TPM全员设备管理与维护培训教材
TPM管理专题培训教材(42张)课件
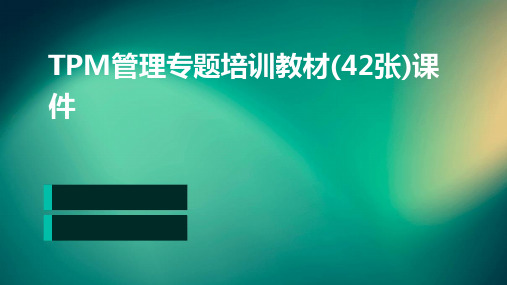
信息化平台在TPM中实施案例分享
案例一
某大型制造企业通过引入ERP系统, 实现了TPM相关数据的集中管理和流 程优化,提高了工作效率和响应速度 。
案例二
案例三
某汽车制造企业通过引入MES系统, 实现了车间生产管理和调度的智能化 和可视化,提高了生产效率和产品质 量。
某电力公司通过实施CMMS系统,实 现了设备维护和维修管理的自动化和 智能化,降低了运维成本和故障率。
提高操作人员技能水平,确保正 确操作设备。
定期对设备进行检查,及时发现 并处理潜在问题。
进行设备定期保养
按照保养计划对设备进行维护, 确保设备处于良好状态。
制定设备自主保全计划
明确保全目标、时间表和责任人 。
总结与改进
对设备自主保全活动进行总结, 针对存在问题进行改进,持续提 高设备管理水平。
设备自主保全检查与评价标准
设备完好率
反映设备技术状态的指标,计算公式 为(完好设备台数/总台数)×100% 。
故障率
反映设备故障频次的指标,计算公式 为(故障次数/运行时间)×100%。
维修费用率
反映设备维修成本的指标,计算公式 为(维修费用/总产值)×100%。
设备综合效率(OEE)
反映设备整体性能的指标,综合考虑 设备可用率、性能效率和质量合格率 三个因素。
根据培训需求,设计针对性的培训课程,包括理论课程和实践 操作课程,确保培训内容的全面性和实用性。
采用多种培训方式,如集中授课、现场教学、案例分析等,提 高培训的趣味性和互动性。
制定详细的培训计划,合理安排培训时间和地点,确保培训的 顺利进行。
培训效果评估和持续改进方向
01
培训效果评估
TPM原理(培训教材)ppt课件

04
员工培训与团队建设
员工技能培训方案设计
培训需求分析
通过岗位分析、员工能力评估 等方式,明确员工所需技能及 培训目标。
培训内容设计
根据培训目标,制定详细的培 训计划,包括课程安排、教学 方法、培训资源等。
培训实施与管理
组织培训活动,确保培训计划 的顺利执行,同时关注员工学 习进度和反馈,及时调整培训 方案。
团队协作能力提升途径
01
02
03
团队建设活动
组织各类团队建设活动, 如拓展训练、团队协作游 戏等,增强团队成员间的 信任和默契。
沟通技巧培训
提供沟通技巧培训,帮助 员工掌握有效的沟通方法 ,促进团队内部信息交流 。
协作意识培养
强调团队协作的重要性, 鼓励员工积极参与团队工 作,分享知识和经验。
企业文化在TPM中渗透
设备故障诊断与处理技术
故障诊断方法
故障案例分析与经验总结
运用振动分析、油液分析、红外测温 等故障诊断技术,对设备故障进行准 确判断和定位。
对典型故障案例进行分析和总结,提 炼故障处理经验和教训,为类似故障 的处理提供参考。
故障处理技术
针对不同类型的故障,采取相应的维 修措施,如更换零件、调整参数、清 洗油路等。
企业文化宣导
通过企业内部宣传、员工手册等方式,传播企业的核心价 值观和理念,增强员工对企业文化的认同感。
TPM与企业文化融合
将TPM理念与企业文化相结合,形成具有企业特色的TPM 管理模式,推动企业文化的落地实施。
员工行为规范
制定员工行为规范,明确员工在TPM实施过程中的责任和 义务,引导员工自觉遵守企业文化和TPM要求。
可视化展示
