某皮带轮注射成型模具及成型工艺设计【文献综述】
模具毕业设计文献综述参考模板

第九章注射模导向定位系统
9-1概念:注射模中保证活动零件按照既定的轨迹运动的结构,叫导向系统;保证前后模之间及各活动零件之间相对位置精度的结构叫定位系统。
见图.
9-2 必要性:
1、前后模要反复开合;
2、模具精度要求高;
3、生产过程中承受高压;
4、生产过程中承受高温;
5、模具寿命要求高。
9-3 分类:
1.导柱导套
2.锥面定位机构
3.侧向抽芯机构的导向定位机构。
9-4 作用:
1、导向;
2、定位;
3、承受侧向压力;
4、支承模具重量。
9-5 导柱导套
1、分类:边钉G.P.,水口边S.P.,
中托边E.G.P.。
2、导柱导套的设计:
1)形状。
2)材料及热处理:
3)公差与配合:
➢导柱的固定H7/k6,
➢导柱与导套的配合为H7/f7。
3.中托边(E.G.P.):
1)应用场合:
(1)有司筒;(2)唧嘴偏心;
(3)小于2mm的顶针较多;(4)顶针一边多一边少。
2) 大小和数量设计:
(1)对4040以下模架采用2支中托边,直径等于回针直径或比回针直径大5mm;
(2)对4040以上模架采用4支中托边,直径等于回针直径.
. 3) 位置:见下图 在导向定位系统
设计过程中需要自己考虑的设计有:边锁、管位、中托边。
(注:论文素材和资料部分来自网络,供参考。
请预览后才下载,期待你的好评与关注。
)。
注塑模具-文献综述格式模板

说明1.根据学校《毕业设计(论文)工作暂行规定》,学生必须撰写毕业设计(论文)文献综述。
文献综述作为毕业设计(论文)答辩委员会对学生答辩资格审查的依据材料之一。
2.文献综述应在指导教师指导下,由学生在毕业设计(论文)工作前期内完成,由指导教师签署意见并经所在专业教研室审查。
3.文献综述各项内容要实事求是,文字表达要明确、严谨,语言通顺,外来语要同时用原文和中文表达。
第一次出现缩写词,须注出全称。
4.学生撰写文献综述,阅读的主要参考文献应在10篇以上(土建类专业文献篇数可酌减),其中外文资料应占一定比例。
本学科的基础和专业课教材一般不应列为参考资料。
5.文献综述的撰写格式按毕业设计(论文)撰写规范的要求,字数在2000字左右。
文献综述应与开题报告同时提交。
毕业设计(论文)文献综述第2章主题部分(居中小二黑体)(段前1行,段后0.5行) (说明:主题是综述主要内容的叙述部分。
一般要叙述所选研究题目的国内外研究现状;本研究至目前的主要他人研究成果;比较各种学术观点,阐明本研究的发展趋势;目前存在的问题。
对当前工作的现状,今后的发展趋势应作重点、详尽而具体地叙述。
)(格式参照第1章)下面为表、图的排版要求:表2-1 HDPE的主要性能指标(五号宋体)(表内字小五号宋体)密度/(g/cm3) 0.941~0.965 屈服强度/MPa 22~30 体积质量/( cm3/ g) 1.03~1.06 拉伸强度/MPa 27吸水率24h/(%) <0.01 拉伸弹性模量/GPa 0.84~0.95玻璃化温度/℃-120~-125 抗弯强度/MPa 27~40熔点/℃105~137 弯曲弹性模量/GPa 1.1~1.4 计算收缩率/(%) 1.5~3.0 抗压强度/MPa 22比热容/(J/(kg·K) 2310 抗剪强度/MPa —注:表要求绘制,不允许剪贴图2-1 原始铝合金磨痕形貌(五号宋体)毕业设计(论文)文献综述。
滚轮注塑成型工艺及模具设计大学论文
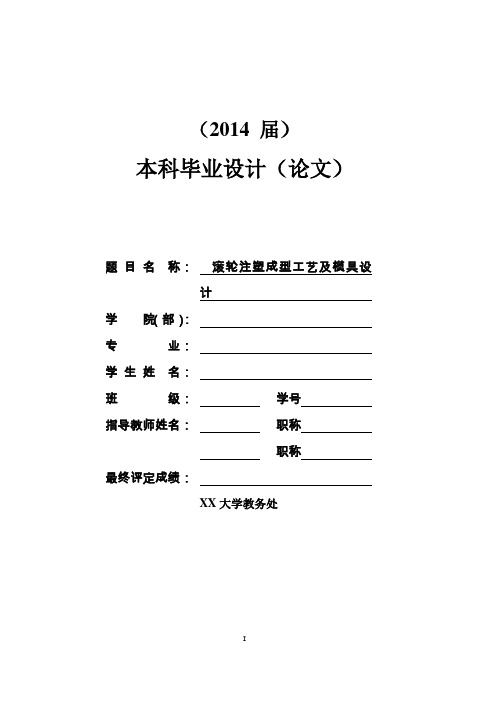
(2014 届)本科毕业设计(论文)摘要本设计是滚轮塑料零件的注塑模具设计,在结合了传统的机械设计后把CAD/CAM 技术应用在注塑模具的设计上,在CAD系统实行了模型和注塑模具的设计。
本文介绍了我国当前模具技术的发展状况以及CAD/CAM在模具上的应用,其中包括AUTOCAD。
主要的机械部分设计,其内容包括塑料注塑模具的工作原理及应用,设计准则。
塑料注塑模的设计计算,包括模具结构设计,注塑机的选用,浇注系统的设计,动、定模,浇注系统,脱模机构,顶出机构,冷却系统等设计等方面。
如此设计出的结构可确保模具工作运行可靠。
全套设计加 197216396或401339828关键词:CAD;CAM;注塑模;工艺ABSTRACTIt is to design the holder injection mould, references to the traditional mechanical design, focus on the CAD/CAM application in the plastic mould design, that is to say to apply the CAD system in model and plastic injection mould design. This artic introduces the mould technology and the CAD/CAM application of mould in china nowadays. Including AUTOCAD,MASTERCAM. While main mechanical designs content the principle and application of the plastic mould, design standards. The calculation of the plastic mould design concerns about the mould construction design, choosing Injection Molding Machine, injection system ,the move mould, immobility mould, the irrigating system, the doffing mould organ, the goring organ, the cooling system’s design and so on.The