龙门吊涂装工艺
浅谈起重机舾装件的高质量涂装
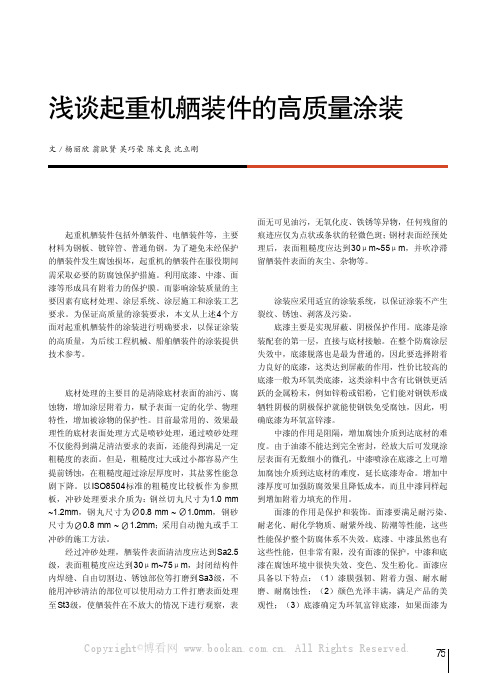
浅谈起重机舾装件的高质量涂装文/杨丽欣 翁耿贤 吴巧荣 陈文良 沈立刚0 引言起重机舾装件包括外舾装件、电舾装件等,主要材料为钢板、镀锌管、普通角钢。
为了避免未经保护的舾装件发生腐蚀损坏,起重机的舾装件在服役期间需采取必要的防腐蚀保护措施。
利用底漆、中漆、面漆等形成具有附着力的保护膜。
而影响涂装质量的主要因素有底材处理、涂层系统、涂层施工和涂装工艺要求。
为保证高质量的涂装要求,本文从上述4个方面对起重机舾装件的涂装进行明确要求,以保证涂装的高质量,为后续工程机械、船舶舾装件的涂装提供技术参考。
1 底材处理底材处理的主要目的是清除底材表面的油污、腐蚀物,增加涂层附着力,赋予表面一定的化学、物理特性,增加被涂物的保护性。
目前最常用的、效果最理性的底材表面处理方式是喷砂处理,通过喷砂处理不仅能得到满足清洁要求的表面,还能得到满足一定粗糙度的表面。
但是,粗糙度过大或过小都容易产生提前锈蚀,在粗糙度超过涂层厚度时,其盐雾性能急剧下降。
以ISO8504标准的粗糙度比较板作为参照板,冲砂处理要求介质为:钢丝切丸尺寸为1.0 mm ~1.2mm,钢丸尺寸为̮0.8 mm ~̮1.0mm,钢砂尺寸为̮0.8 mm ~̮1.2mm;采用自动抛丸或手工冲砂的施工方法。
经过冲砂处理,舾装件表面清洁度应达到Sa2.5级,表面粗糙度应达到30μm~75μm,封闭结构件内焊缝、自由切割边、锈蚀部位等打磨到Sa3级,不能用冲砂清洁的部位可以使用动力工件打磨表面处理至St3级,使舾装件在不放大的情况下进行观察,表面无可见油污,无氧化皮、铁锈等异物,任何残留的痕迹应仅为点状或条状的轻微色斑;钢材表面经预处理后,表面粗糙度应达到30μm~55μm,并吹净滞留舾装件表面的灰尘、杂物等。
2 涂层系统涂装应采用适宜的涂装系统,以保证涂装不产生裂纹、锈蚀、剥落及污染。
底漆主要是实现屏蔽、阴极保护作用。
底漆是涂装配套的第一层,直接与底材接触。
桥门式起重机通用涂漆工艺规程(18)
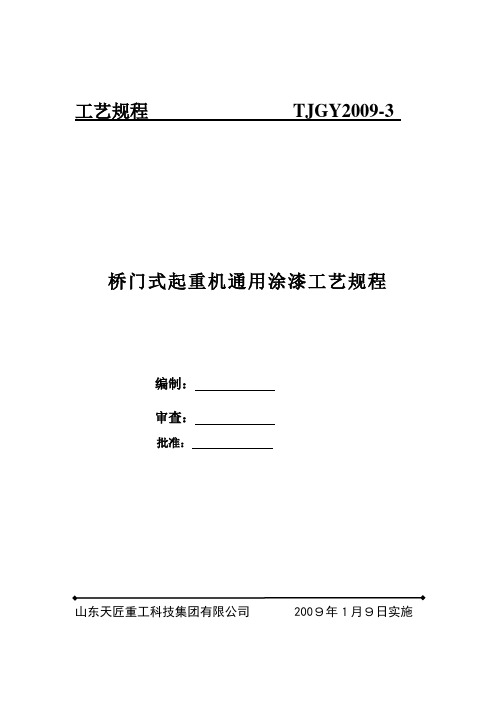
工艺规程TJGY2009-3桥门式起重机通用涂漆工艺规程编制:审查:批准:山东天匠重工科技集团有限公司2009年1月9日实施目录1、除锈 (1)2、涂漆 (1)3、涂漆质量检查 (2)4、表面质量 (4)1、除锈1.1除锈前钢板有水份、油污、灰尘时,应用压缩空气、洗涤剂吹干或脱脂。
1.2表面除锈:见表1 表12、涂漆2.1涂漆施工温度:见表2 表22.2涂漆种类选择见表3 表32.3不涂装部位:铭牌、机械加工配合面、制动轮圆柱表面、齿轮接手,涂漆前应涂上润滑脂或用塑料包扎。
2.4底漆应在金属结构件除锈检验合格后24小时之内涂上。
2.5涂漆应按如下顺序进行:先涂底漆,再涂中间漆。
每次涂漆应在前一涂层干燥后进行。
一般涂漆间隔时间见如下表:(即表4)表4 间隔时间单位:小时2.6涂漆道数、厚度、工作粘度(涂4#杯测,25℃)见表5表53、涂漆质量检查3.1涂漆外观质量检查见表6。
3.2漆厚度部位检查:3.2.1一般每涂完一道油漆后检查漆膜厚度,测量时,主梁、端梁各10处。
见表73.2.2测量仪器:用两点式微磁厚度仪及其基准试片。
表6表73.3漆膜附着力检查:用专用刀在漆膜上划六条互相垂直间距为2mm的直线,如图1所示,刀痕要划到钢板上。
操作时,切割刀应垂直于切割平面。
用力均匀,以25~50mm/秒速度切割,然后用软毛刷沿着方格图形的对角线轻轻地向后刷5次,向前刷5次。
如在切口交叉处涂层有少许薄片分离。
划格区受影响明显地不大于5%,即为合格,超过为不合格。
图14、表面质量4.1油漆漆膜厚度要求:底漆一道,厚度≥25μm;面漆涂2道,漆膜厚度≥50μm;漆膜总后度应≥75μm。
4.2漆膜附着力技术要求:按ISO 2409《色漆和清漆一划格试验》中一级质量要求并按ISO 2409划格试验方法,在主梁、端梁上各取10处进行测试其等级评定方法。
见图1操作方法:(1)用专用切刀和钢尺在漆膜上切割格子图形。
(2)切割条数在格子图形的一边上为6条。
龙门吊上刷标识施工方案
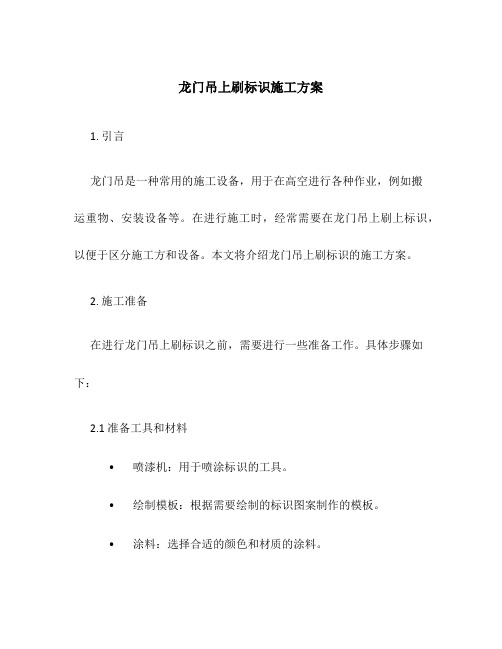
龙门吊上刷标识施工方案1. 引言龙门吊是一种常用的施工设备,用于在高空进行各种作业,例如搬运重物、安装设备等。
在进行施工时,经常需要在龙门吊上刷上标识,以便于区分施工方和设备。
本文将介绍龙门吊上刷标识的施工方案。
2. 施工准备在进行龙门吊上刷标识之前,需要进行一些准备工作。
具体步骤如下:2.1 准备工具和材料•喷漆机:用于喷涂标识的工具。
•绘制模板:根据需要绘制的标识图案制作的模板。
•涂料:选择合适的颜色和材质的涂料。
•手套和口罩:用于保护施工人员的安全。
2.2 确定标识位置根据需要刷标识的位置和要求,确定标识的具体位置和大小。
可以进行精确测量,以确保标识的位置准确无误。
2.3 准备工作区在进行刷标识之前,需要清理龙门吊的表面,确保表面干净光滑。
可以使用清洁剂清洗表面,然后用干净的布擦干。
3. 施工步骤进行施工前,需要进行具体的施工步骤。
下面是一般的施工步骤:3.1 安装绘制模板首先,将绘制模板放置在需要刷标识的位置,使用胶带或其他固定方法固定模板。
确保模板贴合表面,并且不会移动。
3.2 准备喷漆机将合适的涂料倒入喷漆机的喷涂室内,根据需要调节喷漆机的喷涂压力和喷漆方式。
确保喷漆机正常工作。
3.3 进行标识刷涂将喷漆机对准绘制模板上的标识区域,轻轻按下喷漆机的扳机,开始刷涂标识。
根据需要,可以进行多次喷涂,以达到理想的效果。
3.4 等待涂料干燥完成标识刷涂后,等待涂料干燥。
根据所用涂料的类型和环境条件,大约需要几小时或几天的时间。
在此期间,要注意保护标识,避免外界物体碰撞或污染。
3.5 清理施工区在涂料完全干燥后,可以清理施工区。
清理过程中,要注意将喷漆机和工具的残留涂料妥善处理,并保持施工区整洁。
4. 施工注意事项在进行龙门吊上刷标识的施工过程中,需要注意以下事项:•安全第一:施工过程中要注意自己的安全,佩戴好手套和口罩,避免涂料接触皮肤和吸入有害气体。
