典型铸铁件铸造工艺设计
铸造成形技术铸造工艺设计

①选择铸件的浇注位置及分型面 ②型芯的数量、形状及其固定方法 ③确定工艺参数(加工余量、起模
斜度、圆角、 收缩率) ④浇冒口、冷铁形状、尺寸及其布
置
铸造工艺图——在零件图上用各种工艺 符号表示出铸造工艺方案的图形
它是制造模样和铸型,进行生产准备 和铸件检验的依据——基本工艺文件。
使型腔和主要芯位于下箱,便于下 芯、合型和检查型腔尺寸。
3.铸造工艺参数的确定
铸造工艺参数包括收缩余量、 加工余量、起模斜度、铸造圆角、 芯头、芯座等。
①收缩余量:
为了补偿收缩,模样比铸件图纸尺寸 增大的数值称收缩余量。收缩余量的大小 与铸件尺寸大小、结构的复杂程度和铸造 合金的线收缩率有关,常常以铸件线收缩 率表示:
工艺 打箱、清理等工艺操作 根据批量大小填写必要条
卡片 过程及要求
件
⑨ 综合整个设计内容
实例分析:
以C6140车 床进给箱体 为例分析毛 坯的铸造工 艺方案如下: 质量约35Kg。
车床进给箱体零件图
该零件没有特殊质量要求的表面, 仅要求尽量保证基准面D不得有明显 铸造缺陷,以便进行定位。
材料:灰铸铁HT150,勿需考虑补缩。
为了便于采用机器造型、尽量 避免活块,故凸台和凹槽均应 用型芯来形成。
为了克服基准面朝上的缺点, 必须加大D面的加工余量。
单件、小批量生产,采用手 工造型,使用活块造型较型芯 更为方便。同时,因铸件的尺 寸允许偏差较大,九个轴孔不 必铸出。
此外,应尽量降低上型高度, 以便利用现有砂箱。
显然,在单件生产条件下,宜 采用方案II或方案III。
在制订铸造工艺方案时,主要应着 眼于工艺上的简化。
1.分型面
三个方案供选择: 方案I:分型面在轴孔 的中心线上。 方案II:从基准面D分 型,铸件绝大部分位于 下型。 方案III:从B面分型, 铸件全部置于下型。
铸造工艺学课程设计案例

成果报告需以PDF格式提交,同时附上所有相关数据和图表。
报告内容
报告需包含设计思路、工艺流程、数据分析及结论等部分,要求 内容详实、逻辑清晰。
成果展示形式和内容安排建议
展示形式
鼓励采用多媒体形式进行展示,如PPT、视频等。
内容安排
建议按照设计背景、设计思路、工艺流程、数据 分析、结论与展望等顺序进行展示。
时间安排
每个小组展示时间不超过20分钟,需提前做好时 间规划。
课程设计评价标准及成绩评定方法
01
评价标准
将从设计创新性、实用性、技术 难度、报告质量等方面进行综合 评价。
02
成绩评定方法
03
优秀作品选拔
采用百分制评分,其中设计创新 性占30%、实用性占20%、技术 难度占20%、报告质量占30%。
铸造材料选择
根据零件使用要求、生产批量和成本 等因素,选择合适的铸造合金,如铸 铁、铸钢、铝合金等。
性能要求
铸造合金应具有良好的流动性、收缩 性、偏析倾向小等性能,以保证铸件 质量。同时,合金成分和性能应符合 相关标准或技术条件的规定。
03
案例分析:典型铸件生产工艺设计
铸件结构分析与设计优化建议
根据评分结果,选拔出优秀作品 进行表彰和奖励。
THANKS
感谢观看
推广新技术和新材料
积极推广先进的铸造技术和新材料,如3D打印技术、高性能铸造合 金等,提高铸件的精度和性能。
加强人才培养
加强铸造领域的人才培养和引进,提高从业人员的专业素质和技能水 平,为铸造行业的发展提供有力的人才保障。
06
课程设计成果展示与评价标准
课程设计成果提交要求说明
提交时间
所有成果需在课程结束前一周内提交,逾期将不予受理。
铸造工艺设计

36
对于内腔形状复杂的大铸件,常将形成内腔的型芯分割 成数块,使每块形状简单,尺寸较小,便于操作、搬运、 烘干,简化芯盒结构。
JMU College of Mechanical and Energy
31
(3)使型腔和主要型芯位于下箱,以便于造型、下 芯、合型和检查型腔尺寸。
图2-21_1 尽量使型腔及主要型芯位于下型
JMU College of Mechanical and Energy Engineering 32
• 简化工艺 便于合箱
二、型芯的形状、数量及分块
型芯是铸件的一个
重要的组成部分。
型芯的功用是形成 铸件的内腔,孔洞和 形状复杂、阻碍起模 部分的外形。
图4-6 车轮铸件的型芯方案
