磨损及磨讲义损理论
磨损及磨损理论
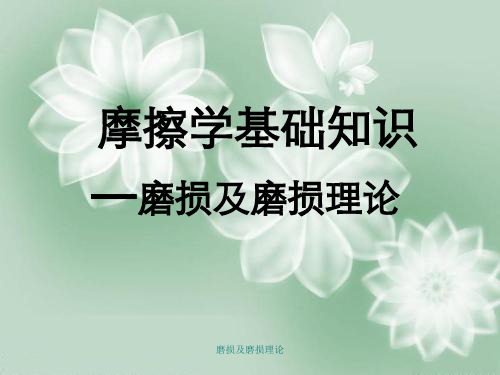
磨损及磨损理论
❖ 粘着磨损又称擦伤或咬合磨损。 ❖ 出现条件:相对滑动速度小,接触面氧化膜脆弱,
润滑条件差,接触应力大。 根据粘着点的强度和破坏位置不同,粘着磨损
一下五种不同的形式(五类典型粘着磨损) :
(1)轻微磨损:
摩擦学基础知识 —磨损及磨损理论
磨损及磨损理论
第一节 概 述
任何机器运转时,相互接触的零件之间都将因相对运动而产 生摩擦,而磨损正是由于摩擦产生的结果。由于磨损,将造成 表层材料的损耗,零件尺寸发生变化,直接影响了零件的使用 寿命。从材料学科特别是从材料的工程应用来看,人们更重视 研究材料的磨损。据不完全统计,世界能源的1/3~1/2消耗 于摩擦,而机械零件80%失效原因是磨损。
粘着结合强度比摩擦副基体金属抗剪切强度都低,剪切破坏发生在 粘着结合面上,表面转移的材料较轻微。
此时虽然摩擦系数增大,但是磨损却很小,材料迁移也不显著。通常 在金属表面具有氧化膜、硫化膜或其他涂层时发生轻微粘着摩损。
(2)涂抹:
粘着结合强度大于较软金属抗剪切强度,小于较硬金属抗剪切强度。 剪切破坏发生在离粘着结合面不远的较软金属浅层内,软金属涂抹在硬 金属表面。这种模式的摩擦系数与轻微磨损差不多,但磨损程度加剧。
材料以极细粒状脱落,出现许多“豆斑”状凹坑。
宏观上光滑,高倍才能观察到细小的磨粒滑痕。
低倍可观察到条条划痕,由磨粒切削或犁沟造成。
存存在在压压坑坑,,间间或或有有粗粗短短划划痕痕,,由由磨磨粒粒冲冲击击表表面面造造成成
磨损及磨损理论
3. 表面破坏方式与机理对应关系
磨损及磨损理论
1.8磨损的评定
摩擦磨损与润滑_宏观磨损规律与磨损理论课件
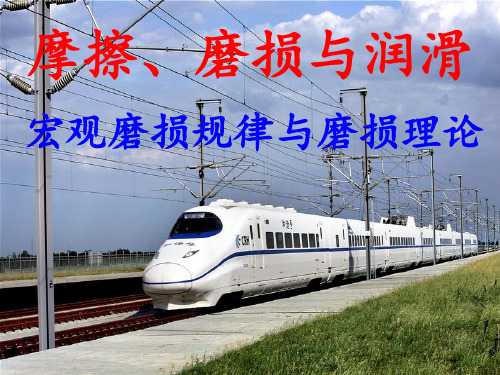
图 滑动轴承的磨合
二、磨损过程曲线
9、良好的磨合性能表现特征有哪些?提高磨 这时候,润滑油黏度 合性能的措施可以有哪些? 高好,还是低好呢?另外,
1)、合理选用磨合规范;
加入添加剂又可以起到什 么作用呢?
磨合时间短,磨合磨损量小,以及磨合后的表 2)、选择适当的润滑油和添加剂; 面耐磨性高。
3)、采用合适的材料配对; 4)、控制制造精度和表面粗糙度。
轻微工况下表面压力 不高而润滑充足, 润 滑膜易于形成, 磨损 主要由于粗糙峰的机 械作用引起
三、表面品质与磨损
16、这幅图呢? 磨损量有什么不 同?
