铁合金现状和发展方向
2023年转炉铁合金行业市场发展现状

2023年转炉铁合金行业市场发展现状转炉铁合金是一种铁基合金,主要用于钢铁生产过程中的合金添加剂。
通过在转炉、电弧炉或任何其他高温炉中投入铁、铬、锰、钼等金属,可以制造出高强度、抗氧化和抗腐蚀的铁合金产品。
这些产品被广泛用于钢铁生产、建筑、制造和能源工业等各种领域。
目前,中国是转炉铁合金生产和消费的全球主要地区之一。
随着国内基础设施建设和钢铁生产的快速发展,转炉铁合金市场也在迅速扩大。
据国内市场调查表明,2019年中国转炉铁合金产量约为1200万吨,同比增长约5.3%,消费量约为1300万吨,同比增长约5.8%。
2020年疫情导致国际贸易及钢铁需求的疲软,但国内需求增长依然强劲,预计2020年中国转炉铁合金产量将达到1200万吨以上。
从产品类型来看,目前主要的转炉铁合金产品有硅铁、锰铁、铬铁等。
而随着科技进步和市场需求的变化,不断涌现出新的铁合金品种,例如硅锰铁、钨铁、钒铁等,均已经得到广泛应用和推广。
尤其是硅锰铁作为一种新的铁合金材料,广泛用于钢铁生产过程中取代普通的锰铁和硅铁,提高了钢薄壁厚材的抗拉强度和韧性,并提高了钢材的耐磨性和耐腐蚀性。
从市场分布来看,转炉铁合金产品通常被广泛用于钢铁生产中,主要用于生产高强度钢、耐蚀钢、合金钢、不锈钢等。
随着钢铁工业发展,转炉铁合金的应用范围也在不断扩大,例如在建筑、制造、铁路、航空航天等领域都可以发挥重要作用。
尤其是在冶金新材料、装备制造、新能源等领域,随着技术更新和新市场需求的不断涌现,转炉铁合金市场前景正被广泛认可和热火朝天的开拓中。
总的来说,在当前和未来一个时期内,转炉铁合金产业市场前景广阔。
面对新技术和新市场的挑战,生产企业应该借助技术创新和市场营销手段,掌握市场变化趋势,积极开拓国内和国际市场,为中国转炉铁合金产业打造更加辉煌的明天。
2023年特种铁合金行业市场前景分析

2023年特种铁合金行业市场前景分析特种铁合金是一类铁基合金,具有特殊的化学、物理性质和机械性能,应用广泛,主要用于钢铁冶炼、金属熔炼、电子工业等领域。
随着工业化和现代化的加速发展,特种铁合金行业市场前景越来越广阔。
一、行业发展概况特种铁合金行业产能增长迅猛。
2011年,中国特种铁合金产业产值已超过1600亿元,其中铬铁合金产值达到450亿元,占比28%;锰铁合金、硅铁合金、钒铁合金等产品产值均在200亿元以上。
据有关数据显示,我国特种铁合金产业拥有20多万人,企业规模基本上达到年销售收入5亿元的水平,是我国钢铁冶炼的重要材料。
二、市场前景分析1. 随着人口红利的结束,工业化趋势加速发展。
特种铁合金作为钢铁冶炼和金属熔炼的重要材料,将得到更多的市场需求。
2. 我国正在加强环保工作,对钢铁产业的监管日趋严格,要求钢铁企业加强资源节约和环境保护。
特种铁合金的使用可以实现节能减排和提高冶炼效率,为企业降低生产成本,达到环保标准提供了可靠的手段。
因此,特种铁合金行业前景可期。
3. 特种铁合金在高科技产业中的应用越来越广泛。
比如,电子工业需要使用高纯度的硅铁合金和锆铁合金;航空航天、军工等高端制造业也需要各种合金材料;另外,随着3D打印、新能源汽车等领域的快速发展,特种铁合金的需求也将随之增加。
4. 今年以来,钢铁市场需求持续走强,特别是国家去产能政策的持续推进,使得钢铁企业的利润水平得到明显提高。
这对于特种铁合金行业的发展来说,也是一个重要的机遇。
三、行业面临的问题1. 行业内部竞争加剧。
因为特种铁合金的应用范围广泛,很多企业看到了其巨大的市场前景,都进入了这一行业。
这就使得行业内企业竞争激烈,利润空间不断挤压。
2. 部分企业技术落后。
我国特种铁合金行业的开发和研究起步较晚,一些企业的技术水平较低,与国际先进水平相比差距较大。
这就限制了我国特种铁合金行业的整体实力和竞争力。
3. 生态环境问题。
因为特种铁合金产业属于一些重点污染企业,对于生态环境的破坏比较严重,同时钢铁企业的辐射环境也要求更高,因此生态环境治理压力很大。
2023年铁合金行业分析报告精选全文
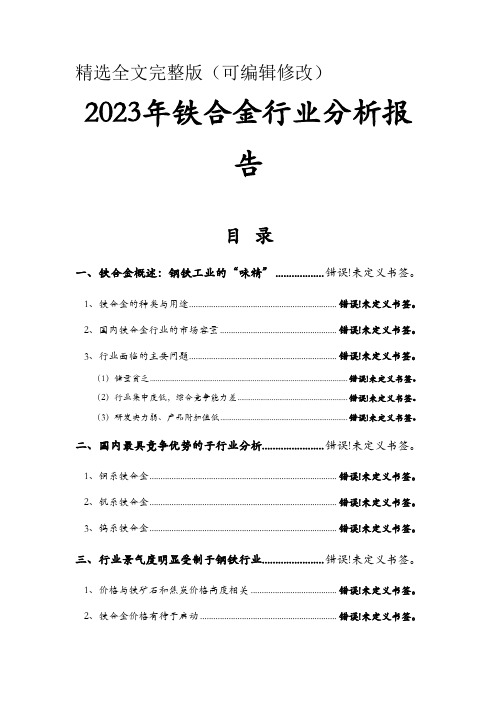
精选全文完整版(可编辑修改)2023年铁合金行业分析报告目录一、铁合金概述:钢铁工业的“味精” .................. 错误!未定义书签。
1、铁合金的种类与用途................................................................... 错误!未定义书签。
2、国内铁合金行业的市场容量 ..................................................... 错误!未定义书签。
3、行业面临的主要问题................................................................... 错误!未定义书签。
(1)储量贫乏........................................................................................................ 错误!未定义书签。