structure designed in such way can ensure the reliable running of the mould. Keywords: CAD;CAM;PLASTIC INJECTION;MOULD目录摘要 (II)ABSTRACT ......................................................................................................................... I II 目录 .................................................................................................................................. I V 第1章绪论 . (1)1.1模具的作用与地位 (1)1.2 本次设计研究目的及意义 (1)1.3 CAD发展概况 (1)1.4 注塑模CAD内容 (2)第2章塑件的工艺分析 (4)2.1塑件的工艺性分析 (4)2.1.1塑件的原材料分析 (4)2.1.2 聚甲醛的注塑工艺参数 (4)2.2塑件的结构和尺寸精度及表面质量分析 (6)2.2.1结构分析 (6)2.2.2尺寸精度分析 (6)2.2.3表面质量分析 (6)2.3计算塑件的体积和质量 (6)第3章注射机的选择及校核 (7)3.1 注射机的选择 (7)3.2 型腔数目的确定及校核 (8)3.3 锁模力的校核 (9)3.4 开模行程的校核 (9)第4章浇注系统的设计 (10)4.1 分型面的选择 (10)4.2 主流道的设计 (11)4.3 浇口设计 (11)4.3.1 剪切速率的校核 (12)4.3.2 主流道剪切速率校核 (12)4.3.3 浇口剪切速率的校核 (12)第5章成型零部件设计 (14)5.1 型腔和型芯工作尺寸计算 (14)5.2 型腔侧壁厚度计算 (15)第6章合模导向机构设计 (16)第7章温度调节系统设计 (17)7.1 对温度调节系统的要求 (17)7.2 冷却系统设计 (17)7.2.1 设计原则 (17)7.2.2 冷却时间的确定 (17)7.2.3 塑料熔体释放的热量 (18)7.2.4 高温喷嘴向模具的接触传热 (18)7.2.5 注射模通过自然冷却传导走的热量 (19)7.2.6 冷却系统的计算 (20)7.2.7 凹模冷却系统的计算 (20)第8章模具工作原理说明 (22)总结 (23)参考文献 (24)致谢 (25)第1章绪论1.1模具的作用与地位模具是指工业生产上通过注塑、压铸或锻压等方式生产产品所用的各种模型和工具,是工业生产中极其重要而又不可或缺的特殊基础工艺装备,被称为“工业之母”。
(模具专业)毕业设计文献综述参考word
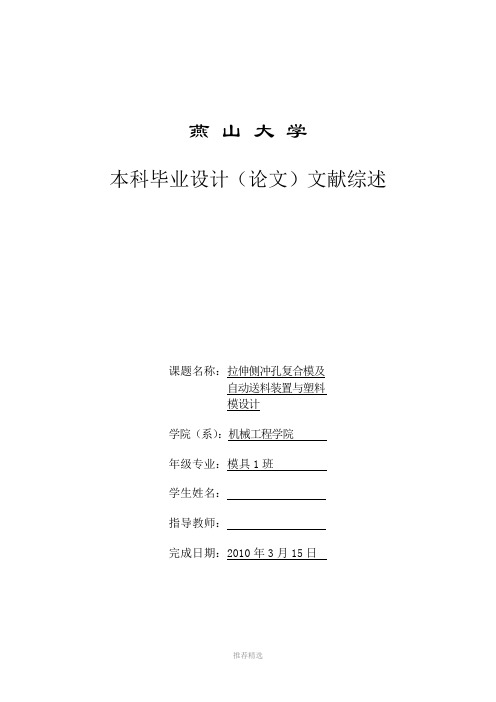
燕山大学本科毕业设计(论文)文献综述课题名称:拉伸侧冲孔复合模及自动送料装置与塑料模设计学院(系):机械工程学院年级专业:模具1班学生姓名:指导教师:完成日期:2010年3月15日一、课题国内外现状模具生产技术水平的高低,已成为衡量一个国家产品制造水平高低的重要标志[2]。
因为模具在很大程度上决定着产品的质量、效益和新产品的开发能力。
在电子、汽车、电机、电器、仪器、仪表、家电和通信等产品中60%—80%的零部件都要依靠模具成型。
用模具生产部件所具备的高精度、高复杂程度、高一致性、高生产率和代消耗,是其他加工制造方法所不能比拟的。
模具又是“效益扩大器”,用模具生产的最终产品的价值,往往是模具自身价值的几十倍、上百倍。
目前,全世界模具年产值约为600亿美元,日、美等工业发达国家的模具工业产值已超过机床工业。
我国的模具工业的发展,也日益受到人们的关注和重视。
近几年,我国模具工业一直以每年15%左右的增长速度发展。
二、研究主要成果现代模具设计的内容是:产品零件(常称为制件)成型工艺优化设计与力学计算,尺寸与尺寸精度确定与设计等,因此模具设计常分为制件工艺分析与设计、模具总体方案设计、总体结构设计、施工图设计四个阶段[7]。
(1)AD/CAE/CAM 计算机辅助设计、模拟与制造一体化CAD/CAE/CAM 一体化集成技术是现代模具制造中最先进、最合理的生产方式。
(2)设备在现代模具制造中的作用现代模具制造尽可能地用机械加工取代人工加工。
这就确定了先进设备在现代制造中的作用,尤其现在加工中心、数控高速成型铣床、数控铣床、数控车床、多轴联动机床、数控模具雕刻机、电火花加工机床、数控精密磨床、三坐标测量机、扫描仪等现代化设备在工厂中的广泛使用。
(3)代模具制造中的检测手段模具的零部件除了有高精度的几何要求外,其形位精度要求也较高,一般的量具是很难达到理想的目的,这时就要依赖精密零件测量系统。
这种精密零件测量系统简称C M M ,即Coordinate Measuring Machine ,是数控加工中心的一种变形。
皮带轮注塑模具的设计研究

产业与科技论坛 2012 年第 11 卷第 21 期
皮带轮注塑模具的设计研究
□何 禛
【内容摘要】本文首先确定了颗粒状的聚氯乙烯胶料为注模材料,选定了型号 XS - ZY - 250 的卧式注塑机。在模具的设计中, 设计了水平抽芯结构型腔以及浇注系统等,给出了设计的导柱导向机构合模结构以及脱模机构的分析等。从设计 分析可知确定的结构与方式都是相对合理的,这一研究显然对于注塑模具的进一步发展具有一定的意义。
【关键词】注塑模具; 浇注系统; 成型零件; 定距螺钉 【作者单位】何禛,台州技工学校
随着零件加工方法的增多与生产要求的提高,对批量生 产的产品不仅要 考 虑 生 产 效 率、材 料 利 用 率、产 品 质 量 稳 定 性,也要降低能 耗 与 成 本。 而 皮 带 轮 零 件,因 其 产 品 尺 寸 精 度要求较高,也大 多 属 大 批 量 生 产 产 品,需 要 综 合 考 虑 产 品 生产效率、质量稳 定 性 及 成 本 等 因 素,宜 选 用 注 塑 模 进 行 加 工生产。本文基于这一背景分析了皮带轮注塑模具,这一研 究对于注塑模具的进一步发展具有一定的意义。
