精益生产案例讲课
精益生产实战ppt课件
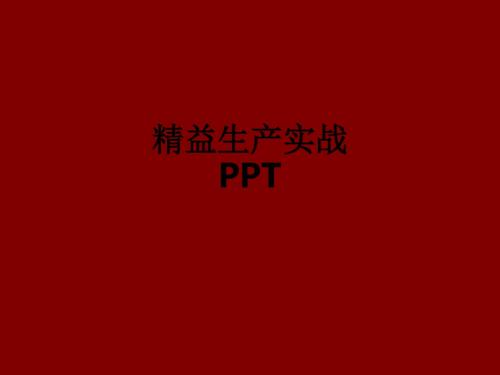
TPS:危机的产物
战后的日本,社会混乱、经济萧条。 丰田的经营状况很糟:49年底公司急需2亿日元的过年周转资金、到了如果得 不到银行融资便会倒闭、被人收购的境地。 银行答应提供资金,但有附加条件: “分离销售公司”与“裁减过剩人员”。 丰田喜一郎对分离销售公司可以忍痛接受;但他以前宣布过不裁员,既不想 放弃对员工的承诺,也不想放弃重建公司的机会。而工会方面认为“公司肯 定裁员”,在4月7日开始实行罢工。丰田面临进退两难的处境,发表了包括 “募集1600名自愿辞职员工”内容的重建方案。在此期间,丰田的汽车产量 直线下降、公司每天亏损惨重,丰田喜一郎主动承担领导责任、6月5日毅然 决定辞去总经理职务,此后1700名员工自愿辞职。 6月10日,历时二个月的罢工终于结束,丰田恢复正常生产。 留下的经营者和全体员工痛定思痛,决不想让悲剧重演,在大野耐一的领导、 推进下产生了准时化生产方式、加上自働化,进而产生了TPS 。 TPS : Toyota’s Production System
精益生产(Lean Production )
精,即少而精
不投入多余的生产要 素,只是在适当的时 间生产必要数量的市 场急需产品(或下道 工序急需的产品)
益,产生效益念
(1)价值:以客户的观点定义价值,而且通过对各个环节中 采用的杜绝一切浪费(人力、物力、时间、空间)的方法 与手段满足顾客对价格的要求。 (2)价值流:从原材料到成品赋予价值的全部活动 (3)价值流动:让价值增值环节无间断的流动起来;去掉生 产环节中一切无用的东西,每个工人及其岗位的安排原则 是必须增值,撤除一切不增值的岗位;精简产品开发设计、 生产、销售、管理中一切不产生附加值的工作。 (4)需求拉动:让用户按需要拉动生产,而不是把用户不太 想要的产品强行推给客户; (5)尽善尽美:用尽善尽美的价值创造过程为用户提供尽善 尽美的价值。追求精益求精和不断改善。
精益生产现场改善培训案例

精益生产现场改善培训案例近年来,精益生产成为了企业提高效率和降低成本的重要手段。
为了帮助员工更好地理解和应用精益生产的原则和工具,某公司决定开展精益生产现场改善培训。
以下是培训中的一些案例,展示了精益生产在实际生产现场中的应用。
1. 5S整理工作站在一家制造公司的生产线上,工作人员经常因为工具和物料摆放混乱而浪费时间。
通过培训,员工学习了5S整理原则,并开始整理工作站。
他们将工具、物料和文件按照使用频率和使用顺序进行了布置,使得操作更加流畅和高效。
2. 平衡生产线在一家汽车装配厂,生产线上的工作站之间存在明显的瓶颈,导致生产效率低下。
通过培训,员工学习了平衡生产线的方法,重新安排了工作站的任务分配,使得生产线上的工作负载更加均衡,提高了整体生产效率。
3. 精益布局设计一家仓库经常出现货物堆积、拣选错误等问题,影响了物流运转的效率。
通过培训,仓库管理人员学习了精益布局设计的原则,并重新规划了货物存放和拣选区域。
优化后的布局使得货物的流动更加顺畅,减少了物料处理时间和错误率。
