FMEA(失效模式与影响分析)
FMEA失效模式后果分析

• 介绍 • FMEA失效模式分析 • 后果分析 • 风险优先级排序 • 改进措施和预防措施 • 案例分析
01
介绍
FMEA的定义
FMEA(Failure Modes and Effects Analysis)即失效模式和影响分析,是一种预 防性的质量工具,用于评估产品设计或流程中潜在的失效模式及其对系统性能的影 响。
失效模式是指产品或过程中可能发生的故障、异常或性能下降的情况。根据不同的分类标准,失效模式可以分为 不同的类型。
详细描述
失效模式是指产品或过程中可能发生的故障、异常或性能下降的情况。根据产品或过程的性质和用途,失效模式 可以分为机械、电气、化学、热等多种类型。同时,根据失效的严重程度和影响范围,失效模式可以分为致命、 严重、一般和轻微等不同级别。
风险优先级排序的方法和步骤
步骤
风险优先级排序通常包括以下步骤
1. 识别潜在失效模式
分析产品或过程中可能出现的各种失效模式。
2. 评估失效模式的影响
评估每种失效模式对产品或过程性能的影响程度,包括安全性、可 靠性、有效性等方面的影响。
风险优先级排序的方法和步骤
3. 评估失效模式的概率和可检测性
01
应用实例2
医疗器械FMEA分析中,对潜在的失效模式如设备故障、误操作等进行风险评估,制定相应的风险管 理计划,确保产品的安全性和可靠性。
05
改进措施和预防措施
改进措施的定义和分类
定义
改进措施是指针对已经发生的失效模式,采 取的修复、补偿或纠正措施,以降低或消除 失效模式对产品或过程的影响。
分类Βιβλιοθήκη 改进措施可以分为临时性措施和永久性措施。 临时性措施通常用于快速解决问题,而永久 性措施则用于长期解决失效模式。
FMEA失效模式与影响分析培训课程大纲

常用FMEA工具概述
FMEA表格
用于记录失效模式、影响、原因、控制措施等信息,是FMEA分 析的基础工具。
故障树分析(FTA)
通过图形化方式展示系统失效的逻辑关系,帮助识别潜在失效模式 。
因果图(鱼骨图)
用于分析失效原因,从人、机、料、法来自环等方面进行深入挖掘。软件辅助进行FMEA分析优势
高效性
通过减少产品失效,可以降低维修和 保修成本,提高客户满意度。
培训课程目标与内容
• 课程目标:使学员掌握FMEA的基本原理和方法,能够独立完 成FMEA分析,并具备在团队中推广和应用FMEA的能力。
培训课程目标与内容
课程内容 FMEA基本概念和原理
失效模式识别与评估
培训课程目标与内容
影响分析与风险控制
案例二
某石油化工企业对炼油装置进行FMEA分析,识别潜在的设备故障和操作风险,制定相应 的预防措施和应急预案,确保了生产过程的安全稳定运行。
案例三
某电力公司对变电站设备进行FMEA分析,通过识别潜在的电气故障和机械故障模式,优 化设备维护和检修计划,提高了电网运行的稳定性和可靠性。
04
FMEA工具与软件介绍
软件可快速处理大量数 据,提高分析效率。
准确性
软件内置算法可准确计 算风险优先数(RPN)
,避免人为误差。
可视化
软件提供图形化界面, 方便用户直观理解分析
结果。
可追溯性
软件可记录分析过程和 数据,方便后续审查和
改进。
工具软件操作演示
FMEA软件界面介绍
展示软件界面,介绍各功能模块。
数据输入与编辑
演示如何在软件中输入和编辑FMEA 相关数据。
案例分析
FMEA失效模式及其影响分析
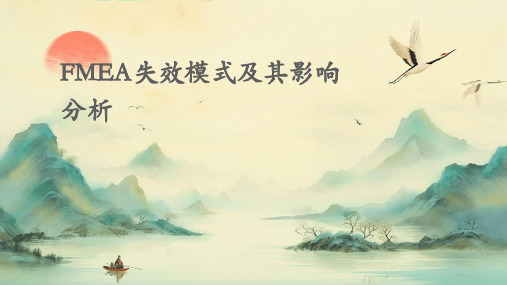
03
FMEA失效影响分析
直接和间接影响
直接影响
指失效模式对产品或系统的性能、安 全性、可靠性和可用性等直接造成的 影响。例如,电池的充电功能失效会 导致设备无法正常工作。
间接影响
指失效模式引发的连锁反应或次生问 题,可能涉及到供应链、生产、销售 和服务等环节。例如,关键零部件的 失效可能导致整条生产线停产。
制中的问题,提高产品的可靠性和安全性。
识别和评估
总结词
在FMEA失效模式分析中,识别和评估是关键步骤,需要全面考虑各种可能的失效模式,并对其影响进行量化评 估。
详细描述
在识别阶段,团队需要充分了解产品或过程的设计、制造和使用环境,找出可能出现的各种失效模式。这些失效 模式可能包括机械、电气、化学、热学等多个方面。在评估阶段,团队需要分析每种失效模式的发生概率、严重 程度以及可检测性,为后续的优先级排序提供依据。
静态性
FMEA通常在产品设计阶段进行,对后续生产和使用的动 态变化考虑不足,可能无法全面反映产品在实际使用中的 失效模式。
