自动螺丝刀的设计
螺丝刀设计分析报告
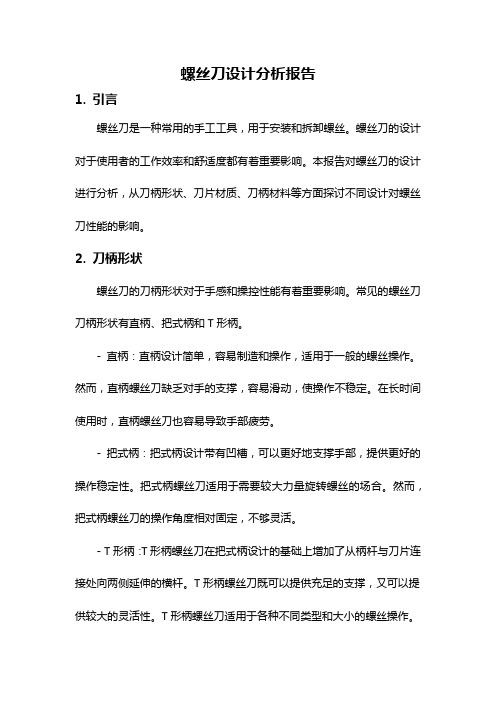
螺丝刀设计分析报告1. 引言螺丝刀是一种常用的手工工具,用于安装和拆卸螺丝。
螺丝刀的设计对于使用者的工作效率和舒适度都有着重要影响。
本报告对螺丝刀的设计进行分析,从刀柄形状、刀片材质、刀柄材料等方面探讨不同设计对螺丝刀性能的影响。
2. 刀柄形状螺丝刀的刀柄形状对于手感和操控性能有着重要影响。
常见的螺丝刀刀柄形状有直柄、把式柄和T形柄。
- 直柄:直柄设计简单,容易制造和操作,适用于一般的螺丝操作。
然而,直柄螺丝刀缺乏对手的支撑,容易滑动,使操作不稳定。
在长时间使用时,直柄螺丝刀也容易导致手部疲劳。
- 把式柄:把式柄设计带有凹槽,可以更好地支撑手部,提供更好的操作稳定性。
把式柄螺丝刀适用于需要较大力量旋转螺丝的场合。
然而,把式柄螺丝刀的操作角度相对固定,不够灵活。
- T形柄:T形柄螺丝刀在把式柄设计的基础上增加了从柄杆与刀片连接处向两侧延伸的横杆。
T形柄螺丝刀既可以提供充足的支撑,又可以提供较大的灵活性。
T形柄螺丝刀适用于各种不同类型和大小的螺丝操作。
3. 刀片材质螺丝刀的刀片材质直接影响其耐用性和操作效果。
常见的刀片材质有碳钢、合金钢和不锈钢。
- 碳钢:碳钢刀片价格低廉,易于加工,适合一般家用。
然而,碳钢刀片容易生锈,需要定期维护,并且容易变形或破损。
- 合金钢:合金钢刀片相对碳钢更为耐用,具有较高的硬度和耐磨性。
合金钢刀片在使用中能够较好地保持刀片形状,不易变形,能够满足一般工作需求。
- 不锈钢:不锈钢刀片具有优异的抗氧化和抗腐蚀性能,能够长时间保持亮度和锋利度,不需要经常保养。
不锈钢刀片也容易加工,适合高端用户需求。
4. 刀柄材料螺丝刀的刀柄材料对于手感和使用寿命有较大影响。
常见的刀柄材料有塑料、橡胶和木柄。
- 塑料:塑料刀柄具有轻量、坚固和经济的特点,广泛应用于大多数螺丝刀。
然而,塑料刀柄材料耐用性相对较低,容易磨损或破裂,特别是在高负荷操作中。
- 橡胶:橡胶刀柄具有良好的防滑性能,可以提供更好的手感和操作稳定性。
5三轴自动拧紧机故障维修方案设计

湖南高等职业技术学校毕业设计题目:三轴自动拧紧机故障维修方案设计学生姓名指导教师专业班级目录1.任务背景 (1)1.1设备简介 (1)1.2设备故障现象 (1)2. 设备故障原因分析 (2)2.1设备工作原理 (2)2.2故障原因分析 (2)3.安全操作规程 (2)3.1工作前要求 (2)3.2工作中要求 (3)3.3工作后要求 (3)4.诊断流程方案设计及实施 (4)4.1设备故障诊断流程方案 (4)4.2维修方案实施 (4)5.修复验证 (7)5.1修复方法 (7)5.2修复后验证 (10)6.总结 (11)参考文献 (12)三轴自动拧紧机故障维修方案设计指导教师:1.任务背景1.1设备简介螺栓拧紧机应用非常广泛,大多被使用在产品组装装配、电子、电器、仪表装配等行业,汽车行业的应用尤为广泛,比如轮胎拧紧机。
本次维修的螺栓拧紧机是三轴自动拧紧机,额定功率为10kw,额定电流为32A.[1] 下方1.2设备故障现象拧紧机二号枪头找不着帽,设备因拧紧不合格报警,如图1-1所示图1-12.设备故障原因分析2.1设备工作原理来自机头扭矩传感器的反馈电信号输给上位机,上位机根据反馈差值控制伺服电机,带动减速机,再连接到电动螺丝刀进行拧紧工作,通过传感器反馈信号至上位机形成闭环控制,达到设定的扭矩要求。
上位控制系统+伺服电机+电动螺丝刀+扭矩传感器=伺服拧紧机。
伺服电机作为动力源,输出动力减速器;增大力矩/扭矩扭矩传感器;检测扭矩、力矩角度和伺服电机形成闭环控制。
2.2故障原因分析经过现场观察三轴自动拧紧机二号枪头不认帽报警,螺栓与枪头不匹配,托盘举升机举升不到位等,可能是如下几个原因导致:(1)枪头达到使用台数导致枪头不认帽(2)枪头与螺栓不匹配导致枪头不认帽(3)托盘举升机举升不到位,枪头无法对零件进行加工,设备报警(4)枪头断裂导致设备报警(5)零件螺栓漏装导致设备报警3.安全操作规程3.1工作前要求(1)穿戴防护用品(如白色工作服、劳保鞋、工作帽),车间内发现不按要求穿戴的人员应清出,并及时对违规人员进行指正,未整改完成前禁止进入生产作业区域。
LED组打螺丝工艺-螺丝锁附介绍 V2.1

φ 3.0 孔径 2.5 2.5 2.6 2.6 2.4 2.4 2.3 公差
┼0.05 ─0 ┼0.05 ─0 ┼0 ─0.05 ┼0 ─0.05 ┼0.05 ─0 ┼0.05 ─0 ┼0.10 ─0
φ 3.5 孔径 2.9 2.9 3 3 2.8 2.8 2.7 公差
┼0.05 ─0.05 ┼0.05 ─0.05 ┼0.05 ─0.05 ┼0.05 ─0.05 ┼0.10 ─0 ┼0.10 ─0 ┼0.10 ─0
┼0 ─0.05 ┼0 ─0.05 ┼0 ─0.05 ┼0 ─0.05 ┼0.05 ─0 ┼0.05 ─0 ┼0.10 ─0
φ 2.8 孔径 2.4 2.4 2.4 2.4 2.3 2.3 2.2 公差
┼0 ─0.05 ┼0 ─0.05 ┼0.05 ─0 ┼0.05 ─0 ┼0 ─0.05 ┼0 ─0.05 ┼0.05 ─0.05
5.2 被锁件的螺丝槽处产生暴裂/螺丝断裂
上海信耀电子有限公司
Shanghai Seeyao Electronics Co.,Ltd.
信诚天下 |耀动未来
五、螺丝锁附不良的介绍
5.3 螺丝滑丝
上海信耀电子有限公司
Shanghai Seeyao Electronics Co.,Ltd.
