液压缸计算公式
液压缸设计计算范文
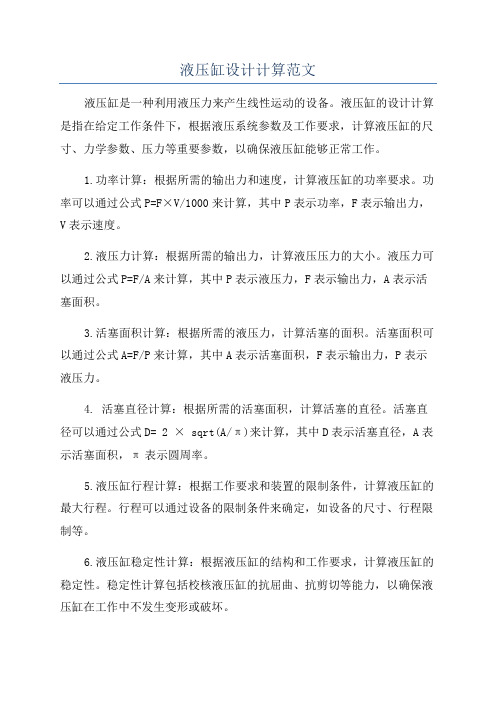
液压缸设计计算范文液压缸是一种利用液压力来产生线性运动的设备。
液压缸的设计计算是指在给定工作条件下,根据液压系统参数及工作要求,计算液压缸的尺寸、力学参数、压力等重要参数,以确保液压缸能够正常工作。
1.功率计算:根据所需的输出力和速度,计算液压缸的功率要求。
功率可以通过公式P=F×V/1000来计算,其中P表示功率,F表示输出力,V表示速度。
2.液压力计算:根据所需的输出力,计算液压压力的大小。
液压力可以通过公式P=F/A来计算,其中P表示液压力,F表示输出力,A表示活塞面积。
3.活塞面积计算:根据所需的液压力,计算活塞的面积。
活塞面积可以通过公式A=F/P来计算,其中A表示活塞面积,F表示输出力,P表示液压力。
4. 活塞直径计算:根据所需的活塞面积,计算活塞的直径。
活塞直径可以通过公式D= 2 × sqrt(A/π)来计算,其中D表示活塞直径,A表示活塞面积,π表示圆周率。
5.液压缸行程计算:根据工作要求和装置的限制条件,计算液压缸的最大行程。
行程可以通过设备的限制条件来确定,如设备的尺寸、行程限制等。
6.液压缸稳定性计算:根据液压缸的结构和工作要求,计算液压缸的稳定性。
稳定性计算包括校核液压缸的抗屈曲、抗剪切等能力,以确保液压缸在工作中不发生变形或破坏。
7.寿命计算:根据液压缸的设计参数和工作条件,计算液压缸的寿命。
寿命计算包括根据液压缸的设计寿命和使用条件,计算液压缸的可靠性和寿命预测。
在进行液压缸设计计算时,需要考虑以下几个重要因素:1.工作条件:包括工作压力、工作温度、介质类型等。
2.力学要求:包括输出力、速度、行程等。
3.设备限制:包括装置的尺寸、行程限制等。
4.安全要求:包括液压缸的稳定性、可靠性等。
在进行液压缸设计计算时,需要根据实际情况进行具体分析。
一般来说,液压缸的设计计算是一个复杂的工作,需要涉及力学、流体力学、材料力学等多个学科的知识,并以此为基础进行具体计算。
液压计算常用公式

溢流阀的保养及故障排除减压阀的保养及故障排除流量控制阀的保养及故障排除方向控制阀的保养及故障排除的油封漏油B 机械操作的阀芯不能动作1、排油口有背压2、压下阀芯的凸块角度过大3、压力口及排油口的配管错误同上凸块的角度应在30°以上。
修正配管。
C 电磁阀的线圈烧坏1、线圈绝缘不良2、磁力线圈铁芯卡住3、电压过高或过低4、转换的压力在规定以上5、转换的流量在规定以上6、回油接口有背压更换电磁线圈。
更换电磁圈铁芯。
检查电压适切调整。
降下压力,检查压力计。
更换流量大小的控制阀低压用为1.0kgf/cm²,高压用为kgf/cm²回油口直接接回油箱,尤其是泄油(使用外部泄油)D 液控阀不会作动1、液控压力不足2、阀芯胶着,分解清理之,洗净3、灰尘进入,分解清理之,洗净液控压力为3.5kgf/cm²以上,在全开或中立回油阀须加装止回阀使形成液控压力。
分解清理之,洗净。
电磁阀的保养及故障排除故障原因处置A 动作不良1、因弹簧不良致滑轴无法恢复至原位置2、阀芯的动作不良及动作迟缓3、螺栓上紧过度或因温度上升至本体变形4、电气系统不良更换弹簧。
