固态成形原理讲义-板料解读
固态成形原理讲义拉拔62页PPT
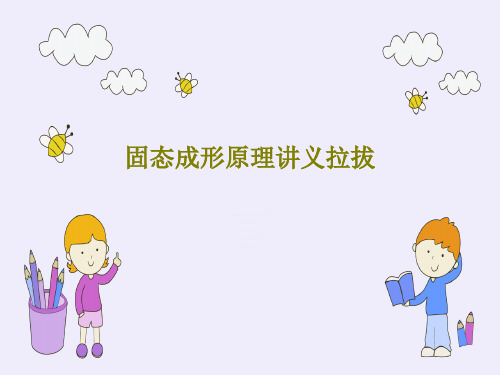
55、 为 中 华 之 崛起而 读书。 ——周 恩来
固态成形原理讲义拉拔
36、如果我们国家的法律中只有某种 神灵, 而不是 殚精竭 虑将神 灵揉进 宪法, 总体上 来说, 法律就 会更好 。—— 马克·吐 温 37、纲纪废弃之日,便是暴政兴起之 时。— —威·皮 物特
38、若是没有公众舆论的支持,法律 是丝毫 没有力 量的。 ——菲 力普斯 39、一个判例造出另一个判例,它们 迅速累 聚,进 而变成 法律。 ——朱 尼厄斯
40、人类法律,事物有规律,这是不 容忽视 的。— —爱献 生
ቤተ መጻሕፍቲ ባይዱ
谢谢!
51、 天 下 之 事 常成 于困约 ,而败 于奢靡 。——陆 游 52、 生 命 不 等 于是呼 吸,生 命是活 动。——卢 梭
北京科技大学固态成型工艺原理与控制 -

第一章轧制原理1. 轧制:靠旋转的轧辊与轧件之间形成的摩擦力将轧件拖进辊缝之间,并使之受到压缩产生塑性变形的过程。
轧辊表面状态的影响4)轧件的化学成份的影响5)轧辊化学成分的影响2.轧制变形区:指轧制时,轧件在轧辊作用下发生变形的体积。
实际的轧制变形区分为弹性变形区、塑形变形区、弹性恢复区。
3. 咬入角:轧件被咬入轧辊时轧件和轧辊最先接触点(实际上为一条线)和轧辊中心的连线与两轧辊中心连线所构成的角度。
4. 金属变形区的流动规律:(1)沿轧件断面高度上的变形、应力、流动速度分布都是不均匀;(2)在几何变形区内,轧件与轧辊接触表面上,不但有相对滑动,而且还有粘着;(3)变形不但发生在几何变形区内,而且也产生在几何变形区以外;(4)在粘着区内有一个临界面,在这个面上金属的流动速度分布均匀,并且等于该处轧辊的水平速度。
α≤5.平辊轧制咬入条件:β6.假设由咬入阶段过渡到稳定轧制阶段的摩擦系数不变及其他条件相同时,则稳定轧制阶段允许的咬入角比咬入阶段的咬入角大2倍。
7. 极限咬入条件 :βα= 理论上允许的极限稳定轧制条件 :y x y K βα=8. 剩余摩擦力:咬入力和水平阻力的差值称之为剩余摩擦力。
9. 剩余摩擦角ω:等于金属与轧辊间的接触摩擦角β与合力作用角ϕ的差值。
ϕ<α时,产生剩余摩擦力。
当ϕ=2α时,轧制过程建成,剩余摩擦角达到最大值。
10. 改善咬入条件的方法: 增加轧辊直径D 、减小压下量、用钢锭的小头先送入轧辊或以带有楔形端的钢坯进行轧制、增加后推力、改变轧件或轧辊的表面状态,以提高摩擦角、合理的调节轧制速度,轧制速度提高,摩擦系数降低、增加轧件与轧辊的接触面积或采用合适的孔型侧壁倾角。
11. 宽展:轧制过程中轧件的高度承受轧辊压缩作用,压缩下来的体积,将移向纵向及横向。
由移向横向的体积所引起的轧件宽度的变 化。
12. 宽展分类:自由宽展(坯料在轧制过程中,被压下的金属体积其金属质点横向移动时具有向垂直于轧制方向的两侧自由移动的可能性,此时金属流动除受辊接触摩擦的影响外,不受其他任何的阻碍和限制)、限制宽展(轧制过程中,金属质点横向移动时,除受接触摩擦的影响外,还承受孔型侧壁的限制作用)、强制宽展(轧制过程中,金属质点横向移动时,不仅不受任何阻碍,反而受强烈的推动作用,使轧件宽度产生附加的增长)13. 影响宽展的因素(在其他条件一定的情况下,正比于高向移动体积和变形区长度,以及摩擦系数。
