炼钢对石灰的要求
冶金石灰标准

冶金石灰标准冶金石灰是冶金工业中常用的一种原材料,其质量标准对于冶金生产过程中的效果和产品质量有着重要的影响。
本文将对冶金石灰的标准进行详细介绍,以便于相关行业人士更好地了解和应用。
一、外观要求。
冶金石灰应呈白色或微黄色,无明显杂质和机械杂质,外观应均匀细腻,无结块和结晶。
二、化学成分。
1. 钙氧化物含量不低于90%,镁氧化物含量不超过1.5%。
2. 有效碱度不低于85%,活性钙含量不低于75%。
3. 硫分含量不超过0.1%,氧化铁含量不超过0.5%。
三、物理性能。
1. 石灰石含量不超过5%。
2. 灰分含量不超过3%。
3. 粒度分布,通过60目筛的物料不应低于95%,通过200目筛的物料不应高于10%。
四、石灰质量控制。
1. 采用石灰石为原料生产的冶金石灰,应符合国家标准GB/T 3280的要求。
2. 采用石灰石和石灰为原料生产的冶金石灰,应符合国家标准GB/T 3281的要求。
五、包装与贮存。
1. 冶金石灰应采用防潮、防雨、防晒的包装材料包装,包装应完好无损,标识清晰。
2. 冶金石灰应存放在干燥通风的库房内,远离酸碱物质,防潮防雨。
六、质量检验。
1. 对冶金石灰的质量应进行定期检验,检验项目包括外观、化学成分、物理性能等。
2. 检验应由具备相应资质的检测机构进行,检测结果应符合国家标准要求。
七、质量控制。
1. 冶金石灰生产企业应建立健全的质量管理体系,制定严格的质量控制标准和流程。
2. 对原材料、生产过程和成品进行全程监控,确保产品质量稳定可靠。
八、应用范围。
冶金石灰主要用于冶金工业中的炼铁、炼钢等生产过程中,可用于熔炼矿石、去除硫等。
以上就是冶金石灰的标准要求,希望可以对相关行业人士有所帮助。
冶金石灰的质量对于冶金生产过程中的效果和产品质量有着重要的影响,因此在生产和应用过程中应严格按照标准要求进行操作,确保产品质量和生产效果。
钙质消石灰一级二级三级石灰标准

钙质消石灰一级二级三级石灰标准钙质消石灰是指含有不少于90%的氧化钙和不超过8%的氢氧化钙的石灰。
按照国家标准,钙质消石灰分为一级、二级和三级三种标准。
本文将从不同级别的钙质消石灰的特点、用途和生产工艺等方面进行探讨。
一级钙质消石灰是指含有氧化钙不少于90%、氢氧化钙不超过8%的石灰。
它的特点是纯净,质量稳定,用途广泛。
一级钙质消石灰广泛用于建筑材料、冶金、化工、环保等行业。
在建筑材料行业,一级钙质消石灰常用于生产砌筑砂浆、混凝土、石灰砂浆和石膏制品等;在冶金行业,一级钙质消石灰则用于炼钢、炼铁、镁 metal 和镁合金的生产过程中;在化工领域,一级钙质消石灰主要用于生产氢氧化钙、氯化钙、石灰氯化钙和石灰氯化镁等;在环保方面,一级钙质消石灰则被用于烟气脱硫、废水处理等。
二级钙质消石灰是指含有氧化钙不少于80%、氢氧化钙不超过10%的石灰。
它的特点是价格较低,适用于一些对石灰纯度要求不高的行业。
在建筑材料行业,二级钙质消石灰主要用于生产石灰沙和石灰石材等;在冶金行业,二级钙质消石灰通常用于石灰焙烧;在环保领域,二级钙质消石灰则用于烟气处理、工业废水处理等。
三级钙质消石灰是指含有氧化钙不少于70%、氢氧化钙不超过15%的石灰。
它的特点是价格低廉,但纯度较低,适用范围较窄。
在建筑材料领域,三级钙质消石灰主要用于生产石灰砂浆;在冶金行业,三级钙质消石灰通常用于石灰焙烧和矿石浮选;在环保方面,三级钙质消石灰则用于废水处理、烟气处理等。
从生产工艺来看,不同级别的钙质消石灰在生产过程中需要进行不同程度的石灰石的焙烧、消石灰的石灰化、粉碎、筛分等工艺。
一级钙质消石灰的生产工艺要求较高,需要采用先进的设备和技术,以确保产品的质量和稳定性;而二级和三级钙质消石灰的生产工艺相对简单,成本较低。
不同级别的钙质消石灰在用途、特点、价格和生产工艺等方面都有所区别,但它们都在各自的领域发挥着重要的作用。
随着工业的不断发展和技术的不断进步,钙质消石灰的应用领域也将不断扩大,为各行各业的发展提供稳定可靠的原材料保障。
炼钢金属原料的种类及对铁水、废钢、铁合金的要求

【本章学习要点】本章学习炼钢金属原料的种类及对铁水、废钢、铁合金的要求,常用的铁合金的作用,非金属料的种类、作用及其要求。
原材料的质量和供应条件直接影响炼钢的技术经济指标。
保证原材料的质量,既指保证原材料化学成分和物理性质满足技术要求,还指原材料化学成分和物理性质保持稳定,这是达到优质、高产、低耗的前提条件。
炼钢原材料可分为金属料和非金属料两大类。
第一节金属料炼钢用的金属料主要有铁水、废钢、生铁、原料纯铁、海绵铁、中间合金材料和铁合金。
一、铁水铁水是转炉炼钢最主要的金属料,一般占转炉金属料70%以上。
铁水的成分、温度是否适当和稳定,对简化、稳定转炉操作,保证冶炼顺行以及获得良好的技术经济指标都十分重要。
转炉炼钢对铁水有如下要求:1)温度:温度是铁水带入炉内物理热多少的标志,是转炉炼钢热量的重要来源之一。
铁水温度过低,将造成炉内热量不足,影响熔池升温和元素的氧化过程,不利于化渣和去除杂质,还容易导致喷溅。
一般要求入炉铁水温度不低于l250℃,而且要稳定。
2) 硅:铁水中硅的氧化能放出大量的热量,生成的Si02是渣中主要的酸性成分,是影响熔渣碱度和石灰消耗量的关键因素。
铁水含硅高,则转炉可以多加废钢、矿石,提高钢水收得率,但铁水含硅量过高,会因石灰消耗量的增大而使渣量过大,易产生喷溅并加剧对炉衬的侵蚀,影响石灰熔化,从而影响脱磷、脱硫。
如果铁水含硅量过低,则不易成渣,对脱磷、脱硫也不利。
因此,要求铁水含硅质量分数在0.2%~0.6%。
3)锰:锰是钢中有益元素,对化渣、脱硫以及提高炉龄都是有益的。
但冶炼高锰生铁将使高炉焦比升高,为了节约锰矿资源和降低炼铁焦比,一般采用低锰铁水,锰质量分数为0.2%~0.4%。
4)磷:磷是一个强发热元素。
一般讲磷是有害元素,但高炉冶炼中无法去除磷。
因此,只能要求进入转炉的铁水含磷量尽量稳定,且铁水含磷越低越好。
5)硫:硫也是有害元素。
炼钢过程虽然可以去硫,但会降低炉子生产率,增加原材料消耗。
