工艺卡片模板2019年
工艺卡片模板年

工艺管理文件
工艺卡片
XXX公司
受控号:
工艺卡片
文件编号:001
发布日期:2019年2月
实施日期:2019年2月
会签页
目录
1.原辅材料控制指标 (05)
2.公用工程控制指标 (05)
3.主要工艺参数控制指标 (06)
4.主要产品、中间产品质量控制指标 (07)
5.安全环保指标 (08)
6.分析频率一览表 (08)
7.修改控制页 (13)
备注:工艺指标分为公司级控制指标、厂级控制指标和车间级控制指标。
1.原辅材料控制指标
2.公用工程控制指标
3.主要工艺操作控制指标
备注:☆公司级控制指标;●厂级控制指标;▲车间级控制指标。
5. 安全环保考核指标
6. 分析频率一览表。
(精编)生产工艺涂装工艺卡片模板
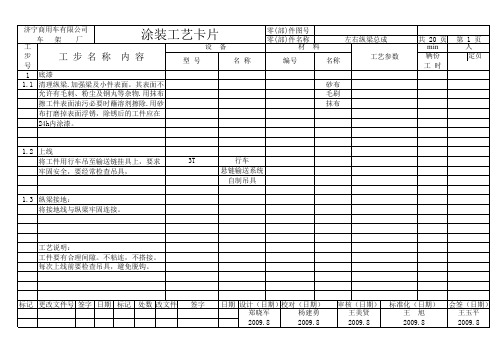
零(部)件名称工步定员号11.11.21.3标记更改文件号签字日期标记处数签字日期王 旭王玉平2009.82009.82009.82009.8自制吊具悬链输送系统布打磨掉表面浮锈,除锈后的工件应在牢固安全,要经常检查吊具,将接地线与纵梁牢固连接。
擦工件表面油污必要时蘸溶剂擦除.用砂工艺参数min 工 步 名 称 内 容 车 架 厂共 20 页第 1 页左右纵梁总成辆份工 时设 备材 料允许有毛刺、粉尘及钢丸等杂物.用抹布底漆人型 号名 称编号名称清理纵梁.加强梁及小件表面。
其表面不砂布毛刷抹布将工件用行车吊至输送链挂具上,要求3T行车工艺说明:工件要有合理间隙。
不粘连,不搭接。
每次上线前要检查吊具,避免脱钩。
24h内涂漆。
上线纵梁接地:设计(日期)校对(日期)审核(日期)更改文件号郑晓军杨建勇王美贤会签(日期)标准化(日期)2009.8零(部)件名称标记更改文件号签字日期标记处数签字日期王 旭王玉平2009.82009.82009.82009.82009.8王美贤 车 架 厂左右纵梁总成共 20 页第 2 页审核(日期)标准化(日期)会签(日期)郑晓军杨建勇更改文件号设计(日期)校对(日期)上线工件接地自制吊具零(部)件图号零(部)件名称工步定员号1.41.4.1标记更改文件号签字日期标记处数签字日期2009.82009.82009.82009.82009.8郑晓军杨建勇王美贤王 旭标准化(日期)会签(日期)更改文件号设计(日期)校对(日期)审核(日期)王玉平网将调好的油漆过滤一遍。
下限温度低时取上限)。
用75μm的过滤烧碱测〕,施工温度10℃-35℃,温度高时取粘度计DEPAINT[A。
B]漆雾凝聚剂释至施工粘度。
(20~26 s用涂-4粘度计MZS01-02-DT 专用稀释剂湿碰湿间隔:3分钟合,搅拌均匀,并用专用配套稀释剂稀涂-4L30专用固化剂施工温度:10-35℃按B:A=3:1(重量比)的比例将底漆混调漆间MZS01-02-D 专用底漆施工粘度:20-26S用搅拌棒将A、B两组分别充分搅拌均后,调漆电动搅拌器min 人辆份工 时喷漆左右纵梁总成工 步 名 称 内 容设 备材 料工艺参数型 号名 称编号名称济宁商用车有限公司涂装工艺卡片车 架 厂共 20 页第 3 页零(部)件名称标记更改文件号签字日期标记处数签字日期杨建勇王美贤王 旭王玉平2009.82009.82009.82009.8更改文件号设计(日期)郑晓军2009.8会签(日期)校对(日期)审核(日期)标准化(日期)车 架 厂共 20 页第 4 页左右纵梁总成调漆添加固化剂添加稀料零(部)件名称工步定员号1.4.2标记更改文件号签字日期标记处数签字日期2009.82009.82009.82009.82009.8郑晓军杨建勇王美贤王 旭标准化(日期)会签(日期)更改文件号设计(日期)校对(日期)审核(日期)王玉平报废。
机械加工工艺卡片模板

12
车削
以底平面和前端面为基准,夹紧两侧面,车©30孔,
加工设备C616A车床
131
车削
车2x45倒角,
加工设备C616A车床
14
去
毛刺
去毛刺
15
总见入
库
总见入库
设计 (日期)
校对 (日期)
审核 (日期)
标准化
(日期)
会签
(日期)
标记
处数
更改文
件号
签字
日期
标记
处数
更改文
件号
签字
日期
机械加工工序卡片(一)
机械加工工序卡片
产品型号
零件图号
共页
产品名称
零件名称
第页
车间
工序号
工序名称
材料牌号
毛坯种类
毛坯外形尺寸
每件毛坯可制件数
每台件数
设备名称
设备型号
设备编号
同时加工件数
夫具编号
夹具名称
切削液
工位器具编号
工位器具名称
工序工时/min
准终
单件
工
步 号
工步内容
工艺装备
主轴转速
/(r/min)
机械加工工艺过程卡片
机械加工工艺过程卡片
产品型号
零件图号
共
1页
产品名称
零件名称
第
1页
材料牌 号
毛坯外形尺寸每件毛坯可制件数
每台件数
备注
工序号
工序名 称
工序内容
设备
工艺装备
01
检验
外协毛坯检验
02
铣削
夹轴承孔两侧毛坯,铣轴承底面,照顾尺寸30mm和表面粗糙度,
加工工艺过程卡片模板
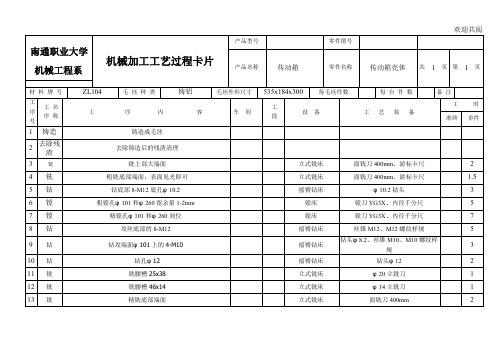
14
去毛刺
15
检验
设计(日期)
校对(日期)
审核(日期)
标准化(日期)
会签(日期)
标记
处数
更改文件号
签字
日期
标记
处数
更改文件号
签字
日期
立式铣床