JMU College of Mechanical and Energy Engineering 35
JMU College of Mechanical and Energy Engineering
21
选择分型面时应尽量避免不必要的型芯。
制造型芯需要专门的芯盒、芯骨,还需烘干及下芯 等工序,增加了铸件成本。
若按图中方案1分开模造型,其上、下内腔均需采用型芯。 图中方案Ⅱ,采用整模造型,则上、下内腔均可由砂垛形成,
省掉了型芯。
JMU College of Mechanical and Energy 22
(1) 铸件的重要加工面或主要工作面应朝下或位于侧 面,避免砂眼、气孔和夹渣
JMU College of Mechanical and Energy Engineering
7
车床床身铸件的浇注位置方案
上
下
重要加工面应朝下或位于侧面。 由于床身导轨面是关键表面,不容许有明显的表面缺陷, JMU College of Mechanical and Energy Engineering 而且要求组织致密,因此通常都将导轨面朝下浇注。 8
大型铸铁件的铸造工艺设计

大型铸铁件的铸造工艺设计杜瑞祥(天津三达铸造有限公司,天津300251)摘要:通过分析大型铸铁件的特点,认为其浇注工艺设计的主要原则应当是:分散底注、快速浇注和高温浇注;并对各种浇注工艺的优缺点进行了详细分析。
最后用叶片环状支架、压缩机缸体上侧、横梁等大型铸铁件的浇注工艺实例说明采用分散底注的浇注方式,同时适当提高浇注温度和速度,可以提高铸件成品率。
关键词:大型铸铁件;分散底注;快速浇注;高温浇注中图分类号:T G 244+-2文献标识码:A文章编号:1003—8345(2009)05—0043—04C as t i ngM et hodD es i g n of I I ea vy I r on C a s t i ngs D U R ui —xi ang(S anda Foundry Co .Lt d .,Ti anji n300251,C hi n a)A bs t r ac t :Bas edont he anal ys i s ofchar act e r i s t i c s ofhea vy i ID n cast i ngs ,i t7sco nsi d er e d t h att hei r cast i n g m et ho d des i gnpr i nci pl e sho ul dbea s :bo t t o m gat i ngw i t hdi sper sed i ngat es ,f a s t a ndhi gh t e m pe r at ur epo ur i n g .T head vant age sanddi sadV ant ages of V ar i ou s cast i n g m et ho ds w e r eana l yz ed i n det ai l ,and t he cast i n g met ho ds of s o m e hea vy i ron cas t i ngs su ch ast he r i ng —s haped br a cket of bl ades ,t op cyl i nder bl ock a nd c r oss be am of com pr es sor a nds oonw e r e t a kenasexa m pl e st o showt hatiti s pos s i bl et oi ncr eas et her a teof qual i 矗ed cas t i ngsby ad opt i n g bo t t o m gat i ng w i t h di sper sed i ngat e s a nd pr ope r l yi ncr e asi ng po ur i ng t e m pe r at ur e a nd po ur i ngra t e 。
典型铸铁件铸造工艺设计与实例

典型铸铁件铸造工艺设计与实例叙述铸造生产中典型铸铁件一一气缸类铸件、圆筒形铸件、环形铸件、球墨铸铁曲轴、盖类铸件、箱体及壳体类铸件、阀体及管件、轮形铸件、锅形铸件及平板类铸件的铸造实践。
内容涉及材质选用、铸造工艺过程的主要设计、常见主要铸造缺陷及对策等。