固态成形原理讲义-锻造(2011.4)

(6) 变形不均
变形不均时,在各区 金属间产生附加应力。 附加应力必定是成对 出现,在趋向伸长较 多的区域受附加压应 力,在趋向伸长较少 的区域受附加拉应力。
图1-16 用凸肚形轧辊轧制时 坯料的变形和附加应力简图
变形不均匀引起的不良后果: 1) 可能引起物体应力状态的改变;2) 可能导致物体的 破坏;3) 造成物体的歪扭;4) 形成残余应力;5) 可能 残留铸态组织或粗大晶粒; 6) 使坯料轴心偏析区外 移;7) 引起剪切变形和局 部粗晶。
套环内镦粗:
图2-50 套环内镦粗
2.2 拔长成形原理 使坯料横截面减小而长度增加的成形工序。 特点:拔长是增长类成形工序,但就每次压缩时 变形区的应变情况看,属于压缩类应变。它是连 续地局部加载,是通过轴向正应变ε1的累积而达 到最终增长的目的。
2.2.1 矩形截面坯料的拔长 特点:
(1)外端金属对变形区金属流动的影响 相对送进量(进料比): l/a较小时:金属多沿轴向流动,轴向的变形程度 ε l 较大,横向的变形程度ε a 较小;随着l/a的不断 增大:εl逐渐减小,εa逐渐增大。
2 锻造工步的成形原理
2.1 镦粗成形原理 2.1.1 平砧镦粗 坯料在上下平砧间或镦粗平板间进行的镦粗 称为平砧镦粗。 (1)圆形截面坯料镦粗特点
区域I 区域I:由于摩擦影响最大,该区变形十分困难, 称为“难变形区”。 区域II 区域II:该区受摩擦的影响较小,应力状态有利 II 于变形,因此该区变形程度最大,称为“大变形 区”。 区域III III:其变形程度介于区域I与区域II之间, 区域III 称为“小变形区”。
规律:沿加载方向的正应力随受力面积不断扩大, 其绝对值逐渐减小。 以冲孔为例:
1.3 影响锻压工序内力情况的因素
固态成形原理-轧制理论(新)
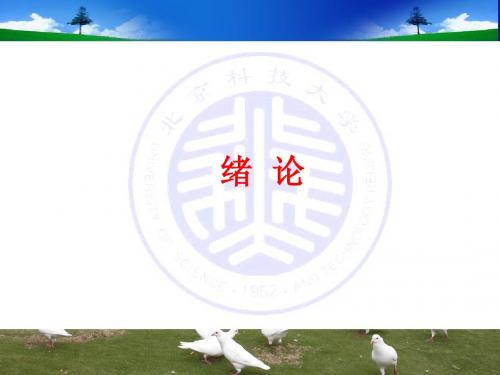
1.2.1平辊轧制的咬入条件
Nx>Tx
>
Nx=Tx =
Nx<Tx <
1.2.2 型钢轧制的咬入条件 箱形孔型中轧制时轧件的咬入条件
三辊工作机 座孔型
特点:
1)轧辊对轧件的作用力
2)咬入时力的平衡方程式和咬入条件(板书)
T1孔型侧壁作用在轧件前端侧面上的摩擦力; P1孔型侧壁作用在轧件前端侧面上的正压力; 0合力作用点与上、下轧辊轴心连线的夹角; 孔型侧壁与垂直线的夹角称孔型侧壁斜角; P2孔型槽底作用在轧件前端上的正压力; T2孔型槽底作用在轧件前端的摩擦力; F轧件的惯性力。
Vb Ab Vh Ah
Vb 、 Ab 向宽度方向移动的体积与其所消耗功; Vh 、 Ah高度方向移动体积与其所消耗的功。
h h b 1.15 ( Rh ) 2H 2
考虑因素:摩擦、相对压下量、变形区长度、轧辊形 状、轧件宽度、前滑。
(6)S.艾克隆德公式 依据:宽展决定于压下量及轧件与轧辊接触面上纵横 阻力的大小 。 假定:接触面范围内,横向及纵向的单位面积上的单 位功是相同的,在延伸方向上,滑动区为接触弧长的 2/3及粘着区为接触弧长的 1/3。 b 2 2 b 8m Rhh B 2 2m( H h) Rh ln B
