钢带轧制常见缺陷原因分析
轧制缺陷及质量控制
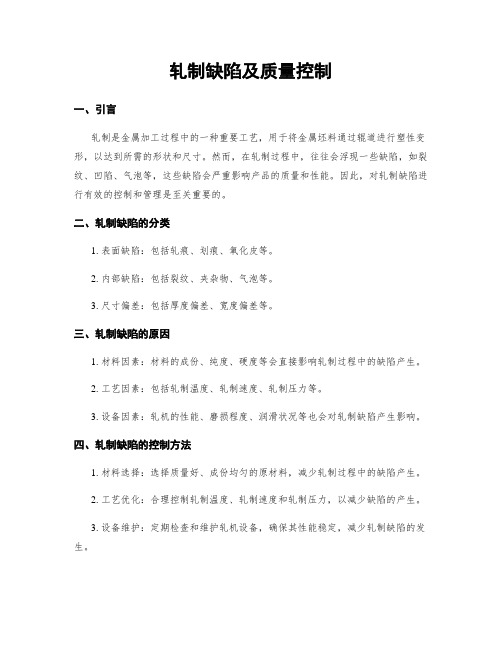
轧制缺陷及质量控制一、引言轧制是金属加工过程中的一种重要工艺,用于将金属坯料通过辊道进行塑性变形,以达到所需的形状和尺寸。
然而,在轧制过程中,往往会浮现一些缺陷,如裂纹、凹陷、气泡等,这些缺陷会严重影响产品的质量和性能。
因此,对轧制缺陷进行有效的控制和管理是至关重要的。
二、轧制缺陷的分类1. 表面缺陷:包括轧痕、划痕、氧化皮等。
2. 内部缺陷:包括裂纹、夹杂物、气泡等。
3. 尺寸偏差:包括厚度偏差、宽度偏差等。
三、轧制缺陷的原因1. 材料因素:材料的成份、纯度、硬度等会直接影响轧制过程中的缺陷产生。
2. 工艺因素:包括轧制温度、轧制速度、轧制压力等。
3. 设备因素:轧机的性能、磨损程度、润滑状况等也会对轧制缺陷产生影响。
四、轧制缺陷的控制方法1. 材料选择:选择质量好、成份均匀的原材料,减少轧制过程中的缺陷产生。
2. 工艺优化:合理控制轧制温度、轧制速度和轧制压力,以减少缺陷的产生。
3. 设备维护:定期检查和维护轧机设备,确保其性能稳定,减少轧制缺陷的发生。
4. 润滑控制:选择合适的润滑剂,保证轧制过程中的润滑效果,减少磨擦和磨损,降低缺陷产生的可能性。
五、质量控制措施1. 检测方法:采用超声波、X射线、磁粉探伤等非破坏性检测方法,及时发现和排除轧制缺陷。
2. 检测设备:使用高精度的检测设备,确保对轧制缺陷的检测准确性和可靠性。
3. 检测标准:制定严格的轧制缺陷检测标准,明确缺陷的类型、数量和尺寸要求。
4. 检测频率:根据产品的重要性和应用领域,确定合理的检测频率,确保产品质量的稳定性和可靠性。
六、案例分析以某钢铁公司为例,该公司采用了先进的轧制设备和严格的质量控制措施,成功地控制了轧制缺陷的发生。
通过优化工艺参数,选择高质量的原材料,并定期进行设备维护和润滑控制,该公司的产品质量得到了有效提升。
同时,该公司还建立了完善的质量检测体系,采用先进的检测设备和严格的检测标准,确保产品质量的稳定性和可靠性。
带钢产生的缺陷

带钢缺陷及其产生的原因带钢缺陷常见的几种:1、结疤特征:钢带表面呈“蛇状”或“鳞状”的金属薄片,外形近似一个闭和的曲线。
一种是嵌在表面上不易脱落;一种是粘和到表面上易脱落。
产生原因:(1)钢锭由于浇注条件不同而产生的结疤、重皮,是轧制钢带表面产生结疤的主要原因。
(2)钢带内部靠近表面层的气泡及夹杂层在轧制中破裂变成结疤。
(3)轧辊表面不好,有缺陷或有砂眼,使钢带表面粗糙。
2、裂纹特征:钢带表面完整性比较严重的破裂,它是以纵向、横向或一定角度的形式出现的尖底裂缝。
产生原因:(1)钢质不良,带坯上有非金属夹杂及皮下气泡。
(2)带坯表面缺陷清楚不彻底。
(3)热轧钢带加热制度不当,轧制时金属延伸不均。
3、分层(又称起层)特征:钢带截面上有局部的、明显的金属结构分离层。
产生原因:(1)钢质不良,带坯有皮下气泡和非金属夹杂物。
(2)坯料有缩孔残余或严重的疏松。
4、气泡:特征:钢带表面上有分布无规律的且大小不同的圆形凸包,沿凸包切断后称层状。
产生原因:(1)由于钢锭凝固时气体析出形成气泡。
(2)酸洗时,金属内部孔隙中进入氢原子形成气泡(3)冶炼过程中,浇铸过程中脱气不良造成的。
5、表面夹杂:特征:钢带表面上的非金属夹杂物,颜色为红棕色、淡黄色、灰白色、形状为点状、块状或长条状。
产生原因:(1)炼钢时造渣不好或盛钢桶不净。
(2)热轧时,坯料在加热过程中,炉渣或耐火材料碎块粘附到坯料上。
6、麻点:特征:钢带表面存在细小凹坑群和局部的粗糙面,麻点的数量多,面积小,形状不规则;凹坑的数量少,面积大。
产生原因:(1)热轧时压入了氧化铁皮,酸洗未净,又经过冷轧造成。
(2)冷轧时,粘在轧辊或平整机组工作辊上的氧化铁皮压入钢带表面上。
(3)轧辊磨损严重造成钢带的麻面。
(4)冷轧钢带时表面不净,粘有污泥尘土,或异物压入钢带表面后脱落。
(5)钢带严重的锈蚀。
(6)过酸洗造成钢带的麻眼。
7、划痕:特征:钢带表面呈直而细得沟痕,一般是沿轧制方向,连续或断续的分布于带钢的全长或局部。
轧制缺陷及质量控制

轧制缺陷及质量控制一、引言轧制是金属加工中的一种重要工艺,用于将金属坯料通过轧机进行塑性变形,以获得所需的形状和尺寸。
然而,在轧制过程中,由于各种因素的影响,会产生一些缺陷,如裂纹、夹杂物、表面缺陷等,这些缺陷会严重影响产品的质量和性能。
因此,对轧制缺陷进行有效的控制和管理,是确保产品质量的关键。
二、轧制缺陷的分类1. 表面缺陷:包括轧痕、轧花、氧化皮、划伤等。
2. 内部缺陷:包括夹杂物、裂纹、孔洞等。
3. 尺寸偏差:包括厚度偏差、宽度偏差等。
三、轧制缺陷的原因分析1. 材料因素:原材料的质量和成份会直接影响轧制过程中的缺陷产生。
如含有夹杂物、氧化皮等。
2. 工艺参数:轧制过程中的轧制力、轧制速度、轧制温度等参数的控制不当,会导致缺陷的产生。
3. 设备状况:轧机的磨损、不平衡等问题会影响轧制质量。
4. 操作人员:操作人员的技术水平和经验也会对轧制质量产生影响。
四、轧制缺陷的质量控制方法1. 前期控制:在轧制前对原材料进行严格的检查和筛选,确保材料的质量符合要求。
2. 工艺参数控制:根据产品的要求和轧制材料的特性,合理设置轧制力、轧制速度、轧制温度等参数,以减少缺陷的产生。
3. 设备维护:定期对轧机进行检修和维护,确保设备的正常运行,减少设备因素对轧制质量的影响。
4. 操作人员培训:加强对操作人员的培训和技术指导,提高其对轧制过程中缺陷产生原因的认识和处理能力。
5. 检测方法:采用先进的无损检测技术,如超声波检测、磁粉检测等,对轧制产品进行全面的检测,及时发现和排除缺陷。
6. 质量管理体系:建立完善的质量管理体系,包括质量控制计划、质量检验记录、质量问题分析等,确保轧制产品的质量稳定可控。
五、案例分析某钢铁厂在轧制过程中,时常浮现轧制缺陷问题,导致产品质量不稳定,客户投诉频繁。
