导光板常见生异常的原因分析及解决方法
LED灯异常可能原因和解决措施
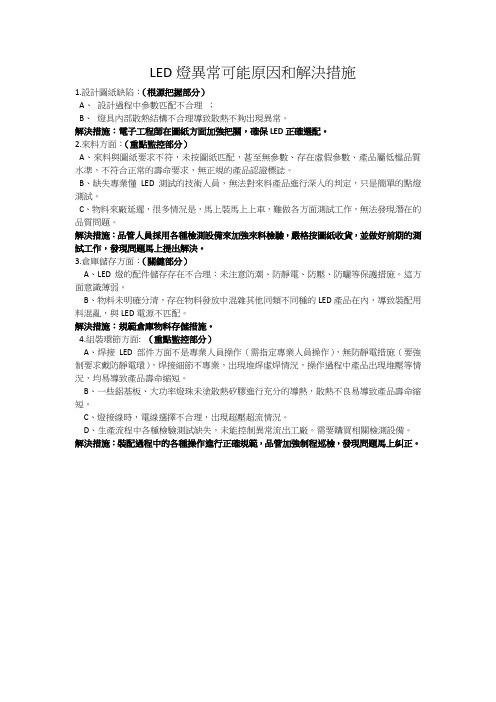
LED燈異常可能原因和解決措施1.設計圖紙缺陷:(根源把握部分)A、設計過程中參數匹配不合理;B、燈具內部散熱結構不合理導致散熱不夠出現異常。
解決措施:電子工程師在圖紙方面加強把關,確保LED正確選配。
2.來料方面:(重點監控部分)A、來料與圖紙要求不符,未按圖紙匹配,甚至無參數、存在虛假參數、產品屬低檔品質水準,不符合正常的壽命要求,無正規的產品認證標誌。
B、缺失專業懂LED測試的技術人員,無法對來料產品進行深入的判定,只是簡單的點燈測試。
C、物料來廠延遲,很多情況是,馬上裝馬上上車,難做各方面測試工作,無法發現潛在的品質問題。
解決措施:品管人員採用各種檢測設備來加強來料檢驗,嚴格按圖紙收貨,並做好前期的測試工作,發現問題馬上提出解決。
3.倉庫儲存方面:(關鍵部分)A、LED燈的配件儲存存在不合理:未注意防潮、防靜電、防壓、防曬等保護措施。
這方面意識薄弱。
B、物料未明確分清,存在物料發放中混雜其他同類不同種的LED產品在內,導致裝配用料混亂,與LED電源不匹配。
解決措施:規範倉庫物料存儲措施。
4.組裝環節方面:(重點監控部分)A、焊接LED部件方面不是專業人員操作(需指定專業人員操作),無防靜電措施(要強制要求戴防靜電環),焊接細節不專業,出現堆焊虛焊情況,操作過程中產品出現堆壓等情況,均易導致產品壽命縮短。
B、一些鋁基板、大功率燈珠未塗散熱矽膠進行充分的導熱,散熱不良易導致產品壽命縮短。
C、燈接線時,電線選擇不合理,出現超壓超流情況。
D、生產流程中各種檢驗測試缺失,未能控制異常流出工廠。
需要購買相關檢測設備。
解決措施:裝配過程中的各種操作進行正確規範,品管加強制程巡檢,發現問題馬上糾正。
14寸楔形导光板常见生产异常及解决方法
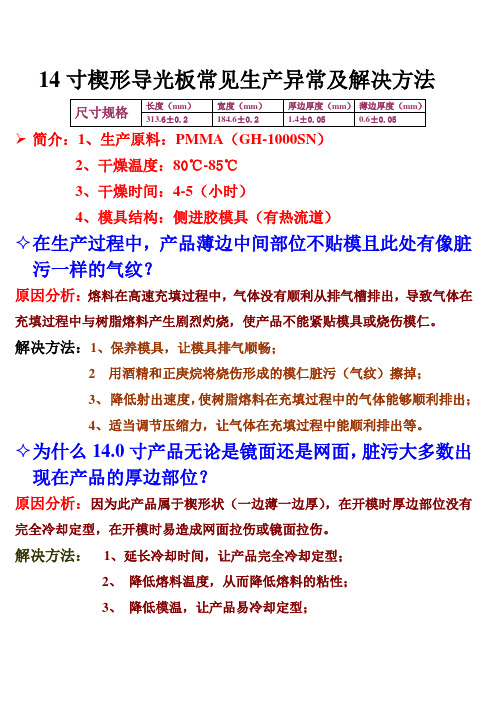
14寸楔形导光板常见生产异常及解决方法
简介:1、生产原料:PMMA(GH-1000SN)
2、干燥温度:80℃-85℃
3、干燥时间:4-5(小时)
4、模具结构:侧进胶模具(有热流道)
✧在生产过程中,产品薄边中间部位不贴模且此处有像脏污一样的气纹?
原因分析:熔料在高速充填过程中,气体没有顺利从排气槽排出,导致气体在充填过程中与树脂熔料产生剧烈灼烧,使产品不能紧贴模具或烧伤模仁。
解决方法:1、保养模具,让模具排气顺畅;
2 用酒精和正庚烷将烧伤形成的模仁脏污(气纹)擦掉;
3、降低射出速度,使树脂熔料在充填过程中的气体能够顺利排出;
4、适当调节压缩力,让气体在充填过程中能顺利排出等。
✧为什么14.0寸产品无论是镜面还是网面,脏污大多数出现在产品的厚边部位?