第1章气缸类铸件1.1低速柴油机气缸体1.1.1 一般结构及铸造工艺性分析1.1.2 主要技术要求1.1.3 铸造工艺过程的主要设计1.1.4 常见主要铸造缺陷及对策1.1.5 铸造缺陷的修复1.2中速柴油机气缸体1.2.1 一般结构及铸造工艺性分析1.2.2 主要技术要求1.2.3 铸造工艺过程的主要设计1.3空气压缩机气缸体1.3.1 主要技术要求1.3.2 铸造工艺过程的主要设计第2章圆筒形铸件2.1 气缸套2.1.1 一般结构及铸造工艺性分析2.1.2 工作条件2.1.3 主要技术要求2.1.4 铸造工艺过程的主要设计2.1.5 常见主要铸造缺陷及对策2.1.6 大型气缸套的低压铸造2.1.7 气缸套的离心铸造2.2冷却水套2.2.1 一般结构及铸造工艺性分析2.2.2 主要技术要求2.2.3 铸造工艺过程的主要设计2.2.4 常见主要铸造缺陷及对策2.3烘缸2.3.1 结构特点2.3.2 主要技术要求2.3.3 铸造工艺过程的主要设计2.4活塞2.4.1 结构特点2.4.2 主要技术要求2.4.3 铸造工艺过程的主要设计2.4.4 砂衬金属型铸造第3章环形铸件3.1活塞环3.1.1 概述3.1.2 材质3.1.3 铸造工艺过程的主要设计3.2 L形环3.2.1 L形环的单体铸造3.2.2 L形环的筒形铸造第4章球墨铸铁曲轴4.1 主要结构特点4.1.1曲臂与轴颈的连接结构4.1.2 组合式曲轴4.2主要技术要求4.2.1 材质4.2.2 铸造缺陷4.2.3 质量检验4.2.4 热处理4.3铸造工艺过程的主要设计4.3.1 浇注位置4.3.2 模样4.3.3 型砂及造型4.3.4 浇冒口系统4.3.5 冷却速度4.3.6 熔炼、球化处理及浇注4.4 热处理4.4.1 退火处理4.4.2 正火、回火处理4.4.3 调质(淬火与回火)处理4.4.4 等温淬火4.5常见主要铸造缺陷及对策4.5.1 球化不良及球化衰退4.5.2 缩孔及缩松4.5.3 夹渣4.5.4 石墨漂浮4.5.5 皮下气孔4.6大型球墨铸铁曲轴的低压铸造第5章盖类铸件5.1柴油机气缸盖5.1.1 一般结构及铸造工艺性分析5.1.2 主要技术要求5.1.3铸造工艺过程的主要设计5.2空气压缩机气缸盖5.2.1 一般结构及铸造工艺性分析5.2.2 主要技术要求5.2.3 铸造工艺过程的主要设计5.3其他形式气缸盖5.3.1 一般结构5.3.2 主要技术要求5.3.3铸造工艺过程的主要设计第6章箱体及壳体类铸件6.1大型链轮箱体6.2增压器进气涡壳体6.3排气阀壳体6.4球墨铸铁机端壳体6.5球墨铸铁水泵壳体6.6球墨铸铁分配器壳体第7章阀体及管件7.1灰铸铁大型阀体7.2灰铸铁大型阀盖7.3球墨铸铁阀体7.4管件7.5球墨铸铁螺纹管件7.6球墨铸铁管卡箍7.6.1 主要技术要求7.6.2 铸造工艺过程的主要设计7.6.3 常见主要铸造缺陷及对策第8章轮形铸件8.1 飞轮8.2调频轮8.3中小型轮形铸件8.4球墨铸铁轮盘第9章锅形铸件9.1大型碱锅9.2中小型锅形铸件第10章平板类铸件10.1大型龙门铳床落地工作台10.2大型立式车床工作台10.3大型床身中段10.4 大型底座中国机械工业出版社精装16开定价:299元。
轮盘类铸铁件铸造工艺
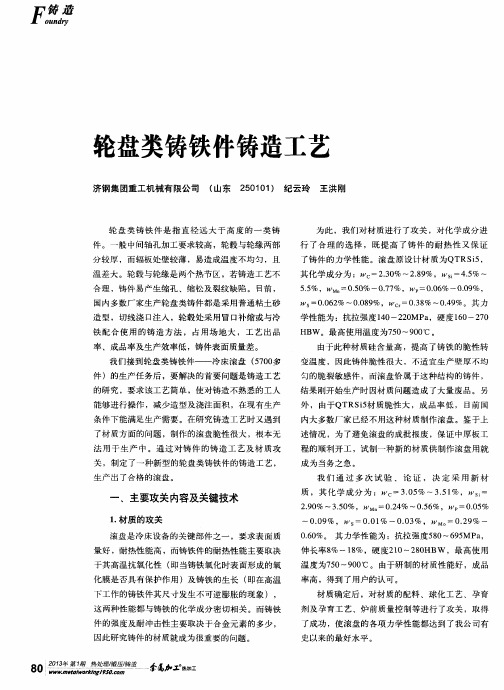
足 够 的 造 型及 浇 注 面 积 ,且 工 艺 复杂 ,对铸 造 不 熟 的工 人 无法 操 作 ,满 足 不 了生 产 要 求 。
为 此 ,我 们 通 过 比较 ,选 择 了金 属 型树 脂 砂 组
2 . 9 0 % ~3 . 5 0% , WM = 0 . 2 4% ~ 0 . 56 % , WP =0 . 0 5 %
、
主要攻关 内容及关键技术
1 . 材质 的攻关
滚盘 是 冷 床 设备 的关 键 部 件之 一 ,要 求表 面 质 量 好 ,耐 热 性 能 高 ,而铸 铁 件 的 耐热 性 能 主 要取 决
s =0 . 0 6 2 % ~0 . 0 8 9 %,Wc =0 . 3 8 %~0 . 4 9 %。其 力