面铣刀400mm、游标卡尺
2
4
铣
粗铣底部端面,表面见光即可
立式铣床
面铣刀400mm、游标卡尺
1.5
5
钻
钻底部8-M12底孔φ10.2
摇臂钻床
φ10.2钻头
3
6
镗
粗镗孔φ101和φ260留余量1-2mm
镗床
镗刀YG3X、内径千分尺
5
7
镗
精镗孔φ101和φ260到位
镗床
Байду номын сангаас镗刀YG3X、内径千分尺
7
南通职业大学机械工程系
机械加工工艺过程卡片
产品型号
零件图号
产品名称
传动箱
零件名称
传动箱壳体
共
1
页
第
1
页
材料牌号
ZL104
毛坯种类
铸铝
毛坯外形尺寸
535x184x300
每毛坯件数
每台件数
备注
工
序
号
工名
序称
工序内容
车间
工
段
设备
工艺装备
工时
准终
单件
1
铸造
铸造成毛坯
2
去除残渣
去除铸造后的残渣清理
3
铣
铣上部大端面
8
钻
攻丝底部的8-M12
工艺卡
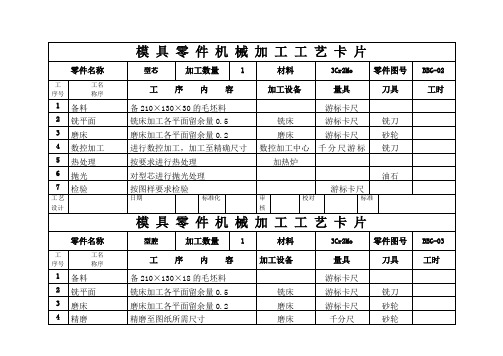
1 3 4 9 4 2 10
备料 车外圆平面 车外圆平面 数控加工 精车外圆平面 热处理 检验
备 20× 15 两件 25× 10 的板料 车床加工各外圆平面留余量 0.5; 车床车各外圆平面留余量 0.2 数控加工成型面至所需尺寸 车床车至各尺寸 按要求进行热处理加工 按图纸要求检验 车床 数控车床 数控加工中心 数控车床 加热炉
备料 铣平面 磨平面 划线 钻孔 攻丝 精磨 热处理 检验
备 305×75×40 板料 铣床加工各平面留余量 0.5 磨床加工各平面留余量 0.5 按图纸尺寸定位各孔 先钻小孔后在扩大至所需尺寸 按照图纸攻丝 精磨至所需尺寸 按要求进行热处理加工 按图样要求检验 铣床 磨床 工作台 立式钻床 丝锥 磨床 加热炉
铣刀 砂轮 麻花钻 砂轮
工艺
日期
标准化
审核
校对
标准
模 具 零 件 机 械 加 工 工 艺 卡 片
零件名称
工 序号 工名 称序
推板
加工数量 序 内 容
1
材料 加工设备
45 钢
零件图号 刀具
BBG-11
工
量具 游标卡尺
工时定额
1 2 3 4 5 6 7 8
备料 铣平面 磨平面 划线 钻孔 热处理 精磨 检验
游标卡尺 游标卡尺 高度尺 游标卡尺 千分尺 游标卡尺
铣刀 砂轮 麻花钻 砂轮
工艺 设计
日期
标准化
审 核
校对
标准
模 具 零 件 机 械 加 工 工 艺 卡 片
零件名称
工 序号 工名 称序
动模座板
加工数量 序 内 容
1
材料 加工设备
45 钢
零件图号 刀具
BBG-12
工艺过程工序卡(范本)

毛坯外形尺寸
每毛坯课制件数
每台件数
设备名称
设备型号
设备编号
同时加工件 数
夹具编号
夹具名称
切削液
工位器具编号
工位器具名称
工序时间
准终
单件
描图
工步号
工步名称
工艺装备
主轴转速(r/min)
切削速度(m/min)
进给 量
(mm)
被吃刀量(mm)
工时(min)
描校
机动
单件
底图号
装订号
设汁
(日期)
审 核 (日期)
工时(min)
机动
单件
底图号
装订号
设计
(日期)
审核
(日期)
标准化
(日期)
会签
(日期)
标记
处数
更改文件号
签字
日期
标记
处数
更改文件号
签字
日期
底图号
切削速度(m/min)
进给 量
(mm)
被吃刀量(mm)
工时(min)
描校
机动
单件
底图号
装订号
设IP
(日期)
审 核 (日期)
标准化 (日期)
会签
(日期)
标记
处数
更改文件号
签?
日期
标记
处数
更改文件号
签字
日期
*****学院
机械加工工艺过程卡片
产品型号
零件图号
共页
产品名称
零件名称
第2页
车间
工序号
工序名称
材料牌号
工序时间
准终
单件
描图
工艺卡片模板100例
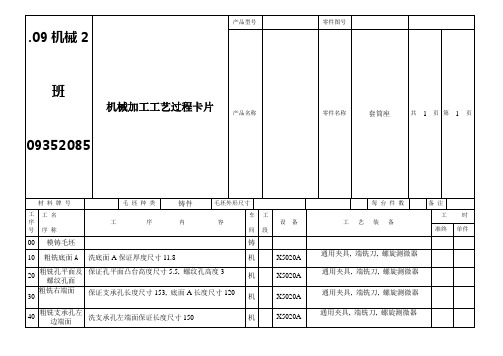
单件
设计(日期)
校对(日期)
审核(日期)
标准化(日期)
会签(日期)
标记
处数
更改文件号
签字
日期
标记
处数
更改文件号
签字
日期
机械加工工艺过程卡片
产品型号
零件图号
产品名称
零件名称
套筒座
共
1
页
第
1
页
材料牌号
毛坯种类
铸件
毛坯外形尺寸
每台件数
备注
工
序
号
工名
序称
工序内容
车
间
工
段
设备
工艺装备
工时
准终
单件
00
模铸毛坯
铸
10
粗铣底面A
洗底面A保证厚度尺寸11.8
机
X5020A
通用夹具,端铣刀,螺旋测微器
20
粗铣孔平面及螺纹孔面
保证孔平面凸台高度尺寸5.5,螺纹孔高度3
通用夹具,螺纹刀,扩孔钻,千分尺
130
检验入库
设计(日期)
校对(日期)
审核(日期)
标准化(日期)
会签(日期)
刘涛
标记
处数
更改文件号
签字
日期
标记
处数
更改文件号
签字
日期
机械加工工艺过程卡片
产品型号
零件图号
产品名称
零件名称
共
页
第
页
材料牌号
毛坯种类
毛坯外形尺寸
每毛坯件数
每台件数
备注
工
序
号
工名
序称
工序内容
车
生产工艺卡(3篇)
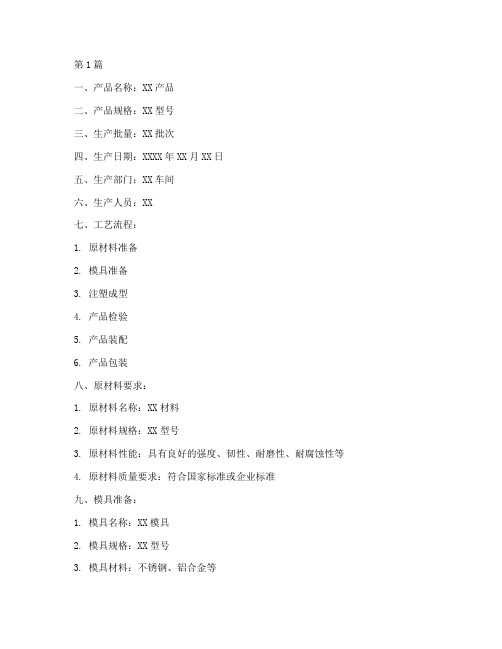