利用图表、仪表盘、3D模型等可视 化手段,将分析结果直观展示给管 理人员和操作工人,提高决策效率 和操作便捷性。
TPM全员设备维护与管理培训讲义

TPM全员设备维护与管理培训讲义1. 简介TPM(全员设备维护与管理)是一种通过维护设备的可靠性和精度来提高生产效率的管理方法。
本文档将介绍TPM的基本概念、操作流程以及培训内容,帮助全员了解和实施TPM。
2. TPM的基本概念TPM是Total Productive Maintenance的缩写,意为全员设备维护与管理。
它的目标是通过消除设备故障和减少生产中的没有价值的时间来提高设备的效率和可用性。
TPM的四大支柱是: - 预防性维护:通过定期检查设备、更换易损件等措施来预防设备故障。
- 细节管理:对设备进行巡检,保持设备的整洁、有序和易于操作。
- 故障隐患消除:对设备故障进行分析,找出根本原因并采取措施消除。
- 提高维护技术:提高维护人员的技能和知识,以更好地管理和维护设备。
3. TPM的操作流程TPM的操作流程包括以下几个步骤:步骤一:设备规划•制定设备的维护计划和目标。
•对设备进行分类和评估,确定关键设备和重点改善项目。
步骤二:故障分析和消除•对设备故障进行分析,找出根本原因。
•制定故障预防计划,采取措施消除故障隐患。
步骤三:维护活动•制定设备的维护计划和标准操作规程。
•进行定期检查、润滑和更换易损件等维护活动。
•培训维护人员,提高其技术和知识水平。
步骤四:细节管理•建立设备巡检和保养记录。
•维护设备的整洁、有序和易于操作。
•采取措施预防设备的污染和损坏。
步骤五:持续改善•回顾和评估设备的维护情况。
•制定改善计划,提高设备的可靠性和精度。
4. TPM的培训内容TPM的培训内容主要包括以下方面:设备维护基础知识•设备类型和分类•设备故障的原因和分类•维护活动和标准操作规程设备的巡检和保养•设备巡检的方法和步骤•设备保养的方法和步骤•巡检和保养记录的管理和分析故障预防和消除•故障分析的方法和步骤•故障预防计划的制定和执行•故障消除的措施和方法维护人员的培训和管理•维护人员的岗位职责和要求•维护人员的技术和知识培训•维护人员的绩效评估和激励措施TPM的实施和改善•TPM的操作流程和步骤•TPM的评估和改善方法•TPM与其他管理方法的整合5. 总结TPM是一种通过维护设备的可靠性和精度来提高生产效率的管理方法。
TPM基础知识培训教材(2024)
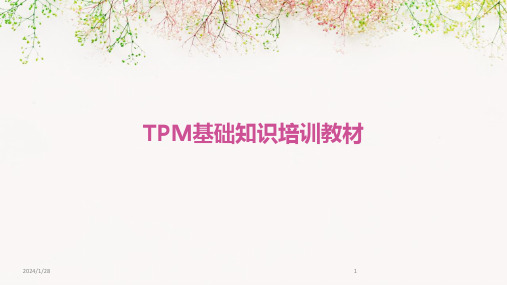
自主维修
持续改进
鼓励员工自主进行维修 工作,提高维修效率和
质量。
20
不断总结经验教训,优 化自主维护流程和方法
。
计划维护
01
02
03
04
制定维护计划
根据设备特性和使用状况,制 定合理的维护计划,包括定期
维护、预防性维护等。
执行维护计划
按照计划进行设备维护,确保 设备处于良好状态。
标准化和规范化
将改善成果进行标准化和规范 化,形成可复制、可推广的管 理模式和经验。
2024/1/28
17
04
TPM的八大支柱
2024/1/28
18
个别改善
识别问题和机会
通过观察和数据分析,识别设备、流程或系统中 的问题和改进机会。
实施改善措施
按照计划实施改善措施,包括设备改造、流程优 化、操作调整等。
15
实施自主维护
2024/1/28
01 初期清扫 通过清扫设备,发现设备存在的问题和隐患。
02 污染源和困难点对策 针对发现的问题和隐患,制定相应的对策措施。
