8第三章催化加氢-2一氧化碳加氢合成甲醇
甲醇合成的工艺方法介绍

甲醇合成的工艺方法介绍自1923年开始工业化生产以来,甲醇合成的原料路线经历了很大变化。
20世纪50年代以前多以煤和焦碳为原料;50年代以后,以天然气为原料的甲醇生产流程被广泛应用;进入60 年代以来,以重油为原料的甲醇装置有所发展。
对于我国,从资源背景来看,煤炭储量远大于石油、天然气储量,随着世界石油资源的紧缺、油价的上涨和我国大力发展煤炭洁净利用技术的背景下,在很长一段时间内煤是我国甲醇生产最重要的原料。
下面简要介绍一下甲醇生产的各种方法。
按生产原料不同可将甲醇合成方法分为合成气(CO+H2方法和其他原料方法。
一、合成气(CO+H2生产甲醇的方法以一氧化碳和氢气为原料合成甲醇工艺过程有多种。
其发展的历程与新催化剂的应用,以及净化技术的进展是分不开的。
甲醇合成是可逆的强放热反应,受热力学和动力学控制,通常在单程反应器中,CO和CO2的单程转化率达不到100%,反应器出口气体中,甲醇含量仅为6~12%,未反应的CO、CO2和H2需与甲醇分离,然后被压缩到反应器中进入一步合成。
为了保证反应器出口气体中有较高的甲醇含量,一般采用较高的反应压力。
根据采用的压力不同可分为高压法、中压法和低压法三种方法。
1、高压法即用一氧化碳和氢在高温(340~420℃高压(30.0~50.0MPa下使用锌-铬氧化物作催化剂合成甲醇。
用此法生产甲醇已有八十多年的历史,这是八十年代以前世界各国生产甲醇的主要方法。
但高压法生产压力过高、动力消耗大,设备复杂、产品质量较差。
其工艺流程如图所示。
经压缩后的合成气在活性炭吸附器1中脱除五羰基碳后,同循环气一起送入管式反应器2中,在温度为350℃和压力为30.4MPa下,一氧化碳和氢气通过催化剂层反应生成粗甲醇。
含粗甲醇的气体经冷却器冷却后,迅速送入粗甲醇分离器3中分离,未反应的一氧化碳与氢经压缩机压缩循环回管式反应器2。
冷凝后的粗甲醇经粗甲醇储槽4进入精馏工序,在粗分离塔5顶部分离出二甲醚和甲酸甲酯及其他低沸点不凝物,重组分则在精分离塔6中除去水和杂醇,得到精制的甲醇。
甲醇合成原理方法与工艺

甲醇合成原理方法与工艺图1煤制甲醇流程示意图煤气经过脱硫、变换,酸性气体脱除等工序后,原料气中的硫化物含量小于0.1mg/m3。
进入合成气压缩机,经压缩后的工艺气体进入合成塔,在催化剂作用下合成粗甲醇,并利用其反应热副产3.9MPa中压蒸汽,降温减压后饱和蒸汽送入低压蒸汽管网,同时将粗甲醇送至精馏系统。
一、甲醇合成反应机理自CO加氢合成甲醇工业化以来,有关合成反应机理一直在不断探索和研究之中。
早期认为合成甲醇是通过CO在催化剂表面吸附生成中间产物而合成的,即CO是合成甲醇的原料。
但20世纪70年代以后,通过同位素示踪研究,证实合成甲醇中的原子来源于CO2,所以认为CO2是合成甲醇的起始原料。
为此,分别提出了CO和CO2合成甲醇的机理反应。
但时至今日,有关合成机理尚无定论,有待进一步研究。
为了阐明甲醇合成反应的模式,1987年朱炳辰等对我国C301型铜基催化剂,分别对仅含有CO或CO2或同时含有CO和CO2三种原料气进行了甲醇合成动力学实验测定,三种情况下均可生成甲醇,试验说明:在一定条件下,CO和CO2均可在铜基催化剂表面加氢生成甲醇。
因此基于化学吸附的CO连续加氢而生成甲醇的反应机理被人们普遍接受。
对甲醇合成而言,无论是锌铬催化剂还是铜基催化剂,其多相(非匀相)催化过程均按下列过程进行:①扩散——气体自气相扩散到气体一催化剂界面;②吸附——各种气体组分在催化剂活性表面上进行化学吸附;③表面吸附——化学吸附的气体,按照不同的动力学假说进行反应形成产物;④解析——反应产物的脱附;⑤扩散——反应产物自气体一催化剂界面扩散到气相中去。
甲醇合成反应的速率,是上述五个过程中的每一个过程进行速率的总和,但全过程的速率取决于最慢步骤的完成速率。
研究证实,过程①与⑤进行得非常迅速,过程②与④的进行速率较快,而过程③分子在催化剂活性界面的反应速率最慢,因此,整个反应过程的速率取决于表面反应的进行速率。
提高压力、升高温度均可使甲醇合成反应速率加快,但从热力学角度分析,由于CO、C02和H2合成甲醇的反应是强放热的体积缩小反应,提高压力、降低温度有利于化学平衡向生成甲醇的方向移动,同时也有利于抑制副反应的进行。
甲醇的工艺流程
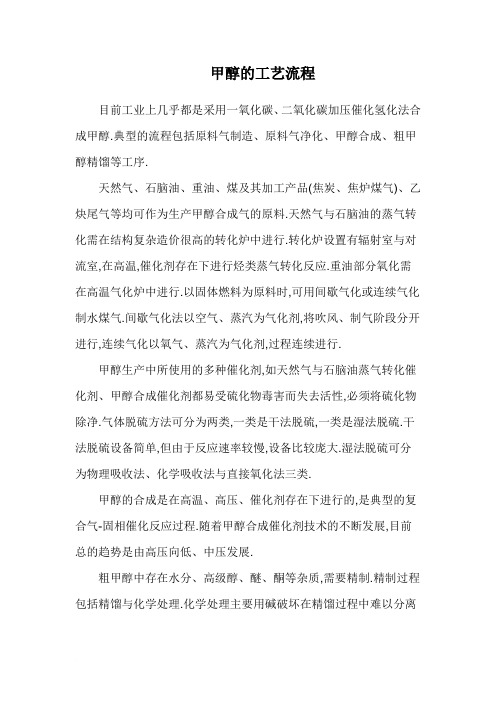
甲醇的工艺流程目前工业上几乎都是采用一氧化碳、二氧化碳加压催化氢化法合成甲醇.典型的流程包括原料气制造、原料气净化、甲醇合成、粗甲醇精馏等工序.天然气、石脑油、重油、煤及其加工产品(焦炭、焦炉煤气)、乙炔尾气等均可作为生产甲醇合成气的原料.天然气与石脑油的蒸气转化需在结构复杂造价很高的转化炉中进行.转化炉设置有辐射室与对流室,在高温,催化剂存在下进行烃类蒸气转化反应.重油部分氧化需在高温气化炉中进行.以固体燃料为原料时,可用间歇气化或连续气化制水煤气.间歇气化法以空气、蒸汽为气化剂,将吹风、制气阶段分开进行,连续气化以氧气、蒸汽为气化剂,过程连续进行.甲醇生产中所使用的多种催化剂,如天然气与石脑油蒸气转化催化剂、甲醇合成催化剂都易受硫化物毒害而失去活性,必须将硫化物除净.气体脱硫方法可分为两类,一类是干法脱硫,一类是湿法脱硫.干法脱硫设备简单,但由于反应速率较慢,设备比较庞大.湿法脱硫可分为物理吸收法、化学吸收法与直接氧化法三类.甲醇的合成是在高温、高压、催化剂存在下进行的,是典型的复合气-固相催化反应过程.随着甲醇合成催化剂技术的不断发展,目前总的趋势是由高压向低、中压发展.粗甲醇中存在水分、高级醇、醚、酮等杂质,需要精制.精制过程包括精馏与化学处理.化学处理主要用碱破坏在精馏过程中难以分离的杂质,并调节PH.精馏主要是除去易挥发组分,如二甲醚、以及难以挥发的组分,如乙醇高级醇、水等.甲醇生产的总流程长,工艺复杂,根据不同原料与不同的净化方法可以演变为多种生产流程.下面简述高压法、中压法、低压法三种方法及区别高压法高压工艺流程一般指的是使用锌铬催化剂,在300—400℃,30MPa高温高压下合成甲醇的过程.自从1923年第一次用这种方法合成甲醇成功后,差不多有50年的时间,世界上合成甲醇生产都沿用这种方法,仅在设计上有某些细节不同,例如甲醇合成塔内移热的方法有冷管型连续换热式和冷激型多段换热式两大类,反应气体流动的方式有轴向和径向或者二者兼有的混合型式,有副产蒸汽和不副产蒸汽的流程等.近几年来,我国开发了25-27MPa压力下在铜基催化剂上合成甲醇的技术,出口气体中甲醇含量4%左右,反应温度230-290℃.中压法中压法是在低压法研究基础上进一步发展起来的,由于低压法操作压力低,导致设备体积相当庞大,不利于甲醇生产的大型化.因此发展了压力为10MPa左右的甲醇合成中压法.它能更有效地降低建厂费用和甲醇生产成本.例如ICI公司研究成功了51-2型铜基催化剂,其化学组成和活性与低压合成催化剂51-1型差不多,只是催化剂的晶体结构不相同,制造成本比51-1型高贵.由于这种催化剂在较高压力下也能维持较长的寿命,从而使ICI公司有可能将原有的5MPa的合成压力提高到l0MPa,所用合成塔与低压法相同也是四段冷激式,其流程和设备与低压法类似.低压法ICl低压甲醇法为英国ICl公司在1966年研究成功的甲醇生产方法.从而打破了甲醇合成的高压法的垄断,这是甲醇生产工艺上的一次重大变革,它采用51-1型铜基催化剂,合成压力5MPa.ICl法所用的合成塔为热壁多段冷激式,结构简单,每段催化剂层上部装有菱形冷激气分配器,使冷激气均匀地进入催化剂层,用以调节塔内温度.低压法合成塔的型式还有联邦德国Lurgi公司的管束型副产蒸汽合成塔及美国电动研究所的三相甲醇合成系统.70年代,我国轻工部四川维尼纶厂从法国Speichim公司引进了一套以乙炔尾气为原料日产300吨低压甲醇装置(英国ICI专利技术).80年代,齐鲁石化公司第二化肥厂引进了联邦德国Lurge公司的低压甲醇合成装置.编辑本段甲醇的具体生产方法1. 天然气制甲醇的生产方法天然气是制造甲醇的主要原料.天然气的主要组分是甲烷,还含有少量的其他烷烃、烯烃与氮气.以天然气生产甲醇原料气有蒸汽转化、催化部分氧化、非催化部分氧化等方法,其中蒸汽转化法应用得最广泛,它是在管式炉中常压或加压下进行的.由于反应吸热必须从外部供热以保持所要求的转化温度,一般是在管间燃烧某种燃料气来实现,转化用的蒸汽直接在装置上靠烟道气和转化气的热量制取.