皮带轮注射模设计

皮带轮注射模设计尹相昶【摘要】随着技工学校的一体化教学改革,对学生的培养及专业教师的专业水平有了更高的要求.而校企合作就是提高学生及专业教师技能水平的有效途径之一,本设计就是本校“校中厂”典型注射模实例之一,由专业教师带领预备技师班的学生一起设计,即达到了学生的培养目标,又提高了专业教师的专业水平.本设计详细介绍了皮带轮注射模设计的整个流程,包括塑件的分析、型腔数及位置布局方案设计、浇注系统设计、侧向抽芯机构的设计、脱模机构设计、排气系统的设计.【期刊名称】《模具制造》【年(卷),期】2017(017)012【总页数】7页(P38-43,49)【关键词】皮带轮;注射模;侧向抽芯;一模两腔【作者】尹相昶【作者单位】河源技师学院广东河源 517000【正文语种】中文【中图分类】TQ320.66一般塑件的脱模方向都与开闭模的方向相同。
但是随着塑料工业的快速发展,塑件的结构越来越复杂,有些塑件的侧面带有侧孔或侧凹,则脱模方向与开闭模方向不一致,塑件就不能由推杆等推出机构推出脱模,此时就必须设计一种机构能在塑件脱模推出之前,先将侧向分型的零件抽出,然后再把塑件从模具内推出。
而侧向分型抽芯机构就能满足这一要求,模具上成型侧孔或侧凹做成可侧向移动的活动型芯,在塑件脱模推出之前,先将活动型芯抽出,再利用推出机构进行脱模。
结构工艺性分析:①该塑件的外形为回转体,壁厚均匀,且符合壁厚要求;②从塑件图1可见该塑件的结构较为复杂,有侧凹部分,所以在模具设计时必须考虑侧向抽芯机构。
塑件的形状为圆柱形,轮廓尺寸为ϕ60×10mm,属于小型塑件。
此次设计的模具需要成型的塑料零件是皮带轮,材质是聚氯乙烯(PVC),PVC的热稳定性和耐热性较差,软化温度接近于分解温度,因此在加工时要加入各种稳定剂和增塑剂。
PVC在70℃~80℃时软化,150℃~170℃时呈熔融状态,190℃以上分解并放出有毒的氯化氢。
由于增塑剂加入量的不同,可制得硬质HPVC和软质SPVC。
注射成型技术的原理、工艺及应用
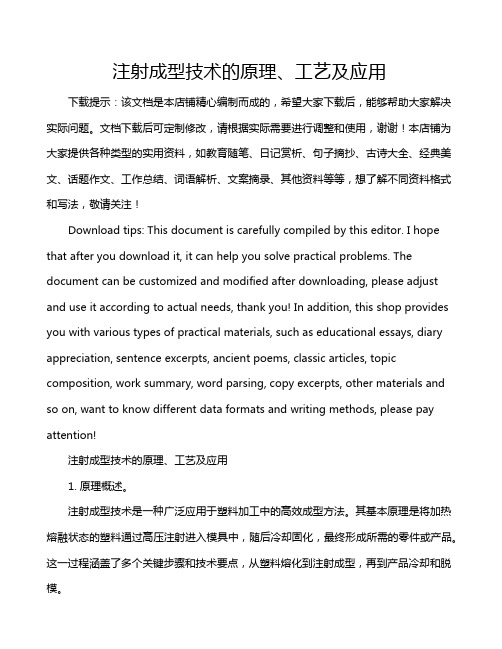
注射成型技术的原理、工艺及应用下载提示:该文档是本店铺精心编制而成的,希望大家下载后,能够帮助大家解决实际问题。
文档下载后可定制修改,请根据实际需要进行调整和使用,谢谢!本店铺为大家提供各种类型的实用资料,如教育随笔、日记赏析、句子摘抄、古诗大全、经典美文、话题作文、工作总结、词语解析、文案摘录、其他资料等等,想了解不同资料格式和写法,敬请关注!Download tips: This document is carefully compiled by this editor. I hope that after you download it, it can help you solve practical problems. The document can be customized and modified after downloading, please adjust and use it according to actual needs, thank you! In addition, this shop provides you with various types of practical materials, such as educational essays, diary appreciation, sentence excerpts, ancient poems, classic articles, topic composition, work summary, word parsing, copy excerpts, other materials and so on, want to know different data formats and writing methods, please pay attention!注射成型技术的原理、工艺及应用1. 原理概述。
HPVC皮带轮的注塑模设计与应用
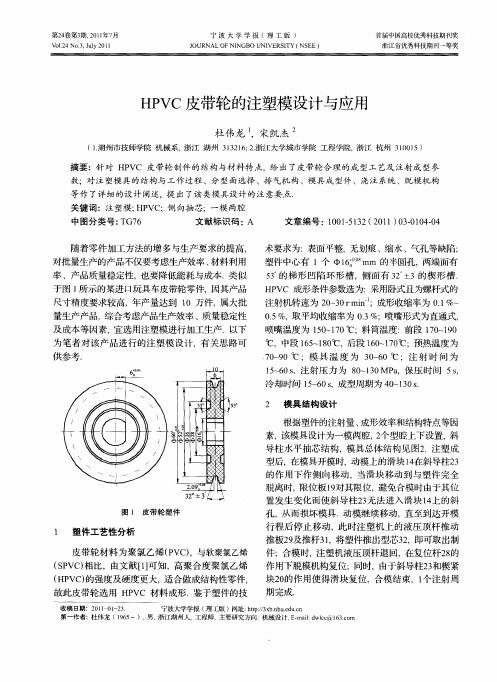
图 I 皮带轮塑件
1 塑 件 工艺 性分 析
行程 后停 止移动 , 此时注塑机上的液压顶杆推动 推板2及推杆 3, 9 将塑件推出型芯3 , 1 2 即可取出制 件; 合模 时, 注塑机液压顶杆退回, 在复位杆2 的 8 作用下脱模机构复位;同时, 由于斜导柱2 和楔紧 3 块2 的作用使得滑块复位, 0 合模结束,1 注射周 个 期完成.
1 705 +. / 13
o
广
H1 03l ̄0 =. ∞ m 1 .)o .l 9 , =1 0 × - 1 L 0 ( + 5 J 9 3
广 1 7 o11 + 03
衬套 中, 通常在淬火后嵌入模具, 这样在损坏时便
于更换或修磨 . 衬套与定模座板之问的配合采用 H / 6 主流 7 . m
皮带轮材料 为聚 氯乙烯(V ) P C ,与软聚氯乙烯 (P C 相 比,由文献 [ 可知, SV ) 1 ] 高聚合度聚氯乙烯 ( P C 的强度及硬度更大, HV ) 适合做成结构性零件,
故此皮带轮选用 H V 材料成形 . PC 鉴于塑件的技
收稿 日期:2 1 卜2 . 0 卜0 3 宁波大学学报 ( 理工版 )网址: t :3 b b uc ht / x . u d _ p/ n c n 第一 作者 : 伟 龙 ( 9 5 ),男, 江 湖州 人,工程 师 , 要研 究方 向 : 械设 计 Emald c@ 13cm 杜 16 一 浙 主 机 - i wl : c 6. o
道衬套嵌入定模座板之后 , 由定位圈压住其大 再 端面 ,也能 起 到抵抗 熔 体反 压 力的 作用 .
分 流 道 开 设在 定模 座 板 与 中 间板 之 问 ,并 在
H 1( o 3 6500 =. m 1+m ) - . 1 55 =1 × ×1 9 .
