陶瓷工艺学第八章坯体的干燥
第八章 干燥脱脂
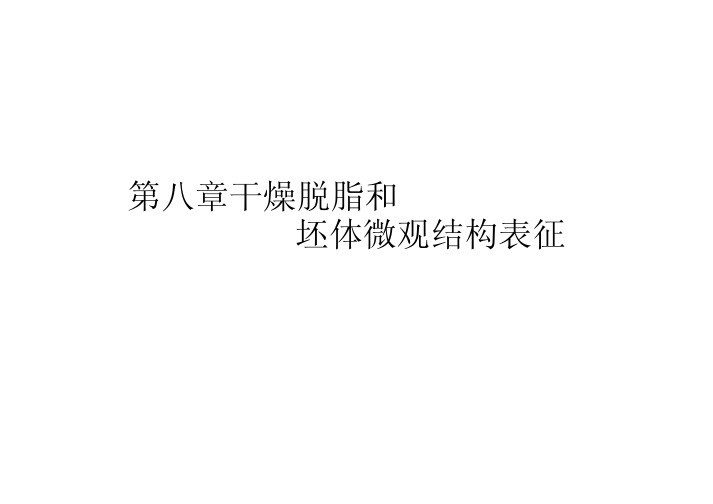
第二速降段(FRP2)
• 当气液界面进入到胚体内部,通往表面的液体流动消失,内部的水分 只有通过在内部蒸发后再扩散到表面,这标志着第二速降段(FRP2) 的开始 • 由于气液界面开始远离表面,胚体会因固体所收的压应力减少而发生 一些膨胀,对一个从一边干燥的平板,这会使其向已干燥的一面凸起
干燥的一面
颗粒层的干燥——沉积成环
• 这个沉积特性环的是由于毛细流 动引起。干燥中的点滴和底部的 颗粒之间的销连接确,可以使水 分保由内而外补充,从而保持持 续的蒸发。 • 开始时,边缘地区的液流固化形 成一个环。 • 随着干燥过程的继续,边缘区域 的液流达到了一种饱和状态,液流 带着粒子来到边缘地区,在饱和 的环和过饱和的悬浊液之间沉积。 Fig.8.1 稀释的胶状的颗粒在干燥过程中呈 • 如果想减少胚体的裂纹和扭曲, 现出明显的颗粒移动,导致沉积出一个环 干燥过程中水分分布运动很重要
湿润的一面
• 随着湿润的区域越来越薄,其中的收缩力会更有效的减小,造成更大 的拉力
水分分布和运动
• 要想避免胚体的变形和移动,研究水分的分布式很重要的
a. CRP
b.FRP1 & FRP2
干燥应力
• 对于一个平板,在它的平面方向上(xy面)固相之间的应力为:
σx =σy = p − p
P是液体之间的张力(负压),<p>是液体内的平均压力
精细陶瓷的干燥
• 精细陶瓷中,固相包含着很多刚性的微米级颗粒或微粒grain,在第五 章中所讨论的凝胶的干燥原则同样适应于精细陶瓷,但还有一些重要 的不同: 1. 在精细陶瓷中没有观察到像在聚合的凝胶中那样观测到很大的干燥 拉应力。线性收缩只有10%,远小于凝胶中的50%. 2. 陶瓷中的气孔也很大,所以渗透性更大,液体流动更容易,细毛细 血管压力。
陶瓷坯料干燥
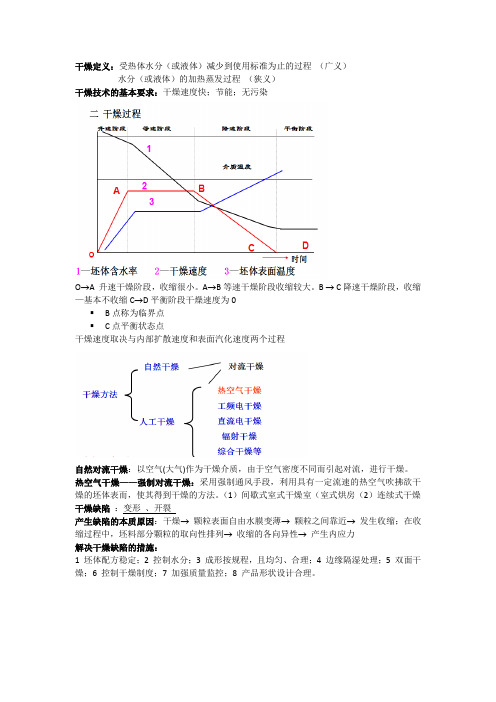
干燥定义:受热体水分(或液体)减少到使用标准为止的过程(广义)
水分(或液体)的加热蒸发过程(狭义)
干燥技术的基本要求:干燥速度快;节能;无污染
O→A 升速干燥阶段,收缩很小。
A→B等速干燥阶段收缩较大。
B → C降速干燥阶段,收缩—基本不收缩C→D平衡阶段干燥速度为0
▪B点称为临界点
▪C点平衡状态点
干燥速度取决与内部扩散速度和表面汽化速度两个过程
自然对流干燥:以空气(大气)作为干燥介质,由于空气密度不同而引起对流,进行干燥。
热空气干燥——强制对流干燥:采用强制通风手段,利用具有一定流速的热空气吹拂欲干燥的坯体表而,使其得到干燥的方法。
(1)间歇式室式干燥室(室式烘房(2)连续式干燥干燥缺陷:变形、开裂
产生缺陷的本质原因:干燥→颗粒表面自由水膜变薄→颗粒之间靠近→发生收缩;在收缩过程中,坯料部分颗粒的取向性排列→收缩的各向异性→产生内应力
解决干燥缺陷的措施:
1 坯体配方稳定;
2 控制水分;
3 成形按规程,且均匀、合理;
4 边缘隔湿处理;
5 双面干燥;
6 控制干燥制度;
7 加强质量监控;
8 产品形状设计合理。
第八章 坯体的干燥.