由于天然气蒸汽转化法制的合成气中,氢过量而一氧化碳与二氧化碳量不足,工业上解决这个问题的方法一是采用添加二氧化碳的蒸汽转化法,以达到合适的配比,二氧化碳可以外部供应,也可以由转化炉烟道气中回收.另一种方法是以天然气为原料的二段转化法,即在第一段转化中进行天然气的蒸汽转化,只有约1/4的甲烷进行反应,第二段进行天然气的部分氧化,不仅所得合成气配比合适而且由于第二段反应温度提高到800℃以上,残留的甲烷量可以减少,增加了合成甲醇的有效气体组分.天然气进入蒸汽转化炉前需进行净化处理清除有害杂质,要求净化后气体含硫量小于0.1mL/m3.转化后的气体经压缩去合成工段合成甲醇.2. 煤、焦炭制甲醇的生产方法煤与焦炭是制造甲醇粗原料气的主要固体燃料.用煤和焦炭制甲醇的工艺路线包括燃料的气化、气体的脱硫、变换、脱碳及甲醇合成与精制.用蒸汽与氧气(或空气、富氧空气)对煤、焦炭进行热加工称为固体燃料气化,气化所得可燃性气体通称煤气是制造甲醇的初始原料气,气化的主要设备是煤气发生炉,按煤在炉中的运动方式,气化方法可分为固定床(移动床)气化法、流化床气化法和气流床气化法.国内用煤与焦炭制甲醇的煤气化——般都沿用固定床间歇气化法,煤气炉沿用UCJ炉.在国外对于煤的气化,目前已工业化的煤气化炉有柯柏斯-托切克(Koppers-Totzek)、鲁奇(Lurge)及温克勒(Winkler)三种.还有第二、第三代煤气化炉的炉型主要有德士古(Texaco)及谢尔-柯柏斯(Shell--Koppers)等.用煤和焦炭制得的粗原料气组分中氢碳比太低,故在气体脱硫后要经过变换工序.使过量的一氧化碳变换为氢气和二氧化碳,再经脱碳工序将过量的二氧化碳除去.原料气经过压缩、甲醇合成与精馏精制后制得甲醇.3.油制甲醇的生产方法工业上用油来制取甲醇的油品主要有二类:一类是石脑油,另一类是重油.原油精馏所得的220℃以下的馏分称为轻油,又称石脑油.以石脑油为原料生产合成气的方法有加压蒸汽转化法,催化部分氧化法、加压非催化部分氧化法、间歇催化转化法等.目前用石脑油生产甲醇原料气的主要方法是加压蒸汽转化法.石脑油的加压蒸汽转化需在结构复杂的转化炉中进行.转化炉设置有辐射室与对流室,在高温、催化剂存在下进行烃类蒸汽转化反应.石脑油经蒸汽转化后,其组成恰可满足合成甲醇之需要.既无需在转化前后补加二氧化碳或设二段转化,也无需经变换、脱碳调整其组成.重油是石油炼制过程中的一种产品,根据炼制方法不同,可分为常压重油、减压重油、裂化重油及它们的混合物.以重油为原料制取甲醇原料气有部分氧化法与高温裂解法两种途径.裂解法需在1400℃以上的高温下,在蓄热炉中将重油裂解,虽然可以不用氧气,但设备复杂,操作麻烦,生成炭黑量多.重油部分氧化是指重质烃类和氧气进行燃烧反应,反应放热,使部分碳氢化合物发生热裂解,裂解产物进一步发生氧化、重整反应,最终得到以H2、CO为主,及少量CO2、CH4的合成气供甲醇合成使用.重油部分氧化法所生成的合成气,由于原料重油中碳氢比高,合成气中一氧化碳与二氧化碳含量过量,需将部分合成气经过变换,使一氧化碳与水蒸气作用生成氢气与二氧化碳,然后脱除二氧化碳,以达到合成甲醇所需之组成.合成后的粗甲醇需经过精制,除去杂质与水,得到精甲醇.4.联醇生产方法与合成氨联合生产甲醇简称联醇,这是一种合成气的净化工艺,以替代我国不少合成氨生产用铜氨液脱除微量碳氧化物而开发的一种新工艺.联醇生产的工艺条件是在压缩机五段出口与铜洗工序进口之间增加一套甲醇合成的装置,包括甲醇合成塔、循环机、水冷器、分离器和粗甲醇贮槽等有关设备,工艺流程是压缩机五段出口气体先进人甲醇合成塔,大部分原先要在铜洗工序除去的一氧化碳和二氧化碳在甲醇合成塔内与氢气反应生成甲醇,联产甲醇后进入铜洗工序的气体一氧化碳含量明显降低,减轻了铜洗负荷,同时变换工序的一氧化碳指标可适量放宽,降低了变换的蒸汽消耗,而且压缩机前几段气缸输送的一氧化碳成为有效气体,压缩机电耗降低.联产甲醇后能耗降低较明显,可使每吨氨节电50kw.h,节省蒸汽0.4t,折合能耗为200万kJ.联醇工艺流程必须重视原料气的精脱硫和精馏等工序,以保证甲醇催化剂使用寿命和甲醇产品质量。
甲醇合成工艺过程及优化分析
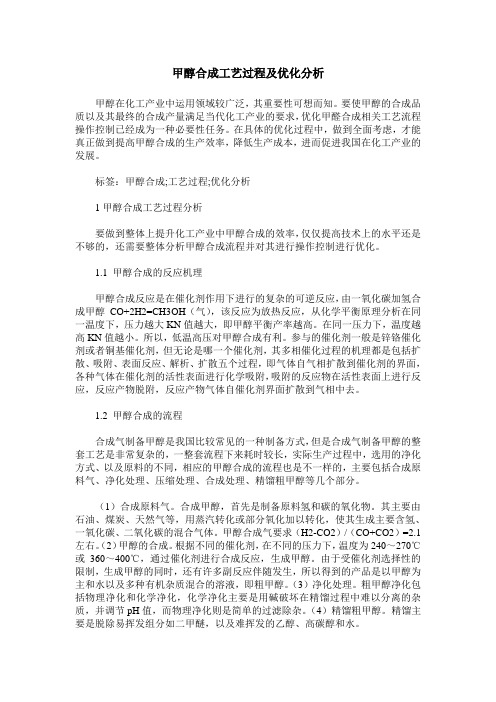
甲醇合成工艺过程及优化分析甲醇在化工产业中运用领域较广泛,其重要性可想而知。
要使甲醇的合成品质以及其最终的合成产量满足当代化工产业的要求,优化甲醛合成相关工艺流程操作控制已经成为一种必要性任务。
在具体的优化过程中,做到全面考虑,才能真正做到提高甲醇合成的生产效率,降低生产成本,进而促进我国在化工产业的发展。
标签:甲醇合成;工艺过程;优化分析1甲醇合成工艺过程分析要做到整体上提升化工产业中甲醇合成的效率,仅仅提高技术上的水平还是不够的,还需要整体分析甲醇合成流程并对其进行操作控制进行优化。
1.1 甲醇合成的反应机理甲醇合成反应是在催化剂作用下进行的复杂的可逆反应,由一氧化碳加氢合成甲醇CO+2H2=CH3OH(气),该反应为放热反应,从化学平衡原理分析在同一温度下,压力越大KN值越大,即甲醇平衡产率越高。
在同一压力下,温度越高KN值越小。
所以,低温高压对甲醇合成有利。
参与的催化剂一般是锌铬催化剂或者铜基催化剂,但无论是哪一个催化剂,其多相催化过程的机理都是包括扩散、吸附、表面反应、解析、扩散五个过程,即气体自气相扩散到催化剂的界面,各种气体在催化剂的活性表面进行化学吸附,吸附的反应物在活性表面上进行反应,反应产物脱附,反应产物气体自催化剂界面扩散到气相中去。
1.2 甲醇合成的流程合成气制备甲醇是我国比较常见的一种制备方式,但是合成气制备甲醇的整套工艺是非常复杂的,一整套流程下来耗时较长,实际生产过程中,选用的净化方式、以及原料的不同,相应的甲醇合成的流程也是不一样的,主要包括合成原料气、净化处理、压缩处理、合成处理、精馏粗甲醇等几个部分。
(1)合成原料气。
合成甲醇,首先是制备原料氢和碳的氧化物。
其主要由石油、煤炭、天然气等,用蒸汽转化或部分氧化加以转化,使其生成主要含氢、一氧化碳、二氧化碳的混合气体。
甲醇合成气要求(H2-CO2)/(CO+CO2)=2.1左右。
(2)甲醇的合成。
根据不同的催化剂,在不同的压力下,温度为240~270℃或360~400℃,通过催化剂进行合成反应,生成甲醇。
3.催化加氢

因溶剂对加氢反应速度有影响,对选择性也有
催化加氢用于合成有机产品外,还用于精制过程。
(1)合成有机产品
1.苯制环己烷 2.苯酚制环己醇 3. 丙酮制异丙醇
4.羧酸或酯制高级伯醇
Cr O RCOOH 2H 2 Cu RCH 2OH H 2O Cr O RCOOR 2H 2 Cu RCH 2OH R OH
回收氢
3.2 催化加氢反应的一般规律
一、热力学分析 二、催化剂
反应热效应 化学平衡 温度 压力 氢用量比
金属、骨架催化剂、金属氧化物、 金属硫化物、金属络合物 不饱和键、含氧、 含氮化合物、氢解 机理 动力学方程 温度(速度、选择性) 压力(气相、液相加氢) 溶剂
三、作用物的结构与反应速度
四、动力学及反应条件
5.以CO为原料,进行加氢反应,因催化剂的不同,可生成 不同有机产品。
CO 2H 2 CH 3OH nCO (2n 1)H 2 CnH2 n 2 nH2O
℃ ℃ ℃ ℃ ℃ ℃ ℃
合成汽油
6.己二腈合成己二胺 N C(CH2 )4 C N 4H2 骨架镍 H2 N(CH2 )6 NH2
A +H2
B
H2↑ ,优点:X↑ ,有利于移走反应热。 缺点:yB↓, 分离难,循环量大,能耗大
3.2.2催化剂
(1)作用
不改变反应平衡,只改变反应速度,降低反应
过程活化能,降低温度压力(设备投资降低)。
(2)考核指标
活性、选择性、操作条件、寿命、抗毒性、成本
(3)影响催化剂性能的主要因素
1.化学组成 活性组分、助催化剂、载体 2.结构 比表面、孔结构、晶型、表面性质 3.制备工艺 共沉淀、浸渍、离子交换、机械混合等
思考题全 (1)

第一章第一节1.什么叫烃类热裂解过程的一次反应和二次反应?答:一次反应:由原料烃类经热裂解生成乙烯和丙烯的反应。
二次反应:主要是指一次反应生成的乙烯,丙烯等低级烯烃进一步发生反应生成多种产物,甚至最后生成焦或碳2.简述一次裂解反应的规律性。
答:1) 同碳原子数的烷烃,C-H键能大于C-C键能,故断链比脱氢容易。
2) 碳链越长的烃分子越容易断链。
3) 烷烃的脱氢能力与分子结构有关。
叔氢最易脱去,仲氢次之,伯氢又次之。
4) 有支链的烃容易断链或脱氢。