首钢长治钢铁有限公司企业标准
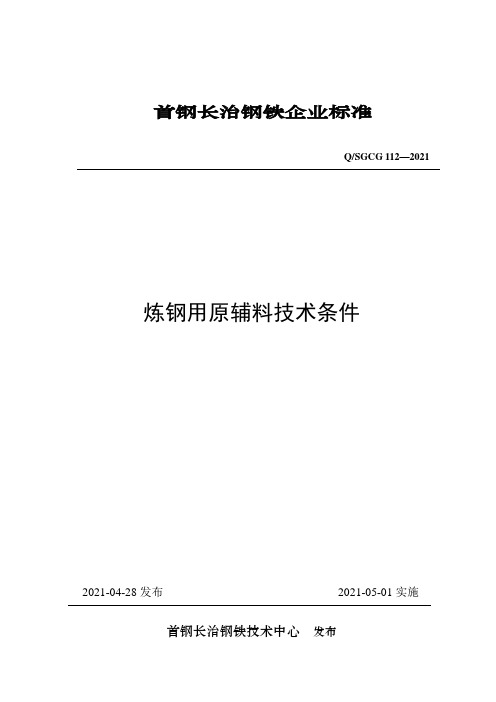
首钢长治钢铁企业标准Q/SGCG 112—2021 炼钢用原辅料技术条件2021-04-28发布2021-05-01实施首钢长治钢铁技术中心发布Q/SGCG112—2021炼钢用原辅料技术条件1 范围本标准规定了炼钢用原辅料的技术要求、退货技术要求、试验方法、检验规那么等。
本标准适用于炼钢用原辅料。
2 引用标准GB4223 废钢铁YB/T5217 萤石YB/T5279 石灰石YB/T5278 白云石YB/T042 冶金石灰3 技术要求3.1 废钢铁3.1.1 供炼钢用废钢:单重≤500kg,边长≤700mm,其中重型废钢厚度≥10mm;中型废钢厚度≥6mm;统料废钢厚度≥2mm〔其中4 mm≤厚度<6mm为优质统料废钢〕。
特殊品种用废钢Ni、Cr、Cu、Mo 含量不大于0.30%〔公司内部回收的废钢除外,但需分类管理〕。
其他执行GB4223-2004。
3.1.2调温废钢:3.1.2.1 选用自产废钢,成份要求如下:.2.2 形状及尺寸应满足调温需要。
3.2 炼钢用副原料3.2.1 炼钢用铁矿石:TFe≥60%,SiO2≤6%,H2O≤2%,S≤50%,粒度10~50mm,<10mm和>50mm比例之和不大于10%。
炼钢用烧结矿:TFe≥55%,SiO2≤6%,H2O≤2%,粒度10~50mm,<10mm和>50mm比例之和不大于10%。
3炼钢用球团矿:TFe≥63%,SiO2≤8%,H2O≤2%,粒度8~16mm,<8mm和>16mm比例之和不大于10%。
炼钢用冷固球团:3.2.4.1化学成分〔%〕:TFe≥50% ,SiO2 ≤%,S≤0.25%,FeO≥20% ,P≤0.040%,CaO≥10.0% ,MgO≥4.0%。
P、CaO、MgO根据用户需要随机抽查。
3.2.4.2粒度尺寸:长30mm,宽20mm,厚20mm,形状为椭圆球形,<5mm的粉末率≯5%。
3.2.4.3抗压强度≥800N/个球。
转炉炼钢知识问答
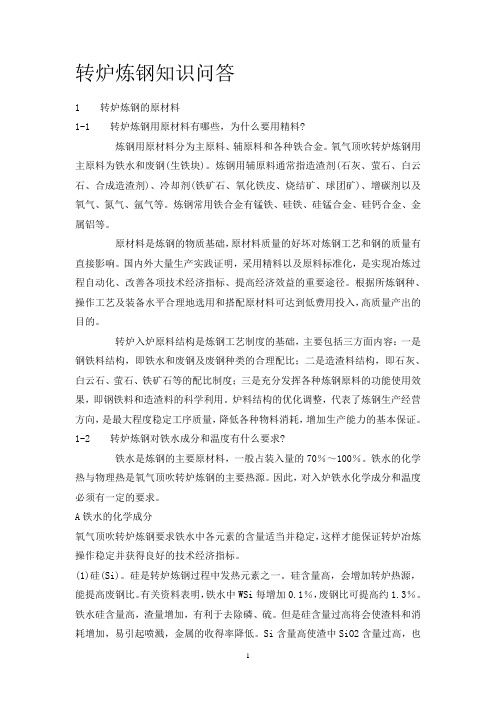
转炉炼钢知识问答1 转炉炼钢的原材料1-1 转炉炼钢用原材料有哪些,为什么要用精料?炼钢用原材料分为主原料、辅原料和各种铁合金。
氧气顶吹转炉炼钢用主原料为铁水和废钢(生铁块)。
炼钢用辅原料通常指造渣剂(石灰、萤石、白云石、合成造渣剂)、冷却剂(铁矿石、氧化铁皮、烧结矿、球团矿)、增碳剂以及氧气、氮气、氩气等。
炼钢常用铁合金有锰铁、硅铁、硅锰合金、硅钙合金、金属铝等。
原材料是炼钢的物质基础,原材料质量的好坏对炼钢工艺和钢的质量有直接影响。
国内外大量生产实践证明,采用精料以及原料标准化,是实现冶炼过程自动化、改善各项技术经济指标、提高经济效益的重要途径。
根据所炼钢种、操作工艺及装备水平合理地选用和搭配原材料可达到低费用投入,高质量产出的目的。
转炉入炉原料结构是炼钢工艺制度的基础,主要包括三方面内容:一是钢铁料结构,即铁水和废钢及废钢种类的合理配比;二是造渣料结构,即石灰、白云石、萤石、铁矿石等的配比制度;三是充分发挥各种炼钢原料的功能使用效果,即钢铁料和造渣料的科学利用。
炉料结构的优化调整,代表了炼钢生产经营方向,是最大程度稳定工序质量,降低各种物料消耗,增加生产能力的基本保证。
1-2 转炉炼钢对铁水成分和温度有什么要求?铁水是炼钢的主要原材料,一般占装入量的70%~100%。
铁水的化学热与物理热是氧气顶吹转炉炼钢的主要热源。
因此,对入炉铁水化学成分和温度必须有一定的要求。
A铁水的化学成分氧气顶吹转炉炼钢要求铁水中各元素的含量适当并稳定,这样才能保证转炉冶炼操作稳定并获得良好的技术经济指标。
(1)硅(Si)。
硅是转炉炼钢过程中发热元素之一。
硅含量高,会增加转炉热源,能提高废钢比。
有关资料表明,铁水中WSi每增加0.1%,废钢比可提高约1.3%。
铁水硅含量高,渣量增加,有利于去除磷、硫。
但是硅含量过高将会使渣料和消耗增加,易引起喷溅,金属的收得率降低。
Si含量高使渣中SiO2含量过高,也会加剧对炉衬的冲蚀,并影响石灰渣化速度,延长吹炼时间。
炼钢生产工艺考试题

4.常用脱氧元素的脱氧能力由弱→强的顺序 是: A. Si→Mn→Ca→Al B. Ca→Si→Mn→Al C.Mn→ Si→ Al→ Ca 5. 转炉冶炼过程炉渣中MgO的来源是: A.铁水、废钢 B.加入的石灰 C.加 入的白云石 D.炉衬耐火材料 6.转炉内衬耐火材料广泛采用 • A.镁铬质 B.白云石质 C.镁碳质 7.在转炉内衬损坏的各种原因中,高温下的 对炉衬危害最大。
ቤተ መጻሕፍቲ ባይዱ
• 三、判断题:(错画“×”,对画“√”, 每题1分,共15分) • 1.活性石灰特点是氧化钙含量高、气孔率高、 活性度小于300ml。 ( ) • 2.炉渣的来源是由石灰、白云石和萤石等造 渣材料熔化组合而成。 ( ) • 3.合金加入顺序:合金化的合金元素先加, 脱氧用的合金元素后加。 ( ) • 4.铁水中硅含量过高,会使石灰加入过多, 渣量大,对去磷无影响。 ( ) • 5.双渣法是指吹炼过程中到出或扒出部分炉 渣,再重新加石灰造渣。 ( )
• 四、选择题:(每题1分,共15分) 1.转炉炼钢的主要金属料是指( )。 • A.铁水、氧化铁皮、矿石 B.铁水、铁 合金、脱氧剂 C.铁水、废钢 2. 挡渣出钢的作用是 。 • A.防止回磷 B提高钢水纯净度 C..提 高合金吸收率 D提高出钢口寿命 3. 当转炉炼钢终点碳高、温度高时,可加 调温。 • A.矿石 B.白云石 C.废钢 D.石灰石
• 五、问答题:(每题6分,共30分) 1. 什么是活性石灰,使用活性石灰有什么好 处? 2. 炼钢的基本任务是什么? 3.单渣法与双渣法有何区别? 4.若终点[C] 和温度在钢种的上限值,而终点 [P]高于目标值,该如何操作? 5.碳氧反应在炼钢过程中有哪些作用? 6.炼一炉钢分为哪几期,各期的主要任务是 什么? 7.什么是溅渣护炉技术? 8.什么是炉渣返干现象?
