反应釜的设计计算
反应釜的设计计算

• 查《机械设计课程设计》可知:联轴器应选GY4,类型为凸缘联轴器。 • 搅拌轴材料的选择 • 常用优质碳素钢有35、45、50钢,其中以45钢应用最多。搅拌轴受到扭转和弯 曲的组合作用,其中以扭转为主。本次设计选用45钢作为搅拌轴的材料。
P T 9550 n
4 T 9550 5 198 .96 N m 960
m 3.02 10 pa s
4
d=400mm b=80mm n= 238.8r/min
Re 2.1106
结构计算计算结果
• • • • 经查《过程设备设计》功率曲线可知,功率准数Np=6 搅拌功率P=3.91kw 叶轮距槽底的安装高度Hi =400mm 挡板宽度Wb =120mm
过程装备与控制工程课程设计
Course design of process equipment and control engineering
任务书
• • • • • • 主要内容: 1 设计方案的确定及工艺流程的说明; 2 反应器的工艺计算; 3 基本尺寸计算及基本结构设计; 4 壳体、开孔补强与搅拌轴及耳式支座的强度校核; 5 绘制反应器的装配图。
筋板内侧间距
螺纹中心至底板外 缘距离
支座材料的屈服强 度
筋板厚度
底板厚度
8mm
10mm
底板宽度
支座筋板设计温度下的 拉伸弹性模量 筋板材料的许用应力
160mm
19700Mpa
底板长度
设计温度下支 座材料的许用 应力 地脚螺栓材料 Q235B,腐蚀 裕量3mm,规 格M24
310mm
113Mpa
50mm
180 32180 d 33.96mm 4 2 6 7.9 10 10
夹套(反应釜)加热能力设计计算说明

夹套(反应釜)加热能力设计计算说明已知条件:反应釜(反应罐)中的总物料的质量为4100kg,其中纯水质量3800kg,药材质量为300kg。
已知反应釜的夹套为两个部分:筒身以及底盖的夹套。
其中筒身夹套的覆盖面积为5.52m2,底盖夹套的覆盖面积为1.61m2。
加热蒸汽为3公斤(温度为143.2℃),将总物料(4100 kg)从10摄氏度加热至沸腾100摄氏度。
解:反应釜夹套加热冷热两侧的传热温差为:143.2-(10+100)÷2=88.2℃,所需要的热量:4.2×4100×90=1.5498×106 kJ。
选择的反应釜夹套的平均传热系数为900 w/(m2•k),(注:需依据项目需要确定参数,并保留10%余量)加热过程的计算:假设纯水进量为25 m3/h,3800 kJ水量的进入的时间为9 min,在反应釜中通纯水3 min后,随即打开底盖的夹套进行加热,待纯水即将达到3800 kg之际,剩余的6 min,内底盖夹套提供的热量(143.2-20)×1.61×900×6×60=6.4266×104 kJ,至此,温度提高至6.4266×104÷4.2÷4100=3.73℃进水完毕,釜内温度升高至13.73℃,紧接着将水从13.73℃加热至100℃,所需热量4.2×4100×86.3=1.486086×106 kJ反应釜内物料总体积4100m3,受热面积为1.61+5.52=7.13 m2,将总重为4100kg物料从 3.73℃加热至100℃,所需时间1.486086×106×1000÷(900×7.31×(143.2-(13.73+100)÷2))=2682s=44.7 min。
反应釜容积计算公式
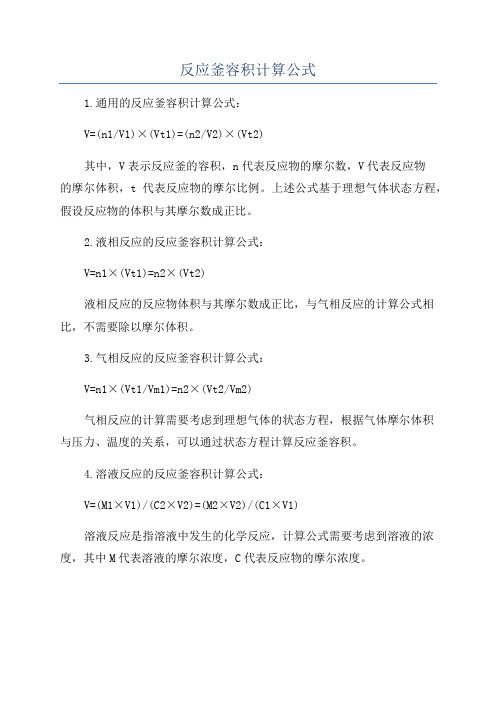
反应釜容积计算公式1.通用的反应釜容积计算公式:V=(n1/V1)×(Vt1)=(n2/V2)×(Vt2)其中,V表示反应釜的容积,n代表反应物的摩尔数,V代表反应物的摩尔体积,t代表反应物的摩尔比例。
上述公式基于理想气体状态方程,假设反应物的体积与其摩尔数成正比。
2.液相反应的反应釜容积计算公式:V=n1×(Vt1)=n2×(Vt2)液相反应的反应物体积与其摩尔数成正比,与气相反应的计算公式相比,不需要除以摩尔体积。
3.气相反应的反应釜容积计算公式:V=n1×(Vt1/Vm1)=n2×(Vt2/Vm2)气相反应的计算需要考虑到理想气体的状态方程,根据气体摩尔体积与压力、温度的关系,可以通过状态方程计算反应釜容积。
4.溶液反应的反应釜容积计算公式:V=(M1×V1)/(C2×V2)=(M2×V2)/(C1×V1)溶液反应是指溶液中发生的化学反应,计算公式需要考虑到溶液的浓度,其中M代表溶液的摩尔浓度,C代表反应物的摩尔浓度。
需要注意的是,上述公式只是一般性的计算公式,具体情况下需要根据实际反应情况进行调整。
同时,在实际设计中要考虑到反应速率、反应平衡等因素,以及考虑釜内混合均匀度、传热效果等工程因素。
