冲压模具课程设计报告范例
冲压模具课程设计--带凸缘无底筒形件

冲压模具设计课程设计学院:姓名:寒冰色手学号:专业:11机制目录1零件冲压工艺分析---------------------------------------------03 1.1 制件介绍---------------------------------------------------03 1.2 产品结构形状分析-------------------------------------------032.零件冲压工艺方案的确定--------------------------------------033冲模结构的确定-----------------------------------------------044.零件冲压工艺计算--------------------------------------------044.1零件毛坯尺寸计算-------------------------------------------044.2 排样------------------------------------------------------064.3 拉深工序的拉深次数和拉深系数的确定------------------------064.4 冲裁力、拉深力的计算--------------------------------------074.5 拉深间隙的计算--------------------------------------------094.6 拉深凸、凹模圆角半径的计算--------------------------------09 4.7 计算模具刃口尺寸------------------------------------------094.8 计算模具--------------------------------------------------105. 选用标准模架----------------------------------------------125.1 模架的类型------------------------------------------------125.2 模架的尺寸------------------------------------------------126. 选用辅助结构零件------------------------------------------136.1 导向零件的选用--------------------------------------------136.2 模柄的选用------------------------------------------------136.3 卸料装置--------------------------------------------------146.4 推件、顶件装置--------------------------------------------146.5 定位装置--------------------------------------------------147 参考文献--------------------------------------------------141零件冲压工艺分析1.1 制件介绍零件名称:心子隔套材料:08钢料厚:1.0mm批量:大批量1.2 产品结构形状分析由图1可知该零件为圆筒件经过翻遍处理,翻边处有过渡圆弧,且半径为R=2.5mm故非常适合用模具拉深或翻边进行处理,故要对毛坯进行计算。