转炉炼钢题库
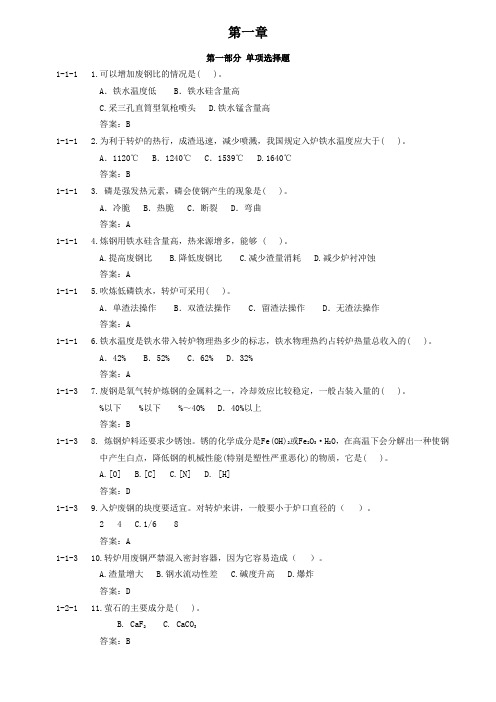
第一章第一部分单项选择题1-1-1 1.可以增加废钢比的情况是( )。
A.铁水温度低 B.铁水硅含量高C.采三孔直筒型氧枪喷头D.铁水锰含量高答案:B1-1-1 2.为利于转炉的热行,成渣迅速,减少喷溅,我国规定入炉铁水温度应大于( )。
A.1120℃ B.1240℃ C.1539℃ D.1640℃答案:B1-1-1 3. 磷是强发热元素,磷会使钢产生的现象是( )。
A.冷脆 B.热脆 C.断裂 D.弯曲答案:A1-1-1 4.炼钢用铁水硅含量高,热来源增多,能够 ( )。
A.提高废钢比B.降低废钢比C.减少渣量消耗D.减少炉衬冲蚀答案:A1-1-1 5.吹炼低磷铁水,转炉可采用( )。
A.单渣法操作 B.双渣法操作 C.留渣法操作 D.无渣法操作答案:A1-1-1 6.铁水温度是铁水带入转炉物理热多少的标志,铁水物理热约占转炉热量总收入的( )。
A.42% B.52% C.62% D.32%答案:A1-1-3 7.废钢是氧气转炉炼钢的金属料之一,冷却效应比较稳定,一般占装入量的( )。
%以下 %以下 %~40% D.40%以上答案:B1-1-3 8. 炼钢炉料还要求少锈蚀。
锈的化学成分是Fe(OH)2或Fe2O3·H2O,在高温下会分解出一种使钢中产生白点,降低钢的机械性能(特别是塑性严重恶化)的物质,它是( )。
A.[O]B.[C]C.[N]D. [H]答案:D1-1-3 9.入炉废钢的块度要适宜。
对转炉来讲,一般要小于炉口直径的()。
2 4 C.1/6 8答案:A1-1-3 10.转炉用废钢严禁混入密封容器,因为它容易造成()。
A.渣量增大B.钢水流动性差C.碱度升高D.爆炸答案:D1-2-1 11.萤石的主要成分是( )。
B. CaF2C. CaCO3答案:B1-2-1 12.我国石灰活性度的测定采用()。
A.盐酸滴定法B.温升法法 D.煅烧法答案:A1-3-2 13.合金加入顺序按脱氧能力强弱来安排,常用脱氧剂加入顺序为( )。
石灰石在炼钢中的作用
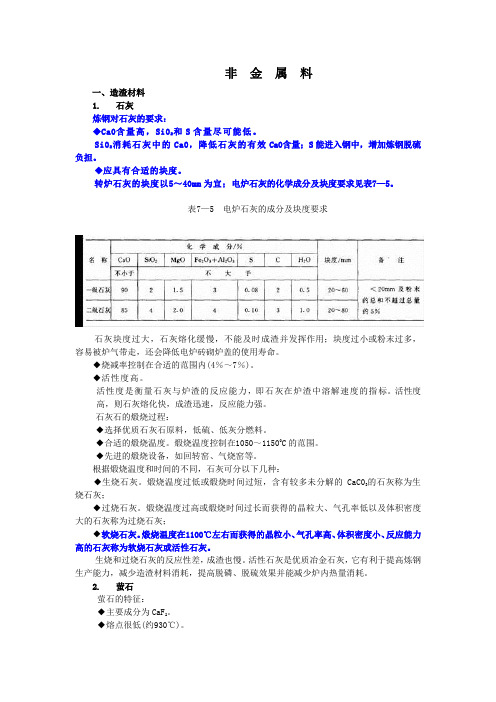
非金属料一、造渣材料1.石灰炼钢对石灰的要求:◆Ca0含量高,Si02和S含量尽可能低。
Si02消耗石灰中的Ca0,降低石灰的有效Ca0含量;S能进入钢中,增加炼钢脱硫负担。
◆应具有合适的块度。
转炉石灰的块度以5~40mm为宜;电炉石灰的化学成分及块度要求见表7—5。
表7—5 电炉石灰的成分及块度要求石灰块度过大,石灰熔化缓慢,不能及时成渣并发挥作用;块度过小或粉末过多,容易被炉气带走,还会降低电炉砖砌炉盖的使用寿命。
◆烧减率控制在合适的范围内(4%~7%)。
◆活性度高。
活性度是衡量石灰与炉渣的反应能力,即石灰在炉渣中溶解速度的指标。
活性度高,则石灰熔化快,成渣迅速,反应能力强。
石灰石的煅烧过程:◆选择优质石灰石原料,低硫、低灰分燃料。
◆合适的煅烧温度。
煅烧温度控制在1050~11500C的范围。
◆先进的煅烧设备,如回转窑、气烧窑等。
根据煅烧温度和时间的不同,石灰可分以下几种:◆生烧石灰。
煅烧温度过低或煅烧时间过短,含有较多未分解的CaC03的石灰称为生烧石灰;◆过烧石灰。
煅烧温度过高或煅烧时间过长而获得的晶粒大、气孔率低以及体积密度大的石灰称为过烧石灰;◆软烧石灰。
煅烧温度在1100℃左右而获得的晶粒小、气孔率高、体积密度小、反应能力高的石灰称为软烧石灰或活性石灰。
生烧和过烧石灰的反应性差,成渣也慢。
活性石灰是优质冶金石灰,它有利于提高炼钢生产能力,减少造渣材料消耗,提高脱磷、脱硫效果并能减少炉内热量消耗。
2.萤石萤石的特征:◆主要成分为CaF2。
◆熔点很低(约930℃)。
◆改善碱性熔渣流动性且又不降低碱度的稀释剂,又称助熔造渣剂。
◆增强渣钢间的界面反应能力。
◆大量使用萤石会增加转炉喷溅,加剧对炉衬的侵蚀。
炼钢使用的萤石要求:◆CaF2的含量越高越好,而Si02的含量要适当,其他杂质如S、Fe等含量要尽量低。
◆块度要合适,并且干燥清洁。
冶炼优质钢用的萤石使用前要在60~100℃低温下烘烤8h以上。
石灰石炼钢工艺流程

石灰石炼钢工艺流程下载温馨提示:该文档是我店铺精心编制而成,希望大家下载以后,能够帮助大家解决实际的问题。
文档下载后可定制随意修改,请根据实际需要进行相应的调整和使用,谢谢!并且,本店铺为大家提供各种各样类型的实用资料,如教育随笔、日记赏析、句子摘抄、古诗大全、经典美文、话题作文、工作总结、词语解析、文案摘录、其他资料等等,如想了解不同资料格式和写法,敬请关注!Download tips: This document is carefully compiled by the editor. I hope that after you download them, they can help you solve practical problems. The document can be customized and modified after downloading, please adjust and use it according to actual needs, thank you!In addition, our shop provides you with various types of practical materials, such as educational essays, diary appreciation, sentence excerpts, ancient poems, classic articles, topic composition, work summary, word parsing, copy excerpts, other materials and so on, want to know different data formats and writing methods, please pay attention!石灰石是一种常见的矿石,其在炼钢工艺中扮演着重要的角色。