高成本
FMEA需要投入大量时间和资源进行数据收集、分析和改 进措施制定,对于小型企业或项目可能存在成本压力。
06
案例研究
案例一:汽车制造业的FMEA应用
总结词
汽车制造业是FMEA应用的重要领域,通过分析失效 模式及其影响,可以优化产品设计、生产和质量控制 。
FMEA失效模式及其影响 分析
• 介绍 • FMEA失效模式分析 • FMEA失效影响分析 • FMEA实施步骤 • FMEA的优点和局限性 • 案例研究
01
介绍
FMEA的定义
• FMEA(Failure Modes and Effects Analysis)即失效模式与影响分析, 是一种预防性的质量工具,用于评估 产品设计或流程中潜在的失效模式及 其对系统性能的影响。它通过识别、 评估和优先处理那些可能对产品或流 程性能产生最大影响的失效模式,帮 助组织减少或消除潜在的问题,提高 产品和流程的可靠性和安全性。
失效模式与影响分析FMEA
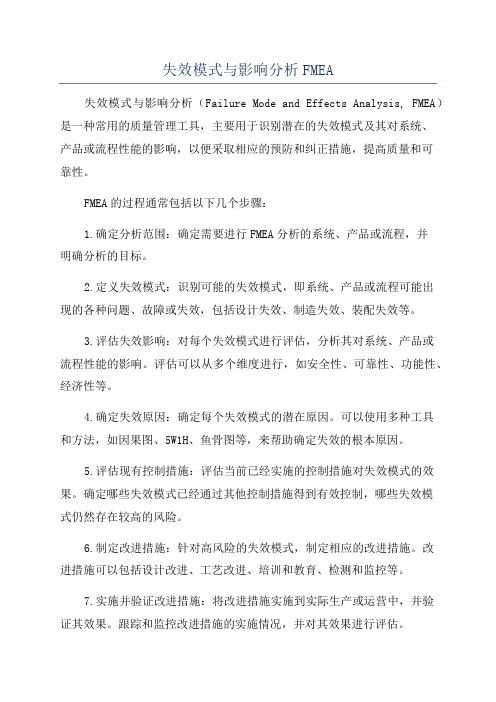
失效模式与影响分析FMEA失效模式与影响分析(Failure Mode and Effects Analysis, FMEA)是一种常用的质量管理工具,主要用于识别潜在的失效模式及其对系统、产品或流程性能的影响,以便采取相应的预防和纠正措施,提高质量和可靠性。
FMEA的过程通常包括以下几个步骤:1.确定分析范围:确定需要进行FMEA分析的系统、产品或流程,并明确分析的目标。
2.定义失效模式:识别可能的失效模式,即系统、产品或流程可能出现的各种问题、故障或失效,包括设计失效、制造失效、装配失效等。
3.评估失效影响:对每个失效模式进行评估,分析其对系统、产品或流程性能的影响。
评估可以从多个维度进行,如安全性、可靠性、功能性、经济性等。
4.确定失效原因:确定每个失效模式的潜在原因。
可以使用多种工具和方法,如因果图、5W1H、鱼骨图等,来帮助确定失效的根本原因。
5.评估现有控制措施:评估当前已经实施的控制措施对失效模式的效果。
确定哪些失效模式已经通过其他控制措施得到有效控制,哪些失效模式仍然存在较高的风险。
6.制定改进措施:针对高风险的失效模式,制定相应的改进措施。
改进措施可以包括设计改进、工艺改进、培训和教育、检测和监控等。
7.实施并验证改进措施:将改进措施实施到实际生产或运营中,并验证其效果。
跟踪和监控改进措施的实施情况,并对其效果进行评估。
通过进行FMEA分析,可以帮助组织识别和管理潜在的风险,提前采取预防措施,减少系统、产品或流程的失效概率,以实现质量和可靠性的提升。
FMEA分析可以应用于各个领域,如制造业、医疗设备、航空航天、汽车等。
FMEA的应用具有以下几个特点和优势:1.预防导向:FMEA分析主要关注于预防失效模式的发生,通过分析潜在的失效原因和影响,预测可能的失效模式,制定相应的预防措施,从而避免质量问题的发生。
2.多维度评估:FMEA分析不仅关注失效模式的影响对系统、产品或流程的影响,还可以从多个维度进行评估,如安全性、可靠性、功能性、经济性等,以全面了解失效模式的风险。
FMEA作业规范(失效模式及影响分析)

失效模式及影響分析(FMEA)1.定義:1) 英文 Failure Mode and Effects Analysis, 縮寫FMEA。
是一種由下而上的歸納式系統分析或流程分析方法,用來評估潛在性的錯誤。
包含找出什麼會造成錯誤,以及會發生錯誤的方法﹝失效模式﹞,決定每個失效模式對系統的影響。
根據經驗分析産品設計與生産工藝中存在的弱點和可能産生的缺陷公及這些缺陷産生的後果與風險,在決策過程中採取措施加以清除。
3) 分爲設計失效模式分析過程失效分析.過程FMEA是以工藝過程的每道工序爲分析物件; 設計FMEA是以系統或零部件爲分析物件;因此FMEA分析要從系統組成零件列表中或加工工藝流程事確定産品設計專案或過程專案.基本思路:劃分分析物件,確定每一物件的分析內容,研究分析結果及處理措施,製作FMEA分析表;4) FMEA流程分析流程缺陷的名稱潛在失效的後果建議糾正措施想象中可能産生的缺陷失效嚴重度評估缺陷被發現的概率缺陷産生的頻度缺陷産生的原因二.FMEA的分類1) 設計FMEA是由設計主管工程師/4組在設計早期彩的一種分析技術,用來在最大範圍內保證已充分地考慮到和指明各種潛在的失效模式及其相關的起因和理,評估最後的産品以及每個與之相關的系統,系統和零部件,以最嚴密的形式總結了設計思想.2) 在設計階段使用FMEA時常用:a. 