冲压模具设计实验报告
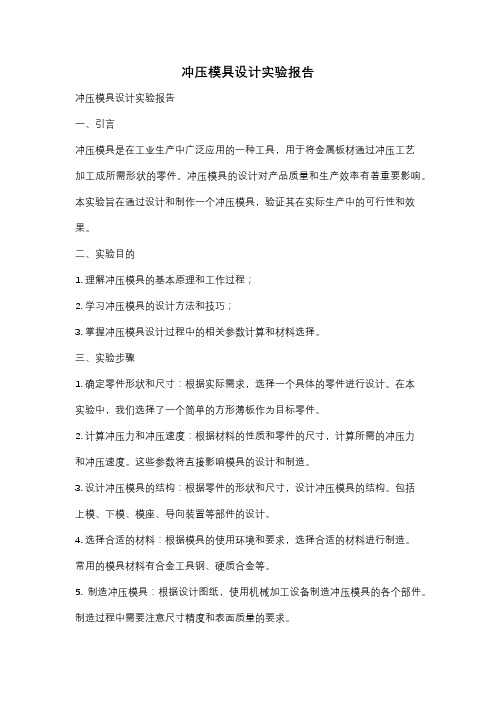
冲压模具设计实验报告冲压模具设计实验报告一、引言冲压模具是在工业生产中广泛应用的一种工具,用于将金属板材通过冲压工艺加工成所需形状的零件。
冲压模具的设计对产品质量和生产效率有着重要影响。
本实验旨在通过设计和制作一个冲压模具,验证其在实际生产中的可行性和效果。
二、实验目的1. 理解冲压模具的基本原理和工作过程;2. 学习冲压模具的设计方法和技巧;3. 掌握冲压模具设计过程中的相关参数计算和材料选择。
三、实验步骤1. 确定零件形状和尺寸:根据实际需求,选择一个具体的零件进行设计。
在本实验中,我们选择了一个简单的方形薄板作为目标零件。
2. 计算冲压力和冲压速度:根据材料的性质和零件的尺寸,计算所需的冲压力和冲压速度。
这些参数将直接影响模具的设计和制造。
3. 设计冲压模具的结构:根据零件的形状和尺寸,设计冲压模具的结构。
包括上模、下模、模座、导向装置等部件的设计。
4. 选择合适的材料:根据模具的使用环境和要求,选择合适的材料进行制造。
常用的模具材料有合金工具钢、硬质合金等。
5. 制造冲压模具:根据设计图纸,使用机械加工设备制造冲压模具的各个部件。
制造过程中需要注意尺寸精度和表面质量的要求。
6. 调试和测试:将制造好的冲压模具安装到冲床上,进行调试和测试。
检查模具的结构和功能是否符合设计要求,调整和修正可能存在的问题。
7. 总结和评价:根据实验结果,总结冲压模具设计和制造的经验教训,评价模具的性能和可行性。
四、实验结果经过实验,我们成功设计和制造了一个用于冲压方形薄板的模具。
在实际测试中,模具的结构稳定,冲压速度和力度符合设计要求。
所制造的零件尺寸精确,表面质量良好。
这表明我们的设计和制造过程是正确和有效的。
五、实验分析通过这个实验,我们深入了解了冲压模具的设计和制造过程。
在设计过程中,我们需要考虑材料的选择、零件形状和尺寸、冲压力和速度等因素。
这些因素相互关联,需要综合考虑,才能设计出高效和可靠的冲压模具。
冲压模具课程设计说明书(圆筒类)

冲压模具课程设计说明书学校:XXXXXX系别:XXXXXX专业:模具设计与制造学号:XXXXXXXXXX姓名:XX目录1、引言1.1零件设计任务1.2零件图2、冲裁件的工艺分析2.1工件材料2.2工件结构形状2.3工件的尺寸精度2.4确定工艺方案3、冲压模具总体设计3.1模具类型3.2操作与定位方式3.3卸料及出件方式4、冲压模具工艺及设计计算4.1排样设计及计算4.1.1零件展开尺寸计算4.1.2.各部分工作尺寸4.2设备选择5、总装图6、结论7、参考文献1、引言冲模在冲压中至关重要,没有符合要求的冲模,批量冲压生产就难以实现;没有先进的冲模,先进的冲压工艺也无法实现。
冲压工艺与模具,冲压设备与冲压材料构成冲压加工的三大要素,只有他们结合才能得出冲压件。
与机械加工及塑性加工的其他方法相比,冲压加工无论在技术方面还是经济方面都具有独特的优点,主要表现如下:(1)冲压加工的生产效率高,操作方便,易于实现机械化和自动化。
这是因为冲压是依靠冲模及冲压设备完成加工的,普通压力机的行程次数为每分钟几十次,高速压力要每分钟达数百次甚至上千次以上,而且每次冲压行程就可以得到一个冲压件。
(2)冲压时由于模具保证了冲压件的尺寸及形状精度,一般不破坏冲压件的表面质量,且模具寿命一般比较长,所以冲压的质量很稳定,互换性好,具有“一模一样”的特性。
