粉末压制成形模具设计
粉末冶金模具设计
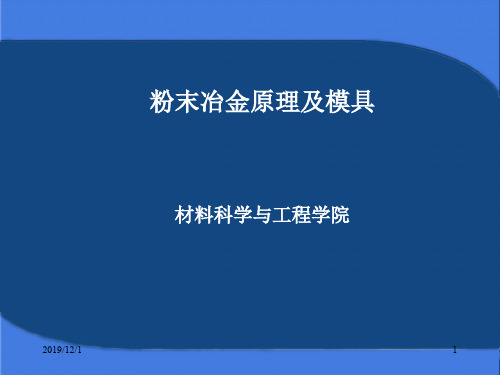
粉末移动成形法分类:侧向移动成形法和轴向移动 成形法
多台阶压坯的组合模冲设计
一般可以按照台阶分别设计模冲,以保证各横截面 上的粉末填装系数和压缩比相同或者相近。当压坯 相邻台阶的高度差较小时,可以用一个模冲来压制 这二个台阶。
当相连台阶的高度差不超过压坯较高台阶高度的
2019/12/1
33
25%时,可以采用整体模冲来压制。
m:阴模外径与内径之比; ρ:压坯的相对密度 当相对密度为:0.80~0.85时,m=2~4,可粗略 估算:
对于铁基:P侧剩=0.18~0.20P 对于铜基: P侧剩=0.20~0.22P
2019/12/1
5
•精整压力的计算
外箍内的精整: 精整压力Fc=F1+F2+F3
其中:F1为实现轴套纯变形所需要的力;
形状完整,具有一定强度
3.5 压制过程的图示
2019/12/1
2
•压制压力的计算
模压过程的总压制力等于净压力与外摩擦力 之和
单位压制压力与压坯密度定量关系的研究, 是近60年来粉末成形理论研究的主要内容
•脱模力的计算
压制压力去掉后,侧压力因为高度方向的弹 性后效,侧压力会下降35~77%
2019/12/1
影响压坯密度分布均匀性的因素:
•粉末成分和性能
•模具表面质量
•摩擦力
•压制时粉体产生柱式流动,几乎不产生明显
的横向流动 2019/12/1
8
压坯中中立层的位置可以表示压坯密度分布
的均匀程度。通过压制方式和压模结构合理
选择使中立层2边受相同压缩,提高密度分布
均匀性 2019/12/1
9
2019/12/1
2019/12/1
粉末冶金模具设计
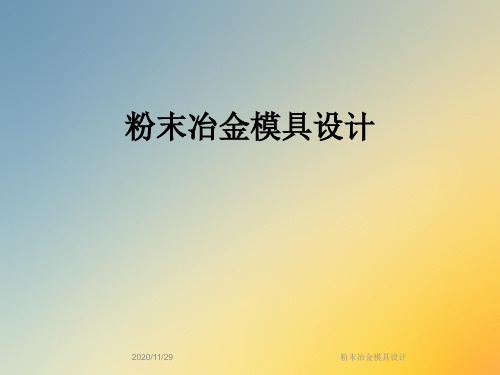
2020/11/29
粉末冶金模具设计
•带斜面的第五类压坯
当压坯斜面与垂直方向的夹角超过25°~30°,或 者具有多个斜面和平面时,一般按照斜面和平面的 分界线设计组合下模冲。斜面的装粉高度等于斜面 的压坯平均高度乘以粉末填装系数。
x=(d2-d1)h/d1
或者 y=x/l=100(d2-d1)/d1(k-1)
其中:d2为要求的压坯平均密度;d1为单向压 制的平均密度;h为压坯高度;k为压缩比;l 为装粉高度与压坯高度之差。
2020/11/29
粉末冶金模具设计
非同时双向压制原理为压模结构设计提供了 压坯密度均匀分布的理论基础;也为粉末压 机的设计提供了重要基础,使得多凸轮和凸 轮曲柄粉末压机更好地满足粉末压坯密度均 匀分布的要求。
2020/11/29
粉末冶金模具设计
摩擦压制
在压制过程中,让阴模或芯杆与样品侧面产 生同向相对移动,即运动得更快,借助粉末 与模壁之间的摩擦,带动与阴模或芯杆接触 的粉末层移动,从而可改善沿压坯高度方向 的密度分布均匀性。
2020/11/29
粉末冶金模具设计
2020/11/29
粉末冶金模具设计
2020/11/29
距离,用先压缩高区粉末再同时压缩高低区粉末的
方法,使压坯各横截面上的粉末受到相同的压缩程
度。
2020/11/29
粉末冶金模具设计
2020/11/29
粉末冶金模具设计
如果压坯中间带内、外台阶,除不同横截面需要 设计组合下模冲外,还有根据粉末移动成形法的 要求设计组合上模冲。
金属粉末注塑模具

金属粉末注塑成型结合了注塑成型的成 性优势与金属出众的物理性能。他正 在迅速成为一种金属粉末的新型生产 技术,用于需要高产量、高性能、低 成本和复杂形状的场合。
金属粉末注塑的适用范围
各种汽车、电子、电脑外围设备、医疗、 工业、军事和航空部件。
汽车应用包括涡轮增压器、刹车和点火 部件,以及氧传感器。
整理:区分物品的用途,清除不要用 的东西 。20.11. 1020.1 1.1009:3709:37 :1809:3 7:18No v-20
重视合同,规范运行,确保质量,信 誉承诺 。2020 年11月1 0日星 期二9时 37分18 秒Tues day , November 10, 2020
全员参与,强化管理,精益求精,铸 造品质 。20.11. 102020 年11月 10日星 期二9 时37分1 8秒20. 11.10
1.用量少,用较少的粘接剂能使混合 料产生较好的流变性;
