对轧制弹簧扁钢的冷床控制优化设计
八钢650机组轧制弹扁的生产组织优化
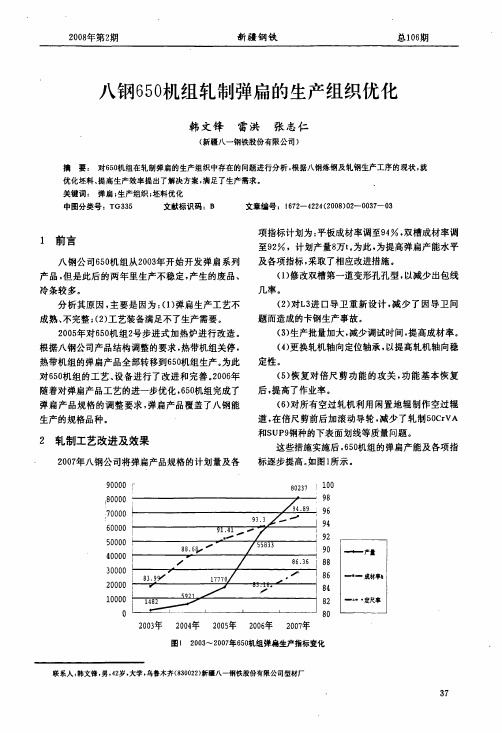
2008年第2期新疆钢铁总106期八钢650机组轧制弹扁的生产组织优化韩文锋雷洪张志仁(新疆八一钢铁股份有限公司)摘要:对650机组在轧制弹扁的生产组织中存在的问题进行分析。
根据八钢炼钢及轧钢生产工序的现状,就优化坯料、提高生产效率提出了解决方案,满足了生产需求。
关键词:弹扁;生产组织;坯料优化中图分类号:T G 335文献标识码:B文章编号:1672--4224(2008)02一0037一031前言八钢公司650机组从2003年开始开发弹扁系列产品.但是此后的两年里生产不稳定,产生的废品、冷条较多。
分析其原因,主要是因为:(1)弹扁生产工艺不成熟、不完整;(2)工艺装备满足不了生产需要。
2005年对650机组2号步进式加热炉进行改造。
根据八钢公司产品结构调整的要求,热带机组关停,热带机组的弹扁产品全部转移N 650机组生产。
为此对650机组的工艺、设备进行了改进和完善。
2006年随着对弹扁产品工艺的进一步优化,650机组完成了弹扁产品规格的调整要求,弹扁产品覆盖了八钢能生产的规格品种。
2轧制工艺改进及效果2007年八钢公司将弹扁产品规格的计划量及各项指标计划为:平板成材率调至94%,双槽成材率调至92%,计划产量8万t 。
为此,为提高弹扁产能水平及各项指标,采取了相应改进措施。
(1)修改双槽第一道变形孔孔型,以减少出包线几率。
(2)对L3进口导卫重新设计,减少了因导卫问题而造成的卡钢生产事故。
(3)生产批量加大,减少调试时间,提高成材率。
(4)更换轧机轴向定位轴承,以提高轧机轴向稳定性。
(5)恢复对倍尺剪功能的攻关,功能基本恢复后,提高了作业率。
(6)对所有空过轧机利用闲置地辊制作空过辊道,在倍尺剪前后加滚动导轮,减少了轧制50C r V A 和S U P 9钢种的下表面划线等质量问题。
这些措施实施后。
650机组的弹扁产能及各项指标逐步提高。
如图l 所示。
//94.8993一.3夕一9.1.,41,一/88.6p ,7/55833./7/86.3683.!少717770/…,,.∥7㈨,//“岁‘1:::/.2003年2004年2005年2006年2007年圈12003~2007年650机组弹扁生产指标变化联系人:韩文锋。
型材轧制中冷床控制系统优化
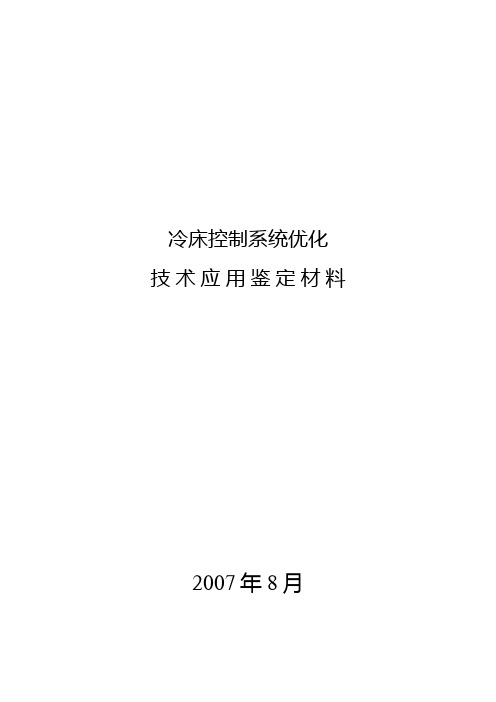
冷床控制系统优化技术应用鉴定材料2007年8月目录鉴定材料之一--------冷床控制系统优化鉴定大纲鉴定材料之二--------冷床控制系统优化工作报告鉴定材料之三--------冷床控制系统优化技术总结报告鉴定材料之四--------冷床控制系统优化经济效益分析报告鉴定材料之五--------冷床控制系统优化使用报告鉴定材料之一冷床控制系统优化鉴定大纲第一小型轧钢厂2007年8月鉴定大纲山东省冶金工业总公司对济钢集团总公司第一小型轧钢厂完成的《冷床控制系统优化》项目进行技术鉴定,鉴定委员会制定鉴定大纲如下:一、项目名称:冷床控制系统优化二、项目来源:自选三、项目内容经过对控制程序的仔细分析和细致的现场观察,对冷床区控制程序进行全面的优化,主要有:升降裙板控制使用高实时性算法,提高位臵控制的精度;对各种故障报警进行全面检测分析,并制定智能控制策略确保冷床不出现乱钢;设定参数自动根据线速度进行选择,减轻工人劳动强度等等;在满足工艺要求的情况下尽量减少检测元件的数量,提高运行的可靠性。
确保了全线速度提高到17.5m/s以上,而且故障率大大的降低。
不仅提高了机时产量而且确保了作业率。
四、项目起止时间2004年9月~2006年12月五、承担单位:济钢第一小型轧钢厂六、鉴定材料及提供单位1、冷床控制系统优化鉴定大纲…………………………………鉴定委员会2、冷床控制系统优化工作报告…………………………………济钢第一小型轧钢厂3、冷床控制系统优化技术总结报告…………………………………济钢第一小型轧钢厂4、冷床控制系统优化使用情况报告…………………………………济钢第一小型轧钢厂5、冷床控制系统优化经济效益分析报告…………………………………济钢第一小型轧钢厂六、鉴定程序1、讨论通过鉴定大纲2、听取工作报告3、听取技术报告4、听取应用情况报告5、听取经济效益分析报告6、现场考察7、专家评议8、讨论通过鉴定意见9、鉴定委员会委员签字鉴定委员会2007年8月鉴定材料之二:冷床控制系统优化工作报告第一小型轧钢厂2007年8月冷床控制系统优化工作报告一、课题来源:2003年底一小型进行全连轧改造,配备120米步进式冷床一台,完成对棒材的冷却和剪切收集。
冷床传动系统中传动轴的优化设计论文

冷床传动系统中传动轴的优化设计论文冷床传动系统中传动轴的优化设计论文摘要:在热轧钢管生产过程中,步进式冷床作为必不可少的设备之一,具有极其重要的作用。
而传动系统中的传动轴作为步进式冷床的重要组成部分,是钢管完成步进动作的关键影响部件。
本文以步进式冷床的结构及其工作原理为着手点,对步进式冷床传动系统合成运动进行了深入分析,并在此基础上提出了传动轴的优化设计建议,以期为步进式冷床传动系统的优化提供理论支持。
