板弹簧疲劳断裂原因的分析与改进措施
汽车中的板簧的断裂失效分析

材料断裂理论与失效分析汽车中的板簧的断裂失效分析专业:材料工程(锻压)类型:应用型姓名:***学号:15S******汽车中的板簧的断裂失效分析引言汽车板簧是汽车悬架系统中最传统的弹性元件,由于其可靠性好、结构简单、制造工艺流程短、成本低而且结构能大大简化等优点,从而得到广泛的应用。
汽车板簧一般是由若干片不等长的合金弹簧钢组合而成一组近似于等强度弹簧梁。
在悬架系统中除了起缓冲作用而外,当它在汽车纵向安置,并且一端与车架作固定铰链连接时,即可担负起传递所有各向的力和力矩,以及决定车轮运动的轨迹,起导向的作用,因此就没有必要设置其它的导向机构,另外汽车板簧是多片叠加而成,当载荷作用下变形时,各片有相对的滑动而产生摩擦,产生一定的阻力,促使车身的振动衰减,但是板簧单位重量储存的能量最低,因些材料的利用率最差。
1. 材质是什么?65Mn/低碳钢哪一类合适?材质一般为硅锰钢。
因为碳素弹簧钢因淬透性低,较少使用于汽车中;锰钢淬透性好,但易产生淬火裂纹,并有回火脆性。
因此,硅锰钢在我国应用在汽车的板簧上较为广泛。
65Mn 钢更为合适,因为:低碳钢为碳含量低于0.25%的碳素钢,因其强度低、硬度低而软,又称软钢。
它包括大部分普通碳素结构钢和一部分优质碳素结构钢,大多不经热处理用于工程结构件,有的经渗碳和其他热处理用于要求耐磨的机械零件。
低碳钢退火组织为铁素体和少量珠光体,其强度和硬度较低,塑性和韧性较好。
因此可以看出,低碳钢不符合板簧材料高强度和高硬度的要求。
65Mn弹簧钢,含有0.90%~1.2%的Mn元素,提高了材料的淬透性,© 12mm 的钢材油中可以淬透,表面脱碳倾向比硅钢小,经热处理后的综合力学性能优于碳钢,但有过热敏感性和回火脆性。
Mn 是弱碳化物形成元素,在钢中主要以固溶的形式存在于基体中。
一部分固溶于铁素体(或奥氏体),另一部分形成含Mn的合金渗碳体(Fe、Mn )。
Mn还能显著提高钢的淬透性,改善热处理性能,强化基体、降低珠光体的形成温度,细化珠光体的片间距离,从而提高钢的强度和硬度。
板弹簧疲劳断裂原因的分析与改进措施

BL客车后钢板弹簧疲劳断裂原因的分析与改进措施田洪森(机电系,北京100044)摘要:本文通过对BL客车后钢板弹簧断裂断口形状、设计应力、原材料及理化性能等方面的分析,找出造成钢板弹簧疲劳断裂的原因,提出了改进的措施,使该钢板弹簧的疲劳寿命达到日本五十铃公司标准的要求。
关键词:钢板弹簧;疲劳断裂;原因分析;改进措施1问题的提出BL客车是对日本五十铃公司BE22客车技术引进、吸收、消化后的一种轻型客车,该客车后悬挂弹性元件是一变刚度钢板弹簧,该种钢板弹簧的优点是在客车空载、满载状态下呈非线性状态,即悬挂在客车空载、满载状态下接近等频性,从而可以提高客车的平顺性,乘客乘坐舒适性,本文通过分析BL客车后钢板弹簧在设计、试制、试验过程中出现非正常疲劳断裂原因分析,提出了改进措施,使其达到了日本五十铃公司BE22客车后钢板弹簧疲劳寿命的标准要求。
2 BL客车后钢板弹簧的结构BL客车后钢板弹簧为一多片半椭圆形且由主、副簧组成的变刚度钢板弹簧,总片数为12片,其中主簧9片,副簧3片,主片片厚为10mm,其余片厚为9mm,采用的弹簧钢为60Si2Mn,其中3~9片端部压延,使钢板弹簧接近等应力梁。
3 BL后钢板弹簧疲劳试验情况3.1 试验标准:按五十铃公司提供的BE22客车后钢板弹簧疲劳寿命试验标准执行即: 1)按实车状态夹紧;2)变形中心:Fa=58.5mm,Fmax=137mm(2.5G),Fmin=20mm;3)振动频率:60-120cpm;4)从产品中随机抽取三架钢板弹簧;5)疲劳寿命:疲劳循环次数3≥20万次。
3.2 试验设备:钢板弹簧疲劳试验机。
3.3 疲劳寿命试验结果如下:4对钢板弹簧疲劳断裂原因分析根据以上试验结果可以看出,疲劳断裂的簧片均在第7片且同在钢板弹簧的大卷耳端,且位置距钢板弹簧中心螺栓距离也差别不大(138、142、150),说明该钢板弹簧在此处存在规律性疲劳断裂源,而非偶然原因造成的,下面根据疲劳断裂试验结果及设计、生产过程对钢板弹簧疲劳断裂的原因进行分析。
钢板弹簧折断原因及提高使用寿命的措施

简述疲劳断裂的原因和提高零件疲劳强度的方法

简述疲劳断裂的原因和提高零件疲劳强度的方法下载提示:该文档是本店铺精心编制而成的,希望大家下载后,能够帮助大家解决实际问题。
