间歇生产过程安全控制分析(新编版)
我对近阶段生产组织问题分析及措施(最终版)

我对近阶段生产组织问题分析及措施(最终版)第一篇:我对近阶段生产组织问题分析及措施(最终版)我对近阶段生产组织问题分析及措施自7月份以来,采矿场生产任务和计划相比完成的很不理想,7月份欠产1500吨,8月份欠产4000多吨,9月上旬依然没有达到日均950吨的计划目标。
除去8月份因井下涌水影响近3000吨出矿量外,8月份因采矿场自身组织问题依然欠产1000多吨,为此,采矿场多次召开各个层次的会议。
分析查找原因,制定和落实措施,期望尽快扭转生产组织的不利局面。
作为部门党政主要负责人,今天民主生活会,我要分析一下自己在采矿场生产组织管理中存在的主观问题和承担的管理责任及整改措施。
希望参会的领导和各位同事对我没有认识到问题及时提出来,以利于进一步改进我的管理工作,进一步改进采矿场的各项管理工作,达到和超额完成公司的安全生产任务,同时,也能够使员工在提升绩效的基础上获得更好的收入。
一、采矿场生产组织不力的主观原因1、劳动纪律管理松懈,迟到早退现象时有发生少部分和生产密切相关的班组存在班组长随意安排休息现象,降低了劳动效率。
同时操检结合工作在部分班组执行不力,机电设备故障修复时配合不力,延长了修复时间。
2、维修人员技术责任心不强或技术水平差,维修工作拖拉,不能在最短的时间内修复。
3、部分信号操作人员责任心缺乏或操作技能低,也是造成井口操车设备故障多发的原因之一。
4、采矿场调度员管理组织协调不力,出现问题时不能及时协调当班各方力量,督促快速处理,没有充分行使采矿场赋予的权利,遇到问题就汇报分管生产领导,等领导协调。
5、机电设备管理人员(班组长)对生产任务的紧迫性认识不到位,出现故障维护时间观念不强,出现问题时有拖拉和延误现象。
考虑到这些同志是工作骨干,考核时没有严格按制度考核。
6、生产班组员工大局意识不强,对生产任务的紧迫性认识不到位,少部分员工存在对绩效考核结果无所谓的态度,工作积极性和责任心较差。
二、本人承担的管理责任1、承担劳动纪律管理松懈,检查、处罚不力主要责任。
生产现场不安全行为起因分析与控制
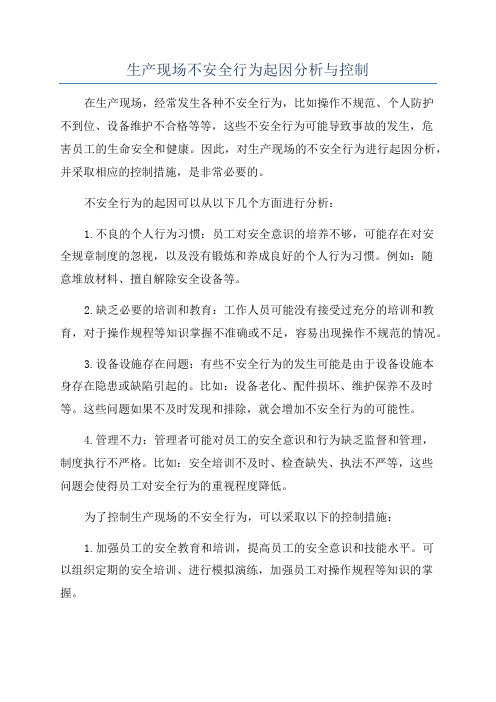
生产现场不安全行为起因分析与控制在生产现场,经常发生各种不安全行为,比如操作不规范、个人防护不到位、设备维护不合格等等,这些不安全行为可能导致事故的发生,危害员工的生命安全和健康。
因此,对生产现场的不安全行为进行起因分析,并采取相应的控制措施,是非常必要的。
不安全行为的起因可以从以下几个方面进行分析:1.不良的个人行为习惯:员工对安全意识的培养不够,可能存在对安全规章制度的忽视,以及没有锻炼和养成良好的个人行为习惯。
例如:随意堆放材料、擅自解除安全设备等。
2.缺乏必要的培训和教育:工作人员可能没有接受过充分的培训和教育,对于操作规程等知识掌握不准确或不足,容易出现操作不规范的情况。
3.设备设施存在问题:有些不安全行为的发生可能是由于设备设施本身存在隐患或缺陷引起的。
比如:设备老化、配件损坏、维护保养不及时等。
这些问题如果不及时发现和排除,就会增加不安全行为的可能性。
4.管理不力:管理者可能对员工的安全意识和行为缺乏监督和管理,制度执行不严格。
比如:安全培训不及时、检查缺失、执法不严等,这些问题会使得员工对安全行为的重视程度降低。
为了控制生产现场的不安全行为,可以采取以下的控制措施:1.加强员工的安全教育和培训,提高员工的安全意识和技能水平。
可以组织定期的安全培训、进行模拟演练,加强员工对操作规程等知识的掌握。
2.建立健全的安全检查和管理制度,加大对生产现场的监督和管理力度。
制定操作规程和安全标准,明确员工的责任和义务,对违章作业进行及时纠正和处理。
3.加强设备设施的维护和保养,及时排除存在的安全隐患和缺陷。
定期对设备进行检测和维修,确保设备的正常运行和使用安全。
4.建立和完善事故报告和分析制度,对每起事故进行详细的调查和分析,查找事故的原因和责任,并采取相应的控制措施,防止类似事故再次发生。
5.倡导员工主动参与安全管理,设立安全奖惩制度,提高员工对安全行为的重视程度。
定期开展安全宣传活动,引起员工的关注和参与,形成全员参与的安全文化。
间歇生产过程安全控制分析实用版
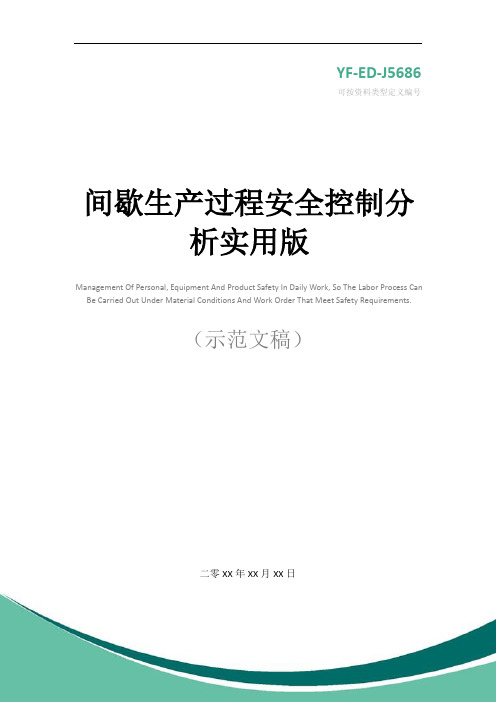
YF-ED-J5686可按资料类型定义编号间歇生产过程安全控制分析实用版Management Of Personal, Equipment And Product Safety In Daily Work, So The Labor Process Can Be Carried Out Under Material Conditions And Work Order That Meet Safety Requirements.(示范文稿)二零XX年XX月XX日间歇生产过程安全控制分析实用版提示:该安全管理文档适合使用于日常工作中人身安全、设备和产品安全,以及交通运输安全等方面的管理,使劳动过程在符合安全要求的物质条件和工作秩序下进行,防止伤亡事故、设备事故及各种灾害的发生。