(3)冲压可加工出尺寸范围较大、形状较复杂的零件,如小到钟表的秒表,大到汽车纵梁,覆盖件等,加上冲压时材料的冷变形硬化效应,冲压的强度和硬度都较高。
(4)冲压一般没有切削碎屑生成,材料的消耗较少,且不需要加热设备,所以是一种节省材料,节能的加工方法,冲压件的成本较低。
但是,冲压加工时模具一般具有专用性,又是一个复杂零件需要数套模具才能加工成形,且模具制造的精度高,技术要求高,是技术密集型产品。
所以,只有在冲压件生产批量较大的情况下,冲压加工的有点才能充分得到体现,从而获得较好的经济效益。
冲压模具课程设计优秀

落料冲孔复合模设计实例(一)零件工艺性分析工件为图1所示的落料冲孔件,材料为Q235钢,材料厚度2mm ,生产批量为大批量。
工艺性分析内容如下:1.材料分析Q235为普通碳素结构钢,具有较好的冲裁成形性能。
2. 结构分析零件结构简单对称,无尖角,对冲裁加工较为有利。
零件中部有一异形孔,孔的最小尺寸为6mm ,满足冲裁最小孔径min d ≥mm 20.1=t 的要求。
另外,经计算异形孔距零件外形之间的最小孔边距为5.5mm ,满足冲裁件最小孔边距min l ≥mm 35.1=t 的要求。
所以,该零件的结构满足冲裁的要求。
3. 精度分析:零件上有4个尺寸标注了公差要求,由公差表查得其公差要求都属IT13,所以普通冲裁可以达到零件的精度要求。
对于未注公差尺寸按IT14精度等级查补。
由以上分析可知,该零件可以用普通冲裁的加工方法制得。
(二)冲裁工艺方案的确定零件为一落料冲孔件,可提出的加工方案如下: 方案一:先落料,后冲孔。
采用两套单工序模生产。
方案二:落料—冲孔复合冲压,采用复合模生产。
方案三:冲孔—落料连续冲压,采用级进模生产。
方案一模具结构简单,但需两道工序、两副模具,生产效率低,零件精度较差,在生产批量较大的情况下不适用。
方案二只需一副模具,冲压件的形位精度和尺寸精度易保证,且生产效率高。
尽管模具结构较方案一复杂,但由于零件的几何形状较简单,模具制造并不困难。
方案三也只需一副模具,生产效率也很高,图1 工件图但与方案二比生产的零件精度稍差。
欲保证冲压件的形位精度,需在模具上设置导正销导正,模具制造、装配较复合模略复杂。
所以,比较三个方案欲采用方案二生产。
现对复合模中凸凹模壁厚进行校核,当材料厚度为2mm 时,可查得凸凹模最小壁厚为4.9mm ,现零件上的最小孔边距为5.5mm ,所以可以采用复合模生产,即采用方案二。
(三)零件工艺计算 1.刃口尺寸计算根据零件形状特点,刃口尺寸计算采用分开制造法。
《冲压模具课程设计》范例

【(一)范例】(1)题目:东风EQ-1090汽车储气简支架(2)原始数据数据如图7—1所示。
大批量生产,材料为Q215,t=3mm。
图7-1零件图(3)工艺分析此工件既有冲孔,又有落料两个工序。
材料为Q235、t=3mm的碳素钢,具有良好的冲压性能,适合冲裁,工件结构中等复杂,有一个直径φ44mm的圆孔,一个60mm×26mm、圆角半径为R6mm的长方形孔和两个直径13mm的椭圆孔。
此工件满足冲裁的加工要求,孔与孔、孔与工件边缘之间的最小壁厚大于8mm。
工件的尺寸落料按ITll级,冲孔按IT10级计算。
尺寸精度一般,普通冲裁完全能满足要求。
(4)冲裁工艺方案的确定①方案种类该工件包括落料、冲孑L两个基本工序,可有以下三种工艺方案。
方案一:先冲孔,后落料。
采用单工序模生产。
方案二:冲孔一落料级进冲压。
采用级进模生产。
方案三:采用落料一冲孔同时进行的复合模生产。
②方案的比较各方案的特点及比较如下。