炼钢试题
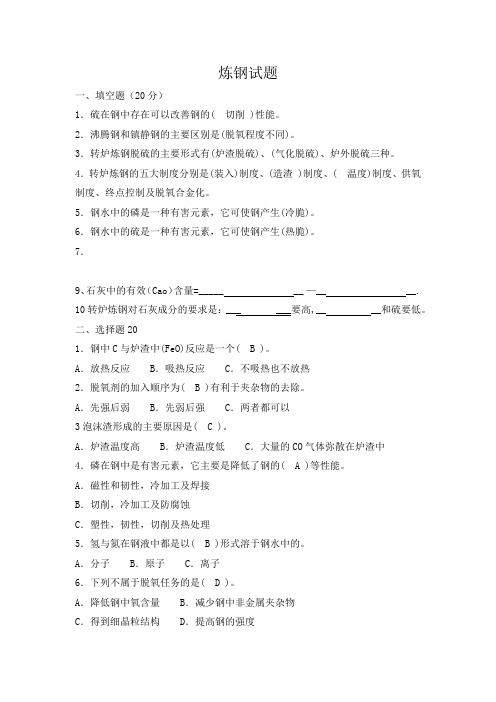
炼钢试题一、填空题(20分)1.硫在钢中存在可以改善钢的( 切削 )性能。
2.沸腾钢和镇静钢的主要区别是(脱氧程度不同)。
3.转炉炼钢脱硫的主要形式有(炉渣脱硫)、(气化脱硫)、炉外脱硫三种。
4.转炉炼钢的五大制度分别是(装入)制度、(造渣 )制度、( 温度)制度、供氧制度、终点控制及脱氧合金化。
5.钢水中的磷是一种有害元素,它可使钢产生(冷脆)。
6.钢水中的硫是一种有害元素,它可使钢产生(热脆)。
7.9、石灰中的有效(Cao)含量=_____ __ —__ __. 10转炉炼钢对石灰成分的要求是:___ ___要高,__ __和硫要低。
二、选择题201.钢中C与炉渣中(FeO)反应是一个( B )。
A.放热反应 B.吸热反应 C.不吸热也不放热2.脱氧剂的加入顺序为( B )有利于夹杂物的去除。
A.先强后弱 B.先弱后强 C.两者都可以3泡沫渣形成的主要原因是( C )。
A.炉渣温度高 B.炉渣温度低 C.大量的CO气体弥散在炉渣中4.磷在钢中是有害元素,它主要是降低了钢的( A )等性能。
A.磁性和韧性,冷加工及焊接B.切削,冷加工及防腐蚀C.塑性,韧性,切削及热处理5.氢与氮在钢液中都是以( B )形式溶于钢水中的。
A.分子 B.原子 C.离子6.下列不属于脱氧任务的是( D )。
A.降低钢中氧含量 B.减少钢中非金属夹杂物C.得到细晶粒结构 D.提高钢的强度7.钢中内生夹杂的产生主要来源于( B )A.炉衬及钢包耐火材料侵蚀夹杂物B.冶炼过程中元素被氧化及脱氧时形成的氧化物C.炉料内在夹杂物8、一般情况下,脱磷主要在冶炼( A )进行。
A.前期B.中期C.后期9、炉渣( )中含量对脱硫有利A.二氧化硅(SiO2)B.三氧化二铝(Al2O3)、五氧化二磷(P2O5)、氧化镁(MgO)C.氧化钙(CaO)、氧化锰(MnO)10、在转炉吹炼中,造成炉渣“返干”现象的主要原因是( )。
A渣料量大B供氧量大于碳氧反应所耗氧量C供氧量小于碳氧反应所耗氧量三、判断题101、硅是转炉炼钢过程中发热元素之一。
氧化钙在冶金领域的应用

氧化钙在冶金领域的应用冶金氧化钙(石灰)主要用于,钢厂,不锈钢厂,炉料厂等。
规格有;转炉小块。
高炉大块。
烧结生石灰粉。
一般要求粉灰氧化钙78%以上。
一般钢厂块灰83以上。
特钢和不锈钢等要求85以上。
含硅,含硫。
含镁。
烧失量都要低。
活性度280-320之间。
(凤阳明帝)氧化钙在冶金领域的应用:1、生产脱硫吸收剂。
石灰石破碎到0 ~2mm ,其中+ 2 mm < 5 %、0~0. 45 mm > 50 %的粉状代替原石灰或消石灰,在吸收塔内与水混合搅拌成浆液,吸收浆液与烟气接触混合,烟气中的二氧化硫与浆液中的碳酸钙以及鼓入的空气进行化学反应被脱除,最终反应产物为石膏。
脱硫后的生石灰烟气经加热升温后排入烟囱。
2、生产高档造纸用涂布级重质碳酸钙产品。
这类高附加值的微细、超细及活性重质碳酸钙在造纸工艺中应用十分广泛,粉碎后一般粒径- 2μm ≥90 %的用于中性施胶造纸工艺; - 2μm 粒径≥50 %的主要用于涂布纸的填料。
3、生产焦炉煤气:每生产1t焦炭约产生300m3焦炉煤气。
焦炉煤气煤气热值约为16750KJ/m3 焦炉煤气成分主要有5种,体积含量为:H2+CH4+CO+CO2+N2=(50%~58%)+(22%~25%)+CO+CO2+N2 注意,焦炉煤气中含有大量粉尘、焦油、硫等杂质,对石灰生产不利,必须经过脱除焦油、脱硫等净化工序后,得到的净煤气才能用于焙烧石灰。
4、生产高炉煤气:每生产1t铁约产生2000m3高炉煤气。
高炉煤气煤气热值约为3768~4187KJ/m3,冶炼炼钢生铁时发热值较低,冶炼特殊生铁时发热值较高(419~628KJ/m3)高炉煤气成分主要有5种,体积含量为:CO+H2+N2+CO2+CH4=(25%~30%)+(2%~4%)+(55%~58%)+(13%~16 %)+CH4注意,根据有关资料,当空气中的CO浓度超过16mg/L时,即有中毒危险。
高炉煤气中含有大量的CO,应严防漏气,避免CO中毒事故。
铸造炼钢造渣材料(精)
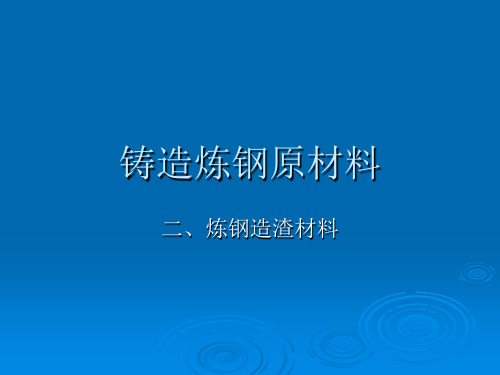
电石块的要求
放在密封的容器内保存,在使用前需经高
温烘烤。
石灰
活性度高。活性度是衡量石灰与炉渣的反
应能力,即石灰在炉渣中溶解速度的指标。 活性度高,则石灰熔化快,成渣迅速,反 应能力强。 电炉石灰的化学成分及块度要求见下表。
石灰成分及块度要求
萤石
主要成分为CaF2。 熔点很低(约930℃)。 改善碱性熔渣流动性且又不降低碱度的稀 释剂,又称助熔造渣剂。 增强渣钢间的界面反应能力。 大量使用萤石会增加转炉喷溅,加剧对炉 衬的侵蚀。
硅石与石英砂
硅石与石英砂的特征: 主要成分是Si02。 是酸性炉炼钢的主要造渣材料。 在碱性电炉炼钢过程中,硅石和石英砂主 要用于还原期调整中性渣的成分。 在碱性炉中,大量加入硅石和石英砂,易 造成炉衬渣线侵蚀严重。
炼钢用硅石的要求
Si02含量在90%以上,FeO<0.5%,并要
求表面清洁,块度一般为15~50mm,使用 前须在100~200℃温度下干燥4h。 炼钢用石英砂的要求: Si02含量大于95%,FeO<0.5%,水分小 于0.5%,粒度一般为1~3mm,使用前应 在400℃左右的温度下进行长时间的烘烤。
电石块
电石块的特征: 主要成分为CaC2,是由石灰和焦炭在高温下炼制 的暗灰色不规则的块状固体。 纯CaC2的熔点高达2300℃,但CaC2与Ca0的共 晶温度为1640℃,工业上所用的电石块的熔点约 为1620℃。 在电炉钢的冶炼过程中,电石块常用作造还原渣, 并兼有脱硫作用。 电石块遇水即发热分解放出乙炔气体,具有难闻 气味,与火焰接触即可燃烧,温度可达3000℃, 又常用于金属切割。
铸造炼可少的一环。
炼钢要使得钢中的杂质降低,这些杂质被 分离出来后进入熔渣,因为熔渣比重轻, 飘浮在钢水上面,就比较容易除去。 另外熔渣还可以保护钢水不和大气直接接 触。 造渣就是在炼钢过程中加入称为造渣剂的 炼钢物质,比如氟化钙或氧化钙等,以便 形成炉渣。