由对于繁重的工作条件, 粘着磨损出现的可能性增 加,相互交叉的痕迹方向 将避免大面积的接触点, 从而提高抗磨损性能。
另问:上面4幅模型中,机床导轨宜采用哪种轨迹方向呢?
Archard体积磨损 度修正公式
考虑表面膜的影响以及切向应力 和边界膜解附使接触峰点尺寸的 数;β为与表面膜有关的系数;σs 为受压屈服极限。 增加
式中, km 为与材料性质有关的系数;α为常数; f 为摩擦系
从Holm 和Achard 修正公式可以得出:磨损量与滑动距离和载荷 成正比,而与摩擦副中软材料的屈服极限或硬度成反比。 实验研究表明:磨损量与滑动距离成正比的结论基本上适合于各种 磨损条件。而磨损量与载荷的正比关系只适合于一定的载荷范围。 例如, 钢对钢的摩擦时, 当载荷超过H/ 3 时, 磨损量将随载荷以 指数形式增加。磨损量与材料硬度成反比的关系也已被许多实验所 证实, 特别适合于磨粒磨损。
二、磨损过程曲线
5、请仔细观察每一幅图,各有什么特征?
二、磨损过程曲线
6、磨合前后的变化?
磨合使接触 面积显著地 增加和峰顶 半径增大。
摩擦学第五章磨损 ppt课件
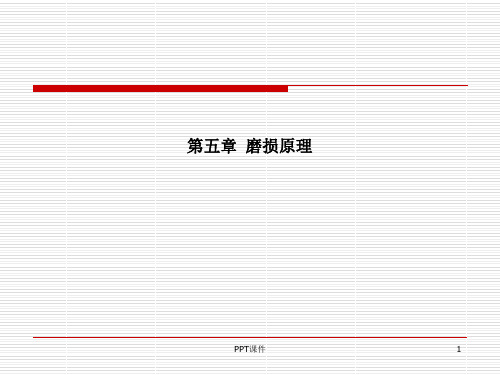
按照磨损程度的不同,粘着磨损可以分为以下五类: 1) 轻微磨损 粘着点的剪切强度比形成该粘着点的任何一方的基体金属的剪切强度
都小(如锡与铁对磨),磨损发生在粘着点的界面上,材料转移十分轻微, 甚至不产生材料转移。磨合属于这种磨损。
PPT课件
11
2) 涂抹
粘着点的剪切强度介于形成该粘着点的两种基体金属的剪切强度之间 (如铅与钢对磨),剪切破坏发生在较软金属的浅表层内,并使该表层的材 料转移到较硬金属表面上,使后者的表面上被涂抹上薄薄的一层。
PPT课件
18
磨损(过程)量计算:
(1)Ⅰ物体上原子a1,在运动过程中分别与Ⅱ物体上b1、b2……逐次接 触,每滑动距离d就与一个新的原子接触,当滑动L距离时,a1遇到的 原子数L/d; (2)每两个物体接触面积为Ar,Ar面积上的原子数等于Ar/d2;因之两 接触面滑动L距离时,原子总的接触次数Na等于;
PPT课件
7
(5)磨损速率(磨损强度)
I=V / t
I W / t
(6)相对耐磨性 它是标准试样的磨损率与被测试样磨损率之比(%)。
PPT课件
8
三、磨损的分类
1、粘着磨损或粘附磨损(Adhesive wear);
2、磨料磨损或磨粒磨损 (Abrasive wear);
3、疲劳磨损或表面疲劳磨损(Surface fatigue wear);
0-t1
PPT课件
t1-t2 t2-t3 时间
3
2、磨损不仅是材料本身固有特性的表现,更是摩擦学系统特性的反映。 因此,磨损也具有条件性和相对性。
4章磨损

二、磨损的基本特性
磨损系数表示磨损量与工况之间的关系。当载荷与速 度为已知,并可求出一定工况下的磨损系数时,就可估算 磨损量,以预测摩擦学系统的寿命;也可根据磨损系数来 确定磨损类型,因为不同的磨损类型具有不同的磨损系数。 (5)磨损速率(磨损强度):
I V
I W
t
t
此外,还采用相对耐磨性这一参数,它是标准试样的 磨损率与被测试样磨损率之比。
§4-3
磨粒磨损
