油缸和液压系统设计说明和计算
油缸推力计算公式详解

油缸推力计算公式详解在工程领域中,油缸是一种常见的液压传动装置,用于产生直线运动。
在设计和使用油缸时,我们经常需要计算油缸的推力,以确保其能够满足工作需求。
本文将详细介绍油缸推力的计算公式,并对其进行详细解析。
油缸推力的计算公式如下:F = A × P。
其中,F表示油缸的推力,单位为牛顿(N);A表示油缸的有效工作面积,单位为平方米(m²);P表示油缸的压力,单位为帕斯卡(Pa)。
首先,我们来详细解析上述公式中的各个参数。
1. 油缸的有效工作面积(A)。
油缸的有效工作面积是指油缸活塞的有效工作面积,通常由油缸的直径和活塞面积计算得出。
油缸的有效工作面积决定了油缸能够产生的推力大小,其计算公式如下:A = π× (D/2)²。
其中,A表示油缸的有效工作面积,单位为平方米(m²);π表示圆周率,约为3.14;D表示油缸的直径,单位为米(m)。
2. 油缸的压力(P)。
油缸的压力是指液压系统中施加在油缸内的压力,通常由液压泵提供。
油缸的压力决定了油缸能够产生的推力大小,其计算公式如下:P = F/A。
其中,P表示油缸的压力,单位为帕斯卡(Pa);F表示油缸的推力,单位为牛顿(N);A表示油缸的有效工作面积,单位为平方米(m²)。
通过上述公式,我们可以清晰地了解油缸推力的计算方法。
在实际工程中,我们可以根据具体的油缸参数和工作条件,通过上述公式计算出油缸的推力大小,从而合理设计和选择油缸,确保其能够满足工作需求。
除了上述的基本计算公式外,还有一些需要注意的问题:1. 油缸的摩擦力。
在实际工程中,油缸的运动会受到摩擦力的影响,从而影响油缸的推力。
因此,在计算油缸推力时,需要考虑油缸的摩擦力,通常可以通过实验或者经验数据进行修正。
2. 油缸的工作环境。
油缸的工作环境也会对其推力产生影响,例如温度、湿度、粉尘等因素都会影响油缸的工作性能。
因此,在计算油缸推力时,需要考虑其工作环境,从而合理选择油缸的材料和密封结构。
油缸油压计算公式

油缸油压计算公式在液压系统中,油缸是一种常用的执行元件,它通过液压力来产生线性运动。
而油压则是决定油缸工作效果的重要因素之一。
在设计和使用液压系统时,了解油缸油压的计算公式是非常重要的。
本文将介绍油缸油压的计算公式及其应用。
油缸油压计算公式可以通过以下公式来表示:P = F / A。
其中,P表示油压,单位为帕斯卡(Pa);F表示作用在油缸上的力,单位为牛顿(N);A表示油缸的有效面积,单位为平方米(m²)。
这个公式简单明了地表示了油压与作用力和有效面积之间的关系。
通过这个公式,我们可以很容易地计算出油缸的油压,从而更好地控制液压系统的工作效果。
在实际应用中,我们可以通过以下步骤来计算油缸的油压:1. 确定作用在油缸上的力F。
这个力可以是由液压系统提供的,也可以是外部施加在油缸上的。
2. 确定油缸的有效面积A。
油缸的有效面积可以通过油缸的尺寸和结构参数来计算得出。
3. 将力F和有效面积A代入公式P = F / A中,即可得到油压P的数值。
通过这个计算公式,我们可以更好地了解油缸的工作状态,从而更好地设计和使用液压系统。
除了上述的基本计算公式外,还有一些衍生的计算公式,可以更好地帮助我们理解和应用油缸油压。
例如,当液压系统中有多个油缸同时工作时,我们可以通过以下公式来计算系统的总油压:Ptotal = (F1 + F2 + ... + Fn) / A。
其中,Ptotal表示系统的总油压;F1, F2, ..., Fn表示作用在各个油缸上的力;A表示系统的总有效面积。
通过这个公式,我们可以更好地控制液压系统中各个油缸的工作状态,从而更好地提高系统的工作效率和稳定性。
此外,当液压系统中的油压发生变化时,我们也可以通过以下公式来计算油缸的速度:v = Q / A。
其中,v表示油缸的速度,单位为米每秒(m/s);Q表示液压系统的流量,单位为立方米每秒(m³/s)。
通过这个公式,我们可以更好地控制油缸的速度,从而更好地满足各种工况下的需求。
液压油缸吨位计算公式举例说明

液压油缸吨位计算公式举例说明液压油缸的吨位计算公式是根据液压油缸的面积和工作压力来计算的。
液压油缸是一种将液压能转化为机械能的装置,它利用液压力的传递来产生力和位移。
在液压系统中,液压油缸常常用于各种工业机械和工程设备中,如机床、挖掘机、升降机等。
吨位是液压油缸所能产生的力的单位,一般以吨(Ton)为单位,1吨等于1000千克。
液压油缸的吨位计算公式如下:吨位=液压油缸的有效面积×工作压力其中吨位是液压油缸所能产生的力,单位为吨;液压油缸的有效面积是指液压油缸的有效工作面积,单位为平方厘米;工作压力是指液压油缸所受的工作压力,单位为兆帕(MPa)。
举个例子来说明液压油缸吨位的计算公式:假设液压油缸的有效面积为100平方厘米,工作压力为10兆帕,我们可以通过公式计算该液压油缸的吨位。
吨位=液压油缸的有效面积×工作压力=100平方厘米×10兆帕=1000平方厘米兆帕根据国际单位制换算规则,1平方厘米兆帕等于1千牛顿。
所以该液压油缸的吨位为1000千牛顿。
进一步换算,1千牛顿等于0.1吨,所以该液压油缸的吨位为0.1吨。
这个例子说明了如何通过液压油缸的有效面积和工作压力来计算液压油缸的吨位。
使用这个计算公式,我们可以确定液压油缸所需的吨位,从而选择合适的液压油缸进行工作。
需要注意的是,液压油缸吨位的计算公式只是一个理论值,实际情况中还需要考虑液压系统的实际工作情况、机械装置的负载要求、安全系数等因素。
在选择和使用液压油缸时,还需要根据具体情况进行综合考虑和评估,以确保安全可靠地完成工作任务。