文档下载后可定制修改,请根据实际需要进行调整和使用,谢谢!本店铺为大家提供各种类型的实用资料,如教育随笔、日记赏析、句子摘抄、古诗大全、经典美文、话题作文、工作总结、词语解析、文案摘录、其他资料等等,想了解不同资料格式和写法,敬请关注!Download tips: This document is carefully compiled by this editor. I hope that after you download it, it can help you solve practical problems. The document can be customized and modified after downloading, please adjust and use it according to actual needs, thank you! In addition, this shop provides you with various types of practical materials, such as educational essays, diary appreciation, sentence excerpts, ancient poems, classic articles, topic composition, work summary, word parsing, copy excerpts, other materials and so on, want to know different data formats and writing methods, please pay attention!疲劳断裂与提高零件疲劳强度1. 疲劳断裂的原因。
钢板弹簧单边折断

焊接修复是一种常见的钢板弹簧单边折断修复方法,通过将断裂部分焊接在一起,实现修复。
详细描述
焊接修复具有操作简单、成本低廉的优点,适用于小范围、小尺寸的钢板弹簧断裂。然而,焊接过程中可能造成 钢板局部变形,影响钢板弹簧的平整度和刚度。此外,焊接质量受操作人员技能水平影响较大,需要经验丰富的 焊接工人进行操作。
钢板弹簧的断裂会影响车辆的制动 性能,特别是在紧急制动时,可能 导致制动距离延长。
承重能力
钢板弹簧是车辆承重的主要部件之 一,单边折断会降低车辆的承重能 力,影响货物运输和乘坐舒适度。
02
钢板弹簧单边折断原因分析
材料缺陷
01
钢板弹簧材料本身存在缺陷,如 夹杂物、气泡、裂纹等,这些缺 陷降低了材料的力学性能,容易 引发断裂。
道路状况不佳,如颠簸、坑洼等,会导致钢板弹簧承受额外的冲击和振动,从而 增加断裂的可能性。
载荷分布不均
钢板弹簧在承载过程中,如果载荷分布不均,会导致部分钢 板过载或欠载,从而引发断裂。
钢板弹簧的设计不合理,如长度、曲率半径等参数不合适, 也会导致载荷分布不均,增加断裂的风险。
03
钢板弹簧单边折断预防措施
材料质量控制
01
02
03
选用优质材料
确保钢板弹簧所用的材料 质量可靠,具有足够的强 度和耐久性,以降低断裂 的风险。
严格控制材料成分
对材料的化学成分进行严 格控制,确保各成分含量 符合标准要求,以提高材 料的综合性能。
进行材料检验
对采购回来的材料进行质 量检验,确保材料质量符 合要求,防止不合格材料 流入生产环节。
定期维护保养
对钢板弹簧进行定期维护 保养,清除表面污垢、锈 迹和杂物,保持其良好的 工作状态。
汽车后桥板簧的断裂分析

汽车后桥板簧的断裂分析摘要:整车可靠性耐久道路试验中,后桥板簧是重要试验验证对象,是影响整车性能的重要因素之一。
本文通过对耐久性道路试验中的后板簧断裂现象,应用设计复核、宏观分析、微观分析、金相分析、硬度检测等技术手段开展分析判断,阐述了后桥板簧表面凹坑缺陷、后悬架无减振器是造成板簧早期断裂的关键及实施优化的设计方案,为后续车型开发提供必要的经验积累。
关键词:汽车后桥板簧断裂前言板簧是汽车悬架系统的弹性元件,具有可靠性好、结构简单、制造工艺流程短、成本低等优点。
车板簧一般是由若干片不等长的簧片组成,簧片按照一定的组合方式使得板簧呈现线性或非线性弹性特征,在悬架系统中起到缓冲作用。
汽车在非平整路面上行驶时,在交互冲击载荷作用下,各片板簧有相对的滑动而产生摩擦,产生一定的阻力,促使车身的振动衰减。
板簧结构在商用车及轻小型车辆上应用广泛,实际应用场景中,在交变应力下板簧可能发生疲劳和断裂,故板簧应具有较高的疲劳强度和耐蚀等性能。
一、后板簧断裂案例某汽车后悬架根据该车型的总质量、底盘布置等特点,采用板簧结构,用于连接车身与后桥,且不装后减振器。
主要由三片不等长的钢板弹簧组成,并用夹箍将三片板簧固定,防止各簧片横向错位,在弹簧回弹将力传递给其他片,减少主板簧片的应力。
后悬架采用板簧结构,开发阶段需在试验场进行道路耐久试验验证,试验场给汽车提供各种类型的路面试验条件,满足零件的耐久试验要求。
在可靠性耐久道路试验中,3台试验车均出现了后钢板弹簧断裂的情况,在第一片到第三片板簧均有发生断裂情况。
二、后板簧断裂原因探讨为确定后桥板簧断裂的根本原因,应用设计复核、金相分析、硬度检查等技术手段开展分析。
1、设计复核应用CAE软件对板簧设计进行复核,对板簧应力分析结果与已量产车型进行横向对比,根据分析结果并结合设计经验,板簧设计满足设计要求。
按汽车行业标准QC/T 29035-1991对板簧进行强度台架测试,测试结果均不低于试验标准(板簧的疲劳寿命不小于8万次)。
汽车中的板簧的断裂失效分析