2.不反应,在去除粘接剂的过程中与 金属粉末不起任何化学反应;
3.易去除,在制品内不残留碳。
脱除黏结剂的方法
⑴黏结剂热脱除方法 ⑵催化型黏结剂脱除剂 ⑶溶剂抽提方法
4.烧结
烧结是在低于基体金属熔点的温度 下加热、保温,粉末颗粒间产生扩 散、固溶、化合和熔接,致使塑件 收缩并强化。
决定混料属性的五大因素
①粉末特征 ②黏结剂组成 ③粉末–黏结比例 ④混合方法和造粒技术
粉末介 绍
金属粉末注塑机设备及工艺流程图~
①粉末选用
金属粉末颗粒尺寸一般在0.5~20μm;从理论上讲, 颗粒越细,比表面积也越大,易于成型和烧结。 而传统的粉末冶金工艺则采用大于40μm的较粗的 粉末。有机胶粘剂 有机胶粘剂作用是粘接金 属粉末颗粒,使混合料在注射机料筒中加热具有 流变性和润滑性,也就是说带动粉末流动的载体。 因此,粘接剂的选择是整个粉末的载体。因此, 粘拉选择是整个粉末注射成型的关键。
粉末冶金材料模具设计
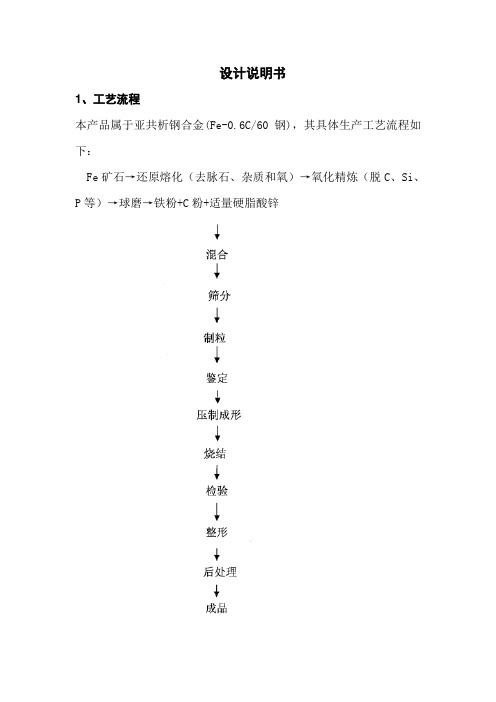
设计说明书1、工艺流程本产品属于亚共析钢合金(Fe-0.6C/60钢),其具体生产工艺流程如下:Fe矿石→还原熔化(去脉石、杂质和氧)→氧化精炼(脱C、Si、P等)→球磨→铁粉+C粉+适量硬脂酸锌2、压坯设计2.1产品零件分析该产品采用Fe-0.6C(60钢),属于铁基制品,其制品密度依靠较高的压坯密度来达到,因此,在压制成形时需要采用较高的单位压力(一般在400-500MPa)。
由于该产品零件形状比较简单,带一个外台阶,采用简单的单上双下模冲即可成形,并使其密度分布均匀。
有配合、定位、相对运动要求的零部件,产品尺寸精度和形位精度及表面粗糙度要求较高,因此,该产品的的尺寸精度定义为IT8、形位精度如图所示为7级,表面粗糙度精度要求为7级。
2.2压坯精度设计由模具设计任务书的零件成品图可得知该产品压坯同轴度需控制在0.08mm,相当于IT10级;压坯垂直度控制为0.1mm,相当于IT11级;压坯侧面平行度为0.15mm,相当于IT12级。
2.3压坯密度和单重的确定由于已知压坯密度ρ=6.6g/cm3,因此压坯单重W=ρ×V ,由成品图给数据计算其压坯体V=h×S,算的V=166.8cm3 ,所以求的压坯单重W=6.6×166.8=1100.8g。
3、压机与压制方式选择3.1压机压力选择铁基制品一般采用固相烧结,其制品密度除了依靠烧结温度、保温时间之外,在一定程度上还依靠较高的压坯密度来达到,因此该产品采用500MPa的单位压力。
根据任务书要求,截面积S=74.0cm2 ,所以F=P×S=5×74=370t脱模压力,根据实际生产经验,铁基压坯的脱模压力P脱模≈0.13P=0.13×500MPa=65MPa3.2压制类型的选择年生产量为50万件,假设每年的工作时间为300天,每天工作时间为8小时,则p=500000/300/8/60=3.47=4件/min,所以选择自动压制。
粉末冶金:钢压模具设计

好的材料 ➢ 高密度、高精度件用耐磨性好的材料 ➢ 整形模用耐磨性好的材料
绘制模具装配图和零件图
➢ 绘制模具装配图和零件图 ➢ 标注尺寸偏差和形位公差 ➢ 标注其他加工要求
绘制模具装配图和零件图
模具示例
模具示例
设计模具结构
根据制品图纸设计坯件,选择压机和压制方式,设计 模具结构草图 ➢ 从生产工艺、压制成形和经济成本方面分析制品图纸 及技术要求,看是否适于用粉末冶金方法生产 ➢ 根据制品图纸及技术要求和粉末冶金生产工艺的特点, 设计坯件的几何形状、精度和密度 ➢ 为了使制品适于压制成形,或为了简化模具结构,常 对制品形状进行修改,设计出适合于压制的压坯 ➢ 在设计坯件形状的同时要确定压制方向,然后根据压 坯的形状、高径比、生产批量和压机来选择压制方式、 压模结构类型
粉末成形模具分类
➢ 压模、精整模、复压模、锻模、挤压模、 热压模、等静压模、粉浆浇注模、松装 烧结模
➢ 钢模、硬质合金模、石墨模、塑料橡皮 模和石膏模
钢压模具结构
钢压模具一般由 阴模、模冲、芯棒 组成
钢压模具结构
1—模柄 2,9—法兰圈 3—上模冲 4—模套 5—阴模 6—模座 7—弹簧 8—下模冲 10—下模冲座 11—压垫 12—下模板 13—顶杆 14—顶板
