第六章 石油炼制中废气来源及处理
植物油厂废气的控制及处理

植物油厂废气的控制及处理作者:常颜辉来源:《中国新技术新产品》2009年第13期摘要:植物油厂生产过程中,不可避免地会产生一定量的废液、废气和废渣。
相对来说,植物油厂的废液较多,过去人们提到“三废”处理,主要是对废液的处理,而往往忽视油脂生产过程中的大气排放物和臭气。
随着人民对环境的要求越来越高,如何控制和处理植物油厂的废气,已提到了议事日程上来。
关键词:植物油;大气排放;车间现就植物厂的废气来源及控制和处理方法简述如下。
1 油厂大气排放及臭气的来源1.1 油厂大气排放物来自气力输送和除尘系统。
植物油厂的固体物料运输除了采用带式输送机等机械输送设备外,还常常用到气力输送;油料预处理工段为保证车间工艺及卫生要求,在有粉尘逸出的地方也需要通风除尘系统。
不管是气力输送还是通风除尘,均需向空气中排放废气,尽管废气须经二级除尘处理达标后才排放,但受除尘效果及操作因素控制,不可避免地会有一些粉(灰)尘排入大气中,其排放量主要受油料处理量及系统的处理能力而定。
来自蒸炒工序。
植物油料在炒坯过程中,为了达到入榨要求,要去除一定的水份,从而产生大量的蒸汽,现有的设备一般是直接排放到大气中。
这类排放物除水份外还有少量油料中的挥发性物质,由于数量少,影响有限。
来自油脂浸出尾气。
油脂浸出时要用到工业乙烷等溶剂,这些溶剂在浸出过程中与料坯进行浸泡、萃取,得到混合油和湿粕,然后分别再将溶剂从湿粕和混合油中蒸发、蒸馏,经冷凝和分水后循环使用。
同时,在浸出过程中料坯带入的不凝气体成为尾气将被排放,其中的溶剂一般用吸收法或冷冻法加以回收,但仍将带走部分溶剂。
一般浸出车间总的溶剂消耗要求控制在5kg/t料以下。
据测算,其中相当一部分溶剂(三分之一左右)是从尾气中逃逸的,如果尾气中夹带溶剂过多,既不安全,也容易造成对周围环境的影响。
来自油料、油脂精炼车间。
油脂的脱色和脱臭工序,为了保证工艺效果,一般必须在真空条件下进行,油脂中的挥发性有机物(脱臭馏出物)被真空系统抽出,再经真空泵由冷却水喷射而直接冷凝下来并混入水中。
石油炼制中废气来源及处理

过程气进入转化器的温度可按下述要求确定: ① 比预计的出口硫露点高14~17℃ ② 一级转化器的温度应足以使COS和CS2充分水解成H2S和CO2 ③ 获得令人满意的反应速度下,温度尽可能低,以提高H2S转化率
石油炼制中的废气处理-酸性气回收
石油炼制中的废气处理-酸性气回收
余热锅炉(又称废热锅炉) ① 回收热量以产生高压蒸汽(蒸汽压力通常为1.0~3.5MPa) ② 降低过程气温度,满足下游要求
转化器 ① H2S与SO2在催化剂床层上继续反应生成元素硫; ② COS和CS2等有机化合物水解为H2S与CO2
石油炼制中的废气处理-酸性气回收
• 荷兰Comprimo 公司改进SCOT工艺中的吸收-再生部分 • 二段再生塔:一段再生产生半贫液部分半贫液返回吸收塔中
部,另一部分半贫液进入二段再生塔进行深度气提,得到的超 贫液再送到吸收塔的顶部 • 降低超贫液的温度 • 效果:超贫液的低温和超低H2S 分压均有利于H2S在吸收塔内 醇胺溶液中的溶解,降低排入尾气中H2S 的浓度至10-50 ppmv;再生的蒸汽消耗量节省30%
定,常规分流法则炉温过高) ② 进入反应炉的原料气量提高至1/3以上
两种分流法的问题:部分原料气直接进入催化反应段,当原料气 中含有重烃尤其是芳香烃时,会在催化剂上结焦,影响催化剂的 活性和寿命,同时影响硫磺颜色
石油炼制中的废气处理-酸性气回收
克劳斯法工艺—硫循环法(很少采用) H2S含量为5~10%时,将部分硫产品喷入反应炉燃烧 → 维持炉温
直流法三级硫磺回收工艺
石油炼制中的废气处理-酸性气回收
克劳斯法工艺—常规分流法 ① H2S含量15~30%时,用直流法难以使反应炉内燃烧稳定 ② 1/3原料气 + 化学计量配给的空气进入反应炉内,使原料气中
石油炼制工程
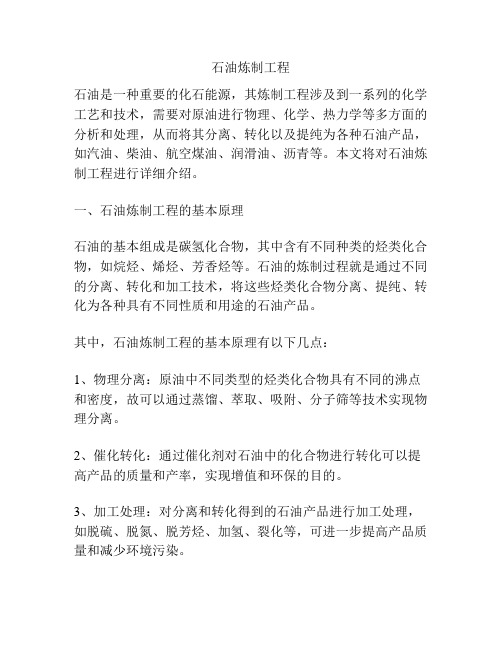
石油炼制工程石油是一种重要的化石能源,其炼制工程涉及到一系列的化学工艺和技术,需要对原油进行物理、化学、热力学等多方面的分析和处理,从而将其分离、转化以及提纯为各种石油产品,如汽油、柴油、航空煤油、润滑油、沥青等。
本文将对石油炼制工程进行详细介绍。
一、石油炼制工程的基本原理石油的基本组成是碳氢化合物,其中含有不同种类的烃类化合物,如烷烃、烯烃、芳香烃等。
石油的炼制过程就是通过不同的分离、转化和加工技术,将这些烃类化合物分离、提纯、转化为各种具有不同性质和用途的石油产品。
其中,石油炼制工程的基本原理有以下几点:1、物理分离:原油中不同类型的烃类化合物具有不同的沸点和密度,故可以通过蒸馏、萃取、吸附、分子筛等技术实现物理分离。
2、催化转化:通过催化剂对石油中的化合物进行转化可以提高产品的质量和产率,实现增值和环保的目的。
3、加工处理:对分离和转化得到的石油产品进行加工处理,如脱硫、脱氮、脱芳烃、加氢、裂化等,可进一步提高产品质量和减少环境污染。
二、石油炼制工程的基本工艺1、初步分离:在这个阶段,将原油通过加热使得低沸点的烃类化合物蒸发并进一步冷凝成液态油品,就得到了原油的分馏组分,包括轻质馏分、中间馏分和重馏分等。
其中轻质馏分通常用于生产汽油和液化石油气,中间馏分用于生产煤油和柴油,而重馏分则用于生产沥青和蜡等。
2、加氢:加氢技术常常用于提高石油产品的质量和减少环境污染。
通过加入氢气,可以对石油中的烯烃、芳香烃等不稳定化合物进行加氢还原,减少其中的硫、氮等有害元素的含量,同时提高汽油、柴油等产品的辛烷值和氧化稳定性。
3、催化裂化:该工艺技术可以将重馏分中的长链烃类化合物裂解成较短链的烃类化合物,从而提高汽油和柴油的辛烷值和抗爆性能。
通过加入催化剂进行裂解,可适当降低裂解温度和降低能耗。
4、脱硫、脱氮:这是一种对石油产品进行加工处理的技术,通过将石油产品中的硫、氮等对环境和人体有害的元素去除,减少其排放到大气中的污染物,同时提高产品的质量和使用效果。
石油精炼厂如何处理废弃物和副产品?

石油精炼厂如何处理废弃物和副产品?随着全球能源需求的增加,石油精炼厂在满足能源供应的同时也产生了大量的废弃物和副产品。
这些产物及其处理方式对于环境保护和资源利用至关重要。
本文将介绍石油精炼厂处理废弃物和副产品的常见方法。
1. 废水处理:石油精炼过程中,废水是一种重要的废弃物。
这些废水中含有各种有害物质,如重金属、有机化合物和悬浮物等。
为了避免对水体环境的污染,石油精炼厂通常采用物理、化学和生物处理的综合手段来处理废水。
物理处理包括沉淀、过滤和吸附等过程,化学处理主要是利用氧化、还原和中和等反应来去除有害物质,而生物处理则通过微生物的作用将有机物降解为无害物质。
2. 催化剂回收:在石油精炼过程中,催化剂被广泛应用于催化裂化、重整和加氢等反应中。
随着反应的进行,催化剂会失活或污染,需要进行处理或更换。
为了提高资源利用率和减少环境污染,石油精炼厂通常采用催化剂的再生和回收。
再生包括焙烧、洗涤和再活化等步骤,回收则通过物理和化学方法将有价值的组分从催化剂中分离出来,并进行再利用。
3. 废气处理:石油精炼过程中,会产生大量的废气,其中包括挥发性有机物、硫化物和氮化物等有害物质。
这些废气对于大气环境和人体健康都具有潜在的危害。
为了控制废气排放,石油精炼厂通常采用物理吸附、化学吸收和催化氧化等手段进行处理。
物理吸附利用活性炭等吸附剂吸附有害物质,化学吸收则通过溶液中的化学反应将有害物质转化为无害物质,催化氧化则利用催化剂促进废气中有害物质的氧化反应。
4. 副产品利用:除了废弃物外,石油精炼过程中还会产生各种副产品,如焦油、沥青和重油等。
这些副产品在传统意义上并不具有直接经济价值,但通过进一步加工和改性,可以转化为有用的化工产品。
例如,焦油可以用于制备沥青和染料,沥青可以用于道路建设,重油可以用作燃料。
通过副产品的综合利用,不仅可以减少资源的浪费,还可以提高石油精炼厂的经济效益。
总之,石油精炼厂处理废弃物和副产品是一个综合性的工程,涉及废水、催化剂和废气等多个方面。
石油化工行业VOCs废气处理工艺简介

石油化工行业VOCs废气处理工艺简介1、高浓度废气处理工艺1)洗涤法◆原理:将气体通入含喷淋系统的洗涤塔中,气体经过填料床的均匀分布,与洗涤液充分接触,利用气体中污染物的溶解性或化学性质,将气体中的污染物吸收或通过化学反应去除,从而达到气体净化的目的。
除此之外,洗涤塔还有降温、除尘、除油的作用。
通常采用的方式为逆流式洗涤。
常用的洗涤剂包括清水、植物液、硫酸溶液、氢氧化钠溶液、次氯酸钠溶液等。
其中清水洗涤和植物液洗涤是利用污染物的溶解性,植物液的一些基团也参与化学反应;硫酸溶液洗涤、氢氧化钠溶液洗涤和次氯酸钠洗涤则是利用了污染物的化学性质。
◆特点(1)反应快速,洗涤剂与气体接触的时间一般不超过12秒;(2)适用性强,常和其它处理工艺结合,是有效的预处理设施;(3)常用立式结构,节约占地;(4)操作简单,除了定期更换洗涤剂外基本为无人操作(洗涤剂更换也可通过增加配套PLC自动控制系统实现无人操作);(5)工艺灵活,若气体性质发生变化,则通过更换洗涤剂即可继续使用;(6)建设成本低。
◆适用条件适用性较强,可起到除尘、除油、降温、除臭的作用,常作为其它工艺的预处理设施。
◆应用于石化行业洗涤法应用于石化行业的具体表现形式为油洗塔。
油洗塔是乙烯装置热回收区的关键核心设备,其作用是将来自裂解炉的裂解气中的重油和轻油组分冷凝,并最大的实现热量回收。
原理为将来自裂解炉的裂解气和急冷油/水逆流接触冷却,裂解气中的重油和轻油组分因此得以冷凝。
冷凝的热媒和冷媒可采用直接或间接接触形式进行热交换。
2)催化燃烧法◆原理通过引风机将废气送入净化装置换热器换热,再送入到加热室,通过加热装置,使气体达到催化反应温度,再通过催化床内催化剂作用,使有机气体分解成二氧化碳和热能。
◆特点(1)高浓度时耗能仅为风机功率,浓度较低时自动间歇补偿加热;(2)催化起燃温度为300~500℃。
◆适用条件(1)中、高浓度的有机废气,最佳浓度2500-3000mg/m³;(2)主要针对烃类、苯类、酮类、醚类、酯类、醇类、酚类。
石油炼化尾气处理方案

石油炼化尾气处理方案石油炼化过程中产生的尾气包含了大量的有害物质,对环境和人体健康都会造成严重影响。
因此,尾气处理方案成为石油炼化企业必须面对的重要课题。
首先,尾气处理方案可以采用物理方法进行处理。
物理方法主要包括分离和吸附。
分离是将尾气中的固体颗粒、液滴和液体物质分离出来,可以利用重力沉淀、离心分离等方法进行。
吸附是利用吸附剂吸附尾气中的有害物质,然后进行再生或处理。
这种方法可以有效去除尾气中的颗粒物、挥发性有机物等。
其次,化学方法也是一种有效的尾气处理方案。
化学方法主要通过化学反应将尾气中的有害物质转化为无害物质。
例如,可以使用催化剂将尾气中的一氧化碳、二氧化氮等气体转化为无害的二氧化碳和氮气。
此外,还可以使用化学药剂将尾气中的有机物进行氧化或还原反应,从而降低有机物的浓度。
另外,生物处理也是一种有效的尾气处理方案。
生物处理利用微生物对尾气中的有害物质进行降解分解,将其转化为无害物质。
生物处理可以使用活性污泥法、固定化法等方法进行。
通过优化微生物种类和环境条件,可以实现高效降解尾气中的有害物质。
最后,综合利用也是一种重要的尾气处理方案。
综合利用指的是将尾气中的有害物质转化为有价值的化学品或能源。
例如,可以利用尾气中的有机物生产生物燃料或化工原料。
此外,还可以通过从尾气中回收有价值的物质,如石油中的硫、氮等元素,从而实现资源循环利用。
总之,针对石油炼化尾气的处理,可以采取物理、化学、生物和综合利用等多种方法进行。
不同的尾气特点和处理要求可能需要采用不同的方案。
因此,石油炼化企业需要根据实际情况选择合适的尾气处理方案,以保护环境,并确保生产过程的可持续发展。
油田挥发性有机物的来源及控制措施

2017年12月 ENVIRONMENTALPROTECTION OFOIL & GASFIELDS Vol.27 No.6 ·27·
油田挥发性有机物的来源及控制措施
周 娟1,2 张 海 玲1,2 邱 奇1,2
(1.中 国 石 油 长 庆 油 田 分 公 司 油 气 工 艺 研 究 院 ;2.低 渗 透 油 气 田 勘 探 开 发 国 家 工 程 实 验 室 )
石 油 生 产 过 程 中,由 于 生 产 设 备 和 装 置 多 且 分 散,加 上 长 距 离 的 原 油 集 输 管 线,VOCs的 排 放 无 规 律,浓度变化较大,成分复杂,因此治 理难 度 较 大。目 前,国内对油田 VOCs的排放和控制尚处于研 究 摸索 阶段。
本文结合油田原 油 生 产 实 际,分 析 和 梳 理 VOCs 的来源和控制技术。
关键词 石油开采;挥发性有机物 (VOCs);源解析;控制措施
DOI:10.3969/j.issn.10053158.2017.06.007 文 章 编 号 :10053158(2017)06002702
0 引 言
挥发性有机物(VOCs)是大气臭氧和二次 气 溶胶 形成的主要前体物之一,是导致 雾霾 天气形 成 的 主要 原因之一。“十三五”规划中明确 提出 在 重点 区域、重 点行业推进 VOCs排放总量控制,目前多个省 份 已经 颁布 实 施 了 VOCs污 染 整 治 实 施 方 案。 推 进 VOCs 污染的治理已经成为当下大气污染控制的重要任务。
④使用罐车装卸原油时,采 用液 下装卸 系 统 降低 VOCs的 挥 发 损 失 。
⑤ 废 水 处 理 采 用 生 化 处 理 系 统 时 ,需 加 盖 处 理 。 ⑥ 油 井 套 管 气 尽 可 能 回 收 利 用 ,避 免 直 接 放 空 。 ⑦精细化 管 理,减 少 “跑、冒、滴、漏”现 象。 加 强 设备设施的日 常 管 理,严 格 执 行 操 作 规 程,定 期 开 展 泄漏检 测 与 修 复。 减 少 原 油 的 输 转,控 制 收 发 油 速 度,如需要人工 上 储 罐 量 液 位,尽 可 能 选 择 罐 内 外 压 差最小的清晨或傍晚时操作。
石油废气处理方法

石油废气处理方法
石油废气处理方法有多种,以下是其中几种常见的方法:
1.吸附法:利用活性炭等吸附剂对石油废气中的有机化合物进行
吸附,然后再进行脱附和回收。
这种方法能够有效去除废气中的有机物,达到净化和回收的目的。
2.生物法:利用微生物在适宜的环境下对石油废气中的有机物进
行降解和转化,将其转化为无害或低害的物质。
这种方法具有处理效率高、无二次污染等优点。
3.催化燃烧法:将石油废气中的有机物在催化剂的作用下进行燃
烧,将其转化为无害的二氧化碳和水。
这种方法具有处理效率高、设备简单等优点,但是需要高温燃烧,会消耗大量的能源。
4.冷凝法:将石油废气通过冷凝器进行冷却,使其中的有机物冷
凝成液体状态,然后进行分离和回收。
这种方法具有处理效率高、无二次污染等优点,但是需要消耗大量的能量。
5.膜分离法:利用膜分离技术对石油废气中的有机物进行分离和
回收。
这种方法具有处理效率高、操作简单等优点,但是需要高精度的膜材料和设备。
第六章 石油炼制中废气来源及处理

石油炼制的基本流程
石油一次加工 石油二次加工 石油产品精制
石油炼制产品
石油炼制中的污染物来源
原油二级电化学脱盐工艺流程图
石油炼制中的污染物来源
石油炼制中的污染物来源
370℃
520℃
原油常、减压蒸馏工艺流程图 催化裂化工艺流程图
石油炼制中的污染物来源
石油炼制中的污染物来源
炼厂气处理单元
炼油过程中各类装置(催化裂化、加氢裂化、加氢精制和延 迟焦化等)所产生的气体 含有氢、甲烷、乙烷和乙烯、丙烷和丙烯、丁烷和丁烯、H2S、 COS、CO2等 炼厂气脱硫 Claus法回收硫磺
① H2S选择性催化氧化为元素硫,反应不可逆 ② H2S催化氧化为S及SO2,然后去Claus催化反应段(Selectox工艺)
Selectox工艺有一次通过法和循环法
• H2S含量<5%时可采用一次通过法 • H2S含量>5%时将过程气进行循环(控制过程气出口温度<371℃)
石油炼制中的废气处理-酸性气回收
反应炉、余热锅炉、转化器、硫冷凝器、再热器等 反应炉(又称燃烧炉) 正常炉温 980~1370℃ 主要作用 ① 使原料气中1/3体积的H2S氧化为SO2; ② 使原料气中烃类、硫醇氧化为CO2等惰性组分 反应炉形式 ① 外置式(与余热锅炉分开设置),硫磺回收规模超过30t/d比较适用 ② 内置式(与余热锅炉组合为一体) 反应物在炉内的停留时间一般至少为0.5s
克劳斯法工艺—Selectox循环直接氧化法
石油炼制中的废气处理-酸性气回收
酸气中 >55% H2S含量 适用 工艺 30-55% 15-30% 10-15% 预热酸气 和空气的 分流法 5-10% < 5% 硫循 环法 直接氧 化法
石油化工行业的环境污染源与治理对策

石油化工行业的环境污染源与治理对策石油化工行业是我国经济发展的重要支柱之一,但其发展过程中也带来了严重的环境污染问题。
本文将从环境污染源和治理对策两个方面探讨石油化工行业的环境污染情况,并提出相应的治理对策。
一、石油化工行业的环境污染源1.大气污染源石油化工行业在生产过程中排放大量气体,其中包括二氧化硫、氮氧化物和颗粒物等。
这些污染物对大气造成直接污染,导致大气质量下降,甚至形成雾霾天气。
同时,部分挥发性有机物还可能生成光化学臭氧,在地表层形成臭氧污染。
2.水体污染源石油化工生产过程中会产生废水,其中富含有机物、重金属等有害物质。
如果未经处理直接排入水体,会引起水质恶化,并危及人类健康。
此外,在危险品运输和储存等环节也存在意外泄漏的风险,导致水域受到污染。
3.土壤污染源石油化工行业使用大量的化学品,包括溶剂、催化剂等。
这些物质在生产和储运过程中容易发生泄漏,导致土壤污染。
通过土壤微生物和植物的吸收转运,有害物质进入食物链,并对人体健康造成潜在威胁。
4.固体废弃物污染源石油化工行业产生大量固体废弃物,包括渣滓、废料、残渣等。
未经严格处理和处置,这些固体废弃物可能直接投放到环境中,影响土地资源的可持续利用,并加重环境问题。
二、石油化工行业的环境治理对策1.减少排放措施通过技术改造和装备更新提升石油化工企业的生产水平,减少污染物排放。
采用低硫低氮燃料替代高硫高氮燃料,引入先进的排放控制技术如脱硫除尘设备等,有效降低大气污染。
2.强化废水治理加强对石油化工企业废水处理的监管力度,确保达到国家规定的排放标准。
推广生物降解、膜分离等先进技术,提高废水处理效率。
同时,鼓励企业实施循环利用,将符合要求的废水用于生产过程中。
3.加强事故预防与应急处置完善石油化工行业的安全生产管理制度,严格落实各项安全措施和监测预警机制,以避免事故发生。
对于危险品运输和储存环节,建立健全应急处置体系及装备,并组织常态化演练,确保在突发情况下能够做出及时反应。
石油炼制工业固体废弃物的产生情况及处置措施分析

石油炼制工业固体废弃物的产生情况及处置措施分析摘要:从生产设施、辅助生产设施、环保设施三个方面对石油炼制工业固体废弃物的产生情况进行了统计分析,并以《国家危险废物名录》为依据对固体废弃物的种类进行了判别,在此基础上提出了分类处置措施,最后对目前石油炼制工业固体废弃物在处置过程中存在的主要问题及解决思路进行了展望。
关键词:石油炼制工业固体废物分类处置1 概述随着石油产量的增长,以石油及其加工产品为基本原料的石油化学工业产生的固体废弃物数量也逐年增长,截至20__年1月1日,我国内地共有石油炼制企业52座,原油加工能力35330.0万吨每年[1]。
石油炼制企业生产过程中,有多种工业固体废弃物产生,主要包括废催化剂、废瓷球、废矿物油(泥)、碱渣等,并且多为危险废物。
如处理不当,固体废弃物中有害物质便会通过雨水和大气到处扩散,污染大气、地表水和地下水,使环境遭到严重的破坏,危害人类的健康。
国外对固体废弃物的研究起步较早,美国1977年颁布了“资源保护及回收法案(RCRA)”、1984年修订了RCRA关于危险固体废弃物(HSWA)的修正案及一系列有关固体废弃物的储存、运输、排放和处置的法规,通过执行这些法律、法规,使各石油化工生产厂家建立了一套行之有效的环境保护机制[2]。
在我国,“三废”对环境的污染已引起国家的高度重视,制订了一系列完善的法规,对污染的治理技术也日臻完善和不断提高,但对废渣的治理起步较晚[3]。
本文对石油炼制工业固体废弃物的产生情况进行了统计分析,并对工业固体废弃物的资源化、减量化、无害化处置途径进行了介绍,最后对当前国内石油炼制工业固体废弃物处置过程中存在的问题及解决方案进行了展望。
2 产生情况石油炼制工业产生的工业固体废弃物有废催化剂、废瓷球、废矿物油(泥)、碱渣等,主要来自于生产设施、辅助生产设施和环保设施,其中生产设施包括渣油加氢装置、重油催化裂化装置、蜡油加氢裂化装置、柴油加氢装置、石脑油加氢装置、催化重整装置、苯抽提装置、甲基叔丁基醚装置、液化气脱硫醇装置等;辅助生产设施包括变压吸附装置、硫磺回收装置、储运装置等;环保设施主要有污水处理装置。
石油储罐废气治理工程方案

石油储罐废气治理工程方案一、项目背景及概述石油储罐是用来储存原油、成品油等石油制品的设备,在储存过程中会产生大量挥发性有机物(VOCs)废气。
这些废气如果排放到大气中会对环境造成严重污染,同时也会对工人的健康造成危害。
因此,对石油储罐废气进行治理工程是非常必要的。
本文将详细介绍石油储罐废气治理工程的方案,包括废气的产生和成分分析、治理手段的选择、技术参数的确定、设备选型等内容,以期为相关企业提供参考。
二、废气产生和成分分析1.废气产生石油储罐废气主要来源于以下几个方面:(1)充放油作业:在对储罐进行充放油操作时,会产生大量挥发性有机物。
(2)气体泄漏:由于储罐设备老化或操作不当,会产生气体泄漏,导致废气排放。
(3)储罐通风:储罐在存储过程中会进行通风操作,导致挥发性有机物的排放。
2.成分分析石油储罐废气的成分主要包括苯、甲苯、二甲苯、乙苯、酚类、氨类、硫化氢等有机物,其中多为挥发性有机化合物,具有较强的毒性和危害性。
三、治理手段的选择根据石油储罐废气的产生和成分分析,选取合适的治理手段对废气进行处理是非常重要的。
目前常见的治理手段主要包括吸附、压缩、吸收、氧化等方法。
在对比各种治理手段的特点和适用范围后,我们决定采用吸附和氧化的联合处理技术。
1.吸附技术吸附是利用吸附剂对废气中的有机物进行吸附,从而实现净化的技术。
吸附剂的选择对处理效果具有重要影响。
在本项目中,我们将选用具有较高吸附性能和稳定性的活性炭作为吸附剂,通过对废气进行适当的吸附过程,将有机物去除。
2.氧化技术氧化技术是利用氧化剂将有机物氧化分解成无害物质的一种处理方法。
在本项目中,我们将使用催化氧化技术,通过添加催化剂促进有机物的氧化反应。
四、技术参数的确定1.废气处理量:根据石油储罐的运作情况和废气产生量,确定废气处理量为3000立方米/小时。
2.吸附过程参数:活性炭的吸附容量为20g/g,吸附剂的吸附时间为3-5分钟。
3.氧化过程参数:催化氧化剂的添加量为0.1-0.5%,氧化温度为180-300摄氏度,氧化反应时间为2-3秒。
炼油厂废气工业流程

炼油厂废气处理工艺流程一般包括以下步骤:
1. 吸收:将废气引入吸收塔,喷入吸收剂并进行充分搅拌和接触。
吸收剂可以包括碱溶液、酸溶液或有机溶剂等,用于吸收废气中的有害物质。
2. 净化和干燥:在吸收塔中,废气中的有害物质被吸收剂吸收或中和,从而去除有害物质。
同时,吸收剂也可能会吸附一些水蒸气和微小颗粒物。
为了进一步净化吸收剂,并去除可能残余的湿气和颗粒物,需要对吸收剂进行干燥和净化的操作。
3. 循环使用吸收剂:经过净化和干燥的吸收剂需要循环使用,以充分利用资源并减少排放。
可以使用干燥器将吸收剂中的水分去除,以确保其干燥并可以再次使用。
4. 排放:经过上述处理步骤后,废气中的有害物质已经去除,达到了排放标准,可以将其排放到大气中。
整个工艺流程的关键在于确保废气得到充分的处理,同时也要注意节约资源、减少排放和环保要求。
在具体操作中,可能还需要根据炼油厂的实际情况和废气性质进行调整和优化。
另外,为了确保炼油厂废气处理工艺的顺利进行,需要注意以下几点:
1. 定期检查和维修设备,确保设备的正常运行,避免因设备故障导致废气处理效率下降。
2. 严格控制吸收剂的质量和使用量,以确保废气得到充分的吸收和处理。
3. 定期监测废气处理效果,确保废气达标排放。
4. 加强员工培训,提高员工环保意识和操作技能,确保废气处理工艺的正确实施。
5. 积极配合政府监管部门,遵守相关环保法规,确保炼油厂废气得到妥善处理。
总之,炼油厂废气处理工艺需要综合考虑环保要求、资源利用、排放控制和操作管理等多个方面,以确保炼油厂的正常运营和环境保护之间的平衡。
石油行业存在的环境污染及治理方法

石油行业存在的环境污染及治理方法一、环境污染带来的问题近年来,随着全球工业化进程不断加快,石油行业作为主要的能源供应来源之一,扮演着重要角色。
然而,在满足人们用能需求的同时,石油行业也面临着环境污染的挑战。
以下将从空气和水源两个方面分析石油行业存在的环境污染问题。
1. 空气污染在炼油过程中产生大量尾气回收物和废弃物气体。
这些废弃物排放包括有害颗粒物、硫化物、一氧化碳等有毒有害成分与另外还会释放出温室气体(二氧化碳)等造成臭名昭著国际危害因此空気質素差会给周边居民健康造成直接或间接影响,并可能对大范围地区产生影响。
2. 水源污染除了空气污染外,石油行业还对水源产生不良影响。
原始开采导致地下水质量下降,增加了灌溉、饮用水源的风险。
而炼油过程中的工业废水排放则是主要问题之一。
废水中含有重金属、有机物等污染物质,会直接或间接危害水生生物和人类健康。
二、治理方法探讨面对这些环境问题,石油行业必须积极采取措施来减少环境污染并保护自然资源。
以下是几种有效的治理方法:1. 技术改进石油公司可以通过投资新技术来减少尾气排放,并提高炼油工艺的效率和环保性能。
例如,在挖掘阶段,采用现代化设备和技术可以最大限度地降低地下水和土壤受到污染的风险;在储运过程中使用封闭式系统可避免挥发性有机物泄露等。
2. 废弃物处理针对产生的大量固体和液体废弃物,应该建立规范的处理体系进行分类处置。
通过科学合理利用资源构建合适成品处理设备及操作流程对于压缩/整形/焚化等后续处理方式进行必要操作处置方可产出高价值产品废弃物的无害化处理。
3. 环境监测与管理石油企业应加强对各个环节的严格监管,在生产过程中搭建健全环保基础设施,并实施定期检查和报告制度。
此外,引入第三方评估机构参与环境评估工作,提高治理透明度。
4. 推广清洁能源转型减少对传统石油资源依赖,推动清洁能源技术创新和应用。
逐步替代化石能源使用并发展替代品如太阳能、风力发电等可以减少对环境的进一步污染,并降低二氧化碳排放量。
2021年九年级上学期化学人教新版第六章:燃料及其利用7.2燃料的合理利用和开发《讲义解析版》

燃料的合理利用和开发知识集结知识元燃料的合理利用与开发知识讲解•1.三大化石燃料:煤、石油、天然气(均为混合物,并且均为不可再生能源)•煤——“工业的粮食”•为了使煤得到综合利用,可以将煤干馏,即隔绝空气加强热,使煤分解为焦炭、煤焦油、煤气等有用的物质。
(干馏是化学变化)•煤燃烧排放的污染物:SO2、NO2、CO、烟尘等。
(SO2、NO2可导致酸雨)•煤中主要含碳元素。
•石油——“工业的血液”•由石油炼制的部分产品和主要用途:溶剂油、汽油、航空煤油、煤油、柴油、润滑油、石蜡、沥青。
•利用石油中各成分的沸点不同,可以将石油分馏,使石油中各成分分离。
(分馏是物理变化)•汽车尾气中的污染物:CO、未燃烧的碳氢化合物、氮的氧化物、含铅化合物和烟尘。
•石油中主要含碳、氢元素。
•天然气•在我国农村,使用沼气的好处如下:•①可以解决生活用燃料问题;②改善农村环境、卫生状况;③提高肥效。
•甲烷燃烧的化学方程式:CH4+2O2CO2+2H2O(甲烷燃烧会产生明亮的蓝色火焰。
)•甲烷的化学性质:可燃性。
•甲烷的物理性质:无色无味的气体,密度比空气小,极难溶于水。
•甲烷是最简单的有机物、相对分子质量最小的有机物。
•天然气的主要成分是甲烷(沼气)。
•可燃冰:科学家们在海底发现了大量可燃冰,它是一种甲烷水合物,是甲烷与水在低温高压下形成的。
•可燃冰的缺点:如果在开采中甲烷气体大量泄漏于大气中,会造成更加严重的温室效应。
•可燃冰的优点:能量高、热值大,是替代化石燃料的新能源。
•2.燃料燃烧对空气的影响•煤燃烧时排放出SO2、NO2等污染物,这些气体或气体在空气中反应后的生成物溶于雨水,会形成酸雨。
•酸雨危害的模拟实验【实验操作】向一个空集气瓶和一个充满SO2的集气瓶中各加入少量水。
分别将表中所列物质放入上述两种液体中,观察现象。
【实验现象】见下表•【实验结论】酸雨呈酸性,能与多种物质发生反应。
酸雨的危害:①腐蚀大理石建筑、钢铁制品;②污染江河湖海,使土壤酸化;③影响水中动植物生长,破坏森林、农作物的生长。
石油化工行业的污染排放问题与治理方案
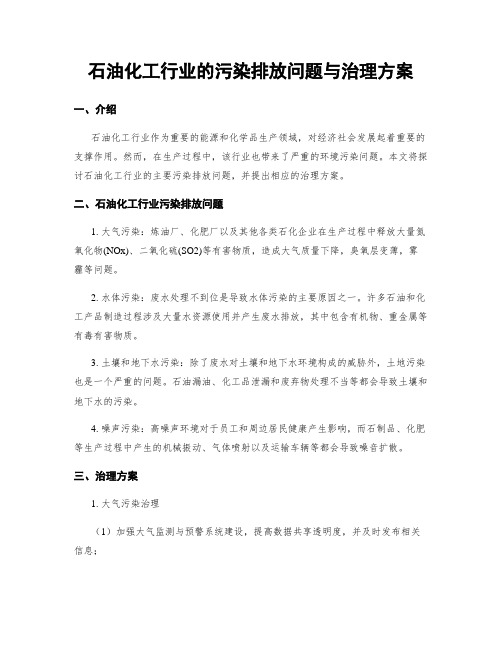
石油化工行业的污染排放问题与治理方案一、介绍石油化工行业作为重要的能源和化学品生产领域,对经济社会发展起着重要的支撑作用。
然而,在生产过程中,该行业也带来了严重的环境污染问题。
本文将探讨石油化工行业的主要污染排放问题,并提出相应的治理方案。
二、石油化工行业污染排放问题1. 大气污染:炼油厂、化肥厂以及其他各类石化企业在生产过程中释放大量氮氧化物(NOx)、二氧化硫(SO2)等有害物质,造成大气质量下降,臭氧层变薄,雾霾等问题。
2. 水体污染:废水处理不到位是导致水体污染的主要原因之一。
许多石油和化工产品制造过程涉及大量水资源使用并产生废水排放,其中包含有机物、重金属等有毒有害物质。
3. 土壤和地下水污染:除了废水对土壤和地下水环境构成的威胁外,土地污染也是一个严重的问题。
石油漏油、化工品泄漏和废弃物处理不当等都会导致土壤和地下水的污染。
4. 噪声污染:高噪声环境对于员工和周边居民健康产生影响,而石制品、化肥等生产过程中产生的机械振动、气体喷射以及运输车辆等都会导致噪音扩散。
三、治理方案1. 大气污染治理(1)加强大气监测与预警系统建设,提高数据共享透明度,并及时发布相关信息;(2)推行清洁能源替代计划,加速从传统燃煤到天然气或可再生能源发电转型;(3)实施大规模减排措施,采用先进技术降低NOx、SO2等有害物质排放;(4)加强排放标准管理,鼓励企业投资更新设备以达到更严格的排放标准。
2. 水体污染治理(1)完善废水处理设施建设,在源头上控制并削减有害物质的排放;(2)推进水资源循环利用,提高废水处理设施的效能;(3)加强废水监管,建立完善的管理体系和追溯机制。
3. 土壤和地下水污染治理(1)落实企业主体责任,建立严格、科学的土壤及地下水保护标准,并对企业进行监督检查以确保其执行;(2)加强事故应急预案编制与培训工作,为突发情况提供快速响应措施;(3)开展土壤修复技术研究与示范项目,在已受到污染区域实施生态修复。
石油加工中的废气处理技术
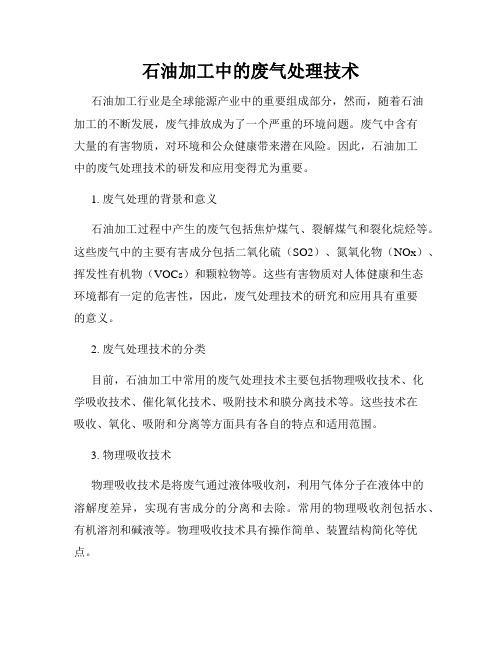
石油加工中的废气处理技术石油加工行业是全球能源产业中的重要组成部分,然而,随着石油加工的不断发展,废气排放成为了一个严重的环境问题。
废气中含有大量的有害物质,对环境和公众健康带来潜在风险。
因此,石油加工中的废气处理技术的研发和应用变得尤为重要。
1. 废气处理的背景和意义石油加工过程中产生的废气包括焦炉煤气、裂解煤气和裂化烷烃等。
这些废气中的主要有害成分包括二氧化硫(SO2)、氮氧化物(NOx)、挥发性有机物(VOCs)和颗粒物等。
这些有害物质对人体健康和生态环境都有一定的危害性,因此,废气处理技术的研究和应用具有重要的意义。
2. 废气处理技术的分类目前,石油加工中常用的废气处理技术主要包括物理吸收技术、化学吸收技术、催化氧化技术、吸附技术和膜分离技术等。
这些技术在吸收、氧化、吸附和分离等方面具有各自的特点和适用范围。
3. 物理吸收技术物理吸收技术是将废气通过液体吸收剂,利用气体分子在液体中的溶解度差异,实现有害成分的分离和去除。
常用的物理吸收剂包括水、有机溶剂和碱液等。
物理吸收技术具有操作简单、装置结构简化等优点。
4. 化学吸收技术化学吸收技术是通过将废气通过特定的化学吸收剂,使有害成分通过化学反应与吸收剂发生反应,从而实现有害成分的去除。
常用的化学吸收剂包括氨水、碱液和酸液等。
化学吸收技术可以根据废气的成分进行选择,具有针对性强、去除效果好等优势。
5. 催化氧化技术催化氧化技术是利用催化剂催化氧化废气中的有害成分,使其转化为无害的物质。
常用的催化剂包括贵金属催化剂、金属氧化物催化剂和氧化钒催化剂等。
催化氧化技术具有高效转化率、催化反应瞬时等特点。
6. 吸附技术吸附技术是利用吸附剂对废气中的有害成分进行吸附、富集和分离的技术。
常用的吸附剂包括活性炭、分子筛和纳米材料等。
吸附技术具有选择性强、再生能力好等特点。
7. 膜分离技术膜分离技术是利用半透膜对废气中的有害成分进行选择性分离和去除的技术。
常用的膜材料包括聚合物膜、陶瓷膜和复合膜等。
炼猪油废气措施流程

炼猪油废气措施流程下载温馨提示:该文档是我店铺精心编制而成,希望大家下载以后,能够帮助大家解决实际的问题。
文档下载后可定制随意修改,请根据实际需要进行相应的调整和使用,谢谢!并且,本店铺为大家提供各种各样类型的实用资料,如教育随笔、日记赏析、句子摘抄、古诗大全、经典美文、话题作文、工作总结、词语解析、文案摘录、其他资料等等,如想了解不同资料格式和写法,敬请关注!Download tips: This document is carefully compiled by theeditor. I hope that after you download them,they can help yousolve practical problems. The document can be customized andmodified after downloading,please adjust and use it according toactual needs, thank you!In addition, our shop provides you with various types ofpractical materials,such as educational essays, diaryappreciation,sentence excerpts,ancient poems,classic articles,topic composition,work summary,word parsing,copy excerpts,other materials and so on,want to know different data formats andwriting methods,please pay attention!炼猪油废气措施流程一般包括以下几个步骤:1. 废气收集在炼油设备上方安装集气罩,将废气收集起来。
- 1、下载文档前请自行甄别文档内容的完整性,平台不提供额外的编辑、内容补充、找答案等附加服务。
- 2、"仅部分预览"的文档,不可在线预览部分如存在完整性等问题,可反馈申请退款(可完整预览的文档不适用该条件!)。
- 3、如文档侵犯您的权益,请联系客服反馈,我们会尽快为您处理(人工客服工作时间:9:00-18:30)。
1. 净化分离器;2. 气液分离器;3. 吸收塔;4. 换热器;5. 解吸塔; 6. 冷却塔;7. 空冷器;8. 酸性气体分离器
石油炼制中的废气处理-酸性气回收
乙醇胺吸收再生系统工艺流程
石油炼制中的废气处理-酸性气回收
乙醇胺法脱硫的主要操作参数及控制指标
• 乙醇胺浓度及酸气负荷
石油炼制中的废气处理-酸性气回收
焚烧炉(灼烧炉):将Claus装置尾气中的硫和硫化物转化为SO2 2H2S (g) +SO2 (g) ⇋ 3Sx(s)+2H2O (g) X=2,6,8
Claus尾气成分
H2S (%) 0.3-0.6 S (%) 0.01-0.02 CS2 (%) 0.02-0.33 COS (%) 0.02-0.33 H2 N2 H2O ( %) ( %) ( %) 0.5-4 约60 约30
直流法三级硫磺回收工艺
石油炼制中的废气处理-酸性气回收
克劳斯法工艺—常规分流法 ① H2S含量15~30%时,用直流法难以使反应炉内燃烧稳定 ② 1/3原料气 + 化学计量配给的空气进入反应炉内,使原料气中 H2S及烃类和硫醇燃烧 非常规分流法 ① 原料气H2S含量为30~55%(直流法难以使反应炉内火焰稳 定,常规分流法则炉温过高) ② 进入反应炉的原料气量提高至1/3以上
原油
石油化学工业
按生产行业分:石油炼制废气、石油化工废气 合成纤维废气、石油化肥废气
175℃到352℃,每25℃切割一个馏分
350℃到500℃,每25℃切割一个馏分
石油的组成
碳和氢(占97%-99%)、少量氧、硫、氮等
(1)碳氢化合物 烷烃(包括直链和支链烷烃)、环烷烃(多数是烷基环戊烷、烷 基环己烷)和芳香烃(多数是烷基苯),一般不含有烯烃 (2)含硫化合物 硫醇(RSH)、硫醚(RSR)、二硫化物(RSSR)、噻吩 (3)含氧化合物 主要为环烷酸和酚类(以苯酚为主),两者称为石油酸 少量脂肪酸 (4)含氮化合物 吡啶 吡咯 喹啉 胺类(RNH2)
延迟焦化工艺流程图
氧化沥青尾气
常减压装置的下脚渣油通入空气氧化生产沥青时产生的恶臭性气体
加热炉炉管清焦:空气-蒸汽烧焦 高压水力除焦产生废水
9
石油炼制中的污染物来源
火炬废气
• 开、停工及非正常操作(如放气减压)情况下,将可燃性气 体泄到火炬燃烧所产生的废气 • 火炬排污量比加热炉大
石油炼制中的废气
• 按排放方式分:有组织排放和无组织排放
氧化沥青尾气 催化再生废气 燃烧烟气 含H2S气体 臭气 废气名称
石油炼制中的废气
主要污染物 总烃 苯并(a)芘;氧、 氮和硫的杂环化合物 SO2、CO、CO2、尘 SO2、NOX、CO、 CO2、尘 H2S、氨 SO2、有机硫、氨、 硫醇、酚、有机胺 来源 油品储罐、污水处理隔油池、工 艺装置加热炉、装卸油、轻油和 烃类气体运输设施及管线、阀门 及泵等的泄漏 沥青生产装置 催化裂化装置 加热炉、锅炉、焚烧炉、火炬 各类炼厂气(加氢精制、加氢裂 化、延迟焦化等)、气体脱硫、 含硫尾气的回收处理 硫磺回收、污水处理、污泥处理
0.15-0.3
热焚烧:氧过量(20~100% )、480~815℃ 催化焚烧:尾气加热到316~427℃,与适量空气混合,进入催化剂床层 回收余热的焚烧炉通常采用强制通风,在正压下操作
石油炼制中的废气处理-Claus装置尾气
SCOT (Shell Claus Off-gas Treating)工艺 • 荷兰Shell 开发的硫磺回收尾气处理工艺 • 基本原理:采用钴-钼催化剂,将Claus尾气中硫化物加氢还原 为H2S,然后用醇胺溶液吸收和再生提浓,提浓H2S 返回到 Claus 段再次转化 • 效果:总硫低于250ppmv ,与上游的Claus 装置一起,总硫 回收率可达99.8%
• 火焰反应区形成S2 • 催化反应区形成S6和S8,T↓和P↑有 利于反应进行 • 确保过程气的温度高于硫露点
②催化反应段或催化转化段,即燃烧生成的SO2与酸气中其余 H2S在催化剂作用下反应生成元素硫,放出少量热量
总反应
石油炼制中的废气处理-酸性气回收
克劳斯法工艺流程简图
石油炼制中的废气处理-酸性气回收
克劳斯法工艺—直流法 ① 原料气中的H2S含量应大于50%,保证酸气与空气燃烧的 反应热足以维持反应炉内温度不低于980℃ ② 反应炉内H2S转化率一般可达60~70%
硫冷凝器:分离 硫和提高平衡转 化率 再热器:提高 反应速率,确 保过程气温度 高于硫露点, 但降低转化率 多级转化器: 提高总转化率
石油炼制中的废气处理-酸性气回收
克劳斯法(Claus)回收硫磺的原理
克劳斯反应:将H2S氧化转变成S的反应,分为两个阶段 ①热反应段或燃烧反应段,即将1/3体积的H2S燃烧生成SO2, 并放出大量热量,酸气中的烃类全部在此阶段燃烧
石油炼制中的废气处理-酸性气回收
克劳斯法(Claus)回收硫磺的原理
石油炼制中的废气处理-Claus装置尾气
Super-SCOT 工艺 进一步提高尾气净化度和节能降耗 • 荷兰Comprimo 公司改进SCOT工艺中的吸收-再生部分 • 二段再生塔:一段再生产生半贫液部分半贫液返回吸收塔中 部,另一部分半贫液进入二段再生塔进行深度气提,得到的超 贫液再送到吸收塔的顶部 • 降低超贫液的温度 • 效果:超贫液的低温和超低H2S 分压均有利于H2S在吸收塔内 醇胺溶液中的溶解,降低排入尾气中H2S 的浓度至10-50 ppmv;再生的蒸汽消耗量节省30%
石油炼制中的废气处理-酸性气回收
余热锅炉(又称废热锅炉) ① 回收热量以产生高压蒸汽(蒸汽压力通常为1.0~3.5MPa) ② 降低过程气温度,满足下游要求 转化器 ① H2S与SO2在催化剂床层上继续反应生成元素硫; ② COS和CS2等有机化合物水解为H2S与CO2
石油炼制中的废气处理-酸性气回收
有组织排放:指经常性的固定排放源,如:加热炉和锅炉燃烧废气、 催化再生烟气、氧化沥青尾气、硫磺回收尾气、焦化放空气、焚烧 炉烟气等 无组织排放:指间断性、较难控制、不经过排气筒的排放
① 烃类气体排放 — 装卸油操作、油品输送及储存过程中的挥发、设备管
固态废弃物:催化裂化、催化加氢 和催化重整等排出的废催化剂
第六章 石油炼制中的废气来源及处理
• 石油炼制中的污染物来源 • 石油炼制工业污染物排放标准 • 石油炼制中废气的治理
参考资料 • 国家环境保护局 《石油化学工业废气治理》 1996-03 • 石油炼制工业污染物排放标准(GB 31570—2015) • 石油化学工业污染物排放标准(GB 31571—2015)
道阀门泄漏、敞口储存的物料和废液的挥发,装卸催化剂粉尘污染等 ( “跑、冒、滴、漏” 现象) ② 恶臭气体排放 — 废水集输及污水处理场中硫化氢、有机硫、氨、有机 胺、有机酸等随挥发染源分:燃烧烟气、生产工艺废气、火炬废气和其他
燃烧烟气占废气排放总量的60%
— 石化加热炉多以减压渣油为燃料,含硫约0.2-3% — 废气中含有SO2、NOx和粉尘(粉尘量很少) — 经除尘后高空排放
两种分流法的问题:部分原料气直接进入催化反应段,当原料气 中含有重烃尤其是芳香烃时,会在催化剂上结焦,影响催化剂的 活性和寿命,同时影响硫磺颜色
石油炼制中的废气处理-酸性气回收
克劳斯法工艺—硫循环法(很少采用) H2S含量为5~10%时,将部分硫产品喷入反应炉燃烧 → 维持炉温 克劳斯法工艺—直接氧化法:原料气中H2S含量<5%时采用
处理含微量硫化氢的气体以及需要较高脱硫率的场合
• 湿法脱硫:用液体吸收剂洗涤气体。所用吸收剂包括碱 液和醇胺(一乙醇胺(MEA)和二乙醇胺(DEA))
• 炼厂气中常含有硫化氢和有机硫化物 气体脱硫
石油炼制中的废气处理-酸性气回收
醇胺法脱硫的原理
石油炼制中的废气处理-酸性气回收
20-40℃:反应向右进行,脱硫脱碳; >105℃:反应向左进行,硫化胺盐和碳酸盐分解逸出H2S和CO2, 醇胺重复利用
• Selectox 催化剂(SiO2-Al2O3):催化H2S氧化为S和SO2,但不催化 氧化烃类、氢和氨等 • 酸气中芳香烃含量小于 1000ml/m3,减少芳香烃在催化剂上裂解结炭
Selectox工艺的累计转化率(97%)高于Claus法平衡转化率
石油炼制中的废气处理-酸性气回收
克劳斯法主要设备及操作条件(以直流法为例)
石油炼制中的废气处理-酸性气回收
工艺 催化裂化 催化重整 延迟焦化 热裂化 加氢裂化 气体 大量丙稀、丁烯、 异丁烷 氢 甲烷,少量烯烃 丙烯、丁烯、少 量异丁烷 异丁烷 产物气体用途 烷基化 油品的加工精制 制氢 叠合 烷基化的补充原料
石油炼制中的废气处理-酸性气回收
炼厂气脱硫方法 • 干法脱硫:将气体通过固体吸附剂,使硫化氢和其他硫 化物吸附于其上,达到脱硫的目的
① H2S选择性催化氧化为元素硫,反应不可逆 ② H2S催化氧化为S及SO2,然后去Claus催化反应段(Selectox工艺)
Selectox工艺有一次通过法和循环法
• H2S含量<5%时可采用一次通过法 • H2S含量>5%时将过程气进行循环(控制过程气出口温度<371℃)
石油炼制中的废气处理-酸性气回收
急冷液:低温含硫氨水 吸收塔:醇胺
石油炼制中的废气处理-Claus装置尾气
LS-SCOT 工艺 ( Low Sulfur SCOT ) • 采用添加剂以改善再生,使贫液中H2S含量小于10×10-6 • 增加吸收塔和再生塔塔板数量 • 降低吸收塔溶剂和气体的温度至35℃左右(比SCOT工艺低 5℃) 增加冷却器的面积 • 投资费用比SCOT 工艺高15%,硫回收率从SCOT 工艺的 99.8%提高到99.95% 串级SCOT 工艺:荷兰STORK 公司开发 • 吸收塔底的富液送至上游吸收塔中部,提高富液的酸性气负荷 • 再生塔设计为共有装置 • 减少溶剂循环总量和蒸汽消耗量,操作灵活(上游吸收塔停工, 也可保证连续运行)