马氏体转变和残奥量
残余奥氏体名词解释
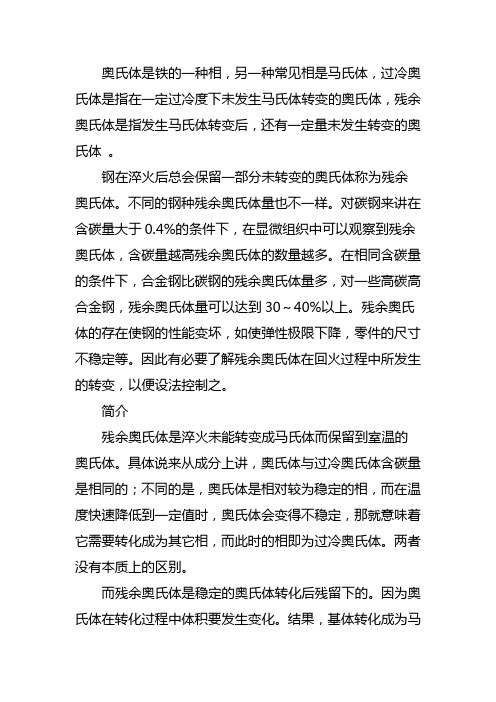
奥氏体是铁的一种相,另一种常见相是马氏体,过冷奥氏体是指在一定过冷度下未发生马氏体转变的奥氏体,残余奥氏体是指发生马氏体转变后,还有一定量未发生转变的奥氏体。
钢在淬火后总会保留一部分未转变的奥氏体称为残余奥氏体。
不同的钢种残余奥氏体量也不一样。
对碳钢来讲在含碳量大于0.4%的条件下,在显微组织中可以观察到残余奥氏体,含碳量越高残余奥氏体的数量越多。
在相同含碳量的条件下,合金钢比碳钢的残余奥氏体量多,对一些高碳高合金钢,残余奥氏体量可以达到30~40%以上。
残余奥氏体的存在使钢的性能变坏,如使弹性极限下降,零件的尺寸不稳定等。
因此有必要了解残余奥氏体在回火过程中所发生的转变,以便设法控制之。
简介残余奥氏体是淬火未能转变成马氏体而保留到室温的奥氏体。
具体说来从成分上讲,奥氏体与过冷奥氏体含碳量是相同的;不同的是,奥氏体是相对较为稳定的相,而在温度快速降低到一定值时,奥氏体会变得不稳定,那就意味着它需要转化成为其它相,而此时的相即为过冷奥氏体。
两者没有本质上的区别。
而残余奥氏体是稳定的奥氏体转化后残留下的。
因为奥氏体在转化过程中体积要发生变化。
结果,基体转化成为马氏体后,残余部分由于空间的限制,导致该部分只能以奥氏体存在;对于碳钢而言,当过冷至零度以下,这部分残余奥氏体会全部转化成为马氏体。
残余奥氏体的形态钢经DIF区变形0.6后淬火到300℃再碳分配60s所获得的典型残余奥氏体形貌如下图1所示:图1 残余奥氏体的形态TEM测试结果表明,经DIF区变形后再进行Q&P处理的残余奥氏体形态为无规则形态,即残余奥氏体并不完整且发生弯曲破裂。
残余奥氏体边缘存在有高密度的位错。
奥氏体存在于马氏体板条中间大约有几十纳米厚度。
这种现象主要是由于DIF区变形的缘故。
晶粒越细残余奥氏体强化效果就越明显。
与粗晶奥氏体相比较,细晶奥氏体相中要发生马氏体相变需要更多的自由能来满足相变驱动力的要求。
在细小晶界积聚的高密度位错抑制了马氏体的生长。
马氏体转变

马氏体相变的
分子动力学模拟
200,000 Zr atoms 1024-node Intel Paragon XP/S-150
六. 不同材料中的马氏体转变 1. 有色合金 许多有色合金也存在马氏体转变。 马氏体外形基本上仍属条片状,金相形貌与铁基 马氏体有区别。 马氏体亚结构多为层错和孪晶,极少有位错型。
' '
薄板状马氏体
薄片状马氏体
三. 马氏体转变的热力学 1. 相变驱动力
G
T0为相同成分的马氏 体和奥氏体两相热力学 平衡温度,此时
ΔGγ→α′
ΔGγ→α’ = 0
ΔGγ→α’ 称为马氏体相 变驱动力。 Ms T0 Gα′ Gγ T
自由焓——温度曲线