有助於對設計要求的評估及對設計方案的相互權衡;b. 建立一套改進設計和開發試驗的優先控制系統;c. 爲推薦和跟蹤低風險的措施提供一個公開的的討論形式;d. 爲將來分析研究現場情況,評價設計時的更改及開發更先進的設計,提供參考;e. 有助於對製造和裝配要求的最初設計;f. 提高在設計開發過程中已考慮潛在失效及其對系統和産品使用影響的可能性;g. 對制定全面,有效的設計試驗計劃和開發專案提供更多資訊;3) 過程FMEA由製造主管工程師/小組,採用的分析技術,用在最大範圍內,保證充分地考慮到並指明失效模式及其相關的後果起因/機理,以最嚴密的形式總工程師結了工藝過程設計的設計思想,與一個工程師在任何製造過程中經常經歷的思維過程是一致的.過程FMEA假設設計的産品會滿足設計要求,它們的影響及避免措施由設計FMEA來解決.主要考慮與製造計劃的製造廠裝配過程有關的産品設計參數,以便最大限度地保證産品能滿足顧客要求和期望.3.FMEA的意義爲設計:生産、質保部門提供共用的資訊資源也爲同類産品的設計提供資料。
失效模式与影响分析

失效模式与影响分析失效模式与影响分析(英文:Failure mode and effects analysis,FMEA),又称为失效模式与后果分析、失效模式与效应分析、故障模式与后果分析或故障模式与效应分析等,是一种操作规程,旨在对系统范围内潜在的失效模式加以分析,以便按照严重程度加以分类,或者确定失效对于该系统的影响。
FMEA广泛应用于制造行业产品生命周期的各个阶段;而且,FMEA在服务行业的应用也在日益增多。
失效原因是指加工处理、设计过程中或项目/物品(英文:item)本身存在的任何错误或缺陷,尤其是那些将会对消费者造成影响的错误或缺陷;失效原因可分为潜在的和实际的。
影响分析指的是对于这些失效之处的调查研究。
基本术语失效模式(又称为故障模式)观察失效时所采取的方式;一般指的是失效的发生方式。
失效影响(又称为失效后果、故障后果)失效对于某物品/项目(英文:item)之操作、功能或功能性,或者状态所造成的直接后果。
约定级别(又称为约定级)代表物品/项目复杂性的一种标识符。
复杂性随级数接近于1而增加。
局部影响仅仅累及所分析物品/项目的失效影响。
上阶影响累及上一约定级别的失效影响。
终末影响累及最高约定级别或整个系统的失效影响。
失效原因(又称为故障原因)作为失效之根本原因的,或者启动导致失效的某一过程的,设计、加工处理、质量或零部件应用方面所存在的缺陷严重程度(又称为严重度)失效的后果。
严重程度考虑的是最终可能出现的损伤程度、财产损失或系统损坏所决定的,失效最为糟糕的潜在后果[1]。
历史从每次的失效/故障之中习得经验和教训,是一件代价高昂而又耗费时间的事情,而FMEA 则是一种用来研究失效/故障的,更为系统的方法。
同样,最好首先进行一些思维实验。
二十世纪40年代后期,美国空军正式采用了FMEA[2]。
后来,航天技术/火箭制造领域将FMEA用于在小样本情况下避免代价高昂的火箭技术发生差错。
其中的一个例子就是阿波罗空间计划。
失效模式与影响分析(FMEA)

可能给错药 药物名称或外表 厂商制造原 造成病人伤 相似 因 害
1
1
10
10
三、举例
4.分析失效模型和影响因素 表4.3 护士到病人单位给药 失效模式 原因 结果 S 1.护士太 可能给错 护士没有核对 匆忙。2. 药造成病 10 病人身份 病人没有 人伤害 识别手圈 1.无法识 给药途径 药物给药途径 别医嘱。 错误造成 10 错误 2.缺乏相 影响结果 关知识。
护士对药 卡 到备药间 备药 到病人病 房给药
三、举例
4.分析失效模型和影响因素
4.1 护士给药 表4.1护士核对给药纪录单
失效模式 结果 S 没有依照处 1.医嘱遗失。 给药记录单没有 方给药可能 10 2.书写医嘱 更新 影响病人结 时分心 果 1.书写医嘱 时不注意。 没有依照处 2.写后的医 方给药可能 给药时间不正确 嘱没有双重 10 影响病人结 核对。3.没 果 有计算机处 方系统 原因 O 5 D 5 RPN 改善措施 250
O
D RPN 改善措施
1.加强培 训。2.病 10 人佩戴手 圈
1
1
5
5
250
三、举例
5. 评判结果 失效模式 给药记录单没有更新 RPN 250
给药时间不正确 药物不正确 药物名称或外表相似
护士没有核对病人身份
250 250 10
10
药物给药途径错误
250
三、举例
6.根本原因分析 6.1列出最需要改善的失效模式: 给药记录单没有更新、给药时间不正确、药物不 正确、药物给错途径 6.2 对相应失效模式分析原因。