材料断裂理论与失效分析汽车中的板簧的断裂失效分析专业:材料工程(锻压)类型:应用型姓名:***学号: 15S******汽车中的板簧的断裂失效分析引言汽车板簧是汽车悬架系统中最传统的弹性元件,由于其可靠性好、结构简单、制造工艺流程短、成本低而且结构能大大简化等优点,从而得到广泛的应用。
汽车板簧一般是由若干片不等长的合金弹簧钢组合而成一组近似于等强度弹簧梁。
在悬架系统中除了起缓冲作用而外,当它在汽车纵向安置,并且一端与车架作固定铰链连接时,即可担负起传递所有各向的力和力矩,以及决定车轮运动的轨迹,起导向的作用,因此就没有必要设置其它的导向机构,另外汽车板簧是多片叠加而成,当载荷作用下变形时,各片有相对的滑动而产生摩擦,产生一定的阻力,促使车身的振动衰减,但是板簧单位重量储存的能量最低,因些材料的利用率最差。
1.材质是什么?65Mn/低碳钢哪一类合适?材质一般为硅锰钢。
因为碳素弹簧钢因淬透性低,较少使用于汽车中;锰钢淬透性好,但易产生淬火裂纹,并有回火脆性。
因此,硅锰钢在我国应用在汽车的板簧上较为广泛。
65Mn钢更为合适,因为:低碳钢为碳含量低于0.25%的碳素钢,因其强度低、硬度低而软,又称软钢。
它包括大部分普通碳素结构钢和一部分优质碳素结构钢,大多不经热处理用于工程结构件,有的经渗碳和其他热处理用于要求耐磨的机械零件。
低碳钢退火组织为铁素体和少量珠光体,其强度和硬度较低,塑性和韧性较好。
因此可以看出,低碳钢不符合板簧材料高强度和高硬度的要求。
65Mn弹簧钢,含有0.90%~1.2%的Mn元素,提高了材料的淬透性,φ12mm 的钢材油中可以淬透,表面脱碳倾向比硅钢小,经热处理后的综合力学性能优于碳钢,但有过热敏感性和回火脆性。
Mn是弱碳化物形成元素,在钢中主要以固溶的形式存在于基体中。
一部分固溶于铁素体(或奥氏体),另一部分形成含Mn的合金渗碳体(Fe、Mn)。
Mn还能显著提高钢的淬透性,改善热处理性能,强化基体、降低珠光体的形成温度,细化珠光体的片间距离,从而提高钢的强度和硬度。
重型汽车钢板弹簧断裂失效形式及应用现状

重型汽车钢板弹簧断裂失效形式及应用现状钢板弹簧(Leaf Spring)是广泛用于汽车悬架结构的具有一定弹性的元件,由宽度相等长度不相同的复合金属弹簧片组合而成,该元件各个部位的强度是相等的,可以起到很强的减缓压力的作用,但是钢板弹簧由于长期受到大力压迫导致其在达到一定的承受值后会发生断裂,本文重点分析了钢板弹簧断裂的形式,并提出相关的技术改进方案供相关生产商参考。
标签:钢板弹簧;断裂失效形式;应用现状车辆在正常行驶时,会受到自身振动和外部一定强度的挤压力作用,此时钢板弹簧会压缩从而吸收车辆的动能,将动能转化为弹簧的弹性势能,由此车辆的动能逐渐被转化,避免了巨大的冲击作用,起到很好的缓冲效果,使车辆运行更平稳,操作更流畅,安全性更好。
当钢板弹簧承受的压力过大会发生断裂失效,下面重点分析钢板弹簧断裂的几种形式。
1 钢板弹簧断裂失效的形式1.1 中心孔失效中心孔是钢板弹簧最脆弱的部位,因为钢板弹簧受到力作用时,其所承受的力会共同作用于中心孔,使其发生断裂失效。
其断裂时会产生很多裂纹,其位于孔板的结合处,跨越整板。
经过专业人员研究发现,该种失效是由于螺栓松动,弹簧承受的作用力被汇集到中心孔,中心孔承受力的表面积小,故而力的强度就大,当强度超过一定的值,孔就断裂,导致裂纹,随后弹簧便失效。
1.2 卷耳失效车辆在行驶过程中会不可避免受到各种摩擦力以及外力碰撞作用,此外,司机在驾驶过程中也会出现挂挡力度过大等不规范的操作,如果卷耳和衬套之间过于紧密,会导致发热,变硬等现象,这会使钢板膨胀变大,导致一定的变型,使得弹簧卷上方失效。
当车辆行驶过长时间时,卷耳上已有的些许裂纹会进一步加速断裂,加速弹簧失效的过程。
1.3 腐蚀疲劳钢板弹簧持续受力,而且很多零件露天之后会遭到空气腐蚀,生锈变型,致使弹簧在裂纹处承受力大幅度降低,裂纹便会不断加深,当达到极限时,弹簧便会断裂。
失效的切面看起来像是一系列同心的半圆形,在腐蚀和摩擦的作用下,裂纹外侧变暗。
轻型车钢板弹簧断裂原因分析与改进

摘要:针对轻型车钢板弹簧在台架疲劳试验中早期断裂的问题,通过对钢板弹簧断裂样品进行受力结构、断口及理化检验等分析,确定淬火开裂是导致钢板弹簧发生断裂的直接原因。
通过对钢板弹簧的热处理工艺提出改进措施,使钢板弹簧热处理后的硬度、显微组织和晶粒度满足技术要求,提高了钢板弹簧的疲劳寿命。
关键词:弯曲载荷断口分析淬火开裂热处理疲劳试验中图分类号:TG142文献标识码:BDOI :10.19710/ki.1003-8817.20170200轻型车钢板弹簧断裂原因分析与改进张炜1惠恩栋2潘艳春1高东宏1赵凤梅2(1.中国第一汽车集团有限公司研发总院,长春130011;2.富奥辽宁汽车弹簧有限公司,辽阳111000)作者简介:张炜(1986—),男,工程师,学士学位,研究方向为金属材料和制造工艺的开发及应用技术。