➢ 制品生产工艺流程及工艺参数:粉末混合料成分、杜 装密度、流动性、压制性、单位压制压力、压坯密度、 压缩比、弹性后效、烧结收缩率、精整余量、机加工 余量、复压装模间隙和压下率等
➢ 压机类型及主要技术参数:公称压力、脱模压力、压 机行程、每分钟压制次数、工作台面积、压机自动化 程度和安全保险装置等
粉末冶金模具设计说明书

粉末冶金模具设计说明书粉末冶金模具设计说明书一、设计任务生产一批两个台阶面的钢制模坯,如图所示,数据要求:A=10mm,B=30mm,C=20mm,D=20mm,E=10 mm,F=10mm。
二、压坯设计1.产品零件分析该产品采用Fe-0.05C(50钢),属于铁基制品,其制品密度依靠其较高的压坯密度来达到,因此在压制成型时需要采用较高的单位压力(一般在300~800MPa)。
由于该产品零件形状比较简单,采用简单的上下模冲压制成型。
2.松装密度和压坯密度的确定采用水雾化铁粉压制,松装密度范围2.5~3.2,取常用值2.8,即松装密度:ρ松=2.8g/cm3压坯密度:γ压=6.6g/cm3压缩比:C=γ/ρ=2.36三、压制成形与压力机确定1.压制压力的选择采用500MPa 的单位压力,由已知可得压坯截面积22222S=(B (3010)62844mm ππ-=-A )= 则其压制力F=p×S=500MPa×628mm 2=314kN脱模压力F 脱=ƒ´p 侧余S 侧=0.2×100×1570=31.4kNƒ´——粉末对阴模壁的静摩擦系数,此处ƒ´=0.2p 侧余——残余侧压力,此处p 侧余=0.2p=0.2×500MPa=100MPa S 侧——侧面积, S 侧=πEB+πFC=3.14(10×30+10×20)=1570mm 2侧压力p 侧 =ξp=p ν/(1-ν)=0.38×500MPa=190MPa2.装粉高度确定带台阶面压坯成形模具的设计原则 1)粉末充填系数相同或相近 2)压缩比相同或相近 压缩比 C=γ/ρ=2.36装粉台阶高度 E 0=CE=2.36×10mm=23.6mm装粉总高度D 0=C(E+F)=2.36×20mm=47.2mm2.1压坯高度验算 max max 2.8(10)(18510)74.26.6H F mm ργ=-=⨯-= ——F max =185mm (设计手册表4-20TPA50/2压力机的最大装料高度)H=D 0=47.2mm<H max 可行 3.压制方式的选择c31406286628S S K S++===侧f 侧S 侧f =πD(B+C)=3140mm 2 S 侧c =πDA =628mm 2 K>单向K max =5(ƒ=0.1,表3-5),压坯有台阶面,选择双向压制。
粉末压制成形模具设计

表1金属粉末压制成形坯料计算
计算内容
定义或计算公式
有关说明
压制坯在垂直于压制
压制坯面积Fp(cm2) 方向的平面的投影面
-
积
压制坯体积Vp(cm3)
Vp=(1+ξ/100)Ve
芯棒磨损余 量
Δd=dn′-dn-δa δa—芯棒尺寸实际偏差量
后续精压芯
=dmax±lrp
棒直径(孔 “+”—精压后回弹使孔径减小时
件) “-”—精压后回弹使孔径增大时
烧结坯内尺 寸
压制坯内尺 寸
ds=drp±ηrp “+”—为负偏差精压时
“-”—为正偏差精压时
dp=ds±ε “+”—烧结后内尺寸减小时 “-”—烧结后内尺寸增大时
2.凹模预应力圈尺寸
为了提高压制成形模具的寿命,并
保证压制件的尺寸精度,凹模常采用预
应力圈结构,如图2所示。其尺寸取决于
压制时凹模内壁所承受的侧压力大小。
对于铁粉末压制,其侧压力可按经验公
式估算:
pc=Ccρmp
(9)
式中Cc=0.00725,m=6.8
而预应力圈的尺寸,必须保证凹模具有最大刚度,设凹模筒内半径为r1, 则有:
其他参数
而在进行压制成形模具设计时,还需知道以下 参数:
(1)预先给定的粉末压制坯的密度ρp; (2)压制(和后续塑性加工)后制件线回弹量,用相 对值αp(αrp)或绝对量lp(lrp)表示; (3)制件烧结后的线收缩量,用相对值β或绝对量 ε表示; (4)烧结氧化或其他原因引起的质量损耗量,用 相对值ζ表示; (5)后续塑性加工引起的制件密度增加量,用相 对值τ表示。
粉末模压成型工艺
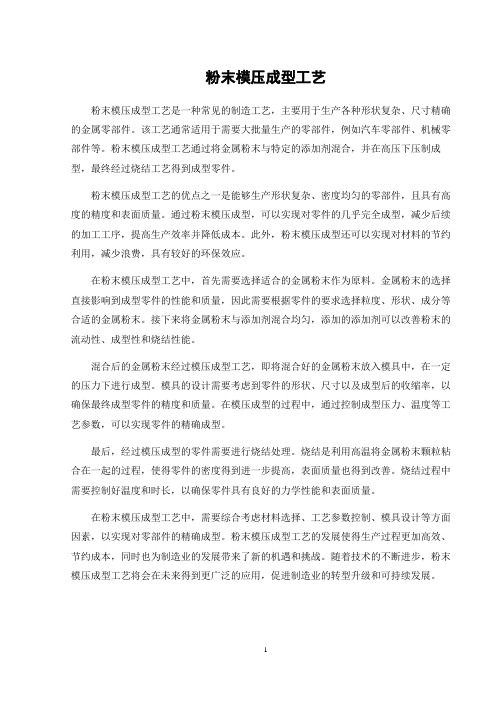