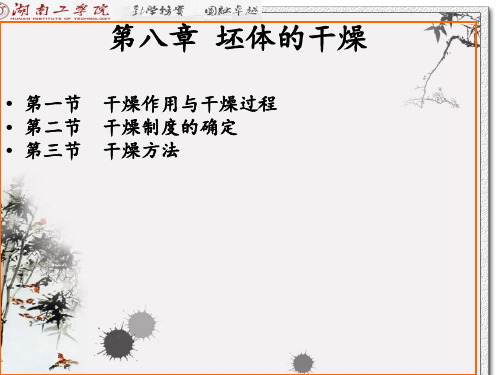
• 影响内扩散的因素: • 1.组成坯体物料的性质 • 2.生坯温度 • 3.坯体表面与内部的湿度差
2.影响外扩散的因素: 外扩散:坯体表面水分汽化,并通过水汽膜向外界扩
散的过程。 动力:坯体表面的水蒸气压与周围的水蒸气分压之差
影响因素:干燥介质及生坯表面的蒸气分压、干燥介 质及生坯表面的温度,干燥介质的流速和方向,生坯 表面粘滞气膜的厚度、热量的供给方式、干燥方法。
3. 其它影响因素 (1)干燥方式 (2)坯体的厚度和形状 (3)干燥器的结构及坯体在干燥器中的放置方式与位
置
二、干燥介质参数的确定
1.干燥介质的温度 (1)根据坯体组成、结构、尺寸、最终含水率等,确
定介质温度,以保证坯体均匀受热。 (2)考虑热效率问题 (3)模型、热源和干燥设备的限制 2.干燥介质的湿度
坯体单位时间、单位体积内
产生的热量与频率、电场强
度及坯体的介质损耗有关。
特点:
(1)均匀快速,热、湿传导方向一致; (2)具有选择性高; (3)热效率; (4)干燥设备体小、轻巧,便于自控 (5)具有微波辐射,需进行特殊防护 (6)设备费用高,耗电量大。
(三)红外干燥
是利用远红外辐射元件发出的远红外线为被加热物 体所吸收,直接转变为热能而达到加热干燥的方法。
第八章 坯体的干燥
• 第一节 干燥作用与干燥过程 • 第二节 干燥制度的确定 • 第三节 干燥方法
第一节 干燥作用与干燥过程
一、干燥作用
排除生坯水分的过程属于干燥过程。目的是提高生
坯强度,便于检查、修坯、搬运、施釉和烧成等。 二、干燥过程 1.升速干燥(0--A) 2.等速干燥阶段(A--B) 3.降速干燥阶段(B--C) 4.平衡阶段(C--D)
浅析陶瓷高湿坯体的干燥机理及模式

浅析陶瓷高湿坯体的干燥机理及模式技术创造第一生产力,随着现代科技的进步,陶瓷机械行业正发生着日新月异的变化。
陶机的发展给陶瓷生产带来了极大的便利,并革命性地提高了陶瓷的品质。
品质的提升又给陶机提出了更高的要求,两者之间的需求平衡不断被打破,才有了今天陶瓷及陶瓷机械行业一派繁荣的景象。
但繁荣背后也存在一些不足,如一些传统陶瓷产品的部分生产环节依旧延续着80年代的生产工艺,一些新兴产品因某个生产环节脱钩而无法保证其品质。
目前,陶瓷高湿坯体的干燥情况是陶瓷行业需要共同探讨的问题之一。
2 陶瓷高湿坯体的干燥发展状况及出现的问题卫生洁具干燥成形后需放置5~10天,此时含水率约为8%~10%,然后再放入烘干房内1~2天,此时制品已完全干燥。
整个过程耗费了大量的时间与人力,同时这种干燥方式受气候的影响较大,很难保证产品的品质。
其它的高湿坯体,如新兴起的环保建材陶板、传统的西瓦及耐火材料硼板坩锅等干燥周期也较长。
如今在多年从业经验的基础上以及引入国外同行的先进理念,在高湿坯的干燥难题上终于有所突破。
高湿坯体在快速干燥过程中出现的各种开裂和变形等问题。
其主要原因为:干燥过快导致产品内外的含水量相差较大,造成坯体内外收缩不一致,从而导致坯体变形、开裂。
其根本原因是:坯体含水量对坯体体积的影响。
一般地,坯体含水量对体积的影响在一个定量前后相差很大,我们称这个含水量为临界含水量,其值为8%左右(受坯体工艺配方影响)。
如果坯体含水量小于8%时,含水量的变化对体积的影响较小。
因此,在快速干燥过程中合理地控制干燥速度就不易出现坯体变形、开裂等缺陷。
例如,目前墙地砖的成形水分都控制在7%左右,其干燥周期可控制范围为30~90min(坏体越厚需时越长)。
因此,当坯体含水量低于8%以后,可以采用一些现有的干燥手段进行快速干燥。
当坯体中的水分处于临界含水量时,坯体内外的含水量相差较大,对坯体体积的影响较大,内外体积变化不一,易致坯体变形、开裂。
陶瓷工艺学第八章坯体的干燥
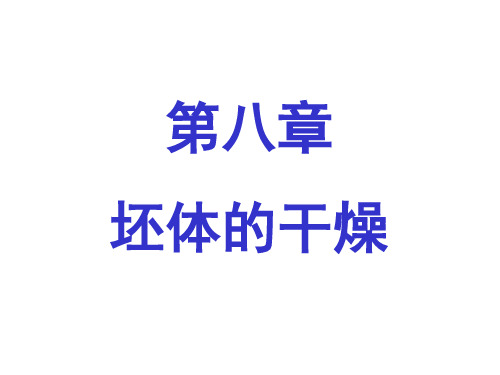
2.3 干燥介质的流速和流量
提高介质的流速和流量可以提高干燥速度。
注意防止变形、开裂。
第三节 干燥方法