生烧石灰、轻烧石灰、过烧石灰的鉴别与理化指标以及对转炉生产的影响

生烧石灰、轻烧石灰、过烧石灰的鉴别与理化指标以及对转炉生产的影响摘要:活性石灰在现代转炉炼钢过程中发挥着极其重要的作用,主要用作造渣材料。
随着对钢产品质量及产量要求的不断提高以及对炼钢成本的不断控制,对活性石灰的质量要求也在不断提高。
本文将主要介绍不同品质活性石灰的质量鉴别与理化指标以及对转炉生产的影响。
关键词:活性石灰质量鉴别理化指标转炉生产1前言活性石灰的质量对转炉生产有着极大的影响,他直接关系到转炉炼钢脱磷、脱硫以及造渣的效率。
采用优质的活性石灰可加快造渣速度、缩短冶炼周期、提高钢水收得率、净化钢水质量、保护炉衬等。
作为钢铁企业质量管理人员,我们更需要采用科学合理的质量控制手段为转炉炼钢把好活性石灰质量关。
2问题的提出活性石灰(主要成分是CaO)是在回转窑或竖窑中通过煅烧石灰石(主要成分是CaCO3)而成,该过程是复杂的物理及化学变化过程,加热到一定温度后发生如下反应:CaCO3(s)= CaO (s) +CO2(g)目前炼钢转炉生产中需要的是优质的轻烧石灰,但由于活性石灰生产过程中受地域资源、石灰石粒度、燃料供给、工艺控制等诸多因素的影响,不能完全保证能生产出优质的轻烧石灰,如果在转炉中加入生烧石灰或过烧石灰,则会极大的影响钢水的品质,还会增加金属料耗,为了能快速的鉴别活性石灰的质量、杜绝不合格活性石灰被加入转炉,同时为转炉精细化控制提供参考,我们提出对活性石灰的质量鉴别方法及理化指标进行讨论。
3活性石灰质量的鉴别3.1 生烧石灰3.1.1 生烧石灰的产生原因(1)石灰石粒度过大:在一定温度下,随着煅烧的进行,石灰层的厚度逐渐增加,热量难以进入石灰石内部,所以煅烧结束后石灰块中间存有石灰石夹心。
(2)燃料热值低或燃料比例小:目前国内煅烧石灰主要以焦炭作为燃料,若焦炭热值低或用料比例小甚至焦炭粒度不合理,都有可能造成煅烧温度达不到要求或温度不均匀,继而造成石灰的生烧。
(3)供风不合理:合理的供风量及供风压力,再加上科学的窑内结构,这些条件直接决定了窑内气流的分布,气流分布不合理会使燃料在窑腔内的燃烧不均匀,燃料释放的热量就会不均匀,最终温度低的地方出现生烧。
炼钢金属原料的种类及对铁水、废钢、铁合金的要求

【本章学习要点】本章学习炼钢金属原料的种类及对铁水、废钢、铁合金的要求,常用的铁合金的作用,非金属料的种类、作用及其要求。
原材料的质量和供应条件直接影响炼钢的技术经济指标。
保证原材料的质量,既指保证原材料化学成分和物理性质满足技术要求,还指原材料化学成分和物理性质保持稳定,这是达到优质、高产、低耗的前提条件。
炼钢原材料可分为金属料和非金属料两大类。
第一节金属料炼钢用的金属料主要有铁水、废钢、生铁、原料纯铁、海绵铁、中间合金材料和铁合金。
一、铁水铁水是转炉炼钢最主要的金属料,一般占转炉金属料70%以上。
铁水的成分、温度是否适当和稳定,对简化、稳定转炉操作,保证冶炼顺行以及获得良好的技术经济指标都十分重要。
转炉炼钢对铁水有如下要求:1)温度:温度是铁水带入炉内物理热多少的标志,是转炉炼钢热量的重要来源之一。
铁水温度过低,将造成炉内热量不足,影响熔池升温和元素的氧化过程,不利于化渣和去除杂质,还容易导致喷溅。
一般要求入炉铁水温度不低于l250℃,而且要稳定。
是渣中主要的酸性成分,是影 2)硅:铁水中硅的氧化能放出大量的热量,生成的Si02响熔渣碱度和石灰消耗量的关键因素。
铁水含硅高,则转炉可以多加废钢、矿石,提高钢水收得率,但铁水含硅量过高,会因石灰消耗量的增大而使渣量过大,易产生喷溅并加剧对炉衬的侵蚀,影响石灰熔化,从而影响脱磷、脱硫。
如果铁水含硅量过低,则不易成渣,对脱磷、脱硫也不利。
因此,要求铁水含硅质量分数在0.2%~0.6%。
3)锰:锰是钢中有益元素,对化渣、脱硫以及提高炉龄都是有益的。
但冶炼高锰生铁将使高炉焦比升高,为了节约锰矿资源和降低炼铁焦比,一般采用低锰铁水,锰质量分数为0.2%~0.4%。
4)磷:磷是一个强发热元素。
一般讲磷是有害元素,但高炉冶炼中无法去除磷。
因此,只能要求进入转炉的铁水含磷量尽量稳定,且铁水含磷越低越好。
5)硫:硫也是有害元素。
炼钢过程虽然可以去硫,但会降低炉子生产率,增加原材料消耗。
技能认证炼钢工知识考试(习题卷43)
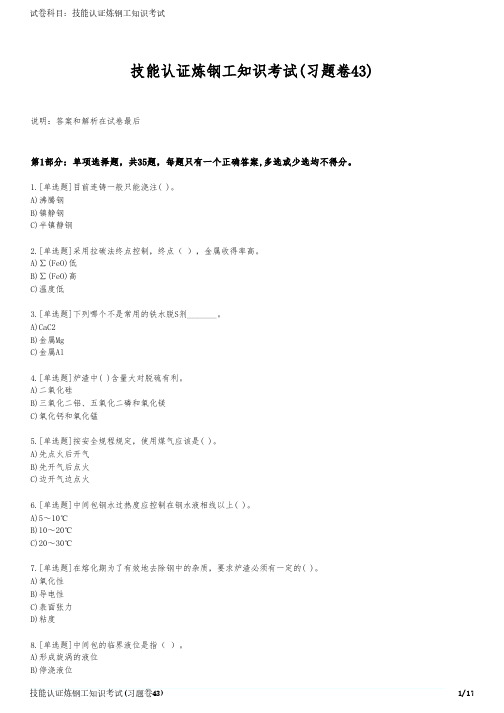
技能认证炼钢工知识考试(习题卷43)说明:答案和解析在试卷最后第1部分:单项选择题,共35题,每题只有一个正确答案,多选或少选均不得分。
1.[单选题]目前连铸一般只能浇注( )。
A)沸腾钢B)镇静钢C)半镇静钢2.[单选题]采用拉碳法终点控制,终点( ),金属收得率高。
A)∑(FeO)低B)∑(FeO)高C)温度低3.[单选题]下列哪个不是常用的铁水脱S剂_______。
A)CaC2B)金属MgC)金属Al4.[单选题]炉渣中( )含量大对脱硫有利。
A)二氧化硅B)三氧化二铝、五氧化二磷和氧化镁C)氧化钙和氧化锰5.[单选题]按安全规程规定,使用煤气应该是( )。
A)先点火后开气B)先开气后点火C)边开气边点火6.[单选题]中间包钢水过热度应控制在钢水液相线以上( )。
A)5~10℃B)10~20℃C)20~30℃7.[单选题]在熔化期为了有效地去除钢中的杂质,要求炉渣必须有一定的( )。
A)氧化性B)导电性C)表面张力D)粘度8.[单选题]中间包的临界液位是指( )。
C)溢流液位D)开浇液位9.[单选题][Al]减小,硫的分配系数( )。
A)增大B)减小C)不变D)无法确定10.[单选题]在同样(FeO%)条件下炉渣碱度R=( )左右时,炉渣氧化性最强A)1B)2C)3D)411.[单选题]热焖法钢渣处理装载机在铲渣作业过程中,装载机轮胎容易发生( )现象。
A)燃烧B)爆炸C)冒烟D)熄火12.[单选题]转炉吹炼中期,炉气中CO、CO2体积比大约为( )。
A)4:1B)5:1C)6:1D)7:113.[单选题]石灰中的杂质二氧化硅高时,就需多加( ),增大了渣量,而大量炉渣的熔化和加热就增加了电能的消耗量。