第1篇一、产品名称:XX产品二、产品规格:XX型号三、生产批量:XX批次四、生产日期:XXXX年XX月XX日五、生产部门:XX车间六、生产人员:XX七、工艺流程:1. 原材料准备2. 模具准备3. 注塑成型4. 产品检验5. 产品装配6. 产品包装八、原材料要求:1. 原材料名称:XX材料2. 原材料规格:XX型号3. 原材料性能:具有良好的强度、韧性、耐磨性、耐腐蚀性等4. 原材料质量要求:符合国家标准或企业标准九、模具准备:1. 模具名称:XX模具2. 模具规格:XX型号3. 模具材料:不锈钢、铝合金等4. 模具质量要求:无砂眼、裂纹、变形等缺陷十、注塑成型:1. 注塑机型号:XX型号2. 注塑温度:XX℃3. 注塑压力:XXMPa4. 注塑时间:XX秒5. 注塑速度:XXmm/s6. 注塑注意事项:a. 模具预热至设定温度b. 严格按照工艺参数进行注塑c. 注意注塑过程中的压力、温度、时间等参数的调整d. 注塑完成后,待产品冷却至室温十一、产品检验:1. 检验项目:外观、尺寸、性能等2. 检验标准:符合国家标准或企业标准3. 检验方法:a. 外观检验:目测、触摸、量具测量等b. 尺寸检验:卡尺、千分尺等c. 性能检验:拉伸试验机、冲击试验机等十二、产品装配:1. 装配件名称:XX部件2. 装配件规格:XX型号3. 装配顺序:先装配内部零件,再装配外部零件4. 装配方法:手工装配、机械装配等5. 装配注意事项:a. 严格按照装配图纸进行装配b. 注意装配过程中的对位、紧固等操作c. 避免装配过程中产生划痕、变形等缺陷十三、产品包装:1. 包装材料:纸箱、气泡袋、胶带等2. 包装规格:XX型号3. 包装方法:将产品放入纸箱,用气泡袋填充,封箱,贴上标签4. 包装注意事项:a. 包装过程中注意轻拿轻放,避免产品损坏b. 标签信息准确,包括产品名称、规格、生产日期、批次等c. 包装牢固,确保产品在运输过程中不受损坏十四、生产过程中应注意的问题:1. 原材料质量:确保原材料符合要求,避免因原材料质量导致产品不合格2. 模具质量:定期检查模具,发现异常及时处理3. 注塑成型:严格按照工艺参数进行注塑,避免产品出现变形、气泡等缺陷4. 产品检验:严格进行产品检验,确保产品合格率5. 产品装配:注意装配过程中的对位、紧固等操作,避免产品出现装配缺陷6. 产品包装:确保包装牢固,防止产品在运输过程中损坏十五、生产过程中异常处理:1. 原材料异常:发现原材料质量问题时,及时与供应商沟通,确保原材料质量2. 模具异常:发现模具异常时,立即停止生产,修复或更换模具3. 注塑成型异常:发现产品出现变形、气泡等缺陷时,调整注塑参数,重新注塑4. 产品检验异常:发现产品不合格时,及时通知相关部门,查找原因,进行处理5. 产品装配异常:发现装配过程中出现缺陷时,及时修正,确保产品合格6. 产品包装异常:发现包装过程中出现问题时,及时调整包装方法,确保产品安全运输本生产工艺卡适用于XX产品生产过程中的各个环节,各部门应严格按照本工艺卡执行,确保产品质量。
机械加工工艺卡片模板

1
设备名称
设备型号
设备编号
同时加工件数
立式钻床
C620-1
夹具编号
夹具名称
切削液
3
钻模
工位器具编号
工位器具名称
工序工时/min
准终
单件
工步号
工步内容
工艺装备
主轴转速
/(r/min)
切削速度
/(m/min)
进给量/(mm/r)
背吃刀量/mm
走刀
次数
公步工时/min
机动
辅助
1
钻 孔为 ,
立钻
200
14.4
更改号
签字
日期
标记
处数
更改号
签字
日期
机械加工工序卡片
产品型号
零件图号
共8页
产品名称
零件名称
偏心轮
第4页
车间
工序号
工序名称
材料牌号
20
车
20cr
毛坯种类
毛坯外形尺寸
每件毛坯可制件数
每台件数
热轧圆钢
Φ
1
1
设备名称
设备型号
设备编号
同时加工件数
卧式车床
C620-1
夹具编号
夹具名称
切削液
1
三爪卡盘
工位器具编号
0.36
2
扩 孔为 ,偏心距为9
立钻
320
15.7
0.2
3
倒两面空口角
设计(日期)
校对(日期)
审核(日期)
标准化(日期)
会签(日期)
标记
处数
更改文件号
签字
日期
标记
处数
工艺卡片模板

机械加工工艺过程卡片班级: 1404032姓名:机械加工工艺过程卡片产品名称轴套部件名称轴套共( 7)页第( 1)页资料牌GCR15 毛坯种铸毛坯外型尺每毛坯可制件1每台件 1备注号类件寸数数工序号工序工序内容车间工段设备工艺装备工步工时名称备料Θ50×45 的棒料1车粗车端面及外圆金工CA6140三爪卡盘, YG6硬质合金车刀,表面粗糙度仪2钻钻θ6, θ10,, θ14,, θ 18金工Z3025麻花钻,钻床专用夹具,内通孔径千分尺3镗粗,精巧镗θ20 通孔θ 30金工CA6140C620-1 车床专用夹具内圆柱孔,θ 30 至θ36 的圆径百分尺,表面粗糙度仪表锥孔4车粗车精车θ49 至标准尺寸金工CA614090 度外圆车刀,游标卡尺,θ48三爪卡盘5车换端面保护夹θ48 面粗,金工CA614090 度外圆车刀,游标卡尺,精车θ50 至标准尺寸θ40三爪卡盘6车端面至标准尺寸保证长金工CA614090 度外圆车刀,游标卡尺,度 30mm,40mm三爪卡盘设计日期审查日期标准化日会签日期期标志处改正文件签日期指导数号字01— 01—产品型号部件图号01(厂机械加工工序卡片共(7)名)产品名称轴套部件名称轴套第(2)页页车间工序号工序名称资料牌号机加工GCR15车削车间每毛坯可制件毛坯种类毛坯外形尺寸每台件数数锻造Θ50×451设备名称设备型号设备编号同时加工件数CA61401夹具编号ZY—01夹具名称三爪卡盘切削液工序工时标准单件主轴转切削速度进给量切削深进给工序工时工步号工步内容工艺装备速 