折流杆换热器的设计
折流杆换热器

(2)折流杆换热器的总有效冷却面积大于垂直弓形折流板换热器的总有效冷却面积。垂直弓形折流板换热器的折流板把壳程分为几段,蒸汽在各段之间流动很不顺畅,每一段都存在“有效传热区”和“死区”[2],“死区”会导致不凝性气体大量积聚,从而使热传递量下降[3]。而折流杆换热器几乎没有“死区”,换热效果好。由于换热器的垂直安装形式,换热器上段的热传递率大于下段的热传递率。为了提高换热效果,换热器下段的折流杆的间距可以缩短些。
韶关发电厂8号汽轮机的4号低压加热器,原设计为垂直弓形板换热器,加热器的设计参数(由改造前工况及生产能力确定)见表1。由于流体横向冲刷管束产生低频振动及蒸汽的作用,引起U形管弯头及换热管与管板连接破裂。1998年,茂港电力设备厂对4号低压加热器实施改造。改造方案是用折流杆换热器代替垂直弓形板换热器,不改变原换热器的壳体,只更换换热器管芯,仍为垂直安装。壳程流体采用上进下出方式,附属设备及管接口均不变。换热管由原来的d19mm×1mm黄铜管更换成d19mm×2mm锅炉用无缝钢管。改造技术协议要求,机组带满负荷时,凝结水温升不低于21℃,改造后的加热器性能试验数据与计算结果见表2。
换热器设计完整版
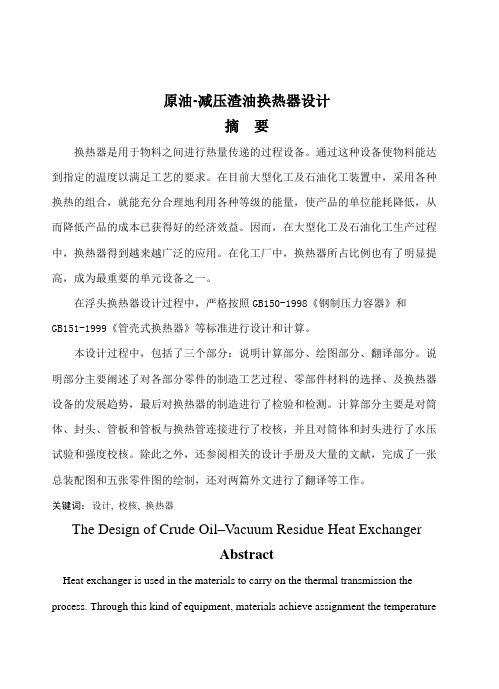
这类换热器都是通过板面进行传热的换热器。板面式换热器按传热板面的结构形式可分为以下五种:螺旋板式换热器,板式换热器,板翅式换热器,板壳是换热器和伞式换热器。板面式换热器的传热性能要比管式换热器优越,由于结构上的特点,使流体能在较低的速度下就达到湍流状态,从而强化了传热。板面是换热器采用板材制作,在大规模组织生产时,可降低设备成本,但其耐压性能比管式换热器差。
(3)其他形式换热器
这类换热器是指一些具有特殊结构的换热器一般是为满足工艺特殊要求而设计的,如石墨换热器,聚四氟乙烯换热器和热管式换热器等。
1.2
1.2.1设计参数的确定
压力容器设计参数主要有设计压力,设计温度,厚度,及其附加量,焊接接头系数和许用应力等。
(1)设计压力
为压力容器的设计载荷之一,其值不低于最高工作压力。最高工作压力系指容器顶部在正常工作过程中可能产生的最高表压。设计压力应视内压和外压容器分别取值。
In this design process, including three parts:explanation calculations part,cartography part, translationpart.Explanation computation the part mainly elaborated to various part of components manufacture technological process, the spare part materialselecting, and the heatexchanger equipment development trend, finallyithas carried on the examination and the testforthe heatexchanger manufacture. The calculations part mainly was to the tube body, the shell cover,the tube plate and the tube plate and the heat transfer pipe coupling hasbeencarried on the examination, and hasbeen carried on the hydraulic pressure test and the intensity examination to the tube body and the shell cover. In addition, referringthe related design handbook and the massive literature,ithas completed an assembly drawing andfivedetail drawing plan,andhas carried onwork andtwotranslations.
换热器折流板各种型式的讨论

换热器折流板各种型式的讨论兰州四方容器设备有限责任公司李建仓摘要:本文介绍了换热器所用折流板的几种型式,对其结构及工作形式作了阐述,并将其优点及缺点进行了说明和总结,从而为折流板换热器的设计选型及制造提供了依据和指导。
折流板顾名思义是用来改变流体流向的板,常用于管壳式换热器设计壳程介质流道,根据介质性质和流量以及换热器大小确定折流板的多少。
折流板是列管式换热器中的一个零件可用以起到提高传热系数和支承管束的作用;但由于它结构简单所以往往被设计者所忽视。
现实的情况可以证实到目前为止无论是我国自行设计还是国外引进的设备折流板的结构常是五花八门,其中有些结构既制造复杂又不利于提高传热系数。
其原因在于设计者没有根据具体的传热性质来认真地对它进行分析后再确定具体的结构和尺寸。
本文拟对各种型式折流板的优缺点一一列出并进行对比,提出换热器在什么情况下所适用哪种折流板的一些个人意见和有关同志进行商榷。
折流板有常用折流板和异形折流板之分。
常用折流板主要有弓形和圆盘-圆环折流板,其中弓形又分为单弓形、双弓形和三弓形,如图一:图一异形折流板有:矩形折流板、折流杆型折流板和格栅折流板等,如图二~四:矩形折流板(图二)折流杆换热器示意图(图三)格栅折流板(图四)这些折流板都有各自的优缺点,逐一说明如下;一、弓形折流板。
大部分换热器都采用弓形折流板。
弓形折流板在壳程内的放置形式上下方向排列的形式,用以造成液体剧烈扰动以增大传热系数;左右方向排列的,多数用于卧式换热器,设备中都伴随着有气相的吸收冷凝,以利于冷凝液和气体的流动,当列管是正方形排列时,为了使介质形成湍流以提高换热效果,则采用转角切口。
单弓形折流板主要是为了提高整体的壳程的错流程度,切口的百分数一般为20%~49%;通常为20%~25%,最佳大小为20%,此时单位压降下传热膜系数最高,小于20%(缺口处不布管除外)压降较大;切口超过20%,导致形成流体流速的滞留区,切口过大或过小,都会降低管束的传热性能;为了减小振动,亦可采用缺口处不布管,缺口可减小到15%或者25%左右,其压降只有单弓形的1/3左右。