关键词:步进式冷床;传动系统;传动轴冷床作为热轧钢管生产过程中的重要设备,步进式冷床因其运行平稳、钢管表面保存完好等特点,近年来在生产实践中逐步得到了推广使用,但作为新兴的冷床设备仍存在很大的改进空间。
因此,本文笔者将结合自己的工作实践就步进式冷床传动系统中传动轴的优化设计问题进行探究,以供商榷。
1步进式冷床的结构及其工作原理1.1步进式冷床的结构动齿条、静齿条、偏心轮、传动轴、长轴、电机以及拖钢架、拨钢器是构成步进式冷床的主要组成部分(如图1所示)。
其中,动齿条负责以步进式将钢管从静齿条上往后移,固定在支座上的静齿条承接轧件任务,偏心轮依靠电机并利用长轴带动传动轴实现转动,一般步进式冷床会将平衡摆配置到偏心轮传动轴上,以维持动齿条的平衡[1]。
1.2步进式冷床的工作原理步进式冷床的工作原理为:在起始位置时,偏心轮处于低位,静齿条高于动齿条;当钢管滚入静齿条,动齿条向高位步进,偏心轮由电机带动同时向高位移动至最高点,之后往下运行至起始点平衡位置,完成一个周期,如此循环往复。
2步进式冷床传动系统合成运动分析2.1步进式冷床传动系统中主轴偏心轮的合成运动分析步进式冷床传动系统中主轴偏心轮在运作过程中,呈现出360°径向圆周轨迹,床面主传动偏心轮围绕固定点以一个偏心距为半径,呈现出顺时针圆周轨迹[2]。
由步进式冷床传动系统中主轴偏心轮的合成运动分析可以看出,动齿条步进大致可以划分成两大阶段,首先在90°至270°这一过程中,动齿条全程参与托钢动作,并发挥主要的作用;其次在270°至90°这一过程中,动齿条完全不参与托钢动作,而是脱离轧件,为进行下一次托钢动作做准备,是两个步进循环周期间所应有的辅助运动过程。
宣钢小型轧钢厂冷床优化改造
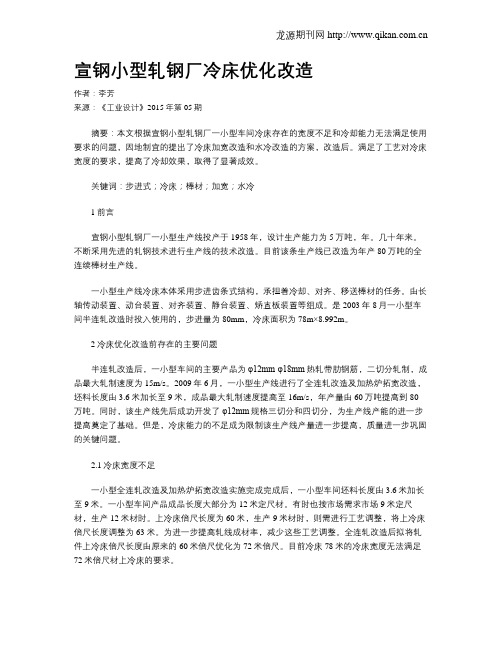
宣钢小型轧钢厂冷床优化改造作者:李芳来源:《工业设计》2015年第05期摘要:本文根据宣钢小型轧钢厂一小型车间冷床存在的宽度不足和冷却能力无法满足使用要求的问题,因地制宜的提出了冷床加宽改造和水冷改造的方案,改造后。
满足了工艺对冷床宽度的要求,提高了冷却效果,取得了显著成效。
关键词:步进式;冷床;棒材;加宽;水冷1前言宣钢小型轧钢厂一小型生产线投产于1958年,设计生产能力为5万吨,年。
几十年来。
不断采用先进的轧钢技术进行生产线的技术改造。
目前该条生产线已改造为年产80万吨的全连续棒材生产线。
一小型生产线冷床本体采用步进齿条式结构,承担着冷却、对齐、移送棒材的任务。
由长轴传动装置、动台装置、对齐装置、静台装置、矫直板装置等组成。
是2003年8月一小型车间半连轧改造时投入使用的,步进量为80mm,冷床面积为78m×8.992m。
2冷床优化改造前存在的主要问题半连轧改造后,一小型车间的主要产品为φ12mm-φ18mm热轧带肋钢筋,二切分轧制,成品最大轧制速度为15m/s。
2009年6月,一小型生产线进行了全连轧改造及加热炉拓宽改造,坯料长度由3.6米加长至9米,成品最大轧制速度提高至16m/s,年产量由60万吨提高到80万吨。
同时,该生产线先后成功开发了φ12mm规格三切分和四切分,为生产线产能的进一步提高奠定了基础。
但是,冷床能力的不足成为限制该生产线产量进一步提高,质量进一步巩固的关键问题。
2.1冷床宽度不足一小型全连轧改造及加热炉拓宽改造实施完成完成后,一小型车间坯料长度由3.6米加长至9米。
一小型车间产品成品长度大部分为12米定尺材。
有时也按市场需求市场9米定尺材,生产12米材时。
上冷床倍尺长度为60米,生产9米材时,则需进行工艺调整,将上冷床倍尺长度调整为63米。
为进一步提高轧线成材率,减少这些工艺调整。
全连轧改造后拟将轧件上冷床倍尺长度由原来的60米倍尺优化为72米倍尺。
目前冷床78米的冷床宽度无法满足72米倍尺材上冷床的要求。
优特钢冷床上钢系统的优化与改造
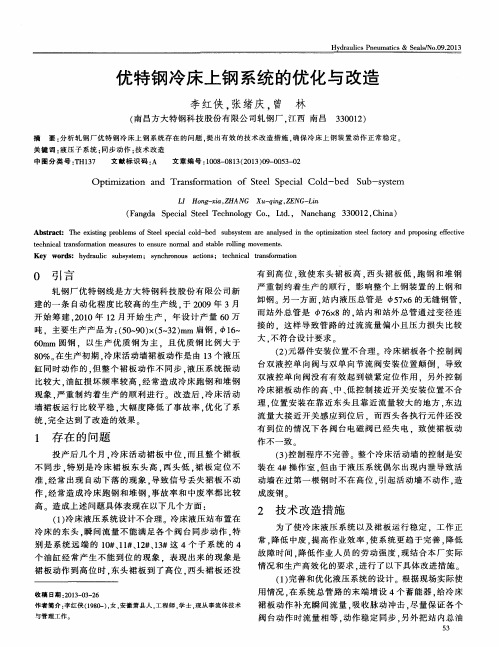
优 特钢冷床 上钢 系统 的优化 与改造
李红侠 , 张绪庆 , 曾 林
( 南 昌方 大特 钢科 技 股份 有 限公 司轧钢 厂 , 江西 南 昌
摘
3 3 0 0 1 2 )
墙裙 板 运行 比较 平稳 . 大 幅度 降低 了 事故 率 , 优 化 了系
统. 完全 达 到 了改造 的效 果 。
1 存 在 的 问题
投 产后 几 个 月 . 冷 床 活 动裙 板 中位 . 而且 整 个 裙 板 不 同步 , 特 别是 冷 床裙 板 东 头 高 , 西头低 , 裙 板 定 位 不
Байду номын сангаас
要: 分 析 轧 钢 厂 优 特 钢 冷 床 上 钢 系统 存 在 的 问题 , 提 出有 效 的 技 术 改 造 措 施 , 确 保 冷床 上钢 装 置 动 作 正 常 稳 定 。
关键词 : 液 压 子 系统 ; 同步动作 ; 技 术 改 造 中图分类号 : T H1 3 7 文献标识码 : A 文章编号 : 1 0 0 8 — 0 8 1 3 ( 2 0 1 3 ) 0 9 — 0 0 5 3 — 0 2
成废 钢
准。 经 常 出现 自动 下落 的现 象 。 导 致 信号 丢 失 裙板 不 动 作. 经 常造 成 冷 床 跑钢 和 堆 钢 . 事 故 率 和 中废 率 都 比较 高 造 成上 述 问题 具体 表 现在 以下 几个 方 面 : ( 1 ) 冷 床液 压 系统设 计 不合 理 。冷 床液 压站 布 置在