模具的文献综述

模具的文献综述1.1模具的简介近年来,由于我国国民经济的高速、稳定的增长,促进了我国模具工业的迅速发展壮大,因此,模具设计与制造专业或者相关的材料成型与控制专业已经成为我国国内具有优势的热门专业之一。
在日常生活中我们的许多制品都是由模具来生产制造出来的,所以,越来越多的人开始从事模具行业的设计,因此,我国的模具设计水平有了进一步的提高和发展的空间。
随着国民经济的高速发展,市场对模具的需求量不断增长,模具工业快速发展,必然会带来模具工业企业的所有制成分也发生了巨大变化,除了国有专业模具厂外,集体、合资、独资和私营也得到了快速发展。
随着与国际接轨的脚步不断加快,市场竞争的日益加剧,人们已经越来越认识到产品质量、成本和新产品的开发能力的重要性。
而模具制造是整个链条中最基础的要素之一,模具制造技术现在已经逐渐的成为衡量一个国家产品制造水平的重要标志和发展程度的标志之一。
模具是用来成型物品的工具,这种工具有各种零件构成。
不同的模具是通过所成型材料物理状态的改变来实现,模具是由不同的零件所构成的。
它主要是通过所成型材料的物理状态改变来实现物品外形的加工。
在冲裁、成形冲压、模锻、冷镦、挤压、粉末冶金件压制、压力铸造,以及工程塑料、橡胶、陶瓷等制品的压塑或注塑的成形加工中,用以在外力作用下使坯料成为有特定形状和尺寸的制件的工具。
对于冲裁、成形冲压、模锻、冷模具具有特定的轮廓或内腔形状,应用具有刃口的轮廓形状可以使坯料按轮廓线形状发生分离,即进行冲裁,用内腔形状可以使坯料获得相应的立体形状。
模具一般分为动模和定模两个部分,或着称为凸模和凹模两个部分,它们可分可合。
分开时装入坯料或取出制件,合拢时使制件与坯料分离或成形。
在冲裁、成形冲压、模锻、冷镦、压制和压塑过程中,分离或成形所需的外力通过模具施加在坯料上。
零件的构成形式是多样的,不同的模具由不同的零件构成。
模具在挤压、压铸和注塑过程中,外力则由气压、柱塞、冲头等,施加在坯料上,模具承受的是坯料的胀力。
注塑模具设计文献综述

毕业设计(论文)文献综述(2012届)题目电话机三维造型与注塑模具设计指导教师院系班级学号姓名二〇一一年十二月五日[塑料模具的发展] 文献综述摘要模具是塑料成型加工的一种重要的工艺装备,模具生产的最终产品的价值往往是模具自身价值的几十倍、上百倍,因此模具工业是国民经济的基础工业,模具的生产技术水平的高低,已成为衡量一个国家产品制造业水平高低的重要标志。
由于塑料模具工业快速发展及上述各方面差距的存在,因此我国今后塑料模具的发展必将大于模具工业总体发展速度。
塑料模具生产企业在向着规模化和现代化发展的同时,专和精仍旧是一个必然的发展趋势。
关键字:塑料模具、发展、标准化、CAD/CAM 、差距塑料模具是成型塑料制品的工艺装备或工具。
根据塑料成型工艺方法的不同,通常将塑料模具分为注射模具、压缩模具、传递模具、挤出模具、中空吹塑模具、热成型模具等。
合理的加工工艺、高效的设备、先进的模具是实现现代塑料制品生产必不可少的三大重要因素。
尤其是塑料模具对实现塑料成型工艺要求、保证塑料制件质量、降低生产成本起着重要的作用。
一副品质优良的塑料模具可成型几十万次,甚至上百万次。
这与模具设计、选材、制造和使用维护有着很大关系。
对塑料模具设计的要求是:能生产出在尺寸精度、外观、物理性能、力学性能等各方面均能满足使用要求的优质制件。
在模具使用时,力求生产效率高、自动化程度高、操作简便、寿命长;在模具制造方面,要求结构合理、制造容易、成本低廉。
我国塑料模具的发展现状整体来看,中国塑料模具无论是在数量上,还是在质量、技术和能力等方面都有了很大进步,但与国民经济发展的需求、世界先进水平相比,差距仍很大。
一些大型、精密、复杂、长寿命的中高档塑料模具每年仍需大量进口。
在总量供不应求的同时,一些低档塑料模具却供过于求,市场竞争激烈,还有一些技术含量不太高的中档塑料模具也有供过于求的趋势。
近年来,塑料模具工业迅速发展,体现在模具产品向着大型、精密、复杂的方向发展,综合技术含量不断提高,模具制造周期不断缩短。
注射成型工艺与注射模设计概述
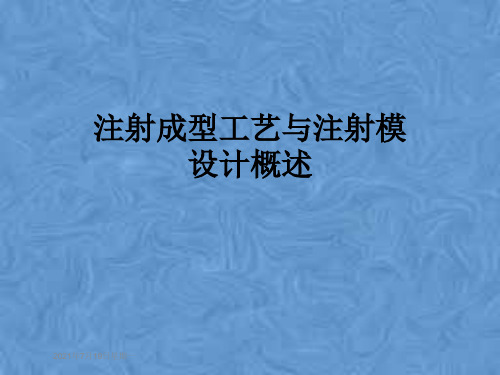
5.2 注射模的典型结构
5.2.6 角式注射机用注射模
5.3 注射模与注射机
5.3.1 注射机的分类 注射机分卧式注射成型机、立式注射成型机、角式注射成型机
和多模注射机等几种。 (1)卧式注射机
卧式注射机的注射装置和合模装置的轴线呈一线并水平排列。
5.3 注射模与注射机
5.3.1 注射机的分类 (2)立式注射机 注射装置与合模装置的轴线呈一线并与水平方向垂直 排列。 (3)角式注射机 角式注射机一般为柱塞式注射机,它的注射装置和合 模装置的轴线相互垂直排列。
5.1 注射模的分类及结构组成
5.1.2 注射模具的结构组成
注射模具由动模和定模两部分组成; 定模部分安装在注射机的固定模板上; 动模部分安装在注射机的移动模板上。 原理:在注射成型过程中,动模随注射机上的合模系统运动,
同时动模部分与定模部分由导柱导向而闭合构成浇注系统和 型腔,塑料熔体从注射机喷嘴流经模具浇注系统进入型腔。 冷却后开模时,动模与定模分离,取出塑件。 结构组成: 成型部分、浇注系统、导向机构、侧向分型与抽芯机构、推 出机构、温度调节系统、排气系统、支承零部件
4.2 注射成型工艺
注射成型工艺包括成型前的准备、注射过程和塑件的后处理。 1.成型前的准备 2.注射过程
注射过程一般包括加料、塑化、注射、冷却和脱模几个阶段。 (1)加料:加原料到注射机料斗的过程; (2)塑化:在料筒内由固态转变成熔体的过程; (3)注射 注射过程可分为充模、保压、倒流、浇口冻结后的冷
5.1 注射模的分类及结构组成
5.1 注射模的分类及结构组成
5.1.2 注射模具的结构组成 结构组成:成型部分、浇注系统、导向机构、侧向分型与抽 芯机构、推出机构、温度调节系统、排气系统、支承零部件