除了上述公式外,还可以通过数值模拟、实验方法进行反应釜容积的优化设计。
近年来,随着计算机模拟技术的不断发展,反应釜容积的计算方法也更加准确和可靠。
然而,在实际设计中仍然需要根据经验和实际情况进行调整和修正,以达到最佳的设计目标。
总之,反应釜容积的计算公式是根据反应条件、反应物的摩尔比例和摩尔体积等因素进行综合考虑的。
在实际设计中需要根据具体反应情况进行调整和优化,以达到预期的反应效果。
夹套反应釜设计
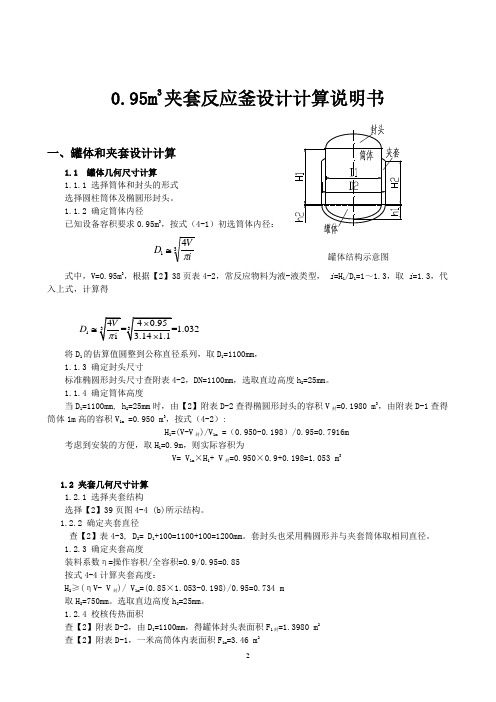
0.95m 3夹套反应釜设计计算说明书一、罐体和夹套设计计算1.1 罐体几何尺寸计算1.1.1 选择筒体和封头的形式 选择圆柱筒体及椭圆形封头。
1.1.2 确定筒体内径已知设备容积要求0.95m 3,按式(4-1)初选筒体内径:式中,V=0.95m 3,根据【2】38页表4-2,常反应物料为液-液类型, i =H 1/D 1=1~1.3,取 i =1.3,代入上式,计算得1D ≅将D 1的估算值圆整到公称直径系列,取D 1=1100mm ,1.1.3 确定封头尺寸标准椭圆形封头尺寸查附表4-2,DN=1100mm ,选取直边高度h 2=25mm 。
1.1.4 确定筒体高度当D 1=1100mm, h 2=25mm 时,由【2】附表D-2查得椭圆形封头的容积V 封=0.1980 m 3,由附表D-1查得筒体1m 高的容积V 1m =0.950 m 3,按式(4-2):H 1=(V-V 封)/V 1m =(0.950-0.198)/0.95=0.7916m考虑到安装的方便,取H 1=0.9m ,则实际容积为V= V 1m ×H 1+ V 封=0.950×0.9+0.198=1.053 m31.2 夹套几何尺寸计算 1.2.1 选择夹套结构选择【2】39页图4-4 (b)所示结构。
1.2.2 确定夹套直径查【2】表4-3, D 2= D 1+100=1100+100=1200mm 。
套封头也采用椭圆形并与夹套筒体取相同直径。
1.2.3 确定夹套高度装料系数η=操作容积/全容积=0.9/0.95=0.85 按式4-4计算夹套高度:H 2≥(ηV- V 封)/ V 1m =(0.85×1.053-0.198)/0.95=0.734 m 取H 2=750mm 。
选取直边高度h 2=25mm 。
1.2.4 校核传热面积查【2】附表D-2,由D 1=1100mm ,得罐体封头表面积F 1封=1.3980 m 2查【2】附表D-1,一米高筒体内表面积F 1m =3.46 m 2314iV D π≅罐体结构示意图校核传热面积:实际总传热面积F=F 筒+ F 1封=F 1m ×H 2 +F 1封=3.46×0.75+1.398=3.99 m 2>3.8 m 2,可用。
反应釜设计计算范文

反应釜设计计算范文反应釜是一种广泛应用于化工工业中的重要设备,主要用于进行化学反应。
在设计反应釜时,需要考虑很多参数和因素,以确保反应釜的效率和安全性。
第一步是确定所需反应釜的容积。
容积的选择取决于反应物质的种类和数量,反应的速率以及反应的尺度。
较大的容积可容纳更多的反应物,但也需要更强的搅拌和加热/冷却能力来确保反应的均匀性和控制温度。
第二步是确定反应釜的形状。
常见的反应釜形状包括圆筒形、球形、卧式和立式。
选择合适的形状取决于工艺要求、操作方便性和设备布局。
第三步是计算反应釜的加热和冷却能力。
加热能力的计算要考虑反应的放热量和反应速率,采用装有加热元件(如蒸汽夹套)的方式来提供热源。
冷却能力的计算要考虑反应过程中产生的热量,以确保温度控制在安全范围内。
第四步是选择搅拌方式和功率。
搅拌的目的是保持反应物的均匀混合,以提高反应速率和产物质量。
常用的搅拌方式包括机械搅拌和磁力搅拌。
搅拌功率的计算取决于反应物的黏度、密度和反应速率等参数。
第五步是选择反应釜的材料。
材料的选择要考虑反应物的性质,如酸碱度、温度和压力等。
常见的反应釜材料包括碳钢、不锈钢、玻璃钢和钛合金等。
第六步是考虑反应釜的安全问题。
安全设计要求包括压力容器的设计压力、温度和材料强度等,以保证釜体在正常工作和突发情况下的安全性。
除了上述的设计计算,还需要进行相应的实验和测试来验证设计的合理性和准确性。
这些实验包括对反应釜的稳定性、温度和压力控制的测试,以及对搅拌效果和反应转化率的测试。
反应釜的设计计算是一个综合性的工作,需要考虑很多因素和参数。
只有全面地分析和计算,才能确保反应釜的高效运行和安全操作。
反应釜计算体积公式

反应釜计算体积公式反应釜是一种用于进行化学反应的设备,它具有一个封闭的容器,能够控制反应温度、压力和时间等参数。
