机械加工行业APS生产计划排程应用案例
APS高级生产计划与生产排程-PPT
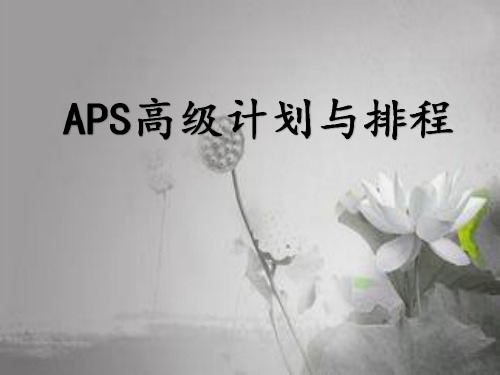
拉动计划-看板
传统MPS/MRP模式
APS精益混合管理模式
精益 传统 产模精
1、什么是APS? 2、APS在制造信息化位置与关系?
4、APS的难度与挑战
制造企业面临的困境
• 我们很多人身体长期都处于亚健康状态,忽视了三 高(高血糖、高血压、高血脂)。
• 制造企业存在长期亚健康状态,忽视“三高”:
当资源需要动态选择加工时,也就是对顺序规则从 新选择时, 如最小准备时间规则等。
4、资源组成员分配规则 当须选择多个资源,替代资源时,如最小
资源利用率资源等。
APS计划和排程
APS是一种新的计划方法
• 一个新的计划方法: “APS 在客户订单输入时, 能及时计划: .人力产能
.生产设备与工具产能排程 .物料需求计划
2,具体设备产能的、模具、物料、人员的约束计算,无论是按日、班次、 分钟计划非常重要,这影响到客户的精确交期。对插单、模拟调整是很多 企业非常重要的。产能是和多个产品、交期、需求同时变化的。尤其是瓶 颈产能,如有合理的排程顺序,产能是可以最有效利用的。(没必要那么
详细、尽量避免插单等)
3,MPS是主生产排程(Master production schedule),应该是具体指导生产 的,它应该受到产能、模具、物料、人员约束的可执行的主排程。但是。 可惜的是,MPS确实是无约束的手工调整来应对变化,品种一多,再变化 频繁,就力不从心了。如果MPS都是不可执行的计划排程,那么依据它的 MRP就更不准了。(MPS可以计划可以较粗,可以用RCCP分析来调整 MPS)
精益管理的两种方法
连续拉动 – 看板
– 丰田生产系统 – 零件超市系统 – 补充系统 – 订单点系统 – JIT (准时化) 主要消灭时间延迟 广播拉动 – APS – TOC(DBR)
aps之可视化排程

APS高级计划与排程之可视化排程1. APS基本概念什么是排程?一个排程是针对加工过程中,将要发生的不同事件的计划.排程有两个要素:能力和负荷.能力描述可以工作的能力; 负荷描述已经被使用的能力的数量资源: 资源可以被细分为:(1),个人/小组–一个人或一个特别技能的小组(2),工作中心–一台设备, 工作区域或生产线,它们需要排程, 管理和一样的成本方法一个工作中心可以有多个单元.(3)外加工–可以执行外加工服务的供应商(4),资源组–在同样时间需要的一组资源.或是可以互相替代的资源.一个资源的能力: 是按照能力的单元.有多少个生产订单可以同时在资源工作.(1)有限能力: 能力被限制.(2)无限能力: 能力没有限制或可以通知.日历: 描述正常工作天数, 开始时间, 班次, 制造设施的在班时间或一个特别的资源例外日历: 描述区别于正常工作天数开始时间, 班次, 制造设施的在班时间或一个特别的资源什么是向后排程?是从最后一个工序和工作的需要的完成日期向后计划每一个加工工序的完成日期什么是向前排程?是从第一工序的下达日期按每一个顺序向前计划一开始日期.生产定单 :一个任务或生产的数量,它们将要在一起生产,共享同样的需要完成日期.生产定单的要素:(1),工序. 工作定单可以包括多个有顺序的工序. 是执行加工过程的一任务工序的要素:开始日期–工序排程的开始日期完成日期 -工序排程的完成日期冻结–保持一个或多个工序在一时间内被固定,不允许自动重排.并发资源–在执行一个工序时需要多个资源 (例如. 利用准备和在机器操作的人.(2), 物料–采购的物料或半成品.(3),优先级–在排程过程中,决定哪一个工作订单最先得到能力处理(4),下达日期 - “最早允许开始日期” ,针对于向前排程的工作订单.(5), 想要日期–工作定单需要完成的日期(6), 开始日期–工作定单的第一个工序的开始日期(7), 完成日期–一个完成的工作定单的最后一个工序的完成日期.产销量–制造企业通过销售,价值减去物料成本和外加工服务的所有金额.它是效率和利润评价.库存–所有投资原材料和资本设备的开支.经营费用(OE) –所有保持业务经营,包括那些设施和人工的开支.Visual 的专利同步排程器–基于用户可选的工厂排程.排程窗口- 图型显示排程.产销量窗口–一排程的产销值,是用户定义当前和将来瓶颈的主要工具.派工单–对每一个车间资源所有固定的和下达的工序的清单排程资源使用的信息(1)能力:描述你的可以工作的能力(2),负荷:负荷描述多少已经分配的能力一个资源的能力是以能力的单元来表述的在同样的资源同时工作的多少任务.决定一资源的能力l班次日历时间(小时/班)l每班的能力单元(单元/班)2 排程设置排程类型: 同步排程器支持两类:有限和无限能力检查物料可用性: 现有量, 计划可用,零件的得到的提前器适合容限: 排程算法考虑对给定工序排程的差异时间的百分比.例如,你设置90,它假设你能完成剩余的10%.排程器就寻找一个可以适合90%的差异的工序.排程模式(1), 向后排程: 生产订单的想要日期驱动订单的排程.是从最后一个工序和工作的需要的完成日期向后计划每一个加工工序的完成日期(2), 向前排程 : 生产订单的下达日期驱动订单的排程.是从第一工序的下达日期按每一个顺序向前计划一开始日期.工序持续时间:每一个工作订单工序有一计算开始数量,基于满足生产订单的下游工序的需要数量和损耗水平.计算基于运行时间,运行类型和负荷大小.资源小时 = (准备小时 x #机器数) + (开始数量 x 运行小时)/件一个附加因素是移动小时.虽然不会产生负荷,他们却会影响下一个工序的开始. 