烧结烟道余热回收
烧结机烟道废气余热回收利用

i n g r e c o n s t r u c t i o n
近几 年 我公 司 积极 响应 国 家号 召 , 推 动 循 环
量。
经济 的发 展 , 充 分 利 用 烧 结 环 冷 机 废 气余 热 回收 发电, 先后在 2 0 0 9年 建 设 了 2×3 6 0 m 烧 结 余 热 发 电项 目, 2 0 1 1 年 建设 了 6×1 8 0 m 烧 结余 热发 电
烧结烟道余热回收

烧结烟道余热回收工程技术方案书天津华能能源设备有限公司二○一三年五月一、总述1. 项目实施企业简介用户提供2. 设计依据××××××,提供336㎡烧结大烟道余热锅的设计依据。
3. 设计原则采用已有的成熟技术,注重技术的适用性、可靠性、经济性和先进性,工艺技术及装备水平达到国内先进水平;设备选型原则:设备以国产化为主,尽量考虑设备的大型化;布置原则:考虑未来发展,合理使用场地,工艺布置和物料流程合理、通畅,尽量避免各工序间的相互干扰;整套系统工程的设计符合国家标准。
4. 主要设计内容余热回收系统:余热锅炉系统、给水系统、除尘系统、烟道系统、控制系统;5. 设计概要利用烧结主抽烟道内的高温段废气进行余热回收。
二、系统设计方案1、工程概述钢铁冶金企业是国家支柱产业,在现代化建设中起着重要作用,同时这些企业也是耗能大户,能耗占产品成本比例较大。
因此企业的节能降耗显得尤其重要。
烧结工序是高炉矿料入炉前的准备工序,有块状烧结和球团状烧结两种。
烧结工序能耗在钢铁企业中仅次于炼铁而居第二位,在烧结总能耗中,冷却机废气带走的显热约占总能耗的20~28%,而其排放的余热约占总能耗热能的49%,回收和利用这些余热,显然极为重要。
余热回收主要在烧结矿成品显热及冷却机的排气显热两个方面。
目前余热回收技术主要应用在冷却机的排气显热回收上。
烧结机生产时,热烧结矿经过滑车在轨道上移动,通过鼓风机吹风,使冷却风强制穿过料矿层,经料矿加热后,冷却风温一般温度可达300~400℃,最高可达450℃左右。
这部分的冷却风都可以利用其余热。
烧结主抽烟道内的高温段废气热量回收有很大潜力,机尾处烟箱的平均温度为380-420℃(实测温度),流量为80000Nm3/h,采用热管式蒸汽回收装置回收烟气余热,在主抽烟道余热回收段加旁通管及阀门保证大烟道内排烟温度不低于130℃(露点温度以上)。
钢铁厂烧结主抽烟道余热回收工程实践_杜蒙

钢铁厂烧结主抽烟道余热回收工程实践杜蒙王辉王丽丽李鹏元徐永权(中钢集团鞍山热能研究院有限公司)摘要介绍了福建三钢180m2烧结机主抽烟道余热回收的工艺流程、实际应用、遇到的问题、解决办法及经济评价,为今后烧结主抽烟道余热回收提供了经验。
关键词烧结主抽烟道余热回收热管Engineering practice of sintering main flue gas waste heat recoveryin steel factoryDu Meng Wang Hui Wang Lili Li Pengyuan Xu Yongquan(Sinosteel AnshanResearch Institute of Thermo-Energy Co.,Ltd.)Abstract The technological process of sintering main flue gas waste heat recovery,practical applica-tion,problems in the application and solutions,and economic evaluation of application in Fujian San-ming steel180m2sintering machine were introduced,and the experience was provided for the future sintering main flue gas waste heat recovery.Keywords sintering main flue waste heat recovery heat pipe多年以来,国内外对烧结余热的回收利用进行了大量的研究。
烧结过程中可供利用的余热占钢铁厂总能耗的12%,其中烧结矿的余热占8%,烧结废气余热占4%。
烧结冷却机余热利用现在已经被普遍采用,而烧结机主抽烟道废气的余热利用也逐渐被重视起来。
烧结主排烟气减排与余热高效回收技术

果 ,并对 国内烧结主排烟气减排与余热 高效 回收提 出了建议 。 关键词
Te h l g e f e s i n r d to nd f ce twa t e tr c v r c no o is o miso e uc i n a e i in seh a e o e y