03
制定自主维护基准
根据设备特性和使用要求,制定自主维护的基准和标 准。
04 总点检 定期对设备进行全面检查,确保设备处于良好状态。
05
自主点检
2024/1/28
31
06
TPM的推进策略与技巧
2024/1/28
32
领导层的支持与推动
1
确立TPM在公司战略中的地位
领导层应明确TPM对公司长期发展的重要性,将 其纳入公司战略规划,并提供相应的资源支持。
2 3
营造全员参与的氛围
领导层需积极倡导全员参与TPM的理念,通过演 讲、座谈会等方式与员工沟通,激发员工的参与 热情。
2024版TPM培训课程(经典)
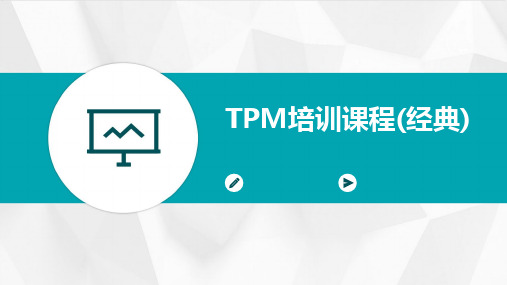
问题剖析与解决
针对案例中出现的问题进行深入剖析, 提出有效的解决方案和措施。
THANKS
感谢观看
战。
TPM实施效果评估与持续改
06
进
TPM实施效果评估指标体系构建
关键绩效指标(KPI)设定
01
包括设备综合效率(OEE)、故障率、维修成本等核心指标。
评估维度划分
02
从设备性能、维护管理、人员技能等多个维度进行全面评估。
权重分配与评分标准
03
根据各指标重要性和实际情况,合理分配权重,制定评分标准。
预防措施
分析设备故障的原因和规 律,采取针对性的预防措 施,降低设备故障率。
案例分析:提高设备利用率和降低故障率
案例选择
选择与设备管理和维护相关的典 型案例进行分析。
分析方法
通过案例分析,总结提高设备利用 率和降低故障率的经验和教训。
改进措施
根据案例分析结果,制定针对性的 改进措施,提高设备管理和维护水 平。
03 促进企业文化建设
TPM活动强调团队合作和持续改进,有助于形成 积极向上的企业文化氛围。
案例分析:成功实施TPM企业
案例一
某汽车制造企业通过实施TPM活动,成功提高了设备综合 效率,降低了维修成本,同时提高了产品质量和生产效率。
案例二
某电子企业通过TPM活动的推进,实现了生产现场的规范 化、标准化管理,有效减少了设备故障和不良品率,提高 了企业整体运营水平。
结合企业战略和业务发展 需求,制定年度、季度、 月度等周期性培训计划。
培训课程开发
针对员工需求,开发符合 企业实际的培训课程,包 括内部培训和外部引进课 程。
培训实施与跟进
组织培训活动,确保培训 计划的落实,并对培训效 果进行跟进和评估。
TPM管理培训TPM管理培训课程(2024)
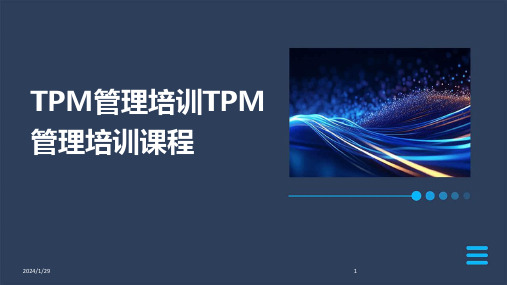
5S管理原则及实施步骤
3. 宣传教育
向员工宣传5S理念和方法,提高认识和参与 度。
5. 检查评估
定期对实施效果进行检查评估,发现问题及 时整改。
2024/1/29
4. 实施整改
按照计划进行现场整改,包括清理、整顿、 标识等。
6. 持续改进
将5S管理纳入日常工作中,不断推动现场管 理的持续改进。
2024/1/29
3
TPM定义与发展历程
TPM定义
Total Productive Maintenance,全员生产维护,是一种以提高设备综合效率 为目标,以全系统的预防维修为过程,全体人员参与为基础的设备保养和维修 管理体系。
发展历程
TPM起源于日本,20世纪60年代开始在日本企业中得到广泛应用,后逐渐传播 到欧美等发达国家,成为世界范围内广泛认可的设备管理理论和方法。
2024/1/29
4
TPM核心理念与目标
核心理念