1)热空气干燥
2)工频电干燥
3)直流电干燥
4)辐射干燥
5)综合干燥
1. 热空气干燥
湿气排除 燃烧室 燃烧器 主送风机
红外辐射器
入坯
出坯
高强度喷嘴
热气再循环
热气分布器
英国带式快速干燥器
干燥缺陷分析
变形和开裂是最常见的干燥缺陷,本质是不均匀收缩引起
的内应力造成的。直接原因可能是以下几方面。 1. 配方设计和坯料制备的原因 1.1 坯料配方中塑性粘土太多、太少。 1.2 坯料细度太粗、太细。 1.3 坯料含水率太高,组分分布不均匀。 1.4 练泥和成形过程造成颗粒的定向排列从而导致不均匀应力。 2. 成型过程的原因 2.1 成形时泥料受力不均匀,造成致密度不一致,收缩不均匀。 2.2 模型吸水能力不均匀,造成不均匀收缩。 模型的不均匀干燥;模型制作、使用过程局部油污。
3. 干燥收缩与变形
3.1收缩与变形的原因
干燥 颗粒表面自由水膜变薄 颗粒之间靠近 发
生收缩 坯料部分颗粒的取向性排列 收缩的各向异 性 产生内应力
内应力大于塑性状态屈服值时 变形
内应力大于或塑性状态的破裂破裂值或弹性状态抗 拉强度时 开裂
3.2 影响坯体收缩变形的主要因素
1)坯体中粘土性能 (颗粒 粗细 ,多少 ,分布 ) 细 , 吸附水膜厚,可塑性好,收缩变形大。 2)粘土吸附阳离子的种类 3)坯体的含水率 含水率大,收缩大,变形开裂的可能性大。 4)坯体的成形方法 与含水率的关系 5)坯体的形状 形状复杂、 薄厚不匀容易变形开裂。
实验 陶瓷坯体的干压成形
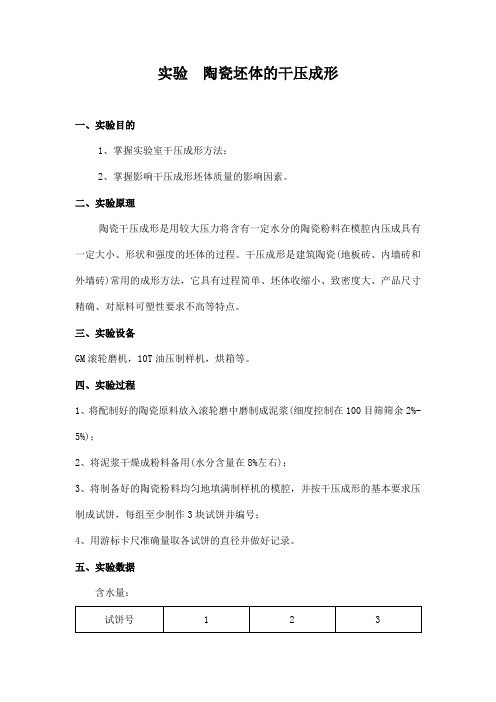
实验陶瓷坯体的干压成形
一、实验目的
1、掌握实验室干压成形方法;
2、掌握影响干压成形坯体质量的影响因素。
二、实验原理
陶瓷干压成形是用较大压力将含有一定水分的陶瓷粉料在模腔内压成具有一定大小、形状和强度的坯体的过程。
干压成形是建筑陶瓷(地板砖、内墙砖和外墙砖)常用的成形方法,它具有过程简单、坯体收缩小、致密度大、产品尺寸精确、对原料可塑性要求不高等特点。
三、实验设备
GM滚轮磨机,10T油压制样机,烘箱等。
四、实验过程
1、将配制好的陶瓷原料放入滚轮磨中磨制成泥浆(细度控制在100目筛筛余2%-5%);
2、将泥浆干燥成粉料备用(水分含量在8%左右);
3、将制备好的陶瓷粉料均匀地填满制样机的模腔,并按干压成形的基本要求压制成试饼,每组至少制作3块试饼并编号;
4、用游标卡尺准确量取各试饼的直径并做好记录。
五、实验数据
含水量:
六、实验分析
讨论分析影响陶瓷干压成形坯体性质的因素。
陶瓷工艺学_景德镇陶瓷大学中国大学mooc课后章节答案期末考试题库2023年

陶瓷工艺学_景德镇陶瓷大学中国大学mooc课后章节答案期末考试题库2023年1.坯体在干燥时发生收缩最重要的阶段是:()答案:等速干燥阶段2.注浆成型过程中:()答案:以上均不是3.元代出现双层结构的镂空高足杯,清代又出现外层镂空、内层绘画的转心瓶使用的是()装饰技术答案:镂空4.渗花彩料由()等材料,按一定的比例配制而成。
答案:助渗剂色剂稀释剂增稠剂5.针孔缺陷可由以下几种可能原因引起。
()答案:坯釉配方烧成成型施釉6.变形产生原因与()等有关答案:烧成制度器形设计坯釉配方7.烧成制度包括()答案:气氛制度压力制度温度制度8.施釉的目的在于()答案:改善坯体的表面性能提高产品的使用性能增加产品的美感9.坯体的总收缩率等于干燥收缩率加上烧成收缩率。
答案:错误10.煅烧后的合成颜料,先要破碎,然后经稀氢氧化钠碱洗答案:错误11.瓷器是陶瓷制品中,胎体玻化或部分玻化、吸水率不大于3%、有一定透光性、断面细腻呈贝壳状或石状、敲击声清脆的一类制品答案:正确12.釉粘度过大,易产生釉面不光滑和橘釉等缺陷,釉粘度过小,易产生流釉、堆釉和干釉等缺陷。
答案:正确13.对于注浆料,宜多加入膨润土,防止稠化,有利于注浆。
答案:错误14.陶器的吸水率一般>3%,不透光,未玻化或玻化程度差,结构不致密,断面粗糙,敲击声沉浊答案:正确15.传统陶瓷的原材料包括天然矿物,如粘土、石英、长石等。