方案一:模具结构简单,制造方便,但需要两道工序,两副模具,成本相对较高,生产效率低,且更重要的是在第一道工序完成后,进入第二道工序必然会增大误差,使工件精度、质量大打折扣,达不到所需的要求,难以满足生产需要。
故而不选此方案。
方案二:级进模是一种多工位、效率高的加工方法。
但级进模轮廓尺寸较大,制造复杂,成本较高,一般适用于大批量、小型冲压件。
而本工件尺寸轮廓较大,采用此方案,势必会增大模具尺寸,使加工难度提高,因而也排除此方案。
方案三:只需要一套模具,工件的精度及生产效率要求都能满足,模具轮廓尺寸较小、模具的制造成本不高。
故本方案用先冲孔后落料的方法。
③方案的确定综上所述,本套模具采用冲孔一落料复合模。
(5)模具结构形式的确定复合模有两种结构形式,正装式复合模和倒装式复合模。
分析该工件成形后脱模方便性,正装式复合模成形后工件留在下模,需向上推出工件,取件不方便。
倒装式复合模成形后工件留在上模,只需在上模装一副推件装置,故采用倒装式复合模。
冲压模具毕业设计范文

冲压模具设计实例:选择合适的冲 压模具设计实例
模拟结果:观察模拟结果,分析模 具工作过程
添加标题
添加标题
添加标题
添加标题
模拟过程:使用计算机辅助设计软 件进行模拟
优化设计:根据模拟结果对冲压模 具设计进行优化
冲压模具设计优化
优化目标:提高模 具寿命、降低成本、 提高生产效率
材料类型: 钢、铝、 铜、塑料 等
材料性能: 强度、硬 度、耐磨 性、耐腐 蚀性等
材料成本: 经济性、 可回收性 等
模具寿命: 耐用性、 维护成本 等
加工工艺: 铸造、锻 造、热处 理等
环保要求: 无毒、无 污染等
模具尺寸:根据冲压件的尺 寸和精度要求确定模具尺寸
模具材料:选择合适的模具 材料,如钢、铝、铜等
冲压模具毕业设计范 文
汇报人:
目录
冲压模具设计概述
冲压模具设计基础
冲压模具设计实例
冲压模具设计优化
冲压模具设计规范 与标准
冲压模具设计展望
冲压模具设计概述
冲压模具:用于将金属板材或非金属板材通过压力加工成所需形状的模具 定义:冲压模具是一种特殊的成型工具,用于将金属板材或非金属板材通过压力加工成所需形状 作用:冲压模具可以大大提高生产效率,降低生产成本,提高产品质量 应用领域:广泛应用于汽车、家电、电子、机械、航空航天等领域
模具类型:根据冲压工艺选 择合适的模具类型
模具精度:根据冲压件的精 度要求确定模具精度
模具寿命:根据冲压件的生产 数量和生产周期确定模具寿命
模具维护:定期对模具进行维 护和保养,保证模具的正常使
用
冲压模具设计实例
零件名称: 冲压模具
冲压模具设计实验报告

冲压工艺与模具设计实验报告分院:机电与能源工程学院专业班级:机械设计制造及其自动化104班*名:***学号: **********指导老师:**日期: 2013 年 12 月1.零件的工艺性分析(1)结构工艺性该零件结构简单,形状对称,无悬臂,孔径、孔边距均大于 1.5倍料厚,可以直接冲出,因此比较适合冲裁。
(2)精度由表3-11和表3-12可知,该零件的尺寸精度均不超过ST4等级,因此可以通过普通冲裁方式保证零件的精度要求。
(3)原材料08钢是常用冲压材料,具有良好的塑性,适合冲裁加工。
综上所述,该零件具有良好的冲裁工艺性,适合冲裁加工。
图12.工艺方案确定该零件需要落料和冲孔两道工序完成,可采用的方案有三种:方案一:单工序冲裁,先落料再冲孔。
方案二:复合冲裁,落料冲孔同时完成。
方案三:级进冲裁,先冲孔再落料。
由于是大批量生产,因此方案一不满足生产效率的要求,方案二和方案三都具有较高的生产效率,虽然方案三比方案二操作方便,但方案二能得到较高的精度和较好的平面度,且由于被冲板料较薄并不允许产生翘曲,特别是外孔和内孔的同轴度要求,因此选择方案二,即采用复合冲压。