1、洗净控制阀内部除去油中的混入物。
2、检查过滤器,必要时洗涤过滤器或更换液压油。
3、检查滑轴的磨耗情形,必要时须更换。
松开螺栓上紧程度(对角交互上紧) 检查插入端子部的接触状态,确认电磁线圈的动作是否正常,如果线圈断线或烧损时须更换。
B 磁力线圈噪音及烧损1、负荷电压错误2、灰尘等不纯物质进入3、电磁线圈破损,烧损4、阀芯的异常磨耗检查电压,使用适当的电磁线圈。
除去不纯物。
更换更换C 内部漏油大外部漏油1、封环损伤2、螺栓松更换再上紧液压机器其他故障及排除共振、振动及噪音故障原因处置A 弹簧与弹簧共振二组以上控制阀的弹簧的共振(如溢流阀及溢流阀、溢流阀及顺序阀、溢流阀及止回阀)1、将弹簧的设定压力错开,10kgf/cm²或10%以上。
液压油缸吨位计算公式举例说明

液压油缸吨位计算公式举例说明液压油缸的吨位计算公式是根据液压油缸的面积和工作压力来计算的。
液压油缸是一种将液压能转化为机械能的装置,它利用液压力的传递来产生力和位移。
在液压系统中,液压油缸常常用于各种工业机械和工程设备中,如机床、挖掘机、升降机等。
吨位是液压油缸所能产生的力的单位,一般以吨(Ton)为单位,1吨等于1000千克。
液压油缸的吨位计算公式如下:吨位=液压油缸的有效面积×工作压力其中吨位是液压油缸所能产生的力,单位为吨;液压油缸的有效面积是指液压油缸的有效工作面积,单位为平方厘米;工作压力是指液压油缸所受的工作压力,单位为兆帕(MPa)。
举个例子来说明液压油缸吨位的计算公式:假设液压油缸的有效面积为100平方厘米,工作压力为10兆帕,我们可以通过公式计算该液压油缸的吨位。
吨位=液压油缸的有效面积×工作压力=100平方厘米×10兆帕=1000平方厘米兆帕根据国际单位制换算规则,1平方厘米兆帕等于1千牛顿。
所以该液压油缸的吨位为1000千牛顿。
进一步换算,1千牛顿等于0.1吨,所以该液压油缸的吨位为0.1吨。
这个例子说明了如何通过液压油缸的有效面积和工作压力来计算液压油缸的吨位。
使用这个计算公式,我们可以确定液压油缸所需的吨位,从而选择合适的液压油缸进行工作。
需要注意的是,液压油缸吨位的计算公式只是一个理论值,实际情况中还需要考虑液压系统的实际工作情况、机械装置的负载要求、安全系数等因素。
在选择和使用液压油缸时,还需要根据具体情况进行综合考虑和评估,以确保安全可靠地完成工作任务。
液压缸计算公式
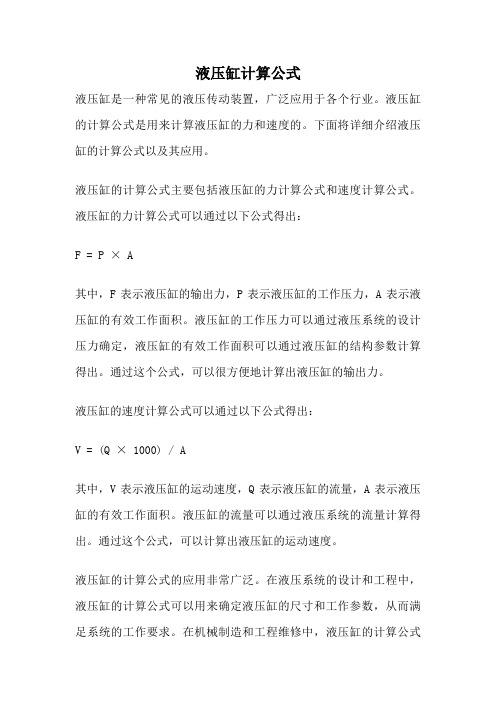
液压缸计算公式液压缸是一种常见的液压传动装置,广泛应用于各个行业。
液压缸的计算公式是用来计算液压缸的力和速度的。
下面将详细介绍液压缸的计算公式以及其应用。
液压缸的计算公式主要包括液压缸的力计算公式和速度计算公式。
液压缸的力计算公式可以通过以下公式得出:F = P × A其中,F表示液压缸的输出力,P表示液压缸的工作压力,A表示液压缸的有效工作面积。
液压缸的工作压力可以通过液压系统的设计压力确定,液压缸的有效工作面积可以通过液压缸的结构参数计算得出。
