精益生产案例分析
非常好的精益生产案例值得借鉴

总结各案例的优点和不足
案例1:优点是 提高了生产效 率,降低了成 本;不足是忽 视了员工培训 和团队建设。
案例2:优点是 实现了精益生产, 提高了产品质量; 不足是忽视了客 户需求和市场变
化。
案例3:优点是 优化了生产流程, 提高了生产效率; 不足是忽视了员 工满意度和员工
流失率。
案例4:优点是 实现了精益生产, 提高了产品质量; 不足是忽视了供 应链管理和供应
商关系。
对其他企业的借鉴意义
精益生产可以提高生产效率,降低 成本
精益生产可以优化生产流程,提高 生产灵活性
添加标题
添加标题
添加标题
添加标题
精益生产可以减少浪费,提高产品 质量
精益生产可以提升员工素质,提高 员工满意度
对未来精益生产的展望
持续改进:不断优化生产流程,提 高生产效率
绿色生产:注重环保和可持续发展, 降低生产对环境的影响
解决方案:加强质量管理,提高员工技能,确保产品质量
问题:库存积压,资金周转困难 解决方案:实施JIT(准时生 产),减少库存,提高资金周转率
解决方案:实施JIT(准时生产),减少库存,提高资金周转 率
问题:员工士气低落,离职率高 解决方案:加强企业文化建设, 提高员工满意度,降低离职率
解决方案:加强企业文化建设,提高员工满意度,降低离职 率
精益生产的核心思想
消除浪费:通过 持续改进,消除 生产过程中的浪 费,提高生产效 率
持续改进:不断 追求更好的生产 方式,持续改进 生产流程
准时生产:根据 市场需求,准时 生产出所需的产 品,减少库存积 压
质量至上:注重 产品质量,追求 零缺陷,提高客 户满意度
精益生产的应用范围
化工企业精益生产案例
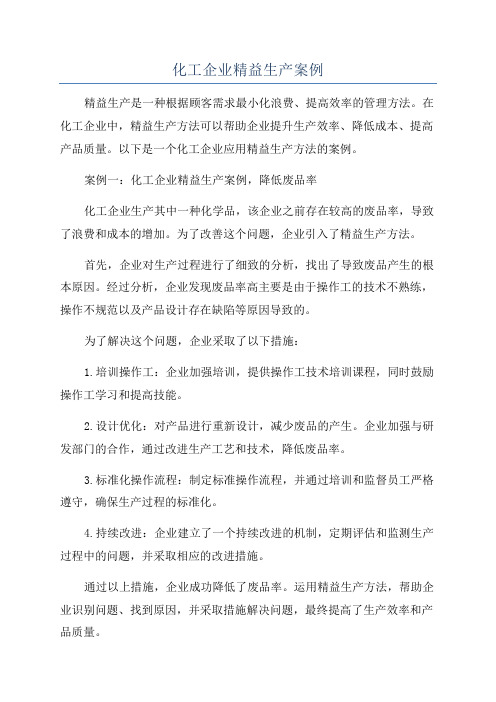
化工企业精益生产案例精益生产是一种根据顾客需求最小化浪费、提高效率的管理方法。
在化工企业中,精益生产方法可以帮助企业提升生产效率、降低成本、提高产品质量。
以下是一个化工企业应用精益生产方法的案例。
案例一:化工企业精益生产案例,降低废品率化工企业生产其中一种化学品,该企业之前存在较高的废品率,导致了浪费和成本的增加。
为了改善这个问题,企业引入了精益生产方法。
首先,企业对生产过程进行了细致的分析,找出了导致废品产生的根本原因。
经过分析,企业发现废品率高主要是由于操作工的技术不熟练,操作不规范以及产品设计存在缺陷等原因导致的。
为了解决这个问题,企业采取了以下措施:1.培训操作工:企业加强培训,提供操作工技术培训课程,同时鼓励操作工学习和提高技能。
2.设计优化:对产品进行重新设计,减少废品的产生。
企业加强与研发部门的合作,通过改进生产工艺和技术,降低废品率。
3.标准化操作流程:制定标准操作流程,并通过培训和监督员工严格遵守,确保生产过程的标准化。
4.持续改进:企业建立了一个持续改进的机制,定期评估和监测生产过程中的问题,并采取相应的改进措施。
通过以上措施,企业成功降低了废品率。
运用精益生产方法,帮助企业识别问题、找到原因,并采取措施解决问题,最终提高了生产效率和产品质量。
案例二:化工企业精益生产案例,提高设备利用率化工企业发现,其生产线的设备利用率较低,导致生产效率不高。
为了提高设备利用率,企业采用了精益生产方法。
首先,企业通过对生产线进行分析,找出导致设备利用率低的原因。
经过分析,企业发现设备故障率高、设备停机时间长以及设备维护不到位等原因导致了设备利用率低的问题。
为了解决这个问题,企业采取了以下措施:1.设备维护:企业加强设备的维护工作,定期检查和保养设备,防止故障的发生。
2.培训操作员:加强员工对设备操作的培训,提高操作员对设备使用和维护的技能。
3.优化生产计划:根据设备的特点和生产需求,优化生产计划,减少设备闲置时间。
精益生产案例分享
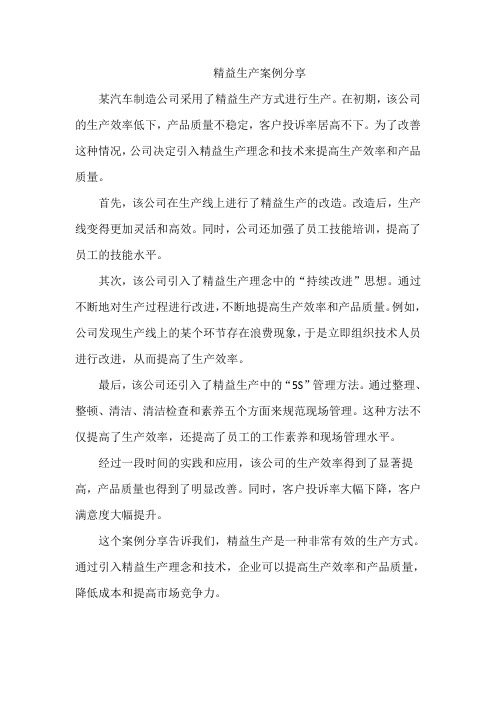
精益生产案例分享
某汽车制造公司采用了精益生产方式进行生产。
在初期,该公司的生产效率低下,产品质量不稳定,客户投诉率居高不下。
为了改善这种情况,公司决定引入精益生产理念和技术来提高生产效率和产品质量。
首先,该公司在生产线上进行了精益生产的改造。
改造后,生产线变得更加灵活和高效。
同时,公司还加强了员工技能培训,提高了员工的技能水平。
其次,该公司引入了精益生产理念中的“持续改进”思想。
通过不断地对生产过程进行改进,不断地提高生产效率和产品质量。
例如,公司发现生产线上的某个环节存在浪费现象,于是立即组织技术人员进行改进,从而提高了生产效率。
最后,该公司还引入了精益生产中的“5S”管理方法。
通过整理、整顿、清洁、清洁检查和素养五个方面来规范现场管理。
这种方法不仅提高了生产效率,还提高了员工的工作素养和现场管理水平。
经过一段时间的实践和应用,该公司的生产效率得到了显著提高,产品质量也得到了明显改善。
同时,客户投诉率大幅下降,客户满意度大幅提升。
这个案例分享告诉我们,精益生产是一种非常有效的生产方式。
通过引入精益生产理念和技术,企业可以提高生产效率和产品质量,降低成本和提高市场竞争力。
非常好的精益生产案例值得借鉴

非常好的精益生产案例值得借鉴前言精益生产是一种专注于提高效率和降低浪费的经营管理方法。
通过消除不必要的步骤和资源浪费,精益生产可以帮助企业实现更高的产出和更好的质量,从而获得竞争优势。
本文将介绍一些非常好的精益生产案例,展示出这种方法的实际应用和可行性,以供其他企业借鉴。
案例一:丰田汽车丰田汽车是精益生产的经典案例之一。
丰田公司以“丰田生产方式”(Toyota Production System,TSP)闻名于世。
TSP 的核心思想是通过限制生产速度来提高质量,消除浪费和降低成本。
丰田将员工视为最重要的资源,鼓励员工参与改进流程,并不断学习和提高。
通过实施流程改进和标准化操作,丰田成功地降低了库存水平、缩短了交付周期,并提高了产品的质量。
流程改进丰田汽车通过实施精细的生产计划和精确的生产控制来改进流程。
他们使用所谓的“拉动式生产”(Pull Systems),这意味着生产进程只会在下一阶段需要材料和部件时才会启动,以此保持生产流程的稳定性。
这种方式可以防止过度生产和库存积压,并减少浪费。
标准化操作丰田汽车非常注重标准化操作。
他们制定了详细的作业指导书,确保每位员工都能按照标准程序工作。
通过标准化操作,丰田能够减少错误和变量,并提高整体生产效率。
标准化操作还使得员工之间可以互相替代,以应对人员变动和流程变化。
持续改进丰田汽车秉持着“持续改进”的信念。
他们鼓励员工积极参与改进流程,并通过小改进和创新来不断提高生产效率和质量。
丰田实行所谓的“就地解决问题”(Genchi Genbutsu),即员工应该亲自去现场了解问题并找到解决方案。
这种方法帮助丰田构建了一个持续改进的文化,使得所有员工都在努力寻找问题并付诸行动。
案例二:美国空军美国空军也是一个非常成功的精益生产案例。
空军一直致力于在各个领域实施精益生产,以提高效率、降低成本,并最大限度地满足任务需求。
下面将以飞机维修作业为例,介绍空军如何运用精益生产方法改进维修流程:改进维修流程空军通过改进维修流程来提高效率。
精益生产案例分析
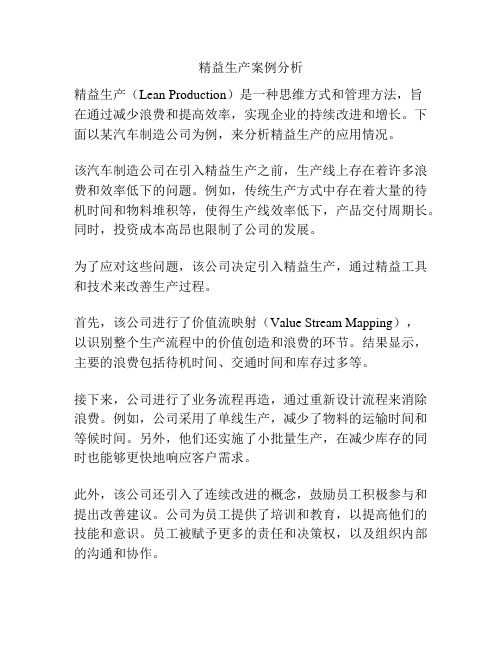
精益生产案例分析精益生产(Lean Production)是一种思维方式和管理方法,旨在通过减少浪费和提高效率,实现企业的持续改进和增长。
下面以某汽车制造公司为例,来分析精益生产的应用情况。
该汽车制造公司在引入精益生产之前,生产线上存在着许多浪费和效率低下的问题。
例如,传统生产方式中存在着大量的待机时间和物料堆积等,使得生产线效率低下,产品交付周期长。
同时,投资成本高昂也限制了公司的发展。
为了应对这些问题,该公司决定引入精益生产,通过精益工具和技术来改善生产过程。
首先,该公司进行了价值流映射(Value Stream Mapping),以识别整个生产流程中的价值创造和浪费的环节。
结果显示,主要的浪费包括待机时间、交通时间和库存过多等。
接下来,公司进行了业务流程再造,通过重新设计流程来消除浪费。
例如,公司采用了单线生产,减少了物料的运输时间和等候时间。
另外,他们还实施了小批量生产,在减少库存的同时也能够更快地响应客户需求。
此外,该公司还引入了连续改进的概念,鼓励员工积极参与和提出改善建议。
公司为员工提供了培训和教育,以提高他们的技能和意识。
员工被赋予更多的责任和决策权,以及组织内部的沟通和协作。
通过精益生产的应用,该汽车制造公司取得了显著的改进和成果。
公司生产效率提高了30%,产品交付时间缩短了50%。
另外,公司库存水平减少了60%,大幅降低了企业的资金占用成本。
除此之外,品质管理也得到了明显的提升。
公司通过实行全员质量管理,强调“Do it right the first time”的原则,减少了缺陷率。
总之,精益生产的应用使得该汽车制造公司在面临激烈竞争的市场中获得了差异化优势。
通过减少浪费和提高效率,公司在成本控制上取得了明显的改善,提高了客户满意度。
此外,精益生产还培养了公司内部的团队合作精神和创新意识,为企业的可持续发展打下了坚实的基础。
继续写相关内容,1500字精益生产(Lean Production)作为一种有效的生产管理方法,不仅可以帮助企业提高效率,降低成本,还能够提高产品质量和客户满意度。
精益生产案例

精益生产案例引言精益生产是一种通过最大限度地减少浪费,提高生产效率和产品质量的方法。
它始于丰田生产系统,如今已经被广泛应用于各种行业和组织中。
本文将介绍三个精益生产的案例,以展示其在不同领域的应用。
案例一:汽车制造在汽车制造业中,精益生产被广泛用于提高生产效率和降低成本。
丰田汽车公司是精益生产的典型代表之一。
他们采用了精益生产的原则和技术,通过提高生产线的流程效率,使得汽车制造过程更加高效和可持续。
丰田的生产线采用了“单件流水线”模式,每个工人都负责完成整个工作过程,从而减少了不必要的等待和处理时间。
此外,丰田还推崇“质量至上”的原则,通过在每个生产环节中设置严格的质量控制标准,确保产品质量。
另一个值得注意的案例是日本的一个零件制造公司。
该公司通过消除浪费和优化工作流程,成功地提高了生产效率。
他们分析了原本复杂的生产流程,将其简化为一系列简单的步骤,让每个工人都能清楚地知道自己的工作内容和目标。
案例二:医疗服务精益生产同样适用于医疗服务行业。
一个典型的案例是德国某医院的急诊科。
该医院采用了精益生产的原则和工具,通过优化流程和增加资源的使用效率,将就医时间缩短了70%。
在过去,患者在急诊科等待就医时间往往较长。
该医院通过对患者流程进行重新设计,将患者按照病情严重程度进行分类,并在每个分类中设置不同的诊疗团队。
这样,医护人员可以更有效地处理患者,避免了等待时间过长的问题。
此外,该医院还引入了标准化的医疗流程,并充分利用ICT技术,提供了在线预约、电子病历等便捷服务。
这些措施不仅提高了医疗服务的质量,也提高了患者的满意度。
案例三:酒店管理精益生产的原则也可以应用于酒店管理领域。
一个例子是一家高端度假村酒店。
这家酒店通过精益生产的方法,优化了业务流程,提高了客户满意度,并在市场上取得了成功。
首先,酒店管理团队对酒店的工作流程进行了深入分析,并找出了其中的浪费和问题。
然后,他们采取了一系列措施,如优化客房清洁流程、提高服务质量等。
精益生产案例

精益生产案例精益生产(Lean Production)是一种以精益思维为基础的生产管理方法,旨在通过减少浪费、提高效率和质量,实现生产过程的优化。
下面列举10个精益生产案例,以展示其在不同领域的应用和效果。
1. 丰田生产系统(T oyota Production System,简称TPS)是精益生产的典型案例。
TPS通过标准化流程、零库存、及时生产等手段,实现了生产效率和质量的大幅提升。
丰田汽车以其高效、灵活和质量稳定的生产模式成为全球汽车行业的典范。
2. 亚马逊的仓储和物流管理也是一个成功的精益生产案例。
亚马逊通过使用先进的仓储机器人、优化的物流网络和实时数据分析,实现了高效的订单处理和快速的配送服务,提高了客户满意度。
3. 丹麦乐高公司采用精益生产方法,实现了高效的生产和供应链管理。
乐高通过精细的计划、准确的库存控制和灵活的生产调度,保证了产品的高质量和及时交付,同时降低了库存成本。
4. 耐克公司在生产和供应链管理中采用了精益生产的方法。
耐克通过减少生产过程中的浪费、优化供应链和加强与供应商的合作,提高了生产效率和产品质量,同时缩短了产品上市时间。
5. 日本的富士康科技集团(Foxconn)是全球最大的电子制造服务公司之一,也是精益生产的成功案例。
富士康通过引进先进的生产设备、标准化工作流程和持续的员工培训,实现了高效的生产和质量控制,为客户提供高品质的电子产品。
6. 美国的快餐连锁企业麦当劳通过精益生产的方法,实现了订单处理和服务的高效率。
麦当劳通过优化餐厅布局、标准化工作流程和使用先进的点餐系统,提高了订单处理速度和客户满意度。
7. 日本的丸红公司是一家全球知名的物流和供应链管理公司,也是精益生产的典范。
丸红公司通过优化仓储和运输流程、精细的库存管理和实时数据分析,实现了高效的物流运作和准时交货。
8. 德国汽车制造商奔驰公司采用精益生产方法,实现了高质量和高效率的生产。
奔驰通过持续改进生产流程、优化零部件供应和自动化生产线,提高了生产效率和产品质量。
精益生产成功案例

精益生产成功案例精益生产是一种管理理念和方法,旨在通过消除浪费,提高生产效率和品质,实现持续的改进和提升。
下面我们将介绍一些精益生产的成功案例。
1.丰田生产系统(TPS):丰田汽车公司是精益生产的开创者。
TPS主要关注生产过程中的浪费和瑕疵,并通过“Just-in-Time”(即时生产)和“Jidoka”(自动停工)的原则,实现了高效的生产和优质的产品。
TPS的成功在于其对员工参与和持续改进的鼓励,以及对质量问题的立即回应。
2.通用电气:通用电气公司采用精益生产理念,优化了其生产流程和供应链管理。
通过分析和优化整个生产过程中的活动和环节,通用电气成功地减少了废品、库存和停工时间。
精益生产的应用帮助通用电气实现了高效生产和投资回报,同时提高了产品质量和客户满意度。
3.美国电子零件制造公司(AMEC):AMEC是一家为全球电子制造企业提供电子零件生产和组装服务的公司。
AMEC采用了精益生产的原则,在生产流程中消除了多余的步骤和浪费。
该公司通过提高生产效率和质量,降低成本和交货时间,有效提升了其竞争力。
AMEC还鼓励员工积极参与,提供培训和奖励机制,以促进持续改进和创新。
4.日本曙光灯泡公司:日本曙光灯泡公司是一家生产灯泡和光源产品的公司。
该公司采用精益生产的原则,通过持续改进和创新,实现了生产效率的提高和成本的降低。
曙光灯泡公司注重员工的培训和参与,鼓励他们提出改进建议,并将其纳入生产流程中,以实现更好的效果。
通过精益生产的应用,曙光灯泡公司成功地提高了生产效率和产品质量,同时降低了生产成本。
5.伊顿公司:伊顿公司是一家全球性的动力管理企业,采用精益生产的原则优化了其生产和供应链管理。
伊顿通过减少库存、提高生产效率和质量,实现了较高的客户满意度和市场份额。
该公司还通过精益思维培养了员工的持续改进意识和能力,并鼓励他们参与决策和问题解决过程。
以上是一些成功应用精益生产的案例,这些企业通过消除浪费、提高效率和质量,实现了更高水平的竞争力和持续的发展。
5个案例,秒懂精益生产精髓!【标杆精益】

5个案例,秒懂精益生产精髓!【标杆精益】全文总计1639字,需阅读4分钟,以下为正文:精益生产,创造性地解决了适应市场多品种、少批量产品需求带来的切换和浪费问题,被称为是当前工业界最佳的一种生产组织体系和方式,一经问世即受到狂热追捧。
精益生产改善体现在日常工作中的点点滴滴,下面分享5个经典案例,希望能给大家带来启示:—1—自动化与防呆防错一个小改善的大效果有一家生产复印机的工厂,他们的复印机里面有一个小风扇,这个小风扇非常重要,一旦装反了,就会导致机械损坏。
但由于是流水线作业,操作工在装配时,由于疲劳、遗忘等多种原因,可能会出错。
主管就要求操作工装好后要进行检查,用手摸一下,试下风向。
但是每天生产数千台复印机,操作工人可能就会产生错觉,有风?没风?不开心了,走神了,还是会产生装反的现象。
后来,就通过发掘员工潜能,在复印机旁边装一个小风车,如果装配正确就会有风,风车会转,因此只要风车会转,装配就是完好的,否则,就是错误的。
这样这家公司复印机的合格率就大大提高了。
—2—如何强化管理目视化的改善某企业有一个开放式的大办公室,有200人在一起办公。
由于管理不到位,经常发生办公室的灯、空调没有关的现象。
最近,公司高层也知道了此事,指示行政部必须强化管理,尽快解决此问题。
于是行政部想了许多办法,如:出台制度、人走灯灭、保安检查、领导值班检查、进行处罚、公告等。
一开始还能起到一定作用,但时间一长,由于监督不到位,老问题还是继续发生,制度落实不好。
其实,制度固然重要,但不能迷信制度。
这属于无意识犯错,无意识犯错是不可以用制度来约束的。
管理很重要,但员工的自主管理更重要。
一个公司通过努力也想出了好办法:他们在公司的门上设计了一个卡通画,只要一锁门,就会有一个卡通画跳出来,问“你关灯了吗?”通过这种人性化的管理和提醒,忘记关灯和空调的现象终于杜绝了。
—3—美国西南航空学丰田标准化与简单化日本产品曾经是低劣产品的代名词,美国人曾经看不起日本企业。
精益生产改善案例

精益生产改善案例精益生产是一种持续改善的管理方法,旨在消除浪费、提高效率和质量。
在实践中,精益生产可以应用于各种行业和组织,带来显著的改善效果。
下面我们将介绍一个关于精益生产改善的案例,以便更好地理解其实际应用。
这个案例发生在一家汽车零部件制造公司。
在过去,该公司的生产线存在着许多浪费,如过多的库存、不必要的运输、瑕疵品的产生等。
这些问题导致了生产效率低下和成本的增加,因此公司决定引入精益生产来改善现状。
首先,公司对生产线进行价值流分析,找出了造成浪费的根本原因。
他们发现,生产线上存在着不必要的等待时间、过多的库存积压和瑕疵品的频繁出现。
为了解决这些问题,公司采取了一系列措施。
首先,他们优化了生产线的布局,将工作站重新排列,减少了物料运输的距离,缩短了等待时间。
其次,他们实施了定期保养和设备维护计划,以确保设备的正常运转,减少了停机时间。
同时,他们加强了对员工的培训,提高了生产线的灵活性和适应性,减少了瑕疵品的产生。
经过这些改进措施的实施,公司取得了显著的成效。
生产效率得到了提高,库存周转率大幅增加,瑕疵品率显著下降。
同时,员工的工作积极性和满意度也得到了提升。
通过这个案例,我们可以看到精益生产在实际应用中的巨大潜力。
只要公司能够深入分析问题,找出根本原因,并采取有效的改进措施,就能够取得显著的改善效果。
因此,我们鼓励更多的企业和组织引入精益生产,不断优化自身的生产流程,提高竞争力。
总之,精益生产改善案例向我们展示了一种持续改善的管理方法,它能够帮助企业发现和消除各种形式的浪费,提高效率和质量,实现持续增长。
希望这个案例能够对大家有所启发,促使更多的企业关注精益生产,实现更好的发展。
精益生产成功案例

精益生产成功案例第一篇:精益生产成功案例精益生产网站案例1一家专业生产汽车刹车盘(鼓)美资公司,在中国设有2 家工厂,产品几乎覆盖了美国、欧洲、日本和韩国的所有车型。
同时水泵的可提供型号达到了500 种,主要是满足上面这几个国家主流车型的需要。
同时,借助市场调研和与一些客户的紧密合作,该公司装配线产品追溯性标示过程复杂,造成冗杂处理的浪费;手工打标记等不仅劳动强度大,而且容易造成疲劳错误。
铸造车间产品种类和生产区域无标示,将导致分检的时间损失及混淆。
-铸造现场、热处理车间5S 尚有较大改进空间,尤其是整顿、清洁和进一步的标准化工作。
、其他影响:同时,制造方式的变革也暴露出在原来的成批生产方式中隐藏至深的大量问题,如设备故障多发,维修速度慢以及缺乏保养;设备换模具时间长;刀具整备时间长;作业员技能单一等。
改善效果:经过三个月的维持与改善,同时辅以培训 , 一些主要问题得到明显的改善:·在不影响现有产出情况下,较大幅度降低成品库存总量。
总库存量减少了 4 0 %。
·按照用户的需求节拍,进行小批量多频次的生产和物料周转(目标:单件流),缩短生产周期。
生产提前期从 15 天缩短到 5 天。
·应用快速换模的项目方法(四步法)和技术手段,缩短生产线的换型时间。
·运用 IE 工程和看板管理,辅以必要的柔性生产布局设计及多技能员工培训,改善现有的工艺及流程,消除瓶颈限制,在制品减少 66 %,实现流畅化制造。
·全面生产性维护(TPM):对设备效能作了详细测定 , 并根据以往开机时间的历史纪录,分析总体生产效率(OEE),改进设备维护计划,提高运行效率, 在没有增加设备的前提下,月产量提高了30%,不良率由 8% 降到了 4%,OEE 从原来的 60% 提高到 85 %。
·现场的物流及 5S 改善,减少搬运、寻找、等待等浪费活动。
精益生产网站案例2一家美商独资生产硅胶和塑料按键产品的企业,产品广泛应用于手机、家用电器、工业电子设备等产品上。
精益生产改善方案案例分析

销售
9、要学生做的事,教职员躬亲共做; 要学生 学的知 识,教 职员躬 亲共学 ;要学 生守的 规则, 教职员 躬亲共 守。21 .6.1321 .6.13Su nday , June 13, 2021
10、阅读一切好书如同和过去最杰出 的人谈 话。08:04:0808 :04:080 8:046/1 3/2021 8:04:08 AM
4、产品工序分析法 产品工序分析法的目的和目标 5、作业人员工序分析法
作业人员工序分析法的定义
5.2作业人员工序分析法的目的
1、是否有不必要的停滯 2、搬运的次数是否太多 3、搬运的距離是否太长 4、搬运的方法是否有问題 5、是否能同時实施加工及检查
工程分析案例:
1、优化生产线 自主改造装配线,实现HFC1020前桥混线装配
一个流生产:
自主设计制作本体流水装配线,在人员没有改变的前 提下,生产能力从加班日产200台提升到8小时产250 台;而且改变了长期以来落后的摆地摊装配方式。
推进精益生产:
1、现场是基础;
2、改善是手段。
库房的仓位
形迹管理
如图:通过不懈努力,所有工序的刀、辅、量具有 了“新家”,让它们也实现了定置
IE是英语industrial engineering 的缩写,即工业管理。
2、动作及动作分析法
定义:由人的身体各部位的运动所组成的行动、行为称之为 “动作”。
3、动作改善的目标和顺序
4、基本动作分析法与作业改善
4.1基本动作分析法的分析 方法
经过归纳将基本动作分 为以下三类:
Ⅰ第1类:作业进行时必 要的动作;
CT 设定
精益改善 生产 项目管理 规格
MRP
ERP 系统 设计 管理
精益生产经典案例

精益生产经典案例
精益生产是一种通过消除浪费、提高效率和质量的管理方法,它在全球范围内得到了广泛的应用。
下面我们将介绍一些精益生产的经典案例,希望能够给大家带来一些启发和思考。
第一个案例是丰田生产系统。
丰田生产系统是精益生产的典范,它通过精益的管理理念和方法,实现了高效率、高质量和低成本的生产。
丰田生产系统强调的是对员工的尊重和信任,鼓励员工参与持续改进和创新,从而实现了生产过程的精益化。
第二个案例是通用电气公司的精益生产实践。
通用电气公司在生产过程中采用了精益生产的方法,通过价值流映射和精益工具的运用,实现了生产效率的提高和浪费的减少。
同时,通用电气公司还注重员工的培训和激励,使员工能够更好地参与精益生产的实践和改进。
第三个案例是福特汽车公司的精益生产实践。
福特汽车公司在生产过程中引入了精益生产的理念和方法,通过价值流分析和持续改进,实现了生产效率和质量的提升。
福特汽车公司还注重产品的标准化和流程的优化,从而降低了生产成本和提高了产品的竞争力。
以上这些案例都充分展现了精益生产的优势和价值,它不仅可以帮助企业提高生产效率和质量,还可以促进员工的参与和团队的协作。
希望这些经典案例能够给大家带来一些启发,促使更多的企业和组织能够引入精益生产的理念和方法,实现持续改进和可持续发展。
精益生产案例分享

精益生产案例分享:丰田汽车1. 背景丰田汽车公司是世界上最大的汽车制造商之一,以其高效的生产方式和卓越的质量管理而闻名。
丰田在20世纪50年代引入了精益生产方法,这一方法通过减少浪费、提高效率和质量来优化生产流程。
下面将以丰田汽车为例,介绍其在生产过程中应用精益生产的具体案例。
2. 过程2.1 TPS(丰田生产系统)丰田生产系统(Toyota Production System,简称TPS)是精益生产方法的核心。
其主要原则包括“消除浪费”、“建立流程”和“实现标准化”。
TPS通过以下几个关键元素来实现这些原则:2.1.1 精确计划在TPS中,每个工作站都有一个明确的计划,并按照计划进行操作。
这样可以避免不必要的等待时间和浪费。
2.1.2 拉动式生产TPS采用拉动式生产模式,即根据需求进行生产,而不是按照预定计划进行推动式生产。
这样可以减少库存和过剩生产。
2.1.3 Jidoka(自动停线)丰田引入了Jidoka概念,即在生产过程中发现问题时立即停线,确保问题不会进一步传递。
这有助于提高质量和避免缺陷。
2.2 案例:丰田生产线改进丰田在其汽车生产线上应用精益生产方法,不断改进生产效率和质量。
下面是一个具体案例:2.2.1 背景在某条汽车装配线上,存在着许多浪费和效率低下的问题。
工人需要花费大量时间等待零部件供应、处理缺陷和调整机器。
这导致了生产周期长、质量不稳定和成本增加。
2.2.2 过程改进丰田采取了以下措施来改善这条装配线的效率:2.2.2.1 流程优化首先,丰田分析了装配线上的每个工序,并找出了其中的浪费和瓶颈。
他们通过重组工序、优化布局和消除不必要的动作来简化流程,并减少等待时间。
2.2.2.2 JIT(准时生产)丰田实施了JIT生产模式,即按需生产。
他们与供应商建立了紧密的合作关系,确保零部件能够准时到达装配线。
这样可以减少库存和等待时间。
2.2.2.3 自动化和标准化丰田引入了更多的自动化设备和机器人来替代繁重的人工劳动。
精益生产案例分析

精益生产案例分析案例:精益生产理念在工业企业管理及整体布局中的应用(1)生产工艺的布置及管理一般的生产方式,由于考虑生产一方的便利,简单形成大批量生产,生产供货周期变长。
并由于以长期需要预估来制定生产计划,执行生产计划,因而不能充分适应顾客需要的变化。
设备的布局影响生产线的布局,进而影响厂房的布局,最终影响整体布局。
车间布置应重视其实用性,摒弃传统的、固定的车间形状。
以生产工艺为基础,物流运输便利、快捷为前提,尽可能避免建筑大量小型厂房,将工艺或物流相关联的厂房建成联合厂房形式。
车间主要由生产线、仓库及物流通道组成。
精益生产理念的生产车间,车间内的物料做到一个流传递,使生产线更简洁,工艺更加流畅化。
提倡在必要的时刻生产必要数量的必要产品。
以制止“过量生产”,杜绝各种铺张为手段达到降低成本之目的,并对市场需求的变化作出快速而有效的反应。
详细优势体现在:削减工序间在制品存储量,削减流淌资金的占用;准时发觉质量异常,有效杜绝批量不良;实现节拍式生产,供应工作效率,充分发挥人员效能,确保生产能力;有效掌握生产节拍,把握生产进度支配;有效地缩短生产交货周期,敏捷应对市场(订单)的变化;最少化的设备资产的投入。
易于暴露问题点,有效揭示生产运行不良环节,成为提升生产管理水平“推动力”。
(2)厂区内仓储布置与物流组织厂区的整体物流做到精细物流、精细供应链、JIT(准时制生产)、BTO(订单式生产)、VM(I供应商管理库存)、柔性制造、机敏制造、零库存、库存最小化等。
使物流的流程、流向、流量、流速、载体等要素合理、优化;使物流协调、有序、标准、集成;实现路线简洁,尽量紧凑,避免迂回、倒流和往复,削减装卸搬运环节;能协调匹配,消退瓶颈;实现路径最短、先进先出、就近入库、匀称存放、低层满装、分区存放、紧急优先、路线组合、多机协同、顺序排队、先装后卸等策略;对运输单元(内外车辆搬运输送设备)实行动态跟踪管理与调度。
企业内仓储布置应以精益物流概念为宗旨,合理计算仓储面积,达到总负荷数最小的仓库货区的布置方法。
精益生产防错法案例
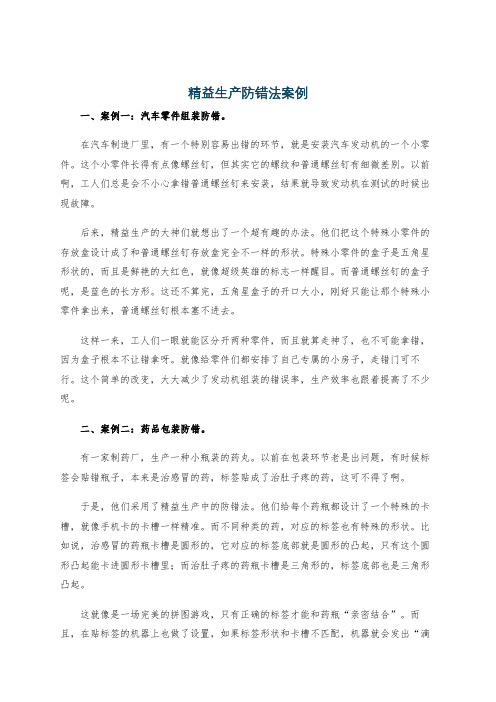
精益生产防错法案例一、案例一:汽车零件组装防错。
在汽车制造厂里,有一个特别容易出错的环节,就是安装汽车发动机的一个小零件。
这个小零件长得有点像螺丝钉,但其实它的螺纹和普通螺丝钉有细微差别。
以前啊,工人们总是会不小心拿错普通螺丝钉来安装,结果就导致发动机在测试的时候出现故障。
后来,精益生产的大神们就想出了一个超有趣的办法。
他们把这个特殊小零件的存放盒设计成了和普通螺丝钉存放盒完全不一样的形状。
特殊小零件的盒子是五角星形状的,而且是鲜艳的大红色,就像超级英雄的标志一样醒目。
而普通螺丝钉的盒子呢,是蓝色的长方形。
这还不算完,五角星盒子的开口大小,刚好只能让那个特殊小零件拿出来,普通螺丝钉根本塞不进去。
这样一来,工人们一眼就能区分开两种零件,而且就算走神了,也不可能拿错,因为盒子根本不让错拿呀。
就像给零件们都安排了自己专属的小房子,走错门可不行。
这个简单的改变,大大减少了发动机组装的错误率,生产效率也跟着提高了不少呢。
二、案例二:药品包装防错。
有一家制药厂,生产一种小瓶装的药丸。
以前在包装环节老是出问题,有时候标签会贴错瓶子,本来是治感冒的药,标签贴成了治肚子疼的药,这可不得了啊。
于是,他们采用了精益生产中的防错法。
他们给每个药瓶都设计了一个特殊的卡槽,就像手机卡的卡槽一样精准。
而不同种类的药,对应的标签也有特殊的形状。
比如说,治感冒的药瓶卡槽是圆形的,它对应的标签底部就是圆形的凸起,只有这个圆形凸起能卡进圆形卡槽里;而治肚子疼的药瓶卡槽是三角形的,标签底部也是三角形凸起。
这就像是一场完美的拼图游戏,只有正确的标签才能和药瓶“亲密结合”。
而且,在贴标签的机器上也做了设置,如果标签形状和卡槽不匹配,机器就会发出“滴滴滴”的警报声,就像在大声喊“错啦,错啦”。
自从采用了这个方法,药品包装贴错标签的错误几乎就没有再出现过了。
三、案例三:电子厂电路板焊接防错。
在电子厂里面,电路板焊接是个技术活,但也很容易出错。
精益生产管理的成功案例

精益生产管理的成功案例精益生产管理(Lean Production Management)促使企业实现高效运营、降低成本并提升质量。
下面将介绍三个成功应用精益生产管理的案例。
案例一:丰田汽车公司丰田汽车公司是一个广为人知的精益生产管理的成功案例。
该公司在汽车制造业中引入了丰田生产系统(Toyota Production System),凭借其卓越的精益管理理念,有效地提高了效率、质量和利润。
丰田生产系统强调持续改进和减少浪费。
通过精确计划、高效布局和员工参与决策等措施,丰田成功地降低了库存、提高了生产灵活性,同时还能满足客户需求。
案例二:波音公司波音公司是另一个成功应用精益生产管理的案例。
该航空制造企业采用了精益管理的方法来提高生产效率、降低成本并提供高质量的产品。
波音公司运用精益生产管理来优化供应链、改进生产流程、减少制造时间和提高资源利用率。
通过精细制定的生产计划、物料缩短流程和追求卓越质量的理念,波音不断提高产品竞争力,为客户提供满意的解决方案。
案例三:日本服装公司日本一些服装公司通过精益生产管理的方式,实现了生产过程的高效、卓越的质量和最小化的浪费。
这些公司主要通过以下措施来提升业绩。
首先,改善生产流程。
服装企业会合理安排生产线,确保各个生产环节之间的流程顺畅,并减少传统大量存货。
其次,强调员工培训和参与,使每个人都能理解自己的角色和责任,并为精益生产目标贡献力量。
再次,注重质量管理。
这些企业通过引入严格的质量控制措施,确保产品达到最高标准。
结论:以上三个案例展示了精益生产管理在不同行业中的成功应用。
丰田汽车公司、波音公司和日本服装公司通过实施精益管理的策略,优化了生产流程、提高了质量、降低了成本,进而实现了业务的卓越表现。
这些成功案例表明,精益生产管理已经成为许多企业提高竞争力和持续发展的重要工具。
精益生产案例

精益生产案例
精益生产是一种通过最大限度地减少浪费,提高效率和质量的生产方式。
它通过精益思维和方法,帮助企业实现更高效的生产和运营,从而提升竞争力。
下面我们将介绍一个精益生产的案例,以便更好地理解这种生产方式的实际运用。
某汽车制造公司引入精益生产理念后,取得了显著的成果。
首先,他们通过价值流映射,清晰地了解了整个生产流程中的价值和浪费,找到了许多可以改进的地方。
他们发现,在零部件供应和生产线的布局上存在很多浪费,因此他们重新规划了供应链,并优化了生产线的布局,大大减少了不必要的等待和运输时间,提高了生产效率。
其次,他们通过实施精益生产工具,如5S、Kanban和持续改进等,不断优化生产流程。
通过5S整理工作环境,使生产现场更加整洁、有序,减少了寻找工具和材料的时间;通过Kanban管理零部件库存,避免了过多的库存积压,降低了库存成本;通过持续改进,鼓励员工不断提出改进意见并实施,使生产过程更加高效和灵活。
最后,他们注重员工的培训和激励,使员工更加积极参与精益生产的实施。
他们为员工提供了相关的培训课程,让员工了解精益生产的理念和方法,激发了员工的改进意识。
同时,他们建立了激励机制,奖励那些提出优化建议并得到认可的员工,激励员工积极参与精益生产的实施。
通过以上的案例,我们可以看到精益生产在实际应用中取得了显著的成果。
它不仅帮助企业减少了浪费,提高了效率和质量,还激发了员工的改进意识,促进了企业持续发展。
因此,精益生产不仅是一种生产方式,更是一种管理理念,它可以帮助企业在竞争激烈的市场中立于不败之地。
希望以上案例能够对大家有所启发,促使更多的企业引入精益生产,实现持续改进和发展。
精益生产改善案例

精益生产改善案例
精益生产是一种以减少浪费、提高效率和质量为目标的生产管理方法,它通过不断改善流程,优化资源利用,实现生产效益的最大化。
下面我们将分享一个精益生产改善的案例,希望能够给大家带来启发。
这个案例发生在一家制造业企业,该企业生产线上存在着大量的浪费,包括等待时间、运输不畅、过度生产、库存积压等问题。
这些问题导致了生产效率低下,成本偏高,产品质量不稳定,客户满意度下降。
为了解决这些问题,企业采取了精益生产的改善措施。
首先,他们对生产流程进行了价值流映射,找出了存在的各种浪费和瓶颈。
然后,他们通过精益工具,比如5S、Kanban、单分钟交换模具等,对生产线进行了优化。
在这个过程中,他们引入了员工参与的改善活动,鼓励员工提出改进建议,并给予奖励。
经过一段时间的努力,企业取得了显著的成效。
生产效率得到了提升,生产周期缩短了,库存量减少了,产品质量得到了保障,客户满意度也有了明显的提升。
企业的整体竞争力得到了增强,市场份额也有所扩大。
通过这个案例,我们可以看到精益生产的改善方法对企业的重要性。
它不仅可以帮助企业降低成本,提高效率,还可以优化资源配置,提升产品质量,增强市场竞争力。
因此,我们建议各个制造业企业都可以尝试引入精益生产的理念,结合自身实际,找出适合自己的改善路径,不断优化生产流程,实现持续改善和增长。
总之,精益生产改善案例告诉我们,只有不断挖掘和消除各种浪费,不断优化生产流程,企业才能够在激烈的市场竞争中立于不败之地,实现可持续发展。
希望这个案例能够给大家带来一些启发,也希望更多的企业可以加入精益生产的改善行列,共同推动制造业的发展和进步。
精益生产经典案例

精益生产改善案例生产管理追求无库存,就是要彻底改变以超量库存保发货的传统做法,变以造型为中心的推动式生产为以清理为起点的拉动式生产。
实行期量流或一个流生产方式,逐步扩大看板生产品种,造型生产线实行柔性生产,生产作业计划和生产统计应用计算机管理,大幅度地压缩工序、在制品和成品库存,最大限度地降低资金占用,提高生产组织管理水平。
质量管理追求无缺陷,就是要不断提高质量管理和产品质量水平。
质量管理要从“全面质量管理”转向“零缺点管理”,进一步减少不良损失,用精益思想研究和实施质量改进和攻关,提高产品的工艺水平。
落实质量责任制,严格厂内质量评审,严肃工艺纪律,使每个环节、每道工序、每名职工都切实做到精心操作,严格把关,确保产品内在质量和表面质量达到优质品标准。
设备管理追求无停台,就是要提高设备的可动率和开动率,提高工装的工艺水平和使用寿命。
要坚持以生产现场为中心,抓好现场巡检,现场维修,实行设备封闭管理。
工装采取快速换模方法,满足小批量多品种生产的需求。
要通过采用一系列有效措施,不断提高设备工装的技术状态,为保证生产顺利进行和生产优质产品提供可靠的必要条件。
成本管理追求无浪费,就是要狠抓投入产出管理,做到少投入,多产出,优质低耗,降低成本。
深入开展三级经济核算,抓好产品收到率、原材料投入、成品产出率、清理合格率等环节的考核。
要整顿库房,对原材料、产成品、备品、备件等重新制定最高最低储备限额,做到用最低的储备满足生产的需要,大幅度地降低消耗,减少浪费,活化资金,降低产品成本。
优化生产,就是全厂每个生产环节都要达到整体优化标准,建立起以车间主任为首,以生产工人为主体,以生产现场为中心的现场“三为”管理机制。
实施生产要素一体化管理,强化现场“5S”管理和定置管理,现场工位器具标准化、改善生产现场环境,提高现场文明生产水平,使生产要素达到最佳状态。
优质服务,就是要强化科室为一线,后方为前方服务。
职能科室要切实转变工作作风,提高工作质量、服务质量和工作效率,充分发挥指导服务的职能。
- 1、下载文档前请自行甄别文档内容的完整性,平台不提供额外的编辑、内容补充、找答案等附加服务。
- 2、"仅部分预览"的文档,不可在线预览部分如存在完整性等问题,可反馈申请退款(可完整预览的文档不适用该条件!)。
- 3、如文档侵犯您的权益,请联系客服反馈,我们会尽快为您处理(人工客服工作时间:9:00-18:30)。
山东宏远肠衣有限公司精益生产案例分析
项目背景:
山东郓城宏远肠衣有限公司属一家私营股份制企业,建于1996年11月。
公司占地面积18000平方米,固定资产518万元,按欧盟标准承建的生产线两条及一套完整的现代化办公设备。
生产厂区布局整齐,环境幽雅已取得国家商检部门的卫生注册。
现为中国肉类协会天然肠衣分会会员,拥有独立的进出口权及欧盟注册。
宏远肠衣主要生产盐渍山、绵羊及猪肠衣的各种规格产品,产品主要销往欧洲国家和地区及日本,业务往来以"诚心诚意"为原则。
产品质量以"客户满意"为标准,企业信誉一直受到外商的好评。
年生产能力达1000余万桶。
虽然宏远肠衣基础管理及效益相对同行企业要好,但基于宏远肠衣未来三年技术及人才扩张战略需要,宏远肠衣领导层决定通过管理咨询进一步提高生产管理的精细化和标准化,通过管理培训较全面的提高全体员工的工作技能。
宏远肠衣精益生产项目2005年5月立项并启动。
项目内容主要包括:生产精细化管理、生产流程优化、动作研究及动作规范、全员技能培训等。
项目效果:
项目组通过对企业深入细致的现场考察以及广泛的员工访谈,分析出企业现状中隐藏的问题,重点包括在制品积压严重(5月份清案子清出8000把肠衣,金额接近80万元),生产流程尤其是质量检验流程存在严重不足,造成因返工而重复量码严重影响生产效率,班组及工作台布局不尽合理影响工作效率,企业班组长、主管等管理技能严重不知应岗位要求,生产工人操作标准不详细影响作业效率等。
针对以上问题,项目组制定了工作计划措施,组织编制了中国肠衣行业140多年来第一部生产标准,调整了生产作业流程和检验流程,规范了现场生产管理,为企业员工进行了多轮管理理念和技能培训,重点包括5S与精益生产培训、员工职业化培训、QC工具培训等,以及其他相关督导服务。
通过管理咨询和培训服务,企业收效非常明显。
取消了“集中清案子”这一行业痼疾,相当于每月增加4-5个工作日,在制品积压由8000把减少到千余把,日产出数量在人员数量不变的情况下由每天1500把提高到2000把以上。
管理人员管理的意识和能力均得到明显的提升,全体员工学习的主动性普遍增强,员工的积极心态和自信心等大为增强,员工主动流失率几乎为零。
青岛前丰制帽有限公司5S与精益生产咨询
项目背景:
青岛前丰制帽成立于1994年,是一家帽子专业生产厂家,拥有3个工厂,占地总面积360亩,建筑总面积5万平方米,制帽设备2000余台,其中电脑绣花机100台,拥有职工1500余人。
公司注册资本1000万元,投资总额9000万元。
公司主要设计生产棉、毛、麻、化纤、皮革等多种面料、多种款式的运动帽、工作帽、时装帽、广告帽等。
产品销往美国、韩国、日本、加拿大、墨西哥、南美洲及欧洲等多个国家和地区。
青岛前丰制帽经过十余年的发展,市场不断拓展,与此同时,市场竞争压力也日渐增大,为挖掘公司生产潜力,降低损耗,提高效率,进一步增强公司竞争力,前丰制帽领导层决定通过管理咨询进一步提高公司生产管理的精细化和标准化,通过管理培训较全面的提高全体员工的工作技能。
通过深入调研,青岛前丰制帽在生产管理中存在以下问题:
生产布局混乱,现场杂物堆积,在制品积压严重,现场物流不顺畅,现场存在很多让员工犯错误的死角。
计划管理缺乏统筹管理,生产计划缺乏权威性,计划员多角色:业务员、跟单员、计划
员、采购员,信息的及时有效性差,产能、进度,计划总体控制能力和细化不足
物流管理方面,供方选择不充分,采购计划不明确,到货质量不确保严重影响交期,库房管理混乱,物料分类、编码、标识不到位,剩料没有及时处理。
技术和质量管理严重缺乏标准,比如采购标准、检验标准,标准细化不到位,工艺操作规程不能真正起到指导生产的作用。
解决措施:
员工理念和技能提升。
目前公司的员工大多来自经济欠发达地区,文化层次较低,现代化产业工人的理念和技能缺乏。
管理人员大多从生产一线成长起来,缺乏职业化的管理技能培训。
以上两点是目前中国大多数企业尤其劳动密集型企业所面对的共同问题。
培训内容如下:1、优秀员工的职业理念;2、5S与精益生产培训;3、管理基本技能培训(管理理念、管理工具等);4、团队精神培训等。
现场管理以5S作为应用技术,制定详细可行的现场标准和员工素养标准;成立废品回收小组,集中处理以前的现场积压和生产中废料的回收利用;在5S实施取得成效、在制品大量减少的前提下,规范调整了生产线的布局,使产品流程更加顺畅。
2007年,公司在5S的基础之上,推行“一个流生产”(一个流生产的详细介绍见下面相关文章),通过培训和实际效果转变全体员工的生产理念,认识到产品流程积压的危害,使生产流程中绣花工序的生产服从后工序缝纫工序的要求;强化拉动式计划的实施和监督;绣花工序推行快速切换技术;优先补单安排;最终一个流生产得以顺利推行,产品生产周期缩短明显。
随之编制详细实用的质量标准和生产工艺标准,进一步提升产品的质量水平。
咨询效果:
通过咨询,企业在以下方面获得收益:
员工理念和技能:大部分员工能够正确认识个人与企业的关系,做到个人目标和企业目标的协同,2006年春节过后,员工主动流失率低于3%。
认识到规范做事、精细做事的重要性以及浪费的识别和解除的方法,同时也深刻认识到持续学习与创新的重要性。
管理人员能够掌握基本的管理技能和工具,比如拉动式计划、4W1H、4M1E、PDCA的管理方法和技术。
现场的规范流畅。
通过5S的推行实施,在制品积压减少50%,生产效率提高30%。
生产流程中在制品的积压量从项目开始前的800万元,压缩到450万元。
革除了企业十多年来使用袋子和箱子作为周转器具的习惯,同时可以有效解决个人记件和企业整体效益的矛盾。
2007年“一个流生产”实施的成功,生产流程中在制品的积压量从5月份的350万元,下降到9月份的170万元,产品生产周期明显缩短,8月份一个5000打的定单之前的生产周期需要20多天,而现在只需要5天。
一个流生产实施后现场效果见右边部分照片。
目前青岛前丰制帽有限公司在董事长和总经理的带领下,公司上下掀起了持续学习、提升理念和全员革新的高潮。