毕业设计--螺旋折流板换热器开题报告

中国矿业大学化工学院毕业论文(设计)开题报告题目:螺旋折流板式换热器的设计专业:过程装备与控制工程姓名:桂大强班级:过控08-2班学号:06082908指导教师:朱荣涛一、概述以及设计目的折流板是提高换热器工效的重要部件。
传统换热器中最普遍应用的是弓形折流板,由于存在阻流与压降大、有流动滞死区、易结垢、传热的平均温差小、振动条件下易失效等缺陷,近年来逐渐被螺旋折流板所取代。
理想的螺旋折流板应具有连续的螺旋曲面。
由于加工困难,目前所采用的折流板,一般由若干个1/4的扇形平面板替代曲面相间连接,形成近似的螺旋面。
在折流时,流体处于近似螺旋流动状态。
相比于弓形折流板,在相同工况下,这样的折流板(被称为非连续型螺旋折流板)可减少压降45%左右,而总传热系数可提高20%~30%,在相同热负荷下,可大大减小换热器尺寸。
虽然非连续螺旋折流板的加工技术比较成熟,在石化行业也已得到推广应用,但仍存在诸多不足之处。
例如,扇形板连接处成非光滑的锐角过渡,对轴向运动的流体存在反压,流体通过时的突然转向会造成能量损失,在螺旋角较大时能耗更严重;相邻两片扇形板空间对接时,必须附加角接板才能填补缝隙,既费工又废料,又增大了流体的阻力。
相比之下,具有理想螺旋曲面的连续型螺旋折流板有着更好的传热与流动特性,但在实际应用时必须首先解决其加工难题。
螺旋折流板换热器的提出基于这样一种思想:通过改变壳侧折流板的布置,使壳侧流体呈连续的螺旋状流动。
因此,理想的折流板布置应该为连续的螺旋曲面。
但是,螺旋曲面加工困难,而且换热管与折流板的配合也较难实现。
考虑到加工上的方便,采用一系列的扇形平面板(称之为螺旋折流板)替代曲面相间连接,在壳侧形成近似螺旋面,使壳侧流体产生近似连续螺旋状流动。
一般来说,出于加工方面的考虑,一个螺距取2~4 块折流板,相邻折流板之间有连续搭接和交错搭接两方式,按流道又可分为单螺旋和双螺旋两种结构。
本次设计的螺旋折流板式换热器是我之前学习所没有接触过的,在传统的学习知识上面添加了一些新的元素,使得设计更具色彩性,同时主线没有改变,依然是列管式换热器。
折流杆换热器的结构选型及设备计算
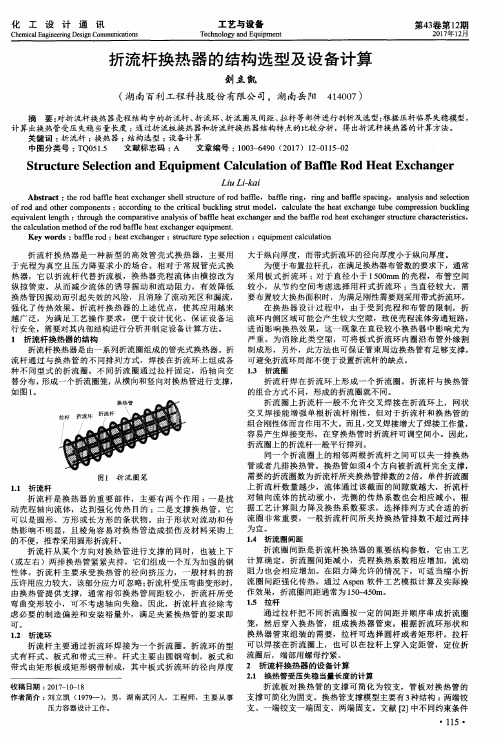
折流杆换热器 的结构选 型及 设备计算
刘 立 凯
( 湖 南百利工程科技股份有 限公 司 ,湖南岳 阳
4 1 4 0 0 7 )
摘 要: 对折 流杆换热器壳程结构 中的折流杆 、 折流环 、 折流 圈及 间距 、 拉杆等部件进行剖析及选型 ; 根据压杆 临界 失稳模型 , 计 算 出换热管受压失稳 当量长度 ; 通过折 流板换 热器和折 流杆换 热器结构特点的 比较分析 ,得 出折流杆换热器的计算方法 。 关键词 : 折流杆 ; 换热器 ; 结构选型 ; 设备计 算
如图1 。
大于纵 向厚度 ,而 带式折流环 的径 向厚度小于纵 向厚度 。 为便于布置拉杆 孔,在满足换热器布管数的要求下,通 常 采 用板 式折 流环 ; 对 于直径 小于 1 5 0 0 mm 的壳程 ,布 管空 间 较 小,从 节约 空间考虑 选择 用杆 式折流 环 ;当直径 较大 ,需 要 布 置 较 大 换 热 面积 时 ,为 满 足 刚 性 需要 则 采 用 带式 折 流 环 。 在 换 热 器 设 计 过 程 中 , 由于 受 到 壳 程 和 布 管 的 限 制 ,折 流环 内侧区域可 能会产生较大 空隙,致使壳程流体 旁通 短路 , 进 而影 响换热 效果 ,这 一现 象在 直径 较小换 热器 中影 响尤 为 严 重 。为 消 除此 类 空隙,可将 板式折 流环 内圈沿布 管外缘 割 制 成形 ,另外 ,此方法也可保 证管束周边换 热管有足够支撑 , 可 避 免 折 流 环 局 部不 便 于 设置 折流 杆 的缺 点 。
l i uLi k a i
Ab s t r a c t: t h e r o d b a le f h e a t e x c h a n g e r s h e l l s t r u c t u r e o f r o d b a le f ,b a le f r i n g, r i n g a n d b a le f s p a c i n g ,a n a l y s i s a n d s e l e c t i o n o f r o d nd a o t h e r c o mp o n e n t s;a c c o r d i n g t o t h e c r i t i c a l b u c k l i n g s t r u t mo d e l ,c a l c u l a t e t h e h e a t e x c h a n g e t u b e c o mp r e s s i o n b u c k l i n g e q u i v a l e n t l e n g t h;t h r o u g h t h e c o mp a r a t i v e a n a l y s i s o f b a le f h e a t e x c h a n g e r a n d t h e b a le f r o d h e a t e x c h a n g e r s t r u c t u r e c h ra a c t e r i s t i c s , t h e c a l c u l a t i o n me t h o d o f t h e r o d b a le f h e a t e x c h ng a e r e q u i p me n t .
重沸器采用折流杆换热器的优缺点分析
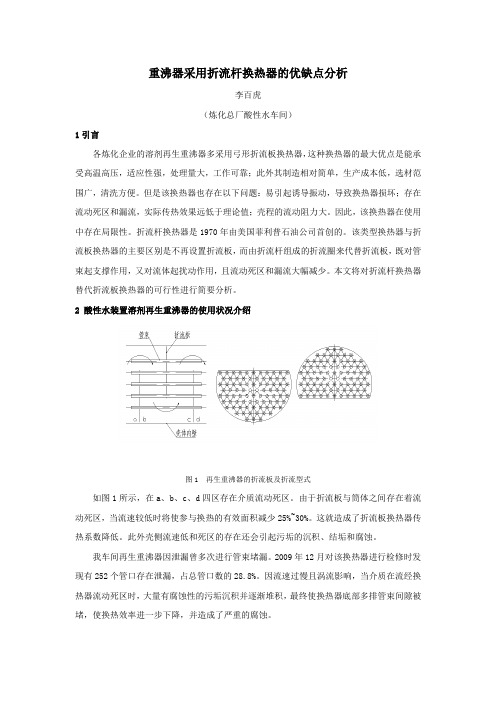
重沸器采用折流杆换热器的优缺点分析李百虎(炼化总厂酸性水车间)1引言各炼化企业的溶剂再生重沸器多采用弓形折流板换热器,这种换热器的最大优点是能承受高温高压,适应性强,处理量大,工作可靠;此外其制造相对简单,生产成本低,选材范围广,清洗方便。