TPM的核心理念是“全员参与、预 防为主、持续改进”,强调全员参与 设备管理,通过预防性维护和持续改 进提高设备综合效率。
目标
TPM的目标是追求设备综合效率最大 化,实现设备零故障、零不良、零浪 费和零灾害,同时提高员工素质和企 业竞争力。
2024/1/29
等。
设备故障类型与原因分析
01
02
03
04
机械故障
由于机械部件磨损、断裂等原 因引起的故障。
电气故障
由于电气元件损坏、线路短路 等原因引起的故障。
液压故障
由于液压系统泄漏、堵塞等原 因引起的故障。
人为故障
由于操作不当、维护不及时等 原因引起的故障。
2024/1/29
tpm培训教材
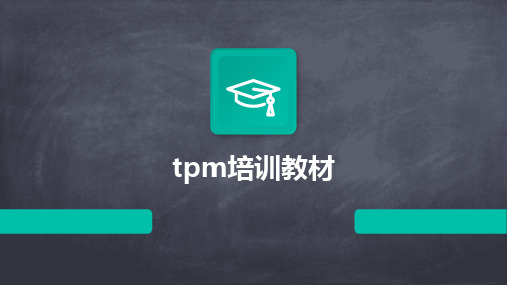
01 TPMChapterTPM定义及发展历程TPM定义发展历程TPM核心理念与目标核心理念目标TPM实施意义及价值实施意义TPM的实施可以提高企业设备管理水平,保障生产顺利进行,降低生产成本,提高产品质量和企业竞争力。
同时,TPM还可以培养员工自主维护意识,提高员工技能和素质。
价值体现TPM的价值体现在多个方面,包括提高设备综合效率、降低维修费用、减少停机时间、提高产品质量、增强企业竞争力等。
通过实施TPM,企业可以实现设备管理的全面优化和持续改进,为企业创造更大的经济效益和社会效益。
02设备管理与维护基础知识Chapter设备分类及功能特点设备分类功能特点设备故障类型与原因分析故障类型原因分析故障原因可能包括设计缺陷、制造问题、使用不当、维护不足等。
设备维修策略与方法维修策略维修方法03 TPMChapter制定TPM推进计划明确TPM推进目标根据企业实际情况,制定符合自身发展的TPM推进目标,如提高设备综合效率、降低故障率等。
制定推进计划根据目标,制定详细的推进计划,包括时间表、责任人、资源需求等。
组建推进团队成立专门的TPM推进团队,负责计划的执行和跟进。
制定自主保全基准实施自主保全教育开展自主保全活动030201建立自主保全体系开展专业保全活动制定专业保全计划实施专业保全跟踪专业保全效果推进改善提案活动鼓励员工提出改善提案01评估和改善提案02跟踪改善效果0304 TPMChapter如何有效组织培训和教育01020304如何激发员工参与热情如何运用目视化管理手段制定目视化管理标准,明确各类标识、图表、看板等的在生产现场和设备上设置明显的标识和警示,提醒员工如何进行持续改进和优化05 TPMChapter1 2 3设备综合效率(OEE)提升率故障率降低率维修费用节约率TPM实施效果评价指标体系设计数据收集、整理和分析方法数据整理数据收集对收集到的数据进行分类、筛选和整理,去除异常值和无效数据,确保数据的准确性和可靠性。
TPM培训讲义课件142张

• 只要我们坚持做下去,我们也敢于象日本人那样,追求并 期待“零”目标的实现。
第二部分:TPM活动内容
一、自主保全
(一)、什么是自主保全
第一部分:认识TPM
一、什么是TPM
TPM即全员效率维修(Total Productive Maintenance)。 定义:
以最有效的设备利用为目标,以维修预防、预防维 修、改善维修和事后维修综合构成生产维修为总运行体 制,由设备的全程管理部门、使用、维修等所有有关人 员,从最高经营管理者到第一线作业人员全体参与,以 自主的小组活动来推行生产维修,使损失最小化,效益 最大化的活动。 要点:效率最大化、全员参与