液压油缸压力计算公式液压油缸设计计算公式
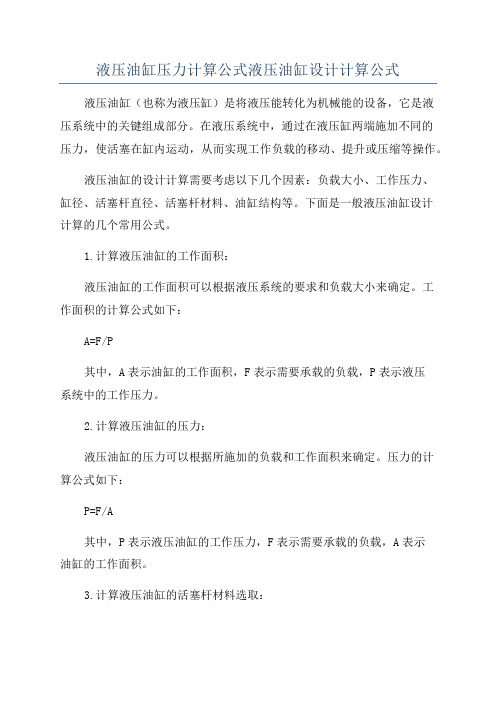
液压油缸压力计算公式液压油缸设计计算公式液压油缸(也称为液压缸)是将液压能转化为机械能的设备,它是液压系统中的关键组成部分。
在液压系统中,通过在液压缸两端施加不同的压力,使活塞在缸内运动,从而实现工作负载的移动、提升或压缩等操作。
液压油缸的设计计算需要考虑以下几个因素:负载大小、工作压力、缸径、活塞杆直径、活塞杆材料、油缸结构等。
下面是一般液压油缸设计计算的几个常用公式。
1.计算液压油缸的工作面积:液压油缸的工作面积可以根据液压系统的要求和负载大小来确定。
工作面积的计算公式如下:A=F/P其中,A表示油缸的工作面积,F表示需要承载的负载,P表示液压系统中的工作压力。
2.计算液压油缸的压力:液压油缸的压力可以根据所施加的负载和工作面积来确定。
压力的计算公式如下:P=F/A其中,P表示液压油缸的工作压力,F表示需要承载的负载,A表示油缸的工作面积。
3.计算液压油缸的活塞杆材料选取:液压油缸的活塞杆材料需要根据所承载负载和工作压力来选择,以满足强度和刚度的要求。
常见的活塞杆材料有碳钢、不锈钢、铬钼合金钢等。
一般用弯曲应力公式进行计算,考虑到材料的抗弯刚度,活塞杆的直径可以根据以下公式得到:d=((32*M*L)/(π*σ))^(1/3)其中,d表示活塞杆的直径,M表示活塞杆所承受的最大弯矩,L表示活塞杆的长度,σ表示选定材料的抗弯应力。
4.计算液压油缸的活塞直径:液压油缸的活塞直径可以通过活塞面积和活塞杆直径计算得到。
计算公式如下:D=(4*A)/(π*d^2)其中,D表示液压油缸的活塞直径,A表示油缸的工作面积,d表示活塞杆的直径。
5.计算液压油缸的油缸容积:液压油缸的油缸容积可以通过活塞面积和活塞行程来计算。
计算公式如下:V=A*l其中,V表示油缸的容积,A表示油缸的工作面积,l表示活塞的行程。
通过上述公式的计算,可以得到液压油缸的设计参数,从而满足液压系统的工作要求。
需要注意的是,在实际设计过程中,还应该考虑其他因素,如密封结构、摩擦损失、液压系统的动态响应等,以确保液压油缸的安全可靠运行。
液压缸的设计和计算
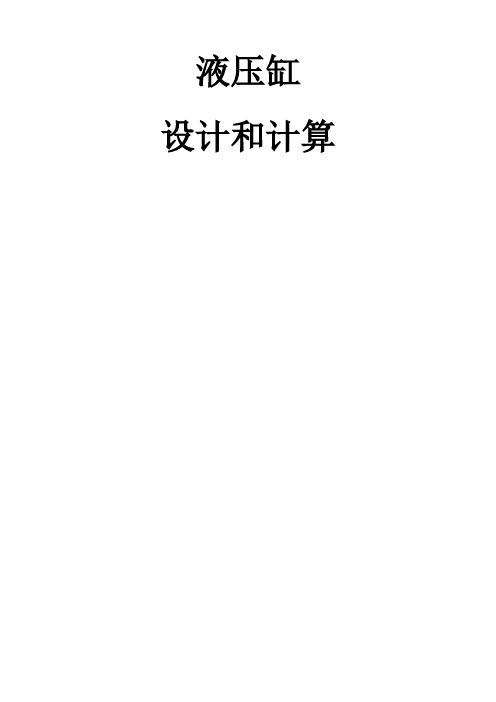
液压缸设计和计算液压缸的设计和计算液压缸的设计是整个液压系统设计中的一部分,它是在对整个系统进行了工况分析,编制了负载图,选定了工作压力之后进行的; 一、设计依据:1了解和掌握液压缸在机械上的用途和动作要求;2了解液压缸的工作条件;3了解外部负载情况;4了解液压缸的最大行程,运动速度或时间,安装空间所允许的外形尺寸以及缸本身的动作;5设计已知液压系统的液压缸,应了解液压系统中液压泵的工作压力和流量的大小、管路的通径和布置情况、各液压阀的控制情况;6了解有关国家标准、技术规范及参考资料;二、设计原则:1保证缸运动的出力、速度和行程;2保证刚没各零部件有足够的强度、刚度和耐用性;3保证以上两个条件的前提下,尽量减小缸的外形尺寸;4在保证刚性能的前提下,尽量减少零件数量,简化结构;5要尽量避免缸承受横向负载,活塞杆工作时最好承受拉力,以免产生纵向弯曲;6缸的安装形式和活塞杆头部与外部负载的连接形式要合理,尽量减小活塞杆伸出后的有效安装长度,增加缸的稳定性;三、设计步骤:1根据设计依据,初步确定设计档案,会同有关人员进行技术经济分析;2对缸进行受力分析,选择液压缸的类型和各部分结构形式;3确定液压缸的工作参数和结构尺寸;4结构强度、刚度的计算和校核;5根据运动速度、工作出力和活塞直径,确定泵的压力和流量;6审定全部设计计算资料,进行修改补充;7导向、密封、防尘、排气和缓冲等装置的设计;8绘制装配图、零件图、编写设计说明书;四、液压缸设计中应注意的问题液压缸的设计和使用正确与否,直接影响到它的性能和是否易于发生故障;所以,在设计液压缸时,必须注意以下几点:1、尽量使液压缸的活塞杆在受拉状态下承受最大负载,或在受压状态下具有良好的稳定性;2、考虑液压缸行程终了处的制动问题和液压缸的排气问题;3、正确确定液压缸的安装、固定方式;4、液压缸各部分的结构需根据推荐的结构形式和设计标准进行设计,尽可能做到结构简单、紧凑、加工、装配和维修方便;5、在保证能满足运动行程和负载力的条件下,应尽可能地缩小液压缸的轮廓尺寸;6、要保证密封可靠,防尘良好;五、计算液压缸的结构尺寸1、缸筒内径D 根据负载的大小来选定工作压力或往返运动速度比,求得液压缸的有效工作面积,从而得到缸筒内径D,再从GB2348-80标准中选取最近的标准值作为所设计的缸筒内径;液压缸的有效工作面积为…… 24D p F A π== 以无杆腔作工作腔时………… p FD π4=以有杆腔作工作腔时………… 24d p F D +=π 2、活塞杆外径d 通常先从满足速度或速度比的要求来选择,然后再校核其结构强度和稳定性;若速度比为v λ,则 vv Dd λλ1-= 也可根据活塞杆受力状况来确定:受拉力作用时,d =~; 受压力作用时,则有3、缸筒长度L 缸筒长度L 由最大工作行程长度加上各种结构需要来确定,即:l —— 活塞的最大工作行程;B —— 活塞宽度,一般为~1D ;A —— 活塞杆导向长度,取~D ;M —— 活塞杆密封长度,由密封方式定;C —— 其他长度; 注意:从制造工艺考虑,缸筒的长度最好不超过其内径的20倍;六、强度校核对液压缸的缸筒壁厚δ、活塞杆直径d和缸盖固定螺栓的直径,在高压系统中必须进行强度校核;1、缸筒壁厚校核δ 缸筒壁厚校核分薄壁和厚壁两种情况;当D/δ≥10时为薄壁,壁厚按下式进行校核:δ≥δδδ2[δ]当D/δ<10时为厚壁,壁厚按下式进行校核:δ≥δ2(√[δ]+0.4δδ[δ]−1.3δδ−1)pt ——缸筒试验压力,随缸的额定压力的不同取不同的值D ——缸筒内径σ——缸筒材料许用应力2、活塞杆直径校核活塞杆的直径d按下式进行校核:3、液压缸盖固定螺栓直径校核液压缸盖固定螺栓直径按下式计算:F ——液压缸负载k ——螺纹拧紧系数~Z ——固定螺栓个数σ——螺栓材料许用应力七、液压缸稳定性校核活塞杆轴向受压时,其直径d一般不小于长度L的1/15;当L/d≥15时,须进行稳定性校核,应使活塞杆承受的力F不能超过使它保持稳定工作所允许的临界负载Fk ,以免发生纵向弯曲,破坏液压缸的正常工作;Fk 的值与活塞杆材料性质、截面形状、直径和长度以及缸的安装方式等因素有关,验算可按材料力学有关公式进行;• 当活塞杆细长比 21/ψψ>k r l 时,则• 当活塞杆细长比21/ψψ≤k r l 且120~2021=ψψl -- 安装长度,其值与安装方式有关;Ψ1 -- 柔性系数,对钢取Ψ1=85;Ψ2 -- 末端系数,由液压缸支承方式决定;E -- 活塞杆材料的弹性模量,对钢取E=× 1011Pa ;J -- 活塞杆横截面惯性矩;A -- 活塞杆横截面面积;f -- 由材料强度决定的实验数值,对钢取f=×108 N /m2; α--系数,对钢取α=1/5000;rk --活塞杆横截面的最小回转半径;八、缓冲计算液压缸的缓冲计算主要是估计缓冲时缸中出现的最大冲击压力,以便用来校核缸筒强度、制动距离是否符合要求;液压缸在缓冲时,缓冲腔内产生的液压能E 1和工作部件产生的机械能E 2分别为:当E 1=E 2时,工作部件的机械能全部被缓冲腔液体所吸收,则有九、油缸的试验1.油缸试验压力,低于16MPa乘以工作压力的,高于16乘以工作压力的;2.最低启动压力:是指液压缸在无负载状态下的最低工作压力,它是反映液压缸零件制造和装配精度以及密封摩擦力大小的综合指标;3.最低稳定速度:是指液压缸在满负荷运动时没有爬行现象的最低运动速度,它没有统一指标,承担不同工作的液压缸,对最低稳定速度要求也不相同;4.内部泄漏:液压缸内部泄漏会降低容积效率,加剧油液的温升,影响液压缸的定位精度,使液压缸不能准确地、稳定地停在缸的某一位置;。
液压油缸推力计算公式

液压油缸推力计算公式
液压油缸推力计算公式是液压系统领域中非常重要的一种计算方法。
液压油缸是液压系统中的重要组成部分,负责将压力转化为力,推动机械设备运转,因此其推力大小的计算非常关键。
液压油缸推力计算公式的基本原理是根据液压油缸的几何尺寸和液压系统的工作压力,计算出液压油缸的理论推力大小。
液压油缸推力的大小受到多种因素的影响,如液压油缸的内径、活塞杆的直径、液压系统的工作压力等。
液压油缸推力计算公式的具体表达式如下:
F=π/4×D²×P
其中,F表示液压油缸的推力大小,单位为牛顿(N)或千克力(kgf);π为圆周率,约等于3.14;D为液压油缸的内径,单位为米(m)或毫米(mm);P为液压系统的工作压力,单位为帕斯卡(Pa)或巴(bar)。
由公式可以看出,液压油缸的推力大小与液压油缸的内径和液压系统的工作压力成正比,而与液压油缸的活塞杆直径无关。
因此,在设计液压系统时,需要根据液压油缸的推力需求和工作环境压力等因素,合理选择液压油缸的内径和液压系统的工作压力,以确保液压油缸的推力能够满足机械设备的需求。
需要注意的是,液压油缸的实际推力大小与其理论推力大小存在一定的误差。
这是由于液压油缸的摩擦力、密封性能、活塞杆的弯曲等因素的影响所导致的。
因此,在实际应用中,需要根据实际情况对液压油缸的推力进行调整和修正,以确保其能够正常工作。
液压油缸推力计算公式是液压系统设计和应用中非常重要的一种计算方法。
合理地应用该公式,可以有效地计算出液压油缸的理论推力大小,为机械设备的正常运行提供有力的支持。
油缸顶出力计算公式

油缸顶出力计算公式油缸是一种常用的液压传动元件,它通过液压油的压力来产生力和运动。
油缸的顶出力是指油缸在工作过程中产生的推力,它是油缸性能的重要指标之一。
在液压系统设计和应用中,我们经常需要计算油缸的顶出力,以便选择合适的油缸型号和确定工作参数。
油缸顶出力的计算涉及到液压油的压力、油缸的有效面积和摩擦阻力等因素。
一般来说,油缸的顶出力可以通过以下公式来计算:F = P × A Ff。
其中,F表示油缸的顶出力,单位为牛顿(N);P表示液压油的压力,单位为帕斯卡(Pa);A表示油缸的有效工作面积,单位为平方米(m²);Ff表示摩擦阻力,单位为牛顿(N)。
在实际工程中,我们需要根据具体的情况来确定油缸的顶出力。
下面我们将分别介绍液压油的压力、油缸的有效工作面积和摩擦阻力的计算方法。
1. 液压油的压力计算。
液压系统中的液压油通常由液压泵提供,其压力取决于液压泵的工作压力和系统的压力损失。
在计算油缸的顶出力时,我们需要根据液压系统的工作压力来确定液压油的压力。
一般来说,液压系统的工作压力可以通过液压泵的性能参数和系统的压力损失来确定。
2. 油缸的有效工作面积计算。
油缸的有效工作面积是指油缸活塞的有效工作面积,它是油缸顶出力计算中的重要参数。
油缸的有效工作面积可以通过油缸的几何尺寸和活塞直径来确定。
一般来说,油缸的有效工作面积可以通过以下公式来计算:A = π× d² / 4。
其中,A表示油缸的有效工作面积,单位为平方米(m²);π表示圆周率,约为3.14;d表示油缸活塞的直径,单位为米(m)。
3. 摩擦阻力的计算。
油缸在工作过程中会受到摩擦阻力的影响,摩擦阻力是油缸顶出力计算中需要考虑的因素之一。
摩擦阻力的大小取决于油缸的摩擦系数和工作条件。
一般来说,摩擦阻力可以通过实验或计算来确定。