1.3.2.2 宽展分类 (1)自由宽展 : 特点:
(2)限制宽展 特点:
图1-11 限制宽展 (a. 箱形孔内的宽展; b.闭口孔内的宽展)
(3)强制宽展 特点:
1.3.2.3 宽展的组成
组成:滑动宽展B1、翻平宽展B2和鼓形宽展 B3 。
(1)宽展沿轧件横断面高度上的分布 滑动宽展B1、翻平宽展B2和鼓形宽展B3的数 值,依赖于摩擦系数和变形区的几何参数的变 化。摩擦系数值越大,不均匀变形就越严重,翻 平宽展和鼓形宽展的值就越大,滑动宽展越小。
第三章 固态材料塑性成形 材料成型技术基础

检验 锻件
1)绘制锻件图
锻件图是以零件图为基础结合自由锻过程 特征绘制的技术资料。 锻件图是组织生产过程、制定操作规范、 控制和检查产品品质的依据。
锻件图绘制时要考虑的因素:
(1) 敷料 敷料是为了简化锻件形状、便于锻造而增 添的金属部分。自由锻适宜于锻制形状简单的锻件,对零 件上一些较小的凹挡、台阶、凸肩、小孔、斜面和锥面等 应进行适当的简化,以减少锻造的困难,提高生产率。 (2) 加工余量 自由锻件的精度低、表面品质较差,需 再经切削加工才能成为零件,应留足加工余量。锻件加工 余量的大小与零件的形状、尺寸、加工精度和表面粗糙度 等因素有关,通常自由锻件的加工余量为4~6mm。 (3) 锻件公差 锻件名义尺寸的允许变动量。自由锻 件的公差一般为±1~±2mm 。
塑性成形应避免在脆性区 (蓝脆区与热脆区)加热
2)变形速度
变形速度↑,使金属晶体的临界剪应力升 高,断裂强度过早达到,塑性降低;再结晶来 不及克服加工硬化,可锻性↓; 变形速度↑,变形产生的热效应提高温度, 可锻性↑。
3)应力状态 塑性变形时,三各方向的压应力的数目越多, 则金属表现的塑性越好;拉应力的数目越多, 则塑性越差。且同号应力状态下引起的变形抗 力大于异号应力状态下的变形抗力。
举 例
双联齿轮,批量为10件/月,材料为45钢。
该双联齿轮属小批量生产,采用自由锻。
φ25mm的孔,放加工余量后小于φ20mm,无法锻 出。不采用锻孔,该孔由机械加工成形。
退刀槽用敷料。
半径上工余量放3.5mm,高度上工余量放3mm。
锻件公差取±1mm。
2)坯料尺寸计算
坯料质量可按下式计算: G坯料=G锻件+G烧损+G料头 式中 G烧损——加热时坯料表面氧化烧损 的质量(通常第一次加热取被加热金属的2%~ 3%,以后各次加热取1.5%~2%) G料头——锻造中被切掉或冲掉的那 部分金属质量
固态成形课件3

相对普通铸铁件 “ 锻件如锅饼,铸件似面包” 锻造流线更增强工件强度。
金属铸锭经塑性变形后,铸造组织 的内部缺陷如气孔、缩孔、微裂纹等得 到焊合,再结晶后可细化晶粒,金属的 各种力学性能得到提高。 冲压件又具有重量轻、精度高、刚 性好等优点。 2.节约金属 指轧制、冲压、模锻等; (自由锻无此优点)。 3.生产率高(自由锻除外) 4.适应性广 质量、尺寸大小约束少; 对重载荷、强而韧的工件是基本选择。 5.不宜内腔形状复杂的零件 但由于锻压件是在固态成形,金属的流动受到限制。因此, 对于形状复杂、尤其是内腔形状复杂的零件,从制造工艺上锻 件远不及铸件容易实现。