2. 转变温度Ms和Mf 相变驱动力用来提供切变能 量、亚结构畸变能、膨胀应变 能、共格应变能、界面能等, 所以要有足够大相变驱动力。 Ms为马氏体转变起始温度, 是奥氏体和马氏体两相自由能 之差达到相变所需的最小驱动 力(临界驱动力)时的温度。 Mf为马氏体转变终了温度。 T
(3) 其它形貌马氏体 在高碳钢,高镍Fe-Ni-C合金中, 或在应力诱发作用下,会形成蝶 状马氏体。 呈V形柱状,成片出现。 两翼的惯习面为{225}γ,夹角 为136°,结合面为{100}γ。 位向关系为K-S关系。
蝶状马氏体 {100}γ
晶内亚结构为位错,无孪晶。
136°
蝶状马氏体示意图
(155)
(321) 和 (332) 之间
{111} {133} {8,8,11}β {344}β {344}β {100}β
2. 无机材料 1963年Wolten根据ZrO2中正方相t→单斜相m的转 变具有变温、无扩散及热滞的特征,将这种转变称 为马氏体转变,ZrO2中的t→m相变还表现出表面浮 凸及相变可逆的特点。 在无机和有机化合物、矿物质、陶瓷以及水泥的 一些晶态化合物中也有切变型转变。如压电材料 PbTiO3、BaTiO3、及K(Ta、Nb)O3等钙钛氧化物高 温顺电性立方相→低温铁电性正方相的转变;高温 超导体YBaCu2O7-x高温顺电相→超导立方相的转变 均为马氏体转变。
马氏体转变原理

三、马氏体转变的无扩散性
实验测定出母相与新相成分一致 ; 马氏体形成速度极快,一片马氏体在5×10-55×10-7秒内生成; 碳原子在马氏体和奥氏体中的相对于铁原子保持不变的间隙位置 。
四、马氏体转变具有一定的位向关系和惯习面 马氏体转变时马氏体与奥氏体存在着严格的晶体学关系: 1、位向关系
(2) 马氏体转变不完全性
马氏体转变量是在 Ms ~ Mf 温度范围内,马氏体的转变 量是温度的函数,与等温
马氏体转变量与温度的关系
时间没有关系。
爆发式转变时马氏体转变量与温度的关系 过冷奥氏体向马氏体转变是在零下某一温 度突然发生并在一次爆发中形成一定数量 的马氏体,伴有响声并放出大量潜热。
表面浮凸:预先磨光表面的试样,在马氏体相变后 表面产生突起,这种现象称之为表面浮凸现象。
马氏体转变时产生表面浮凸示意图
高碳轴承钢马氏体的等温形成1.4%C,1.4%Cr, 浮凸,直接淬至100℃等温10小时 800×
下图是三种不变平面应变,图中的 C) 既有膨胀 又有切变,钢中马氏体转变即属于这一种。
(2)位向关系
马氏体转变的晶体学特征是马氏体与母相之间存 在着一定的位向关系。在钢中已观察到到的有 K—S 关 系、西山关系和G—T关系。 (1)K—S关系 {110} αˊ∥{111}γ; <111> αˊ∥<110>γ
[-111] (110) (111)
[-101]
按K-S关系,马氏体在奥氏体中共有 24种不同的空 间取向。
c原子溶入m点阵中使扁八面体短轴方向上的fe原子间距增长了36而另外两个方向上则收缩4从而使体心立方变成了体心正方点阵由间隙c原子所造成的这种不对称畸变称为畸变偶极可以视其为一个强烈的应力场c原子就在这个应力场的中心这个应力场与位错产生强烈的交互作用而使m的强度提高