粉末模压成型工艺粉末模压成型工艺是一种常见的制造工艺,主要用于生产各种形状复杂、尺寸精确的金属零部件。
该工艺通常适用于需要大批量生产的零部件,例如汽车零部件、机械零部件等。
粉末模压成型工艺通过将金属粉末与特定的添加剂混合,并在高压下压制成型,最终经过烧结工艺得到成型零件。
粉末模压成型工艺的优点之一是能够生产形状复杂、密度均匀的零部件,且具有高度的精度和表面质量。
通过粉末模压成型,可以实现对零件的几乎完全成型,减少后续的加工工序,提高生产效率并降低成本。
此外,粉末模压成型还可以实现对材料的节约利用,减少浪费,具有较好的环保效应。
在粉末模压成型工艺中,首先需要选择适合的金属粉末作为原料。
金属粉末的选择直接影响到成型零件的性能和质量,因此需要根据零件的要求选择粒度、形状、成分等合适的金属粉末。
接下来将金属粉末与添加剂混合均匀,添加的添加剂可以改善粉末的流动性、成型性和烧结性能。
混合后的金属粉末经过模压成型工艺,即将混合好的金属粉末放入模具中,在一定的压力下进行成型。
模具的设计需要考虑到零件的形状、尺寸以及成型后的收缩率,以确保最终成型零件的精度和质量。
在模压成型的过程中,通过控制成型压力、温度等工艺参数,可以实现零件的精确成型。
最后,经过模压成型的零件需要进行烧结处理。
烧结是利用高温将金属粉末颗粒粘合在一起的过程,使得零件的密度得到进一步提高,表面质量也得到改善。
烧结过程中需要控制好温度和时长,以确保零件具有良好的力学性能和表面质量。
在粉末模压成型工艺中,需要综合考虑材料选择、工艺参数控制、模具设计等方面因素,以实现对零部件的精确成型。
粉末模压成型工艺的发展使得生产过程更加高效、节约成本,同时也为制造业的发展带来了新的机遇和挑战。
随着技术的不断进步,粉末模压成型工艺将会在未来得到更广泛的应用,促进制造业的转型升级和可持续发展。
1。
粉体成形模具设计课件
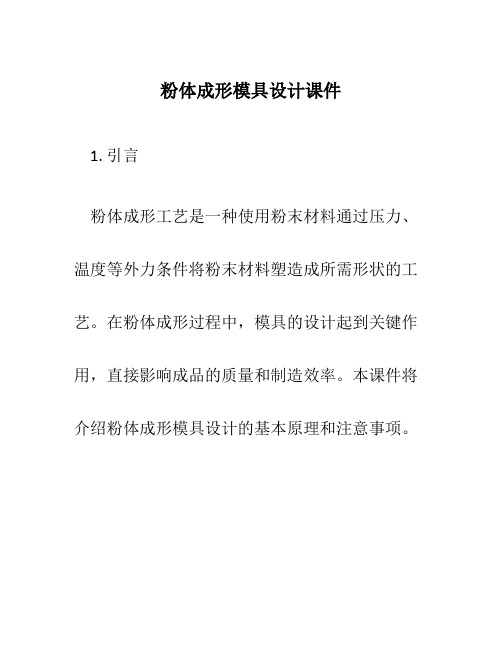
粉体成形模具设计课件1. 引言粉体成形工艺是一种使用粉末材料通过压力、温度等外力条件将粉末材料塑造成所需形状的工艺。
在粉体成形过程中,模具的设计起到关键作用,直接影响成品的质量和制造效率。
本课件将介绍粉体成形模具设计的基本原理和注意事项。
2. 粉体成形模具的分类根据粉体成形工艺的特点和要求,粉体成形模具可以分为压制模具、注射模具、挤压模具等。
各种模具在设计上有一些共性,但也有一些独特的要求。
2.1 压制模具设计要点压制模具用于将粉末材料在一定温度和压力下压制成形。
其设计要点包括: - 模具结构设计:模具应具有足够的刚性和稳定性,以承受高压下的冲击力和变形力,并保证成品的形状和尺寸精度。
- 凸模和凹模设计:凸模应具有充分的刚性和耐磨性,凹模则需考虑排料和顶出等因素。
- 压头设计:压头应根据成品形状的复杂程度和压制力的大小进行合理设计。
2.2 注射模具设计要点注射模具用于将粉末材料注入到模腔中,通过压力和温度使其固化成形。
其设计要点包括: - 模具结构设计:注射模具应具有较高的刚性和耐磨性,以承受注射时的压力和冲击力。
- 模腔设计:模腔应根据产品的形状和尺寸合理设计,以确保成品的几何形状和尺寸精度。
- 引导系统设计:引导系统用于将粉末材料引导到模腔中,其设计要考虑粉末流动性和材料浇注的均匀性等因素。
2.3 挤压模具设计要点挤压模具用于将粉末材料在挤压机内通过挤压头挤出,并在模具中固化成形。
其设计要点包括:- 模具结构设计:挤压模具要求具有足够的刚性和稳定性,以承受挤压时的冲击力和变形力。
- 模腔设计:模腔应根据挤压头和产品的形状合理设计,以确保挤压成品的形状和尺寸精度。
- 冷却系统设计:冷却系统用于快速降低模具温度,以便加快成品的固化速度和提高生产效率。
3. 粉体成形模具设计步骤粉体成形模具设计一般包括以下几个步骤:3.1 确定产品形状和尺寸根据产品的要求和实际应用,确定所需的形状和尺寸。
粉末压制成形模具设计.ppt
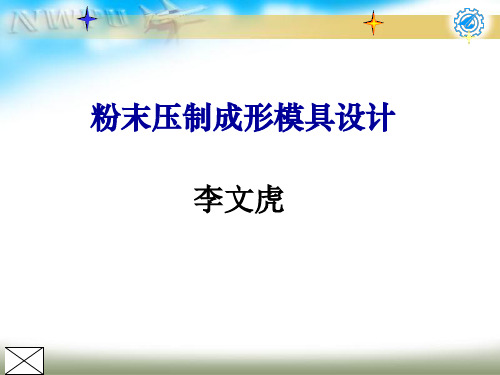
式估算:
pc=Ccρmp
(9)
式中Cc=0.00725,m=6.8
而预应力圈的尺寸,必须保证凹模具有最大刚度,设凹模筒内半径为r1, 则有:
当pc≤200MPa时, r2=2r1,r3=4r1 当pc>200MPa时: r3=(pc/140+0.67)r1,