经过对生产过程的分析和改进,采取了以下措施:1. 强化原材料的筛选工作,严格控制夹杂物和氧化皮的含量。
2. 优化工艺参数,合理调整轧制力、轧制速度和轧制温度,降低缺陷的产生率。
带钢轧制时产生的主要缺陷与分析

带钢轧制时产生的主要缺陷与分析带钢轧制时产生的主要缺陷与分析在热带轧机上轧制带钢所形成的缺陷最主要有下列几种:(1)结疤。
在板坯清理时对裂口及裂纹没有全部清除干净,结果在轧制时形成结疤;板坯加热时过热,特别是铬不锈钢,轧制时在带钢上形成结疤。
带钢坯表面大量集结的非金属夹杂物,也是产生结疤的原因。
(2)裂边。
板坯侧面缺陷未全面清除干净,这是带钢裂边的原因。
(3)过热。
板坯在过高温度下长时间停留会引起过热。
过热板坯轧制时会产生大裂口和剥落;邻近过热的部分出现细裂纹,细裂纹在进一步轧制时会变成结疤。
为防止板坯过热必须严格遵守规定的加热制度,尤其是高温下的均热时间。
加热铁素体类钢时,温度超过850℃后必须快速加热。
(4)机械损伤。
轧入碎屑、压痕、划痕是热轧不锈带钢表面最有特征的缺陷。
轧人碎屑和压痕缺陷是由于坯料上的结疤块、裂边在导卫上摩擦时有碎片落到带钢表面上以及其他东西被轧辊或矫直机辊子压人而形成的。
划痕大部分是在带钢运动时,下表面与不光滑的导卫、辊面不平的辊子及被动辊相接触时形成的。
上表面划痕通常是在未卷紧运送时卷层间摩擦造成的。
在卷取中,带钢与卷取机成形辊和喂料辊之间发生摩擦时,带钢表面上会产生很多短条状划伤。
(5)带钢厚薄不均。
带钢长度上的厚度不均匀与沿板坯长度加热的均匀性及带钢在机架间张力值有关。
带钢的前端和后端一般比中部厚一些,这是因为在连续式精轧机组中带钢端部没有张力的缘故。
带钢后端一般比前端厚,这是温度不同所致热轧带钢开裂的改进热轧带钢生产的工艺流程:铁液一铁液预处理一顶底复吹转炉一脱氧合金化一吹氩一板坯连铸一铸坯检验一加热一粗轧高压水除鳞一立辊轧一可逆式粗轧一中轧一热卷箱一精轧高压水除鳞一精轧一层流冷却一卷取一入库。
热轧带钢在生产检验及用户使用过程中常出现的开裂现象,并对开裂带钢进行了化学成分及低倍和金相检验分析。
结果表明,化学成分符合要求,铸坯存在皮下气泡、带钢存在非金属夹杂及游离渗碳体是带钢出现开裂主要原因,针对以上情况给你针对性改进建议,具体如下。
轧制缺陷及质量控制
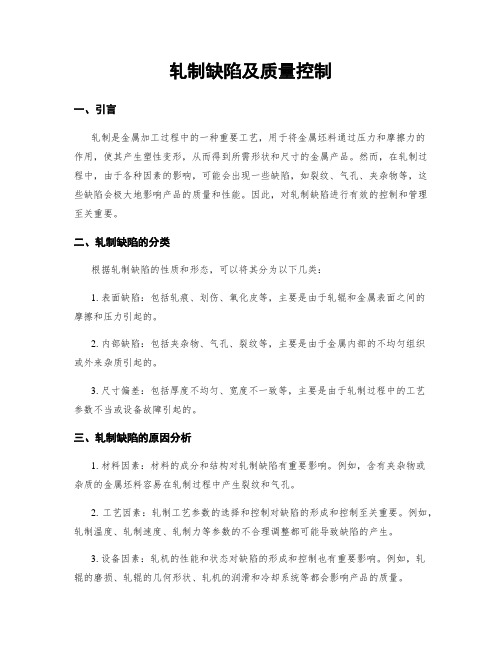
轧制缺陷及质量控制一、引言轧制是金属加工过程中的一种重要工艺,用于将金属坯料通过压力和摩擦力的作用,使其产生塑性变形,从而得到所需形状和尺寸的金属产品。
然而,在轧制过程中,由于各种因素的影响,可能会出现一些缺陷,如裂纹、气孔、夹杂物等,这些缺陷会极大地影响产品的质量和性能。
因此,对轧制缺陷进行有效的控制和管理至关重要。
二、轧制缺陷的分类根据轧制缺陷的性质和形态,可以将其分为以下几类:1. 表面缺陷:包括轧痕、划伤、氧化皮等,主要是由于轧辊和金属表面之间的摩擦和压力引起的。
2. 内部缺陷:包括夹杂物、气孔、裂纹等,主要是由于金属内部的不均匀组织或外来杂质引起的。
3. 尺寸偏差:包括厚度不均匀、宽度不一致等,主要是由于轧制过程中的工艺参数不当或设备故障引起的。
三、轧制缺陷的原因分析1. 材料因素:材料的成分和结构对轧制缺陷有重要影响。
例如,含有夹杂物或杂质的金属坯料容易在轧制过程中产生裂纹和气孔。
2. 工艺因素:轧制工艺参数的选择和控制对缺陷的形成和控制至关重要。
例如,轧制温度、轧制速度、轧制力等参数的不合理调整都可能导致缺陷的产生。
3. 设备因素:轧机的性能和状态对缺陷的形成和控制也有重要影响。
例如,轧辊的磨损、轧辊的几何形状、轧机的润滑和冷却系统等都会影响产品的质量。
四、轧制缺陷的质量控制措施为了有效控制轧制缺陷,提高产品的质量和性能,可以采取以下措施:1. 优化材料选择:选择质量好、含杂质少的金属坯料,减少夹杂物和杂质对产品质量的影响。
2. 严格控制工艺参数:根据不同的金属材料和产品要求,合理选择轧制温度、轧制速度、轧制力等参数,确保轧制过程中的温度和力的均匀分布。
3. 定期维护设备:定期对轧机进行维护和检修,保证轧辊的几何形状和表面光洁度,确保润滑和冷却系统的正常运行。
4. 引入先进的检测技术:利用先进的无损检测技术,如超声波检测、磁粉检测等,对轧制产品进行全面、准确的检测,及时发现和处理缺陷。
轧制缺陷及质量控制
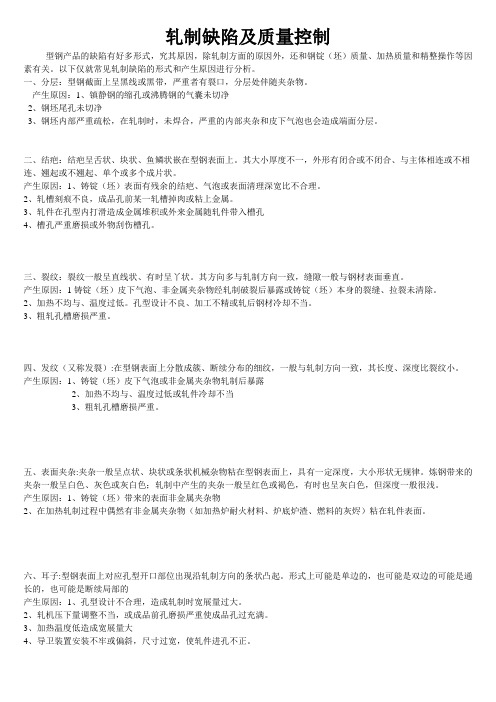
轧制缺陷及质量控制型钢产品的缺陷有好多形式,究其原因,除轧制方面的原因外,还和钢锭(坯)质量、加热质量和精整操作等因素有关。
以下仅就常见轧制缺陷的形式和产生原因进行分析。
一、分层:型钢截面上呈黑线或黑带,严重者有裂口,分层处伴随夹杂物。
产生原因:1、镇静钢的缩孔或沸腾钢的气囊未切净2、钢坯尾孔未切净3、钢坯内部严重疏松,在轧制时,未焊合,严重的内部夹杂和皮下气泡也会造成端面分层。
二、结疤:结疤呈舌状、块状、鱼鳞状嵌在型钢表面上。
其大小厚度不一,外形有闭合或不闭合、与主体相连或不相连、翘起或不翘起、单个或多个成片状。
产生原因:1、铸锭(坯)表面有残余的结疤、气泡或表面清理深宽比不合理。
2、轧槽刻痕不良,成品孔前某一轧槽掉肉或粘上金属。
3、轧件在孔型内打滑造成金属堆积或外来金属随轧件带入槽孔4、槽孔严重磨损或外物刮伤槽孔。
三、裂纹:裂纹一般呈直线状、有时呈丫状。
其方向多与轧制方向一致,缝隙一般与钢材表面垂直。
产生原因:1铸锭(坯)皮下气泡、非金属夹杂物经轧制破裂后暴露或铸锭(坯)本身的裂缝、拉裂未清除。
2、加热不均与、温度过低。
孔型设计不良、加工不精或轧后钢材冷却不当。
3、粗轧孔槽磨损严重。
四、发纹(又称发裂):在型钢表面上分散成簇、断续分布的细纹,一般与轧制方向一致,其长度、深度比裂纹小。
产生原因:1、铸锭(坯)皮下气泡或非金属夹杂物轧制后暴露2、加热不均与、温度过低或轧件冷却不当3、粗轧孔槽磨损严重。