回火过程组织转变的五个阶段

回火过程组织转变的五个阶段
1. 马氏体分解
在回火初期,马氏体组织开始分解,析出渗碳体或碳化物。
这一过程是通过固态相变进行的,马氏体中的碳原子逐渐向碳化物中迁移,使马氏体中的碳含量逐渐降低。
2. 碳化物聚集长大
随着回火温度的升高,碳化物开始聚集长大,形成一定大小的碳化物颗粒。
这个过程会继续进行,直到达到某个温度后,碳化物不再长大。
3. 残余奥氏体转变为铁素体
在回火过程中,残余奥氏体转变为铁素体。
这个过程是通过固态相变进行的,奥氏体中的碳原子逐渐向铁素体中迁移,使奥氏体中的碳含量逐渐降低。
4. 碳化物弥散强化
在回火过程中,碳化物在铁素体基体上弥散分布,对铁素体基体产生强化作用。
这个过程会增加材料的强度和硬度。
5. 晶粒长大
随着回火温度的升高,晶粒会逐渐长大。
这个过程会增加材料的韧性。
当晶粒长大到一定程度时,材料的性能达到最佳状态。
第五节马氏体转变

板条状M----低碳{111}、中碳{225} 片状M-------中高碳{225}、高碳{259}
惯习面与M形状的关系
4.转变的非恒温性和不完全性
Ms点以下形成M----在连续冷却条件下
未获100%M,有残余奥氏体存在—AR 冷处理—针对高碳钢、高碳合金钢和
某些中碳合金钢的Mf点低于室温,将 此类钢继续深冷至零下温度的操作。
重点: 1.马氏体转变的主要特点; 2.马氏体的组织形态; 3.马氏体的热力学分析; 4.马氏体的力学性能 难点: 1.马氏体转变的特点; 2.影响马氏体转变的因素。
§5-1马氏体相变的主要特征
一、马氏体的晶体结构
AM 无扩散型相变 只有点阵重构而无成分变化
C在-Fe中的过饱和固溶体
M或´
1.晶体结构----体心正方点阵
2.奥氏体的层错能
层错能低—利滑移—产生位错—板条M
层错能高—不利滑移—产生孪晶—片M
证明:①18-8型钢不锈钢,其A层错能较低,在液氮中淬火—板条M
②Fe-33Ni合金,层错能高,淬火后其孪晶区扩大
3.A和M的强度
Ms点处 s206MPa 低—{111} 板条M s206MPa {259} 片M
2.马氏体的反常正方度----M正方度与碳含量的关系不符合上式
1)无序分布,c/a
反常低正方度 碳原子在M中有序化转变
2)c原子几乎都处于同一组空隙位置(完全有序化):
T回升至室温无序转变c/a
二、马氏体转变的特点 1.切变共格和表面浮凸现象
①与M相交的表面,一边凹陷,一边突起,牵动相邻A也呈倾突现象; ②刻划一条直线,马氏体形成后变成一条折线 说明: ①马氏体转变以切变的方式实现; ②M和A的界面为共格界面
钢的热处理-马氏体转变
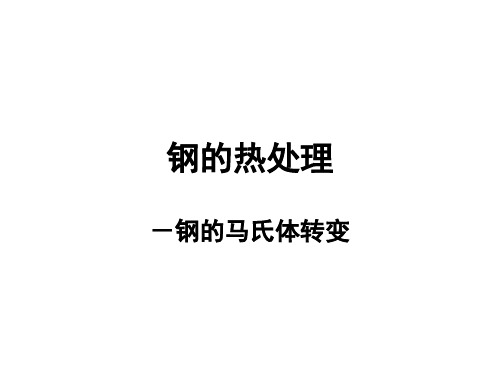
自由能
M
A F
T4 T1 T3 T T2
T0 温度
