8万吨由乙烯氧氯化法生产氯乙烯装置建成投产。
1979年又引进了两套年产20万吨乙烯氧氯化生产装置,分别建在山东齐鲁石化公司和上海氯碱总厂。
2004年电石法工艺路线占我国PVC能力的60%以上。
电石是我国PVC生产最主要的原料之一。
2004年国内电石产量654万吨,其中西南地区产量为111.53万吨,约占全国的17.05%,其中四川产量为66.53万吨,占全国的10.17%。
(3)氯乙烯生产工艺的发展前景由于传统的电石乙炔法制氯乙烯需要消耗大量电能,对环境造成了严重的污染,我国在几家较大的氯乙烯生产厂引进了日本、欧洲的平衡氧氯化生产工艺,该工艺由于具有成本低、质量高、污染小、易于大规模生产等优点,是目前世界上比较通用的氯乙烯生产工艺。
但是,平衡氧氯化法生产氯乙烯需要大量消耗石油中的乙烯,随着石油资源的日益短缺和对氯乙烯供不应求矛盾的日益尖锐,这一工艺也暴露出它的弊端。
最初的氯乙烯生产全部以乙炔为原料。
60年代后期,随着乙烯装置大型化及乙烯氧氯化技术的成熟,乙烯法在经济和环保等方面占有明显的优势,在世界范围内乙炔法迅速被乙烯法取代。
迄今为止,全世界氯乙烯装置93%以上采用乙烯法,在工业发达国家如日本,以全部淘汰了乙炔法,仅在我国及其它发展中国家仍占有相当比重。
随着聚氯乙烯的发展,氯乙烯的生产工艺技术也不断完善,特别是乙烯工业的快速发展,VCM的生产越来越趋向于采用大型的乙烯氧氯化法生产工艺技术。
在国内,除上述已投产的5套乙烯氧氯化法生产装置以外,上海天原化工集团公司将在上海化工园区新建,30万t/a VCM装置,齐鲁与台塑合资新建20万t/a VCM装置,DOW化学公司与天津合资拟建20万t/a VCM装置,北二化拟扩20万t/a,锦西拟扩20万t/a等等。
由此可见,进一步扩大VCM装置的生产能力,引人先进的计算机生产管理系统,不断改善VCM生产工艺和设备,是国内外VCM生产的发展方向。
因此,我国VCM生产的发展应该在引进国外先进工艺技术的同时,结合实际,合理确定发展规模,尽可能降低成本,讲求效益,从而进一步提高产品的市场竞争能力。
1.1.3 氯乙烯生产工艺概述目前世界上有5种氯乙烯(VCM)生产方法,即电石乙炔法、乙烯氧氯化法、电石乙炔—二氯乙烷联合法、混合烯炔法及石油(或天然气)乙炔法。
电石乙炔法是生产氯乙烯最早工业化的方法,主要利用乙炔和氯化氢为原料,用HgCl2做催化剂进行加成反应,生成氯乙烯,该法的优点是设备工艺简单,投资少,产品纯度高,缺点是电石耗电大,使成本上升,反应中使用的催化剂污染较严重。
电石乙炔法是生产氯乙烯最早工业化的方法,设备工艺简单,投资少,产品纯度高。
反应基本原理:乙炔和氯化氢在以氯化汞为活性组份,以活性碳为载体的催化剂上气相反应生成氯乙烯。
5主反应:22222CaC +H O=C H +Ca(OH)2H g c l 22C H + HCl CH=CHC1+124.7 7kJ −−−→副反应:2223C H + H O =CH CHOC 2H 2+HgCl 2−−→ClCH=CHCl+HgCl 2 232C H =C H C I +H C l C H C H C l−−→ 乙烯氧氯化法是利用乙烯和氯化氢氯化生成二氯乙烷,二氯乙烷热裂化生成氯化氢和氯乙烯,氯气、氧气、和氯化氢反应生成二氯乙烷的方法,整个过程中氯化氢始终保持平衡,该法的主要优点是利用二氯乙烷热裂解所产生的氯化氢作为氯化剂,从而使氯得到了完全利用。