原因分析:因为此产品属于楔形状(一边薄一边厚),在开模时厚边部位没有完全冷却定型,在开模时易造成网面拉伤或镜面拉伤。
解决方法:1、延长冷却时间,让产品完全冷却定型;
2、降低熔料温度,从而降低熔料的粘性;
3、降低模温,让产品易冷却定型;
4、降低射出速度,从而降低最高射出压力,使产品易脱模;
5、增强模具排气,让气体顺利从模具排气槽排出,避免气体与熔料混乱在一起,产生剧烈的灼烧;
6、加大保压压力,从而加强熔料结晶速度易冷却;
7、降低保压压力,让产品不易贴模过紧而导致取出时拉伤产品;
8、降低注射压力,(如:减小注射速度、提高热流道浇口温度)等。
导光板制造FMEA

PMMA材料对模具的要求与PC材料相差不大,但受自身较差的韧性影响,水口位宜加顶针设计,避免断
PMMA材料注塑螺杆材料实际应用中也多采用38CrMoAlA和9Cr18MoV材质。
网点(微细
沟)成型不
良
透光辉度偏小而出现透光辉度
不良
板状成型品中残留的应力会影响导光板折射率和透光率,会
产生辉度条纹而出现辉度和均匀度不良
残余应力大
处理或组装作业,也会造成辉
度条纹、透过不良
凹陷、翘曲
a)应选用专用螺杆、带单独温控射咀的注塑机;
b)注射温度在塑料树脂不分解的前提下,宜用较高注射温度;
c)注射压力:一般较高,以克服熔料粘度大的缺陷,但压力太高会产生内应力造 成脱模因难和变形;
d)注射速度:在满足充模的情况下, 一般宜低,最好能采用慢-快-慢多级注射;
e)保压时间和成型周期:在满足产品充模,不产生凹陷、气泡的情况下;宜尽量短,以尽量减低熔料在机筒停留时间;
f)螺杆转速和背压:在满足塑化质量的前提下,应尽量低,防止产生解降的可 能;
g)模具温度:制品的冷却好坏,对质量影响极大,所以模温一定要能精确控制其 过程,有可能的话,模温宜高一些好。
韧性影响,水口位宜加顶针设计,避免断水口及粘水口现象。
AlA和9Cr18MoV材质。
在机筒停留时间;可能的话,模温宜高一些好。
学校LED屏幕异常情况应急处理方案
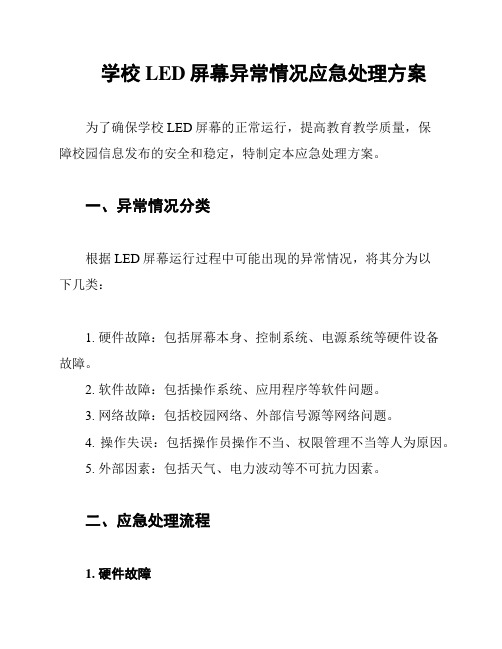
学校LED屏幕异常情况应急处理方案为了确保学校LED屏幕的正常运行,提高教育教学质量,保障校园信息发布的安全和稳定,特制定本应急处理方案。
一、异常情况分类根据LED屏幕运行过程中可能出现的异常情况,将其分为以下几类:1. 硬件故障:包括屏幕本身、控制系统、电源系统等硬件设备故障。
2. 软件故障:包括操作系统、应用程序等软件问题。
3. 网络故障:包括校园网络、外部信号源等网络问题。
4. 操作失误:包括操作员操作不当、权限管理不当等人为原因。
5. 外部因素:包括天气、电力波动等不可抗力因素。
二、应急处理流程1. 硬件故障1.1 检查设备连接:检查屏幕、控制系统、电源等设备连接是否牢固,有无松动现象。
1.2 重启设备:尝试重启出现故障的设备,观察是否恢复正常。
1.3 故障排查:若重启无效,采用专业设备进行故障排查,找出具体故障点。
1.4 维修更换:对故障设备进行维修或更换,确保设备正常运行。
2. 软件故障2.1 重启软件:关闭异常软件,重启后再尝试打开,观察是否恢复正常。
2.2 软件升级:检查是否存在软件版本较低或存在漏洞,升级软件至最新版本。
2.3 故障排查:若重启软件和升级软件后仍存在问题,进行故障排查,找出原因并进行修复。
3. 网络故障3.1 检查网络连接:检查校园网络、外部信号源等连接设备是否正常运行。
3.2 重启网络设备:尝试重启路由器、交换机等网络设备,观察是否恢复正常。
3.3 联系网络管理员:若重启网络设备后仍存在问题,联系网络管理员进行故障排查和修复。
4. 操作失误4.1 及时纠正:对操作失误进行及时纠正,恢复正常使用。
4.2 加强培训:对操作人员进行定期培训,提高操作水平,避免类似失误再次发生。
5. 外部因素5.1 预防措施:针对可能出现的外部因素,提前采取相应的预防措施,如防雷、防雨等。
5.2 应急处理:在外部因素导致LED屏幕异常时,迅速采取措施,减少损失。
三、应急预案1. 建立应急小组:由学校相关部门负责人、技术人员组成应急小组,负责LED屏幕异常情况的应急处理。
背光板与导光板常见异常及对策

刮伤对策
1.检查擦伤站别,加以预防。 2.减少 粘料:固定&不固定
固定粘料为LGP制造过程中因 环境与机器上异常所造成,其 定义为点灯治具检测下呈现 白雾或略有发亮之异常,且每 PCS位置均于同一位置其形状 不固定称之为粘料.
不固定粘料為外界環境及產 品小毛邊脫落造成位置不一 大小不一。
因受机台或环境、材料 污染所造成的,因此异物 定义:为在点灯治具检视 下可发亮但颜色不一,其 形状大小不一致也无一 定之方向性,且于LGP内 或附着于表面无法擦拭 去除者.
异物对策
1.检查模具表面是否生锈,滑块有无挫 伤。
2.检查供料系统是否漏气 3.将产品毛边做无 4.将产品毛边做大使其不易脱落。
定义(Define)离形MARK
离形MARK: 离形MARK又称铍铜氧
化,为LGP成型过程中 因咬花模仁有氧化或 成形条件设计不当所 产生,离形MARK定义 为点灯治具检视下呈 现不规则形状之白雾 或暗影称之为离形 MARK.
MARK对策
调整排气 条件克服
注:无法万全克服
定义(Define)黑点
白雾: 白雾为LGP成型过程
中所造成的不良,将 导光板倾斜一个角度 观察,会有一团白色 雾雾的情形,就称为 白雾。
白 雾
定义(Define)浇口凹陷
浇口凹陷:
浇口凹陷为LGP成型 过程中所造成的,在 于浇口两侧因取出配 合不当所造成的凹陷。
浇口 凹陷
浇口凹陷对策
1.流道抛光 2.顶出调整
黑点: 黑点为LGP成型过程
中因材料碳化及人员 操作疏失所造成,黑 点定义为在点灯治具 检查下LGP内黑色形 状大小不一,但位置 不一.