磨粒磨损是指在摩擦过程中,由于摩擦表面上硬 的微凸体或摩擦界面上的硬颗粒而引起物体表面材料 损耗的一种磨损,这是最常见的一种磨损现象。据统 计,因磨粒磨损而产生的损失约占各类磨损所造成的 全部损失的一半。挖掘机、运输机许多零件的磨损都 属于磨粒磨损。
一、主要类型
由于物体表面本身硬的微凸体使对偶表面产生的磨粒 磨损称为两体磨粒磨损(Two-body abrasive wear);由于摩 擦表面上存在自由硬颗粒而产生的磨粒磨损称为三体磨粒 磨损(Three- body abrasive wear)。
(3)刮伤 沿滑动方向形成严重的划痕,剪切破坏发生 在较软金属的表层。
一、主要类型
按照磨损程度的不同,粘着磨损可以分为以下五类:
(4)胶合 表面局部温度相当高,粘着点的面积较大, 由于粘着点的剪切强度比形成粘着的任何一方基 体金属的剪切强度都要高(如铜与钢对磨),故在 摩擦副的一方或双方的基体金属上产生较深层的 破坏。因而,既有较多的软金属转移到硬金属表 面上,同时也有部分硬金属转移到软金属表面上。
三、磨损的分类 实际的磨损现象大都是多种类型磨损同时存 在,或磨损状态随工况条件的变化而转化。因此, 在分析和处理磨损问题时,必须善于分析并抓住 主要的磨损类型,或着眼于主要的磨损过程,才 能采取有效的减磨措施。
磨损及磨损理论

粘着结合强度比两基体金属的抗剪强度都高,切应力高于粘着结合强度。 剪切破坏发生在摩擦副金属较深处,表面呈现宽而深的划痕。
此时表面将沿着滑动方向呈现明显的撕脱,出现严重磨损。如果滑动继 续进行,粘着范围将很快增大,摩擦产生的热量使表面温度剧增,极易出现 局部熔焊,使摩擦副之间咬死而不能相对滑动。 这种破坏性很强的磨损形式,应力求避免。
所以磨损是机器最常见、最大量的一种失效方式。据调查, 轮胎压痕(SEM 5000X) 联邦德国在1974年钢铁工业中约有30亿马克花费在维修上,其中 直接由于磨损造成的损失占47%,停机修理所造成的损失与磨损 直接造成的损失相当,如果再加上后续工序的影响,其经济损失 还需加上10%一20%。
摩擦痕迹 (350X)
1.6
磨损过程的一般规律:
1、磨损过程分为三个阶段:
表面被磨平, 实际接触面 积不断增大, 表面应变硬 化,形成氧 化膜,磨损 速率减小。
随磨损的增长,磨耗 增加,表面间隙增大, 表面质量恶 化,机件快速失效。
斜率就是磨损速率,唯一稳定值; 大多数机件在稳定磨损阶段(AB 段)服役; 磨损性能是根据机件在此阶段 的表现来评价。
(3)磨损比
冲蚀磨损过程中常用磨损比(也有称磨损率)来度 量磨损。
Hale Waihona Puke 材料的冲蚀磨损量(g或μ m 3) 磨损比= 造成该磨损量所用的磨料量(g)
它必须在稳态磨损过程中测量,在其它磨损阶段 中所测量的磨损比将有较大的差别。 不论是磨损量、耐磨性和磨损比,它们都是在一 定实验条件或工况下的相对指标,不同实验条件或 工况下的数据是不可比较的。
当材料产生塑性变形时,法向载荷W与较软材料的屈服极限σy之间的关系:
(1)
当摩擦副产生相对滑动,且滑动时每个微凸体上产生的磨屑为半球形。 其体积为(2/3)πa3,则单位滑动距离的总磨损量为:
金属磨损基本理论