三、举例
3. 分析流程 主题1:病人辨识和输血流程:
制作及佩 戴手圈 采血和 备血 检验科 流程 送血到 病房 核对 病人
失效模式及影响分析

失效模式及影响分析失效模式及影响分析(Failure mode and effects analysis,简称FMEA)是一种用于系统故障预防和可靠性改进的方法。
通过对系统的各个组成部分及其可能的失效模式和影响进行分析,能够帮助识别和消除潜在的故障点,提高系统的可靠性和安全性。
失效模式(Failure mode)是指系统、产品或组件在正常条件下未能按预期执行其功能或要求的方式,即失效的特定表现形式。
常见的失效模式包括:停止工作、性能下降、产生误差、漏水/泄露、短路、断裂等。
影响(Effects)是指失效模式对系统、用户、环境或企业造成的潜在危害或负面影响。
影响的级别可以从事故、严重故障、中度故障、轻微故障、降低可靠性等方面来评估。
FMEA通过对失效模式和其影响进行分析,可以进行以下几个方面的评估:1. 严重性评估(Severity Evaluation):根据失效模式对系统、用户或环境的影响程度,评估其严重性级别。
将影响分为高、中、低等级,并确定具体的损失程度。
2. 发生频率评估(Occurrence Evaluation):根据失效模式发生的概率或频率,评估其出现的可能性。
通过对设备或系统历史数据的统计分析,可确定每年失效次数或概率。
3. 检测能力评估(Detection Evaluation):根据可用的检测手段和方法,评估对失效模式的检测能力。
检测能力可以通过验证和验证手段的准确性和可靠性来评估。
通过对这三个因素进行综合评价,可以计算出风险优先数(Risk Priority Number, RPN)。
RPN是一个综合评估指标,用于确定优先改进的失效模式。
FMEA的主要目的是帮助预防失效,减少系统故障,并且在设计或改进产品或过程时识别并降低风险。
通过FMEA分析,可以及早发现和解决潜在问题,提高系统可靠性,减少维修和停机时间,降低成本和提高用户满意度。
FMEA可以应用于各个领域,如制造业、软件开发、航空航天等。
FMEA失效分析与失效模式分析
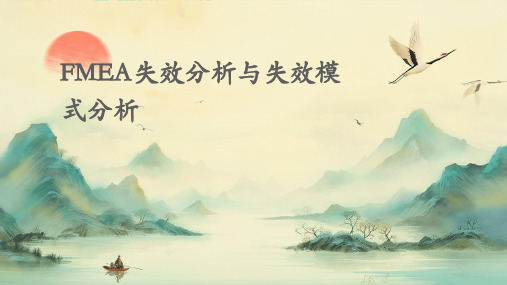
FMEA失效分析通常包括失效模式分析作为其一部分,两者都是质量 保证和可靠性工程的重要工具。
02
FMEA失效模式分析
失效模式的定义与分类
失效模式定义
在产品或过程中,可能导致产品或系 统不能达到预期功能的现象或问题。
失效模式分类
按失效的性质可分为功能失效、潜在 失效、外观失效等;按失效的原因可 分为设计缺陷、制造缺陷、使用不当 等。
06
案例研究
案例一:汽车刹车系统的FMEA失效分析
总结词
全面分析,预防为主
详细描述
通过对汽车刹车系统进行FMEA失效分析, 识别出潜在的失效模式和原因,并采取相应 的预防措施,确保刹车系统的可靠性和安全
性。
案例二
要点一
总结词
细致入微,失效定位
要点二
详细描述
对电子产品电路板进行FMEA失效模式分析,准确定位失 效模式和原因,提出改进措施,提高电路板的可靠性和稳 定性。
失效风险
指产品或系统在实现其功能过程中可能出现的故障、异常或性能下降的风险。
分类
按照失效模式和影响分析(FMEA)的方法,失效风险可分为功能失效风险和潜在失效 风险。
失效风险的分析方法
01
故障树分析(FTA)
通过建立故障树,分析系统各部件的故障对系统整体性能的影响。
02
事件树分析(ETA)
通过建立事件树,分析系统各事件的发生对系统性能的影响。
失效模式的分析方法
故障树分析法
01
通过建立故障树,分析导致故障的各种因素,确定故障发生的
概率和影响程度。
故障模式与影响分析法
02
分析产品或系统的各种故障模式,评估其对系统功能的影响程
失效模式与影响分析
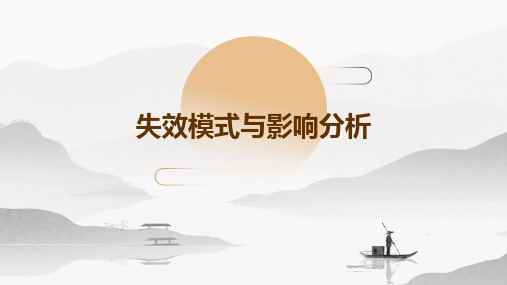
将改进和预防措施付诸实施,并对实施效果进行跟 踪和评估。
06
失效模式与影响分析的案例 研究
案例一
总结词
电子产品中的热设计失效是常见的失效 模式之一,可能导致设备性能下降、损 坏或安全问题。
VS
详细描述
热设计失效通常表现为过热、散热不良等 现象,可能由于设计缺陷、材料选择不当 、生产工艺问题等原因引起。这种失效模 式可能导致电子设备性能下降、加速设备 老化、引发火灾等安全问题,对用户和企 业造成重大损失。
设备或部件的物理损坏,如机械零件磨损、 电子元件烧毁等。