A)萤石B)石灰C)硅铁D)镁砂14.[单选题]氧气作为底气气源时,需要同时输入保护气体,不能作为保护气体使用的是( )。
A)天然气B)N2C)CO2D)丙烷15.[单选题]炉渣的粘度和温度的关系是( )。
造渣材料
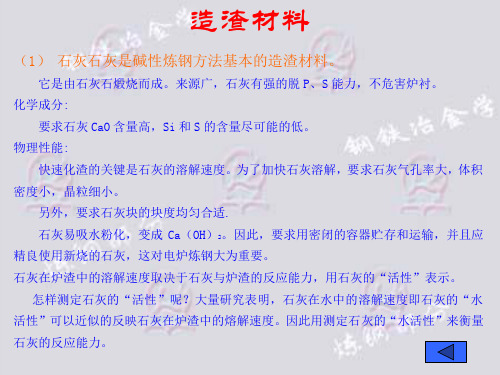
(3)生白云石
近年来, 国外氧气转炉普遍采用白云石等含 MgO 的材 料造渣,增加渣中 MgO 含量,以减少炉衬中 MgO 向炉渣中 转移,且能促进前期化渣。
(4)合成造渣材料
将石灰和熔剂预先在炉外制备成低熔点的造渣材料。 将其加入炉内,必能加速成渣过程,提高炼钢的技术经济 指标,但是由于制备困难,应用还不普遍。 (本节完)
煅烧情况
石灰石主要成分是 CaCO3,其分解温度为 880~910℃。分解反应为: CaCO3→CaO+CO2 石灰石的短少温度和煅烧时间对石灰质量影响很大,因此可见石灰石分为三类:生烧、过 烧、软烧。 a 生烧石灰 煅烧温度过低(<920℃)或煅烧时间过短,石灰含有较多未分解的 CaCO3。 石灰生烧率高,使用时将在炼钢炉内继续完成分解反应,使化渣时间延长;炉子热效率低, 给冶炼操作带来很多不便。生烧率可用灼减表示。石灰的的灼减大,表明生烧率高。应当将灼 减控制在适当范围内(4~7%) 。 b 过烧石灰 煅烧温度过高(>1200℃)或煅烧时间过长,石灰石分解快,CaO 晶粒长大快,晶粒粗大, 气孔率低,体积密度大,反应能力差,不利于快速成渣。 c 软烧石灰(活性石灰) 煅烧温度控制在 1050~1150℃, 获得晶粒细小, 气孔率高 (>40%) ,体积密度小 (约 1.6g/cm ) 反应能力高的石灰的活性石灰,有利于快速成渣。
3
(2)萤石
萤石的主要成分是 CaF2 它的熔点很低(约 930℃) , 是炼钢普遍应用的助熔剂。 萤石化渣的最大优点是:①化渣快,②能迅速降低熔 渣熔点,③稀释炉渣。缺点是:化渣作用不持久。因为在 炼钢温度下渣中的 F 能挥发。另外,大量使用萤石易引起 喷溅,并加剧对炉衬的侵蚀。因此,萤石用量不宜过多, 一般控制在石灰用量的法基本的造渣材料。
石灰石在炼钢中的作用

炼钢厂使用生石灰的作用炼钢主要指的是将生铁炼成钢铁,它是通过一个氧化还原的过程。
因为在炼钢的过程中需要加入熔剂将生铁的硫、磷形成炉渣然后去除,使用石灰是适宜的熔剂。
炼钢厂使用生石灰有效碱一般为主要作用是将化废钢,磷等杂物去除,通过氧化过程,在脱硫的作用形成一个还原条件的。
以上阐述是炼钢厂使用生石灰的作用,由于生石灰在工业上的用途比较广泛,目前作用为脱硫剂还有污水处理剂的较多,所以根据每个行业的需求不同,可要求产品质量的高低。
钢厂石灰石作用农业上的作用:用生石灰配制石灰硫黄合剂,波尔多液等农药。
利用纯净的石灰石粉和氯气反应制得漂白的。
生石灰用作干燥剂和消毒剂。
石灰有生石灰和熟石灰。
石灰与烧碱制成的碱石灰,用作二氧化碳的吸收剂。
纯碱是用石灰石,食盐,氨等原料经过多步反应制得(索尔维法)。
用石灰石粉浆刷树干,可保护树木。
石灰石粉大量用做建筑材料,也是许多工业的重要原料。
利用消石灰和纯碱反应制成烧碱(苛化法)。
炼铁用石灰石作熔剂,除去脉石。
土壤中施用熟石灰可中和土壤的酸性,改善土壤的结构,供给植物所需的钙素。
生石灰吸潮或加水成为消石灰,消石灰也叫熟石灰,它的主要成分是。
熟石灰经调配成石灰浆,石灰膏,石灰砂浆等,用作涂装材料和砖瓦粘合剂。
玻璃由石灰石,等混合,经高温熔融制得。
石灰石烧加工制成较纯的粉状石灰石粉,用做橡胶,塑料,纸张,牙膏,化妆品等的填充料。
电石(主要成分是)是生石灰与焦炭在电炉里反应制得。
水泥是由石灰石和粘土等混合,经高温煅烧制得。
钢厂石灰石作用、石灰石用途、广泛产品市场前景看好、但因为石灰石在中国面广量丰无地方资源优势可言、必须靠实力和其他优势获取市场份额。
因此面对这一资源在开发应用时应慎重选择取短的工序、可能简单的方法现实的市场以低成本、高质量提高市场竞争能力。
综合国内外石灰石产品深加工发展现状介绍我国石灰石矿几种主要用途。
常见的是生产硅酸盐水泥。
一般石灰石经过破碎、磨矿后均能达到水泥原料的要求。
1 炼钢用原材料

1 炼钢用原材料原材料是炼钢的基础,原材料的质量对炼钢工艺和钢的质量有直接影响。
倘若原材料质量不合技术要求,势必导致消耗增加,产品质量变差,有时还会出现废品,造成产品成本的增加。
国内外实践证明,采用精料以及原料标准化,是实现冶炼过程自动化的先决条件,也是改善各项技术经济指标和提高经济效益的基础。
炼钢用原材料一般分为主原料、辅原料和各种铁合金。
1.1 主原料氧气顶吹转炉炼钢用主原料为铁水和废钢。
1.1.1 铁水铁水一般占转炉装入量的70%~100%。
铁水的物理热与化学热是氧气顶吹转炉炼钢的基本热源。
因此,对入炉铁水温度和化学成分必须有一定要求。
1.1.1.1 铁水的温度铁水温度的高低是带入转炉物理热多少的标志,铁水物理热约占转炉热收入的50%。
因此,铁水的温度不能过低,否则热量不足,影响熔池的温升速度和元素氧化过程,也影响化渣和去除杂质,还容易导致喷溅。
我国规定,入炉铁水温度应大于1250℃,以利于转炉的热行,成渣迅速,减少喷溅。
小型转炉和化学热量不富裕的铁水,保证铁水的高温入炉极为重要。
转炉炼钢时入炉铁水的温度还要相对稳定,如果相邻几炉的铁水入炉温度有大幅的变化,就需要在炉与炉之间对废钢比作较大的调整,这对生产管理和冶炼操作都会带来不利影响。
1.1.1.2 铁水的化学成分氧气顶吹转炉能够将各种成分的铁水冶炼成钢,但铁水中各元素的含量适当和稳定,才能保证转炉的正常冶炼和获得良好的技术经济指标,因此力求提供成分适当并稳定的铁水。
表1-1是国家标准规定的炼钢用生铁化学成分,表1-2是我国一些钢厂用铁水成分。
A 硅(Si)硅是炼钢过程的重要发热元素之一,硅含量高,热来源增多,能够提高废钢比。
有关资料认为,铁水中ωsi每增加0.1%,废钢比可提高1.3%。
铁水硅含量视具体情况而定。
例如美国,由于废钢资源多,所以大多数厂家使用的铁水ωsi=0.80%~1.05%。