你可以表达一个有效的工序持续时间:工序持续时间= 资源小时 +移动小时 = 准备小时 + (开始数量 x 运行小时)/件+移动小时服务工序(外加工):工序持续时间 =运送天数工序提前期决定工序什么时候开始,这个日期叫工序的“可开始日期” .如果能力是不限制,工序就可以在这个日期开始.但是,它不能在这个日期之前开始,因为之前的工序仍需要时间完成. “可开始日期”也是车间日历的一个功能.日期不包括资源关闭时间.后排排程:工序可能开始日期 = 想要完成日期–后续工序持续时间的合计向前排程:工序可能开始日期 = 下达日期 + 之前工序持续时间的合计工序重叠以上公式在没有工序重叠时,才是正确的.工序的最小移动数量: 可以规定你需要完成工序的多少件或数量,在他们开始满足下一个工序之前.这会造成工序的可开始日期更有利.(迟于一个想后排程,提前一个向前排程).如, 如果一个工序的结束数量是100,最小移动数量是50, 那么下一个工序可以在之前的工序持续时间的一半开始.假设运行率是一样的.如果消耗工序运行率快于供应工序,那么,它就迟于一半开始.因为在供应工序完成生产之前,它就不能用完件数.工序开始日期和状态当你运行排程器,如果你已经开始(下达)一工序,VISUAL 把状态考虑进去.VISUAL 考虑完成的数量,针对你需要完成的工序分派剩余时间给结束数量你能首先排程开始的工作订单,或者冻结或不冻结开始工序.外加工开始日期w对外加工工序,用服务接受录入/服务状态功能来指明一个日期,当发料给供应商.当运行一新排程,VISUAL 用这个日期来减去运输天数.w基于你已经从经开始工序的事实,从这个工序的需要的运输天数.物料提前期w如果你检查物料可用性,物料就获得提前期进入计算,就像工序提前期.就是说,物料可用量约束工序的开始日期.w如果你计划对一个物料可用的及时性的工序的开始日期,开始日期不会改变.例如, 会考虑一具有提前期15天,没有库存物料, 如果当前车间资源负荷会允许工序从今天的5天开始,检查物料可用性推这个工序到15天,也影响所有相关的工序.在检查物料的可用性,VISUAL 考虑四件事:1,当前库存水平是否满足需求.2,在定量的计划接收的采购3,零件的提前期的最大时间.4,考虑计划工作订单的预期的物料.并发资源如果对一个工序规定准备和运行为并发资源,对这些资源增加平行资源小时需求,VISUAL用那些资源的能力和日历作为主要资源排程.并发资源的日历可以约束主要资源的排程.间断工序排程器支持工序的间断排程. 你可以设置一车间资源以至于VISUA排程间断的工序当在一单元里,一负荷出现冲突. VISUAL用最小分割尺寸比较运行的排程持续时间.如果排程持续时间是一至少最小分割尺寸,那么,排程器建立一“分割”排程.继续排程直到找到一个选择的“分割”的排程,分离时间,除非有足够成功的工序的持续时间的排程.每一个排程,脱节的分割是独立的和包含它的自己的准备和已分配的单元.一个分割可以使用不同的单元,相关的使用率,最小/最大设置,具有不同的任何其它分割的单元号.资源最小和最大在同样的工序,多个资源单元上平行运行.对每一个工序,你能规定最小单元需要开始的工序.VISUAL直到至少这是许多同时发生的单元可用时,才对工序排程.你也可以规定最大资源的能用的工序.如果你不用VISUAL 来用平行的,规定一个最大和排程一个工序,就设置最大为1.生产订单的优先级允许你为生产订单设置1-50.当生产订单争夺同样的资源时,你可以决定采用哪个优先级. 尤其对插单业务.排程类型你可以标志工序排程的两种类型:1,排程连续意味着有足够的能力执行整个工序2,排程间断,你能规定一个最小的分割尺寸.VISUAL必须在分割符合条件之前,在一个单元上排程一个最小分割作为需要的运行持续时间.能力类型你可以标志车间资源两种方法:1,一般是有限能力2, 无限能力日历为一资源规定三班的每一班的持续时间,7天的资源周日历.日历例外允许你修正你的日历.日历可以被定义为特殊资源和/或特别的排程.资源能力VISUAL 定义给定的资源能力是每一天的每一班可用的小时和有多少个能力单元期间可用. 如, 工作中心有3台机器,每天运行8小时,所以工作中心有24小时的能力.(如果工作中心预计有3台机器,每天同班运行8小时,机器就有24小时可用.如果有3个任务或更少,总共24小时或更少,那么工作中心的计划是正确的.然而,工作中心的计划不是由于只有三个任务可以在任何时间运行而不顾持续时间.VISUAL 可以设置这个作为一班8小时,使用3个能力单元.这意味你可以排程在给定的时间期间,对最大的3个设备来符合适合的排程,这不同于24小时能力,由一个单元可用24小时.当你规定能力单元的数量, VISUAL 给每一个分配一个单元号,用0开始.例如,如果一个钻床资源在第一班有3个能力单元, VISUAL 在单元上,排程工序0,1,2,排程器总是先给0号资源单元的负荷然后1等等).一些工序时间比在班的时间少当每一个工序花两小时,你有能力8小时/班和3个能力单元.排程器排程用2小时做12个.每天: 每一个单元可以做4个/8小时.使用三个平行运行.班之间的能力变化考虑同样的例子, 增加一第二班8小时,使用两个能力单元.排程器看到这个工作中心具有最大的3个机器.首先两个班可用16小时(8小时/第一班和8小时/第二班),然后,第三个只有8小时可用(第一班的8小时) .当排程器对这个工作中心加载工序时,它首先研究1号单元的能力(第一个机器).因此,它可以在机器上排到16小时.如果第一机器和第二机器都不可用,排程器用第三台机器,只有这天第一班的8小时可用的第三台机器.重要的是,注意这个工序剩余的正好是在这个单元为整个持续时间.意思是工序不适合使用额外的下一天的第二班时间,不管它是否可用.或因为在第二班没有第三个机器.假设是在开始时你不能移动工序的机器. 