根据使用领域不同,可分为日用陶瓷、建筑卫生陶瓷、化工陶瓷、化学瓷、电瓷及其他工业用陶瓷。
答案: 正确。
陶瓷工艺学7第八章陶瓷的烧成

•MgCO3.CaCO3 → CaO+MgO+CO2 ↑ 730~950 ℃
•FeS2+O2 → Fe+SO2 ↑
•4FeS+7O2 → 2Fe2O3+4SO2 ↑
350-450 ℃
500-800 ℃
一、坯体在烧制过程中的物理变化
2、氧化分解与晶型转变期(300~950 ℃ ) (4)石英的晶型转变和少量液相的形成
一、坯体在烧制过程中的物理变化
• 坯体的烧制是一个由量变到质变物理变化和化学变化交 错进行的过程。可以将日用陶瓷的烧成过程分为四个阶段。
一、坯体在烧制过程中的物理变化
•1、坯体水分蒸发期(室温~300 ℃ ) •坯体在这一阶段主要任务是排除干燥后的残余水。随着水 分的排出,固体颗粒紧密靠拢,伴随着少量收缩。但这种收 缩不能完全填补水分排除后所遗留的空隙。控制坯体入窑水 分是本阶段快速升温的关键。一般日用瓷坯体入窑水分控制 在2%以下。因为温度高于120 ℃时坯体内部的水分发生强烈 汽化。蒸汽压力超过坯体的抗张强度极限时,造成制品开裂, 对于厚壁制品尤为突出。 •本阶段要加强通风,目的是使被水气饱和的烟气得到及时排 除,不致因其温度继续下降到露点而析出液态水,凝聚在制 品表面造成“水迹”或开裂等缺陷。
•瓷石 450-700 ℃ •粘土矿物排除结构水也与升温速度有关。随着升温速度的加快残 留结构水的排除向高温推移,甚至要到1000 ℃以上才能完成。
一、坯体在烧制过程中的物理变化
2、氧化分解与晶型转变期(300~950 ℃ )
•(2)碳酸盐的分解 •CaCO3→CaO+CO2 ↑ •MgCO3 → MgO+CO2 ↑ •4FeCO3 → 2Fe2O3+3CO2 ↑ •(3)碳素、有机物和硫化物的氧化 •氧化反应和反应温度如下: •C有机物+O2 →CO2 ↑ • C碳素+O2 → CO2 ↑ 350 ℃以上 600 ℃ 850~1000 ℃ 500~850 ℃ 800~1000 ℃
陶瓷坯体的干燥过程

陶瓷坯体的干燥过程在对流干燥过程中介质与坯体之间既有热交换,又有质交换,可以将其分为下面三个既同时进行又相互联系的过程:(1)传热过程干燥介质的热量以对流方式传给坯体表面,又以传导方式从表面传向坯休内部。
坯体表面的水分得到热量而汽化,由液态变为气态。
(2)外扩散过程坯体表面产生的水蒸汽,通过层流底层,在浓度差的作用下,以扩散方式由坯体表面向干燥介质中移动。
(3)内扩散过程由于湿坯体表面水分蒸发,使其内部产生湿度梯度,促使水分由浓度较高的内层向浓度较低的外层扩散,称湿传导或湿扩散。
当坯体中存在有温度梯度时,也会引起水分的扩散移动,移动的方向指向温度降低的方向,即与温度梯度的指向相反,这种单由温度梯度引起的水分移动称热湿传导或称热扩散。
在实际的干燥过程中,水分的内扩散过程一般包括湿传导和热湿传导的共同作用。
(二)坯体干燥过程的特点干燥过程依次分为如下几个阶段;(1)加热阶段由于干燥介质在单位时间内传给坯体表面的热量大于表面水分蒸发所消耗的热量,因此受热表面温度逐步升高,直至等于干燥介质的湿球温度,即到达图中A点,此时表面获得热与蒸发耗热达到动平衡,温度不变。
此阶段坯体水分减少,干燥速率增加。
(2)等速干燥阶段本阶段仍继续进行自由水排除。
由于坯体含水分较高,表面蒸发了多少水量,内部就能补充多少水量,即坯体内部水分移动速度(内扩散速度)等于表面水分蒸发速度,亦等于外扩散速度,所以表面维持潮湿状态。
另外,介质传给坯体表面的热量等于水分汽化所需之热量,所以坯体表面温度不变,等于介质的湿球温度。
坯体表面的水蒸汽分压等于表面温度下的饱和水蒸汽分压,干燥速率恒定,故称等速干燥阶段。
因本阶段是排除自由水,故坯体会产生体积收缩,收缩量与水分降低量成直线关系,若操作不当,干燥过快,坯体极易变形、开裂,造成干燥废品。
等速干燥阶段结束时,物料水分降低到临界值,K点即为临界水分点。