五、表面夹杂:夹杂一般呈点状、块状或条状机械杂物粘在型钢表面上,具有一定深度,大小形状无规律。
炼钢带来的夹杂一般呈白色、灰色或灰白色;轧制中产生的夹杂一般呈红色或褐色,有时也呈灰白色,但深度一般很浅。
产生原因:1、铸锭(坯)带来的表面非金属夹杂物2、在加热轧制过程中偶然有非金属夹杂物(如加热炉耐火材料、炉底炉渣、燃料的灰烬)粘在轧件表面。
六、耳子:型钢表面上对应孔型开口部位出现沿轧制方向的条状凸起。
带钢轧制常见缺陷原因分析
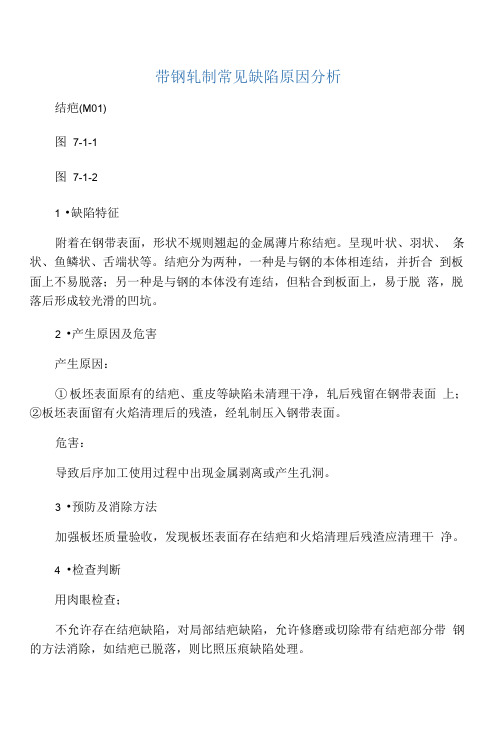
带钢轧制常见缺陷原因分析结疤(M01)图7-1-1图7-1-21•缺陷特征附着在钢带表面,形状不规则翘起的金属薄片称结疤。
呈现叶状、羽状、条状、鱼鳞状、舌端状等。
结疤分为两种,一种是与钢的本体相连结,并折合到板面上不易脱落;另一种是与钢的本体没有连结,但粘合到板面上,易于脱落,脱落后形成较光滑的凹坑。
2•产生原因及危害产生原因:①板坯表面原有的结疤、重皮等缺陷未清理干净,轧后残留在钢带表面上;②板坯表面留有火焰清理后的残渣,经轧制压入钢带表面。
危害:导致后序加工使用过程中出现金属剥离或产生孔洞。
3•预防及消除方法加强板坯质量验收,发现板坯表面存在结疤和火焰清理后残渣应清理干净。
4•检查判断用肉眼检查;不允许存在结疤缺陷,对局部结疤缺陷,允许修磨或切除带有结疤部分带钢的方法消除,如结疤已脱落,则比照压痕缺陷处理。
7.2 气泡(M02)图7-2-1闭合气泡图7-2-2 口气泡图7-2-3开口气泡1•缺陷特征钢带表面无规律分布的圆形或椭圆形凸包缺陷称气泡。
其外缘较光滑,气泡轧破后,钢带表面出现破裂或起皮。
某些气泡不凸起,经平整后,表面光亮,剪切断面呈分层状。
2•产生原因及危害产生原因:①因脱氧不良、吹氮不当等导致板坯内部聚集过多气体;②板坯在炉时间长,皮下气泡暴露或聚集长大。
危害:可能导致后序加工使用过程中产生分层或焊接不良。
3•预防及消除方法①加强板坯质量验收,不使用气泡缺陷暴露的板坯;②严格按规程加热板坯,避免板坯在炉时间过长。
4•检查判断用肉眼检查;不允许存在气泡缺陷。
7.3表面夹杂(M03)图7-3-1图7-3-21•缺陷特征板坯中的夹杂或夹渣经轧制后在钢带表面暴露的块状或长条状的夹杂缺陷称表面夹杂。
其颜色一般呈棕红色、黄褐色、灰白色或灰黑色。
2•产生原因及危害产生原因:板坯皮下夹杂轧后暴露或板坯原有的表面夹杂轧后残留在带钢表面。
危害:可能导致后序加工过程中产生孔洞、开裂、分层。
3•预防及消除方法加强板坯检查验收,不使用表面存在严重夹杂或夹渣的板坯。
钢在轧制中常见的缺陷总结

(2)轧件温度不均或压下量不均,造成各部延伸不一致。
(3)矫直机调整不当,钢轨受力偶作用。
(4)在冷却台架上翻钢时因温度较高也会出现扭转。
弯曲
钢轨沿垂直或水平方向呈现不平直的现象叫弯曲,一般呈镰刀形或波浪形,仅在端部的弯曲又叫弯头。
(1)由于重轨的头、腰、底面积相差较大,使轧制、冷却等工序操作易产生弯曲。
(4)轨形切深孔压下量过大.轨底侧压过大,使轧件出现耳子。再轧时形成折迭。
(5)有时由于孔型严重磨损.将轧件表面啃伤后再轧时形成折选。
(6)导卫板安装不当.有棱角或粘有铁皮使轧件划伤,再轧后形成折迭。
扭转
钢轨上某部分相对另一部分,沿长度方向绕其轴线旋转定角度称扭转,严重时象麻花.扭转分全长和局部扭转两种。
有单边的也有双边的有时耳子产生在型钢的全长也有局部或断续的方圆钢产生较1轧机调整不当或孔型磨损严重使成品前孔来料过大或成品孔压下量过大产生过充满多产生双边耳2进入成品孔前因事故造成温度过低进入成品孔时延伸降低宽展过大多产生双边耳子
型钢常见缺陷
缺陷名称
缺陷特征
产生原因
结疤
型钢表面上的疤状金属薄块。其大小、深浅不等,外形极不规则,常呈指甲状、鱼鳞状、块状、舌头状无规律地分布在钢材表面上,结疤下常有非金属夹杂物。
由于钢坯未清理,使原有的结疤轧后仍残留在钢材表面上。
表面夹杂
暴露在钢材表面上的非金属物质称为表面夹杂,一般呈点状、块状和条状分布,其颜色有暗红、淡黄、灰白等,机械的粘结在型钢表面上,夹杂脱落后出现一定深度的凹坑,其大小、形状无一定规律。
(1)钢坯带来的表面非金属夹杂物。
(2)在加热或轧制过程中,偶然有非金属夹杂韧(如加热炉的耐火材料及炉渣等),炉附在钢坯表面上,轧制时被压入钢材,冷却经矫直后部分脱落
轧制缺陷及质量控制

轧制缺陷及质量控制一、引言轧制是金属加工过程中的重要环节之一,对于确保产品质量具有重要意义。
本文将详细介绍轧制过程中常见的缺陷类型及其产生原因,并探讨如何通过质量控制手段来预防和解决这些缺陷问题。
二、轧制缺陷类型及原因1. 表面缺陷表面缺陷是指轧制产品表面出现的瑕疵,如麻点、划痕、氧化皮等。
其主要原因包括:- 轧辊表面粗糙度不合格:轧辊表面粗糙度过高或过低都会导致产品表面出现缺陷;- 轧辊表面污染:轧辊表面存在杂质、油污等污染物会直接影响产品表面质量;- 轧制过程中的热裂纹:高温下,金属材料容易发生热裂纹,进而导致表面缺陷。
2. 尺寸偏差尺寸偏差是指轧制产品的尺寸与设计要求之间存在的差异。
常见的尺寸偏差包括过大或过小的厚度、宽度、长度等。
尺寸偏差的原因主要有:- 轧机设备调整不当:轧机设备的调整不当会导致产品尺寸偏差;- 材料厚度不均匀:原材料的厚度不均匀会直接影响轧制产品的尺寸;- 轧机辊系磨损:轧机辊系磨损会导致轧制压力不均匀,进而影响产品尺寸。
3. 内部缺陷内部缺陷是指轧制产品内部存在的缺陷,如气孔、夹杂物等。
内部缺陷的主要原因包括:- 原材料质量问题:原材料中存在气孔、夹杂物等缺陷;- 轧机设备故障:轧机设备的故障会导致轧制产品内部出现缺陷;- 轧制过程中的温度控制不当:温度控制不当会导致金属材料内部产生缺陷。
三、质量控制手段1. 轧辊表面处理为了避免表面缺陷的产生,可以采取以下措施:- 定期对轧辊进行磨削和抛光,确保其表面粗糙度符合要求;- 加强轧辊的清洁工作,防止污染物附着在轧辊表面;- 对轧辊进行定期检测,及时发现并修复轧辊表面的磨损和裂纹。