得 了 良好 的效果 。
烧结 主排烟气 和冷却 机废 气都 属 于中 、低 温
热 源 。 烧 结 主 排 烟 气 平 均 温 度 一 般 不 超 过 l0 ,其 中机 尾风 箱 排 出 的 烟气 温 度 为 30~ 5℃ 0
收 稿 日期 : 1 —0 2 2 1 4— 7 0 毛艳丽( 98一 ) 工程师 ;10 9 辽宁省鞍山市 16 , 14 0
19 94年此技术 于荷兰 克鲁斯 艾 默伊登 厂 的 3 l号
( 3 m )烧 结机 首 次应 用 ,之后 推 广 到 该 厂 的 12 2
高 ,冷强度 稍降低 ,平 均粒 度 约 1m 7 m,烧 结 机 焦粉 消耗 从 6 k/ 降 低 到 4 k/。艾 默 伊 登 厂 0 gt 8 gt
o i t r wa t a fsn e s e g s
Ma a l Z agD n l Q uig o ni hn o gi uY l Y n
( nte T cn lg e t ) A s l eh o yC ne e o r
A s at T ema rn uta sltn n e pl a o sl r msi d co dei bt c h j ds i o i s dt i api t nr usf i o r ut na f・ r oi rl uo a h r ci e t o e sn e i n l
烧结工序余热回收与烟气脱硫结合的研究

烧结工序余热回收与烟气脱硫结合
的研究
烧结工序余热回收与烟气脱硫结合的研究是一项重要的研究内容,近年来在能源利用和环境保护方面得到了广泛的关注。
烧结工序中产生的大量热量,是一种高效的、可再生的能源,但是这种能源也会产生可致癌物质烟尘等有害物质,为了减少这些有害物质对环境的污染,就必须实施有效的脱硫技术来达到脱硫的目的。
烧结工序余热回收与烟气脱硫结合的研究,即将烧结工序中的余热回收与烟气脱硫技术结合起来。
首先,要发挥烟气脱硫厂的最大效率,将余热回收的温度作为烟气脱硫的补充温度,以达到充分利用烟气脱硫的效率。
其次,要实现余热回收系统的节能,将有效地利用烟气脱硫后的热量,使其成为可以被烧结加工利用的源头。
烧结工序余热回收与烟气脱硫结合的研究,可以通过烧结设备的改造来实现。
将烧结炉的热量通过热量回收装置回收,并将烟气通过烟气脱硫装置进行脱硫处理,使烟气排放达到环保标准。
此外,还可以将脱硫后的烟气送入被加热的热风炉中,以便将热量释放出来,以替代部分燃料,以达到节能的目的。
烧结工序余热回收与烟气脱硫结合的研究,不仅可以有效地节省能源,减少污染,而且还可以提高烧结加工的生产效率,降低生产成本,从而获得双重好处。
因此,这项研究具有重要的意义,可以为烧结行业的发展和环境保护提供有效的技术支持。
烧结余热回收利用
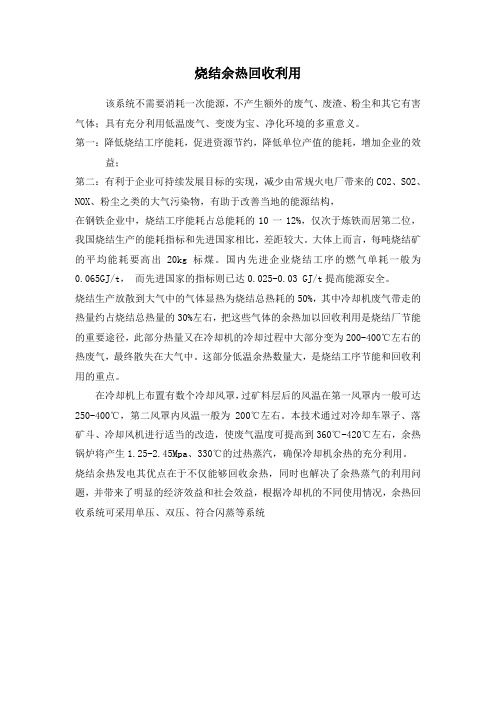
烧结余热回收利用该系统不需要消耗一次能源,不产生额外的废气、废渣、粉尘和其它有害气体;具有充分利用低温废气、变废为宝、净化环境的多重意义。
第一:降低烧结工序能耗,促进资源节约,降低单位产值的能耗,增加企业的效益;第二:有利于企业可持续发展目标的实现,减少由常规火电厂带来的CO2、SO2、NOX、粉尘之类的大气污染物,有助于改善当地的能源结构,在钢铁企业中,烧结工序能耗占总能耗的10一12%,仅次于炼铁而居第二位,我国烧结生产的能耗指标和先进国家相比,差距较大。
大体上而言,每吨烧结矿的平均能耗要高出20kg标煤。
国内先进企业烧结工序的燃气单耗一般为0.065GJ/t,而先进国家的指标则已达0.025-0.03 GJ/t提高能源安全。
烧结生产放散到大气中的气体显热为烧结总热耗的50%,其中冷却机废气带走的热量约占烧结总热量的30%左右,把这些气体的余热加以回收利用是烧结厂节能的重要途径,此部分热量又在冷却机的冷却过程中大部分变为200-400℃左右的热废气,最终散失在大气中。
这部分低温余热数量大,是烧结工序节能和回收利用的重点。
在冷却机上布置有数个冷却风罩,过矿料层后的风温在第一风罩内一般可达250-400℃,第二风罩内风温一般为200℃左右。
本技术通过对冷却车罩子、落矿斗、冷却风机进行适当的改造,使废气温度可提高到360℃-420℃左右,余热锅炉将产生1.25-2.45Mpa、330℃的过热蒸汽,确保冷却机余热的充分利用。
烧结余热发电其优点在于不仅能够回收余热,同时也解决了余热蒸气的利用问题,并带来了明显的经济效益和社会效益,根据冷却机的不同使用情况,余热回收系统可采用单压、双压、符合闪蒸等系统单压系统采用单级进汽汽轮机及单压烧结余热锅炉的单压不补汽系统。
一般余热锅炉排气温度在170℃,排气用于烘干物料。