O 引 言
轧钢 厂 优 特 钢线 是 方 大特 钢 科 技股 份 有 限公 司新
Q460C钢的成分设计及控轧控冷工艺优化的开题报告

Q460C钢的成分设计及控轧控冷工艺优化的开题报告一、选题背景Q460C钢是一种高强度低合金结构钢,具有良好的焊接性、韧性和可锻性,在国内外建筑、大型机械、海洋、轨道交通等领域得到广泛应用。
但是,由于其碳当量较高,易产生相变,厚板加工性能有限,且在低温环境下易产生冷脆性,因此需要对其成分设计和控轧控冷工艺进行优化,以提高其综合性能。
二、研究目的和意义本研究旨在对Q460C钢的成分设计和控轧控冷工艺进行优化,以提高其综合性能,具体包括以下目标:1.通过成分设计,降低Q460C钢的碳当量,提高其韧性和可加工性;2.通过控轧控冷工艺的优化,控制相变行为,改善其显微组织和力学性能;3.通过对优化后的Q460C钢进行性能评价,验证成分设计和控轧控冷工艺的有效性,为其在相关领域的应用提供技术支持和保障。
三、研究内容和方法1.成分设计通过对Q460C钢的成分进行设计和优化,选择合适的合金元素和含量,降低其碳当量,提高其韧性和可加工性。
其中,主要在以下方面开展研究:(1)合金元素的选择:通过文献调研、计算机模拟等手段,选定适合Q460C钢的合金元素,如Mn、Si、Ni、Cr等,并确定其合理含量范围;(2)成分设计的优化:利用正交试验等方法,构建成分设计模型,确定最佳的成分组成,以达到预期的物理、化学、力学性能,并制备试样;2.控轧控冷工艺优化通过控制轧制和冷却过程中的温度、形变速率、停留时间等工艺参数,控制相变行为,促进显微组织的均匀化和晶粒细化,提高Q460C钢的力学性能。
其中,主要在以下方面开展研究:(1)工艺参数的选择:通过试验和计算机模拟等手段,确定合适的轧制和冷却工艺参数,例如轧制温度、终轧温度、冷却速率、停留时间等;(2)控轧控冷工艺优化:利用正交试验等方法,构建控轧控冷工艺优化模型,确定最佳的工艺参数组合,并制备试样;3.性能评价对优化后的Q460C钢进行宏观、微观、力学性能测试和分析,检验成分设计和控轧控冷工艺的优化效果,并与未经优化处理的Q460C钢进行对比。
板带材轧机中液压系统的优化设计与控制

板带材轧机中液压系统的优化设计与控制随着工业技术的不断发展,板带材轧机已广泛应用于金属加工行业。
而液压系统作为板带材轧机的重要组成部分,对轧机的性能和效率起着至关重要的作用。
优化设计与控制液压系统,可以提高轧机的工作效率、降低能源消耗和提升生产质量。
本文将讨论板带材轧机液压系统的优化设计与控制方案。
一、液压系统的优化设计1. 液压系统的布局优化在板带材轧机中,液压系统的布局是一个关键因素。
合理的布局可以提高系统的工作效率和可靠性。
优化布局应遵循以下原则:(1)尽量减少液压元件的安装距离,降低系统的压力损失;(2)合理安排液压元件的摆放位置,方便维护和检修;(3)避免液压元件之间的相互干扰,减少系统的故障风险。
2. 液压系统的参数优化液压系统的参数优化是提高系统性能的关键。
在板带材轧机中液压系统的参数优化主要包括以下几个方面:(1)液压元件的选型优化:根据轧机的工作条件,选择合适的液压元件,优化设计工作压力、流量和功率等参数;(2)控制阀的优化:采用先进的控制阀技术,提高控制精度和灵敏度;(3)油液的选择:使用优质液压油,提高系统的稳定性和寿命。
3. 液压系统的节能优化能源消耗是板带材轧机的重要问题,液压系统的节能优化可以降低工作过程中的能源消耗。
实现液压系统的节能优化可以从以下几个方面入手:(1)减小液压泵的功率损失:采用高效液压泵,减小泵的功率损失;(2)优化液压系统的工作参数:合理调节液压系统的工作压力和流量,降低能源消耗;(3)采取能量回收技术:利用液压系统中的压力能量,通过能量回收装置将其转化为电能储存起来,以供其他部分使用。
二、液压系统的控制方案1. 液压系统的控制策略液压系统的控制策略是指通过控制液压元件的工作状态和参数,实现对板带材轧机的控制。
常用的液压系统控制策略包括:(1)开关控制:通过液压元件的开关控制,实现对液压系统的工作状态的控制;(2)比例控制:通过液压元件的流量和压力比例控制,实现对液压系统的精确控制;(3)自适应控制:根据板带材轧机的工作状态和参数,自适应调节液压系统的工作状态和参数,以达到最佳工作效果。
小规格钢材上冷床问题及优化方案
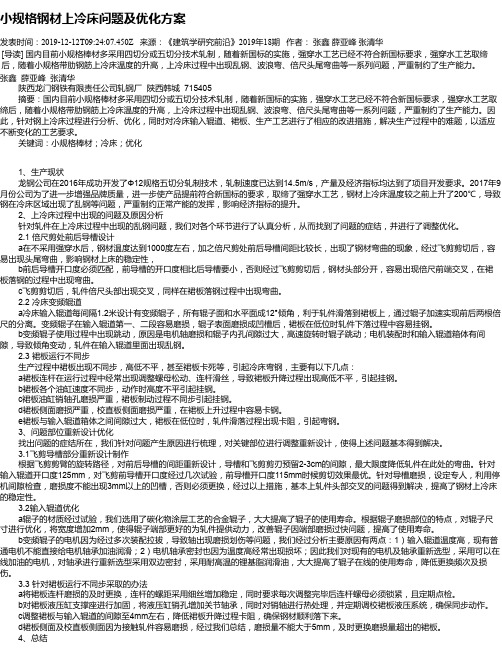
小规格钢材上冷床问题及优化方案发表时间:2019-12-12T09:24:07.450Z 来源:《建筑学研究前沿》2019年18期作者:张鑫薛亚峰张清华[导读] 国内目前小规格棒材多采用四切分或五切分技术轧制,随着新国标的实施,强穿水工艺已经不符合新国标要求,强穿水工艺取缔后,随着小规格带肋钢筋上冷床温度的升高,上冷床过程中出现乱钢、波浪弯、倍尺头尾弯曲等一系列问题,严重制约了生产能力。
张鑫薛亚峰张清华陕西龙门钢铁有限责任公司轧钢厂陕西韩城 715405 摘要:国内目前小规格棒材多采用四切分或五切分技术轧制,随着新国标的实施,强穿水工艺已经不符合新国标要求,强穿水工艺取缔后,随着小规格带肋钢筋上冷床温度的升高,上冷床过程中出现乱钢、波浪弯、倍尺头尾弯曲等一系列问题,严重制约了生产能力。