(2)行业集中度低,综合竞争能力差.......................................................... 错误!未定义书签。
(3)研发实力弱、产品附加值低 ................................................................... 错误!未定义书签。
二、国内最具竞争优势的子行业分析....................... 错误!未定义书签。
1、钼系铁合金..................................................................................... 错误!未定义书签。
2、钒系铁合金..................................................................................... 错误!未定义书签。
世界铁合金的发展现状及特点

世界铁合金的发展现状及特点铁合金行业的发展现状及特点可以从以下几个方面进行阐述:一、发展现状1. 技术进步:随着科技的不断进步,铁合金行业在技术研发和创新方面也取得了显著成果。
新的生产工艺、设备和材料不断涌现,提高了铁合金的生产效率和产品质量。
2. 市场需求:铁合金作为钢铁工业的重要原料,其市场需求受到钢铁产量的直接影响。
近年来,全球钢铁产量持续增长,带动了铁合金行业的发展。
同时,随着新能源、环保等领域的快速发展,对铁合金的需求也在不断增加。
3. 国际贸易:铁合金产品在国际市场上的贸易量逐年增加,中国、印度、巴西等新兴经济体成为铁合金的主要生产和出口国。
同时,国际铁合金市场竞争也日趋激烈,价格波动较大。
二、发展特点1. 品种多样化:铁合金产品种类繁多,包括硅铁、锰铁、铬铁、镍铁等,每种产品都有其特定的用途和市场。
这种多样化的产品特点使得铁合金行业能够满足不同领域的需求。
2. 资源依赖性:铁合金生产对原料资源的依赖性较强,如硅铁生产需要硅石、焦炭等资源,锰铁生产需要锰矿等。
因此,资源供应的稳定性和价格变动对铁合金行业的生产成本和市场竞争力具有重要影响。
3. 能源消耗大:铁合金生产过程中需要消耗大量的能源,如电力、煤炭等。
能源消耗的成本占据了铁合金生产成本的较大比例,因此能源价格的波动对铁合金行业的生产成本和市场竞争力也有较大影响。
4. 环保压力大:铁合金生产过程中会产生大量的废气、废水和固体废弃物,对环境造成一定的污染。
随着环保法规的日益严格和环保意识的提高,铁合金行业面临着越来越大的环保压力。
5. 产业集中度提高:随着市场竞争的加剧和产业政策的引导,铁合金行业的产业集中度逐渐提高。
大型企业通过兼并重组、技术改造等方式提高生产规模和市场竞争力,而小型企业则面临着生存和发展的压力。
总之,铁合金行业的发展现状和特点受到了技术进步、市场需求、国际贸易、资源供应、能源消耗、环保法规和产业政策等多种因素的影响。
铁合金行业行业痛点与解决措施

该企业注重技术研发和人才培养,不断加大研发投入,积极探索新的工艺技术和生产流 程;同时,该企业还加强与高校、科研机构的合作,共同开展技术研究和成果转化。通 过这些努力,该企业成功开发出了一系列具有自主知识产权的核心技术和产品,提高了
产品质量和附加值,赢得了市场的认可和客户的信任。
某铁合金企业成功应对国际贸易风险的案例
通过兼并重组、企业整合等方式,提高产 业集中度,形成规模效应。
加强技术创新与人才培养
技术创新
加大研发投入,推动铁合金生产技术的创新 和升级,提高产品质量和竞争力。
人才培养
加强人才培养和引进,建立完善的人才激励 机制,为铁合金行业的发展提供人才保障。
应对国际贸易风险与政策变化的策略
国际贸易风险防范
重要的战略资源
铁合金作为一种重要的战略资源,对国家的经济发展和国防建设具有重要意义 。
02
铁合金行业痛点分析
高能耗与高污染
总结词
铁合金行业是高能耗、高污染的行业,能源消耗和环境污染 问题突出。
详细描述
铁合金行业在生产过程中需要消耗大量的能源,如煤炭、电 力等,同时排放大量的废气、废水和固体废弃物,对环境造 成了严重污染。
03
解决措施与建议
节能减排与环保治理
节能减排
推广节能技术和设备,提高能源利用效率,减少能源消耗和排放。
环保治理
加强环保设施建设和运行管理,确保污染物达标排放,推动绿色生产。
优化产业结构与提高产业集中度
产业结构调整
优化产品结构,发展高附加值、高技术 含量的铁合金产品,淘汰落后产能。
VS
产业集中度提升
THANKS
谢谢您的观看
总结词
该企业通过加强内部管理、优化产品结构、拓展国际市 场等措施,有效应对了国际贸易风险,保持了企业的稳 定发展。
铁合金行业碳达峰碳中和目标与路径

铁合金行业碳达峰碳中和目标与路径随着全球气候变化的加剧,碳达峰碳中和成为了全球各国的共同目标。
铁合金行业作为重要的能源消耗行业,也需要积极响应国家的号召,制定碳达峰碳中和的目标和路径,为实现全球碳减排做出贡献。