在实际工程中,我们需要根据液压系统的工作压力、油缸的有效工作面积和摩擦阻力来确定油缸的顶出力。
液压机油缸设计计算公式
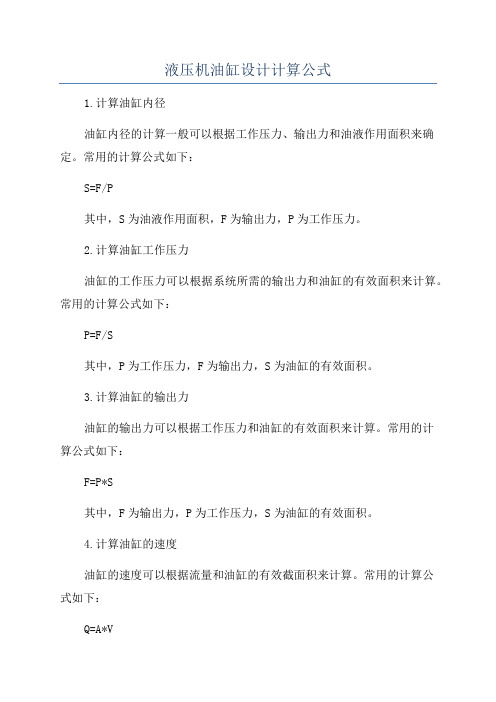
液压机油缸设计计算公式
1.计算油缸内径
油缸内径的计算一般可以根据工作压力、输出力和油液作用面积来确定。
常用的计算公式如下:
S=F/P
其中,S为油液作用面积,F为输出力,P为工作压力。
2.计算油缸工作压力
油缸的工作压力可以根据系统所需的输出力和油缸的有效面积来计算。
常用的计算公式如下:
P=F/S
其中,P为工作压力,F为输出力,S为油缸的有效面积。
3.计算油缸的输出力
油缸的输出力可以根据工作压力和油缸的有效面积来计算。
常用的计
算公式如下:
F=P*S
其中,F为输出力,P为工作压力,S为油缸的有效面积。
4.计算油缸的速度
油缸的速度可以根据流量和油缸的有效截面积来计算。
常用的计算公
式如下:
Q=A*V
其中,Q为流量,A为油缸的有效截面积,V为油缸的速度。
除了以上的计算公式外,液压机油缸的设计还需要考虑油缸的结构形式、工作环境、密封性能、轴向稳定性等因素,这些因素会直接影响油缸的性能和使用寿命。
因此,设计液压机油缸时需要综合考虑以上因素,并根据具体的应用要求进行合理的选择和优化。
综上所述,液压机油缸设计计算公式是制定液压机油缸尺寸和参数的重要依据,通过合理的计算和选择,可以确保液压机油缸的性能和使用寿命,从而实现液压系统的稳定运行和高效工作。
WY100履带式液压挖掘机斗杆油缸液压系统设计

重庆交通大学综合课程设计说明书题目:WY100履带式液压挖掘机斗杆油缸液压系统设计专业:交通建设与装备班级:装备1101班姓名:******学号:************指导教师:******摘要液压挖掘机应用面广、使用量大,在工程机械市场占有很重要的地位。
目前已成为工程机械第一主力机械。
对于液压式挖掘机而言,其设计核心就是对液压系统的设计,由于工程作业环境条件恶劣,要求实现的动作复杂,于是它对液压系统的设计提出了很高的要求,其液压系统也是工程机械液压系统中较为复杂的。
因此,对挖掘机的液压系统的分析设计对推动我国挖掘机发展具有十分重要的意义。
本次课程设计是在基于工程机械液压传动、机械原理、机械设计等方面的理论知识上针对WY100型液压挖掘机工作装置斗杆油缸部分的液压系统进行设计,同时采用伺服先导操纵系统、结合人机关系原理,使其具有造型美观、操作舒适、性能稳定可靠、具备多种作业功能的特点。
关键词:液压挖掘机,斗杆油缸,WY100ABSTRACTHydraulic excavator,a wide range of applications,the use of a large quantity,a very important position in the market engineering machinery,has now become the first main machines of mechanical engineering.For the hydraulic excavator,the core of designing excavator is hydraulic technique.Because of the bad working condition and complicated working movements of the excavator, it has high requirements for its hydraulic system.Since the excavator’s hydraulic system is the pretty complicated one in all constructional machine, the analysis and research of its hydraulic system make very important to promote the development of excavator.The task of curriculum design based on the theoretical knowledge of Hydraulic Transmission of Engineering Machinery, Theory of Machines, Mechanical Designing, etc, is the design of dipper cylinder hydraulic system for WY100 type hydraulic excavator. At the same time,adopting the servo pilot control system and combining with human-technology relationships make the excavator have beautiful sculpt,controlling comfortable,good quality,multiple functions of working.KEY WORDS:Hydraulic excavator,dipper cylinder,WY100目录摘要...................................................................I ABSTRACT............................................................II 