合金元素对Ms点的影响原因分 析
2.其它因素对Ms点的影响 (1)奥氏体晶粒大小的影响
一般情况是,增大奥氏体的晶粒尺寸会 使Ms点升高,反之使其降低。
2.奥氏体与马氏体的强度
实验发现,不论奥氏体中加入何种元素或 其Ms点如何变化,凡是在Ms点温度,奥氏 体的屈服强度极限小于某一极限值(约 2条1马0M氏P体a)或时{2,25就}γ片形状成马惯氏习体面;为当{1奥11氏}γ的体板的 屈服强度极限大于该极限值时,则形成惯 习面为 {259}γ片状马氏体;当相变过程中 在奥氏体与马氏体内均发生滑移变形时, 形成{111}γ马氏体;当在奥氏体中产生滑移 而在马氏体中发生孪生时,形成{225}γ 马 氏体;只在马氏体中发生孪生时才形成 {259}γ 马氏体。
这种因形变而促生的马氏体又称为应力诱发 马氏体,或加工诱发马氏体。
Md点:塑性变形能促生马氏体的最高温度,高于Md 点,则在变形温度下只能使奥氏体发生变形,不 形成马氏体。
注意: Md点以下的塑性变形对随后冷却时发生的马 氏体转变有抑制作用。
2. Md点以上塑性变形的影响
(1)对具有变温型马氏体转变的钢,奥氏体的预 先变形会降低Ms点,并减少冷却时产生的马氏体 量。变形温度越高,此作用越大。但总体来说, 变形对Ms点和马氏体量的影响并不十分明显。
二、马氏体的等温形成
具有等温马氏体转变方式的合金(尤其 是工业用钢)为数不多。
首先在Fe-Ni(22.5~26%)-Mn(2~4%)发现 马氏体的等温转变现象。
马氏体转变

非平衡条件下,金属和合金中发生的非扩散的晶型转变。
是固态一级相变的一种基本类型。
产物称为马氏体,通常具有板、片状的外形。
研究简史19世纪中叶,英国人索尔拜首次用显微镜观察了淬硬钢的金相组织,后对此种针状组织物命名为马氏体。
图1示出高碳钢淬火态的金相组织,针状物(其空间形态为板片状)为马氏体,基底为残留奥氏体。
20世纪20年代,美国人芬克和苏联人库尔久莫夫分别(独立地)用x射线衍射技术确定了钢中马氏体的本质:体心正方结构,碳在a-Fe中的过饱和固溶体,奥氏体在非平衡(大过冷)条件下转变成的一种介稳相。
到50年代,不但积累了大量有关钢中马氏体转变的技术资料,而且还发现在一系列有色合金及某几种纯金属中也发生相似的转变。
在此基础上,逐渐认识到,以钢中马氏体形成为代表的相变,是一种与历来了解的固态扩散型晶型转变具有本质区别的固态一级相变--非扩散的晶型转变,定名为马氏体转变。
各种合金系中经马氏体转变形成的低温产物皆称为马氏体,如钛合金中马氏体、铜合金中马氏体等。
马氏体转变是金属热处理时发生的相变的基本类型之一,对钢的强化热处理及形状记忆合金的应用技术具有重要意义。
(1)宏观形状效应。
不但有体积变化,而且有形状变化。
如图2所示,在母相的自由表(平)面上,转变成马氏体的那块面积发生一定角度的倾斜,并仍保持为平面。
由此带动邻近的母相呈山峰状凸起(另一侧下凹),原始态表面的直线刻痕转入新相后仍为直线,在界面处不断开,保持连续。