学 性 能 为 :抗 拉 强度 1 4 0 ~2 2 0 MP a ,硬 度 1 6 0 ~2 7 0 H B W 。最 高使 用温 度为 7 5 0 ~9 0 0 C。 由于 此种 材 质 硅 含 量高 ,提 高 了铸 铁 的脆 性 转 变温 度 ,因此 铸 件 脆性 很 大 ,不适 宜 生 产 壁厚 不 均 匀 的脆 裂 敏感 件 ,而 滚盘 恰 属于 这 种 结 构 的铸 件 , 结 果 刚 开 始生 产 时 因材 质问 题造 成 了大 量废 品 。另 外 , 由于QT R S i 5 材 质 脆性 大 ,成 品率 低 , 目前 国 内 大 多数 厂 家 已经 不 用这 种 材 质制 作 滚 盘 。鉴 于 上
芯 叠浇 工 艺 ,即 采 用 金属 型 芯 盒树 脂砂 制 芯 ,然 后
铸造工艺设计步骤

铸造工艺设计:就是根据铸造零件的结构特点,技术要求,生产批量和生产条件等,确定铸造方案和工艺参数,绘制铸造工艺图,编制工艺卡等技术文件的过程.设计依据:在进行铸造工艺设计前,设计者应掌握生产任务和要求,熟悉工厂和车间的生产条件,这些是铸造工艺设计的基本依据.设计内容:铸造工艺设计内容的繁简程度,主要决定于批量的大小,生产要求和生产条件.一般包括下列内容:铸造工艺图,铸件(毛坯)图,铸型装配图(合箱图),工艺卡及操作工艺规程.设计程序:1零件的技术条件和结构工艺性分析;2选择铸造及造型方法;3确定浇注位置和分型面;4选用工艺参数;5设计浇冒口,冷铁和铸肋;6砂芯设计;7在完成铸造工艺图的基础上,画出铸件图;8通常在完成砂箱设计后画出;9综合整个设计内容.铸造工艺方案的内容:造型,造芯方法和铸型种类的选择,浇注位置及分型面的确定等.铸件的浇注位置是指浇注时铸件在型内所处的状态和位置.分型面是指两半铸型相互接触的表面.确定砂芯形状及分盒面选择的基本原则,总的原则是:使造芯到下芯的整个过程方便,铸件内腔尺寸精确,不至造成气孔等缺陷,使芯盒结构简单.1保证铸件内腔尺寸精度;2保证操作方便;3保证铸件壁厚均匀;4应尽量减少砂芯数目;5填砂面应宽敞,烘干支撑面是平面;6砂芯形状适应造型,制型方法.铸造工艺参数通常是指铸型工艺设计时需要确定的某些数据.1铸件尺寸公差:是指铸件各部分尺寸允许的极限偏差,它取决于铸造工艺方法等多种因素.2主见重量公差定义为以占铸件公称质量的百分率为单位的铸件质量变动的允许值.3机械加工余量:铸件为保证其加工面尺寸和零件精度,应有加工余量,即在铸件工艺设计时预先增加的,而后在机械加工时又被切去的金属层厚度,称为机械加工余量,简称加工余量.代号用MA,由精到粗分为ABCDEFGH和J9个等级。
4铸造收缩率K的定义是K=式中L摸样工作面的尺寸;L铸件尺寸.5起模斜度:为了方便起模,在模样,芯盒的出模方向留有一定斜度,以免损坏砂型或砂芯.这个斜度称为起模斜度.6最小铸出孔及槽.7工艺补正量:因工艺需要在铸件相应非加工面上增加的金属层厚度称为工艺补正量.8分型负数:为了保证铸件尺寸精度,在拟订工艺时,为抵消铸件在分型面部位的增厚,在模样上相应减去的尺寸,称为分型负数.9反变形量:在模样上做出的预变形量.10砂芯负数(砂芯减量):为了保证铸件尺寸准确,将芯盒的长.宽尺寸减去一定量,这个被减去的尺寸称为砂芯负数.11非加工壁厚的负余量:为了保证铸件尺寸的准确性,凡形成非加工壁厚的木模或芯盒内的肋板厚度尺寸应该减小,即小于图样尺寸,所减小的厚度尺寸称为非加工壁厚的负余量.12分芯负数:对于分段制造的长砂芯或分开制造的大砂芯,在接缝处应留出分芯间隙量,即在砂芯的分开面处,将砂芯尺寸减去间隙尺寸,被减去的尺寸称为分芯负数.判断铸件变形方向:铸件冷却缓慢的一侧必定受到拉应力而产生内凹变形;冷却较快的一侧必定受到压应力而产生外凸变形.浇注系统由浇口杯(外浇口)、直浇道、直浇道窝、横浇道和内浇道等部分组成。
铸造工艺设计概论

(三)设计内容和程序 铸造工艺设计内容: 1)铸造工艺图 2)铸件(毛坯)图 3)铸型装配图(合箱图) 4)工艺卡及操作工艺规程
此外铸造工艺设计应注意保护环境、 节省能源、最大限度的提高生产效率。 使用保温冒口、湿型、制芯
铸造工艺方案的确定
砂型铸造工艺方案主要包括以下内容: 1)造型方法(机器、手工) 2)造芯方法 3)铸型种类的选择(砂型、金属型) 4)浇注位置 5)分形面选择
第四章
铸造工艺设计
吴士平
主讲
第四章
铸造工艺设计概念
第一节 铸造工艺设计的概念、设计的依据、内 容及程序
