低转炉炼钢石灰消耗项目建议书
降低石灰消耗资料

三、现状调查
2009年以来,铁水成分差、渣量大,同时品种钢比例大使 得石灰消耗居高不下,2月份进厂灰耗高达68Kg/T以上,严重 影响到公司及转炉厂的生产及成本。
造成石灰消耗波动因素有很方面的原因包括装入制度、铁 水成份不稳定,厂灰成份不稳定,外购灰、铁水温度、操作技 术水平和冶炼控制枪位,人的心理因素等等。
一助
2月
1
七、对策实施
实施(1)
实施一:作业长炉长和一助对每一炉钢全程监控,做到三个心中有数, 结合各种实际情况,控制冶炼过程,操作前期采用较大氧气流量较低枪位 吹炼,以便快速升温,过程中氧气流量变枪位控制,减少喷溅和返干,终 点大氧气流量低枪位操作,吹炼过程底吹氩气加大炉内搅拌力,使其成渣 快,脱磷率高,提高终点命中率。
2
▪ 实施二:做到三个心中有数。在冶炼控制过程中减少过 氧化渣的形成,尽量做到终点C>0.08%。倒炉时少倒渣、多留 渣,溅干渣。Si>0.80%如果大量留渣,极易造成前期喷溅和 过程中喷溅。在铁水Si>0.80%时,少留或不留渣。在留渣操 作工艺过程中,由于存在上一炉的渣,在初期渣中,含有很高 的FeO、SiO2。为了保证炉渣中的FeO不过量导致前期的低温 喷溅严重,一助在冶炼枪位必须比正常枪位低100mm左右, 石灰分批加入,以确保石灰能够均衡连续熔化达到去磷效果。
南昌长力钢铁股份有限公司 炼钢厂转炉车间炉前丙班QC小组
一、小组概况
▪ 小组名称: ▪ 活动时间: ▪ 课题类型: ▪ 活动次数:
降低石灰消耗(在55Kg/T以下) 2009年2至8月 现场型 七次共十四小时
序号
1 2 3 4 5 6 7 8 9 10 11 12
姓名
谈承富 谢宇宁 沈永斌 万俊文 吴坚强 熊重辉 万春芽 蔡海建 刘洪云 徐志昌 余国安 尹振江
降低转炉钢铁料消耗的措施

降低转炉钢铁料消耗的措施钢铁料消耗是转炉生产的一项重要综合性技术经济指标,也是转炉成本构成的主体,占炼钢的成本的80%。
影响钢铁料消耗的原因是:1、转炉吹损过大铁水条件较差,其Si成分波动较大,喷溅率达到5%。
低硅铁水时易因热量不充足、操作不当造成严重后吹,使渣中氧化铁含量大增,增加了铁损。
2、钢水收得率低高温浇铸时坯壳较薄,容易引发生产事故。
由于事故多发导致回浇余钢水、连铸坯废量增多。
同时由于切割隔嘴更换不及时,氧压不合理致使隔口较大,降低了钢水收得率。
3、出钢温度高出钢温度高会增加连铸事故,同时使铁水烧损过多。
解决措施:调整炉龄结构用部分低价辅料代替废钢入炉量,降低钢铁料成本。
2、提高石灰质量采用优质石灰石烧制石灰,对石灰加入量实行精确控制。
3、减少渣料加入量钢渣量每增加10kg/t,钢铁料消耗会升高2.5kg/t,应实行小渣量操作。
4、提高高拉碳率提高高拉碳率,会大幅度减少后吹,减少了金属氧化损失。
5、降低渣中FeO含量在确保不烧枪、不粘钢的前提下降低过程枪位,在满足脱磷前提下降低渣中全铁含量,将渣中全铁含量控制在16%以下。
6、降低出钢温度采用全程钢包加盖工艺,以降低出钢温度。
7、提高连铸金属收得率1)连铸过程采取低温快铸的操作思路,优化结晶器保护渣理化性能,确保浇铸过程的稳定,杜绝浇铸过程中的粘结现象,减少重新甩坯。
