坯体的干燥
陶瓷工艺学6坯体的干燥09.

综合干燥
综合干燥是一种强化干燥方法,由于几种方法同时采用, 往往能使生坯快速干燥而不致出现干燥缺陷。常采用的综 合干燥方法有如下几类:
1、辐射干燥和热空气对流干燥相结合
目前采用热风-红外线干燥,坯体在开始干燥时所必须的热 量由红外线供给,保证坯体热扩散和湿扩散方向一致。红 外线照射加热一段时间后,内扩散被加快,接着喷射热风, 使外扩散加快,如此反复进行,水分可迅速排出。
化学结合水:包含在矿物的分子结构中,结合牢固,
排除时需要较大能量。
干燥技术-坯体中水的类型
一定干燥条件下,物料中的水分按能否除, 可分为自由水分和平衡水分。
干燥过程中可除去部分称为自由水分。
物料中的水分是自由水与平衡水之和。
传质传热过程
干燥过程既是传热过程,又是传质过程。 传热过程:通过物料表面将热传给物料,再以传 导的方式向内部传送,物料表面水分获得热量后汽化。 传质过程:物料表面的水蒸气向干燥介质中移动 的气相传质(外扩散过程);内部水向表面扩散的内部 传质(内扩散过程)。
最终含水率的影响因素
最终含水率与周围介质的温度、相对湿度和 坯料组成有关。
最终含水率过高,则坯体强度不够,降低窑 炉效率,过低则在干燥后坯体会在大气中吸湿, 或在施釉过程中急剧吸水,造成坯体表面膨胀, 是施釉后开裂的主要原因之一。
影响干燥速率的因素
外扩散速率:这常决定于干燥介质的温度、湿 度和流态(流速的大小和方向)以及物料的性 质。干燥介质的温度越高(相对湿度就越小), 流速越快(边界层应越薄),外扩散速度越大。
干燥方法
自然干燥法:将湿坯置于露天或室内的场地上,借 助风吹和日晒的自然条件使物料得以干燥的办法。成本 低,但干燥速度慢,产量低,劳动强度大,受气候影响 大,难以适应大规模的工业生产。
陶瓷坯体不同干燥方式的对比研究

燥速 度的 l 倍。 2 将含水量为 2 w% 2 t 的陶瓷坯体 干燥至恒重 , 普通电热干燥 的运行成本最高 , 约为远红外干燥的 1 倍和微波干燥 . 5
的4 . 。分析了远红外干燥 和微 波干燥在 陶瓷工业应用 的可行性 , 出了需要解决 的技术难题 。 2倍 指
关键 词 陶瓷坯体 ; 微波干燥 ; 远红外干燥 ; 干燥速度
Fg2 Ifae - r ig c a a t r t s o ec r mi b d i. nr rd d yn h r ce i i fh e a c o y sc t
料内部的水分以液态或气态的形式沿毛细管扩散到
物料表面 , 再由表面蒸发 到干燥周围介质 中嗍 从图 。
13可 以看 出 , 同干燥 方 式下 陶瓷 湿坯 经历 的干燥  ̄ 不 过程 大致相 同 , 均可 分为 三个 阶段 : 热阶段 、 加 等速 干
等是新世纪对干燥技术的基本要求n 1 。
微波干燥对陶瓷坯体的干燥过程进行实验研究 , 研究 不 同干燥方法对干燥速率 、 内外温差的影响。 坯体 分
析各种干燥方式的可行性及经济性 , 探讨远红外干 燥、 微波干燥在生产实用中的前提条件及需要解决的
关键技 术 问题 。
在陶瓷行业 中, 热风干燥 由于热风来源丰富 , 价 格便宜 , 成为最常使用的一种传统干燥方 法 , 然而直
中图分类号:_ 7 .+ 文献标识码 : T Q1 463 A
存在任何危害[ 微波干燥 以干燥速度快 、 2 1 。 选择性加
0 引 言
陶瓷产品的干燥是陶瓷生产工艺中非常重要的
工序之一。干燥是—个技术相对简单 , 应用却十分广 泛的工业过程 , 其不但关 系着陶瓷的产品质量及成品 率, 而且影响陶瓷企业的整体能耗和生产成本。据统
陶的工艺流程
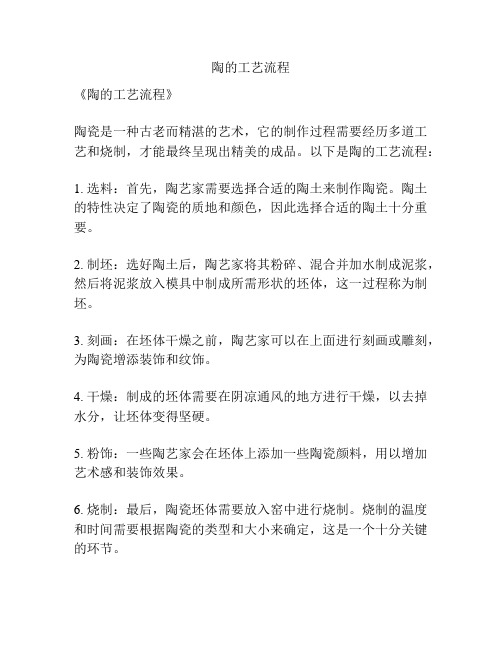
陶的工艺流程
《陶的工艺流程》
陶瓷是一种古老而精湛的艺术,它的制作过程需要经历多道工艺和烧制,才能最终呈现出精美的成品。
以下是陶的工艺流程:
1. 选料:首先,陶艺家需要选择合适的陶土来制作陶瓷。
陶土的特性决定了陶瓷的质地和颜色,因此选择合适的陶土十分重要。
2. 制坯:选好陶土后,陶艺家将其粉碎、混合并加水制成泥浆,然后将泥浆放入模具中制成所需形状的坯体,这一过程称为制坯。
3. 刻画:在坯体干燥之前,陶艺家可以在上面进行刻画或雕刻,为陶瓷增添装饰和纹饰。
4. 干燥:制成的坯体需要在阴凉通风的地方进行干燥,以去掉水分,让坯体变得坚硬。
5. 粉饰:一些陶艺家会在坯体上添加一些陶瓷颜料,用以增加艺术感和装饰效果。
6. 烧制:最后,陶瓷坯体需要放入窑中进行烧制。
烧制的温度和时间需要根据陶瓷的类型和大小来确定,这是一个十分关键的环节。