•涂料选择:根据龙门吊的材质和使用环境,选择适合的涂料。
龙门吊刷漆安全技术措施

河南神火煤业公司薛湖煤矿综采车间龙门吊刷漆安全技术措施编制单位:编制人:责任人:总工程师:编制日期:综采车间龙门吊刷漆安全技术措施为确保综采车间龙门吊除锈、刷漆作业过程中人员的安全,保证龙门吊除锈、刷漆的质量,特制定以下施工安全技术措施。
根据领导安排,综采车间承接薛湖矿水暖管道主管路的安装任务,具体负责综掘车间西侧至职工宿舍楼2号楼两路水暖管道的安装,长度总计约为300米,管路全部为直径200mm的厚壁钢管,其中除综掘车间敷设地点外,其余工作全部为架空支架高空安装,架空管路采用6米设置一个支架进行支撑,为保证安全施工,特制订安全技术措施。
一、焊接施工要求与注意事项1、管路焊接用坡口焊接方式,分三步进行焊接,第一,先底焊固定管路;第二,进行填充焊接;第三,覆盖焊接。
焊接接口要求无砂眼、无气孔、无夹渣、外观无缺陷,不漏气不漏水。
2、电焊设备使用前必须进行仔细检查,电焊机必须完好,电流调节装置灵活可靠,电焊机焊把线及焊钳应保证连接可靠,电焊机电源线及焊把线其外皮必须完好无受伤、无损坏,且绝缘可靠。
3、下雨,浓雾天气严禁施工。
4、工作人员必须劳动防护佩戴齐全。
5、氧气、乙炔要有防倒措施,必须牢固可靠,氧气、乙炔带无漏气现象,表盘显示正常,割枪必须完好。
6、保证氧气、乙炔放置地点10m范围内无明火点,两瓶间距必须大于5m。
7、施工现场放置两台8kg干粉灭火器。
二、高空作业注意事项1、严禁恐高症者、禁忌病症者进行高空作业。
2、各特殊工种作业人员必须持证上岗。
3、高空作业者必须佩戴安全帽,挂好安全带,穿防滑鞋,扎紧带好劳动工具。
4、严禁酒后和带病作业。
5、施工前对所用设备和工具进行排查,保证其性能完好。
6、严禁工作期间取笑、打闹、影响工作注意力。
7、上下安全梯、架必须保证牢固、稳定、安全性。
8、梯架、支撑架体严禁堆放材料杂物,确保梯架通道顺畅。
9、严禁利用起吊设备、升降设施运送上下人员。
10、起吊构件、管道要使用合格的专用起吊用具,吊挂点要固定牢靠,设有专人指挥。
起重机通用油漆施工工艺

1 目的为了达到油漆涂装的防腐效果及外表的美观,中途油漆建议在油漆施工中应严格按照以下要求进行操作。
2 范围本标准规定了喷丸件、涂漆件的质量要求与检验方法。
本标准适用于甲板机械、船用起重机、铸件毛坯的防护、装饰用途漆膜层的质量检验。
3总则油漆施工是一个非常重要的步骤,在油漆选定的情况下,油漆的质量是要靠施工工艺来实现的。
在本施工工艺中,将从一下几个方面给出控制原则:3.1表面处理要求3.2油漆的涂装方法及预涂装3.3施工质量控制3.4施工环境控制3.5油漆的储存使用(详见相关施工指导)3.6质量记录3.7不合格处置3.8安全方面详细工艺如下3.1 表面处理要求3.1.1 喷丸前检查3.1.1 喷丸前采用温水加清洁剂(3%~5%),使用高压清洗枪喷洗工件表面因转运、探伤等原因形成的油污、脏物;干燥后才能进行喷丸。
3.1.2 目测工件表面不允许有油脂、污垢、裂缝、焊瘤、蚀坑等缺陷,允许有铁锈、机械杂质。
3.1.3 冷焊件喷丸前钢板原始锈蚀等级不超过GB/T 8923规定的锈蚀等级B级要求。
3.1.4检查工件的孔、机加面、螺孔等应保护的部位是否根据要求进行保护。
3.1.5 表面预处理a)进行抛丸处理前,须进行底材表面预处理,即将表面的污染物如油污,油脂及其它处理干净。
b)抛丸处理前需要对一下部位用电动工具进行打磨处理:I. 底材表面的钻孔边缘、气割面及其边缘II.焊缝突起的部分、焊渣以及飞溅的焊点这些部位应处理到表面平整,或有一定坡度的起伏表面,以保证油漆能以较均匀的漆膜覆盖钢铁表面。
c)钢材的边角及边缘钢材的边角及边缘,由于这些部位较尖,在喷涂时不能达到设计的漆膜厚度,因此这些部位必须用电动工具打磨成圆角(r =2cm)。
d)要进行防腐涂装的表面,必须用喷砂或抛丸的处理的方法对底材进行处理至ISO8501-1:1988 Sa 2.5级。
其文字表达即为:达到非常彻底的喷砂除锈处理。
在不放大的情况下进行观察时,表面应无可见的油脂、污物、附着不牢的氧化皮、铁锈、旧油漆及其它杂质。
桁架式龙门吊刷漆作业指导书
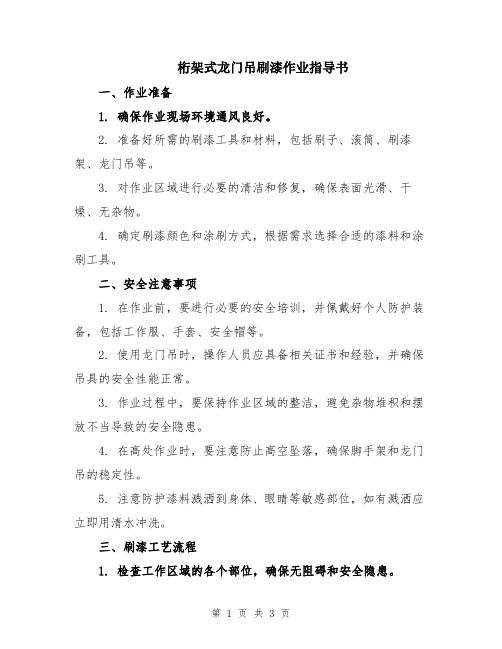
桁架式龙门吊刷漆作业指导书一、作业准备1. 确保作业现场环境通风良好。
2. 准备好所需的刷漆工具和材料,包括刷子、滚筒、刷漆架、龙门吊等。
3. 对作业区域进行必要的清洁和修复,确保表面光滑、干燥、无杂物。
4. 确定刷漆颜色和涂刷方式,根据需求选择合适的漆料和涂刷工具。
二、安全注意事项1. 在作业前,要进行必要的安全培训,并佩戴好个人防护装备,包括工作服、手套、安全帽等。
2. 使用龙门吊时,操作人员应具备相关证书和经验,并确保吊具的安全性能正常。
3. 作业过程中,要保持作业区域的整洁,避免杂物堆积和摆放不当导致的安全隐患。
4. 在高处作业时,要注意防止高空坠落,确保脚手架和龙门吊的稳定性。
5. 注意防护漆料溅洒到身体、眼睛等敏感部位,如有溅洒应立即用清水冲洗。
三、刷漆工艺流程1. 检查工作区域的各个部位,确保无阻碍和安全隐患。
2. 使用刷子或滚筒对作业区域进行底漆涂刷,涂刷前要将漆料充分搅拌均匀。
3. 底漆干燥后,使用砂纸对表面进行打磨处理,清除灰尘和粗糙物。
4. 再次搅拌漆料,使用刷子或滚筒对作业区域进行面漆涂刷。
5. 涂刷漆料时要注意涂布均匀,不得有浮粉、滴落等现象,确保漆面光滑。
6. 在涂刷完一遍后,要等待表面干燥后进行第二遍的涂刷。
7. 完成涂刷后,对作业区域进行清理,包括清除漆料溅洒的地方和整理工具。
四、质量控制要点1. 刷漆前要对作业区域进行充分的清洁和修复,确保无油污和杂物的存在。
2. 漆料要选择质量优良的产品,根据需要选择合适的漆面和颜色。
3. 涂刷时要均匀涂布,避免过厚或过薄,确保漆面光滑。
4. 涂刷过程中要注意及时清理刷子或滚筒,避免堵塞和污染。
5. 涂刷面漆时要避免漆料飞溅和滴落,保持工作区域整洁。