通过这个公式,可以很方便地计算出液压缸的输出力。
液压缸的速度计算公式可以通过以下公式得出:V = (Q × 1000) / A其中,V表示液压缸的运动速度,Q表示液压缸的流量,A表示液压缸的有效工作面积。
液压缸的流量可以通过液压系统的流量计算得出。
通过这个公式,可以计算出液压缸的运动速度。
液压缸的计算公式的应用非常广泛。
在液压系统的设计和工程中,液压缸的计算公式可以用来确定液压缸的尺寸和工作参数,从而满足系统的工作要求。
在机械制造和工程维修中,液压缸的计算公式可以用来评估液压缸的工作性能和故障排除。
液压缸的计算公式还可以用来优化液压系统的设计。
通过合理选择液压缸的尺寸和工作参数,可以提高液压系统的效率和稳定性。
同时,液压缸的计算公式也可以用来对液压系统进行性能测试和评估,为系统的优化提供依据。
液压缸的计算公式是液压系统设计和工程应用中的重要工具。
通过合理应用这些公式,可以方便地计算液压缸的力和速度,从而满足系统的工作要求。
液压缸的计算公式的应用范围广泛,对于液压系统的设计、制造和维修都具有重要意义。
希望本文的介绍对读者有所帮助。
液压缸压力计算公式及单位
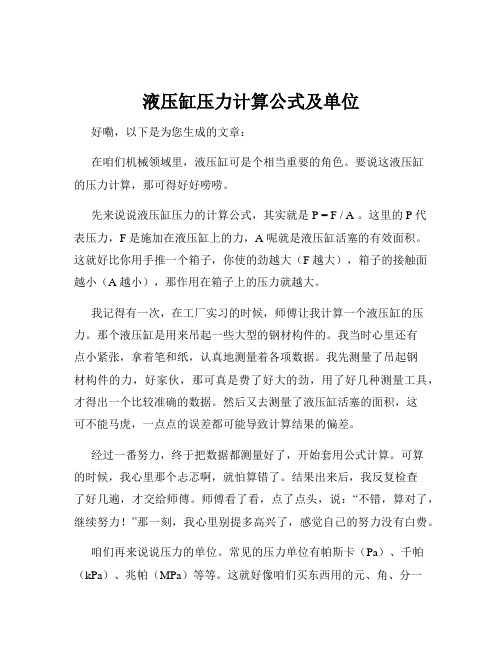
液压缸压力计算公式及单位好嘞,以下是为您生成的文章:在咱们机械领域里,液压缸可是个相当重要的角色。
要说这液压缸的压力计算,那可得好好唠唠。
先来说说液压缸压力的计算公式,其实就是 P = F / A 。
这里的 P 代表压力,F 是施加在液压缸上的力,A 呢就是液压缸活塞的有效面积。
这就好比你用手推一个箱子,你使的劲越大(F 越大),箱子的接触面越小(A 越小),那作用在箱子上的压力就越大。
我记得有一次,在工厂实习的时候,师傅让我计算一个液压缸的压力。
那个液压缸是用来吊起一些大型的钢材构件的。
我当时心里还有点小紧张,拿着笔和纸,认真地测量着各项数据。
我先测量了吊起钢材构件的力,好家伙,那可真是费了好大的劲,用了好几种测量工具,才得出一个比较准确的数据。
然后又去测量了液压缸活塞的面积,这可不能马虎,一点点的误差都可能导致计算结果的偏差。
经过一番努力,终于把数据都测量好了,开始套用公式计算。
可算的时候,我心里那个忐忑啊,就怕算错了。
结果出来后,我反复检查了好几遍,才交给师傅。
师傅看了看,点了点头,说:“不错,算对了,继续努力!”那一刻,我心里别提多高兴了,感觉自己的努力没有白费。
咱们再来说说压力的单位。
常见的压力单位有帕斯卡(Pa)、千帕(kPa)、兆帕(MPa)等等。
这就好像咱们买东西用的元、角、分一样,不同的场合用不同的单位。
比如说,一般小一点的压力,咱们就用帕斯卡;要是压力比较大,像液压缸这种能承受大力的,就常用兆帕。
比如说,汽车的液压制动系统,里面的液压缸压力就不是很大,可能用千帕来表示就比较合适。
而像大型起重机的液压缸,那压力可就大了去了,就得用兆帕来衡量。
在实际应用中,准确计算液压缸的压力非常重要。
如果压力计算不准确,可能会导致设备无法正常工作,甚至出现安全事故。
这可不是闹着玩的!所以,咱们在计算的时候,一定要认真仔细,不能有半点马虎。