信诚天下 |耀动未来
┼0.05 ─0 ┼0.05 ─0 ┼0.05 ─0 ┼0.05 ─0 ┼0.05 ─0 ┼0.05 ─0 ┼0.05 ─0 ┼0.05 ─0 ┼0.05 ─0.05
φ 2.8 孔径 2.3 2.3 2.4 2.4 2.2 2.2 2.1 1.9 2 公差
┼0 ─0.05 ┼0 ─0.05 ┼0 ─0.05 ┼0 ─0.05 ┼0.05 ─0 ┼0.05 ─0 ┼0.10 ─0 ┼0.10 ─0 ┼0.10 ─0
对自动弹夹式螺丝刀刀头的设计

对自动弹夹式螺丝刀刀头的设计摘要:当今市面上螺丝刀刀头的设计较为简单,螺丝刀与螺钉简单接触,很容易出现脱落的现象。
通过设计电磁感应螺丝刀,使得螺丝刀头与螺钉十分牢固地接触。
再加一个限距控制环,在达到限制距离内,自动断开电动机和电磁铁开关,从而达到了自动控制的作用。
在做出以上的改进后,上螺钉变得更加高效快捷,从而很大地提高了工作效率,适应了高速发展的社会节奏。
关键词:螺丝刀电磁铁限距控制环效率螺丝刀作为工程制造和家庭生活的一种常用的工具,发挥着极其重大的作用。
市面上出现了种类繁多的螺丝刀来满足人们的需求,如电动螺丝到、气动螺丝刀等等,基本满足了家庭生活的需要。
随着经济的高速发展和工业技术的提高,对螺丝刀的改进迫在眉睫。
对于工厂中一天需要装配上万个螺钉的装配工人来说,效率显得尤为重要。
由于螺丝刀与螺钉的接触面积较小,使得它们很容易脱落。
虽然现在出现了带磁性的螺丝刀,但期的使用和磨损后大多数螺丝刀也失去了吸铁石的功能,通过设计电磁感应螺丝刀头,大大增强螺丝刀头的磁性。
再增添一个限距控制环,通过限制螺钉与外物的距离,自动控制电机和电磁铁,起到开关的作用。
在不使螺钉和螺丝刀脱落的前提下,自动控制整个上螺丝钉过程,大大提高了工作效率。
1 主要研究内容(1)针对螺丝刀头吸引螺钉的状况下,为降低螺钉从螺丝刀头脱离或脱落的几率,采用电磁铁的控制来吸引螺钉,提高工作效率。
(2)针对螺丝刀在拧到一定程度的时候,利用简单的机械结构,能够自动停止电机,利用螺丝刀杆的惯性将螺钉拧紧,从而节省能源。
(3)在螺丝刀头处安设开关,能够自动地控制电磁铁及电机。
2 总体结构及工作原理2.1 螺丝刀头的结构组成如图1。
2.2 特殊结构说明(1)限距控制环。
限距控制环是一个直径略大于螺丝刀头的直径,且其可在螺丝刀头尖部前后移动。
当限距控制环不受轴向压力时,其在弹簧的作用下处于如图一所示的位置;当受到轴向压力时,限距控制环向后移动。
(2)SB4开关SB4是一个小型的行程开关,不工作的情况下处于闭合状态。
基于工业机器人的步进电机智能装配系统设计

摘要:设计了基于 PLC与工业机器人的步进电机智能装配系统,该控制系统由总控单元、行走单元、雕铣机单元、装 配单元、输送单元、立体仓库单元等组成,采用以太网通信,实现了机器人、机器视觉、PLC之间的数据与 I/O信号交换, 能完成了步进电机各零部件的搬运、加工和装配等工序。提高了工厂智能制造与装配水平、降低了人工成本,具有较高推 广应用价值。
ChangzhouJiangsu213164,China)
Abstract:Theintelligentassemblysystem ofsteppingmotorbasedonProgrammableLogicalController(PLC)andindustrial robotisdesigned.Thecontrolsystem wascomposedofgeneralcontrolunit,walkingunit,engravingandmillingunit,assemblyunit, conveyingunitandwarehouseunit,andetc.WithadoptingEthernetcommunication,thedataandI/Osignalexchangeamongrobot, machinevision,andPLCwererealized,andthehandlingandadditionofpartsofsteppingmotorwerecompletedofworkingandassemb lingprocedures.Itimprovesthelevelofintelligentmanufacturingandassembly,reducesthelaborcost,andhashighapplicationvalue.
《拧螺丝机结构设计毕业设计(论文)word格式》
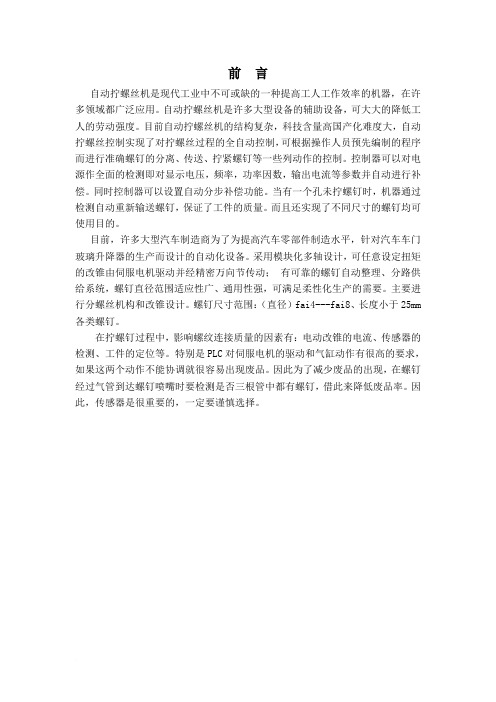
前言自动拧螺丝机是现代工业中不可或缺的一种提高工人工作效率的机器,在许多领域都广泛应用。
自动拧螺丝机是许多大型设备的辅助设备,可大大的降低工人的劳动强度。
目前自动拧螺丝机的结构复杂,科技含量高国产化难度大,自动拧螺丝控制实现了对拧螺丝过程的全自动控制,可根据操作人员预先编制的程序而进行准确螺钉的分离、传送、拧紧螺钉等一些列动作的控制。
控制器可以对电源作全面的检测即对显示电压,频率,功率因数,输出电流等参数并自动进行补偿。
同时控制器可以设置自动分步补偿功能。
当有一个孔未拧螺钉时,机器通过检测自动重新输送螺钉,保证了工件的质量。
而且还实现了不同尺寸的螺钉均可使用目的。
目前,许多大型汽车制造商为了为提高汽车零部件制造水平,针对汽车车门玻璃升降器的生产而设计的自动化设备。
采用模块化多轴设计,可任意设定扭矩的改锥由伺服电机驱动并经精密万向节传动;有可靠的螺钉自动整理、分路供给系统,螺钉直径范围适应性广、通用性强,可满足柔性化生产的需要。
主要进行分螺丝机构和改锥设计。
螺钉尺寸范围:(直径)fai4---fai8、长度小于25mm 各类螺钉。
在拧螺钉过程中,影响螺纹连接质量的因素有:电动改锥的电流、传感器的检测、工件的定位等。
特别是PLC对伺服电机的驱动和气缸动作有很高的要求,如果这两个动作不能协调就很容易出现废品。
因此为了减少废品的出现,在螺钉经过气管到达螺钉喷嘴时要检测是否三根管中都有螺钉,借此来降低废品率。
因此,传感器是很重要的,一定要谨慎选择。
第一章绪论1.1锁螺丝机研究的目的和意义螺丝机是一种非传统的机器,是为了提高汽车零部件的制造水平针对汽车玻璃升降器的生产而设计的自动化设备。
针对经电磁振动给料器整理后在螺钉输送槽中有序排列的分离问题,提出一种由螺钉分离板、档钉板、固定斜槽板及圆柱销相配合的螺钉自动分离装置。
利用气缸驱动螺钉分离板、挡钉板,利用挡钉板上固定的圆柱销受固定斜槽板上的起移动凸轮作用的斜槽限制,将位于螺钉输送槽最前端的一只螺钉分离开,并仅将一只螺钉推入螺钉分离板侧面的落钉口。
螺丝刀的设计