在设计和操作反应釜时,准确计算其体积是非常重要的,因为它可以影响到反应条件的控制和反应物的使用量。
反应釜的体积可以通过几种方法来计算,其中最常用的方法是基于釜体的几何形状进行计算。
根据反应釜的形状可以分为圆柱形、球形和锥形等。
下面将分别介绍这三种形状反应釜的体积计算公式。
1.圆柱形反应釜的体积计算公式:圆柱形反应釜的容积可以通过计算釜体的底面积乘以高度来得到。
公式如下:V=πr^2h其中,V为反应釜的体积,π为圆周率,r为釜体的半径,h为釜体的高度。
2.球形反应釜的体积计算公式:球形反应釜的容积可以通过计算球体的体积来得到。
公式如下:V=(4/3)πr^3其中,V为反应釜的体积,π为圆周率,r为球体的半径。
3.锥形反应釜的体积计算公式:锥形反应釜的容积可以通过计算锥体的体积来得到。
公式如下:V=(1/3)πr^2h其中,V为反应釜的体积,π为圆周率,r为锥体的底面半径,h为锥体的高度。
需要注意的是,在实际计算中,反应釜的几何形状可能会比较复杂,无法简单地通过上述公式进行计算。
这时候可以采用离散法来进行计算,将反应釜体积划分为多个小体积,并分别计算其体积后再求和。
这在计算复杂形状的反应釜体积时比较常用。
此外,还需要考虑反应釜中的其它构造物对容积的影响,如搅拌器、冷却装置等,需要适当调整计算公式。
总之,在计算反应釜的体积时,首先确定釜体的几何形状,然后根据相应的公式进行计算,如果形状较为复杂,可以采用离散法进行计算。
同时,也需要考虑附加结构物对容积的影响,以提高计算的准确性。
反应釜的设计计算

反应釜的设计计算
1.反应釜的容积计算:
反应釜的容积计算是根据反应物的质量、浓度、摩尔体积等参数来确定的。
计算方法通常是根据反应物的化学方程式和反应平衡常数,通过平衡恒等式的推导得出。
具体计算方法可以参考化学工程的教材和相关设计规范。
2.反应釜的尺寸计算:
反应釜的尺寸计算主要包括釜体直径、高度、壁厚等参数的确定。
尺寸计算的依据通常是根据反应釜的容积、压力、温度和材料的力学性能等因素来确定的。
壁厚的计算可以使用ASME或其他相关设计规范中给出的公式和方法,以满足压力容器设计的安全要求。
3.反应釜的搅拌装置设计计算:
反应釜的搅拌装置的设计计算主要包括搅拌桨的形状、尺寸、转速等参数的确定。
搅拌装置的设计计算是根据反应液的性质、反应速率以及搅拌对于混合、传质等效果的要求来确定的。
4.反应釜的换热装置设计计算:
反应釜的换热装置主要包括壁面换热和内部换热两种形式。
壁面换热可以通过增加釜体壁厚、增大换热面积等方式来提高传热效率。
内部换热与液相或气相之间的流体传热有关,通常可以通过增加搅拌或循环流动来提高传热效率。
5.其他关键参数的计算:
其他关键参数的计算还包括反应釜的最大操作压力、操作温度、材料的选型等。
这些参数的计算依据主要是根据反应物的性质、反应过程的要求以及压力容器设计和安全规范来确定。
综上所述,反应釜的设计计算是一个复杂的过程,需要考虑多个因素的综合影响,以确保反应釜的性能和安全运行。
在进行设计计算时,需要基于理论和实践经验,并结合相关规范和标准来进行。
同时,还需要进行工程实践和实验验证,以验证设计计算的准确性和可行性。
夹套反应釜设计计算

夹套反应釜设计计算首先,夹套反应釜的热传导方程是非常重要的设计依据。
热传导方程可以用来推导出夹套和反应体系之间的热传导系数,从而确定夹套的尺寸和设计条件。
热传导方程的基本形式可以表示为:Q=k*A*ΔT/Δx其中,Q是热通量,k是热传导系数,A是传热面积,ΔT是温度差,Δx是传热距离。
夹套反应釜的设计计算中还需要确定传热系数k。
传热系数与夹套和反应体系之间的传热面积、流体的导热性质有关。
传热系数的计算可以采用经验公式或者利用流体力学和传热学的计算方法。
对于常见的工艺流体,可以使用流体传热系数的经验公式进行计算。
在进行夹套反应釜的设计计算时,需要考虑到反应体系的热容和传热特性。
热容是指单位质量物质在单位温度变化下所吸收或放出的热量。
传热特性包括传热速率、传热强度等参数。
这些参数对于夹套反应釜的设计和操作都有很大的影响。
在设计夹套反应釜时,还需要考虑到反应体系的冷却方式。
冷却方式可以分为直接冷却和间接冷却两种。
直接冷却是指利用夹套内部的冷却介质来降低反应体系的温度,而间接冷却则是通过外部介质进行冷却。
直接冷却通常可以实现较高的冷却速率,但也会带来传热效果的不均匀性。
间接冷却通常可以实现较好的传热效果,但需要更复杂的设备和操作。
在进行夹套反应釜的设计计算时,还需要考虑到夹套和反应体系之间的绝热性能。
绝热性能可以通过计算夹套和反应体系之间的热传导系数和传热面积来确定。
通过合理设计绝热层的材料和结构,可以减少热量的损失,提高反应体系的稳定性。