2)提高中包连铸寿命,减少热换中包次数,降低甩废率。
3)严格控制中包浇余钢水量,将中包大块高度控制在200mm以下。
4)根据铸坯断面尺寸选用合适的切割嘴,将焊缝减小,以减少切割渣。
更多精彩内容请登录中国冶金装备网。
转炉炼钢降低石灰消耗

转炉炼钢降低石灰消耗华西炼钢厂:闫海龙、赵盛贤、朱凌之内容提要:转炉炼钢造渣工艺采用留渣操作,同时配加轻烧白云石,降低石灰消耗。
华西钢铁公司炼钢厂从2012年以后开始实施,技术已经成熟,石灰消耗明显下降,取得较好的经济效益。
一、生产条件及生产现状华西钢铁公司炼钢厂现有600t混铁炉一座,40t顶底复吹转炉两座,铁水从高炉进入炼钢厂,经过KR脱硫处理,后倒入600t混铁炉,再进入转炉冶炼。
炉后配有两个吹氩站,配有废钢调温设施。
连铸分别为R6m两台,1#机断面为150╳150mm2热送高线厂,2#机断面为165╳225mm2、165╳280mm2,分别送不锈钢轧钢厂和带钢厂。
生产的品种有:Q195、Q195B、Y195-1、U195L、Q215、Q235A、Q235B、Q345B、DQ345B、H08、H08A、08Al、H11MMn2SiA、DR、DR-1、40#、70#、ML35、JD2、40Cr、30Mn2、SAE10B08、SAE10B17、45#、45#-2、20#、65Mn、HRB400E 2012年之前,转炉造渣料由石灰、煤球、萤石、球团矿(冷却剂),在出钢结束后,根据炉渣情况,当炉渣氧化性高时则加150~200kg/炉改渣剂,以利于溅渣护炉。
2012年前转炉造渣石灰消耗比较高,一般消耗在75kg/t钢以上,高则超过85kg/t 钢。
在2010年4月随意抽了10炉,其数据见表1:从表一中可以看出,这10炉钢的平均铁水单耗为905.39kg/t钢,铁水+生铁块+废钢合计消耗为1144.49kg/t钢,其中石灰单耗为70.2kg/t钢,而当时铁水条件相对不错,铁水成分都较好,Si含量在0.48~0.55%之间,P、S含量较低,铁水中Mn含量还可以,铁水温度平均在1355℃,但石灰消耗还是高于70kg/t钢。
二、降低石灰消耗采取的工艺措施1.采用留渣操作采用留渣操作最担心的是安全问题,因此转炉开始实测留渣操作时对炉内所留的炉渣要心中有数,对于严重后吹的转炉渣则不实行留渣操作,其溅渣结束后把后吹的炉渣倒尽,对于一般的炉渣,在溅渣结束后到出部分炉渣,留1/2炉渣在转炉内,紧接着加入废钢,然后兑铁水。
120t转炉降低石灰消耗实践
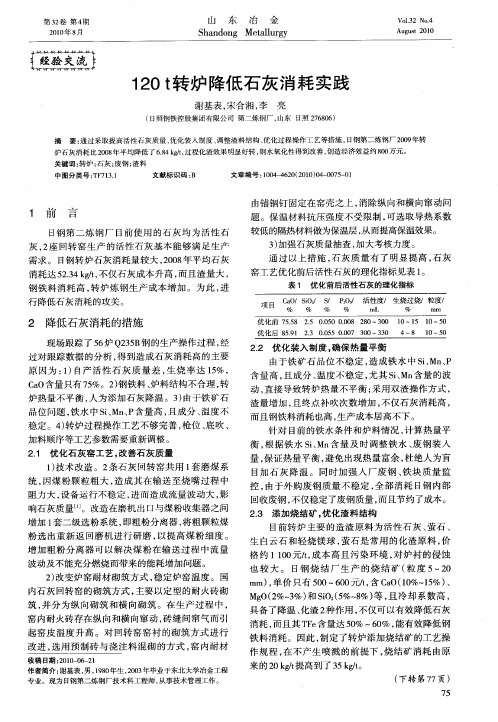
稳定 。4 转炉 过程操 作 工艺 不够 完善 , 位 、 吹 、 ) 枪 底
加料顺 序等工艺参 数需要 重新 调整 。 21 优化 石灰 窑工艺 , . 改善石灰质 量
衡 , 据 铁 水 S、 含 量 及 时 调整 铁 水 、 钢装 入 根 iMn 废 量 , 证 热量 平衡 , 免 出现热 量 富余 , 保 避 杜绝人 为 盲 目加 石 灰 降 温 。 同 时加 强 人 厂 废 钢 、 块 质 量 监 铁
第3卷 第4 2 期 21年 8 00 月
山 东 冶 金
S a d n M eal r y hnog tl g u
V0 _ 2 l No4 3 .