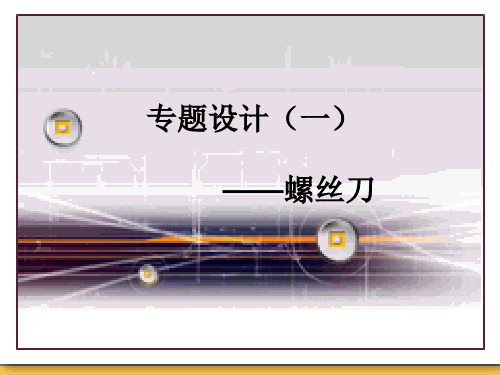
效果图
Precise wrap - is used to catch a nail or pencils, using only small finger muscles. Something that caught your thumb and forefinger located in middle. Such wrap should not be used to need power tools or action
调研资料螺丝刀的用法螺丝刀的分类螺丝刀规格市场上常见的螺丝刀调研分析螺丝刀调研表设计目标的确定定位人群产品特性设计展开人机界面设计加工工艺的可行性细节设计色彩设计手绘草图以草案方式提出解决问题的方案以及必要的使用方式示意图设计评价问答法专题设计时间进度表用法
专题设计(一)
——螺丝刀
目录
专题设计时间进度表 调研资料
加工工艺的可行性、细节设计、色彩设计
螺丝刀的加工工艺多种多 样,但其的作用我关键在与刀 头,而他的加工工艺差不多统 一,在次关键考虑刀柄的加工 工艺,根据其使用的材料的不 同,如塑胶可吹塑成型。他们 的加工工艺不会有什么大的问 题,现有技术都能实现。 螺丝刀的细节注意的是他 的外观,注重安全、多功能、 易清洁、方便。 螺丝刀的色彩范围广,只 要是看个人爱好,不同绚丽颜 色能给使用者带来一定的视觉 效果,
图SX-1
图SX-2
修理工对螺丝刀的使用
螺丝刀的分类
分类:结构形状——1、直形。这是最 常见的一种。头部型号有一字,十字, 米字,T型(梅花型),H型(六角), 等 ;2、L形。多见于六角螺丝刀,利 用其较长的杆来增大力矩,从而更省力; 3、T形。汽修行业应用较多。 动力源——手动和电动。 批头或者刀头——一字的和十字的。
人教版生活与科技第2册第一章第3节《螺丝刀和螺丝钉》教学设计

人教版生活与科技第2册第一章第3节《螺丝刀和螺丝钉》教学设计一. 教材分析《螺丝刀和螺丝钉》这一节内容主要让学生了解螺丝刀和螺丝钉的种类、用途和正确的使用方法。
通过学习,学生能够掌握螺丝刀和螺丝钉的基本知识,提高生活中使用工具的技能。
二. 学情分析学生在学习这一节内容前,已经学习了简单的生活工具使用方法,对于螺丝刀和螺丝钉有一定的认知。
但部分学生可能对螺丝刀和螺丝钉的种类和用途不够了解,需要通过实例和操作来加深理解。
三. 教学目标1.知识与技能:了解螺丝刀和螺丝钉的种类、用途和正确的使用方法。
2.过程与方法:通过观察、操作、实践,学会正确使用螺丝刀和螺丝钉。
3.情感态度价值观:培养学生热爱科学、热爱生活的情感,提高生活中使用工具的技能。
四. 教学重难点1.重点:螺丝刀和螺丝钉的种类、用途和正确的使用方法。
2.难点:如何正确使用螺丝刀和螺丝钉,以及在不同场景下选择合适的螺丝刀和螺丝钉。
五. 教学方法采用“实例导入、分组讨论、实践操作、总结提高”的教学方法,让学生在实践中学习,提高学生的操作技能和解决问题的能力。
六. 教学准备1.教具:螺丝刀、螺丝钉、实物道具等。
2.学具:每人一套螺丝刀和螺丝钉,用于实践操作。
七. 教学过程1.导入(5分钟)教师通过展示生活中常见的物品,如桌子、椅子、电脑等,引导学生思考这些物品是如何组装而成的。
进而引出本节内容的主题——螺丝刀和螺丝钉。
2.呈现(10分钟)教师展示各种螺丝刀和螺丝钉的图片,讲解它们的名称、用途和特点。
同时,让学生观察并说出自己生活中见过的螺丝刀和螺丝钉。
3.操练(15分钟)教师分发螺丝刀和螺丝钉,让学生分组进行实践操作。
教师巡回指导,纠正操作不当的学生。
4.巩固(10分钟)教师提问:如何正确使用螺丝刀和螺丝钉?在不同场景下应如何选择合适的螺丝刀和螺丝钉?学生分组讨论,分享自己的心得。
5.拓展(5分钟)教师引导学生思考:除了螺丝刀和螺丝钉,生活中还有哪些常见的工具?它们的作用是什么?6.小结(5分钟)教师总结本节课的重点内容,强调正确使用螺丝刀和螺丝钉的方法及其在生活中的重要性。
一种螺钉自动锁付系统的设计与应用

一种螺钉自动锁付系统的设计与应用摘要:一种螺钉自动锁付系统的构成和工作原理,该系统集成螺钉自动上料、螺钉孔自动定位、锁紧扭矩精准可调、锁紧结果反馈、记录及异常报警功能。
该系统具备较好的智能性、一致性和可推广性,实际使用中可有效提高生产效率。
关键词:螺钉连接、自动锁付;视觉定位;0引言在空调生产装配过程中,广泛使用到螺钉连接,由其决定的装配质量直接关系到产品的安全性和可靠性。
因此,螺钉的锁付技术是一项非常关键的技术,既要满足产品的性能要求,保障产品的品质,还需有效提高生产效率。
传统的螺钉锁付方式是使用电动或气动螺丝刀,通过手工的方式拧紧螺钉,由于存在作业重复、劳动强度大、效率难以提升等问题,在实际生产中已经逐渐无法满足需求。
为了改善人工作业存在的问题,实现螺钉锁付的智能化和自动化,本文介绍一款螺钉自动锁付系统。
该系统集成了螺钉自动上料、螺钉孔自动定位、锁紧扭矩可调,锁紧结果反馈及异常报警等功能。
1螺钉自动锁付系统架构设计螺钉自动锁付系统应用在流水线一侧打螺钉工位处,由机器人、锁批组件、螺钉送料机、控制柜等构成,见图1。
图1 自动锁付系统基本构成2系统原理及工作流程螺钉自动锁付系统的原理:利用视觉定位引导系统,自动识别待锁付产品上螺钉孔位置,从而引导机器人移动到锁付点,使锁批组件对正螺钉孔;由自动送料机将螺钉送入锁批组件头部螺钉夹嘴中,智能电批启动,将螺钉拧入螺钉孔。
工作流程:系统启动,机器人由原点移动至等待位;自动送料机通过透明软管将螺钉输送到螺钉夹嘴中;待锁付产品随流水线运转至打螺钉工位后,由线体上的机械定位机构限定其位置;机器人接收到产品到位信号,随即运动到图像采集点;相机采像,获取螺钉孔图像坐标;视觉系统将图像坐标转换为机器人坐标,机器人随即运动至坐标对应的锁付点;锁批组件启动,完成螺钉锁紧的工作;随后机器人返回至等待位。
锁批组件中的智能电批将锁紧扭矩值、旋转圈数、旋转时间等参数反馈给控制柜中的电批控制器;电批控制器判定螺钉锁紧合格(无浮高、滑牙),则传递“完成”信号给PLC,PLC发出“放行”指令,产品放行,流水线继续运转。
米家电动螺丝说明书

米家电动螺丝说明书
产品参数:
品牌: MIUI/小米
名称:米家电动螺丝刀
生产日期:2021/12/3
功能特点:
1.机身设计:
该产品采用的简洁一体化设计,外部无螺丝,机身采用工程塑料制作,做了磨砂处理,使用手感细腻,磨砂质感在提升手感的同时,还可以起到防滑的作用。
手柄采用的切面设计,不是圆柱设计,这样一来握持舒适度就得到了有效的提升。
电动按键扁平化设计,前按键拧入,后按键拧出,顺应直觉思维,上手快,操作前不用刻意去看。
2.携带方便:
机身握持处最窄不到3cm,小手也可以轻松握住,机身净重量仅仅185g,非常方便携带。
3.批头设计:
在将手柄间接设计之后,将批头进行了加长设计,长达5cm的批头,提升了扭矩,让你更省力。
而且有6种常用批头可供选择,基本可以满足日常的所有使用环境。
该产品的电动模式最大扭矩为3N.m,手动模式最大扭矩为8N.m。
4.安全保护:
手柄的充电口使用了防尘盖的设计,这样一来可以防止在使用过程中由于灰尘等颗粒掉入充电口,造成安全隐患。
充电也做了安全保护,支持充电过程中的过流、过压、过温和短路保护。
5.超长续航:
内置1500mAh锂电池,满电可以拧180颗螺丝,充电口上方还带有低电量提示灯,当电量低于20%的时候,按下按键提示灯会快闪5秒。
基于PLC的桌面型全自动锁螺丝机控制系统设计

基于PLC的桌面型全自动锁螺丝机控制系统设计作者:覃羡烘黄永程杨斌来源:《山东工业技术》2018年第07期摘要:本文从机械系统结构、控制系统硬件构建、控制系统软件设计、报警系统、通信等方面,对桌面型全自动锁螺丝机进行了详细的介绍,对自主开发的自动锁螺丝设备,设计了基于可编程控制器(PLC)的控制系统。
该系统融合了视觉定位、伺服驱动和可编程等技术。
该设备参数调节方便、运行可靠、操作简单,解决了自动化程度低的可题,节约了时间和劳动力,大大提高了产品生产效率。
关键词:PLC;桌面型全自动锁螺丝机;控制系统;可编程DOI:10.16640/ki.37-1222/t.2018.07.0041 前言自动锁螺丝机也叫自动送锁螺丝机、自动拧螺丝机、自动螺丝机、自动打螺丝机、自动螺丝紧固系统等。
目前现有的手持式自动送锁螺丝机,虽然可以解放一只手出来,但仍然需一只手提起起子对准螺丝孔位锁螺丝,人工对准孔需要很丰富的经验,也会产生一定的误差;全自动送锁螺丝机,虽然在手持式自动送锁螺丝机自动送料基础上又添加了机械臂或流水线、工作台、自动控制定位等功能,是送锁螺丝机的TOP产品,但是它结构复杂,成本比较高。
所以,在制造成本和可编程方向有很大发展空间。
本文针对这个问题,在原有的全自动送锁螺丝机基础上进行改装,使用可编程控制器(PLC)来设计自动拧紧螺丝,节约人工成本又提高了生产效率。
2 全桌面型自动锁螺机概述自动锁螺丝机在国内外已得到广泛应用,分为手握式、平台走程序式、直锁式、拔叉式、转盘循环式等结构。
目前在不少企业应用前景十分广阔,主要应用于汽车零部件生产、电脑、显示屏、电机、灯具、手机、打印机、电路板、电池、仪表等的自动组装,可以大大提高生产效率,降低生产成本,提高可靠性。
桌面型自动锁螺丝机有以下一些优缺点:由于其单人即可高效操作,一人相当于多人的效率,所以节省成本;其可靠性很好,一天可工作20小时以上;对于锁同样螺丝的产品,只需更换旋具,可锁不同产品,通过简单编程,通用性高;采用高精密度轨道设计,由机器作业,杜绝了人为因素带来的不良影响,有着良好的稳定性;具有漏锁/浮锁滑牙检测功能,客户可以选配;只要螺丝在规定的范围内可以通用;灵活性强,对于更换不同的产品,只需更换夹具和调用相对应程序组即可[1]。
AMR北京汽保展亮点产品

转速是同样手柄的3倍。
可轻松切换刀头转向,操作便捷。
锌合更长使用寿命。
特有航空铝合金材工程学设计,握持舒适。
产品配备26个六角、四角、花型螺丝。
牛津布袋设计,并挎在皮带上,方便作业人员携带。
企业:上海巴兰仕汽车检测设备股份有限公司改装,厂家接受改装的车型也是很多的,车。
车上设备使用独立的发电机驱动,在进行上门服务时,蓄电池的过度消耗而导致车辆无法起动的情况,动机长时间怠速运转造成的环境污染及能源浪费。
的设备,均会采用国家级安全标准进行加固,常使用,所有的设计都会进行紧凑化处理。
是设备的使用及拿取还是极为方便的,不会因为空间狭小而出现拿取不便的情况。
速转换。
此款轮胎拆装机主轴具有纵向调节功能,装范围,能对15~30英寸轮辋进行换胎操作。
控系统,可通过设备上的屏幕对换胎过程进行实时监控,查看的繁琐操作,所有过程尽收眼底。
品所有操作均通过操作台进行控制,摇杆对机器进行操控,使整个换胎过程变得简单容易。
金奔腾“黑金刚-钺”汽车智能云诊断仪企业:北京金奔腾汽车科技有限公司东风日产、郑州日产、江铃陆风、东南汽车、江西五十铃等车系上达到原厂专用诊断仪级别。
同时,在新能源汽车方面率先完成了国内主流新能源车型的匹配功能。
此外,该设备具备防盗遥控器手工匹配、里程表调校、保养灯归零、节气门匹配、电子胎压灯复位、转向角标定、大灯初始化、蓄电池匹配和齿讯学习等11大特殊功能。
同时,该设备可提供在线交流互动、远快速WiFi下载升级、海量维修资料共享、诊断案例视频库等多项云服务功能。
2018.04015抽屉出现变形的情况,该款工具车使用了全进口的滑轨轨道,滑轨最高可以承重46 kg,而整个工具车最高可以承重600 kg。
飞鹰国际UV-A灯企业:珠海市飞鹰电器有限公司该款产品最大亮点就是通过35 W的LED短波冷光源,UV漆喷涂的部位照射3 min后,漆面就可以快速干透,行抛光和打磨处理,很大程度提升了喷漆效率。
漆灯造型大体一致,但是采用的光源却发生了改变。
工具安全隐患排查小结(3篇)

第1篇一、前言随着我国经济的快速发展,工业生产对工具的需求日益增加。
工具作为生产过程中的重要组成部分,其安全性直接关系到生产效率和员工的生命安全。
为保障生产安全,降低事故发生率,提高员工的安全意识,近期,我单位对生产现场的工具安全隐患进行了全面排查。
现将排查情况及整改措施总结如下:二、排查范围及内容1. 排查范围:本次排查涉及我单位生产现场所有使用的工具,包括机械设备、电动工具、手动工具、液压工具等。
2. 排查内容:(1)工具的完好性:检查工具是否存在损坏、磨损、变形等情况;(2)工具的防护装置:检查工具是否配备防护装置,如安全防护罩、限位装置等;(3)工具的维护保养:检查工具的维护保养记录,确保工具处于良好状态;(4)工具的存放环境:检查工具的存放场所是否符合要求,是否通风、干燥、防潮、防火等;(5)操作人员的操作规范:检查操作人员是否正确使用工具,是否存在违规操作现象。
三、排查结果1. 工具完好性方面:部分工具存在磨损、变形、损坏等情况,如扳手、螺丝刀等。
2. 工具防护装置方面:部分工具未配备防护装置,如电钻、砂轮机等。
3. 工具维护保养方面:部分工具的维护保养记录不完整,保养周期较长。
4. 工具存放环境方面:部分工具存放场所不符合要求,存在潮湿、积尘、杂物堆积等问题。
5. 操作人员操作规范方面:部分操作人员存在违规操作现象,如未佩戴防护用品、操作不当等。
四、整改措施1. 对损坏、磨损、变形的工具进行更换或维修,确保工具的完好性。