4. 消除浪费在一家食品加工厂,员工经常因为物料不足、工具失效等原因停止工作,造成了生产线的停滞和浪费。
通过培训,员工学习了消除浪费的方法,如及时补充物料、定期检修和维护工具等。
这些措施使得生产线的运转更加稳定,减少了停机时间和浪费。
5. 持续改进一家电子产品制造公司发现产品的良品率低,经常出现质量问题。
通过培训,员工学习了持续改进的方法,如设立质量检查点、建立问题解决小组等。
员工积极参与改进活动,通过不断的问题分析和改进措施,最终提高了产品的质量和良品率。
6. 价值流映射在一家纺织厂,生产线上的流程繁杂,导致生产周期长和库存积压。
通过培训,员工学习了价值流映射的方法,绘制了整个生产过程的价值流图,并找出了各个环节中的浪费和瓶颈。
根据分析结果,他们采取了相应的改进措施,缩短了生产周期和库存周转时间。
7. 一次性设备准备在一家医药公司的生产车间,设备准备时间过长,影响了生产效率。
《精益生产案例讲课》课件
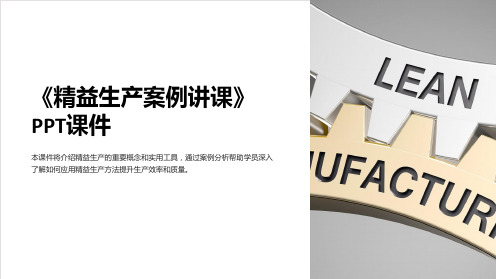
2 Kanban看板
利用Kanban看板管理和控 制生产活动,减少库存和 提高响应速度。
3 5S整理法
通过整理、整顿、清扫、 清洁和纪律的方式,创造 一个良好的工作环境。
案例分析
运用前面所学的精益生产知识和技巧,深入分析真实案例,从中获得宝贵的实践经验和启发。
1
问题诊断
通过对问题进行分析和诊断,找出根本
电子产品装配
了解如何应用精益生产工具和方 法,改善电子产品装配过程中的 问题并提高产线效率。
食品加工工厂
探索在食品加工领域中,如何运 用精益生产原则简化流程和提高 生产效率。
精益生产概述
深入了解精益生产的核心理念和基本原则,了解其对企业生产流程的重要影响。
1 减少浪费
通过消除不必要的环节和活动,提高生产效率和资源利用率。
改进成果
经过精益生产的实施,我们 显著提高了生产效率和产品 质量,取得了令人瞩目的成 果。
问题和讨论
为了帮助学员更好地理解精益生产,我们将与学员进行互动,并解答他们的问题和疑虑。
常见问题
解答学员常见的关于精益生产的问题,如如何应用 到不同行业和规模的企业中。
实战经验分享
和学员分享实战经验,让他们获得更多实际应用的 启发和思路。
价值流分析
通过深入理解价值流,找到非 价值增加的环节,并优化生产 过程。
标准化工作流程
建立标准的工作流程,确保每 个环节都能按照最佳实践进行。
精益生产工具和方法
介绍精益生产常用的工具和方法,如价值流图、Kanban看板、5S整理法过绘制价值流图,识别 出不必要的步骤和浪费, 提高生产效率。
《精益生产案例讲课》 PPT课件
本课件将介绍精益生产的重要概念和实用工具,通过案例分析帮助学员深入 了解如何应用精益生产方法提升生产效率和质量。
精益生产培训通用课件
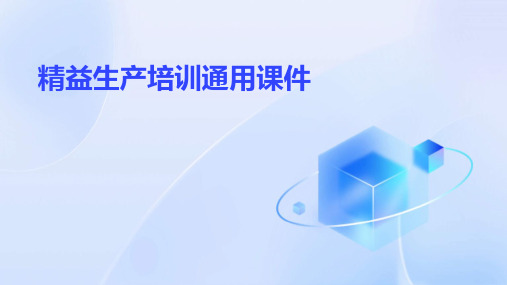
案例二:某电子产品制造公司的精益生产实践
总结词
该电子产品制造公司通过引入精益生产理念和工具,实 现了生产效率提升、产品质量提高和成本降低。
详细描述
该公司在精益生产实践中,注重员工培训和跨部门协作 ,采用了单件流、看板系统、快速换模等工具,并应用 了自动化和智能化设备,实现了生产流程的简化和优化 ,提高了生产效率和产品质量。