Au u t 2 0 g s 01
一一 ~ 交一 流一 验
1 0t 转炉 降低 石灰 消 耗 实践 2
串 广十
钢 铁 料 消耗 高 , 炉 炼 钢生 产 成 本增 加 。为 此 , 转 进 行 降低石灰 消耗 的攻 关 。
窑 工艺优化 前后活 性石灰 的理化指 标见表 1 。
表 1 优 化 前 后 活 性 石 灰 的 理化 指标
项目
a cO % i O %
活
生
2 降低 石灰 消耗 的措施
控, 由于外 购 废 钢 质量 不 稳 定 , 部 消 耗 日钢 内部 全 回收废钢 , 不仅稳 定 了废 钢质量 , 而且节 约 了成本 。
23 添 加烧结 矿 , . 优化 渣料结构
1技术 改 造 。2 ) 条石 灰 回转 窑共 用 1 套磨 煤 系
统, 因煤粉 颗 粒 粗 大 , 成其 在 输 送 至烧 嘴过 程 中 造
现场跟 踪 了 5 炉 Q 3 B 的生 产操作 过程 , 6 25 钢 经
白灰消耗攻关计划
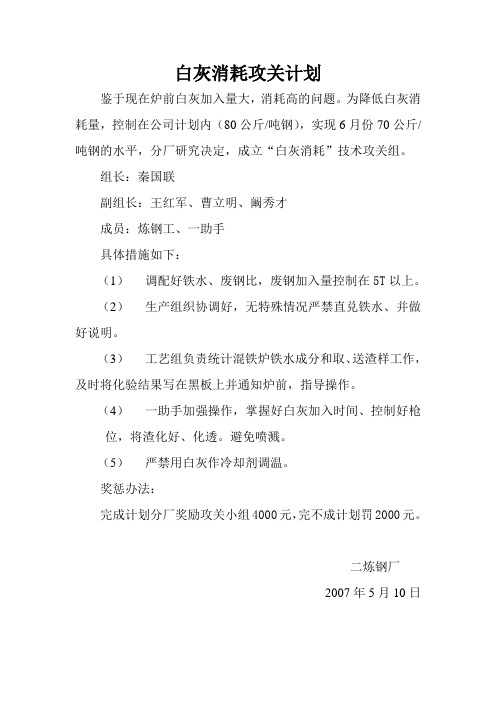
白灰消耗攻关计划
鉴于现在炉前白灰加入量大,消耗高的问题。
为降低白灰消耗量,控制在公司计划内(80公斤/吨钢),实现6月份70公斤/吨钢的水平,分厂研究决定,成立“白灰消耗”技术攻关组。
组长:秦国联
副组长:王红军、曹立明、阚秀才
成员:炼钢工、一助手
具体措施如下:
(1)调配好铁水、废钢比,废钢加入量控制在5T以上。
(2)生产组织协调好,无特殊情况严禁直兑铁水、并做好说明。
(3)工艺组负责统计混铁炉铁水成分和取、送渣样工作,及时将化验结果写在黑板上并通知炉前,指导操作。
(4)一助手加强操作,掌握好白灰加入时间、控制好枪
位,将渣化好、化透。
避免喷溅。
(5)严禁用白灰作冷却剂调温。
奖惩办法:
完成计划分厂奖励攻关小组4000元,完不成计划罚2000元。
二炼钢厂
2007年5月10日。
2024年石灰和石膏项目建议书

石灰和石膏项目建议书目录序言 (4)一、背景和必要性研究 (4)(一)、石灰和石膏项目承办单位背景分析 (4)(二)、石灰和石膏项目背景分析 (5)二、后期运营与管理 (6)(一)、石灰和石膏项目运营管理机制 (6)(二)、人员培训与知识转移 (7)(三)、设备维护与保养 (8)(四)、定期检查与评估 (8)三、石灰和石膏项目概论 (9)(一)、创新计划及石灰和石膏项目性质 (9)(二)、主管单位与石灰和石膏项目执行方 (9)(三)、战略协作伙伴 (10)(四)、石灰和石膏项目提出背景和合理性 (11)(五)、石灰和石膏项目选址和土地综合评估 (12)(六)、土木工程建设目标 (14)(七)、设备采购计划 (14)(八)、产品规划与开发方案 (14)(九)、原材料供应保障 (15)(十)、石灰和石膏项目能源消耗分析 (16)(十一)、环境保护 (17)(十二)、石灰和石膏项目进度规划与执行 (17)(十三)、经济效益分析与投资预估 (18)(十四)、报告详解与解释 (19)四、石灰和石膏项目建设地分析 (21)(一)、石灰和石膏项目选址原则 (21)(二)、石灰和石膏项目选址 (21)(三)、建设条件分析 (22)(四)、用地控制指标 (23)(五)、用地总体要求 (24)(六)、节约用地措施 (25)(七)、总图布置方案 (27)(八)、运输组成 (28)(九)、选址综合评价 (31)五、人员培训与发展 (31)(一)、培训需求分析 (31)(二)、培训计划制定 (33)(三)、培训执行与评估 (34)(四)、员工职业发展规划 (35)六、石灰和石膏项目落地与推广 (37)(一)、石灰和石膏项目推广计划 (37)(二)、地方政府支持与合作 (38)(三)、市场推广与品牌建设 (38)(四)、社会参与与共享机制 (39)七、科技创新与研发 (40)(一)、科技创新战略规划 (40)(二)、研发团队建设 (42)(三)、知识产权保护机制 (43)(四)、技术引进与应用 (44)八、质量管理与监督 (45)(一)、质量管理原则 (45)(二)、质量控制措施 (47)(三)、监督与评估机制 (48)(四)、持续改进与反馈 (50)九、市场营销与品牌推广 (53)(一)、市场调研与定位 (53)(二)、营销策略与推广计划 (54)(三)、客户关系管理 (56)(四)、品牌建设与维护 (57)十、危机管理与应急响应 (59)(一)、危机预警机制 (59)(二)、应急预案与演练 (60)(三)、公关与舆情管理 (62)(四)、危机后期修复与改进 (64)序言随着全球市场一体化步伐的加快,跨界合作已经成为推动企业发展新趋势。
210转炉厂降低钢铁料消耗实践

内 , 渣 F O 的含 量控 制在 1 % ~l% 的范 终 e 4 6
围内 ; 终点 P不能 超过 0 0 8 的钢 种 , 对 .1% 如
耗 太高 , 容易 喷 溅 , 过 工 艺调 整 , 大 能 消 通 扩
钢 种 石 耗
.