Si氧化生成的SiO2是炉渣的主要酸性成分。
石灰质量要求

(1)炼钢用石灰质量标准
指标
等级
化学成分(%)
CaO
MgO
SiO2
S
P
备注
铁水脱硫用石灰
≥90
≤5
≤2.0
≤0.03
≤0.01
钝化
转炉用石灰
一级品
≥0
---
二级品
≥90
≤2.0
≤0.030
≤0.010
精炼用石灰
一级品
≥92
≤1.5
≤0.020
≤0.010
---
二级品
≥90
≤2.0
≤0.030
≤0.010
续表
指标
等级
灼减(%)
活性度4N,
40±1℃,10min
粒度(mm)
铁水脱硫用石灰
≤2.0
≥360
0.5~1.5
转炉用石灰
一级品
≤4.0
≥360
20~50
二级品
≤4.0
≥360
精炼用石灰
一级品
≤4.0
≥360
10~30
二级品
≤4.0
≥360
(2)铁水脱硫用萤石粉标准
1、转炉用石灰一级品430元/吨,到山钢运费100元/吨。
2、转炉用石灰二级品410元/吨,到山钢运费100元/吨。
3、铁水脱硫用萤石粉1960元/吨,到山钢运费40元/吨。
指标等级
化学成分(%)
水分
粒度
(mm)
CaF2
SiO2
S
P
铁水脱硫用萤石粉
≥85
≤5.0
≤0.1
≤0.06
≤1.0
0.5~1.5
- 1、下载文档前请自行甄别文档内容的完整性,平台不提供额外的编辑、内容补充、找答案等附加服务。
- 2、"仅部分预览"的文档,不可在线预览部分如存在完整性等问题,可反馈申请退款(可完整预览的文档不适用该条件!)。
- 3、如文档侵犯您的权益,请联系客服反馈,我们会尽快为您处理(人工客服工作时间:9:00-18:30)。
炼钢对石灰的要求石灰按其煅烧程度可分为软烧石灰、中烧石灰和硬烧石灰。
它们之间最明显的区别,表现在活性度上,用4N HCI滴定,软烧石灰一般>300ml;中烧石灰250~300ml之间,硬性石灰一般低于100ml。
它们的消化速度不一样。
一块软烧石灰可以在几秒钟内消化,而硬烧石灰通常需要几小时。
900℃煅烧的石灰溶于水的速度比1200℃生产的硬烧石灰快50倍。
在炼钢过程中,它们对炉渣的反应能力也不一样。
在相同的熔炼条件下,硬烧石灰脱磷和脱硫的能力比软烧石灰差。
随着冶炼技术的发展(LD炼钢法的产生)及某些特殊钢种的要求,在炼钢生产中,要求入炉的石灰在渣中迅速熔解,具有较快的成渣速度,较早地形成高碱度炉渣,因此不光对石灰的化学成份要求更高,而且对石灰的物理性能也要求具有很快的反应能力。
为了满足这种要求,便产生了具有这种特征的石灰——活性石灰。
目前,国内、外转炉炼钢普遍采用活性石灰。
所谓活性石灰,是指体积密度小、气孔率高、表面积大、反应能力强的石灰。
用这种石灰炼钢可以得到较快的成渣速度,提高脱磷和脱硫的效率;同时可以缩短冶炼时间、提高炉龄、降低原材料单耗;从而可以提高钢的质量和产量、降低成本、稳定操作、为冶炼自动化创造良好条件。
石灰对氧气转炉钢过程的影响可见下表。
项目一般石灰活性石灰石灰消耗公斤/吨钢60 50 萤石消耗公斤/吨钢4 2 氧消耗标米3/吨钢51.0 50.0 渣量公斤/吨钢130 115 收得率(%)90 91 渣的性质粘•薄发泡•厚喷溅较频繁少金属喷溅较多较少氧气转炉炼钢对石灰质量的要求可概括如下:(1)主要物理性能:1、粒度:石灰粒度对于造渣时间有很大影响,一般多采用5-40毫米。
粒度大,造渣速度慢;过小,往炉中装料时容易飞散,而且煅烧时燃料中的硫大部分吸附在小颗粒的外壳,影响钢水的质量。
2、活性度:是指与水的反应能力,规定最高升温时间小于10分钟为活性石灰,或在5分钟之内4N H C I耗量>300ml的为活性石灰;要求石灰气孔率应>40%,体积密度应<2克/厘米3。
(2)主要化学性能:1、SiO2低。
CaO与SiO2是配制炉渣碱度的根据,SiO2愈低而CaO愈高愈好。
一般要求SiO2低于1.2%,否则易于在石灰表面形成薄膜,严重妨碍造渣。
2、S、P含量低。
石灰中S、P的会影响钢的质量。
采用LD法炼钢时,石灰中硫含量为0.1%,钢中的硫含量则为0.04%。
石灰中增加0.01%的硫相当于全部炉料中增加0.001%的硫。
活性石灰硫含量一般要求小于0.05%,有的则要求小于0.02%,磷含量也希望在0.05%以下。
3、残留CO2低,灼碱低。
石灰中CO2含量高或CaCO3的含量高,在转炉炼钢过程中热耗也就高,一般CO2应控制在2%以下,但是,残留CO2与活性有关,CO2高一些,活性也好一些,所以残余CO2含量有允许到3%的情况。
灼碱包括石灰中残留CO2,一般要求低于3%。
灼碱不仅和煅烧程度有关,还与贮运设备、方法和气象条件的影响有关。
为了降低灼碱,以保证石灰质量,石灰的生产应在炼钢厂附近进行。
活性石灰的煅烧机理2010-05-28 21:00 活性石灰的煅烧机理活性石灰在氧气转炉炼钢中,其作用是十分重要的。
活性石灰是如何煅烧成的?怎样才能避免硬烧和完全烧结的石灰?这必须从活性石灰的煅烧机理谈起。
活性石灰与硬烧(烧结)石灰的区别,在于其内比表面积大、体积密度稳定。
内比表面积大,主要是CaO的晶粒小(活性石灰单晶粒大小为0.2~0.6微米;硬烧石灰单晶粒在10微米左右),体积密度稳定,就是石灰石在分解过程中,放出约占整个重量40%的CO2后,不使体积发生变化(硬烧石灰其体积密度收缩)。
那么是什么原因能影响比表面积及体积密度呢?实验中发现,CaO小晶体的直径首先取决于煅烧温度的高低及煅烧时间,特别是头几小时的煅烧情况,每一温度下皆标有一定的“最终晶粒度”。
此外人们还断定,这种小晶粒被成比例的窄晶粒带所包围,与CaO小晶粒增长的同时出现体积的收缩,烧成的石灰的体积密度增加。
人们还发现被煅烧的石灰石的纯度、气孔率和矿床影响着石灰的体积密度和气孔率,石灰石含杂质较多的,则经煅烧之后,石灰裂纹收缩可能严重,特别是氧化铁含量高时更是如此;多孔的石灰石,分解之后,当然比致密石灰烧成的体积密度小,气孔率高。
从上述可知,影响石灰的内表面积及体积密度的主要原因是煅烧的温度及煅烧的时间。
而煅烧的温度及煅烧的时间实质又是什么的呢?把石灰煅烧成石灰的过程,就是把石灰石的主要成份碳酸钙(CaCO3)热分解成氧化钙(CaO)和二氧化碳(CO2)的过程。