3.烃类热裂解的一次反应主要有哪几个?烃类热裂解的二次反应主要有哪几个?答:一次反应有:1) 烃热裂解:脱氢反应、断链反应2) 环烷烃热裂解:开环反应3) 芳香烃热裂解:脱氢缩合反应、断侧链反应4) 烯烃热裂解:断链反应、脱氢反应二次反应主要有:1) 烯烃的裂解(即二次反应—断链)2) 烯烃的聚合、环化、缩合与生焦反应3) 烯烃的脱氢和加氢反应4) 烃分解生碳4. 什么叫焦,什么叫碳?结焦与生碳的区别有哪些?答:有机物在惰性介质中经高温裂解,释放出氢或其它小分子化合物生成碳,并非独个碳原子,而是以若干碳原子稠合形式的碳,称为生碳。
若产物中尚含有少量氢,碳含量约为95%以上,称为结焦。
结焦是在较低温度下﹙<1200K﹚通过芳烃缩合而成,生碳是在较高温度下﹙>1200K﹚通过生成乙炔的中间阶段,脱氢为稠和的碳原子。
5. 试述烃类热裂解的反应机理。
答:热裂解的自由基反应机理:C2H6→C2H4+H26. 什么叫一级反应?写出一级反应动力学方程式和以转化率表示的动力学方程式。
答:一级反应:反应速度与浓度的一次方成正比一级反应动力学方程式:r=-dc/dt=kc以转化率表示的动力学方程式:㏑[β/(1-α)]=ktβ—体积增大率,它随转化深度而β=裂解气体积(标准态)/原料气体积(标准态)第一章第二节1. 烃类裂解有什么特点?答:1) 高温(反应温度高,一般为800℃以上,最高快可达900℃以上)2) 强吸热反应3) 短停留时间4) 低烃分压2. 裂解供热方式有哪两种?答:直接供热和间接供热。
化工工艺学催化加氢甲醇幻灯片PPT
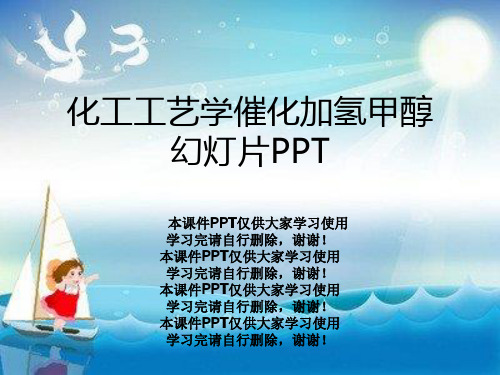
2021/5/23
《化工工艺学》第三章 催化加氢
21
3.用途
①甲醇+酸 → 酯+水 ②甲醇+氧气→甲醛 ③甲醇+NH3 → 甲胺、二甲胺、三甲胺④
甲醇 →醋酸(羰基合成) ⑤甲醇合成人造蛋白是很好的禽畜饲料。 ⑥作石油添加剂。
2021/5/23
《化工工艺学》第三章 催化加氢
22
4、技术要求(GB338-92)[?为
工业甲醇是无色、类似酒味的挥发性 液体。相对密度0.7914;熔点-93.9℃; 沸点65℃;折光率1.3288;动力粘度 (120℃时)0.56cp;膨胀系数(20℃ 时)0.001031;蒸汽压12.8KPa;蒸汽 密度1.1kg/m3.
能与水、乙醇、醚、苯酮类和其它有 机溶剂混合;能与多种化合物形成共沸物。
不同催化剂产物不同
2021/5/23
《化工工艺学》第三章 催化加氢
8
三.氢的来源
➢1.水电解,能耗高
➢2.石化厂副产物
a)催化重整 b)裂解制乙烯 c)炼焦气
➢3.烃转化制氢气
①水蒸气转化法: CH4+H2O≒ 3H2+CO
工艺流程(图) CO+H2O ≒ H2+CO2
2021/5/23 ②部分氧《化化工法工艺:学》第三章C催H化加4氢+O2 ≒
用Cu-Zn-Al氧化物作催化剂。
▪ 2021/5/233.中压法:《化在工工2艺4学0》第-三2章9催0化℃加氢,压力10-15M24 Pa,
三. CO加氢合成甲醇
1.原理:
➢ 主:CO+2H2 → CH3OH(g)+Q
➢ 副:CO2+3H2 → CH3OH(g)+H2O(g)
甲醇合成原理方法与工艺
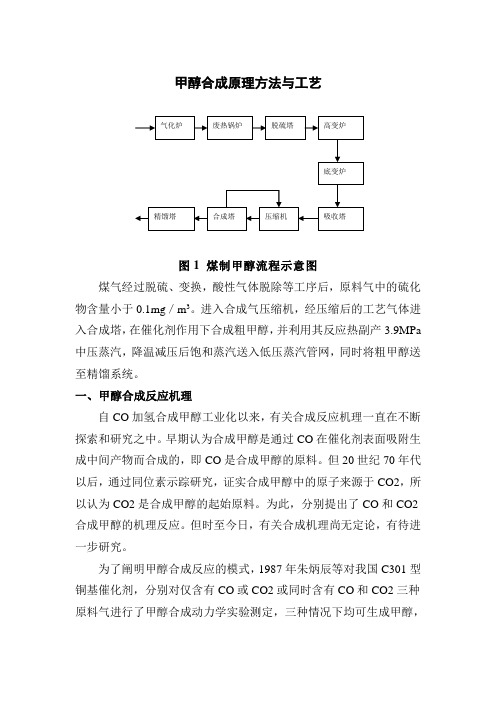
甲醇合成原理方法与工艺图1 煤制甲醇流程示意图煤气经过脱硫、变换,酸性气体脱除等工序后,原料气中的硫化物含量小于0.1mg/m3。
进入合成气压缩机,经压缩后的工艺气体进入合成塔,在催化剂作用下合成粗甲醇,并利用其反应热副产3.9MPa 中压蒸汽,降温减压后饱和蒸汽送入低压蒸汽管网,同时将粗甲醇送至精馏系统。
一、甲醇合成反应机理自CO加氢合成甲醇工业化以来,有关合成反应机理一直在不断探索和研究之中。
早期认为合成甲醇是通过CO在催化剂表面吸附生成中间产物而合成的,即CO是合成甲醇的原料。
但20世纪70年代以后,通过同位素示踪研究,证实合成甲醇中的原子来源于CO2,所以认为CO2是合成甲醇的起始原料。
为此,分别提出了CO和CO2合成甲醇的机理反应。
但时至今日,有关合成机理尚无定论,有待进一步研究。
为了阐明甲醇合成反应的模式,1987年朱炳辰等对我国C301型铜基催化剂,分别对仅含有CO或CO2或同时含有CO和CO2三种原料气进行了甲醇合成动力学实验测定,三种情况下均可生成甲醇,试验说明:在一定条件下,CO和CO2均可在铜基催化剂表面加氢生成甲醇。
因此基于化学吸附的CO连续加氢而生成甲醇的反应机理被人们普遍接受。
对甲醇合成而言,无论是锌铬催化剂还是铜基催化剂,其多相(非匀相)催化过程均按下列过程进行:①扩散——气体自气相扩散到气体一催化剂界面;②吸附——各种气体组分在催化剂活性表面上进行化学吸附;③表面吸附——化学吸附的气体,按照不同的动力学假说进行反应形成产物;④解析——反应产物的脱附;⑤扩散——反应产物自气体一催化剂界面扩散到气相中去。
甲醇合成反应的速率,是上述五个过程中的每一个过程进行速率的总和,但全过程的速率取决于最慢步骤的完成速率。
研究证实,过程①与⑤进行得非常迅速,过程②与④的进行速率较快,而过程③分子在催化剂活性界面的反应速率最慢,因此,整个反应过程的速率取决于表面反应的进行速率。
提高压力、升高温度均可使甲醇合成反应速率加快,但从热力学角度分析,由于CO、C02和H2合成甲醇的反应是强放热的体积缩小反应,提高压力、降低温度有利于化学平衡向生成甲醇的方向移动,同时也有利于抑制副反应的进行。
二氧化碳加氢制甲醇二氧化碳转化率
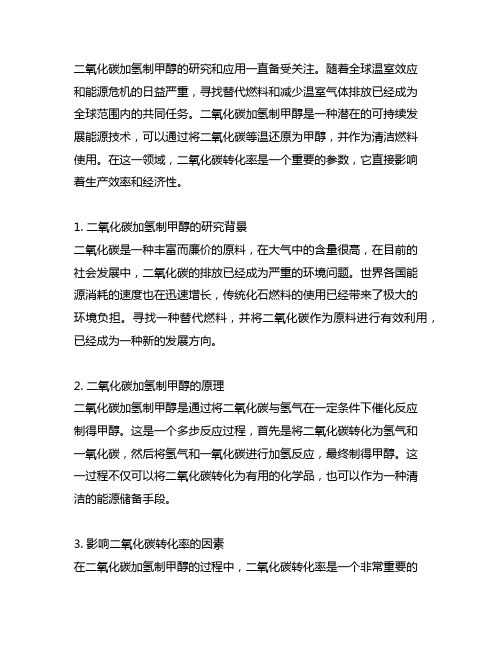
二氧化碳加氢制甲醇的研究和应用一直备受关注。
随着全球温室效应和能源危机的日益严重,寻找替代燃料和减少温室气体排放已经成为全球范围内的共同任务。
二氧化碳加氢制甲醇是一种潜在的可持续发展能源技术,可以通过将二氧化碳等温还原为甲醇,并作为清洁燃料使用。
在这一领域,二氧化碳转化率是一个重要的参数,它直接影响着生产效率和经济性。
1. 二氧化碳加氢制甲醇的研究背景二氧化碳是一种丰富而廉价的原料,在大气中的含量很高,在目前的社会发展中,二氧化碳的排放已经成为严重的环境问题。
世界各国能源消耗的速度也在迅速增长,传统化石燃料的使用已经带来了极大的环境负担。
寻找一种替代燃料,并将二氧化碳作为原料进行有效利用,已经成为一种新的发展方向。
2. 二氧化碳加氢制甲醇的原理二氧化碳加氢制甲醇是通过将二氧化碳与氢气在一定条件下催化反应制得甲醇。
这是一个多步反应过程,首先是将二氧化碳转化为氢气和一氧化碳,然后将氢气和一氧化碳进行加氢反应,最终制得甲醇。
这一过程不仅可以将二氧化碳转化为有用的化学品,也可以作为一种清洁的能源储备手段。
3. 影响二氧化碳转化率的因素在二氧化碳加氢制甲醇的过程中,二氧化碳转化率是一个非常重要的参数,它直接决定着甲醇的产量和产品质量。
影响二氧化碳转化率的因素主要包括反应条件、催化剂的选择和催化剂的性能等几个方面。
反应温度、压力、氢气/二氧化碳的摩尔比等条件都会对反应的效率产生重要的影响。
催化剂的选择和性能对二氧化碳转化率也有着至关重要的影响,其中催化剂的活性、选择性、稳定性等性能参数是影响二氧化碳转化率的关键因素。
4. 目前的研究进展针对二氧化碳加氢制甲醇过程中二氧化碳转化率的提高,国内外的研究者已经做出了大量的工作。
在反应条件方面,有学者通过优化反应条件,比如调节反应温度和压力,确定合适的氢气/二氧化碳摩尔比等方法,提高了反应的效率。
也有研究者专注于催化剂的研究和开发,设计了更有效的催化剂,并对其进行了系统的表征和评价,提高了二氧化碳转化率。
一氧化碳加氢制甲醇的催化剂研究

一氧化碳加氢制甲醇的催化剂研究1. 引言1.1 背景介绍传统的一氧化碳加氢制甲醇的催化剂主要是铜基催化剂,但铜基催化剂在高温下易发生结晶变化,导致活性降低。
寻找新型高效稳定的催化剂对提高一氧化碳加氢制甲醇的效率和产率至关重要。
本研究旨在探究不同类型催化剂在一氧化碳加氢制甲醇反应中的作用机制,并通过优化催化剂的设计和活性组分以及表面结构的特征分析,提高催化剂的稳定性和活性,从而为提高一氧化碳加氢制甲醇的产率和效率提供理论基础和技术支撑。
1.2 研究意义一氧化碳加氢制甲醇是一种重要的工业化学反应,能够实现二氧化碳的高效利用和可持续发展。
随着社会经济的快速发展,能源需求不断增加,化石燃料的消耗导致了二氧化碳排放的持续增加,加剧了全球变暖和环境污染。