2. 轧机设备调整与维护为了控制尺寸偏差,需要进行轧机设备的调整与维护工作:- 对轧机设备进行定期的检查和维护,确保其工作状态良好;- 对轧机设备进行精确的调整,确保产品尺寸与设计要求一致;- 定期检测轧机辊系的磨损情况,及时更换磨损严重的辊子。
轧制缺陷及质量控制

轧制缺陷及质量控制一、引言轧制是金属加工中常见的一种方法,用于将金属块或板材通过辊轧机进行塑性变形,以获得所需的形状和尺寸。
然而,在轧制过程中,由于材料的物理特性和加工条件的变化,可能会产生各种缺陷,如裂纹、疲劳、气泡等。
因此,实施有效的质量控制措施对于确保轧制产品的质量至关重要。
二、轧制缺陷的分类及原因1. 表面缺陷:包括划痕、氧化皮、锈蚀等。
这些缺陷可能由于材料表面的污染、辊轧机的磨损或加工条件的不当而产生。
2. 内部缺陷:包括气孔、夹杂物、裂纹等。
这些缺陷可能由于材料的不均匀性、热处理不当或轧制过程中的应力积累而产生。
三、质量控制措施1. 原材料选择:选择高质量的原材料,并进行严格的质量检查,以确保材料的均匀性和无明显缺陷。
2. 加热控制:控制轧制前的加热温度和时间,以确保材料的均匀加热,降低内部应力。
3. 辊轧机调整:定期检查和调整辊轧机的辊面形状和间隙,以确保均匀的轧制压力和变形。
4. 冷却控制:控制轧制后的冷却速度和方式,以避免快速冷却引起的应力和变形。
5. 检测技术:使用先进的检测技术,如超声波检测、X射线检测等,对轧制产品进行无损检测,及时发现和修复缺陷。
6. 质量记录和分析:建立完善的质量记录系统,记录每批轧制产品的质量数据,并进行分析,以识别潜在的质量问题和改进措施。
四、质量控制的效益1. 提高产品质量:通过有效的质量控制措施,可以减少轧制缺陷的发生,提高产品的表面光洁度和内部质量。
2. 降低生产成本:及早发现和修复轧制缺陷,可以减少废品率,降低生产成本。
3. 提高客户满意度:提供高质量的轧制产品,可以满足客户对产品质量的需求,提高客户满意度。
4. 保护品牌形象:通过实施有效的质量控制措施,可以保护企业的品牌形象,树立良好的企业信誉。
五、结论轧制缺陷及质量控制是轧制过程中不可忽视的重要环节。
通过选择优质原材料、控制加工条件、使用先进的检测技术和建立完善的质量记录系统,可以有效减少轧制缺陷的发生,提高产品质量,降低生产成本,提高客户满意度,保护企业品牌形象。
轧制缺陷及质量控制
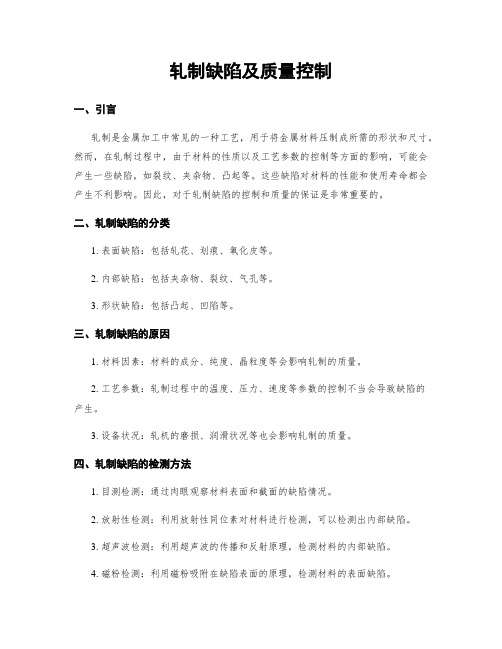
轧制缺陷及质量控制一、引言轧制是金属加工中常见的一种工艺,用于将金属材料压制成所需的形状和尺寸。
然而,在轧制过程中,由于材料的性质以及工艺参数的控制等方面的影响,可能会产生一些缺陷,如裂纹、夹杂物、凸起等。
这些缺陷对材料的性能和使用寿命都会产生不利影响。
因此,对于轧制缺陷的控制和质量的保证是非常重要的。
二、轧制缺陷的分类1. 表面缺陷:包括轧花、划痕、氧化皮等。
2. 内部缺陷:包括夹杂物、裂纹、气孔等。
3. 形状缺陷:包括凸起、凹陷等。
三、轧制缺陷的原因1. 材料因素:材料的成分、纯度、晶粒度等会影响轧制的质量。
2. 工艺参数:轧制过程中的温度、压力、速度等参数的控制不当会导致缺陷的产生。
3. 设备状况:轧机的磨损、润滑状况等也会影响轧制的质量。
四、轧制缺陷的检测方法1. 目测检测:通过肉眼观察材料表面和截面的缺陷情况。
2. 放射性检测:利用放射性同位素对材料进行检测,可以检测出内部缺陷。
3. 超声波检测:利用超声波的传播和反射原理,检测材料的内部缺陷。
4. 磁粉检测:利用磁粉吸附在缺陷表面的原理,检测材料的表面缺陷。
5. 热红外检测:利用红外辐射的原理,检测材料的缺陷情况。
五、轧制缺陷的质量控制1. 优化工艺参数:通过对轧制过程中的温度、压力、速度等参数的调整,减少缺陷的产生。
2. 提高材料质量:选择高纯度、均匀性好的材料,可以降低缺陷的发生率。
3. 定期设备维护:对轧机进行定期的检修和维护,保证设备的正常运行。
4. 强化人员培训:对操作人员进行培训,提高其对轧制缺陷的识别和处理能力。
5. 建立完善的质量管理体系:制定相应的标准和规范,对轧制缺陷进行严格的控制和管理。
六、案例分析以某钢铁公司为例,该公司通过优化工艺参数,提高材料质量,并加强设备维护,成功降低了轧制缺陷的发生率。
同时,该公司还建立了完善的质量管理体系,对轧制缺陷进行了严格的控制和管理。
经过一段时间的实施,该公司的产品质量得到了显著提升,客户的满意度也大幅度提高。
热轧带钢表面质量缺陷原因分析
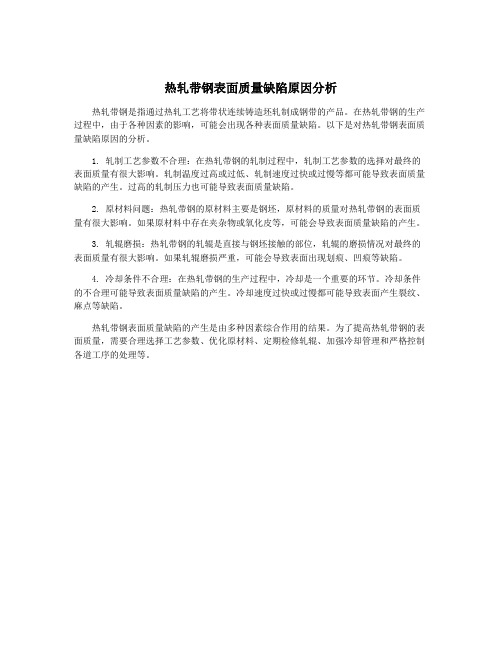
热轧带钢表面质量缺陷原因分析
热轧带钢是指通过热轧工艺将带状连续铸造坯轧制成钢带的产品。
在热轧带钢的生产过程中,由于各种因素的影响,可能会出现各种表面质量缺陷。
以下是对热轧带钢表面质量缺陷原因的分析。
1. 轧制工艺参数不合理:在热轧带钢的轧制过程中,轧制工艺参数的选择对最终的表面质量有很大影响。
轧制温度过高或过低、轧制速度过快或过慢等都可能导致表面质量缺陷的产生。
过高的轧制压力也可能导致表面质量缺陷。
2. 原材料问题:热轧带钢的原材料主要是钢坯,原材料的质量对热轧带钢的表面质量有很大影响。
如果原材料中存在夹杂物或氧化皮等,可能会导致表面质量缺陷的产生。
3. 轧辊磨损:热轧带钢的轧辊是直接与钢坯接触的部位,轧辊的磨损情况对最终的表面质量有很大影响。
如果轧辊磨损严重,可能会导致表面出现划痕、凹痕等缺陷。
4. 冷却条件不合理:在热轧带钢的生产过程中,冷却是一个重要的环节。
冷却条件的不合理可能导致表面质量缺陷的产生。
冷却速度过快或过慢都可能导致表面产生裂纹、麻点等缺陷。
热轧带钢表面质量缺陷的产生是由多种因素综合作用的结果。
为了提高热轧带钢的表面质量,需要合理选择工艺参数、优化原材料、定期检修轧辊、加强冷却管理和严格控制各道工序的处理等。
冷轧带钢常见缺陷
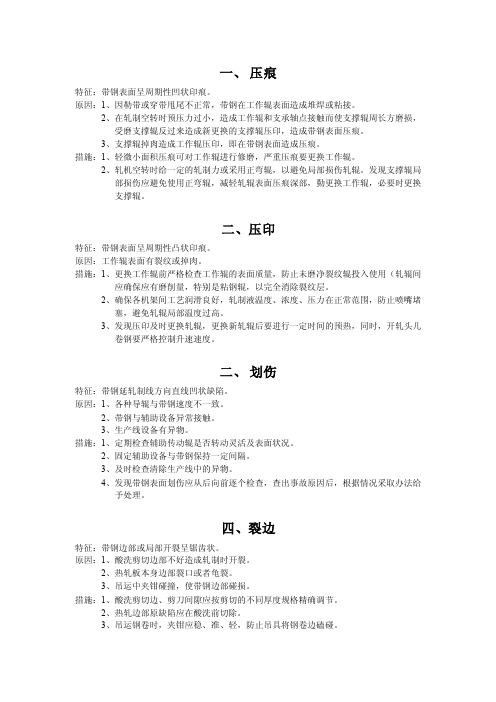