在经历了以上几个工艺流程后,陶艺家就可以得到精美的陶瓷作品了。
陶的工艺流程虽然看起来简单,但其中包含着对陶艺家技术和耐心的考验,也因此体现了陶瓷艺术的独特魅力。
陶瓷的简单制作过程
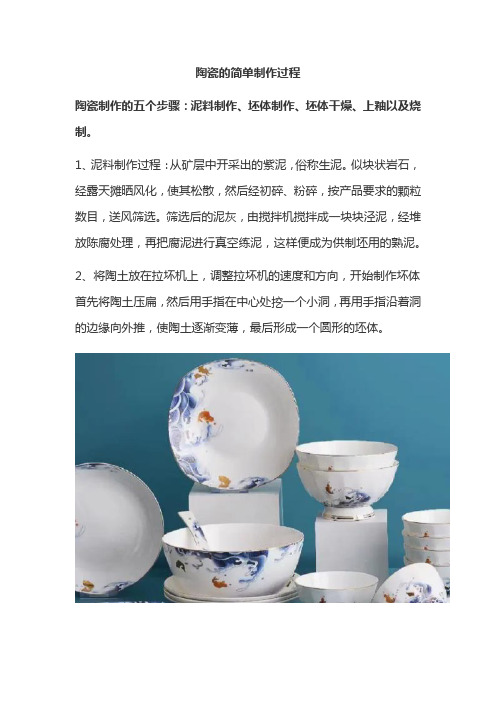
陶瓷的简单制作过程陶瓷制作的五个步骤:泥料制作、坯体制作、坯体干燥、上釉以及烧制。
1、泥料制作过程:从矿层中开采出的紫泥,俗称生泥。
似块状岩石,经露天摊晒风化,使其松散,然后经初碎、粉碎,按产品要求的颗粒数目,送风筛选。
筛选后的泥灰,由搅拌机搅拌成一块块泾泥,经堆放陈腐处理,再把腐泥进行真空练泥,这样便成为供制坯用的熟泥。
2、将陶土放在拉坏机上,调整拉坏机的速度和方向,开始制作坏体首先将陶土压扁,然后用手指在中心处挖一个小洞,再用手指沿着洞的边缘向外推,使陶土逐渐变薄,最后形成一个圆形的坯体。
3、陶瓷坯体干燥是指坯体中水分排除的过程。
坯体经干燥后强度得到提高。
这有利于搬运、装窑和烧成,水分减少能防止在烧成初期升温时因坯体水分大量排放而造成废品。
坯体经干燥后留有2%左右的残余水分即可。
4、上釉,就是所谓在烧制陶、瓷器时,首先应该烧制毛胚,烧好后拿出来上釉,然后再烧的一种方式。
在烧制好的毛坯上涂覆上一层玻璃质的釉层,主要起到保护和装饰作用。
5、烧制是指以粘土为胎,经过手捏、轮制、模塑等方法加工成型后,在1000-1200度左右的高温下焙烧而成的物品,陶艺的制作工艺按顺序可分为原料加工(包括配泥和配釉)、泥坯塑制、赋釉及煅烧四大工序,在中国陶器的产生距今已有11700多年的悠久历史。
陶瓷的原料:陶瓷及其他硅酸盐制品所用原料大部分是天然的矿物或岩石,其中多为硅酸盐矿物。
这些原料种类繁多,资源蕴藏丰富,在地壳中分布广泛,这为陶瓷工业的发展提供了有利的条件,早期的陶瓷制品,均是用单一的黏土矿物原料制作的。
后来,随着陶瓷工艺技术的发展及对制品性能要求的提高,人们逐渐地在坯料中加入了其他矿物原料,即除用黏土作为可塑性原料以外,还适当添入石英作为瘠性原料,添入长石以及其他含碱金属及碱土金属的矿物作为熔剂原料。
目前,陶瓷原料的分类尚无统一的方法,一般按原料的工艺特性划分为可塑性原料、瘠性原料、熔剂性原料和功能性原料四大类。
陶瓷工艺原理_郑州大学中国大学mooc课后章节答案期末考试题库2023年
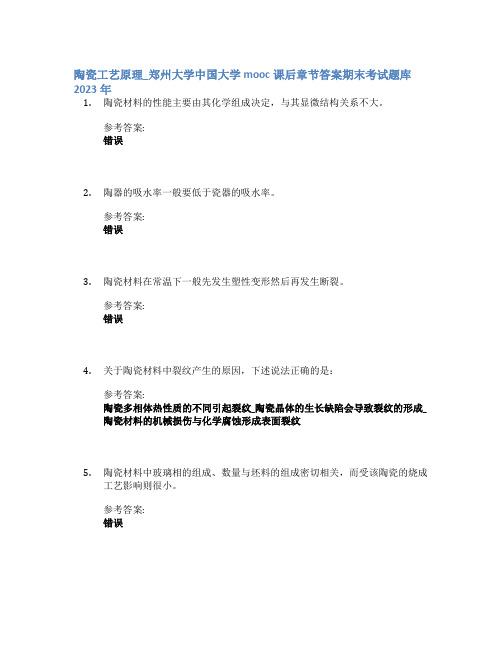
陶瓷工艺原理_郑州大学中国大学mooc课后章节答案期末考试题库2023年1.陶瓷材料的性能主要由其化学组成决定,与其显微结构关系不大。
参考答案:错误2.陶器的吸水率一般要低于瓷器的吸水率。
参考答案:错误3.陶瓷材料在常温下一般先发生塑性变形然后再发生断裂。
参考答案:错误4.关于陶瓷材料中裂纹产生的原因,下述说法正确的是:参考答案:陶瓷多相体热性质的不同引起裂纹_陶瓷晶体的生长缺陷会导致裂纹的形成_陶瓷材料的机械损伤与化学腐蚀形成表面裂纹5.陶瓷材料中玻璃相的组成、数量与坯料的组成密切相关,而受该陶瓷的烧成工艺影响则很小。
参考答案:错误6.陶瓷的显微结构主要由生产工艺决定,与其化学组成关系不大。
参考答案:错误7.采用陶瓷生产工艺,可以制备出高质量的大理石墙地砖。
参考答案:错误8.干燥缺陷是由不均匀收缩引起的内应力造成的。
参考答案:正确9.微波干燥是以微波辐射使生坯内极性强的分子,主要是水分子运动随交变电场的变化而加剧,发生摩擦而转化为热能使生坯干燥的方法。
参考答案:正确10.采用圆形的泥浆搅拌池比采用六角形的搅拌效果好。
参考答案:错误11.注浆成型是指在石膏模的毛细管力作用下,含有一定水分的粘土泥浆脱水硬化、成型的过程。
参考答案:正确12.对于普通陶瓷来说,所含的晶相越多、玻璃相越少,则强度越高。
参考答案:正确13.按照概念和用途,特种陶瓷又可进一步划分为:参考答案:结构陶瓷_功能陶瓷14.为了提高陶瓷坯料的可塑性,加入的最佳矿物原料是:参考答案:膨润土15.下列属于釉中网络形成剂的组分是:参考答案:二氧化硅16.陶瓷工业中常用的长石类型有钾长石、钠长石、钙长石和钡长石。
参考答案:错误17.陶瓷材料的相变增韧主要是利用单斜相ZrO2向四方相ZrO2的转变实现的。
参考答案:错误18.多晶陶瓷材料的强度随晶粒尺寸的增大而升高。
参考答案:错误19.在釉料配方中提高Na2O或CaO的含量可使釉的熔融温度降低。
坯体在窑前干燥窑中出现裂纹的疑难解答等

以前段辊上集中抽湿为主袁辊下后段加热为主袁同时主加
热风管接入点分布在干燥窑后段为宜袁 这样便于调节温