锻造比对锻件的锻透程度和力学性能有很大 影响。 当锻造比达到2时,随着金属内部组织的致密 化,锻件纵向和横向的力学性能均有显著提高; 当锻造比为2-5时,由于流线化的加强,力学 性能出现各向异性,纵向性能虽仍略提高,但横 向性能开始下降; 锻造比超过5后,因金属组织的致密度和晶粒 细化度均已达到最大值,纵向性能不再提高,横 向性能却急剧下降。 因此,选择适当的锻造比相当重要。一般, 碳素结构钢取2-3,合金结构钢取3-4。对于某些 高合金工具钢和特殊性能的合金钢,为促进合金 碳化物分布的均匀化,击碎钢中的碳化物,常采 用较大的锻造比,如高速钢取5-12,不绣钢取46。 锻造比越大,锻造流线越明显;锻造流线的 稳定性很高,不能用热处理方法消除,只有经过 碳素钢钢锭拔长锻比对力学 锻压使金属变形,才能改变其方向和形状。 性能的影响
3.温锻 在高于室温和低于再结晶温度范围内进行的锻造工艺称为温锻。
与热锻相比,坯料氧化脱碳少,有利于提高工件的精度和表面质量;与 冷锻相比,变形抗力减小、塑性增加,一般不需要预先退火、表面处理
和工序间退火。温锻适用于变形抗力大、冷变形强化敏感的高碳钢、中
固态成形课件

5、计算中间工序次数及尺寸 每一次变形受材料抗拉极限限制时,需 分步完成总变形。 拉深系数 m=d/D(d:本次,D:前次)
6、确定模具类型与结构 7、选择冲压设备 根据冲裁力、拉深力确定
余块
自由锻锻件图
金属材料
始锻温度/℃
终锻温度/℃
碳素结构钢
碳素工具钢 合金结构钢 合金工具钢 高速工具钢 弹 簧 钢 轴 承 钢
2、塑性变形对金属组织的影响 A、冷变形强化 由于畸变严重,硬度、强度加大,塑 性明显下降,使得塑变抗力加大,进一步 变形困难
B、残余应力 晶格扭曲、变形不一致引起。
3、冷变形后加热时的组织与性能 A、回复: 加热温度较低,T回=(0.25-0.3)T熔, 原子扩散能力弱,显微组织无本质变化。位 错微量改善,残余应力部分消失,硬化基本 保留。 B、再结晶: 加热温度 T再=(0.4)T熔,原子扩散 能力增强,破碎晶粒重新形核并长大,形成 新的晶粒,消除了原先的畸变,使得机械性 能各指标恢复,内应力、硬化消除。
空心件。 基本过程 受力状态 破坏现象 C、弯曲 板料受压弯曲成所需(模具)形状。 受力状态 回弹 D、翻边、胀形、收口、压筋
2、冲压设备:剪床 冲床 3、常用方法 A、简单:一个冲程完成一个工序。 B、连续:一个冲程在模具不同位置完成 多个工序。 C、复合:一个冲程在模具同一位置上下 完成多个工序。
5、常用金属材料的锻造性能 塑性变形的难易程度,取决于材料性能 与变形条件。通过金属的塑性和变形抗力来 衡量 A、影响因素 材料组织本身(化学组织、元素数量、晶格结
构、晶粒粗细)
变形条件(温度范围、变形速度、变 形形式等) B、常用材料锻造性 碳钢-合金钢 铸铁
二、锻造形式
1、自由锻 使在上下砧铁(平面)中的金属受压力 或冲力后(局部)变形。 尺寸精度低、形状简单、效率低,尺寸 大小范围宽。 设备常用空气锤、蒸汽-空气锤 常用工序:拔长、镦粗、冲孔
湖大材料工程基础课件第三章材料固态成形工艺
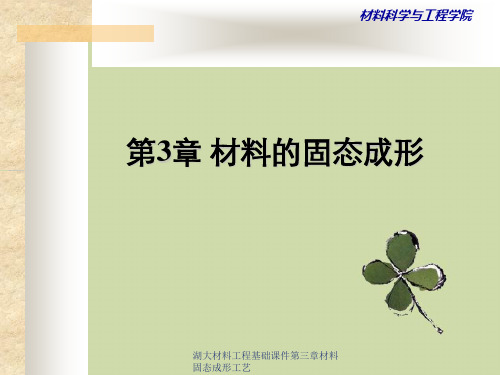