一、压痕特征:带钢表面呈周期性凹状印痕。
原因:1、因勒带或穿带甩尾不正常,带钢在工作辊表面造成堆焊或粘接。
2、在轧制空转时预压力过小,造成工作辊和支承轴点接触而使支撑辊周长方磨损,受磨支撑辊反过来造成新更换的支撑辊压印,造成带钢表面压痕。
3、支撑辊掉肉造成工作辊压印,即在带钢表面造成压痕。
措施:1、轻微小面积压痕可对工作辊进行修磨,严重压痕要更换工作辊。
2、轧机空转时给一定的轧制力或采用正弯辊,以避免局部损伤轧辊。
发现支撑辊局部损伤应避免使用正弯辊,减轻轧辊表面压痕深部,勤更换工作辊,必要时更换支撑辊。
二、压印特征:带钢表面呈周期性凸状印痕。
原因:工作辊表面有裂纹或掉肉。
措施:1、更换工作辊前严格检查工作辊的表面质量,防止未磨净裂纹辊投入使用(轧辊间应确保应有磨削量,特别是粘钢辊,以完全消除裂纹层。
2、确保各机架间工艺润滑良好,轧制液温度、浓度、压力在正常范围,防止喷嘴堵塞,避免轧辊局部温度过高。
3、发现压印及时更换轧辊,更换新轧辊后要进行一定时间的预热,同时,开轧头几卷钢要严格控制升速速度。
二、划伤特征:带钢延轧制线方向直线凹状缺陷。
原因:1、各种导辊与带钢速度不一致。
2、带钢与辅助设备异常接触。
3、生产线设备有异物。
措施:1、定期检查辅助传动辊是否转动灵活及表面状况。
2、固定辅助设备与带钢保持一定间隔。
3、及时检查清除生产线中的异物。
4、发现带钢表面划伤应从后向前逐个检查,查出事故原因后,根据情况采取办法给予处理。
四、裂边特征:带钢边部或局部开裂呈锯齿状。
原因:1、酸洗剪切边部不好造成轧制时开裂。
2、热轧板本身边部裂口或者龟裂。
3、吊运中夹钳碰撞,使带钢边部碰损。
措施:1、酸洗剪切边、剪刀间隙应按剪切的不同厚度规格精确调节。
2、热轧边部原缺陷应在酸洗前切除。
3、吊运钢卷时,夹钳应稳、准、轻,防止吊具将钢卷边磕碰。
五、热划伤特征:带钢沿轧制线方向无规律的条状凹痕。
原因:1、轧辊和热带温度过高。
轧制缺陷及质量控制

轧制缺陷及质量控制一、引言轧制是金属加工中的一种重要工艺,用于将金属坯料通过辊道压制成所需的形状和尺寸。
然而,在轧制过程中,可能会浮现一些缺陷,如裂纹、夹杂物和凹坑等,这些缺陷会降低产品的质量和性能。
因此,进行轧制缺陷的控制和质量管理是至关重要的。
二、轧制缺陷的分类1. 裂纹:轧制过程中,由于应力集中或者金属内部的缺陷,可能会导致裂纹的产生。
裂纹可以分为表面裂纹和内部裂纹两种类型。
2. 夹杂物:夹杂物是指金属中的非金属杂质,如氧化物、硫化物和氮化物等。
夹杂物会影响金属的强度和韧性。
3. 凹坑:凹坑是指金属表面的凹陷,可能是由于辊道表面的磨损或者金属表面的缺陷导致的。
三、轧制缺陷的原因分析1. 材料因素:材料的成份和内部缺陷会直接影响轧制过程中的缺陷产生。
例如,材料中含有大量夹杂物或者过多的硬质相,会增加裂纹和凹坑的产生风险。
2. 设备因素:轧制设备的质量和性能直接影响轧制过程中的缺陷控制。
例如,辊道的磨损和不平整会导致凹坑的产生,辊道的间隙不合适会增加夹杂物的产生风险。
3. 工艺因素:轧制工艺参数的选择和控制对缺陷的产生和控制起着重要作用。
例如,轧制温度、轧制速度和轧制压力的选择需要根据材料的性质和要求进行合理调整。
四、轧制缺陷的控制措施1. 材料控制:选择合适的原材料,并进行必要的检测和筛选,以确保材料中的夹杂物和缺陷控制在合理范围内。
2. 设备维护:定期检查和维护轧制设备,确保辊道的平整度和间隙的合适性,减少凹坑和夹杂物的产生。
3. 工艺优化:根据不同材料的特性和产品的要求,优化轧制工艺参数,如温度、速度和压力等,以减少裂纹和凹坑的产生。
4. 检测技术:采用先进的无损检测技术,如超声波检测和磁粉探伤等,对轧制产品进行全面的检测,及时发现和排除缺陷。
5. 质量管理:建立完善的质量管理体系,包括质量检验、质量控制和质量反馈等环节,确保轧制产品的质量稳定和持续改进。
五、轧制缺陷的质量控制1. 检测方法:采用适当的检测方法对轧制产品进行质量控制,如外观检查、尺寸测量和物理性能测试等。
轧制缺陷及质量控制

轧制缺陷及质量控制一、引言轧制是金属加工中的一种重要工艺,用于将金属块材变形成所需的形状和尺寸。
然而,在轧制过程中,由于材料的特性和操作条件的不同,会产生一些缺陷,如裂纹、气泡、夹杂物等,这些缺陷会降低产品的质量和性能。
因此,进行轧制缺陷的控制和质量的监控是非常重要的。
二、轧制缺陷的分类1. 表面缺陷:包括划痕、麻点、皮膜剥离等。
2. 内部缺陷:包括裂纹、气泡、夹杂物等。
三、轧制缺陷的原因1. 材料因素:材料的化学成分、结构和纯度等会影响轧制过程中的缺陷形成。
2. 设备因素:轧机的结构、参数设置、润滑和冷却等条件会对轧制缺陷产生影响。
3. 操作因素:操作人员的技术水平、操作规程的执行等也会对轧制缺陷产生影响。
四、轧制缺陷的控制方法1. 材料选择:选择质量好、纯度高的原材料,减少缺陷的可能性。
2. 设备维护:定期对轧机进行维护和保养,确保设备的正常运行。
3. 工艺控制:控制轧制的温度、速度、压力等参数,减少缺陷的产生。
4. 检测方法:使用先进的无损检测技术,如超声波检测、磁粉检测等,及时发现和修复轧制缺陷。
5. 培训与管理:加强操作人员的培训,提高其技术水平和质量意识,严格执行操作规程。
五、质量控制体系建立完善的质量控制体系对于轧制过程中的缺陷控制至关重要。
以下是一个典型的质量控制体系的组成部分:1. 质量目标:明确轧制产品的质量要求,包括物理性能、化学成分等指标。
2. 质量计划:制定轧制过程中的质量控制计划,包括检测方法、检测频率等。
3. 质量检测:通过各种检测方法对轧制产品进行全面的检测,及时发现缺陷并采取措施修复。
4. 不良品处理:对于出现缺陷的产品,及时进行分类、记录和处理,以防止不良品流入市场。
5. 过程改进:根据质量检测结果和不良品处理情况,对轧制过程进行改进和优化,提高产品质量。
6. 内部审核:定期进行内部审核,评估质量控制体系的有效性和符合性。