消除浪费
总结词
消除浪费是精益生产的核心原则之一,旨在消除生产过程中 的非增值活动,提高效率和效益。
详细描述
消除浪费需要从产品设计、流程优化、生产计划等方面入手 ,减少库存、降低成本、优化人力资源等非增值环节。同时 ,需要关注员工培训和流程标准化,确保消除浪费的措施得 到有效执行。
拉动式生产
总结词
推广成功案例
及时总结和分享成功案例,鼓励其他 部门或团队进行效仿。
定期评估与调整
定期对生产过程进行评估和调整,以 确保其符合市场需求和公司战略。
如何推广精益生产理念与工具
培训与教育
实践与总结
通过内部培训、外部培训、在线学习等方 式,普及精益生产理念和工具。
鼓励员工在实际工作中运用精益生产理念 和工具,不断总结经验并分享。
跨部门交流
外部参观学习
组织不同部门之间的交流活动,分享各自 在推行精益生产方面的经验和教训。
组织参观其他优秀企业,学习他们在精益 生产方面的成功经验。
06
总结与展望
对精益生产的总结与评价
总结
精益生产是一种以客户需求为导向,通 过消除浪费、提高生产效率和质量,实 现持续改进的生产方式。它在制造业、 服务业等领域都有广泛的应用,可以帮 助企业提高竞争力。
趋势分析
近年来,全球制造业和服务业都在积极探索和实践精益生产的理念和方法。未来,精益生产有望在全球范围内得 到更广泛的应用和推广。同时,随着企业对于员工培训和技能提升的重视,精益生产的培训和教育也将得到进一 步的发展和普及。Leabharlann THANKS感谢观看
精益生产讲座071216

庫存 浪費
常見的庫存: ☆ 原材料、零部件 ☆ 半成品 ☆ 成品 ☆ 在製品 ☆ 輔助材料 ☆ 在途品
庫存的危害: ☆ 額外的搬運儲存成本 ☆ 造成空間浪費 ☆ 資金佔用(利息及回報損失) ☆ 物料價值衰減 ☆ 造成呆料廢料 ☆ 造成先進先出作業困難 ☆ 掩蓋問題,造成假像
庫存造成額外成本
製造過多/過早 浪費
等待不創造價值
搬運浪 費
空間、時間、人力和工具 浪費
搬運過程中的放置、堆積、移 動、整理等都造成浪費。
移動費時費力
浪費
常見的等待現象: ☆ 材料損失 ☆ 設備折舊 ☆ 人工損失 ☆ 能源損失 ☆ 價格損失 ☆ 訂單損失 ☆ 信譽損失
不良造成額外成本
動作
浪費
常見的12種浪費動作: ① 兩手空閒 ② 單手空閒 ③ 作業動作停止 ④ 動作幅度過大 ⑤ 左右手交換 ⑥ 步行多
56
第五講:精益生產的問題與困擾
生產效率不升反降 高層主管的動力不夠 幹部不願改變 員工不願改變 生產線經常停線 機器太大 設備經常壞掉
生產線上的問題更多了
57
精益生產的本質
解決問題
降低庫存
暴露問題
58
何謂『善』?
善 百戰百勝,非 之善者也,不戰而屈人之兵, 善之善者也,故上兵伐謀,其次伐交,其次伐
44
自働化—將人類的智慧賦予機器
作業面要窄; 物流容易; 容易移動; 容易換模; 容易改造;
一個流動; 逆時方向; 防錯裝置; 各自獨立; 絕對安全;
45
物量的安定
切換:在生產不同類別產品需要更換時,生產線 必須暫時停止生產活動,以便能更換并確定新的 產品所需要的工作條件,這種更換設定的動作就 稱為切換.