综上所述,夹套反应釜的设计计算是一个复杂的过程,需要考虑到反应体系的热传导、传热特性、冷却方式和绝热性能等多个方面的因素。
只有通过合理的设计和计算,才能确保夹套反应釜的安全和高效运行。
标准反应釜外表面积计算表(标准反应釜外表面积计算表)

标准反应釜外表面积计算表(标准反应釜外表面积计算表)下面是修正后的文章:表格:标准反应釜外表面积计算表注:设备外形按K型搪瓷反应釜尺寸计算,封头按标准椭圆封头,保温厚度按50mm计。
表中表面积为保温后的设备外表面积,m2;表中设备净尺寸为:D上×D下×[釜盖高度+釜体高度],mm;釜规格型号,L。
釜规格:K100釜数量,个:3单釜保温表面积,m2:2.19设备净尺寸:60×700×[235+500]封头总深度,mm:上封头:175下封头:200保温后设备尺寸:70×800×[235+500]表面积:2.19釜规格:K300釜数量,个:3单釜保温表面积,m2:3.29设备净尺寸:70×900×[310+600]封头总深度,mm:上封头:200下封头:250保温后设备尺寸:80×1000×[310+600] 表面积:3.29釜规格:K500釜数量,个:3单釜保温表面积,m2:5.10设备净尺寸:90×1000×[335+1000]封头总深度,mm:上封头:250下封头:275保温后设备尺寸:100×1100×[335+1000]表面积:5.10釜规格:K1000釜数量,个:2+1单釜保温表面积,m2:7.59设备净尺寸:1200×1300×[410+1200]封头总深度,mm:上封头:325下封头:350保温后设备尺寸:1300×1400×[410+1200] 表面积:7.59釜规格:K1500釜数量,个:1单釜保温表面积,m2:6.81设备净尺寸:1300×1450×[435+1400]封头总深度,mm:上封头:350下封头:385保温后设备尺寸:1400×1550×[435+1400]表面积:6.81釜规格:K2000釜数量,个:2单釜保温表面积,m2:11.75设备净尺寸:1300×1450×[435+1740]封头总深度,mm:上封头:350下封头:385保温后设备尺寸:1400×1550×[435+1740] 表面积:11.75釜规格:K3000釜数量,个:3单釜保温表面积,m2:14.81设备净尺寸:1600×1750×[510+1735]封头总深度,mm:上封头:425下封头:460保温后设备尺寸:1700×1850×[510+1735]表面积:14.81釜规格:K5000釜数量,个:1单釜保温表面积,m2:6.57设备净尺寸:1750×1900×[5147+2335]封头总深度,mm:上封头:460下封头:500保温后设备尺寸:1850×2000×[510+2335]表面积:19.89修正后的文章:下面是标准反应釜外表面积计算表。
反应釜的设计计算

反应釜的设计计算反应釜是一种用于进行化学反应的容器,广泛应用于化工工艺中。
反应釜的设计计算涉及到多个方面,包括容积计算、工作压力计算、热量传递计算等。
本文将对反应釜的设计计算进行详细介绍。
1.容积计算反应釜的容积设计是根据反应物的种类、反应速度以及所需达到的反应程度等因素来确定的。
容积计算的基本原则是要确保釜内具有足够的空间容纳反应物和产物,并保持充足的搅拌和传热效果。
容积计算的公式如下:容积=反应物的摩尔数*摩尔体积*反应的摩尔系数其中,反应物的摩尔数可以通过化学方程式中的系数获得,摩尔体积可以通过气体状态方程计算获得。
2.工作压力计算工作压力是指反应釜内的压力,在设计计算中需要考虑到反应釜能够承受的最大工作压力以及安全系数。
通常情况下,反应釜的工作压力一般为1.5倍于反应压力,以确保在正常操作和异常情况下都能保持压力稳定。
工作压力计算的公式如下:工作压力=反应压力*安全系数3.热量传递计算热量传递是指在反应釜内进行反应过程中热量的传递和控制。
反应釜的热量传递计算主要包括反应物的升温时间、反应热量的计算以及冷却系统的设计等。
反应物的升温时间可以通过热传导方程计算得出:T=(Ts-T0)/(a*A*h)其中,T代表升温时间,Ts代表反应温度,T0代表初始温度,a代表热扩散系数,A代表表面积,h代表热传递系数。
反应热量的计算可以通过反应物的反应热以及反应的相对摩尔数来获得。
冷却系统的设计通常包括冷却剂的选择、冷却剂流量的计算以及冷却剂进出口温度的控制等。
综上所述,反应釜的设计计算是一个复杂而全面的过程,需要综合考虑反应物、反应压力、热量传递等多个因素。
在进行设计计算时,需要依据具体的使用要求和工艺参数进行合理的估算和选择,以确保反应釜的安全可靠运行。
间歇操作釜式反应器的设计—间歇操作釜式反应器体积和数量的计算