4、实现高速化、连续化、可控化加工。 5、研究与开发使环境净化,低噪音、小无震动、节省能
源、资源或再利用的加工技术。
湖大材料工程基础课件第三章材料
2021/3/29
固态成形工艺
9
材料科学与工程学院
§1.2 金属的塑性加工成形性
金属的可锻性是表示金属在热状态下经受 压力加工时塑性变形的难易程度。
可锻性的优劣一般常用金属的塑性和变形 抗力两个指标来综合衡量。
湖大材料工程基础课件第三章材料
2021/3/29
固态成形工艺
11
材料科学与工程学院
影响可锻性的因素
(1)金属的成分:纯金属好于合金,低碳钢优于高 碳钢,低碳低合金钢优于高碳高合金钢;有害 杂质元素一般使可锻性变坏
金(高铬不锈钢);Ⅵ—加热时形成
低熔点第2相的合金(含硫的铁、含
锌的镁合金);Ⅶ—冷却时形成有
塑性第2相的合金(碳钢和低合金钢
、 - 钛合金和 钛合金);Ⅷ—
冷却时形成脆性第2相的合金(高温
合金、沉淀硬化不锈钢);Tm —熔
湖大材料工程化基温础课度件。第三章材料固 Nhomakorabea成形工艺
13
材料科学与工程学院
2)变形速度:一方面随着变形速度的增加,回复 与再结晶过程来不及进行,不能及时消除加工 硬化现象,故使塑性降低,变形抗力增大,可 锻性变坏。另一方面随着变形速度的增高,产 生热效应,使 金属的塑性升 高,变形抗力 降低,又有利 于改善可锻性。
论,轧制、挤压、拉拔、锻造及板材成形等加工
方法。
湖大材料工程基础课件第三章材料
2021/3/29
固态成形原理讲义-挤压

l
r
l 图4-3 挤压时的外力、应力和变形状态图 r 1-挤压筒;2-挤压垫片;3-填充挤压前垫片的原始位置; 4模子;P-挤压力;-填充挤压阶段;-平流阶段;-紊流阶段
轴对称问题,r =;r =。 I区:对着模孔的区域,应力分布为l<r= ; II区: I区周围的区域,应力分布为l>r=。
s
dD 0 tg
(4-10)
将近似条件
n b 代入式 s (4-10)并积分得
x 2 s (1
1 3 ctg ) Ln D C
(4-11)
将D=Da, x =xb=代入(4-11)并与(4-11)相减得
x s (1
1 3 ctg ) Ln ( L D 2 ) 2 s 锭 Da Da L Db 2 ) 2 s 锭 Da Da
a
b
第二类型
图4-15 金属在挤压开始与末期两种类型的流动示意图 a-易挤压的金属;b-难挤压的金属
(2)摩擦及润滑的影响 摩擦力T和挤压力P之间关系
P Rs T
Rs Rs P Rs T
Rs不考虑外摩擦时挤压变形所需的力,牛顿; T挤压时的总摩擦力,牛顿; 在其它条件不变的情况下,Rs越大或T越小,则金属 流动越均匀。 润滑作用: (1)减小摩擦,使金属的流动趋 于均匀;(2)防止某些粘性较大的金属粘结工具, 以提高产品的表面质量。
3)皮下缩尾 皮下缩尾出现在制品表皮内,存在一层使金属径向上不连 续的缺陷。 原因:挤压时,剧烈滑移区金属和死区金属之间发生断裂 或形成滞流区,死区金属参与流动而包覆在制品的外面, 形成分层或起皮。
图4-7-4 皮下缩尾形成过程 1-表面层;2-死区
图4-8 镶填物在正挤压过程中的变化 a-挤压前;b-无润滑;c-有润滑
固态成形原理-板料成形原理

(3)剪切断面分析