第1章绪论.. (1)1.1 挖掘机的功用及类型 (1)1.2 发展动态 (2)1.3 液压传动应用于挖掘机上的优缺点 (3)1.4 本设计的内容 (4)第2章液压挖掘机的结构与传动原理 (5)2.1 液压挖掘机整机组成 (5)2.2 液压挖掘机结构 (6)2.3 液压挖掘机传动原理 (8)第3章挖掘机工况分析及液压系统设计 (10)3.1 液压挖掘机的工作分析 (10)3.2 挖掘机液压系统的设计要求 (15)3.3 挖掘机液压系统的分析 (16)3.4 液压系统原理图的设计 (18)第4章工作装置铲斗油缸液压系统的设计 (20)4.1 WY100液压挖掘机参数 (23)4.2 斗杆液压缸和系统压力初选 (24)4.3 斗杆液压缸设计及校核 (25)4.4 斗杆油缸主要设计参数 (27)第5章液压系统发热温升计算 (28)5.1 计算液压系统的发热功率 (28)5.2 计算液压系统散热功率 (29)第6章结论 (31)参考文献 (32)第1章绪论挖掘机是用来进行土方开挖的一种施工机械。
液压站与油缸计算公式

液压站与油缸计算公式液压站和油缸是液压系统中的两个重要组成部分。
液压站是指液压系统中的动力源,负责产生和维护液压系统所需的压力和流量;而油缸是液压系统中的执行元件,负责将液压能转化为机械能,并实现对工作对象的动力输出。
液压站与油缸的计算公式是根据液压系统的工作原理和性能参数进行推导和应用的。
以下是液压站和油缸计算的一些常用公式:1.液压站的功率计算公式:液压站的功率通常表示为其所需的功率输入,计算公式为:P=Q*p/η其中,P表示液压站的功率(单位为瓦特W),Q表示液压站输出液流量(单位为立方米/秒m³/s),p表示液压站输出液体的压力(单位为帕斯卡Pa),η表示液压泵的总效率(取值范围为0-1)。
2.液压站的流量计算公式:液压站的流量计算公式根据液压系统的需求来确定,通常为:Q=Q1+Q2其中,Q表示液压站的输出液流量(单位为立方米/秒m³/s),Q1表示液压泵的额定流量(单位为立方米/秒m³/s),Q2表示液压站其他液压元件的流量消耗(单位为立方米/秒m³/s)。
3.油缸的力计算公式:油缸的力计算公式是通过液压系统的压力和油缸的活塞面积来确定的,计算公式为:F=p*A其中,F表示油缸输出的力(单位为牛顿N),p表示液压泵输出的液体压力(单位为帕斯卡Pa),A表示油缸活塞面积(单位为平方米m²)。
4.油缸的速度计算公式:油缸的速度可以通过液压系统的流量和油缸的工作面积来计算,计算公式为:V=Q/A其中,V表示油缸的速度(单位为米/秒m/s),Q表示液压泵的输出流量(单位为立方米/秒m³/s),A表示油缸的工作面积(单位为平方米m²)。
5.液压缸的容积计算公式:液压缸的容积计算公式是根据液压缸的工作面积和行程来确定的,计算公式为:V=A*S其中,V表示液压缸的容积(单位为立方米m³),A表示液压缸的工作面积(单位为平方米m²),S表示液压缸的行程(单位为米m)。
液压油缸速度计算

液压油缸速度计算液压油缸是液压系统中的一个重要组件,用于实现机械设备的运动控制。
在液压系统设计中,液压油缸的速度计算是一个关键问题,它涉及到液压系统的性能和稳定性。
本文将介绍液压油缸速度计算的基本原理、计算方法和实际应用。
液压油缸的速度计算是指根据给定的液压系统参数和设备要求,计算出液压油缸的速度。
液压油缸的速度计算通常分为两种情况:给定压力和给定流量。
在给定压力的情况下,我们需要计算出液压油缸的速度;在给定流量的情况下,我们需要计算出液压油缸的压力。
首先,我们来介绍给定压力情况下液压油缸速度的计算方法。
在液压系统中,压力和速度之间存在着一定的关系,我们可以用流量来表示这种关系。
液压油缸的速度可以通过以下公式计算:速度=流量/面积其中,流量是液压系统提供给液压油缸的流体流量,单位通常是立方米每秒(m^3/s)或升每分钟(l/min);面积是液压油缸的有效面积,单位通常是平方米(m^2)。
要计算液压油缸的速度,我们需要先确定液压系统提供的流量和液压油缸的有效面积。
液压系统的流量可以通过流量计或液压泵的参数来确定;液压油缸的有效面积可以通过油缸的几何参数计算得到。
将流量和面积代入上述公式即可计算出液压油缸的速度。
接下来,我们来介绍给定流量情况下液压油缸压力的计算方法。
在液压系统中,流量和压力之间存在着一定的关系,我们可以用速度来表示这种关系。
液压油缸的压力可以通过以下公式计算:压力=流量/速度其中,流量和速度的单位同上述描述。
要计算液压油缸的压力,我们需要先确定液压系统提供的流量和液压油缸的速度。
液压系统的流量可以通过流量计或液压泵的参数来确定;液压油缸的速度可以通过实测或计算得到。
将流量和速度代入上述公式即可计算出液压油缸的压力。
液压油缸速度的计算对于液压系统设计和运行非常重要,它直接影响到液压系统的性能和稳定性。
合理的速度计算可以确保液压油缸的工作效率和安全性。
同时,我们还需要考虑到液压油缸的工作条件和实际需求,如负载要求、运动轨迹和工作环境等。
液压系统设计与计算
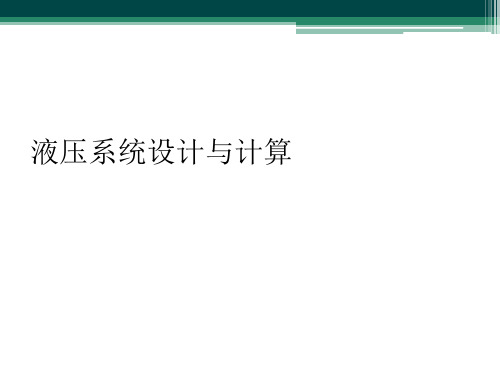
(2)确定执行元件的主要结构参数
以缸为例,主要结构尺寸指缸的内径D和活塞杆的直 径d,计算后按系列标准值确定D和d。
对有低速运动要求的系统,尚需对液压缸有效工作面 积进行验算,即应保证:
式中
A q min v min
(10.8)
:A—液压缸工作腔的有效工作面积;
v m in—控制执行元件速度的流量阀最小稳定流量;
17
1.3.2 选择液压泵
先根据设计要求和系统工况确定泵的类型, 然后根据液压泵的最大供油量和系统工作压力来 选择液压泵的规格。