三、间歇操作釜式反应器的体积和数量计算
由物料衡算求出每小时需处理的物料体积V0后,即可进行反应釜的 体积V和数量n的计算。
计算时,在反应釜体积和数量这两个变量中必须先确定一个。由于 数量一般不会很多,通常可以用几个不同的n值来算出相应的V值, 然后再决定采用哪一组n和V值比较合适。
⒈ 给定V,求n
• 按设计任务每天需操作的批次为:
24V0 24V0
VR
V
VO 每小时需处理的物料体积
• 设备中物料所占体积即反应器有效体积 VR 与设备实际体积即反应 器体积V之比称为设备装料系数,以符号 表示,具体数值根据实 际情况而变化。
• 每天每只反应釜可操作的批次为:
24 24 t '
• 操作周期t又称工时定额,是指生产每一批物料的全部操作时间。由 于间歇反应器是分批操作,其操作时间由两部分构成:一是反应时间
,用 表示;二是辅助时间,即装料、卸料、检查及清洗设备等所需
时间,用 '表示。
• 生产过程需用的反应釜数量 n' 可按下式计算:
n' V0 ( ' )
V
• 由上式计算得到的 n'值通常不是整数n,需圆整成整数。这样反应釜 的生产能力较计算要求提高了,其提高程度称为生产能力的后备系 数,以 表示,即:
理的物料总重量 GD , 用它除以物料的密度ρ,即得每天所需处理物料 的总体积VD,
VD
GD
操作周期
操作周期又称工时定额,是指生产每一批料的全部操作时间,即从 准备投料到操作过程全部完成所需的总时间。
例如萘磺化制取2—萘磺酸的操作周期计算如下:
检查设备
加萘 加硫酸及升温 反应 压出料 操作周期
夹套式反应釜设计

一·反应釜的总体设计首先对工艺要求进行分析,以便能确定反应釜设计的总体方案。
1.确定筒体的直径和高度①选取反应釜装料系数η=0.8,由V=V 0/η 可得操作容积:V 0=η·V=0.8*4=3.2 m3 对于液-液相类型选取长径比H/D i =1.1D i =3)/(4D H V π=31.1*4*4π=1666.98 mm 将此结果圆整至公称标准系列,选取筒体直径D i =1600 mm②确定封头。
选取标准椭圆形封头(JB/T 4746-2002),查 教材 表8-27 DN=1600mm 时的标准椭圆形封头封头容积V F =0.586 m 3 , 曲面高度h1=300 mm ,直边高度h2=25 mm ,表面积Fh=2.901 m 2计算1米高的筒体容积V 1=42Di π=46.1*14.32=2.0096 m 3 ③确定筒体高度H=1V V V F -=0096.2586.04-=1.698 m 筒体高度圆整为H=1.7m=1700mm于是H/D=1700/1600=1.0625,复合结果基本符合原定范围。
2. 确定夹套的直径和高度①确定夹套的直径夹套内径Dj 与釜体的内径Di 有关,如下关系:Di/mm 500-600 700-1800 2000-3000Dj/mm Di+50 Di+100 Di+200因此,Dj=1600+100=1700 mm ,符合压力容器公称直径系列。
②确定夹套的高度 Hj=1V V V F-η=0096.2586.04*8.0-=1.30076 m 圆整夹套高度Hj=1300 mm验算夹套的总传热面积 F=10.21 m 2. 〉8 m 2夹套传热面积符合设计要求。
3. 选择釜体法兰根据筒体操作压力0.2MPa ,温度110℃和筒体直径1600mm ,查 教材—表10-1初选甲型平焊法兰,再查标准JB 4701-2000 甲型平焊法兰《过程设备机械设计》标11 和 教材—表10-10,在110℃工作范围内Q235-B 的最大允许工作压力为0.4MPa ,大于筒体设计压力,所选甲型平焊法兰合适。
反应釜容积计算公式
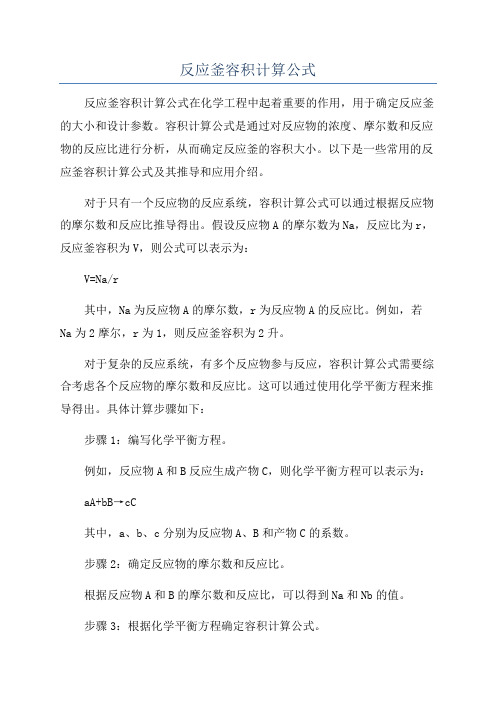
反应釜容积计算公式反应釜容积计算公式在化学工程中起着重要的作用,用于确定反应釜的大小和设计参数。
容积计算公式是通过对反应物的浓度、摩尔数和反应物的反应比进行分析,从而确定反应釜的容积大小。
以下是一些常用的反应釜容积计算公式及其推导和应用介绍。
对于只有一个反应物的反应系统,容积计算公式可以通过根据反应物的摩尔数和反应比推导得出。
假设反应物A的摩尔数为Na,反应比为r,反应釜容积为V,则公式可以表示为:V=Na/r其中,Na为反应物A的摩尔数,r为反应物A的反应比。
例如,若Na为2摩尔,r为1,则反应釜容积为2升。
对于复杂的反应系统,有多个反应物参与反应,容积计算公式需要综合考虑各个反应物的摩尔数和反应比。
这可以通过使用化学平衡方程来推导得出。
具体计算步骤如下:步骤1:编写化学平衡方程。
例如,反应物A和B反应生成产物C,则化学平衡方程可以表示为:aA+bB→cC其中,a、b、c分别为反应物A、B和产物C的系数。