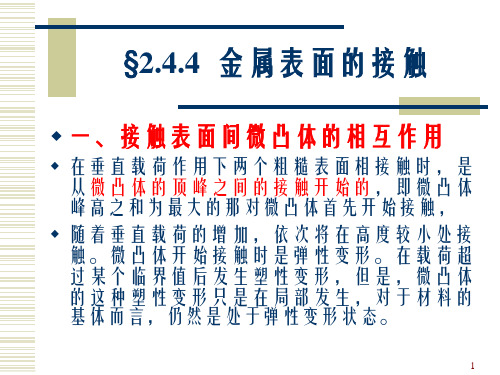
而轮廓接触面积一般为表观接触面积的 5%~15%。
7
真实接触面积的影响因素
影响接触表面真实接触面积的主要因素是: 1、接触载荷 2、表面粗糙度。
8
1.载荷
显然、在确定的表面状态下,随着载荷的增加,真实 接触面积是不断增大的,
研究表明:实际接触面积与载荷之间的关系不仅取决 于变形的形式,而且还取决于表面轮廓的分布。
摩擦学的学科性质
摩擦学过程涉及的影响因素很多,是一门 多学科、跨学科的边缘科学。
它主要涉及材料学、冶金学、机械学、固 体力学、表面物理、表面化学等诸多学科。
18
摩擦学特性是系统特性
摩擦磨损过程极其复杂,摩擦学性能不是材 料的固有属性,而是整个摩擦副的系统特性。
在摩擦学系统中任一外部因素(如载荷、速 度、运动形式、持续时间、环境温度、介质、 润滑条件、接触面状况等)和内部因素(如 材料成分,组织结构,表面物理、化学、力 学性能等)稍有变化,都可能引起材料摩擦 磨损性能的较大变化。
2. 干摩擦(无润滑摩擦)在大气条件下, 摩擦表面间名义上没有润滑剂存在时产 生的摩擦称为干摩擦,或无润滑摩擦。
25
3、流体(润滑)摩擦:相对运动的两物体表面完 全被流体隔开时产生的摩擦称为流体(润滑) 摩擦。当流体为液体时称为液体摩擦;流体为 气体时称为气体摩擦。流体摩擦时摩擦发生在 流体内部。
10
在清除了氧化膜的洁净金属表面上 很容易出现固体粘附(冷焊)现象,
实际上对于任何固体,这种现象均会发生,但 是、它常常因接触面积小(由于表面粗糙不平) 和受压表面的弹性而被掩盖;
出现这种现象的原因在于固体表面分子间的相 互吸引,分子相互吸引的各种形式均通过粘附 现象反映出来。
摩擦和磨损ppt课件
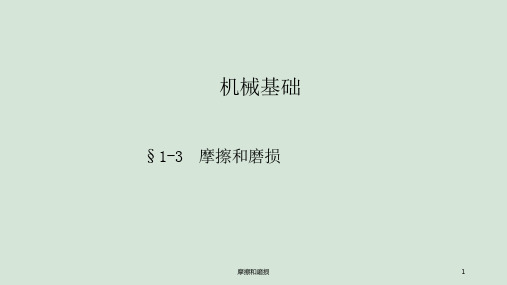
当摩擦表面的不平度的尖峰相互作用的各点发生粘着后,在相对滑动时, 材料从运动副的一个表面转移到另一个表面,故而形成粘着磨损。
严重的粘着磨损会造成运动副咬死,不能正常运转 。
影响因素: ①同类摩擦副材料比异类材料容易粘着,如钢件运动副的 相对运动; ②脆性材料比塑性材料的粘着能力高; ③在一定范围内,零 件的表面粗糙度愈小,抗粘着能力愈强。
机械基础
§1-3 摩擦和磨损
摩擦和磨损
1
§1-4 摩擦与磨损
摩擦和磨损是自然界和社会生活中普遍存在的现象。 有时人们利用它们有利的一面,如车辆行驶、带传动等是利用
摩擦作用,精加工中的磨削、抛光等是利用磨损的有用方面。 由于摩擦的存在造成了机器的磨损、发热和能量损耗。 据估计目前世界上约有30%~50%的能量消耗在各种形式的摩擦 中,约80%的机器是因为零件磨损而失效。
磨损会影响机器的精度,强敌工作的可靠性,甚至促使机器提前报废。
摩擦和磨损
8
§1-4 摩擦与磨损 1. 磨损过程
磨
损 量
Q
磨 合
稳定磨损
剧烈磨损
0 t2
t1
时间t
0~t1 :磨合阶段 t1~t2:稳定磨损阶段
t2~~:剧烈磨损阶段
摩擦和磨损
9
§1-4 摩擦与磨损
1. 磨损过程
(1)磨合阶段
在运转初期,摩擦副的接触面积较小,单位面积上的实际载荷较 大,磨损速度较快。随着磨合的进行,实际接触面积不断增大,磨损