(1) 液压泵的最高供油压力
ppp pl (10.11)
式中: p—执行元件的最高工作压力;
pl —进油路上总的压力损失。
18
(2)确定液压泵的最大供油量 液压泵的最大供油量为:
khAt (10.15)
式中: A—油箱的散热面积;
t —液压系统的温升;
k h —油箱的散热系数,其值可查阅液压设计手册。
系统的温升为 t kh A
(10.16)
计算温升值如果超过允许值,应采取适当的冷却措施。
27
1.5 绘制正式工作图和编制技术文件
10.1.5.1 绘制正式工作图 正式工作图包括液压系统原理图、液压系统装配图、
30
机床的外形示意图。
1-左主轴头;2-夹具;3-右主轴头;4-床身;5-工件
31
2.1 确定对液压系统的工作要求
根据加工要求,刀具旋转由机械传动来实现;主轴头 沿导轨中心线方向的“快进一工进—快退—停止”工作循环 拟采用液压传动方式来实现。故拟选定液压缸作执行机构。
考虑到车削进给系统传动功率不大,且要求低速稳定 性好,粗加工时负载有较大变化,故拟选用调速阀、变量 泵组成的容积节流调速方式。
液压缸设计步骤和液压缸计算方法档
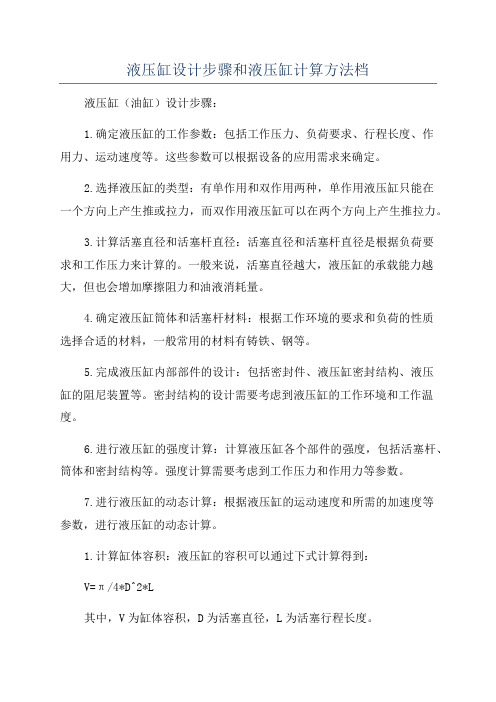
液压缸设计步骤和液压缸计算方法档液压缸(油缸)设计步骤:1.确定液压缸的工作参数:包括工作压力、负荷要求、行程长度、作用力、运动速度等。
这些参数可以根据设备的应用需求来确定。
2.选择液压缸的类型:有单作用和双作用两种,单作用液压缸只能在一个方向上产生推或拉力,而双作用液压缸可以在两个方向上产生推拉力。
3.计算活塞直径和活塞杆直径:活塞直径和活塞杆直径是根据负荷要求和工作压力来计算的。
一般来说,活塞直径越大,液压缸的承载能力越大,但也会增加摩擦阻力和油液消耗量。
4.确定液压缸筒体和活塞杆材料:根据工作环境的要求和负荷的性质选择合适的材料,一般常用的材料有铸铁、钢等。
5.完成液压缸内部部件的设计:包括密封件、液压缸密封结构、液压缸的阻尼装置等。
密封结构的设计需要考虑到液压缸的工作环境和工作温度。
6.进行液压缸的强度计算:计算液压缸各个部件的强度,包括活塞杆、筒体和密封结构等。
强度计算需要考虑到工作压力和作用力等参数。
7.进行液压缸的动态计算:根据液压缸的运动速度和所需的加速度等参数,进行液压缸的动态计算。
1.计算缸体容积:液压缸的容积可以通过下式计算得到:V=π/4*D^2*L其中,V为缸体容积,D为活塞直径,L为活塞行程长度。
2.计算活塞面积:根据活塞直径计算活塞面积,可以通过下式计算得到:A=π/4*D^2其中,A为活塞面积,D为活塞直径。
3.计算活塞杆面积:根据活塞杆直径计算活塞杆面积,可以通过下式计算得到:A'=π/4*D'^2其中,A'为活塞杆面积,D'为活塞杆直径。
4.计算推力:根据工作压力和活塞面积计算液压缸的推力,可以通过下式计算得到:F=P*A其中,F为液压缸的推力,P为工作压力,A为活塞面积。
5.计算液压缸的速度:液压缸的速度可以通过可控阀门来调节,一般使用油流量来计算液压缸的速度,可以通过下式计算得到:V=Q/A其中,V为液压缸的速度,Q为油流量,A为活塞面积。
油缸(液压缸)设计指导书
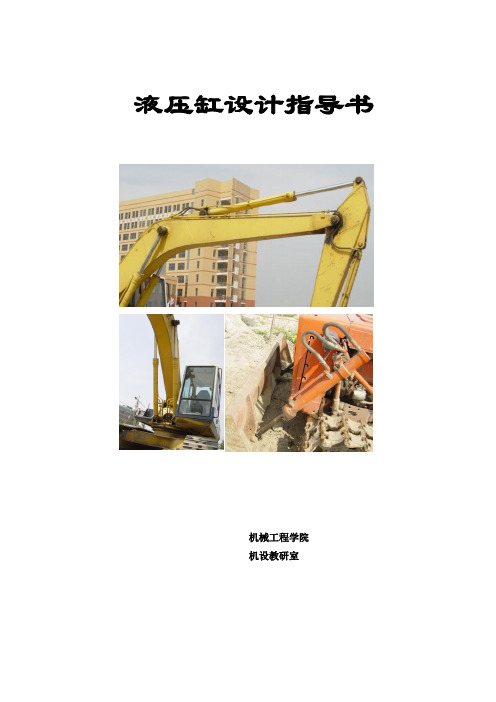
液压缸设计指导书机械工程学院机设教研室一、设计目的油缸是液压传动系统中实现往复运动和小于360°回摆运动的液压执行元件。
具有结构简单,工作可靠,制造容易以及使用维护方便、低速稳定性好等优点。
因此,广泛应用于工业生产各部门。
其主要应用有:工程机械中挖掘机和装载机的铲装机构和提升机构,起重机械中汽车起重机的伸缩臂和支腿机构,矿山机械中的液压支架及采煤机的滚筒调高装置,建筑机械中的打桩机,冶金机械中的压力机,汽车工业中自卸式汽车和高空作业车,智能机械中的模拟驾驶舱、机器人、火箭的发射装置等。
它们所用的都是直线往复运动油缸,即推力油缸。
所以进一步研究和改进液压缸的设计制造,提高液压缸的工作寿命及其性能,对于更好的利用液压传动具有十分重要的意义。
通过学生自己独立地完成指定的课程设计任务,提高理论联系实际、分析问题和解决问题的能力,学会查阅参考书和工具书的方法,提高编写技术文件的能力,进一步加强设计计算和制图等基本技能的训练,为毕业后成为一名出色的机械工程师打好基础。
为此,编写了这本“液压缸设计指导书”,供机械专业学生学习液压传动课程及课程设计时参考。
二、设计要求1、每个参加课程设计的学生,都必须独立按期完成设计任务书所规定的设计任务。
2、设计说明书和设计计算书要层次清楚,文字通顺,书写工整,简明扼要,论据充分。
计算公式不必进行推导,但应注明公式中多符号的意义,代入数据得出结果即可。
3、说明书要有插图,且插图要清晰、工整,并选取适当此例。
说明书的最后要附上草图。
4、绘制工作图应遵守机械制图的有关规定,符合国家标准。
5、学生在完成说明书、图纸后,准备进行答辩,最后进行成绩评定。
三、设计任务设计任务由指导教师根据学生实际情况及所收集资料情况确定。
最后人均一题,避免重复。
四、设计依据和设计步骤油缸是液压传动的执行元件,它与主机及主机的工作结构有着直接的联系。
不同的机型和工作机构对油缸则有不同的工作要求。
液压油缸的设计与计算