因此,为了煅烧成石灰——即完成上述反应。
就需要与此相适合的温度和热量。
石灰石中的碳酸钙在矿物学上一般是方解石。
碳酸钙分解温度大约为900oC,但在实际使用时,为了完成上述热分解,由于受到石灰石颗粒内部二氧化碳分压的影响,所以,温度要稍高一些。
对于达到了分解温度的石灰石,必须给予为进一步分解而要吸收的热量(分解热)。
但该分解热在常温标准下,一公斤碳酸钙需要422千卡,在分解温度标准下,一公斤碳酸钙需要396千卡。
想弄清楚煅烧的时间是怎样影响内比表面与体积密度,先要弄清楚块状石灰石分解的规律性。
通过实验发现石灰石的碳酸钙分解速度因其形状而异。
即使是形状基本一定的石灰石,因为粒度不同,其分解速度,即煅烧所需要的时间都有所不同。
当然,上述的论证结果都是煅烧粒度大小基本相同的同一类石灰石,但实际生产中,进入窑炉的石灰石颗粒是大小不一的(有一定比例的选择范围),这种颗粒带的宽度如不根据窑炉进行选择,那么会对石灰的内比表面积及体积密度产生影响。
假设有三种粒度dk1<dk2<dk3,煅烧好的时间分别为t1、t2、t3,它们都不相等,那么,如果以t2温度煅烧,则粒度为kd1的将在窑内出现过烧(硬烧),而dk3则由于煅烧时间不够,会出现欠烧,因此必须按窑型严格地选择颗粒范围进行煅烧,其一定粒度范围的最大和最小之比为2:1,该范围以外的石灰石比例应在10%以内。
石灰的煅烧工艺及其结构对活性度的影响摘要: 以活性石灰为研究对象,用SEM等技术,研究了石灰的煅烧工艺、微观结构与活性度之间的关系,探讨了生产活性石灰的机理及影响石灰活性的因素。
结果表明:石灰石中CaCO3晶体的发育程度以及杂质的含量、煅烧工艺等对石灰的活性有较大的影响。
温度过高或保温时间过长,会使氧化钙晶体发育完好,会使石灰的活性降低。
最佳的煅烧工艺制度为1150℃保温30min。
关键词: 活性石灰; 煅烧工艺; 显微结构随着我国钢铁工业的不断发展,对钢的品种、质量和能耗等都提出了严格的要求。
活性石灰是钢铁生产中的最重要的辅助原料,它是一种优质轻烧石灰,具有粒度较小、反应能力强、冶炼时容易熔解及优良的造渣能力等特点。
其质量直接影响到钢铁生产过程和钢铁质量。
而衡量活性石灰质量的重要指标之一是活性度。
如何提高活性石灰的质量和产量,是人们所关心的问题。
近年来,国内也纷纷开展了这一方面的研究工作[1~3]。
从活性石灰的生产工艺出发,研究了活性石灰的煅烧工艺、微观结构与活性度三者之间的关系,从理论上探讨生产活性石灰的机理,为制定优质活性石灰的生产工艺制度提供理论依据。
1 实验方法 1.1 样品的制备选取乌龙泉矿优质石灰石,制成小于50mm的颗粒,将样品在硅碳棒电炉中进行煅烧。
实验着重探讨了烧成温度、保温时间等因素对石灰结构及活性度的影响。
1.2 石灰活性度的测定按照原西德CGT法测定石灰的活性度。
将煅烧好的石灰迅速冷却,制成粒径小于10mm的样品,每次© 1994-2009 ChinaAcademic Journal Electronic Publishing House. All rights reserved. 取50g,放入2L40℃的温水中,以酚酞为指示剂,用浓度为4mol L的盐酸进行滴定,至到10min内红色消失,盐酸消耗总体积数(mL)即为石灰的活性度。
1.3 活性石灰样品微观结构的分析将煅烧好的石灰用日本公司生产的JSM25610LV 型扫描电镜进行微观结构的观察。
2 结果分析与讨论 2.1 石灰石的显微结构对石灰活性度的影响为了探讨石灰石的结构对煅烧后石灰活性的影响,实验中选择了2种石灰石,即乌龙泉石灰石和安徽石灰石。
它们的微观形貌图见图1。
由图1可以看出,乌龙泉石灰石中CaCO3晶体发育程度较差,颗粒比安徽石灰石小,同时还伴随一些杂质,煅烧后CaO晶粒也比较小。
它们的活性度也有明显的差别。
乌龙泉矿生产的活性石灰活性度为182.4mL,而安徽生产的活性石灰活性度为427.5mL。
图1 石灰石的扫描电镜照片 2.2 石灰结构与煅烧制度的关系实验中以乌龙泉矿优质石灰石为原料,通过改变煅烧温度、煅烧时间,对所获得的各物料进行活性度的测定及微观结构分析。
石灰活性度的测定结果见表1。
表1 不同煅烧条件下石灰活性度的分析结果煅烧制度(温度 保温时间) 850℃ 15min 900℃ 15min1000℃ 15min1100℃ 15min1150℃ 15min1150℃ 30min1150℃ 45min活性度 mL 21.527.890.2308.3413.9417.5408.3 由表1可以明显看出,随着石灰石煅烧温度的提高,石灰活性度明显提高,在1150℃时,石灰活性度高于400mL,达到优质活性石灰的标准。
在1150℃的实验条件下,随着保温时间的延长,石灰活性度达到最高值后下降。
在不同煅烧条件下,活性石灰的显微结构见图2。
在850℃,石灰石表面出现一些孔洞,说明CaCO3开始分解,但仍保持着CaCO3晶体的形状。
随着石灰石煅烧温度的提高,石灰的空隙率增大,说明CaCO3分解程度增大,形成CaO晶体的数量也增加。
因此,石灰活性也相应增大,在1150℃保温15min时已有很好的CaO晶体结构形成。
随着保温时间的延长,CaO晶粒继续增加并发育长大,保温30min时活性石灰的空隙率及CaO晶体的数量达到最大,此时石灰活性也最高。
继续延长保温时间至45min 时,CaO晶粒开始聚集,空隙开始收缩,石灰活性开始降低,此时的物料若随炉缓慢冷却,CaO晶粒将继续长大,且在晶粒表面及边缘变得圆滑。
2.3 讨论 2.3.1 生产活性石灰的机理石灰的活性与煅烧工艺、石灰的矿物组成、结构有着密切的关系。
在石灰的矿物组成中有游离氧化钙和结合氧化钙2种形式,其中游离氧化钙又有活性氧化钙和非活性氧化钙之分[4],而石灰的活性主要取决于活性游离氧化钙的含量。
石灰石的锻烧是石灰石菱形晶格重新结晶转化为石灰的立方晶格的变化过程。
该过程是一个比较复杂的物理化学过程。
当石灰石加热到分解温度后,会发生如下反应 CaCO3(s)CaO(s)+CO2(g)+178.16kJ 此反应为吸热反应。