由于冲裁变形的特点,使冲出的工件断面明显地分成
三个特征区,即圆角带、光亮带与断裂带。
圆角带:
光亮带:
圆角带
光亮带
断裂带:
断裂带
断裂带
圆角带
光亮带
4)凸模与凹模之间的间隙
a)间隙对冲裁件质量的影响 对切断面的要求: 对零件表面的要求: 对尺寸精度的要求: 影响冲裁件质量的因素:
2)弹—塑性弯曲和线性纯塑
性弯曲
切向应力与切向应变的函数关
系为: f ( )
弹性变形范围内(见图1-12(d)
实际应变与工程应变关系:
1 ln1 e1 2 ln1 e2
3 ln 1 e3
体积不变条件:
1 2 3 0
(1)变形板料中一点,其应变或应力状态的几 何表示方法
采用主轴表示法,可将应变分量减少为3个
主条应件,变3分个量主应1 变、中2只、有3两。个由是塑独性立变的形。体一积般不规变
2.2 弯曲
视频
图1-10 弯曲变形过程 1-凸模;2-凹模
变形特点: a)圆角附近部分: 远离圆角的直边部分: 靠近圆角处的直边: (b)在变形区内: 纵向纤维bb: 纵向纤维aa: 应变中性层(图中oo层):
(c)弯曲变形区 变薄因数: (d)变形区的横断面情况: 1)宽板(板宽B与板 厚t之比大于3)弯曲时: 2)窄板(B<3t)弯曲时:
1 板材成形的基本变形方式
1.1 板材成形中的应力应变状态及其几何表示方法 工程应变,主应变为:
e1
l1
l0 l0
e2
b1 b0 b0
e3
t1
t0 t0
在塑性变形中,一般用对数应变(实际应变):
固态成形原理-挤压成形原理

沿横断面径向上,外层金属的主延伸变形比内层 的大;沿纵向上制品后端的主延伸变形比前端的 大。
挤压筒内的金属,存在两个难变形区。 前端难变形区:位于挤压筒与模子交界的环形死 区部位。 后端难变形区:位于塑性变形区压缩锥后面的锭 坯未变形部分。
图4-7 正挤压时的弹性变形区 a-平模挤压;b-锥形模挤压
(4)反向挤压时金属流动的特点: 特点: 优点: 缺点:
图4-13-1反挤压时作用于金属的力 1-挤压筒;2-空心挤压杆;3-模子;4-锭坯未挤压部分;5-塑性变形
区;6-挤压制品
图4-14挤压实验的坐标网格对比 1-反挤压;2-正挤压
(5) 横向挤压金属流动特点:先镦粗再横向挤压
图4-14-1 十字接头锻件图 图4-14-2 十字接头的横向挤压过程示意图
4.1 概述 挤压特点: 4.2 挤压的基本方法 正挤压:
图4-1 挤压的基本方法 1一挤压筒;2一模子;3一挤压杆;4一锭坯;5一制品
反挤压:
不动的
可动的
挤压杆为不可动的反向挤压过程
1 可动的
3 不动的
挤压杆可动的反向挤压过程
横向挤压棒材 1-挤压杆;2-挤压金属;
3-挤压模
4.3 挤压时金属的流动
3)皮下缩尾 皮下缩尾出现在制品表皮内,存在一层使金属径向上不连 续的缺陷。 原因:挤压时,剧烈滑移区金属和死区金属之间发生断裂 或形成滞流区,死区金属参与流动而包覆在制品的外面, 形成分层或起皮。
图4-7-4 皮下缩尾形成过程 1-表面层;2-死区
图4-8 镶填物在正挤压过程中的变化 a-挤压前;b-无润滑;c-有润滑
(4)挤压时金属变形流动分区 的假定 (看书)
(5) “死区”的应力应变分析
固态成形技术PPT课件

典型锻件的锻造比