通信故障
信息传输中断或延迟,影响系统间的通信和 数据传输。
软件故障
计算机程序中的错误或不稳定性,可能导致 系统崩溃或数据丢失。
人为错误
操作失误、配置错误或使用不当,导致系统 功能异常或数据损坏。
潜在失效模式
潜在硬件故障
设备或部件可能存在的潜在问题,如早期磨损、 潜在的电子元件缺陷等。
总结词
桥梁结构中的疲劳失效是一种常见的失效模式,可能导致结构断裂、坍塌等严重后果。
详细描述
桥梁结构在长期承受车辆、风、地震等载荷的作用下,可能会出现疲劳损伤。这种损伤 通常不易被察觉,但随着时间的推移,损伤累积到一定程度后,可能导致结构断裂、坍 塌等严重后果。疲劳失效不仅会造成重大经济损失,还可能对人们的生命安全构成威胁。
使用条件
设备的工作负载、使用频率、持 续时间等条件影响设备的寿命和 可靠性,可能导致失效。
维护状况
定期维护和保养的执行情况直接 影响设备的性能和寿命,维护不 足可能导致设备提前失效。
03
影响分析
功能影响分析
功能影响分析是失效模式与影响分析中重要的一环,主要目的是评估产品或系统的功能失效对整个系 统的影响程度。
失效模式与影响分析FMEA
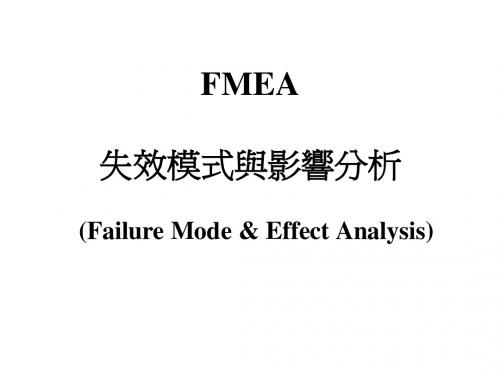
Cpk ≥1.67 ≥1.50 ≥1.33 ≥1.17 ≥1.00 ≥0.83 ≥0.67 ≥0.51 ≥0.33 <0.33
6(Moderate) 7(High) 经常发生 8(High) 9(Very High) 几乎不可避免 10(Very High)
难检度(Detection) 十.难检度 难检度
在现行的控制措施下 侦测失效发生的能 在现行的控制措施下,侦测失效发生的能 力 划分标准 主观判定 统计资料 1----有有效手段完全可以检测出来 有有效手段完全可以检测出来 10----无任何手段可以检测出来 无任何手段可以检测出来
难检度(D)划分标准
等级/评分
1~2 3~5 6~8 9 10
决定优先改善之失效模式 建议改善措施 改善实施
六.结果应用 结果应用
误解 满足客户要求 工作负担 误解----满足客户要求
六.结果应用 结果应用
实际----实际 避免采用不良率高的设计和制程 集中资源 循序改善产品设计和制程 集中资源,循序改善产品设计和制程 循环改善 不断提升设计和制程可靠度 循环改善,不断提升设计和制程可靠度 改进设计之参考 制程检验 测试标准 检验程序 检验规范等之参 制程检验,测试标准 检验程序,检验规范等之参 测试标准,检验程序 考 下次 下次FMEA分析之参考 分析之参考 产品可靠性 制程安全性 环保之评估参考 产品可靠性,制程安全性 制程安全性,环保之评估参考 工程师训练之参考
十二.设计FMEA与制程FMEA 之区别
对象 实施阶段 FMEA 团队成员 分析失效原因出发点 建议控制措施出发点
十三.设计FMEA
定义 定义: 预测产品设计中某些设计目标值可能产 生的失效及分析这些失效会对个产品外 结构,功能 及必能稳定性,可靠性及对 观,结构 功能 及必能稳定性 可靠性及对 结构 功能,及必能稳定性 制程造成的影响,并针对之从产品设计和 制程造成的影响 并针对之从产品设计和 制程设计等方面提出改善措施
FMEA(失效模式与影响分析)

失效模式与影响分析即“潜在失效模式及后果分析”。
FMEA是在产品设计阶段和过程设计阶段,对构成产品的子系统、零件,对构成过程的各个工序逐一进行分析,找出所有潜在的失效模式,并分析其可能的后果,从而预先采取必要的措施,以提高产品的质量和可靠性的一种系统化的活动。
FMEA又根据产品故障可能产生的环节:设计、制造过程、使用、承包商(供应商)以及服务可细分为:1. DFMEA:设计FMEA2. PFMEA:过程FMEA3. EFMEA:设备FMEA4. SFMEA:体系FMEA一、概念潜在的失效模式及后果分析(Failure Mode and Effects Analysis,简记为FMEA),是“事前的预防措施”,并“由下至上。
关键词:潜在的—失效还没有发生,它可能会发生,但不一定会发生。
“核心”集中于:预防—处理预计的失效,其原因及后果/影响。
主要工作:风险评估—潜在失效模式的后果影响。
FMEA 开始于产品设计和制造过程开发活动之前,并指导贯穿实施于整个产品周期。
进行分析系统中每一产品所有可能产生的故障模式及其对系统造成的所有可能影响,并按每一个故障模式的严重程度,检测难易程度以及发生频度予以分类的一种归纳分析方法。