1前言钢板弹簧是汽车悬架系统中重要的弹性零件,它是由若干个弹簧片组合而成的近似等强度的弹性梁,通过使车架与车桥之间作弹性连接,起到缓和由车轮传递到车架的冲击,影响车辆的平顺性、安全性及舒适性[1]。
钢板弹簧具有结构简单、成本低、工作可靠且维修方便等优点,被广泛应用于轻、中、重型等商用车,原材料一般为热轧态的合金弹簧钢,如60Si2MnA 、55CrMnA 、50CrVA 等,经过变截面轧制、卷耳加工、热处理、喷丸处理、表面处理等工艺制成[2]。
热处理是钢板弹簧生产工艺中最重要的环节,一般采用淬火+中温回火的处理工艺,保证材料获得较高的弹性极限和疲劳极限,以满足钢板弹簧在交变载荷下的可靠性要求。
某公司生产的轻型车钢板弹簧在进行台架疲劳试验时发生断裂,疲劳寿命仅为2.2万次,未满足规定的大于16万次的疲劳寿命技术要求。
主要通过受力结构、宏观和微观断口、硬度、显微组织及晶粒度等分析钢板弹簧发生断裂的原因,依此提出可行的工艺改进措施,并对改进后的钢板弹簧进行可靠性验证。
2钢板弹簧受力结构及断口分析2.1受力结构分析钢板弹簧台架疲劳试验装置见图1,钢板弹簧在两端卷耳和中间平直段处三点受力,通过中间曲柄连杆机构的上下移动施加交变的弯曲载荷,在平直段螺栓夹紧处的应力最大。
弹簧断裂原因分析报告

弹簧断裂原因分析报告弹簧是一种广泛应用于工业和日常生活中的机械零件,其具有弹性变形和恢复的特性。
然而,有时候弹簧会发生断裂的情况,这可能会导致机械系统的故障或事故发生。
因此,对于弹簧断裂原因的分析非常重要,以便采取相应的预防措施。
弹簧的断裂原因是多样的,以下是一些常见的原因分析:1. 材料质量问题:弹簧制造过程中所选用的材料可能存在质量问题。
例如,材料的强度不符合设计要求,存在缺陷或杂质等。
这些问题可能导致弹簧在使用过程中发生过早的疲劳断裂。
2. 过载或过应力:当弹簧承受超出其承载能力的应力或载荷时,会导致弹簧瞬间失去弹性变形的能力,从而发生断裂。
过载通常是由于设计不当、使用不当或突发的外力冲击等原因引起的。
3. 疲劳断裂:长期重复加载和卸载会导致弹簧的疲劳断裂。
如果弹簧在使用过程中受到频繁的动态应力加载,而弹簧材料的强度和耐久性不够,就容易发生疲劳断裂。
4. 腐蚀或腐蚀疲劳:当弹簧长时间处于恶劣的环境中,如潮湿、高温或有腐蚀性物质的环境,弹簧材料容易受到腐蚀性介质的侵蚀。
腐蚀会损害弹簧的表面或内部结构,导致腐蚀疲劳断裂。
5. 不当安装或维护:如果弹簧在安装或维护过程中受到错误的处理或操作,如过紧或过松的安装、弯曲或扭转过载等,就可能导致弹簧断裂。
此外,缺乏定期检查和维护也可能使弹簧受到磨损或损坏,进而导致断裂。
针对弹簧断裂的原因分析,下面是一些预防和解决措施建议:1. 选择高质量的材料,并确保材料符合设计要求。
2. 严格控制弹簧所承受的应力或载荷,避免过载。
3. 进行弹簧的疲劳寿命试验和使用寿命评估,并根据结果调整设计和使用要求。
4. 在恶劣环境下使用时,采取相应的防腐措施,如表面镀层、材料的选择和密封等。
5. 确保正确的安装和维护程序,并遵循制造商提供的建议。
总之,弹簧断裂的原因可以有很多,包括材料质量、过载、疲劳、腐蚀以及不当安装和维护等。
通过对断裂原因的分析,可以采取相应的预防措施,从而提高弹簧的使用寿命和减少故障风险。
几种钢板弹簧断裂故障的原因分析

关 键词 : 板簧
断裂
1 J - 刖 L ‘ 图 2中弧高 h减 小 , 导致骑 马
板 簧 以其 结构 简单 , 便宜 可靠 等 因素 , 使 其成
为商 川 乍最 常采 用 的 弹性 元 件 之 … 。 对 于 其 常
见 失 效 形 式—— 断 裂 的原 冈 分 析 就 显 得 格 外 重
螺栓松 动 ,如按 此状 态继续 路 试将会 出现 板 簧断 裂故 障 。
要 。我 仃 J 结合 以 下几种 故障分 析板 簧断 裂 的主 要
原【 六 】
2 断裂 故 障分 析
2 . 1 故 障一 : 中心 螺栓处 断裂( 见图 1 )
5 1 5 N / m m 2 , 极 限应 力 9 8 1 N / mm 2 , 符合 设计 要求 。 且为保 证 主片 的寿命 , 板簧 各片通 过调 整弧 高 , 使 主片产 生负 的预应力 , 如图 4 。从 而保证 主片 有更
高 的疲 劳 寿命 , 不 至 于 出现 主片过 早 断裂 , 影 响整
角。 2 . 2 . 2 解决措 施 :
图 7 表面 脱 碳 层
该 板 簧 片厚 为 8 mm,按 标 准 G B / T 1 9 8 4 4规 定, 脱层 不 应超 过 0 . 2 4 am, r 但 实 测结 果 为 0 . 3 m m。 不符 合要求 ,因此判 断板 簧断 裂的原 因为脱碳 层
车安全 。初步 分析非设 计原 因导致 断裂 。
图 4 板 簧 各 片 装 配示 意 图
2 ) 工 艺 因素 : 经 扫描 电镜 分 析 , 在 断 裂 起 始
处可 以观察 到一些表 面 凹坑 , 如 图 5所示 。
弹簧抗疲劳断裂知识
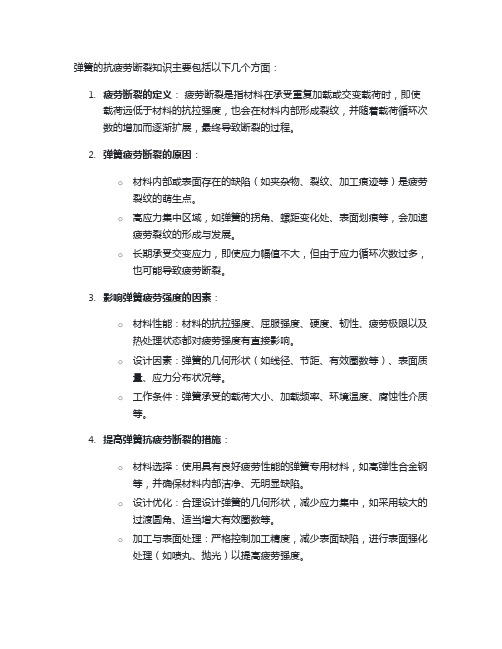