毕业文献综述

塑料注射成型模具设计文献综述11021470125 毛辉武摘要:本文将对塑料注射成型模具进行综述,介绍了模具行业的发展状况,以及我们模具与国外存在的差距与我们塑料模具的发展趋势;介绍了塑料模具,以及计算机CAD辅助技术,逆向技术、热流道技术、微注射成型技术在塑料模具中的应用与塑料模具技术的发展。
关键词:模具塑料注射成型模具 CAD逆向技术Abstract:This article will carry on the summary to the PlasticInjection Molding Mold. Briefed the mold profession development condition, as well as our mold and overseas existence disparity and our plastic mold's trend of development. Introduced the plastic mold, as well as computer auxiliary technology, reversion technology, hot flow channel technology, micro injection molding technology in plastic mold's application and plastic mold technology development.Keywords: mold,plastic injection molding mold ,CAD ,reverse technology模具的历史模具的出现可以追溯到几千年前的陶器时代和青铜器铸造年代,但其大规模使用却是随着现代工业的掘起而发展起来的。
进入70年代向高速化、精密化、启动化、安全化发展的第二阶段。
在这个过程中不断涌现各种高效率、高寿命、高精度的多功能自动模具。
6、洗衣机皮带轮的注射模设计
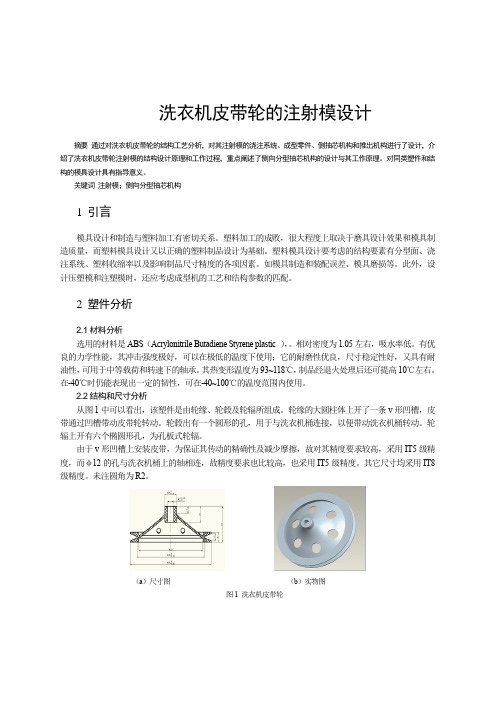
洗衣机皮带轮的注射模设计摘要通过对洗衣机皮带轮的结构工艺分析,对其注射模的浇注系统、成型零件、侧抽芯机构和推出机构进行了设计,介绍了洗衣机皮带轮注射模的结构设计原理和工作过程,重点阐述了侧向分型抽芯机构的设计与其工作原理。
对同类塑件和结构的模具设计具有指导意义。
关键词注射模;侧向分型抽芯机构1 引言模具设计和制造与塑料加工有密切关系。
塑料加工的成败,很大程度上取决于磨具设计效果和模具制造质量,而塑料模具设计又以正确的塑料制品设计为基础。
塑料模具设计要考虑的结构要素有分型面、浇注系统、塑料收缩率以及影响制品尺寸精度的各项因素。
如模具制造和装配误差、模具磨损等。
此外,设计压塑模和注塑模时,还应考虑成型机的工艺和结构参数的匹配。
2 塑件分析2.1材料分析选用的材料是ABS(Acrylonitrile Butadiene Styrene plastic ),。
相对密度为1.05左右,吸水率低。
有优良的力学性能,其冲击强度极好,可以在极低的温度下使用;它的耐磨性优良,尺寸稳定性好,又具有耐油性,可用于中等载荷和转速下的轴承。
其热变形温度为93~118℃,制品经退火处理后还可提高10℃左右。
在-40℃时仍能表现出一定的韧性,可在-40~100℃的温度范围内使用。
2.2结构和尺寸分析从图1中可以看出,该塑件是由轮缘、轮毂及轮辐所组成。
轮缘的大圆柱体上开了一条v形凹槽,皮带通过凹槽带动皮带轮转动。
轮毂出有一个圆形的孔,用于与洗衣机桶连接,以便带动洗衣机桶转动。
轮辐上开有六个椭圆形孔,为孔板式轮辐。
由于v形凹槽上安装皮带,为保证其传动的精确性及减少摩擦,故对其精度要求较高,采用IT5级精度,而φ12的孔与洗衣机桶上的轴相连,故精度要求也比较高,也采用IT5级精度。
其它尺寸均采用IT8级精度。
未注圆角为R2。
(a)尺寸图(b)实物图图1 洗衣机皮带轮3 模具的结构设计3.1型腔的布置模具型腔布置包括两方面的内容,即模具型腔的数目和各型腔在模具中的排列。
关于注射模具结构设计的文献综述【文献综述】
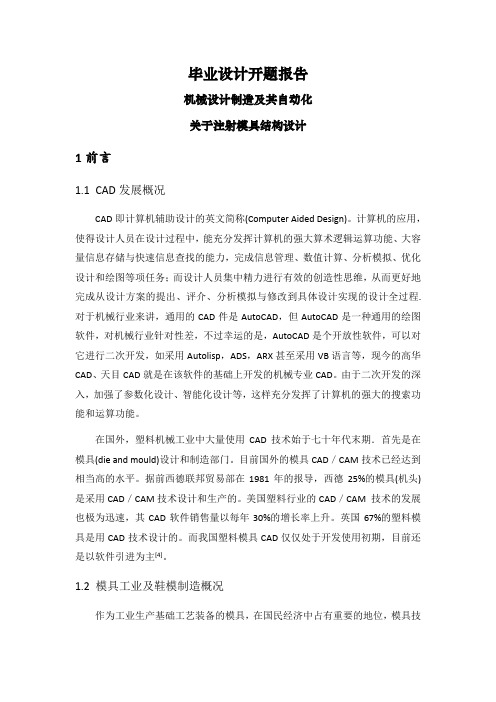
毕业设计开题报告机械设计制造及其自动化关于注射模具结构设计1前言1.1 CAD发展概况CAD即计算机辅助设计的英文简称(Computer Aided Design)。
计算机的应用,使得设计人员在设计过程中,能充分发挥计算机的强大算术逻辑运算功能、大容量信息存储与快速信息查找的能力,完成信息管理、数值计算、分析模拟、优化设计和绘图等项任务;而设计人员集中精力进行有效的创造性思维,从而更好地完成从设计方案的提出、评介、分析模拟与修改到具体设计实现的设计全过程.对于机械行业来讲,通用的CAD件是AutoCAD,但AutoCAD是一种通用的绘图软件,对机械行业针对性差,不过幸运的是,AutoCAD是个开放性软件,可以对它进行二次开发,如采用Autolisp,ADS,ARX甚至采用VB语言等,现今的高华CAD、天目CAD就是在该软件的基础上开发的机械专业CAD。
由于二次开发的深入,加强了参数化设计、智能化设计等,这样充分发挥了计算机的强大的搜索功能和运算功能。
在国外,塑料机械工业中大量使用CAD技术始于七十年代末期.首先是在模具(die and mould)设计和制造部门。
目前国外的模具CAD/CAM技术已经达到相当高的水平。
据前西德联邦贸易部在1981年的报导,西德25%的模具(机头)是采用CAD/CAM技术设计和生产的。
美国塑料行业的CAD/CAM 技术的发展也极为迅速,其CAD软件销售量以每年30%的增长率上升。
英国67%的塑料模具是用CAD技术设计的。
而我国塑料模具CAD仅仅处于开发使用初期,目前还是以软件引进为主[4]。