二、目的·能够容易、低成本地对产品或过程进行修改,从而减轻事后危机的修改。
·找到能够避免或减少这些潜在失效发生的措施;三、RPN的评价准则1.1 设计FMEA严重性(Severity :S)1)评分原则a)衡量是小的影响程度b)失效影响:产品或制程的某一失效对产品外观,结构,功能,性能稳定性,可靠性影响c)或对下一制程,使用者或设备的影响d)或对最终客户、政府法规、安全、环保的违及e)划分标准——主观判定2)设计:FMEA风险评估标准说明严重性(Severity :S):严重性是对下一个制程、系统或客户所发生的潜在失效模式效果的严重性进行评估,严重性仅适用于效果,严重性等级指数的减低只能透过设计变更才能够生效,严重性应该在1~10的等级上评估。
FMEA失效分析
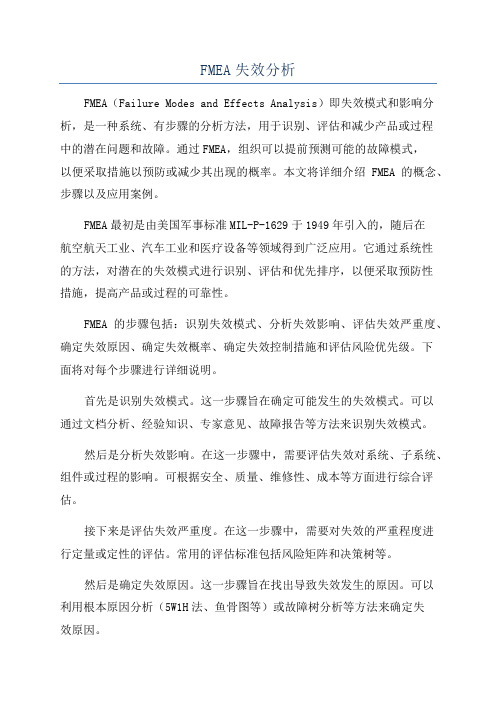
FMEA失效分析FMEA(Failure Modes and Effects Analysis)即失效模式和影响分析,是一种系统、有步骤的分析方法,用于识别、评估和减少产品或过程中的潜在问题和故障。
通过FMEA,组织可以提前预测可能的故障模式,以便采取措施以预防或减少其出现的概率。
本文将详细介绍FMEA的概念、步骤以及应用案例。
FMEA最初是由美国军事标准MIL-P-1629于1949年引入的,随后在航空航天工业、汽车工业和医疗设备等领域得到广泛应用。
它通过系统性的方法,对潜在的失效模式进行识别、评估和优先排序,以便采取预防性措施,提高产品或过程的可靠性。
FMEA的步骤包括:识别失效模式、分析失效影响、评估失效严重度、确定失效原因、确定失效概率、确定失效控制措施和评估风险优先级。
下面将对每个步骤进行详细说明。
首先是识别失效模式。
这一步骤旨在确定可能发生的失效模式。
可以通过文档分析、经验知识、专家意见、故障报告等方法来识别失效模式。
然后是分析失效影响。
在这一步骤中,需要评估失效对系统、子系统、组件或过程的影响。
可根据安全、质量、维修性、成本等方面进行综合评估。
接下来是评估失效严重度。
在这一步骤中,需要对失效的严重程度进行定量或定性的评估。
常用的评估标准包括风险矩阵和决策树等。
然后是确定失效原因。
这一步骤旨在找出导致失效发生的原因。
可以利用根本原因分析(5W1H法、鱼骨图等)或故障树分析等方法来确定失效原因。
接下来是确定失效概率。
在这一步骤中,需要评估失效发生的概率。
可以通过统计数据、经验数据、专家意见等方法来估计失效概率。
然后是确定失效控制措施。
在这一步骤中,需要确定预防性或纠正性措施,以降低或消除潜在失效的发生。
可以采用设计改进、质量控制、教育培训等方法来实施失效控制措施。
最后是评估风险优先级。
在这一步骤中,需要对失效模式进行排序,以确定优先处理的失效模式。
一般采用风险优先级数(Risk Priority Number, RPN)来评估风险优先级,计算公式为RPN = 严重度× 发生可能性× 控制措施程度。
FMEA失效模式及分析手段

通过X光谱进行照射来分析不良,一般用在肉眼所看 不到的位置
三、声学扫描
通过超声波对内部进行扫描分析。 适用于晶元内部封装,各种孔洞,X光无法穿透物料
四、SEM&EDX
扫描电子显微镜&能谱仪
五、XPS
XPS: X光线电子能谱,也被称作化学分析用电子能谱。
原理:XPS的原理是用X射线去辐射样品,使原子或分子的内层电子或价电子 受激发射出来。被光子激发出来的电子称为光电子。可以测量光电子的能 量,以光电子的动能/束缚能为横坐标,相对强度(脉冲/s)为纵坐标可做 出光电子能谱图。从而获得试样有关信息。 适用于:元素的定性分析 ,鉴定元素的成分;元素的定量分析,原子的 含量或相对尝试;固体表面分析;化合物的结构;
FMEA是Failure Mode and Effects Analysis的 首字母简写即“失效模式与影响分析”,是在 产品的设计阶段和过程设计阶段,对构成 产品的子系统、零件、以及对构成的各个 程序逐一进行分析,找出所有潜在的失效 模式,分析其可能的影响,评估其风险, 降低其可能发生的概率,以提高产品质量 的可造性,确保顾客满意的系统化活动。
狭义:产品外观、功能的不良
FMEA
失效模式与影响分析
广义:引起不良的定位及分析
基于失效现象,能过信息收集、功能测试、电性能测试 以及简单的外观检查,确定失效部位与失效模式
使用各种物理、化学手段分析导致焊点失效或缺陷产生的机理,如 虚焊、污染、静电损伤、潮湿应力、介质腐蚀、疲劳损伤、离子迁 移、应力过载......