度和湿度曲线遥
压力控制院干燥窑前段为微负压袁后段为正压遥 如果
Байду номын сангаас
窑前干燥前前段温渊达到 150~180 益冤或者整体温度过高
同时袁该区域的烟气湿度又过小话袁特别容易导致坯体出
现横向裂纹或面裂等缺陷曰 如果窑前干燥前段温度或者
而淘汰一些不能更好的适应陶瓷生产的机器遥 这将会让
喷墨机从品牌之间的竞争转变到用户的自主化筛选遥
综合种种原因分析袁我国在线使用的第一批喷墨机性
能已经近乎于野精疲力竭冶袁所以笔者认为袁在 2014 年年
底在这一个陶企集中停产的野检修期冶里将会迎来我国陶
瓷喷墨打印机的一次换机浪潮浴
渊陈广玉冤
编辑部院0757-82269827 传真院0757-82269827 蔡飞虎院0757-82710910 渊佛山市玻尔陶瓷科技有限公司冤 孔海发院0757-83135108 渊0冤13702559893 程昭华院13927717401(佛山市佳窑陶业技术有限公司)
窑前干燥的调试大概可以参照以下温度曲线进行初步的
调试袁然后待产品出窑后的实际情况袁再进行下一步的微
调遥 窑前干燥前段温度院60~110 益袁 干燥中段温度 150~
180 益袁干燥后段温度院140~160 益遥
窑前干燥烟气湿度的要求院 干燥前段烟气需略带湿
度而后段烟气必须是高温干燥的遥 加热与抽湿方式院一般
潘雄院13927769832渊广东新润成陶瓷有限公司冤 韩复兴院18237699507渊河南信阳方浩实业有限公司冤 秦威院13927270859渊佛山市达索陶瓷科技有限公司
卫生陶瓷—烧制工艺流程

卫生陶瓷—烧制工艺流程卫生陶瓷是指用于卫生设备、卫生洁具制造的陶瓷材料。
它由陶瓷原料粉末经过成型、烧制等工艺制成。
下面是卫生陶瓷的烧制工艺流程的详细介绍。
1.原料准备:最常用的卫生陶瓷原料是瓷土和氧化铝。
瓷土是细粒的高岭土,氧化铝是氧化铝粉末。
在烧制工艺中,这些原料需要经过精细研磨和混合,以确保成品的光泽和均匀性。
2.成型:将混合好的原料制成成型坯体,常用的成型方法有干压成型和注浆成型。
干压成型是将原料粉末放入模具中,通过压力将其压实成形。
注浆成型是将原料粉末与水浆混合后灌入模具,通过振动和真空抽取将水分抽走形成坯体。
3.干燥:成型后的坯体需要经过干燥才能烧制。
常用的干燥方法有自然干燥和热风干燥。
自然干燥是将坯体放置在通风的环境中,通过空气对其进行干燥。
热风干燥是通过加热和送风设备,将热风对坯体进行干燥。
4.烧制:干燥后的坯体需要进行烧制。
烧制是将坯体置于高温环境中,使其发生化学变化从而形成陶瓷材料。
常用的烧制方法有窑炉烧制和隧道窑烧制。
窑炉烧制是将坯体放置在窑炉中,通过加热和控制温度,使坯体在特定的时间和温度下进行烧制。
隧道窑烧制是将坯体放置在一个贯穿整个生产线的隧道窑中,通过传送带将坯体从一个端口送入隧道窑,经过一段时间后从另一个端口取出,整个过程都处于高温环境中。
5.冷却:烧制后的陶瓷材料需要经过冷却才能进行下一步的处理。
冷却的目的是使陶瓷材料逐渐降温,防止其因温度过高而发生破裂。
6.配置釉料:烧制过程中,陶瓷表面需要涂上一层釉料,以提高其光泽和光滑度。
配制釉料需要选择合适的颜料和添加剂,并将其与适量的水进行混合和搅拌,直至形成均匀的釉料浆料。
7.釉料涂敷和装饰:陶瓷材料经过冷却后,将进行釉料涂敷和装饰。
涂敷釉料是将釉料均匀地涂抹在陶瓷表面,装饰是对陶瓷进行花纹、图案或颜色的装饰,常用的装饰方法有喷涂、刻画和贴花。
8.再次烧制:涂抹完釉料和进行装饰后,陶瓷材料需要再次进行烧制。
这次烧制的目的是将釉料烧成一层坚硬的琉璃层,使其与基体一体化,增强陶瓷的光泽和韧性。
单元六陶瓷坯体干燥

内、外扩散哪个慢,哪个就成为控制因素。影响生坯内扩散的 内因有含水率、生坯的组成与结构等。瘠性原料可以减少成型水分、 减少干燥收缩、加速内扩散。生坯温度是内扩散的重要外因。温度 升高,水的粘度降低、毛细管中水的弯月面表面张力及其合力也降 低,可提高水的内扩散速度。同时,也可加快处于降温干燥阶段的 生坯内水蒸气的扩散速度。当温度梯度与湿度梯度方向一致时会显 著加快内扩散速度。
(3)降速干燥阶段 在降速干燥阶段,生坯失去外表面的水膜,颗粒靠拢,毛细管 的直径更小,使内扩散阻力增大,外扩散因此受到制约,μ 随有绝 对含水率ω 的降低而降低。 (4)平衡阶段 坯体的水分与环境的交换呈平衡状态,干燥过程终止, μ =0,J 不变,此时的含水率为最终含水率。最终含水率除与周围介质温度、 相对湿度有关外,还与坯料组成有关。 此时,一般含水率<2%。