但是该换热器也存在以下问题:易引起诱导振动,导致换热器损坏;存在流动死区和漏流,实际传热效果远低于理论值;壳程的流动阻力大。
因此,该换热器在使用中存在局限性。
折流杆换热器是1970年由美国菲利普石油公司首创的。
该类型换热器与折流板换热器的主要区别是不再设置折流板,而由折流杆组成的折流圈来代替折流板,既对管束起支撑作用,又对流体起扰动作用,且流动死区和漏流大幅减少。
本文将对折流杆换热器替代折流板换热器的可行性进行简要分析。
2 酸性水装置溶剂再生重沸器的使用状况介绍图1 再生重沸器的折流板及折流型式如图1所示,在a、b、c、d四区存在介质流动死区。
由于折流板与筒体之间存在着流动死区,当流速较低时将使参与换热的有效面积减少25%~30%。
这就造成了折流板换热器传热系数降低。
此外壳侧流速低和死区的存在还会引起污垢的沉积、结垢和腐蚀。
我车间再生重沸器因泄漏曾多次进行管束堵漏。
2009年12月对该换热器进行检修时发现有252个管口存在泄漏,占总管口数的28.8%。
因流速过慢且涡流影响,当介质在流经换热器流动死区时,大量有腐蚀性的污垢沉积并逐渐堆积,最终使换热器底部多排管束间隙被堵,使换热效率进一步下降,并造成了严重的腐蚀。
3 折流杆换热器的结构特点折流杆换热器的核心部分是由一系列焊有折流杆的折流圈组成的折流圈笼。
如下图所示。
图2 折流圈示意图1—折流圈; 2—折流杆; D1、D2—分别为折流圈的内经和外径图3 折流圈笼和管板的组装图从以上两图可以看出折流杆是均匀地焊接在折流圈上,每一个折流圈相隔一定的距离,按一定排列分别焊接在拉杆上,从而形成一个折流圈笼。
折流杆可以是圆形、方形、或长方形。
大型折流杆式换热器的设计开发
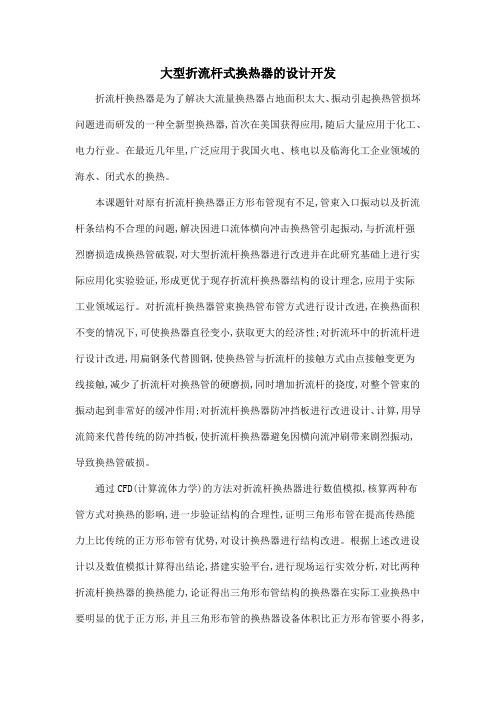
大型折流杆式换热器的设计开发折流杆换热器是为了解决大流量换热器占地面积太大、振动引起换热管损坏问题进而研发的一种全新型换热器,首次在美国获得应用,随后大量应用于化工、电力行业。
在最近几年里,广泛应用于我国火电、核电以及临海化工企业领域的海水、闭式水的换热。
本课题针对原有折流杆换热器正方形布管现有不足,管束入口振动以及折流杆条结构不合理的问题,解决因进口流体横向冲击换热管引起振动,与折流杆强烈磨损造成换热管破裂,对大型折流杆换热器进行改进并在此研究基础上进行实际应用化实验验证,形成更优于现存折流杆换热器结构的设计理念,应用于实际工业领域运行。
对折流杆换热器管束换热管布管方式进行设计改进,在换热面积不变的情况下,可使换热器直径变小,获取更大的经济性;对折流环中的折流杆进行设计改进,用扁钢条代替圆钢,使换热管与折流杆的接触方式由点接触变更为线接触,减少了折流杆对换热管的硬磨损,同时增加折流杆的挠度,对整个管束的振动起到非常好的缓冲作用;对折流杆换热器防冲挡板进行改进设计、计算,用导流筒来代替传统的防冲挡板,使折流杆换热器避免因横向流冲刷带来剧烈振动,导致换热管破损。
通过CFD(计算流体力学)的方法对折流杆换热器进行数值模拟,核算两种布管方式对换热的影响,进一步验证结构的合理性,证明三角形布管在提高传热能力上比传统的正方形布管有优势,对设计换热器进行结构改进。
根据上述改进设计以及数值模拟计算得出结论,搭建实验平台,进行现场运行实效分析,对比两种折流杆换热器的换热能力,论证得出三角形布管结构的换热器在实际工业换热中要明显的优于正方形,并且三角形布管的换热器设备体积比正方形布管要小得多,有较明显的经济成本优势;扁钢条折流杆更优于圆钢,避免了对换热管的硬磨损和起到了更好的防振缓冲作用;导流筒的优化设计使换热器避免了进口高速的流体横向冲刷,对换热管起到了很好的保护作用,流体进入换热器后全部为纵向流,使换热管充分的与壳侧介质接触,增强了换热效果。
折流杆换热器的设计
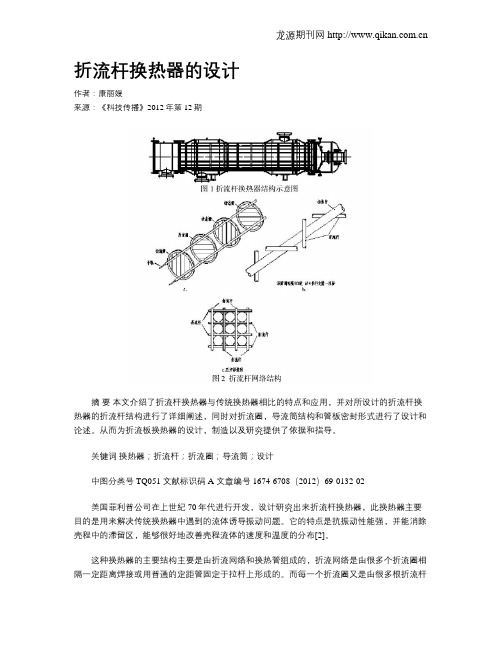
折流杆换热器的设计作者:康丽媛来源:《科技传播》2012年第12期摘要本文介绍了折流杆换热器与传统换热器相比的特点和应用,并对所设计的折流杆换热器的折流杆结构进行了详细阐述,同时对折流圈,导流筒结构和管板密封形式进行了设计和论述。
从而为折流板换热器的设计,制造以及研究提供了依据和指导。
关键词换热器;折流杆;折流圈;导流筒;设计中图分类号TQ051 文献标识码A 文章编号 1674-6708(2012)69-0132-02美国菲利普公司在上世紀70年代进行开发,设计研究出来折流杆换热器,此换热器主要目的是用来解决传统换热器中遇到的流体诱导振动问题。
它的特点是抗振动性能强,并能消除壳程中的滞留区,能够很好地改善壳程流体的速度和温度的分布[2]。
这种换热器的主要结构主要是由折流网络和换热管组成的,折流网络是由很多个折流圈相隔一定距离焊接或用普通的定距管固定于拉杆上形成的。
而每一个折流圈又是由很多根折流杆相互平行通过一定的间距焊接在外环上形成的。
这些折流网络和换热管进行热交换就达到换热器的换热目的。
这种换热器能够改善常规的板式折流板换热器的流体诱导振动。
在这种结构中,支撑管子的折流杆与管子几乎不存在间隙,管束中每根传热管的上、下、左、右都得到了可靠的支撑,而且从根本上改变了流体的流动状况,变折流板换热器的横向流动为平行于管子的轴向流动,从而消除了产生液体诱导振动的根源,增加了传热效率,减小了压力降。
另外折流杆换热器不易结垢,流体在经过折流杆时产生文丘里效应对管壁有强烈的冲刷作用,而且由于平行流动,避免了死区,也使得污垢难以形成。
在某项目中,因传统的换热器均不能解决诱导振动、传热效率和压降的问题,故设计一台折流杆换热器,以满足工艺及节能减排的需要。
1 设计方法1.1 折流杆结构设计此折流板换热器的最主要特点是采用了折流板网络结构作为热交换的载体。
这也是与传统换热器最主要的区别。
设计的关键也是在于折流板网络的构造设计。
管壳式换热器折流板的设计

设计折流板的设计壳式换热器折流板的管壳式换热器HTRI2012 上海CC China Meeting11062012-11-06管壳式换热器折流板的设计管壳式换热器中折流板的常用形式----单弓----NTIW(单弓窗口不布管)----双弓----螺旋折流板----双螺旋折流板----折流杆(Rod Baffle)管壳式换热器折流板的设计•单弓折流板的阻挡和扰流作用使得流体冲击折流板时改变流向,同时由于流通截面的突变而在弓形折流板缺口处形成流体速度突变和压力突变,且在折流板背面形成回流区,造成压力损失。