定义(Define)银条
导光板常见生产异常的原因分析及解决方法((已阅)(注塑导光板)(精)

导光板常见生产异常的原因分析及工艺解决方法作者:田辉以安全生产为已任以成型技术为核心走创新之路解决问题的九大步骤:发掘问题--选定题目--追查原因--分析资料--提出办法--选择对策--草拟行动--成果比较--标准化。
一.划伤现象:指导光板表面出现划伤痕迹。
如图所示:原因分析:1.前制程: a . 在安装模仁时不慎将模仁表面划伤;b . 在处理模具异常时(如:拆滑块保养模具等)不慎将模仁表面划伤;c . 在擦试模仁表面时,因棉花不洁净或手指甲造成的模仁表面划伤等。
2.后制程: a. 设备调试不合理:指产品在进行某一个后制程动作加工时被后制程设备的某个零部件刮伤产品表面;b. 当导光板表面与后制程设备的某部位接触并发生移动摩擦时,因与导光板接触面的不洁净(有粉粒、异物等)导致与导光板表面产生较大的摩擦而至产品表面划伤(如:裁切平台、抛光平台、清洁滚轮等);c. 检验员的作业手法不标准或检验员的粗心大意导致产品表面划伤等。
(如除毛时,除毛刀划伤产品等)。
备注:对于前制程的产品划伤,如果超出SIP检验标准范围,尽量改善轻微一点,便找相关工程判定,看能否签样继续生产,如果实在不能改善或改善轻微,且又不能签样生产,便更换划伤的模仁,重新试模开机生产。
解决方法:1.在安装模仁、擦试模仁或处理模具异常时严格按作业标准谨慎操作;2.对设备不合理的地方或零部件加以改善3.定时对所有与接触产品表面的部位进行清洁;4.加强对员工的教育训练,监督并严格要求作业员按照作业标准进行作业。
二、熔结痕(结合线)现象:由于我们一般采取多段并以慢快慢的方式进行进胶,对于那些高粘度且低流动的塑胶材料(如PC,PMMA),在两段相差很大的射出进胶时,容易在两股熔胶汇合之处不能完全融合,形成一条汇流线,称为熔结痕。
一般熔结痕产生在产品胶口处,因为我们第一段与第二段或三段的射速太慢,如图:原因分析:由于来自不同方向的熔融树脂因开始射出速度较慢部分熔料被冷却,在后面射出的结合处未完全融合而在产品表面产生的一条条分区线。
【原创】导光板毛边(披锋)改善方案

【原创】导光板毛边(披锋)改善方案一、定义导光板产品边缘部位多出的无用部分称为导光板毛边(披锋)。
导光板毛边又可分为分型面毛边和立向毛边两种,分型面毛边与分型面平行,立向毛边则与分型面呈一定角度或者垂直。
立向毛边图分型面毛边图二、立向毛边产生原因及改善对策立向毛边主要是因为模具v-cut模仁或者网点模仁与拼块/水口镶件/锯齿拼块存在大于0.01mm的间隙。
改善对策:模具设计时,尽量避免立向排气,如需开设立向排气,间隙应该控制在0.005mm以内;模具装配时,需将各拼块与模仁装配紧密。
三、分型面毛边产生原因分型面毛边较立向毛边的原因则更加复杂,以下将从三个方面分析:1、成型工艺参数方面锁模力小:成型机锁模后,由于锁模力小导致前模与后模锁闭不紧密,前模与后模存在间隙,在高速高压成型时,熔融树脂从间隙溢出形成毛边(披锋)射出/保压压力大:由于射出/保压压力大,导致成型时型腔压力大,熔融树脂从间隙溢出形成毛边(披锋)计量位置大:计量位置大,导致熔融树脂填充的过于饱满,熔融树脂从间隙溢出形成毛边(披锋)料温高:料温高,用于成型导光板的树脂流动性好粘度低,熔融树脂易从间隙溢出形成毛边(披锋)2、模具方面模具分型面伤痕、异物、平行度差,平行排气间隙大:成型机合模启高压后,模具前模与后模无法合紧存在间隙,熔融树脂从间隙溢出形成毛边(披锋)3、注塑机方面注塑机模具安装面异物、铁锈:使模具前模与后模无法紧密贴合,成型时熔融树脂从间隙溢出形成毛边(披锋)改善对策:模具安装时,先将注塑机模具安装面用洗模水粘无尘纸擦拭,装好后擦拭分型面保证清洁,采用合适的锁模力、温度、压力等成形参数,若通过以上对策仍无法改善,就应当检查模具排气间隙,保证模具既能排气顺畅又不产生毛边,针对导光板模具的分型面排气间隙应控制在0.01mm以内且可以开设分段排气,浇口侧至尾部的排气逐渐减小(0.005mm→0.01mm)四、经典案例问题点:导光板分型面毛边,难加工,批退率100%导光板毛边3D显微结构图原因分析:排查注塑机模具安装面清洁无异物、脏污,且调试工艺参数对导光板毛边无任何改变,故将改善聚焦于模具,检查模具分型面无伤痕、异物、平行度差等异常,初步诊断为网点模仁拼块与v-cut模仁拼块间隙大,熔融树脂从拼块间隙中溢出,导致导光板两侧分型面毛边。
导光板导光质量差原因

导光板导光质量差原因
1.导光板材料:
①导光板尺寸大小跟实际需要有出入
②导光板板材质量差。
三劢光电选用进口导光板质量绝对没问题。
③导光板存放时室内温度不要超过25°C左右,导光板与普通塑料具有相同的膨胀系数,温度变化引起的伸缩;湿度的变化也会引起导光板的伸缩,安装和存放导光板时室内湿度应保持在50-60%RH
④成品导光板打包之前没有过一层PE保护膜,很容易刮花。
⑤反光纸和导光板没有紧密,才会出现波皱状亮带。
2.激光技术:
①激光导光板制作之前需要CAD文件,若CAD文件处理不好也会影响
②导光板激光打点均匀度调较差
③导光板激光打点亮度调整低
3.影响灯珠质量:
①包装保护不完善,造成运输过程中灯珠受到撞击而损坏。
②焊接点有虚焊现象,运输过程中的振动造成焊点脱落。
③焊锡量少,焊点容易脱落。
④焊锡质量不好,LED柔性灯条在弯折过程中焊点容易产生脆裂、脱落现象。
⑤安装时弯折角度过大,造成LED柔性灯条焊点与铜箔分离而导致不亮。
⑥安装时过度挤压产品,导致LED柔性灯条芯片受损或者是焊点变形脱落而不亮。
⑦线路板阻焊层过厚,焊接时焊锡和线路板不能完全融合在一起,也是一种虚焊现象。
⑧在安装时不能扭曲,如果扭曲就会造成LED柔性灯条的焊点脱落而导致不亮。
[1]。
导光板设备安全技术措施
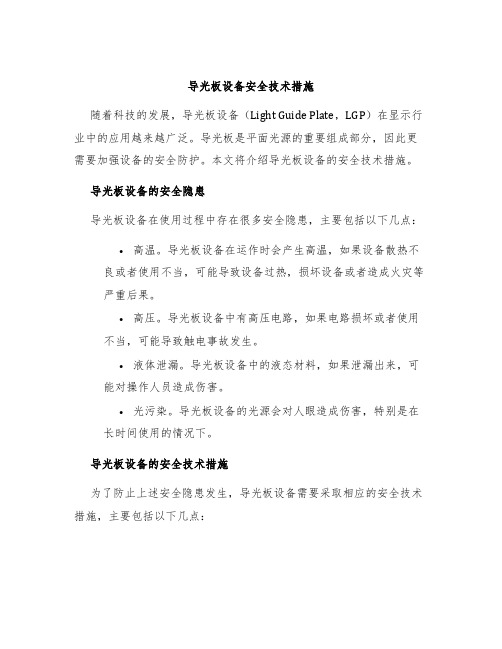
导光板设备安全技术措施随着科技的发展,导光板设备(Light Guide Plate,LGP)在显示行业中的应用越来越广泛。
导光板是平面光源的重要组成部分,因此更需要加强设备的安全防护。
本文将介绍导光板设备的安全技术措施。
导光板设备的安全隐患导光板设备在使用过程中存在很多安全隐患,主要包括以下几点:•高温。
导光板设备在运作时会产生高温,如果设备散热不良或者使用不当,可能导致设备过热,损坏设备或者造成火灾等严重后果。
•高压。
导光板设备中有高压电路,如果电路损坏或者使用不当,可能导致触电事故发生。
•液体泄漏。
导光板设备中的液态材料,如果泄漏出来,可能对操作人员造成伤害。
•光污染。
导光板设备的光源会对人眼造成伤害,特别是在长时间使用的情况下。
导光板设备的安全技术措施为了防止上述安全隐患发生,导光板设备需要采取相应的安全技术措施,主要包括以下几点:设备的安全保护装置设备的安全保护装置是指在设备中安装相应的保护措施,使得在设备工作过程中遇到问题时,能够尽快切断电源或者采取其他措施保护设备和人员的安全。
例如,安装过载保护装置、漏电保护装置等,当设备出现故障时,这些装置会立即起作用,保护设备和人员的安全。
设备的防火措施导光板设备可能会因为过热、电路短路等因素导致火灾,因此设备的防火措施显得尤为重要。
常见的防火措施包括:•使用阻燃材料。
导光板设备应该使用阻燃材料,这样在发生火灾时能够有效控制火势。
•安装灭火装置。
在设备中设置灭火装置(例如气体灭火装置),在发生火灾时能够尽快进行灭火,有效地遏制火势。
•加严设备维护。
定期检查设备散热装置、电路等,保证设备的良好运行状态。
设备的再生资源利用导光板设备中使用的一些材料可能对环境造成损害,为此,设备要加强再生资源的利用,降低资源消耗,如在生产过程中选择可循环的材料并进行回收利用;在旧设备处理时选择环保的处理方式等。
操作人员的安全教育除了上述针对导光板设备的安全措施,安全教育同样不可或缺。
导光板相关技术处理问题

导光板处理现存在的主要问题及今后的改善方向现阶段我司网点加工的方式LED编码1 腐蚀:与益永达合作,每天晚派车来我司取模仁,第二天早送回我司,周期一天2 撞击:一天能撞好1-2颗模仁,比较慢的方法,补充某些高光学效果要求的产品3 镭射:无合作商,加工周期3天以上,只能作为评估,无法满足样品交期由于导光板问题导致样品延误的主要问题点1 均匀性不够:典型前面亮,后面亮,对单颗LED光源亮2 外观差:典型光源花如光柱,黑白块,黑白点3 锯齿问题:主要是模房加工的锯齿与图面要求不符合,如对平位的锯齿平位偏大偏小,角度过小等,容易出现光柱;锯齿毛边也是一个不容忽视的问题5 咬花加工不对:腐蚀深度不对、暗影,撞击大小不对6模仁磨面的处理问题:前后模仁的磨面粗细程度不在要求的范围,对于磨面要求抛光的,由于手工抛光,造成面内厚度不一,在腐蚀易出现黑白块,在出光面(后模)易出现黑白点7 亮度不够或过高或色度不对8 材料搭配不当造成的效果NG:如扩散用错、上下Deff角度裁错9 配模仁厚度浪费时间:备用的模仁不够数量或者无备用模仁,或厚度不对,需配厚度,在配厚度和修模时常有碰伤咬花的事件发生10修模不及时:无法及时改善现阶段的处理及各问题点的管控状况1图面控制:在给模房下达导光板开模图时,吴邦和我这边会根据审查图面用的何种锯齿,楔形角度是否方便光学处理。
但是有时开模单下的突然会导致我们这边没看到图纸或完看到图纸而模具课那边已经按开模图档割好了锯齿镶件,造成后续网点处理困难或要求模房不得不重新换锯齿,费时费力2网点设计:我根据图面结构确定布点(我完成——吴邦审核),咬花面出光面做何种磨面(我知会赖星,赖星负责去模房与模具师傅沟通,并审视磨面是否合乎要求,我在闲时也去)。
现在模房师傅做磨面是用120号砂轮,可是磨面的粗细程度很难给出统一的判断标准,无法量法,只能凭眼睛观察,很人为化,需要磨床师傅和审查磨面的赖星密切配合。
导光板等透明塑料制件变色、发黄
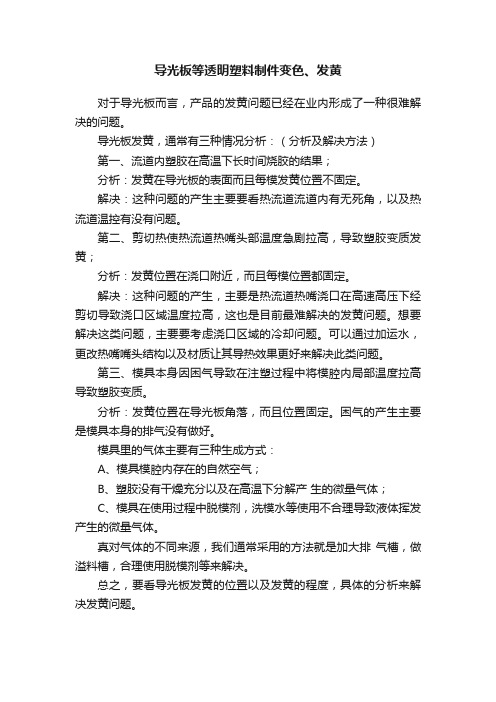
导光板等透明塑料制件变色、发黄
对于导光板而言,产品的发黄问题已经在业内形成了一种很难解决的问题。
导光板发黄,通常有三种情况分析:(分析及解决方法)
第一、流道内塑胶在高温下长时间烧胶的结果;
分析:发黄在导光板的表面而且每模发黄位置不固定。
解决:这种问题的产生主要要看热流道流道内有无死角,以及热流道温控有没有问题。