(3)自由水 自由水又称机械结合水,它分布于固体颗粒之 间,可以在干燥的过程中全部除去。在自由水的排出过程中坯体的 颗粒相互靠拢而使坯体收缩,其收缩体积约等于所排出自由水的体 积。因此,自由水又称为收缩水。
干燥过程只需排除自由水即可。赶走吸附水没有什么实际意义, 因为它很快又从空气中吸收水分达到平衡。而结构水一般不在干燥 过程中排除,而要在烧成过程中除去。一般确定干燥后的含水率时, 不应低于平衡水分,否则坯体还会从大气中吸湿“反潮”。
6.1 干燥原理 6.1.1湿坯中水分类型及结构形式
陶瓷湿坯中的水分,按其不同的结构形式共分三种类型: (1) 化学结合水 化学结合水是指参与组成矿物晶格的水分。 例如高岭土中有两个分子的结构水(Al2O3·2SiO2·2H2O),不能经 过干燥除去,排出时需要较高的能量。高岭土的结构水要在450~ 650℃之间才能除去。 (2) 吸附水 吸附水是指依靠坯料质点静电引力和质点间毛 细结构形成的毛细管力,存在于物理颗粒表面或微毛细管中的水分。 这种水的吸附量取决于坯料性质,特别是粘土原料的种类和用量。 当坯体的吸附水量与外界达到平衡时,该水称为平衡水。
陶瓷坯体的干燥过程

陶瓷坯体的干燥过程在对流干燥过程中介质与坯体之间既有热交换,又有质交换,可以将其分为下面三个既同时进行又相互联系的过程:(1)传热过程干燥介质的热量以对流方式传给坯体表面,又以传导方式从表面传向坯休内部。
坯体表面的水分得到热量而汽化,由液态变为气态。
(2)外扩散过程坯体表面产生的水蒸汽,通过层流底层,在浓度差的作用下,以扩散方式由坯体表面向干燥介质中移动。
(3)内扩散过程由于湿坯体表面水分蒸发,使其内部产生湿度梯度,促使水分由浓度较高的内层向浓度较低的外层扩散,称湿传导或湿扩散。
当坯体中存在有温度梯度时,也会引起水分的扩散移动,移动的方向指向温度降低的方向,即与温度梯度的指向相反,这种单由温度梯度引起的水分移动称热湿传导或称热扩散。
在实际的干燥过程中,水分的内扩散过程一般包括湿传导和热湿传导的共同作用。
(二)坯体干燥过程的特点干燥过程依次分为如下几个阶段;(1)加热阶段由于干燥介质在单位时间内传给坯体表面的热量大于表面水分蒸发所消耗的热量,因此受热表面温度逐步升高,直至等于干燥介质的湿球温度,即到达图中A点,此时表面获得热与蒸发耗热达到动平衡,温度不变。
此阶段坯体水分减少,干燥速率增加。
(2)等速干燥阶段本阶段仍继续进行自由水排除。
由于坯体含水分较高,表面蒸发了多少水量,内部就能补充多少水量,即坯体内部水分移动速度(内扩散速度)等于表面水分蒸发速度,亦等于外扩散速度,所以表面维持潮湿状态。
另外,介质传给坯体表面的热量等于水分汽化所需之热量,所以坯体表面温度不变,等于介质的湿球温度。
坯体表面的水蒸汽分压等于表面温度下的饱和水蒸汽分压,干燥速率恒定,故称等速干燥阶段。
因本阶段是排除自由水,故坯体会产生体积收缩,收缩量与水分降低量成直线关系,若操作不当,干燥过快,坯体极易变形、开裂,造成干燥废品。
等速干燥阶段结束时,物料水分降低到临界值,K点即为临界水分点。
此时尽管物料内部仍是自由水,但在表面一薄层内已开始出现大气吸附水。
坯体干燥过程中应控制哪些参数
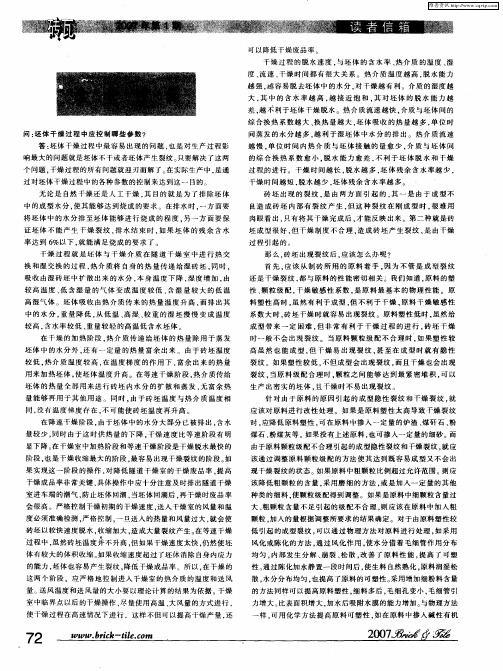
系 数 大 时 , 坯 干燥 时就 容 易 出现 裂纹 。原 料塑 性 低 时 , 然 给 砖 虽 成 型 带 来 一 定 困 难 , 非 常 有 利 于 干 燥 过 程 的 进 行 , 坯 干 燥 但 砖 时 一 般 不 会 出现 裂 纹 。 当原 料 颗 粒 级 配 不 合 理 时 , 果 塑 性 较 如
问 : 体 干 燥 过 程 中 应 控 制 哪些 参 数 ? 坯
间 蒸 发 的水 分 越 多 , 利 于 湿 坯 体 中水 分 的 排 出 。热 介 质 流 速 越 越 慢 , 位 时 间 内 热 介 质 与 坯 体 接 触 的 量 愈 少 , 质 与 坯 体 间 单 介 的综 合 换 热 系数 愈 小 . 水 能 力 愈 差 , 利 于 坯 体 脱 水 和 干 燥 脱 不 过 程 进 行 。 干燥 时 间越 长 , 水 越 多 , 体 残 余 含 水 率 越 少 , 脱 坯 干燥 时 间越 短 , 脱水 越 少 , 体残 余 含 水 率 越 多 。 坯 砖 坯 出 现 的裂 纹 , 由 两 方 面 引 起 的 , 一 是 由 于 成 型 不 是 其 良造 成 砖 坯 内 部 有 裂 纹 产 生 , 这 种 裂 纹 在 刚 成 型 时 , 难 用 但 很 肉眼 看 出 , 只有 将 其 干燥 完 成 后 , 能反 映 出来 。第 二 种 就是 砖 才 坯 成 型 很 好 , 干燥 制 度 不 合 理 , 成 砖 坯 产 生裂 纹 , 由干 燥 但 造 是