1.2 模具工业及鞋模制造概况作为工业生产基础工艺装备的模具,在国民经济中占有重要的地位,模具技术也已成为衡量一个国家产品制造水平的重要标志之一。
我国模具工业在政府十分重视及关怀下,并提出相应的优惠政策进行模具技术开发,在模具工业中大量采用先进技术和设备,努力提高模具设计和制造水平,取得显著的经济效益。
10ml一次性注射器外套注射模具及成型工艺设计成型【文献综述】
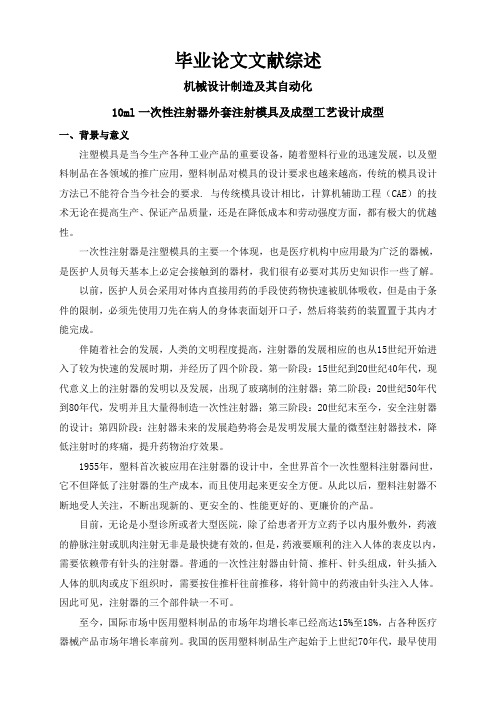
毕业论文文献综述机械设计制造及其自动化10ml一次性注射器外套注射模具及成型工艺设计成型一、背景与意义注塑模具是当今生产各种工业产品的重要设备,随着塑料行业的迅速发展,以及塑料制品在各领域的推广应用,塑料制品对模具的设计要求也越来越高,传统的模具设计方法已不能符合当今社会的要求. 与传统模具设计相比,计算机辅助工程(CAE)的技术无论在提高生产、保证产品质量,还是在降低成本和劳动强度方面,都有极大的优越性。
一次性注射器是注塑模具的主要一个体现,也是医疗机构中应用最为广泛的器械,是医护人员每天基本上必定会接触到的器材,我们很有必要对其历史知识作一些了解。
以前,医护人员会采用对体内直接用药的手段使药物快速被肌体吸收,但是由于条件的限制,必须先使用刀先在病人的身体表面划开口子,然后将装药的装置置于其内才能完成。
伴随着社会的发展,人类的文明程度提高,注射器的发展相应的也从15世纪开始进入了较为快速的发展时期,并经历了四个阶段。
第一阶段:15世纪到20世纪40年代,现代意义上的注射器的发明以及发展,出现了玻璃制的注射器;第二阶段:20世纪50年代到80年代,发明并且大量得制造一次性注射器;第三阶段:20世纪末至今,安全注射器的设计;第四阶段:注射器未来的发展趋势将会是发明发展大量的微型注射器技术,降低注射时的疼痛,提升药物治疗效果。
1955年,塑料首次被应用在注射器的设计中,全世界首个一次性塑料注射器问世,它不但降低了注射器的生产成本,而且使用起来更安全方便。
从此以后,塑料注射器不断地受人关注,不断出现新的、更安全的、性能更好的、更廉价的产品。
目前,无论是小型诊所或者大型医院,除了给患者开方立药予以内服外敷外,药液的静脉注射或肌肉注射无非是最快捷有效的,但是,药液要顺利的注入人体的表皮以内,需要依赖带有针头的注射器。
普通的一次性注射器由针筒、推杆、针头组成,针头插入人体的肌肉或皮下组织时,需要按住推杆往前推移,将针筒中的药液由针头注入人体。
【CN109865839A】涨紧皮带轮成型模具【专利】
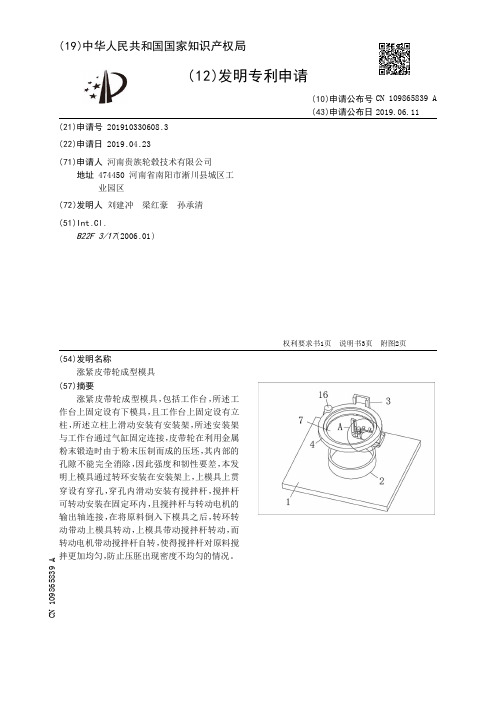
(19)中华人民共和国国家知识产权局(12)发明专利申请(10)申请公布号 (43)申请公布日 (21)申请号 201910330608.3(22)申请日 2019.04.23(71)申请人 河南贵族轮毂技术有限公司地址 474450 河南省南阳市淅川县城区工业园区(72)发明人 刘建冲 梁红豪 孙承清 (51)Int.Cl.B22F 3/17(2006.01)(54)发明名称涨紧皮带轮成型模具(57)摘要涨紧皮带轮成型模具,包括工作台,所述工作台上固定设有下模具,且工作台上固定设有立柱,所述立柱上滑动安装有安装架,所述安装架与工作台通过气缸固定连接,皮带轮在利用金属粉末锻造时由于粉末压制而成的压坯,其内部的孔隙不能完全消除,因此强度和韧性要差,本发明上模具通过转环安装在安装架上,上模具上贯穿设有穿孔,穿孔内滑动安装有搅拌杆,搅拌杆可转动安装在固定环内,且搅拌杆与转动电机的输出轴连接,在将原料倒入下模具之后,转环转动带动上模具转动,上模具带动搅拌杆转动,而转动电机带动搅拌杆自转,使得搅拌杆对原料搅拌更加均匀,防止压胚出现密度不均匀的情况。
权利要求书1页 说明书3页 附图2页CN 109865839 A 2019.06.11C N 109865839A权 利 要 求 书1/1页CN 109865839 A1.涨紧皮带轮成型模具,包括工作台(1),其特征在于,所述工作台(1)上固定设有下模具(2),且工作台(1)上固定设有立柱(3),所述立柱(3)上滑动安装有安装架(4),所述安装架(4)与工作台(1)通过气缸(5)固定连接,所述安装架(4)内可转动安装有转环(6),所述转环(6)上可拆卸连接有上模具(7),所述上模具(7)上贯穿设有穿孔,且上模具(7)的上端固定设有升降安装架(8),所述升降安装架(8)内可转动安装有搅拌杆(9),所述穿孔的下端活动连接有挡板(10),且当挡板(10)挡住穿孔时,所述挡板(10)的下表面与上模具(7)的下表面齐平。
汽车轮胎定型胶囊注射成型及其模具技术的探讨
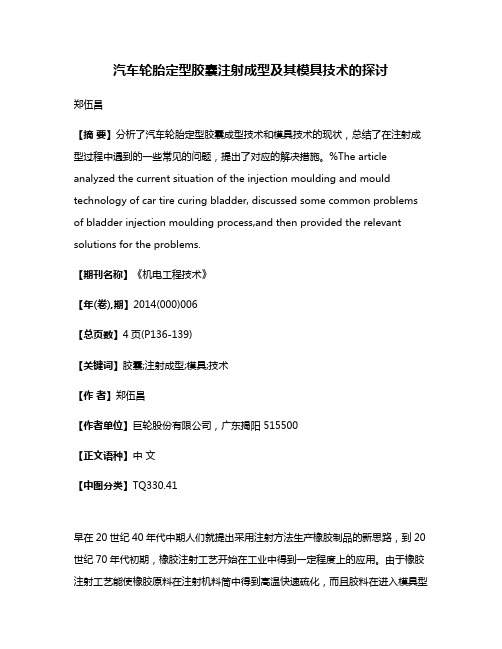
汽车轮胎定型胶囊注射成型及其模具技术的探讨郑伍昌【摘要】分析了汽车轮胎定型胶囊成型技术和模具技术的现状,总结了在注射成型过程中遇到的一些常见的问题,提出了对应的解决措施。
%The article analyzed the current situation of the injection moulding and mould technology of car tire curing bladder, discussed some common problems of bladder injection moulding process,and then provided the relevant solutions for the problems.【期刊名称】《机电工程技术》【年(卷),期】2014(000)006【总页数】4页(P136-139)【关键词】胶囊;注射成型;模具;技术【作者】郑伍昌【作者单位】巨轮股份有限公司,广东揭阳 515500【正文语种】中文【中图分类】TQ330.41早在20世纪40年代中期人们就提出采用注射方法生产橡胶制品的新思路,到20世纪70年代初期,橡胶注射工艺开始在工业中得到一定程度上的应用。