2 ・ 6
S H 终渣 碱度 控制 在 3 2— . P C, . 3 6的 范 围 内 ,
终 渣 F O 的含 量 控 制 在 1 % ~1 % 的 范 围 e 6 8
起 大量 氧化 铁 , 随后在元 素 氧化 、 池被 加热 熔
时 , 往突然 引起 碳 的激 烈 氧化 , 往 容易造成 爆
内; 同时相应 降低 轻 烧镁球 加人 量 , 控制 好终
发性 的喷溅 。吹炼 到 2 % 以后 , 2 防止 F O蓄 e 积过 多 , 压枪脱 碳 , 吹炼 到 7 % 以后 , 防 止 0 为 熔 渣 返干 , 又提 高枪 位 , 近终点 压枪 均匀 成 接
渣 Mg O的含量 , 求调 度室 及 时根 据 转 炉热 要
2 0转 炉厂 降 低钢 铁 料 消 耗 实践 1
2 0转 泞 r 1
摘
刘
要
彭
钢铁料消耗 占转炉生产成本 7 % 以上 。降低 钢铁料 消耗不仅 可 以降低生 产成本 , 0 而且 有 利 于改善其他技术经济指标 , 是公 司降低产 品成本 的有效手段之 一。根据集团公司的要求和我 厂降本增效 的 目标 ,1 2 0转炉厂成立了降低钢铁料攻关小组 , 对 目前形势 , 针 在保证安全顺 产的
120t转炉降低石灰消耗实践

参考文献(2条) 1.黄希轱 钢铁冶金原理 1990 2.王雅贞;张岩;张红文 转炉炼钢工艺与设备 2001
本文链接:/Periodical_sdyj201004030.aspx
(上接第 75 页)
2.出钢温度,由 1 640~1 680 ℃调整 到 1 600~1 640 ℃,有效降低了渣料消耗,提高了炉 衬寿命。2)优化过程枪位,采用恒压变枪操作。根 据跟踪数据绘制枪位图,合理控制枪位。转炉一直 采用“变枪、变压”操作,由于操作水平限制,导致过 程化渣效果差,产生溢渣、喷溅、返干等现象,于是 改 为“ 恒 压 、变 枪 ”操 作 方 式 。 3)调 整 转 炉 底 吹 模
3 经济效益
和冷却水系统流程 3 部分组成。气路系统流程:外
按风中含湿量每减少 1 g/m3降低焦比 0.8 kg/t 计
界大气进入空气过滤器,除去灰尘后进入脱湿器,高 算,若 3 200 m3高炉年产量为 360 万 t,可节约焦炭 1
温高湿空气在脱湿器内(冷却器)进行热交换,降温 万 t,经济效益可达 3 000 多万元/a。每年多喷煤 2 万
4结语
循环冷却水系统,循环使用。 根据高炉对鼓风机入口的湿度要求,通过控制
进脱湿器的冷水流量,达到控制鼓风机入口湿度的 目的。冷水流量调节阀的开度根据负荷的大小自动 调节。鼓风机脱湿装置的所有温度、压力检测均由 热电阻和压力变送器实现;冷水换热器出口的流量 检测由电磁流量计实现。鼓风机入口处的空气温 度、湿度检测采用在线温、湿度检测仪进行。冷凝水 箱中冷凝水液位由液拉控制器自动控制。所有检测
换。降温脱去部分水分,而冷水被空气加热温度升 益约 6 000 万元/a。扣除全年蒸汽消耗量、冷却水补
50万吨短流程绿色电炉炼钢项目建议书

50万吨短流程绿色电炉炼钢项目建议书建议书:关于建设50万吨短流程绿色电炉炼钢项目一、项目背景及目标近年来,随着环境污染问题日益严重,绿色低碳发展已成为全球的共识。
钢铁行业作为国民经济的重要支柱产业,在高能耗、高污染的形势下,亟需推动绿色转型。
为此,我们建议启动50万吨短流程绿色电炉炼钢项目,以实现对传统钢铁生产的转变,提高资源利用率、降低能耗和污染排放。
二、项目描述1.项目规模:计划年产50万吨钢材。
2.建设地点:选取适宜的工业园区或经济开发区进行项目建设。
3.建设内容:(1)建设有关设施:包括电炉炼钢车间、原料库房、产品仓库、废水处理站等。
(2)采购生产设备:引进先进的电炉、炉水循环设备、新型气体净化装置等相关设备。
(3)配套设施:建设独立的电力供应系统、废水处理系统、燃气供应系统等。
三、项目优势分析1.绿色环保:采用短流程技术,减少渣钢产量和二次加工成本,显著降低二氧化碳、二氧化硫等排放,符合国家对环保的要求。
2.资源利用率高:电炉炼钢过程中能减少生铁、钢水和渣钢的损耗,大幅提高废钢资源的利用率。