过程引起的。
答 : 体 干燥 过 程 中最 容 易 出 现 的 问题 。 坯 也是 对生 产 过 程 影 响 最 大 的问 题就 是 坯 体不 干 或 者坯 体 产生 裂纹 。 只要 解 决 了这 两
陶瓷制作工艺流程介绍
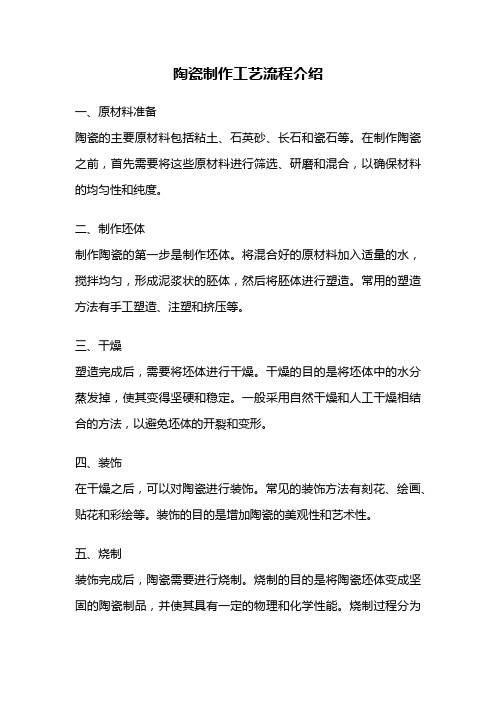
陶瓷制作工艺流程介绍一、原材料准备陶瓷的主要原材料包括粘土、石英砂、长石和瓷石等。
在制作陶瓷之前,首先需要将这些原材料进行筛选、研磨和混合,以确保材料的均匀性和纯度。
二、制作坯体制作陶瓷的第一步是制作坯体。
将混合好的原材料加入适量的水,搅拌均匀,形成泥浆状的胚体,然后将胚体进行塑造。
常用的塑造方法有手工塑造、注塑和挤压等。
三、干燥塑造完成后,需要将坯体进行干燥。
干燥的目的是将坯体中的水分蒸发掉,使其变得坚硬和稳定。
一般采用自然干燥和人工干燥相结合的方法,以避免坯体的开裂和变形。
四、装饰在干燥之后,可以对陶瓷进行装饰。
常见的装饰方法有刻花、绘画、贴花和彩绘等。
装饰的目的是增加陶瓷的美观性和艺术性。
五、烧制装饰完成后,陶瓷需要进行烧制。
烧制的目的是将陶瓷坯体变成坚固的陶瓷制品,并使其具有一定的物理和化学性能。
烧制过程分为干燥烧和高温烧两个阶段,其中高温烧的温度通常在1000℃以上。
六、上釉烧制完成后,陶瓷制品需要进行上釉。
釉料是由玻璃粉末和颜料等原料制成的,可以增加陶瓷的光泽和防水性。
上釉的方法有浸釉、刷釉和喷釉等。
七、再次烧制上釉完成后,需要再次进行烧制。
这次烧制的温度通常较低,一般在800℃左右。
烧制完成后,陶瓷制品表面形成一层光滑的釉面,具有一定的强度和耐磨性。
八、检验和包装对陶瓷制品进行检验和包装。
检验的目的是检查陶瓷的质量和外观是否符合要求,包装的目的是保护陶瓷制品不受损坏。
常见的包装方式有纸盒包装、泡沫包装和木箱包装等。
以上就是陶瓷制作的主要工艺流程。
从原材料准备到最后的包装,每个环节都需要精心操作,以确保制作出优质的陶瓷制品。
陶瓷制作工艺的精湛和独特性,使得陶瓷成为了一门独具魅力的艺术和工艺。
无论是在餐桌上的瓷器、装饰品、还是建筑陶瓷,都能展现陶瓷的独特魅力和艺术价值。
陶瓷坯体干燥过程控制

陶瓷坯体在立式干燥器里经过以下几个运 动阶段。
第一阶段(见图2):准备装卸坯体。
嬲嬲黑
嬲嬲嬲
丹弼弼
o。o o o o同目羁黑黑蔑
出 坯机
进坯机
过程中各个机构的状态如表2所示。
确黑霓! {熙黑嬲I 一一 i黑黑熟I 一…- 。。再坼搿晶。煦黑熙。。 出川l i诵目目I 进刖。 ;弱目囡j l同踊同;
1正式干坯机I
停止 停止 停止 运行
第二阶段(见图3):装坯和卸坯。 进坯机把坯体输送到干坯机口时,干坯机 内部的光电管检测到坯体,吊篮的辊棒开始运 行,在这个过程中出坯和进坯是同时进行的。 干燥完成的坯体被输出干燥器,在出坯机上光 电管检测到坯体后将坯体继续向前输送。而待 干燥的坯体则同时进入干燥器,同时根据光电 管输入的信号对于燥的坯体进行记数,在这个
口詈同 ,[]宝目 同同 同同同
立式十坯机
图2准备装卸坯体
坯体自翻坯机出来,进入进坯机,进坯机 上的光电管检测到坯体后,进坯机上电机开始 工作,将坯体有序地排列成几排,等待装入干 坯机干燥。在这一阶段,各个机构的运动状态 如表l所示。
陶艺(第六章)-坯体的干燥
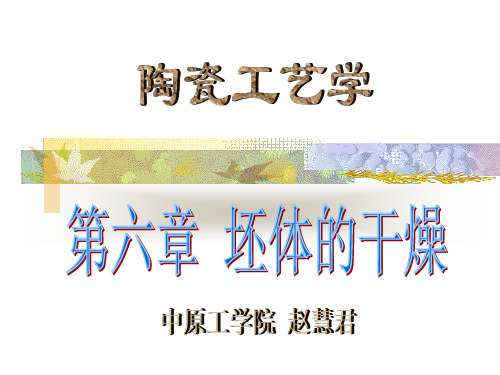
干燥:依靠蒸发而使成型后的坯体脱水 的过程。 干燥的目的
提高坯体强度,减少生坯的变形和破损
提高坯体的吸水率,以便进行施釉操作解坯体干燥过程的实质和产生 收缩的原因 掌握坯体干燥过程中的变化规律
选择合适的干燥制度和干燥设备
平衡阶段:当坯体干燥到表面水分达到 平衡水分时,表面干燥速度降为零。 表面蒸发 坯体 吸附 周围介质
平衡水分的多少取决于坯体的性质和周 围介质的温度和湿度,此时坯体中的水 分称为干燥最终水分。
干燥前状态
临界状态
干燥中止状态
干燥收缩与变形
自由水排出
颗粒表面水膜变薄 颗粒靠拢 直至与周围介质水分平衡 排除孔隙水
G I ( 0.2) M a b F Z L H
G—干燥排出水份的质量,kg; F—坯体受辐射表面积,m2; Z—干燥时间,h; I—辐射强度,w/m2;
β—坯体对辐射线的吸收能力; L—辐射距离,cm。
辐射干燥的优点:
能保证坯体清洁; 设备结构简单,易于实现自动化控制; 干燥速度较快;
干燥过程
外扩散--表面蒸发。 内扩散--表面水分蒸发后,坯体内部 的水分移动分为湿传导和热湿传导。
湿传导--∵水分梯度,∴水分移动 热湿传导--∵温度梯度,∴水分移动
加热阶段(升速阶段):坯体表面被加 热升温,水分不断蒸发,直到表面温度 达到干燥介质的湿球温度,坯体吸收的 热量与蒸发水分所消耗的热量达到动态 平衡,则干燥进入等速阶段。 由于升速阶段时间很短,因此排出水 量不多。
影响干燥速度的因素
1、影响内扩散的因素
组成坯体物料的性质:粗颗粒、瘠性料 量多时,毛细管粗、内扩散阻力小而利于 内扩散速度的提高。 生坯温度:温度升高,水的粘度降低, 表面张力降低,内扩散阻力减小。采取措 施使坯体温度梯度与湿度梯度方向一致。
陶瓷坯体的干燥-精讲课件
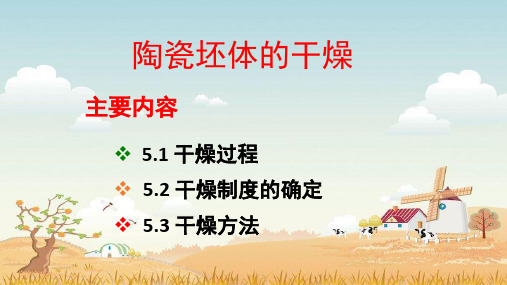
• 举例:“陶瓷砖”按吸水率可分为五大类:
GB/T4100.1-1999 干压陶瓷砖—第1部分 瓷质砖 GB/T4100.2-1999 干压陶瓷砖—第2部分 炻瓷砖 GB/T4100.3-1999 干压陶瓷砖—第3部分 细炻砖 GB/T4100.4-1999 干压陶瓷砖—第4部分 炻质砖 GB/T4100.5-1999 干压陶瓷砖—第5部分 陶质砖
第八章 显微结构与性质
第九章 粘结、修坯与施釉
第十章 烧成与窑具
第十一章 陶瓷装饰
▪ 以材料性质─结构─工艺之间的关系为纲,阐明材 料的组成,结构与性能的内在联系;讨论工艺方法 对产品性能的影响;将技术基础的有关原理与生产 工艺,性能控制融合在一起。
五 陶瓷的发展历史
四个时期
✓无釉陶器时期 ✓原始瓷器时期 ✓透明釉时期 ✓ 半透明胎时期
5.1 干燥过程
坯体干燥性能
3) 吸附阳离子的种类和数量 Na+ > Ca2+ >Ba2+ >H+ >Al3+ ——>气孔率提高 吸附离子数量多则强度提高 吸附Na+ ,泥料干后强度最高(粘土颗粒平行排列)
4) 成型方法 可塑:压力提高,有序排列颗粒较多,强度提高 注浆:泥浆胶溶程度完全, 颗粒面-面排列,强度
5.1 干燥过程
坯体干燥性能
2、影响干坯强度和气孔率的因素 1) 原料的组成和矿物组成 可塑性提高,干后强度提高 颗粒形状和堆积方式决定干坯强度与气孔率 高岭土:边——面堆积,气孔率高, 渗透性好 伊利石:面——面堆积,气孔率低, 渗透性低 致密坯体——抗开裂性能好 2) 坯料细度 细度提高,晶片越薄则干后强度提高
类别 种类
工艺陶瓷的生产工艺
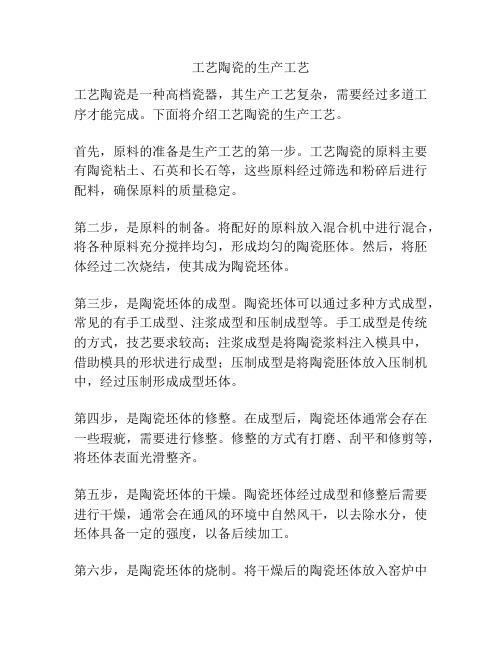
工艺陶瓷的生产工艺工艺陶瓷是一种高档瓷器,其生产工艺复杂,需要经过多道工序才能完成。
下面将介绍工艺陶瓷的生产工艺。
首先,原料的准备是生产工艺的第一步。
工艺陶瓷的原料主要有陶瓷粘土、石英和长石等,这些原料经过筛选和粉碎后进行配料,确保原料的质量稳定。
第二步,是原料的制备。
将配好的原料放入混合机中进行混合,将各种原料充分搅拌均匀,形成均匀的陶瓷胚体。
然后,将胚体经过二次烧结,使其成为陶瓷坯体。
第三步,是陶瓷坯体的成型。
陶瓷坯体可以通过多种方式成型,常见的有手工成型、注浆成型和压制成型等。
手工成型是传统的方式,技艺要求较高;注浆成型是将陶瓷浆料注入模具中,借助模具的形状进行成型;压制成型是将陶瓷胚体放入压制机中,经过压制形成成型坯体。
第四步,是陶瓷坯体的修整。
在成型后,陶瓷坯体通常会存在一些瑕疵,需要进行修整。
修整的方式有打磨、刮平和修剪等,将坯体表面光滑整齐。
第五步,是陶瓷坯体的干燥。
陶瓷坯体经过成型和修整后需要进行干燥,通常会在通风的环境中自然风干,以去除水分,使坯体具备一定的强度,以备后续加工。
第六步,是陶瓷坯体的烧制。
将干燥后的陶瓷坯体放入窑炉中进行烧制,烧制的温度可达到数百度甚至更高。
烧制的目的是将陶瓷坯体中的水分和有机物烧掉,使其形成致密的结构,并且提高陶瓷的硬度和耐磨性。
第七步,是陶瓷品的涂釉。
烧制后的陶瓷坯体通常呈白色,没有光泽。
为了增加陶瓷的美观度和表面光洁度,需要对其进行涂釉。
涂釉的方式有浸泡、刷涂和喷涂等,涂釉会形成一层玻璃状的保护层,使陶瓷更加光滑耐用。
最后一步,是陶瓷品的装饰和包装。
对于工艺陶瓷来说,装饰是非常重要的环节。
装饰包括刻花、彩绘和镶嵌等,使得陶瓷品更加精美。
最后,将陶瓷产品进行包装,以保护其完整性,并方便运输和销售。
综上所述,工艺陶瓷的生产工艺包括原料的准备、原料的制备、陶瓷坯体的成型、陶瓷坯体的修整、陶瓷坯体的干燥、陶瓷坯体的烧制、陶瓷品的涂釉和陶瓷品的装饰和包装等步骤。