7. 外部认证:通过第三方机构的认证,证明质量控制体系符合相关标准和要求。
常见带钢表面缺陷的原因和防止措施

名称
出现的形状
发生的原因
防止措施
散沙状铁皮
1)高温的轧件在粗糙的表面
1)加强轧辊冷却水,防止精
的轧辊上轧制,精轧机向形
轧机工作辊表面粗糙;
铁皮呈黑褐色,比较圆
成的二次氧化铁皮被压入而
2)换辊的管理;
细,成散沙状分布
成为散沙状铁皮;
3)控制轧制温度。
2)含碳量高,精轧温度高时
的圆周
1)不规则、不定形的
1)由于开卷时带钢过松而引
1)良好的带钢卷形;
刮伤
锐器刮伤;2)正反面
起;
2)开卷时给一定的张力;
同时发生;3)多数出
2)吊运的带钢卷在宽度方向
3)吊运要注意;
数带卷的内部
上发生滑动;
1)较浅细的擦伤,在
1)输送辊道的辊子回转不良
1)辊道辊子彻底检查;
轧制方向连续或断续出
引起的划伤;
卷取压痕
钢头部和卷筒扇形板贴
二圈以后就出现被压印而成
2)提前打开助卷辊;
压出的大块凹形压痕
了这种缺陷;
3)提高卷筒的正圆度的精度。
2)卷筒扇形板印压而成缺陷
1)轧制和精整线上的各种辊
1)彻底检查各种辊子;
钢板的正面或反面出现
子,附有杂物(凹烙印)
2)防止轧辊上带有异物;
辊印
有一定节距的凹、凸印
2)轧制和精整线上的各种辊
易发生。
1)加强轧辊冷却水;
铁皮在板面上呈不规则
精轧前段工作辊冷硬层薄膜
2)轧辊冷却水喷嘴的管理;
流星状铁皮
分布,其形状是顺着轧
剥落,呈流星状,当轧件的
3)限制轧制节奏;
轧制缺陷及质量控制

轧制缺陷及质量控制轧制是金属加工过程中常见的一种方法,但在轧制过程中可能会出现各种缺陷,影响产品质量。
因此,对轧制缺陷的控制是非常重要的。
本文将从轧制缺陷的定义、分类、原因、检测方法和质量控制措施等方面进行详细介绍。
一、轧制缺陷的定义1.1 轧制缺陷是指在金属轧制过程中出现的各种缺陷,如裂纹、气泡、夹杂物等。
1.2 这些缺陷可能会导致产品表面不平整、内部组织不均匀、性能下降等问题。
1.3 轧制缺陷的存在严重影响产品的质量和使用寿命。
二、轧制缺陷的分类2.1 表面缺陷:如划痕、皱纹、氧化皮等。
2.2 内部缺陷:如夹杂物、气泡、夹杂等。
2.3 尺寸缺陷:如厚度不均匀、偏差过大等。
三、轧制缺陷的原因3.1 材料原因:如原材料质量差、含杂质过多等。
3.2 工艺原因:如轧制温度、轧制速度、轧制压力等参数控制不当。
3.3 设备原因:如轧机设备老化、维护不及时等。
四、轧制缺陷的检测方法4.1 目视检测:通过肉眼观察产品表面和截面来检测缺陷。
4.2 磁粉探伤:利用磁粉粒在缺陷处产生磁粉堆积,通过观察磁粉分布来检测缺陷。
4.3 超声波探伤:利用超声波在材料内部传播的原理来检测内部缺陷。
五、轧制缺陷的质量控制措施5.1 加强原材料质量控制,确保原材料无夹杂物、氧化皮等缺陷。
5.2 优化轧制工艺参数,合理控制轧制温度、速度、压力等参数。
5.3 定期维护和保养轧机设备,确保设备运行稳定、精度高。
综上所述,轧制缺陷是金属加工过程中常见的问题,但通过严格的质量控制措施和有效的检测方法,可以有效减少轧制缺陷的发生,提高产品质量和生产效率。
希望本文的介绍能对相关行业的从业人员有所帮助。
轧制缺陷及质量控制
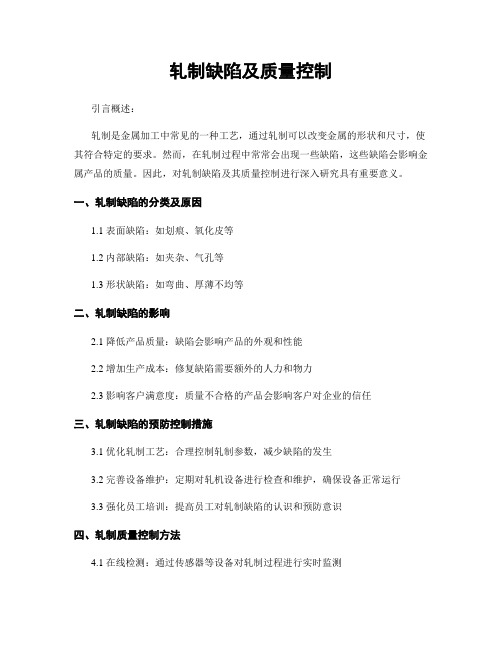
轧制缺陷及质量控制
引言概述:
轧制是金属加工中常见的一种工艺,通过轧制可以改变金属的形状和尺寸,使其符合特定的要求。
然而,在轧制过程中常常会出现一些缺陷,这些缺陷会影响金属产品的质量。
因此,对轧制缺陷及其质量控制进行深入研究具有重要意义。
一、轧制缺陷的分类及原因
1.1 表面缺陷:如划痕、氧化皮等
1.2 内部缺陷:如夹杂、气孔等
1.3 形状缺陷:如弯曲、厚薄不均等
二、轧制缺陷的影响
2.1 降低产品质量:缺陷会影响产品的外观和性能
2.2 增加生产成本:修复缺陷需要额外的人力和物力
2.3 影响客户满意度:质量不合格的产品会影响客户对企业的信任
三、轧制缺陷的预防控制措施
3.1 优化轧制工艺:合理控制轧制参数,减少缺陷的发生
3.2 完善设备维护:定期对轧机设备进行检查和维护,确保设备正常运行
3.3 强化员工培训:提高员工对轧制缺陷的认识和预防意识
四、轧制质量控制方法
4.1 在线检测:通过传感器等设备对轧制过程进行实时监测
4.2 人工检验:对轧制后的产品进行目视检查和尺寸测量
4.3 抽样检测:定期抽取产品进行全面检验,确保产品质量符合标准
五、轧制缺陷处理方法
5.1 修磨:对表面缺陷进行修磨处理,恢复产品表面光洁度
5.2 热处理:对内部缺陷进行热处理,消除缺陷并提高产品性能
5.3 重新轧制:对形状缺陷的产品进行重新轧制,确保产品尺寸和形状符合要求
总结:
轧制缺陷及质量控制是金属加工中一个重要的环节,只有通过科学的方法对轧制缺陷进行预防和控制,才能生产出高质量的金属产品,提高企业的竞争力和市场占有率。
希望本文的内容能够对相关行业的从业人员有所帮助。
轧制缺陷及质量控制

轧制缺陷及质量控制一、引言轧制是金属加工中常用的一种工艺,用于将金属块材或者板材通过辊道进行塑性变形,从而得到所需的形状和尺寸。
然而,由于材料的性质、设备的使用以及操作人员的技术水平等因素的影响,轧制过程中往往会浮现一些缺陷,如表面裂纹、厚度不均匀等,这些缺陷会直接影响产品的质量和性能。
因此,轧制缺陷的控制是保证产品质量的关键环节。
二、轧制缺陷分类及原因1. 表面缺陷表面缺陷是指在轧制过程中金属表面浮现的缺陷,如裂纹、气泡、氧化皮等。
这些缺陷通常由以下原因引起:- 材料的表面质量不良,存在夹杂物或者氧化皮;- 轧机辊道不平整或者磨损严重;- 轧制过程中润滑不良,导致金属与辊道之间磨擦增大。
2. 几何缺陷几何缺陷是指轧制过程中金属产品的形状和尺寸偏差,如厚度不均匀、边部不直等。
这些缺陷通常由以下原因引起:- 轧机辊道调整不当,导致金属材料厚度不均匀;- 轧机辊道磨损严重,失去了原有的几何形状;- 轧机操作人员技术水平不高,操作不当。