3.经济效益显著:采用电炉炼钢技术,不仅能降低原料和能源成本,还有望通过高效生产提升销售竞争力。
4.技术含量高:引进先进的电炉炼钢设备,提高产品质量和市场竞争力,为企业带来长期发展的动力。
四、项目实施计划2.项目立项:完成项目建议书的编写,获得相关政府部门的批准,明确项目建设规模和目标。
3.选址规划:根据实地考察和专业评估,选取适宜的建设地点,并进行项目规划和设计。
4.设备采购:确定项目设备需求,对国内外钢铁设备制造商进行调研,进行设备采购和合同签订。
5.项目建设:按照项目规划和时间节点,进行土地平整、基础设施建设、设备安装调试等工作。
6.试生产和调试:完成项目建设后,进行设备调试和试生产,确保设备正常运行和产品质量达标。
7.正式生产:完成试生产和调试后,进行正式生产,逐步实现项目产能释放和效益提升。
xxx钢铁公司碳捕集项目建议书1

投 收期 节能目标 环形窑的 环形石灰窑的设备投资小,占地小; 优势 环形石灰窑没有粉料,入炉原料数量大幅度减少; 人员编制、维修量、运行成本均减小,还可在线检修,对生产的影响减小。 建设时间 项目工程 24 个月内验收结束 资金来源 项目资金由 xxxxxxxxxx 出资 合作方式 合作基础 社会效益 和可复制 性 环形窑项目在全国钢铁行业使用了 150 台以上。
(以上两期个项目的投资额度均为初期估算,最终以设计图纸为依据进行工 程预算,并以预算为投资依据。) 资回 22 个月。
xxxx 公司石灰生产的碳捕集项目建议书
项目名称 项目业主 单位 技术依托 单位 节能服务 单位 项目概要 和投资规 模 xxxxxxx 公司石灰生产的碳捕集项目 xxxxxxx 公司 xxxxxxx 公司 xxxxxxxxx 工程技术有限公司 xxxxxxxxxxx 工程技术有限公司 项目业主单位现有钢铁产能 xxxxx 万吨。炼钢过程需要消耗石灰,每吨钢需 要消耗 80 公斤活性石灰,项目业主单位共要消耗 130 万吨石灰。目前业主 的单位的石灰是在各个厂区使用高炉煤气高温煅烧而成。 依据石灰煅烧化学 反应方程式:CaCO3 = CaO+CO2,每生产一吨石灰可以产生纯净 CO2 0.78 吨,项目业主单位采用了常规的煅烧方式和生产方式,CO2 不能回收,每 年排放 100 万吨的 CO2 。 本项目以年产 130 万吨活性石灰为前提条件条件,采用由 xxxxxxx 公司和 xxxxxxx 公司联合开发的以环形窑为核心的密闭石灰煅烧系统,将煅烧石灰 后的纯净 CO2 气体经过冷却和加压灌装后, 完成 130 万吨石灰生产过程中的 碳捕集工程,每年共捕集纯净 CO2 100 万吨。 该碳捕集技术为国际领先技术,在国际刚刚是新兴产业的时候就由 xxxxxxxxx 公司在钢铁行业率先实现了碳捕集并实现了碳汇的积累,具有应 对气候变化的示范效应,将在今后 50 年里数十万亿美金的国际碳捕集技术 市场上占有至高地位。 100 万吨纯净 CO2 的碳捕集工程项目分为两期,第一期建设一套年产 13 万 吨活性石灰密闭煅烧系统和 10 万吨纯净 CO2 的捕集系统的示范工程。 第二 期工程将项目业主单位的各个石灰厂改造为相应配套产能的活性石灰密闭 煅烧系统和纯净 CO2 的捕集系统, 石灰的总产能为 117 万吨, 纯净 CO2 的 捕集系统的产能为 90 万吨。 第一期工程 13 万吨活性石灰密闭煅烧系统和 10 万吨碳捕集系统新建工程新 建工程包含一套内径 10m 外径 16m 环形密闭煅烧石灰窑,一套高炉煤气管 道系统、一套蓄热式辐射管加热系统和相应的原料和产品的场地和转运系 统;还包含一套纯净 CO2 冷却装置,一套除尘装置、一套加压灌装装置。年 产活性石灰 13 万吨,年收集纯净 CO2 10 万吨,活性石灰进入钢铁系统, 替代了原有产能, 不计利润 (在有能源消耗节能量、 石灰石物料消耗节约量、 化学活度提高值的效益时要进行计算) 。纯净 CO2 进入市场销售,销售价 600 元/吨计算,纯净 CO2 利润 400 元/吨,年利润 4000 万元。