(2)非扩散。
生成相与母相成分相同,以共格或半共格界面为生长相界面,故不存在相界面迁移的热激活机制。
形核率和长大速度皆与扩散型转变的热动力学处理结果显著不符。
(3)惯习现象。
生成相的片、板的空间取向不是任意的,而是平行于母相的某个晶面(称为惯习面)。
作为母相的一个原子面,惯习面在相变过程中既不畸变,也不转动,是不变平面。
图3是对图2的局部作进一步标注,a'b'曲面发生转动,面积也有变化;但AB线段长度不变,方向也不变。
金属材料热处理原理 第五章 马氏体转变

二、马氏体转变的主要特点 1. 切变共格和表面浮凸现象
钢因马氏体转变而产生的表面浮凸
马氏体形成时引起的表面倾动
马氏体是以切变方式形成的,马氏体与奥氏体 之间界面上的原子既属于马氏体,又属于奥氏体, 是共有的;并且整个相界面是互相牵制的,这种界 面称之为“切变共格”界面。
马氏体和奥氏体切变共格交界面示意图
4. 马氏体转变是在一个温度范围内完成的
马氏体转变量与温度的关系
Ms—马氏体转变开始温度;Mf—马氏体转变终了点; A、B—残留奥氏体。
5. 马氏体转变的可逆性
在某些铁合金中,奥氏体冷却转 变为马氏体,重新加热时,已形成的 马氏体又可以逆马氏体转变为奥氏体, 这就是马氏体转变的可逆性。一般将 马氏体直接向奥氏体转变称为逆转变。 逆转变开始点用As表示,逆转变终了 点用Af表示。通常As温度比Ms温度高。
2. 马氏体转变的无扩散性
马氏体转变的无扩散性有以下实验证据:
(1) 碳钢中马氏体转变前后碳的浓度没有 变化,奥氏体和马氏体的成分一致,仅发生晶 格改组:
γ-Fe(C) → α-Fe(C)
面心立方 体心正方
(2) 马氏体转变可以在相当低的温度范围 内进行,并且转变速度极快。
3. 具有一定的位向关系和惯习面
西山关系示意图
③ G-T关系
{111}γ∥{110}α′ 差1°;<110>γ∥<111>α′ 差2°。
(2) 惯习面
马氏体转变时,新相总是在母相的某个晶面族上 形成,这种晶面称为惯习面。在相变过程中从宏观上 看,惯习面是不发生转动和不畸变的平面,用它在母 相中的晶面指数来表示。
钢中马氏体的惯习面随碳含量及形成温度不同而 异,常见的有三种:(1) 含碳量小于0.6%时,为{111}γ; (2) 含碳量在0.6%~1.4%之间时,为{225}γ;(3) 含碳 量高于1.4%时,为{259}γ。随马氏体形成温度下降, 惯习面有向高指数变化的趋势。
第四章马氏体转变
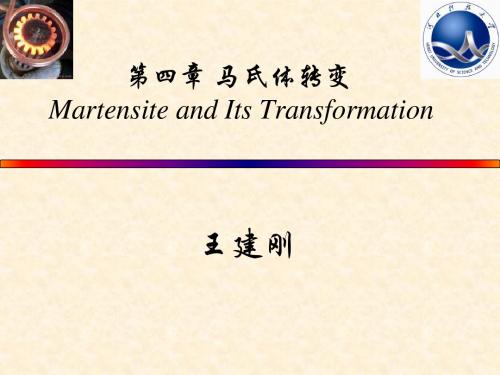
马氏体研发史
1930年,Γ. B.库尔久莫夫和G.萨克斯(Sacks)首先 测得Fe-C合金马氏体与母相奥氏体保持一定的晶体学位向关 系,即K-S关系。 1933年,R. E.迈尔(Mehl )测得在中、高碳钢中马氏体 在奥氏体的{225},晶面上形成,被称为惯习面。