管壳式换热器折流板的设计•单弓折流板间距与切割率增大,将降低壳程压降, 但同时壳程传热系数减小;折流板间距与切割率减小,将增大壳程传热系数, 但同时壳程压降也急剧增大。
即壳程压降与壳程传热系数同增或同减, 但壳程压降增大或减小的幅度大于壳程传热系数。
为此, 在压降允许范围内, 减小折流板间距与圆缺率, 加强传热效果。
管壳式换热器折流板的设计•单弓-窗口不布管减小管子的无支撑间距,牺牲部分换热空间,降低诱导及弹性振动的可能性,同时增加壳程流体的流通量。
管壳式换热器折流板的设计•双弓双弓弓形折流板换热器保留了弓形折流板的结构形式, 但增加了切割面积, 使壳程流动形式从单弓时的错流改变成顺错流态, 并克服了流体急剧回弯流动造成的管束震动,在相同压降下即可把流速提高至二倍以上, 从而提高传热速率。
尤其适合用于壳侧流体流量大, 粘度大的场合。
管壳式换热器折流板的设计•螺旋折流板螺旋折流板换热器突破了壳程介质流横向垂直和管子相切的传统观念, 流体在壳侧呈连续柱塞状螺旋流动,不会出现传统折流板换热器内的流动死区,并且由于旋流产生的涡与管束传热界面边界层相互作用, 使湍流度大幅度增强, 有利于提高壳侧膜传热系数。
管壳式换热器折流板的设计•螺旋折流板连续螺旋折流板换热器的折流板形状是自壳体进口向出口推进的完全螺旋面,介质在壳体内做到相对连续平稳旋转流动。
高温高压U型折流杆换热器的制造技术

赵 洪 勇
( 镇海 石化 建 安工程 有 限公 司 , 浙江 宁波
3 1 5 2 0 7 )
摘 要: 折流杆式换热器是一种 壳体 内的折流元件 由一系列细小 的折流杆组成的管壳式换热器, 是 为 了改善常规的板式折流板换热器的流体诱导振动而设计的。折流杆与换热管之h e a t e x c h a n g e t u b e b e n d i n g, s t r e s s r e l i e f t r e a t me n t a n d h i g h a s s e mb l y p r e c i s i o n . Ma k i n g b r e a k —
中图分类号 : T H 4 9 ; T Q 0 5 1 . 5 ; T Q 0 5 0 . 6 文献标志码 : B 文章编号 : 1 0 0 1 — 4 8 3 7 ( 2 0 1 5 ) 0 7—0 0 7 0一 O 5
d o i : 1 0 . 3 9 6 9 / j . i s s n . 1 0 0 1 — 4 8 3 7 . 2 0 1 5 . 0 7 . 0 1 2
t h r o u g h s o n a b o v e d i ic f u l t i e s, o u r c o mpa n y t a c k l e s t h e p r o c e s s i n g a n d ma nu f a c t u in r g p r o b l e ms i n f a b ic r a —
密, 决定 了换 热器 管束 是 否 能够 满 足 设 计 技 术 要 求 。 而对 于 高 温 高 压 工 况 下 的 U 型 折流 杆 换 热
钛管折流杆换热器的设计与制造
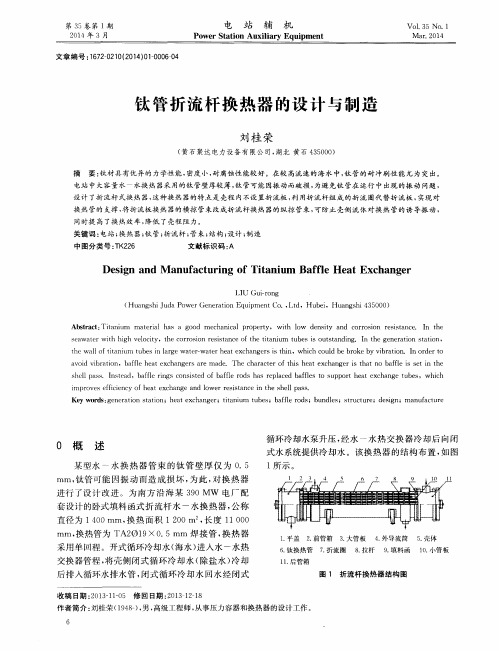
w
换 热管的支撑 , 将折流板换热 器的横掠 管束 改成折流杆换 热器的纵掠 管柬 , 可防止 壳侧 流体 对换 热管 的诱 导振 动 , 同时提 高 了换 热效率 , 降低 了壳程 阻力。 关键词 : 电站 ; 换热 器; 钛 管; 折流杆 ; 管 束; 结构 ; 设计 ; 制造
第3 5卷 第 l 期
2 0 1 4年 3月
电 站
辅
机
Vo l | 3 5 No . 1
Ma r .2 01 4
Po we r S t a t i o n Au x i l i a r y Equi pm e nt
文章编号 : 1 6 7 2 — 0 2 1 0 ( 2 O 1 4 ) 0 卜0 0 0 6 0 4
Hu b e i ,H u a n g s h i 4 3 5 O 0 O )
Ab s t r a c t : Ti t a n i u m ma t e r i a l h a s a g o o d me c h a n i c a 1 p r o p e r t y , wi t h 1 O W d e n s i t y a n d c o r r o s i o n r e s i s t a n c e . I n t h e s e a wa t e r wi t h h i g h v e l o c i t y ,t h e c o r r o s i o n r e s i s t a n c e o f t h e t i t a n i u m t u b e s i s o u t s t a n d i n g .I n t h e g e n e r a t i o n s t a t i o n, t h e wa l l o f t i t a n i u m t u b e s i n l a r g e wa t e r - wa t e r h e a t e x c h a n g e r s i s t h i n ,wh i c h c o u l d b e b r o k e b y v i b r a t i o n .I n o r d e r t O a v o i d v i b r a t i o n,b a f f l e h e a t e x c h a n g e r s a r e ma d e .Th e c h a r a c t e r o f t h i s h e a t e x c h a n g e r i s t h a t n o b a f f l e i s s e t i n t h e s h e l l[ ) a s s .I n s t e a d ,b a f f l e r i n g s c