该系统总投资 约 7000 万元,投资回收期 22 个月。 第二期工程将项目业主单位的各个石灰厂改造为相应配套产能的活性石灰 密闭煅烧系统和纯净 CO2 的捕集系统, 石灰的总产能为 117 万吨, 纯净 CO2 的捕集系统的产能为 90 万吨。 117 万吨活性石灰进入钢铁系统, 替代了原有 产能,不计利润。90 万吨纯净 CO2 进入市场销售,销售价 600 元/吨计算, 纯净 CO2 利润 400 元/吨,年利润 36000 万元。该系统总投资约 63000 万元, 投资回收期 22 个月。
关于生产石灰的降本增效的提议
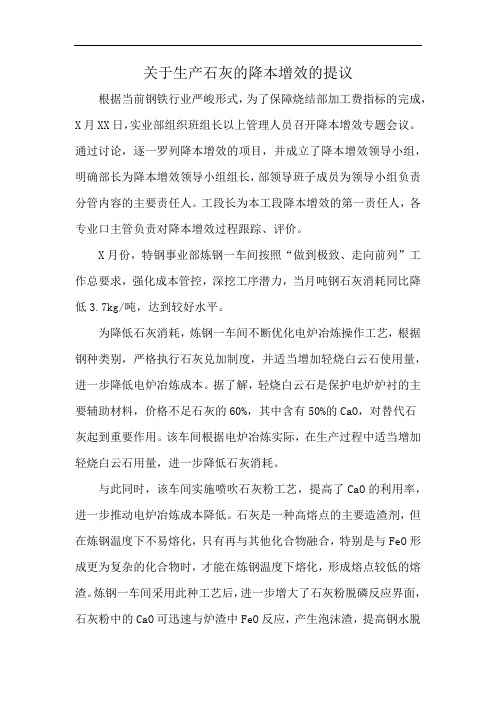
关于生产石灰的降本增效的提议
根据当前钢铁行业严峻形式,为了保障烧结部加工费指标的完成,X月XX日,实业部组织班组长以上管理人员召开降本增效专题会议。
通过讨论,逐一罗列降本增效的项目,并成立了降本增效领导小组,明确部长为降本增效领导小组组长,部领导班子成员为领导小组负责分管内容的主要责任人。
工段长为本工段降本增效的第一责任人,各专业口主管负责对降本增效过程跟踪、评价。
X月份,特钢事业部炼钢一车间按照“做到极致、走向前列”工作总要求,强化成本管控,深挖工序潜力,当月吨钢石灰消耗同比降低3.7kg/吨,达到较好水平。
为降低石灰消耗,炼钢一车间不断优化电炉冶炼操作工艺,根据钢种类别,严格执行石灰兑加制度,并适当增加轻烧白云石使用量,进一步降低电炉冶炼成本。
据了解,轻烧白云石是保护电炉炉衬的主要辅助材料,价格不足石灰的60%,其中含有50%的CaO,对替代石
灰起到重要作用。
该车间根据电炉冶炼实际,在生产过程中适当增加轻烧白云石用量,进一步降低石灰消耗。
与此同时,该车间实施喷吹石灰粉工艺,提高了CaO的利用率,进一步推动电炉冶炼成本降低。
石灰是一种高熔点的主要造渣剂,但在炼钢温度下不易熔化,只有再与其他化合物融合,特别是与FeO形成更为复杂的化合物时,才能在炼钢温度下熔化,形成熔点较低的熔渣。
炼钢一车间采用此种工艺后,进一步增大了石灰粉脱磷反应界面,石灰粉中的CaO可迅速与炉渣中FeO反应,产生泡沫渣,提高钢水脱
磷效率,石灰消耗降低效果明显。
据统计,X月份,炼钢一车间累计产钢3.8万吨,全月成本挖潜完成比例达134.34%,为事业部成本降低做出积极贡献。
- 1、下载文档前请自行甄别文档内容的完整性,平台不提供额外的编辑、内容补充、找答案等附加服务。
- 2、"仅部分预览"的文档,不可在线预览部分如存在完整性等问题,可反馈申请退款(可完整预览的文档不适用该条件!)。
- 3、如文档侵犯您的权益,请联系客服反馈,我们会尽快为您处理(人工客服工作时间:9:00-18:30)。
低转炉炼钢石灰消耗项目建议书一、在我公司经济建设中的意义和作用石灰的主要成份是C a 0,是炼钢的主要造渣材料,具有脱磷、脱硫能力,也是炼钢用量最多的造渣材料。
在炼钢生产中,石灰消耗的上升,造成转炉冶炼渣量的增加;冶炼渣量的增加,则冶炼铁损增加,钢铁料耗也就上升了,因此,降低石灰消耗对于降低炼钢成本具有重要意义。
降低炼钢石灰消耗可降低企业生产吨钢能耗,降低温室气体C0排放,减少吨钢渣量,减少钢渣堆放对环境的污染。
另外,随着企业年产钢的不断提高,转炉炼钢石灰用量也大幅上升,给原本石灰矿产资源紧缺的企业的生产带来一定的压力,在石灰生产能力有限情况下,降低炼钢石灰消耗工作成为我们炼钢人的一个新课题。
二、石灰消耗水平炼钢厂活性石灰消耗,30t转炉65.63kg/t如表1, 100t转炉59.55kg/t如表2:表1: 30t转炉石灰消耗表2: 80t转炉石灰消耗三、攻关主要内容和工作目标1)吨钢石灰消耗企业转炉不大于5 5公斤、钢松转炉不大于50公斤;2)不影响转炉炉衬寿命,不增加补炉材料消耗;3)保证产品质量,不因降低石灰消耗而影响钢水质量;四、影响冶金石灰消耗高的主要原因根据目前我厂石灰消耗情况,影响石灰消耗的因数主要有以下几点:1、石灰质量的影响石灰质量不稳定,石灰活性度低,石灰的生烧率、过烧率波动大,石灰不易化透,增加了转炉炉前的冶炼难度和石灰消耗。