或准备时间是.但是,当员工引起的能力变化也许是一个问题.既是如此,一个操作者可以在机器之间移动.你可以提高工作订单的优先级来纠正这个问题.当排程工序时,如果单元0和单元1有负荷,而单元2没有,排程器从单元2开始.然而,如果,单元0和1都可用,排程器找到更好的排程在单元0和1选择较好的计划.在向前排程时,如果遇到较早完成,VISUAL将自动延迟排程的开始.在向后排程时:如果有较迟的开始,也许由于有更多的能力,VISUAL选择较早的完成日期排程的结果:是决定开始日期和完成日期对每一个工序,排程决定一个开始和完成日期.第一个工序的开始日期就是工作订单的开始日期;最后一个工序的完成日期就是工作订单的完成日期.VISUAL 可以同时对多个能力单元的资源工序排程.一般来说,在一特别的资源单元,每一个排程规定开始和结束时间决定关键路径是在工作订单里的一组工序,工作订单控制的持续时间的. 这是排程器考虑约束资源的规则.你可以称这个路径“关键路径” .关键路径工序出现在排程是绿色,如果延迟了关键路径工序是橄榄色.同步排程器是强有力的工具,排程和重排程所有下达的,确定的工作订单,基于完成日期和你定义优先级.你可以为你的客户提供精确的可用和交货期.w生产计划使用排程器决定几个重要的事情:w你的确认和下达的工作订单的每一个工序的开始和结束.w是否,每一个工作中心已经分配给定的能力,来满足这些订单的想要日期.w什么时候可以增加能力来提高你的交货.w当你有超出资源能力,你可以用同步排程器建立“what-if”决定能力,负荷,日历设定变化的结果w你可以从报价窗口,订单录入,制造窗口检查计划可用性和工作订单,从报价和客户订单的影响.在你已经设置和验证车间资源和零件提前期之后,你可以开始排程处理:排程任务w 1. 开始排程器.w 2. 设置同步排程器参数.w 3. 建立新的排程或激活存在的排程.w 4. 选择合适的排程选项w 5. 运行排程.w查看结果w 1. 打开排程窗口.w 2. 加载你建立的排程.w 3. 查看排程.APS的算法:APS的排序方法很多,最常用的有顺排和倒排两种方法,或是将两者混合使用。
某PCBA企业应用易普优APS实现生产计划智能排产案例
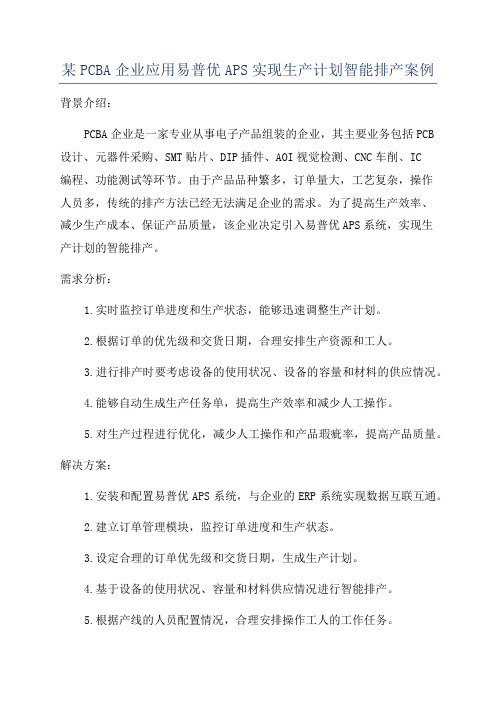
某PCBA企业应用易普优APS实现生产计划智能排产案例背景介绍:PCBA企业是一家专业从事电子产品组装的企业,其主要业务包括PCB设计、元器件采购、SMT贴片、DIP插件、AOI视觉检测、CNC车削、IC编程、功能测试等环节。
由于产品品种繁多,订单量大,工艺复杂,操作人员多,传统的排产方法已经无法满足企业的需求。
为了提高生产效率、减少生产成本、保证产品质量,该企业决定引入易普优APS系统,实现生产计划的智能排产。
需求分析:1.实时监控订单进度和生产状态,能够迅速调整生产计划。
2.根据订单的优先级和交货日期,合理安排生产资源和工人。
3.进行排产时要考虑设备的使用状况、设备的容量和材料的供应情况。
4.能够自动生成生产任务单,提高生产效率和减少人工操作。
5.对生产过程进行优化,减少人工操作和产品瑕疵率,提高产品质量。
解决方案:1.安装和配置易普优APS系统,与企业的ERP系统实现数据互联互通。
2.建立订单管理模块,监控订单进度和生产状态。
3.设定合理的订单优先级和交货日期,生成生产计划。
4.基于设备的使用状况、容量和材料供应情况进行智能排产。
5.根据产线的人员配置情况,合理安排操作工人的工作任务。
6.根据产品的工艺流程,自动生成生产任务单,减少人工操作。
7.建立生产过程监控模块,对生产过程进行实时监测和优化。
实施效果:1.易普优APS系统的引入使得企业的生产计划更加智能化和高效化,大大减少了人工操作和排产调整的时间。
2.通过对订单优先级和交货日期的合理安排,提高了订单交付的准时率,增强了客户的满意度。
3.通过智能排产,合理利用设备资源和人员配置,提高了设备的利用率和工人的工作效率,降低了生产成本。
4.自动生成生产任务单的功能简化了操作流程,减少了人为因素引起的生产错误,提高了生产效率和产品质量。
5.生产过程的监控与优化,减少了产品瑕疵率,提高了产品的质量可靠性。
总结:通过应用易普优APS系统进行生产计划智能排产,PCBA企业实现了生产计划的高效、准确、智能化管理。
机械加工行业APS生产计划排程应用案例
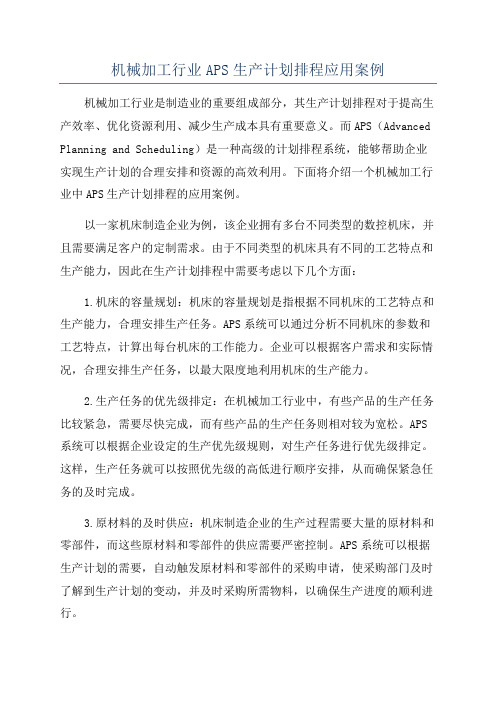
机械加工行业APS生产计划排程应用案例机械加工行业是制造业的重要组成部分,其生产计划排程对于提高生产效率、优化资源利用、减少生产成本具有重要意义。
而APS(Advanced Planning and Scheduling)是一种高级的计划排程系统,能够帮助企业实现生产计划的合理安排和资源的高效利用。
下面将介绍一个机械加工行业中APS生产计划排程的应用案例。
以一家机床制造企业为例,该企业拥有多台不同类型的数控机床,并且需要满足客户的定制需求。
由于不同类型的机床具有不同的工艺特点和生产能力,因此在生产计划排程中需要考虑以下几个方面:1.机床的容量规划:机床的容量规划是指根据不同机床的工艺特点和生产能力,合理安排生产任务。
APS系统可以通过分析不同机床的参数和工艺特点,计算出每台机床的工作能力。
企业可以根据客户需求和实际情况,合理安排生产任务,以最大限度地利用机床的生产能力。
2.生产任务的优先级排定:在机械加工行业中,有些产品的生产任务比较紧急,需要尽快完成,而有些产品的生产任务则相对较为宽松。
APS 系统可以根据企业设定的生产优先级规则,对生产任务进行优先级排定。
这样,生产任务就可以按照优先级的高低进行顺序安排,从而确保紧急任务的及时完成。