复合闪蒸单级补汽系统采用补汽式汽轮机的复合闪蒸单级补汽系统,烧结余热锅炉生产主蒸汽同时生产高温热水,高温热水再降压蒸发双压系统采用补汽式汽轮机的双压单级补汽系统,烧结余热锅炉生产两个不同的蒸汽,一为主蒸汽,另一个为低压补汽。
烧结机大烟道余热回收项目设计总结

烧结机大烟道余热回收项目设计总结烧结机大烟道余热回收项目设计总结一、引言随着工业化进程的加快,能源消耗成为制约可持续发展的重要因素之一。
对于钢铁行业来说,烧结机大烟道产生的废热是一种值得回收利用的高温能源。
本项目旨在设计一套科学高效的烧结机大烟道余热回收系统,以降低能耗,减少环境污染,提高能源利用率。
二、项目概述本项目针对某钢铁企业的烧结机大烟道进行余热回收设计。
通过在烟道上设置余热回收装置,将高温烟气中的余热转化为其它形式的能源,如热水或蒸汽,用于企业内部的供热和供电。
该项目具有较高的技术难度和经济价值,可有效减少环境污染和能源消耗。
三、设计思路3.1 烟道热源分析:通过对烧结机大烟道的烟气温度、烟气流量和烟气组分等进行测试分析,确定烟道的热源条件和参数。
3.2 余热回收方式选择:根据烟道特点和热源参数,选择合适的余热回收方式。
本项目采用了烟尘热交换器和燃气锅炉两种方式,分别回收烟气中的热量。
3.3 设备选型和布置:根据热源参数和回收方式,对烟尘热交换器和燃气锅炉进行选型和布置设计。
同时,考虑到设备之间的热能耦合和烟气清洁处理,合理设置管道和控制装置。
3.4 系统集成与自动控制:将烟道余热回收系统与原有的供热和供电系统进行集成,实现自动化控制和优化运行。
通过构建数据监测和分析系统,实时监测余热回收效果,调整系统参数,提高能源利用效率。
四、技术难点4.1 热源分析准确性问题:烟道热源参数的准确测量是技术难点之一。
通过使用高精度仪器和仪表,对烟气温度、流量和组分进行准确测量,解决了该问题。
4.2 烟尘热交换器结构设计问题:烟尘热交换器的结构设计需要兼顾换热效果和清洁处理的要求。
通过优化换热器的内部结构,增加清洁设备,有效解决了烟尘的问题。
5、技术经济性分析本项目采用了先进的烟尘热交换技术和燃气锅炉技术,成功实现烟道余热的有效回收利用,起到了显著的节能减排效果。
根据经济分析和效益评估,该项目在短期内即可收回投资成本,并可长期稳定运行,实现可持续发展。
烧结机大烟道外置式烟气余热回收工程实践

护环境的作用。本文对烧结大烟道外置式余热回收技术在 360 ㎡烧结机上的应用进行了分析,并深入的研究了大烟道余热回收
时无法达到产能的外置式锅炉,在经过实践验证后,本文对解决这一难题的良好方案进行了提出,以供参考。
关键词 :烧结机 ;烟气余热利用 ;大烟道
中图分类号 :TF046.4
文献标识码 :A
文章编号 :11-5004(2021)04-0227-2
3~5 个风箱内,向同一取风管道内引入即可,在烟道上通过对 单个取风管道的引出,能够由取风管道线输送到沉降室中进行 除尘处理,然后用于外置式锅炉内部进行余热换热,高温烟气 在经过锅炉的余热换热后,会再次向大烟道前半部分输送,余 热回收阶段所应用的外置式烧结机中,并没有对增压风机进行 设置。此类方式不仅减少了引风机所需消耗的电能,并且由于 外置式锅炉在整个余热回收阶段的阻力低于 600Pa,因此,无需 对引风机进行设置,避免了磨损引风机,此类方式被应用到了 大部分工程中 [1]。
工期通常为 30 d
较少运用,但通常产能无法 大规模运用,能够达到较高
满足设计要求
的产能
227
Copyright©博看网 . All Rights Reserved.
M 管理及其他 anagement and other
2 工程实例 2.1 设计工艺流程
某钢铁厂在结合以上问题后,在大烟道余热回收阶段,提出 了具有实用性、创新性的一种新兴的烧结大烟道外置式余热锅 炉系统。从工艺和原理方面,通过与烧结生产的结合,决定采用 多点式进行取烟,各支路上所设置的开度阀门为可调节型的,此 类方式能够从温度和烟气量方面,有效的对进口处的烟气进行 调节和控制,并且不会对正常烧结造成影响 [2]。
要定时进行激波清灰
烟气余热回收专题总结汇报

烟气余热回收专题总结汇报烟气余热回收是一种能源利用技术,将工业生产过程中产生的高温烟气中的余热进行回收再利用,能够有效降低能源消耗和环境污染,具有重要的经济和环境效益。
本文将对烟气余热回收的原理、技术、应用和前景进行总结和汇报。
一、烟气余热回收的原理烟气余热回收的原理主要是利用换热器将高温烟气中的热能传递给介质,实现能量的转移和利用。
烟气余热回收系统通常包括烟气源、热交换装置、介质流动系统和热能利用设备。
烟气经过烟气源后进入热交换装置,通过换热器将烟气中的热能传递给介质,再经过介质流动系统传递给热能利用设备进行能量的利用。