由于橡胶注射工艺能使橡胶原料在注射机料筒中得到高温快速硫化,而且胶料在进入模具型腔前经过预热和塑化,使橡胶制品在密闭、高压的型腔内硫化成型,制品的质量均匀、稳定,尺寸精度高,并且橡胶注射法自动化程度较高,与传统的模压法相比,其生产效率高很多,因此采用注射工艺生产橡胶制品的技术日益得到广泛的应用。
相对橡胶压制工艺来说,橡胶的注射工艺虽然起步慢,模具和设备制造成本高,模具精度要求也高,而且目前在国内应用范围也不是那么广泛,但是橡胶注射成型工艺具有效率高、产品质量好、自动化程度高、操作简便、节省原材料、简化生产工艺流程等很多优点,因此,在橡胶制品生产力日益增长的当今市场上,橡胶注射工艺逐渐被广大用户所采用。
- 1、下载文档前请自行甄别文档内容的完整性,平台不提供额外的编辑、内容补充、找答案等附加服务。
- 2、"仅部分预览"的文档,不可在线预览部分如存在完整性等问题,可反馈申请退款(可完整预览的文档不适用该条件!)。
- 3、如文档侵犯您的权益,请联系客服反馈,我们会尽快为您处理(人工客服工作时间:9:00-18:30)。
毕业论文文献综述机械设计制造及其自动化某皮带轮注射成型模具及成型工艺设计一、背景与意义注射模塑(又称注射成型或简称注塑),是成型塑料制品的一种重要方法。
几乎所有的热塑性塑料及多种热固性塑料都可用此法成型。
用注射模塑可成型各种形状、尺寸、精度,满足各种要求的模制品。
注塑制品约占塑料制品总量的20%~30%,尤其是塑料作为工程结构材料的出现,注塑制品的用途已从民用扩大到国民经济各个领域,并将逐步代替传统的金属和非金属材料的制品,包括各种工业配件,仪器仪表零件结构件、壳体等。
在尖端技术中,也是不可缺少的。
在我国实现四个现代化建设中起着重要的作用。
皮带轮属于盘毂类零件,一般相对尺寸比较大,在传统制造工艺上一般以铸造、锻造为主。
一般尺寸较大的设计为用铸造的方法,材料一般都是铸铁(铸造性能较好),很少用铸钢(钢的铸造性能不佳);一般尺寸较小的,可以设计为锻造,材料为钢。
传统工艺不但能耗大,而且很笨重。
现在采用注射成型皮带轮,质量轻,实践证明刚性也不差。
皮带轮各项指标及材质的选用是以能够达到使用要求的前提下上尽量减少原材料、工艺可行、成本最低的选择原则!皮带轮主要用于远距离传送动力的场合,例如小型柴油机动力的输出,农用车,拖拉机,汽车,矿山机械,机械加工设备,纺织机械,包装机械,车床,锻床,一些小马力摩托车动力的传动,农业机械动力的传送,空压机,减速器,减速机,发电机,轧花机等等。
皮带轮传动的优点有:皮带轮传动能缓和载荷冲击;皮带轮传动运行平稳、低噪音、低振动;皮带轮传动的结构简单,调整方便;皮带轮传动对于皮带轮的制造和安装精度不象啮合传动严格;皮带轮传动具有过载保护的功能;皮带轮传动的两轴中心距调节范围较大。
皮带传动的缺点有:皮带轮传动有弹性滑动和打滑,传动效率较低和不能保持准确的传动比;皮带轮传动传递同样大的圆周力时,轮廓尺寸和轴上压力比啮合传动大;皮带轮传动皮带的寿命较短。
三角皮带的规格是由背宽(顶宽)与高(厚)的尺寸来划分的,根据不同的背宽(顶宽)与高(厚)的尺寸,国家标准规定了三角带的O 、A、B、C、D、E等多种型号,每种型号的三角带的节宽、顶宽、高度都不相同,所以皮带轮也就必须根据三角带的形状制作出各种槽型;这些不同的槽型就决定了皮带轮的O型皮带轮、A型皮带轮、B型皮带轮、C型皮带轮、D型皮带轮、E型皮带轮等多种型号。
二、国内外研究状况注射成型技术已经历了大约125年的发展过程,由于各种各样的工艺方法及技术的引入、改进和提高,这种成型技术显得更具有经济性。
注射成型具有成型周期短,能一次成型外形复杂、尺寸精确、带有嵌件的制品;对成型各种塑料的适应性强;生产效率高,易于实现全自动化生产等一系列优点,是一种比较经济而先进的成型技术,因此世界各国对于它的研究都不曾间断。
与早期开发的John Wesley Hyatt生产工艺专利相比,目前采用的生产理论方法存有较少的概念上差异。
其基本过程仍然是在加热料筒内产生推动压力,形成熔料层流,并流入空的模腔内。
在循环生产周期中,不管是采用单个浇口还是多个浇口;高或低的熔料流动速率;待注射熔料与模腔壁之间温差的高或低;流畅的加工流程或突变式的加工流程,其基本过程完全相同。
由于许多新型聚合物、共混物和复合材料体系要求采用特殊的、先进的加工方法或技术才能顺利地注射模塑成型。
辅助性材料的涌现,导致开发出许多更具有粘弹性的新树脂或新材料。
也就是说,这些新型材料呈现出有更好的熔体弹性。
而先进的注射成型工艺已开始着重于研究粘弹性材料伴随加工参数的响应状态。
随着新技术的渗透,注射成型技术也在不断发展和完善。
1.共注射成型采用共注射成型有助于观察到制件中独特的结构。
塑料“A”先注射充入部分型腔,然后塑料“B”紧跟着“A”注射进入型腔并保持初始推动流动压力场。
根据表皮区和芯层区的尺寸大小,按正确的比例关系计量出“A”和“B”的用料量,可制得1个内芯层为“B”外表完全由“A”包裹的制件。
共注射成型并非一门新的工艺技术。
英国ICI公司早在70年代就开始应用这一技术。
现采用的ICI生产工艺类似“三明治模塑”。
2.气体辅助注射成型气体辅助注射成型技术主要是为了减轻重量和节省循环时间等而逐渐发展起来的。
通常的共注射成型中,首先注射外层材料,并只部分填充型腔。
然后气体通过喷嘴注射或直接进入模腔内,模塑制件的芯层部位。
液化气体也可注射到待成型制件的芯层部位。
一般而言,在芯层内气体压力推动熔料向前流动,直至完全充满型腔,并防止制件表层在固化阶段从模腔壁凹下。
相连的表皮层紧巾着模腔壁,气体则保存在模塑制件的芯层区间。
3.低压注射成型低压注射成型也并不是一种新的工艺,但采用的加工方法,可使设备工序能更好地与预料中的熔体响应相匹配。
低压注射成型只是控制或调节塑料粘弹特性的一种加工方法。