r2=(r1 r3) ½
(10a) (10b)
3.模具受力件的强度校核
(1)冲头一般处于压应力状 态,其强度校核式为:
σ=P/Fmin≤[σ] (14) 式中:P—金属粉末压制力 Fmin—冲头最小截面积 [σ]—淬硬钢许用压应力
(2)对支承模座和固定板也需
进行抗压强度校核:
σ=P/F≤[σ]
(15)
通常,与冲头模座投影面积
相当的中间固定板其厚度可
压制坯的计算,其实质就是根据所加工的粉 末零件,决定压制坯的体积、质量和相关尺寸, 以确定压制凹模型腔的尺寸和检验压制坯的尺寸 精度。
表1金属粉末压制成形坯料计算
计算内容
定义或计算公式
有关说明
压制坯在垂直于压制
压制坯面积Fp(cm2) 方向的平面的投影面
-
积
压制坯体积Vp(cm3)
Vp=(1+ξ/100)Ve
取5~8mm。
(3)当细长型冲头(多为下冲头)和芯棒的长径比L/d≥3时,还需进行抗弯
强度校核
(a)计算纵向弯曲失稳临界载荷
的长度,等于从冲头固定板到冲头导入凹模部分中间
位置和距离 ;
Jmin—冲头最小截面矩 ;
E—工具钢材料的弹性模量,一般可取E=2.15×105MPa ;
Pcr—产生纵向失稳的临界载荷 . (b)选取冲头的抗弯安全系数:
金属粉末压制成型中的模具设计优化
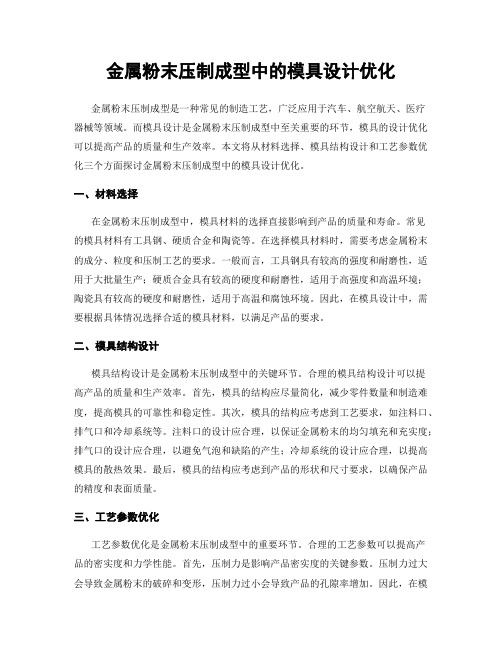
金属粉末压制成型中的模具设计优化金属粉末压制成型是一种常见的制造工艺,广泛应用于汽车、航空航天、医疗器械等领域。
而模具设计是金属粉末压制成型中至关重要的环节,模具的设计优化可以提高产品的质量和生产效率。
本文将从材料选择、模具结构设计和工艺参数优化三个方面探讨金属粉末压制成型中的模具设计优化。
一、材料选择在金属粉末压制成型中,模具材料的选择直接影响到产品的质量和寿命。
常见的模具材料有工具钢、硬质合金和陶瓷等。
在选择模具材料时,需要考虑金属粉末的成分、粒度和压制工艺的要求。
一般而言,工具钢具有较高的强度和耐磨性,适用于大批量生产;硬质合金具有较高的硬度和耐磨性,适用于高强度和高温环境;陶瓷具有较高的硬度和耐磨性,适用于高温和腐蚀环境。
因此,在模具设计中,需要根据具体情况选择合适的模具材料,以满足产品的要求。
二、模具结构设计模具结构设计是金属粉末压制成型中的关键环节。
合理的模具结构设计可以提高产品的质量和生产效率。
首先,模具的结构应尽量简化,减少零件数量和制造难度,提高模具的可靠性和稳定性。
其次,模具的结构应考虑到工艺要求,如注料口、排气口和冷却系统等。
注料口的设计应合理,以保证金属粉末的均匀填充和充实度;排气口的设计应合理,以避免气泡和缺陷的产生;冷却系统的设计应合理,以提高模具的散热效果。
最后,模具的结构应考虑到产品的形状和尺寸要求,以确保产品的精度和表面质量。
三、工艺参数优化工艺参数优化是金属粉末压制成型中的重要环节。
合理的工艺参数可以提高产品的密实度和力学性能。
首先,压制力是影响产品密实度的关键参数。
压制力过大会导致金属粉末的破碎和变形,压制力过小会导致产品的孔隙率增加。
因此,在模具设计中,需要根据金属粉末的特性和产品的要求确定合适的压制力。
其次,压制速度是影响产品力学性能的关键参数。
压制速度过快会导致金属粉末的流动不均匀,压制速度过慢会导致产品的变形和裂纹。
因此,在模具设计中,需要根据金属粉末的流动性和产品的要求确定合适的压制速度。
粉末冶金模具设计

2020/3/25
13
2020/3/25
14
2020/3/25
15
•压制方式的选择依据
压制方式和方法不同,上、下模冲、芯杆和阴 模相对于粉末压坯的相对运动方向及速度也不 同,从而使外摩擦对压坯密度的均匀分布产生 有害或者有利的影响。
单向压制
S侧max/S=[1-(ρ下/ρ上)m]/μξ=K
当柱状压坯S侧/S<K或者圆柱体压坯高径比 H/D<K/4时,采用单向压制可以满足压坯密度 分布均匀性的要求
压制时,成形主体的下模冲向上推移粉末,或者 成形台阶的上模冲将粉末和成形台阶的浮动下模 冲向下推移,或者利用组合上模冲将粉末和带内 台阶浮动阴模或芯杆向下推移,把台阶部分的粉 末推到所要求的位置。
2020/3/25
31
•带斜面的第五类压坯