此时尽管物料内部仍是自由水,但在表面一薄层内已开始出现大气吸附水。
青岛科技大学陶瓷课件8-2干燥
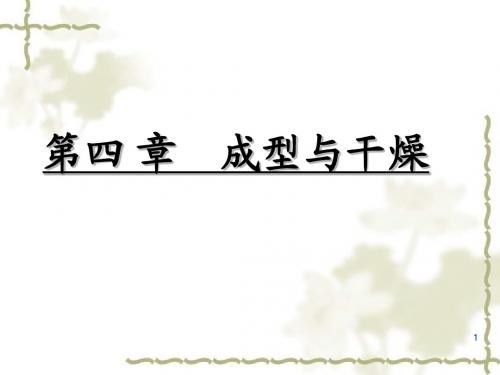
23
主要特点:
(1)均匀快速。 热、湿传导方向一致 (2)具有选择性 (3)热效率高
(4)干燥设备体小、轻巧,便于自控
(5)具有微波辐射,需进行特殊防护。
(6)设备费用高,耗电量大。
24
5. 远红外干燥
(1)原理 是利用远红外辐射元件发出的远红外线为 被加热物体所吸收,直接转变为热能而达 到加热干燥的方法。
6
4.3.2 坯体干燥过程
介质与坯体之间既有热交换,又有质交换,可以将 其分为下面三个既同时进行又相互联系的过程: (1)传热过程 干燥介质的热量以对流方式传给坯体表面,又以 传导方式从表面传向坯休内部。
(2)外扩散过程(表面蒸发) 坯体表面产生的水蒸汽,在浓度差的作用 下,以扩散方式由坯体表面向干燥介质中移动。
25
水是红外敏感物质,在红外线的作用下水分 子的键长和键角振动,偶极矩反复改变,吸 收的能量与偶极矩变化的平方成正比,干燥 过程主要是由水分子大量吸收辐射能,因此 效率很高。
水分的红外吸收光谱图
26
(3)远红外干燥的优点 干燥速度快,生产效率高 辐射与干燥几乎同时开始,无明显的预热阶 段。 实际的例子很多,如:原用80℃热风干燥要2 h时的生坯,改用远红外干燥,生坯温度约 80℃,仅需10 min。 又如卫生器生坯在通风的厂房里要干燥18天, 改用近红外干燥仅用1天,再改用远红外干燥, 时间和能量消耗又都减少1/2左右。
(1)条件 坯体干燥过程中形成的水分梯度使坯体出现 不均匀的收缩,从而产生应力。 当应力大于呈塑性状态的坯体强度时,就会引 起开裂。 干燥制度或坯体造型不妥等情况。
13
(2)开裂类型 整体开裂 边缘开裂 中心开裂
表面裂纹 结构裂纹
精选陶瓷生产技术及设备之坯体的干燥培训课件

0 ①——坯体含水率
②——干燥速度 ③——坯体表面温度
即在干燥后期使坯体接触高温、低湿的热风。
F
K 平衡水分
C
时间,t
4.3 干燥方法及设备
● 干燥方法分类:
热风干燥(对流干燥) 电干燥——工频电干燥、高频电干燥 辐射干燥—— 微波干燥、远红外干燥
4.3 干燥方法及设备
一、热风干燥(对流干燥)
根据干燥器的结构不同,对流式干燥器有:室式、隧道式、 链式、推板式干燥器等几种形式。
4.3 干燥方法与设备
三、辐射干燥
(二)远红外干燥
水分子也是红外敏感物质。当入射的红外线频率与含水物质的固有 振动频率一致时,就会大量吸收红外线,从而改变和加剧其极性分 子的振动与偶极矩的转动,使物体温度升高。
远红外干燥就是利用远红外辐射器发出的远红外线为湿坯体所吸收, 直接转变为热能而使生坯干燥的方法。 水分在远红外区域有很宽的吸收带,因此远红外的干燥效果要比近红 外干燥好的多。
2. 浇(淋)釉
● 概念。适用于 墙地砖、圆形浅底 盘(碟、碗)类制 品。
5.1 施釉方法与设备
一、传统施釉方法
2. 浇(淋)釉
● 特点:施釉效率高;釉 面光滑平整、少有波纹。
● 影响釉层厚度及均匀性 的因素
--坯体含水率 --釉浆浓度 --施釉时间(传送带速)
钟罩式浇釉法示意图
5.1 施釉方法与设备
2. 坯体的形状、大小及厚薄。 3. 干燥强度——干燥介质(热风)的温度、湿度、流速及流量。 4. 坯体的受热面积(与热风接触面积)。 5. 干燥平衡水分的高低。 6. 干燥器的结构与热工性能。
4.2 干燥制度的制定
二、影响坯体干燥质量的因素
● 坯体干燥质量的衡量标准:各部位干燥比较均匀,平衡水分 (干燥残余水分)达到要求,无变形或开裂现象。
陶瓷坯体的干燥-精讲课件
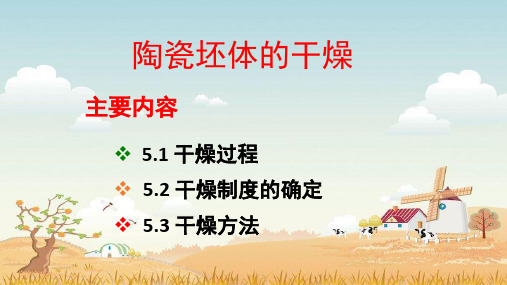
• 举例:“陶瓷砖”按吸水率可分为五大类:
GB/T4100.1-1999 干压陶瓷砖—第1部分 瓷质砖 GB/T4100.2-1999 干压陶瓷砖—第2部分 炻瓷砖 GB/T4100.3-1999 干压陶瓷砖—第3部分 细炻砖 GB/T4100.4-1999 干压陶瓷砖—第4部分 炻质砖 GB/T4100.5-1999 干压陶瓷砖—第5部分 陶质砖
第八章 显微结构与性质
第九章 粘结、修坯与施釉
第十章 烧成与窑具
第十一章 陶瓷装饰
▪ 以材料性质─结构─工艺之间的关系为纲,阐明材 料的组成,结构与性能的内在联系;讨论工艺方法 对产品性能的影响;将技术基础的有关原理与生产 工艺,性能控制融合在一起。
五 陶瓷的发展历史
四个时期
✓无釉陶器时期 ✓原始瓷器时期 ✓透明釉时期 ✓ 半透明胎时期
5.1 干燥过程
坯体干燥性能
3) 吸附阳离子的种类和数量 Na+ > Ca2+ >Ba2+ >H+ >Al3+ ——>气孔率提高 吸附离子数量多则强度提高 吸附Na+ ,泥料干后强度最高(粘土颗粒平行排列)
4) 成型方法 可塑:压力提高,有序排列颗粒较多,强度提高 注浆:泥浆胶溶程度完全, 颗粒面-面排列,强度
5.1 干燥过程
坯体干燥性能
2、影响干坯强度和气孔率的因素 1) 原料的组成和矿物组成 可塑性提高,干后强度提高 颗粒形状和堆积方式决定干坯强度与气孔率 高岭土:边——面堆积,气孔率高, 渗透性好 伊利石:面——面堆积,气孔率低, 渗透性低 致密坯体——抗开裂性能好 2) 坯料细度 细度提高,晶片越薄则干后强度提高
类别 种类
陶瓷坯体干燥过程与变形开裂的原因
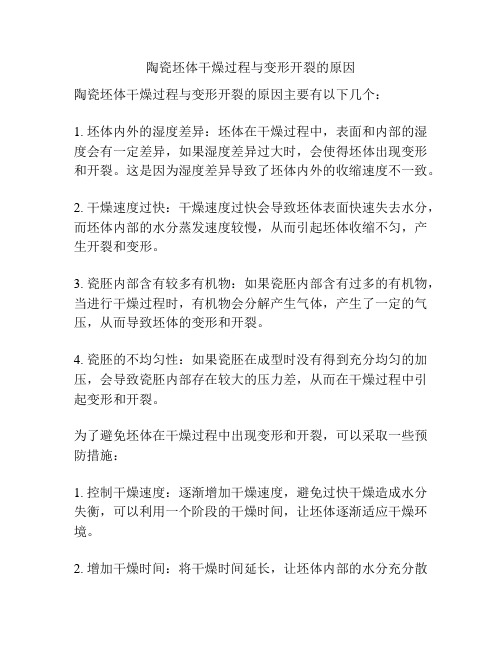
陶瓷坯体干燥过程与变形开裂的原因
陶瓷坯体干燥过程与变形开裂的原因主要有以下几个:
1. 坯体内外的湿度差异:坯体在干燥过程中,表面和内部的湿度会有一定差异,如果湿度差异过大时,会使得坯体出现变形和开裂。
这是因为湿度差异导致了坯体内外的收缩速度不一致。
2. 干燥速度过快:干燥速度过快会导致坯体表面快速失去水分,而坯体内部的水分蒸发速度较慢,从而引起坯体收缩不匀,产生开裂和变形。
3. 瓷胚内部含有较多有机物:如果瓷胚内部含有过多的有机物,当进行干燥过程时,有机物会分解产生气体,产生了一定的气压,从而导致坯体的变形和开裂。
4. 瓷胚的不均匀性:如果瓷胚在成型时没有得到充分均匀的加压,会导致瓷胚内部存在较大的压力差,从而在干燥过程中引起变形和开裂。
为了避免坯体在干燥过程中出现变形和开裂,可以采取一些预防措施:
1. 控制干燥速度:逐渐增加干燥速度,避免过快干燥造成水分失衡,可以利用一个阶段的干燥时间,让坯体逐渐适应干燥环境。
2. 增加干燥时间:将干燥时间延长,让坯体内部的水分充分散
发,减小湿度差异。
3. 控制环境湿度:控制好干燥室的湿度,避免湿度变化较大。
4. 控制坯体成型质量:保证坯体成型时的均匀性,提高坯体的抗变形能力。
- 1、下载文档前请自行甄别文档内容的完整性,平台不提供额外的编辑、内容补充、找答案等附加服务。
- 2、"仅部分预览"的文档,不可在线预览部分如存在完整性等问题,可反馈申请退款(可完整预览的文档不适用该条件!)。
- 3、如文档侵犯您的权益,请联系客服反馈,我们会尽快为您处理(人工客服工作时间:9:00-18:30)。
B C 降速干燥阶段 表面温度—升高至介质温度。 坯体温度 干燥速度—逐渐减小至零, 与介质达到平衡。 吸热—蒸发水分,提高坯体温度。 坯体含水率 收缩—基本不收缩。 干燥速度 CD 平衡阶段 坯体与介质达到平衡状态,干燥过程完成。 注意:1)B点称为临界点,此后进入干燥安全状态。 2)C点平衡状态点,标志着干燥结束。但含水 率不为零。 3)“返潮”问题。
2)坯料的颗粒组成和矿物组成 粗颗粒,瘠性料,毛细管粗扩散阻力小有利于水分的 扩散。 3)生坯的温度以及内外湿度差 温度高,水分粘度小、表面张力小有利于扩散。 湿度差大,湿扩散速度快。 1.2 影响外扩散的因素 表面水分汽化,向介质扩散。 相关因素:干燥介质、生坯温度; 干燥介质的流速、 方向。 1.3 其它因素 1)干燥方式; 2)坯体厚度和形状 3)干燥设备的结构以及坯体放置位置是否合理。
第八章 坯体的干燥