因此,针对钢上冷床过程进行分析、优化,同时对冷床输入辊道、裙板、生产工艺进行了相应的改进措施,解决生产过程中的难题,以适应不断变化的工艺要求。
关键词:小规格棒材;冷床;优化1、生产现状龙钢公司在2016年成功开发了Φ12规格五切分轧制技术,轧制速度已达到14.5m/s,产量及经济指标均达到了项目开发要求。
2017年9月份公司为了进一步增强品牌质量,进一步使产品提前符合新国标的要求,取缔了强穿水工艺,钢材上冷床温度较之前上升了200℃,导致钢在冷床区域出现了乱钢等问题,严重制约正常产能的发挥,影响经济指标的提升。
2、上冷床过程中出现的问题及原因分析针对轧件在上冷床过程中出现的乱钢问题,我们对各个环节进行了认真分析,从而找到了问题的症结,并进行了调整优化。
2.1 倍尺剪处前后导槽设计 a在不采用强穿水后,钢材温度达到1000度左右,加之倍尺剪处前后导槽间距比较长,出现了钢材弯曲的现象,经过飞剪剪切后,容易出现头尾弯曲,影响钢材上床的稳定性, b前后导槽开口度必须匹配,前导槽的开口度相比后导槽要小,否则经过飞剪剪切后,钢材头部分开,容易出现倍尺前端交叉,在裙板落钢的过程中出现弯曲。
轧钢步进式冷床的优化改进
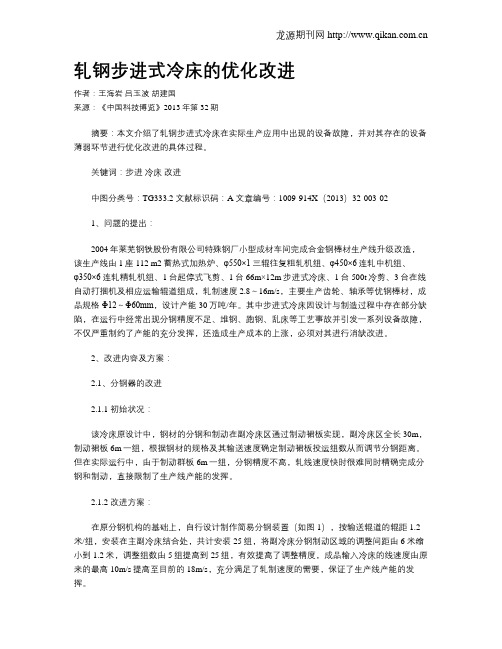
轧钢步进式冷床的优化改进作者:王海岩吕玉波胡建国来源:《中国科技博览》2013年第32期摘要:本文介绍了轧钢步进式冷床在实际生产应用中出现的设备故障,并对其存在的设备薄弱环节进行优化改进的具体过程。
关键词:步进冷床改进中图分类号:TG333.2 文献标识码:A 文章编号:1009-914X(2013)32-003-021、问题的提出:2004年莱芜钢铁股份有限公司特殊钢厂小型成材车间完成合金钢棒材生产线升级改造,该生产线由1座112 m2蓄热式加热炉、φ550×1三辊往复粗轧机组、φ450×6连轧中机组、φ350×6连轧精轧机组、1台起停式飞剪、1台66m×12m步进式冷床、1台500t冷剪、3台在线自动打捆机及相应运输辊道组成,轧制速度2.8~16m/s,主要生产齿轮、轴承等优钢棒材,成品规格Φ12~Φ60mm,设计产能30万吨/年。
其中步进式冷床因设计与制造过程中存在部分缺陷,在运行中经常出现分钢精度不足、堆钢、跑钢、乱床等工艺事故并引发一系列设备故障,不仅严重制约了产能的充分发挥,还造成生产成本的上涨,必须对其进行消缺改进。
2、改进内容及方案:2.1、分钢器的改进2.1.1 初始状况:该冷床原设计中,钢材的分钢和制动在副冷床区通过制动裙板实现,副冷床区全长30m,制动裙板6m一组,根据钢材的规格及其输送速度确定制动裙板投运组数从而调节分钢距离。
但在实际运行中,由于制动群板6m一组,分钢精度不高,轧线速度快时很难同时精确完成分钢和制动,直接限制了生产线产能的发挥。
2.1.2 改进方案:在原分钢机构的基础上,自行设计制作简易分钢装置(如图1),按输送辊道的辊距1.2米/组,安装在主副冷床结合处,共计安装25组,将副冷床分钢制动区域的调整间距由6米缩小到1.2米,调整组数由5组提高到25组,有效提高了调整精度,成品输入冷床的线速度由原来的最高10m/s提高至目前的18m/s,充分满足了轧制速度的需要,保证了生产线产能的发挥。
锻压厂轧钢车间冷床电控系统优化
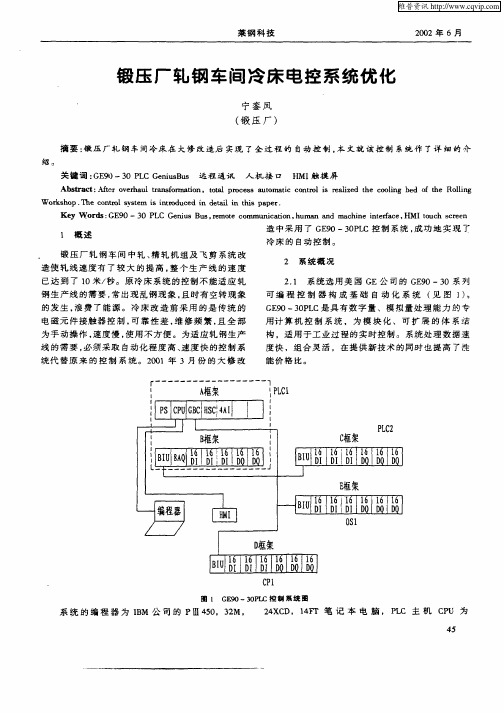
Ke o d : 9 y W r s GE 0—3 L e isB s rmoe c mmu iain, u n a d m c ie itr c , 0 P C G nu u ,e t o nct o h ma n a hn nef e HMItu h sre a o c ce n
45
维普资讯
宁 銮 凤 : 压 厂 轧 钢 车 间冷 床 电控 系统 优 化 锻
I 9 C6 3CPU3 61
第 3期 ( 第 9 总 9期 ) 刊 专
裙 板 高 位 信 号 一 制 动 器 得 电一 松 开 一 延 时 一 离 合 得 电一 合 上一 动 梁 启 动 一 减 速 位接 近 开 关 发 信 号
维普资讯
莱 钢 科 技
20 o 2年 6月
锻 压 厂 轧 钢 车 间 冷 床 电 控 系 统 优 化
宁 銮 凤 ( 压厂 ) 锻
摘 要 : 压 厂 轧 钢 车 间冷 床 在 大修 改 造 后 实现 了 全 过 程 的 自动 控 制 , 文 就 该 控 制 系统 作 了详 细 的 介 锻 本
2 1 系统 选 用 美 国 G . E公 司 的 G g E 0—3 0系 列
可 编 程 控 制 器 构 成 基 础 自动 化 系 统 ( 图 1 。 见 )
Gg E 0—3 P C是 具 有 数 字 量 、模 拟 量 处理 能 力 的 专 0L
用计 算 机 控 制 系 统 ,为 模 块 化 、 可 扩 展 的 体 系 结
棒材生产线冷床自动控制系统的设计与实现
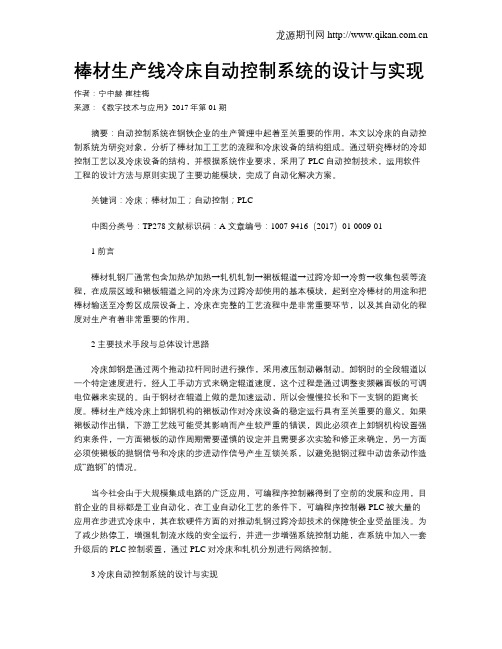
棒材生产线冷床自动控制系统的设计与实现作者:宁中赫崔桂梅来源:《数字技术与应用》2017年第01期摘要:自动控制系统在钢铁企业的生产管理中起着至关重要的作用,本文以冷床的自动控制系统为研究对象,分析了棒材加工工艺的流程和冷床设备的结构组成。