陶瓷坯体干燥过程与变形开裂的原因
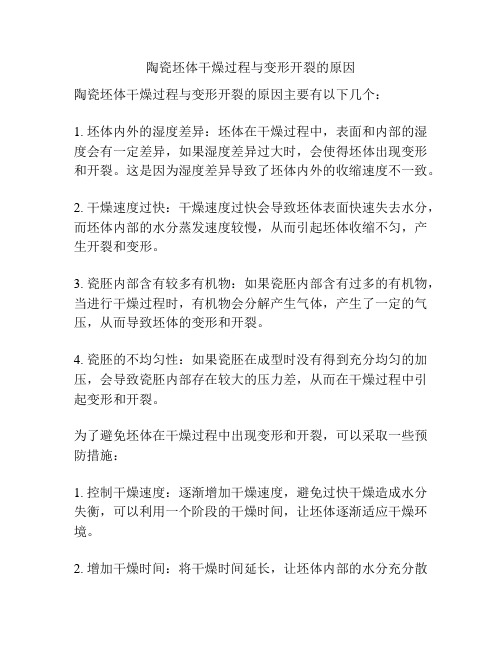
陶瓷坯体干燥过程与变形开裂的原因
陶瓷坯体干燥过程与变形开裂的原因主要有以下几个:
1. 坯体内外的湿度差异:坯体在干燥过程中,表面和内部的湿度会有一定差异,如果湿度差异过大时,会使得坯体出现变形和开裂。
这是因为湿度差异导致了坯体内外的收缩速度不一致。
2. 干燥速度过快:干燥速度过快会导致坯体表面快速失去水分,而坯体内部的水分蒸发速度较慢,从而引起坯体收缩不匀,产生开裂和变形。
3. 瓷胚内部含有较多有机物:如果瓷胚内部含有过多的有机物,当进行干燥过程时,有机物会分解产生气体,产生了一定的气压,从而导致坯体的变形和开裂。
4. 瓷胚的不均匀性:如果瓷胚在成型时没有得到充分均匀的加压,会导致瓷胚内部存在较大的压力差,从而在干燥过程中引起变形和开裂。
为了避免坯体在干燥过程中出现变形和开裂,可以采取一些预防措施:
1. 控制干燥速度:逐渐增加干燥速度,避免过快干燥造成水分失衡,可以利用一个阶段的干燥时间,让坯体逐渐适应干燥环境。
2. 增加干燥时间:将干燥时间延长,让坯体内部的水分充分散
发,减小湿度差异。
3. 控制环境湿度:控制好干燥室的湿度,避免湿度变化较大。
4. 控制坯体成型质量:保证坯体成型时的均匀性,提高坯体的抗变形能力。
- 1、下载文档前请自行甄别文档内容的完整性,平台不提供额外的编辑、内容补充、找答案等附加服务。
- 2、"仅部分预览"的文档,不可在线预览部分如存在完整性等问题,可反馈申请退款(可完整预览的文档不适用该条件!)。
- 3、如文档侵犯您的权益,请联系客服反馈,我们会尽快为您处理(人工客服工作时间:9:00-18:30)。
特点:微波对良导体能够产生全反射(金属),对不良导体
则部分反射,大部分吸收。微波干燥器外壳以及防护板全部 采用金属材料制成。微波干燥快速安全。 资料报道:碗盘类制品热空气干燥需要几十分钟,微波干燥
只需要3分钟就能完成。英国的微波-真空干燥技术1.5分钟
即可完成,大大延长了石膏模具的寿命。
23
4.3 红外干燥 远红外波长 2.5~1000um 近红外波长 0.75~2.5um 根据水分子对红外线的吸收特性,通常选择的干燥波长为 2.5~15um的远红外线。 1)远红外反射器 基体、辐射涂层、热源、保温装置部分构成。 基体:金属(钢、铝)、陶瓷(碳化硅、锆英石质耐火材料) 辐射层:全波涂料2.5~15(SiC、-Fe2O3、 -Fe2O3 为主体) 长波涂料6um以上(锆钛系、锆英石系) 短波涂料3.5um以下(富含SiO2、半导体氧化钛TiO1.9) 采用涂刷粘结、等离子喷涂和复合烧结的方法与基体结合。
9
干燥介质的种类 温度、湿度, 影响速度的参数 流量、流速等 坯体的性质
2)坯料的颗粒组成和矿物组成 粗颗粒,瘠性料,毛细管粗扩散阻力小有利于水分的扩散。
3)生坯的温度以及内外湿度差 温度高,水分粘度小、表面张力小有利于扩散。
湿度差大,湿扩散速度快。
1.2 影响外扩散的因素 表面水分汽化,向介质扩散。(表面水蒸气分压与介质分压差) 相关因素:干燥介质、生坯的温度; 干燥介质的流速、方向。 1.3 其它因素 1)干燥方式; 2)坯体厚度和形状
注意:1)B点称为临界点,转折点(阶段、收缩)后进入干燥
安全状态。 2)C点平衡状态点,标志着干燥结束。但含水率不为零。
3)“返潮”问题。
3. 干燥收缩与变形
内应力大于塑性状态屈服值时 变形 内应力大于或塑性状态的破裂破裂值或弹性状态抗拉强度时 开裂
7
3.2 影响坯体收缩变形的主要因素
1)坯体中粘土的性能 细 吸附水膜厚 粗细 可塑性好 多少 分布 收缩变形大
等静压法
自由水 坯体中水分的种类 吸附水
1%~3%
(通过干燥排除)
化学结合水
干燥的目的:排除坯体中的水分,同时赋予坯体一定的干燥 强度,满足搬运以及后续工序(修坯、粘结、施釉)的要求。
3
2. 干燥过程 坯体干燥过程四个阶段示意图
升速阶段 等速阶段 降速阶段 平衡阶段
1 A 2 3 B
介质温度
O
1—坯体含水率 2—干燥速度
3.1 干燥制度不合理:温度、湿度、流速和方向控制不当。 干燥太快;介质湿度太大引起水分冷凝于坯体上。
3.2 坯体放置不平衡或放置方法不当局部收缩阻力太大。
4. 器型设计不合理:结构复杂、薄厚不均匀。
1- 2- 3- 4 1-口沿 2-撑口泥 3-腹部 4-底肩 5-底心
5
28
29
作业 1.常见注浆成型的方法有哪些?