2、入炉铁水、生铁成分的影响铁水和生铁中的硅含量的影响。
铁水和生铁中的硅含量的高低,直接决定炉前每炉的石灰加入量。
石灰有效氧化钙按85%计算,在终渣碱度控制在2.8 的情况下,铁水或生铁中的硅含量每增加0.1%,石灰加入量将增加7Kg/t 。
铁水、生铁的磷、硫的影响。
磷、硫含量高,为满足所炼钢种要求,生产过程中必须增加石灰用量以达到目标。
3、冶炼操作的影响(1)操作方面原因一方面操作工在加石灰时没有根据原材料的硅含量来配加石灰,而是凭经验来配加;另一方面操作工在后期操作控制不当,终渣没有化好化透,石灰利用率低,导致终点倒炉成分不合格,增加补吹次数。
当终点成分不满足出钢条件需加料补吹时,补吹时的石灰加入量没有控制,盲目多加,造成补吹时加的石灰利用率低。
(2)留渣操作方面炉前各个班组运用熟练程度各不相同,留渣操作不规范,导致炉前班组留渣率高低相差较大,影响留渣降石灰耗的效果。
(3)高碱度护炉的影响个别时候炉前终点控制水平差导致炉况恶化,不得不通过提高碱度来护炉,导致石灰用量增加。
五、拟采取的攻关措施针对以上存在的问题,为降低石灰消耗, 合理有效利用石灰, 根据我厂30t、100t 氧气顶吹转炉经过多年的降石灰消耗探索,从技术上、操作上和管理上入手,采取提高石灰质量,规范留渣操作、合理控制石灰加入量、加强护炉等措施来降低石灰消耗。
具体如下:1、完善转炉静态模型自动化炼钢工艺100t 转炉静态模型自动化炼钢系统通过现场模式的控制模型和理论计算模式的控制模型,优化造渣模型,实行对石灰加入量自动计算并按模式自动完成加入炉内,使转炉操作实现标准化规范化,减少并稳定石灰加入量。
完善转炉静态模型自动化炼钢工艺,包括出钢终点目标计算模型、供氧模型、造渣模型,根据入炉原材料条件,制定最佳冶炼操作模式,加强过程控制,提高一倒命中率和出钢命中率。
因此可减少后吹,稳定钢水氧化性,避免因钢水过氧化而影响溅渣护炉效果。
(1)提高一倒命中率(钢种普碳钢、低合金钢要求:C: 0.10〜0.20%,温度:1630〜1670C),合格率达80%以上。
(2)提高出钢时钢水成分命中率(一次补吹W 50秒出钢),合格率达80% 以上。
(3)提高渣样合格率(碱度合格率》80% (FeO) %合格率》80% (MgO % 合格率》90% (碱度:2.5〜3. 0, (FeO) % 20%^合格,(MgO %=〜12%为合格)。
2、按硅炼钢30t 转炉实行按硅炼钢。
按硅炼钢是指根据原料中的硅含量和炉渣碱度来配加石灰,达到既不浪费石灰又能满足冶炼工艺要求,以合理利用石灰,减少渣量,降低石灰耗、钢铁料耗目的。
因此计划做如下工作:( 1 )解决铁水硅含量的准确性和实时性问题。
第一阶段先在4#炉试验,炉炉取铁水样分析;第二阶段根据高炉来的铁水成分、重量及混铁炉进铁前、后取样,推算出混铁炉剩余铁水重量,以此为基础,以后再下次进铁水后就可以推算出进铁后的铁水成分,每班每座混铁炉只要取样验证一次即可。
( 2)与外部联系,加强废钢管理,及时掌握废钢中生铁的成分与重量。
( 3)软件方面应做到铁水、生铁、石灰成分的实时传输及获取,并根据原料中的硅含量和控制的碱度计算理论石灰加入量,指导操作工加入石灰。
( 4)振料系统和加料系统改造以满足按硅炼钢要求。
( 5)建立按硅炼钢的合格率考核制度,严厉考核炉长。
3、转炉顶底复吹改造及工艺技术优化通过对企业小吨位转炉顶底复吹改造,一方面加强炉内熔池的搅拌,增加反应得动力学条件,提高石灰的熔化速度和石灰的利用率,提高转炉脱硫、脱磷能力,从而降低石灰消耗。
另一方面加强炉内搅拌,冶金反应达到平衡状态, 降低钢水中氧含量,有利于转炉炉衬的维护,从而降低石灰消耗。
根据冶炼过程反应的特点, 优化复吹工艺优化, 使复吹效果达到最佳状态。
4、完善循环留渣操作制度。
在炉渣碱度达不到3.0的情况下,先按照含Mg的碱度达2.5以上进行留渣操作,通过留渣技术降低石灰消耗。
留渣操作就是结合溅渣护炉技术,使溅渣后的残渣保留在炉内,作为下一炉前期渣继续冶炼的操作方式。