6. 涂刷完毕后要检查漆面,如有需要可进行修补或重新涂刷。
五、作业完工及验收1. 作业完工后要及时清理作业现场,包括清理工具和废弃物。
2. 漆面干燥后,进行最终验收,检查漆面质量和颜色是否符合要求。
起重机现场涂装方案

起重机现场防腐油漆施工方案吊车外表生锈、腐蚀严重,油漆脱落,现根据现场情况及业主建议,提出施工方案:一、起重机大车走台平面及小车平面机械除锈(除锈等级中级),对局部地方进行补漆,刷红丹环氧防锈底漆两遍,高级氟碳面漆两遍。
二、起重机大车走台小车平台的侧面及底部机械除锈(除锈等级中级),对局部地方进行补漆,对刷红丹环氧防锈底漆两遍,高级氟碳面漆两遍。
三、轨道底部铁板,刷沥青漆一底一面,轨道机械除锈等级中级,刷沥青漆一底一面。
四、除锈方法:电动工具除锈,除锈等级为S t2级。
金属面标准:氧化皮部分破裂脱落,是堆粉状,除锈后肉眼可以见到腐蚀小凹点。
金属除锈质量标准:完全除去金属表面的油脂,疏松氧化皮,浮锈等杂物,紧附的氧化皮点蚀锈坑或旧漆等斑点残留物的面积在任何100㎜×100㎜的面积上不得超过1/3。
五、涂料要求:1、底漆采用环氧防锈底漆,面漆采用高级氟碳面漆。
(附氟碳漆的性能)氟碳漆是由氟碳树脂为主要成分的A、B双组分油漆,它具有以下特点:(1)超强耐候性、防腐蚀性、强自洁性。
(2)强附著性、高装饰性、防水、防老化、耐酸、耐碱。
(3)良好的柔韧性、抗划伤性、耐洗刷性。
(4)优异的耐褪色、不开裂、耐粉化、耐磨损性能等其它普通防腐油漆所不能达到的特性。
2、涂料的品种、性能、颜色、涂刷层数及表面标记等应符合设计规定,涂料应有生产厂家的合格证书。
3、涂料的耐温性能,抗腐性能应按输热介说度及环境条件进行选择。
按涂料工艺要求稀释至适当温度,搅拌均匀,色调一致,及时使用,涂料应密封保存,自然。
4、干燥的现场涂漆应防止漆膜油漆污物和损坏,漆膜为干燥固化剂不得由下道工序施工。
六、涂漆质量应符合以下要求:1、与基础面黏结牢固,厚度符合要求,面层色调一致,光亮清洁,无皱纹、无气泡。
2、漆膜均匀,完整无漏涂,无损坏。
七、设备维护保养:1、对设备的电缆表面进行擦洗除污,检查是否有破损。
2、对钢丝绳、减速机、卷扬机和电机进行清洁保养并进行上油处理。
起重机规程:06起重机涂装工艺规程
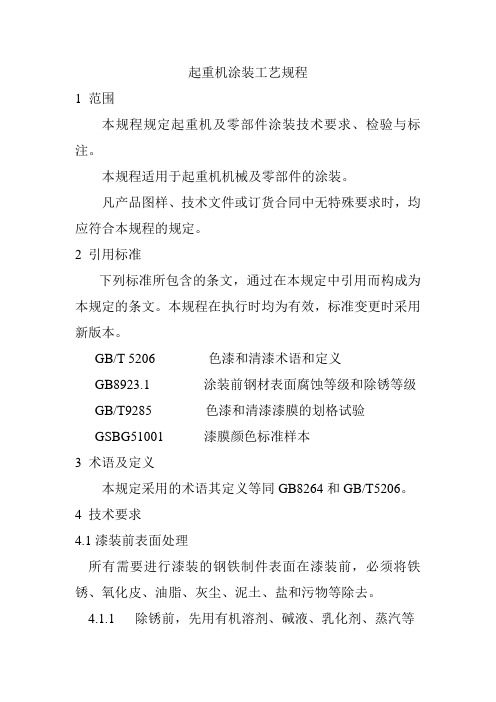
起重机涂装工艺规程1 范围本规程规定起重机及零部件涂装技术要求、检验与标注。
本规程适用于起重机机械及零部件的涂装。
凡产品图样、技术文件或订货合同中无特殊要求时,均应符合本规程的规定。
2 引用标准下列标准所包含的条文,通过在本规定中引用而构成为本规定的条文。
本规程在执行时均为有效,标准变更时采用新版本。
GB/T 5206 色漆和清漆术语和定义GB8923.1 涂装前钢材表面腐蚀等级和除锈等级GB/T9285 色漆和清漆漆膜的划格试验GSBG51001 漆膜颜色标准样本3 术语及定义本规定采用的术语其定义等同GB8264和GB/T5206。
4 技术要求4.1漆装前表面处理所有需要进行漆装的钢铁制件表面在漆装前,必须将铁锈、氧化皮、油脂、灰尘、泥土、盐和污物等除去。
4.1.1 除锈前,先用有机溶剂、碱液、乳化剂、蒸汽等除去钢铁制件表面的抽脂、污垢。
4.1.2 钢铁制件表面的除锈方法、等级及适用范围见JB/T5000.12---2007表1。
4.1.3 若焊接结构件成型后需要热处理,则除锈工序应放在热处理工序之后进行。
4.1.4 除锈的待涂表面与涂底漆的间隔时间不得多于6h。
酸洗除锈后立即经磷化处理的待涂表面与涂底漆的间隔时间不得少于48h(冬季寒冷不得少于72h)。
涂漆前表面均不得有返锈或污染。
4.1.5 用于制造结构件的钢铁板材及型材(壁厚大于5mm),应预先进行除锈。
除锈等级Sa21/2级,并立即涂保养底漆即进行制造前的表面预处理。
涂料技术要求见JB/T5000.12---2007附录A中表A6。
推荐厚度范围15~30um,推荐涂料品种:无机硅酸锌底漆、环氧富锌底漆、磷化底漆、铁红环氧脂底漆。
4.2 涂层设计要求4.2.1 各种涂装类别、产品使用环境、适用产品及部件范围、推荐涂层厚度及涂料品种JB/T5000.12---2007表2。
4.2.2 产品中一些特殊部位及部件的涂装技术要求。
4.2.2.1 铆接件相互接触的表面,在连接前必须涂厚度30~40um防锈漆,所用涂料见JB/5000.12---2007表2中A、B类底漆的规定。
龙门吊除锈刷油施工方案.doc
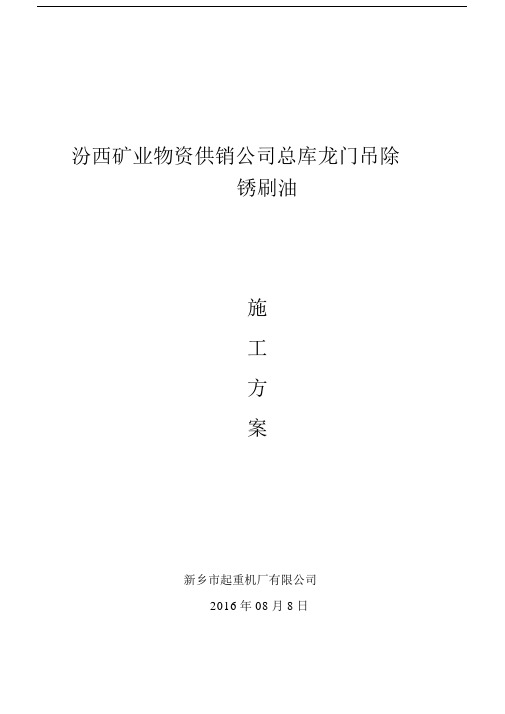
汾西矿业物资供销公司总库龙门吊除锈刷油施工方案新乡市起重机厂有限公司2016年 08月 8日目录1概述2施工准备3施工方法4质量保证措施5质量检查6安全技术措施7施工设备、机具计划8施工手段用料9管理体系1、概述1.1 工程概况汾西矿业集团物资供销公司总库位于孝义市贾家庄,龙门吊规格为32/10t,跨度 27 米。
施工前搭建脚手架,手工机械除锈表面处理,防腐涂层采取一遍底漆、两遍面漆的防腐工艺,底漆采用防锈漆,面漆采用桔红醇酸磁漆。
2、施工准备2.1 施工前认真核对涂漆种类。
2.2 施工前根据本方案准备好各种施工设备、机具、手段用料等。
2.3 防腐的各种材料进场,并经甲、乙双方检验合格。
3、施工方法3.1 施工程序搭脚手架→钢结构表面处理→涂刷底漆一道→涂面漆两道3.2 材料验收3.2.1 所有原材料必须具有出厂质量证明书或化学分析报告,各项技术要求符合标准规定。
龙门吊钢结构防腐工程中使用的所有原材料均应符合国家有关标准及本规范的相关技术指标,并且有出厂合格证和检验报告等技术资料。
防腐施工必须按国家现行的有关规定及防腐材料的使用说明执行。
其材料必须在规定的有效期内使用。
3.2.2 所有油漆必须确认在有效期内方可使用,过期的材料必须经复检合格方可使用。
3.2.3 材料经检验合格后按品种、规格分类存放。
3.2.4 防腐涂层采取一遍底漆、两遍面漆的防腐工艺,底漆采用环氧富锌底漆,面漆采用桔红醇酸磁漆。
3.3 具体工艺3.3.1 脚手架搭设必须由专业人员搭设;3.3.2 脚手架必须经专职安全员检查确认后方可使用。