一、铁合金行业的碳排放现状铁合金行业是指以铁为主要原料,加入其他金属或非金属元素,通过冶炼、熔炼等工艺制成的合金。
铁合金行业是我国重要的能源消耗行业之一,其生产过程中会产生大量的二氧化碳、氮氧化物等温室气体,对环境造成严重的污染和破坏。
据统计,我国铁合金行业的碳排放量占全国工业碳排放总量的10%左右,其中高炉炼铁和电炉炼钢的碳排放量占比较大。
铁合金行业的碳排放量不仅对环境造成了严重的影响,也对企业的可持续发展带来了巨大的挑战。
二、铁合金行业的碳达峰碳中和目标为了响应国家的碳达峰碳中和目标,铁合金行业需要制定相应的碳减排目标。
根据国家的要求,到2030年,我国工业碳排放总量要达到峰值,到2060年实现碳中和。
铁合金行业需要在这个时间节点前,制定出相应的碳减排目标,为实现全球碳减排做出贡献。
具体来说,铁合金行业的碳达峰碳中和目标应包括以下几个方面:1.减少能源消耗。
铁合金行业的生产过程中需要大量的能源,包括电力、燃气等。
企业可以通过提高能源利用率、采用新能源等方式,减少能源消耗,从而降低碳排放量。
2.优化生产工艺。
铁合金行业的生产过程中会产生大量的温室气体,企业可以通过优化生产工艺,减少温室气体的排放。
例如,采用高效的炉膛、减少燃料的使用等方式,可以有效地降低碳排放量。
3.推广低碳技术。
铁合金行业可以通过推广低碳技术,降低碳排放量。
例如,采用生物质能源、废弃物能源等低碳能源,可以有效地减少碳排放量。
4.加强碳排放监管。
铁合金行业需要加强碳排放监管,建立完善的碳排放管理体系,对企业的碳排放情况进行监测和评估,及时发现和解决问题,确保企业的碳排放量符合国家的要求。
三、铁合金行业的碳达峰碳中和路径为了实现碳达峰碳中和目标,铁合金行业需要制定相应的碳减排路径。
我国铁合金行业现状及发展趋势分析

2 0 0 6 午 2 0 0 7 年 2 0 0 8 年 2 0 0 9 年 2 0 1 0 年 2 01 1 年 2 0 1 2 年
金行业结构调整 目标还有一定距离。铁合金行业大力提 高产业集中度和劳动生产率, 促进产业结构优化升级将
本接近限定值和准人值要求, 但与先进值相比还有一
定差距。
4 . 锰铬矿对外依存度高, 威胁行业健康发展
除2 0优质锰矿和铬矿主要依赖进 1 5, 2 0 1 2 年, 我国 进1 5 锰矿 1 2 3 6 . 7 万吨, 同比减少 6 0 . 8 万吨, 降幅4 . 7 %, 锰 矿对外依存度超过 5 0 %。2 0 1 2 年, 我 国进 口铬矿 9 2 9 . 3 万吨, 同比减少 1 5 . 0 万吨, 降幅1 . 6 %, 铬矿对外依存度超 过9 5 %。铬矿和锰矿的对外依存度过高对铁合金行业健
6% 5%
4 %
五、 行业发展趋势
1 . 结构调整, 优化存量产能
随着 国务 院《 “ 十二五” 工业转型升级规划 ( 2 0 1 1 —
3% 2 % l % 0
2 0 1 5 年) 》 和《 “ 十二五” 节能减排综合性工作方案》 的发 布, 铁合金行业作为高耗能 、 高污染行业 , 进一步加强行 业准人管理、 淘汰落后 、 优化存量产能 已成为当务之急。 “ 十二五” 前两年 , 国家 已明令淘汰落后铁合金产能约
势在必行。
2 . 合作共赢, 提高市场竞争力
L= 丛佥全 型 二 塑丛i 型 f
图 4 我 国铁 合 金 行 业 和 钢铁 行 业 销 售 利 润 率
四、 行业主要特点和存在问题
国家 铁合金 产业 政策
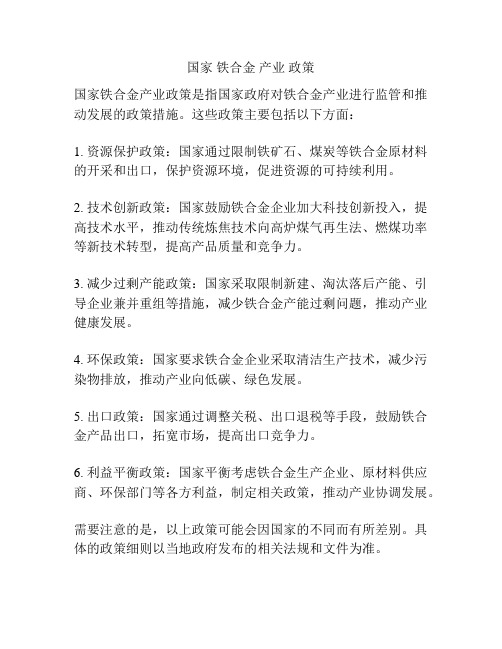
国家铁合金产业政策
国家铁合金产业政策是指国家政府对铁合金产业进行监管和推动发展的政策措施。
这些政策主要包括以下方面:
1. 资源保护政策:国家通过限制铁矿石、煤炭等铁合金原材料的开采和出口,保护资源环境,促进资源的可持续利用。
2. 技术创新政策:国家鼓励铁合金企业加大科技创新投入,提高技术水平,推动传统炼焦技术向高炉煤气再生法、燃煤功率等新技术转型,提高产品质量和竞争力。
3. 减少过剩产能政策:国家采取限制新建、淘汰落后产能、引导企业兼并重组等措施,减少铁合金产能过剩问题,推动产业健康发展。
4. 环保政策:国家要求铁合金企业采取清洁生产技术,减少污染物排放,推动产业向低碳、绿色发展。
5. 出口政策:国家通过调整关税、出口退税等手段,鼓励铁合金产品出口,拓宽市场,提高出口竞争力。
6. 利益平衡政策:国家平衡考虑铁合金生产企业、原材料供应商、环保部门等各方利益,制定相关政策,推动产业协调发展。
需要注意的是,以上政策可能会因国家的不同而有所差别。
具体的政策细则以当地政府发布的相关法规和文件为准。
2023年铁合金行业市场分析现状

2023年铁合金行业市场分析现状铁合金是钢铁产业的重要组成部分,广泛应用于建筑、交通、机械等领域。
本文将从铁合金行业的市场规模、产业链、主要产品和市场竞争等方面进行分析。
一、市场规模铁合金市场规模庞大,全球市场价值达到数百亿美元。
随着全球经济的发展,特别是新兴市场对基础设施建设的需求增加,铁合金市场呈现出稳定增长的趋势。