总之,液压缸压力的计算和单位虽然看起来有点复杂,但只要咱们掌握了方法,多实践,多积累经验,就一定能轻松应对。
液压计算常用公式
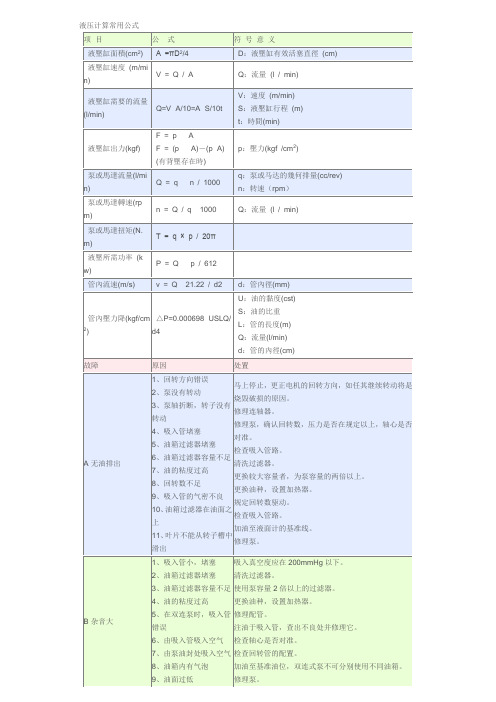
液压计算常用公式溢流阀的保养及故障排除减压阀的保养及故障排除流量控制阀的保养及故障排除方向控制阀的保养及故障排除电磁阀的保养及故障排除3、电磁线圈破损,烧损4、阀芯的异常磨耗更换更换C 内部漏油大外部漏油1、封环损伤2、螺栓松更换再上紧液压机器其他故障及排除共振、振动及噪音故障原因处置A 弹簧与弹簧共振二组以上控制阀的弹簧的共振(如溢流阀及溢流阀、溢流阀及顺序阀、溢流阀及止回阀)1、将弹簧的设定压力错开,10kgf/cm²或10%以上。
2、改变一方弹簧的感度。
3、使用遥控溢流阀。
B 弹簧及配管共振控制阀的弹簧与空气的共振(如排泄管露长的溢流阀,压力计内管及配管的共振)1、改变弹簧的感度2、管路的长度、大小及材质变更。
(用手捉住时,音色会改变时)3、利用适当的支持,使管路不致振动。
(用手捉住时,声音便停止时)C 弹簧与空气共振控制阀的弹簧与空气共振(如溢流阀、阀口的空气,止回阀口的空气等)将油路的空气完全排出D 液压缸共振因有空气引起液压缸的振动将空气排出。
尤其在仅有单侧进油时油封密封必须充分上油或涂上牛脂状之二硫化铜E 油流动的声音油流动的噪音、油箱、管路的振动如(1)溢流阀的油箱接口流出的油冲到油箱的声音(2)调整阀油箱口处有L形是的声音(3)二台泵的排出侧附近行使合流时的声音更换排油管路。
管路应尽可能使用软管。
流动安定后,方可使其合流。
F 油箱共振油箱的共鸣声1、油箱顶板使用较厚的铁板。
2、顶板与泵、电机之间再铺上一层铁饼内或橡胶。
3、泵、电机不装于油箱上方,而另外以橡皮管连接。
G 阀的切换声滑轴阀的切换声1、降低引导压力。
2、加上节流阀。
H 配管冲击声控制阀变换时,因压力急激变动致配管发出冲击声更换控制阀或管路,降低压力的急激变动,使用特殊轴塞。
如闭路满油阀的油路I 液控单向阀追击声液控单向阀的二次侧产生背压时的追击声1、消除二次侧的背压2、提高液控压力3、使用外部放泄的液控单向阀流量不足、压力不足1、泵没有排油详见泵的保养及故障排除A液压缸、液压马达等不规则之连动油温显著上升。
液压油缸推力计算公式

液压油缸推力计算公式
液压油缸推力计算公式是液压系统领域中非常重要的一种计算方法。
液压油缸是液压系统中的重要组成部分,负责将压力转化为力,推动机械设备运转,因此其推力大小的计算非常关键。
液压油缸推力计算公式的基本原理是根据液压油缸的几何尺寸和液压系统的工作压力,计算出液压油缸的理论推力大小。
液压油缸推力的大小受到多种因素的影响,如液压油缸的内径、活塞杆的直径、液压系统的工作压力等。
液压油缸推力计算公式的具体表达式如下:
F=π/4×D²×P
其中,F表示液压油缸的推力大小,单位为牛顿(N)或千克力(kgf);π为圆周率,约等于3.14;D为液压油缸的内径,单位为米(m)或毫米(mm);P为液压系统的工作压力,单位为帕斯卡(Pa)或巴(bar)。