六、TOP-SIMS飞行时间二次离子质谱
TOF-SIMS是通过用一次离子激发样品表面,打出极其 微量的二次离子,根据二次离子因不同的质量而飞行到探 测器的时间不同来测定离子质量的极高分辨率的测量技术 。
- 1、下载文档前请自行甄别文档内容的完整性,平台不提供额外的编辑、内容补充、找答案等附加服务。
- 2、"仅部分预览"的文档,不可在线预览部分如存在完整性等问题,可反馈申请退款(可完整预览的文档不适用该条件!)。
- 3、如文档侵犯您的权益,请联系客服反馈,我们会尽快为您处理(人工客服工作时间:9:00-18:30)。
FMEA(失效模式与影响分析)Failure Mode and Effects Analysis潜在失效模式与后果分析在设计和制造产品时,通常有三道控制缺陷的防线:避免或消除故障起因、预先确定或检测故障、减少故障的影响和后果。
FMEA正是帮助我们从第一道防线就将缺陷消灭在摇篮之中的有效工具。
FMEA是一种可靠性设计的重要方法。
它实际上是FMA(故障模式分析)和FEA(故障影响分析)的组合。
它对各种可能的风险进行评价、分析,以便在现有技术的基础上消除这些风险或将这些风险减小到可接受的水平。
及时性是成功实施FMEA的最重要因素之一,它是一个“事前的行为”,而不是“事后的行为”。
为达到最佳效益,FMEA必须在故障模式被纳入产品之前进行。
FMEA实际是一组系列化的活动,其过程包括:找出产品/过程中潜在的故障模式;根据相应的评价体系对找出的潜在故障模式进行风险量化评估;列出故障起因/机理,寻找预防或改进措施。
由于产品故障可能与设计、制造过程、使用、承包商/供应商以及服务有关,因此FMEA又细分为设计FMEA、过程FMEA、使用FMEA和服务FMEA四类。
其中设计FMEA和过程FMEA最为常用。
设计FMEA(也记为d-FMEA)应在一个设计概念形成之时或之前开始,并且在产品开发各阶段中,当设计有变化或得到其他信息时及时不断地修改,并在图样加工完成之前结束。
其评价与分析的对象是最终的产品以及每个与之相关的系统、子系统和零部件。
需要注意的是,d-FMEA在体现设计意图的同时还应保证制造或装配能够实现设计意图。
因此,虽然d-FMEA不是靠过程控制来克服设计中的缺陷,但其可以考虑制造/装配过程中技术的/客观的限制,从而为过程控制提供了良好的基础。
进行d-FMEA有助于:·设计要求与设计方案的相互权衡;·制造与装配要求的最初设计;·提高在设计/开发过程中考虑潜在故障模式及其对系统和产品影响的可能性;·为制定全面、有效的设计试验计划和开发项目提供更多的信息;·建立一套改进设计和开发试验的优先控制系统;·为将来分析研究现场情况、评价设计的更改以及开发更先进的设计提供参考。
过程FMEA(也记为p-FMEA)应在生产工装准备之前、在过程可行性分析阶段或之前开始,而且要考虑从单个零件到总成的所有制造过程。
其评价与分析的对象是所有新的部件/过程、更改过的部件/过程及应用或环境有变化的原有部件/过程。
需要注意的是,虽然p-FMEA不是靠改变产品设计来克服过程缺陷,但它要考虑与计划的装配过程有关的产品设计特性参数,以便最大限度地保证产品满足用户的要求和期望。
p-FMEA一般包括下述内容:·确定与产品相关的过程潜在故障模式;·评价故障对用户的潜在影响;·确定潜在制造或装配过程的故障起因,确定减少故障发生或找出故障条件的过程控制变量;·编制潜在故障模式分级表,建立纠正措施的优选体系;·将制造或装配过程文件化。
FMEA技术的应用发展十分迅速。
50年代初,美国第一次将FMEA思想用于一种战斗机操作系统的设计分析,到了60年代中期,FMEA技术正式用于航天工业(Apollo计划)。
1976年,美国国防部颁布了FMEA的军用标准,但仅限于设计方面。
70年代末,FMEA技术开始进入汽车工业和医疗设备工业。
80年代初,进入微电子工业。
80年代中期,汽车工业开始应用过程FMEA确认其制造过程。
到了1988年,美国联邦航空局发布咨询通报要求所有航空系统的设计及分析都必须使用FMEA。
1991年,ISO-9000推荐使用FMEA提高产品和过程的设计。
1994年,FMEA又成为QS-9000的认证要求。
目前,FMEA已在工程实践中形成了一套科学而完整的分析方法。
FMEA可以描述为一组系统化的活动,其目的是:认可并评价产品/过程中的潜在失效以及该失效的后果;确定能够消除或减少潜在失效发生机会的措施;将全部过程形成文件.无论是产品设计或者是过程设计,FMEA所关注的主要是策划和设计的过程,但随着其使用的场合不同又有不同的区分.常见的FMEA类别有:DFMEA:设计FMEAPFMEA:过程FMEAEFMEA:设备FMEASFMEA:体系FMEA在进行FMEA时有三种基本的情形,每一种都有其不同的范围或关注焦点:情形1:新设计,新技术或新过程.FMEA的范围是全部设计,技术或过程.情形2:对现有设计或过程的修改(假设对现有设计或过程已有FMEA).FMEA的范围应集中于对设计或过程的修改,由于修改可能产生的相互影响以及现场和历史情况.情形3:将现有的设计或过程用于新的环境,场所或应用(假设对现有设计或过程已有FMEA).FMEA的范围是新环境或场所对现有设计或过程的影响.█FMEA—8D流程的介绍QS9000、ISO/TS16949、ISO9001、TL9000、ISO14001、OHSAS18001等管理体系中都有涉及到“预防措施”;依据“ISO9001:2000质量管理体系—基础和术语”的定义,“预防措施”是指“为消除潜在不合格或其他潜在不期望情况的原因所采取的措施”,或者简单地定义为:采取预防措施是为了防止发生。