通过研究棒材的冷却控制工艺以及冷床设备的结构,并根据系统作业要求,采用了PLC自动控制技术,运用软件工程的设计方法与原则实现了主要功能模块,完成了自动化解决方案。
关键词:冷床;棒材加工;自动控制;PLC中图分类号:TP278 文献标识码:A 文章编号:1007-9416(2017)01-0009-011 前言棒材轧钢厂通常包含加热炉加热→轧机轧制→裙板辊道→过跨冷却→冷剪→收集包装等流程,在成层区域和裙板辊道之间的冷床为过跨冷却使用的基本模块,起到空冷棒材的用途和把棒材输送至冷剪区成层设备上,冷床在完整的工艺流程中是非常重要环节,以及其自动化的程度对生产有着非常重要的作用。
2 主要技术手段与总体设计思路冷床卸钢是通过两个拖动拉杆同时进行操作,采用液压制动器制动。
卸钢时的全段辊道以一个特定速度进行,经人工手动方式来确定辊道速度,这个过程是通过调整变频器面板的可调电位器来实现的。
由于钢材在辊道上做的是加速运动,所以会慢慢拉长和下一支钢的距离长度。
棒材生产线冷床上卸钢机构的裙板动作对冷床设备的稳定运行具有至关重要的意义。
如果裙板动作出错,下游工艺线可能受其影响而产生较严重的错误,因此必须在上卸钢机构设置强约束条件,一方面裙板的动作周期需要谨慎的设定并且需要多次实验和修正来确定,另一方面必须使裙板的抛钢信号和冷床的步进动作信号产生互锁关系,以避免抛钢过程中动齿条动作造成“跑钢”的情况。
当今社会由于大规模集成电路的广泛应用,可编程序控制器得到了空前的发展和应用,目前企业的目标都是工业自动化,在工业自动化工艺的条件下,可编程序控制器PLC被大量的应用在步进式冷床中,其在软硬件方面的对推动轧钢过跨冷却技术的保障使企业受益匪浅。
对轧制弹簧扁钢的冷床控制优化设计
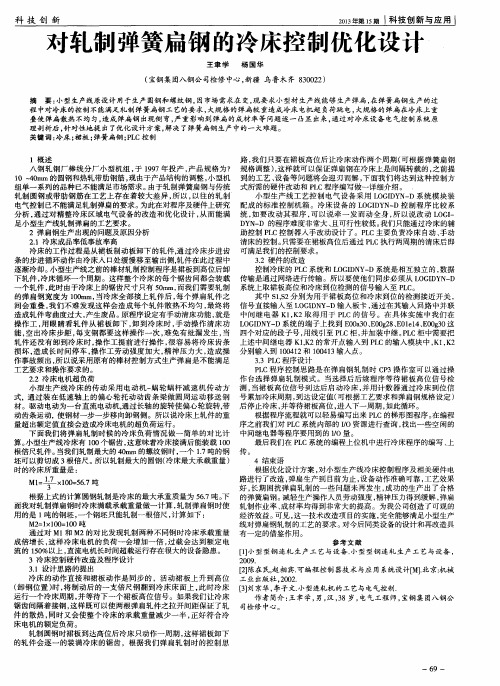
2 0 1 3 年第1 5 期l 科技 创新 与应 用
对轧制 弹簧扁钢 的冷 床控制优化设计
王 聿 学 杨 国 华
( 宝钢 集团八钢公 司检修 中心 , 新疆 乌鲁木 齐 8 3 0 0 2 2 )
摘 要: 小型生产线原设计 用于生产圆钢和螺纹钢 , 因市场需求在 变, 现要求小型材 生产线能够生产弹扁 , 在弹簧扁铜生产的过 程 中对 冷床 的控 制 不 能满 足 轧制 弹 簧 扁 钢 工 艺的 要 求 , 大 规格 的 弹扁 较 重 造成 冷床 电机 超 负荷 跳 电 , 大规格 的 弹扁 在冷 床 上 重 叠使 弹扁散热不均 匀, 造成弹扁钢 出现侧 弯, 严重影响到 弹扁的成材率等 问题逐 一凸显 出来 , 通过对冷床设备 电气控制 系统原 理剖 析 后 , 针 对性 地提 出 了优 化设 计 方 案 , 解 决 了弹 簧扁 铜 生 产 中 的一 大难 题 。 关键 词 : 冷床 ; 裙板; 弹簧 扁 钢 ; P L C控 制
1概 述
八钢 轧钢厂棒线分厂小型机组 , 于1 9 9 7年 投 产 , 产品规格为? 1 0 4 0 m m 的 圆钢 和 热 轧带 肋 钢筋 , 现 由于 产 品结 构 的调 整 , 小 型机 组 单一 系列 的 品种 已不 能满 足 市场 需 求 。由于轧 制 弹 簧扁 钢 电气控制 已不能满足轧制 弹扁的要求。 为此在对程序及硬件上研究 分析 , 通过对精整冷床区域电气设备的改造 和优化设计 , 从而能满 足 小 型生 产 线 轧制 弹 扁 的工 艺 要求 。 2 弹 扁钢 生 产 出 现 的 问题 及 原 因分 析 2 . 1冷床成品率低事故率高 冷床 的工作过程是从裙板制动板卸下 的轧件, 通过冷床步进齿
3 . 2硬 件 的改 造
弹簧扁钢半连轧生产工艺实践及改进

2008年第2期新疆钢铁总106期弹簧扁钢半连轧生产工艺实践及改进张海军(新疆八一钢铁股份有限公司)摘要;八钢弹簧扁钢由热带机组转移至,J650机组半连轧生产线生产,介绍了针对试生产出现的问题,进行的工艺改造以及轧制工艺改进优化,重点介绍半连轧生产工艺改进及取得的效果。
关键词;弹簧扇钢;半连轧;延伸系数;工艺优化中图分类号:T G335文献标识码:B文章编号;1672--4224(2008)02--0040--03l前言2000年八钢650机组进行了连轧机组改造,新上3立8平共1l架轧机,50m步进式冷床,300t冷剪机.剪后收集装置等设备,初步具备了生产弹扁的工艺条件。
弹扁生产工艺布置为半连续式。
工艺流程:加热一一彩650m m轧机轧制(7道)一一彩530m m轧机轧制(3道)——精轧机组轧制(8道)。
粗轧机组为彩650m m、彰530m m三辊半闭口式胶木瓦轧机各一列;精轧机组平轧机为二辊式短应力轧机七架,包括髟480m m平辊轧机4架、彩430m m 平辊轧机2架、∥430m m立辊轧机1架;够500m m框架式立辊轧机2架。
2问题的提出连轧改造后组织了几次弹扁试生产,生产中出现了一些问题:(1)1号、2号加热炉为推钢式加热炉,上下两面加热,加热不均匀;炉筋管引起的黑印。
这些因素造成了轧制中轧件尺寸波动,另外当轧机或设备出现故障,高温段的钢不能向后倒出,轧制后出现脱碳。
(2)连轧机组中平轧机不能换槽,轧机底座通过螺栓固定在轨座上,槽孔打坏或槽孔磨损后,只能换辊。
降低了作业率。
增加了辊耗。
(3)连轧进出口导卫存在问题,进出口导卫固定在轧机底座横梁上。