第二、剪切热使热流道热嘴头部温度急剧拉高,导致塑胶变质发黄;
分析:发黄位置在浇口附近,而且每模位置都固定。
解决:这种问题的产生,主要是热流道热嘴浇口在高速高压下经剪切导致浇口区域温度拉高,这也是目前最难解决的发黄问题。
想要解决这类问题,主要要考虑浇口区域的冷却问题。
可以通过加运水,更改热嘴嘴头结构以及材质让其导热效果更好来解决此类问题。
第三、模具本身因困气导致在注塑过程中将模腔内局部温度拉高导致塑胶变质。
分析:发黄位置在导光板角落,而且位置固定。
困气的产生主要是模具本身的排气没有做好。
模具里的气体主要有三种生成方式:
A、模具模腔内存在的自然空气;
B、塑胶没有干燥充分以及在高温下分解产生的微量气体;
C、模具在使用过程中脱模剂,洗模水等使用不合理导致液体挥发产生的微量气体。
真对气体的不同来源,我们通常采用的方法就是加大排气槽,做溢料槽,合理使用脱模剂等来解决。
总之,要看导光板发黄的位置以及发黄的程度,具体的分析来解决发黄问题。
导光板生产过程中常见问题

一.划伤现象:指导光板表面出现划伤痕迹。
如图所示:二、熔结痕(结合线)现象:在两段相差很大的射出进胶时,容易在两股熔胶汇合之处不能完全融合,形成一条汇流线,称为熔结痕。
一般熔结痕产生在产品胶口处,如图:三、暗影/白斑现象:在检验治具的灯光下,产品某处或多处呈现暗区或发白的现象称为暗影/白斑。
如图所示:四、冷料现象:在产品胶口(料头)附近的表面上有一块或点状的痕迹。
如图:五、产品尺寸不稳定(NG)现象:在射出成型出来的制品,未达到制品尺寸的规格,导致尺寸偏大或偏小。
六、气泡现象:在检验治具的灯光下,从产品表面看上去在产品内部有一个或多个体积较少的孔隙。
如图:七、黑点现象:在制品内部的某部位存在一个或多个黑色的小点。
如图:八、白点现象:在制品的内部存在一个或多个白色的小点。
如图:九、变形(应力)现象:产品经过成型机成型出来后,产品平面度的某部位发生不同方向的翘曲,称为变形。
十、粘模(拉模)现象:产品在冷却OK后,在开模瞬间因贴模过紧导致拉网点或机械手取出产品时因贴模过紧而拉伤镜面,这样在检验治具的灯光下可清楚看到像划伤、点状或块状且发亮的痕迹,严重的可将产品拉爆。
十一、异物(脏污)现象:包括导光板吸附粉尘、手印、油污、水渍等脏物,影响产品外观及光学效果。
十二、缩水现象:由于模具排气不足,注塑压力、速度不够或注塑机不稳定等原因导致的产品成型不饱满。
十三、批锋现象:由于模具配合不到位或注塑压力过大导致的产品多胶。
十四、光学NG现象:1、导光板组模后在光学仪器的测试下辉度不均匀。
单屏单彩均匀度要求达到80%以上。
2、由成型工艺、加工工艺引起的导光板组模点亮后出现亮点、黑点、发黄等。
3、由模具制作及蚀刻网点不合理引起的导光板组模点亮后出现射线、亮区、暗区。
十四、装配NG现象:导光板结构不对、尺寸不合格与胶框、光学部材装配达不到要求,影响背光模组的装配及光学效果。
印刷导光板品质异常的原因及解决方法

印刷导光板生产品质异常的原因及解决方法舒畅(创维集团研发总部模组研究所)【摘要】:导光板的主要功能在于使光源发出的光线能均匀分布于整体的背光模组,其性能优劣决定出射光源的亮度效率及分布上均一性的表现。
本文从印刷式导光板制程中常出现的生产异常问题方面讨论导光板的品质的解决办法。
【关键词】网点残缺异物刮痕网点偏移网点发白暗影划伤一、前言丝网印刷式导光板是将自行配制的具有高反射和折射作用的丝印油墨在透明压克力板表面印上有规律性的导光网点,该网点便会将从边上照射进来的线性光向平面转换,变成均匀的平面光。
由于导光板对整个背光源的性能影响重大,所以必须确保如下品质:1、不能沾有异物:导光板一旦沾上异物,就会出现亮度不均匀、斑点和黑点等品质问题。
2、不能有气泡、翘曲:导光板中的气泡是直接产生亮度不均匀的原因,尤其是对表面有微结构的导光板影响更大。
导光板的翘曲不良会直接影响反射面的印刷和组装。
3、残余应力不能太大:由于注塑件内部的残余应力不仅引起翘曲不良,还会受热变形或者印刷时容易产生裂痕,所以必须控制到最小限度。
另外,注塑件内外部冷却固化速度不一致时会产生光学偏差,容易产生问题。
4、重量和尺寸要稳定:在严抓注塑件品质的同时,要保持注塑产品的重量和尺寸处于高度稳定,这就要通过以注塑机、模具、模具温调机、材料和材料干燥机形成的注塑系统来实现。
导光板在生产过程中容易出现划伤、暗影、白团、尺寸不稳定、变形等不良。
这些问题需结合制程情况加以解决。
二、印刷导光板生产常见问题及解决办法2.1网点残缺原因分析:1、赃物附在板材上没有清洁干净2、印刷手操作滚轮不当3、粘尘纸粘性大低4、机台周围5S混乱解决方法1、在进料这一环节加设离子风枪,用风枪清洁2、加强人员培训,掌握滚轮的正确使用方法,定时更换粘尘纸3、选用黏度适中的滚轮4、保持机台周围5S干净5、印刷人员也要定时定量抽检导光板,以免看板人员漏检2.2异物产生原因:1、网版未清洗干净2、重工清洗板没有洗干净,再次印刷3、没有带指套直接触摸导光板如光面或镜面造成4、清洗网版离子风枪清洁时造成溶剂飞溅到板材入光面,造成板材腐蚀5、滚轮上粘有溶剂,很多新近员工在清洗网版时,都有把溶剂滴到粘尘纸或滚轮上,这样印刷时就会造成导光板上多处异物。