计算 锻造比 部位
锻件 名称
碳素钢轴类 最大
零件
截面
合金钢轴类 最大
零件
截面
热轧辊
辊身
2.0~2.5 2.5~3.0 2.5~3.0
冷轧辊
辊身 3.5~5.0
锤头
水轮机主 轴 水轮机立 柱 模块
计算 部位
锻造比
最大截面 ≥2.5
轴身
≥2.5
最大截面 ≥3.0 最大截面 ≥3.0
齿轮轴
3.2 金属塑性成形过程的理论基础
⑶应力状态:
三个方向中的压应力数目越多,塑性越好,变形抗力 增大;拉应力数目多,则金属的塑性就差,变形抗力降低。
3.2.2 塑性变形基本规律
⑴体积不变规律
金属固态成形加工中金 属变形后的体积等于变形前 的体积(又叫质量恒定定理 )
⑵最小阻力定律
金属在塑性变形过程中 ,其质点都将沿着阻力最小 的方向移动。(最小周边法则 )
3.1 概述
金属塑性成形的主要方法
金属固态塑性成形优缺点
优点: ⑴组织细化致密、力学性能提高; ⑵体积不变的材料转移成形,材料利用率高; ⑶生产率高,易机械化、自动化等。 ⑷可获得精度较高的零件或毛坯,可实现少无切削加工。
缺点: ⑴不能加工脆性材料; ⑵难以加工形状特别复杂(特别是内腔)、体积特别大的制品; ⑶设备、模具投资费用大。
3.2 金属塑性成形过程的理论基础 塑性成形性能(可锻性)
衡量因素——塑性指标和变形抗力; 塑性越高,变形抗力越低,可锻性越好。
3.2 金属塑性成形过程的理论基础
影响金属塑性成形性能的因素:
内在因素、加工条件、应力状态等。
⑴内在因素: ①化学成分—钢的含碳量越大,塑性成形性越差;
固态成形原理讲义-挤压

图4-20-1 模孔排列对制品长度的影响 a-同心圆距模子中心15mm;b-同心圆距模子中心20mm
b)垫片的影响: C)挤压筒的影响:
挤压铝合金壁板的扁挤压筒 a-扁挤压筒;b-用扁挤压筒挤压示意图 1-模子;2-锭坯;3-挤压筒;4-挤压杆;5-壁板
4.4 挤压力的计算 4.4.1 影响挤压力的诸因素 (1)被挤压金属化学成份的 影响 碳含量: Si元素: S: P:
图4-23 定径受力情况
压应力σn值比σs要小,考虑到热挤压时的摩擦系数较大,故摩擦应力 近似取为 τk =0.5τσs 根据静力平衡条件:
π 2 σ xa × Da = τ kxπDa L定
4
(4-6)
在变形区(2区)的单元体上坯料所受的应力如图4-24示。 变形区(2区)与死区(4区)的分界面(即单元体的锥面)是在坯料内 部由于塑性流动不同而被切开的,所以作用在该分界面上的切应力可以认为 达到了极值。
图4-9-4 折迭的形成情 况
图4-9-5 凹模锥角对改 善金属流动的影响图
4.3.2.3其它挤压过程金属流动的特点 (1)用单孔模正向挤压非园实心型材的金属流动特 点:
图4-10-1 单孔挤压非圆形材
(2)多模孔正向挤压实心断面型材时金属流动的特点
A E B C A D E C B E C D A B C C A B A A B D E C B C D A B E B A A
σl在II区沿长度方向分布
σl τk
II
σr=σθ
II
a a
I
σl沿横断面的分布
σr在II区沿长度方向分布
4.3.2.2 棒材挤压时的金属流动
(1) 填充挤压阶段的变形特点
σl τk σr=σθ