横梁通过四个联接螺栓固定在轧机底座上,横梁高低可调,导卫在横梁上左右可调,调节高低及对中性困难,导卫稳定性差。
(4)轧制工艺还有待于进一步优化。
针对这些问题,陆续进行了一些工艺改造:2002年5月,2号加热炉大修改造,由推钢式加热炉改造为双蓄热步进式加热炉,在后续使用中,发生过烧嘴壳体损坏,阀体内漏,燃烧系统供热不足等问题,影响了正常生产,2004年6月改为单蓄热式;通过连轧线轧机液压横移改造,改造后,导卫底座固定在轨座联接横梁上,标高固定,导卫底座中心线与轧制线重合,导卫与导卫底座键连接,通过压板螺栓固定。
工程最优化设计MATLAB大作业-棒材连轧车间倍尺飞剪至冷床距离的优化
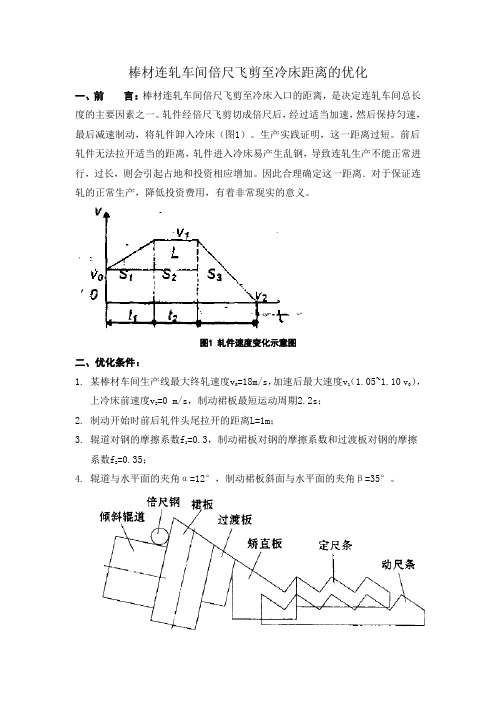
棒材连轧车间倍尺飞剪至冷床距离的优化一、前言:棒材连轧车间倍尺飞剪至冷床入口的距离,是决定连轧车间总长度的主要因素之一。
轧件经倍尺飞剪切成倍尺后,经过适当加速,然后保持匀速,最后减速制动,将轧件卸入冷床(图1)。
生产实践证明,这一距离过短。
前后轧件无法拉开适当的距离,轧件进入冷床易产生乱钢,导致连轧生产不能正常进行,过长,则会引起占地和投资相应增加。
因此合理确定这一距离.对于保证连轧的正常生产,降低投资费用,有着非常现实的意义。
图1 轧件速度变化示意图二、优化条件:1.某棒材车间生产线最大终轧速度v0=18m/s,加速后最大速度v1(1.05~1.10 v),上冷床前速度v2=0 m/s,制动裙板最短运动周期2.2s;2.制动开始时前后轧件头尾拉开的距离L=1m;3.辊道对钢的摩擦系数f1=0.3,制动裙板对钢的摩擦系数和过渡板对钢的摩擦系数f2=0.35;4.辊道与水平面的夹角α=12°,制动裙板斜面与水平面的夹角β=35°。
图2 上冷床装置结构5.轧件上冷床的过程(1)轧件向冷床区传送。
由于辊道呈倾斜布置,轧件将在辊道和裙板侧面形成的夹角处向前传送,此时裙板必须处于高位(如图2所示)。
同时,为了满足相邻两根轧件都能顺利上冷床,轧件尾部到达分钢点(裙板下降到低位的时刻所对应的位置)时与下一根轧件头部必须拉开一定距离。
因此,倾斜辊道向冷床区传送轧件的过程是一个加速过程。
一般将倾斜辊道分成三段控制,并使每段辊道线速度超前于成品机架出口速度。
(2)倍尺钢尾部到达分钢点时裙板由高位下降到低位,倍尺钢沿裙板顶面从倾斜辊道滚落到裙板顶面与过渡板侧面形成的夹角处,倍尺钢开始摩擦制动。
(3)为了接收来自倍尺剪的下一根倍尺钢,裙板到达低位后立刻返回到中位并延长一定时间,倍尺钢完成摩擦制动。
(4)为了将完成制动的倍尺钢输送到矫直板的第一个槽,裙板上升到高位并延长一定时间,以等待下一根倍尺钢尾部到达分钢点。
60Si2Mn弹簧钢的控轧控冷工艺

#工艺技术#60Si2Mn 弹簧钢的控轧控冷工艺张 鹏 冯光纯(重庆工业高等专科学校,重庆400050) (重庆大学冶金系)摘 要 弹簧钢60Si2Mn 经奥氏体再结晶区1000e 控轧,轧后以6~10e /s 的冷速进行控制冷却,可获得细小的珠光体+少量铁素体组织,同时减少了脱碳,显著提高了弹簧钢的冲击韧性。
关键词 弹簧钢 控轧控冷 韧性 脱碳Controlled Rolling and Cooling Process of Spring Steel 60Si2MnZhang Peng(Chongqing Polytechnic College,Chongqing 400050)Feng Guangchun(Chongqing University)Abstract By con trolled rolling in austenite recrystallization zone at 1000e and cooled with 6~10e /sec after rolled,the fine pearlite with little ferri te in spring steel 60Si2Mn could be obtained,to decrease the decarbonization and obviously in -crease the impact energy of spring steel.Material Index Spring Steel,Con trolled Rollin g and Cooling ,Toughness,Decarbonization60Si2Mn 弹簧钢主要用于汽车板簧即汽车悬挂系统中的减振部件,其重量约占整车重量的10%。
随着我国汽车工业的发展,弹簧钢的需求量不断增加,对其性能的要求也越来越高。
如何提高汽车板簧的疲劳强度和使用寿命,发挥金属材料的潜力,减少材料用量,以减轻车身自重,受到广泛的关注[1]。
冷床自动控制设计\调试及应用
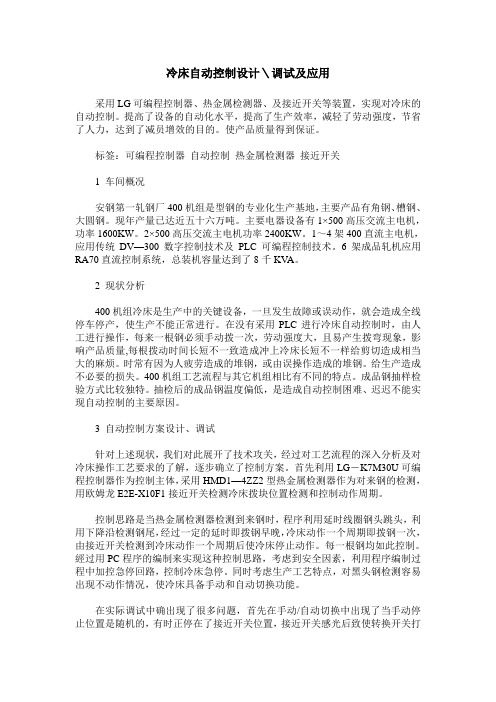
冷床自动控制设计\调试及应用采用LG可编程控制器、热金属检测器、及接近开关等装置,实现对冷床的自动控制。
提高了设备的自动化水平,提高了生产效率,减轻了劳动强度,节省了人力,达到了减员增效的目的。
使产品质量得到保证。
标签:可编程控制器自动控制热金属检测器接近开关1 车间概况安钢第一轧钢厂400机组是型钢的专业化生产基地,主要产品有角钢、槽钢、大圆钢。