因此,零件的磨损是决定机器使用寿命的主要因素。
摩擦和磨损
2
§1-4 摩擦与磨损
一、 摩擦
1. 定义:两物体的接触表面阻碍它们相对运动的机械阻力。 相互摩擦的两个物体称为摩擦副。
磨损及磨损原理-第二讲

碳钢微动疲劳时表面损伤疲劳裂 纹扩展 循环次数 104,×400
诊断:
只要断口具有疲劳破坏特
征,裂纹源发生于微动磨痕,
裂纹扩展呈现阶段性即可确
认为微动疲劳破坏。
磨损及磨损原理-第二讲
(2)微动疲劳曲线(交变应力与循环周次曲线)
评定材料微动疲劳性能 的主要方法是在微动条 件下测定其应力(s)— 循环数(N)曲线,称为 s—N曲线。
磨损及磨损原理-第二讲
微动磨损的发生过程:
微动磨损基本上属于粘着磨损和磨粒磨损的混合机理: • 载荷使微凸体产生粘着磨损,而往复运动引起断裂并产生磨
屑。微动与腐蚀通常是同时发生的,被称作微动腐蚀。
• 例如,当钢磨粒产生后,出生的磨粒表面被氧化成Fe2O3, 形成褐红色粉末,这些氧化颗粒具有研磨性,由于表面之间 的紧配合和小振幅往复运动(约为几十微米),界面接触没 有暴露的机会,因而磨粒很难逃逸出摩擦表面,后续的往复 运动就会产生磨粒磨损和氧化. 往复运动通常来自外部振动, 但多数情况是接触界面的某个表面承受周期应力(或疲劳) 的结果,这将引发早起疲劳裂纹而产生更大的微动磨损,称 为微动疲劳。
根据被氧化磨屑的颜色,往往可以断定是否发生微动 磨损。如被氧化的铁屑呈红色,被氧化的铝屑呈黑色,则
磨损及磨损原理-第二讲
振动时就会引起磨损。
左图为303不 锈钢轴表面产 生微动腐蚀后 的照片。
在外观上,微动磨损的表面特 征是黑色金属上有褐红色斑点且 临近区域被抛光,因为硬质铁氧 化体磨屑具有研磨作用。
种复合型式的磨损。在有振动的机械中,螺纹联接、花键 联接和过盈配合联接等都容易发生微动磨损。
微动磨损的机理:摩擦表面间的法向压力使表面上的 微凸体粘着。粘合点被小振幅振动剪断成为磨屑,磨屑接 着被氧化。被氧化的磨屑在磨损过程中起着磨粒的作用, 使摩擦表面形成麻点或虫纹形伤疤。这些麻点或伤疤是应 力集中的根源。
摩擦学原理第章磨损理论
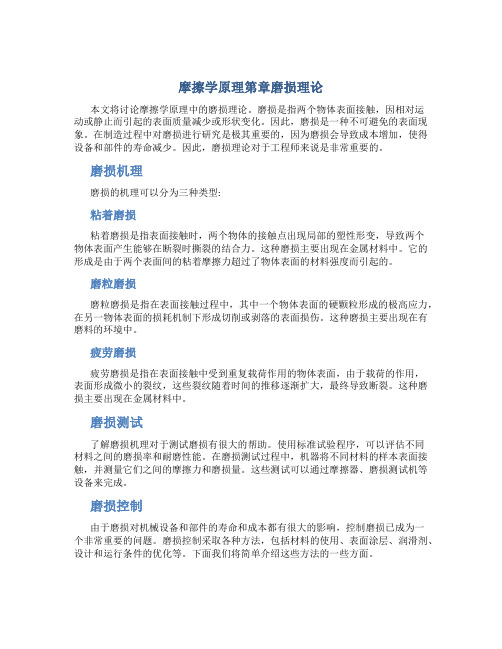
摩擦学原理第章磨损理论本文将讨论摩擦学原理中的磨损理论。
磨损是指两个物体表面接触,因相对运动或静止而引起的表面质量减少或形状变化。
因此,磨损是一种不可避免的表面现象。
在制造过程中对磨损进行研究是极其重要的,因为磨损会导致成本增加,使得设备和部件的寿命减少。
因此,磨损理论对于工程师来说是非常重要的。
磨损机理磨损的机理可以分为三种类型:粘着磨损粘着磨损是指表面接触时,两个物体的接触点出现局部的塑性形变,导致两个物体表面产生能够在断裂时撕裂的结合力。
这种磨损主要出现在金属材料中。
它的形成是由于两个表面间的粘着摩擦力超过了物体表面的材料强度而引起的。
磨粒磨损磨粒磨损是指在表面接触过程中,其中一个物体表面的硬颗粒形成的极高应力,在另一物体表面的损耗机制下形成切削或剥落的表面损伤。
这种磨损主要出现在有磨料的环境中。
疲劳磨损疲劳磨损是指在表面接触中受到重复载荷作用的物体表面,由于载荷的作用,表面形成微小的裂纹,这些裂纹随着时间的推移逐渐扩大,最终导致断裂。