目录一、设计要求——————————————————————-11、目的—————————————————————————12、题目—————————————————————————1二、总述————————————————————————-21、作者的话——————————————————————--22、设计提要———————————————————————3三、各零部件的设计及验算————————————————-51、缸筒设计———————————————————————52、法兰设计———————————————————————143、活塞设计———————————————————————194、活塞杆设计——————————————————————215、缓冲装置和排气阀设计—————————————————26四、外接线路和程序———————————————————-271、液压设配外接线路———————————————————272、操作板————————————————————————283、程序地址分配—————————————————————294、芯片接线图——————————————————————315、PLC程序指令—————————————————————-33五、参考文献———————————————————————38一、设计要求1、目的①、培养学生综合运用所学的基础理论和专业知识,独立进行机电控制系统的初步设计工作,并结合设计或实验研究课题进一步巩固和扩大知识领域。
②、培养学生搜集、阅读和综合分析参考资料,运用各种标准和工具书籍以及编写技术文件的能力,提高计算、绘图等基本技能。
③、培养学生掌握机电产品的一般程序和方法,进行工程师基本素质的训练。
④、树立正确的设计思想及严肃认真的工作作风。
2、题目液压油缸的压力和速度控制①、执行元件:液压油缸;②、传动方式:电液比例控制;③、控制方式:单片微机控制、PLC控制;④、控制要求:速度控制、推力控制;⑤、主要设计参数:油缸工作行程————600、400mm;额定工作油压————4MP;移动负载质量————1000、2000kg;负载移动阻力————5000、10000N;移动速度控制————3、6m/min。
液压油缸压力计算公式 液压油缸设计计算公式
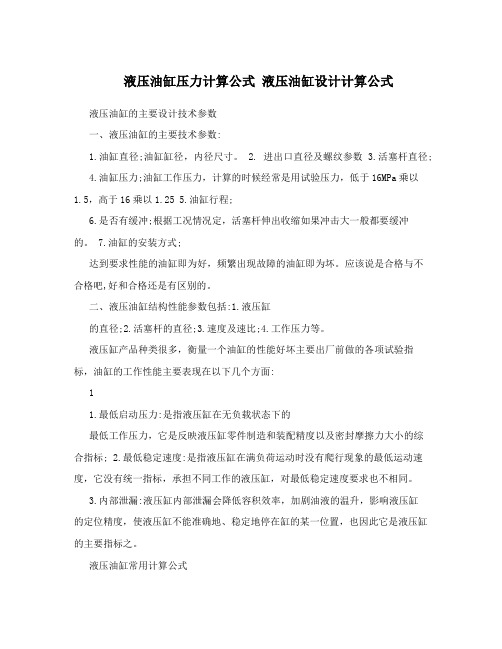
液压油缸压力计算公式液压油缸设计计算公式液压油缸的主要设计技术参数一、液压油缸的主要技术参数:1.油缸直径;油缸缸径,内径尺寸。
2. 进出口直径及螺纹参数3.活塞杆直径;4.油缸压力;油缸工作压力,计算的时候经常是用试验压力,低于16MPa乘以1.5,高于16乘以1.25 5.油缸行程;6.是否有缓冲;根据工况情况定,活塞杆伸出收缩如果冲击大一般都要缓冲的。
7.油缸的安装方式;达到要求性能的油缸即为好,频繁出现故障的油缸即为坏。
应该说是合格与不合格吧,好和合格还是有区别的。
二、液压油缸结构性能参数包括:1.液压缸的直径;2.活塞杆的直径;3.速度及速比;4.工作压力等。
液压缸产品种类很多,衡量一个油缸的性能好坏主要出厂前做的各项试验指标,油缸的工作性能主要表现在以下几个方面:11.最低启动压力:是指液压缸在无负载状态下的最低工作压力,它是反映液压缸零件制造和装配精度以及密封摩擦力大小的综合指标; 2.最低稳定速度:是指液压缸在满负荷运动时没有爬行现象的最低运动速度,它没有统一指标,承担不同工作的液压缸,对最低稳定速度要求也不相同。
3.内部泄漏:液压缸内部泄漏会降低容积效率,加剧油液的温升,影响液压缸的定位精度,使液压缸不能准确地、稳定地停在缸的某一位置,也因此它是液压缸的主要指标之。
液压油缸常用计算公式液压油缸常用计算公式项目公式液压油缸面积(cm 2 ) A =πD 2 /4 液压油缸速度 (m/min) V = Q / A 液压油缸需要的流量 (l/min)液压油缸出力 (kgf) 泵或马达流量 (l/min)Q=V×A/10=A×S/10t F = p × AF = (p × A) , (p×A) ( 有背压存在时) Q = q × n / 1000符号意义D :液压缸有效活塞直径 (cm) Q :流量 (l / min)2V :速度 (m/min) S :液压缸行程 (m) t :时间 (min) p :压力 (kgf /cm 2 ) q :泵或马达的几何排量 (cc/rev) n :转速( rpm )泵或马达转速 (rpm) Q :流量 (l / min) n = Q / q×1000 泵或马达扭矩(N.m) T = q × p / 20π液压所需功率(kw) P = Q × p / 612 管内流速 (m/s) d :管内径 (mm) v = Q ×21.22 / d 2U :油的黏度 (cst)管内压力降 (kgf/cm 2 )P=0.000698×USLQ/d 4 S :油的比重非标液压、机电、试验、工控设备开发研制。
液压系统的设计与计算步骤

液压系统的设计与计算:
1、根据液压系统的要求设计液压系统,拟订油路图。
2、计算与选型
(1)油缸的工作压力、面积和流量
柱塞上的外部载荷P:(包括压板、板坯、密封阻力、工作载荷和柱塞)。
柱塞直径d:(柱塞总的工作面积F =P/p,每个缸子的柱塞面积为F/n)。
油缸的流量Q。
选型:
(2)油泵的选择
油泵工作压力的确定
低压泵工作压力(p d)的确定:(液压油流速取3.5m/s)
包括:板坯、压板、柱塞、摩擦阻力、局部压损和沿程压损。
高压泵工作压力(p g)的确定:
包括:主要指系统压力、板坯、压板、柱塞、摩擦阻力、局部压损和沿程压损。
油泵流量的确定:
总流量Q bz=K·Q z (k取1.2)
高压泵的流量:Q g=VxF/10(V取0.24m/min )
低压泵的流量:Q d= Q bz- Q g
根据流量和压力选型:
油泵电机功率的确定:
(3)阀的选择
(4)油管的计算(内径与壁厚)与选择
(5)液压系统性能的验算(包括压力损失的验算和系统发热的验算)