二、烟气余热回收的技术烟气余热回收技术主要包括烟气换热器、燃气余热锅炉、直接排烟余热利用和间接排烟余热利用。
其中,烟气换热器是最常用和成熟的烟气余热回收技术,通过将高温烟气中的热能传递给介质,实现能量的利用。
燃气余热锅炉是将余热回收利用于锅炉的烧烤和加热过程中,可以大幅降低燃料消耗和环境污染。
直接排烟余热利用是将余热直接用于生产过程中,如加热水和蒸汽等。
间接排烟余热利用是将余热用于其他过程中,如发电和冷却等。
这些技术能够有效地回收烟气中的余热,提高能源利用效率。
三、烟气余热回收的应用烟气余热回收技术广泛应用于各个行业,如钢铁、化工、电力、纺织等。
在钢铁行业,烟气余热回收可以用于加热水和发电等;在化工行业,烟气余热回收可以用于蒸汽产生、工艺加热等;在电力行业,烟气余热回收可以用于发电和供热等;在纺织行业,烟气余热回收可以用于蒸汽产生和加热水等。
烟气余热回收技术的应用可以有效降低能源消耗和环境污染,提高能源利用效率,具有很大的应用前景。
四、烟气余热回收的前景随着环境保护意识的增强和能源消耗的增加,烟气余热回收技术将越来越受到重视和广泛应用。
烟气余热回收技术可以有效降低能源消耗和环境污染,提高能源利用效率,具有很大的经济和环境效益。
未来,随着技术的不断发展和创新,烟气余热回收技术将进一步完善和推广,成为重要的能源利用技术之一。
烧结余热回收发电浅谈

烧结余热回收发电浅谈耿乃弟一、我国钢铁企业的能耗状况钢铁生产消耗大量的能源和载能工质, 其能耗占我国国民经济总能耗的10%左右。
成本中能源费用占有相当大的比重, 钢铁联合企业中这一比重已达到30%,甚至更高。
日本钢铁工业的吨钢能耗维持在0.65tce左右。
我国74家大中型钢铁企业的吨钢能耗为0.80tce,与日本相比差约0.15tce。
我国能耗最低的宝钢的吨钢能耗与日本相比也有约50kgce的差距。
我国能源消耗高的原因虽然很多, 企业规模小是一个很重要的原因。
我国重点大中型企业(进入统计范围内) 74 家钢产量占全国的90% ,而日本5大钢铁企业的钢产量占日本的70%以上。
由于装备小,一些节能效果显着,但投资大,投资回收期长的节能措施无法实施。
例如:日本干熄焦、高炉TRT、转炉煤气回收的普及率100%。
我国的干熄焦装置只有17套,年处理焦炭480万t,占我国机焦产量的4%。
TRT只在大高炉有少量装置。
二、钢铁企业余热余能资源情况钢铁企业余热余能的范围包括焦化、烧结/球团、炼铁、炼钢及轧钢等主要生产工序,各主要生产工序的余热余能参数大致如下:1、焦化工序的钢比系数为0.404t(焦)/(t钢);焦炉煤气产生量为410m3/(t 焦);红焦温度为1000℃,上升管焦炉煤气温度为700℃,焦炉烟气温度为200℃;2、烧结工序的钢比系数为1.44t(矿)/(t钢);机尾烧结矿温度为800℃,烧结烟气温度为300℃;球团工序的钢比系数为0.25t(矿)/(t钢),球团矿排出温度为500℃;3、炼铁工序的钢比系数为0.91t(铁)/(t钢);高炉渣产量为320t(渣)/(t 铁),液态高炉渣温度为1500℃;高炉煤气发生量为1650m3/t(铁),高炉煤气热值为3350kJ/m3,炉顶高炉煤气温度为200℃;高炉冷却水平均温度为40℃;热风炉排烟温度为500℃;4、炼钢工序转炉钢比系数为0.84t(钢)/(t钢),电炉钢比系数为0.16t(钢)/(t钢);连铸比为100%;连铸坯温度为900℃;钢渣温度为1550℃;转炉煤气产生量为115m3/(t钢),热值为8370kJ/m3,烟罩处转炉煤气温度为1600℃;电炉炉顶排放口烟气温度为1200℃;5、轧钢工序钢比系数为0.92t(材)/(t钢);加热炉炉尾或入蓄热式烧嘴烟气平均温度为900℃;加热炉汽化冷却蒸汽压力为1.5MPa,温度为200℃;基于以上参数,我国钢铁工业吨钢余热余能资源总量为0.455tce/(t钢),各工序所占比例见下图。
烧结大烟道余热回收设备工艺原理

烧结大烟道余热回收设备工艺原理引言伴随着工业化进程的不断加快,工业排放的大量烟尘和高温废气对人类的生存环境造成了很大的危害。
为了减轻环境负担,提升资源利用效率,烧结大烟道余热回收设备逐渐受到广泛关注。
本文将就此设备的原理及其重要性进行详细探讨。
烧结大烟道余热回收设备的定义大烟道排放的烟气温度一般在1000℃左右,所含热量是废气中有机物可燃部分和无机物热辐射吸收的热量。
烧结大烟道余热回收设备利用这一热源,通过热交换,将废气中的热量转移至其他工艺流体,从而实现能量回收和资源利用。
设备组成烧结大烟道余热回收设备主要由余热烟道、余热锅炉、余热水箱、余热回收装置和自控系统组成。
其中,余热烟道是流经余热回收装置的废气通道;余热锅炉的作用是将经过余热回收装置的热水、蒸汽或气体加热至一定温度;余热水箱是储存余热水的设备;余热回收装置是实现废气余热回收的核心设备;自控系统是设备的智能控制中心,实现设备运行的自动化和安全性控制。