一、概念 铸造工艺设计:是根据铸造零件的结构特点、 技术要求、生产批量和生产条件等,确定铸造方 案和工艺参数,绘制铸造工艺图,编制工艺卡等 技术文件的过程。
• 铸造工艺设计的有关文件,是生产准备、 管理和铸件验收的依据,并用于直接指 导生产操作。因此铸造工艺设计的好坏, 对铸件的品质、生产率和成本起着重要 作用。
2、芯头斜度 对垂直芯头,上下芯头都应设有斜度。
3、芯头间隙
4、压环、防压环和积砂槽
(二)芯头承压面积计算 芯头的承压面积应足够大,以保证在金 属液最大浮力的作用下不超过铸型的许 用压应力。 由于砂芯的强度通常都大于铸型的 强度,故只核算铸型的许用压力即可。 芯头的承压面积S应满足下式
(2)零件技术要求 金属材质牌号、金相组织、力学性能 要求、铸件尺寸及重量公差及其它特殊 性能要求,如是否经水压、气压试验等。 铸造工艺设计时应注意尽量满足这些要 求。
(3)产品数量及生产期限 应尽量采用先进技术以保证铸件的质 量及数量,保证生产期限。缩短生产, 周期,获得最大的经济效益。
(二)生产条和生产效率、造型和制芯机种类、 机械化程度、烘干炉和热处理炉的能力 等。 (2)车间原材料的应用情况和供应情况 (3)工人技术水平和生产经验 (4)模具等工艺装备的加工能力和生产经验
大型灰铁铸件的铸造工艺

大型灰铁铸件的铸造工艺
大型灰铁铸件的铸造工艺可以分为以下几个步骤:
1. 模具准备:选择合适的灰铁模具,并进行准备工作,包括清洁、涂抹模脱剂等。
2. 铸型制备:将模具装配到铸造设备上,根据铸件的形状和尺寸,在模具中制备出与铸件相对应的空腔,可以采用砂型、金属型等不同的铸造方式。
3. 熔炼铁水:将铁矿石和其他合金原料放入熔炉中,通过高温熔炼,得到液态的铁水。
4. 铸注铁水:将熔融的铁水倒入预先准备好的铸型中,注意控制铁水的温度和流量,保证铁水充分填充整个铸型空腔。
5. 固化冷却:等到铁水完全填充整个铸型后,放置一段时间,让铁水逐渐固化和冷却,使铸件形成固态。
6. 脱模清理:待铁水完全固化后,拆卸模具,取出铸件。
对于有砂模的铸件,需要清理剩余砂粒和其他杂质。
7. 后处理:根据实际需要,对铸件进行修磨、去毛刺、清除氧化皮等后处理工
序,以提高铸件的精度和表面质量。
需要注意的是,大型灰铁铸件的铸造工艺还需要考虑铁水的浇注方式、冷却方式、铸型材料的选择等因素,以保证铸件的质量和性能。
铸造工艺图及设计实例

汇报人: 日期:
目录
• 铸造工艺图 • 铸造材料及特性 • 铸造设备及工具 • 铸造设计实例 • 铸造工艺优化及改进建议 • 铸造工艺图及设计软件应用
01
铸造工艺图
铸造工艺流程图
造型材料准备
包括对铸造用砂、型砂等的选择 、混砂、配制等过程。
模样和芯盒准备
根据图纸准备木模、木芯盒等。
造型和制芯
将模样放入芯盒内,填入型砂, 形成铸型。
落砂和清理
铸件冷却后打开铸型,去除铸件 表面和内部的残砂和夹杂物。
浇注
将熔融的金属注入铸型中。
合型
将上、下铸型组合起来,形成完 整的铸型。
铸造模具设计图
模具材料选择
根据铸造合金和模具使用条件 选择模具材料,如铸铁、铜合
金等。
模具结构设计
根据产品图纸和铸造工艺要求 ,设计模具结构,包括浇口位 置、分型面选择等。
组成。
数控铣床
用于模具型腔的铣削加工,主要由 主轴、工作台、控制系统等组成。
数控磨床
用于模具型腔的磨削加工,主要由 工作台、主轴、控制系统等组成。
铸造用辅助设备
混砂机
用于混制型砂,一般由混砂转子、型砂输送装置、润 湿装置等组成。
砂处理设备
用于对型砂进行干燥、冷却、输送等处理,一般由干 燥器、冷却器、输送装置等组成。
浇注机
用于浇注金属液体,一般由浇包、浇道、控制系统等 组成。
铸造工具及选用
1 2
模样和芯盒
用于制作铸造用的模样和芯盒,一般由木材或塑 料制成。
浇口杯和分流锥
用于浇注金属液体,一般由耐火材料制成。
3
冒口和冷铁
用于控制铸件的温度和补缩,一般由铸铁或铸钢 制成。
第四章 铸件结构与工艺设计

铸件结构设计 砂型铸造工艺设计 铸造工艺设计实例
第一节 铸件结构设计
铸件结构不仅会直接影响到铸件的力学性 能、尺寸精度、重量要求和其它使用性能, 同时,对铸造生产过程也有很大影响。 所谓铸造工艺性良好的铸件结构,应该是 铸件的使用性能容易保证,生产过程及所 使用的工艺装备简单,生产成本低。 铸件结构要素与铸造合金的种类、铸件的 大小、铸造方法及生产条件密切相关。