第一节 干燥的作用与干燥过程
第二节 干燥制度的确定
第三节 干燥方法
第一节 干燥的作用与干燥过程
1. 干燥的作用: 坯体成形含水率 排除坯体中的水分 注浆法 可塑法 压制法 等静压法 30%~35% 15%~26% 3%~14% 1%~3%
坯体中水分的种类
自由水 (通过干燥排除) 化学结合水 吸附水
2.2 干燥介质的湿度 湿度太低,干燥太快,容易产生变形和开裂。 例如:大件的卫生瓷坯体,通常采用分段干燥方法。
2.3 干燥介质的流速和流量
提高介质的流速和流量可以提高干燥速度。
注意防止变形、开裂。
第三节 干燥方法
1)热空气干燥
2)工频电干燥
3)直流电干燥
4)辐射干燥
5)综合干燥
1. 热空气干燥
1.3 链式干燥
修坯 脱模
成形
常利用隧道窑余热与成形机、自动脱模机、修坯 机配套 形成自动流水线。适应中、小件产品,热效率 高。 国产链式干燥机比较落后。
1.4 辊道传送式干燥
一种与辊道窑一体(下层)的干燥方式。 热源:辊道窑余热或热风机供热。 特点:热效率高,干燥质量好。 1.5 喷雾干 燥
泥浆含水率:30%~50% 造雾方式:压力式、气流式 热空气温度:400~600℃ 流体流动方式:逆流、顺流式 特点:工艺简单,生产效率高 产量大, 颗粒流动性好,坯体 强 度高,致密度高 。
3. 干燥过程的原因 3.1 干燥制度不合理 温度、湿度、流速和方向控制不当。 干燥太快;介质湿度太大引起水分冷凝于坯体上。 3.2 坯体放置不平衡或放置方法不当局部收缩阻力太大。 4. 器型设计不合理:结构复杂、薄厚不均匀。
泥 3-腹部 4-底肩 5-底心
5
3. 干燥收缩与变形
3.1收缩与变形的原因
干燥 颗粒表面自由水膜变薄 颗粒之间靠近 发
生收缩 坯料部分颗粒的取向性排列 收缩的各向异 性 产生内应力
内应力大于塑性状态屈服值时 变形
内应力大于或塑性状态的破裂破裂值或弹性状态抗 拉强度时 开裂
3.2 影响坯体收缩变形的主要因素
1)坯体中粘土性能 (颗粒 粗细 ,多少 ,分布 ) 细 , 吸附水膜厚,可塑性好,收缩变形大。 2)粘土吸附阳离子的种类 3)坯体的含水率 含水率大,收缩大,变形开裂的可能性大。 4)坯体的成形方法 与含水率的关系 5)坯体的形状 形状复杂、 薄厚不匀容易变形开裂。
4.3 红外干燥 远红外波长 2.5~1000um 近红外波长 0.75~2.5um 根据水分子对红外线的吸收特性,通常选择的干燥波长为 2.5~15um的远红外线。 1)远红外反射器 基体、辐射涂层、热源、保温装置部分构成。
基体:金属(钢、铝)、陶瓷(碳化硅、锆英石质耐火材料) 辐射层:全波涂料2.5~15(SiC、-Fe2O3、 -Fe2O3 为主体) 长波涂料6um以上(锆钛系、锆英石系) 短波涂料3.5um以下(富含SiO2、半导体氧化钛TiO1.9) 采用涂刷粘结、等离子喷涂和复合烧结的方法与基体结合。 热源:电阻丝。辐射体温度高,辐射强度高。400~500℃最好。
2)红外干燥远特点
A) 速度快,效率高。
B) 热效率高,节约能源,单位坯体能耗是近红外的1/2, 热空气干燥的1/3。 C) 设备小,造价低,占地面积小。 D) 干燥效果好, 5. 综合干燥 干燥方法特点结合干燥过程各阶段的特点 5.1 辐射干燥和热空气对流干燥相结合 例如英国带式快速干燥器 5.2 工频电干燥、红外干燥与热风干燥相结合 大件注浆产品先用电热干燥除去大部分水分后,施釉后采用 红外干燥和热风干燥交替进行,除去剩余水分。
第二节 干燥制度的确定
干燥过程各 阶段的速度 影响速度 的参数 干燥介质的种类 温度、湿度, 流量、流速等 坯体的性质
1. 影响干燥速度的因素
1.1 影响内扩散的因素 热湿传导:温度差引起的水分沿温度梯度方 内扩散 向扩散。 热端 冷端 形式 湿传导:湿度差引起水分沿湿度方向的扩散。 湿端 干端 1)热湿传导方向与湿传导方向一致性。 微波干燥、远红外干燥。