烧结大烟道余热回收设备的工艺原理主要包括废气预处理、热回收和余热利用。
在每个步骤中,有必要采用科学的技术措施,以保证设备的稳定性和效率。
1. 废气预处理烧结大烟道排放出的废气含有很高的水分和烟尘等有害物质,对设备正常运行及其余热回收产生不利影响。
因此,为了减少废气的污染物质,需要先对废气进行预处理。
这个过程中可以采用干燥和除尘装置,将废气的温度降低到可以处理的范围内,并去除其中的烟尘和杂质。
2. 热回收废气进入余热回收装置之后,通过导热、对流和辐射等多种方式,将烟气中的热量传递给热介质,以获得所需的热量。
热介质可以是流体、气体或蒸汽等,在传递热量的过程中,需要适当控制热介质流速和传热面积大小,以实现较高的热回收效率。
3. 余热利用热介质在获得热量之后,即可利用余热锅炉进一步提取能量。
通过余热锅炉将热介质加热,使其达到蒸汽或热水的有效温度,进而与其他工艺流体进行热交换。
这样就可以将大烟道排放的废气中的热能重新利用起来,减少能源浪费,提高能源利用效率。
烟道中的余热回收设备有什么作用

烟道中的余热回收设备有什么作用
说起余热回收,可能很多人还不是很熟悉,如果是生活在北方的农村,那对利用余热的原理就很熟悉了。
北方村里通常是睡火炕,屋里有火炉子,其实就是用高温烟气来将土炕进行加热。
在工业中,烟道内烟气的温度也会很高。
热管余热回收器,专用于烟气管道中的余热回收设备,是一种节能减排的换热设备。
热管换热器安装在锅炉的烟道口处,当高温烟气经过换热器时,烟气的热量通过换热器与相对低温的新风进行热量交换,以达到技能的目的。
工业生产中,锅炉是能源消耗的主要源头,据统计,在印染、烘干、各类制造业中,锅炉所排出的烟气占能耗的15%甚至更多。
热管余热回收器是将烟气中含有的热量与其他介质(如水、气等)进行换热,转换为可再利用的热量。
热管余热回收器的工作原理也不复杂,利用热管的快速热传递原理,来进行工作的。
热管余热回收设备主要作用有两点:
一、提高热效率:锅炉的有效热效率通常在85%以上,烟气是热量损失的主要场所。
在尾部安装余热回收器,可有效提高锅炉热效率,减少热量损失,大幅度降低排烟温度,减少热污染。
二、减少二氧化碳排放:锅炉排烟的主要成分是二氧化碳、二氧化硫、氮气、一氧化碳以及各种混合物。
安装热管余热回收设备后,通过余热回收再利用,可以增加企业的经济效益和社会效益,在回收余热资源的同时节约能源,促进经济的可持续发展。
烟道尾部余热回收技术在有机热载体锅炉节能降耗中的应用

烟道尾部余热回收技术在有机热载体锅炉节能降耗中的应用摘要:本文浅析了有机热载体炉能耗偏高问题的主要成因,针对某企业有机热载体锅炉尾部加装烟气余热回收装置,分析了余热回收技术在提高有机热载体锅炉效率方面所起到的积极意义。
关键词:锅炉;节能;应用0 引言有机热载体炉因具有“高温低压”(常压或较低压力时出口温度就可达300℃)、安全、高效等特点,且供热温度可以精确控制,能够满足中小型企业的生产需求,在我县得到了广泛使用。
虽然其优点很多,但在节能降耗方面还有挖掘的潜力,本文对此类设备的节能现状进行了分析,并实际检验了余热回收技术在节能降耗中的作用。
1 有机热载体锅炉能耗状况1.1 排烟温度偏高导致排烟热损失过大热量传递方式有热传导、热辐射、热对流3种,我们的有机热载体锅炉主要是通过辐射和对流受热来提高锅炉温度,缺少蒸汽锅炉前后管板烟气辐射和管束对流辐射,相比之下受热面和受热路径就显得小很多,相当一部分的火焰及烟气直排大气,排烟温度高达200℃以上,导致排烟热损失过大。
1.2 油汽共存现象导致浪费能源《有机热载体炉安全技术监察规程》第30条规定:“有机热载体必须经过脱水后方可使用”,这是因为新加油、换油或者维修过程中容易混入水分,所以一般锅炉加入热载体后要进行脱水操作,当油温升至110℃以上时,水分被汽化,且汽化量随温度升高不断增加,当高位油槽放空阀大量排气时,还会出向喷油,此时往往会紧急关闭放空阀,导致脱水不净,产生气阻现象,影响热载体循环流量的稳定,浪费能源。
1.3 停炉不规范导致热损耗增加停炉时未能做到炉停泵转,造成了热油自然冷却在系统内,当下次继续使用时,因系统管壁有较厚的油膜,人为的缩小的系统管径,这样,不但增加了循环泵的阻力,同时也影响了传热,而且还损耗了可用热载体。
1.4 缺少保温措施导致散热损失增加有不少单位出于经济成本的考虑,锅炉或者管道不进行保温措施处理,导致大量热能的散失。
还有一些单位不能及时对锅炉受热面的积灰进行清理,影响了传热,导致出口温度偏低,供热不足,浪费了燃料。
热电厂烟道气余热回收利用分析与措施研究

热电厂烟道气余热回收利用分析与措施研究热电厂烟道气余热回收利用是当前能源领域中热能回收利用的重要方向之一、烟道气是指燃烧过程中的烟尘和烟气,对环境造成污染,同时也含有大量的热能。