下载后可以对文件进行定制修改,请根据实际需要调整使用。
一、控制条件分析在工业控制方面,间歇生产过程同连续生产过程相同都要满足:①安全生产;②设备工艺指标和产品质量指标;③环保法规;④经济指标等基本要求。
在生产过程中,间歇过程也同样要求有对参数的调节控制功能。
特别是在诸如反应器的平稳反应阶段,精馏操作中某单一组分平稳馏出阶段,间歇过程的控制要求同连续生产过程相同,即采用保持一组给定的相对稳定的操作条件而保证生产的稳定运行。
但是,不同于连续过程,由间歇过程的按配方操作批量生产、生产中整体工艺条件(参数)是动态的等特性,间歇过程要求其控制系统具备更加完善和特殊控制功能。
其控制要求可概括如下。
(1)顺序控制间歇生产过程是顺序执行配方规定的生产操作的批量生产过程。
所以要求间歇控制系统具有的一项功能就是驱动生产过程一步一步地顺序执行不同的生产操作。
工业上称这种控制模式为顺序(程序)控制。
操作中的顺序错误可能导致危险物的生成甚至直接就会发生事故。
根据各步间的转换条件,顺序控制又可分为时间驱动、事件驱动和混合驱动三种顺序控制方式。
第一种是根据操作配方规定的时间段、时间点转换操作步骤,如产品的保温固化时间等。
某原料药厂间歇精馏装置工艺安全自控设计
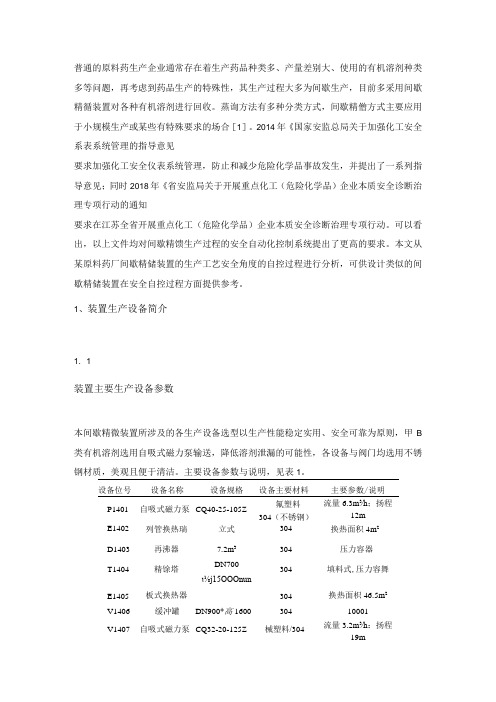
普通的原料药生产企业通常存在着生产药品种类多、产量差别大、使用的有机溶剂种类多等问题,再考虑到药品生产的特殊性,其生产过程大多为间歇生产,目前多采用间歇精循装置对各种有机溶剂进行回收。
蒸询方法有多种分类方式,间歇精僧方式主要应用于小规模生产或某些有特殊要求的场合[1]。
2014年《国家安监总局关于加强化工安全系表系统管理的指导意见要求加强化工安全仪表系统管理,防止和减少危险化学品事故发生,并提出了一系列指导意见;同时2018年《省安监局关于开展重点化工(危险化学品)企业本质安全诊断治理专项行动的通知要求在江苏全省开展重点化工(危险化学品)企业本质安全诊断治理专项行动。
可以看出,以上文件均对间歇精馈生产过程的安全自动化控制系统提出了更高的要求。
本文从某原料药厂间歇精储装置的生产工艺安全角度的自控过程进行分析,可供设计类似的间歇精储装置在安全自控过程方面提供参考。
1、装置生产设备简介1. 1装置主要生产设备参数本间歇精微装置所涉及的各生产设备选型以生产性能稳定实用、安全可靠为原则,甲B 类有机溶剂选用自吸式磁力泵输送,降低溶剂泄漏的可能性,各设备与阀门均选用不锈钢材质,美观且便于清洁。
主要设备参数与说明,见表1。
设备位号 设备名称 设备规格 设备主要材料主要参数/说明 P1401 自吸式磁力泵 CQ40-25-105Z 氟塑料304(不锈钢)流量6.3m 3∕h ;扬程12m E1402 列管换热瑞 立式 304换热面积4m 2 D1403 再沸器 7.2m 3 304压力容器 T1404 精馀塔 DN700 304填料式,压力容舞 E1405 板式换热器 ι⅛j15OOOnun 304换热面枳46.5m 2 V1406 缓冲罐 DN900*高1600 30410001 V1407 自吸式磁力泵 CQ32-20-125Z械塑料/304 流量3.2m 3∕h :扬程19mE1408列管换热器立式304换热面枳4m2 E1409丙河接收罐卧式3043OOO1P1410自吸式磁力泵CQ40-25-105氟塑料/304流量20m3∕h;扬程16m制药工艺与装哥表1主要生产设备参数与说明1.2装置主要生产设备说明原料药生产过程中待回收的丙酮溶剂,根据现行GB50160《石油化工企业设计防火规范的火灾危险性分类为甲B类液体。
间歇生产过程安全控制分析(新编版)

( 安全管理 )单位:_________________________姓名:_________________________日期:_________________________精品文档 / Word文档 / 文字可改间歇生产过程安全控制分析(新编版)Safety management is an important part of production management. Safety and production are inthe implementation process间歇生产过程安全控制分析(新编版)一、控制条件分析在工业控制方面,间歇生产过程同连续生产过程相同都要满足:①安全生产;②设备工艺指标和产品质量指标;③环保法规;④经济指标等基本要求。
在生产过程中,间歇过程也同样要求有对参数的调节控制功能。
特别是在诸如反应器的平稳反应阶段,精馏操作中某单一组分平稳馏出阶段,间歇过程的控制要求同连续生产过程相同,即采用保持一组给定的相对稳定的操作条件而保证生产的稳定运行。
但是,不同于连续过程,由间歇过程的按配方操作批量生产、生产中整体工艺条件(参数)是动态的等特性,间歇过程要求其控制系统具备更加完善和特殊控制功能。
其控制要求可概括如下。
(1)顺序控制间歇生产过程是顺序执行配方规定的生产操作的批量生产过程。
所以要求间歇控制系统具有的一项功能就是驱动生产过程一步一步地顺序执行不同的生产操作。
工业上称这种控制模式为顺序(程序)控制。
操作中的顺序错误可能导致危险物的生成甚至直接就会发生事故。
根据各步间的转换条件,顺序控制又可分为时间驱动、事件驱动和混合驱动三种顺序控制方式。
第一种是根据操作配方规定的时间段、时间点转换操作步骤,如产品的保温固化时间等。
第二种是根据被控对象的操作状态或偶发事件等转换操作步骤,如反应器加(卸)料结束、间歇式精馏的二馏出组分转换的判断等。
而更多的是第三种驱动方式,即同时依据时间和操作状态做出判断,如反应中二次反应的加料、反应中止剂的投放等。
生产时的危险控制范文

生产时的危险控制范文在生产过程中,危险是无处不在的。
为了确保工人的生命安全和生产活动的顺利进行,有效的危险控制措施至关重要。
本文将就生产时的危险控制进行详细阐述。
首先,要确保工作场所的安全环境。
企业应落实科学的布局规划和防护设施。
例如,在化工企业中,要对易燃、易爆、有毒、有害等物品进行合理分类仓储,并采取相应的防火、防爆、通风等措施,以减少火灾、爆炸和中毒等意外事故的发生。
其次,严格要求工人佩戴个人防护装备。
根据不同的生产环境和危险程度,工人应佩戴符合国家标准的个人防护装备,如安全帽、防护眼镜、耳塞、防护手套等。
同时,企业应定期检测和维修这些装备,确保其正常使用和防护效果。
另外,要定期进行安全培训。
企业应每年进行至少一次的安全培训,向工人普及安全知识,培养他们的安全意识和应急处理能力。
培训内容应涵盖常见的事故类型、危险源辨识、正确使用个人防护装备等方面,以确保工人在工作中能够及时应对和处理各种危险情况。
此外,要建立完善的应急预案。
应急预案是应对突发事件的重要依据。
企业应明确不同紧急情况下的处置程序和责任分工,并进行定期的演练和评估。
预案涵盖的内容包括应急报警、灭火、疏散、救护等,以便在危险事件发生时能够迅速有效地采取措施,最大限度地减少损失和伤亡。
还应加强对危险源的监控和检测。
企业应采用先进的监测设备,对危险源进行实时监控,确保及时发现和处理隐患。
例如,在化工企业中,应定期检测和监控环境空气中的有害物质浓度,以及管道、设备等的泄漏情况,确保生产过程中不会产生对工人和环境的严重威胁。
最后,要加强对工人安全意识的培养。
企业应注重培养和提高工人的安全责任感和意识。
可以通过举办安全知识竞赛、发布安全通报、组织安全交流会等方式,提高工人对危险的认识和预防能力。
同时,要重视员工的心理健康,建立健全的心理辅导体系,及时帮助员工化解压力和焦虑情绪,保持工作积极动力。
总之,生产过程中的危险控制是企业安全生产的核心任务。
生产现场不安全行为起因分析与控制

生产现场不安全行为起因分析与控制1. 前言生产现场不安全行为是造成一定的人身财产损失的重要原因之一,更是导致工伤事故发生的主要原因。
解决这类问题至关重要,本文将就不安全行为的起因进行分析,并提出一些控制方法,以期达到提高生产安全的目的。
2. 生产现场不安全行为起因分析2.1 对生产安全意识的缺乏生产过程中,操作人员对自身的安全意识不够强烈,缺乏对危险的认识。
这样的心态会导致操作人员没有及时发现和避免潜在的危险因素。
2.2 对安全标准的不了解许多操作人员对安全规章制度缺乏了解,不知道哪些行为是不安全的。
同时,由于操作人员工作繁忙、时间紧迫,熟悉安全制度的时间很少,也不愿意参与制定制度的过程。
2.3 设备不良和缺乏维护如果生产设备不良或者缺乏维护,也会导致不安全行为的发生。
比如操作人员在维修机器时,由于机器受损或未得到修复,操作人员必须采取一些不安全的方式进行操作,从而导致事故的发生。
2.4 操作人员技术能力不足缺乏经验和技术能力的操作人员不能及时处理突发事件,可能会进行错误的操作,导致原本可控的危险变得更加危险,甚至危及生命。
2.5 不安全行为常态化习惯性的不安全行为会使人们变得麻木,就算出现风险也会继续执行这些行为。
如此一来,生产过程中出现的安全隐患往往被掩盖,难以及时发现和控制。
3. 生产现场不安全行为控制3.1 加强人员教育培训应该通过各种途径,加强人员对安全的培训和教育。
要确保每位操作人员都深入了解安全的意义和安全制度。
还要进一步提高安全意识,鼓励人们在日常工作中更加注重安全问题,构建安全第一的生产文化。
3.2 制定和强制执行安全制度制定一套完善的安全制度,并向所有工作人员传达有关规定和制度。
同时,把这些规定和制度贯穿于企业生产和管理的方方面面,并建立有效的处罚机制以确保其有效实施。
3.3 完善安全保障措施企业应当从设备的质量保证、安全检查检测、安全宣传等各方面入手,深入开展各种形式的安全宣传与教育,提升所有工作人员的安全意识,并完善安全保障设施,各类人员应配备符合要求的安全设备,如防护眼镜、耳塞、手套、安全带等,提高人们在紧急情况下的自我保护能力。
间歇生产的难点和对策

间歇生产的难点和对策间歇生产是指生产过程中存在停顿或间隔的一种生产方式。
在这种生产模式下,生产线上的设备在完成一次生产任务后会停止运行,直到下一个任务开始前再次启动。
间歇生产相对于连续生产来说,具有一定的灵活性和适应性,但也存在一些难点需要克服。
首先,间歇生产的难点之一是生产线的调度问题。
由于生产线上的设备在任务完成后会停止运行,因此如何合理安排各个任务的顺序和时间是一个挑战。
如果任务之间的间隔时间过长,会导致生产效率低下;而如果间隔时间过短,则可能会导致设备无法及时准备好下一个任务所需的物料和工具。
因此,需要进行细致的调度规划,确保每个任务之间的间隔时间既能保证设备充分准备,又能最大限度地提高生产效率。
其次,间歇生产还面临着生产线平衡的问题。
由于每个任务之间存在不同的间隔时间,可能会导致生产线上的各个工序之间出现不平衡的情况。
例如,某个工序可能需要更长的时间来完成,而其他工序则需要更短的时间。
这样就会导致某些工序处于空闲状态,而其他工序则需要加班加点来赶进度。
为了解决这个问题,可以通过优化工艺流程、调整设备配置和提高员工技能水平等方式来实现生产线的平衡。
另外,间歇生产还需要面对产品质量控制的挑战。
由于生产过程中存在停顿和间隔,可能会导致产品质量出现波动。
例如,在停机期间设备可能会发生变化或老化,从而影响产品的质量稳定性。
为了解决这个问题,可以采取一些措施来提高产品质量稳定性,如定期维护设备、加强质量监控和提高员工技能水平等。
此外,间歇生产还需要面对供应链管理的挑战。
由于停机期间设备不运行,可能会导致物料和零部件的库存紧张。
为了确保供应链的畅通,需要建立一个高效的供应链管理系统,及时采购和储备所需物料和零部件,并与供应商建立稳定的合作关系。
针对以上难点,可以采取一些对策来克服。
首先,在生产线调度方面,可以借助先进的调度算法和信息技术来实现自动化调度。
通过建立一个智能调度系统,可以根据设备状态、任务需求和优先级等因素进行合理的任务安排,提高生产效率和资源利用率。
生产现场危险点分析及预控措施

生产现场危险点分析及预控措施生产现场是一个充满潜在危险的环境,如果不注意安全措施,可能会导致严重的事故发生。
为了保障工人的安全和生产环境的稳定,下面将对生产现场的危险点进行分析,并提出一些预控措施。
1.梯子使用不当梯子是生产现场常用的工具,但如果使用不当,容易造成高处坠落事故。
解决这个问题的方法是:-在梯子的底部设置防滑垫,以增加稳定性。
-操作人员使用梯子时,必须牢固站稳,并且不能超过梯子的负荷限制。
-梯子的设置和使用必须符合施工规范,并进行定期检查和维护。
2.电气设备安全问题电气设备故障可能导致火灾、触电等严重事故。
为了减少这些风险,必须采取以下措施:-安装电路的线材必须符合规范,并且经过专业人员对接和绝缘处理。
-设置对电气设备进行定期巡检和维护的计划,并确保设备正常运行。
-生产现场应配备灭火设备,并进行定期检查和演练,以防止火灾事故的发生。
3.机械设备操作不当机械设备是生产现场常见的危险源,如果不正确操作可能导致事故。
预控措施如下:-所有机械设备必须由受过培训的工人操作,并且需要定期进行安全培训和考核。
-在设备上安装安全防护装置,以防止工人操作时出现意外伤害。
-在生产现场设置明显的警示标志,提醒工人注意机器运转状态。
-机械设备的保养和维护必须定期进行,以确保设备的正常运行。
4.仓库储物不安全仓库是存放原材料和成品的地方,如果处理不当,容易导致堆积物倒塌、物品损坏等危险情况。
处理措施如下:-存放的物品必须根据质量、形状和重量进行分类和整理,并确保物品的堆放稳定。
-在仓库内设置明确的出入口,并确保通道畅通,以便人员疏散和紧急情况处理。
-对于易燃、易爆等危险品,必须按照规定储存,并在仓库内明显位置设置警示标志。
5.不合理使用化学品生产现场常常使用化学品,如果不正确使用可能会带来严重危害。
预控措施如下:-安全存放化学品,遵循化学品存储要求,并在储存区域设置明显的警示标志。
-工人必须经过专业培训,了解化学品的性质、危害和正确使用方法。
安全生产过程控制要点范本(2篇)

安全生产过程控制要点范本1. 系统安全管理在整个安全生产过程中,建立系统的安全管理机制是最基本且关键的要点之一。
该机制包括制定安全生产规章制度、设立安全责任机构、开展安全教育培训等措施,以确保安全措施的有效实施。
2. 风险评估与控制在安全生产过程中,风险评估是不可或缺的环节。
通过对生产环节进行全面的风险评估,确定安全隐患和风险点,然后采取相应的控制措施进行安全管理和防范,如安全设备的选择和使用、制定安全操作规程等。
3. 安全设备和保护措施在安全生产过程中,科学合理地配置设备和采取保护措施是确保安全的重要手段。
对于潜在的安全风险,应选择适当的安全设备来防护和控制,如安全阀、报警装置等,并且要定期检测和维修保养,确保其正常运行。
同时,还要确保工作场所的安全环境,如配备防护栏杆、安全标识等。
4. 安全生产教育培训安全生产教育培训是提高员工安全意识和安全技能的重要途径。
通过定期组织开展安全培训、进行实际操作演练等方式,加强员工对安全生产的认识和理解,提高员工应对紧急情况和突发事件的能力,从而减少事故发生的可能性。
5. 安全生产监测与预警在安全生产过程中,对关键环节进行监测和预警是非常必要的。
通过使用各种安全监测系统和装置,实时监测生产环境和设备状态,如气体浓度监测、温度监测等,及时发现异常情况并做出相应处理,确保安全生产的稳定运行。
6. 应急预案和演练准备和实施应急预案是确保安全生产的重要环节。
根据可能发生的事故类型,制定相应的应急预案,并组织定期演练以提高员工的应急响应能力。
在应急情况下,要做到迅速、有序、科学地处置,最大限度地减少人员伤亡和财产损失。
7. 严格遵守法律法规在安全生产过程中,严格遵守国家、地方和企业制定的相关法律法规是根本要求。
要确保生产过程中符合安全标准和操作规程,不得擅自修改或违规操作。
同时,要定期进行安全检查和评估,及时发现和解决安全问题。
8. 安全责任落实安全责任是企业安全管理的核心,必须由企业高层主管负起最终责任,并落实到每个岗位和每个员工。
精选1化工生产安全运行及控制
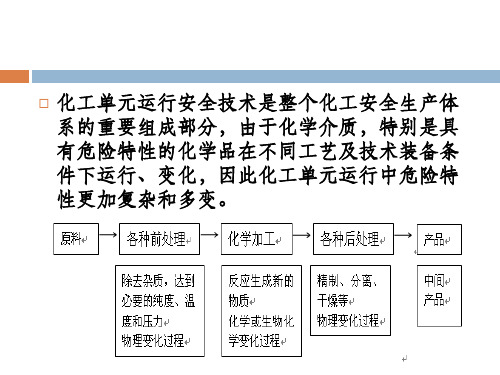
如果外来的扰动是可以测量的,则可组成单回路的反馈加前馈控制系统
先进控制是对那些不同于常规单回路 PID控制,并具有比常规 PID控制更好控制效果的控制策略的统称,而非专指某种计算机控制算法。
先进控制与常规 控制关系
1.3.1温度控制系统蒸汽加热器的温度自动控制系统:由蒸汽加热器、温度变送器TT,温度控制器 TC和蒸汽流量控制阀组成。控制的目标是保持流体出口温度恒定。
1.3.2流量控制系统由管路系统、孔板和差压变送器、流量控制器FC和流量控制阀组成。控制的目标是保持流量恒定。
简单控制系统组成
① 被控对象也称对象 ,是指被控制的生产设备或装置。被控对象需要控制的变量称为被控变量。 ② 测量变送器 测量被控变量,并按一定的规律将其转换为标准信号的输出,作为测量值。标准信号的含义是其上下限符合规定系列:0~l0mA, 4~20mA, 0.02~0.1MPa等。
1.2.1 自动化仪表技术的发展需要测定的参数:温度、压力、流量、液面……测量原理基本不变,测量手段变化迅速气动→电动就地控制→中央控制室仪表屏操作→计算机操作站模拟信号→数字信号……
20世纪50年代:电子管时代多用气动控制,采用气动信号作为统一标准信号电子管式的自动平衡记录仪就地式控制
20世纪60年代:晶体管取代电子管开始用电动仪表计算机在生产过程中应用,实现直接数字控制(DDC-Directly Digital Comtrol)
1.1.3 影响工业生产过程控制的因素
从负反馈角度分析:测量的影响一些生产过程的变量很难测定技术的发展,使过去某些不可测变量变为可测变量间接测量:利用可测变量与相关模型,计算不可测量的变量测不准原理:任何物体的一些成对的性质,比如位置和动量,不可能对两者同时精密测定。
化工过程分析-间歇过程

添加平行设备的发酵过程
第一步 平行设备
第二步
12
12
12
12
3
3
3
3
循环周期6小时
第一阶段设立异步平行发酵罐,循环周期缩短
添加中间储罐的发酵过程
第一步 第二步
12
12
3 3 3 33 3 33
第二阶段分离设备尺寸所小至250kg, 中间储罐最大存放量750kg。
例题
单产品间歇生产过程包括四个步骤,分别为: ➢ 反应时间4小时, ➢ 溶剂混合1小时, ➢ 分离2小时, ➢ 干燥1小时, 批次处理量1000kg。如何减少覆盖操作的
A
B
1
C
A
B
1
C
A
2
3
4
B
C
(a)流水作业
A
2
3
4
B
C
(b)工件作业
流水作业 ➢生产期限的划分 ➢生产策略:单产品生产策略;混合产品生产 策略 ➢例题-两个产品间歇生产过程时间(小时)
生产阶段
阶段1
阶段2
A
5
2
B
2
4
单产品策略:某一产品的所有批次生产完成后再进 行下一产品的生产,AAABBB
第一步 第二步
1kg 溶 剂
1kg A 1kg B
1.2kg A,B
反应
分离
0.8kg C
0.76 kg C
2.24kg A,B和 溶 剂
尺寸因子
设备j的尺寸因子:生产单位质量(或体积)的最终产品 所需的间歇设备的特征尺寸称为该产品在这个设备单元上 的尺寸因子,用Sj表示,其单位为体积/千克或面积/千克
无限中间储罐(UIS) :指当物料完成某单元过 程的操作后,物料可以转移到中间储罐内,这里 储罐的体积无限大,而且可以停留无限长时间。
化工企业检修安全控制范文(二篇)

化工企业检修安全控制范文一、引言化工企业是一个高风险的行业,涉及到多种危险品和高温高压设备。
为了确保检修工作的安全进行,保护员工的生命财产安全,化工企业必须建立完善的检修安全控制措施。
本文将就化工企业检修安全控制的重要性和具体措施进行详细阐述。
二、化工企业检修安全控制的重要性1. 保护员工安全健康:化工企业检修过程中,常常需要进行高空、高温、高压、有毒有害物质的作业。
通过建立科学合理的安全控制措施,能够有效降低事故风险,保护员工的安全和健康。
2. 降低财产损失:检修作业是一个危险性较高的工作,一旦发生事故,不仅会造成人员伤亡,还会给企业带来巨大的经济损失。
通过制定严格的安全控制措施,可以有效降低此类事故的发生概率,保护企业财产安全。
3. 提高企业形象:建立完善的检修安全控制措施,不仅能保护员工和财产安全,还能提高企业的形象和声誉。
外界对企业的安全管理有较高的评价,客户、股东和社会公众对企业的认可度也会大幅提升。
三、化工企业检修安全控制的具体措施1. 制定检修作业安全手册:对检修作业的安全规范、安全流程、禁止行为进行详细的规定,向员工普及安全知识,强调对有毒有害物质的正确使用及处理方法,提高员工的安全意识。
2. 安全培训:针对具备不同岗位的员工进行不同层次的安全培训,包括但不限于岗前培训、定期培训和临时培训。
培训内容包括安全操作规程、事故案例分析、急救措施等,提高员工应对突发事件的能力。
3. 设置专门的安全检查部门:成立安全检查小组,对检修现场进行日常巡视,及时发现和排除安全隐患,确保检修作业的安全进行。
4. 质量监控:严格执行质量监控制度,确保检修设备的安全可靠。
对于涉及到高温、高压、有毒有害物质的设备,应定期进行检查、维修和更换,保证设备处于良好的工作状态。
5. 紧急救援预案:制定完善的紧急救援预案,明确各岗位员工的逃生路线和应急救援措施,定期组织演练,提高员工对灾害事故的应急反应能力,确保能够迅速有效地处理突发事件。
间歇生产过程温度控制分解
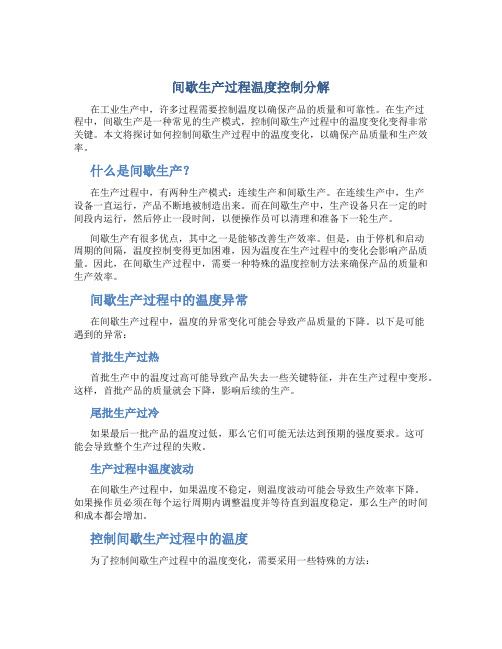
间歇生产过程温度控制分解在工业生产中,许多过程需要控制温度以确保产品的质量和可靠性。
在生产过程中,间歇生产是一种常见的生产模式,控制间歇生产过程中的温度变化变得非常关键。
本文将探讨如何控制间歇生产过程中的温度变化,以确保产品质量和生产效率。
什么是间歇生产?在生产过程中,有两种生产模式:连续生产和间歇生产。
在连续生产中,生产设备一直运行,产品不断地被制造出来。
而在间歇生产中,生产设备只在一定的时间段内运行,然后停止一段时间,以便操作员可以清理和准备下一轮生产。
间歇生产有很多优点,其中之一是能够改善生产效率。
但是,由于停机和启动周期的间隔,温度控制变得更加困难,因为温度在生产过程中的变化会影响产品质量。
因此,在间歇生产过程中,需要一种特殊的温度控制方法来确保产品的质量和生产效率。
间歇生产过程中的温度异常在间歇生产过程中,温度的异常变化可能会导致产品质量的下降。
以下是可能遇到的异常:首批生产过热首批生产中的温度过高可能导致产品失去一些关键特征,并在生产过程中变形。
这样,首批产品的质量就会下降,影响后续的生产。
尾批生产过冷如果最后一批产品的温度过低,那么它们可能无法达到预期的强度要求。
这可能会导致整个生产过程的失败。
生产过程中温度波动在间歇生产过程中,如果温度不稳定,则温度波动可能会导致生产效率下降。
如果操作员必须在每个运行周期内调整温度并等待直到温度稳定,那么生产的时间和成本都会增加。
控制间歇生产过程中的温度为了控制间歇生产过程中的温度变化,需要采用一些特殊的方法:预热生产系统在运行生产系统之前,将炉子或系统预热到生产温度。
这有助于确保在第一次生产之前的温度稳定。
在生产过程中使用温控设备使用电脑或智能设备来控制温度的变化,可提高生产效率和产品质量。
这种方法允许操作员位置远离生产现场,设备可以自动调整温度以确保生产的稳定性。
增加加热元件在间歇生产过程中使用更多的加热元件,可以加快加热过程,使温度更加平稳。
煤矿生产过程系统安全性分析
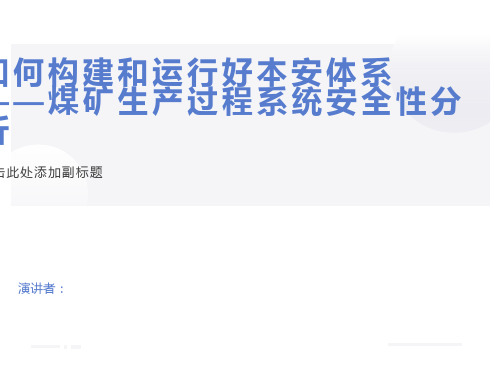
3 环境的因素分析
煤矿井下作业环境特殊,表现为四种情况:
工作空间狭小。 工作环境随开采过程不断移动,环境多变,缺乏规律性。
面临着顶板、瓦斯、矿尘、水、火和地热等自然灾害的威胁。 受到各种有毒有害气体侵袭。
环境的因素分析
3 环境的因素分析
作业环境区域的划分
最舒适区域 舒适区域 不舒适区域 不能忍受区域
管理因素分析
基层领导对安全工作不够重视,安全检查制度没有真正落实,还有流于形式的现象,形势严峻。 缺乏重大事故应急预案和调查分析机构,事故处理结案率低,同类事故重复发生。
5 煤矿事故鱼刺分析
我国煤矿事故之所以频繁发生, 很重要的原因在于对煤矿事故的发生机理缺乏清晰明确的认识,对事故的预防缺乏理论的支持和指导,不能对煤矿事故发生的原因进行全面系统的分析,不能找出导致煤矿事故的根本原因, 从而不能采取行之有效的措施和对策来预防和控制煤矿事故的发生。
机器设备因素分析
2 机器设备发生事故原因分析
制造上的缺陷 包括使用材料、加工方法、工艺、技能上的缺陷等。
2 机器设备因素分析
机器设备发生事故原因分析
维修保养和使用上的缺陷
机器设备系统随时间的延续,产生磨损、耗伤、腐蚀等故障,致使发生事故的可能性增加。 当使用超过机器设备的额定负荷,操作技术不熟练,以及缺乏安全作业的技巧等都可能导致不安全状态,增加了机器设备发生事故的可能性。
2 机器设备因素分析
早期故障
发生于机器设备试制或投产早期的试运转期间,由于设计或生产加工中潜在的缺点所致。
机器设备可靠性分析
2 机器设备因素分析
偶发故障
出现在早期故障之后的时期内,故障是偶然因素引起的,可以看作是在某时刻机械所积累的不安全因素超过了本身所能容忍的极限。
间歇生产过程控制与安全
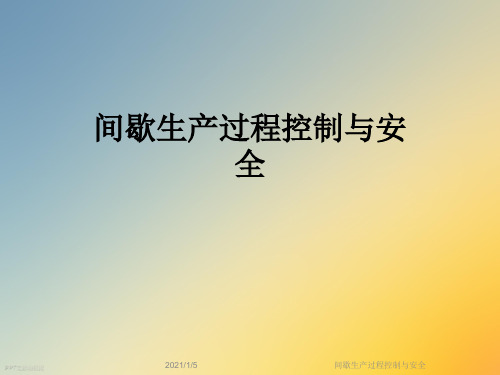
PPT文档演模板
间歇生产过程控制与安全
目前企业使用SIS系统时 必需关切的主要问题之一
• 由于国际标准IEC61508/61511 、国家标准GB/T21109.12007出台较晚,目前国内只有SHB-206-1999
《石油化工紧急停车及安全联锁系统设计导则》,用于设计、 施工和运行.因此在选用SIS时往往只注意了控制器达到 AK5、AK6或达到SIL3标淮.而没有提供一个SIS系统整体 设计,包括输入输出部分的解决方案.
•首批重监管化工工艺十五个 •您所在企业的工艺在目录内吗?
•重点讲解
PPT文档演模板
间歇生产过程控制与安全
当前国内外流程工业安全控制技术 简介
(1)采用继电器搭建或专用仪表 在60~70年采用电动单元组合仪表老装置中, 使用较为普遍。
一般另外设置报警辅助操作台,由重要的工艺 参数指示记录仪和信号闪光报警器、手动停车 及复位、投运按钮等部分组成。
• 当反应超温、搅拌失效或冷却失效时,能 及时加入聚合反应终止剂。安全泄放系统。
•
• •
PPT文档演模板
其它工艺的安全控制要求请详见
《首批重点监管的危险化工工艺安全控制要求、 重点监控参数及推荐的控制方案》
间歇生产过程控制与安全
安全自动化在中国展开(商机!)
• 第一,安全标准的强制化、法律化势在必行。
•要求达到安全度等级SIL2以上的工艺装置
•D C S
PPT文档演模板
•大型和高度危险化工装置要按照推荐的控制方案
•
装备紧急停车系统。
间歇生产过程控制与安全
ESD的主流结构
• 这种产品符合IEC61508标准并达到或获得TÜV等级认证, 主要有以下三种主流结构:
- 1、下载文档前请自行甄别文档内容的完整性,平台不提供额外的编辑、内容补充、找答案等附加服务。
- 2、"仅部分预览"的文档,不可在线预览部分如存在完整性等问题,可反馈申请退款(可完整预览的文档不适用该条件!)。
- 3、如文档侵犯您的权益,请联系客服反馈,我们会尽快为您处理(人工客服工作时间:9:00-18:30)。
( 安全管理 )单位:_________________________姓名:_________________________日期:_________________________精品文档 / Word文档 / 文字可改间歇生产过程安全控制分析(新编版)Safety management is an important part of production management. Safety and production are inthe implementation process间歇生产过程安全控制分析(新编版)一、控制条件分析在工业控制方面,间歇生产过程同连续生产过程相同都要满足:①安全生产;②设备工艺指标和产品质量指标;③环保法规;④经济指标等基本要求。
在生产过程中,间歇过程也同样要求有对参数的调节控制功能。
特别是在诸如反应器的平稳反应阶段,精馏操作中某单一组分平稳馏出阶段,间歇过程的控制要求同连续生产过程相同,即采用保持一组给定的相对稳定的操作条件而保证生产的稳定运行。
但是,不同于连续过程,由间歇过程的按配方操作批量生产、生产中整体工艺条件(参数)是动态的等特性,间歇过程要求其控制系统具备更加完善和特殊控制功能。
其控制要求可概括如下。
(1)顺序控制间歇生产过程是顺序执行配方规定的生产操作的批量生产过程。
所以要求间歇控制系统具有的一项功能就是驱动生产过程一步一步地顺序执行不同的生产操作。
工业上称这种控制模式为顺序(程序)控制。
操作中的顺序错误可能导致危险物的生成甚至直接就会发生事故。
根据各步间的转换条件,顺序控制又可分为时间驱动、事件驱动和混合驱动三种顺序控制方式。
第一种是根据操作配方规定的时间段、时间点转换操作步骤,如产品的保温固化时间等。
第二种是根据被控对象的操作状态或偶发事件等转换操作步骤,如反应器加(卸)料结束、间歇式精馏的二馏出组分转换的判断等。
而更多的是第三种驱动方式,即同时依据时间和操作状态做出判断,如反应中二次反应的加料、反应中止剂的投放等。
(2)离散控制间歇生产过程中大量地使用位式控制元件,如泵、位式阀门、冰机和压缩机等,这些设备的控制信号,以及顺序操作状态标志和时间等大量信号均是离散的开关量和数字信号。
这些离散信号的传输和处理是间歇过程控制的重要环节。
(3)调节控制前面已经提到,在间歇生产过程中也同样要应用与连续生产过程控制相同的控制方法和回路来控制温度,压力、流量等工艺参数。
但是,由于间歇生产过程中的各种工艺参数是动态的,随着生产的进行,被控变量的设定值,甚至被控变量将会产生变化,控制器的参数值也可能需要进行重新整定。
所以,在间歇生产过程中常常要求控制回路具有“重组”和“重整”的功能。
(4)人—机接口在间歇生产过程中,操作工人的干预是正常操作的一部分,在生产中起到十分重要的作用。
往往是一个关键的操作是由操作工人操纵控制系统启动的,而不是由控制系统自动触发。
如反应物料的加入、中止剂的加入、产品的导出等多数是由人工判断和启动的。
即在间歇生产过程中,操作工人一定要了解过程的运行状态和进程。
因此,设计一个人—机接口的友好界面,便于操作人员掌握生产的动态信息和人为地控制生产的进行是决定间歇安全控制系统成败的一个关键。
二、间歇控制模型(1)过程不执行任何控制任务,描述间歇过程本身特点。
如系统各单元的尺寸、功能、连接特点及原料、产品的物理化学性能等。
(2)过程I/O现场的传感器产生描述过程现状的模拟和数字信号。
•如热电偶等测量元件模拟信号输出,限位开关、电机启停的开关信号,涡轮流量计的脉冲信号,智能变送器的数字信号等。
而现场的执行器接受控制系统的输出信号,执行操作指令。
(3)联锁过程控制中的联锁包括安全联锁和过程联锁。
安全联锁是一个保护人员、设备安全的控制系统。
这一系统应是不受其他控制回路或控制信号影响的相对独立的控制系统。
过程联锁的功能是保证过程系统按配方规定的顺序实施加工生产,避免产生误动作而影响生产进行和产品质量。
(4)调节控制/离散控制实施对过程系统的实时控制。
这里有三种控制形式:手动控制,基本的调节控制/离散控制和复杂的调节控制/离散控制。
手动控制主要用于操作人员对间歇过程的干预,替代自控系统以手动方式进行间歇生产的操作。
基本的调节控制/离散控制形式应用于实现各控制回路和控制自动操作,按配方要求控制过程变量。
而复杂调节控制/离散控制则通过组合多个控制回路和控制器构成串级,前馈和智能控制等先进控制系统,具有协调间歇过程各单元设备和实现设备优化操作的功能。
(5)顺序控制其作用是保证间歇生产过程按计划时间(状态)和顺序进入不同的操作工序,并与其他控制子系统一同完成配方规定的生产任务。
它的功能主要包括判断过程时间、过程状态,适时发出转换指令并更换应用控制软件、修正必要的状态和操作参数等。
由图1—10可知,间歇控制模型除了上面介绍的有关过程的几部分外,还将包括批量生产管理,配方管理,生产调度等部分。
它们的主要功能是:根据生产计划选择并确定最优的生产调度方案,协调各间歇(批量)生产的顺序、时间、设备连接等关系;根据过程控制配方调配生产所需资源,协调安排共享资源的使用方式;采集和管理生产数据,监视生产过程。
三、间歇生产过程安全控制间歇生产的过程控制主要存在着参数的调节控制和顺序控制两种控制任务。
其中,参数控制主要涉及模拟信号的传输、变换和处理,其控制思想和目的与连续过程控制很相似。
而顺序控制主要涉及数字开关信号的通讯和处理,其控制目的主要是控制生产过程按配方规定的顺序和状态有序地完成间歇生产过程。
顺序控制在间歇生产过程中起着非常重要的作用。
(1)顺序生产过程间歇生产过程是顺序执行操作步骤(例如前处理一加料一反应一排料一后处理)的生产过程。
因此,清楚地描述间歇过程的操作顺序和转换条件是设计顺序控制的前提条件,特别是对于复杂的间歇生产过程,转换条件及各步骤内的具体操作的描述是非常必要的。
关于操作过程的描述有多种方法,其中常用的便利方法是采用图示描述方法。
下面,利用图1—11所示间歇反应过程简图,介绍几种常用的图形描述方法。
①流程图流程图是一种常用的描述和定义顺序的图示方法。
这种方法适用于在过程的顺序特性已经确定的情况下,向编程人员布置和分配编程任务。
图1—12描述了反应釜组分A阶段的控制步骤流程图。
但是,流程图描述法存在着没有严格的作图标准、作图和修改工作量大等缺点。
特别是作为控制软件的设计依据,存在着流程图上不能表示全部过程参数,难于准确描述多分支过程的并行及相互关系等问题。
②过程时间图图l—13是反应釜的过程时间操作图。
过程时间图的水平轴是时间控制、状态轴。
一般由具体的操作状态的排序构成,如图1—13所示,横轴描述了反应器的加料、反应、冷却、卸料几个阶段及相应各阶段中的控制步骤。
纵轴是动作、参数轴,列举了动作内容和过程参数。
图形描述了过程与时间、过程与动作、动作与动作、过程与操作参数等相互关系。
为设计人员提供了生产过程所需的全部控制元件、过程操作与动作顺序及与过程相关的工艺参数,为开发间歇生产控制策略提供了确切依据。
是一种比较理想的顺序图示方法。
注意过程时间图一般不能被直接用于编制控制软件,需将其转换成其他有利于编程的形式后加以间接利用。
另外,作图和修改的不便也是过程时间图方法的一个缺点。
③顺序功能图顺序功能图是用图形符号和文字叙述相结合的表示方法对顺序控制系统的过程、功能和特性进行描述的方法。
它针对顺序控制系统的控制条件和过程,提出了一套简单易学且精确严密的顺序逻辑控制功能的表示方法。
顺序功能图的基本结构如图1—14所示。
除上述三种图形表示法外,常用的图形表示法还有:状态转移图、决策表等方法。
(2)控制系统构成间歇生产过程是依据事先制订的明确任务,在一个或多个间歇设备上,一定时间内完成自开车到停车的全部生产周期的生产过程。
间歇生产过程中存在着参数控制、顺序控制和各种协调、管理等控制操作。
间歇反应过程顺序功能见图l—15。
由于技术的限制,早期的间歇生产过程无法实现自动控制,特别是生产的顺序操作和协调管理工作主要是由人工完成的。
在人工操作的过程中,由于作业人员的专业素质、操作经验、心理状态等都直接影响着作业的准确可靠性,因此,随机不安全因素很多。
随着电子技术和信息技术的发展,新一代基于微处理器技术的控制系统的出现,促进了间歇过程自动化的发展。
目前,利用DCS、PLC等构成的控制系统在间歇生产控制中发挥了巨大的作用。
可编程控制器(PLC)是一种以微处理器为基础的新一代通用型工业控制装置。
按照国际电工委员会的定义,PLC是一种专门为在工业环境下应用而设计的数字运算操作的电子装置。
它采用可以编制程序的存储器,用宋在其内部存储执行逻辑运算、顺序运算、计时、计数和算术运算等操作的指令,并能通过数字式或模拟式的输入和输出,控制各种类型的机械或生产过程。
图1—16给出了可编程控制器(PLC)的基本结构。
图1—16PLC结构示意图由图可以看出,PLC采用了典型的计算机结构,主要包括CPU、RAM、ROM和输入输出接口电路等,其内部采用总线结构进行数据和指令的传输。
为了适应工业控制的需要,目前,PLC产品已经系列化、模块化、标准化。
各生产厂家的设计有各种系列化产品和多种模块供用户选择,采用模块化组合方式可以适应大小规模不同、功能复杂程序和现场环境各异的各种控制要求。
且构成的控制系统维护方便,易于功能扩展。
与其他控制装置相比较,PLC具有可靠性高,通用性强,控制系统构成和操作方便、灵活、具有极强的逻辑运算和控制功能及较完善的通讯功能等特点。
因此,PLC在工业控制,特别是顺序控制中得到了广泛的应用。
四、优化安全运行操作分析在流程工业中各个生产单元或装置选择合适的安全运行操作条件是稳态最优化的最重要问题之一,这种问题可分为下述三种情况。
(1)物料平衡最优物料平衡用来决定主要物流通过工厂如炼油厂最合适的生产流径。
在分析物料平衡时,每种工艺物流或自变量是很重要的,物料平衡通常关系到主要产品的规格或组分损耗,这在分析计算时要用到,但不是独立的最优化变量而是作为约束条件来处理。
物料平衡的目的是使不同并联加工设备的进料(处理量)分配过程的最优化。
组分最优化在线调和过程决定一个炼油厂(或化工厂)的生产负荷。
物料平衡是物件以及物系安全的基础。
(2)能量平衡最优操作工况的第二个问题是过程能量平衡。
能量平衡通常受到装置中循环塔和公用工程供料总管上的压力等的影响。
物流最优分配对能量平衡也是十分重要的。
例如燃烧过程中的空气或氧气就存在着优化配比问题。
由于一个工厂的能量流的测量有一定困难,如燃料热值、蒸汽和瓦斯气流量的测量等都有较大误差,因此,能量平衡计算往往不是很准确。