1934年,西山测得Fe-Ni合金马氏体相变时存在西山关系。 1949年,Greniger和Troiano测定了Fe-22 % 、Ni-0.8C%合 金中的马氏体位向,发现了G-T关系。 1951年,J. W. Christian首先提出了马氏体相变的层错形核 模型。1953年,Frank首先提出 Fe-C{225},马氏体与母相 间的位错界面模型。它促成了K-D位错胞核胚模型的提出。
4.1.2 马氏体转变的特点
一、表面浮凸现象和切变共格 二、无扩散性 三、具有特定的位向关系 四、惯习面的不变性 五、马氏体相变具有一个形成温度范围 六、马氏体转变的可逆性
4.1.2 马氏体转变的特点
一、表面浮凸现象和切变共格 (200~196℃)
马氏体形成时试样表面浮凸现象
4.1.2 马氏体转变的特点
{111}γ //{110}α 差1º; <110>γ // <111>α 差2º
•四、惯习面和不变平面
马氏体相变不仅新相和母相之间有严格的位向关系,而 且马氏体是在母相的一定晶面上开始形成的,这个晶面即 称为惯习面,通常以母相的晶面指数表示。 钢中马氏体的惯习面常见的有三种:{111}γ 、{225}γ 、 和{259}γ。惯习面随碳含量及形成温度不同而异: 碳含量小于 0.6%时为{111}γ, 碳含量在 0.6%~1.4%之间为{225}γ, 碳含量高于 1.4%时为{259}γ 。
4.1.2 马氏体转变的特点
第4章_马氏体转变

4.1.2 马氏体转变的特点
1. 表面浮凸效应和共格切变性
共格界面的界面能比非 共格界面小,但其弹性应 变能却较大。因此随着马 氏体的形成必定会在其周 围奥氏体点阵中产生一定 的弹性应变,从而积蓄一 定的弹性应变能 (或称共格 弹性能) 。
马氏体形成时在其周围奥氏体点阵 中引起的应变场(示意图)
4.1.2 马氏体转变的特点
马氏体转变量是在 Ms~Mf 范围内通过不断降温来增 加, 即马氏体转变量是温度的函数,与等温时间无关。
马氏体转变量与温度和等温时间的关系图
在很多情况下,冷却到Mf 温度后,并不能得到 100%的马氏体组织,仍然保留部分未转变的奥氏体, 称为残余奥氏体,以AR表示。这种现象称为马氏体 转变的不完全性。
另外,马氏体中的碳含量与原奥氏体完全一致,这表 明马氏体转变时也没有发生碳的扩散。因此,马氏体转 变属于无扩散型相变。这是它与其它类型相变相区别的 一个重要持点。
4.1.2 马氏体转变的特点
3. M转变的位向关系及惯习面
马氏体转变时马氏体与奥氏体存在着严格的晶体学关 .2 马氏体转变的特点
1. 表面浮凸效应和共格切变性
可见,马氏体形成是以切变的方式实现的,同时马氏 体和奥氏体之间界面上的原子为两相所共有,即新相和 母相间保持共格关系。
4.1.2 马氏体转变的特点
1. 表面浮凸效应和共格切变性
由于这种界面是以母相切变维持共格关系,故称为 “切变共格”界面,即原A中的任一平面在转变成M后 仍为一平面。M的长大便是依靠母相中原子做有规则的 迁移(切变)使界面推移而不改变界面上共格关系。