弹簧的抗疲劳断裂知识主要包括以下几个方面:1.疲劳断裂的定义:疲劳断裂是指材料在承受重复加载或交变载荷时,即使载荷远低于材料的抗拉强度,也会在材料内部形成裂纹,并随着载荷循环次数的增加而逐渐扩展,最终导致断裂的过程。
2.弹簧疲劳断裂的原因:o材料内部或表面存在的缺陷(如夹杂物、裂纹、加工痕迹等)是疲劳裂纹的萌生点。
o高应力集中区域,如弹簧的拐角、螺距变化处、表面划痕等,会加速疲劳裂纹的形成与发展。
o长期承受交变应力,即使应力幅值不大,但由于应力循环次数过多,也可能导致疲劳断裂。
3.影响弹簧疲劳强度的因素:o材料性能:材料的抗拉强度、屈服强度、硬度、韧性、疲劳极限以及热处理状态都对疲劳强度有直接影响。
o设计因素:弹簧的几何形状(如线径、节距、有效圈数等)、表面质量、应力分布状况等。
o工作条件:弹簧承受的载荷大小、加载频率、环境温度、腐蚀性介质等。
4.提高弹簧抗疲劳断裂的措施:o材料选择:使用具有良好疲劳性能的弹簧专用材料,如高弹性合金钢等,并确保材料内部洁净、无明显缺陷。
o设计优化:合理设计弹簧的几何形状,减少应力集中,如采用较大的过渡圆角、适当增大有效圈数等。
o加工与表面处理:严格控制加工精度,减少表面缺陷,进行表面强化处理(如喷丸、抛光)以提高疲劳强度。
o热处理工艺:选择合适的热处理工艺,以提高材料的综合力学性能,包括硬度、强度和韧性。
5.疲劳寿命评估与测试:通过应力-寿命(S-N)曲线、高周疲劳试验、低周疲劳试验等方法评估弹簧的疲劳寿命,并据此选择合适的弹簧设计和使用方案。
通过以上各项措施,可以有效提高弹簧的抗疲劳断裂性能,确保其在长期使用中保持稳定的功能性和安全性。
客车后钢板弹簧疲劳断裂原因的分析与改进措施
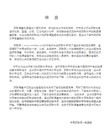
2)
簧片在断口处是否有附加应力产生除设计应力外,如果因某种原因有附加应力产生,使总应力加大也可能造成钢板弹簧片断裂,通过对断裂簧片断口处观察,发现此处在压延时造成了轻微急弯,使该片端部同上一片形成点接触,对这一点从试验后两片间的摩擦痕迹也证明了此点(如图)
摘 要:本文通过对BL客车后钢板弹簧断裂断口形状、设计应力、原材料及理化性能等方面的分析,找出造成钢板弹簧疲劳断裂的原因,提出了改进的措施,使该钢板弹簧的疲劳寿命达到日本五十铃公司标准的要求。
关键词:钢板弹簧;疲劳断裂;原因分析;改进措施
4 对钢板弹簧疲劳断裂原因分析
根据以上试验结果可以看出,疲劳断裂的簧片均在第7片且同在钢板弹簧的大卷耳端,且位置距钢板弹簧中心螺栓距离也差别不大(138、142、150),说明该钢板弹簧在此处存在规律性疲劳断裂源,而非偶然原因造成的,下面根据疲劳断裂试验结果及设计、生产过程对钢板弹簧疲劳断裂的原因进行分析。
......
I=7 σ1=37 σ2=41 σ3=44 σ4=47 σ5=17 σ6=2
......
注:I—片序 σ—应力 kg/mm2 各应力点为平均间隔(100mm)。
1 问题的提出
BL客车是对日本五十铃公司BE2ቤተ መጻሕፍቲ ባይዱ客车技术引进、吸收、消化后的一种轻型客车,该客车后悬挂弹性元件是一变刚度钢板弹簧,该种钢板弹簧的优点是在客车空载、满载状态下呈非线性状态,即悬挂在客车空载、满载状态下接近等频性,从而可以提高客车的平顺性,乘客乘坐舒适性,本文通过分析BL客车后钢板弹簧在设计、试制、试验过程中出现非正常疲劳断裂原因分析,提出了改进措施,使其达到了日本五十铃公司BE22客车后钢板弹簧疲劳寿命的标准要求。
钢板弹簧断裂问题研究
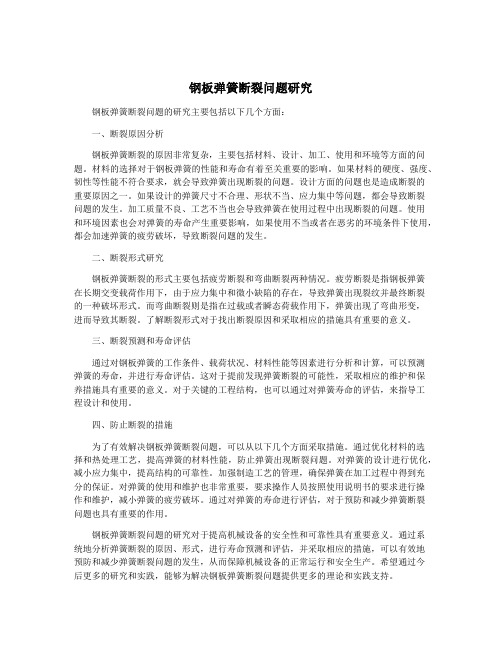
钢板弹簧断裂问题研究钢板弹簧断裂问题的研究主要包括以下几个方面:一、断裂原因分析钢板弹簧断裂的原因非常复杂,主要包括材料、设计、加工、使用和环境等方面的问题。
材料的选择对于钢板弹簧的性能和寿命有着至关重要的影响。
如果材料的硬度、强度、韧性等性能不符合要求,就会导致弹簧出现断裂的问题。
设计方面的问题也是造成断裂的重要原因之一。
如果设计的弹簧尺寸不合理、形状不当、应力集中等问题,都会导致断裂问题的发生。
加工质量不良、工艺不当也会导致弹簧在使用过程中出现断裂的问题。
使用和环境因素也会对弹簧的寿命产生重要影响,如果使用不当或者在恶劣的环境条件下使用,都会加速弹簧的疲劳破坏,导致断裂问题的发生。
二、断裂形式研究钢板弹簧断裂的形式主要包括疲劳断裂和弯曲断裂两种情况。
疲劳断裂是指钢板弹簧在长期交变载荷作用下,由于应力集中和微小缺陷的存在,导致弹簧出现裂纹并最终断裂的一种破坏形式。
而弯曲断裂则是指在过载或者瞬态荷载作用下,弹簧出现了弯曲形变,进而导致其断裂。
了解断裂形式对于找出断裂原因和采取相应的措施具有重要的意义。
三、断裂预测和寿命评估通过对钢板弹簧的工作条件、载荷状况、材料性能等因素进行分析和计算,可以预测弹簧的寿命,并进行寿命评估。
这对于提前发现弹簧断裂的可能性,采取相应的维护和保养措施具有重要的意义。