2. 对未配备防护装置的工具,按照规定配备相应的防护装置,如安全防护罩、限位装置等。
3. 加强工具的维护保养,完善维护保养记录,确保工具处于良好状态。
4. 优化工具存放环境,确保工具存放场所通风、干燥、防潮、防火等。
5. 加强操作人员的安全教育培训,提高操作人员的安全意识,规范操作行为。
五、总结通过本次工具安全隐患排查,我单位发现并解决了部分安全隐患,提高了生产现场的安全管理水平。
2013“市长杯”创意杭州工业设计大赛分赛场
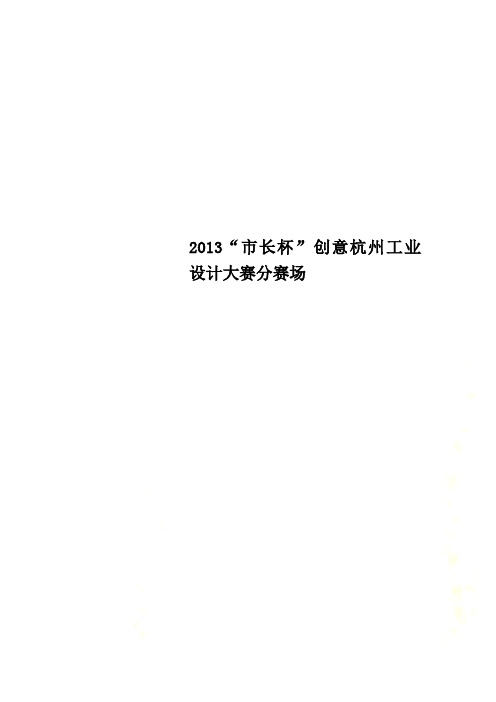
2013“市长杯”创意杭州工业设计大赛分赛场2013“市长杯”创意杭州工业设计大赛分赛场拟奖作品公示2013“市长杯”创意杭州工业设计大赛创意组“瑞德i-life杯”分赛场获奖作品名单奖项名称参赛作品名称设计者参赛单位(院校)银奖皮肤管家乐维浩浙江科技学院银奖走出美丽冯迪、沈泓浙江工业大学铜奖CATCH测距套件王超丕浙江科技学院铜奖iPhone三防对讲手机壳毛威浙江科技学院铜奖Toothcare 皮伟、章婧莱湖南大学设计艺术学院2013“市长杯”创意杭州工业设计大赛创意组“吉利杯”分赛场获奖作品名单奖项名称参赛作品名称设计者参赛单位(院校)金奖帝豪混合动力A级两厢车曹辰刚同济大学银奖帝豪 MPV 王志涛武汉理工大学银奖新款帝豪EC8 马新乐郑州轻工业学院铜奖帝豪跑车朱嘉辰武汉理工大学铜奖吉利帝豪戴翔宇浙江工业大学铜奖吉利 CONCEPT SUV 秦昊江南大学铜奖EVADE概念车邦艳飞、杨德勇个人ORCINUS多功能环保皮卡车探索设铜奖陈峥峥浙江工业大学计2013“市长杯”创意杭州工业设计大赛创意组“淘宝杯”分赛场获奖作品名单奖项名称参赛作品名称设计者参赛单位(院校)小“C”电炖盅(淘宝杯--小熊电金奖孟帝北京吉利大学器)家庭——爱婴系列移动电源金奖何连春自由职业(淘宝杯——品胜电子)义乌市帝格电子科技有银奖萌芽(淘宝杯——小熊电器)翟震限公司银奖电魔坊(淘宝杯——品胜电子)吕磊个人银奖光影大师(淘宝杯——品胜电子)袁文昱中国地质大学(武汉)铜奖电魔坊(淘宝杯——品胜电子)何方北京理工大学珠海学院享乐-家庭分享套装移动电源设计铜奖邓森、梁世鸽、李萍杭州半木设计有限公司(淘宝杯——品胜电子)铜奖品45°(淘宝杯——品胜电子)管钰荣杭州电子科技大学2013“市长杯”创意杭州工业设计大赛创意组“下一代新秀杯”分赛场获奖作品名单奖项名称参赛作品名称设计者参赛单位(院校)金奖声声慢陆晶晶胡思亮浙江农林大学银奖米量陈思聪浙江工业大学郑贤强、黄琴、李元、顾银奖竹制办公用品-方便近在咫尺南京理工大学梦颖、麻云鹏铜奖Desksides_桌沿系列李景元浙江大学铜奖排列组合-桌面三件套李炳、李俊生沈阳航空工业学院铜奖“印象”Impression文件别针王纬国武汉科技大学2013“市长杯”创意杭州工业设计大赛创意组“朱炳仁铜屋杯”分赛场获奖作品名单奖项名称参赛作品名称设计者参赛单位(院校)金奖花好月圆——香台罗英煌华南农业大学艺术学院银奖同心同德吴乙嘉、段亚静杭州电子科技大学银奖故宫纸镇艾文龙松果设计银奖云王焱自由设计师铜奖古韵梁伟兴华南农业大学艺术学院铜奖一山一水,一世界赖胜利、曹源浙江农林大学铜奖紫禁城·文房四宝孙晋红、史嘉玲、刘玮南京林业大学铜奖灯芯肖丹丹浙江理工大学铜奖芬眠香炉孙誉佳松果设计优秀奖一草一木刘佩轩武汉科技大学中国计量学院现代科技优秀奖宫寿铜炉任凯学院优秀奖窗格·小意邹许美芸、刘玮南京林业大学优秀奖浮光朱琴琴浙江工业大学优秀奖铜壶系列之“方圆之间”廖春安浙江工业大学优秀奖故宫博物院旅游纪念品——香炉艾鑫武汉科技大学优秀奖故宫宫灯徐明独立设计师优秀奖圆缺苏贝杭州科技职业技术学院优秀奖坛周江棒杭州科技职业技术学院李彩萍、段雨辰、罗云、优秀奖故宫记忆南京林业大学刘玮优秀奖仁世铜香炉王聿丰、刘匍陕西科技大学优秀奖香薰炉——天地相交时运亨通王美兰南京林业大学优秀奖铜牦牛镇纸摆件冯东升中央美院优秀奖文房铜宝韩宇复旦大学视觉艺术学院优秀奖一叶扁舟刘洋甫武汉科技大学优秀奖烟的轨迹王梦佳、黄蕾,李陈宁中国美术学院优秀奖爱莲说孙誉佳个人2013“市长杯”创意杭州工业设计大赛创意组“王星记”分赛场获奖作品名单奖项名称参赛作品名称设计者参赛单位(院校)金奖扇脉马秋萍、戴舒灵浙江工业大学银奖王星记扇盒邬幸娟杭州电子科技大学银奖手握清凉朱亚静中国计量学院铜奖加木扇架沈阳波、谢婷婷浙江工业大学铜奖声声碎-檀香木扇褚文祺浙江工业大学铜奖王星记扇子LOGO设计孙雨欣浙江大学城市学院2013“市长杯”创意杭州工业设计大赛创意组“张小泉杯”分赛场获奖作品名单奖项名称参赛作品名称设计者参赛单位(院校)李洋、陈旭、江南大学金奖叠.律吴吴银奖刀削便携组合毛成杰中国计量学院银奖变形剪刀李陈洪中国计量学院铜奖计米数剪刀陈佳妍、林璐浙江理工大学铜奖力道刘兵封自由设计师铜奖树梢上的莺刀范银萍、甄智椋江南大学罗江浩、陈逸凡铜奖“随剪”系列中国美术学院吴宇琴铜奖信息保护剪苏达浙江工业大学优秀奖卷尺介刀赖雪锋广东科学技术职业学院优秀奖多功能可收缩小刀沈杏烊广东科学技术职业学院优秀奖“二”刀林楷广东科学技术职业学院优秀奖刀架切刀广东科学技术职业学院优秀奖存丝留片廖细旭广东科学技术职业学院优秀奖板中藏刀毛成杰中国计量学院优秀奖“灵活”蔬果刨王芬芬浙江大学城市学院优秀奖儿童安全剪刀周珍中国计量学院优秀奖逆剪顾赛南浙江机电职业技术学院优秀奖永不变钝刀座组合马贤君中国计量学院优秀奖180°厨刀朱亚静中国计量学院优秀奖清道夫楚文宝中原工学院优秀奖度量布剪陈建江、章徐涛、张顺杭州未末设计有限公司优秀奖把护安全杭州未末设计有限公司优秀奖剪.影陈文格浙江工业大学优秀奖易用小刀设计邓家超、郝梦刘树福、徐晓赟马丽丽、严瑾中原工学院优秀奖随心剪陈思聪浙江工业大学优秀奖两用美工剪刀张枫林湖南大学优秀奖梯形刀砧三件套设计葛弘扬、王文浩中国计量学院优秀奖剪.