这种磨损主要出现在金属材料中。
磨损测试了解磨损机理对于测试磨损有很大的帮助。
使用标准试验程序,可以评估不同材料之间的磨损率和耐磨性能。
在磨损测试过程中,机器将不同材料的样本表面接触,并测量它们之间的摩擦力和磨损量。
这些测试可以通过摩擦器、磨损测试机等设备来完成。
磨损控制由于磨损对机械设备和部件的寿命和成本都有很大的影响,控制磨损已成为一个非常重要的问题。
磨损控制采取各种方法,包括材料的使用、表面涂层、润滑剂、设计和运行条件的优化等。
下面我们将简单介绍这些方法的一些方面。
材料的选择材料的选择对于磨损控制至关重要。
选择适合特定应用的材料,可以延长生命周期,增加效率,降低维护成本。
通常使用高硬度、高耐磨损的金属、陶瓷和聚合物等材料来提高材料的耐磨性能。
表面涂层涂层是一种能够提高材料表面耐磨性能和摩擦系数的方法。
涂层可以使材料表面粗糙度减小,并降低摩擦力。
常用的涂层材料有核化镀层、磷化处理和高分子膜等。
(设备管理)设备的磨损保养讲义

设备的磨损设备在使用(或闲置)过程中会产生磨损。
磨损有两种形式:一种是有形磨损,亦称物质磨损或物质损耗;一种是无形磨损,也称精神磨损或经济磨损。
无论有形磨损还是无形磨损,其结果都会造成经济损失。
为了减少设备磨损和在设备磨损后及时进行补偿,就必须首先弄清产生磨损的原因和磨损的规律,以便采取相应的技术、组织、经济措施。
一、产生磨损的原因及其规律(一)产生磨损的原因及其规律设备无论在使用或是在闲置过程中,都会产生磨损。
磨损,即设备在实物形态上的磨损。
设备在运转使用中,作相互运动的零、部件的表面,在力的作用下,因摩擦而产生各种复杂的变化,使表面磨损、剥落和形态改变,以及由于物理、化学的原因引起零、部件疲劳、腐蚀和老化等等。
设备使用过程中的有形磨损,既有正常磨损,又有因保管、使用不当和因受自然力的腐蚀(工作环境恶劣所致)而引起的非正常磨损。
这种磨损的结果,通常表现为:(1)使组成设备的各零、部件的原始尺寸改变。
当磨损到一定程度时,甚至会改变零、部件的几何形状。
(2)使零、部件之间的相互配合性质改变,导致传动松动,精度和工作性能下降。
(3)零件损坏,甚至因个别零件的损坏而引起与之相关联的其他零件的损坏,导致整个部件损坏,造成严重事故。
设备在闲置过程中,自然力的作用(如油封油质中的腐蚀性介质的侵蚀,空气中的水分和有害气体的侵蚀等等)是产生磨损的主要原因,如果保管不善,缺乏必要的维护保养措施,就会使设备受腐蚀,随着时间的延长,腐蚀面和深度不断扩大、加深,造成精度和工作能力自然丧失,甚至因锈蚀严重而报废。
在一般情况下,设备在使用过程中,零、部件的磨损都有一定规律,大致可分为三个阶段:第一阶段是初期磨损阶段(也称磨合磨损阶段)。
在这个阶段,设备各零、部件表面的宏观几何形状和微观几何形状(粗糙度)都要发生明显的变化。
这种现象的产生,原因是零件在加工、制造过程中,无论经何种精密加工,其表面仍有一定粗糙度。
当互相配合作相对运动时,如粗糙表面由于摩擦而磨损。
哈工大摩擦磨损理论 第六章 磨损1-金属1

图6-6 钢(HB223)的磨损常数和平均压力的关系曲线
图6-7 表面龟裂
3.影响粘着磨损的因素
影响粘着磨损的主要因素有,载荷、添加剂、摩擦副材料的组合、速 度和温度等。载荷和添加剂对粘着磨损的影响在第五章中已有初步介绍, 这里主要介绍其它因素对粘着磨损的影响。 1)摩擦副材料组合的影响 摩擦的相容性:通常,将一定的配对材料在发生摩擦和磨损时抵抗粘 着的性能称为摩擦的相容性。如果摩擦副在工作过程中具有低摩擦、高耐 磨度的性能,则摩擦的相容性好,反之则摩擦的相容性差。 冶金相容性:两种金属在固态能互相溶解的性能称为金属的冶金相容 性。金属间能互溶的材料,其冶金相容性好。 一般来说,相同金属或晶格类型、晶格间距、电子密度、电化学性能 相近的金属的冶金相容性好; 冶金相容性好的金属组合,其摩擦相容性就差,即磨损增大。 例如,铅、锡、铜和铟与铁的冶金相容性差,因此这四种材料可作为 滑动轴承耐磨材料的基础金属。
疲劳磨损 (接触疲劳)
齿轮副、滚 动轴承疲劳
曲轴轴颈的 氧化磨损; 化工设备中 的零件表面 飞机操纵杆 花键、销子 燃气轮机叶 片遭受石英 砂粒的侵蚀
腐蚀磨损
微动磨损
冲蚀磨损
第二节 金属的磨损
一、粘着磨损
当摩擦表面有相对运动时,由于粘结,使接触表面的材料从一个表面转 移到另一个表面的现象,称为粘着磨损。
相当于式(6-1)中的 C 值,由此可源自阿查得给常数 C 值 以更明确的定义。
表 6- 3 各种材料组合的
k
值
材 料 组 合
k
160×10-3
45×10-3
锌对锌
低碳钢对低碳钢
铜对铜
不锈钢对不锈钢
32×10-3
21×10-3
铜在低碳钢上滑动
第6章 磨损理论

微动磨损
定义:相对接触的两个固体表面因微幅振 动(振幅<100μm)所产生的磨损。 发生部位:联接件:轴颈、螺栓联接、键 槽、花键、金属密封、离合器。 现象:表面产生疲劳裂纹。 磨损机理:
微动磨损是因微振产生的腐蚀、粘着、磨料和 疲劳等的一种综合磨损过程。
磨损机理
周期性的微振动
接触变形 氧化磨损 磨 磨粒磨损 粘着磨损 屑
.
弹性接触
d
.
K pV E p / R p
' 1 2
'
P为名义压力 ,V为滑动速度。 磨损率与pV成正比,选择材料参考pV系数值
防止和减轻粘着磨损的措施
1 合理选择摩擦副材料
脆性材料比塑性材料的抗粘着能力高。
宜选用互溶性小的金属,不要选用同种或晶格 类型相近的金属。Al,Sn,Cu,In与Fe的互溶 差,可作滑动轴承的基材。
Hm /Ha>1.3,材料耐磨性不再提高,低磨损区 Hm /Ha<1.25,K将随Ha /Hm的2.5次幂而下降
Ha K 0.57 K 0 Hm
2.5
增加金属材料的表面硬度,可增加其耐磨性。
硬度、粒径对磨损的影响
硬度
压力
疲劳磨损
定义:材料表面在循环接触应力的作用下,萌 生裂纹,导致产生片状或颗粒的磨屑,表面形 成 豆状凹坑、麻点,这种磨损称为疲劳磨损。 基本类型
磨损机理
磨损过程
粘着——剪切——再粘着——再剪切的循环
阿查德磨损定律:
W =KWL/HS VS材料磨损量与滑动距离成正比 式中: WVS 、Wvh分别为软、硬表面 材料磨损量与载荷成正比 的磨损体积量, W 软材料磨损与其硬度成反比 K, ,L分别为磨损系数,载荷和滑动长 度, Hs,Hh分别为软、硬表面布氏硬度