精益生产——改变世界的生产方式和案例讲解

丰田公司一定有一种抗拒风险的强有力的 方法
案例分析一
通过丰田工厂生产现场的分析探究TPS的奥秘
观看日本丰田某零部件工厂VCD,该厂建 厂大约40多年,厂房陈旧、空间狭小,生 产设备生产设备普普通通,但其生产效率 是国内企业的几倍甚至几十倍,质量水平
达到3PPM超过了6 σ 。
试分析其生产现场作业的特点,其实现高 效率、高质量水平的因素是什么?
精益生产既是一种以最大限度地减少企业生产所占用的资 源和降低企业管理和运营成本为主要目标的生产方式,同 时它又是一种理念,一种文化。实施精益生产就是决心追 求完美的历程,也是追求卓越的过程。
精益生产案例讲课件

第三篇 搬运和改善搬运
搬运和文化 搬运的定义 改进搬运方式的目的 改进搬运(MH)的步骤 工序分析和搬运 搬运分析 布置
目录
1、搬运的定义
点击此处添加正文,请言简意赅的阐述观点。
1.1生产现场和运输业的搬运
点击此处添加正文,请言简意赅的阐述观点。
1.2搬运和停滞
点击此处添加正文,请言简意赅的阐述观点。
追求零浪费!!
精益生产方式的内涵
尊重人格 鼓舞士气
设备“智能化”
全员“TQC”
准时化
准时生产“零库存”
自働化
质量控制“零缺陷”
进行团队改善活动
减少作业时间转换
优化生产线布局
多能训练“少人化”
流水作业“一个流”
看板管理拉动生产
计划指导均衡生产
5
安全性
你们的安全方面是否存在问题、事故是否很多、是否有不安全作业
6
士气
你们是否有士气、干劲 作业人员关系是否存在问题、作业人员配置是否合理
2.2现场分析 ⑴对事实进行实事求是的分析
序号
项目
问题
1 2 3 4 5 6
对象 作业人员 目的 场所、位置 时间 方法
标准作业“程序化”
弹性工作“少耗工”
彻底排除浪费降低成本
JAC价值流分析
减少库存,使之最小化
遵循准时化的原则,由顾客需求拉动生产
前道工序的售出情况也就是最终工序的使用情况。 零库存、零距离、零缺陷。 整个供应链以同一生产节拍(即最终产品的销售速度)来一个一个地生产,供应。
最后工序
销售
第1类动作 为了进行作业,对作业对象如零部件、材料、夹具、工具等进行提取、使用、加工、组装等实际作业,以及作业完成之后的必要整理。包括以下动作: 空手 抓 搬运 调整角度 拆分 使用
精益生产案例讲课(jac)课件

03
JAC公司精益生产实施过程
价值流分析
总结词
识别并分析产品或服务的全部价值流,包括从 原材料到最终产品的所有活动。
01
总结词
确定价值流中的关键过程和活动。
03
总结词
制定改进计划并实施。
05
02
详细描述
JAC公司通过价值流分析,识别出生产过程 中的瓶颈和浪费,为后续的流程改进提供了 依据。
06
04
总结词
采用自动化技术减少人工干 预和错误。
详细描述
JAC公司引入了自动化生产 线和智能设备,减少了人工 干预和错误,提高了生产效
率和产品质量。
总结词
识别并消除生产过程中的浪费。
详细描述
通过分析生产过程,JAC公司发现了多种浪 费现象,如过度生产、库存积压等,采取 措施消除这些浪费,降低了成本。
总结词
提高生产自动化程度。
可持续发展
企业应关注可持续发展,通过精益 生产减少浪费和排放,实现绿色生 产。
全球化运营
随着全球化进程的加速,企业应加 强全球化运营能力,拓展国际市场, 提高竞争力。
THANK YOU
感谢聆听
详细描述
通过价值流分析,JAC公司确定了关 键过程和活动,如原材料采购、生产 计划、质量控制等,为后续的改进提 供了重点。
详细描述