o n s i s t e d o f b a f f l e r o d s h a s r e p l a c e d b a f f l e s t O s u p p o r t h e a t e x c h a n g e t u b e s ,wh i c h i mp r o v e s e f f i c i e n c y o f h e a t e x c h a n g e a n d l o we r r e s i s t a n c e i n t h e s h e l l p a s s . Ke y wo r d s : g e n e r a t i o n s t a t i o n;h e a t e x c h a n g e r ;t i t a n i u m t u b e s ;b a f f l e r o d s ;b u n d l e s ;s t r u c t u r e ;d e s i g n ;ma n u f a c t u r e
折流杆式换热器.doc
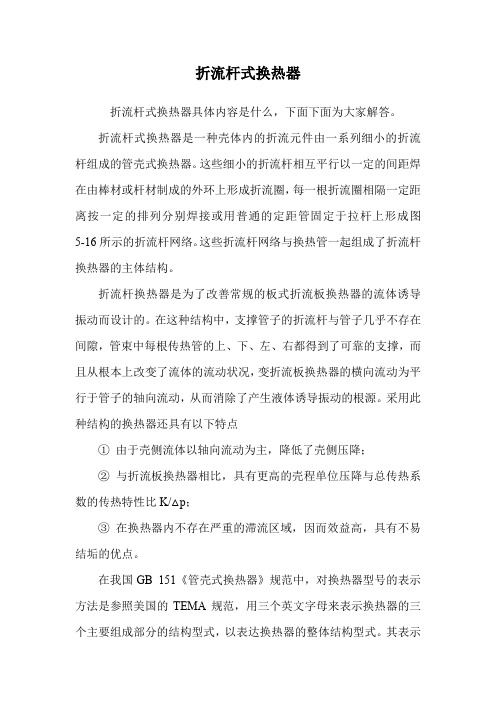
折流杆式换热器折流杆式换热器具体内容是什么,下面下面为大家解答。
折流杆式换热器是一种壳体内的折流元件由一系列细小的折流杆组成的管壳式换热器。
这些细小的折流杆相互平行以一定的间距焊在由棒材或杆材制成的外环上形成折流圈,每一根折流圈相隔一定距离按一定的排列分别焊接或用普通的定距管固定于拉杆上形成图5-16所示的折流杆网络。
这些折流杆网络与换热管一起组成了折流杆换热器的主体结构。
折流杆换热器是为了改善常规的板式折流板换热器的流体诱导振动而设计的。
在这种结构中,支撑管子的折流杆与管子几乎不存在间隙,管束中每根传热管的上、下、左、右都得到了可靠的支撑,而且从根本上改变了流体的流动状况,变折流板换热器的横向流动为平行于管子的轴向流动,从而消除了产生液体诱导振动的根源。
采用此种结构的换热器还具有以下特点①由于壳侧流体以轴向流动为主,降低了壳侧压降;②与折流板换热器相比,具有更高的壳程单位压降与总传热系数的传热特性比K/△p;③在换热器内不存在严重的滞流区域,因而效益高,具有不易结垢的优点。
在我国GB 151《管壳式换热器》规范中,对换热器型号的表示方法是参照美国的TEMA规范,用三个英文字母来表示换热器的三个主要组成部分的结构型式,以表达换热器的整体结构型式。
其表示方法如下:在上述表示方法中,DN为换热器的公称直径,对卷制圆筒为圆筒内径,对钢管制圆筒为钢管外径。
A为换热器的公称换热面积,它是以换热管外径为基础,扣除伸入管板内的换热管长度后,计算得到的管束外表面积经圆整后得到的计算换热面积。
LN为公称长度,它是指换热管的长度,换热管为直管时,取直管长度,换热管为U型管时,指U型管的直管段长度。
S表示换热管管材。
pt/ps为管/壳程设计压力,而设计压力是指在相应的设计温度下,用以确定换热器圆筒厚度及其他受压元件厚度的压力,一般取略高于工作压力。
Ⅰ级管束是指采用较高级、高级冷拔换热管,适用于无相变传热和易产生振动的场合,Ⅱ级管柬为采用普通级冷拔换热管,适用于重沸、冷凝传热和无振动的一般场合。
螺旋折流板式换热器的设计毕业设计
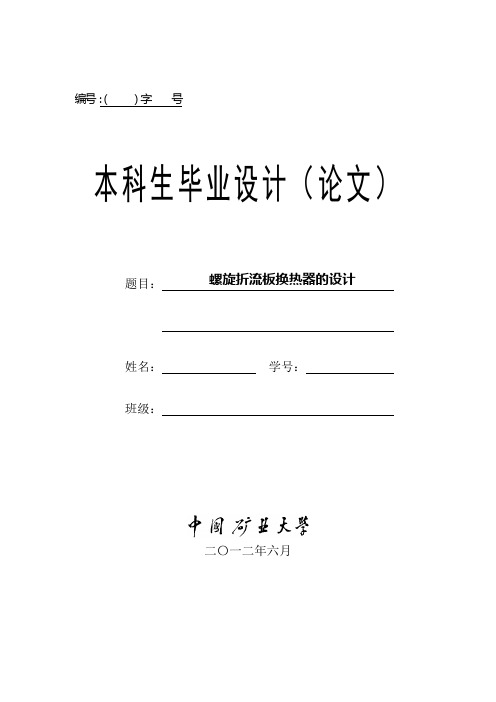
编号:()字号本科生毕业设计(论文)题目:姓名:学号:班级:二〇一二年六月螺旋折流板换热器的设计中国矿业大学本科生毕业设计学院:化工学院专业:过程装备与控制工程设计题目:螺旋折流板换热器的设计专题:基于起重机械虚拟仿真计算与分析的简单探索毕业设计(论文)原创性声明和使用授权说明原创性声明本人郑重承诺:所呈交的毕业设计(论文),是我个人在指导教师的指导下进行的研究工作及取得的成果。
尽我所知,除文中特别加以标注和致谢的地方外,不包含其他人或组织已经发表或公布过的研究成果,也不包含我为获得及其它教育机构的学位或学历而使用过的材料。
对本研究提供过帮助和做出过贡献的个人或集体,均已在文中作了明确的说明并表示了谢意。
作者签名:日期:指导教师签名:日期:使用授权说明本人完全了解大学关于收集、保存、使用毕业设计(论文)的规定,即:按照学校要求提交毕业设计(论文)的印刷本和电子版本;学校有权保存毕业设计(论文)的印刷本和电子版,并提供目录检索与阅览服务;学校可以采用影印、缩印、数字化或其它复制手段保存论文;在不以赢利为目的前提下,学校可以公布论文的部分或全部内容。
作者签名:日期:学位论文原创性声明本人郑重声明:所呈交的论文是本人在导师的指导下独立进行研究所取得的研究成果。
除了文中特别加以标注引用的内容外,本论文不包含任何其他个人或集体已经发表或撰写的成果作品。
对本文的研究做出重要贡献的个人和集体,均已在文中以明确方式标明。
本人完全意识到本声明的法律后果由本人承担。
作者签名:日期:年月日学位论文版权使用授权书本学位论文作者完全了解学校有关保留、使用学位论文的规定,同意学校保留并向国家有关部门或机构送交论文的复印件和电子版,允许论文被查阅和借阅。
本人授权大学可以将本学位论文的全部或部分内容编入有关数据库进行检索,可以采用影印、缩印或扫描等复制手段保存和汇编本学位论文。
涉密论文按学校规定处理。
作者签名:日期:年月日导师签名:日期:年月日教研室(或答辩小组)及教学系意见中国矿业大学毕业设计任务书学院化工学院专业年级过控2008 学生姓名桂大强任务下达日期:2011年 12月 20 日毕业设计日期:2012 年 2 月 1 日至 2012 年 6 月 15 日毕业设计题目:螺旋折流板式换热器的设计毕业设计专题题目:基于起重机械虚拟仿真计算与分析的简单探索毕业设计主要内容和要求:1 毕业设计题目螺旋折流板式换热器的设计2 主要设计参数设计一个满足工艺要求的螺旋折流板式换热器,具体的参数如下:介质分别为丁二烯和水,工作压力分别为0.39MPa、0.45MPa,入口温度分别是39.9℃、34℃,出口温度分别是36.9℃、38℃,丁二烯的质量流量是17000Kg/h。
折流杆换热器的设计
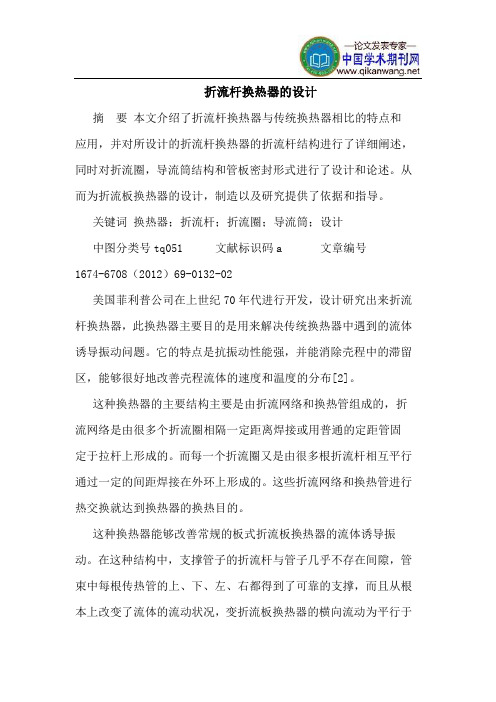