(压铸)便于取出铸件的设计
熔模铸件平面上的工艺孔和工艺肋
2.铸件的组合设计 2.铸件的组合设计
因工艺的局限而无法整铸的结构,应采用组合设计。
铸钢底座的铸焊
组合床身铸件
a)砂型铸件改为b)组合压铸件 a)砂型铸件改为b)组合压铸件
第二节 砂型铸造工艺设计
1) 2) 3) 4)
砂型铸造工艺具体设计内容包括: 选择铸件的浇注位置和分型面; 确定工艺参数(机械加工余量、起模斜度、铸造圆 角、收缩量等); 确定型芯的数量、芯头形状及尺寸; 确定浇冒口、冷铁等的形状、尺寸及在铸型中的 布置等。 然后将工艺设计的内容(工艺方案)用工艺符号或文 字在零件图上表示出来,即构成了铸造工艺图。
冒口 上 中 上 下
中 下 放收缩率1% 放收缩率1% 余量:上面>侧面> 余量:上面>侧面>下面 单件小批 手工三箱造型 大批量
外 型 芯 块
两箱机器造型
第三节 铸造工艺设计实例
例1:支架零件铸造工艺设计
材料为HT200,单件、小批量生产工作时承受中等 静载荷,试进行铸造工艺设计。
1.零件结构分析: 零件结构分析: 零件结构分析 筒壁过厚,转角处未采用圆角。修改后的结 构如图b)所示。 选择铸造方法及造型方法: 2.选择铸造方法及造型方法: 3.选择浇注位置和分型面
球墨铸铁的工艺设计
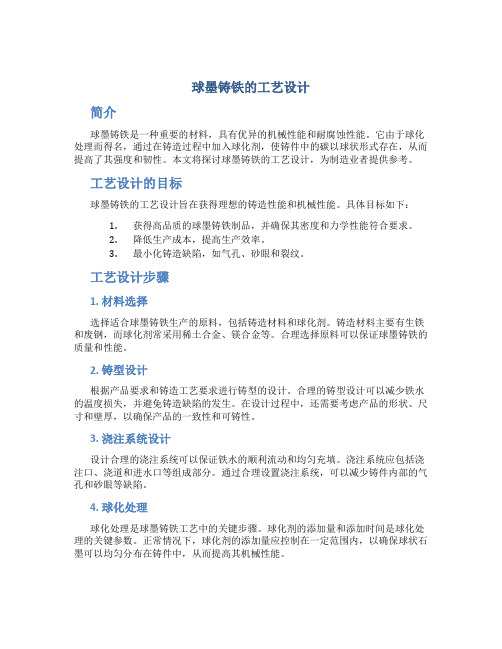
球墨铸铁的工艺设计简介球墨铸铁是一种重要的材料,具有优异的机械性能和耐腐蚀性能。
它由于球化处理而得名,通过在铸造过程中加入球化剂,使铸件中的碳以球状形式存在,从而提高了其强度和韧性。
本文将探讨球墨铸铁的工艺设计,为制造业者提供参考。
工艺设计的目标球墨铸铁的工艺设计旨在获得理想的铸造性能和机械性能。
具体目标如下:1.获得高品质的球墨铸铁制品,并确保其密度和力学性能符合要求。
2.降低生产成本,提高生产效率。
3.最小化铸造缺陷,如气孔、砂眼和裂纹。
工艺设计步骤1. 材料选择选择适合球墨铸铁生产的原料,包括铸造材料和球化剂。
铸造材料主要有生铁和废钢,而球化剂常采用稀土合金、镁合金等。
合理选择原料可以保证球墨铸铁的质量和性能。
2. 铸型设计根据产品要求和铸造工艺要求进行铸型的设计。
合理的铸型设计可以减少铁水的温度损失,并避免铸造缺陷的发生。
在设计过程中,还需要考虑产品的形状、尺寸和壁厚,以确保产品的一致性和可铸性。
3. 浇注系统设计设计合理的浇注系统可以保证铁水的顺利流动和均匀充填。
浇注系统应包括浇注口、浇道和进水口等组成部分。
通过合理设置浇注系统,可以减少铸件内部的气孔和砂眼等缺陷。
4. 球化处理球化处理是球墨铸铁工艺中的关键步骤。
球化剂的添加量和添加时间是球化处理的关键参数。
正常情况下,球化剂的添加量应控制在一定范围内,以确保球状石墨可以均匀分布在铸件中,从而提高其机械性能。
5. 熔炼工艺控制在球墨铸铁的熔炼过程中,需要注意炉温和熔化时间的控制。
炉温过高可能导致熔体的超热和石墨球化的不完全,而炉温过低则可能影响球墨铸铁的流动性和充填性。
熔炼时间过长会增加能耗和生产成本,而熔炼时间过短可能导致熔体的质量不稳定。
6. 凝固过程控制凝固过程控制是确保球墨铸铁质量的关键环节。
通过合理控制凝固温度和凝固时间,可以使球墨铸铁具有优异的力学性能。
此外,正确的冷却方法和冷却速度也会对凝固过程产生影响。
7. 硬度调控球墨铸铁通常需要进行硬度调控,以满足不同工程应用的要求。
大型灰铸铁皮带轮铸造工艺设计
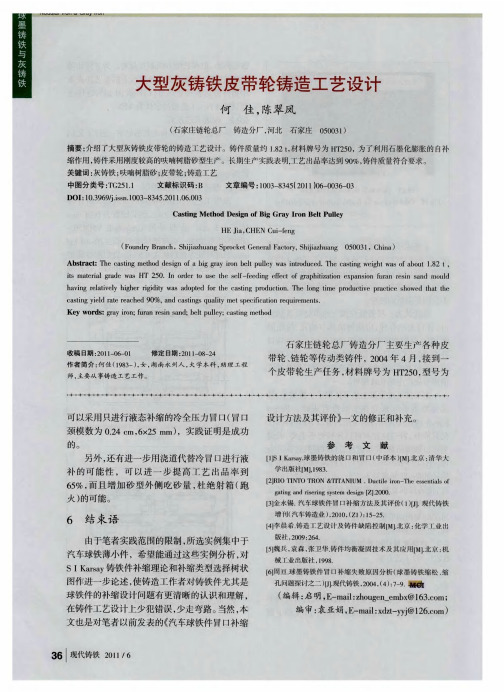
03 x .8 8 V5 .1 O x 5 6 4
⑥浇注系统各单元断面比例为: 直 F : 内 F :横F =
12: . 1 2 4: 3- 212 e . 1 1: = 5. 2 3: . m
综 上 所 述 , 注 系统 见 图 2 各 单 元 尺 寸 选 浇 ,
择 如下 :
F盲 2 . c 选 用  ̄5 m; = 54 m , 6m
F措数量 为 2 ,采用 梯 形截 面 尺寸 为 3/ 个 6 3 ̄ 5高 ) 2 3 ( mm; F 数量 为 4个 ,采用 梯形 截 面 尺寸 为 4/ 0
3 x 4 高 ) m。 6 1( m 23 冒 口设计 .