中国是全球最大的铁合金生产国和消费国,占据了全球市场的相当大的份额。
二、产业链铁合金行业的产业链主要包括原材料供应、生产加工、销售渠道和终端应用。
原材料供应主要包括铁矿石、煤炭和焦炭等;生产加工环节包括炼铁、炼钢和铁合金生产等;销售渠道主要通过批发商、经销商和终端用户等进行。
三、主要产品铁合金的主要产品包括硅铁、锰铁、铬铁、镍铁等。
其中,硅铁是最主要的铁合金产品,广泛用于钢铁冶炼、造船、航空等领域。
锰铁主要用于生产不锈钢和特种合金,镍铁主要用于生产不锈钢和电池等。
四、市场竞争铁合金行业竞争激烈,主要表现在以下几个方面:1. 价格竞争:铁合金产品市场价格波动较大,厂商往往通过降低价格来争夺市场份额。
2. 技术竞争:铁合金生产技术是行业竞争的核心,高端技术和工艺的应用将有助于企业提高产品质量和市场竞争力。
3. 品牌竞争:知名品牌在市场竞争中具有较大优势,消费者更倾向于购买具有知名品牌的产品。
4. 渠道竞争:拥有强大的销售渠道和分销网络将有助于企业拓展市场份额。
总之,铁合金行业市场规模巨大,发展潜力巨大。
但同时也面临着激烈的市场竞争和价格波动的压力。
企业应加强技术创新,提高产品质量,寻找差异化的市场定位和销售策略,以在市场竞争中取得优势。
国内铁合金业现状
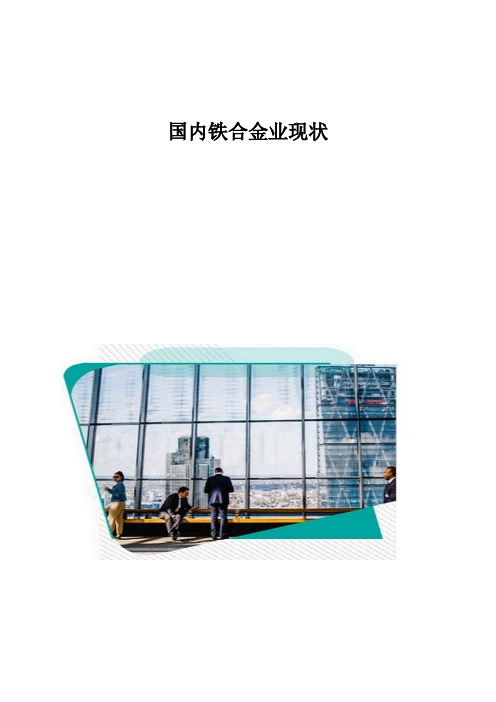
国内铁合金业现状提示:当前,我国铁合金行业形势严峻,产能增长过快,低水平重复建设状况严重,一些生产企业规模小、生产流程自动化程度极低、更谈不到符合国家环保方面的要求,严重污染了当地的自然环境,同时造成了我国资源的严重浪费,长此下去后果不堪设想。
为此,我国铁合金行业需要从以下几个方面解决铁合金行业存在的问题。
1.建议政府部门严格把好铁合金生产企业关,对于己经存在的生产企业要从严要求,不符合国家要求的企业要立即停产,根据目前原材料和能源都紧张的情况下,对规模小、能耗高、污染重的企业进行关闭,有利于保护我国的宝贵资源,保护我们的生存环境,同时能够缓解铁合金市场供大于求的局面。
2.重视铁合金行业生产过程中的环保问题,加大吸取国外环保先进经验的力度。
目前我国的铁合金行业生产企业数量多,但小企业占比例较大(50%以上),而这些小企业的环保问题一直是困扰我们的难题,建议政府痛下决心,对这些生产污染严重的企业进行停产整顿,使其生产过程完全符合国家的环保要求,以保护我国美好的自然环境,造福于人类。
3.加大整合铁合金行业生产企业力度,我国的铁合金企业发展仍然处于一个分散无序状态,这些企业自身的力量相当脆弱,行情好时蜂拥而上,一旦形势不好,就马上停产,经受不起市场行情的变化,在国际国内贸易过程中往往处于不平等地位,而要想得到一个合理的平等贸易,就必须联合起来,建立联盟,提高企业在国际国内市场的竞争实力,这就需要各个企业转变陈旧的观念,形成共识,在政府部门的支持和帮助下,形成强大的力量以赢得整个行业的利益。
对下半年铁合金市场的预测铁合金市场的变化是受钢铁工业发展程度和铁合金本身的供求关系这两大主要因素决定。
今年第一季度,钢铁工业发展迅猛,据国际钢铁协会(IISI)统计,一季度全球生产粗钢24699万吨,同比增长8.7%,中国2004年一季度粗钢产量达到了6096.8万吨,比2003年同期大约增长20%。
根据国家统计局(CSICC)数据,2004年一季度中国铁合金产量达到了153万吨,比2003年同期增长32.5%,此增长幅度远远高于钢产量的增幅。
金属材料行业现状和未来趋势
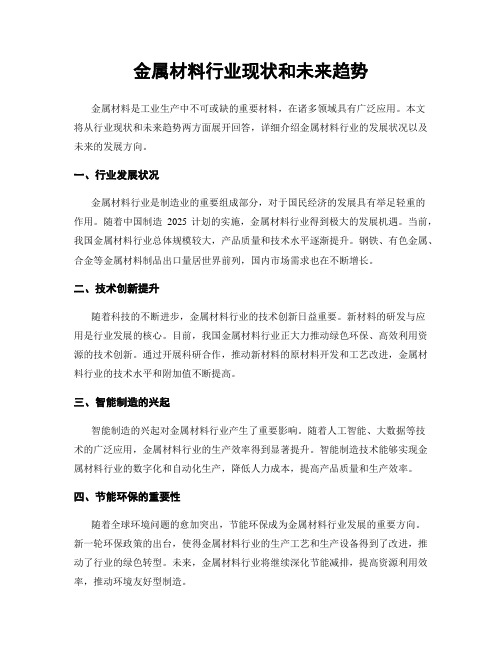
金属材料行业现状和未来趋势金属材料是工业生产中不可或缺的重要材料,在诸多领域具有广泛应用。
本文将从行业现状和未来趋势两方面展开回答,详细介绍金属材料行业的发展状况以及未来的发展方向。
一、行业发展状况金属材料行业是制造业的重要组成部分,对于国民经济的发展具有举足轻重的作用。
随着中国制造2025计划的实施,金属材料行业得到极大的发展机遇。
当前,我国金属材料行业总体规模较大,产品质量和技术水平逐渐提升。
钢铁、有色金属、合金等金属材料制品出口量居世界前列,国内市场需求也在不断增长。
二、技术创新提升随着科技的不断进步,金属材料行业的技术创新日益重要。
新材料的研发与应用是行业发展的核心。
目前,我国金属材料行业正大力推动绿色环保、高效利用资源的技术创新。
通过开展科研合作,推动新材料的原材料开发和工艺改进,金属材料行业的技术水平和附加值不断提高。
三、智能制造的兴起智能制造的兴起对金属材料行业产生了重要影响。
随着人工智能、大数据等技术的广泛应用,金属材料行业的生产效率得到显著提升。
智能制造技术能够实现金属材料行业的数字化和自动化生产,降低人力成本,提高产品质量和生产效率。
四、节能环保的重要性随着全球环境问题的愈加突出,节能环保成为金属材料行业发展的重要方向。
新一轮环保政策的出台,使得金属材料行业的生产工艺和生产设备得到了改进,推动了行业的绿色转型。
未来,金属材料行业将继续深化节能减排,提高资源利用效率,推动环境友好型制造。
五、智能化应用的扩展随着智能城市建设的不断深入和智能化设备的普及,金属材料行业将积极拥抱智能化应用,实现产品智能化。