折流杆换热器的设计摘要本文介绍了折流杆换热器与传统换热器相比的特点和应用,并对所设计的折流杆换热器的折流杆结构进行了详细阐述,同时对折流圈,导流筒结构和管板密封形式进行了设计和论述。
从而为折流板换热器的设计,制造以及研究提供了依据和指导。
关键词换热器;折流杆;折流圈;导流筒;设计中图分类号tq051 文献标识码a 文章编号1674-6708(2012)69-0132-02美国菲利普公司在上世纪70年代进行开发,设计研究出来折流杆换热器,此换热器主要目的是用来解决传统换热器中遇到的流体诱导振动问题。
它的特点是抗振动性能强,并能消除壳程中的滞留区,能够很好地改善壳程流体的速度和温度的分布[2]。
这种换热器的主要结构主要是由折流网络和换热管组成的,折流网络是由很多个折流圈相隔一定距离焊接或用普通的定距管固定于拉杆上形成的。
而每一个折流圈又是由很多根折流杆相互平行通过一定的间距焊接在外环上形成的。
这些折流网络和换热管进行热交换就达到换热器的换热目的。
这种换热器能够改善常规的板式折流板换热器的流体诱导振动。
在这种结构中,支撑管子的折流杆与管子几乎不存在间隙,管束中每根传热管的上、下、左、右都得到了可靠的支撑,而且从根本上改变了流体的流动状况,变折流板换热器的横向流动为平行于管子的轴向流动,从而消除了产生液体诱导振动的根源,增加了传热效率,减小了压力降。
另外折流杆换热器不易结垢,流体在经过折流杆时产生文丘里效应对管壁有强烈的冲刷作用,而且由于平行流动,避免了死区,也使得污垢难以形成。
在某项目中,因传统的换热器均不能解决诱导振动、传热效率和压降的问题,故设计一台折流杆换热器,以满足工艺及节能减排的需要。
1 设计方法1.1 折流杆结构设计此折流板换热器的最主要特点是采用了折流板网络结构作为热交换的载体。
这也是与传统换热器最主要的区别。
设计的关键也是在于折流板网络的构造设计。
折流板网络结构是由很多个折流删组成的。
折流杆换热器课程设计
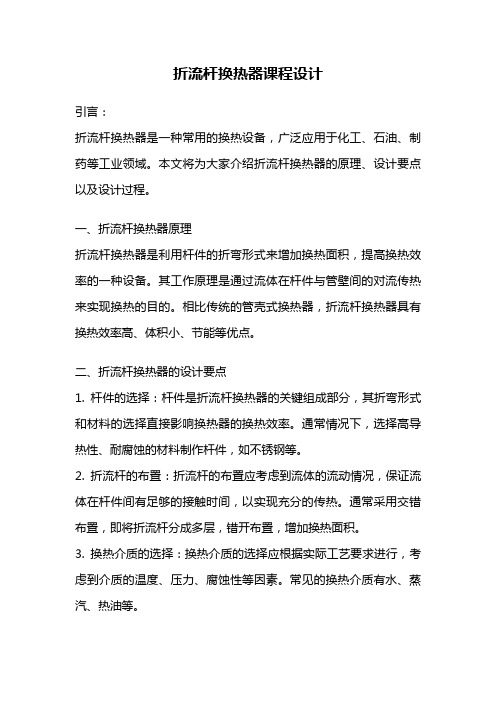
折流杆换热器课程设计引言:折流杆换热器是一种常用的换热设备,广泛应用于化工、石油、制药等工业领域。
本文将为大家介绍折流杆换热器的原理、设计要点以及设计过程。
一、折流杆换热器原理折流杆换热器是利用杆件的折弯形式来增加换热面积,提高换热效率的一种设备。
其工作原理是通过流体在杆件与管壁间的对流传热来实现换热的目的。
相比传统的管壳式换热器,折流杆换热器具有换热效率高、体积小、节能等优点。
二、折流杆换热器的设计要点1. 杆件的选择:杆件是折流杆换热器的关键组成部分,其折弯形式和材料的选择直接影响换热器的换热效率。
通常情况下,选择高导热性、耐腐蚀的材料制作杆件,如不锈钢等。
2. 折流杆的布置:折流杆的布置应考虑到流体的流动情况,保证流体在杆件间有足够的接触时间,以实现充分的传热。
通常采用交错布置,即将折流杆分成多层,错开布置,增加换热面积。
3. 换热介质的选择:换热介质的选择应根据实际工艺要求进行,考虑到介质的温度、压力、腐蚀性等因素。
常见的换热介质有水、蒸汽、热油等。
4. 流体的流速和流量:流体的流速和流量对换热效果有直接影响。
流速过快会造成流体过早离开换热器,导致换热不充分;流速过慢则会使流体停留时间过长,增加传热阻力。
因此,应根据具体工艺要求合理选择流速和流量。
三、折流杆换热器的设计过程1. 确定设计参数:根据工艺要求和换热器的使用条件,确定设计参数,包括换热面积、流体流速、流量等。
2. 杆件布置设计:根据换热器的尺寸和布置要求,设计折流杆的布置方式,保证流体在杆件间有充分的接触时间。
3. 杆件材料选择:根据介质的温度、压力、腐蚀性等要求,选择合适的杆件材料。
4. 杆件尺寸计算:根据换热器的设计参数和折流杆的布置情况,计算杆件的尺寸,包括长度、直径等。
5. 换热介质选择:根据工艺要求和介质性质,选择合适的换热介质。
6. 换热器壳体设计:设计换热器的壳体结构,包括进出口管道的布置、支撑方式等。
7. 换热器的强度计算:根据设计参数和杆件尺寸,进行换热器的强度计算,确保其满足使用要求。
折流杆换热器CAD系统的开发

折流杆换热器C A D 系统的开发吴金星魏新利(郑州大学化工学院,郑州450002)摘要本文阐述了折流杆换热器CA D 系统的开发方法,包括:把大量线图、数表进行数据程序化,利用A D SRX 技术、PD B 界面设计技术和参数化图形设计技术对折流杆换热器的一百多种类型、三万多种规格的零部件进行了设计,将数据信息采用数据文件和数据库的方式进行集成和管理,从而实现折流杆换热器工艺、机械、零部件子系统的集成。
关键词折流杆换热器CA D 系统参数化设计系统集成1引言折流杆换热器是近年来开发的一种新型高效换热设备,壳程支撑结构为折流栅,每一个折流栅由若干平行的折流杆焊接在一个折流圈上,四个折流栅为一组,每组包括两个横栅和两个纵栅,交错布置,构成鼠笼式支撑结构。
它的主要特点是:壳程流体沿轴线呈纵向流动,传热效率高,流体流动阻力小,抗流体诱导振动性能好,抗结垢能力强,使用寿命长和节约材料等,在工程中应用越来越多。
在传统的换热器设计过程中,采用手工计算和绘图,需查阅大量的图表和反复核算,设计工作量大、周期长、效率低,设计质量不高。
随着计算机和CA D 技术发展,采用计算机硬、软件技术对换热器进行自动设计、修改及输出,为提高换热器的设计质量提供了强大的工具。
因此,按照我国标准[l ][2]开发和研制折流杆换热器CA D 系统具有巨大的经济效益和社会效益。
2折流杆换热器C A D 系统的组成及其功能折流杆换热器CA D 系统对工艺与设备进行综合设计,实现从工艺计算、机械设计、零部件设计到系统集成的自动化,即只要输入必要的工艺参数,系统可自动设计出性能优良的换热器,并自动绘制图纸和输出有关设计资料。
在分析传统设计过程和设计资料的基础上,运用软件工程和并行工程技术,开发的折流杆换热器CA D 系统包括:工艺设计子系统、机械设计子系统、零部件设计子系统、化工流体物性参数数据库、工程材料数据库和公共模块六部分。