r/min m/min mm/r度 mm次数灵活辅助三爪卡盘,YG6硬质1粗车端面及外圆合金车刀,表面粗9045122s糙度仪01— 01—产品型号部件图号02(厂机械加工工序卡片共(7)名)产品名称轴套部件名称轴套第(3)页页车间工序号工序名称资料牌号机加工GCR15钻孔车间每毛坯可制件毛坯种类毛坯外形尺寸每台件数数锻造Θ50×451设备名称设备型号设备编号同时加工件数Z30251夹具编号夹具名称切削液ZY—02钻床专用夹具工序工时标准单件260s主轴转切削速度进给量切削深进给工序工时工步号工步内容工艺装备速 r/min m/min mm/r度mm次数灵活辅助钻Z3025 摇臂钻床,钻2θ6, θ10 , , θ1410024530200s60s床专用夹具,,θ18 通孔产品型号部件图号01— 01—(厂03名)机械加工工序卡片共( 7)页第(4)页产品名称轴套部件名称轴套车间工序号工序名称资料牌号机加工GCR15车间车削每毛坯可制件毛坯种类毛坯外形尺寸每台件数数锻造Θ50×451设备名称设备型号设备编号同时加工件数CA61401夹具编号夹具名称切削液ZY—04三爪卡盘工序工时标准单件主轴转切削速度进给量切削深进给工序工时工步号工步内容工艺装备速 r/min m/min mm/r度 mm次数灵活辅助粗,精巧镗θ20C620-1 车床专用通孔θ30圆柱孔,夹具内径百分尺,3θ30 至θ36 的圆330492521s 表面粗糙度仪表锥孔01— 01—产品型号部件图号04(厂机械加工工序卡片共(7)名)产品名称轴套部件名称轴套第(5)页页车间工序号工序名称资料牌号机加工GCR15车削车间每毛坯可制件毛坯种类毛坯外形尺寸每台件数数锻造Θ50×451设备名称设备型号设备编号同时加工件数CA61401夹具编号夹具名称切削液ZY—01三爪卡盘工序工时标准单件110s主轴转切削速度进给量切削深进给工序工时工步号工步内容工艺装备速 r/min m/min mm/r度 mm次数灵活辅助粗车精车θ49 至90 度外圆车刀,游4标准尺寸θ4812035350s60s 标卡尺,三爪卡盘产品型号部件图号01— 01—(厂05名)机械加工工序卡片共(7)页第(6)页产品名称轴套部件名称轴套车间工序号工序名称资料牌号机加工GCR15车间车削每毛坯可制件毛坯种类毛坯外形尺寸每台件数数锻造Θ50×451设备名称设备型号设备编号同时加工件数CA61401夹具编号夹具名称切削液ZY—01三爪卡盘工序工时标准单件130s主轴转切削速度进给量切削深进给工序工时工步号工步内容工艺装备速r/min m/min mm/r度mm次数灵活辅助5换端面保护夹θ48 粗精车θ50至标准尺寸θ4090 度外圆车刀,游标卡尺,三爪卡盘120462370s60s产品型号部件图号01— 01—(厂06名)机械加工工序卡片共(7)页第(7)页产品名称轴套部件名称轴套车间工序号工序名称资料牌号机加工GCR15车间车削每毛坯可制件毛坯种类毛坯外形尺寸每台件数数锻造Θ50×451设备名称设备型号设备编号同时加工件数CA61401夹具编号夹具名称切削液ZY—01三爪卡盘工序工时标准单件130s主轴转切削速度进给量切削深进给工序工时工步号工步内容工艺装备速r/min m/min mm/r度mm次数灵活辅助6车端面至标准尺寸保证长度90 度外圆车刀,游标卡尺,三爪卡盘12046270s60s 17mm,40mm。
工艺技术卡片

工艺技术卡片工艺技术卡片一、产品介绍名称:XXXXXXXXX型号:XXXXXXXXX用途:XXXXXXXXX二、工艺概述1. 工艺流程:XXXXXXXXX2. 原材料:XXXXXXXXXa. 主要原材料:XXXXXXXXXb. 辅助原材料:XXXXXXXXX3. 设备清单:XXXXXXXXXa. 主要设备:XXXXXXXXXb. 辅助设备:XXXXXXXXX三、工艺步骤与操作说明1. 工艺步骤:a. 步骤 1:XXXXXXXXXb. 步骤 2:XXXXXXXXXc. 步骤 3:XXXXXXXXXd. 步骤 4:XXXXXXXXXe. 步骤 5:XXXXXXXXXf. 步骤 6:XXXXXXXXX2. 操作说明:a. 操作人员应具备相关技能和知识,熟悉操作流程和危险警示。
b. 操作步骤应按照工艺流程进行,不得随意省略或更改。
c. 操作人员需穿戴相关防护用品,如手套、护目镜、口罩等。
d. 操作结束后,及时清理、维护设备,确保设备正常运行。
四、质量控制要点1. 质量标准:XXXXXXXXXa. 外观要求:XXXXXXXXXb. 物理性能要求:XXXXXXXXXc. 化学性能要求:XXXXXXXXX2. 检测方法:a. 外观检测:XXXXXXXXXb. 物理性能检测:XXXXXXXXXc. 化学性能检测:XXXXXXXXX3. 质量控制措施:a. 现场检验:在生产过程中定期进行抽样检验,确保产品符合质量标准。
b. 机器自检:设备应配备自动检测装置,能够实时监测关键质量指标。
c. 生产工艺监控:对关键工艺参数进行监控和调整,确保产品一致性和稳定性。
五、安全注意事项1. 操作人员需穿戴相关防护用品,避免接触有害物质。
2. 熟悉紧急疏散路线和应急预案,确保在事故发生时能够正确应对。
3. 严格按照操作规程进行操作,不得搞乱或私自调整设备参数。