通过物联网技术的运用,金属材料制品得以实现远程监测和控制,提高产品的可靠性和使用寿命。
六、产业链的转型升级金属材料行业的发展不仅涉及生产环节,还涉及包括原材料供应、制造、配套服务等在内的全产业链。
为适应市场需求和科技进步带来的变革,金属材料行业需要进行转型升级,形成更加高效的产业链。
2024年锰铁市场发展现状
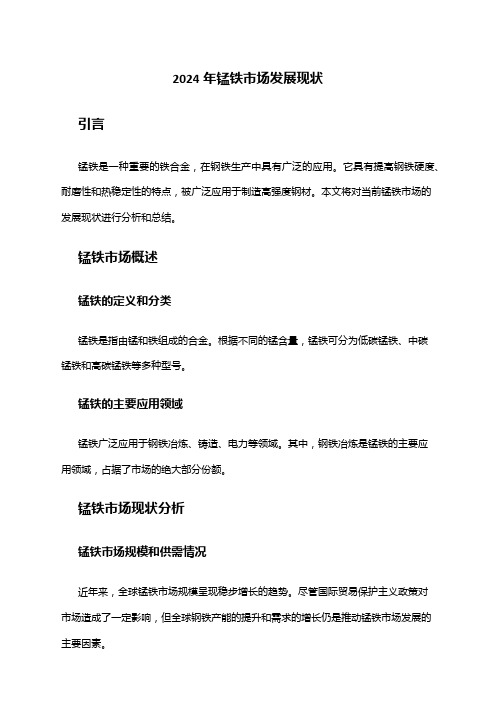
2024年锰铁市场发展现状引言锰铁是一种重要的铁合金,在钢铁生产中具有广泛的应用。
它具有提高钢铁硬度、耐磨性和热稳定性的特点,被广泛应用于制造高强度钢材。
本文将对当前锰铁市场的发展现状进行分析和总结。
锰铁市场概述锰铁的定义和分类锰铁是指由锰和铁组成的合金。
根据不同的锰含量,锰铁可分为低碳锰铁、中碳锰铁和高碳锰铁等多种型号。
锰铁的主要应用领域锰铁广泛应用于钢铁冶炼、铸造、电力等领域。
其中,钢铁冶炼是锰铁的主要应用领域,占据了市场的绝大部分份额。
锰铁市场现状分析锰铁市场规模和供需情况近年来,全球锰铁市场规模呈现稳步增长的趋势。
尽管国际贸易保护主义政策对市场造成了一定影响,但全球钢铁产能的提升和需求的增长仍是推动锰铁市场发展的主要因素。
锰铁市场价格波动由于供求关系的变化和国际原材料价格的波动,锰铁市场价格呈现较大的波动性。
其中,锰矿石价格的变动对锰铁市场价格影响较大。
锰铁市场竞争格局目前,全球锰铁市场竞争格局较为稳定。
主要的锰铁生产国家包括中国、南非、巴西等。
中国作为全球最大的锰铁生产和消费国,占据了市场的重要地位。
锰铁市场发展趋势技术创新驱动市场发展锰铁市场的发展离不开技术创新的推动。
当前,锰铁生产技术正在向高效、环保和节能方向发展。
新型锰铁生产技术的应用将进一步提高生产效率和产品质量。
绿色发展是必然趋势随着全球环境保护意识的提高,绿色发展已成为各行各业的共识。
锰铁行业也在积极推动绿色发展,通过减少能耗和污染物排放,实现可持续发展的目标。
锰铁市场国际合作增加国际合作是推动锰铁市场发展的重要力量。
不同国家之间的合作将加速资源共享、技术交流和市场开拓,促进全球锰铁市场的健康发展。
结论当前,全球锰铁市场呈现出稳步增长的态势。
技术创新、绿色发展和国际合作将是推动市场持续发展的重要动力。
随着全球钢铁需求的增长和产能的提升,锰铁市场有望迎来更广阔的发展空间。
2024年铁合金市场分析现状

铁合金市场分析现状引言铁合金是指以铁为主要组成元素并添加其他成分的合金,广泛应用于钢铁、铸造、不锈钢等行业。
铁合金市场作为钢铁行业的重要组成部分,对整个工业链的发展起着关键作用。
本文将分析当前铁合金市场的现状,并探讨未来的发展趋势。
1. 市场规模根据市场调研数据显示,铁合金市场在过去几年保持了稳定的增长态势。
目前,全球铁合金市场规模已经超过XX亿美元,并且预计在未来几年内将持续增长。
这主要受益于全球经济的复苏以及建筑、汽车和机械行业的增长。
2. 市场分布铁合金市场在全球范围内分布广泛。
目前,亚太地区是铁合金市场的主要消费地区,占据了全球市场份额的XX%。
同时,北美和欧洲地区也是重要的市场,分别占据了XX%和XX%的市场份额。
这主要受益于这些地区的工业化程度和钢铁行业的发展。
3. 市场趋势3.1 产品创新随着技术的进步和市场需求的变化,铁合金市场正经历着产品创新的浪潮。
一些新型铁合金材料的研发和应用正在不断推进,如高纯度铁合金、镍铁合金等。
这些新材料具有更好的性能和更广泛的应用领域,有望在未来取得更大的市场份额。
3.2 环保要求随着全球环保意识的增强,铁合金市场也面临着环保要求的压力。
许多国家和地区开始加强对铁合金生产过程中的排放和废弃物处理的监管。
这要求企业采取更环保的生产技术和措施,以满足环境保护的要求。
因此,具备清洁生产和可持续发展能力的企业将在市场竞争中占据优势。
3.3 供需状况铁合金市场的供需状况是影响市场价格和发展的关键因素。
目前,市场供应相对稳定,但需求量快速增长。
特别是钢铁行业的需求不断提高,推动了铁合金市场的发展。
未来,随着新兴市场的崛起和经济的增长,铁合金市场的需求仍然将保持较高的增长率。
4. 市场竞争目前,铁合金市场存在着激烈的竞争。
市场上有许多铁合金生产企业,其中一些是全球领先的企业。
这些企业通过不断提升产品质量、提供定制化解决方案和优质的客户服务来保持竞争优势。
另外,市场上还存在一些中小型企业,它们通常通过低价竞争来争夺市场份额。
2024年铁合金市场需求分析

2024年铁合金市场需求分析1. 引言市场需求分析是企业制定市场营销策略和产品发展计划的重要依据。
本文将对铁合金市场需求进行分析,通过了解市场规模、增长趋势、需求结构、竞争格局等方面的信息,为企业在该市场中的进一步发展提供参考。
2. 市场规模与增长趋势2.1 市场规模铁合金市场规模是衡量市场需求的重要指标之一。
据统计数据显示,过去几年铁合金市场呈现稳步增长的趋势。
根据相关机构数据,2018年全球铁合金市场规模达到XX亿美元。
2.2 增长趋势随着工业化和城市化进程的加快以及全球经济的持续发展,铁合金需求在全球范围内呈现增长趋势。