现年产量已达近五十六万吨。
主要电器设备有1×500高压交流主电机,功率1600KW。
2×500高压交流主电机功率2400KW。
1~4架400直流主电机,应用传统DV—300数字控制技术及PLC可编程控制技术。
6架成品轧机应用RA70直流控制系统,总装机容量达到了8千KV A。
2 现状分析400机组冷床是生产中的关键设备,一旦发生故障或误动作,就会造成全线停车停产,使生产不能正常进行。
在没有采用PLC进行冷床自动控制时,由人工进行操作,每来一根钢必须手动拨一次,劳动强度大,且易产生拨弯现象,影响产品质量,每根拨动时间长短不一致造成冲上冷床长短不一样给剪切造成相当大的麻烦。
时常有因为人疲劳造成的堆钢,或由误操作造成的堆钢。
给生产造成不必要的损失。
400机组工艺流程与其它机组相比有不同的特点。
成品钢抽样检验方式比较独特。
抽检后的成品钢温度偏低,是造成自动控制困难、迟迟不能实现自动控制的主要原因。
3 自动控制方案设计、调试针对上述现状,我们对此展开了技术攻关,经过对工艺流程的深入分析及对冷床操作工艺要求的了解,逐步确立了控制方案。
首先利用LG-K7M30U可编程控制器作为控制主体,采用HMD1—4ZZ2型热金属检测器作为对来钢的检测,用欧姆龙E2E-X10F1接近开关检测冷床拨块位置检测和控制动作周期。
控制思路是当热金属检测器检测到来钢时,程序利用延时线圈钢头跳头,利用下降沿检测钢尾,经过一定的延时即拨钢早晚,冷床动作一个周期即拨钢一次,由接近开关检测到冷床动作一个周期后使冷床停止动作。
优化冷床上钢系统,提高上钢稳定性

优化冷床上钢系统,提高上钢稳定性尹莹莹;李希宝【摘要】本文主要介绍了山东石横特钢公司棒材车间在生产小规格多切分螺纹时(φ10×5、φ12×4),冷床上钢系统不稳定,乱钢现象严重,针对此现象成功地对冷床上钢系统进行了优化改造,可有效降低设备故障时间,提高成材率,保证产品质量,创造较高的经济效益。
%This paper mainly introduces the unstable bedsteel system and steel chaos phenomenon in the production of small size multi cutting thread (Φ10 “5 ,12”,4 ) in workshops of Shandong Shiheng Special Steel Company. In accordance with this phenomenon, this paper described how to optimize the bedsteel system , which can effectively reduce the fault time , improve yield rate , ensure product quality and create higher economic benefits.【期刊名称】《现代制造技术与装备》【年(卷),期】2014(000)002【总页数】2页(P55-56)【关键词】小规格多切分;冷床上钢系统;分钢装置【作者】尹莹莹;李希宝【作者单位】山东石横特钢集团有限公司,泰安 271612;山东石横特钢集团有限公司,泰安 271612【正文语种】中文山东石横特钢集团有限公司第一棒材车间(以下简称一棒)是国产棒材全连轧生产线,于2005年4月份建成投产年设计能力为60万t,现已达到100万t的生产能力。
- 1、下载文档前请自行甄别文档内容的完整性,平台不提供额外的编辑、内容补充、找答案等附加服务。
- 2、"仅部分预览"的文档,不可在线预览部分如存在完整性等问题,可反馈申请退款(可完整预览的文档不适用该条件!)。
- 3、如文档侵犯您的权益,请联系客服反馈,我们会尽快为您处理(人工客服工作时间:9:00-18:30)。
对轧制弹簧扁钢的冷床控制优化设计
小型生产线原设计用于生产圆钢和螺纹钢,因市场需求在变,现要求小型材生产线能够生产弹扁,在弹簧扁钢生产的过程中对冷床的控制不能满足轧制弹簧扁钢工艺的要求,大规格的弹扁较重造成冷床电机超负荷跳电,大规格的弹扁在冷床上重叠使弹扁散热不均匀,造成弹扁钢出现侧弯,严重影响到弹扁的成材率等问题逐一凸显出来,通过对冷床设备电气控制系统原理剖析后,针对性地提出了优化设计方案,解决了弹簧扁钢生产中的一大难题。
标签:冷床;裙板;弹簧扁钢;PLC控制
1 概述
八钢轧钢厂棒线分厂小型机组,于1997年投产,产品规格为?10 ~40mm 的圆钢和热轧带肋钢筋,现由于产品结构的调整,小型机组单一系列的品种已不能满足市场需求。
由于轧制弹簧扁钢与传统轧制圆钢或带肋钢筋在工艺上存在着较大差异,所以,以往的轧制电气控制已不能满足轧制弹扁的要求。
为此在对程序及硬件上研究分析,通过对精整冷床区域电气设备的改造和优化设计,从而能满足小型生产线轧制弹扁的工艺要求。
2 弹扁钢生产出现的问题及原因分析
2.1 冷床成品率低事故率高
冷床的工作过程是从裙板制动板卸下的轧件,通过冷床步进齿条的步进循环动作由冷床入口处缓慢移至输出侧,轧件在此过程中逐渐冷却。
小型生产线之前的棒材轧制控制程序是裙板到高位后卸下轧件,冷床循环一个周期。