3.模具总体设计(1)模具类型的选择对于复合模,由于倒装复合模操作方便安全,实际生产中优先考虑倒装结构。
所以选用倒装复合模。
(2)模具零件结构形式确定1)送料及定位方式条料由于是沿着一定的方向“推进”模具的,因此它的定位必须是两个方向的:○1在与送料方向垂直方向(即左右方向)上定位,以保证条料沿正确的方向送进,称为导料,常用的有导料板、导料销;○2在送料前方定位,以控制条料每次送进模具的距离(即步距),称为挡板,常用的有挡料销、侧刃等。
这里采用手工送料,导料销导料,挡料销挡料。
2)卸料与出件方式卸料零件的作用是卸下箍在凸模或凸凹模外面的制件或废料,根据卸料力的来源不同,分为刚性卸料装置和弹性卸料装置两种。
拉深件切边时需要采用废料切断力卸料。
模具冲压实训课程设计

模具实训课程设计班级:模具1217姓名:小贺冲件名称:缺角片零件图:如下图所示:生产批量:中批量材料:10钢料厚:2mm1.冲压件工艺性分析此工件只有落料和冲孔两个工序。
材料为10钢,具有良好的冲压性能,适合冲裁。
工件结构相对简单,有一个8mm的孔,孔与边缘的距离也满足要求,工件尺寸可看作IT14级,尺寸精度较低,普通冲裁完全能满足要求。
2.冲压工艺方案的确定该工件包括冲孔和落料两个基本工序,可有以下三种工艺方案:方案一:先落料,后冲孔。
采用单工序模生产方案二:落料——冲孔正装冲压。
采用复合模生产。
方案三:冲孔——落料级进模冲压。
采用级进模生产。
方案一模具结构简单,但需两道工序两副模具,成本高而生产效率低,难以满足中批量生产要求。
方案二只需一副模具,工件的精度及生产效率都较高。
方案三也只需一副模具,但工件精度不高,模具制造及维护成本太高。
通过对上述三种方法的分析比较,方案二为最佳。
3.主要设计计算(1)排样方式的确定及其计算搭边a1=2.0mm a=2.2mm条料宽度偏差Δ=0.20mm 0.5mm选1400Χ3500mm的钢板条料宽度=+2a+c)=34.4mm材料利用率为61.51%.(2)冲压力的计算该模具采用复合模,弹性卸料,上出件。
Tb=300MpaL=26+13+18+2+4+7+8+=113.96mmF=KLtTb=1.3=88888.8N=F=0.0588888.8N=44444.4N=F=0.0688888.8N=5333.28N=F++=98666.568N(3)压力中心的确定及计算该工件冲裁力不大,压力中心偏移圆孔中心较小,为了便于模具的加工与装配,模具中心选在圆孔中心。
(4)在确定工作零件刃口尺寸计算方法之前,首先要考虑工作零件的加工方法及模具装配方法。
结合模具结构及工件生产批量,适于采用配合加工落料凸模、凹模、凸凹模及固定板、卸料板。
使制造成本降低,装配工作简化。
因此工作零件刃口尺寸计算就按配合加工的方法计算,具体计算如下先选凹模为基准件,=0.246mm =0.360mmX=0.5磨损后增大的尺寸:=mm mm=mm=mm=mm=mm=(6-0.12+0.50.06)=mm=(8-0.15+0.50.15)0.15=mm凸模实际刃口尺寸与落料凹模配制,保证最小双面合理间隙值=0.246mm(5)卸料橡胶的设计卸料板工作行程6mm橡胶工作行程11mm橡胶自由高度44mm橡胶的预压缩量6.6mm每个橡胶承受的载荷1111.1N橡胶的外径40mm橡胶的安装高度37.4mm4.模具总体设计(1)模具类型的选择复合模(2)定位方式的选择因为该模具采用的是条料,控制条料的送进方向采用导料销,无侧压装置。