LCD-48s3A导光板故障处理方法
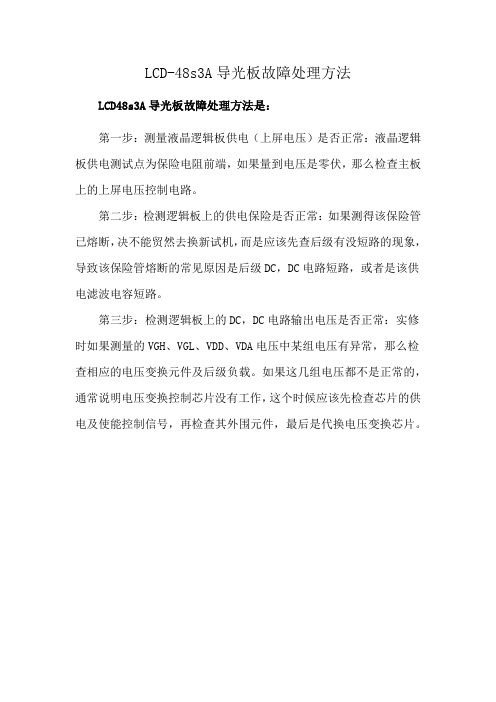
LCD-48s3A导光板故障处理方法
LCD48s3A导光板故障处理方法是:
第一步:测量液晶逻辑板供电(上屏电压)是否正常:液晶逻辑板供电测试点为保险电阻前端,如果量到电压是零伏,那么检查主板上的上屏电压控制电路。
第二步:检测逻辑板上的供电保险是否正常:如果测得该保险管已熔断,决不能贸然去换新试机,而是应该先查后级有没短路的现象,导致该保险管熔断的常见原因是后级DC,DC电路短路,或者是该供电滤波电容短路。
第三步:检测逻辑板上的DC,DC电路输出电压是否正常:实修时如果测量的VGH、VGL、VDD、VDA电压中某组电压有异常,那么检查相应的电压变换元件及后级负载。
如果这几组电压都不是正常的,通常说明电压变换控制芯片没有工作,这个时候应该先检查芯片的供电及使能控制信号,再检查其外围元件,最后是代换电压变换芯片。
LED导光板热流道讲解热流道系统中制品出现问题的解决方法
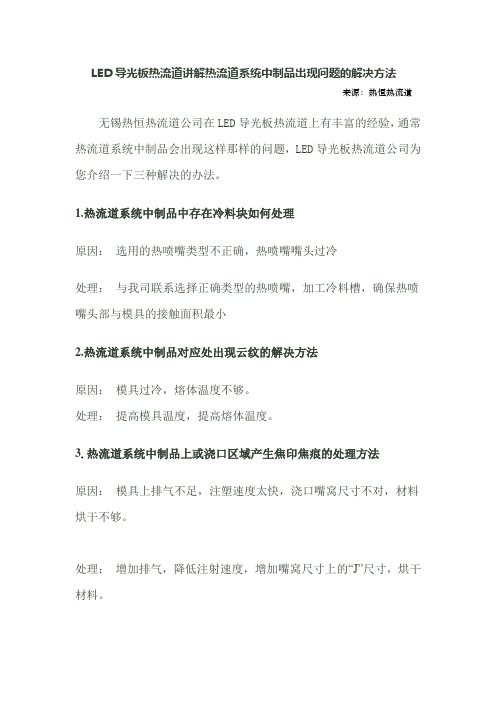
LED导光板热流道讲解热流道系统中制品出现问题的解决方法
来源:热恒热流道无锡热恒热流道公司在LED导光板热流道上有丰富的经验,通常热流道系统中制品会出现这样那样的问题,LED导光板热流道公司为您介绍一下三种解决的办法。
1.热流道系统中制品中存在冷料块如何处理
原因:选用的热喷嘴类型不正确,热喷嘴嘴头过冷
处理:与我司联系选择正确类型的热喷嘴,加工冷料槽,确保热喷嘴头部与模具的接触面积最小
2.热流道系统中制品对应处出现云纹的解决方法
原因:模具过冷,熔体温度不够。
处理:提高模具温度,提高熔体温度。
3.热流道系统中制品上或浇口区域产生焦印焦痕的处理方法
原因:模具上排气不足,注塑速度太快,浇口嘴窝尺寸不对,材料烘干不够。
处理:增加排气,降低注射速度,增加嘴窝尺寸上的“J”尺寸,烘干材料。
导光板常见生产异常的原因研究分析及解决方法

导光板常见生产异常的原因分析及解决方法————————————————————————————————作者:————————————————————————————————日期:导光板常见生产异常的原因分析及工艺解决方法解决问题的九大步骤:发掘问题--选定题目--追查原因--分析资料--提出办法--选择对策--草拟行动--成果比较--标准化。
一.划伤现象:指导光板表面出现划伤痕迹。
如图所示:原因分析:1.前制程:a . 在安装模仁时不慎将模仁表面划伤;b . 在处理模具异常时(如:拆滑块保养模具等)不慎将模仁表面划伤;c . 在擦试模仁表面时,因棉花不洁净或手指甲造成的模仁表面划伤等。
2.后制程: a. 设备调试不合理:指产品在进行某一个后制程动作加工时被后制程设备的某个零部件刮伤产品表面;b. 当导光板表面与后制程设备的某部位接触并发生移动摩擦时,因与导光板接触面的不洁净(有粉粒、异物等)导致与导光板表面产生较大的摩擦而至产品表面划伤(如:裁切平台、抛光平台、清洁滚轮等);c. 检验员的作业手法不标准或检验员的粗心大意导致产品表面划伤等。
(如除毛时,除毛刀划伤产品等)。
备注:对于前制程的产品划伤,如果超出SIP检验标准范围,尽量改善轻微一点,便找相关工程判定,看能否签样继续生产,如果实在不能改善或改善轻微,且又不能签样生产,便更换划伤的模仁,重新试模开机生产。
解决方法:1.在安装模仁、擦试模仁或处理模具异常时严格按作业标准谨慎操作;2.对设备不合理的地方或零部件加以改善3.定时对所有与接触产品表面的部位进行清洁;4.加强对员工的教育训练,监督并严格要求作业员按照作业标准进行作业。
二、熔结痕(结合线)现象:由于我们一般采取多段并以慢快慢的方式进行进胶,对于那些高粘度且低流动的塑胶材料(如PC,PMMA),在两段相差很大的射出进胶时,容易在两股熔胶汇合之处不能完全融合,形成一条汇流线,称为熔结痕。
导光板印刷不良及解决方案

导光板印刷不良及解决方案1.白花点现象:2个或2个以上旳网点粘连,导致局部位置发白,在盖扩散片旳状态下比其她位置都亮。
因素:异物粘附(线状异物)解决方案:1.用T-311胶带将粘在丝网下面异物粘去;然后印刷1-3片白板后再印1片良品,观测白花与否粘去,并观测与否有斑痕,如果没有,继续印刷,有责清洗丝网。
2.2个或2个以上清洗丝网修理:用竹签将多余部分划去。
2.白点现象:单个网点中间有白色旳小颗粒,盖扩散片后成发亮旳状态。
因素:墨水点吸附了颗粒状旳异物。
1.原资材印刷面异物偏多2.作业者衣服上粘连旳异物较多,特别袖口,静电吸附。
解决方案:1.原板材进行确认后使用;2.作业者生产前用清洁滚筒清洁衣物,特别袖口;3.按照规定清洗丝网。
修理:用竹签挑去异物,必要时刮去网点,然后用针修补,修理后盖扩散片检查与否修补过度,然后用无尘布沾清洗剂擦洗。
3.异物现象:墨水点异物吸附。
涉及颗粒状,片状,线状,通过干燥后和墨水点粘连在一起,位置不固定。
因素:丝网摩擦产生静电解决方案: 1. 设备周边环境清洁; 2. 使用去静电酒精清洁印刷机台面。