3.原材料的及时供应:机床制造企业的生产过程需要大量的原材料和零部件,而这些原材料和零部件的供应需要严密控制。
APS系统可以根据生产计划的需要,自动触发原材料和零部件的采购申请,使采购部门及时了解到生产计划的变动,并及时采购所需物料,以确保生产进度的顺利进行。
4.工人的安排和调度:机械加工行业的生产过程需要大量的工人参与,而工人的安排和调度对生产计划的顺利进行至关重要。
APS系统可以根据机床的工作状态和工人的能力,合理安排工人的上岗时间和任务分配,以最大限度地发挥工人的工作效率,提高生产效率。
以上是一个机械加工行业中APS生产计划排程的应用案例。
通过引入APS系统,可以实现生产计划的合理排定和资源的高效利用,从而提高生产效率、优化资源配置,减少生产成本,为企业带来更好的经济效益。
生产管理计划与排程aps系统设计、选型、实施和应用
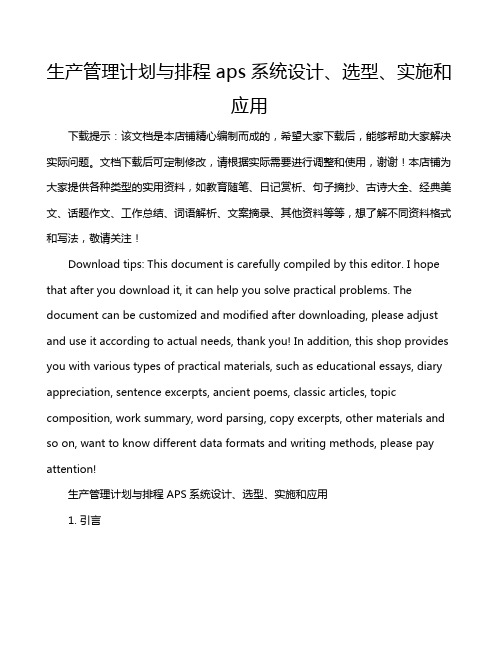
生产管理计划与排程aps系统设计、选型、实施和应用下载提示:该文档是本店铺精心编制而成的,希望大家下载后,能够帮助大家解决实际问题。
文档下载后可定制修改,请根据实际需要进行调整和使用,谢谢!本店铺为大家提供各种类型的实用资料,如教育随笔、日记赏析、句子摘抄、古诗大全、经典美文、话题作文、工作总结、词语解析、文案摘录、其他资料等等,想了解不同资料格式和写法,敬请关注!Download tips: This document is carefully compiled by this editor. I hope that after you download it, it can help you solve practical problems. The document can be customized and modified after downloading, please adjust and use it according to actual needs, thank you! In addition, this shop provides you with various types of practical materials, such as educational essays, diary appreciation, sentence excerpts, ancient poems, classic articles, topic composition, work summary, word parsing, copy excerpts, other materials and so on, want to know different data formats and writing methods, please pay attention!生产管理计划与排程APS系统设计、选型、实施和应用1. 引言在现代复杂的制造环境中,有效的生产管理计划与排程系统(APS)是提高生产效率和资源利用率的关键。
APS高级生产计划与生产排程
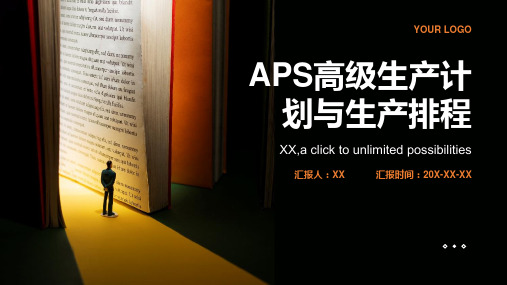
大数据分析:利用 大数据技术对生产 数据进行深入分析, 优化生产流程,提 高生产效率。
物联网技术:实现设 备与APS的实时连接, 提高生产数据的实时 性和准确性。
云计算技术:提供弹 性的计算和存储资源, 支持大规模生产数据 的处理和分析。
APS在智能制造领域的应用前景
APS与智能制造的融合,实现生产过程的智能化和自动化
生产排程:根据 生产计划和实际 生产情况,对生 产流程进行优化 排程,提高生产 效率和资源利用 率。
实时监控与调整: 对生产过程进行 实时监控,及时 发现和解决生产 中的问题,确保 生产计划的顺利 实施。
数据分析与预测: 通过对历史数据 和实时数据的分 析,预测未来的 市场需求和生产 趋势,为生产计 划的制定提供有 力支持。
汇报人:XX 汇报时间:20X-XX-XX
APS高级生产计划与生产排程的原 理
生产计划与排程的基本原理
生产计划与排程的概念定义 生产计划与排程的目标和原则 生产计划与排程的流程和步骤 生产计划与排程的优化方法
APS的计划与排程算法
计划算法:基于约束理论,考虑多种生产约束条件,制定最优的生产计划。 排程算法:采用启发式搜索和优化算法,快速生成可行的生产排程方案。 算法特点:支持多工厂、多车间、多设备的协同生产计划与排程,提高生产效率。 算法应用:广泛应用于离散制造业,实现生产计划的精细化管理。
APS系统的培训和推广
培训内容:介绍APS系统的基本概念、原理和功能 培训方式:线上培训、线下培训、企业内部培训等 推广方式:通过行业会议、企业交流、宣传资料等方式推广APS系统 实施效果:提高生产效率、降低成本、优化资源配置等
APS高级生产计划与生产排程的案例 分析
案例一:某制造企业的APS应用
aps应用案例
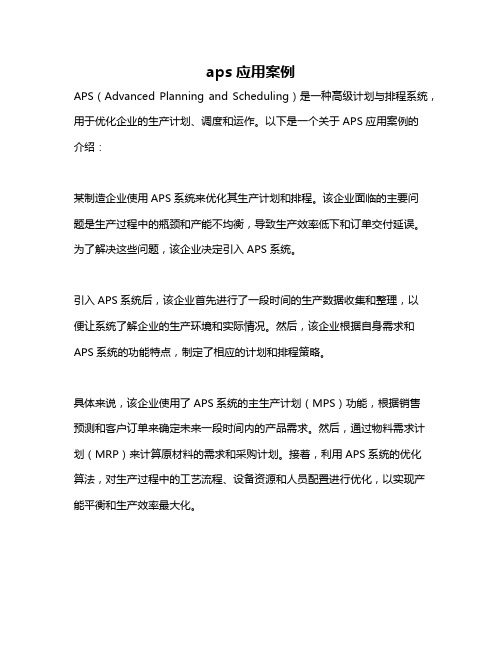
aps应用案例APS(Advanced Planning and Scheduling)是一种高级计划与排程系统,用于优化企业的生产计划、调度和运作。
以下是一个关于APS应用案例的介绍:某制造企业使用APS系统来优化其生产计划和排程。
该企业面临的主要问题是生产过程中的瓶颈和产能不均衡,导致生产效率低下和订单交付延误。
为了解决这些问题,该企业决定引入APS系统。
引入APS系统后,该企业首先进行了一段时间的生产数据收集和整理,以便让系统了解企业的生产环境和实际情况。
然后,该企业根据自身需求和APS系统的功能特点,制定了相应的计划和排程策略。