生活杨正彦无锡太湖学院2013“市长杯”创意杭州工业设计大赛创意组“经纬创意杯”分赛场获奖作品名单奖项名称参赛作品名称设计者参赛单位(院校)金奖经纬国际创意产业园logo类何自然个人金奖自动缫丝机车头外观类余美子中国计量学院银奖经纬国际创意产业园logo类虞佳依浙江大学城市学院银奖自动缫丝机车头外观类吕多沈阳理工大学铜奖经纬国际创意产业园logo类焦宜红云南民族大学铜奖自动缫丝机车头外观类戴玉琼沈阳理工大学2013“市长杯”创意杭州工业设计大赛创意组“观唐杯”分赛场获奖作品名单奖项名称参赛作品名称设计者参赛单位(院校)金奖公共休闲沙发吕多沈阳理工大学银奖箍椅赖胜利、曹源浙江农林大学银奖墨灯李航浙江大学城市学院刘德、章李锋、倪佳欢、铜奖公园座椅设计浙江工业大学钱爱华铜奖雅致家庭办公家具林哲沈阳理工大学铜奖浮影王文波中国计量学院铜奖驻竹座椅夏泽宗浙江大学城市学院铜奖剪窗花坐凳俞丽娅浙江农林大学铜奖雅风书房系列灯钟诚2013“市长杯”创意杭州工业设计大赛创意组“巨星杯”分赛场获奖作品名单奖项名称参赛作品名称设计者参赛单位(院校)金奖工具设计侯纯阳沈阳理工大学银奖工具设计李康沈阳理工大学银奖工具设计张雷沈阳理工大学银奖T字型螺丝刀欧思思中原工学院铜奖Rotating Spanner邱麒、支尚、田壮、井九久、高毓磊北京服装学院铜奖多功能分类行李箱设计蔡儆琦、鲁金帅、高源,路晓丹、戚硕中原工学院铜奖多尺寸扳手设计郑盛娜毛云鹏浙江工业大学铜奖工具设计施晶晶沈阳理工大学铜奖三口径扳手师艳江中原工学院优秀奖“轻松拧”螺丝刀改良设计耿伟潮武汉科技大学优秀奖工具设计郭晓蕾沈阳理工大学优秀奖凹面螺丝刀潘成彦中国计量学院优秀奖工具设计贾梦月沈阳理工大学优秀奖工具设计季嘉男沈阳理工大学优秀奖工具设计李娜沈阳理工大学优秀奖工具设计吕金莲沈阳理工大学优秀奖激光灯—螺丝刀设计殷建明、卢美、蓝鋆滋浙江农林大学优秀奖随“机”应变楚文宝中原工学院优秀奖黑暗探视_LED可旋转省力螺丝刀设计章徐涛、张顺、陈建江杭州未末工业设计有限公司邱麒、支尚、田壮、井九优秀奖MULTI-SIZE SPANNER北京服装学院久、高毓磊2013“市长杯”创意杭州工业设计大赛创意组“万事利丝绸杯”分赛场获奖作品名单奖项名称参赛作品名称设计者参赛单位(院校)特等奖《南海圣境》李程个人金奖《青花瓷—印》钟琴个人银奖《丝韵天堂》李程个人银奖《蝶·变》郑好南安普敦大学铜奖《印象西湖》姚惠蓉个人铜奖《蛇舞荷花》刘蓉蓉个人铜奖《莲塘普照》胡霄燕个人铜奖《眺月》刘蓉蓉个人铜奖《见证》陈敏绍兴文理学院元培学院优秀奖《浪漫古城》孙艳苹个人优秀奖《国粹传承》沈蓉绍兴文理学院元培学院优秀奖《水忆杭州》陆炫绍兴文理学院元培学院优秀奖《青花---》杨帅个人优秀奖《绿岛夜曲》俞昕彦个人优秀奖《杭之冬》姚伟宁浙江工业大学优秀奖《荷塘月色》吕明度ESMOD优秀奖《荷叶颂》黄大成个人优秀奖《湖蝶》屠乐希浙江理工大学优秀奖《三潭印月》钟雅春个人2013“市长杯”创意杭州工业设计大赛创意组“制高光电杯”分赛场获奖作品名单奖项名称参赛作品名称设计者参赛单位(院校)特等奖足下光影吴杪榆中原工学院金奖登山伴侣施仲义中国计量学院张彦、陈晓宇、楚文宝、银奖阳光伴“旅”中原工学院丁强强、王雪晴银奖和·风周超浙江工业大学铜奖炫彩夹灯冯肖个人铜奖健身王文浩、葛弘扬、余晓炜中国计量学院铜奖Flashlight OR lamp 张加帆浙江理工大学铜奖Sapling户外照明灯蒋惠梁浙江工业大学铜奖害羞的蘑菇蒋惠梁浙江工业大学优秀奖平衡床头灯·流动的光金燕燕、林璐浙江理工大学优秀奖The treet lamp庭院灯陈杉杉浙江工业大学艺术学院优秀奖灯——祥蔡明洁浙江大学城市学院浙江大学城市学院创意优秀奖影趣施李静与艺术分院戴新宇、何阿琼、张云、优秀奖TO SHARE THE LIGHT中原工学院朱峻明、范纯真优秀奖freestyle 坚果小灯毛成杰中国计量学院优秀奖竹节灯毛成杰中国计量学院优秀奖折纸定时灯冯肖个人戴新宇、朱峻明、何阿琼、中原工学院优秀奖洁光范纯真、张云毛成杰陈剑驰徐磊章优秀奖新苗中国计量学院俊邵丁2013“市长杯”创意杭州工业设计大赛创意组“天堂伞杯”分赛场获奖作品名单奖项名称参赛作品名称设计者参赛单位(院校)卢维佳、郝雨、王敏璐、金奖Coin Handle雨伞柄湖南大学金生辉银奖小鲤鱼套伞王柳青浙江工业大学银奖新结构与外观伞秦英个人铜奖Hey!Bunny ears 赖胜利、曹源浙江农林大学铜奖伞与夹赖胜利、曹源浙江农林大学铜奖十二生肖宋涛杭州万向职业技术学院李臻、李全伟、査晓云任铜奖“坠”美中原工学院媛、胡玉晶铜奖“呼叫的士”雨伞许赛静浙江工业大学优秀奖45°Cup Umbrella 葛弘扬、王文浩中国计量学院优秀奖便携式充气伞季阳阳、周小燕、沈小焱、浙江工业大学洪海云、苗茜优秀奖“Sucker”吸盘式伞的创新设计宋涛杭州万向职业技术学院优秀奖随意吸-带吸盘的伞柴愉双浙江科技学院优秀奖转转动画伞劳秋燕、余佳浙江农林大学优秀奖Warm 劳秋燕、陆晶晶、胡思亮浙江农林大学优秀奖Hanging everywhere 欧思思中原工学院葛弘扬、王文浩、余晓炜、中国计量学院优秀奖独树一帜伞朱李丽优秀奖雨“韵”--交互光点伞马兰浙江工业大学优秀奖随处一挂谷永增杭州电子科技大学优秀奖体贴-引路人刘佩轩武汉科技大学浙江理工大学科技与艺优秀奖sunshine多功能伞架陈婷婷术学院优秀奖易扣欧思思中原工学院优秀奖香味伞柄姚青青浙江农林大学优秀奖挂钩伞王旭阳武汉科技大学田壮、邱麒、支尚、高毓优秀奖光伞北京服装学院磊、井九久优秀奖弯&直伞柄刘俊云中国计量学院优秀奖绿叶“程”荫姚宣辰江南大学优秀奖小护士-----多一份安全冯清艳江南大学优秀奖天堂喵喵林凯莉、陶良丽、李青原中原工学院2013“市长杯”创意杭州工业设计大赛创意组“苏泊尔超越杯”分赛场获奖作品名单奖项名称参赛作品名称设计者参赛单位(院校)金奖分离式电饼铛设计冯肖个人银奖智能豆浆机梁海方鲁迅美术学院银奖90后榨汁机设计黄浩、王小宇、赵亚晨中国美术学院铜奖易取蒸锅设计毛成杰中国计量学院铜奖星星之火可以做饭邓小明、胡廖、贾小曼、王胜男、刘恩俊、杜齐星中原工学院铜奖鸣悦张顺章徐涛杭州未末工业设计有限公司铜奖食生•序周寅瑄、杨子扬、俞斌、任甄南京艺术学院、浙江理工大学城市学院铜奖“E-cook”电磁炉余真珍浙江工业大学艺术学院优秀奖面面俱到向泓兴、李正洲、周敏、夏承安江西财经大学优秀奖“合”-便携式早餐机设计施鹏飞、田炎梅、闫琦南京艺术学院、浙江理工大学城市学院优秀奖舞韵碧裳赖胜利曹源浙江农林大学优秀奖变色保温电水壶设计戴新宇、朱峻明、何阿琼张云、范纯真中原工学院优秀奖浮点电磁炉马贤君、赖鹏中国计量学院优秀奖家电“圆”梁德超中国计量学院优秀奖手提多士炉毛成杰中国计量学院优秀奖早餐搭档-粥锅吴杨华联想电子优秀奖淘煲石静中原工学院杭州未末工业设计有限优秀奖I cook(智能厨房交互终端)章徐涛公司杭州未末工业设计有限优秀奖冷热饮陈建江公司优秀奖年轮电磁炉王子秋旻、潘思博中国美术学院优秀奖微波罩靳亚雄大连交通大学优秀奖一个人的精彩陈异子个人浙江理工大学科技与艺优秀奖Le yao——摇式豆浆机设计易永华术学院向泓兴、李正洲、周敏、优秀奖“圆”美新生活江西财经大学夏承安优秀奖烤乐姚安琪个人杨云、陈潍滔、黎珊、俞优秀奖“U”优生活个人育耿优秀奖“四位•一体”组合电饭锅施菲菲中国计量学院优秀奖层层回味黄旭东浙江树人大学优秀奖印象•环何翠颖湖南科技学院优秀奖扇香电磁炉盛厚福湖南科技学院优秀奖“开裂”电水壶熊灵锋浙江树人大学优秀奖YOYO电水壶周超浙江工业大学优秀奖莲形电磁炉钱爱华浙江工业大学优秀奖“油”然而生李斌、闫晨晨、史修迪、邱培杰南京艺术学院、浙江理工大学城市学院优秀奖锅色添香李斌、闫晨晨、史修迪、邱培杰南京艺术学院、浙江理工大学城市学院2013“市长杯”创意杭州工业设计大赛创意组“圣奥杯”分赛场获奖作品名单奖项名称参赛作品名称设计者参赛单位(院校)金奖Secret系列孙威南京林业大学银奖领航张云冲南京林业大学银奖cool一族时尚办公家具肖红霞浙江农林大学铜奖蜂巢办公系列朱晨希浙江农林大学铜奖“卓远”主管办公空间设计俞梦杰、曹愉静浙江工业大学铜奖办公桌沈卫琴浙江工业大学铜奖Mimer