C
29 32 .~ .
( %)
B%) (
S b
O.5 0
S i
14 . . —17 源自Mn 09 . . 一1 1
P
≤ 0.5 1
S
≤0.2 1
截面 总面积 :
2 铸 造 工 艺设 计
2 1 总体 工艺方 案 .
F阳 — — ,l : _—
c m
() 1
不 小 于 1 。 2h
() 2
④验算浇注时间 : 型 内平 均液 面上升 速度 :
: :
铸件化学成分根据铸件壁厚 和技术条件选 择, 控制范围见表 l; Ⅲ炉前三角试样的白口宽度大 致为 4 7 m, ~ 均以中间值作为生产控制 目 m 标值。
22 浇注 系统截 面积计 算 .
0 6 m/ .lc s
3 t
参阅文献[ , 2 铸件壁厚大于 4 m V值应 】 0m ,
为 :.~ . c /。验 算 结果 与 要求 值接 近 , 注 08 1 m s 0 浇 时 间取 8 是合理 的。 :5s
铸造工艺设计
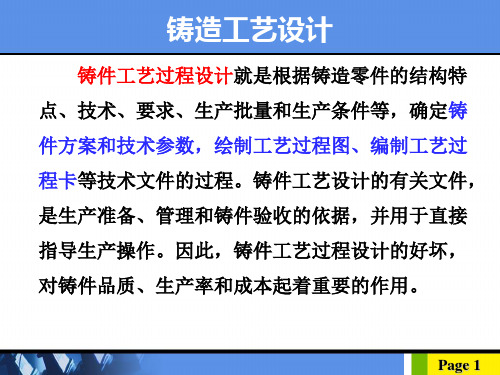
Page 32
铸造工艺过程图的绘制
名称
技术符号和表示方法
Байду номын сангаас
名称
技术符号和表示方法
用红色线表示,并用红色写出“ 上、中、下”字样
置
选择
的选择
Page 4
2.3.2浇注位置和分型面的选择
• 重要加工面应朝下或位于侧面
浇注位置是 指浇注时铸 件在铸型中 所处的位置。
保证卷筒周 围质量均匀
Page 5
1)浇注位置选择原则
铸件的大平面尽可能朝下或采用倾斜浇注 铸型的 上表面除了容易产生砂眼、气孔、夹渣外,大平面还常 产生夹砂缺陷。同时也有利于排气、减小金属液对铸型 的冲刷力。
1-冒口; 2、3-砂芯
图2-29 铸钢链轮的浇注位置
Page 8
2)分型面的选择原则
•便于起模,使造型工艺简化。考虑 分型面形状和数目,活块,型芯。
分型面(Parting line)是指 两半铸型相互接触的表面。除了实 型铸造法外,都要选择分型面。
Page 9
2)分型面的选择原则
(1)应尽可能使全部或大部分铸件,或者加工基准面 与重要的加工面处于同一半型内。 以避免因合型不准产 生错型,保证铸件尺寸精度。
Page 1
2.3.1 铸造工艺设计内容与步骤
铸造工艺过程设计的内容 • 铸造工艺过程设计的内容主要决定于批量大小、
生产要求和生产条件。一般包括:铸造工艺过程 图、铸件图、铸型装配图、工艺过程卡、操作技 术规程。广义地讲,凡铸造技术装备的设计内容, 诸如模样图、模板图、芯盒图、砂箱图、压铁图、 专用检具图、专用量具图及组芯夹具图等,均属 于铸造工艺过程设计的内容。
铸造工艺设计方案

要求:①掌握铸造工艺方案的制定,
铸造工艺参数确定的原则;② 熟悉浇注系统的组成以及冒口的作用; ③了解冒口尺寸的计算方法。
重点:砂型铸造工艺图的绘制; 难点:浇注位置及分型面的选择。
砂型铸造工艺设计:
为获得好的铸件,减少工 作量,降低成本,合理制订铸 造工艺方案,绘制铸造工艺图。
√
×
2.分型面的选择原则
重要性:
①恰当与否会影响铸件质量; ②使制模、造型、造芯、合箱或清理 等工序复杂化; ③甚至还可增大切削加工的工作量。
1)便于起模,使造型工艺简化
尽量使分型面平直、数量少,避 免不必要的活块和型芯。 √
×
起重臂的分型面
√
大平面还常产生夹砂缺陷,故对平板、圆盘类铸件,大平面应朝下。
加工表面上的起模斜度应结合加工 余量直接表示出,而不加工表面上的 斜度(结构斜度)仅需用文字注明。
熟悉浇注系统的组成以及冒口的作用; 分型面:砂箱间的接触表面。 §4-1 铸造工艺方案的确定 □大批量生产条件下,采用机器造型,需要改用图中所示的环状型芯,使铸型简化成只有一个分型面。 一般大量生产的定型产品、特殊重要的单件生产的铸件,铸造工艺设计订得细致,内容涉及较多。 共型芯:增加型芯稳定性、提高模板和砂箱利用率。 熟悉浇注系统的组成以及冒口的作用; 铸钢件:表面粗糙,余量比铸铁大 ①选择铸件的浇注位置及分型面。 铸件的孔、槽是否铸出,不仅取决于工艺上的可能性,还须考虑其必要性。 3)尽量使型腔及主要型芯位于下型 单件、小批生产的一般性产品,铸造工艺设计内容可以简化。 不加工的特形孔、价格较贵的非铁金属铸孔,尽量铸出。 它是制造模样和铸型,进行生产准备和铸件检验的依据(基本工艺文件)。 三、砂芯形状、个数及分块 a)垂直芯头 b)水平芯头 三、砂芯形状、个数及分块 尽量使分型面平直、数量少,避免不必要的活块和型芯。 方案III:从B面分型,铸件全部置于下型。 采用分型方案I时的铸造工艺图 1)铸件的重要加工面应朝下或位于侧面。