(6)柱塞缸壁厚的计算。
液压系统的设计与计算

下午2时22分
18
五、验算液压系统性能
液压系统初步确定后就需对系统的有关性能加以验算,以检测 系统的设计质量,并对液压系统进行完善和改进。根据液压系 统的不同,需要验算的项目也有所不同,但一般的液压系统都 要进行回路压力损失和发热温升的验算。
1. 系统压力损失的验算
p pl p pv
液压系统的压力损失包括沿程、局部损失和阀的局部损失。
液压与液力传动
第九章 液压系统的设计与计算
液压系统的设计与计算是液压机械总设计的一部分, 是对前面各章内容的综合运用。总设计过程为: (1)根据整机的用途、特点和性能,明确对液压系统的 设计任务。 (2)对工况进行分析,确定液压系统的主要参数; (3)拟定出合理的液压系统原理图; (4)计算和选择液压元件的规格 (5)演算液压系统的性能 (6)绘制工作图、编写技术文件。
要求验算液压缸尺寸 即
A qmin
vmin
• 在D和d确定之后,可求得液压缸所需流量为:
q1=vmaxA
下午2时22分
13
3 执行元件工况图
工况图是指液压执行元件结构参数确定之后,根 据主机工作循环,算出不同阶段中的实际工作压力、 流量和功率随时间变化图,如图所示。
工况图反映了液压系统在整个工作循环中,三个参 数的随时间变换情况。
动摩擦因数0.1, 液压执行元件为液压元件。
设计液压缸的面积和确定液压系统控制图
下午2时22分
21
一、负载分析
(1)切削力:
Fe 22.5DS0.8(HB)0.6
式中,Fe为钻削力,N; D为钻头直径,mm;S为每 转进给量,mm; HB为工件硬度。
对于直径为13.9mm的孔,转速n1=360r/min, S1=0.147mm/r; 对于直径为8.5mm的孔,转速n2= 550r/min, S2=0.096mm/r; 带入上式,可得:
- 1、下载文档前请自行甄别文档内容的完整性,平台不提供额外的编辑、内容补充、找答案等附加服务。
- 2、"仅部分预览"的文档,不可在线预览部分如存在完整性等问题,可反馈申请退款(可完整预览的文档不适用该条件!)。
- 3、如文档侵犯您的权益,请联系客服反馈,我们会尽快为您处理(人工客服工作时间:9:00-18:30)。
设计说明和设计计算
1. 概述
常州力安液压设备有限公司在全国同行中具有多年丰富的设计、制造、安装、调试、运行维护的经验和及时、准确的售后服务,已建立了一套完整的设计、制造、服务质量保证体系,于二零零二年通过ISO9002 质量保证体系认证。
1.1 液压油缸:
a.活塞油缸
活塞油缸材料为:42CrMo 锻件,缸体粗加工后进行调质处理,性能优异,质量稳定可靠。
缸体内孔的加工工艺:我公司采用的是推镗+珩磨工艺。
推镗工艺是我公司在实践中发展起来的。
缸体内径尺寸公差不低于GB1800 中的H8。
缸体内径圆度公差应不低于GB1184中8级。
内表面母线的直线度公差不大于1000:0.1,全长上不大于0.15mm。
缸体法兰端面圆跳动公差不低于GB1184中8级。
缸体法兰端面与缸体轴线垂直度公差不低于GB1184中
7级。
缸体内表面粗糙度为GB1031中Ra0.4。
缸体内表面珩磨。
珩磨采用美国善能公司进口珩磨机,可以提高表面质量,降低粗糙度,改善表面润滑条件,减少密封件的磨损。
b・驱动段本体
驱动段本体材料为:42CrMo 锻件,调质处理。
驱动段本体达到的质量指标为:达到的加工精度要求:导向段外径公差不低于GB1801中的f7,圆柱度公差不低于GB1189中的8级,母线直线度公差不大于1000 - 0.1;端面对轴心心线垂直度公差不低于GB1184 中的7级;导向段表面粗糙度不低于
Ra0.4am。
导向段表面镀双层铬,第一层镀0.04~0.05mm乳白铬层(有效防腐层),第二层镀0.04~0.05mm硬铬层(有效抗磨)。
c.密封件
油缸各固定密封部位选用材料为耐油橡胶的O 形密封圈,其胶料硬
度、间隙大小及沟槽尺寸均从GB1236 中选取。
油缸的动密封在高压
40MPa,低压0.5MPa时均有良好的密封性能和较低的启动压力,油缸内部的动密封件均采用MERKE密封圈,耐久性好,无论高压、低压均密封可靠,且启动压力低(v 0.5MPa),在工程上广为采用。
静密封件采用PARKE公司生产的0形密封圈。
油缸的动密封件有足够的抗撕裂强度,耐压32MPa 并应具有耐油、防水、永久变形小、摩阻力小、无粘着、抗老化等良好性能。
这些密封件的耐压性都在32MPa 以上,保证使用寿命大于10 年以上。
d・驱动段底盖、活塞油缸底盖
材料为:42CrMo锻件,调质处理。
缸盖与相关件配合处的圆柱度公差应不低于GB1184中8级,同轴度公差应不低于7级,缸盖与缸体配合的端面与缸盖轴线垂直度公差不低于GB1184中7级,端面圆跳动公差不低于GB1184 中7 级。
e. 导向带
导向带材料采用德国知名品牌MERKEL 公司的复合材料,导向面配合尺寸公差不低于GB1800中的H8与GB1801中f7 ,导向面、配合面的圆柱度公差不低于GB1184中8级,导向面与配合面的同轴度公差不低于GB1184中8级,导向面粗糙度不低于GB1031中Ra0.4。
f. 驱动段后膨胀管
驱动段后膨胀管材料:304,螺纹T460X16和YS 420X16采用GB197 中精度等级7A。
2设计计算
2.1液压缸计算
2)驱动段本体产生推力计算
4)驱动段本体壁厚计算
6)驱动段本体强度校核
7)拉杆强度校核
10)驱动段底盖连接螺钉计算
2. 2液压系统计算
1)系统最高工作压力、最大工作流量,电机功率的计算
2)油箱容积的计算
3)液压系统管路管径的设计计算。