work chair 钟川浙江理工大学铜奖转折多功能公共休闲椅设计陈盈盈中国计量学院现代科技学院铜奖悦动陆南楠浙江大学优秀奖琉透—逸空间丁皓凡南京林业大学优秀奖拼图·凳丁国庆、曹朋武汉科技大学艺术与设计学院优秀奖手臂锻炼办公椅浙江工业大学钱爱华浙江理工大学科技与艺优秀奖i-touch 楼潞璐术学院优秀奖灵动空间主管办公家具系列家具肖红霞浙江农林大学优秀奖靠背椅的再设计毛成杰中国计量学院贾敏、李世龙、崔金伟、优秀奖红与黑中原工学院李莉花、赵辉杰中国美术学院艺术职业优秀奖极易(极一)莫梦莹技术学院优秀奖互动办公沙发陈臻个人优秀奖云端智能办公空间陈石金南京林业大学武汉科技大学艺术与设优秀奖“炫”律丁国庆、曹朋计学院优秀奖檐eaves 贝尚婷浙江理工大学优秀奖心随我移何达文浙江理工大学优秀奖竹椅钟川浙江理工大学浙江理工科技与艺术学优秀奖多功能便携办公桌寿慈涛、申屠鸿院优秀奖幻影黄赛赛浙江农林大学优秀奖变变变赵辉杰中原工学院优秀奖Transformers办公椅造型设计沈佳彬、张明杭州万向职业技术学院优秀奖可DIY链接办公桌组合陈建江、章徐涛、张顺杭州未末工业设计有限公司周小燕、季阳阳、沈小焱、优秀奖网-公共空间休闲家具浙江工业大学洪海云、苗茜优秀奖Modular desk 模块化职员桌设计叶银、张继烽浙江工业大学2013“市长杯”创意杭州工业设计大赛创意组“大天杯”分赛场获奖作品名单奖项名称参赛作品名称设计者参赛单位(院校)金奖紧凑型立加叶皓宇个人银奖战神彭怀涛武汉科技大学银奖长城江韬中原工学院铜奖泰山刘建秀沈阳理工大学铜奖数控机床张亚斌沈阳理工大学铜奖小龙门数控机床郝芳芳武汉科技大学铜奖翘首以待曹崇维中原工学院铜奖大天GABT1020 叶皓宇个人优秀奖智造邓森半木工业设计优秀奖GKS8000高精度冯肖个人优秀奖金刚石冯肖个人优秀奖天门形意施林杰杭州电子科技大学优秀奖NV55A 段瑞龙沈阳理工大学优秀奖数控机床田振沈阳理工大学优秀奖机床2 王强沈阳理工大学优秀奖变形金刚薛光沈阳理工大学优秀奖数控机床2 张步伟沈阳理工大学优秀奖高精度张景然沈阳理工大学优秀奖VERTITURN3 赵盼沈阳理工大学优秀奖小金刚彭怀涛武汉科技大学优秀奖DT615 陈飞成中原工学院优秀奖黑爵士黄迪平中原工学院优秀奖大天红贾敏中原工学院优秀奖O型贾敏中原工学院优秀奖Black Swan 李世龙中原工学院优秀奖KING KONG 李世龙中原工学院优秀奖玺之控王小康中原工学院优秀奖1+1+人张云中原工学院2013“市长杯”创意杭州工业设计大赛创意组“党山杯”分赛场获奖作品名单奖项名称参赛作品名称设计者参赛单位(院校)金奖日月潭张顺、陈建江个人银奖“清”水出芙蓉洪海云浙江工业大学银奖然刘骁葳、马冬妮江南大学铜奖“巧”邱文婷浙江农林大学铜奖竹•语林威豪浙江科技学院铜奖架.浴室柜韩飞、沈泓浙江工业大学优秀奖Exclusive 李世龙中原工学院优秀奖“简.竹”张彦中原工学院优秀奖延展浴室柜李炳郑州轻工业学院优秀奖尚吴持韬浙江农林大学优秀奖360°劳秋燕、余佳浙江农林大学优秀奖鹤鸣陈思宇、王军浙江农林大学优秀奖钢琴键韩飞浙江工业大学优秀奖骑士肩韩飞浙江工业大学韩飞张濛黄银可浙江工业大学优秀奖随心而变陈文格优秀奖折合韩飞、沈泓浙江工业大学优秀奖古韵马兰浙江工业大学优秀奖清雅居阮湘婷浙江工业大学优秀奖静流童艳菁、马秋萍、邱莉峰浙江工业大学优秀奖BOX 张继烽叶银浙江工业大学优秀奖云月余俊男浙江大学优秀奖简艺孙晋、吕米雪武汉理工大学优秀奖中国风浴潘建华武汉科技大学优秀奖清新洁净刘海滨江南大学优秀奖中式浮雕陈小娟个人优秀奖HOUSBC可收纳浴室柜陈建江、章徐涛、张顺个人2013“市长杯”创意杭州工业设计大赛创意组“顿力杯”分赛场获奖作品名单奖项名称参赛作品名称设计者参赛单位(院校)特别奖空间助手系列黄河个人金奖无端系列李雨桐,佟金芮国美银奖BLOOMING 曹源,黄达浙江农林大学银奖Changeable 朱晨希浙江农林大学银奖Space Extend 潘磐中国电子科技集团38所铜奖随居肖红霞浙江农林大学铜奖枪卢芳浙江科技大学铜奖小厨房大空间缪黄云中国计量学院铜奖我非工具潘盛木国美铜奖厨房五金段瑞龙沈阳理工大学优秀奖手舞池嘉昱浙江树人大学优秀奖清风拂翠潘梦笔浙江树人大学邓小明、王胜男、刘恩俊、优秀奖盖头中原工学院杜齐星优秀奖衣帽架张学伍沈阳理工大学优秀奖小蛮腰何达文沈阳理工大学优秀奖伸缩衣架秦亚军中原工学院优秀奖彩虹伞架陈虹莹中国计量学院优秀奖鱼伞架付琪中国计量学院优秀奖美人斜靠麻云鹏南京理工大学优秀奖萤之光刘建秀沈阳理工大学优秀奖花园小架曹源、黄达浙江农林大学优秀奖云端胡玉晶中原工学院优秀奖雨来花开刘冉中原工学院优秀奖易朱健律浙江科技大学优秀奖珊瑚小调韩静沈阳理工大学优秀奖木岛铁苗赵彦雪沈阳理工大学优秀奖鹿奔之原陈林珊浙江树人大学优秀奖凝聚梁方梅、李炳中国科大优秀奖DNA 杨迪中原工学院优秀奖系列多功能伞架方立佳中国计量学院2013“市长杯”创意杭州工业设计大赛创意组“新南杯”分赛场获奖作品名单奖项名称参赛作品名称设计者参赛单位(院校)金奖休闲椅徐军浙江工贸职业技术学院银奖任逍遥徐航、顾浩浩、陈思聪浙江机电职业技术学院铜奖暖椅王晓美个人2013“市长杯”创意杭州工业设计大赛创意组“环宇集团杯”分赛场获奖作品名单奖项名称参赛作品名称设计者参赛单位(院校)金奖翻弈林修文中国美院象山校区银奖趣味儿童家具刘俊夕沈阳理工大学银奖抽象摇马-鹿张坦沈阳理工大学铜奖小短腿毛成杰中国计量大学铜奖布袋外星人缪贝中国美院象山校区铜奖猫头鹰抱枕李逸凡、朱路路、刘爱清中国美院象山校区优秀奖多乐椅翁雪桐浙江理工大学优秀奖rocking chair 章坚个人优秀奖小鸡快跑儿童家具黄赛赛浙江农林大学优秀奖仿生儿童家具吕多沈阳理工大学优秀奖双人儿童音乐桌陈杉杉、陈艾青、高扬浙江工业大学优秀奖智趣童年欢乐桌郑盛娜、毛云鹏浙江工业大学2013“市长杯”创意杭州工业设计大赛创意组“惠宝杯”分赛场获奖作品名单奖项名称参赛作品名称设计者参赛单位(院校)金奖彩霸H480E淋膜机叶皓宇neilDESIGN 银奖精锐切纸机冯迪浙江工业大学朱峻明、戴新宇、何阿琼、中原工学院银奖彩霸H480系列淋膜机范纯真、张云、陈晓宇铜奖F350自动覆膜机楚文宝中原工学院铜奖彩霸H480E升级款高端淋膜机邵丹丹、叶皓宇neilDESIGN 铜奖CB-920T无线桌面胶装机系列叶皓宇neilDESIGN 铜奖淋膜机设计赵宇浙江工业大学优秀奖淋膜机设计曹愉静、俞梦杰浙江工业大学。