基于价值流分析的结果,JAC公司制定了详细 的改进计划,包括改进流程、提高设备效率等, 并逐步实施。
流程改进
总结词
优化生产流程,提高生产效率和产品质量。
详细描述
JAC公司通过分析现有流程,发现并改进了多个低效环 节,如减少生产准备时间、优化物料搬运等,提高了整 体效率。
建立有效的监控和反馈机制。
精益生产-改善项目案例ppt课件

经过改善,共缩短配送距离400米
制定总装二分厂分装区配送标准
经过改善,共缩短配送距离615米
33
Y3的改善 摘录2
配送器具组合“轮子化”
物流配送器具重新设计,按照每个单元车进行物料组合配送。 按照牵引车进行组合排布,使各岗位物料最大化组合配送。
牵引车的组合以及单位 器具的组合, 物料组合度提高50%。
配送交叉 十字路口
说明:红色圈圈标注的区域是交叉比较严重的地方,包括物流配送、成品车、人 流,通过对这一区域的物流路线进行调整,分散至2号厂房西门进出,大大减少 配送路线的交叉。提高配送效率。
31
Y3的改善 摘录1
钣金件存放区
包转件存放区
底盘、包装件存放区
顶盖、纸箱存放区
调整前
调整后
32
Y3的改善 摘录1
6
Y1-生产组织模式变革
“生产组织模式变革”改善路径图
订单计划体系优化 供应保障体系改善 制造模式变革 1、”三天不变”刚性计划; 2、当天作业实物配套率提升; (重点为恰时供货物料改善) 3、作业尾数快速补货流程; 4、自制件在制品库存降低;
当天排产计划变动率降低; 当天作业完成率提升; 建立作业尾数快速补货流程 提升恰时物料实物配套率;
年度供销存大纲 三月滚动计划 月度意向计划 物流订单、生产订单
销售公司
销售公司年度大纲
三月滚动销售计划
月度销售计划
物流订单、定制订单
中国营销总部
年度供销存大纲
三月滚动供销存计划
月度供销存检讨
明晰订单衔接流程 责任清晰化 提高计划准确性
年度供货计划、仓储物流 规划
三月滚动供货计划、 仓储物流资源检讨
精益生产案例分享ppt课件
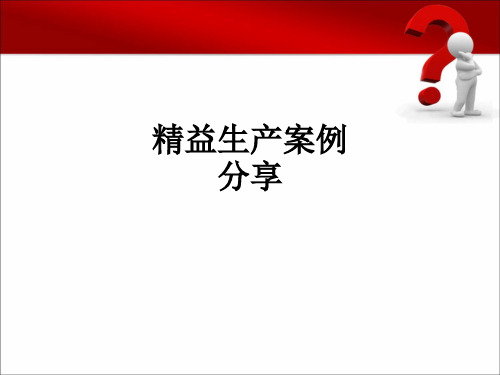
value
to a product or service 对最终产品或服务 不增加价值的 过程
Waste of Inventory 库存浪费
Any supply
in excess of process requirements necessary to produce goods 任何超过加工必须的 物料供应
Inventory Covers All Problem 库存掩盖所有问题
库存水平
维修问题
效率问题
质量问题
交货问题
Low Down Inventory To Expose Problem 通过降库存暴露问题
库存水平
维修问题
效率问题
质量问题
交货问题
Waste of Waiting 等待
Idle Time That Is Produced When Two Dependent Variables Are Not Fully Synchronized
改进后
1.改进后2人,充分发挥个人效益 2.改进后实现单件流 3.交付周期缩短50% 4.采取防错,当场发现 5.员工收入5800-6200
生产效率的提升大家自己算
12
JIT与TPS
Just In Time
适品 · 适量 · 适时
JIT的基本思想是:只在需要的时候、按需要 的量、 生产所需的产品,故又被称为准时制生产、适时生产方式、 看板生产方式。 JIT的核心是:零库存和快速应对市场变化。 JIT的概念最早由日本丰田汽车提出,在大野耐一带领 下创造出一套具竞争优势的运作方式,人们习惯称之为JIT 模式,又称丰田生产方式(TPS)。