对于关键的工程结构,也可以通过对弹簧寿命的评估,来指导工程设计和使用。
四、防止断裂的措施为了有效解决钢板弹簧断裂问题,可以从以下几个方面采取措施。
通过优化材料的选择和热处理工艺,提高弹簧的材料性能,防止弹簧出现断裂问题。
对弹簧的设计进行优化,减小应力集中,提高结构的可靠性。
加强制造工艺的管理,确保弹簧在加工过程中得到充分的保证。
对弹簧的使用和维护也非常重要,要求操作人员按照使用说明书的要求进行操作和维护,减小弹簧的疲劳破坏。
通过对弹簧的寿命进行评估,对于预防和减少弹簧断裂问题也具有重要的作用。
钢板弹簧断裂问题的研究对于提高机械设备的安全性和可靠性具有重要意义。
弹簧疲劳断裂或失效的原因分析

弹簧疲劳断裂或失效的原因分析一、分解弹簧永久变形及其影响因素弹簧的永久变形是弹簧失效的主要原因之一,弹簧的永久变形,会使弹簧的变形或负荷超出公差范围,而影响机器设备的正常工作。
检查弹簧永久变形的方法:1、快速高温强压处理检查弹簧永久变形。
是把弹簧压缩到一定高度或全部并紧,然后放在开水中或温箱保持10~60分钟,再拿出来卸载,检查其自由高度和给定工作高度下的工作载荷。
2、长时间的室温强压处理检查弹簧永久变形:是在室温下,将弹簧压缩或压并若干天,然后卸载,检查其自由高度和给定工作高度下的工作载荷。
二、弹簧断裂及其影响因素弹簧的断裂破坏也是弹簧的主要失效形式之一,弹簧断裂形式可分为;疲劳断裂,环境破坏(氢脆或应力腐蚀断裂)及过载断裂。
1、弹簧的疲劳断裂:弹簧的疲劳断裂属于设计错误,材料缺陷,制造不当及工作环境恶劣等因素。
疲劳裂纹往往起源于弹簧的高应力区,如拉伸弹簧的钩环、压缩弹簧的内表面、压缩弹簧(两端面加工的压缩弹簧)的两端面。
受力状态对疲劳寿命的影响(a)恒定载荷状态下工作的弹簧比恒定位移条件下工作的弹簧,其疲劳寿命短得多。
(b)受单向载荷的弹簧比受双向载荷的弹簧的疲劳寿命要长得多。
(c)载荷振幅较大的弹簧比载荷振幅较少的弹簧的疲劳寿命要短得多。
2、腐蚀疲劳和摩擦疲劳腐蚀疲劳:在腐蚀条件下,弹簧材料的疲劳强度显著降低,弹簧的疲劳寿命也大大缩短。
摩擦疲劳:由于摩擦磨损产生细微的裂纹而导致破坏的现象叫摩擦疲劳。
3、弹簧过载断裂弹簧的外加载荷超过弹簧危险截面所有承受的极限应力时,弹簧将发生断裂,这种断裂称为过载断裂。
过载断裂的形式:(a)强裂弯曲引起的断裂;(b)冲击载荷引起的断裂;(c)偏心载荷引起的断裂三、后处理的缺陷原因及防止措施缺陷一:脱碳对弹簧性能影响:疲劳寿命低缺陷产生原因:1、空气炉加热淬火未保护气2、盐浴脱氧不彻底防止措施:1、空气炉加热淬火应通保护气或滴有机溶液保护:盐浴炉加热时,盐浴应脱氧,杂质BAO质量分数小于0.2%。
重载工程车后双桥钢板弹簧设计改进
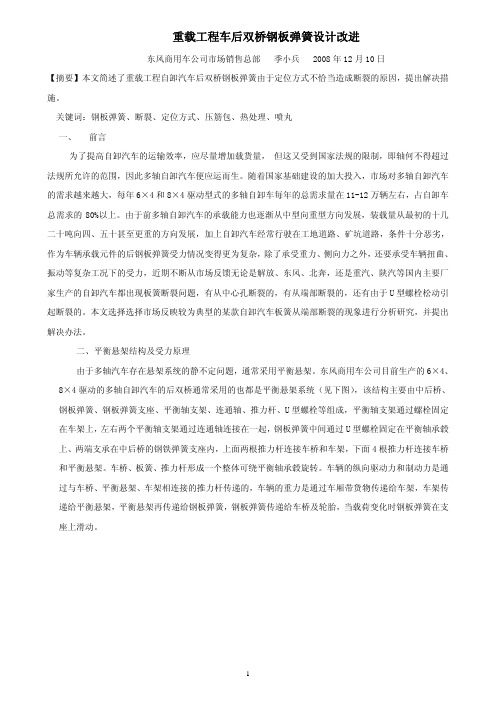
重载工程车后双桥钢板弹簧设计改进东风商用车公司市场销售总部 季小兵 2008年12月10日【摘要】本文简述了重载工程自卸汽车后双桥钢板弹簧由于定位方式不恰当造成断裂的原因,提出解决措施。
关键词:钢板弹簧、断裂、定位方式、压筋包、热处理、喷丸一、 前言为了提高自卸汽车的运输效率,应尽量增加载货量, 但这又受到国家法规的限制,即轴何不得超过法规所允许的范围,因此多轴自卸汽车便应运而生。
随着国家基础建设的加大投入,市场对多轴自卸汽车的需求越来越大,每年6×4和8×4驱动型式的多轴自卸车每年的总需求量在11-12万辆左右,占自卸车总需求的80%以上。
由于前多轴自卸汽车的承载能力也逐渐从中型向重型方向发展,装载量从最初的十几二十吨向四、五十甚至更重的方向发展,加上自卸汽车经常行驶在工地道路、矿坑道路,条件十分恶劣,作为车辆承载元件的后钢板弹簧受力情况变得更为复杂,除了承受重力、侧向力之外,还要承受车辆扭曲、振动等复杂工况下的受力,近期不断从市场反馈无论是解放、东风、北奔,还是重汽、陕汽等国内主要厂家生产的自卸汽车都出现板簧断裂问题,有从中心孔断裂的,有从端部断裂的,还有由于U型螺栓松动引起断裂的。
本文选择选择市场反映较为典型的某款自卸汽车板簧从端部断裂的现象进行分析研究,并提出解决办法。
二、平衡悬架结构及受力原理由于多轴汽车存在悬架系统的静不定问题,通常采用平衡悬架。
东风商用车公司目前生产的6×4、8×4驱动的多轴自卸汽车的后双桥通常采用的也都是平衡悬架系统(见下图),该结构主要由中后桥、钢板弹簧、钢板弹簧支座、平衡轴支架、连通轴、推力杆、U型螺栓等组成,平衡轴支架通过螺栓固定在车架上,左右两个平衡轴支架通过连通轴连接在一起,钢板弹簧中间通过U型螺栓固定在平衡轴承毂上、两端支承在中后桥的钢铁弹簧支座内,上面两根推力杆连接车桥和车架,下面4根推力杆连接车桥和平衡悬架。
汽车零件失效分析—疲劳断裂分析思路及要点

引言
➢ “失效学系统论”是研究系统的模式、结构、性质和规律的理论, 它具有系统性、最优化、模型化等基本原则。
➢ “失效学的方法论”是认识世界和改造世界的方法理论,它具有 普适性、科学性、有效性等性质;