- 1、下载文档前请自行甄别文档内容的完整性,平台不提供额外的编辑、内容补充、找答案等附加服务。
- 2、"仅部分预览"的文档,不可在线预览部分如存在完整性等问题,可反馈申请退款(可完整预览的文档不适用该条件!)。
- 3、如文档侵犯您的权益,请联系客服反馈,我们会尽快为您处理(人工客服工作时间:9:00-18:30)。
典型铸铁件铸造工艺设计
铸造工艺是制造铸铁件的关键环节之一,其设计直接影响到铸件的质量和性能。
本文将以典型铸铁件的铸造工艺设计为主题,对铸造工艺的设计要点和流程进行详细介绍,以期能够为相关从业人员提供一定的参考和指导。
一、典型铸铁件的特点
铸铁件是一种常见的铸造件,其主要特点是具有良好的铸造性能、低成本和高强度。
铸铁件通常被广泛应用于机械制造、汽车工业、农机具等领域,如汽车发动机缸体、机床床身等。
二、铸造工艺设计的要点
铸造工艺设计的关键是确定合适的铸造工艺参数,以实现铸件的准确成型和优良性能。
以下是铸造工艺设计的要点:
1.铸型设计:根据铸件的形状和尺寸,确定合适的铸型结构和尺寸。
铸型的设计应考虑到铸件的收缩和变形,以避免出现缺陷和不合格品。
2.熔炼工艺:根据铸件的材料要求,确定合适的熔炼工艺参数,包括炉温、熔化时间、炉中温度等。
同时,还需要考虑铁水的质量和成分控制,以保证铸件的化学成分符合要求。
3.浇注系统设计:根据铸件的形状和尺寸,确定合适的浇注系统,
包括浇杯、导流冒、浇口等。
浇注系统的设计应考虑到浇注过程中的液态金属流动和气体排出,以避免铸件内部的气孔和夹杂物。
4.冷却系统设计:根据铸件的形状和尺寸,确定合适的冷却系统,包括冷却水道、冷却器等。
冷却系统的设计应考虑到铸件的冷却速度和收缩形变,以避免出现裂纹和变形。
5.铸造工艺参数设计:根据铸件的形状和尺寸,确定合适的铸造工艺参数,包括浇注温度、浇注速度、浇注压力等。
铸造工艺参数的设计应考虑到铸件的凝固过程和收缩变形,以保证铸件的准确成型和良好性能。
三、铸造工艺设计流程
铸造工艺设计的流程一般包括以下几个步骤:
1.确定铸件的形状和尺寸,以及材料要求。
2.根据铸件的形状和尺寸,设计合适的铸型结构和尺寸。
3.根据铸件的材料要求,确定合适的熔炼工艺参数。
4.根据铸件的形状和尺寸,设计合适的浇注系统和冷却系统。
5.根据铸件的形状和尺寸,确定合适的铸造工艺参数。
6.进行铸造试验,验证设计的可行性和合理性。
7.根据试验结果,对铸造工艺进行调整和优化。
四、典型铸铁件的铸造工艺设计案例
以汽车发动机缸体的铸造工艺设计为例,具体的设计流程如下:
1.确定铸件的形状和尺寸,以及材料要求。
汽车发动机缸体通常为复杂的几何形状,要求材料具有较高的强度和耐磨性。
2.根据铸件的形状和尺寸,设计合适的铸型结构和尺寸。
汽车发动机缸体的铸型结构需要考虑到铸件内部的冷却水道和机械加工余量。
3.根据铸件的材料要求,确定合适的熔炼工艺参数。
汽车发动机缸体的材料通常使用铸铁,需要控制好炉温和熔炼时间,以保证铸件的化学成分符合要求。
4.根据铸件的形状和尺寸,设计合适的浇注系统和冷却系统。
汽车发动机缸体的浇注系统应考虑到液态金属的流动和气体的排出,冷却系统应考虑到铸件的冷却速度和收缩形变。
5.根据铸件的形状和尺寸,确定合适的铸造工艺参数。
汽车发动机缸体的铸造工艺参数包括浇注温度、浇注速度和浇注压力等,需要考虑到铸件的凝固过程和收缩变形。
6.进行铸造试验,验证设计的可行性和合理性。
通过试验可以评估铸造工艺设计的准确性和可靠性,并根据试验结果对工艺进行调整
和优化。
通过以上铸造工艺设计的步骤和案例,可以看出铸造工艺设计在铸造过程中的重要性。
合理的铸造工艺设计可以确保铸件的质量和性能,提高生产效率和降低生产成本。
因此,在实际生产中,需要根据具体的铸件形状和材料要求,进行细致的工艺设计和优化,以满足用户对铸件的需求。