寻找一种绿色、高效的方法将二氧化碳转化为有价值的化学品是至关重要的。
研究一氧化碳加氢制甲醇的催化剂不仅可以实现对二氧化碳的转化利用,还可以降低对传统石油资源的依赖。
通过研究催化剂的设计和优化,可以提高反应的选择性和产率,降低反应条件下的能耗和成本。
深入研究一氧化碳加氢制甲醇的催化剂具有重要的科学意义和工程应用前景。
通过对一氧化碳加氢制甲醇的催化剂研究,不仅可以解决能源和环境问题,还可以促进化学工业的可持续发展,对社会和经济具有重要的意义。
1.3 研究目的研究目的是为了寻找高效的催化剂,提高一氧化碳加氢制甲醇的反应活性和选择性。
通过系统研究不同催化剂对反应的影响,探索合适的催化剂设计和优化方法,以达到在较低温度和压力下制备高纯度甲醇的目的。
研究还旨在了解催化剂表面结构对反应性能的影响,从而为进一步优化催化剂设计提供理论依据和实验方向。
通过本研究,希望能为甲醇制备工艺的发展和催化剂设计提供新的思路和方法,促进相关领域的科学研究和工业应用。
2. 正文2.1 一氧化碳加氢制甲醇的反应机理分析一氧化碳加氢制甲醇是一种重要的工业化学反应,其反应机理的研究对于催化剂的设计和优化至关重要。
甲醇合成工段设计

甲醇合成工段设计甲醇是一种重要的有机化合物,广泛应用于化工、医药、农药等领域。
甲醇合成是一项重要的工业过程,本文将对甲醇合成工段设计进行详细介绍。
甲醇合成的主要原料是一氧化碳和氢气,其反应式为CO+2H2→CH3OH。
甲醇合成的催化剂常使用氧化锌和铜,也可以加入一定量的铝、铁等元素。
甲醇合成主要分为三个工段:前处理工段、甲醇合成反应工段和后处理工段。
前处理工段主要用于净化原料气体,氧化锌和铝作为主要催化剂,主要用于除去原料气体中的硫化物、氯化物等杂质。
氧化锌可用于吸附并转化为不溶于液相的硫酸锌,铝主要用于催化氯化物分解。
此外,为了保证反应的正常进行,还需要对原料气体进行预热,提高反应速率。
甲醇合成反应工段是整个甲醇合成过程的核心部分。
反应器常使用固定床反应器或流化床反应器。
固定床反应器采用氧化锌和铝砂作为填料,催化剂为铜。
反应器内的温度和压力是影响甲醇合成反应速率和甲醇纯度的重要参数。
一般情况下,反应温度为200~300℃,压力为5~25MPa。
甲醇合成反应是一个放热反应,需要通过冷却装置散发出的热量进行控制。
后处理工段用于分离和纯化甲醇。
主要包括甲醇气液转化、分馏塔和甲醇净化等过程。
甲醇气液转化是将反应器中的气相甲醇转化为液体甲醇,一般采用低温、高压条件下进行。
分馏塔用于将混合物分离成不同成分的纯净产品,通常采用逐级分离的方式,使得每一级产生的纯度更高。
甲醇净化主要包括去除其中的水、酸、碱等杂质,以提高甲醇的纯度。
在甲醇合成工段设计中,需要考虑以下因素:原料气体净化、反应器的选择和设计、反应温度和压力控制、反应热的散发和控制、甲醇的分离和纯化等。
此外,还需要考虑安全性、经济性等因素,以确保工段的可靠运行和高效生产。
总之,甲醇合成工段设计需要综合考虑多个因素,以确保甲醇合成反应的高效、稳定进行。
通过前处理、反应和后处理工段的合理设计,可以实现甲醇的高纯度分离和纯化,从而满足甲醇在化工、医药、农药等领域的广泛应用需求。
二氧化碳加氢制甲醇路径
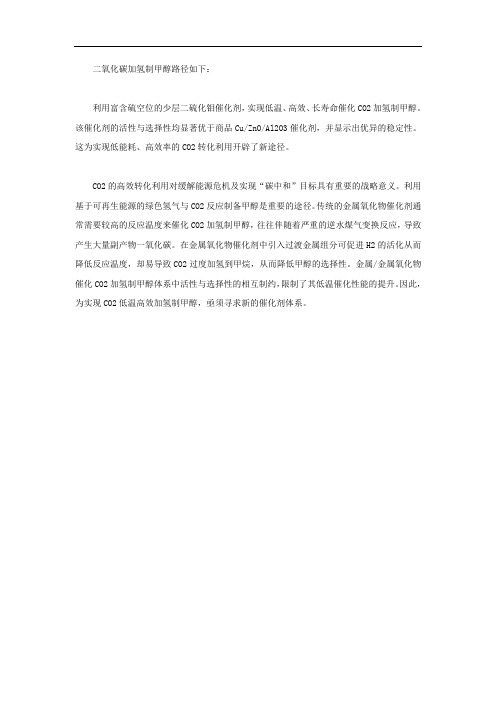
二氧化碳加氢制甲醇路径如下:
利用富含硫空位的少层二硫化钼催化剂,实现低温、高效、长寿命催化CO2加氢制甲醇。
该催化剂的活性与选择性均显著优于商品Cu/ZnO/Al2O3催化剂,并显示出优异的稳定性。
这为实现低能耗、高效率的CO2转化利用开辟了新途径。
CO2的高效转化利用对缓解能源危机及实现“碳中和”目标具有重要的战略意义。
利用基于可再生能源的绿色氢气与CO2反应制备甲醇是重要的途径。
传统的金属氧化物催化剂通常需要较高的反应温度来催化CO2加氢制甲醇,往往伴随着严重的逆水煤气变换反应,导致产生大量副产物一氧化碳。
在金属氧化物催化剂中引入过渡金属组分可促进H2的活化从而降低反应温度,却易导致CO2过度加氢到甲烷,从而降低甲醇的选择性。
金属/金属氧化物催化CO2加氢制甲醇体系中活性与选择性的相互制约,限制了其低温催化性能的提升。
因此,为实现CO2低温高效加氢制甲醇,亟须寻求新的催化剂体系。
甲醇合成工艺

第一章概述甲醇的用途及在化学工业中的地位甲醇俗称“木精”,是重要的有机化工产品,也是重要的有机化工原料,其分子式为CHOH,是碳化工的基础;甲醇产品除少量直接用于溶剂,抗凝剂和燃料外,绝大多数被用于3生产甲醛,农药,纤维,医药,涂料等;长期以来,人们一直把甲醇作为农药、染料、医药等工业的原料;随着科学技术的不断发展与进步,突破了甲醇只作传统原料的范围,甲醇的应用领域不断地被开发出来,广度与深度正在发生深刻变化;随着甲醛等下游产品的不断开发,甲醇在化学工业中的作用必将越来越重要1;甲醇市场的状况及建厂的可行性近几十年来,由于传统加工工业的发展和世界能源结构的变化,以甲醇为原料的新产品的不断开发,世界对甲醇的生产和需求量都大幅增加,表是世界甲醇市场状况,表是国内甲醇市场状况;表世界甲醇生产能力及消耗量及开工率Table World methyl alcohol productivity and consumption, utilization of capacity 年度1987 1991 1993 1995 2000 2020 生产能力万T/年1999 2300 2470 2600 5000 20000总消耗量万T/年1718 2010 2141 2390开工率 % 86 87 92表国内甲醇生产能力及消耗量Table Domestic methyl alcohol productivity and consumption年度1985 1987 1990 1994 1995 2000 生产能力万T/年69生产量万T/年100消耗量120 200 根据预测,世界范围内的生产与需求将持续发展,主要原因是:甲醇下游产品市场的扩大、甲醇作为燃料的使用将大大增加2;甲醇的性质1.3.1一般性状甲醇蒸汽在空气中的浓度随温度的升高而迅速增大;空气中甲醇蒸汽的最高允许浓度为L;甲醇具有明显的麻醉性,甲醇对呼吸道和粘膜有强烈的刺激作用,流经皮肤也能使人发生中毒迹象3;常温常压下,甲醇是易挥发,易燃的无色液体,具有类似酒精的气味;甲醇能与水任意比混溶,但不能形成共沸物,故可用分馏的方法分离甲醇和水;甲醇是良好的有机溶剂,能溶解多种树脂,但不能溶解脂肪;甲醇蒸汽能与空气形成爆炸性混合物,爆炸极限为~%V,燃烧时为蓝色火焰;甲醇比水轻,有很强的毒性,误饮能导致眼睛失明,甚至死亡;1.3.2甲醇的物理性质①甲醇的物理常数如下表所示表甲醇的物理常数Table Thephysicsdateofmethanol项目数值项目数值沸点64.5℃~64.7℃膨胀系数1/℃凝固点-97℃~-97.8℃表面张力0.00221kg/m20 ℃自燃点473℃~461℃蒸汽压力-44℃相对密度20℃-20℃闪点12℃~16℃0℃粘度液体:20℃气体:65℃10℃ 64.5℃折光系数20 ℃100℃ ②甲醇的热力学常数如下表所示表甲醇的热力学常数Table Thethermo-dynamice date of methanol1.3.3甲醇的化学性质甲醇不具酸性,也不具碱性,对酚酞和石蕊试液均呈中性;分子式CH3OH,分子量;项目数值项目数值临界压力蒸发潜热kg 临界温度240℃液体热容-25℃燃烧热mol25℃气体热容kg77℃①氧化反应完全氧化:CH3OH+23O2→CO2+2H2O+mol不完全氧化:CH3OH+21O2→HCHO+H2O+159kJ/mol②脱氢反应CH3OH→HCHO+mol ③与有机酸反应CH3OH+CH3COOH→CH3COOCH3+H2O④与无机酸反应CH3OH+HCl→CH3Cl+H2OCH3OH+H2SO4→CH3SO2OH+H2O⑤与氨反应生成甲胺CH3OH+NH3→CH3NH2+H2O+mol2CH3OH+NH3→CH32NH+2H2O+mol3CH3OH+NH3→CH33N+3H2O+mol⑥与苯作用生成甲苯CH3OH+C6H6→C6H5CH3+H2O⑦与CO 作用生成醋酸CH3OH+CO→CH3COOH⑧与乙炔作用CH3OH+C2H2→CH3OCHCH2⑨与金属Na作用2CH3OH+2Na→2CH3ONa+H2⑩与苯胺作用,生成二甲基苯胺2CH3OH+C6H5NH2→C6H5NCH32+2H2O甲醇发展历史1661年英国玻义耳BoyIe首次从木材干馏的液体产品中发现了甲醇,木材干馏成了制取甲醇最古老的方法,至今甲醇仍称木醇或木精;1834年,杜马Dumas和彼利哥Peligot 