- 1、下载文档前请自行甄别文档内容的完整性,平台不提供额外的编辑、内容补充、找答案等附加服务。
- 2、"仅部分预览"的文档,不可在线预览部分如存在完整性等问题,可反馈申请退款(可完整预览的文档不适用该条件!)。
- 3、如文档侵犯您的权益,请联系客服反馈,我们会尽快为您处理(人工客服工作时间:9:00-18:30)。
【范例】(1)题目:东风EQ-1090汽车储气简支架(2)原始数据数据如图7—1所示。
大批量生产,材料为Q215,t=3mm。
图7-1零件图(3)工艺分析此工件既有冲孔,又有落料两个工序。
材料为Q235、t=3mm的碳素钢,具有良好的冲压性能,适合冲裁,工件结构中等复杂,有一个直径φ44mm的圆孔,一个60mm×26mm、圆角半径为R6mm的长方形孔和两个直径13mm的椭圆孔。
此工件满足冲裁的加工要求,孔与孔、孔与工件边缘之间的最小壁厚大于8mm。
工件的尺寸落料按ITll级,冲孔按IT10级计算。
尺寸精度一般,普通冲裁完全能满足要求。
(4)冲裁工艺方案的确定①方案种类该工件包括落料、冲孑L两个基本工序,可有以下三种工艺方案。
方案一:先冲孔,后落料。
采用单工序模生产。
方案二:冲孔一落料级进冲压。
采用级进模生产。
方案三:采用落料一冲孔同时进行的复合模生产。
②方案的比较各方案的特点及比较如下。
方案一:模具结构简单,制造方便,但需要两道工序,两副模具,成本相对较高,生产效率低,且更重要的是在第一道工序完成后,进入第二道工序必然会增大误差,使工件精度、质量大打折扣,达不到所需的要求,难以满足生产需要。
故而不选此方案。
方案二:级进模是一种多工位、效率高的加工方法。
但级进模轮廓尺寸较大,制造复杂,成本较高,一般适用于大批量、小型冲压件。
而本工件尺寸轮廓较大,采用此方案,势必会增大模具尺寸,使加工难度提高,因而也排除此方案。
方案三:只需要一套模具,工件的精度及生产效率要求都能满足,模具轮廓尺寸较小、模具的制造成本不高。
故本方案用先冲孔后落料的方法。
③方案的确定综上所述,本套模具采用冲孔一落料复合模。
(5)模具结构形式的确定复合模有两种结构形式,正装式复合模和倒装式复合模。
分析该工件成形后脱模方便性,正装式复合模成形后工件留在下模,需向上推出工件,取件不方便。
倒装式复合模成形后工件留在上模,只需在上模装一副推件装置,故采用倒装式复合模。
图7 2粗画排样图(6)工艺尺寸计算 ①排样设计a .排样方法的确定根据工件的形状。
确定采用无废料排样的方法不可能做到,但能采用有废料和少废料的排样方法。
经多次排样计算决定采用直对排法,初画排样图如图7 2所示。
b .确定搭边值查表,取最小搭边值:工件间a l =2.8,侧面a=3.2。
考虑到工件的尺寸比较大,在冲压过程中须在两边设置压边值,则应取。
a=5;为了方便计算取a l =3。
c. 确定条料步距步距:257.5mm ,宽度:250+5+5=260mm . d .条料的利用率21752052.35%257.5260η⨯==⨯e .画出排样图根据以上资料画出排样图,如图7-3所示。