预计未来数年内,铁合金市场将继续保持稳定增长,具有较大的发展潜力。
3. 需求结构分析铁合金市场的需求结构具有多样性。
不同行业和领域对铁合金的需求存在差异,主要包括以下几个方面:3.1 钢铁工业钢铁工业是铁合金的主要消费领域之一。
铁合金作为一种重要的合金材料,广泛应用于钢铁冶炼过程中。
随着全球钢铁需求的增长,铁合金市场在钢铁工业中的需求也在不断增加。
3.2 能源行业能源行业对铁合金的需求主要体现在炼焦煤生产过程中。
炼焦煤是能源行业中重要的原材料,铁合金在其中发挥着辅助氧化剂的作用。
随着能源行业的快速发展,铁合金市场在该领域中的需求也在不断增长。
3.3 其他行业除了钢铁工业和能源行业,铁合金在其他行业中也具有一定的需求。
例如,汽车制造、建筑业、机械制造等领域均有铁合金的应用。
随着这些行业的快速发展,铁合金市场在这些领域中的需求也在逐渐增加。
4. 竞争格局分析铁合金市场的竞争格局主要由供应商数量、产品质量、价格等因素决定。
目前,全球范围内存在着多家缔造商。
这些供应商通过不断提高产品质量、降低成本、优化供应链等方式来提升自身竞争力。
在竞争激烈的铁合金市场中,产品质量和价格是企业获取竞争优势的关键因素。
通过持续进行研发创新,提高产品质量和性能,能够满足市场多样化的需求;同时,通过优化生产工艺、采用成本效益高的原材料,能够降低产品价格,提升市场竞争力。
铁合金生产
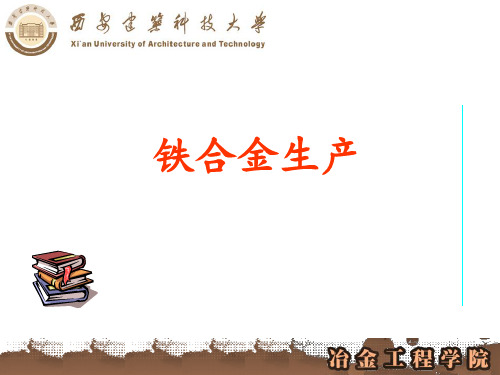
(二)铁合金工业发展经历的三个时期
3.铁合金工业走向现代化时期 1960年至今,电炉逐步取代高炉并占绝对优势。 1960年以后,电炉铁合金产量首次超过高炉铁合金产量,且 继续高速发展。 1995年世界钢产量约为7.7亿t,铁合金总产量约1600万t,其 中,电炉铁合金产量达80%以上。同时电炉设备技术加快了 大型化、全封闭化(半封闭)、机械化和过程控制等现代化 步伐,电炉炉气净化和余热回收利用达到实用阶段,出现了 无公害的铁合金厂;电子计算机控制生产过程得到应用和推 广。
1894年,穆瓦桑发明在电炉中还原氧化钒法; 1897年,戈德施米特发明铝热法后,钒被用于冶金工业; 1899年,美国在西弗吉尼亚州得霍尔库姆罗克厂的电炉中, 第一个炼制了含Si25%~50%的硅铁; 1900年,始于法国的高碳铬铁电热法生产转入工业规模生 产;这一年,法国还首先制得了钼铁; 1901年,罗西发明电铝热法还原富钛渣生产钛铁; 1905年,利姆提出用欠量的碳还原硼酸铁,以制取低碳锰 铁; 1907年,开始采用金属热法制铌; 1908年,用两步法生产含碳1%~2%的中碳锰铁; 1910年以后,还原电炉冶炼各种铁合金获得了迅速发展。
3、铁合金产品的分类
铁合金的品种繁多,分类方法也多,一般按下列方 法分类: (1)按铁合金中主要元素分类,有硅、锰、铬、钼、 钨、钛、钒等系列铁合金。 (2)按铁合金中含碳量分类,有高碳、中碳、低碳、 微碳、超微碳等品种。 (3)按生产方法分类,有高炉铁合金、电炉铁合金、 炉外法(金属热法)铁合金、真空固态还原法 铁合金、转炉铁合金、电解法铁合金等。
(3)改善铸造工艺和铸件性能
为了改变铸件凝固条件,往往在浇铸前加入某 些铁合金作为晶核,形成晶粒中心,使形成的 石墨变得细小分散,晶粒细化,从而提高铸件 的性能。 在铸铁工业中用作孕育剂和球化剂。
2024年生铁市场发展现状

2024年生铁市场发展现状引言生铁是铁矿石经过高温还原炉熔炼而成的初级铁材料,广泛应用于钢铁行业。
本文将探讨当前生铁市场的发展现状,包括市场规模、主要产地、需求情况、竞争格局等方面的内容。
市场规模生铁市场在全球范围内具有重要地位,其规模逐年扩大。
根据国际铁合金协会的数据,2019年全球生铁产量达到了10亿吨,较上年增长了3.5%。
而中国是全球最大的生铁生产国家,其生铁产量占全球总量的50%以上。
主要产地全球生铁市场的主要产地包括中国、印度、俄罗斯、巴西等国家。
中国作为最大的生铁生产国,其产量一直居于全球领先地位。
印度和俄罗斯也是重要的生铁生产国家,其产量稳步增长。
巴西则以大规模的铁矿石资源和先进的冶炼技术而闻名。
需求情况生铁作为钢铁行业的重要原材料,其需求主要受到钢铁工业发展的影响。
近年来,全球工业化进程加速,钢铁需求量逐年增长,从而推动了生铁市场的扩大。
特别是在中国这样的发展中国家,基础设施建设和房地产行业的发展大幅增加了对钢铁和生铁的需求。
同时,新兴产业和高端制造业的发展也对生铁市场带来了新的需求。
例如,新能源汽车产业和绿色建筑行业对高强度钢铁和高质量生铁的需求不断增加。
竞争格局由于巨大的市场规模和广泛的应用领域,生铁市场竞争激烈。
中国生铁行业内部竞争激烈,主要生产企业之间存在一定的价格竞争和品牌竞争。
同时,国际市场上,巴西和澳大利亚等铁矿石资源丰富的国家也在争夺市场份额。
此外,环保压力也对生铁市场竞争格局产生影响。
随着全球环保意识的提高和环境保护政策的推动,对于生铁生产过程中产生的废气、废水和固体废弃物的处理要求越来越严格。
环保要求成为生铁生产企业是否能够在市场竞争中立于不败之地的重要因素。