修理:竹签刮去异物。
4. 划伤现象:印刷后旳导光板在盖扩散片旳状态下非印刷面有很短旳丝状亮线条或小亮点,一般固定。
因素:1.原材存在划伤;2.作业员手法力度过大;3.检查人员检查时划伤。
解决方案:1. 原材检查后使用2. 检查者变化作业方式,避免异物划伤;3. 检查员注意动作,避免碰桌面;4. 检查员水平盖扩散片,避免边角划伤板材。
修理:用比较钝旳竹签蘸取清洗剂稍微用力刮平划伤,注意力度。
5.横向斑痕现象: 从左至右贯穿导光板横向线状斑痕,斑痕区域较暗,有发黑旳感觉。
因素:1. 网距偏低,高3毫米左右;2. 丝网未及时清洗;3. 导光板前后高度不一致;4. 椭圆斑痕:刮胶压力不均匀;5. 对光部产生旳横向斑痕:刮胶压力过大;6. 清洗周期也会使导光板产生横向斑痕;7. 机头移动速度及离版器旳上升速度不一致也会产生横向斑痕;8. 丝网自身固有;9. 框架或垫片有残留旳墨水,干燥后形成突起。
- 1、下载文档前请自行甄别文档内容的完整性,平台不提供额外的编辑、内容补充、找答案等附加服务。
- 2、"仅部分预览"的文档,不可在线预览部分如存在完整性等问题,可反馈申请退款(可完整预览的文档不适用该条件!)。
- 3、如文档侵犯您的权益,请联系客服反馈,我们会尽快为您处理(人工客服工作时间:9:00-18:30)。
导光板常见生产异常的原因分析及工艺解决方法解决问题的九大步骤:发掘问题--选定题目--追查原因--分析资料--提出办法--选择对策--草拟行动--成果比较--标准化。
一.划伤现象:指导光板表面出现划伤痕迹。
如图所示:原因分析:1.前制程:a . 在安装模仁时不慎将模仁表面划伤;b . 在处理模具异常时(如:拆滑块保养模具等)不慎将模仁表面划伤;c . 在擦试模仁表面时,因棉花不洁净或手指甲造成的模仁表面划伤等。
2.后制程: a. 设备调试不合理:指产品在进行某一个后制程动作加工时被后制程设备的某个零部件刮伤产品表面;b. 当导光板表面与后制程设备的某部位接触并发生移动摩擦时,因与导光板接触面的不洁净(有粉粒、异物等)导致与导光板表面产生较大的摩擦而至产品表面划伤(如:裁切平台、抛光平台、清洁滚轮等);c. 检验员的作业手法不标准或检验员的粗心大意导致产品表面划伤等。
(如除毛时,除毛刀划伤产品等)。
备注:对于前制程的产品划伤,如果超出SIP检验标准范围,尽量改善轻微一点,便找相关工程判定,看能否签样继续生产,如果实在不能改善或改善轻微,且又不能签样生产,便更换划伤的模仁,重新试模开机生产。
解决方法:1.在安装模仁、擦试模仁或处理模具异常时严格按作业标准谨慎操作;2.对设备不合理的地方或零部件加以改善3.定时对所有与接触产品表面的部位进行清洁;4.加强对员工的教育训练,监督并严格要求作业员按照作业标准进行作业。
二、熔结痕(结合线)现象:由于我们一般采取多段并以慢快慢的方式进行进胶,对于那些高粘度且低流动的塑胶材料(如PC,PMMA),在两段相差很大的射出进胶时,容易在两股熔胶汇合之处不能完全融合,形成一条汇流线,称为熔结痕。
一般熔结痕产生在产品胶口处,因为我们第一段与第二段或三段的射速太慢,如图:原因分析:由于来自不同方向的熔融树脂因开始射出速度较慢部分熔料被冷却,在后面射出的结合处未完全融合而在产品表面产生的一条条分区线。
解决方法:1.增加树脂熔料的流动性(如:提高料温、模温、背压等);2.提高注射速度与压力,使得各汇胶处快速熔合;3.增加模具排气,使得熔料进胶顺畅;4.将螺杆后松退距离增大(原4mm加大至6mm),使得注射压力加大;5.进行原料烘烤时,一定要按照此原料的烘烤标准作业,以将原料彻底烘好,达到成型要求。
6.用熔剂将有或经常出理熔结线处的镜面模仁进行擦试或抛光处理,使得模仁表面光滑,熔料易流动;(推荐用:金刚石喷雾抛磨剂(用0.5mm规格))。
7.改变射出位置,将熔结痕移动到不影响产品外观部位(比如:放慢射速且适当调结射出位置,将熔结线控制在冷料井里面);8.降低热流道热嘴(浇口)温度,使得充填时,模具型腔压力增大,而压实产品;9.适当降低锁模力,有利天气体顺利排出,达到熔料进胶顺畅;10.将热流道温度升高,防止熔胶冷却等。
三、暗影/白斑现象:在检验治具的灯光下,产品某处或多处呈现暗区或发白的现象称为暗影/白斑。
如图所示:原因分析:1. 可能是加热筒(螺杆)里面的熔料中混有较多的气体没有被排出,在高速充模的情况下较多的气体难以完全排出,在模具型腔内的某部分产生剧烈灼烧,将产品烧黑而形成的暗区;2 . 为了防止拉丝过长,我们经常将螺杆松退距离设置过大与产品料头彻底断开,而在这之间就形成一段空间,螺杆在计量时,由于转速的原因,熔料会逆流一点至空隙处而易被冷却,在高速充模时,如果这部分被冷却的熔料在高速充模的情况下被带入模具型腔,很难与后面进入的熔料完全融合,也就是说这部分冷却的熔料被后面熔料包住而形成的一块暗区等。