这样整个冷床的每个锯齿间都会装载一个轧件,此时由于冷床上的锯齿尺寸只有50mm,而我们需要轧制的弹扁钢宽度为100mm,当冷床全部接上轧件后,每个弹扁轧件之间会重叠,我们不难发现这样会造成每个轧件散热不均匀,最终将造成轧件弯曲度过大,产生废品。
原程序设定有手动清床功能,就是操作工,用眼睛看轧件从裙板卸下,卸到冷床时,手动操作清床功能,空出冷床步距,每支钢都要这样操作一次,难免有纰漏发生,当轧件还没有卸到冷床时,操作工提前进行操作,很容易将冷床齿条损坏,造成长时间停车,操作工劳动强度加大,精神压力大,造成操作事故频出,所以说采用原有的棒材控制方式生产弹扁是不能满足工艺要求和操作要求的。
2.2 冷床电机超负荷
小型生产线冷床的传动采用电动机-蜗轮蜗杆减速机传动方式,通过装在低速轴上的偏心轮托动动齿条梁做圆周运动移送钢材。
驱动电动为一台直流电动机,通过长轴的旋转使偏心轮旋转,带动齿条运动,使钢材一步一步移向卸钢侧。
所以说冷床上轧件的重量超出额定值直接会造成冷床电机的超负荷运行。
下面我们将弹扁轧制时候的冷床负荷情况做一简单的对比计算。
小型生产线冷床有100个锯齿,这意味着冷床接满后能装载100根倍尺轧件。
当我们轧制最大的40mm的螺纹钢时,一个1.7吨的钢坯可以剪切成3根倍尺。
所以轧制最大的圆钢(冷床最大承载重量)时的冷床所重量是:
M1=×100=56.7吨
根据上式的计算圆钢轧制是冷床的最大承重质量为56.7吨。
下面我对轧制弹扁钢时冷床满载承载重量做一计算,轧制弹扁钢时使用的是1吨的钢坯,一个钢坯只能轧制一根倍尺,计算如下:
M2=1×100=100吨
通过对M1和M2的对比发现轧制两种不同钢时冷床承载重量成倍增长,这样冷床电机的负荷一会增加一倍,过载会达到额定电流的150%以上,直流电机长时间超载运行存在很大的设备隐患。
3 冷床控制硬件改造及程序设计
3.1 设计思路的提出
冷床的动作直接和裙板动作是同步的,活动裙板上升到高位(卸钢位置)时,将制动后的一支倍尺钢翻到冷床床面上,此时冷床运行一个冷床周期,并等待下一个裙板高位信号。
如果我们让冷床锯齿间隔着接钢,这样既可以使两根弹扁轧件之拉开间距保证了轧件的散热,同时又会使整个冷床的承载重量减少一半,正好符合冷床电机的额定负荷。
轧制圆钢时裙板到达高位后冷床只动作一周期,这样裙板卸下的轧件会逐一的装满冷床的锯齿,根据我们弹扁轧制时的控制思路,我们只要在裙板高位后让冷床动作两个周期(可根据弹簧扁钢规格调整),这样就可以保证弹扁钢在冷床上是间隔转载的,之前提到的工艺、设备等问题将会迎刃而解,下面我们将达到这种控制方式所需的硬件改动和PLC程序编写做一详细介绍。
小型生产线工艺控制电气设备采用LOGIDYN-D系统模块装配成的标准控制机箱。
冷床设备的LOGIDYN-D控制程序比较系统,如要改动其程序,可以说牵一发而动全身,所以说改动LOGIDYN-D 的程序难度非常大、且可行性较低。
我们只能通过冷床的辅助控制PLC控制器入手改動设计了。
PLC主要负责冷床自动、手动清床的控制。
只需要在裙板高位后通过PLC执行两周期的清床后即可满足我们的控制要求。
3.2 硬件的改造
控制冷床的PLC系统和LOGIDNY-D系统是相互独立的,数据传输是通过
网络进行传输。
所以要使他们同步必须从LOGIDYN-D系统上取裙板高位和冷床到位检测的信号输入至PLC。
其中S1,S2分别为用于裙板高位和冷床到位的检测接近开关,信号直接输入至LOGIDNY-D输入板卡,通过在其输入回路中并联中间继电器K1,K2取得用于PLC的信号。
在具体实施中我们在LOGIDNY-D系统的端子上找到E00a30、E00g28、E01e14、E00g30这四个对应的段子号,用线引至PLC柜,并加装中继。
PLC柜中需要把上述中间继电器K1,K2的常开点输入到PLC的输入模块中,K1,K2分别输入到100412和100413输入点。
3.3 PLC程序设计
PLC程序控制思路是在弹扁钢轧制时CP3操作室可以通过操作台选择弹扁轧制模式。
当选择后后续程序等待裙板高位信号检测,当裙板高位信号到达后启动冷床,并用计数器通过冷床到位信号累加冷床周期,到达设定值(可根据工艺要求和弹扁钢规格设定)后停止冷床,并等待裙板高位,进入下一周期,如此循环。
根据程序流程就可以轻易编写出来PLC的梯形图程序。
在编程序之前我们对PLC系统内部的I/O资源进行查询,找出一些空闲的中间继电器等程序要用到的I/O量。
最后我们在PLC系统的编程上位机中进行冷床程序的编写、上传。
4 结束语
根据优化设计方案,对小型生产线冷床控制程序及相关硬件电路进行了改造,弹扁生产到目前为止,设备动作准确可靠,工艺效果好,长期困扰弹扁轧制的一些问题未再发生,成功的生产出了合格的弹簧扁钢。
减轻生产操作人员劳动强度,精神压力得到缓解,弹扁轧制作业率、成材率均得到非常大的提高。
为我公司创造了可观的经济效益。
可见,这一技术改造项目的实施,完全能够满足小型生产线对弹扁钢轧制的工艺的要求。
对今后同类设备的设计和再改造具有一定的借鉴作用。
参考文献
[1]小型型钢连轧生产工艺与设备.小型型钢连轧生产工艺与设备,2009.
[2]陈在民,赵相宾.可编程控制器技术与应用系统设计[M].北京:机械工业出版社,2002.
[3]刘京华,李子文.小型连轧机的工艺与电气控制.
作者简介:王聿学,男,汉,38岁,电气工程师,宝钢集团八钢公司检修
中心。