等待浪费
《精益生产案例》课件

快速反应生产
追求快速设计、生产和交付,以 满足市场需求的变化。
总结和展望
1
精益生产的优势
提升生产效率、降低成本、提高产品质量和客户满意度。
2
不同行业中的应用
精益生产在各行各业具有广泛的应用前景和可持续发展空间。
3
创新与持续改进
精益生产需要不断创新和改进,以适应快速变化的市场需求。
《精益生产案例》PPT课 件
本课件介绍了精益生产的基本概念和原则,以及在不同行业中的应用案例和 效果分析。
精益生产介绍
精益生产是一种以减少浪费为核心的生产管理方法,旨在提高生产效率和产 品质量。
汽车制造业中的精益生产
Toyota生产系统
通过标准化工作流程、零库存和持续改进来提 高生产效率。
单件流生产
临床试验优化
通过优化试验方案、简化数据采集,提高试验 效率。
标准化操作
确保每个环节按照规定程序操作,避免操作失 误和品质问题。
溯源管理和质量追踪
建立完善的溯源系统,对生产过程进行全面追 踪和质量控制。
服装制造业中的精益生产
多样化设计
根据市场需求和产能灵活调整产 品设计和生产线布局。
定制化生产
利用精益生产原则实现小批量、 个性化定制服装生产。
供应链优化
与供应商建立紧密合作关系,减 少库存和交货时间。
食品加工业中的精益生产
1
原材料采购和质检
确保原材料新鲜、安全,并符合质量标
生产流程优化
2
准。
简化工艺流程,减少时间浪费和能源消
耗。
3
产品包装和分拣
采用自动化设备,提高包装效率和准确 性。
医药制造业中的精益生产
精确配药
- 1、下载文档前请自行甄别文档内容的完整性,平台不提供额外的编辑、内容补充、找答案等附加服务。
- 2、"仅部分预览"的文档,不可在线预览部分如存在完整性等问题,可反馈申请退款(可完整预览的文档不适用该条件!)。
- 3、如文档侵犯您的权益,请联系客服反馈,我们会尽快为您处理(人工客服工作时间:9:00-18:30)。
供应商管理 与评估管理 库存 管理 看板 设定 与管理 MRP ERP 系统 设计 管理
可以做生产线设计的IEr
PTS法标 可靠性 Layout分 准时间 评估 析改善 物流系统 作业标准化
IE工程师入门
入 门 ● 教 程●
员
● 第一线监督者
精益改善 生产 项目管理 规格 产能 可以做流程改善的IEr 制造现场职员 标准 联合作 标准时 作业 程序 快速转产 设定 Cell生产 业分析 间ST设定 评估 分析 的管理 多能工 一个流 可以做作业改善的IEr 生产技术 评价 工艺设计 动作研究 时间研究 IE思想 稼动分析 管理 动作经济原则 作业分析 精益思想 (W.S) 作业 编成 平衡率Line 生产 balancing 计划 CT 设定
成本是否有所提高、原材料燃料单耗是否增加 你们的生产周期是多少?是否出现了赶不上交货期、生 产时间是否可以缩短 你们的安全方面是否存在问题、事故是否很多、是否有 不安全作业 你们是否有士气、干劲 作业人员关系是否存在问题、 作业人员配置是否合理
制造更好的产品
创造更美好的社会
2.2现场分析
⑴对事实进行实事求是的分析 基于5w1h的调查表
接触面积过大 减小接触面 积
改进
但效果不是很好
制造更好的产品
创造更美好的社会
表面完全无接触
改变方式
制造更好的产品
创造更美好的社会
改善四原则
原则 目标 不能取消吗? 取消又会变成如何? 例子 检查的省略 配置变更的搬运省略
取消 简化
不能更为简单吗?
能否把两种以上的工程 合而为一? 能否重排工程?