制得甲醇纯品;1857年法国贝特洛Berthelot用一氯甲烷为原料水解制得甲醇;化学合成法生产甲醇开始于1923年;德国巴登苯胺纯碱BASF公司首先建成了一套以为原料、年产300吨的高压法甲醇合成装置,在全世界开拓乐意合成气作为一种CO和H2工业合成原料的生产史;从20世纪20年代到60年代中期,世界各国甲醇合成装置都用高压法,采用锌铬催化剂;合成甲醇的原料路线在几十年中经历了很大变化;20世纪50年代前,甲醇生产多以煤和焦炭为原料,采用固定床气化的方法生产水煤气作为甲醇原料气;50年代以来,天然气和石油资源大量开采,由于天然气便于输送,适合于加压操作,可降低甲醇装置的投资与成本,在蒸汽转化技术发展的基础上,以煤为原料的甲醇生产流程被广泛采用,至今仍为甲醇生产的最主要原料;估计今后在相当长一段时间中,国外的甲醇仍以烃类原料为主;从发展趋势来看,今后以煤炭为原料生产甲醇的比例会上升,这是因为从世界能源结构分析,固体燃料的贮藏量远多于液体与气体,而煤又不能直接用作汽车、柴油机的燃料,必须通过加工为甲醇才能成为汽车、柴油机燃料;煤制甲醇作为液体燃料颇具吸引力,将成为其主要用途之一;由煤生成甲醇被称为煤的间接液化,是煤炭利用的重要方向;生产中的醇/氮比;90年代,上海焦化厂三联供工程中年产20万吨低压甲醇装置的建设和一些省市年产3~10万吨低压甲醇装置的建设,以及许多中、小氮肥厂联醇装且的投产,使我国甲醇生产跃上新的台阶;目前我国有甲醇生产企业200多家,主要集中在几个较大的生产企业,其产能均在10万吨/年左右;2005年1~11月,我国甲醇产量已达到万吨,同比增长%;进口量为万吨,同比增长%,出口量万吨,同比增长%;1~11月国内甲醇表观消费量已达到万吨,同比增长%;照此增长速度,预计全年甲醇产量有望达到570万吨,表观消费量将达到620万吨左右,产量和表观消费量仍呈稳步增加的趋势1;甲醇的生产方法合成甲醇1.5.1由CO和H2在加热压力下,在催化剂作用下合成甲醇;其中包括高压法340~用CO和H2420℃,30~50MPa,用Zn-Cr催化剂;中压法235~275℃,5MPa左右,用Cu-Zn-Al催化剂;低压法220~280℃,5MPa左右,用Cu-Zn-Cr催化剂及联醇220~270℃,10~13MPa;1.5.2其他合成方法①甲烷直接氧化法:在催化剂作用下发生,2CH4+O2→2CH3OH②液化石油气氧化法③煤气氧化法甲醇生产技术的发展趋势近年来,国外甲醇生产技术发展有以下几个趋向:原料路线多样化、生产规模大型化、合成压力从高压转为低压、多采用铜基催化剂、节能降耗,充分利用余热,降低能耗、过程控制自动、联合生产普遍化1第二章低压鲁奇法制甲醇的原理方法及流程反应方程式合成工段,5MPa下铜基催化剂作用下发生一系列反应主反应: CO+2H2→CH3OH+kmol副反应: 2CO+4H2→CH32O+H2O+kmolCO+3H2→CH4+ H2O+kmol4CO+8H2→C4H9OH+3H2O+kmolCO+H2→CO+kmol除副反应中第三个外,副反应的发生,都增大了CO的消耗量,降低了产率,故应尽量减少副反应;合成法反应机理本反应采用铜基催化剂,5MPa,250℃左右反应,清华大学高森泉,朱起明等认为其机理为吸附理论,反应模式为:H2+2e˙→2H˙CO+H→HCO˙HCO˙+H˙→H2CO˙˙H 2CO˙˙+2H˙→CH3OH+3e˙CH3OH˙→ CH3OH+ e˙前两个反应为控制,即吸附控制;由一氧化碳加氢合成甲醇,是一个可逆反应CO+2H2=CH3OH气反应物中有二氧化碳存在时,亦可发生下列反应CO2+3H2= CH3OH+H2O反应热效应:一氧化碳加氢合成甲醇是放热反应,在25℃时反应热△HT=h 常压下不同温度的反应热可按下式进行计算:△HT =+××10-6T3其中△HT—常压下合成甲醇的反应热,J/molT—开氏温度,K由上式计算得到不同温度下的反应表温度与焓值表Table and enthalpy value tables温度 K 298 573 473 573 673 773△H T97平衡常数由一氧化碳加氢合成甲醇的平衡常数Kf 与标准自由焓△θG T关系如下表示:K f =fCH3OH/ fco×fH22 =exp-△θG T/RT其中:△θG T-----标准自由焓T-----反应温度f----- 逸度由上式可以看出平衡常数Kf 只是温度的函数,当反应温度一定时,可以由△θG T值直接求出Kf 值;不同温度的△θG T与K f 值如下表:表温度的△θG T与K f 值表Table Temperatures △θG T and K f value table温度K △θG T J/mol K f温度K △θG T J/mol K f273 -29917 527450 623 51906 ×10-5373 -7367 673 63958 ×10-5473 16166 ×10-3 723 75967 ×10-6523 27925 ×10-2 773 88002 ×10-6573 39892 ×10-4结论:由上表中可以看出,随着温度的升高,自由焓△θG T增大,平衡常数变小,就说明在低温下反应对甲醇合成有用;由一氧化碳加氢合成甲醇,是一个可逆反应CO+2H2=CH3OH气对反应有KP =PCH3OH/PCO×PH22式中PCH3OH、PCO、PH2分别是CH3OH、CO及H2的分压 KN=NCH3OH/NCO×N H22,式中N CH3OH 、N CO 及N H 分别是CH 3OH 、CO 及H 2的摩尔分率 K Y =Y CH3OH /Y CO ×Y H2 ,式中Y CH3OH 、Y CO 及Y H2分别为CH 3OH 、CO 及H 2的逸度;表甲醇合成反应的平衡常数表Table Methyl alcohol building-up reactions balanced chart从表中可以看出不同温度下的平衡常数值,以及不同压力下的K P 和 K N 值,由表中K N 数据可以看出在同一温度下,压力越大K N 值越大,即甲醇平衡产率越高;在同一压力下,温度越高K N 值越小;所以从热力学观点来看,低温高压对甲醇合成有利;若反应温度高,则必须采用高压,才能有足够大的K N 值;降低反应温度,则所需的压力就可相应的降低;但是实际上还要考虑催化剂的活性温度及耐受程度6;铜基催化剂CuO 、ZnO 、Al 2O 3的组合铜基催化剂大多数采用共沉淀法制备,使用需进行还原,使用温度在280℃左右;温度过高会造成其失活;因此使用中应防止温度过大的波动;目前,国内有C-207系,C-301系和CNJ-202系;国外有英国的51-1型,前苏联的CHM-1型和BASF 等;资料显示,每吨催化剂约能生产500~600吨粗甲醇,催化剂成本中,催化剂占5~7%8;温度℃MPaY CH3OH Y CO Y H2 K f K Y K P K N 200×10-2×10-2×10-2×10-2×10-226 97 234 300×10-4×10-4×10-4×10-4×10-4 400×10-5×10-5 ×10-5×10-5×10-52.3.1造气工段 ①对甲醇原料气的要求 合理的氢碳比例要求f=H 2—CO 2/CO+CO 2=~用半水煤气为原料,氢过量,需要补加CO 2以适应以上要求;经脱硫、变换后,尚含有相当量的二氧化碳,CO CO 2之比太高,气体组成不符合=+-222CO CO CO H ~;甲醇合成的要求,而且经变换后,COS 、CS 2等有机硫转化为H 2S,也需在送往甲醇合成工序前预以清除;因此在甲醇生产总流程中必须设置脱除二氧化碳同时也可脱除残余硫化氢的工序,简称脱碳工序;合理的CO 和CO 2比例合成甲醇原料气中应保持一定量的CO 2,能促进铜基催化剂上甲醇合成的反应速率,使用铜基催化剂时原料气中CO 2应大于5%;CO/CO 2>2摩尔比,使放热减少,从而保持铜基催化剂,延长其寿命;原料气对毒物与杂质的要求原料气需净化,除去油,水,尘粒,羰基铁,氯化物,硫化物;其中主要是硫化物的危害较大,其危害大致有造成催化剂中毒、造成管道设备的羰基腐蚀、造成粗甲醇质量下降等,Lurgi 法要求原料气中硫的含量小于10;②造气的工艺流程普遍采用加压操作,同时水蒸气过量,以提高甲烷的转化率,反应温度为 