步骤2:确定反应物的摩尔数和反应比。
根据反应物A和B的摩尔数和反应比,可以得到Na和Nb的值。
步骤3:根据化学平衡方程确定容积计算公式。
根据化学平衡方程中各个反应物的系数以及反应物的摩尔数和反应比,可以得到反应釜容积的计算公式。
例如,若a为2,b为3,c为1,Na为4摩尔,Nb为6摩尔,反应釜容积的计算公式可以表示为:V = max(aNa/bNb, c)在上述例子中,反应釜容积为2升。
3.反应速率和反应时间对容积的影响容积计算公式还需要考虑反应速率和反应时间对容积的影响。
反应速率决定了反应物转化为产物所需的时间,反应时间决定了反应物在反应釜中停留的时间。
较高的反应速率会导致更快的产物生成,而较长的反应时间会导致反应物在反应中停留的时间更长。
因此,在确定容积计算公式时,需要综合考虑反应速率和反应时间的因素。
一般来说,为了提高反应速率和减少反应时间,可以增加反应釜的搅拌速度、加大反应温度、使用催化剂等方法。
反应釜筒体高度计算公式
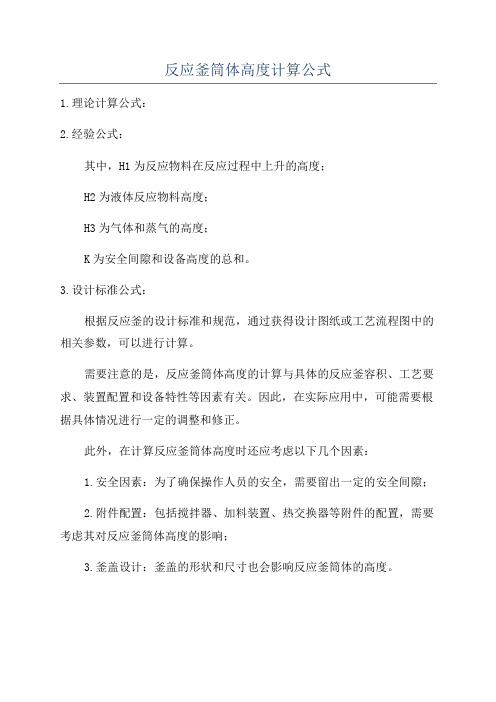
反应釜筒体高度计算公式
1.理论计算公式:
2.经验公式:
其中,H1为反应物料在反应过程中上升的高度;
H2为液体反应物料高度;
H3为气体和蒸气的高度;
K为安全间隙和设备高度的总和。
3.设计标准公式:
根据反应釜的设计标准和规范,通过获得设计图纸或工艺流程图中的相关参数,可以进行计算。
需要注意的是,反应釜筒体高度的计算与具体的反应釜容积、工艺要求、装置配置和设备特性等因素有关。
因此,在实际应用中,可能需要根据具体情况进行一定的调整和修正。
此外,在计算反应釜筒体高度时还应考虑以下几个因素:
1.安全因素:为了确保操作人员的安全,需要留出一定的安全间隙;
2.附件配置:包括搅拌器、加料装置、热交换器等附件的配置,需要考虑其对反应釜筒体高度的影响;
3.釜盖设计:釜盖的形状和尺寸也会影响反应釜筒体的高度。
反应釜加热功率计算

反应釜的加热功率的计算方式:1、反应釜自身重量所需的加热功率:反应釜的重量(KG)*温差*钢的比热(0.11)/860*时间(小时)=1个小时反应釜升温所需的功率*1.2(安全系数);2、反应釜所反应的物料的加热功率:物料的重量(KG)*温差*物料的比热/860*时间=物料升温所需的加热功率*1.2(安全系数);3、反应釜夹套或盘管内导热油升温的加热功率:导热油的重量(KG)*温差*导热油比热(0.55)/860=导热油所需的加热功率;1+2+3=反应釜升温所需的加热功率化工反应搅拌器加热控温案例:物料:环氧树脂;初始温度:40度,要求加热控温到80度;搅拌器容积:1200升;夹套容积:80升;进出口尺寸:1进1出1寸;升温时间:30分钟;其它已知条件:管路长度约1.5米;根据现有参数及要求:我司经过计算及选型,发热功率为:24KW;循环泵浦的功率为1.5KW;机器最高温度为180度,油箱30升。
即AOS-20-24,可完成满足加热控温的要求。
反应釜夹套温度控制——导热油加热器最高温度可达450度.案例展示:需要将1个反应釜5小时内加到200度;已知条件:1、反应釜单台夹层容积700L;2、里面物料为氢氧化镁(碱性);3、总共反应釜物料空间为7.5立方/台,一般物料装至百分之八十;4、反应釜为钢质,暂时估计反应釜本身重量为三吨/台;设计要点、方案选型:一、加热功率计算:1、氢氧化镁比热为0.9Kcal/kg., 860千卡=1KW设室温为25℃,温度差设为200℃,时间为5小时加热功率:KW=W×△t×C/ (860×T)7T加热功率: 700×175×0.9÷(860×5)=256KW;2、夹套内导热油加温需要的加热功率;导热油比热为0.5Kcal/kg., 密度为0.85;860千卡=1KW设室温为25℃,温度差设为220℃,时间为5小时加热功率:KW=W×△t×C/ (860×T)加热功率:KW=595×0.5×195/(860×5)=14KW;3、反应釜升温本身所需功率钢铁比热为0.11Kcal/kg., 860千卡=1KW设室温为25℃,温度差设为175℃,时间为5小时加热功率:KW=3000×175×0.11/(860×5)=14KW;总加热功率:KW=256+14+14=284KW以上计算以热效率为100%,未计加热过程中热量的损失,及反应釜自身金属升温所需的热量得出的结果.实际选择时加0.3倍的安全系数.284KW×1.3=369KW. 实际选择360KW.二、泵的选择根据反应釜夹套容积700L,泵选择RY80-50-200 流量为60m3/h, 扬程为46米.。
反应釜壁厚计算

反应釜壁厚计算