自主保全活动就是以操作人员为主,对设备和装置 依据特定的标准,凭五官进行外表层面的检查。通过一 定的教育训练,使之自主开展清扫、点检、加油、紧固 等设备保全活动,及进一步能对微小的故障做简单的修 理和改善。
我们可以尝试开展如下活动: 1)保养(清扫):对设备工作环境进行清洁和整顿。 2)点检:对设备基本工作环境、外部条件、外观等 进行检查。
备等。 个别改善:针对设备缺陷展开的改善活动。 品质保全:通过设备维修活动改善和提高产品品质的活动。 设备前期管理:即从方案规划、采购到投入服役的全程管理。 教育训练:技术及管理培训,不断提高员工技术技能。 安全与卫生:人员操作安全与环境卫生标准。使人机处于良好工
作状态。 间接部门效率化:提高间接业务部门关联业务效率。
四、 TPM的内容
企业经营效率化
核心是全员参与,预防为主 零故障、零灾害、零不良、……零损失
TPM全员设备管理与维护培训教材

①养成自主管理的习惯,即遵守“ 自己的设备是自己维护”的意识。
②实现故障“0”、不良“0”,员工在 推行中增加自信。
③改变制造中漏油、粉尘的现象, 造就整洁、明亮的现场。
④给工厂访问者好的企业形象,有 利于营销活动。
TPM的基本理念
(1)全面提高企业管理水平:树立成本概念、安全 事故为“0”、不合格品为“0”、设备故障为“0”;
TPM的效果
有形的效果
无形的效果
P——①附加价值生产性1.5-2倍增 加;
②突发故障件数由1/10 1/250;
③设备综合效率提高1.5—2倍 。
Q——①工程不良率减少1/10;
②保管部索赔减少1/4。
C——制造成本节约30%。
D——产品、在制品库存减少一半 。
S——休业灾害“0”、公害“0”。
路漫漫M其悠—远—改善提案数月均达5—10件
路漫漫其悠远
预防保全时代(PM)
• 1951年,美国人最先提出了预防保全( Productive Maintenance)的概念。主 要对机器设备进行一些简单的维护,比如 定时上油、经常擦拭灰尘、更换螺丝螺母 等。
路漫漫其悠远
改良保全时代(CM)
• 1957年,人们开始根据设备零件的使用周 期定期更换零件,使设备运转更加正常。 根据零件的使用周期,在零件使用寿命到 期之前更换零件,既有效地利用了零件, 又防止了故障的发生。
追求பைடு நூலகம்产效率化的极限
项目组活动 工作岗位小团队活动
阶段类别方式, 诊断和合格证
改良保全,计划保全,预防保全
领导的集合教育 成员的教育传达 开发容易制造的制品 开发容易使用的设备 设定不发生不良的条件 和维持管理 生产支援,本部属的效率化 和设备的效率化
2024年度-TPM全员生产性维护培训课件
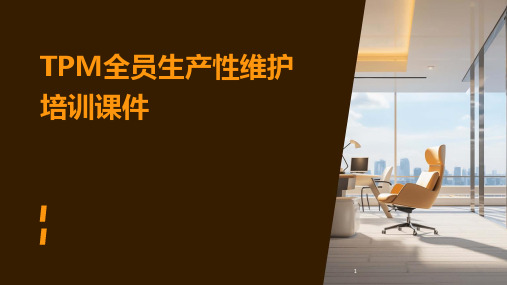
1
目 录
• TPM概述与基本原理 • 设备管理与预防性维护策略 • 自主维护与小组活动推进 • 计划性维护与专业保全实施 • 故障分析与诊断技术提升 • TPM推进策略与领导力建设 • 总结回顾与展望未来发展趋势
2
CHAPTER 01
TPM概述与基本原理
3
TPM定义及发展历程
利用人工智能、大数据等 技术,对设备运行数据进 行实时监测和分析,实现 故障预警和智能诊断。
多学科融合诊断
结合机械、电气、液压等 多学科知识,对复杂故障 进行综合诊断。
22
复杂问题解决方案探讨
跨部门协作
建立跨部门协作机制,共同解决复杂问题,提高问题解决效率。
专家团队支持