马氏体的正方度取决于其碳含量,碳含量愈高,其点 阵中被充填的碳原子数量愈多,则正方度便愈大。当 wC<0.25%时,c/a=1,马氏体为体心立方晶格。
4.6马氏体相变动力学和残留奥氏体
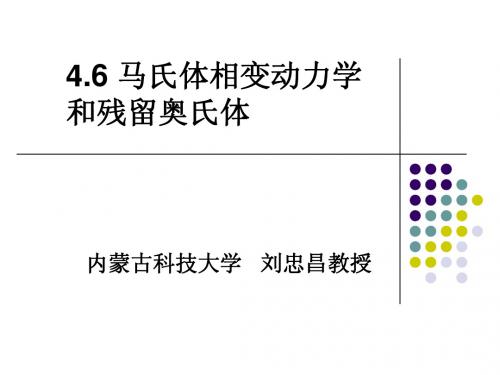
内蒙古科技大学 刘忠昌教授
1.马氏体相变动力学分类:
①变温相变动力学,碳素钢、合金钢的马氏体 相变一般属于此类; ②等温相变动力学,在Fe-Ni-Mn等特殊合金中 出现; ③爆发型转变动力学,在Fe-Ni合金中出现; 此外,还有如在铬轴承钢和高速钢中出现的变 温转变兼有等温相变的动力学。
3.2正确的解释
(1)在等温停留过程中,变温马氏体中的 C、N原子扩散进入奥 氏体中,降低了尚未转变的奥氏体的马氏体点,增加了稳定性。 (2)马氏体中的 C、N原子扩散进入晶界、相界面、位错等缺陷 处,阻碍了马氏体的形核过程。 这一切需增加相变驱动力所需的过冷度,即为θ 值。
近年来,淬火+(碳)配分)工艺( Q-P )多 有研究。相对于传统,经Q-P工艺处理的钢能够 获得更多的残余奥氏体。该工艺通过先淬火至QT 温度(Quenching Temperature,Ms<QT<Mf), 形成部分变温马氏体,在QT温度下停留一段时间, 控制碳的配分,即碳原子从先形成变温马氏体向 未转变奥氏体中扩散富集,最后淬火至室温得到 主要由马氏体和富碳的残余奥氏体组成的多相组 织。 由于碳在马氏体的固溶度远小于奥氏体,在某温 度配分过程中,碳从新鲜马氏体向未转变奥氏体 中扩散,导致未转变奥氏体中的含碳量相对较高。 应用扫描电镜能谱分析,测定出Q-P组织中存在 碳原子分布不均匀的现象,即残留奥氏体中含碳 量较高 。
2.马氏体长大速度
马氏体长大速率不等,分为: ①高速长大的高碳马氏体,无论变温、等温、爆发 型相变,马氏体片的长大速度均为105 cm/s数量级, 即一片马氏体可在10-7s内形成; ②低速长大的低碳型马氏体,长大速度100mm/s数量 级; ③慢速长大马氏体,如U-Cr合金马氏体,其长大速 率仅仅0.5mm/h; ④表面马氏体,如Fe-28.8Ni合金在Ms点以上,长大 速率为1×10-2cm/s; ⑤热弹性马氏体,在光学显微镜下可观察到相界面 的移动。
第五章 马氏体转变(14-1)
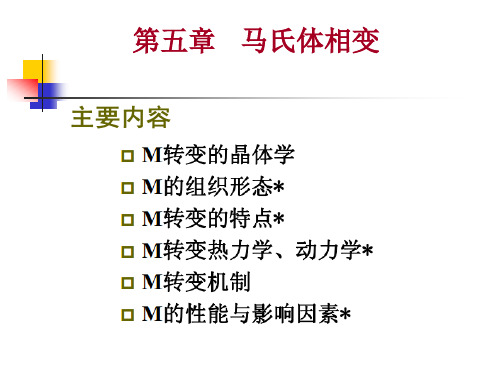
——切变共格性
——C含量越高,Ms越低,残余奥氏体越多
形状改变
界面
非扩散相变 ——原子发生切变 位移,但相对位置 没有发生变化 ——军队式转变 扩散型相变 ——原子不切变,位 置由于扩散而改变 ——平民式转变
界面
形状不改变
注意:马氏体相变的最基本的特征: (1)切变共格性 (2)无扩散性 其他特点均由这两个基本特点派生而来。
(四)淬火冷却速度的影响——有争议?