当压坯斜面与垂直方向的夹角超过25°~30°,或 者具有多个斜面和平面时,一般按照斜面和平面的 分界线设计组合下模冲。斜面的装粉高度等于斜面 的压坯平均高度乘以粉末填装系数。
压力相等时双向压制与非同时双向压制的效 果相同
非同时双向压制中第二次压制的模冲移动距 离:
x=(d2-d1)h/d1
或者 y=x/l=100(d2-d1)/d1(k-1)
其中:d2为要求的压坯平均密度;d1为单向压 制的平均密度;h为压坯高度;k为压缩比;l 为装粉高度与压坯高度之差。
2020/3/25
形状完整,具有一定强度
3.5 压制过程的图示
2020/3/25
2
•压制压力的计算
模压过程的总压制力等于净压力与外摩擦力 之和
单位压制压力与压坯密度定量关系的研究, 是近60年来粉末成形理论研究的主要内容
金属粉末注塑模具

金属粉末注塑模具1. 引言金属粉末注塑模具是一种用于制造金属注塑件的工具。
它通过将金属粉末与粘合剂混合,并将混合物充填到模具中,然后在高温和高压下进行注塑成型。
由于其独特的制造工艺,金属粉末注塑模具广泛应用于各种领域,如汽车制造、航空航天、医疗器械等。
本文将介绍金属粉末注塑模具的工作原理、制造工艺以及优势等方面内容。
2. 工作原理金属粉末注塑模具的工作原理主要包括以下几个步骤:2.1. 混合金属粉末和粘合剂首先,将所需的金属粉末与粘合剂按一定比例混合。
金属粉末可以是不同种类的金属粉末,如铝粉、钛粉、不锈钢粉等,而粘合剂可以是有机聚合物、蜡等。
2.2. 充填模具将混合好的金属粉末和粘合剂充填到注塑模具中。
注塑模具的设计通常根据所需要制造的金属注塑件的形状和尺寸来确定。
2.3. 高温和高压注塑成型将充填好金属粉末和粘合剂的模具置于注塑机中。
注塑机会将模具加热到适当的温度,并施加高压力将金属粉末和粘合剂压缩成实心坯料。
2.4. 去除粘合剂经过注塑成型后,金属粉末注塑件通常还会含有一定比例的粘合剂。
在后续的工艺步骤中,通过烧结、溶解或其他方法去除粘合剂,从而得到纯金属注塑件。
3. 制造工艺金属粉末注塑模具的制造工艺主要包括模具设计、模具制造以及模具调试等环节。
首先,根据所需要制造的金属注塑件的形状和尺寸,进行模具设计。
设计包括模具的结构设计、孔位设计、喷嘴设计等。
模具的设计必须满足金属注塑件的形状要求,同时考虑到生产效率和经济性。
然后,根据设计图纸制造模具。
模具制造过程中需要使用机床、电火花、车削等工艺设备进行加工。
模具材料通常选用高硬度的金属材料,如工具钢、硬质合金等。
最后,进行模具调试。
调试过程中需要调整模具的温度、压力等参数,以确保金属粉末注塑件的质量和形状满足要求。
4. 优势金属粉末注塑模具相比其他金属加工工艺具有以下几个优势:4.1. 精密度高金属粉末注塑模具可以制造出形状复杂、尺寸精确的金属注塑件。
粉末冶金模具设计说明书
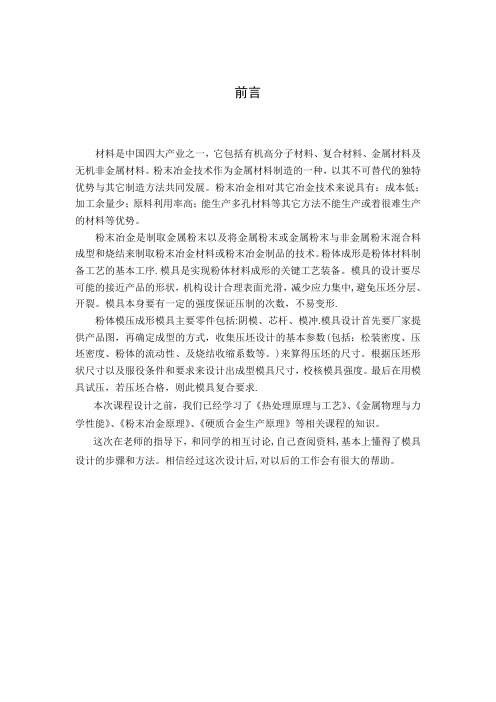
前言材料是中国四大产业之一,它包括有机高分子材料、复合材料、金属材料及无机非金属材料。
粉末冶金技术作为金属材料制造的一种,以其不可替代的独特优势与其它制造方法共同发展。
粉末冶金相对其它冶金技术来说具有:成本低;加工余量少;原料利用率高;能生产多孔材料等其它方法不能生产或着很难生产的材料等优势。
粉末冶金是制取金属粉末以及将金属粉末或金属粉末与非金属粉末混合料成型和烧结来制取粉末冶金材料或粉末冶金制品的技术。
粉体成形是粉体材料制备工艺的基本工序.模具是实现粉体材料成形的关键工艺装备。
模具的设计要尽可能的接近产品的形状,机构设计合理表面光滑,减少应力集中,避免压坯分层、开裂。
模具本身要有一定的强度保证压制的次数,不易变形.粉体模压成形模具主要零件包括:阴模、芯杆、模冲.模具设计首先要厂家提供产品图,再确定成型的方式,收集压坯设计的基本参数(包括:松装密度、压坯密度、粉体的流动性、及烧结收缩系数等。
)来算得压坯的尺寸。
根据压坯形状尺寸以及服役条件和要求来设计出成型模具尺寸,校核模具强度。
最后在用模具试压,若压坯合格,则此模具复合要求.本次课程设计之前,我们已经学习了《热处理原理与工艺》、《金属物理与力学性能》、《粉末冶金原理》、《硬质合金生产原理》等相关课程的知识。
这次在老师的指导下,和同学的相互讨论,自己查阅资料,基本上懂得了模具设计的步骤和方法。
相信经过这次设计后,对以后的工作会有很大的帮助。