在企业实际的管理体系运作中,虽然都会去编制一份有关“预防措施”的形成文件的程序,但真正可以达到预见性地发现较全面的潜在问题通常存在较大难度,也即:这样作业的可操作性不强;取而代之的主要是“纠正措施”;但“纠正措施”与“预防措施”的确是两个不同的概念,“纠正措施”是为了防止同样的问题再次出现所采取的措施。
为能有效地实施“预防措施”,使可能存在的潜在问题无法出现,需要一个从识别问题到控制潜在影响的管理系统,对于这一点,各企业都可能制定各自不同的方法以对应,这些方法也许都是适用的;但这里所要介绍的是一种行之有效且便于操作的制定和实施“预防措施”的方法,即:美国三大车厂(戴姆勒克莱斯特、福特、通用)制定的“潜在失效模式及后果分析”,或简称为FMEA。
FMEA于2002年推出第三版本,该第三版本较第二版本更具备简便的可操作性。
FMEA在汽车零组件生产行业已被广泛的应用,同时这也是美国三大车厂对所属供应商的强制性要求之一。
FMEA 事实上就是一套严密的“预防措施”之识别、控制、提高的管理过程;其不仅可在汽车零组件行业可予使用,也可应用于任何期望能严格控制潜在问题出现的行业,尤其是产品(或服务)质量的好坏可能会极大影响到顾客利益的领域;因此,FMEA能在QS9000及ISO/TS16949一类的汽车业质量管理体系中运用,其同样可应用于其他管理体系之中,而且同样可以在企业内部形成一种严密的“预防措施”系统。
执行FMEA,其实并不困难,它是一种分析技术,即:在一张包括诸多要求的表单上进行分析并加以控制和应用便可达成的过程控制;美国三大车厂在《潜在失效模式及后果分析》一书中已有明确给定了这种表单的格式;该表单包含了如下主要内容:(1)“功能要求”:填写出被分析过程(或工序)的简单说明;(2)“潜在失效模式”:记录可能会出现的问题点;(3)“潜在失效后果”:列出上述问题点可能会引发的不良影响;(4)“严重度”:对上述问题点的不良影响进行评价并赋予分值(得分1~10分),分值愈高则影响愈严重;(5)“潜在失效起因或机理”:该潜在问题点可能出现的原因或产生机理分析;(6)“频度”:上述“起因或机理”出现的几率大小(得分1~10分),分值愈高则出现机会愈大;(7)“现行控制”:列出目前本企业对这一潜在问题点所运用的控制方法;(8)“探测度”:在采用“现行控制”的方法来控制时,该潜在问题可以被检查出来的难易程序(得分:1~10分),得分愈高则愈难以被检出;(9)“风险顺序数”:将上述“严重度”、“频度”、“探测度”得分相乘所得出的结果;该数值愈大则这一潜在问题愈严重,愈应及时采取“预防措施”;(10)“建议措施”:列出对“风险顺序数”较高之潜在问题点所制定的“预防措施”,以防止其发生;(11)“责任及目标完成日期”:写出实施上述“预防措施”的计划案;(12)“措施结果”:对上述“预防措施”计划案之实施状况的确认。
从上述内容项目不难看出这已经包含了处理“预防措施”之识别、控制所需的全部基本要求。
由于FMEA是一种“预防措施”,其必然是一种事先的行动;如果把FMEA当作事情发生以后再执行处置的动作,其将无法达到FMEA的真实效果,亦将把这一FMEA演变成“纠正措施”。
汽车行业产品由于存在人身安全风险及车辆召回等危机,不得不严格执行“预防措施”,其最有效的、最全面的方式也就是运用FMEA。
对于其他行业(或其他管理体系)在执行“预防措施”时,如果采用FMEA,同样将会极大降低失败的机会,事实上这亦是“预防措施”的最终目的。
当然对于其他行业(或其他管理体系)而言,不一定完全按照美国三大车厂给定的“严重度”、“频度”及“探测度”之评价标准进行评分,完全可以视本企业之实际情况设定一系列类似的评价标准以执行对策作业,且在具体操作手法上也可根据实情采用适合于自身的方式,只要能达到更有效地识别、控制潜在问题的发生即可。
总之,认识、了解FMEA,并予以持续采用,将会极大地强化企业的“预防措施”效果,使“错误”、“失败”出现的可能性达到最小。
FMEA 是由美国三大汽车制造公司(戴姆勒-克莱斯勒、福特、通用)制定并广泛应用于汽车零组件生产行业的可靠性设计分析方法。
其工作原理为:(1)明确潜在的失效模式,并对失效所产生的后果进行评分;(2)客观评估各种原因出现的可能性,以及当某种原因出现时企业能检测出该原因发生的可能性;(3)对各种潜在的产品和流程失效进行排序;(4)以消除产品和流程存在的问题为重点,并帮助预防问题的再次发生。
有关FMEA原理的应用主要体现在美国三大汽车制造公司制定的《潜在失效模式和后果分析》表格中。
该表的内容包括:(1)功能要求:填写被分析过程(或工序)的简要说明和工艺描述;(2)潜在失效模式:记录可能会出现的问题点;(3)潜在失效后果:推测问题点可能会引发的不良影响;(4)严重度(S):评价上述失效后果并赋予分值(1-10分,不良影响愈严重分值愈高);(5)潜在失效起因或机理:潜在问题点可能出现的原因或产生机理;(6)频度(O):上述潜在失效起因或机理出现的几率(1-10分,出现的几率愈大分值愈高);(7)现行控制:列出目前本企业对潜在问题点的控制方法;(8)探测度(D):在采用现行的控制方法实施控制时,潜在问题可被查出的难易程度(1-10,查出难度愈大分值愈高);(9)风险顺序数(RPN):严重度、频度、探测度三者得分之积,其数值愈大潜在问题愈严重,愈应及时采取预防措施;(10)建议措施:列出“风险顺序数”较高的潜在问题点,并制定相应预防措施,以防止潜在问题的发生;(11)责任及目标完成日期:制定实施预防措施的计划案;(12)措施结果:对预防措施计划案实施状况的确认。