具体来说,该企业使用了APS系统的主生产计划(MPS)功能,根据销售预测和客户订单来确定未来一段时间内的产品需求。
然后,通过物料需求计划(MRP)来计算原材料的需求和采购计划。
接着,利用APS系统的优化算法,对生产过程中的工艺流程、设备资源和人员配置进行优化,以实现产能平衡和生产效率最大化。
在实施APS系统的过程中,该企业还根据实际情况进行了一些调整和改进。
例如,在遇到生产过程中的异常情况时,该企业及时调整了计划和排程,以适应实际生产的变化。
同时,该企业还通过不断的数据分析和反馈,不断优化APS系统的参数和算法,以提高计划的准确性和可执行性。
通过引入和应用APS系统,该制造企业实现了生产计划的优化和生产效率的提高。
具体来说,该企业的生产效率提高了约30%,订单交付准时率也大幅上升。
此外,该企业还减少了库存积压和浪费现象,降低了库存成本和资金占用成本。
同时,该企业还提高了生产管理的透明度和可预测性,为企业的决策提供了更加科学和可靠的数据支持。
总之,通过引入和应用APS系统,该制造企业实现了生产计划的优化和生产效率的提高,为企业的可持续发展奠定了坚实的基础。
APS产品解决方案及案例介绍

计划
模具排程优化 滚动计划
可视化追溯 模拟系统
基础
物料
BOM/工艺
资源定义
可选资源
数据
模具定义 产能日历设置 排程模型定义
数据同步
ERP 生产计划 采购申请
……
MES 生产订单
……
平台架构 集群管理
服务注册/分配 异步队列管理
接口监控
二次开发
元数据/权限管理
基础架构 Java
SpringBoot 内存数据库 MongoDB 开源数据库 ActiveMQ Vuejs
委外下达
采购下达
7
采购/委外
委外订单 (金蝶云星空)
采购申请 (金蝶云星空)
采购订单 (金蝶云星空) 采购收货检验入库 (金蝶云星空,反写APS计划)
APS服务器部署架构
主要特性: • 根据业务规模可以将APS部
署在1台或N台服务器上 • 支持Linux、windows • 通过Ngnix做负载均衡,可
实用 开放
易用 灵活
✓ 管理驾驶舱等目视化管理 ✓ 算法过程透明,摒弃业界“算法
黑箱” ✓ B/S架构,无须安装客户端
✓ 支持用户界面配置 ✓ 支持复杂模型自定义 ✓ 支持算法模型二次开发 ✓ 支持SAAS低成本租用
9
APS系统算法逻辑主流程
数据准备阶段 ★ 倒推计划阶段
(MRP) ★ 计划调整阶段
根据关键采购原料的计划到货日期以及设备产能等信息,按照BOM自下 到上根据物料约束和产能约束、订单优先级编制计划,最终获得产品的 预计完成时间,与订单交期进行对比
调整产能、调整顺序等
当排产结果与订单需求有偏差时,通过增加班次、 加班、调整生产顺序重新排产来解决,如果调整 后计划仍无法解决,需要与市场沟通更改交期
aps管理系统应用案例
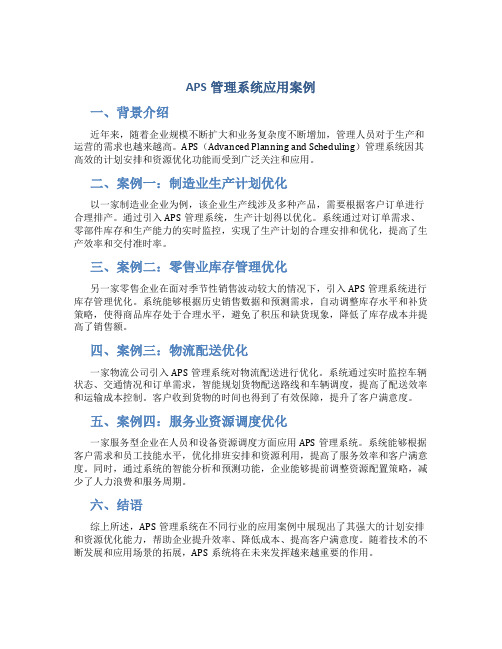
APS管理系统应用案例一、背景介绍近年来,随着企业规模不断扩大和业务复杂度不断增加,管理人员对于生产和运营的需求也越来越高。
APS(Advanced Planning and Scheduling)管理系统因其高效的计划安排和资源优化功能而受到广泛关注和应用。
二、案例一:制造业生产计划优化以一家制造业企业为例,该企业生产线涉及多种产品,需要根据客户订单进行合理排产。
通过引入APS管理系统,生产计划得以优化。
系统通过对订单需求、零部件库存和生产能力的实时监控,实现了生产计划的合理安排和优化,提高了生产效率和交付准时率。
三、案例二:零售业库存管理优化另一家零售企业在面对季节性销售波动较大的情况下,引入APS管理系统进行库存管理优化。
系统能够根据历史销售数据和预测需求,自动调整库存水平和补货策略,使得商品库存处于合理水平,避免了积压和缺货现象,降低了库存成本并提高了销售额。
四、案例三:物流配送优化一家物流公司引入APS管理系统对物流配送进行优化。
系统通过实时监控车辆状态、交通情况和订单需求,智能规划货物配送路线和车辆调度,提高了配送效率和运输成本控制。
客户收到货物的时间也得到了有效保障,提升了客户满意度。
五、案例四:服务业资源调度优化一家服务型企业在人员和设备资源调度方面应用APS管理系统。
系统能够根据客户需求和员工技能水平,优化排班安排和资源利用,提高了服务效率和客户满意度。
同时,通过系统的智能分析和预测功能,企业能够提前调整资源配置策略,减少了人力浪费和服务周期。
六、结语综上所述,APS管理系统在不同行业的应用案例中展现出了其强大的计划安排和资源优化能力,帮助企业提升效率、降低成本、提高客户满意度。
随着技术的不断发展和应用场景的拓展,APS系统将在未来发挥越来越重要的作用。
使用了aps的企业案例

使用了aps的企业案例
一个使用了APS(Advanced Planning and Scheduling)系统的企业案例是仙乐健康。
仙乐健康在生产计划和物料计划安排方面,由于产品品种多、小批量特点突出、客户交货期短、生产计划数据量大,传统ERP系统已无
法满足其需求。
在这种情况下,仙乐健康引入了APS系统,实现了“一键
排产”和“智能排产”。
APS系统将所有生产任务在引擎的指挥和驱动下,有序、快速地安排到各自最合适的工位,相比人工排产,APS带来的直接变化包括工序级排产、速度快、可视化、集成化等优点。
通过实施APS系统,仙乐健康在生产计划和物料计划安排方面取得了显著改善,满足了严格的供应链要求,提高了生产效率和客户满意度。
APS生产排程解决方案ppt课件
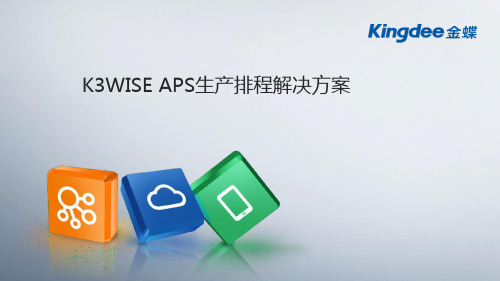