3.3.3 难清理部位(含油污等)先进行脱漆剂喷洒再进行手工或机械打磨,其它部位直接采用手工或机械打磨,按照 GB8923-88《涂装前钢材表面锈蚀等级和除锈等级》的规定 ,采用手工或机械除锈方式的达到cst3 或 dst3 质量等级(视钢构锈烛程度)。
3.3.4 龙门吊钢结构表面除锈应达到cst3 或 dst3 级(视钢构锈烛程度)要求: 应无可见的油脂和污垢,且无附着不牢的起壳氧化皮、铁锈和旧漆皮等附着物,底材显露部分的表面应具有金属光泽。
龙门吊主梁上盖板现场涂漆方案
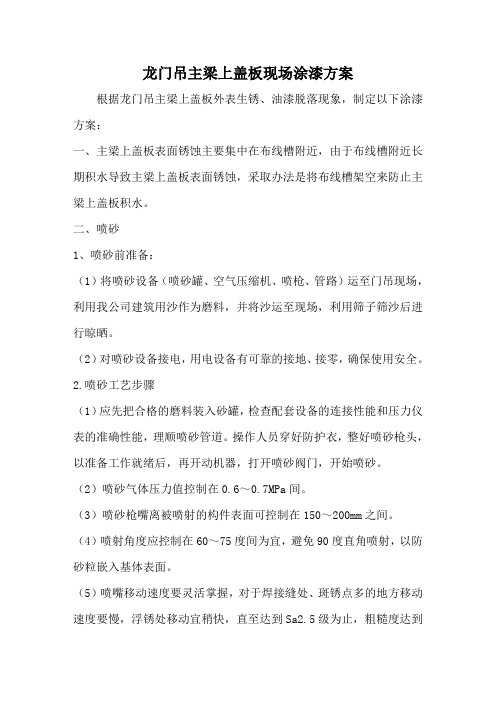
龙门吊主梁上盖板现场涂漆方案根据龙门吊主梁上盖板外表生锈、油漆脱落现象,制定以下涂漆方案:一、主梁上盖板表面锈蚀主要集中在布线槽附近,由于布线槽附近长期积水导致主梁上盖板表面锈蚀,采取办法是将布线槽架空来防止主梁上盖板积水。
二、喷砂1、喷砂前准备:(1)将喷砂设备(喷砂罐、空气压缩机、喷枪、管路)运至门吊现场,利用我公司建筑用沙作为磨料,并将沙运至现场,利用筛子筛沙后进行晾晒。
(2)对喷砂设备接电,用电设备有可靠的接地、接零,确保使用安全。
2.喷砂工艺步骤(1)应先把合格的磨料装入砂罐,检查配套设备的连接性能和压力仪表的准确性能,理顺喷砂管道。
操作人员穿好防护衣,整好喷砂枪头,以准备工作就绪后,再开动机器,打开喷砂阀门,开始喷砂。
(2)喷砂气体压力值控制在0.6~0.7MPa间。
(3)喷砂枪嘴离被喷射的构件表面可控制在150~200mm之间。
(4)喷射角度应控制在60~75度间为宜,避免90度直角喷射,以防砂粒嵌入基体表面。
(5)喷嘴移动速度要灵活掌握,对于焊接缝处、斑锈点多的地方移动速度要慢,浮锈处移动宜稍快,直至达到Sa2.5级为止,粗糙度达到40~80μm。
(6)喷砂后的表面一定要用干燥空气吹或吸的方法净化处理,处理过的表面应无油脂、无锈、无污物,金属基体露出均匀一致的灰白色,粗糙度均匀。
2、喷砂施工中应注意的问题:(1)喷砂工应穿戴劳保装,作好自身的防护工作。
(2)喷砂温度应高于大气露点3度,相对湿度小于或等于80%。
(3)磨料有潮湿时,应对其进行干燥处理,并保持其清洁。
(4)对与喷砂部位相临的不喷砂部位应采取保护措施。
3、检测用粗糙度检测仪检查,用粗糙度测定仪对表面处理的基体表面检查时,每10m2选定8处,每处选定5个点进行测量,每处5个点的算术平均值,作为该处的粗糙度数值。
但5个点内任何一点的最小读数不小于40µm,最大读数不大于80µm为合格。
三、油漆涂装底漆采用滚涂,面漆采用喷涂。
龙门吊除锈刷油施工方案
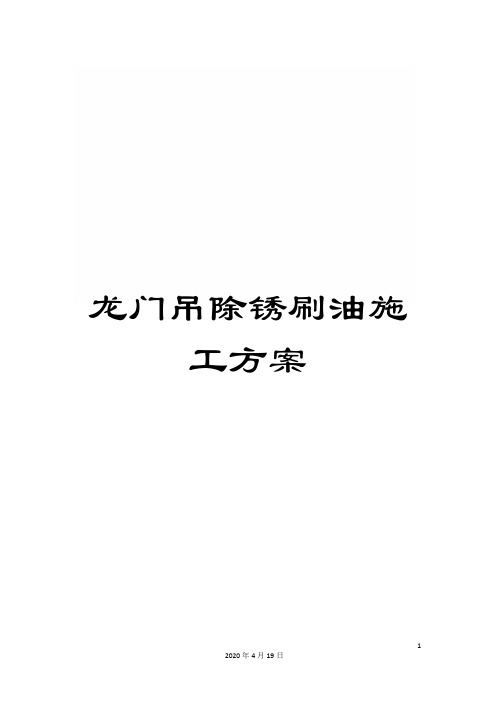
龙门吊除锈刷油施工方案1汾西矿业物资供销公司总库龙门吊除锈刷油施工方案新乡市起重机厂有限公司08月8日目录1概述2施工准备3施工方法4质量保证措施5 质量检查6安全技术措施7施工设备、机具计划8施工手段用料9管理体系1、概述1.1工程概况汾西矿业集团物资供销公司总库位于孝义市贾家庄,龙门吊规格为32/10t,跨度27米。
施工前搭建脚手架,手工机械除锈表面处理,防腐涂层采取一遍底漆、两遍面漆的防腐工艺,底漆采用防锈漆,面漆采用桔红醇酸磁漆。
2、施工准备2.1施工前认真核对涂漆种类。
2.2施工前根据本方案准备好各种施工设备、机具、手段用料等。
2.3防腐的各种材料进场,并经甲、乙双方检验合格。
3、施工方法3.1施工程序搭脚手架→钢结构表面处理→涂刷底漆一道→涂面漆两道3.2材料验收3.2.1所有原材料必须具有出厂质量证明书或化学分析报告,各项技术要求符合标准规定。
龙门吊钢结构防腐工程中使用的所有原材料均应符合国家有关标准及本规范的相关技术指标,而且有出厂合格证和检验报告等技术资料。
防腐施工必须按国家现行的有关规定及防腐材料的使用说明执行。
其材料必须在规定的有效期内使用。
3.2.2所有油漆必须确认在有效期内方可使用,过期的材料必须经复检合格方可使用。
3.2.3材料经检验合格后按品种、规格分类存放。
3.2.4防腐涂层采取一遍底漆、两遍面漆的防腐工艺,底漆采用环氧富锌底漆,面漆采用桔红醇酸磁漆。
3.3 具体工艺3.3.1脚手架搭设必须由专业人员搭设;3.3.2脚手架必须经专职安全员检查确认后方可使用。
3.3.3难清理部位(含油污等)先进行脱漆剂喷洒再进行手工或机械打磨,其它部位直接采用手工或机械打磨,按照GB8923-88《涂装前钢材表面锈蚀等级和除锈等级》的规定,采用手工或机械除锈方式的达到cst3或dst3质量等级(视钢构锈烛程度)。
3.3.4龙门吊钢结构表面除锈应达到cst3或dst3级(视钢构锈烛程度)要求:应无可见的油脂和污垢,且无附着不牢的起壳氧化皮、铁锈和旧漆皮等附着物,底材显露部分的表面应具有金属光泽。
龙门吊防腐要求
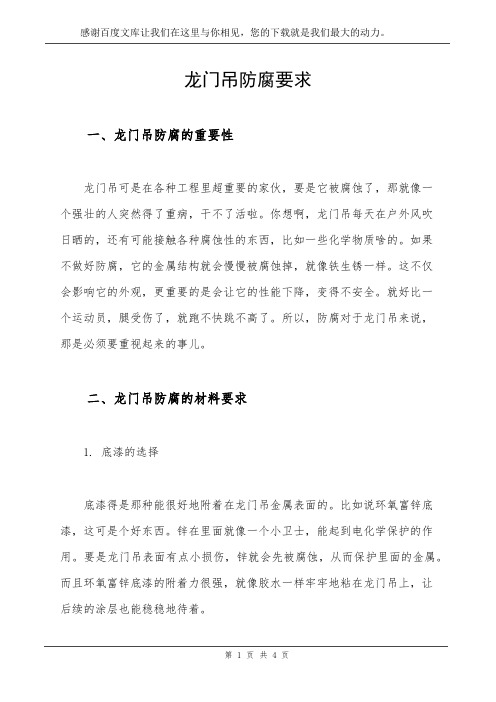
龙门吊防腐要求一、龙门吊防腐的重要性龙门吊可是在各种工程里超重要的家伙,要是它被腐蚀了,那就像一个强壮的人突然得了重病,干不了活啦。
你想啊,龙门吊每天在户外风吹日晒的,还有可能接触各种腐蚀性的东西,比如一些化学物质啥的。
如果不做好防腐,它的金属结构就会慢慢被腐蚀掉,就像铁生锈一样。
这不仅会影响它的外观,更重要的是会让它的性能下降,变得不安全。
就好比一个运动员,腿受伤了,就跑不快跳不高了。
所以,防腐对于龙门吊来说,那是必须要重视起来的事儿。
二、龙门吊防腐的材料要求1. 底漆的选择底漆得是那种能很好地附着在龙门吊金属表面的。
比如说环氧富锌底漆,这可是个好东西。
锌在里面就像一个小卫士,能起到电化学保护的作用。
要是龙门吊表面有点小损伤,锌就会先被腐蚀,从而保护里面的金属。
而且环氧富锌底漆的附着力很强,就像胶水一样牢牢地粘在龙门吊上,让后续的涂层也能稳稳地待着。
2. 中间漆的选择中间漆得有一定的厚度和填充性。
像环氧云铁中间漆就很不错。
它里面的云母氧化铁就像一片片小盾牌,能进一步阻挡外界的腐蚀物质。
而且它可以让整个防腐涂层更加厚实,就像给龙门吊穿上了一件厚厚的防护服中间的那层棉花一样,增加了防腐的能力。
3. 面漆的选择面漆得是那种耐候性好的。
聚氨酯面漆就很适合。
它能经受住阳光的暴晒、雨水的冲刷,还不容易褪色。
这就好比给龙门吊穿上了一件漂亮又耐用的外套,不仅能防腐,还能让龙门吊看起来很新。
三、龙门吊防腐的施工要求1. 表面处理在涂漆之前,龙门吊的表面必须处理得干干净净。
得把那些铁锈、油污、灰尘啥的都去掉。
就像我们洗脸一样,得把脸洗干净了才能擦护肤品。
可以用喷砂或者打磨的方法来处理表面。
喷砂就像一阵小风暴,把那些脏东西都吹走;打磨就像用小刷子把表面刷得光溜溜的。
2. 涂漆工艺涂漆的时候也有讲究。
不能涂得太厚也不能太薄。
太厚了可能会流下来,就像我们吃蛋糕的时候,奶油涂太多会流下来一样难看,而且还浪费材料。
太薄了又起不到很好的防腐作用。
起重机金属结构件除锈油漆工艺守则
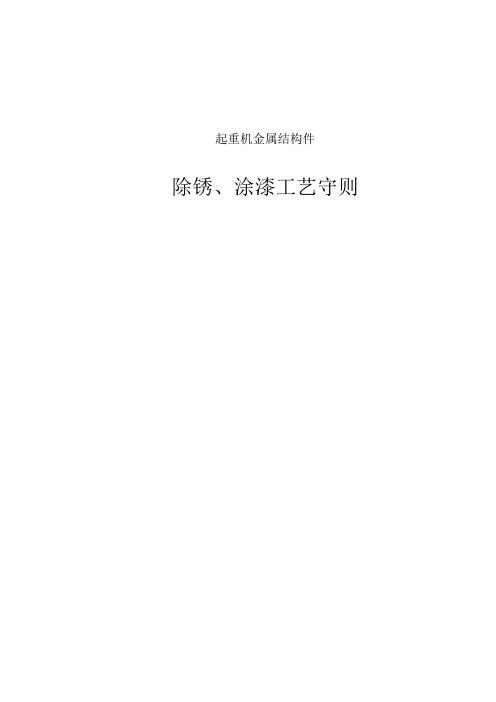
起重机金属结构件除锈、涂漆工艺守则目录一、总贝IJ (2)二、除锈,清理表面 (3)三、涂底漆 (3)四、涂刮腻子 (4)五、涂表面漆 (4)六、涂漆方法 (5)七、涂防化学过氯乙烯漆 (7)八、施工安全要求 (7)九、拆车和零件箱的包装 (7)十、本厂起重机常用的油漆种类 (8)十一、典型件涂底漆要求 (9)十二、起重机涂漆典型工艺过程 (10)一、总则(-)本工艺守则适用于各类起重机产品,对除锈涂漆无特殊要求的其他产品,也可按本守则进行。
(二)油漆颜色按部颁标准Jp2279—78标准执行。
涂漆技术,施工要求等按本厂Q/DQ110—74及Q/DQ111-74{援外}标准执行。
二、除锈、清理表面1、除锈前要做好一切准备工作,如工具,防护用具的准备工作,设备检查,并将加工表面,轴孔及接手,走轮,瓦盖等部件上的间隙,都用胶皮和挡板堵塞当好后,进行除锈。
2、除锈①清除铁锈,氧化皮,污泥,焊渣等(允许抛丸时难以除净地方有残存的少量氧化铁皮)并将残存的少量氧化皮手工除掉。
②机械除锈的喷丸咀,直径采用8mm,使用中不得超过12mm,超过时应换新的。
③除锈后的金属表面应仔细用压缩空气吹净。
3、去除旧漆①当旧漆膜全部变色,整个表面起皱纹,老化,下层漆膜脱落和肉眼可见的漆面裂纹,起泡及出现锈斑等缺陷时,根据具体情况将旧漆全部或局部清除。
允许存在漆层坚固,附着力较好的旧漆。
②使用手工镶去旧漆时,镯后须用钢丝刷刷净,在用砂布打去表面旧漆毛刺,也可以采用机械除锈方法去除旧漆。
③用压缩空气将表面清理干净。
三、涂底漆(刷涂、浸漆、喷涂)1、除锈工作完成后,清理干净金属表面,应及时涂上底漆。
2、涂底漆的金属表面必须干燥,不能有水分,露霜,潮气层存在。
3、涂底漆应在清洁、干燥的地方进行,环境温度最低不得低于5C,相对湿度应低于70-80%,在室外施工时,禁止在烈日、下雨和雾、风沙时喷(刷)漆。
4、根据产品技术要求涂一遍底漆,如需涂二遍底漆的产品必须待第一遍底漆干燥后方可进行,一般干燥时间在温度18°C~23°C时为24~48小时。
起重机翻新涂装工艺流程
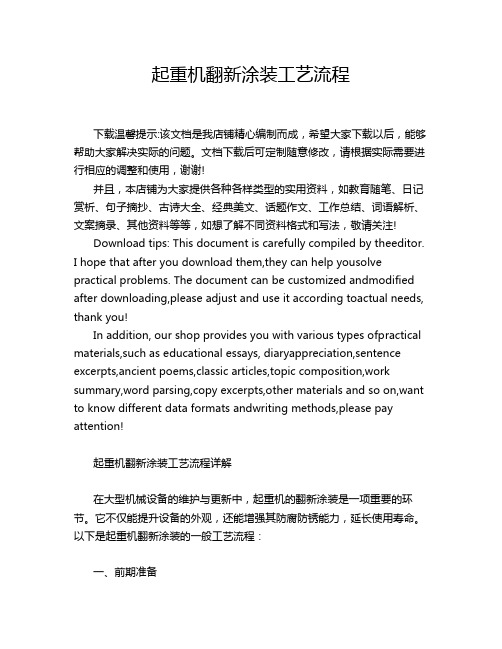
起重机翻新涂装工艺流程下载温馨提示:该文档是我店铺精心编制而成,希望大家下载以后,能够帮助大家解决实际的问题。
文档下载后可定制随意修改,请根据实际需要进行相应的调整和使用,谢谢!并且,本店铺为大家提供各种各样类型的实用资料,如教育随笔、日记赏析、句子摘抄、古诗大全、经典美文、话题作文、工作总结、词语解析、文案摘录、其他资料等等,如想了解不同资料格式和写法,敬请关注!Download tips: This document is carefully compiled by theeditor.I hope that after you download them,they can help yousolve practical problems. The document can be customized andmodified after downloading,please adjust and use it according toactual needs, thank you!In addition, our shop provides you with various types ofpractical materials,such as educational essays, diaryappreciation,sentence excerpts,ancient poems,classic articles,topic composition,work summary,word parsing,copy excerpts,other materials and so on,want to know different data formats andwriting methods,please pay attention!起重机翻新涂装工艺流程详解在大型机械设备的维护与更新中,起重机的翻新涂装是一项重要的环节。
龙门吊防腐技术措施
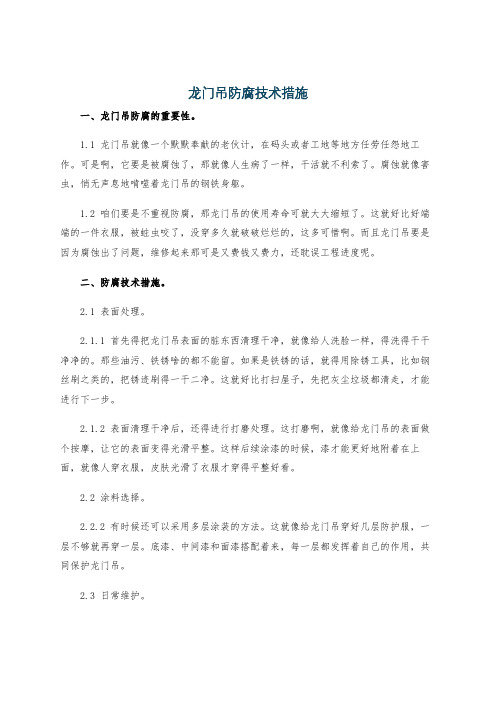
龙门吊防腐技术措施一、龙门吊防腐的重要性。
1.1 龙门吊就像一个默默奉献的老伙计,在码头或者工地等地方任劳任怨地工作。
可是啊,它要是被腐蚀了,那就像人生病了一样,干活就不利索了。
腐蚀就像害虫,悄无声息地啃噬着龙门吊的钢铁身躯。
1.2 咱们要是不重视防腐,那龙门吊的使用寿命可就大大缩短了。
这就好比好端端的一件衣服,被蛀虫咬了,没穿多久就破破烂烂的,这多可惜啊。
而且龙门吊要是因为腐蚀出了问题,维修起来那可是又费钱又费力,还耽误工程进度呢。
二、防腐技术措施。
2.1 表面处理。
2.1.1 首先得把龙门吊表面的脏东西清理干净,就像给人洗脸一样,得洗得干干净净的。
那些油污、铁锈啥的都不能留。
如果是铁锈的话,就得用除锈工具,比如钢丝刷之类的,把锈迹刷得一干二净。
这就好比打扫屋子,先把灰尘垃圾都清走,才能进行下一步。
2.1.2 表面清理干净后,还得进行打磨处理。
这打磨啊,就像给龙门吊的表面做个按摩,让它的表面变得光滑平整。