➢ 鉴于疲劳断裂失效在汽车零部件数量和种类上多发性、失效形式 和影响因素的多样性,有必要系统地分析、归纳和总结分析的思 路和要点,建立和优化分析模式,提高分析和解决问题工作的准 确性和有效性。
3.3.3同轴度不合-力学要素
某轿车自动变速器驱动板接续发生了3件疲劳开裂的问题,间隔里程在 23000~25000公里之间; 该问题应该是发动机曲轴和变速器输入轴的轴中心线的同轴度不良。
变速器
发动机
3.3.4齿轮间隙-力学要素
曲轴第一曲柄弯曲疲劳断裂时有发生,原因是发动机相关齿轮啮合间隙过小,曲 轴断头承受弯曲疲劳载荷; 应关注相关齿轮轮齿的齿面啮合情况。
“材料疲劳强度”总体上属于“显性要素”,靠检验予以确认; “零件的疲劳应力”大多属于“隐性要素”,需要分析评价; “零件的疲劳寿命”属于“半显性要素”,需要充分地评估。
疲劳分析三要素的关系
关注金属材料的疲劳特性,强度(应力)数轴的变化是数学级 数,寿命数轴变化是几何级数。
需要关注疲劳曲线的“斜率”。对于汽车常用的、疲劳强度较 高的结构钢来讲,“寿命阶比”系数大约在1.25~1.40之间。
疲劳断裂的寿命特性
某国产发动机曲轴因“烧瓦”而引起曲柄弯曲疲劳断裂,大量反馈 的车辆行驶里程大致在1~2万公里左右,但后来收集到的最典型的数 据告知,从其更换润滑油到曲轴断裂的行驶里程仅为500公里,其寿 命折损率应为0.1%。 这种寿命数据表达了当时的润滑油市场的情况和换油的频次和几率 问题。 确认零部件的“疲劳寿命”时,要注意 到一种较常见的情况,即机械系统运行 过程中,某些“技术状态”会出现连续 性变化或阶段性的突然变化,导致“应 力要素”异常波动而引起零部件的疲劳 开裂,这种情况下真实的疲劳寿命要低 于、或远低于实际记录的寿命,
高强度变截面板弹簧失效分析及对策

丸,提高疲劳寿命‘3|。
北京:机械工业出版社,19鼹-
182
《金属热处理》2008年第33卷第8期
万方数据
高强度变截面板弹簧失效分析及对策
作者: 作者单位:
刊名: 英文刊名: 年,卷(期):
蔡璐, 王磊, CAI Lu, WANG Lei 蔡璐,CAI Lu(南京工程学院,材料学院,江苏,南京,211167), 王磊,WANG Lei(南京依维柯汽 车有限公司,江苏,南京,210028)
Abstract:Failure analysis was carTied out for trial pmducts of high stren群h t印er leaf spring by means of metallogmphy,
hardness and fhcture analysis.The results show that the spring failure mainly attributes to the improper controlling of the parameters of quenching,tempering,shot peening and so on.When the leaf spring is quenching at 915~925℃,then tempering at 470~480℃for 2 h and stress stren殍hening shot peening,the sen,ice life of the springs is obvious longer, and the pmpenies of the springs can meet the designed requirements. Key words:high stren昏h;leaf spring;failure analysis
- 1、下载文档前请自行甄别文档内容的完整性,平台不提供额外的编辑、内容补充、找答案等附加服务。
- 2、"仅部分预览"的文档,不可在线预览部分如存在完整性等问题,可反馈申请退款(可完整预览的文档不适用该条件!)。
- 3、如文档侵犯您的权益,请联系客服反馈,我们会尽快为您处理(人工客服工作时间:9:00-18:30)。
BL客车后钢板弹簧疲劳断裂原因的分析与改进措施
田洪森
(机电系,北京100044)
摘要:本文通过对BL客车后钢板弹簧断裂断口形状、设计应力、原材料及理化性能等方面的分析,找出造成钢板弹簧疲劳断裂的原因,提出了改进的措施,使该钢板弹簧的疲劳寿命达到日本五十铃公司标准的要求。
关键词:钢板弹簧;疲劳断裂;原因分析;改进措施
1问题的提出
BL客车是对日本五十铃公司BE22客车技术引进、吸收、消化后的一种轻型客车,该客车后悬挂弹性元件是一变刚度钢板弹簧,该种钢板弹簧的优点是在客车空载、满载状态下呈非线性状态,即悬挂在客车空载、满载状态下接近等频性,从而可以提高客车的平顺性,乘客乘坐舒适性,本文通过分析BL客车后钢板弹簧在设计、试制、试验过程中出现非正常疲劳断裂原因分析,提出了改进措施,使其达到了日本五十铃公司BE22客车后钢板弹簧疲劳寿命的标准要求。
2 BL客车后钢板弹簧的结构