三、轧制缺陷的控制方法为了控制轧制过程中的缺陷,提高产品的质量和性能,可以采取以下措施:1. 材料预处理在轧制之前,对原材料进行预处理是非常重要的。
首先,对材料的表面进行清洁,去除氧化皮和夹杂物。
其次,对材料进行退火处理,以提高其塑性和可加工性。
最后,对材料进行表面润滑处理,减少与辊道的磨擦。
2. 轧机设备维护保持轧机设备的良好状态对于控制缺陷至关重要。
定期检查和维护轧机辊道,确保其平整度和几何形状的精确性。
同时,及时更换磨损严重的辊道,以保证轧制过程的稳定性和一致性。
3. 润滑控制在轧制过程中,适当的润滑是减少磨擦、防止表面缺陷的关键。
选择合适的润滑剂,并确保润滑剂的供应充足、均匀。
同时,及时清洗辊道和润滑系统,避免杂质对产品质量的影响。
4. 操作人员培训轧制过程需要经验丰富的操作人员进行操作和监控。
因此,对轧机操作人员进行培训,提高其技术水平和操作规范性是非常重要的。
- 1、下载文档前请自行甄别文档内容的完整性,平台不提供额外的编辑、内容补充、找答案等附加服务。
- 2、"仅部分预览"的文档,不可在线预览部分如存在完整性等问题,可反馈申请退款(可完整预览的文档不适用该条件!)。
- 3、如文档侵犯您的权益,请联系客服反馈,我们会尽快为您处理(人工客服工作时间:9:00-18:30)。
带钢轧制常见缺陷原因分析结疤(M01)图 7-1-1图 7-1-21. 缺陷特征附着在钢带表面,形状不规则翘起的金属薄片称结疤。
呈现叶状、羽状、条状、鱼鳞状、舌端状等。
结疤分为两种,一种是与钢的本体相连结,并折合到板面上不易脱落;另一种是与钢的本体没有连结,但粘合到板面上,易于脱落,脱落后形成较光滑的凹坑。
2. 产生原因及危害产生原因:①板坯表面原有的结疤、重皮等缺陷未清理干净,轧后残留在钢带表面上;②板坯表面留有火焰清理后的残渣,经轧制压入钢带表面。
危害:导致后序加工使用过程中出现金属剥离或产生孔洞。
3. 预防及消除方法加强板坯质量验收,发现板坯表面存在结疤和火焰清理后残渣应清理干净。
4. 检查判断用肉眼检查;不允许存在结疤缺陷,对局部结疤缺陷,允许修磨或切除带有结疤部分带钢的方法消除,如结疤已脱落,则比照压痕缺陷处理。
7.2 气泡(M02)图 7-2-1 闭合气泡图 7-2-2 开口气泡图7-2-3 开口气泡1. 缺陷特征钢带表面无规律分布的圆形或椭圆形凸包缺陷称气泡。
其外缘较光滑,气泡轧破后,钢带表面出现破裂或起皮。
某些气泡不凸起,经平整后,表面光亮,剪切断面呈分层状。
2. 产生原因及危害产生原因:①因脱氧不良、吹氩不当等导致板坯内部聚集过多气体;②板坯在炉时间长,皮下气泡暴露或聚集长大。
危害:可能导致后序加工使用过程中产生分层或焊接不良。
3. 预防及消除方法①加强板坯质量验收,不使用气泡缺陷暴露的板坯;②严格按规程加热板坯,避免板坯在炉时间过长。
4. 检查判断用肉眼检查;不允许存在气泡缺陷。
7.3 表面夹杂(M03)图 7-3-1图 7-3-21. 缺陷特征板坯中的夹杂或夹渣经轧制后在钢带表面暴露的块状或长条状的夹杂缺陷称表面夹杂。
其颜色一般呈棕红色、黄褐色、灰白色或灰黑色。
2. 产生原因及危害产生原因:板坯皮下夹杂轧后暴露或板坯原有的表面夹杂轧后残留在带钢表面。
危害:可能导致后序加工过程中产生孔洞、开裂、分层。
3. 预防及消除方法加强板坯检查验收,不使用表面存在严重夹杂或夹渣的板坯。
4. 检查判断用肉眼检查;钢带表面不允许存在夹杂缺陷。
对局部夹杂缺陷允许用修磨的方法清除,但不得超过标准规定的深度和范围。
7.4 分层(M04)图 7-4-11. 缺陷特征钢带断面出现连续或断续的线条状分离的现象称分层。
2. 产生原因及危害产生原因:①板坯内部聚集过多的非金属夹杂或夹渣;②板坯内部存在严重的中心裂纹或中心疏松,经多道次轧制未能焊合。
危害:导致后续加工使用过程中出现分层或焊接不良;在冷轧轧制时可能断带。
3. 预防及消除方法①加强炼钢冶炼、浇铸过程控制,提高钢质纯净度;②加强板坯质量验收,不使用存在严重中心裂纹或中心疏松的板坯。
4. 检查判断用肉眼检查;不允许存在分层缺陷。
7.5 中心线缺陷(M05)图 7-4-11. 缺陷特征在钢带横断面的中心部位出现明显的连续或断续的细线状缺陷称中心线缺陷。
线条较轻,断断续续,肉眼可见的中心线缺陷称中心偏析I级;明显的连续的线条状,但未完全分开的中心线缺陷称中心偏析II级;明显开口状的中心线缺陷称分层。
2. 产生原因及危害产生原因:连铸流道质量控制不良或铸坯冷却不良。
危害:可能导致顾客使用过程中出现分层,影响焊接质量。
3. 预防及消除方法加强连铸流道质量和铸坯冷却控制。
4. 检查及判断用肉眼检查;中心偏析I级允许存在;有中心偏析II级的产品不能用于汽车大梁等风险产品,但可用于其他产品。
7.7 辊印(M07)图 7-7-1 前机架轧辊网纹图 7-7-2 轧辊网纹1. 缺陷特征钢带表面呈周期分布、外观形状不规则的凸凹缺陷称辊印。
2. 产生原因及危害产生原因:辊子龟裂、局部掉肉,或表面粘有异物,使局部辊面呈凹、凸状,轧制或精整加工时,压入钢带表面形成凸凹缺陷。
危害:凸辊印可能导致后序轧制过程中产生折迭缺陷;凹辊印可能导致后序轧制过程中产生孔洞。
3. 预防及消除方法①定期检查轧辊表面质量,发现辊子掉肉或粘有异物时及时处理;②轧制过程中出现卡钢、甩尾、轧烂等异常情况时,及时检查辊子表面质量,防止辊面损伤或异物粘附;③检查发现轧辊网纹时,立即停机检查轧辊表面质量。
4. 检查判断用肉眼检查,根据辊印周期确定责任工序;允许存在轻微辊印,但其深度或高度不得超过标准规定的范围。
7.8 轧烂(M08)图 7-8-1图 7-8-21. 缺陷特征带钢表面出现多层重叠或轧穿、撕裂等现象称轧烂。
2. 产生原因及危害产生原因:①辊缝调整不当或辊型与来料板型配合不良,带钢延伸不均;②板坯局部加热温度不均或轧件温度不均;③精轧侧导板开口度设定不合理;④精轧过程中秒流量不匹配。