可见光
0.76~0.4
近红外线
5.6~0.76
远红外线
1000~5.6
微波
无线电波
107~103 1010~107
干燥4.1 高频干燥 电磁波频率在107HZ附近,属于超高频微波的范畴,辐射坯体 水分子吸收热量,达到干燥的目的。干燥质量好,成本高。
22
4.2 微波干燥
微波在陶瓷行业应用:微波烧结、微波干燥、微波检测 。 微波干燥常用频率:95525MHZ 245025MHZ
答:(1)机械冲击式粉碎(破碎);(2)球
磨粉碎;(3)行星式研磨;(4)振动粉碎; (5)行星式振动粉碎;(6)雷蒙磨;(7)气 流粉碎;(8)搅拌磨粉碎;(9)胶体磨粉碎 ;(10)高能球磨粉碎;(11)助磨剂。
32
化学法合成粉体的主要方法有哪些? 答:化学法合成粉体的方法分为固相法、液相
例如英国带式快速干燥器
5.2 工频电干燥、红外干燥与热风干燥相结合
大件注浆产品先用电热干燥除去大部分水分后,施釉后采用
红外干燥和热风干燥交替进行,除去剩余水分。
25
湿气排除 主送风机
燃烧器
燃烧室
红外辐射器
入坯
出坯
高强度喷嘴
热气再循环
热气分布器
英国带式快速干燥器
26
§4 – 4 干燥缺陷分析
变形和开裂是最常见的干燥缺陷,本质是不均匀收缩引起 的内应力造成的。直接原因可能是以下几方面。 1. 配方设计和坯料制备的原因 1.1 坯料配方中塑性粘土太多、太少。 1.2 坯料细度太粗、太细。
泥浆含水率:30%~50% 造雾方式:压力式、气流式 热空气温度:400~600℃ 流体流动方式:逆流、顺流式 特点:工艺简单,生产效率高 产量大, 颗粒流动性好,坯体 强 度高,致密度高 。
18
1.6 热泵干燥 基本原理:高温热湿气体经过冷凝换热,排除水分后再加热 循环使用。 1.7 脉冲干燥
基本原理:墙地砖坯体输送的流动方向的两侧,脉冲利用 干热空气来干燥坯体。 2. 工频电干燥 基本原理:将坯体两端加交流电压(相当于并联进入电路),
法和气相法。 其中固相法包括热分解反应法、化合反应法 、氧化物还原法等; 液相法包括沉淀法、醇盐水解法、溶胶-凝 胶法、溶剂蒸发法、微乳液法、水热法; 气相法包括蒸发-凝聚法(PVD)和气相化学 反应法(CVD)
33
已知某厂坯的化学组成为:
SiO2 Al2O3 Fe2O3 CaO MgO K2O Na2 I . 合 O L 计
5
B C降速干燥阶段,表面温度—升高至介质温度。
干燥速度—逐渐减小至零,与介质达到平衡。
吸热—蒸发水分,提高坯体温度。 收缩—基本不收缩。
CD平衡阶段,坯体与介质达到平衡状态,干燥过程完成。
6
3、1收缩与变形的原因:
干燥 颗粒表面自由水膜变薄 颗粒之间靠近 发生收缩
坯料部分颗粒的取向性排列 收缩的各向异性 产生内应力
1.89 5.54 100
63.37 24.87 0.81
1.15
0.32
2.05
试求该坯的实验式?
34
1)换算为无烧失的坯料化学组成,计算各氧化物的质量 分数(%)
SiO2 质量% 67.09 Al2O3 Fe2O3 CaO MgO Na2O K2O 26.33 0.86 1.21 0.34 2.17 2.00
•将各氧化物按规定顺序排列,即得所求坯式: 0.0877K2O 0.1226 Na2O 0.0820CaO 0.0319 MgO
0.9795 Al2O3 0.02
1.3 坯料含水率太高,组分分布不均匀。
1.4 练泥和成形过程造成颗粒的定向排列从而导致不均匀应力。 2. 成形过程的原因
2.1 成形时泥料受力不均匀,造成致密度不一致,收缩不均匀。
2.2 模型吸水能力不均匀,造成不均匀收缩。 模型的不均匀干燥;模型制作、使用过程局部油污。
27
3. 干燥过程的原因
热源:电阻丝。辐射体温度高,辐射强度高。400~500℃最好。 24
2)红外干燥远特点:
A) 速度快,效率高。
B) 热效率高,节约能源,单位坯体能耗是近红外的1/2, 热空气干燥的1/3。
C) 设备小,造价低,占地面积小。
D) 干燥效果好, 5. 综合干燥 干燥方法特点结合干燥过程各阶段的特点
5.1 辐射干燥和热空气对流干燥相结合
11
带石膏模干燥时 温度不大于70℃,否则模型强度降低。
2.3 干燥介质的流速和流量 提高介质的流速和流量可以提高干燥速度。 注意防止变形、开裂。
12
§4– 3 干燥方法
1)热空气干燥 2)工频电干燥 3)直流电干燥 4)辐射干燥 5)综合干燥
13
1. 热空气干燥
室式干燥、隧道式干燥、喷雾干燥、链式干燥及热泵干燥。
常利用隧道窑余热与成形机、自动脱模机、修坯机配套 形成自动流水线。适应中、小件产品,热效率高。
国产链式干燥机比较落后。
16
1.4 辊道传送式干燥
近年来发展起来的一种与辊道窑一体(下层)的干燥方式。 热源:辊道窑余热或热风机供热。
特点:热效率高,干燥质量好,干燥后可直接入窑烧成。
17
1.5 喷雾干 燥
C
3—坯体表面温度
D
时间
4
干燥过程各阶段的特征: OA 升速干燥阶段,温度—逐渐升高至干燥介质湿球温度TA。 干燥速度—由零升至最大,蒸发表面水分。 吸热—蒸发水分,提高坯体温度。 收缩—很小。
A B等速干燥阶段,表面温度—不变,
干燥速度—保持衡定,内扩散速度等于外 扩散速度。 吸热—全部用于蒸发水分。 收缩—较大,相当于成份水分的体积。
1.1 室式干燥(室式烘房) 分类:固定坯架式;活动坯车式。
暖气式;热风式;温度湿度可调式。 特点:设备简单,造价低廉,热效率低,干燥周期长。
14
1.2 隧道式干燥
1—鼓分机 2—总进热风道
3—连通进热风道
4—支进热风道 5—干燥隧道 6—废气排除通道
7—排风机
15
1.3 链式干燥
修坯
脱模 成形
第四节 坯体的干燥
1
第四节 坯体的干燥
§4 – 1 干燥作用与干燥过程 §4 – 2 干燥制度的确定 §4 – 3 干燥方法 §4 – 4 干燥缺陷分析
2
§4– 1 干燥作用与干燥过程
1. 干燥的作用: 排除坯体中的水分
注浆法
坯体成形含水率 可塑法 压制法
30%~35%
15%~26% 3%~14%
10
3)干燥设备的结构以及坯体放置位置是否合理。
2. 干燥介质参数的确定 2.1介质温度: 1)坯体的大小、形状、厚度、组成、含水率 大件、复杂坯体 低温高湿高温低湿(临界点); 小件、简单坯体 高温低湿干燥。 2)热能的充分利用和设备的因素 介质温度太高,热效率低,传热设备使用寿命降低。 2.2 干燥介质的湿度 湿度太低,干燥太快,容易产生变形和开裂。 例如:大件的卫生瓷坯体,通常采用分段干燥方法。