800℃,压力2~3MPa,水/碳摩尔比为 ~;③原料气的净化以煤为原料制甲醇,原料气的净化实际就是一个脱硫的问题,脱硫的方法很多,本设计采用钴钼催化加氢和ZnO 吸收串联脱硫;钴钼催化加氢就是使有机硫化物转变为可被吸收的H 2S ;ZnO 吸收脱硫的实质为: H 2S+ZnO →ZnS+H 2O2.3.2甲醇合成工段 ①甲醇的合成合成工序配置:经过净化的原料气,经预热加压,于5Mpa 、220℃下,从上到下进入Lurgi 反应器,在铜基催化剂的作用下发生反应,出口温度为250℃左右,甲醇7%左右,因此,原料气必须循环,则合成工序配置原则为图;粗甲醇驰放气图合成合序配置原则The Figure Syntheses gathers the foreword disposition principle②甲醇的分离甲醇在高压下容易冷凝,基于这个原理,甲醇的分离采用冷凝分离法,高压下与液相甲醇呈平衡的气相甲醇含量随温度降低,压力增加而下降,表为不同温度下气相甲醇的饱和含量11;表 5MPa下不同温度气相甲醇的饱和含量%Table 5MPa different temperature gas phase methyl alcohol saturated content%T ℃0 10 20 30Y %由表可见,通过水冷水冷后气体温度为30℃左右,可以使气相甲醇含量下降到%5MPa,补充新鲜气后可使这一值下降到%以下,故分离甲醇只要水冷已足够,不需要氨冷,水冷后设分离器,并定期将冷凝下来的甲醇排入粗甲醇贮槽;③气体的循环气体在合成系统内的循环是依靠联合压缩机提供动力以克服流动阻力;④新鲜气的补充和惰性气的排放新鲜气在粗甲醇分离后补充,一般在联合压缩机出口处加入;在合成过程中,未反应的惰性气体累集在系统中,需要进行排放,该气体一般在压缩机前,甲醇分离器后排放6;图甲醇合成的工艺流程Figure Methyl alcohol synthesis technical process1.透平压缩机2.热交换器3.锅炉水预热器4.水冷却器5.甲醇合成塔6.汽包7.甲醇分离器8.粗甲醇贮槽这个流程是德国Lurgi公司开发的甲醇合成工艺,流程采用管壳式反应器,催化剂装在管内,反应热由管间沸腾水放走,并副产高压蒸汽,甲醇合成原料在离心式透平压缩机内加压到以1:5的比例混合循环,混合气体在进反应器前先与反应后气体换热,升温到220℃左右,然后进入管壳式反应器反应,反应热传给壳程中的水,产生的蒸汽进入汽包,出塔气温度约为250℃,含甲醇7%左右,经过换热冷却到40℃,冷凝的粗甲醇经分离器分离;分离粗甲醇后的气体适当放空,控制系统中的惰性气体含量;这部分空气作为燃料,大部分气体进入透平压缩机加压返回合成塔,合成塔副产的蒸汽及外部补充的高压蒸汽一起进入过热器加热到50℃,带动透平压缩机,透平后的低压蒸汽作为甲醇精馏工段所需热源13;第三章 甲醇合成生产工艺计算工艺计算作为化工工艺设计,工艺管道,设备的选择及生产管理,工艺条件选择的主要依据,对平衡原料,产品质量,选择最佳工艺条件,确定操作控制指标,合理利用生产的废料,废气,废热都有重要作用;3.1甲醇合成工艺流程概要合成系统是甲醇厂的核心车间,因为上游的很多工序一长串流程制取的新鲜合成气都是为合成反应要求而配备的,合成技术的变化必然影响全局;若在合成不能充分利用制取甲醇,不论是在物料和能量上都是巨大的损失;合成系统的设备和管路都是在高压下操作,为了安全,防漏,防爆, 对设备的设计和制造,以及生产操作都有很高的要求12;3.1.1甲醇合成流程主线因CO 、H 2 、CO 2在合成塔内反应不能达到平衡且单程转化率很低,出塔气体有大量为未反应的CO 、H 2 、CO 2,甲醇必须分离出系统才可以继续参与循环反应;甲醇合成流程主线方框图如下所示:图甲醇合成流程主线方框图合成分离循环机粗甲醇循环气新鲜气弛放气Figure Methyl alcohol synthesis flow master line block diagram 从图中可以看出主要合成工艺主要是合成,分离,及循环气压缩,三大核心过程组成,更进一步的过程都是在此基础上附加的反应辅助及维持系统的稳定而配备的,例如出塔气换热分离弛放气排放等过程组成;再进一步精细的过程即在此系统附加的仪表监控管道配制等;甲醇合成流程有很多种,但是最基本的步骤单元过程是共同具备的;3.1.2 原则流程简介新鲜气进入新鲜气压缩机,循环气进入循环气压缩机,生至所需压力,两股气体混合后进入塔外换热器与出合成塔的气体进行换热,换热至所需的压力进入甲醇合成塔进行反应,出塔的气体经换热后进入水冷却器,降至醇分所需的温度,并在醇分器中分离出粗甲醇,未反应的气体再次经过排放部分弛放气后,再次进入循环气压缩机增压后再次进行循环操作;由此可见:①甲醇合成流程采用的是循环流程,即分离出产品,未反应的气体再次参与反应,这一点与其他流程不同;②合成系统主要由两部分组成,即甲醇的合成与甲醇分离,前者在合成塔中完成,后者在一系列的传热与汽液分离设备中完成;③合成气流经过设备时,必有阻力,存在压降,使其压力逐渐降低,要其循环必须设循环压缩机升压;3.1.3流程探讨分析①采用循环流程的原因由于平衡和速率的限制,甲醇合成单程转化率很低,约4﹪ ~ 7﹪导致未反应的原料气较多;对甲醇合成而言较好的办法是,分离出甲醇后把未反应的气体返回合成塔重新利用;循环流程之所以必要是有“合成率低”与要求“原料气利用高”二者之间的矛盾是共同决定的;②关于新鲜气补入的位置最有利的位置是在合成塔的进口处,而不宜在合成塔出口或甲醇分离之前,以免甲醇分压降低,减少甲醇收率;循环机放在合成塔之前是最有利的因为在整个循环中,循环机出口压力最大,压力高对合成反应有利;③关于弛放气排放的位置采用循环流程的一个必然结果是惰性气体在系统中的积累;为了维持系统稳定必须排放部分弛放气,因为惰性气体不参与反应 但积累在系统中会降低有效合成气的分压,降低了甲醇合成速率,为此应该设放空管线,防空时应避免尽可能减少有效成分的损失,因此放空位置应选择循环中惰性气体浓度最大的地方,即醇分后应该是合适的9;甲醇生产的物料平衡计算已知 新鲜气中惰性气体含量8%出塔气中惰性气体含量%不含粗甲醇入塔气组分:CO CO 2 H 2 惰性气体% 3% % %粗醇组分摩尔百分比: 甲醇 二甲醚 丁醇 水分 93% % % % 设入塔气2n =100kmol合成塔中:副反应 4CO+8H 2→CH 32CHCH 2OH +3H 2O 2CO+4H 2→CH 32O+H 2O 主反应 CO+2H 2→CH 3OH CO 2+3H 2→CH 3OH+H 2O 以惰性成分为基准:解得 3n =设生成的甲醇为p n kmol,则粗甲醇中其他组分为: 异丁醇CH 32CHCH 2OH二甲醚CH 32O 水份H 2OCO 2生成的水份=p n p n p n p n 生成的甲醇=p n CO 生成的甲醇=p n对进出合成塔的各气体组分列物料平衡方程:则有100×%=3CO x +p n +4×p n +2×p n ①100×3%=23co x +p n ②23H 10061.7%=92.27x 80.003440.008620.9630.044np np np np ⨯+⨯+⨯+⨯+⨯③2233co 3123.3%H CO x xx ++=-④联立①、②、③、④解得p n =,3CO x =%,23co x =%,23H x =%甲醇产量3万吨/年,以8000小时计,则甲醇时产量为h 则入塔气量 V 2=100×3750/32×/=1033463/Nm h 出塔气量 V 3=×V 2=953573/Nm h 令V 1为新鲜气,V 4为循环气以惰性成分为基准:103346×﹪=﹪×V 4 + V 1 ×8﹪ ⑤ 以总物料为基准:103346= V 4 + V 1 ⑥ 联立⑤、⑥,解得 V 1=120823/Nm h V 4=912643/Nm h 驰放气、循环气组分与出塔气的相同,则有: 驰放气V 5=V 3-V 4=95357-91264=40933/Nm h103346×﹪= 91264×﹪+120823CO x ⑦103346×3﹪= 91264×﹪+1208221CO x ⑧103346×﹪= 91264×﹪+ 1208221H x ⑨联立解得:21H x =64%,21CO x =%,3CO x =%水煤气净化过程中,惰性组分流量不变,即V 0惰=V 1惰=V 1×8﹪=9673/Nm h 水煤气 V 0=967/﹪=125303/Nm h