组建专家团队,对复杂问题进行深入研究和分析,提出针对性解 决方案。
提供必要的资源和支持
3
领导者应提供必要的资源,如资金、技术、人力 等,支持TPM活动的开展,确保各项计划和方案 的顺利实施。
26
跨部门协作与资源整合
加强跨部门沟通与协作
建立有效的跨部门沟通机制,促进不同部门之间的信息交 流与合作,共同解决TPM推进过程中遇到的问题。
整合内外部资源
充分利用企业内外部的资源,如专业机构、行业协会、供 应商等,为TPM推进提供有力支持。
备综合效率。
15
CHAPTER 04
计划性维护与专业保全实施
16
计划性维护流程设计
制定维护计划
维护计划审批
根据设备的重要程度、使用频率、故障历 史等数据,制定合理的维护计划,明确维 护周期、维护内容、维护人员等要素。
维护计划需要经过相关部门审批,确保计 划的合理性和可行性。
TPM培训教材(经典)

设备综合效率
(Overall Equipment Effectiveness)
设备综合效率=时间开动率X性能开动率X合格品率 时间开动率=净运行时间/运行时间 性能开动率=实际生产数量/理想生产数量 合格品率=合格品数/总生产数 设备利用率=负荷时间/设备应开动时间
31
故障/停机损失
(Equipment Failure / Breakdown Losses)
5
二.TPM的发展历史
1
事后维修
(BM :Breakdown Maintenance)
故障后再维护;
1950年以前
6
全面生产维护
(TPM: Total Productive Maintenance)
全员参加型的保养
1980年以后
2
改良维修
(CM : Corrective Maintenance )
9
TPM定义及特点
TPM是日本现代设备管理维修制度,它是以达到最 高的设备综合效率为目标,确立以设备一生为对象的生 产维修保全系统,涉及设备的计划、使用、维修等所有 部门,从最高领导到第一线工人全员参加,依靠开展小 组自主活动来推行的生产维修,概括为:T——全员、全 系统、全效率,PM——生产维修(包括事后维修BM、预 防维修PM、改善维修CM、维修预防MP)。
27
开展TPM的八大支柱
安管
品
全理
质
、间
保
卫接
养
生部
环门
境的
管活
理动
设
技
自个
备
能
主别
初
教
保改
期
育
养善
管
训
理
TPM培训课程(经典)ppt课件

详细阐述过程质量控制的方法,包括过程能力分析、控制图应用、 过程性能指数等方面的内容。
过程质量控制的实施与监控
介绍如何实施过程质量控制,包括制定控制计划、进行过程监控和 数据分析等方面的内容。
持续改进思路及实践案例分享
1 2
持续改进概述
介绍持续改进的概念、目的和意义,以及在企业 中的重要性。
解和信任。
明确团队目标
制定明确的团队目标,激发团 队成员的积极性和凝聚力。
优化团队结构
根据团队成员的特长和优势, 合理分配任务和角色,发挥最 大效益。
提升团队士气
通过激励措施、认可优秀表现 等方式提高团队成员的士气和
斗志。
企业文化在TPM中作用
导向作用
企业文化能够引导员工形成正确的价 值观和行为准则,推动TPM顺利实 施。
发展历程
TPM起源于美国,后在日本得到广泛应用和发展。它强调全 员参与,通过自主保全、专业保全、个别改善、初期管理等 手段,提高设备的综合效率,降低生产成本,提升企业竞争 力。
TPM核心理念与目标
核心理念