采用留渣操作能大幅度降低石灰消耗。
首先,加强炉前留渣操作培训,提高留渣操作水平。
其次,改变留渣方式,把原来的全留渣操作方式改为留1/3~1/2 渣的循环操作方式。
稳步提高留渣率,使留渣率由原来的30%以下提高到50%以上从而降低石灰耗,同时又确保终渣碱度护好炉况。
5、加强对原材料的管理,及时把铁水、生铁、石灰等重要原材料信息及时提供到炉前班组供操作工参考。
(1)根据原材料情况,动态调整装入制度,确保炉内热量平衡。
生产大班根据炉前的实际生产情况,根据热值的高低,动态调整装入制度。
当热值低时及时调整铁水加入量以及废钢铁水比例,避免因热值低造成的过氧化钢水侵蚀炉衬。
(2)车间原料工段每周定期对石灰烧透率进行抽查,由车间工艺组负责监督,发现问题及时反馈以确保进仓石灰质量。
(3)拟对炉前各料仓称量电子秤进行改造,提高计量的准确性,为石灰消耗考核提供依据。
优化炼钢静态信息系统,使计量系统的信息正常进入静态系统;使电脑统计的石灰用量与实际石灰用量误差在2〜3公斤/吨钢以内,解决炉前加石灰量与电脑统计不相符的问题。
(4)完善车间石灰消耗管理考核体系,加强对班组石灰单项考核。
炉前石灰消耗直接以炉前班组为单位进行考核,与车间经济责任制考核挂钩,执行到班组(5)要求炉前班组每班每炉必须计算石灰耗,每天统计出炉前各班组当日石灰耗及当月累计石灰耗,使炉前各班组对本班组的石灰用量做到心中有数。
同时对于当班石灰消耗高于60Kg/t 钢的班组,下班后开分析会,分析石灰消耗高的原因,找出问题,提出整改措施。
6、加强对操作工的实际操作技能培训,提高操作工的操作水平(1)准确控制加料重量和氧检枪枪位,尽可能化好过程渣和终点渣,提高石灰的利用率,同时也提高终点的命中率,减少补吹次数和时间,避免钢水过氧化。
2)规范溅渣操作,提高溅渣效果由于原材料质量下滑,炉前一倒成分S、P 偏高,必然增加后吹时间,导致炉渣温度过高,并且过氧化,因此影响溅渣效果。
致使炉子普遍存在问题,炉底深度一直停留在控制目标范围的的边缘,而且炉底接缝周围的炉衬侵蚀严重,要寻找应对措施,以确保炉衬的安全,根据不同的炉况采取不同的溅渣模式, 维护好炉型,降低喷溅造成的石灰消耗。
如3#转炉的溅渣模式:a每班溅渣率为100%且每炉溅渣时间》2分30秒;b总共补吹时间》60秒/炉,加溅渣剂》100公斤/炉;c 溅渣氮气流量控制在8000± 200m3/h;d溅渣枪位控制在600士200mm(标尺);(3) 在确保终点成分和炉内热量平衡情况下,适当提高矿石用量, 矿石加入时间尽可能的提早,使矿石起到脱磷、化渣作用,避免把石灰当作降温剂使用而浪费。
7、提高并稳定石灰质量六、投资概算1 、30t 转炉顶底复吹技术改造572 万元;2、30t 转炉按硅炼钢改造100万元;3、100t 转炉自动炼钢系统160万元。
合计832 万元。
七、经济效益预测1 、直接经济效益(1)吨钢石灰耗55公斤以下,同比下降10公斤/吨钢,预计钢产量为205 万吨,石灰价格按0.35 元/ 公斤计,则经济效益为10 * 205* 0.35 = 717.5 万元。
( 2)吨钢石灰耗50 公斤以下,同比下降9.55 公斤/ 吨钢,预计钢产量为136万吨,石灰价格按0.35 元/公斤计,则经济效益为9.55 * 136* 0.35 = 454.6 万元。
合计节约石灰205*10+9.55*136=3.35 万吨合计经济效益1172.1 万元2、间接经济效益由于造渣料的减少,可减少冶炼喷溅,降低钢铁料耗。
八、社会效益1、预计可减少温室气体CO2 排放量5.6 万吨以上。
生产1公斤石灰由石灰石分解产生的CO有0.786公斤,生产1公斤石灰烧煤气(CO含量为30%煤气1.5立方米)而产生的CQ有0.884公斤,节约石灰3.35 万吨。
则07年预计减少温室气体CO排放量为(0.786+0.884)*3.35=5.6万吨。
2、减少钢渣量5 万吨以上。
转炉炼钢耗1 公斤石灰产生钢渣约1.5 公斤,则07 年预计减少钢渣排放量为3.35*1.5=5.0 万吨。