各子系统及模块的功能如下:(l )工艺设计子系统根据工艺参数,应首先确定换热器的主要结构参数:壳体直径、换热管长度、换热管根数等,并为机械设计子系统提供必需数据;(2)机械设计子系统对换热器进行结构设计和强度校核;(3)零部件设计子系统为总装图的集成提供零部件图;(4)化工流体物性参数数据库根据流体的操作状况,自动查询和修改流体的物性参数,既可为工艺设计子系统提供必需数据,又可供用户单独使用;(5)工程材料数据库根据各种钢材的使用条件,自动查出钢材的常温强度指标和已知条件下的许用应力、弹性模量、平均线性膨胀系数等,既可为机械设计子系统服务,又可供用户单独使用;(6)公共模块包括系统初始化子模块、图框标题栏自动生成子模块、技术要求自动标注子模块、表面粗糙度自动标注子模块、明细栏自动生成子模块、装配图自动消隐子模块等。
《热交换器原理与设计》管壳式热交换器设计21-23
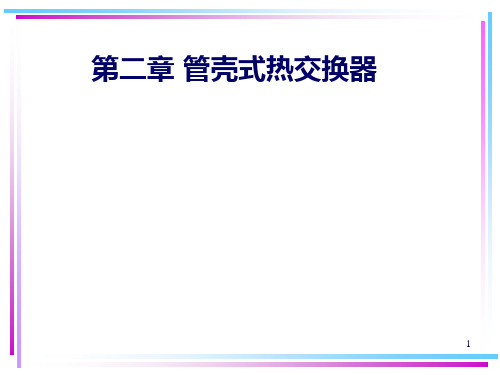
内容 :
管程流通截面积 确定壳体直径 壳程流通截面积
进出口连接管尺寸
一、管程流通截面积的计算 单管程热交换器的管程流通截面积为:
36
At Mt /twt
式中: At——为管程流通截面积,m2;
Mt——为管程流体的质量流量,Kg/s; ρt——为管程流体的密度,Kg/m3; Wt——为管程流体的流速,m/s;
水平 竖直
竖直 转角
(a) (a单 )单弓形 ( 弓a) 形单弓形
转角
过程设备设计
(c()三C)弓三弓形形 (C)三弓形
(b)双(弓 b形 )双(b弓)双形弓形
(d)( 圆d) 盘四弓 -圆形环形(d)四弓形
弓形缺口高度h 应使流体流过缺口时与横向流过管束时的流速相近
缺口大小用弓形弦高占壳体内直径的百分比来表示, 如单弓形折流板,h=(0.20~0.45)Di,最常用0.25Di。 13
作用: a. 减小跨距→防振 b.支承管子→增加管子刚度,防止管子产生过大挠度
形状尺寸: 同折流板
最大无支撑跨距:
换热管外径
10 12 14 16 19 25 32 38 45 57
最大无
钢管
- - 1100 1300 1500 1850 2200 2500 2750 3200
支撑跨距
有色金属 管
750
a1 a2 a3
a2
Dmh1
d0 sn
As a2a3
a3——盘周至圆筒内壁截面减去该处管子所占面积
Dm——环内径D1和盘径D2的算术平均值
sn ——与流向垂直的管间距
50
第三节 管壳式热交换器的传热计算
一、传热系数的确定
经验选用数据
折流杆换热器的设计及制造
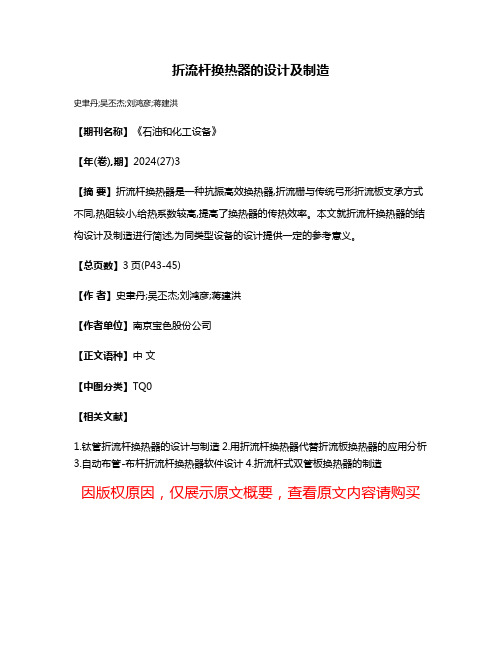
折流杆换热器的设计及制造
史聿丹;吴丕杰;刘鸿彦;蒋建洪
【期刊名称】《石油和化工设备》
【年(卷),期】2024(27)3
【摘要】折流杆换热器是一种抗振高效换热器,折流栅与传统弓形折流板支承方式不同,热阻较小,给热系数较高,提高了换热器的传热效率。
本文就折流杆换热器的结构设计及制造进行简述,为同类型设备的设计提供一定的参考意义。
【总页数】3页(P43-45)
【作者】史聿丹;吴丕杰;刘鸿彦;蒋建洪
【作者单位】南京宝色股份公司
【正文语种】中文
【中图分类】TQ0
【相关文献】
1.钛管折流杆换热器的设计与制造
2.用折流杆换热器代替折流板换热器的应用分析
3.自动布管-布杆折流杆换热器软件设计
4.折流杆式双管板换热器的制造
因版权原因,仅展示原文概要,查看原文内容请购买。
换热器的结构设计 -3
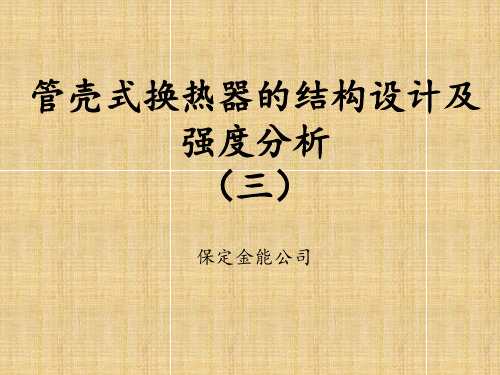
圆筒设计厚度(design thickness )
d C2
计算壁厚与腐蚀余量C2之和称为设计壁厚。是同
时满足强度、刚度和使用寿命的最小厚度。
C2为腐蚀裕度 (corrosion allowance)根据介
质对选用材料腐蚀速度和设计使用寿命共同考虑。 C2=k〃 a, mm;k—腐蚀速度,mm/a;对碳素钢 和低合金钢,C2≥ 1mm;对于不锈钢,当介质腐 蚀性能极微时,取C2=0。
图3-22 ¼ 扇形螺旋折流板
螺旋折流板裁剪方式
非连续螺旋折流板按照裁剪方式还可以分为四分之一椭 圆、四分之一扇形和三分之一扇形,如图所示。四分之一 椭圆螺旋折流板的长短边分别为折流板所在椭圆的长短轴 ,四分之一扇形螺旋折流板左右对称。每片椭圆型钢板采 用四分之一椭圆裁剪方式可以裁出四块折流板,采用四分 之一扇形裁剪方式可以裁出两块折流板,前者材料利用率
2015-4-12
Qust ——管壳式 16 换热器设计
减少流体滞留区,改善两端流体的分布;
3 导 流 筒
增加换热管有效换热长度,提高传热效率
起防冲挡板的作用。
3.2.2 折流板
提高壳程流体流速,增加湍动程度;
使壳程流体垂直冲刷管束,提高壳程传热系 数同时减少结垢。 弓形 圆盘-圆环形 堰形折流板
冷凝器,一般h=0.25~0.45Di,根据冷凝液多少决 定缺口高度;
壳程沸腾再沸器,一般h=0.45Di。
圆缺形,单弓形、 双弓形和三弓形。 单弓形折流板 single segmental baffle
加挡板:增大壳程流体的湍动,提高壳程的α 多管程:增大管内流体u,提高管内α
弓形缺口及通液口设置
折流杆换热器的设计制作
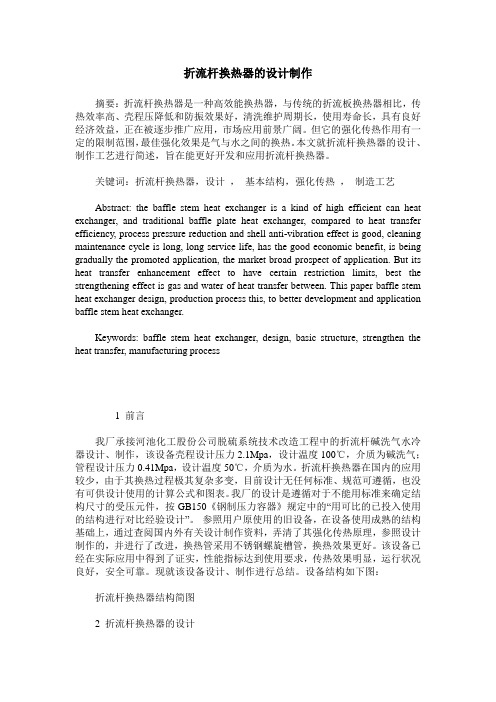
折流杆换热器的设计制作摘要:折流杆换热器是一种高效能换热器,与传统的折流板换热器相比,传热效率高、壳程压降低和防振效果好,清洗维护周期长,使用寿命长,具有良好经济效益,正在被逐步推广应用,市场应用前景广阔。
但它的强化传热作用有一定的限制范围,最佳强化效果是气与水之间的换热。
本文就折流杆换热器的设计、制作工艺进行简述,旨在能更好开发和应用折流杆换热器。