反应釜壁厚的计算可以通过以下步骤进行:
1. 确定反应釜所承受的内部压力。
内部压力可由反应釜中的反应物性质和操作条件决定。
2. 确定反应釜的材料。
根据反应物性质和操作条件,选择合适的材料,如不锈钢、碳钢等。
3. 计算静态应力。
静态应力即材料所能承受的最大内径应力,可通过公式σ = P * D / (2 * t) 计算,其中σ为静态应力,P为内部压力,D为反应釜的内径(或外径),t为釜壁厚度。
4. 根据材料的屈服强度选择合适釜壁厚度。
根据步骤3计算得到的静态应力和所选材料的屈服强度,选择合适的釜壁厚度,确保釜壁足够厚以承受内部压力。
需要注意的是,反应釜壁厚的计算涉及到许多因素,如材料的强度、温度和压力的变化等。
因此,在具体的工程应用中,需要结合实际情况进行详细的计算和设计。
同时,为了确保反应釜的安全运行,建议咨询相关专业技术人员或工程师的意见。
6300l反应釜内表面面积
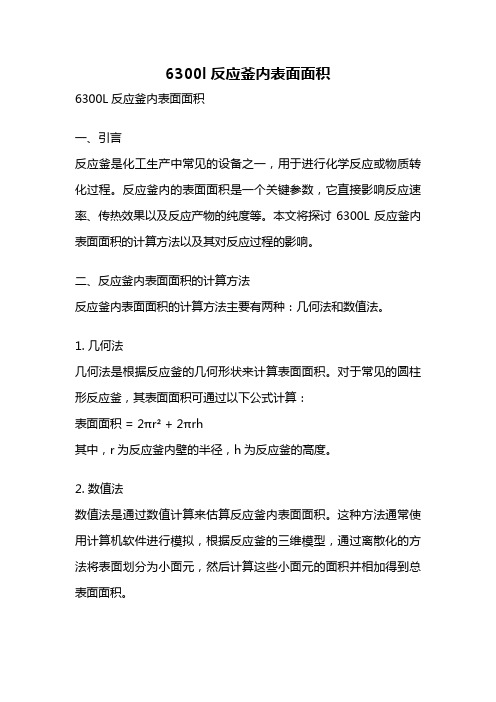
6300l反应釜内表面面积6300L反应釜内表面面积一、引言反应釜是化工生产中常见的设备之一,用于进行化学反应或物质转化过程。
反应釜内的表面面积是一个关键参数,它直接影响反应速率、传热效果以及反应产物的纯度等。
本文将探讨6300L反应釜内表面面积的计算方法以及其对反应过程的影响。
二、反应釜内表面面积的计算方法反应釜内表面面积的计算方法主要有两种:几何法和数值法。
1. 几何法几何法是根据反应釜的几何形状来计算表面面积。
对于常见的圆柱形反应釜,其表面面积可通过以下公式计算:表面面积 = 2πr² + 2πrh其中,r为反应釜内壁的半径,h为反应釜的高度。
2. 数值法数值法是通过数值计算来估算反应釜内表面面积。
这种方法通常使用计算机软件进行模拟,根据反应釜的三维模型,通过离散化的方法将表面划分为小面元,然后计算这些小面元的面积并相加得到总表面面积。
三、反应釜内表面面积对反应过程的影响反应釜内表面面积的大小直接影响反应过程的效率和产物的纯度。
1. 反应速率反应釜内表面面积越大,反应物与反应釜内壁的接触面积就越大,反应速率也就越快。
这是因为反应物需要与反应釜内壁接触才能进行反应,表面积越大,反应物与釜壁的接触就越频繁,反应速率也就越高。
2. 传热效果在某些反应过程中,需要通过反应釜内壁进行传热。
反应釜内表面面积的增大可以提高传热效果,加快反应速率。
这是因为表面积越大,与反应釜内壁接触的面积也就越大,传热的效果也就越好。
3. 反应产物纯度反应釜内表面面积的大小还会影响反应产物的纯度。
在一些反应中,反应产物与反应釜内壁发生副反应,导致产物纯度降低。
而表面面积越大,副反应的发生机会就越大,产物纯度也就越低。
四、结论本文探讨了6300L反应釜内表面面积的计算方法和其对反应过程的影响。
我们发现,反应釜内表面面积的大小与反应速率、传热效果以及反应产物的纯度有密切关系。
因此,在设计反应釜时,应合理计算和控制表面面积,以提高反应效率和产物质量。
- 1、下载文档前请自行甄别文档内容的完整性,平台不提供额外的编辑、内容补充、找答案等附加服务。
- 2、"仅部分预览"的文档,不可在线预览部分如存在完整性等问题,可反馈申请退款(可完整预览的文档不适用该条件!)。
- 3、如文档侵犯您的权益,请联系客服反馈,我们会尽快为您处理(人工客服工作时间:9:00-18:30)。
Di 3
4Vg 3
(H)
41.15 1.22m
10.8
Di
根据标准圆整取 Di 1300mm
精选ppt
10
釜体高度的计算
结构设计计算结果
查表可知,直径为1300mm的椭圆封头总深度 H h350m m,A1.9340m2
内表面积, Vh 0.320m83。
精选ppt
11
结构设计计算结果
对于直立式反应釜,其圆筒部分筒体的高度为
釜体筒体厚度的计算
设定操作温度T=100℃。腐蚀余量为 C2 2mm,钢板负偏差 C1 0.3mm
取焊接接头系数 0.85选材上,由于承受压力较高,所以选择Q345R。
t 18M 9 Pa
内压 0.1MPa
设计压力: pw 0.1MPa
p1.1pw0.1M 1 Pa
P l gh5% Pw, 所以
计算厚度:0.41mm 设计厚度:2.41mm 名义厚度:6mm
精选ppt
16
结构计算计算结果
反应釜的搅拌装置
搅拌功率的计算
粘度计算公式
n
lg m
xi lg i
i1
解得
m3.02104pas
搅拌器直径 d=400mm
叶片直径 b=80mm
叶轮转速 n= 238.8r/min
雷诺数
Re2.1106
搅拌轴材料的选择
常用优质碳素钢有35、45、50钢,其中以45钢应用最多。搅拌轴受到扭转和弯 曲的组合作用,其中以扭转为主。本次设计选用45钢作为搅拌轴的材料。