图7-3排样图②冲裁力的计算 a .冲裁力F查表9-1取材料Q235的抗拉强度σb=386MPa 由 F ≈Lt σb已知:L=181+113+10×2+220.5+50.73+39.7+98.27+π×44+14×2 +48×2+π×6×2+5×4+π×13×2=1124.68所以 F=1124.68×3×386N=1302379N ≈1300kNb .卸料力Fx由Fx=KxF ,已知Kx=0.04(查表2-17) 则 Fx=KxF=0.004×1300=52kN c .推件力F T由F T =nK T F ,已知n=4 K T =0.045(查表2-17) 则 F T =nK T F=4×0.045×1300=23.4kN d .顶件力FD由F D =nK D F ,已知K D =0.05(查表2-17)则 F D =nK D F=0.05×1300=65kN③压力机公称压力的确定本模具采用刚性卸料装置和下出料方式,所以 Fz=F+F T =1323.4kN根据以上计算结果,冲压设备拟选JA21-160。
④冲裁压力中心的确定a .按比例画出每一个凸模刃口轮廓的位置,并确定坐标系,标注各段压力中心坐标点,如图7-4所示。
图7-4压力中心计算图b .画出坐标轴x 、y 。
c .分别计算出各段压力中点及各段压力中点的坐标值,并标注如图7-4所示。
冲裁直线段时,其压力中心位于各段直线段的中心。
冲裁圆弧线段时,其压力中心的位置见图7-5,按下式计算Y=(180Rsin α)/(πα)=RS /b 则 Y=142×188/220.5=121图7-5压力中心的位置所以,根据图7-5求出H 点的坐标为:H(121.27,120.86)。
d .分别计算出凸模刃口轮廓的周长。
冲裁压力中心计算数据见表7-1。
e .根据力学原理,分力对某轴的力矩等于各分力对同轴力矩的代数和,则可求得压力中心坐标(0x ,0y )∑∑===++++++=ni ini ii nnn LxL L L L x L x L x L x 112122110∑∑===++++++=ni ini iinnn LyL L L L y L y L y L y 112122110得 00101.8762.73x y ==综上所述,冲裁件的压力中心坐标为(10l.87,62.73)。
⑤刃口尺寸的计算a .加工方法的确定。
结合模具及工件的形状特点,此模具制造宜采用配作法,落料时,选凹模为设计基准件,只需要计算落料凹模刃口尺寸及制造公差,凸模刃口尺寸由凹模实际尺寸按要求配作;冲孔时,则只需计算凸模的刃口尺寸及制造公差,凹模刃口尺寸由凸模实际尺寸按要求配作;只是需要在配作时保证最小双面合理间隙值Zmin=0.46mm(查表)。
凸凹模刃口尺寸由凸模配作尺寸和凹模配作尺寸结合完成。
b.采用配作法,先判断模具各个尺寸在模具磨损后的变化情况,分三种情况,分别统计如下。
第一种尺寸(增大):181,171,56.5,14.5,98.27,50.73,179,113,56,27,51,75。
第二种尺寸(减小):142,13,26,60,44,6。
第三种尺寸(不变):10,5,60,40。
c.按入体原则查表2-3确定冲裁件内形与内形尺寸公差,工作零件刃口尺寸计算见表。
d.画出落料凹模、凸凹模尺寸,如图7-6所示。
图7—6工作零件尺寸e.卸料装置的设计。
采用图7—7所示的卸料装置,已知冲裁板厚t=3mm,冲裁卸料力FX=52kN。
根据模具安装位置拟选6个弹簧,每个弹簧的预压力为FO≥FX/n=8.67kN查第9章表9-32圆柱螺旋压缩弹簧,初选弹簧规格为(使所选弹簧的工作极限负荷Fj>F预)D=6mm,D=30mm,hO=60mm,Fj=1700mm,hj=13.1mm,n=7,f=1.88mm,t=7.8mm其中,d为材料直径,D为弹簧大径,Fj为工作极限负荷,hO为自由高度,hj 为工作极限负荷下变形量,n为有效圈数,t为节距。
弹簧的总压缩量为66.81xjjFH h mmF∆=⨯=图7 7卸料装置l一打杆;2推板;3一连接推杆;4一推件块(7)模具总体结构设计①模具类型的选择由冲压工艺分析可知,采用复合模冲压,所以本套模具类型为复合模。
②定位方式的选择因为该模具采用的是条料,控制条料的送进方向采用导料销;控制条料的送进步距采用弹簧弹顶的活动挡料销来定步距。
而第一件的冲压位置因为条料有一定的余量,可以靠操作工人目测来确定。
③卸料、出件方式的选择根据模具冲裁的运动特点,该模具采用刚性卸料方式比较方便。
因为工件料厚为3mm,推件力比较大,用弹性装置取出工件不太容易,且对弹力要求很高,不易使用。
而采用推件块,利用模具的开模力来推出工件,既安全又可靠。
故采用刚性装置取出工件。
结构如图7-7所示。
④导柱、导套位置的确定为了提高模具的寿命和工件质量,方便安装、调整、维修模具,该复合模采用中间导柱模架。
(8)主要零部件的设计①工作零部件的结构设计a.落料凹模凹模采用整体凹模,轮廓全部采用数控线切割机床即可一次成形,安排凹模在模架上的位置时,要依据压力中心的数据,尽量保证压力中心与模柄中心重合。
其轮廓尺寸可按公式(2-24)和公式(2-25)计算凹模厚度H=kb=0.20×181=36.2mm(查表2-22得k=0.22)凹模壁厚C=(1.5~2)H=54.3~72.4mm取凹模厚度H=60ram,壁厚C取60mm。
凹模宽度B=b+2c=179+2×60=299mm(送料方向)凹模长度L=181+2×60=301根据工件图样,在分析受力情况及保证壁厚强度的前提下,取凹模长度为315mm,宽度为315mm,所以凹模轮廓尺寸为315mm×315mm×60mm。
b.冲孔凸模根据图样:工件中有4个孔,其中有2个孔大小相等,因此需设计3支凸模。
为了方便固定,都采用阶梯式,长度为L=凹模+固定板+t=60+30+3.5=93.5mm。
c.凸凹模当采用倒装复合模时,凸凹模尺寸计算如下=h1+h2+t+h=20+30+3+10.5=63.5mmH凸凹式中,hl为卸料板厚度,取20mm;h2为凸凹模固定板厚度,取30mm;t为材料的厚度,取3mm;h为卸料板与固定板之间的安全高度,取10.5。
因凸凹模为模具设计中的配作件,所以应保证与冲孔凸模和落料凹模的双边合理间隙Zmin。
②定位零件的设计结合本套模具的具体结构,考虑到工件的形状,设置一个φ6活动挡料销(起定距的作用)和两个φ8的活动导料销。
挡料销和导料销的下面分别采用压缩弹簧,在开模时,弹簧恢复弹力把挡料销顶起,使它处于工作状态,旁边的导料销也一起工作,具体结构如图7—8所示。
图7—8活动挡料销a.卸料板设计卸料板的周界尺寸与凹模周界尺寸相同,厚度为20mm,材料为45钢,淬火硬变为40~45HRC。
b. 卸料螺钉的选用卸料板采用6个M8的螺钉固定,长度L=h1+h2+a=44+8+15=67mm(其中hl为弹簧的安装高度;h2为卸料板工作行程;a 为凸凹模固定板厚度)。
③模架及其他零部件的设计该模具采用中间导柱模架,这种模架的导柱在模具中间位置,冲压时可以防止由于偏心力矩而引起的模具歪斜。
以凹模周界尺寸为依据,查第表9-48选择模架规格导柱:d(mm)×L(mm)分别为φ45×230、φ50×230(GB/T 2861.1)。
导套:d(mm)×L(mm)×D(mm)分别为φ45×125×48、φ45×125×48(GB/T2861.6)。
上模座厚度H上取50mm,下模座厚度H下取60mm,上垫板厚度H垫取10mm,则该模具的闭合高度H闭为H闭=H上+H下+H垫+L+H-h=50+60+10+93.5+63.5-3.5=273mm式中L——凸模高度,mm;H——凸凹模高度,mm;h——凸模冲裁后进入凸凹模的深度,mm。