这样后续涂漆的时候,漆才能更好地附着在上面,就像人穿衣服,皮肤光滑了衣服才穿得平整好看。
2.2 涂料选择。
2.2.2 有时候还可以采用多层涂装的方法。
这就像给龙门吊穿好几层防护服,一层不够就再穿一层。
底漆、中间漆和面漆搭配着来,每一层都发挥着自己的作用,共同保护龙门吊。
2.3 日常维护。
2.3.1 龙门吊在使用过程中,要经常检查它的防腐情况。
这就像定期给人做体检一样,发现哪里有问题就及时处理。
如果发现漆皮脱落了,就得赶紧补上,不能让腐蚀有可乘之机。
2.3.2 另外呢,要注意龙门吊工作的环境。
要是周围环境比较潮湿或者有腐蚀性气体,就得想办法改善。
比如说加强通风,这就好比给龙门吊一个干爽的工作环境,让它不容易被腐蚀。
三、总结。
3.1 龙门吊的防腐可不是一件小事,就像照顾自己的孩子一样,得细心周到。
各个环节都得做到位,从表面处理到涂料选择,再到日常维护,一个都不能少。
3.2 只有把防腐工作做好了,龙门吊才能健健康康地工作,为咱们的工程建设等继续发挥它的重要作用。
桁架式龙门吊刷漆作业指导书
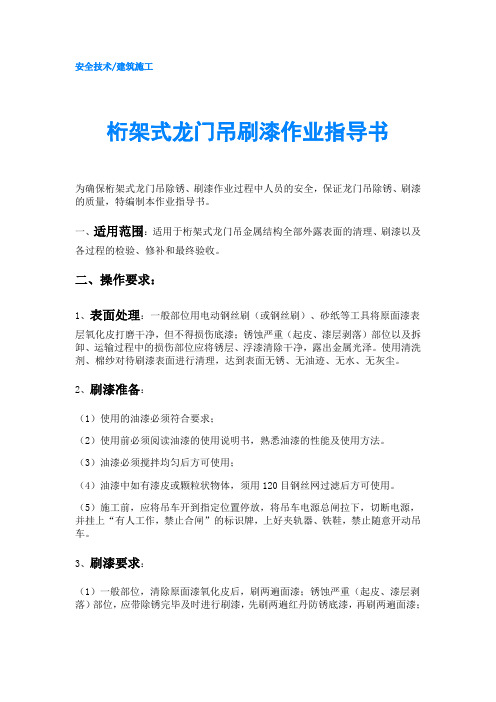
安全技术/建筑施工桁架式龙门吊刷漆作业指导书为确保桁架式龙门吊除锈、刷漆作业过程中人员的安全,保证龙门吊除锈、刷漆的质量,特编制本作业指导书。
一、适用范围:适用于桁架式龙门吊金属结构全部外露表面的清理、刷漆以及各过程的检验、修补和最终验收。
二、操作要求:1、表面处理:一般部位用电动钢丝刷(或钢丝刷)、砂纸等工具将原面漆表层氧化皮打磨干净,但不得损伤底漆;锈蚀严重(起皮、漆层剥落)部位以及拆卸、运输过程中的损伤部位应将锈层、浮漆清除干净,露出金属光泽。
使用清洗剂、棉纱对待刷漆表面进行清理,达到表面无锈、无油迹、无水、无灰尘。
2、刷漆准备:(1)使用的油漆必须符合要求;(2)使用前必须阅读油漆的使用说明书,熟悉油漆的性能及使用方法。
(3)油漆必须搅拌均匀后方可使用;(4)油漆中如有漆皮或颗粒状物体,须用120目钢丝网过滤后方可使用。
(5)施工前,应将吊车开到指定位置停放,将吊车电源总闸拉下,切断电源,并挂上“有人工作,禁止合闸”的标识牌,上好夹轨器、铁鞋,禁止随意开动吊车。
3、刷漆要求:(1)一般部位,清除原面漆氧化皮后,刷两遍面漆;锈蚀严重(起皮、漆层剥落)部位,应带除锈完毕及时进行刷漆,先刷两遍红丹防锈底漆,再刷两遍面漆;(2)除锈后的金属表面与刷防锈漆的间隔时间不得大于6小时,不得过夜,刷漆前表面不得有锈蚀或污染。
阴雨天、大风天气以及气温低于5~6℃时禁止作业。
(3)必须待前一遍油漆充分干燥后,方可进行下一遍油漆的涂刷;(4)涂刷时每层应往复进行、纵横交错,不可按同一方向涂刷,并应保持涂层均匀,不得露涂;(5)涂刷时应尽量保持涂层薄而均匀,以免漆层起皱和影响干燥;每遍涂层的厚度应控制在25um左右,涂层总厚度为100um。
(6)涂刷过程中如发现涂层有不干、皱皮、流柱、露底等现象时,应进行修补或重刷;4、刷漆操作程序:(1)龙门吊的刷漆应遵从自上到下,分段除锈、刷漆的原则;(2)刷漆工两人一组,穿戴好劳保用品(安全带、安全帽、防滑鞋等),站在工字钢梁上使用磨光机(装配钢丝轮刷)对顶部大梁进行除锈,工字钢与电动葫芦行走轮配合处不刷漆,安全带应挂在顶部横梁上;工字钢梁底部应由作业人员站在爬梯上进行除锈、刷漆作业,爬梯顶部与工字钢梁捆绑牢固,作业人员将安全带挂在吊车梁上,使用钢丝轮刷除锈、使用毛刷进行四遍刷漆作业。
起重机公司涂装工艺指导书2021

起重机公司涂装工艺指导书2021涂装作业指导书1.目的规范涂装工艺参数和作业要求,确保涂装产品质量符合要求。
2.适用范围适用于公司涂装产品的生产和检验作业。
3.使用设备喷漆枪及相关检测设备4.工艺要求4.1工艺参数4.1.1调漆单组份油漆:红面漆与稀释剂的重量比例为1:0.25,粘度为20~30S黄面漆与稀释剂的重量比例为1:0.2,粘度为20~30S铁锈红底漆与稀释剂的重量比例为1:0.25,粘度为20~30S双组份油漆:黄面漆、固化剂与稀释剂的重量比例为4:1:1,粘度为20~30S4.1.单组份油漆:一般零部件,底漆两遍,每遍时间间隔为1~1.5小时,头遍漆膜厚度为18±5μm,总漆膜厚度为30±5μm,面漆两遍,每遍时间间隔为2~2.5小时,总漆膜厚度为≥60μm(包括底漆)每批调好漆的油漆应当在当天用完,确实用不完的必须密闭保存。
双组份油漆:一般零部件,底漆两遍,每遍时间间隔为1~1.5小时,头遍漆膜厚度为18±5μm,总漆膜厚度为30±5μm,面漆两遍,每遍时间间隔为2~2.5小时,总漆膜厚度为≥60μm(包括底漆)根据零部件的多少调制相当数量的油漆,调制好的油漆当时必须用完。
4.1.3喷涂气压空气压力应为0.48~0.62Mpa4.2 作业流程4.2.1一般零部件先喷涂底漆两遍,再喷涂面漆两遍。
单组份油漆每批调好漆的油漆应当在当天用完,确实用不完的必须密闭保存,双组份油漆根据零部件的多少调制相当数量的油漆,调制好的油漆当时必须用完。
4.2.2作业环境应清洁、干燥、空气流通,光线充足。
第一遍底漆。
先试喷使雾化效果达到最佳,尖角、棱角边缘等难以保证漆膜厚度的部位应先喷涂一遍,然后再进行整体涂装,操作时应遵循从里到外、从上到下,从边角到大面的顺序,为使喷涂均匀,每枪应迭压前一枪的1/3-2/3,运枪速度应均匀一致,不可时快时慢,喷涂要均匀,无漏涂、无流挂、起泡粗粒等缺陷,喷涂时起枪收枪应在工件之外。
起重机现场涂装方案

起重机现场防腐油漆施工方案吊车外表生锈、腐蚀严重,油漆脱落,现根据现场情况及业主建议,提出施工方案:一、起重机大车走台平面及小车平面机械除锈(除锈等级中级),对局部地方进行补漆,刷红丹环氧防锈底漆两遍,高级氟碳面漆两遍。
二、起重机大车走台小车平台的侧面及底部机械除锈(除锈等级中级),对局部地方进行补漆,对刷红丹环氧防锈底漆两遍,高级氟碳面漆两遍。
三、轨道底部铁板,刷沥青漆一底一面,轨道机械除锈等级中级,刷沥青漆一底一面。
四、除锈方法:电动工具除锈,除锈等级为S t2级。
金属面标准:氧化皮部分破裂脱落,是堆粉状,除锈后肉眼可以见到腐蚀小凹点。
金属除锈质量标准:完全除去金属表面的油脂,疏松氧化皮,浮锈等杂物,紧附的氧化皮点蚀锈坑或旧漆等斑点残留物的面积在任何100㎜×100㎜的面积上不得超过1/3。
五、涂料要求:1、底漆采用环氧防锈底漆,面漆采用高级氟碳面漆。
(附氟碳漆的性能)氟碳漆是由氟碳树脂为主要成分的A、B双组分油漆,它具有以下特点:(1)超强耐候性、防腐蚀性、强自洁性。
(2)强附著性、高装饰性、防水、防老化、耐酸、耐碱。
(3)良好的柔韧性、抗划伤性、耐洗刷性。
(4)优异的耐褪色、不开裂、耐粉化、耐磨损性能等其它普通防腐油漆所不能达到的特性。
2、涂料的品种、性能、颜色、涂刷层数及表面标记等应符合设计规定,涂料应有生产厂家的合格证书。
3、涂料的耐温性能,抗腐性能应按输热介说度及环境条件进行选择。
按涂料工艺要求稀释至适当温度,搅拌均匀,色调一致,及时使用,涂料应密封保存,自然。
4、干燥的现场涂漆应防止漆膜油漆污物和损坏,漆膜为干燥固化剂不得由下道工序施工。
六、涂漆质量应符合以下要求:1、与基础面黏结牢固,厚度符合要求,面层色调一致,光亮清洁,无皱纹、无气泡。
2、漆膜均匀,完整无漏涂,无损坏。
七、设备维护保养:1、对设备的电缆表面进行擦洗除污,检查是否有破损。
2、对钢丝绳、减速机、卷扬机和电机进行清洁保养并进行上油处理。
- 1、下载文档前请自行甄别文档内容的完整性,平台不提供额外的编辑、内容补充、找答案等附加服务。
- 2、"仅部分预览"的文档,不可在线预览部分如存在完整性等问题,可反馈申请退款(可完整预览的文档不适用该条件!)。
- 3、如文档侵犯您的权益,请联系客服反馈,我们会尽快为您处理(人工客服工作时间:9:00-18:30)。
资料编号:HJ/Y-港80/漆-04使用车间:钢构制造部港80油漆涂装工艺规程批准:_____________校核:_____________编制:_____________青岛海西重机有限责任公司2009年10月28日1 基本要求1.1该门式起重机长期处在盐雾多、湿度大及温差大的海洋大气和工业大气的腐蚀环境中工作,同时该起重机工作繁忙、涂装维修困难。
根据起重机涂装寿命不小于15年,涂装质量保证期3年的技术要求,涂装方案采用防腐蚀性能优异、耐海洋性气候、性能可靠的涂装材料。
1.2 本规程书适用于600t门式起重机主梁、刚腿、柔腿等结构件及配套制造的上下小车、维修起重机及大车行走机构的涂装工作。
1.3涂装施工时应严格执行产品使用说明书的有关规定,并接受产品服务工程师的现场指导。
2 引用标准2.1国家标准GB8923-88 涂装前钢材表面锈蚀等级和除锈等级ISO 8504-1:1998或GB13288:1991 表面处理粗糙度标准GB9286-1998 色漆和清漆漆膜的划格试验GB1764-79 漆膜厚度测定法标准GB/T 13912-2002 金属覆盖层钢铁制件热浸镀锌层技术要求及试验方法2.2参考标准及资料SIS 055900 瑞典工业除锈标准ISO8501-1:1988 钢材表面涂装油漆前的除锈和清洁度的目视评定ISO8503 钢材表面粗糙度特征ISO24092/ISO24093 附着力测试-划格法ISO4624 附着力测试-拉开法GSB G51001-94 漆膜颜色标准样卡标准ISO12944-1~8 腐蚀环境评定与划分、涂装防腐期设计、油漆系统选择标准3涂装寿命计算与防腐设计3.1防护年限计算依据:ISO标准:ISO12944-1~8部分。
3.2工作环境及气象条件3.2.1气温:极端最高气温39.9℃, 极端最低气温-18.3℃,年平均气温12.3℃。
3.2.2湿度:最小湿度3%,最大湿度100%,年平均相对湿度65%。
3.2.3工作环境:海洋地区的工业集结区,这里的大气为海洋大气与工业大气的混合物。
3.2.4风速:门式起重机在工作状态的最大风速为20m/s(测量高度为离地10米处),在非工作状态最大风速为40m/s(测量高度为离地10米处)。
3.2.5雾况:有轻度盐雾,按10度设计。
3.2.6地震:地震基本烈度为7度。
3.3涂装防腐设计根据工作环境条件,该门式起重机处于海边海洋和工业性气候,但属于中低的海洋性腐蚀状态。
按照ISO12944-2:1998(E)标准的分类规定,属于C4腐蚀状态:低合金钢暴露于大气中第一年度,厚度将损失50~80μm(相当于400-650g/m2质量损失)3.4涂装寿命设计依据ISO12944-5:1998(E)标准中5.5部分规定,使用寿命为油漆防护体系施工完到第一次油漆大修的保护年限。
它按照ISO4628-1至ISO4628-6的评估,并依据Ri3的标准,将油漆的防护年限定为三个等级,即低级:2~5年,中级:5~15年,高级:大于15年。
基于起重机涂装寿命不小于15年的防腐要求,金属结构件外表面油漆配套方案按C4腐蚀环境设计,箱体结构内壁及装有扶梯的箱形体和桶体内部油漆配套方案按C3腐蚀环境设计。
4、配套油漆系统4.1结构外表面(腐蚀环境-C4)第一道面漆的涂装在厂内施工,第二道面漆待主梁、刚腿、柔腿整体成型后在天津安装现场涂装。
4.2箱体结构内部(腐蚀环境-C3)主梁、刚腿、柔腿各分段结构成型后在厂内涂装内表面底漆、面漆,各分段合拢成型后对内表面面漆进行修补。
内表面示意图如下(以主梁为例)示意图14.3封闭结构内部涂层 产品名称干膜厚度 (微米)道数 底漆环氧富锌底漆Barrier ZEP501封闭面示意图如下:内表面内表面内表面示意图24.4板材、型钢预处理预处理底漆:无机硅酸锌车间底漆,干膜厚度20μm。
4.5梯子、平台、栏杆(1)外部梯子、平台格栅板、栏杆:热浸锌处理。
(2)箱体内部梯子、平台、栏杆,与主机箱体结构内部相同,即:涂层产品名称干膜厚度 (微米) 道数底漆快干型环氧磷酸锌漆Penguard Express ZP 150 1 面漆环氧漆FC 50 1干膜总厚度200 24.6油漆品牌:佐敦(Jotun)。