关键词:折流杆换热器,设计,基本结构,强化传热,制造工艺Abstract: the baffle stem heat exchanger is a kind of high efficient can heat exchanger, and traditional baffle plate heat exchanger, compared to heat transfer efficiency, process pressure reduction and shell anti-vibration effect is good, cleaning maintenance cycle is long, long service life, has the good economic benefit, is being gradually the promoted application, the market broad prospect of application. But its heat transfer enhancement effect to have certain restriction limits, best the strengthening effect is gas and water of heat transfer between. This paper baffle stem heat exchanger design, production process this, to better development and application baffle stem heat exchanger.Keywords: baffle stem heat exchanger, design, basic structure, strengthen the heat transfer, manufacturing process1 前言我厂承接河池化工股份公司脱硫系统技术改造工程中的折流杆碱洗气水冷器设计、制作,该设备壳程设计压力2.1Mpa,设计温度100℃,介质为碱洗气;管程设计压力0.41Mpa,设计温度50℃,介质为水。
- 1、下载文档前请自行甄别文档内容的完整性,平台不提供额外的编辑、内容补充、找答案等附加服务。
- 2、"仅部分预览"的文档,不可在线预览部分如存在完整性等问题,可反馈申请退款(可完整预览的文档不适用该条件!)。
- 3、如文档侵犯您的权益,请联系客服反馈,我们会尽快为您处理(人工客服工作时间:9:00-18:30)。
折流杆换热器的设计
摘要本文介绍了折流杆换热器与传统换热器相比的特点和应用,并对所设计的折流杆换热器的折流杆结构进行了详细阐述,同时对折流圈,导流筒结构和管板密封形式进行了设计和论述。
从而为折流板换热器的设计,制造以及研究提供了依据和指导。
关键词换热器;折流杆;折流圈;导流筒;设计
美国菲利普公司在上世纪70年代进行开发,设计研究出来折流杆换热器,此换热器主要目的是用来解决传统换热器中遇到的流体诱导振动问题。
它的特点是抗振动性能强,并能消除壳程中的滞留区,能够很好地改善壳程流体的速度和温度的分布[2]。
这种换热器的主要结构主要是由折流网络和换热管组成的,折流网络是由很多个折流圈相隔一定距离焊接或用普通的定距管固定于拉杆上形成的。
而每一个折流圈又是由很多根折流杆相互平行通过一定的间距焊接在外环上形成的。
这些折流网络和换热管进行热交换就达到换热器的换热目的。
这种换热器能够改善常规的板式折流板换热器的流体诱导振动。
在这种结构中,支撑管子的折流杆与管子几乎不存在间隙,管束中每根传热管的上、下、左、右都得到了可靠的支撑,而且从根本上改变了流体的流动状况,变折流板换热器的横向流动为平行于管子的轴向流动,从而消除了产生液体诱导振动的根源,增加了传热效率,减小了压力降。
另外折流杆换热器不易结垢,流体在经过折流杆时产生文丘里效应对管壁有强烈的冲刷作用,而且由于平行流动,避免了死区,也使得污垢难以形成。
在某项目中,因传统的换热器均不能解决诱导振动、传热效率和压降的问题,故设计一台折流杆换热器,以满足工艺及节能减排的需要。
1 设计方法
1.1 折流杆结构设计
此折流板换热器的最主要特点是采用了折流板网络结构作为热交换的载体。
这也是与传统换热器最主要的区别。
设计的关键也是在于折流板网络的构造设计。
折流板网络结构是由很多个折流删组成的。
每一个折流栅都是由很多根折流板均匀,并且平行的焊接在一个管圈内组成的,我们通常将这个管圈称作折流圈。
折流杆时最基本的组成部分,它可以是多种多样的,如方形,圆形,长方形等。
折流杆组成的折流删等间距排列成一组,变构成折流网络的一个单元,如图2(a)所示。
为了增加换热管的稳定性,我们将相邻两个折流圈和附带的折流板相互垂直排列。
即其中一个竖直排列,则另一个水平排列。
这样也可以使得每一根换热管在上下左右个方向得到支撑,如图2(b)所示。
为了增加热传导效率,我们将折流栅中相邻的两个折流杆间隔并交错排列,如图2(c)所示。
由此两种热交换介质中的流体由传统的垂直于换热管的横向流动变为平行于换热管的轴向流动,从而消除了产生诱导振动,增加了传热效率,减小了压力降。
图2 折流杆网络结构
换热管的中心距减去换热管直径便是折流杆直径,折流杆与换热管之间没有间距。
折流板平行焊接在折流圈(环)上,折流圈平行排列组成折流栅,折流栅一组一组的排列构成折流网络,这种排列最大的利用了板间的换热面积,使得热
传导效率大大提高,同时也为换热管提供了牢固的支撑。
1.2 折流圈的设计
折流圈一般由圆钢、方钢或方条制成。
折流圈外径等于壳体内径减去GB151、TEMA等设计标准所规定的间隙,可参考者流板的直径选取。
此次设计的换热器折流圈用厚板条制。
折流圈用方钢连接成折流杆网络,圈的间距可视具体情况变化。
对于直径较大的换热器,除用方钢将折流圈连接外,还应用拉杆定距管固定,这样设计即可方便各折流栅的组装焊接,也增加了整组折流栅的稳定性[1]。
1.3 导流筒的设置
为克服进、出口处管束因流体流速过高而产生的冲刷磨损应设置外导流筒。
外导流筒的引入可在不增加筒体直径的前提下,有效的加大进口管的尺寸,从而降低压降,增加设备的效率;同时,为减小流体停滞区,提高传热效率也应设置外导流筒,从而增加换热管的有效换热长度。
在设计导流筒时,应保证接管进出口流通面积、环隙流通截面积与壳程流通面积逐级增加10%~15%[1]。
1.4 管板
由于折流杆对换热管起到了很好的支撑作用,管板的厚度也可以相应的降低,采用薄管板即可满足设计要求。
节约了材料,从而提高的经济性。
2 结论
设计该换热器解决了常规传统换热器难以克服的诱导振动,传热效率低等问题,满足了工艺要求,实现了节能减排,达到了设计目的。
参考文献
[1]王松汉.石油化工设计手册第3卷(化工单元过程)[M].北京:化学工业出版社,2001.
[2]刘明.新型换热器技术进展及其应用[J].山西能源与节能,2004,2:31-32.。