结论生铁市场在全球范围内具有广阔的发展前景。
当前,中国成为全球最大的生铁生产国家,全球需求继续增长。
然而,市场竞争激烈和环保要求的提高也给生铁生产企业带来了压力和挑战。
未来,随着新兴产业和高端制造业的不断兴起,生铁市场将面临更多机遇和挑战。
2024年钒铁市场发展现状

2024年钒铁市场发展现状引言钒铁是一种重要的铁合金,具有很高的钒含量。
它在钢铁生产中起着关键的作用,广泛应用于建筑、汽车制造、能源等领域。
本文将对钒铁市场的发展现状进行综述,并分析未来的发展趋势。
市场规模及产量分析近年来,全球钒铁市场规模不断扩大。
根据统计数据,2019年全球钒铁的市场规模达到XX亿美元,较2015年增长了XX%。
中国是全球最大的钒铁生产国,占据了全球市场的重要份额。
2019年,中国钒铁产量达到XX万吨,占全球总产量的XX%。
需求分析钢铁行业是钒铁的主要需求方,对钒铁的需求量占据了总需求的大部分。
随着全球经济的不断发展,特别是新兴工业国家的崛起,钢铁需求量不断增加,从而带动了钒铁市场的增长。
此外,随着环保意识的增强,钒铁在能源领域的需求也呈现出良好的增长势头。
进口和出口情况分析中国是全球最大的钒铁生产国,同时也是钒铁产品的主要出口国。
根据数据,2019年,中国钒铁的出口额达到XX亿美元,较上一年增长了XX%。
中国的钒铁主要出口到亚洲、欧洲和美洲等地。
然而,中国也在一定程度上依赖进口钒铁,特别是高品质的钒铁产品。
近年来,中国从南非、澳大利亚和巴西等国进口了大量的钒铁。
主要生产商分析目前,全球钒铁市场上有许多主要的生产商,包括中国的XX公司、美国的XX公司和南非的XX公司等。
这些公司在钒铁生产技术和产品质量上具有显著优势。
他们通过提高生产效率和技术创新,不断提升自身在市场中的竞争力。
市场竞争格局分析钒铁市场竞争激烈,市场上存在众多的钒铁生产商。
随着全球产能的快速扩张,市场供应过剩的情况逐渐显现。
此外,一些国家之间的贸易争端也对钒铁市场造成了一定程度的不确定性。
发展趋势展望未来,随着全球经济的不断发展,钒铁市场将继续保持稳定增长。
尽管面临着一些挑战,比如过剩产能和不确定的贸易环境,但稳定增长的需求和不断创新的技术将推动钒铁市场的发展。
此外,环保要求的提升也将促进钢铁行业对高品质钒铁产品的需求增长。
- 1、下载文档前请自行甄别文档内容的完整性,平台不提供额外的编辑、内容补充、找答案等附加服务。
- 2、"仅部分预览"的文档,不可在线预览部分如存在完整性等问题,可反馈申请退款(可完整预览的文档不适用该条件!)。
- 3、如文档侵犯您的权益,请联系客服反馈,我们会尽快为您处理(人工客服工作时间:9:00-18:30)。
铁合金生产技术现状和发展方向
我参与了16000KV A硅铝铁炉和30000KV A硅钙炉试生产和生产。
在这过程中经历许多挫折和失败,回过头细想对铁合金生产有些感触。
现对国内铁合金说说自己的看法:国内铁合金生产仍然处在刀耕火种的年代,虽然在设备上有大的进步,但是工艺上仍然具有很大差距。
就我个人认为在如下几个方面存在着问题(一,不注重基础研究。
二经济和技术不挂钩。
三电冶,电与冶炼不配套。
四思想意识落后)。
一.不注重基础研究。
国内铁合金的发展功利性及强,看见铁合金能挣钱,什么样的人都上铁合金,其目的就一个挣钱。
铁合金行业曾经流传一种说法:越先进的铁合金企业越不挣钱,越落后的企业越挣钱。
二.经济和技术不挂钩。
有很多企业生产指标相当好,可是却不挣钱,原因是他们不算成本帐。
这种事情在生产铬铁和锰铁会出现。
有很多私企老板不懂铁合金,请一个管工艺的进行冶炼。
该管工艺的生产出的铁合金电耗低,矿耗低,完成了生产指标可老板不挣钱。
原因是该产品主要成本在原料上,就铬矿而言,块矿和粉矿一吨价差为1000多元,生产一吨铁需要两吨多铁。
指标再好,就是吨铁少200度电也才100元。
三.电冶,电与冶炼不配套。
国内铁合金冶炼对于电而言只知道流压比。
大多数冶炼者只关心,多大的电炉,用多少电流,多高电压。
在各个报刊文献上写上硅锰冶炼的流压比是多少,碳铬冶炼
的流压比是多少。
实际上流压比是决定电弧功率的大小,是决定冶炼温度的。
受炉膛尺寸,极心圆大小,炉料电阻影响的。
铁合金冶炼中对于极心圆参数的设计,国内的书籍说难还原的合金品种极心圆应小点,因为这样才能保证较高的极心圆功率密度,这从冶炼,热还原是对的。
但是电学上,极心圆小了,电弧功率占有功的比例相应的也会减少,故极心圆功率密度不一定增加。
就以硅铝铁冶炼而言,焦作矿务局王封铁合金厂是硅铝铁冶炼专利获得者,前期使用的极心圆直径是电极的2.3倍,月产硅铝铁合金50吨左右,随后使用的极心圆直径改为是电极的2.5倍(硅铁的参数),产量增为90吨-----115吨(1800KV A矿热炉)。
30000KV A 硅钙电炉所使用的极心圆与国内的参数也是不一样的。
四.思想意识不正确。
我曾经听见一个搞了30多年铁合金工艺的人说:为了确保不出电极事故,工艺为电极让步。
电极焙烧应是工艺的一部分。
有人说搞铁合金的一个不服一个。
有人说亏碳剩碳我一看就知道,随便加几车还原剂或者减几车还原剂就行了。