1 设计任务本课程设计的任务是生产一批有色金属扁材拉制模坯,其形状和尺寸如下图:1.1 产品分析由产品图可知H/D 〈3,因此,该产品适合单向压制.产品的斜边角度不大,因此,装粉比较容易,可用单从头压制。
产品内部的斜角可直接做在芯杆上。
菱角的倒角不长,可适合用上冲头压制。
1。
2 材质的选择该模具生产的产品用于拉制模坯,对产品的强度及耐磨性能要求很高,再根据客户所提供的要求,综合考虑选用硬质合金材料YG8作为材质.2 压坯设计2.1 压坯形状设计型号 D H a b h h 1 h 2 R r e 42—14×5。
- 1、下载文档前请自行甄别文档内容的完整性,平台不提供额外的编辑、内容补充、找答案等附加服务。
- 2、"仅部分预览"的文档,不可在线预览部分如存在完整性等问题,可反馈申请退款(可完整预览的文档不适用该条件!)。
- 3、如文档侵犯您的权益,请联系客服反馈,我们会尽快为您处理(人工客服工作时间:9:00-18:30)。
(b)选取冲头的抗弯安全系数:
对于淬硬钢冲头,一般可取 P/Pcr≤n=2~3 (c)确定冲头最大允许长度: L≤(2∏EJmin/nP)1/2 (17) (18)
坯料
压制坯外 尺寸
_ 三 、压制力与凹模预应力圈尺寸 p:金属粉末平均单位流动压力,由压制 实验曲线或实际经验确定 F:压制坯截面积 1.压制力、顶出力和设备吨位 n:压制模中型腔数量(对一次多件压制)
P=nF
PT=CpP Pout=μFcpc
(6)
(7)
Cp—压力机吨位裕度系数,Cp=1.25~1.30 压制后制件的顶出力由侧压力pc、粉体侧表 面面积Fc和粉体与模壁的摩擦系数μ(=0.1~ 0.2)确定
H0—总装料高度
hh—上冲头导入长度hl—下冲头导入长度 对于固定式结构,由于凹模本身沿高度方向具有分 配粉料的作用,因此可以不考虑上、下冲头的导入部分 (见图1b),则 Hd=H0 (5)
2.凹模型腔与芯棒工作尺寸
凹模型腔的工作尺寸主要决定于粉末零件 的外尺寸,同时必需考虑粉末体在压制、烧结、 后续精压等工序这些外尺寸变化,以及凹模最 大允许磨损量;
冲头调节;
(3)固定式:专用压力机上大批量金属粉末件压制成 形所采用的结构型式。
2.模具封闭高度
如图3所示,当采用固定式模具 结构时,上冲头既可采用固定 式,也可采用浮动式。 其总高度可确定为: Lh=hht+h1+h2。 (12) 式中: hht,hlt—上、下冲头固定板的厚度 h1,h4—分别为上冲头压制和下冲 头顶出行程 h2—压力机在下死点时凹模上端面 与上冲头固定板下端面之间的距离 h3—下冲头导入凹模筒部分的长度
上述回弹与收缩量等的相对值可按下式换 算成绝对值:
lp=αp· /100; b
lrp=αrp· b/100;
(1)
(2)
ε = β· b/100
式中:b—制件的线尺寸
(3)
αp,αrp,β值预先给出。
2.确定压制成形方法
具备了上述技术资料和数据后,可根据实际
生产条件,选择压制设备型式以及相应的压制方
压制坯在垂直于压制 压制坯面积Fp(cm2) 方向的平面的投影面 积 压制坯体积Vp(cm3) 压制坯质量Gp(kg) 装粉质量G0(kg) 压制坯高度Hp(mm) Vp=(1+ξ/100)Ve Gp=ρpVp G0=CmGp Hp=H-lp+ε+Δm
装粉高度H0(mm)
H0=KρHp
Kρ—粉末压实系数, Kρ=ρp/ρ0
芯棒工作尺寸(mm) 计算公式与说明
表凹 2模 金型 属腔 粉与 末芯 压棒 制的 成工 形作 模尺 具寸
型腔名义 尺寸
芯棒名义 尺寸
芯棒最大 允许尺寸
dn=dmax-lp±ε±ηrp±lrp dmax—芯棒最大尺寸
dn′=dmin-lp±ε±ηrp±lrp dmin=d+δl—芯棒最小允许尺寸 d—零件孔径;δ1—孔径下偏差
二 、凹模与芯棒的工作尺寸
1、凹模总高度
所确定的尺寸包括凹模总高度、 凹模型腔及芯棒的工作尺寸
凹模各段的装料高度应与制件中相对应的各段高度成比例,以保证压 制坯密度分布均匀化。而凹模的总高度则主要取决于其装料高度,同时还要 考虑上、下冲头进入凹模的导向部分,如图1a所示。
Hd=H0+hh+hl 式中Hd—凹模总高度 (4)
芯棒磨损余 量
Δd=dn′-dn-δa δa—芯棒尺寸实际偏差量