实时呈现各个资源的产能能力与负荷任 务; 可手工拖动甘特图进行调整; 可对甘特图进行任务分割、工作时间调 整、效能变更,以应对资源设备突发故 障、临时调整加工任务等异常情况
P24
APS应用价值
1、来单一键排程,极大节省排产时间、提高排产的准确性
2、可以进行插单排程
3、可以清晰掌握各个订单按现有产能排产能否满足交期 4、可以清晰掌握各个资源设备的产能利用情况、负荷承载情况,供找出瓶 颈工序 5、可以清晰的掌握各个订单的生产进度
执行汇 报
• 分资源每天汇报生产进度,及时了解生产过程 • 支持按生产状态调正现有生产计划
交期承 诺
• 依据客户重要性、订单紧急程度,支持紧急、普通两种承诺方式 • 自动分析承诺对其它订单的影响
资源模型
主要业务功能
建立生产排程所需的资源模型 1. 创建两级资源模型:主计划资源和作 业资源 2. 设置各资源模型的数量 3. 设置资源的日历方案 4. 设置资源能力
P18
一键排程
P19
功能模块概要
基础数 据
• 灵活多变日历方案,可个性化资源的工作日历 • 可视化资源模型,让生产过程一目了然 • 可视化工艺模型,将产品信息、工序信息、工序流程有机结合
排产
• 提供公司级和车间级两层排程,有效简化系统结构,使系统具有极大扩展性 • 支持来单即排,定期排程,插单排程,反复排程,手动拖拉、周期重排 • 图形化排程结果展示,并可在图形上手动修改排程结果;自动下达并产生单据,自动物料齐套检查
举例2:如果有“下料”,有些企业的 “下料”是需要调用锯床等设备进行切割等加工(如管材切割), 这类工序要维护到工艺路线中;而有些下料则不需要调用生产资源、仅仅是领料发料、移动物料的位 置,则这类要剔除掉、不要作为工序。
APS高级生产计划与生产排程

PS高级生产计划与生产排程的核 心功能
03
资源管理
资源分配:根据生产需求合理分配资源提高资源利用率 资源优化:通过优化算法实现资源最优配置降低生产成本 资源监控:实时监控资源使用情况及时发现和解决问题 资源预测:预测未来资源需求提前做好资源储备和调配准备
生产计划与排程
生产计划:根据市场需求和生产能力制定生产计划包括生产数量、生产时间、生产地点等 生产排程:根据生产计划安排生产任务包括生产顺序、生产时间、生产地点等 生产优化:根据生产计划和生产排程进行生产优化包括生产效率、生产成本、生产质量等 生产监控:对生产过程进行监控包括生产进度、生产质量、生产成本等
设置
数据准备与导入
数据收集:收集生产计划、生 产排程、物料需求等相关数据
数据整理:整理收集到的数据 确保数据的准确性和完整性
数据导入:将整理好的数据导 入到PS系统中
数据验证:验证导入的数据是 否正确如有错误及时更正
系统培训与推广
培训内容:PS高级生产计划与 生产排程的基本原理、操作流 程、注意事项等
生产控制与跟踪
生产计划:制定生产计划包括生产任务、生产时间、生产资源等
生产排程:根据生产计划安排生产任务包括生产顺序、生产时间、 生产资源等
生产监控:实时监控生产进度包括生产任务、生产时间、生产资源等
生产调整:根据生产监控结果调整生产计划和生产排程确保生产顺 利进行。
数据分析与优化
实时监控生产进度及时发现问题 自动调整生产计划优化生产效率 预测生产需求提前准备物料和设备 分析生产数据为决策提供支持
PS未来的发展趋势和挑战
智能化:I、大数据等技术的应用将使PS更加智能化提高生产效率和准确性 集成化:PS将与其他管理系统如ERP、MES等更加紧密地集成实现信息共享和协同工作 定制化:随着市场需求的多样化PS将更加注重定制化生产满足不同客户的需求 挑战:数据安全、系统稳定性、人才短缺等问题将是PS未来发展的主要挑战
aps案例

规划流程
需求规划与 总需求分配
系统
ERP或 ERP或SCM -需求规划模组
各阶制程的 在制品及库存
各阶制程及各品项 阶制程及各品项 建模资料 含限制与派工条件) (含限制与派工条件)
主排程规划
各阶制程的时程化投入量
TFT-LCD产业 TFT-LCD产业 供给规划逻辑
生产排程& 生产排程& 产出平衡规划
东海大学 企业资源整合研究室
Li2002 Professor Li-Chih Wang Li2002 Professor Li-Chih Wang
LCD Industry Background (1)
TFT台湾 TFT-LCD 上下游产业链解析图 (Source: PIDA , IT IS ,宝来证劵汇整 )
东海大学 企业资源整合研究室 Li2002 Professor Li-Chih Wang Li2002 Professor Li-Chih Wang
TFT-LCD业APS规划特性 TFT-LCD业APS规划特性 (续)
2.在Site-需求规划阶段,必须根据市场需求,考虑各阶制程的良率及分 级率,以规划出各阶制程的时程化需求(time-phased demand)—此阶 段可以由SCP/MSP中的需求规划(DP)与总需求分配规划(DDP) . 3. 为达到各阶制程的生产目标(即时程化需求) ,在主排程规划(Master Planning)阶段,必须考虑各阶制程的良率/分级率及已生产未分配量 (e.g., WIP, Bank) ,以规划出各阶制程的时程化投入量(即制令) . 4. 由於主排程规划阶段并未考虑各阶生产现场的实际产能,生产限制与 派工条件,尚须经详细的生产排程规划,以规划出实际可行且可作 为生产现场派工依据的日生产计划 (daily production plan). 5. 以实际可行且可作为生产现场派工依据的日生产计划,进行物料规划 及需求分配(即ATP/CTP),以达到订单满足(order fulfillment)的目 标.