V 0 H2S =12530×﹪=3/Nm h 变换反应方程式:CO+H 2O →CO 2+H 2脱碳反应方程式:K 2CO 3+CO 2+H 2O →2KHCO 3 脱碳反应掉的CO2 V co 2脱==3/Nm h0CO V 3129=773220H V ①20CO V +7732-20H V = ② 2210.2%7.72%co co H x x x ++=-- ③12530×20H x = 20H V ④ 12530×0co x =0CO V ⑤ 12530×20co x =20CO V ⑥联立①、②、③、④、⑤、⑥,解得20H V =133103/Nm h 0CO V =47823/Nm h 20CO V =10993/Nm h 20H x =% 0co x =% 20co x =%年产3万吨甲醇物料平衡结果如下表年产3万吨甲醇物料平衡表Table Yearly produces 30,000 ton methyl alcohol balance sheet of materials物料单位组分合计COCO 2 H 2 惰性成分H 2S 水煤气V%100 Nm 3/h96712530 新鲜气V%64 8 100 Nm 3/h12082入塔气V% 3 100Nm3/h 103346 出塔气V% 100Nm3/h 95357 循环气V% 100Nm3/h 91264 驰放气V% 100Nm3/h 4093甲醇h甲醇的能量平衡计算已知:合成塔入塔气为220℃,出塔气为250℃,热损失以5%计,壳层走4MPa的沸水;查化工工艺设计手册得13,4MPa下水的气化潜热为kg,即kg,密度799.0kg/m3,水蒸气密度为19.18kg/m3,温度为250℃;入塔气热容见;表 5MPa,220℃下入塔气除CH3OH热容Table 5MPa,220℃ under enters the tower gas to eliminate CH3OH heat capacity组分流量:Nm3比热:kJ/kmol℃热量:kJ/℃COCO2H2N2ArCH4合计查得220℃时甲醇的焓值为kmol,流量为;所以:Q入=⨯4.2257.1537+⨯==kJ出塔气热容除CH3OH见表表 5MPa,220℃下出塔气除CH3OH热容Table 5MPa,220℃ under tower gas eliminate CH3OH heat capacity 组分流量:Nm3比热:kJ/kmol℃热量:kJ/℃COCO2H2N2ArCH4CH32O合计查得250℃时甲醇的焓值为kmol,流量为 Nm3所以:Q出=⨯4.229.19766+⨯= kJ由反应式得:Q反应=4.2233.18229⨯+4.2262.25⨯+4.22568.211⨯+4.2220204⨯+4.221.2116⨯⨯1000=+++⨯ kJQ热损失=Q入+Q出⨯5%= ⨯5%= kJ所以:壳程热水带走热量Q传= Q入+Q反应-Q出-Q热损失=+= kJ又:Q传=G热水r热水所以:G热水=99.171408.37462156=21843.8 kg/h即时产蒸气:18.198.21843=1138.88 m3第四章主要设备的选型设备是化工工艺运作的载体,选择合适的设备,对于提高生产率,降低原料,能量的消耗有着重要的作用;甲醇合成塔甲醇合成塔是合成甲醇最重要的核心设备,合成工序的“心脏”设备,它的设计好坏直接决定了合成的工艺水平;甲醇合成塔的内件的形式有很多种,在很长一段时间内甲醇合成塔和氨合成塔是共用的;因为二者在反应放热形式是一样的,只是甲醇合成放热量比合成氨大,温度的控制较为不易;下图是典型的三套管甲醇合成塔基本的构成:由简体、催化剂支承装置、换热构件和气体分布器等组成;甲醇合成反应是强放热过程,反应温度较高,可用高压、中压和低压不同的工艺;由于工艺及反应热的移出方法不同,有不同形式的合成塔1;图甲醇合成塔10Figure methyl alcohol synthetic tower1-催化剂 2-筒体 3-冷却管 4-换热器 5-分布器 6-环隙按冷却方法分为直接冷却的冷激式和间接冷却的冷管式及列管式合成塔;冷激式合成塔内部无换热构件,其反应床层分为若干绝热段,两段之间加入冷的原料气使反应气体直接冷却;冷管式合成塔的内部有换热构件,并把双套管置于催化剂层内,由原料气通过管壁间接带走反应热;列管式合成塔的结构类似管壳式换热器,反应热由管外的锅炉给水带走,同时产生高压蒸汽;不管何种类形式的合成塔内件,它的核心是催化剂框,它的设计好坏直接影响了合成塔的产量和消耗定额1;一个好的合成塔内件催化床的设计应有如下的要求:①能有效的移走反应热,合理的控制催化剂床层的温度分布,使其逼近最佳操作温度线,提高醇净值和催化剂的使用寿命②能保证气体均匀地通过催化剂层,阻力小,气体的处理量较大;③充分的利用高压空间,尽可能多装催化剂,提高容积利用系数;④操作稳定灵活,调节方便,能使用各种操作条件的变化;⑤能保证催化剂在升温,还原过程中操作正常,还原充分,尽可能提高催化反应的活性,达到最大的生产强度;⑥结构简单,运转可靠,装卸催化剂方便;甲醇合成塔的形式有很多种,有ICI四段冷激式,Lurgi 型管壳副产蒸汽式,托普索全径向合成塔,国内亦有多种合成塔,GC型轴径冷激式,Lindar均温型合成塔等1;出塔气冷凝器出塔气中含甲醇%加其它未反应气体,通过冷凝器可使出塔气中大部分甲醇和其它产物冷凝下来,以利分离,一般有喷淋式和壳管式,由设计采用管壳式冷凝器15;甲醇分离器甲醇分离器的作用是将经过冷凝器冷凝下来的液体甲醇和未反应气体进行气液分离,分离出的甲醇在液面控制下在分离器底部减压送粗甲醇贮槽;粗甲醇贮槽贮槽的工作压力为,液体以5MPa减压后,溶于粗甲醇中的气体释放出来,以贮罐气的形式在压力控制下经气体排出口排出,贮槽液体出口管上装有液体控制装置;压缩机压缩机的任务是把合成塔来反应的气体送回甲醇合成塔,其动力由高压蒸汽透平提供.结论甲醇合成工艺,流程采用管壳式反应器,催化剂装在管内,反应热由管间沸腾水放走,并副产高压蒸汽,甲醇合成原料在离心式透平压缩机内加压到以1:5的比例混合循环,混合气体在进反应器前先与反应后气体换热,升温到220℃左右,然后进入管壳式反应器反应,反应热传给壳程中的水,产生的蒸汽进入汽包,出塔气温度约为 250 ℃,含甲醇7%左右,经过换热冷却到40℃,冷凝的粗甲醇经分离器分离;分离粗甲醇后的气体适当放空,控制系统中的惰性气体含量;整个设计所采用的低压法Lurgi甲醇合成技术不仅先进而且成熟,投资和操作费用低,操作简便;通过对年产三万吨甲醇整个合成工段的物料衡算、能量衡算;依据所得的计算结果可以对整个合成工段的主要设备进行选型,以确定最后的设备型号,为更好的完成生产任务创造了条件;。
甲醇合成工艺过程及优化研究
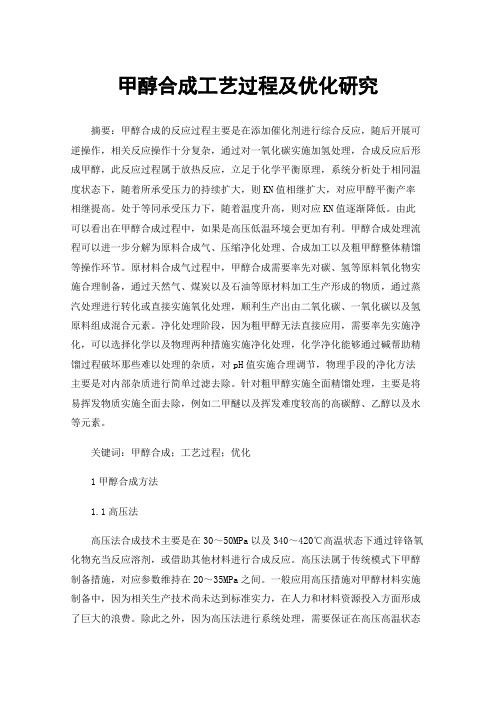
甲醇合成工艺过程及优化研究摘要:甲醇合成的反应过程主要是在添加催化剂进行综合反应,随后开展可逆操作,相关反应操作十分复杂,通过对一氧化碳实施加氢处理,合成反应后形成甲醇,此反应过程属于放热反应,立足于化学平衡原理,系统分析处于相同温度状态下,随着所承受压力的持续扩大,则KN值相继扩大,对应甲醇平衡产率相继提高。
处于等同承受压力下,随着温度升高,则对应KN值逐渐降低。
由此可以看出在甲醇合成过程中,如果是高压低温环境会更加有利。
甲醇合成处理流程可以进一步分解为原料合成气、压缩净化处理、合成加工以及粗甲醇整体精馏等操作环节。
原材料合成气过程中,甲醇合成需要率先对碳、氢等原料氧化物实施合理制备,通过天然气、煤炭以及石油等原材料加工生产形成的物质,通过蒸汽处理进行转化或直接实施氧化处理,顺利生产出由二氧化碳、一氧化碳以及氢原料组成混合元素。
净化处理阶段,因为粗甲醇无法直接应用,需要率先实施净化,可以选择化学以及物理两种措施实施净化处理,化学净化能够通过碱帮助精馏过程破坏那些难以处理的杂质,对pH值实施合理调节,物理手段的净化方法主要是对内部杂质进行简单过滤去除。
针对粗甲醇实施全面精馏处理,主要是将易挥发物质实施全面去除,例如二甲醚以及挥发难度较高的高碳醇、乙醇以及水等元素。
关键词:甲醇合成;工艺过程;优化1甲醇合成方法1.1高压法高压法合成技术主要是在30~50MPa以及340~420℃高温状态下通过锌铬氧化物充当反应溶剂,或借助其他材料进行合成反应。
高压法属于传统模式下甲醇制备措施,对应参数维持在20~35MPa之间。