TPM的核心理念是“全员参与”和 “预防为主”,通过激发员工的自主 性和创造性,实现设备的高效、稳定 、长期运行。
云计算技术为大规模数据处理提供了高效 、灵活的解决方案,未来将在TPM中发挥
越来越重要的作用。
物联网技术
物联网技术将实现设备与系统之间的实时 通信和数据交换,提升TPM的智能化水平
。
大数据分析
随着工业数据的不断增长,大数据分析技 术将成为TPM领域的重要工具,帮助企业 实现更精准的设备管理和维护。
人工智能与机器学习
根据设备功能、用途、结构等特 点,将设备分为不同类型,如生 产设备、辅助设备、动力设备等 。
- 1、下载文档前请自行甄别文档内容的完整性,平台不提供额外的编辑、内容补充、找答案等附加服务。
- 2、"仅部分预览"的文档,不可在线预览部分如存在完整性等问题,可反馈申请退款(可完整预览的文档不适用该条件!)。
- 3、如文档侵犯您的权益,请联系客服反馈,我们会尽快为您处理(人工客服工作时间:9:00-18:30)。
改良保全时代(CM)
• 1957年,人们开始根据设备零件的使用周 期定期更换零件,使设备运转更加正常。 根据零件的使用周期,在零件使用寿命到 期之前更换零件,既有效地利用了零件, 又防止了故障的发生。
(2)预防理念:维修预防(MP)/预防维修(PM) /改善性维修(CM);
(3)全员参与:小组活动、操作员工的自主维护; (4)注意现场现物:设备的目视化管理、整洁的工
作环境; (5)自动化、无人化:构建自动化程度高的生产现
场。
TPM的五要素
(1)TPM致力于设备综合效率最大化的目标; (2)TPM在整个设备一生建立彻底的预防维修体
实
7.4 运转, 保全
施
技能提升训练
阶
8. 造成新制品, 新设备的 初期管理体质
段
9. 组成成品质保全体制
导入准备开始到实施
10. 组成间接管理部分的 效率化体制
11. 组成安全, 卫生和 环境管理体制的
供应链单位同步运行
稳定 12. TPM完全实施和水准 阶段 提升
追求生产效率化的极限
项目组活动 工作岗位小团队活动
Q——①工程不良率减少1/10;
造就整洁、明亮的现场。
②保管部索赔减少1/4。
④给工厂访问者好的企业形象,有
C——制造成本节约30%。
利于营销活动。
D——产品、在制品库存减少一半。
S——休业灾害“0”、公害“0”。
M——改善提案数月均达5—10件。
TPM的基本理念
(1)全面提高企业管理水平:树立成本概念、安全 事故为“0”、不合格品为“0”、设备故障为“0”;
阶段类别方式, 诊断和合格证
改良保全,计划保全,预防保全
领导的集合教育 成员的教育传达 开发容易制造的制品 开发容易使用的设备 设定不发生不良的条件 和维持管理 生产支援,本部属的效率化 和设备的效率化
构建灾害 零,、公害零体系
挑战比PM奖的受奖 更高的目标
二、生产效率化理论
(一)影响效率化的16大浪费 1、16大浪费的含义
——改善设备制造方法、使用方法保全 方法,提高生产效率到极限。
由于是以设备专家为中心的PM,因而 只追求由设备制造方法、保全方法的改 善所能提高的设备效率的极限,对渗透 到设备使用方法的生产的生产效率的综 合性极限追求得不到满足。
2、TPM的特色是“操作的自主保全” 美式PM中,操作人员只管生产(运
2、TPM的成长和发展状况
• 20世纪70年代,日本以美国的PM(预防 保全或生产保全)为基础,开展了独特的 TPM管理活动,收到了令人瞩目的成就。
• TPM起初是从生产部门展开,80年代以后 逐步扩展成为全公司的TPM。