作业的重新估计 自動化
原则4:缩短移动通路距离,并使之简单化
原则5:一般性原则
制造更好的产品
创造更美好的社会
2.4制定对策(考虑改进方案)
要有新的 见解、灵 活的思考
要打破 固定观 念
善于向长 辈学习
有灵感 时马上 记录
改进方案的编成
组合各 种构思 不要忘记 评价 试试使用 构思技巧
对工作的热爱 不输给任何人 的专业精神
制造更好的产品
创造更美好的社会
按型号统计各工序时间发现:
1、前轴总成装配10道装配零部件型号多, 员工来回需走6步,走动时间浪费,且弯腰 动作频繁容易疲劳; 2、装配20道线上工具放置较远,员工拿取 定扭工具需走两步,严重浪费时间。
制造更好的产品
创造更美好的社会
1、员工装配时为拿取零部件需来回走动6步
制造更好的产品
创造更美好的社会
2、员工拿取定扭工具需跨两步
制造更好的产品
创造更美好的社会
分析:
1、能否让员工在左右一步以内拿到工件?
能否杜绝弯腰动作?
2、能否不需跨步,伸手就能拿到工具?
制造更好的产品
创造更美好的社会
针对工位 跨步拿取 零部件的 动作浪费, 我们对10 道、80道 增加了辅 助设施。
Ⅰ第1类:作业进行时必 要的动作; Ⅱ第2类:使第1类动作 推迟进行的动作; Ⅲ第3类:没有进行作业 的动作。
制造更好的产品
创造更美好的社会
1、第1类动作
为了进行作业,对作业对象如零部件、材料、夹具、工 具等进行提取、使用、加工、组装等实际作业,以及作 业完成之后的必要整理。包括以下动作: ⑴空手
制造更好的产品
创造更美好的社会
自主设计制作本体流水装配线,在人员没有改变的前 提下,生产能力从加班日产200台提升到8小时产250台; 而且改变了长期以来落后的摆地摊装配方式。
制造更好的产品
创造更美好的社会
推进精益生产: 1、现场是基础; 2、改善是手段。
库房的仓位
形迹管理
制造更好的产品
创造更美好的社会
制造更好的产品
创造更美好的社会
精益生产之 实战篇
2008年5月
制造更好的产品
创造更美好的社会
何为精益生产方式?
精益生产是麻省理工学院专家对日本 “TPS”的赞誉之称。 精,即少而精,不投入多余的生产要素, 只是在适当的时间生产必要数量的市场急需 产品(或下道工序急需的产品);益,即所 有经营活动都要有益有效,具有经济性。
怎么办?通过在夹具上增设限位块,彻底解决 了由于标识不清,以致前轴主销孔钻反而造成 的工废: 新增 设限 位块
制造更好的产品
创造更美好的社会
第二篇 动作分析
1、IE的创立 2、动作及动作分析法
3、动作改善的目标和顺序
4、基本动作分析法与作业改善
5、动作分析法的改善实例
制造更好的产品
创造更美好的社会
⑵抓
⑶搬运 ⑷调整角度 ⑸拆分 ⑹使用
制造更好的产品
创造更美好的社会
⑺组合 ⑻松开手
2、第2类动作
⑴寻找
3、第3类动作
⑴保持
⑵发现
⑶选择 ⑷考虑 ⑸准备
⑵不可避免的待工
⑶休息
制造更好的产品
创造更美好的社会
4.2、基本动作分析的改善要点
一旦完成基本动作分析,接下来就要根据分析的结果找 出问题的要点,也就是要发现动作中存在的不经济、不 均衡和不合理现象。 基本动作分为以下三类: Ⅰ第1类:作业进行时必要的动作; Ⅱ第2类:使第1类动作推迟进行的动作;
制造更好的产品
创造更美好的社会
1、搬运的定义 1.1生产现场和运输业的搬运 1.2搬运和停滞 2、改进搬运方式的目的
2.1改进搬运方式的目的
加工会使产品增加价值,而搬运是不会增加价值的。
2.2改进搬运方式的着眼点
制造更好的产品
创造更美好的社会
2.3搬运的原则