由公式可以看出,液压油缸的推力大小与液压油缸的内径和液压系统的工作压力成正比,而与液压油缸的活塞杆直径无关。
因此,在设计液压系统时,需要根据液压油缸的推力需求和工作环境压力等因素,合理选择液压油缸的内径和液压系统的工作压力,以确保液压油缸的推力能够满足机械设备的需求。
需要注意的是,液压油缸的实际推力大小与其理论推力大小存在一定的误差。
这是由于液压油缸的摩擦力、密封性能、活塞杆的弯曲等因素的影响所导致的。
因此,在实际应用中,需要根据实际情况对液压油缸的推力进行调整和修正,以确保其能够正常工作。
液压油缸推力计算公式是液压系统设计和应用中非常重要的一种计算方法。
合理地应用该公式,可以有效地计算出液压油缸的理论推力大小,为机械设备的正常运行提供有力的支持。
液压缸设计计算公式
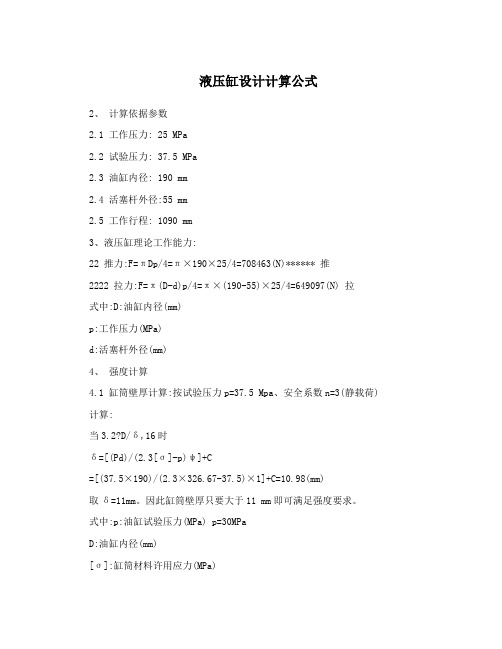
液压缸设计计算公式2、计算依据参数2.1 工作压力: 25 MPa2.2 试验压力: 37.5 MPa2.3 油缸内径: 190 mm2.4 活塞杆外径:55 mm2.5 工作行程: 1090 mm3、液压缸理论工作能力:22 推力:F=πDp/4=π×190×25/4=708463(N)****** 推2222 拉力:F=π(D-d)p/4=π×(190-55)×25/4=649097(N) 拉式中:D:油缸内径(mm)p:工作压力(MPa)d:活塞杆外径(mm)4、强度计算4.1 缸筒壁厚计算:按试验压力p=37.5 Mpa、安全系数n=3(静载荷) 计算:当3.2?D/δ,16时δ=[(Pd)/(2.3[σ]-p)ψ]+C=[(37.5×190)/(2.3×326.67-37.5)×1]+C=10.98(mm)取δ=11mm。
因此缸筒壁厚只要大于11 mm即可满足强度要求。
式中:p:油缸试验压力(MPa) p=30MPaD:油缸内径(mm)[σ]:缸筒材料许用应力(MPa)[σ] =σ/n=980/3=326.67(M Pa) bσ:缸筒材料的抗拉强度(MPa) b查手册:27SiMn的σ=980MPa bn:取安全系数n=3(静载荷)ψ:强度系数(当为无缝钢管时ψ=1)C:计入壁厚公差及腐蚀的附加厚度(一般应将壁厚圆整至标准厚度值)4.4 活塞杆螺纹连接强度计算活塞杆试验最大拉力:22 P=π(D-d)p/422 =π×(190-55)×37.5/4=973646(N)活塞杆危险断面处的拉应力:2 σ =P/ [π×d/4] 12 =973646/[π×45.2/4]=607.1(MPa)式中:P:活塞杆试验最大拉力(N)D:油缸内径(mm)d:活塞杆外径(mm)d:活塞杆危险断面处直径,初选是活塞杆O型圈沟槽1 (mm)σ:活塞杆材料屈服强度(MPa) s查手册 42CrMo钢调质,取σ=930MPa sn:安全系数,取n=1.5因为σ ?[σ]=620MPa,所以螺纹强度能够满足要求。
- 1、下载文档前请自行甄别文档内容的完整性,平台不提供额外的编辑、内容补充、找答案等附加服务。
- 2、"仅部分预览"的文档,不可在线预览部分如存在完整性等问题,可反馈申请退款(可完整预览的文档不适用该条件!)。