合理利用烟道气余热,可以提高能源利用效率,减少环境污染,具有重要的经济和环境效益。
烟道气余热回收利用主要包括以下几方面内容:1.烟气换热器的应用:通过在烟道中设置烟气换热器,将烟气中的热量传递给工艺用水或者空调用水,实现能源的重复利用。
同时通过调整换热器的结构和材料,提高换热器的热效率和寿命,降低能源消耗。
2.燃气脱硫过程中的余热回收:燃气脱硫是热电厂烟气处理的一项重要工艺。
在燃气脱硫过程中,大量的热能被消耗。
可以通过在脱硫系统中设置余热回收装置,将脱硫过程中释放的热能用于燃烧系统或者其他工艺的供热。
3.烟尘处理中的余热回收:烟尘处理是热电厂烟气处理的关键环节之一、在烟尘处理过程中,可以通过采用余热回收技术将烟道气中的热能回收,用于加热水、蒸汽或者其他工艺的供热。
这不仅可以提高能源利用效率,还可以减少烟尘对环境的影响。
4.余热利用系统的建设:热电厂烟道气余热回收利用需要建立完善的余热利用系统。
这包括烟气换热器、余热回收装置、余热供应系统等设备的选型、设计和安装。
同时还需要制定合理的操作管理措施,确保余热利用系统的正常运行。
在研究烟道气余热回收利用的措施时,需要综合考虑烟道气的温度、流量、成分、含尘量等因素。
同时还需要考虑烟道气回收利用系统与燃烧系统之间的协调性和一体化设计,以最大限度地提高能源利用效率和经济效益。
值得注意的是,烟道气余热回收利用不仅可以提高能源利用效率,还可以减少环境污染。
通过减少烟气中的污染物排放,可以改善空气质量,保护环境和人民健康。
总之,热电厂烟道气余热回收利用是一项技术含量较高的工作,需要从燃烧炉选型、燃烧工艺优化、余热回收系统设计等多个方面进行研究和改进。
通过合理利用烟道气的余热,既可以提高能源利用效率,又可以减少环境污染,有着重要的经济和环境效益。
首钢烧结厂烟道气的余热利用

!
首先在一烧 ’ 号机上安装了一 #--0 年 & 月, 套余热回收系统。该系统由软化水站 (负责汽包 软化 水 的 生 产 制 备 和 向 热 管 换 热 器 供 水) 及泵 房、 热管蒸汽换热器、 蒸汽过热器等三部分组成 (见图 #) 。其工艺流程为: 软化水站 ! 软水箱 ! 热管换热器!汽包 ! 蒸汽过热器 ! 二次混合机。
*345 #67834 9: 4; * ’<=:>4?: ;) <=>=)- & ?=2<@,-.= ABC -=%D=<2-E<= <=@(FE2A .=2- BG =H-=)F=F @()-=< %2>.()= C2@ <=>BI=<=F GB< D<BFE>-(), @-=2% J? E@K
(), -.= .=2- D(D= -=>.)BAB,? () L.BE,2), @()-=<(), DA2)-* M@ 2 <=@EA-,-.= DE<DB@= BG @=AG : @EDDB<-(), @-=2% C2@ <=2A(N=F 2)F -.= BJI(BE@ J=)=G(- C2@ BJ-2()=F* @9A BC>D= <=@(FE2A .=2- <=>BI=<?,.=2- D(D= =H>.2),=<,@-=2% .=2-(), %(H
首钢烧结厂 + 套余热回收装置的建成投产, 均为一次试车成功,运行效果良好。此项技术设 计注重发挥热管换热器高效换热的性能,结合 机上冷却烧结工艺的特点,节能效果及经济效 果显著,且投资少,见效快,安全可靠,特别适 用于旧厂改造。
- 1、下载文档前请自行甄别文档内容的完整性,平台不提供额外的编辑、内容补充、找答案等附加服务。
- 2、"仅部分预览"的文档,不可在线预览部分如存在完整性等问题,可反馈申请退款(可完整预览的文档不适用该条件!)。
- 3、如文档侵犯您的权益,请联系客服反馈,我们会尽快为您处理(人工客服工作时间:9:00-18:30)。
烧结烟道余热回收工程技术方案书天津华能能源设备有限公司二○一三年五月一、总述1. 项目实施企业简介用户提供2. 设计依据××××××,提供336㎡烧结大烟道余热锅的设计依据。
3. 设计原则采用已有的成熟技术,注重技术的适用性、可靠性、经济性和先进性,工艺技术及装备水平达到国内先进水平;设备选型原则:设备以国产化为主,尽量考虑设备的大型化;布置原则:考虑未来发展,合理使用场地,工艺布置和物料流程合理、通畅,尽量避免各工序间的相互干扰;整套系统工程的设计符合国家标准。
4. 主要设计内容余热回收系统:余热锅炉系统、给水系统、除尘系统、烟道系统、控制系统;5. 设计概要利用烧结主抽烟道内的高温段废气进行余热回收。
二、系统设计方案1、工程概述钢铁冶金企业是国家支柱产业,在现代化建设中起着重要作用,同时这些企业也是耗能大户,能耗占产品成本比例较大。