一般应用高压措施对甲醇材料实施制备中,因为相关生产技术尚未达到标准实力,在人力和材料资源投入方面形成了巨大的浪费。
除此之外,因为高压法进行系统处理,需要保证在高压高温状态下实施反应处理,导致所形成甲醇内部杂质含量过多,为此该种方法逐渐被化工产业所淘汰。
1.2低压法低压法指采用低温、低压和高活性铜基催化剂在在5~10MPa压力区间合成甲醇的工艺。
8第三章催化加氢-2一氧化碳加氢合成甲醇

高压 Zn-Cr
低压 Cu-Zn-Al2O3
低 中 变 高 变 Cu-Zn-Al2O3 Fe-Cr-K2O
29
(二) 三相流化床反应器合成甲醇工 艺流程
30
催化加氢
五、 甲醇技术及应用的开发进展
1.国外技术进展
(1)传统ICI、Lurgi的技术改造,回收热能,降低能耗
(2)新型反应器,提高转化率 (3)新型催化剂,延长寿命,提高热稳定性
第三章
第一节 概述
催化加氢
第二节 催化加氢的一般规律
第三节 一氧化碳加氢合成甲醇
1
第三节 一氧化碳加氢合成甲醇
一、概述
二、CO加氢合成甲醇 三、合成甲醇பைடு நூலகம்艺流程
2
一、概述
(1)甲醇的性质及用途
﹡工业甲醇是无色、类似酒味的挥发性液体。相对密度
0.7914;熔点-93.9℃;沸点65℃;折光率1.3288;动力 粘度(120℃时)0.56cp;膨胀系数(20℃时)
5
①甲醇+酸 → 酯+水
②甲醇+氧气→甲醛
用途 ③甲醇+NH3 → 甲胺、二甲胺、三甲胺 ④甲醇 →醋酸(羰基合成) ⑤甲醇合成人造蛋白是很好的禽畜饲料。 ⑥作石油添加剂。
6
7
在350℃,于流动系统中进行,所 得到的甲醇产率为67%,二甲醚为 33%。氯甲烷的转化率达98%。水解 速度慢,价格昂贵。
20
(三) 催化剂活化
低压合成甲醇的催化剂,其化学组成是CuO-ZnOAl2O3 ,只有还原成金属铜才有活性。 还原过程为活化:氮气流升温、还原
CuO-ZnO-Al2O3
还原性气体 0.4MPa,99%N2 缓慢地升温, 20℃/h
- 1、下载文档前请自行甄别文档内容的完整性,平台不提供额外的编辑、内容补充、找答案等附加服务。
- 2、"仅部分预览"的文档,不可在线预览部分如存在完整性等问题,可反馈申请退款(可完整预览的文档不适用该条件!)。
- 3、如文档侵犯您的权益,请联系客服反馈,我们会尽快为您处理(人工客服工作时间:9:00-18:30)。
(1)催化剂不 易中毒,再生困 难 (2)副反应多
(1)催化剂易 中毒,再生容易 ,寿命为1-2年 (2)副反应少
CuO-ZnO 中压法 -Al2O3
三元催化剂
10~15
230~270
1970年 工业化
16
反应条件 a.反应温度及压力:
反应条件
反应 温度
可逆放热反应,温度升高,反应速率增加,而 平衡常数下降
高压法: 30~50MPa, 340~
420℃、锌-铬氧化物作催化剂
8
一、热力学分析
(1)生产原料-----合成气的制备
气体原料生 水蒸气转化法 产合成气 部分氧化法
液体原料制 水蒸气转化法 取合成气 部分氧化法
固体原料制 取合成气
9
热力学分析 ①反应热效应
主反应:
放热反应,25℃反应热为△H0298=-90.8KJ/mol。 常压不同温度的反应热按式3-3 (P152 )计算
醇的生产具有十分重要的意义。
4
甲甲醇是最简单的饱和醇,也是重要的化学工业基础原 料和清洁液体燃料,它广泛用于有机合成、医药、农药、涂 料、染料、汽车和国防等工业中。 用于农制造甲醛和农药 (杀虫剂、杀虫螨)、医药(磺胺类、合霉素类)等的原料 、合成对苯二甲酸二甲酯、甲基丙烯酸甲酯、丙烯酸甲酯的 原料之一、醋酸、氯甲烷、甲胺和硫酸二甲酯等多种有机产 品。用作基本有机原料、溶剂及防冻剂。主要用于制甲醛、 香精、染料、医药、火药、防冻剂等。是基础的有机化工原 料和优质燃料。主要应用于精细化工,塑料等领域,用来制 造甲醛、醋酸、氯甲烷、甲氨、硫酸二甲脂等多种有机产品 ,也是农药、医药的重要原料之一,经常作为气相色谱和液 相色谱分析的溶剂。甲醇在深加工后可作为一种新型清洁燃 料,也加入汽油掺烧。
甲烷部分氧化法
合成气生条 2产0件2.甲:64醇在×催10化5Pa剂,低作3压5用0法~下:5,050M采℃Pa用、压27力5℃10左1右.3,2~采
特 收点 率: 不高工(艺流30程%)用 中 2简7,铜压5单℃未基法,,实催:氧铜现化10基化剂~工催过合2业化7程成M化剂P不甲a。,易醇2控35~制,甲醇
增加压力可加快反应速度,所需压力与反应温度有
关。
18
b.空速
反应条件
空速:影响选择性和转化率,直接关系到催化剂的生
产能力和单位时间的放热量。
铜基催化剂上空速与转化率、生产能力
空间适速度宜/h的-1 空C速O转与化催率化/%剂的粗活甲性醇产、量反/[m应3/(温m度3催及化剂·h)] 进塔气体的组成有关 234000000000000CuOZ-nZOn-OC543-r120A...2521Ol2O3:3:201000000-04h0-01 00h222-1685...148
17
催化剂
(二)反应条件
1. 反应温度和压力
①为延长催化剂寿命,开始易用较低温度,过一定
时间再升至适宜温度,其后随着催化剂老化程度升 高,反应程度也相应高。
②因反应放热,反应热应及时移出,否则副反应增
加,催化剂易烧结,活性降低。故严格控制温度, 及时有效地移走反应热是合成塔设计、操作之关键。
5
用途
①甲醇+酸 → 酯+水 ②甲醇+氧气→甲醛 ③甲醇+NH3 → 甲胺、二甲胺、三甲胺 ④甲醇 →醋酸(羰基合成) ⑤甲醇合成人造蛋白是很好的禽畜饲料。 ⑥作石油添加剂。
6
7
氯甲烷水解法
在350℃,于流动系统中进行,所 得到的甲醇产率为67%,二甲醚为 33%。氯甲烷的转化率达98%。水解 速度慢,价格昂贵。
第三章 催化加氢
第一节 概述 第二节 催化加氢的一般规律 第三节 一氧化碳加氢合成甲醇
1
第三节 一氧化碳加氢合成甲醇
一、概述 二、CO加氢合成甲醇 三、合成甲醇工艺流程
2
一、概述
(1)甲醇的性质及用途
﹡工业甲醇是无色、类似酒味的挥发性液体。相对密度 0.7914;熔点-93.9℃;沸点65℃;折光率1.3288;动力
2. 升温:△ G0副<△ G0主,副反应 在热力学上有利,抑制副反应 15 催化剂
二、 催化剂及反应条件
催化剂
①催化剂
方法
催化剂
高压法
ZnO-Cr2O3 二元催化剂
CuO-Zn0
5
件 备注
温度,℃
特点
380~400 230~270
1924年 工业化
反应温度因催化剂种类而异
ZnO-Cr2O3:
380 ~ 400℃
CuO-ZnO-Al2O3: 230 ~ 270℃
与副反应比,主反应是摩尔数减少最多而平衡
反应 常数最小的反应,因此增加压力合成甲醇有利 压力 反应压力因催化剂种类而异
ZnO-Cr2O3: 30 MPa CuO-ZnO-Al2O3: 5 ~10MPa
b. 压力对平衡常数的影响
P↑,KN↑ ,xE↑ ,故应在高压下操作。
12
热力学分析
13
③ 副反应
平行副反应 连串副反应
热力学分析
14
热力学分析
● 从热力学分析最可大知,合成甲醇的反 应温度低,所需操作压力也可以低,
副 反
但温度低,反应速度太慢。关键在于
应 催化剂
1. 主反应分子数减少最 多,加压有利于甲醇生成
3
●甲醇是仅次于三烯和三苯的重要基础有机化工原料,
广泛用于有机合成、染料、合成纤维、合成橡胶、涂料 和国防等工业。甲醇大量用于生产甲醛和对苯二甲酸二 甲酯;
●以甲醇为原料经羰基化反应直接合成醋酸已经工业化; ●近年来,随着技术的发展的能源结构的改变,甲醇又开
辟了许多新的用途,是合成人工蛋白的重要原料; ●以甲醇为原料生产烯烃和汽油已实现工业化。因此,甲
反应热与温度压力关系
?
10
高压低温时反应热大
热力学分析
T<300℃ ,T↓ ,
↑(斜率上升),反应易失控
P低,T高时,△H变化小,故选择20MPa,300~400℃,反应
易控
11
(二) 平衡常数
热力学分析
a. 温度对平衡常数的影响
Kf只与温度有关(和书上式3-5等价)
低温对反应有利 P153表3-8
粘度(120℃时)0.56cp;膨胀系数(20℃时) 0.001031;蒸汽压12.8KPa;蒸汽密度1.1kg/m3。 ﹡能与水、乙醇、醚、苯酮类和其它有机溶剂混合;能与多 种化合物形成共沸物。
﹡工业甲醇易燃、遇明火有燃烧、爆炸的危险。燃烧时发出 蓝色火焰;在常温下挥发出的蒸汽有毒;与空气能形成爆 炸性混合物;爆炸极限为6.0—36%(V)。