BL客车后钢板弹簧为一多片半椭圆形且由主、副簧组成的变刚度钢板弹簧,总片数为12片,其中主簧9片,副簧3片,主片片厚为10mm,其余片厚为9mm,采用的弹簧钢为60Si2Mn,其中3~9片端部压延,使钢板弹簧接近等应力梁。
3 BL后钢板弹簧疲劳试验情况
3.1 试验标准:按五十铃公司提供的BE22客车后钢板弹簧疲劳寿命试验标准执行
即: 1)按实车状态夹紧;
2)变形中心:Fa=58.5mm,Fmax=137mm(2.5G),Fmin=20mm;
3)振动频率:60-120cpm;
4)从产品中随机抽取三架钢板弹簧;
5)疲劳寿命:疲劳循环次数3≥20万次。
3.2 试验设备:钢板弹簧疲劳试验机。
3.3 疲劳寿命试验结果如下:
4对钢板弹簧疲劳断裂原因分析
根据以上试验结果可以看出,疲劳断裂的簧片均在第7片且同在钢板弹簧的大卷耳端,且位置距钢板弹簧中心螺栓距离也差别不大(138、142、150),说明该钢板弹簧在此处存在规律性疲劳断裂源,而非偶然原因造成的,下面根据疲劳断裂试验结果及设计、生产过程对钢板弹簧疲劳断裂的原因进行分析。
4.1 造成钢板弹簧疲劳断裂的直接原因
根据钢板弹簧疲劳断口的断面形状进行宏观分析,发现断口的断面呈河流状,没有一般的疲劳断口所具有的疲劳源→扩展区→瞬断区三部分,说明在疲劳试验过程中微裂纹成核期相对较长,但当微裂纹聚合成较大裂纹后在此处形成应力集中,使此处的应力超过了材料的屈服极限后,裂纹即快速扩展并在很短时间内使簧片断裂。
根据金属材料的断裂力学理论可以判定:造成此种钢板弹簧疲劳断裂的直接原因是簧片在断口处受到了较大应力或材料的极限应力值达不到要求所致。
4.2 造成钢板弹簧疲劳断裂的具体原因
1) 簧片在断口的设计应力分析
钢板弹簧第1、7片应力分布如下:(注:摘自《BL后钢板弹簧设计计算书》)
I=1 σ1=59.2 σ2=4917 σ3=40 σ4=30 σ5=20 σ6=11 σ
7=117
......
I=7 σ1=37 σ2=41 σ3=44 σ4=47 σ5=17 σ6=2
......
注:I—片序σ—应力kg/mm2 各应力点为平均间隔(100mm)。
从以上簧片应力分布可以看出,在最大变形时断口处的应力值也相对较小,并从理论上讲该处也不可能产生最大应力,因此该钢板弹簧设计是合理的,不存在断口处设计应力过大的问题。
2) 簧片在断口处是否有附加应力产生除设计应力外,如果因某种原因有附加应力产生,使总应力加大也可能造成钢板弹簧片断裂,通过对断裂簧片断口处观察,发现此处在压延时造成了轻微急弯,使该片端部同上一片形成点接触,对这一点从试验后两片间的摩擦痕迹也证明了此点(如图)
断口处
由图中可以看出,当钢板弹簧承受载荷时,在断口处除承受正常的应力分配外,还承受一个附加弯曲变形所产生的应力,造成此处产生的应力值过大,超过材料的屈服极限,而使簧片在此处产生疲劳断裂,经对第7片簧片生产工序检查,使第7片簧片端部压延造成急弯属送料台稍高所至。
3) 对疲劳断裂的钢板弹簧原材料成份进行分析及金相组织进行理化分析
a对钢板弹簧采用材料的成分检验结果如下:
从材料成份分析的结果看,其各项指标均符合要求。
b对钢板弹簧理化分析结果如下:
由对钢板弹簧材料的理化结果可知:硬度及脱碳层均符合钢板弹簧标准QCn-29035-91的要求,金相组织亦符合JB3728-84《汽车钢板弹簧金相检验标准》中的要求1~5级中属4级,产品的热处理不存在问题但金相组织级别偏低。
5 结论
通过以上分析可得出引起钢板弹簧疲劳断裂的原因主要有以下两条:
1) 钢板弹簧第7片在压延端部出现轻微急弯,使簧片在该处有附加应力产生,从而使该处的总应力超过其材料的极限应力造成钢板弹簧早期断裂。
2) 钢板弹簧金相组织为回火屈氏体+少量贝氏体,虽然符合JB3782—84中合格品的要求,但要满足钢板弹簧疲劳寿命大于20万次仍属偏低。
6 改进措施
1) 调整料台高度,使符合第7片端部压延技术要求。
2) 严格控制热处理工艺,特别严格控制回火温度和回火加热时间使钢板弹簧的金相组织达到
JB3782-84标准中1~2级的要求对片厚<10mm,其回火加热时间控制在25~30分钟,回火温度控制在500~540℃,主片(10mm)回火加热时间控制在30~35分钟,获得均匀细致的回火屈氏体。
3) 增强簧片表面强化手段,将普通喷丸改为应力喷丸。
4) 如果有形变热处理工艺设备,增加形变热处理工艺,将大大提高钢板弹簧的疲劳寿命,大约可提高3~5倍。
7 效果
按照以上改进措施试制后,从其中随机抽取三架钢板弹簧进行疲劳试验所得结果如下:疲劳循环次数分别达到:22.6万次、25.7万次、23.8万次,金相组织达到1~2级标准,属中等细致的回火屈氏体,同时在达到寿命次数时,疲劳断裂的簧片在最末两片,这也完全符合钢板弹簧首先断小片的要求,断口有明显的疲劳源,且均在拉伸面,裂纹呈波纹状向外扩展,有明显的扩展区和瞬断区,完全属于正常的疲劳断裂,因此该产品完全符合日本五十铃公司BE22客车对后钢板弹簧疲劳寿命的要求。