机械加工行业APS生产计划排程应用案例

一、机械加工行业现状机械制造业在生产管理上的主要特点是:离散为主、流程为辅、装配为重点。
机械制造业的基本加工过程是把原材料分割,大部分属于多种原材料平行加工,逐一经过车、铣、刨、磨或钣金成型等加工工艺,成为零件,然后组装制成为产品的装配式复杂多步骤生产。
生产管理特点如下:➢生产方式:专用设备生产以按订单生产为主,按订单设计、按订单装配和按库存生产为辅;通用设备生产以按订单生产和按库存生产相结合,按订单设计、按订单装配为辅。
➢生产批量:根据机械产品结构和生产批量的不同,可分为单件小批量生产,多品种、中小批量生产和大量流水生产3种类型。
传统上装配车间多属于中小批量生产类型,零部件生产车间则多属于多品种中小批量生产类型或大批量生产类型。
➢产品配置复杂,BOM层次多,边设计边生产,且首件生产周期长,工过程艺变更对生产计划影响较大。
制造工艺复杂,加工工艺路线具有很大的不确定性,一种零部件或产品可以有多种工艺并存,生产过程所需机器设备和工装夹具种类繁多。
➢订单多数按项目型接单制造方式,整个生产运营过程,按项目号、产品型号、零部件进行单件跟踪和成套控制。
➢生产计划:产品结构复杂,制造工艺复杂,产品中各部件制造周期长短不一和产品加工工艺路线的不确定性,造成管理对象动态多变,因此为了保证产品成套、按期交货,又要尽可能减少在制品积压,导致生产物资管理工作十分复杂,需要从每一产品的交货期倒推,周密安排各部件、零件、毛坯的投入/产出数量和时间;生产计划的制订与车间任务工作繁重,影响生产过程的不确定因素多,导致制订生产、采购计划困难。
➢产品零部件加工采用自制和委外加工结合模式,中间部分工序由于工艺特性需要委外加工,甚至需要出口委外,委外周期长。
➢机械制造业企业由于主要是离散加工,产品的质量和生产率很大程度依赖于工人的技术水平,而自动化程度主要在单元级,例如数控机床、柔性制造系统等。
➢产品中各部件制造周期长短不一和产品加工工艺路线的复杂性造成在制品管理不易。
APS简单的正排和倒排算法解析场景一
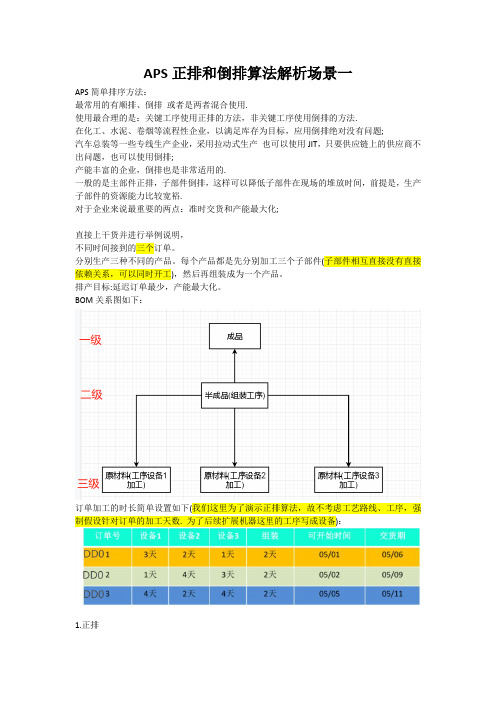
APS正排和倒排算法解析场景一APS简单排序方法:最常用的有顺排、倒排或者是两者混合使用.使用最合理的是:关键工序使用正排的方法,非关键工序使用倒排的方法.在化工、水泥、卷烟等流程性企业,以满足库存为目标,应用倒排绝对没有问题;汽车总装等一些专线生产企业,采用拉动式生产也可以使用JIT,只要供应链上的供应商不出问题,也可以使用倒排;产能丰富的企业,倒排也是非常适用的.一般的是主部件正排,子部件倒排,这样可以降低子部件在现场的堆放时间,前提是,生产子部件的资源能力比较宽裕.对于企业来说最重要的两点:准时交货和产能最大化;直接上干货并进行举例说明,不同时间接到的三个订单。
分别生产三种不同的产品。
每个产品都是先分别加工三个子部件(子部件相互直接没有直接依赖关系,可以同时开工),然后再组装成为一个产品。
排产目标:延迟订单最少,产能最大化。
BOM关系图如下:订单加工的时长简单设置如下(我们这里为了演示正排算法,故不考虑工艺路线、工序,强制假设针对订单的加工天数. 为了后续扩展机器这里的工序写成设备):1.正排分析如下:A.设备1、设备2、设备3处于同一个级别,可以同时开工进行加工;B.可以看出来DD01订单的开始日期为2023-05-01号,加工成半成品最长的时长取决于工序C.设备1需要3天,因为是正排算法当天就是所有工序的开始加工日期;D.设备1工序、设备2工序、设备3工序的开工日期都5月1日;如图:从图中我们汇总订单维度数据如下:这样的正排可以满足这三个订单都可以正常的交货,不会造成延期;2.倒排订单的情况还是跟正排一样的,如图:分析如下:A.对5月1日接到的订单DD01排产>对5月2日接到的订单DD02排产,由于设备2被占用,不得不延长交货期。
B.对5月5日的接到订单排产由于设备1、3被占用,不得不延长交货期。
C.结果:CC1.延迟订单2个,最大延迟三天CC2.订单生产周期都比较短>产能浪费很大如图:从图中我们汇总订单维度数据如下:DD02、DD03分别延期1天和3天;3.增加产能因为倒排会导致两个订单延期,最长延期3天,正常的企业可能会考虑增加设备来解决这个问题,如果我们把设备产提高一倍进行倒排测试,订单的情况还是跟正排一样的,如图:分析如下:3.1对5月1日接到的订单DD01排产,从6日倒排,前两天半空闲资源,也可以准时交货。
企业aps系统应用案例

企业aps系统应用案例
APS(高级计划与排程)系统在企业中的应用案例有很多,下面以某PCBA企业为例:该企业的产品生产是典型的多品种、小批量、多变化的模式。
产品种类有1000多种,主流的200多种,每个月数百个生产订单,分解到工序以后的工单达数千个。
该企业的计划采用了计划部、生产管理部、车间调度三级模式。
计划、排程、下达、报工、调度基本依赖于人工、会议、纸质方式,每周两次调度会;每天下达两次计划,计划、排程、调度工作异常繁重、粗放,对人的能力、经验要求极高。
通过需求调研,确定APS排程的工序模型为“SMT-波峰焊-测试-老化”。
其中,SMT工序是排程的难点,需要考虑线体负荷均衡、连续生产、副资源-钢网限制、减少换模时间、订单交货期、SMT线体区别、自动排程和生产异常等因素。
波峰焊工序的载具为专用模具,由于模具的制造成本很高,考虑订单的成本约束不能制作足够的模具;另外大部分模具也不具备通用型,同一个产品的模具基本特定。
所以在波峰焊生产上就有了混流需求:在同一生产线能够多种产品混合组合生产。
APS系统的应用,可以提高企业的生产效率和管理水平,降低生产成本,增强企业的市场竞争力。
- 1、下载文档前请自行甄别文档内容的完整性,平台不提供额外的编辑、内容补充、找答案等附加服务。
- 2、"仅部分预览"的文档,不可在线预览部分如存在完整性等问题,可反馈申请退款(可完整预览的文档不适用该条件!)。
- 3、如文档侵犯您的权益,请联系客服反馈,我们会尽快为您处理(人工客服工作时间:9:00-18:30)。
一、机械加工行业现状
机械制造业在生产管理上的主要特点是:离散为主、流程为辅、装配为重点。
机械制造业的基本加工过程是把原材料分割,大部分属于多种原材料平行加工,逐一经过车、铣、刨、磨或钣金成型等加工工艺,成为零件,然后组装制成为产品的装配式复杂多步骤生产。
生产管理特点如下:
➢生产方式:专用设备生产以按订单生产为主,按订单设计、按订单装配和按库存生产为辅;通用设备生产以按订单生产和按库存生产相结合,按订单设计、按订单装配为辅。
➢生产批量:根据机械产品结构和生产批量的不同,可分为单件小批量生产,多品种、中小批量生产和大量流水生产3种类型。
传统上装配车间多属于中小批量生产类型,零部件生产车间则多属于多品种中小批量生产类型或大批量生产类型。
➢产品配置复杂,BOM层次多,边设计边生产,且首件生产周期长,工过程艺变更对生产计划影响较大。