4. 定期对设备进行维修和保养,确保设备安全可靠。
六、常见问题与解决方法1. 问题 1:XXXXXXXXX 解决方法:XXXXXXXXX2. 问题 2:XXXXXXXXX 解决方法:XXXXXXXXX3. 问题 3:XXXXXXXXX 解决方法:XXXXXXXXX七、工艺技术指标1. 生产效率:XXXXXXXXX2. 产品质量合格率:XXXXXXXXX3. 环境排放标准:XXXXXXXXX以上是对XXXXXXXXX工艺技术的概述和详细说明,该工艺技术卡片将帮助操作人员正确进行工艺流程,确保产品质量和安全生产。
机械加工工序卡片工艺过程卡片-模板
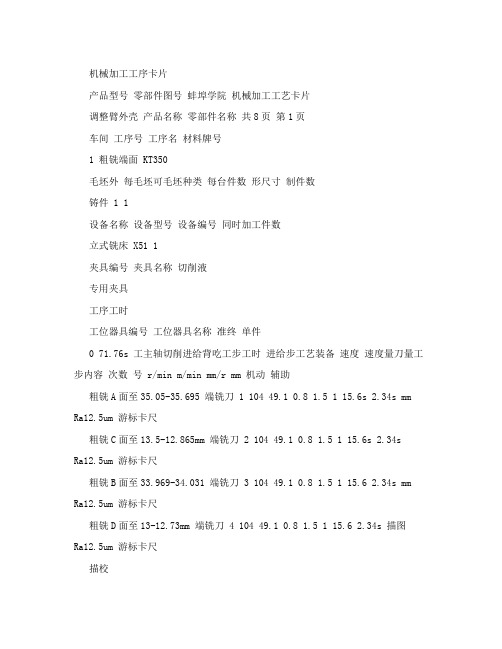
机械加工工序卡片产品型号零部件图号蚌埠学院机械加工工艺卡片调整臂外壳产品名称零部件名称共8页第1页车间工序号工序名材料牌号1 粗铣端面 KT350毛坯外每毛坯可毛坯种类每台件数形尺寸制件数铸件 1 1设备名称设备型号设备编号同时加工件数立式铣床 X51 1夹具编号夹具名称切削液专用夹具工序工时工位器具编号工位器具名称准终单件0 71.76s 工主轴切削进给背吃工步工时进给步工艺装备速度速度量刀量工步内容次数号 r/min m/min mm/r mm 机动辅助粗铣A面至35.05-35.695 端铣刀 1 104 49.1 0.8 1.5 1 15.6s 2.34s mm Ra12.5um 游标卡尺粗铣C面至13.5-12.865mm 端铣刀 2 104 49.1 0.8 1.5 1 15.6s 2.34sRa12.5um 游标卡尺粗铣B面至33.969-34.031 端铣刀 3 104 49.1 0.8 1.5 1 15.6 2.34s mm Ra12.5um 游标卡尺粗铣D面至13-12.73mm 端铣刀 4 104 49.1 0.8 1.5 1 15.6 2.34s 描图Ra12.5um 游标卡尺描校底图号装订号设计审核标准化会签(日期) (日期) (日期) (日期) 标处更改文签日标处更改文签日记数件号字期记数件号字期机械加工工艺过程卡片产品型号零件图号蚌埠学院机械加工工艺过程卡片产品名称零件名称调整臂外壳共1页第1页每毛坯可材料牌号 KT350 毛坯种类铸件毛坯外形尺寸 1 每台件数 1 备注制件数工时工名工序号工序内容车间工段设备工艺装备序称准终单件粗铣凸台粗铣两端面至X51立式铣高速钢套式面铣刀、游标卡35.881 两端面34.031~33.969mm Ra12.5um 床尺、专用夹具 s半精铣凸半精铣两端面至32~31.83mm X51立式铣高速钢套式面铣刀、游标卡58.932 台两端面 Ra6.3um 床尺、专用夹具 s镗孔T716立式金3 镗刀、游标卡尺、专用夹具62.1s Φ62mm 刚镗床X51立式铣 4 铣槽26m 38.5s 铣刀、游标卡尺 +床铣舌台两粗铣、半精铣至12~11.76mm XA613卧式高速钢套式面铣刀、游标卡94.815 面 Ra6.3um 铣床尺、专用夹具 s钻Φ12mm钻、粗铰孔至12.18~12.16mm X525立式复合麻花钻、铰刀内径千分16.566 孔 Ra6.3um 钻床尺 s钻孔31.877 台式小钻床麻花钻5XΦ4(3mm s钻Φ13mm钻孔至 X525立式33.128 孔并钻沉复合麻花钻 13.12~13mmRa25um 钻床 s 头孔钻孔钻孔至13.92~13.8mm X525立式23.01描图 9 复合麻花钻Φ13(8mm Ra25um 钻床 s钻M10螺X525立式77.5610 钻底孔复合麻花钻描校纹底孔钻 s钻Rc1/8锥X525立式77.9511 钻底孔复合麻花钻螺纹底孔钻床 s 底图号12 攻丝攻丝 13 去毛刺钳工台装订号14 清洗清洗机 15 终检设计审核标准化会签 (日期) (日期) (日期) (日期)标记处数更改文件号签字日期标记处数更改文件号签字日期。
工艺卡片模板
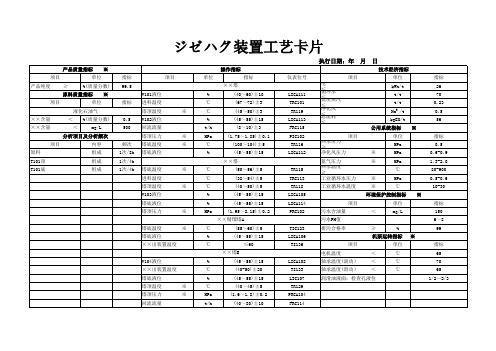
执行日期:年
产品质量指标 项目 产品纯度 项目 ××含量 ××含量 项目 原料 T101顶 T101底 < < ≥ 单位 %(质量分数) ※ 指标 0.5 500 频次 1次/8h 1次/4h 1次/4h 塔底温度 进料温度 塔顶温度 V103液位 塔底液位 塔顶压力 塔底温度 塔底液位 ××出装置温度 V104液位 ××出装置温度 塔底液位 塔顶温度 塔顶压力 回流流量 ※ ※ ※ ※ ※ ※ ℃ ℃ ℃ % % MPa ℃ % ℃ ××塔B % ℃ % ℃ MPa t/h (45~55)±15 (40-50)±20 (45~55)±15 (40~45)±5 (1.6~1.8)±0.2 (40~80)±10 LICA108 TI133 LIC107 TR129 PRCA104 FRC114 单位 液化石油气 %(质量分数) mg/L 内容 组成 组成 组成 原料质量指标 ※ 指标 99.5 V101液位 进料温度 塔顶温度 V102液位 回流流量 塔顶压力 塔底温度 塔底液位 ※ ※ ※ % ℃ ℃ % t/h MPa ℃ % 项目 单位 ××塔 (40~60)±10 (67~72)±3 (45~50)±3 (45~55)±15 (8~10)±3 (1.75~1.85)±0.1 (100~104)±5 (45~55)±15 ××塔 (50~56)±5 (38~54)±5 (40~50)±5 (45~55)±15 (45~55)±15 (1.95~2.15)±0.2 ××精馏塔A (55~60)±5 (45~55)±15 ≤60 TIC123 LICA106 TI136 电机温度 轴承温度(滚动) 轴承温度(滑动) 项目 < < < TR115 TRC113 TR118 LICA105 LICA114 PRC102 污水含油量 污水PH值 排污合格率 ≥ % ※ 指标 65 70 65 1/2—2/3 单位 ℃ ℃ ℃ 机泵运转指标 项目 < LICA111 TRC101 TR119 LICA113 FRC115 PIC102 TR116 LICA112 热水压力 净化风压力 氮气压力 热水温度 工业循环水压力 工业循环水温度 ※ ※ ※ ※ 项目 操作指标 指标 仪表位号 电 循环水 低压蒸汽 净化风 总能耗 项目
(工艺技术)工艺卡片样本

工艺规范产品名称工序名称设备名称编号共 16 页 AH/TLC70-01 框扇下料工装名称编号第 1 页工序简图技术标准1、下料长度L充差≤2000mm±1mm2、下料角度90°±0.5°3、切割后型材断面应平整光洁,外表面清洁无划伤。
操作要求1、切割前检查设备运转是否正常。
2、装夹注意夹紧力适当,牢固,定位正确,切割过程中防止型材变形。
3、型材搬取,存放过程中防止型材划伤,磕碰,表面质量。
4、首件产品严格检查合格后方可生产。
检验方法1、用钢卷尺检查下料长检测工具1.钢卷尺。
2.角度尺。
不合格品处置度。
2、用角度尺检查下料角度。
3、目测外观质量。
更改记录编制批准日期批准审核日期工艺规范产品名称工序名称设备名称编号共 16 页 AH/TLC70-01 铣排水孔工装名称编号第 2 页工序简图技术标准1、排水孔为Φ5×30槽孔,每根料数量2个。
2、纵向位置允差别±3mm,排列均匀。
3、排水孔表面光洁,无毛刺、铣刀不得损坏型材腹板4、排水孔设在外轨道左侧。
操作要求1、铣料前检查设备运转是否正常。
2、注意排水孔的位置均匀和数量。
3、铣孔时避免划伤型材表面质量。
4、首件产品严格检查,合格后方可生产。
检验方法1、用卡尺测量排水孔尺检测工具1、卡尺。
2、卷尺。
不合格品处置寸。
2、用卷尺测量排水孔位置。
更改记录编制批准日期批准审核日期工艺规范产品名称工序名称设备名称编号共 16 页 AH/TLC70-01 铣边框料工装名称编号第 3 页工序简图技术标准1、边框上方仿型铣深度距离为40mm。
2、边框下方仿型铣深度距离为50mm。
3、仿型铣后,光滑无毛刺,深度距离偏差L±1mm。
4、边框左右铣切距离为68mm,距离偏差L±0.5mm。
操作要求1、工作前检查仿型铣床运转是否正常。
2、检查铣刀型号是否正确。
3、工作时型材轻取轻放,避免划伤型材表面质量。
机加工工艺卡模板

1 2
50 150
3 4 5 6 7镗 Nhomakorabea坐标镗 划线工具 台钻 钢丝螺套 喷漆
卡尺 分度头
150 50 50 40 50
划线 划各孔及丝孔定位线。 钻 钻打各孔及丝孔基准孔成。
攻丝 攻各丝孔成,达技术要求。 漆 外表面喷漆。
编制
审核
年
月
日
批准
年
月
日
产 品 名 称
油枕 材 质 ZL104 更改 签字
机加工工艺、工时、 机加工工艺、工时、计件工资流程卡
数量 工序 代号 喷砂 喷砂 车 车左端面达图要求,车左端面5x3.5及右端面10x3.5槽各 成活,达图要求。 镗¢42各孔,镗¢86各面,镗4x2各槽成,达图要求。 机器 设备 喷砂设备 圆车 芯子 卡尺 工装 工具 单件 工时 1000 更改 工时 工序 工 序 内 容 量 具 工时值 更改 工值
工艺卡片模板
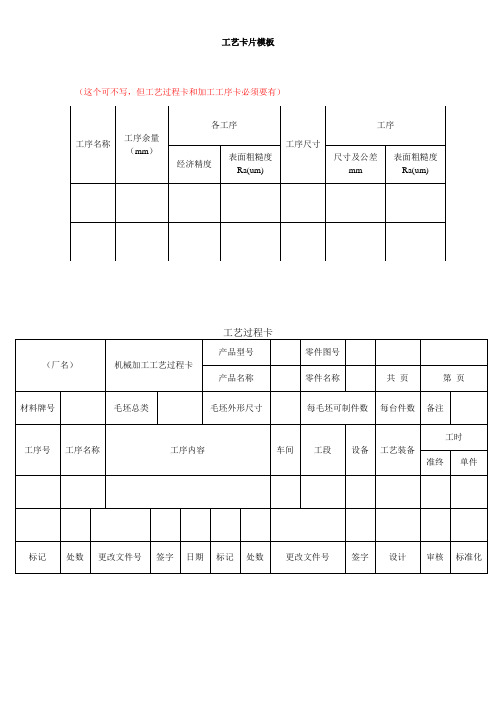
车间
工段
设备
工艺装备
工时
准终
单件
标记
处数
更改文件号
签字
日期
标记
处数
更改文件号
签字
设计
审核
标准化
加工工序卡模板(一)
(厂名)
机械加工工序卡片
产品型号
零件图号
产品名称
零件名称
共页
第页
车间
工序号
工序名称
材料牌号
毛坯种类
毛坯外形尺寸
每毛坯可制件数
每台件数
设备名称
设备型号
设备编号
同时加工件数
夹具编号
夹具名称
切削液
工位器具编号
工位器具名称
工序工时
标准
单件
工步号
工步内容
工艺装备
主轴转速r/min
切削速度m/min
进给量mm/r
切削深度mm
进给次数
工序工时
机动
辅助
设计(日期)
审核(日期)
标准化(日期)
会签(日期)
标记
处数
更改文件号
签字
日期
加工工序卡模板(二)
湖南工程学院
机械加工工序卡片
产品名称
零件名称
零件图号
材料
材料名称
毛坯种类
毛坯尺寸
零件重
每台件数
卡片编号
第 页
1
共 页
加工工序图
工序号
工序名
设 备
夹具
工量具
刃具
工步
工步内容及要求
主轴
转速(r/min)
吃刀深度(mm)
轴向进给量
(mm/r)
加工工艺过程卡片及工序卡

内容。