精选ppt
19
结构设计计算结果
搅拌轴直径的计算
搅拌轴的材料选为45钢,轴材料剪切弹性模量G79GPa,许用剪切应力
40MPa 1o /m
H''
V4g D Vi20
1.150.3208
0.8
1.222
0.96m
4
根据标准圆整取 H'' 100m0m
但是 H/Di 1~3,则重新选取。再取 H/Di 1.3,则有:
Di 1.15m
H" 1.05m
则圆整 则圆整
Di 1200mm H'' =1200mm
精选ppt
12
结构设计计算结果
5
工艺设计计算结果
反应体积
反应器的有效体积:
V r Q 0 0 .6 1 4 3 .7 5 1 .4 4 m 3
反应器的实际体积:
VV r
1.441.8m3 0.8
精选ppt
6
工艺设计计算部分结果参数汇总
C A 0 —原料液中乙酸酐的起始浓度,9.5×10^-2 mol/L;
C A —反映后乙酸酐的浓度,7.6×10^-3 mol/L;
名义厚度:n d C1
nd C 1 圆 2 整 .7m 1 圆 m,圆整 整为6mm。
有效厚度:enC1C2
enC 1C 23.7mm
精选ppt
15
结构计算计算结果
夹套的选择
夹套的内径 夹套高度
夹套筒体厚度
夹套封头厚度
1300mm
0.63m
计算厚度:0.41mm 设计厚度:2.41mm 名义厚度:6mm
过程装备与控制工程课程设计
Course design of process equipment and control engineering
反应釜的设计计算
精选ppt
1
任务书
主要内容: 1 设计方案的确定及工艺流程的说明; 2 反应器的工艺计算; 3 基本尺寸计算及基本结构设计; 4 壳体、开孔补强与搅拌轴及耳式支座的强度校核; 5 绘制反应器的装配图。
轴传递最大转矩:
M m a 9x5 p n n5 9 35 2 5 5 .5 .8 3 3 0 .8 9 1N 9 m 8
搅拌轴为实心轴,则直径:
1
d 4.92
精选ppt
8
釜体直径的计算
结构设计计算结果
对于直立反应釜来说,釜体容积通常是指圆柱形筒体及下封头所包含的容积之
和,根据釜体容积和物料性质,选定
H / D i 值,估算筒体内径 D
。由于此反应
i
为液—液反应,故而取 H / Di 1 ,先忽略釜体封头的容积。
精选ppt
9
结构设计计算结果
筒体内径:
率5.5kw,转速960r/min。
精选ppt
18
结构计算计算结果
减速机的选用 根据轴转速960r/min,电动机功率为5.5kw。查表可知:应选用滚筒减速机,编
号为96012。 联轴器的选用
T 9550 P
T955 50419 .98 N 6m
n
960
查《机械设计课程设计》可知:联轴器应选GY4,类型为凸缘联轴器。
V r —有效体积,1.44m3;
—反应时间,143.75min;
X A —乙酸酐的转化率92%。
Q 0 —单位时间原料液处理量,0.6m3/h;
V —反应器的实际体积,1.8m3;
—装料系数0.8;
精选ppt
7
结构设计部分
釜体结构形式的选择 筒体:圆柱形 釜底的封头形状:标准椭圆型 顶盖连接方法:不可拆 换热器形式:U形夹套
精选ppt
17
结构计算计算结果
经查《过程设备设计》功率曲线可知,功率准数Np=6 搅拌功率P=3.91kw 叶轮距槽底的安装高度Hi =400mm 挡板宽度Wb =120mm
电机的选用 电动机功率P=4.57kw 根据电动机的标准,查《机械设计课程设计》,电动机可选用Y ·132 M 2-6,功
精选ppt
3
接近设计条件的实物图
精选ppt
4
工艺设计计算结果
原料的处理量
C A C A 0 ( 1 A f) 9 5 ( 1 9 2 % ) 7 .6 m o l/m 3
反应时间
Q Vr0F VA r0CA0 r AAf 0.9650 89 21% 03143.75m in
CA0
精选ppt
则计算压力: pc p0.11MPa
P l 忽略不计。
精选ppt
13
结构计算计算结果
计算厚度:
Pc Di
2
Pc
2p tc D i pc210.1 8 0 .1 8 9 2 5 0.1 0 1 0 0.4m 1 m
精选ppt
14
结构计算计算结果
设计厚度:d C2
dC 22.41 m m
精选ppt
2
设计条件:
乙酸酐分解式为
( C H 3 C O ) 2 O H 2 O 2 C H 3 C O O H
该反应的反应速率方程为,反应温度下反应速率常数为0.08 m in -1。每小时处理
量为 0.6m 3,原料中乙酸的浓度 CA095mol/m3。试设计一台连续操作釜式反
应器达到要求: