喷雾造粒方法
喷雾造粒浆料控制点

喷雾造粒浆料控制点喷雾造粒是一种常见的制粒方法,通过将液态或溶液状的物质喷雾成小液滴,然后在气流中干燥和凝固,最终形成颗粒状的固体物质。
这种方法广泛应用于制药、化工、食品、农业等领域,可以制备出具有特定形状、大小和性质的颗粒,以满足不同领域的需求。
喷雾造粒的关键之一是控制喷雾过程中的各个参数,以确保所得到的颗粒具有所需的特性。
其中一个重要的参数是喷雾液的流量和浓度。
喷雾液的流量决定了每单位时间内喷雾出的液滴数量,而浓度则决定了液滴中所含溶质的浓度。
通过调节这两个参数,可以控制颗粒的大小和均匀度。
另一个关键参数是喷雾液的粘度和表面张力。
粘度较高的喷雾液会形成较大的液滴,而粘度较低的喷雾液则会形成较小的液滴。
表面张力则影响液滴的形状,较高的表面张力会使液滴形成球状,而较低的表面张力则会使液滴形成扁平形状。
通过调节粘度和表面张力,可以控制颗粒的形状和流动性。
喷雾造粒中的干燥过程也是一个重要的环节。
在干燥过程中,喷雾液中的溶剂会逐渐蒸发,使颗粒逐渐凝固。
干燥的速度和温度是影响颗粒形成的关键因素。
较高的干燥速度可以得到较小的颗粒,而较低的干燥速度则可以得到较大的颗粒。
温度的选择要根据喷雾液的性质和所需颗粒的特性来确定。
在喷雾造粒过程中,还可以添加一些辅助剂来改变颗粒的性质。
例如,可以添加一些界面活性剂来增加喷雾液的流动性和润湿性,从而得到更均匀的液滴和颗粒。
还可以添加一些稳定剂来防止颗粒在干燥过程中的团聚和变形。
总的来说,喷雾造粒是一种重要的制粒方法,通过控制喷雾过程中的参数和干燥过程中的条件,可以得到具有所需形状、大小和性质的颗粒。
这种方法在制药、化工、食品、农业等领域有着广泛的应用前景。
未来随着技术的不断发展,喷雾造粒技术将会更加成熟和先进,为各个领域的发展带来更多的可能性。
《喷浆造粒工艺》课件
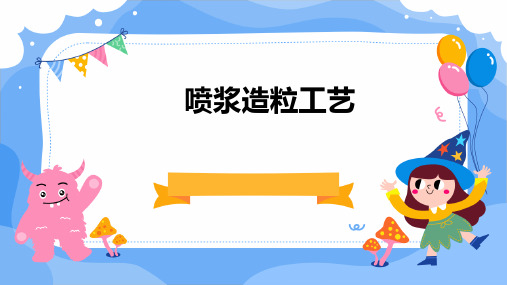
控制反应压力,保证工艺的顺利进行和产品的稳定性 。
时间控制
根据工艺要求,控制反应时间,确保反应完全和产品 的质量。
操作过程中的注意事项
安全操作
遵守安全操作规程,确保操作过程中的安全 。
防止污染
注意防止原料和产品的污染,保证产品的纯 度和质量。
监控设备
定期检查和维修设备,确保设备的正常运行 和工艺的稳定性。
盐业生产
喷浆造粒工艺可用于食盐、锌盐、钙 盐等盐类的生产,通过将不同组分混 合后进行喷浆造粒,得到所需规格的 盐类颗粒。
喷浆造粒工艺的流程
01
02
03
04
固体粉料输送
将所需造粒的固体粉料通过输 送设备送入流化床喷雾造粒机
的进料口。
喷雾造粒
在流化床内,固体粉料经喷雾 器喷出雾滴,雾滴在热气流的 作用下蒸发干燥,形成颗粒。
产品色泽不均
总结词
产品色泽不均会影响产品的外观和性能,也是喷浆造粒工艺中常见的问题之一。
详细描述
产品色泽不均的原因可能是由于原料的色泽差异、喷浆液的浓度不均、干燥温度波动等原因造成的。为了解决这 一问题,可以控制原料的色泽和质量、调整喷浆液的浓度、稳定干燥温度等措施。
产品强度不够
总结词
产品强度不够是喷浆造粒工艺中常见的问题之一,它会影响产品的抗压能力和使用寿命 。
VS
通过物理变化,可以将不同的原料混 合在一起,形成均匀的浆料,为后续 的造粒过程打下基础。此外,物理变 化还可以用于改变物料的粒径分布, 使其更符合产品的规格要求。
工艺参数对产品质量的影响
工艺参数是喷浆造粒工艺中的重要因素,它们对产品质量有着显著的影响。这些 工艺参数包括温度、压力、流量、浓度等,它们会影响到物料的化学反应和物理 变化过程。
喷雾造粒步骤

喷雾造粒步骤
喷雾造粒是一种常用的制粒技术,它将液体通过喷雾器雾化成小颗粒,并在空气中迅速固化成固体颗粒。
下面是喷雾造粒的步骤:
1. 准备工作:选取适合造粒的液体原料,如溶液、悬浮液或熔融液体。
确定好所需的颗粒特性和尺寸,选择合适的喷雾造粒设备。
2. 喷雾器雾化:将液体原料放入喷雾器中,使其通过喷雾嘴成为细小的液滴。
喷雾嘴的选择应根据液体的性质和所需颗粒的大小来确定。
3. 干燥过程:喷出的液滴进一步与空气接触,通过热空气、气流或真空等方式加速蒸发。
在干燥的过程中,液滴的溶剂或溶质会逐渐减少,固体颗粒的形成也随之发生。
4. 固化形成颗粒:在干燥过程中,溶剂或溶质浓度逐渐上升到达临界浓度,形成固体颗粒。
固化的方式可以是溶剂蒸发法、化学反应固化或熔融固化等。
5. 分离和收集:经过固化的颗粒会从气体中分离出来,收集到容器中。
可以通过过滤器、离心分离机或静电效应等方式进行分离和收集。
6. 特殊处理(可选):在收集后,可以进行进一步的处理,如表面修饰、干燥和筛分等,以满足特定的要求。
以上是一般的喷雾造粒步骤,具体的操作流程和设备选择会根据不同实验条件和目的而有所差异。
3喷雾造粒-操作流程

喷雾造粒操作流程
安全防护:必须佩戴口罩、防护眼镜、手套,身着低温防护服
1、组装喷嘴并安放至指定位置
2、用空气胶管连接喷嘴进气口和压缩空气出口,用匹配橡胶管连接喷嘴进浆口
3、匹配橡胶管经过蠕动输送器
4、搬运液氮罐至指定位置,连接液氮罐和喷雾造粒器
5、搬运料浆至指定位置(包括高度),安放料浆搅拌器
6、将匹配橡胶管插入料浆桶内
7、开启料浆搅拌器
8、开启雷达液位仪,确认参数
9、开启液氮自增压,往反应釜注入液氮,控制压力(流量)
10、待注入一半(25L)液氮后,开启喷雾造粒搅拌器
11、待完成液氮注入后,开启压缩空气
12、调节蠕动输送参数,开始蠕动输送泵
13、控制料浆压力
14、喷雾造粒开始
15、粉料托盘进
16、控制出料
17、粉料托盘出
18、粉料托盘进冰箱
重复15~18
19、料浆使用完
20、关闭料浆搅拌器
21、关闭雷达液位仪
22、关闭液氮罐进/排液阀
23、关闭蠕动输送泵
24、关闭压缩空气
25、关闭喷雾造粒搅拌器
26、造粒结束
27、粉料托盘进
28、控制出料
29、粉料托盘出
30、粉料托盘进冰箱
重复25~28
31、出料结束
32、拆除喷雾、匹配橡胶管、压缩空气管,放入清洗盆中
33、移除料浆储桶
34、移除液氮储桶
35、关闭所有电源
36、回收液氮(等待液氮完全蒸发)
37、喷雾造粒结束,准备冷冻干燥。
喷浆造粒复合配方表
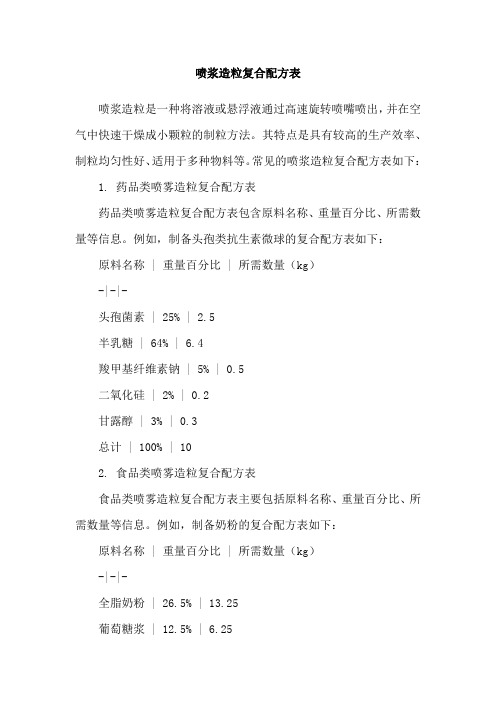
喷浆造粒复合配方表
喷浆造粒是一种将溶液或悬浮液通过高速旋转喷嘴喷出,并在空气中快速干燥成小颗粒的制粒方法。
其特点是具有较高的生产效率、制粒均匀性好、适用于多种物料等。
常见的喷浆造粒复合配方表如下: 1. 药品类喷雾造粒复合配方表
药品类喷雾造粒复合配方表包含原料名称、重量百分比、所需数量等信息。
例如,制备头孢类抗生素微球的复合配方表如下:原料名称 | 重量百分比 | 所需数量(kg)
-|-|-
头孢菌素 | 25% | 2.5
半乳糖 | 64% | 6.4
羧甲基纤维素钠 | 5% | 0.5
二氧化硅 | 2% | 0.2
甘露醇 | 3% | 0.3
总计 | 100% | 10
2. 食品类喷雾造粒复合配方表
食品类喷雾造粒复合配方表主要包括原料名称、重量百分比、所需数量等信息。
例如,制备奶粉的复合配方表如下:
原料名称 | 重量百分比 | 所需数量(kg)
-|-|-
全脂奶粉 | 26.5% | 13.25
葡萄糖浆 | 12.5% | 6.25
水 | 60% | 30
乳化剂 | 1% | 0.5
维生素、矿物质等 | 0.5% | 0.25
总计 | 100% | 50
3. 化工类喷雾造粒复合配方表
化工类喷雾造粒复合配方表包含原料名称、重量百分比、所需数量等信息。
氧化锌浆料喷雾造粒工艺研发方案

氧化锌浆料喷雾造粒工艺研发方案## Developing a Spray Granulation Process for Zinc Oxide Slurry.### Introduction.Zinc oxide is a versatile material with numerous applications, including in paints, cosmetics, and pharmaceuticals. Producing zinc oxide particles with specific size, shape, and properties is essential for meeting these diverse requirements. Spray granulation is a key process for tailoring zinc oxide particle characteristics. This paper presents a comprehensive development plan for a spray granulation process specifically designed for zinc oxide slurry.### Process Design.English:The spray granulation process for zinc oxide slurry involves the following key steps:1. Slurry Preparation: Zinc oxide powder is dispersed in a liquid medium to form a stable slurry.2. Spray Atomization: The slurry is atomized into fine droplets using a nozzle or rotary atomizer.3. Droplet Drying: The atomized droplets undergo evaporation of the liquid phase, resulting in the formation of solid zinc oxide particles.4. Particle Growth and Agglomeration: The solid particles collide and adhere to each other, leading to the formation of larger granules.5. Granule Collection: The granules are collected in a suitable device, such as a cyclone or bag filter.中文:氧化锌浆料喷雾造粒工艺涉及以下关键步骤:1. 浆料制备,将氧化锌粉末分散在液体介质中以形成稳定的浆料。
氧化铝喷雾造粒工艺
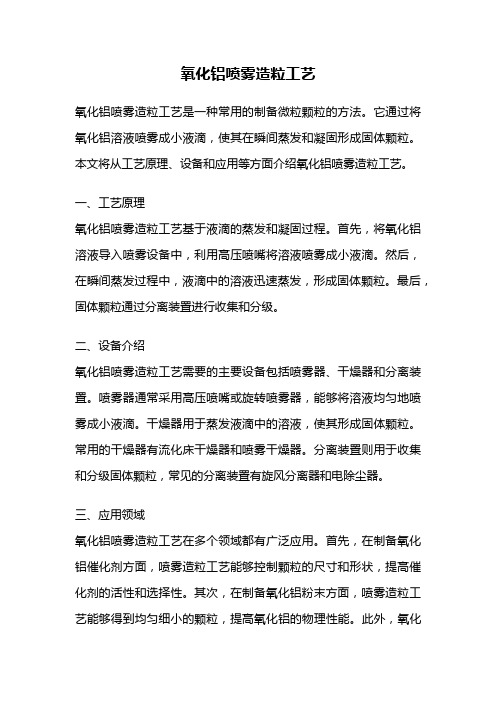
氧化铝喷雾造粒工艺氧化铝喷雾造粒工艺是一种常用的制备微粒颗粒的方法。
它通过将氧化铝溶液喷雾成小液滴,使其在瞬间蒸发和凝固形成固体颗粒。
本文将从工艺原理、设备和应用等方面介绍氧化铝喷雾造粒工艺。
一、工艺原理氧化铝喷雾造粒工艺基于液滴的蒸发和凝固过程。
首先,将氧化铝溶液导入喷雾设备中,利用高压喷嘴将溶液喷雾成小液滴。
然后,在瞬间蒸发过程中,液滴中的溶液迅速蒸发,形成固体颗粒。
最后,固体颗粒通过分离装置进行收集和分级。
二、设备介绍氧化铝喷雾造粒工艺需要的主要设备包括喷雾器、干燥器和分离装置。
喷雾器通常采用高压喷嘴或旋转喷雾器,能够将溶液均匀地喷雾成小液滴。
干燥器用于蒸发液滴中的溶液,使其形成固体颗粒。
常用的干燥器有流化床干燥器和喷雾干燥器。
分离装置则用于收集和分级固体颗粒,常见的分离装置有旋风分离器和电除尘器。
三、应用领域氧化铝喷雾造粒工艺在多个领域都有广泛应用。
首先,在制备氧化铝催化剂方面,喷雾造粒工艺能够控制颗粒的尺寸和形状,提高催化剂的活性和选择性。
其次,在制备氧化铝粉末方面,喷雾造粒工艺能够得到均匀细小的颗粒,提高氧化铝的物理性能。
此外,氧化铝喷雾造粒工艺还可应用于制备陶瓷颗粒、药物载体等领域。
四、优点与挑战氧化铝喷雾造粒工艺具有以下优点:首先,能够制备均匀的颗粒,颗粒尺寸可调控;其次,工艺简单,操作方便,适用于大规模生产;再次,能够得到高纯度的氧化铝颗粒。
然而,氧化铝喷雾造粒工艺也存在一些挑战,如溶液的粘度对喷雾效果有一定影响,溶液浓度和喷雾参数的选择需要经验积累。
氧化铝喷雾造粒工艺是一种常用的微粒制备方法。
通过控制喷雾和干燥过程,能够制备出具有一定尺寸和形状的固体颗粒。
该工艺在氧化铝催化剂和粉末制备等领域有广泛应用,并具有一定的优点和挑战。
随着技术的不断进步,氧化铝喷雾造粒工艺将进一步发展和应用。
喷雾造粒和喷雾干燥
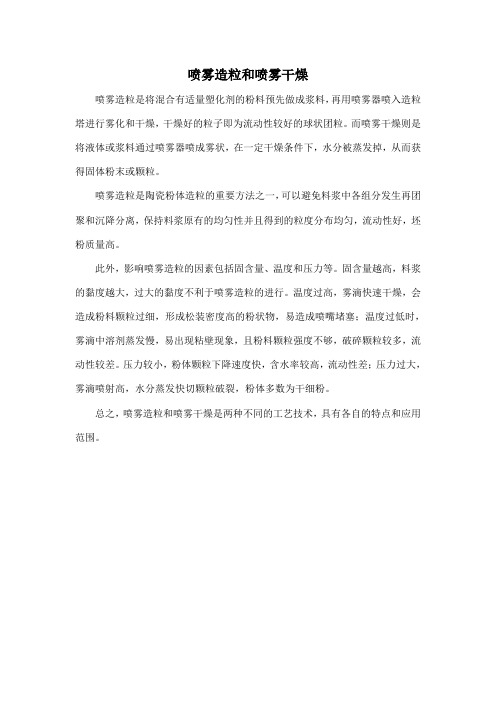
喷雾造粒和喷雾干燥
喷雾造粒是将混合有适量塑化剂的粉料预先做成浆料,再用喷雾器喷入造粒塔进行雾化和干燥,干燥好的粒子即为流动性较好的球状团粒。
而喷雾干燥则是将液体或浆料通过喷雾器喷成雾状,在一定干燥条件下,水分被蒸发掉,从而获得固体粉末或颗粒。
喷雾造粒是陶瓷粉体造粒的重要方法之一,可以避免料浆中各组分发生再团聚和沉降分离,保持料浆原有的均匀性并且得到的粒度分布均匀,流动性好,坯粉质量高。
此外,影响喷雾造粒的因素包括固含量、温度和压力等。
固含量越高,料浆的黏度越大,过大的黏度不利于喷雾造粒的进行。
温度过高,雾滴快速干燥,会造成粉料颗粒过细,形成松装密度高的粉状物,易造成喷嘴堵塞;温度过低时,雾滴中溶剂蒸发慢,易出现粘壁现象,且粉料颗粒强度不够,破碎颗粒较多,流动性较差。
压力较小,粉体颗粒下降速度快,含水率较高,流动性差;压力过大,雾滴喷射高,水分蒸发快切颗粒破裂,粉体多数为干细粉。
总之,喷雾造粒和喷雾干燥是两种不同的工艺技术,具有各自的特点和应用范围。
喷雾制粒方法

喷雾制粒口服固体制剂的生产工艺中,制粒步骤可以说是大多品种都会有一种工艺过程或步骤,将粉末转化为颗粒有许多好处,制粒为改善粉末的性质提供了极大的帮助,其中沸腾制粒是属于最常用的方法,对于对热不敏感的物料来说,沸腾制粒无疑是最佳选择,制成的颗粒可以是最终成型的中间体如颗粒剂、微丸等,也可能是片剂、硬胶囊剂的中间体,需借助制粒来改善颗粒的流动性和可压性,减小粉尘的产生,提高混合均一性,以便于填充、分剂量灌装成品和压片,药物经制粒后可制剂达至预期的速效或长效作用等。
沸腾制粒也称之为流化床制粒,是在流化床干燥工艺过程中加辅助黏合剂喷雾而成,流化床制粒将混合、制粒、干燥于一体,使用热空气自下而上通过松散的物料层形成沸腾床而进行干燥,并由此产生一个从空气到颗粒的有效热传递及液枋到气态的有效转化。
利用物料在流化床利用气流作用,使粉末产生流化状态而混合。
在流化过程中将黏合剂喷入,洒在粉末上,使粉体凝集,并采用热气流对物料进行气固二相的热量传递,将水分带走达到干燥过程。
流化床喷雾制粒通过把液体喷洒成液滴,再把小液滴形成更大的聚合物或者颗粒的过程,制粒过程大致可以看成是先对粉体物料进行一个润湿和成核。
形成小颗粒后有一个小颗粒的固定和生长的过程,然后再经过颗粒间的碰撞和磨擦过程,形成最终的颗粒。
在制粒过程中,将容易分离的黏合剂通过喷雾的形式形成液滴,由于表面的粉末状粒子的碰撞和联结形成液桥,粒子成核使得颗粒长大。
因而黏合剂在颗粒表面或者在粒子间形成架桥,这对于颗粒的生长和外形都有着很大的影响。
沸腾制料的优点就是集混合、制粒、干燥于一体,制粒结束后,对于混合均一性、颗粒水分含量均能满足要求,颗粒外观均匀,形状近似于球形,流动性较好,并且在参数固定,并易于利用仪器仪表在线监控和实时调节,对于温度、风量、压差均可实现在线监测和自动调节,特别是近年来应用了在线水分检测技术后,对于水分的监测更加准确。
并且整个制粒过程均在一个密闭负压的环境中完成,有效的防止了粉末的飞扬,对生产环境和人员影响较小。
喷雾造粒工艺流程

喷雾造粒工艺流程喷雾造粒工艺流程是一种广泛应用在化工、食品、制药等行业的先进制造技术。
它通过将液体原料雾化,然后与干燥介质接触,使其迅速蒸发并形成颗粒状固体产品。
本文将详细介绍喷雾造粒工艺的全过程。
一、前处理在开始喷雾造粒之前,首先需要对原料进行预处理。
这通常包括混合、溶解、过滤和脱气等步骤。
这些步骤的目的是确保原料的纯净度和均匀性,以保证最终产品的质量和稳定性。
二、雾化雾化是喷雾造粒过程的关键步骤。
它通常使用高压或高速旋转的方式,将液态原料分散成微小的液滴。
这种雾化的液滴具有很大的表面积,可以快速地与干燥介质接触并蒸发水分。
三、干燥雾化的液滴与热空气接触后,其中的水分会迅速蒸发,留下固体颗粒。
这个过程被称为干燥。
干燥的过程需要注意控制温度和时间,以防止过热导致的产品质量下降或燃烧。
四、冷却和收集干燥后的颗粒仍然很热,需要通过冷却设备将其冷却至室温。
冷却后的颗粒则通过旋风分离器和袋式过滤器进行收集。
这两个设备可以有效地分离出颗粒和气体,从而提高产品的纯度和回收率。
五、后处理收集到的颗粒还需要经过一系列的后处理步骤,如筛分、包装和储存等。
这些步骤是为了确保产品的质量和安全性,以及满足客户的需求。
总的来说,喷雾造粒工艺是一种高效、节能、环保的生产工艺,其优点主要体现在以下几个方面:1. 产品质量高:由于喷雾造粒过程中液滴的表面积大,干燥速度快,因此可以得到粒径均匀、结构紧密、流动性好的颗粒产品。
2. 生产效率高:喷雾造粒工艺可以实现连续生产,大大提高了生产效率。
3. 节能环保:喷雾造粒工艺的能耗低,产生的污染少,符合现代工业生产的环保要求。
4. 应用广泛:喷雾造粒工艺不仅可以用于化工、食品、制药等行业,还可以用于陶瓷、塑料、金属粉末等领域。
总结来说,喷雾造粒工艺是一种值得推广的先进制造技术。
随着科技的进步和市场需求的变化,喷雾造粒工艺将会得到更广泛的应用和发展。
喷浆造粒原理

喷浆造粒原理
喷浆造粒是一种利用空气对粉状物料进行造粒的方法。
其造
粒原理是:将一定量的水和一定的粉料混合成浆料,利用风机的
抽吸作用,通过喷枪将浆料喷入到料筒中。
在一定压力下,浆料
会被雾化,并喷出料筒外。
喷嘴将雾化后的浆料喷入到料筒的底部,由底部的卸料板将其卸出,经自然沉降后形成颗粒状物料。
该方法不需要用到任何机械设备,而且在不改变原料颗粒大小、
形状和密度的前提下,可以将粉状原料加工成不同规格的颗粒状
产品。
喷浆造粒技术是一种新兴的干法生产技术,主要适用于冶金、建材、化工、医药等工业生产过程中原料和产品的快速干燥和造粒。
它是一种新型的“绿色”干燥技术,是以空气为介质,将原
料通过风机以一定速度和方向吹入到料筒中,在物料被雾化后喷
入到料筒内。
经过充分雾化后,物料中的水分蒸发为水蒸气并被
带出料筒外,然后再经过自然沉降形成颗粒状物料。
该方法具有
产品纯度高、干燥速度快、颗粒形状好、收率高等优点。
—— 1 —1 —。
喷雾干燥法的造粒原理

喷雾干燥法的造粒原理喷雾干燥法是一种常用的颗粒化制备技术,适用于各种行业,如制药、食品、化工等。
它的原理是将化学溶液或悬浮液喷雾成微小液滴,并通过加热和气流干燥的方式将其转化为固体颗粒。
喷雾干燥法的原理可以概括为以下几个步骤:溶液或悬浮液的制备、喷雾成液滴、液滴在热气流中干燥、固体颗粒的收集。
首先,需要制备适合喷雾干燥的溶液或悬浮液。
这一步是非常重要的,因为溶液或悬浮液的物理性质将直接影响到后续的颗粒生成过程。
溶液或悬浮液通常由活性成分、溶剂和辅助剂组成。
活性成分是需要制备成颗粒的物质,溶剂用于将活性成分溶解或分散,辅助剂可以改善溶液的稳定性、流动性等性质。
接下来,将溶液或悬浮液通过喷雾装置喷出,形成微小的液滴。
喷雾装置的设计和操作对颗粒的质量和形态具有重要影响。
传统的喷雾装置包括压缩空气、气旋和压喷等方式。
近年来,也出现了一些新型的喷雾技术,如喷射冷冻干燥和旋转喷雾干燥等。
在液滴形成后,需要使其进行干燥。
一般情况下,会通过热风或气流的方式对液滴进行加热。
热风可以是通过加热设备产生的高温气体,也可以是通过其他方式产生的气流,如喷射冷冻空气等。
在加热的过程中,液滴中的水分会蒸发,溶质或悬浮物质会逐渐形成固体颗粒。
干燥阶段中有两个重要的过程:汽化和冷凝。
汽化是指液滴中水分的蒸发转化为气体,冷凝是指气体转化为固体颗粒。
在这个过程中,各种物理和化学因素会影响颗粒的形成。
例如,溶液中活性成分的溶解度、挥发性等性质,以及喷雾时的温度、湿度、气流速度等因素均会影响颗粒的形态和大小。
最后,固体颗粒会被收集起来,通常通过离心、过滤、筛分等方式进行。
在这个过程中,需要对颗粒进行处理以去除溶剂或辅助剂的残留物。
收集的颗粒可以用于制备药物、食品添加剂、催化剂等。
总之,喷雾干燥法的原理是通过将溶液或悬浮液喷雾成微小液滴,并通过加热和气流干燥的方式转化为固体颗粒。
这一技术的广泛应用及其原理的深入了解,对于提高颗粒制备的效率和质量具有重要意义。
喷雾造粒工艺流程

喷雾造粒工艺流程
喷雾造粒工艺是一种将液体原料通过喷嘴喷射形成微小液滴,然后在热风或其他干燥介质的作用下进行干燥、固化,最终形成颗粒状产品的过程。
这种工艺广泛应用于化工、食品、医药、农药等领域。
下面我们将详细介绍一下喷雾造粒工艺的流程。
1. 原料准备:首先,需要准备好所需的液体原料,这些原料可能是溶液、悬浮液或者乳浊液等。
根据不同的产品需求,可能还需要添加一些助剂,如稳定剂、粘合剂等。
2. 喷雾:将准备好的原料送入喷雾设备中,通过喷嘴将其雾化成微小的液滴。
喷嘴的设计和操作条件对雾化的效果有很大影响,因此需要根据实际需要进行选择和调整。
3. 干燥:雾化后的液滴在热风或者其他干燥介质的作用下迅速蒸发水分,形成固体微粒。
这个过程中需要注意控制干燥温度和时间,以保证产品质量。
4. 固化:部分物料在干燥后还需要进行固化处理,使其具有更好的物理和化学稳定性。
固化的方式有多种,如加热、冷却、化学反应等。
5. 分级:干燥和固化后的颗粒可能会有不同的大小,需要通过分级设备将它们分离出来。
分级的目的是为了得到均匀的产品,提高其使用性能。
6. 包装:最后,将分级后的颗粒进行包装,以便于储存和运输。
总的来说,喷雾造粒工艺是一种复杂而精细的过程,需要对每个环节进行精确的控制。
只有这样,才能生产出高质量的颗粒产品。
简析维药中的喷雾制粒技术

简析维药中的喷雾制粒技术维吾尔医药是祖国医药学不可分割的组成部分,也是新疆璀璨文化中绚烂的一章。
丰富的天然资源是维吾尔药材的主要来源,千年来经过不断增补完善,积累经验已逐渐形成了独具维吾尔特色的药物学。
喷雾制粒技术是将制粒和干燥一步完成,能够在数秒内完成水分的蒸发,使物料被干燥成粉状或颗粒,大大提高了工作效率。
而且喷雾制粒过程是密闭操作,符合GMP标准。
该技术应用已从乳制品、染料、化肥和脱水食品领域扩展到医药、陶瓷、冶金等工业生产中。
在维药的生产中更是被广泛应用,发挥着重要作用。
1 喷雾制粒干燥技术基本原理与工艺过程喷雾制粒机集混合、干燥、喷雾制粒功能于一体,能直接将液态物料一步制成颗粒,具有快速干燥颗粒、粉状物料等多种功能。
工作原理:物料受进风气流的推动在原料容器及扩展室内上下运动利用高速的热气流使粉料悬浮成流化态,液体通过安装在扩展室的气动喷嘴加入到系统中制粒,雾化的液体覆盖流化物料,使流化态的粉末凝结成多孔状的颗粒。
工作时,雾化器喷嘴将原料液分解成雾滴,并将其抛洒于温度为120℃~300℃的热气流,利用雾滴运动时与热气流的速度差,使物料在几秒至几十秒内迅速干燥。
干燥的原料液可以是溶液、乳浊液,也可以是熔融或膏糊液。
干燥的产品可以根据工艺要求制成粉状、颗粒状、团粒状甚至空球状。
利用液态物料作为制粒的润湿黏合剂,可节约大量的酒精,降低生产成本,并能生产出小剂量、无糖或低糖的中药颗粒。
2 喷雾干燥技术的优势及缺陷2.1 喷雾干燥技术的优势2.1.1 喷雾制粒技术可以将混合、制粒、干燥等操作一步完成,大大简化了其生产工艺,缩短了干燥时间,提高了药品的生产效率和产品质量。
2.1.2 喷雾制粒是将一部分制好软材颗粒放入机仓底部作为底粉,将混合好的浸膏或黏合剂由上部或下部喷入流化室内,使粉末聚结制成颗粒,然后进行干燥,药液是在不断的搅拌状态下喷成雾化分散体,瞬时完成干燥,制成的颗粒粒度均匀,流动性好,含水量低,可以直接进行压片填充胶囊。
微囊喷雾造粒机设备工艺原理
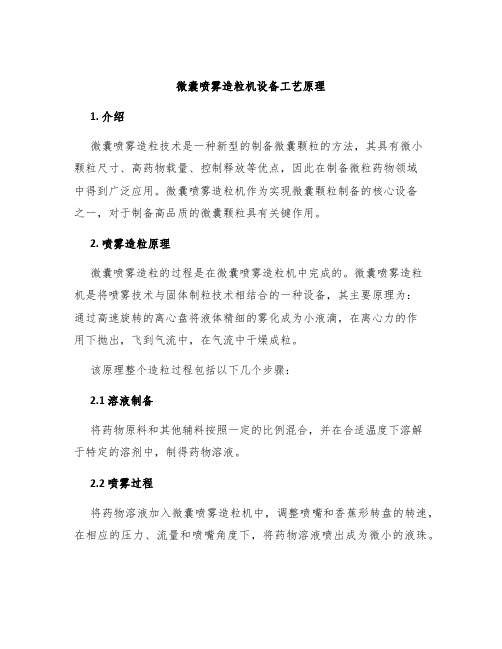
微囊喷雾造粒机设备工艺原理1. 介绍微囊喷雾造粒技术是一种新型的制备微囊颗粒的方法,其具有微小颗粒尺寸、高药物载量、控制释放等优点,因此在制备微粒药物领域中得到广泛应用。
微囊喷雾造粒机作为实现微囊颗粒制备的核心设备之一,对于制备高品质的微囊颗粒具有关键作用。
2. 喷雾造粒原理微囊喷雾造粒的过程是在微囊喷雾造粒机中完成的。
微囊喷雾造粒机是将喷雾技术与固体制粒技术相结合的一种设备,其主要原理为:通过高速旋转的离心盘将液体精细的雾化成为小液滴,在离心力的作用下抛出,飞到气流中,在气流中干燥成粒。
该原理整个造粒过程包括以下几个步骤:2.1 溶液制备将药物原料和其他辅料按照一定的比例混合,并在合适温度下溶解于特定的溶剂中,制得药物溶液。
2.2 喷雾过程将药物溶液加入微囊喷雾造粒机中,调整喷嘴和香蕉形转盘的转速,在相应的压力、流量和喷嘴角度下,将药物溶液喷出成为微小的液珠。
2.3 干燥过程在离心力和高速的气体流动的共同作用下,微小液珠穿过干燥室,很快失去水分,转化为固体颗粒。
2.4 分离过程由于固体颗粒与气体流动速度不同,因此可以通过风力将颗粒从气体中分离出来,得到高质量的微囊粒子。
3. 工艺优势与传统的微粒制备工艺相比,微囊喷雾造粒具有以下优势:3.1 颗粒尺寸小微囊喷雾造粒颗粒尺寸小,一般在1-10微米之间,这有助于提高药物在人体内的生物利用度,并可减少给药次数,从而大大提高药物的效果。
3.2 药物稳定性高微囊颗粒中药物分散均匀,可以保护药物免于环境的影响,从而提高药物的稳定性。
3.3 药物载量高微囊颗粒具有高的药物载量,可以在单位体积或单位质量内载入更多的药物,从而提高药物的效率,并减少用药次数。
3.4 药物释放可控微囊颗粒的药物释放可以控制,可根据需要选择适当的释放方式和调整释放速率,从而达到更好的治疗效果,有效减少副作用。
4. 应用领域微囊喷雾造粒技术广泛应用于制备控释微囊颗粒、口服固体分散剂、注射用药物微球等领域。
高比重喷雾造粒工艺
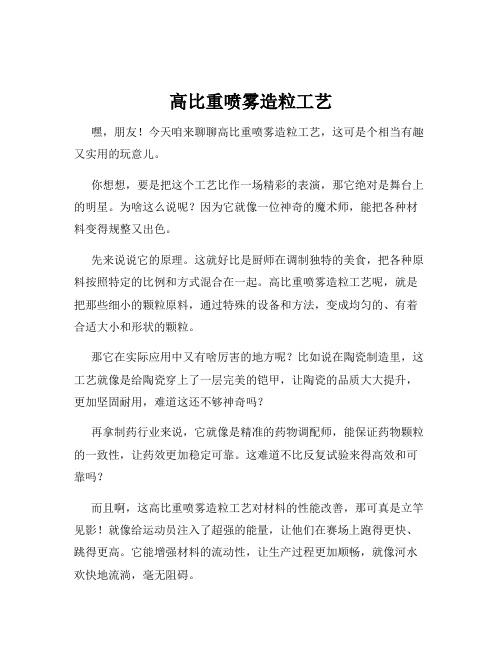
高比重喷雾造粒工艺嘿,朋友!今天咱来聊聊高比重喷雾造粒工艺,这可是个相当有趣又实用的玩意儿。
你想想,要是把这个工艺比作一场精彩的表演,那它绝对是舞台上的明星。
为啥这么说呢?因为它就像一位神奇的魔术师,能把各种材料变得规整又出色。
先来说说它的原理。
这就好比是厨师在调制独特的美食,把各种原料按照特定的比例和方式混合在一起。
高比重喷雾造粒工艺呢,就是把那些细小的颗粒原料,通过特殊的设备和方法,变成均匀的、有着合适大小和形状的颗粒。
那它在实际应用中又有啥厉害的地方呢?比如说在陶瓷制造里,这工艺就像是给陶瓷穿上了一层完美的铠甲,让陶瓷的品质大大提升,更加坚固耐用,难道这还不够神奇吗?再拿制药行业来说,它就像是精准的药物调配师,能保证药物颗粒的一致性,让药效更加稳定可靠。
这难道不比反复试验来得高效和可靠吗?而且啊,这高比重喷雾造粒工艺对材料的性能改善,那可真是立竿见影!就像给运动员注入了超强的能量,让他们在赛场上跑得更快、跳得更高。
它能增强材料的流动性,让生产过程更加顺畅,就像河水欢快地流淌,毫无阻碍。
还有还有,它对于控制颗粒的大小和分布,那也是相当厉害!这就好像是在给一群小朋友排整齐的队伍,大小个儿都安排得明明白白,一点儿也不乱。
这样一来,产品的质量和性能就能得到更好的保障啦。
不过,要想把这高比重喷雾造粒工艺玩儿得转,可也不是一件容易的事儿。
就像学骑自行车,得掌握好平衡和技巧。
得对设备有深入的了解,操作要精细,参数设置要准确。
稍微有一点马虎,可能就达不到理想的效果啦。
总之,高比重喷雾造粒工艺在众多领域都有着不可小觑的作用,只要我们用心去研究和运用,它就能为我们带来意想不到的惊喜和收获!。
喷雾造粒方法

河北工业大学硕士学位论文8)喷雾造粒将干燥室放入井式加热炉中加热,使干燥室保持一个较高的温度,来烘干溶液中多余的水分。
将第二步湿混后的溶液放入雾化枪中,将溶液进行雾化,在干燥室底部得到复合粉末。
当采用相同的喷雾速度时,不同的干燥室温度对复合粉末性能有着明显的影响。
温度太低,如250℃下,收集到的复合粉末颗粒饱满,粒径均匀,但热交换作用较慢,液滴的水分虽然较容易被烘干,其在干燥室里散发出来的水分不易排出,排风和喷雾过程不能同时进行,这样务必会耽误制粉过程,降低的制粉效率,如果操作不当,水分未及时排出,连续的雾化粉末进入干燥室,将会携带水分堆积在干燥室底层,形成结痴,只能破碎后进行筛分,严重影响了复合粉末的质量,进而影响复合涂层的质量;温度过高,导致液滴表面迅速脱水干燥,形成硬壳,但液滴内部仍含有水分,进一步脱水致使硬壳内部形成负压,导致复合粉体有外壳向内塌陷,形成类似苹果状的颗粒,这样的复合粉体表面粗糙,流动性不好,制备出的涂层性能不佳。
经过试验,干燥室温度设定为400℃时,干燥速度与排风速度相宜,既没有出现底层结痴,也没有大规模出现苹果状颗粒,粉末饱满,颗粒粒径差异不大,适合喷涂。
500克混合粉末制备成复合粉末只需1个小时,在保证质量的同时,大大提高了制粉效率。
图3一3,3一4为不同温度下制备出的复合粉末的SEM 扫描照片。
图3一3250℃制备出复合粉体形貌Fig.3一3SEMimageofcomPositePowders图Fig.3一4.3一4400℃复合粉体形貌SEMimageofcomPositePowders9)粉体的筛分制备出的颗粒,由于粘结剂的作用、料浆的沉淀效果、雾化枪雾化程度和干燥室内部环境限制使得制备得到的复合粉末的粒度不同,需要通过分样筛筛选,最终选定选取粒径在200一300目的颗粒进行等离子喷涂,该目数下的颗粒流动性和反应效率都很出色。
10)喷雾造粒法应注意的细节反应等离子喷涂Fe一A1203一FeA12O4复合涂层形成机理的研究将干混混合后的粉末加入在以无水乙醇溶剂中,因为原始铝粉活性大容易和水反应,故而不选水做溶剂。
- 1、下载文档前请自行甄别文档内容的完整性,平台不提供额外的编辑、内容补充、找答案等附加服务。
- 2、"仅部分预览"的文档,不可在线预览部分如存在完整性等问题,可反馈申请退款(可完整预览的文档不适用该条件!)。
- 3、如文档侵犯您的权益,请联系客服反馈,我们会尽快为您处理(人工客服工作时间:9:00-18:30)。
河北工业大学硕士学位论文8)喷雾造粒将干燥室放入井式加热炉中加热,使干燥室保持一个较高的温度,来烘干溶液中多余的水分。
将第二步湿混后的溶液放入雾化枪中,将溶液进行雾化,在干燥室底部得到复合粉末。
当采用相同的喷雾速度时,不同的干燥室温度对复合粉末性能有着明显的影响。
温度太低,如250℃下,收集到的复合粉末颗粒饱满,粒径均匀,但热交换作用较慢,液滴的水分虽然较容易被烘干,其在干燥室里散发出来的水分不易排出,排风和喷雾过程不能同时进行,这样务必会耽误制粉过程,降低的制粉效率,如果操作不当,水分未及时排出,连续的雾化粉末进入干燥室,将会携带水分堆积在干燥室底层,形成结痴,只能破碎后进行筛分,严重影响了复合粉末的质量,进而影响复合涂层的质量;温度过高,导致液滴表面迅速脱水干燥,形成硬壳,但液滴内部仍含有水分,进一步脱水致使硬壳内部形成负压,导致复合粉体有外壳向内塌陷,形成类似苹果状的颗粒,这样的复合粉体表面粗糙,流动性不好,制备出的涂层性能不佳。
经过试验,干燥室温度设定为400℃时,干燥速度与排风速度相宜,既没有出现底层结痴,也没有大规模出现苹果状颗粒,粉末饱满,颗粒粒径差异不大,适合喷涂。
500克混合粉末制备成复合粉末只需1个小时,在保证质量的同时,大大提高了制粉效率。
图3一3,3一4为不同温度下制备出的复合粉末的SEM 扫描照片。
图3一3250℃制备出复合粉体形貌Fig.3一3SEMimageofcomPositePowders图Fig.3一4.3一4400℃复合粉体形貌SEMimageofcomPositePowders9)粉体的筛分制备出的颗粒,由于粘结剂的作用、料浆的沉淀效果、雾化枪雾化程度和干燥室内部环境限制使得制备得到的复合粉末的粒度不同,需要通过分样筛筛选,最终选定选取粒径在200一300目的颗粒进行等离子喷涂,该目数下的颗粒流动性和反应效率都很出色。
10)喷雾造粒法应注意的细节反应等离子喷涂Fe一A1203一FeA12O4复合涂层形成机理的研究将干混混合后的粉末加入在以无水乙醇溶剂中,因为原始铝粉活性大容易和水反应,故而不选水做溶剂。
混合溶液通过机械搅拌的方法使其混合,为了更好的消除内部化学键,在溶液中加入陶瓷球,机械搅拌需要4一5小时,直至混合溶液中的无水乙醇挥发,使溶液变成粘稠状。
长时间的机械搅拌主要目的就是为了让两种粉末进行充分的均匀混合,避免最终得到的复合粉末由于成分分布不均,反应不充分,制备出性能不均的涂层。
4)风干将粘稠状的混合粉体倒入在托盘器皿中,使其风干,风干大约72小时可以使粘稠状变成固状。
当混合粉体中无明显乙醇气味时,可以放入烘干箱中加快残余乙醇挥发,但也应控制在较低温度下进行,本实验控制温度选择在60℃。
5)碾粉破碎风干后的粉为固状,需要将其碾碎成细粉。
此时,铝粉与氧化铁粉已经充分混合均匀,装到容器中保存起来,防止杂质污染。
该混合粉中铝粉和氧化铁粉虽以均匀分布,但仅仅是彼此的接触在一起,没有相互间作用力从而稳固的团聚在一起,仍不适宜喷涂。
6)粘结剂的制备破碎之后的混合粉末颗粒就是原始粉末颗粒的混合,粒径不会发生变化,但是以这样的粒径颗粒进行喷涂的话,容易被吹散,所以必须要提高混合粉末的结合强度,让其相互间粘合,加入适量的粘结剂以达到这个目的。
按混合粉末质量的4%称取粘结剂,然后将粘结剂放入盛有一定量水的烧杯中(水的质量大约为混合粉末的80%),在水浴炉中加热,使用玻璃棒搅拌粘结剂,直至烧杯中形成的液体变成透明状,粘结剂充分溶解,去除杂质并冷却后即可使用。
7)制备喷雾造粒料浆将破碎后的混合粉末放入盛有一定量水的烧杯中(水的质量大约为混合粉末的70%),加入过程需用玻璃棒搅拌,防止粉末结块。
再将冷却后的粘结剂的倒入到烧杯中,给混合粉末上胶,使混合粉末达到一定的机械团聚,增大其混合粉末的粒径,加强其在等离子焰流中的稳定性和反应活性。
将含有粘结剂的混合溶液进行机械搅拌,时间大约为40分钟。
这次湿混为第二次湿混,搅拌的时间不易过长,主要原因有以下两点:第一,经过了第一步湿混,混合粉体得到分布均匀,不再需要外加机械力破坏细粉的化学键。
第二,第二步湿混的溶剂从无水乙醇变成了水,混合粉末中的铝粉活性几乎没变。
在室温下,当铝粉遇到水后,将发生化学反应,生成气体,机械搅拌增加了铝粉与水接触的面积,加快了这一反应,影响粉的质量和制备工艺。
在这个溶液中由于添加了粘结剂,使溶液具备了一定的粘性,生成的气体不容易从溶液中排除,而是以小气泡的形式弥散分布在其中,无形中增加了溶液的体积,使单位溶液的固含量降低,降低了造粉效率。
减少第二步湿混的时间,来减少铝粉发生反应的时间,保证进行正常的喷雾造粒。
河北工业大学硕士学位论文和后,干燥使之形成颗粒状粉体,这种粉料具有较好的流动性与压延性,以便在喷涂工序中可以得到具有较好强度、不易分层脱落的涂层。
制备热喷涂粉末造粒所采用的喷雾造粒技术主要包括有喷雾干燥法、熔融喷雾冷却法、喷雾热分解法等。
本试验中采用喷雾干燥法造粒,其基本原理是把带有粘合剂的粉料液体,用喷雾器喷入干燥室中进行雾化(干燥室温度大约在300℃),干燥室中的雾滴被热气流干燥成颗粒状粉体,然后从干干燥室底部卸出,获得原始喷涂颗粒,经过筛选获得可以喷涂的复合粉体颗粒。
粉料液体可以制备成溶液、悬浮液或者是乳浊液。
颗粒形成机理为液体经雾化形成雾粒,干燥脱水后形成固体颗粒,颗粒在干燥室底部层层堆积形成,在粘结剂的作用下小颗粒聚集在一起形成流动性较好的团粒[49]。
喷雾干燥法主要特点:1、干燥速度快,料液经雾化后比表面积大大增加,在高温热风气流中,瞬间就可蒸发95一98%的水份,完成干燥的时间很短,最慢仅需十几秒,特别适用于热敏性物料的干燥。
2、所得产品为球状颗粒,粒度均匀、流动性好、溶解性好,产品质量好,纯度高。
3、使用范围广,根据物料的特性,可以用热风干燥,也可以用冷风造粒,对物料的适应性强。
4、操作简单稳定,控制方便,容易实现自动化作业,节省人力。
3.3.2喷雾造粒法具体步骤1)原始粉末选用比例本实验制备涂层的原理根据铝热反应:Fe20:+ZAI一ZFe+A1203+829KJ而来,其Fe20:与Al理论反应质量比为2.96:1,考虑到制备过程中材料损失,故选取的原始粉末质量比也为1:3。
2)复合粉体的干混将称重好的原始铁铝粉放在柑祸中,进行初混,搅拌大约10分钟,混合粉中无明显红色铁粉或灰色铝粉的聚集为止。
3)复合粉体的湿混由于微细粉末颗粒粒径较小,存在多种显微力,这些力经常使颗粒发生团聚现象,团聚又可以根据不同作用力分为:软团聚和硬团聚。
由于微细粉体常见团聚现象,故通过干混,并不能将两种粉体混合充分,需要进一步进行湿混。
微细粉体间的团聚可分为两种:软团聚和硬团聚。
软团聚是由粒子间的库仑力及范德华力所致,作用力较弱,所以可以通过一些化学物质的作用或施加机械能的方式,就可以使其大部分力消除,一般使用机械搅拌的方法克服;硬团聚一般指颗粒之间化学键力和氢键作用力等高强作用力连接而形成的团聚体,硬团聚形成的团聚体内部作用力大,颗粒间结合紧密,不易重新分散,粉体表现出的活性差,需要采用特殊的手段进行控制。
对氧化铁粉的粒径进行分析,硬团聚现象异常严重,所以采取湿混的方法来消除其化学键。
3.3喷雾造粒法制备FeZO3/A1复合粉体.3.1喷雾造粒法原理和特点造粒是指将原料粉末按照一定比例混合后制成溶液,并加入一定量的粘合剂,均匀调河北工业大学硕士学位论文3.4确定最终工艺图3一5为复合粉末的XRD检测结果。
,一薪敛橇矿落一A}剔态︸熟淞戒︺甲熟以凡吸︺游舞瓣瓣瓣炭︾﹃谷然冲蕊性`霸注娜︶者仍c佛一︸一仁瀚奎毋罐暴恋餐墨毋了毋荞委2攀浏扮鬓纂图3一5FeZO3/Al复合粉体的XRD衍射图Fig.3一5XRDPatternsoftheFeZO3/A1comPositePowders由XRD检测结果可以看出,采用喷雾造粒制备的复合粉末,仍为原始粉的结构,造粒过程没有生成新的产物,适于反应喷涂。
经大量试验确定了最终制备复合粉末的工艺为:混合粉末与水的质量比(固含量)为40%,添加的粘结剂含量为4%,干燥室的工作温度为400oC。
反应等离子喷涂Fe一A1203一FeA12O4复合涂层形成机理的研究当第二次湿混后进行喷雾工作时,由于铝粉和水反应生成的气泡占据了溶液大部分的空间。
在进行喷雾时,由于混合粉末料浆内部被大量空气占据,内外压力差不够,不容易将雾化枪中的溶液喷出,导致送料不畅,影响制粉效率。
同时由于喷出的物料中混有大量气体,导致雾化枪枪口得不到足够的液体冷却枪嘴,干燥室的高温迅速地将枪口残余的液浆固化,堵塞枪口,造成堵枪,给实验设备造成损坏,同时影响制粉效率。
所以应该尽量避免铝粉和水的反应成为了提高制备效率的关键,经过多次实验后发现,如果将第二次湿混的水温降低到10℃左右,铝粉和水的反应几乎不再发生,故而将第二次湿混所用水用冰水替换。
为了保证在搅拌过程中,由于外界温度太高,从而加热溶液致使反应,使用冰水浴冷却搅拌瓶,抑制生成气体。
在喷雾造粒过程中,待使用料浆也应放置在冰水中冷却,防止随着时间的推移生成气体,同时也要继续搅拌,防止料浆沉淀。
11)本试验采用的制备复合粉的工艺流程如图3一4所示。
Al粉FeZO:粉干混将Fe20:粉和Al粉以一定比例混合湿混要通过加一定分散剂的酒精进行湿混晾干将浆料平铺倒在盘子里风干碾粉破碎使粘在一起的细粉分开加粘结剂将熬好的粘结剂与粉混合制成料浆喷雾造粒筛选粉体。