材 料 牌 号 H T 200 毛 坯 种 类 金属型铸件 毛坯外形尺寸 754×400×186每毛坯件数1每台 件数1 备注工序号 工序名称 工 序 内容 车间 工 段 设 备 工 艺装 备工 时 准终单件01 铸造 金属型铸造毛坯02 回火 热处理 03 探伤检验04 表面喷丸处理1粗以顶面为X 7面铣片车间毛坯种类金属型铸件设备名片车间毛毛片车间毛坯种类金属型铸件设备名称组片车间毛坯片车间毛坯种类金属型铸件设备名称双立轴片车间片车间毛坯种类金属型铸件设备名称片车间毛坯种片车间毛坯种类金属型铸件设备名称片车间学工步工步内学学学工步学工步学学学工步学工步学。
化工企业工艺卡片模板
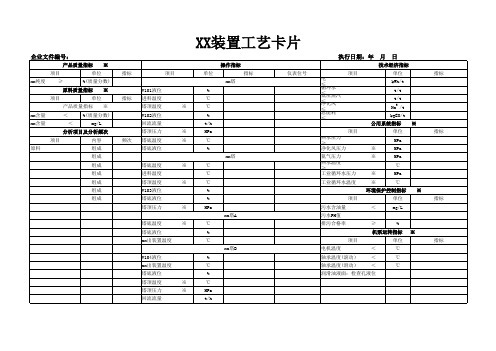
项目
单位
指标
污水含油量
<
mg/L
污水PH值
排污合格率
≥
%
机泵运转指标 ※
项目
单位
指标
电机温度
<
℃
轴承温度(滚动) <
℃
轴承温度(滑动) <
℃
润滑油液面:检查孔液位
仪表位号
执行日期:年 月 日
技术经济指标
电 ≤循环水 ≤低压蒸汽 ≤净化风 ≤总能耗 ≤
项目
单位 kWh/t t/t t/t Nm3 /t kgEO/t 公用系统指标 ※
指标
项目 热水压力
≥
净化风压力
※
单位 MPa MPa
指标
氮气压力
※
MPa
热水温度 ≥
℃
工业循环水压力
※
MPa
工业循环水温度
※
℃
环境保护控制指标 ※
※
塔底液位
塔底温度
※
进料温度
塔顶温度
※
V103液位
塔底液位
塔顶压力
※
塔底温度
※
塔底液位
xx出装置温度
V104液位
xx出装置温度
塔底液位
塔顶温度
※
塔顶压力
※
回流流量
单位
% ℃ ℃ % t/h MPa ℃ %
℃ ℃ ℃ % % MPa
℃ % ℃
% ℃ % ℃ MPa t/h
操作指标 指标
xx塔
xx塔
xx塔A xx塔B
企业文件编号:
产品质量指标 ※
项目
单位
xx纯度 ≥
%(质量分数)
原料质量指标 ※
工艺过程卡模板

零件名称
零件图号
****
001
材料名称及牌号
********
毛坯种类或材料规格
锻件Ø122*157
总工时
工序号
工序名称
工序简要内容
设备名称及型号
夹具
量具
工时
10
锻造
锻造(按毛坯图进行锻造)
20
正火
进行正火处理
30
检验
检查毛坯是否有微裂纹等缺陷
40
车
按零件图纸粗车各部分(留2mm余量)
热处理
无氧化淬火
车床
三爪卡盘
游标卡尺
50
数控车床综合加工
综合加工零件轮廓和孔(磨削留0.30mm余量)
****
****
游标卡尺、千分尺、内径专用表、深度千分尺
60
清洗
清洗、去毛刺
70
检验
检验产品尺寸是否合格
游标卡尺、千分尺、内径专用表、深度千分尺
80
加工中心综合加工
综合加工零件左端孔
立式加工中心VDF-850
三爪卡盘
90
清洗
清洗、去毛刺
100
检验
检验产品尺寸是否合格
110
车
加工左端孔口倒角
车床
三爪卡盘
120
研
研左右端中心孔
130
磨
磨削****外圆及端面
外圆磨床
游标卡尺、千分尺
140
制齿
加工齿轮
150
插齿
加工内孔花键
160
钳工
划钻****油孔
170
车
加工****0中心孔
180
热处理
机械加工工艺卡模板
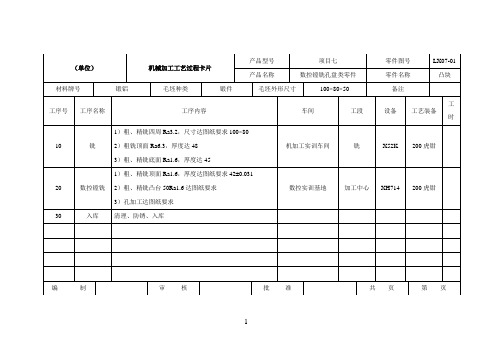
(单位)机械加工工艺过程卡片产品型号项目七零件图号LX07-01产品名称数控镗铣孔盘类零件零件名称凸块材料牌号锻铝毛坯种类锻件毛坯外形尺寸100×80×50 备注工序号工序名称工序内容车间工段设备工艺装备工时10 铣1)粗、精铣四周Ra3.2,尺寸达图纸要求100×802)粗铣顶面Ra6.3,厚度达483)粗、精铣底面Ra1.6,厚度达45机加工实训车间铣X52K 200虎钳20 数控镗铣1)粗、精铣顶面Ra1.6,厚度达图纸要求42±0.0312)粗、精铣凸台50Ra1.6达图纸要求3)孔加工达图纸要求数控实训基地加工中心XH714 200虎钳30 入库清理、防锈、入库编制审核批准共页第页1(单位)数控加工工序卡片产品名称或代号零件名称材料零件图号数控镗铣孔盘类零件凸块锻铝LX07-01 工序号程序编号夹具名称夹具编号使用设备车间20 711/712/713/71 200机用平口虎钳XH714 数控实训中心工步号工步内容刀具号刀具规格mm主轴转速r/min进给量mm/min背吃刀量mm量具备注1 粗铣顶面留余量0.2 T01 Φ80端铣刀500 200 2.8 游标卡尺125±0.022 精铣顶面控制高度尺寸42±0.031达Ra1.6 T01 600 150 0.23 粗铣凸台留侧余量0.5,底余量0.2 T02 Φ16立铣刀500 100 21.84 精铣凸台50Ra1.6成T02 600 80 0.25 钻6×M10-7H、4×Φ12H7、2×Φ30H7中心孔T03 Φ2中心钻1500 1206 钻2×Φ30H7、4×Φ12H7、6×M10-7H至Φ8.5T04 Φ8.5钻头700 807 扩4×Φ12H7至4×Φ11.8T05 Φ11.8钻头500 908 扩2×Φ30H7至2×Φ19T06 Φ19钻头300 80编制审核批准共 4 页第 1 页23(单 位) 数 控 加 工 工 序 卡 片产品名称或代号零件名称 材料 零件图号 数控镗铣孔盘类零件凸块锻铝LX07-01工序号 程序编号 夹具名称 夹具编号使用设备 车 间 20 711/712/713/71200机用平口虎钳XH714数控实训中心工步号 工 步 内 容刀具号 刀具规格 mm主轴转速 r/min 进给量 mm/min 背吃刀量 mm量具 备注9 