• 全球第一家通过TPM认证的企业是日本丰 田集团下属的日本电装公司
预防保全时代(PM)
• 三个“全”之间的关系为:全员参与为基础,全 系统的预防维修为载体,全效率为目标。
结论
全员参与型 生产保全
TPM--“全员参与”是Key(关键)。
TPM展开的四个阶段(12个步骤)
区分
STEP
要点
区分
STEP
要点
1. TOP的 TPM导入决议宣言
导 2. TPM导入教育
入
准 备
3. TPM推进机构组织
保全预防时代(MP)
• 1960年开始,人们不 但对设备进行保养, 而且把保养和预防结 合起来。
全员生产保全时代(TPM)
• 1989年,TPM被重新定义为广义的TPM, 它是指以建立不断追求生产效率最高境界 的企业体质为目标,通过公司领导到第一 线员工全员参与的创新小组改善活动,构 筑预防管理及生产工序中所有损耗发生的 良好机制,最终达成损耗的最小化和效益 的最大化。
制; (3)TPM由各部门共同推行(包括工程、生产、
维修部门) (4)TPM涉及到每个雇员,从最高管理者到现场
工人; (5)TPM是通过动机管理,即自主的小组活动来
推动的。
什么是TPM的三个“全”?
• 将TPM五个要素再进一步归纳,第一个要素可以 简称为“全效率”,第二个要素简称为“全系 统”,三、四、五项从横向、纵向和基层的最小 单元描述了“全员”的概念。
供应链的TPM时代
• 2000年开始,TPM已经跨行业国际化发 展 。TPM并不是只属于日本的产业界,世 界各地对TPM的关心逐年升高。这时也不 是在某个企业实施,它逐渐向服务、流通 等行业发展,逐步优化供应链系统。
TPM与PM比较
TPM的特色
美式PM
1、TPM为了生产系统的效率化,以综 合极限追求为目标。
(自身设备自己维修)
作),日常的保全、检查、维修等保全
——日常保全(清扫、给油、拧紧、点 工作由保全工作由保全负责人员全权负 检等)由操作人员负责,设备检查(诊 责。
断)或修理由专门的保全负责人员负责。
3、在TPM,全员参与的小集团活动— —与职制一体化的小集团活动中,从经 营层、中间层到全员的参与,这称为 “重复小集团活动”。
美式PM不组织全员参与的小集团活动。
TPM的效果
有形的效果
无形的效果
P——①附加价值生产性1.5-2倍增 ①养成自主管理的习惯,即遵守
ቤተ መጻሕፍቲ ባይዱ
加;
“自己的设备是自己维护”的意识。
②突发故障件数由1/10 1/250;
②实现故障“0”、不良“0”,员工 在推行中增加自信。
③设备综合效率提高1.5—2倍。 ③改变制造中漏油、粉尘的现象,
TPM-全员设备管理与维护
装备工程部维修维护科
一、TPM概论
1、什么是TPM?
• TPM 是英文Total Productive Maintenance的 缩写,中文译为“全面生产维护”,也可译为 “全员生产维修”或“全员生产保全”。它是以 提高设备综合效率为目标,以全系统的预防维护 为过程、全体人员参加为基础的设备保养和维修 体制。
阶
段
4、TPM基本方针和 目标设定
5. TPM展开 制定 推进计划
导入 6. TPM 导入运行 开始
公司内报上记载 TPM公司内讲习会宣言
7. 组成生产效率化体质 7.1 个别改善
干部 : 按级别封闭式研修
一般 : 大会宣讲教育
导
7.2 自主保全
委员会, 专门分会 推进事务局
确定目标和效果预测
入
7.3 计划保全