- 3、如文档侵犯您的权益,请联系客服反馈,我们会尽快为您处理(人工客服工作时间:9:00-18:30)。
液压缸计算公式1、液压缸内径和活塞杆直径的确定液压缸的材料选为Q235无缝钢管,活塞杆的材料选为Q235 液压缸内径:4,F4== D,3.14,,pF:负载力 (N)2A:无杆腔面积 () mmP:供油压力 (MPa) D:缸筒内径 (mm) :缸筒外径 (mm) D1 2、缸筒壁厚计算π×,??ηδσψμ1)当δ/D?0.08时pDmax,,(mm) 02,p2)当δ/D=0.08~0.3时pDmax,,(mm) 02.3,-3ppmax3)当δ/D?0.3时,,,,0.4pDpmax,,,,(mm) 0,,2,1.3p,pmax,,,b,, pnδ:缸筒壁厚(mm),:缸筒材料强度要求的最小值(mm) 0:缸筒内最高工作压力(MPa) pmax:缸筒材料的许用应力(MPa) ,p:缸筒材料的抗拉强度(MPa) ,b:缸筒材料屈服点(MPa) ,sn:安全系数3 缸筒壁厚验算22,(D,D)s1(MPa) PN,0.352D1D1P,2.3,lg rLsDPN:额定压力:缸筒发生完全塑性变形的压力(MPa) PrL:缸筒耐压试验压力(MPa) PrE:缸筒材料弹性模量(MPa):缸筒材料泊松比 =0.3 ,同时额定压力也应该与完全塑性变形压力有一定的比例范围,以避免塑性变形的发生,即:,,(MPa) PN,0.35~0.42PrL4 缸筒径向变形量22,,DPDD,1r,,D,,,,(mm) 22,,EDD,1,,变形量?D不应超过密封圈允许范围5 缸筒爆破压力D1PE,2.3,lg(MPa) bD6 缸筒底部厚度Pmax,(mm) ,0.433D12,P:计算厚度处直径(mm) D27 缸筒头部法兰厚度4Fbh,(mm) ,(r,d),aLPF:法兰在缸筒最大内压下所承受轴向力(N)b:连接螺钉孔的中心到法兰内圆的距离(mm):法兰外圆的半径(mm) ra:螺钉孔直径 dL如不考虑螺钉孔,则:Fb4h,(mm) ,r,aP8 螺纹强度计算螺纹处拉应力KF,, (MPa) ,22d,D,,14螺纹处切应力KKFd10,, (MPa) 330.2(d,D)1合成应力22,,,,3,,, nP,s,许用应力 ,Pn0F:螺纹处承受的最大拉力 :螺纹外径 (mm) d0:螺纹底径 (mm) d1K:拧紧螺纹系数,不变载荷取K=1.25~1.5,变载荷取K=2.5~4 :螺纹连接的摩擦因数,=0.07~0.2,平均取=0.12 KKK111:螺纹材料屈服点(MPa) ,s:安全系数,取=1.2~2.5 nn009 缸筒法兰连接螺栓强度计算螺栓螺纹处拉应力KF, (MPa) ,,2dz14螺纹处切应力KKFd10, (MPa) ,30.2dz1合成应力22,,,,3,,1.3,,, nPz:螺栓数量10、缸筒卡键连接卡键的切应力(A处)2,D1PmaxPDmax14,,, (MPa) ,Dl4l1卡键侧面的挤压应力2,D1P2maxPDmax14, ,,c22,,D(D,2h)h(2D,h)1121,44 