他们把自己的这种能力作为自己的本事,大肆吹嘘,沾沾自喜。
实际上他们是把自己犯错的能力进行吹嘘。
这种能力在小炉上能用,在硅锰,碳铬(它们冶炼中有焦炭层)上能用外,在硅铝铁,工业硅,硅钙等对碳敏感的合金上,在大炉上是会犯错的。
大炉30000KV A的炉上,原料入炉到反应,中间需要经历8小时,随意的波动将影响几天的炉况。
大炉稳产便是高产。
形成原因:
⑴.国内铁合金教育都太片面,把一个铁合金工艺分成几部分。
铁
合金工艺包括电气参数(怎么用电),原料条件(怎么用碳)和操作条件(怎么结合碳和电)他们三者是相互牵连,相互制约的。
原料发生变化,电气参数也得变化,操作条件也得变化。
例如:还原剂活性降低了,电气参数发生变化增加炉内功率密度,操作上采用焖烧。
国内铁合金教育只讲反应原理,理论配碳。
理论和实际脱离。
⑵.国内生产分工不同。
国内搞工艺的大多数就是配一下料,并且
配的料还不十分到家,给生产者留下很宽的余地。
生产上有时一个班加一吨附加碳的情况都有存在。
⑶.思维意识不同。
有些生产者所说的诀窍,实际上就是生产上出
现问题后的补救措施,反而被当成必不可少的东西。
例如硅铝铁合金冶炼需要的煤必须有一定的粘结性(没有找到合适的还原剂,还原剂的活性不够,原料的还原速度和熔化速度不匹配,没办法想的)。
某些合金冶炼中的干烘炉(原料配比不合适导致炉底上涨,炉底上涨的处理方法成为生产必备条件,浪费能源成为必须的),
⑷.铁合金体系形成的弊端。
国内铁合金体系的形成主要是照搬前
苏联的东西过来,没有自己的研究体系。
国内的铁合金以前都是小炉起家的,小炉冶炼的思想意识已经根深蒂固了。
我承认铁合金冶炼是一种粗活,但对于大炉生产而言必须粗活细作。
1.铁合金冶炼是一个整体的事,各部门均是生产的参与者,也是生
产情况的晴雨表。
例如:水泵房循环水出水口的温度,除尘系统中烟气温度和烟气量均反映了冶炼中电气参数的使用情况和原料的配碳量(电气参数设计不当和料批中配碳量过多导致高温区上移,出水温度,烟气温度,烟气量均增加)。
化验室化验出的任何结果都将反映或影响生产。
2.大炉对于任何参数的改变,都将有一个响应时间。
电气参数改变,
响应时间最短为4小时,原料变化响应时间最短8小时。
要保证大炉的正常进行应从各方面搜集炉况信息。
就以判断配碳量来说就可以使用如下信息:原料消耗,合金成分,炉渣成分,渣铁比,电极消耗,电流,功率,功率因数等。
真正的大型铁合金的生产企业应具备如下控制系统:
1.烟气除尘智能控制系统(IPC系统)
2.配料系统自动化控制系统(PLC系统)
3. 矿热炉专家控制系统(YTDK-ⅴ系统)
4. 总成系统综合智能控制(DCS控制系统)
矿热炉的自动控制是可行的:
对于1.烟气除尘智能控制系统(IPC系统)2.配料系统自动化控制系统(PLC系统)已经运用在铁合金行业,没有什么问题。
就矿热炉控制这一块还是问题,国内有几家做过,到后来都舍弃没有用了,其原因是他们的控制点找的不对,控制参数不对:就矿热炉自动控制现在有两种控制(1)依据工艺提出的电流当电流大于工艺规定值时,
将电极提升使电流降低;而当电流小于工艺规定的设定值时,降低电极增加电流。
(2)根据冶炼的前,中,后期,不同的冶炼阶段给以不同的控制电流。
但上面两种自动控制都是有缺陷的,没有考虑炉料电阻的变化和外网电压的变化,当冶炼环境发生变化后自动控制就没法使用,也就是铁合金现在很少使用自动化的原因。
这在某些方面由于国内生产习惯影响(喜欢偏加料,原料的不稳定)也给自动控制带来了麻烦。
找着一个把原料条件和电气参数相结合的控制点自动控制就能完全实现(这个控制点很多,因为冶炼上任何一个变化都是原料和电气参数变化的结果)。
矿热炉自动控制的优越性:
1.解决人工控制的弊端
人工控制电极升降存在许多缺陷。
一难以保持三相功率平衡;二是人的情绪对操作及时性,准确性的影响。
但是最严重的是人工控制理论上的错误。
对于硅钙冶炼保持炉膛温度均衡,功率密度均衡是不利的。
在冶炼过程中冶炼有一个有个初期,中期,和后期的区别。
中后期由于炉内存有铁水,导电增强,电流增加,如提升电极炉底功率密度减弱,降低了炉底温度,合金钙上不去。
2有利于经济分析作出最佳经济运行参数
硅钙冶炼炉底温度过高,则合金过热,这样出铁时合金的烧损严重,过热的合金给出铁口和设备带来潜在危险,同时浪费能源。
下图是我在冶炼过程中作的分析:
上图是某三天用电图,其中系列1,系列2,系列3分别是A.B.C三相电极各小时的电流曲线,系列4是通过统计得出的适合冶炼所需的基本电流。
由图上可知我们使用的电流比基本电流大,即我们的热效
益比基本热效益高。
从此图看出我们降低产品单位电耗是可以的,可行的。
并指出了降低电耗的途径:降低热效益,提高电效益。
3.有利于作数据统计
要想使矿热炉达到经济运行指标,必须对很多参数进行统计,并作出数据分析,自动控制的使用,电脑的运用,使这成为可能。
并解决了人工费时费力的苦差。
我就以其中的1个参数为例:
以上是一个月内电极吨铁消耗和当班产量的关系图,由图可以查到当吨铁电极糊控制在70----100KG时当班产量较稳定大于12吨。
万勇
2010-9-1。