随着对加工环境认识的深入,采用低压注射成型将使塑料熔体更能适应生产环境的要求。
4.交变注射成型这项技术的最大难点在于当加工条件突然改变时,对塑料熔体将呈现出怎样的变化行为知之甚少。
通过这种加工工艺,制件的变曲性能与其他机械性能得到了极大的提高。
聚苯乙烯饮水杯和聚丙烯注射器就是采用这种加工方法获得重大改进突破的2个产品。
5.注射-压缩成型采用这种成型方法可以避免瞬间的材料响应,避免了阻碍熔体的流动。
6.模具的冷却模具的冷却是一项关键的工艺技术。
大部分的成型周期都是由传导热量传递组成。
能量可从热的熔体传递至冷的模具上是由于存在温差所致。
模具壁边的塑料表皮有效地隔离着芯层,从而使得这种热传递方式非常低效。
可是,模具冷却通常到设计的最后阶段才得以注意。
较好的冷却设计样式可缩短20%~30%或更短的循环生产时间,并提高劳动生产率。
脉冲冷却技术是在注射塑料进入模腔后,通过采用循环冷却管内非常冻的冷冻液体来调节冷却的一项技术。
脉冲冷却可广泛应用于薄壁制件的成型;要求重复精确表面的制件成型,以及流道深度变化范围宽的复杂型腔方面。
脉冲冷却也可调节材料的突变行为。
例如迟滞流动。
7.熔芯成型工艺熔芯成型法是一种比较新的工艺方法,便于加工内部有交叉复杂的沟道、凹槽或切槽的制件。
这种工艺基本上属于标准或常规型注射成型,这个型芯与常规模具一样具有可折将式的型芯功能,设有限定的内腔壁的嵌件型芯。
这种方法用于高精度制件是切实可行的。
此外,还有多点进料注射成型,推-拉注射成型,夹芯注射成型,层状注射成型,反应注射成型,结构发泡注射成型等等成型方法被研究并且运用到实际的生产中,大大推动了注射成型的发展。
三、研究成果在注射成型发展的这几年中,也取得了不少的成果。
1.金属粉末注射成型技术(Metal Powder Injection Molding,简称MIM)是将现代塑料注射成型技术引入粉末冶金领域而形成的一门新型粉末冶金近净形成技术。
其基本工艺过程是:首先将固体粉末与有机粘结剂均匀混炼,经制粒后在加热塑化状态下(~150oC)用注射成型机注入模腔内固化成型,然后用化学或热分解的方法将成型坯中的粘结剂脱除,最后经烧结致密化得到最终产品。
与传统工艺相比,具有精度高、组织均匀、性能优异、生产成本低等特点,其产品广泛应用于电子信息工程、生物医疗器械、办公设备、汽车、机械、五金、体育器械、钟表业、兵器及航空航天等工业领域。
因此,国际上普遍认为该技术的发展将会导致零部件成型与加工技术的一场革命,被誉为“当今最热门的零部件成型技术”和“21世纪的成型技术”。
MIM始于20世纪70年代末,其工艺包括产品设计、模具设计、质量检测、混炼、注射、脱脂、烧结、二次加工等8个重要环节。
特别是在八十年代中期,这项技术实现产业化以来更获得突飞猛进的发展,每年都以惊人的速度递增。
到目前为止,美国、西欧、日本等十多个国家和地区有一百多家公司从事该工艺技术的产品开发、研制与销售工作。
在日本,许多大型株式会社均参与MIM工业的推广,在这些公司包括有太平洋金属、三菱制钢、川崎制铁、神户制钢、住友矿山、精工-爱普生、大同特殊钢等。
2.计算机辅助成型采用计算机辅助工程(CAE)对加工设计及分析有助于缩短设计周期并可避免代价昂贵的机械失误。
商业性仿真代码常用于流道上标明尺寸,以平衡熔料在流道系统及型腔内的流动,同事确定浇口的最佳开设位置和浇口的数目。
计算注射压力和合模吨位要根据不同的加工条件和材料而定。
收缩率及翘曲率结合初始流向也可准确估算出来。
重要的是要使得这种设计工具帮助熟练分析人员在某个设计方案或加工研究时进行判断和操纵。
结果必须理解为以研究对象和加工材料为前提。
当考虑采用这种方法准确输入数据后,可取得巨大的效益。
另外,这种分析经济性可使设计周期更短和所需的生产时间更短。
应该提醒注意的是,商业性的CAE程序通常是不可直接使用的。
充模仿真可产生有价值的见识,但结果必须重新对其局限性进行重新考虑估计。
应用现代计算机进行注射成型模拟试验,仅限于纯粘性流体(不包括粘弹性的熔融塑料)。
四、发展趋势1.锁模力、注射量的趋向越来越大从注射机问世起,锁模力在1000-5000kN,注射量在50-2000g的中小型注射机占绝大多数。
到了70年代后期,由于工程塑料的发展,特别是在汽车、船舶、宇航、机械以及大型家用电器方面的广泛应用,使大型注射机得到了迅速发展。
美国最为明显。
在1980年全美国约有140台10000kN以上锁模力的大型注塑机投入巾场,到1985年增至500多台。
日本名机公司已经成功地制造了当今世界最大的注塑机,其锁模力达到120000kN,注射量达到92000g。
2.计算机辅助分析软件的开发应用80年代以来,CAD/CAE/CAPP/CAM计算机应用技术在塑机制造业的广泛采用,促进了我国注塑机研发和制造水平的高速发展。
一批国家级高新技术企业都相继引进美国U.G.S和PTC公司的计算机辅助设计和分析等软件,实现了三维立体参数化建模,机构运动仿真,对主关原件分析,对高应力区的应力分布、应力峰值、危险区域等进行准确的分析计算,帮助设计人员迅速地了解、评估和修改设计方案,保证重要零件结构合理性的可靠性达到完美结合。
3.注射机的性能越来越好,效率越来越高国际上移模速度,已从过去的20-30m/min提高到40-50m/min,最高的达到70m/min。
注射速度从过去的100mm/s提高到现在的250mm/s,有的达到450mm/s。
注射压力从过去的120-150MPa提高到目前的180-250MPa。
日本的SN120P机已达到460MPa,它生产的制品收缩率几乎为零,制品公差可保证在0.02-0.03mm,壁厚可保证0.l-0.2mm。
节能方面从过去的流量比例和压力比例控制发展到变量控制或定量控制,变频调速控制,伺服控制技术的注塑机,能耗仅为传统机器的30%,注塑机的高效率主要体现在工作节拍快,制品周期短,普遍比过去提高24%以上。