hhh卡键尺寸一般取h=δ,l=h, ,,122验算缸筒在A断面上的拉应力2,D1P2maxPDmax14,,, (MPa) 2222,,,(D,h)-D(D,h),D11 411、缸筒与端部焊接焊缝应力计算F,b (MPa) ,,,,n22,,Dd,,114D:缸筒外径 (mm) 1d:焊缝底径 (mm) 1:焊接效率,取=0.7 ,,:焊条抗拉强度 (MPa) ,bn:安全系数,参照缸筒壁的安全系数选取如用角焊F2 ,,Dh,1h—焊角宽度 (mm)12、活塞杆强度计算1)活塞杆在稳定工况下,如果只承受轴向推力或拉力,可以近似的用直杆承受拉压载荷的简单强度计算公式进行计算:F (MPa) ,,,,P,2d42)如果活塞杆所承受的弯曲力矩(如偏心载荷等),则计算式:,,FM,,,,,,, (MPa) P,,AWd,,3)活塞杆上螺纹、退刀槽等部位是活塞杆的危险截面,危险截面的合成应力应该满足:F21.8,,,, (MPa) nP2d2对于活塞杆上有卡键槽的断面,除计算拉应力外,还要计算校核卡键对槽壁的挤压应力:F42,,,, pp2,,,,ddc,,2,13F:活塞杆的作用力(N)d:活塞杆直径 (mm):材料许用应力,无缝钢管=100~110MPa, ,,PP中碳钢(调质)=400MPa ,P 2:活塞杆断面积 () mmAd3W:活塞杆断面模数 () mmM:活塞杆所承受弯曲力矩(N.m):活塞杆的拉力 (N) F2:危险截面的直径 (mm) d2:卡键槽处外圆直径 (mm) d1:卡键槽处内圆直径 (mm) d3c:卡键挤压面倒角 (mm) ,:材料的许用挤压应力(MPa) pp13、活塞杆弯曲稳定行计算活塞杆细长比计算L4B,, d:支铰中心到耳环中心距离(油缸活塞杆完全伸出时的安装距); LB1)若活塞杆所受的载荷力完全在活塞杆的轴线上,则按下式验算: F1FKF, 1nk26EI,,101F, (N) K22KLBE5E,,1.8,10(MPa) 1,,,,1,a1,b4d,44I,,0.049dm圆截面:() 64F:活塞杆弯曲失稳临界压缩力 (N) K:安全系数,通常取=3.5~6 nnKKK:液压缸安装及导向系数(见机械设计手册5卷21-292) :实际弹性模量(MPa) E1a:材料组织缺陷系数,钢材一般取a?1/12 b:活塞杆截面不均匀系数,一般取b?1/135E:材料弹性模量,钢材 (MPa) E,2.1,104I:活塞杆横截面惯性矩(m)2:活塞杆截面面积 (m) Ade:受力偏心量 (m):活塞杆材料屈服点(MPa) ,sS:行程 (m)2)若活塞杆所受的载荷力偏心时,推力与支承的反作用力不完全F1处在中线上,则按下式验算:6,A,10SdF, (N) K81,esec,d2FLKB,a,其中: 06EI,10aaa一端固定,另一端自由=1,两端球铰=0.5,两端固定=0.25, 000 a一端固定,另一端球铰=0.35 014、缸的最小导向长度SDH,,202(mm) 导向套滑动面的长度1)在缸径?80mm时A=(0.6~1)D 2)在缸径,80mm时A=(0.6~1)d 