一般工业用淬火介质所能达到的冷却速度 对Ms没有影响。 (五)磁场的影响 外加磁场,诱发M转变,Ms点↑。 原因: 磁场中M的自由能降低,而A的自由能影响不 大,T0 ↑, Ms点↑,类似形变诱发M相变。
f 1 f exp[ MS ( T 1 ( exp[ M q )] S Tq )]
晶体结构类型: 体心立方或体心正方等结构 后者存在正方度: c/a c/a =1+0.046C% ——与 C 含量有关
c b
a
——扁八面体 间隙位置
(1) α马氏体
体心立方(b.c.c), C%<0.1%, c/a=1 体心正方(b.c.t), C%: 0.1%~1.4%, c/a>1; b=a 体心斜方(b.c.p), C%>1.4%, c/a>1, b/a>1
200 ℃本质:奥氏体变形方式的分界温度
Ms↑,A强度低 (<210Mpa), 易滑移(所需应力小) →位错 , 板条; Ms↓, A强度高 (>210Mpa),
临 滑移 界 分 孪生 切 应 力 片状 板条状 200 ℃ 温度
滑移或孪生所需应力与温 度及马氏体亚结构的关系
易孪生(所需应力小)
→孪晶 , 片状。
第十七章-马氏体
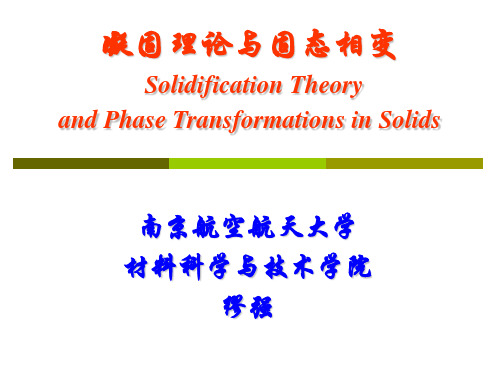
缪强
第十七章 马氏体转变
前言
马氏体转变是由钢奥氏体化后快速冷却,抑 制其扩散型分解,在低温下进行的无扩散型相 变。马氏体转变是钢件热处理强化的主要手段, 产生马氏体组织的热处理工艺称为淬火。因此 马氏体转变的理论研究与热处理生产实践有密 切的关系。
前言
由于钢的成分和热处理条件不同,所获得的 马氏体的形态和亚结构也不相同,继而对钢件 的组织和力学性能产生不同的影响。通过对马 氏体形成规律的了解,才能正确地指导热处理 生产实践,充分发挥钢材的潜力。
第一节 钢中马氏体的晶体结构
结果使短轴方向的Fe间距伸长36%),而另两 个方向缩短4%,从而使体心立方变为体心正方 点阵。
由间隙碳原子造成 的这种非对称畸变称 为畸变偶极,可将其 视为一个强烈的应力 场,C原子就在这个 应力场的中心。
第一节 钢中马氏体的晶体结构
马氏体具有体心正方晶格 (a=b≠c)
第二节 马氏体转变的特点
γ
α’
γ 惯习面
C
F
G
S’ S
B
T’
T
D
E
R
A O
H P
中脊面
N M
马氏体形成时引起的表面倾动
第二节 马氏体转变的特点
若相变前在试样抛光面上刻一直线划痕STR,则 相变后产生浮凸使其变为折线S’T’TR,在显微镜 光线照射下,浮凸两边呈现明显的山阴和山阳。故 马氏体的形成是通过切变方式来进行的,马氏体和 奥氏体界面的原子是二者共有的,而整个相界面是 相互牵制的。
第二节 马氏体转变的特点
这种界面称为切变共格界面,即通过母相的切变 来维持共格关系的,也称第二类共格界面。
在具有共格界面的新旧两相中,原子位置有对应 关系,新相长大时,原子只作有规则的迁动而不改 变共格状态。