因此企业的节能降耗显得尤其重要。
烧结工序是高炉矿料入炉前的准备工序,有块状烧结和球团状烧结两种。
烧结工序能耗在钢铁企业中仅次于炼铁而居第二位,在烧结总能耗中,冷却机废气带走的显热约占总能耗的20~28%,而其排放的余热约占总能耗热能的49%,回收和利用这些余热,显然极为重要。
余热回收主要在烧结矿成品显热及冷却机的排气显热两个方面。
目前余热回收技术主要应用在冷却机的排气显热回收上。
烧结机生产时,热烧结矿经过滑车在轨道上移动,通过鼓风机吹风,使冷却风强制穿过料矿层,经料矿加热后,冷却风温一般温度可达300~400℃,最高可达450℃左右。
这部分的冷却风都可以利用其余热。
烧结主抽烟道内的高温段废气热量回收有很大潜力,机尾处烟箱的平均温度为380-420℃(实测温度),流量为80000Nm3/h,采用热管式蒸汽回收装置回收烟气余热,在主抽烟道余热回收段加旁通管及阀门保证大烟道内排烟温度不低于130℃(露点温度以上)。
2、工程项目基础参数、自然条件地震烈度:本地区地震基本烈度为7度,加速度值0.05g,建筑场地类别II类。
风荷载:m2(n=50) 雪荷载 m2(n=50)、气候条件:(1)用户提供当地气候条件(2)、设计原始条件及要求一座144m2两座,设计参数按相同考虑,由于本工程为改造工程,空间狭窄,余热锅炉的外形尺寸设计要紧凑。
a、烟气参数①、烟气特性a、烟气量工况波动按20%考虑。
b、烟气成份:N2、O2、H2O,其中N2占78%,O2占21%,H2O占1%,烟气含灰量为1g/ Nm3。
成分为铁矿石烧结熟料,粒径为100μm。
②、蒸汽品质钠≤15μg/kg二氧化硅≤20μg/kg③、所提供软化水水质参数:锅炉给水、锅水质量标准执行《工业锅炉水质》(GB/T1576-2008)中有关规定。
锅炉正常连续排污率:≤2%硬度:≤3μe/L油:<1mg/L 铁:≤50μg/L铜:≤10μg/L 钠:≤15μg/kgSiO2:≤20μg/kg PH值:~④、电源动力电源:±7%/380V±15% VAC直流电源:220V/24V VDC3、设计要求及区域范围、设计要求3.1.1主要执行标准及规范《污水综合排放标准》(GB8978-1996)《工业企业厂界噪声标准》(GB12348-90)《钢结构设计规范》(GB50017-2003)《建筑地基基础设计规范》(GB50007-2002)《低压配电装置规范》(GB50054-95)《通用用电设备配电设计规范》(GB50055-93)《建筑物防雷设计规范》(GB50057-94)《钢制化工容器结构设计规范》(HG20583-1998)《化工装置设备布置设计工程规定》()《钢制化工容器设计基础规定》(HG20580-1998)《钢制低温压力容器技术规定》(HG20585-1998)《钢制立式圆筒形固定顶储罐系列》()《化工设备基础设计规定》(HGT20643-1998)《化工装置管道机械专业提出的设计条件》()《钢制有缝对焊管件》(HGT21631-1990)《钢制压力容器》(GB150-1998)3.1.2项目设计指标烧结大烟道余热回收系统蒸汽总产量为10t/h、、350℃,蒸汽全部进入公司蒸汽管网。
此数据为保守值,当烟气量增多或烟气温度增高时。
蒸汽量会相应增加;当烟气减少或温度降低时,蒸汽量会相应减少。
3.1.3项目设计原则结合用户现场状况及项目设计目标,采取系统安全,技术先进、工艺可靠、经济合理的设计原则确定本项目的建设方案。
3.1.4系统安全a、系统设计时,通过科学计算,确保生产系统正常运行;b、烟气温度在蒸发器内放热后,烟气温度降低到200度以上,保证后续设备不受腐蚀。
3.1.5工艺可靠系统通过省煤器、蒸发器等设备组合、系统控制部分,使烟气余热得到最大限度的利用,确保蒸汽蒸发量的稳定可靠。
整个系统工艺设计、施工严谨、紧密可靠。
、设计区域范围1、烟气系统:从烧结烟道取口处阀门开始,至循环烟道进口阀门止(含阀门、膨胀节、除尘器、余热回收装置、烟道等);2、汽水系统:由界区内除氧水系统的进水口开始至汽包出口法兰(含阀门);3、钢构:余热回收装置本体钢架的设计制作;4、其它:负责余热回收界区内的电气自动控制系统;5、土建基础施工;6、运输、安装、调试及人员培训。
4、余热回收工艺系统、工艺组成根据现场情况,余热锅炉可采用卧式结构或立式结构。
工艺上采用单压自然循环余热回收系统,利用烟气余热产蒸汽,实现余热回收。
系统由蒸汽发生器、省煤器、汽包、上升管、下降管、汽水管路、除氧器、电控系统、钢架等组成。
、工艺流程烟气系统流程:来自烧结大烟道的混合烟气380℃--420℃(1区20#--380℃,2区21#--400℃,3区22#--420℃)左右,先经蒸发器、在进入省煤器,烟气温度降到200℃左右从余热锅炉下部排出,经原进风管道,经烟道连接实现烟气余热利用。