4.7结构件各部位面漆颜色部位颜色及色标外表面内表面主梁桔红RAL2004 白色RAL9003 刚腿桔红RAL2004 白色RAL9003 柔腿桔红RAL2004 白色RAL9003 上小车桔红RAL2004 白色RAL9003 下小车桔红RAL2004 白色RAL9003 司机室桔红RAL2004 白色RAL9003 外部梯子栏杆热浸锌处理无箱体内部梯子栏杆白色RAL9003 无行走机构平衡梁黄黑相间警戒线,宽200倾斜45度,黑色RAL9005,黄色RAL1021无封闭面—U形肋内部5 表面处理5.1 钢材表面预处理5.1.1钢材表面预处理前应清理表面积水、油脂及其它污物。
5.1.2钢材在下料前应经抛丸预处理,达到GB8923-88标准的Sa2.5级,表面粗糙度达到40-80μm。
表面处理达到标准并经检查合格后,应及时喷涂车间底漆,其漆层干膜厚度为20μm。
5.2 二次除锈5.2.1主梁、刚腿、柔腿各分段结构,上、下小车车架,行走机构各平衡梁、车架,维修吊主桩、横梁结构及其它结构件采用冲砂除锈,在冲砂前应预先打磨,清除结构表面的焊瘤、飞溅、毛刺,自由边锐角均应打磨至R=2mm,并用高压水、溶剂清除表面的灰尘、可溶盐、油脂等污物,保持所有施工表面清洁与干燥。
冲砂处理后,表面质量需达到GB8923-88标准的Sa2.5级。
5.2.2 主梁下箱体内部、柔腿下横梁内部、U形肋及梯子栏杆采用动力工具(动力砂纸片、砂轮片等)对焊缝区、火工烧损区、自然锈蚀区等部位进行除锈和清理,除锈等级须达到GB8923-88标准的St3级,即在不放大的情况下进行观察,表面应无可见的油脂和污物,并且几乎没有附着不牢的氧化皮、铁锈、油漆涂层和异物,表面应具有金属底材的光泽。
5.3 表面清洁处理5.3.1涂装下道涂层前,对除锈过的表面或前道涂层表面进行清洁处理,清除表面的油脂、灰尘、水分、盐分、焊接烟尘、粉笔或油漆等记号。
5.3.2各分段、组件结构车间底漆完整的区域,应除去表面锌盐、污物、油污等。
5.4 遮蔽5.4.1现场拼装件的安装焊缝两侧各100mm处用胶带纸进行遮蔽,然后再开始涂漆。
拼接完成后用动力工具进行除锈处理,达到GB8923-88标准的St3级,再按原配套油漆涂装。
5.4.2喷涂作业之前,对周围不应涂漆的部位,用塑料薄膜作好遮蔽。
5.5 除锈环境二次除锈应在相对湿度小于85%,构件表面温度高于露点温度3℃时进行,除锈结束后应将表面残留的粉尘和磨料碎屑用吸尘器、清洁干燥的压缩空气或用干净的刷子清除干净,并在4小时之内完成底漆的涂装,以免除锈后的构件表面重新被氧化或返锈。
6 涂装工艺技术要求6.1 各道涂层工艺技术参数6.1.1主结构外部表面(1)环氧富锌底漆Barrier ZEP干膜厚度:70μm;稀释剂:佐敦17号稀释剂;参考稀释比例:0~5%;混合比:PartA:PartB=8:1(体积比)a.用动力搅拌器将基料(PartA)搅拌均匀,然后边搅拌边加入固化剂(PartB),直至充分混合均匀(可适当加入佐敦17号稀释剂)。
喷涂时,油漆桶内用机械或动力装置持续搅拌,边喷涂边搅拌,直至用完。
b.混合使用寿命(23℃):4小时。
c.喷涂实施前对过焊孔、自由边、阴角处等不易喷涂部位进行预涂。
d.主要喷涂方式:高压无气喷涂,喷嘴孔径0.38~0.53mm,喷嘴压力15MPa。
e.环境要求:相对湿度在85%以下,钢板温度不可低于5℃并且大于露点温度3℃以上。
f.表干、硬干、固化时间以及覆涂间隔时间g白色锌盐,在涂装下一道油漆之前也应砂磨除去。
(2)快干型环氧云铁漆Penguard Express MIO干膜厚度:150μm;稀释剂:佐敦17号稀释剂;参考稀释比例:0~5%;混合比:PartA:PartB=4:1(体积比)a.用动力搅拌器充分搅拌基料(PartA),边搅拌边加入固化剂(PartB),继续用动力搅拌器充分搅拌(可适当加入佐敦17号稀释剂),搅拌均匀后待用。
喷涂时,油漆桶内用机械或动力缓慢搅拌,边喷涂边搅拌,直至用完。
b.混合使用寿命(23℃):2小时(随温度升高而缩短)。
c.喷涂实施前对过焊孔、自由边、阴角处等不易喷涂部位进行预涂。
d.主要喷涂方式:高压无气喷涂,喷嘴孔径0.46~0.69mm,喷嘴压力15MPa。
e.环境要求:相对湿度在85%以下,钢板温度不可低于零下5℃并且大于露点温度3℃以上。
f.表干、硬干时间以及覆涂间隔时间。
g保持干燥,以获得平滑、干净的漆膜表面,有利于面漆成膜光滑,得到最佳的防腐效果。
(3)脂肪族聚氨酯面漆Hardtop XP干膜厚度:60μm;稀释剂:佐敦10号稀释剂;参考稀释比例:0~5%;混合比:PartA:PartB=10:1(体积比)a.用动力搅拌器充分搅拌基料(PartA),边搅拌边加入固化剂(PartB),继续用动力搅拌器充分搅拌(可适当加入佐敦10号稀释剂),搅拌均匀后待用。
喷涂时,油漆桶内用机械或动力缓慢搅拌,边喷涂边搅拌,直至用完。
b.混合后使用寿命(23℃):1.5小时。
c.喷涂前,先对边、角、焊缝、阴角等不易喷涂处进行预涂。
d.主要喷涂方式:高压无气喷涂,喷嘴孔径0.28~0.38mm,喷嘴压力15MPa。
e.环境要求:相对湿度在85%以下,钢板温度应不低于0℃并且大于露点温度3℃以上。
f.表干、硬干时间以及覆涂间隔时间。
g面漆喷涂24小时后(环境温度25℃条件下)进行,否则易产生碰伤。
如环境温度变化,应调整待干时间,确定漆膜完全固化后方可包装。
凡碰伤或因需要校正、烧焊处,修补必须按所指定的修补方案执行。
6.1.2 箱体结构内壁及装有扶梯的箱形体和桶体内部(1)快干型环氧磷酸锌漆Penguard Express ZP干膜厚度:150μm;稀释剂:佐敦17号稀释剂;参考稀释比例:0~5%;混合比:PartA:PartB=4:1(体积比)a.用动力搅拌器充分搅拌基料(PartA),边搅拌边加入固化剂(PartB),继续用动力搅拌器充分搅拌(可适当加入佐敦17号稀释剂),搅拌均匀后待用。
喷涂时,油漆桶内用机械或动力缓慢搅拌,边喷涂边搅拌,直至用完。
b.混合使用寿命(23℃):2小时(随温度升高而缩短)。
c.喷涂实施前对过焊孔、自由边、阴角处等不易喷涂部位进行预涂。
d.主要喷涂方式:高压无气喷涂,喷嘴孔径0.46~0.69mm,喷嘴压力15MPa。
e.环境要求:相对湿度在85%以下,钢板温度不可低于零下5℃并且大于露点温度3℃以上。