原则1:达到有效应用化 原则2:自动化 原则3:消除待料停工和空搬运
制造更好的产品
创造更美好的社会
标准作业“程序化”
减少作业时间转换
流水作业“一个流”
优化生产线布局
设备“智能化” 全员“TQC”
计划指导均衡生产
看板管理拉动生产
尊重人格 进行团队改善活动 鼓舞士气
JAC价值流分析
制造更好的产品
创造更美好的社会
制造更好的产品
创造更美好的社会
减少库存,使之最小化
制造更好的产品
可以做生产线改善的IEr
制定 年度 改善 方针 目标
生产 周期 管理
班组长
制造更好的产品
创造更美好的社会
第一篇
工程分析
1、工业工程与工序改善
2、工序改善的步骤 3、工序分析法
4、产品工序分析法
5、作业人员工序分析法
制造更好的产品
创造更美好的社会
1、工业工程与工序改善
1.1工业管理的定义:
工业工程是英文INDUSTRIAL ENGINEERING 的译文,工业工程是为了排除工作中的不经济、 不均衡和不合理现象,使我们更加舒适、快捷、 低成本生产高质量的产品,更好的为客户提供 服务的手法。
如图:通过不懈努力,所有工序的刀、辅、量具有 了“新家”,让它们也实现了定置
制造更好的产品
创造更美好的社会
对B1/6700前轴钻主销孔 工序夹具增设防错装置, 防止钻反。有效保证该工 序质量。
B1/6700前轴 钻主销孔夹具 增加防错装置
制造更好的产品
创造更美好的社会
C576限位装置
自动化
一个人操作 4台机床
2、工序改善的步骤 —— 2.1问题的发生发现
序号 调查项目 调查重点 1 生产量、 你们的生产量是否有所下降、你们是否能提高生产量、 是否因工作人员过多影响生产效率 生产率 你们的产品质量是否有所下降、不合格率是否变得高了、 2 质量
合格率是否能提高、产品缺点是否太多
3 4 5 6
成本 交货期 安全性 士气
序号 1 2 3 4 5 6 项目 对象 作业人员 目的 场所、位置 时间 方法 问题 什么(what) 谁(who) 为什么(why) 什么地方(where) 什么时候(when) 怎样(how)
进行的?
⑵定量分析
制造更好的产品
创造更美的社会
举例:根本原因的找出(5W1H) 清洗后,主销表面有锈迹,原因是注销表面与 器具接触处有积水
两种以上的加工,能否 同时进行作业 加工与检查同时进行 变更加工順序,以便提 高效率
合并
重排
制造更好的产品
创造更美好的社会
例:1、器皿的配置:
制造更好的产品
创造更美好的社会
制造更好的产品
创造更美好的社会
2、过滤台(装置的配合台) 过滤台
过滤台
作业台减少有 效利用空间
制造更好的产品
创造更美好的社会
制造更好的产品
创造更美好的社会
改进前后对比
原来状态
一人操作两台设备 两人每小时精车25台 产品深度不好控制 需要手动操作 两人同时上下班或加班
现在状态
一人操作四台设备 一人每小时精车20台 利用限位自动停车 深度不需人工控制
两人倒早晚班或只要一 人生产
制造更好的产品
创造更美好的社会
关于现场IE管理
创造更美好的社会
遵循准时化的原则,由顾客需求拉动生产
前道工序的售出情况也就是最终工序的使用情况。 零库存、零距离、零缺陷。 整个供应链以同一生产节拍(即最终产品的销售
速度)来一个一个地生产,供应。
看板 看板 看板 看板
销售
前工序 前工序 前工序 最后工序
拉动式(后补充)生产
一个流生产:
一、工程分析
二、动作分析
三、搬运与布置
四、时间分析
制造更好的产品
创造更美好的社会
IE手法与工作职责的基本关系
管理改善必修
实 践 教 程
● 生产副总、总监