水汽系统流程:外来104℃的除氧水,经水给泵补入省煤器后进入蒸汽聚集器,然后通过下降管进入低压蒸汽发生器,吸收烟气中的热量后形成汽水混合物通过上升管进入蒸汽聚集器;在蒸汽聚集器内蒸汽与水分离产生过热蒸汽外输用于生产。
如工艺流程图(另附):、余热锅炉辅助系统疏放水系统--锅炉本体范围内的各设备、管道的最低点设置疏、放水点,确保各下降管、省煤器、蒸发器等的进出口联箱疏、放水的畅通。
放汽系统--在系统的最高点,设置放气点,当上水和启动时,排去锅炉内空气和不凝结气体。
排污系统--在汽包的盐段设连续排污,在水系统的下联箱设定期排污,排去适量的锅炉污水以确保蒸汽品质。
在锅炉下部配置的定期排污扩容器。
事故放水--当锅炉汽包水位高于紧急水位时,打开电动事故放水阀,防止汽包满水。
蒸汽放散--当设备故障时,中蒸汽能够通过锅炉的集汽箱实现紧急快速放散蒸汽。
紧急放散系统和安全阀的排汽配置消音器。
汽水取样系统—系统配置汽水取样分析装置。
包括取样口至取样冷却器间管道、阀门等以及汽水取样器。
汽水组合式取样系统包括以下几点:给水取样:PH值、电导率、O2低压炉水取样:PH值、磷酸根、电导率中压炉水取样:PH值、磷酸根、电导率低压过热蒸汽取样:电导率、SiO2给水系统—系统设置了中、低压和除氧给水系统,由电动给水泵完成。
5、余热回收系统的设计、系统型式采用单压、自然循环余热回收系统。
利用烧结烟气余热产生蒸汽,实现余热回收。
、余热回收系统组成本系统是该项目中的核心部分余热回收产出、350℃过热蒸汽并入管网。
由蒸发器、省煤器、汽包、以及上升管、下降管。
设备辅助系统包括汽水管路、除氧器(含内件)、定排、连排、取样、加药、水泵、仪表系统、钢架等组成。
余热回收设备集中放置,设备顶部平台上设置一台汽包,并设置除氧器。
、余热锅炉系统设计5.3.1锅炉烟气进口至出口,烟气阻力小于1000Pa。
5.3.2系统正常排污量不超过锅炉给水流量的3~5%。
5.3.3锅炉疏放水系统确保能在一小时内将整台锅炉的水以重力放空。
5.3.4管道、阀门及附件的设计压力和设计温度的确定符合标准规范有关规定。
5.3.5负责提供锅炉与其它设备之间的接口设计,并提供锅炉接口清单表。
5.3.6锅炉设有水压试验接口,提供试验方法和详细说明(包括试验用水的水质和水温)。
5.3.7供测量烟道及余热锅炉本体各段温度的测量元件。
5.3.8在符合设计条件及正常投运时,保证达到以下运行性能:①、锅炉在设计工况参数下能达到额定值。
并保证长期安全运行,所有附件及配供的测控设备均能正常投运。
②、主蒸汽额定汽温偏差为±5℃,在可能运行的条件工况下,各段受热面的金属壁温都在允许范围之内。
③、确保锅炉从启动到最大连续负荷范围内,水循环安全可靠。
④、锅炉露天布置,采取可靠的防雨,避雷措施。
⑤、锅炉设计在定压运行下有良好的对负荷变动的适应性,在变负荷运行时,锅炉应有足够的安全可靠性,以适应系统或控制装置在运行中产生的偏差。
⑥、锅炉设计有有效的停炉保护措施,并提供有关设备及系统。
、系统计算产出的热工性能参数(单套)6烟气循环系统管路6.1.1、烟道部分包括:热烟气管道、余热锅炉过渡烟道、余热锅炉烟气通道、余热锅炉出口烟道、低温烟气管道。
热烟气管道、低温烟气管道和余热锅炉出口烟道均采用钢制密封壳体形式,采用外部保温结构,保温层外部设置彩钢板保护层。
余热锅炉过渡烟道、余热锅炉烟气通道采用外加强-内保温的一体化护板结构,由内衬钢板、绝热层、外壳体以及支撑钢结构组成。
内衬板为搭接结构,可以在热态下很好地吸收膨胀。
6.1.2、柔性膨胀节所有的膨胀接均采用非金属柔性膨胀节,用以吸收本系统热态运行时所产生的向上及向后的双向位移量,这种膨胀节具有万向补偿和避免产生由热膨胀引起的推力的功能,同时具有吸收膨胀量大、隔震、减噪、结构轻巧、自重轻等优点。
非金属柔性膨胀节的使用寿命为4年。
烟气管道阀门在烟气管道上设置电动翻板阀。
余热回收系统运行时,翻板阀打开,烟囱翻板阀关闭。
如果锅炉设备需要正常的检修或由于问题停车时,翻板阀关闭,烟囱翻板阀打开,烟气走烟囱,保证烧结正常生产。
阀门的选取与管道尺寸相符。
在阀门的选取上注意漏风率≤2%。
除尘器系统6.3.1主要设备及性能参数余热锅炉系统阻力≤1000Pa6.3.2 设备的主要特点余热回收装置余热回收装置是本项目的核心部分。
其主要由:蒸发器、省煤器、蒸汽聚集器、支架平台爬梯和设备附助系统等组成。
6.4.1蒸发器蒸发器为热管结构,螺旋翅片管受热面结构,分为两组,受热面立式或卧室布置。
蒸发器的集箱管均设置了定期排污管道阀门。
蒸发器为全疏水结构。
蒸发器置于烟气出口的高温烟道内。
6.4.2省煤器省煤器为热管结构,螺旋翅片管受热面结构,分为两组,受热面立式或卧室布置。