1.6 热泵干燥 基本原理:高温热湿气体经过冷凝换热,排除水分后再加热 循环使用。 1.7 脉冲干燥 基本原理:墙地砖坯体输送的流动方向的两侧,脉冲利用 干热空气来干燥坯体。
2. 工频电干燥
基本原理:将坯体两端加交流电压(相当于并联进入电路), 通电后坯体内部发热,蒸发水分干燥。 特点:热湿扩散方向与湿扩散方向一致,干燥效率高, 质量好,干燥后期耗电量大。适用于大厚制品。
湿气排除 燃烧室 燃烧器 主送风机
红外辐射器
入坯
出坯
高强度喷嘴
热气再循环
热气分布器
英国带式快速干燥器
干燥缺陷分析
变形和开裂是最常见的干燥缺陷,本质是不均匀收缩引起
的内应力造成的。直接原因可能是以下几方面。 1. 配方设计和坯料制备的原因 1.1 坯料配方中塑性粘土太多、太少。 1.2 坯料细度太粗、太细。 1.3 坯料含水率太高,组分分布不均匀。 1.4 练泥和成形过程造成颗粒的定向排列从而导致不均匀应力。 2. 成型过程的原因 2.1 成形时泥料受力不均匀,造成致密度不一致,收缩不均匀。 2.2 模型吸水能力不均匀,造成不均匀收缩。 模型的不均匀干燥;模型制作、使用过程局部油污。
2. 干燥介质参数的确定 2.1介质温度 1)坯体的大小、形状、厚度、组成、含水率 、大件、 复杂坯体 低温高湿高温低湿(临界点); 小件、简单坯体 高温低湿干燥。 带石膏模干燥时 温度不大于70℃,否则模型强度
降低。 2)热能的充分利用和设备的因素 介质温度太高,热效率低,传热设备使用寿命降低。
室式干燥、隧道式干燥、喷雾干燥、链式干燥及热泵干燥。 1.1 室式干燥(室式烘房) 分类:固定坯架式;活动坯车式。 暖气式;热风式;温度湿度可调式。
特点:设备简单,造价低廉,热效率低,干燥周期长。
1.2 隧道式干燥
1—鼓分机 2—总进热风道 3—连通进热风道 4—支进热风道 5—干燥隧道 6—废气排除通道 7—排风机
干燥的目的:排除坯体中的水分,同时赋予坯体一定 的干燥 强度,满足搬运以及后续工序(修坯、粘结、 施釉)的要求。
2. 干燥机理及干燥过程
干燥机理
坯体干燥过程
等速干燥阶段 降速干燥阶段 平衡阶段
速阶段
1
介质温度
A
2 3
B
C O
1—坯体含水率 2—干燥速度
D
时间 3—坯体表面温度
干燥过程各阶段的特征: OA 升速干燥阶段 温度—逐渐升高至干燥介质湿球温度TA 干燥速度—由零升至最大,蒸发表面水分。 吸热—蒸发水分,提高坯体温度。 收缩—很小。 A B等速干燥阶段 表面温度—不变, 干燥速度—保持衡定,内扩散速度等于外 扩散速度。 吸热—全部用于蒸发水分。 收缩—较大,相当于干燥水分的体积。
湿 坯 质 量 (g)
通电时间(min)
4. 辐射干燥
基本原理:坯体中的水分选择性吸收特定波长的电磁波, 产生热效应,排除水分。 特点:设备简单,易于实现自动化,干燥速度快,质量好。
种类:高频干燥、微波干燥、红外干燥。
电磁波分类:按波长(um)分。 可见光 近红外线 远红外线 0.76~0.4 5.6~0.76 1000~5.6 微波 无线电波 107~103 1010~107
4.1 高频干燥
电磁波频率在107HZ附近,属于超高频微波的范畴,辐射坯体 水分子吸收热量,达到干燥的目的。干燥质量好,成本高。 4.2 微波干燥 微波在陶瓷行业应用:微波烧结、微波干燥、微波检测 。 微波干燥常用频率:95525MHZ 245025MHZ 特点:微波对良导体能够产生全反射(金属),对不良导体 则部分反射,大部分吸收。微波干燥器外壳以及防护板全部 采用金属材料制成。微波干燥快速安全。 资料报道:碗盘类制品热空气干燥需要几十分钟,微波干燥 只需要3分钟就能完成。英国的微波-真空干燥技术1.5分钟 即可完成,大大延长了石膏模具的寿命。
含水率与耗电量的关系
电 能 消 耗 (
电压:初期 30~40v 后期 220v以上。
kw· h/kg ) 含水率%
3. 直流电干燥
基本原理:泥料中的水分以水化阳离子的形式存在,在电场 作用下,发生电动现象,水分子向负极运动排除。 特点:干燥均匀,速度快,不易变形质量好。 剩余少量水分需要用其它干燥方法排除。