倒4×Φ12H7、6×M10-7H 角C1 T06 300 60 10 扩2×Φ30H7至2×Φ26 T07 Φ26钻头 150 50 11 粗镗2×Φ30H7至2×Φ29.7 T08 Φ29.7镗刀 1100 12012粗镗2×Φ35H8至2×Φ34.6深9.9T09Φ34.6平底镗刀1000100深度尺200±0.02 13 精镗2×Φ35H8(390.00+)深10580.00+Ra1.6成 T10 Φ35H8平底镗刀 1100 80 内径表 千分尺 14 精镗2×Φ30H7(210.00+)Ra1.6成T11 Φ30H7镗刀 1300 100 内径表 千分尺 15 铰4×Φ12H7(180.00+)Ra1.6成T12 Φ12H7铰刀 200 100 内径表 千分尺 16攻6×M10-7H 螺纹成T13M10-H2丝锥 200300螺纹规编 制审 核批 准共 4 页第 2 页(单位)数控加工工序卡片产品名称或代号零件名称材料零件图号数控镗铣孔盘类零件凸块锻铝LX07-01 工序号程序编号夹具名称夹具编号使用设备车间20 711/712/713/71 200机用平口虎钳XH714 数控实训中心工步号工步内容刀具号刀具规格mm主轴转速r/min进给量mm/min背吃刀量mm量具备注17 全数检验18 清理、防锈、入库编制审核批准共 4 页第 3 页4(续)产品名称或代号零件名称材料零件图号(单位)数控加工工序卡片数控镗铣孔盘类零件凸块锻铝LX07-01 工序号程序编号夹具名称夹具编号使用设备车间20 711/712/713/71 200机用平口虎钳XH714型立式加工中心数控实训基地图7-2 工艺附图编制审核批准共 4 页第 4 页5(单位)数控加工刀具卡片产品名称或代号零件名称材料零件图号数控镗铣孔盘类零件凸块锻铝LX07-01 工序号程序编号夹具名称夹具编号使用设备车间20 711/712/713/71 200机用平口虎钳XH714 数控实训基地序号刀具号刀具名称刀具型号刀杆备注名称型号规格1 T01 Φ80波形刀片可转位面铣刀刀体:FM90-80LD15刀片:LDMT1504PDSR-27P套式立铣刀刀柄BT40-XM27-60 XM272 T02 Φ16高速钢直柄立铣刀Φ16强力铣夹头刀柄BT40-C22-95 C22 卡簧C22-163 T03 Φ2中心钻Φ2 弹簧卡头刀柄BT40-ER25-80 ER25 卡簧ER25-104 T04 Φ8.5高速钢直柄麻花钻头Φ8.5莫氏短圆锥钻夹头刀柄BT40-Z16-45 B16 自紧式钻夹头B165 T05 Φ11.8高速钢锥柄麻花钻头Φ11.8莫氏短圆锥钻夹头刀柄BT40-Z16-45 B16 自紧式钻夹头B166 T06 Φ19高速钢锥柄麻花钻头Φ19-M2 有扁尾莫氏圆锥孔刀柄BT40-M2-60 MT27 T07 Φ26高速钢锥柄麻花钻头Φ26-M3 有扁尾莫氏圆锥孔刀柄BT40-M3-75 MT3编制审核批准共 2 页第 1 页6(单位)数控加工刀具卡片产品名称或代号零件名称材料零件图号数控镗铣孔盘类零件凸块锻铝LX07-01 工序号程序编号夹具名称夹具编号使用设备车间20 711/712/713/71 200机用平口虎钳XH714 数控实训基地序号刀具号刀具名称刀具规格刀杆备注名称型号规格8 T08 Φ29.7粗镗刀Φ29.7 倾斜型粗镗刀BT40-TQC25-135 25-38 镗刀头TQC08-29-4 5-L9 T09 Φ34.8平底粗镗刀Φ34.6平底同上同上同上同上10 T10 Φ35平底精镗刀倾斜型微调精镗刀BT40-TQW29-100 Ф29-Ф41微调刀头TQW211 T11 Φ30精镗刀同上同上同上同上12 T12 Φ12H7直柄铰刀Φ12H7弹簧卡头刀柄BT40-ER25-80 ER25 卡簧ER25-1213 T13 机用丝锥M10-H2 攻丝夹头刀柄BT40-G3-90 M3-M12 攻丝夹套GT3-10编制审核批准共 2 页第 2 页7。
- 1、下载文档前请自行甄别文档内容的完整性,平台不提供额外的编辑、内容补充、找答案等附加服务。
- 2、"仅部分预览"的文档,不可在线预览部分如存在完整性等问题,可反馈申请退款(可完整预览的文档不适用该条件!)。
- 3、如文档侵犯您的权益,请联系客服反馈,我们会尽快为您处理(人工客服工作时间:9:00-18:30)。
工艺管理文件工艺卡片
XXX公司
受控号:工艺卡片
文件编号:001
发布日期:2019年2月
实施日期:2019年2月
会签页
目录
1.原辅材料控制指标 (05)
2.公用工程控制指标 (05)
3.主要工艺参数控制指标 (06)
4.主要产品、中间产品质量控制指标 (07)
5.安全环保指标 (08)
6.分析频率一览表 (08)
7.修改控制页 (13)
备注:工艺指标分为公司级控制指标、厂级控制指标和车间级控制指标。
1.原辅材料控制指标
备注:☆公司级控制指标;●厂级控制指标;▲车间级控制指标。
2.公用工程控制指标
备注:☆公司级控制指标;●厂级控制指标;▲车间级控制指标。
3.主要工艺操作控制指标
备注:☆公司级控制指标;●厂级控制指标;▲车间级控制指标。
备注:☆公司级控制指标;●厂级控制指标;▲车间级控制指标。
5. 安全环保考核指标
备注:☆公司级控制指标;●厂级控制指标;▲车间级控制指标。
6. 分析频率一览表
7. 修改控制页。