后续精压芯 drp=dmax±lrp 棒直径(孔 “+”—精压后回弹使孔径减小时 件) “-”—精压后回弹使孔径增大时 烧结坯内尺 寸 压制坯内尺 寸 ds=drp±ηrp “+”—为负偏差精压时 “-”—为正偏差精压时 dp=ds±ε “+”—烧结后内尺寸减小时 “-”—烧结后内尺寸增大时
同样,下冲头的总高度为: Ll=hlt+h3+h4 (13)
3.模具受力件的强度校核
(1)冲头一般处于压应力状 (2)对支承模座和固定板也需
态,其强度校核式为:
ζ=P/Fmin≤[ζ] (14)
进行抗压强度校核:
ζ=P/F≤[ζ] (15)
式中:P—金属粉末压制力 Fmin—冲头最小截面积 [ζ]—淬硬钢许用压应力
法,并选好压制方向。
3.压制坯的计算 压制坯的计算,其实质就是根据所加工的粉 末零件,决定压制坯的体积、质量和相关尺寸, 以确定压制凹模型腔的尺寸和检验压制坯的尺寸 精度。
表1金属粉末压制成形坯料计算
计算内容 定义或计算公式 有关说明
ξ—相对质量损耗量; Ve—零件体积 ρp—压制件平均密度 系数Cm=1.02~1.05,考虑 了装粉及压制时的质量损失 H—粉末零件尺寸, Δm—机加工余量, lp,ε的意义见上
(8)
pc=Ccρmp
2.凹模预应力圈尺寸
为了提高压制成形模具的寿命,并 保证压制件的尺寸精度,凹模常采用预 应力圈结构,如图2所示。其尺寸取决于 压制时凹模内壁所承受的侧压力大小。 对于铁粉末压制,其侧压力可按经验公 式估算: pc=Ccρmp (9) 式中Cc=0.00725,m=6.8
而预应力圈的尺寸,必须保证凹模具有最大刚度,设凹模筒内半径为r1, 则有: 当pc≤200MPa时,
r2=2r1,r3=4r1
当pc>200MPa时: r3=(pc/140+0.67)r1, r2=(r1 r3) ½
(10a)
(10b)
此时,凹模与预应力圈的过盈量为:
△=2pcr2/E
(11)
四 、压制模具的结构设计及其强度校核
1.模具结构形式
(1)组合式:适用于批量不大的金属粉末件压制成形 ,凹模内各段的装粉高度由相应的冲头垫块来调节; (2)固定式:适用于在通用压力机上小批量金属粉末 件压制成形,凹模内各段的装粉高度由浮动模座上的
通常,与冲头模座投影面积
相当的中间固定板其厚度可 取5~8mm。
(3)当细长型冲头(多为下冲头)和芯棒的长径比L/d≥3时,还需进行抗弯
强度校核 (a)计算纵向弯曲失稳临界载荷
Pcr=2∏EJmin/L2
位置和距离 ;
(16)
L—冲头自由部分的长度,等于从冲头固定板到冲头导入凹模部分中间
Jmin—冲头最小截面矩 ;
粉末压制成形模具设计 李文虎
一 、金属粉末的工艺特性和材料性能参数 与压制坯计算
1.金属粉末的工艺特性和材料性能参数
在制定金属粉末压制成形工艺时,其基本特性参数有:
(1)粉末松装(或摇实)密度,即压制前金属粉末在凹模
内的平均密度ρ0; (2)粉末的可压缩性,按实验数据或有关标准确定; (3)粉末的可变形程度,按实验数据或有关标准确定; (4)粉末流动应力。
压制 模具
型腔最大 允许尺寸
后续 精压
型腔磨损 余量 型腔名义 尺寸
型腔最大 允许尺寸 烧结坯外 尺寸
ΔD=Dn′-Dn-δA δA—型腔尺寸实际偏差量 Drpmin=Dmin-lrp
Drpmax=Dmax-lrp Ds=Dmin±ηrp “+”—为正偏差精压时 “-”—为负偏差精压时 Dp=Ds±ε “+”—粉体烧结后收缩时 “-”—粉体烧结后膨胀时
而芯棒的工作尺寸则主要取决于零件的内
尺寸,同样也要考虑其内尺寸在各工序的变化, 并按零件的上极限偏差确定,以保证芯棒留有 最大的磨损余量。具体计算如表2所示。
凹模型腔工作尺寸(mm) 尺寸名称 计算公式与说明 Dn=Dmin-lp±ε±ηrp Dmin—零件最小允许尺寸 ηrp—后续精压余量 Dn′=Dmax-lp±ε±ηrp Dmax—还需知道以下 参数: (1)预先给定的粉末压制坯的密度ρp; (2)压制(和后续塑性加工)后制件线回弹量,用相 对值αp(αrp)或绝对量lp(lrp)表示; (3)制件烧结后的线收缩量,用相对值β或绝对量 ε表示; (4)烧结氧化或其他原因引起的质量损耗量,用 相对值ζ表示; (5)后续塑性加工引起的制件密度增加量,用相 对值η表示。