活塞宽度取B=(0.6~1)D 15、圆柱螺旋压缩弹簧计算材料直径:PKCn d,1.6,P4C,10.615K,,或按照机械设计手册选取(5卷11-28) 4C,4CD 一般初假定C-5~8 C,d有效圈数:'4PGdFdn n,,38PDP'n弹簧刚度4GdGDP',, 348Dn8Cn总圈数n,n,x1x:1/2 (见机械设计手册第5卷 11-18)节距:H(1~2)d,0t, n间距:,,t,d自由高度: H,(n,1)d 0最小工作载荷时高度:H,H-F 10134PDPC8n8nP111FF,,,或者 114P'GdGD最大工作载荷时的高度H,H-Fn0n34PDPC8n8nPnnn或者 FF,,,1n4P'GdGD工作极限载荷下的高度H,H-Fj0j34PDPCP8n8njjjF或者 F,,,1j4P'GdGD弹簧稳定性验算高径比:H0b, D应满足下列要求两端固定 b?5.3 一端固定,另一端回转 b?3.7 两端回转 b?2.6 当高径比大于上述数值时,按照下式计算: P,CP'H,P CB0nP:弹簧的临界载荷 (N) CC:不稳定系数 (见机械设计手册第5卷 11-19) BP:最大工作载荷 (N) n强度验算:,,,0.750minS,,S安全系数 P,max: 弹簧在脉动循环载荷下的剪切疲劳强度, ,0(见机械设计手册第5卷 11-19)8KD,: 最大载荷产生的最大切应力, ,P,maxnmax3,d8KD,: 最小载荷产生的最小切应力, ,P,min1min3,d:许用安全系数当弹簧的设计计算和材料实验精度高时,取 SP=1.3~1.7 ,当精确度低时,取 =1.8~2.2 SSPP,S静强度: 安全系数 S,,SP,max:弹簧材料的屈服极限 ,S15 系统温升的验算在整个工作循环中,工进阶段所占的时间最长,为了简化计算,主要考虑工进时的发热量。
一般情况下,工进速度大时发热量较大,由于限压式变量泵在流量不同时,效率相差极大,所以分别计算最大、最小时的发热量,然后加以比较,取大值进行分析。
当时 ,,10cmmin,,22333,qD00801m050310m0503L,,,,,,,..min.min.min ,44此时泵的效率为0.1,泵的出口压力为3.2MPa,则有320503.., P027kW,,.入6001,.10,,23,,,,,,,. PF225001010kW0037kW出60此时的功率损失为,,,,,,PPP0270037kW0233kW... ,,入出当,时 ,,120cmminq603L,.min32603.., P046kW,,.入6007,.120,,23,,,,,,,. PF225001010kW045kW出60,,,,,,PPP046045kW001kW... ,,入出可见在工进速度低时,功率损失为0.233kW,发热量最大。
,32假设系统的散热状况一般,取K1010kWcmC,,,:,油箱的散热面积A 为,,33222A0065V0065160192m,,,...系统温升为,P0386.,,,,t201??. ,3KA1010192,,.验算表明系统的温升在许可范围内。