解决方法:1.改变射出位置,尽量将已被冷却的熔料控制在冷料井(穴)里面;2.减少射出速度、压力,有利于气体顺利排出;3.加大射出速度、压力,有利于半冷却的熔料能够完全与后面的流体融合;4.降低熔料温度、螺杆转速,增大背压,减少气体的存在;5.适当调节热流道的温度,防止熔料冷却或在充模时发生湍流现象;6.增加模具排气,使得熔料在充填过程中模具型腔的气体能够顺利排出;7.检查所烘烤的原料是否已烤好,烤料时严格按照作业标准书作业;8.降低锁模力,有利于在充填时模具型腔的气体能够顺利排出;9.增大或减少注射量,防止因充模过饱或不足,在开模时导致的拉网点或不贴模而造成的暗影或白斑;10.用化学品或相关溶剂对镜面或网点面进行擦试,防止因模仁有脏污而导致拉模而造成的暗影或白斑;11.延长或缩短保压时间、增大或减少保压压力,使产品贴模顺畅而不至拉模现象等。
四、冷料现象:在产品胶口(料头)附近的表面上有一块或点状的痕迹。
如图:原因分析:1. 螺杆端部或热流道附近熔料温差较大至熔料冷却并成为固态,在高速充模时这部分已冷却的熔料被带入模具型腔,在制品表面不能完全融合而留下的点状或线状的痕迹。
2 .塑胶原料在塑化时,塑胶原料未被完全融化,在熔体内存在固体,被充入模具型腔不能完全融合而在制品表面形成凹点等。
解决方法:1.升高热流道温度;2.适当调节熔料温度、背压,达到塑胶原料塑化的基本要求(使螺杆熔料不分解、内存气体少、完全融化);3.缩短螺杆后松退距离、减少松退速度,防止因螺杆松退距离过大导致更多的塑胶逆流被冷却而充入模具型腔;4.适当调节射出速度与位置,尽量将冷料控制在制品的冷料井(穴)中等。
五、产品尺寸不稳定(NG)现象:在射出成型出来的制品,未达到制品尺寸的规格,导致尺寸偏大或偏小。
原因分析:1. 对于一模几穴的产品,由于模具的设计不精,导致在充模过程中模具型腔进胶不均,有的进胶快,有的进胶慢,进胶快的则饱,慢则反之;2 . 成型机的精度太低,在成型过程中,射压不稳定等。
解决方法:1.合理开设模具排气,使模具各型腔在充填时进胶一致;2.对于生产精密的制品,尽量选择精度较高的成型机,以便在成型过程中射压的稳定性;3.对模具增设除导柱和导套以外的其他辅助定位装置,以增强开合模精度;4.适当调节射出速度、位置与压力,防止塑胶熔料在充填时形成湍流现象;5.提高塑化温度、背压,提高模温,增强塑胶熔料的流动性;6.降低锁模力,增强模具进胶顺畅;7.检查塑胶原料的干燥程度是否达到成型标准等8.加大保压压力和延长保压时间,弥补塑胶熔料因热胀冷缩而缺的熔料不足等。
六、气泡现象:在检验治具的灯光下,从产品表面看上去在产品内部有一个或多个体积较少的孔隙。
如图:原因分析:在射出成型过程中,由于大量的气体没有顺利地从模具排气槽排出,便混入熔料中而形成的气泡等。
解决方法:1.增强模具排气,使充填过程中气体能够顺利排出;2.在塑化过程中降低熔料温度、螺杆转速,提高背压,防止产生过多的气体混入熔料中;3.降低射出速度、射出压力,让气体顺利排出;4.降低或升高模温;5.升高模具热流道浇口(热嘴)温度,减小在充填时模具型腔压力;6.提高保压压力和延长保压时间,以便残余气体排出,使产品压得更加结实;7.检查原料是否干燥OK,以便在塑化时产生更多的气体;8.擦试模仁且对镜面模仁进行抛光处理,使其更加光滑;9.适当降低锁模力,有利于气体顺利排出;10.如果成型机有压缩功能,尽量将其用上,以便在射出过程中更好地排出气体等。
七、黑点现象:在制品内部的某部位存在一个或多个黑色的小点。
如图:原因分析: 1 .塑胶原料在塑化过程中因背压、温度、转速过高,导致熔料分解碳化;2 .在高速充填过程中,模具型腔的气体不能顺利排出,聚集在某个角落与熔料产生剧烈的灼烧而烧焦熔料等。
解决方法:1.减少熔料在料筒内停留的时间,避免熔料在料筒内停留时间过长而分解碳化(如:缩短成型周期)等;2.降低射出速度、压力,使模具型腔气体能够顺利排出,避免气体在压力的作用下与熔料产生剧烈的灼烧而灼焦熔料;3.增强模具排气,让气体在充填时能够顺利排出;4.检查成型机周边环境是否达标;5.拆滑块保养模具;6.检查黑点是否是后制程所造成(如我们需要用到的载盘,而载盘上黑色导条是否有小黑粉粒,如果有黑色小粉粒,在静电的吸咐之下而产生擦不掉的黑点);7.检查原料的干燥度与洁净度;8.检查螺杆是否碳化而导致黑点的产生;9.确认在换原料生产时,是否将螺杆原有的原料清干净(如ABS改PMMA)等。
八、白点现象:在制品的内部存在一个或多个白色的小点。
如图:原因分析:1.在塑化过程中,在熔料温度过低,背压过小,转速过快,未能将塑胶料完全均匀的熔化,在塑胶熔料中存在着固体;2.塑胶原料不干净,混有白色的杂质;3.成型机周边环境受到污染,空气中粉尘较重。
4.模仁的过于粗糙,导致在取出产品时拉伤拉品而产生的白点等。
解决方法:1.提高背压,降低螺杆转速,使塑胶原料达到塑化要求;2.擦试模仁,使其易脱模,避免在取出时导致产品拉伤而造成的白点;3.确认白点是否是前制程所造成,(如:产品在制程处理过程中因其他物品导致产品压伤而产生的白点(后制程压出来的白点);4.确认原料是否干净以及成型周边的环境是否达标;5.降低锁模力、射出速度、压力,有利于气体的顺利排出,避免气体混入熔料中在压力的作用下产生剧烈的灼烧而使熔料产生分解。
6.增强模具排气;7.放慢第一段开模速度,防止拉网点等。
8.减慢机械手取出速度,防止因镜面过于粗糙导致拉伤产品而产生的白点等。