危害:轧制过程中断带,存在轧烂缺陷的钢板无法使用。
3. 预防及消除方法①合理配置轧辊辊型,注意辊缝调整;②加强板坯加热温度控制,保证轧件温度均匀;③合理设定精轧侧导板开口度;④保持连轧过程中秒流量一致。
4. 检查判断用肉眼检查;不允许存在轧烂缺陷。
7.9 压痕(压印、压坑)(M09)1. 缺陷特征钢带表面无周期性分布的凹凸印迹称压痕。
2. 产生原因及危害产生原因:①异物压入,脱落后形成压坑;②卸卷小车托辊表面粘肉;③卷筒、卸卷小车部件松动;④吊运钢卷过程中机械损伤;⑤切边或剪板过程中带钢跑偏,飞边压入钢带。
危害:在后续加工使用过程中可能产生孔洞或断带。
3. 预防及消除方法①防止异物压入;②加强卸卷小车托辊表面质量检查和修磨,定期更换托辊;③加强卷筒、卸卷小车点检,防止部件松动;④精心搬运钢卷,防止机械损伤;⑤防止带钢跑偏。
4. 检查判断用肉眼检查;允许存在轻微压痕缺陷,但不得超过标准规定深度和范围。
7.10 塔形(M10)图 7-10-1 图 7-10-2 1. 缺陷特征钢卷上下端不齐,外观呈塔状称塔形。
2. 产生原因及危害产生原因:①助卷辊间隙调整不当;②夹送辊辊缝呈楔形;③带钢进卷取机时对中不良;④卷取张力设定不合理;⑤卷筒传动端磨损严重,回转时有较大的离心差;⑥带钢有较大的镰刀弯、楔形或板形不良。
危害:塔形严重的钢卷无法开卷使用。
3. 预防及消除方法①加强助卷辊间隙调整;②保持夹送辊辊缝水平;③合理设定卷取机前侧导板,保持带钢对中;④合理设定卷取张力;⑤定期更换卷筒,防止卷筒严重磨损;⑥加强带钢板形控制。
4. 检查判断用肉眼检查,用适当的工具测量塔形高度;允许存在轻微塔形,但塔形高度不得超过标准规定的范围。
7.12 扁卷(M12)1. 缺陷特征钢卷呈椭圆形的现象称扁卷。
2. 产生原因及危害产生原因:①钢卷在搬运过程中,承受过大的冲击;②钢卷卷取张力偏低,卧卷堆放或多层堆放钢卷。
危害:影响钢卷包装和搬运,严重的扁卷无法开卷使用。
3. 预防及消除方法①精心搬运钢卷;②合理设定卷取张力,控制卧卷堆放的层数,必要时采用立卷堆放。
4. 检查判断用肉眼检查,用卷尺测量钢卷内、外径;允许存在轻微扁卷,但钢卷最小内径和最大外径不得超过标准规定的范围。
7.13 瓢曲(M13)图 7-13-1图 7-13-21. 缺陷特征钢板的纵横部分同时在同一个方向出现翘起的现象称瓢曲。
2. 产生原因及危害产生原因:①带钢轧制过程变形不均;②轧制计划编排不合理,在一个轧辊周期内集中轧制窄规格带钢后又集中轧宽规格带钢;③层流冷却不均;④精整生产时,矫直机压下设定不良或压力辊、矫直辊磨损严重;⑤钢板堆放不当。
危害:影响钢板外观形象,严重时可能导致后工序无法加工使用。
3. 预防及消除方法①合理配置辊型,保持带钢变形均匀;②合理编排轧制计划;③控制好层流冷却;④加强矫直机压下设定,定期更换压力辊、矫直辊;⑤钢板堆放应平直。
4. 检查判断用肉眼检查,用适当工具测量钢带不平度;允许存在轻微瓢曲,但其不平度不得超过标准规定的范围。
7.14 波浪(中浪、双边、单边浪)(M14)图 7-14-11. 缺陷特征沿钢带轧制方向呈现高低起伏的波浪形弯曲现象称浪形。
根据分布的部位不同,分为中间浪,肋浪和边浪。
2. 产生原因及危害①辊型不合理,轧辊磨损不均;②轧辊的辊型与来料板形配合不良,精轧后机架压下量过大;③钢带跑偏或辊缝调整不当;④轧辊冷却不均;⑤钢带温度不均。
危害:影响钢板外观质量,严重时后工序无法加工使用。
3. 预防及消除方法①合理配置辊型,合理更换轧辊;②合理编排轧制计划,保证不同规格带钢合理过渡,合理分配各机架的压下量;③加强辊缝楔形差值的检查,轧制过程中保持轧件对中良好;④加强轧辊冷却控制;⑤加强板坯加热和轧制过程中冷却控制,保证钢带温度均匀。
4. 检查判断用肉眼检查,用适当工具测量钢带不平度;钢带允许存在轻微浪形,但不平度不得超过相关标准的规定。
7.15 镰刀弯(M15)L 带钢长度 W 带钢宽度 A 镰刀弯值图 7-14-11. 缺陷特征沿钢带长度方向的水平面上向一侧弯曲的现象称镰刀弯。
2. 产生原因及危害产生原因:①轧辊磨损不均,辊缝呈楔形;②轧件两侧温度不均,轧制过程中延伸不一致;③立辊或侧导板的中心线有偏差;④轧辊发生轴向串动或两侧轴承磨损不均;⑤侧导板开口度过大,钢带对中不良。
危害:影响钢带外观形象,严重时可能导致后工序无法加工使用。
3. 预防及消除方法①加强辊缝检查,保持两侧辊缝水平一致;②加强板坯加热和钢带冷却控制,保证钢带两侧温度均匀;③检查立辊或侧导板中心线;④检查轧辊两侧轴承磨损情况;⑤检查侧导板开口度,确保钢带对中。
4. 检查判断用肉眼检查,用适当工具测量钢带的镰刀弯值;允许存在轻微镰刀弯。
7.16 横折(M16)图 7-17-11. 缺陷特征开卷后带钢表面出现的横向条状折痕称横折。
严重时有手感。
2. 产生原因及危害产生原因:①带钢板形不良;②轧制温度控制不合理,带钢在两相区变形,产生混晶;③低碳钢容易产生横折。
危害:影响钢带外观形象,不能作外观件使用。
3. 预防及消除方法①加强带钢板形控制;②合理控制带钢终轧温度;③通过平整可减轻或消除横折。
4. 检查及判断用肉眼检查;允许存在轻微横折缺陷,根据顾客使用要求,按横折级别判定。
7.17 折迭(M17)图 7-17-1图 7-17-21. 缺陷特征钢带表面局部区域金属折合的现象称折迭。
2. 产生原因及危害产生原因:①板坯缺陷清理深宽比过大;②辊型配置不合理或轧制负荷分配不合理等,导致带钢产生大波浪后被压合;③卷取速度设定不合理,带钢在卷取中出现堆钢、起套。
危害:可能导致冷轧断带,存在折迭的钢板无法使用。
3. 预防及消除方法①加强板坯缺陷清理,避免清理深宽比过大;②合理配置辊型和分配轧制负荷,避免带钢出现大波浪;③合理设定卷取速度,防止卷取过程中堆钢、起套。
4. 检查判断用肉眼检查;不允许存在折迭缺陷。
折边(M18)图 7-18-11. 缺陷特征钢带卷取后边部凸出部分被压折的现象称折边。