制造工艺复杂,加工工艺路线具有很大的不确定性,一种零部件或产品可以有多种工艺并存,生产过程所需机器设备和工装夹具种类繁多。
➢订单多数按项目型接单制造方式,整个生产运营过程,按项目号、产品型号、零部件进行单件跟踪和成套控制。
➢生产计划:产品结构复杂,制造工艺复杂,产品中各部件制造周期长短不一和产品加工工艺路线的不确定性,造成管理对象动态多变,因此为了保证产品成套、按期交货,又要尽可能减少在制品积压,导致生产物资管理工作十分复杂,需要从每一产品的交货期倒推,周密安排各部件、零件、毛坯的投入/产出数量和时间;生产计划的制订与车间任务工作繁重,影响生产过程的不确定因素多,导致制订生产、采购计划困难。
➢产品零部件加工采用自制和委外加工结合模式,中间部分工序由于工艺特性需要委外加
工,甚至需要出口委外,委外周期长。
➢机械制造业企业由于主要是离散加工,产品的质量和生产率很大程度依赖于工人的技术水平,而自动化程度主要在单元级,例如数控机床、柔性制造系统等。
➢产品中各部件制造周期长短不一和产品加工工艺路线的复杂性造成在制品管理不易。
二、业务需求难点
公司主要有三个不同车间:“A车间-C车间-F车间”。
A车间负责中间品A和中间品B 的加工和中间件的组装,有全自动的智能化加工线和手工线,生长周期在1周左右。
C车间主要生产中间品C的零部件生产、多次加工与组装,生长周期在1个月左右。
F车间按照客户订单完成最终成品的组装,生产周期短,制定3日计划。
因此,排程需要考虑部分特殊的工艺和车间的联动计划,具体需求如下:
➢多版本工艺路线:需要支持产品存在多条不同的工艺路线生产。
➢产线/机台负荷均衡:综合考虑各产线之间的负载平衡生产,工序有多个候选机台时,保证机台加工负载均衡;提高设备利用率。
➢物料齐套约束:除了自制件,还需要考虑外购物料是否齐套对生产计划的影响约束。
➢部装和总装车间协同排产:中间品加工、部件组装、成品组装属于不同的车间,排程周期不一样,排程时需考虑按照总装的计划倒推出部装的计划,同时当部装的计划调整时,需考虑调整对总装的计划影响。
➢工序拆分和批量委外加工生产:订单成品和中间件,需要拆分成单件进行生产跟踪;
部分工序需要委外生产,需要集齐N件之后批量委外生产。
➢产品组合(混流)生产:不同种类的中间品C在退火工序一次可加工数量不一样,需要根据订单产品组合生产。
➢炉资源选择条件:如中间品C在退火工序使用退火炉,需根据产品种类选择退火炉设备,且加工数量不一样,要求同时开始同时结束。
➢工序缓冲时间:很多工序是离散工位,需要考虑工序之间的衔接等待缓冲时间。
➢自动一键排程:将计划员的经验和排程逻辑固化到系统排程约束规则后,计划的制定能一键智能排产,自动排程响应计划调整。
➢响应各类生产异常:设备停机、维修、保养;生产延期、缺料、紧急插单都会影响订单的生产,在出现异常的情况应该保持之前已下发锁定的订单生产顺序的不变,快速响应异常调整计划。
➢滚动排程:计划需要考虑生产执行情况,滚动排程,形成闭环计划。
三、易普优APS解决方案
针对该企业的生产计划排程需求,易普优APS(高级计划排程系统)设计并提供了对应的解决方案:
1.排程整体流程设计
业务流程描述:
➢工艺管理系统将APS系统所需的工艺BOM数据传入APS。
➢ERP系统根据订单管理分解出相关的需求订单,检查物料齐套后,将订单数据和物料预计齐套时间传入APS。
➢APS系统根据系统提供的订单、工艺数据,考虑工艺、产能、订单、产品等多方面的约束条件,生成相应的可执行的工序级计划。
➢计划员对排程结果进行评估,若计划NG则往上沟通反馈,乃至计划确认。
根据计划反馈确认委外情况、是否延期或通过其他方式完成。
➢根据计划下达周期锁定N天计划并下达工位作业生产计划到MES系统。
➢MES根据现场的执行情况,对计划的执行以及影响计划的异常进行反馈进入APS,APS对相应的需求订单、设备计划进行滚动排程,生产新的生产计划重
新发布。
2.系统建模与排程结果
易普优APS针对各个工序的资源设备产能约束和排程期望进行系统建模,分工序通过了业务的逻辑建模与功能验证,用真实的数据各车间单工序滚动验证,然后进行三个车间的串联,确保计划实际指导生产。
1)多版本工艺路线:易普优APS支持多条工艺路径的建模方式,如下某中间部件存在自
动化生产线和手动加工线两种不同的工艺路线。
2)产线设备加工负载均衡:易普优APS系统设置资源评估参数,确保设备线体加工负载
均衡。
3)物料齐套约束:易普优APS在排程前,和ERP系统集成,动态获取物料齐套检查后的
物料预计齐套时间,作为订单可以开始排程的最早开始时间约束,确保订单生产不会出现缺料的情况。
4)总装部装计划协同:易普优APS支持总装和部装的多级计划协同,通过总装计划拉动
部装的计划进行逆向排程。
考虑到部装和总装的父子约束关系,易普优APS支持父子订单约束关系,确保子订单完成后,父订单才可以开工。
5)产品组合生产和炉资源选择:需要考虑产品类型,易普优APS可以设置资源有效条件
进行约束控制建模,确保对应种类的产品在相应的资源上生产且符合对应产能节拍和可生产数量,且同进同出。
排程结果如下:针对机车和地铁类型的产品,在不同的退火炉上可生产的数量和种类是不一样的。
6)订单的拆分批量和委外:易普优APS满足在工序模板设置拆分批量,进行订单的拆分
和批量生产。
可支持建立委外资源管理,进行中间工序委外加工管控。
如下,其他工序订单单件拆分,调质工序按照4个为批量进行委外生产。
7)前后工序的衔接等待:易普优APS可支持工序的前后缓冲时间的设置。
8)生产异常反馈:在计划完成后,如出现生产异常或者订单变更;考虑生产执行情况;在
APS系统录入生产实绩和异常反馈,易普优APS支持一键排程,响应计划的调整。
四、应用效果
1.易普优APS系统通过与其他系统的集成,获取生产订单和工艺约束,进行基于有限产
能和设备的一键排产,改变现有通过EXCEL手工排程模式,提高计划员制定计划的效率,解决生产计划和实际生产环节脱节的问题,提高价值链增值效率
2.通过梳理计划员的经验,建立和优化排程规则固化到系统,并考虑更精细化的约束,
排程到具体工位,实现精益生产和均衡生产,提高了设备利用率,使的生产过程的管控和物料的管控更加透明化。
3.通过部装和总装的多车间协同计划,以客户需求为中心,建立企业统一的计划体系。
以计划体系为纽带,全面协调销售、采购、生产、委外加工、库存和发运的关键管理
流程,实现整机装配计划于零部件加工计划的有效衔接,实现企业内部各环节的业务协同,以最快的速度响应客户需求,缩短交货期,提高交货准时率。
4.对于机械行业工艺替代频繁的特点,提供了多工艺路线解决方案,方便企业管理人员
在车间排产时进行灵活决策。
5.通过精细工序级的物料计划,指导物料的配送,通过物料配套检查的齐套时间约束排
程,确保生产计划考虑物料齐套问题,解决机械产品物料复杂,物料缺料待产频繁的难题。
减少因为缺料等问题造成订单的延期,同时也降低了中间工序待料时间,缩短整体制造周期。