螺丝刀的起源与发展历史

螺丝⼑的起源与发展历史螺丝⼑⼤概是⼿动⼯具⾥最简单的产品了,⼀个⼑杆加⼀个⼿柄.即使在DIY动⼿能⼒不算太强的国⼈家庭,应该每个家庭都有那么⼀把。
然⽽就是这么简单的产品,不可思议的具有划时代的意义,他⽐任何⼿动⼯具更资格代表世界⼯业⾰命的进程.谈到螺丝⼑必然先谈螺丝,什么是螺丝,我们⼤约可以从雷锋同志的⽇记略窥⼀⼆,1960年 1⽉12⽇,雷锋在⽇记⾥写道:“虽然是细⼩的螺丝钉,是个细微的⼩齿轮,然⽽如果缺了它,那整个的机器就⽆法运转了,慢说是缺了它,即使是⼀枚⼩螺丝钉没拧紧,⼀个⼩齿轮略有破损,也要使机器的运转发⽣故障的,尽管如此,但是再好的螺丝钉,再精密的齿轮,它若离开了机器这个整体,也不免要当作废料,扔到废铁料仓库⾥去的。
”1962年4⽉7⽇,雷锋再次写道:“⼀个⼈的作⽤对于⾰命事业来说,就如⼀架机器上的⼀颗螺丝钉。
机器由于有许许多多螺丝钉的连结和固定,才成了⼀个坚实的整体,才能运转⾃如,发挥它巨⼤的⼯作能⼒,螺丝钉虽⼩,其作⽤是不可估量的,我愿永远做⼀个螺丝钉。
螺丝钉要经常保养和清洗才不会⽣锈。
⼈的思想也是这样,要经常检查才不会出⽑病。
”精神层⾯的东西我们先不提,但螺丝之于⼯业的意义不⾔⽽喻,2000年,美国《纽约时报》曾发起⼀项“⼈类纪元以来第⼆个千年的最佳⼯具”评选,最终,⼩⼩螺丝荣登榜⾸.⼯业上,螺丝被⼴泛应⽤到各个⼯业领域,⼤到轮船,飞机,⼩到眼镜,⼿机都离不开螺丝,⼈们称他为“⼯业之⽶”,拧动这些⼯业之⽶的产品就是螺丝⼑.在第⼀次⼯业⾰命之前,螺丝很难⽣产,Job与William Wyatt兄弟找到了⼀种在新型机器上⽣产螺丝的⽅法,尽管他们的业务最终商⽤失败了,但他们对螺丝的低成本制造的贡献,最终导致了螺丝的⼤量增加和螺丝起⼦的普及。
螺丝的⽣产通过不断的提⾼效率和尺⼨标准化,螺丝精度的提⾼也极⼤地促进了⽣产的繁荣。
随着螺丝在⼯业应⽤上的逐渐普及,也同时导致了螺丝⼑的改进和多样化。
《3电动工具真奇妙》教学设计教学反思-2023-2024学年小学劳动技术人民版三年级上册

《电动工具真奇妙》教学设计方案(第一课时)一、教学目标:1. 知识与技能:学生能认识和了解电动工具的基本类型,掌握基本的安全使用方法。
2. 过程与方法:通过观察、操作电动工具,提高学生的动手能力和实践能力。
3. 情感态度价值观:培养学生的创新意识和探索精神,增强学生对劳动的热爱和尊重。
二、教学重难点:1. 教学重点:引导学生观察电动工具,了解其工作原理和功能,掌握安全使用方法。
2. 教学难点:如何让学生在实际操作中发现问题,解决问题,提高实践能力和创新意识。
三、教学准备:1. 准备不同类型的电动工具样品,如电钻、砂轮机、切割机等。
2. 准备相关的教学器材和工具,如电线、螺丝刀、安全帽等。
3. 准备教学PPT,包括电动工具的图片和操作演示。
4. 安排学生进行小组合作学习,每组选择一种电动工具进行操作。
5. 准备安全提示牌和安全防护设备,确保学生安全。
四、教学过程:1. 导入新课(5分钟)展示电动工具实物,介绍电动工具的基本知识,引出课题。
2. 知识讲解(15分钟)a. 电动工具的种类及特点:例如电钻、砂轮机、电动锯等;介绍每种工具的特点和使用范围。
b. 使用电动工具的注意事项:安全操作规程、维护保养等。
c. 实例讲解:选择一种电动工具进行操作示范,让学生直观了解操作方法。
d. 小组讨论:让学生分组讨论不同电动工具的使用方法及特点,提出疑问和想法。
3. 实践操作(30分钟)学生根据所学知识,使用电动工具进行实际操作,教师巡回指导。
过程中鼓励学生自主解决问题,教师适时给予帮助。
4. 评价反馈(10分钟)a. 学生自评:学生对自己的操作过程和成果进行评价,总结经验教训。
b. 小组互评:小组间互相评价,分享经验,提出改进建议。
c. 教师总结:教师对本次课进行总结,对表现优秀的学生和小组给予表扬和奖励,对不足之处提出改进意见。
5. 课后作业(5分钟)学生回家后尝试使用不同类型的电动工具,并记录使用心得和感受。
- 1、下载文档前请自行甄别文档内容的完整性,平台不提供额外的编辑、内容补充、找答案等附加服务。
- 2、"仅部分预览"的文档,不可在线预览部分如存在完整性等问题,可反馈申请退款(可完整预览的文档不适用该条件!)。
- 3、如文档侵犯您的权益,请联系客服反馈,我们会尽快为您处理(人工客服工作时间:9:00-18:30)。
一、市场调查研究:
螺丝是常见的一种工件,大到重型机械,小到日常生活用品,我们总能看到螺丝的身影。
因此拧螺丝的螺丝刀在生活和生产中占有很重要的地位。
现在出现的比较多的螺丝刀有普通的手动螺丝刀和电动螺丝刀。
普通手动螺丝刀结构简单,价格低廉,但是效率比较低,特别是有较长的螺钉要拧时更明显。
电动螺丝刀效率高,且省时省力,适合大规模生产使用,且可以设计成带电池的电动螺丝刀,从而可以抵消对电源线的依赖。
二、设计方案:
基于以上对市场现有螺丝刀的性能分析,设计一款电动螺丝刀。
1、设计要求:
能快速拧紧/松出螺丝的的多功能手动螺丝刀,其特征是:单手操作,可实现快速正反转,也可变速为正常螺丝刀一样工作;可更换多种规格的螺丝刀头。
2、结构设计:
本产品由高效变速装置、多功能刀头装置和变速装置组成。
1)高效变速装置主要由手柄、螺丝刀架、固定在螺丝刀柄内的变速直齿轮组组成。
工作时,操作手法和普通螺丝刀相近,握住手柄正反转,简单并排的变速直齿轮组能使螺丝刀杆直接正反旋转。
为了结构紧凑,设计的变速直齿轮组的传动比为1:3.5 ,当用于快速拧紧/松开螺丝时,转一圈手柄,可以使螺丝旋进/松开3.5圈,实现高效旋
高效变速装置
2)多功能刀头装置是便于拆装更换螺丝刀头的装置,可以安装不同规格的螺丝刀头。
3)变速装置紧固螺钉需要较大力矩时,将变速装置小推件拉到如图中所示位置,则螺丝刀的传动比为1比1,可以满足拧紧要求,此时螺丝刀与普通螺丝刀无异。
将变速小推件往右拉,则可实现1:3.5的高效旋转。
作品整体效果图如图-4所示。
图-2 多功能刀头装置
图-3 变速装置
图-4 作品整体效果图
3、螺丝刀控制部分设计:
本设计产品带有自动停止控制功能,以下为该产品的控制模块设计设计如下。
1) 硬件设计如图1。
其主要由单片机、电机、开关电路、模数转换、力传感器等组成的。
由单刀开关控制正反转,来实现拧螺丝和松螺丝两个动作。
当需要拧螺丝时,断开开关S1,打开电源。
单片机将控制模数转换,把扭矩力电压输入到单片机,当扭矩力小于一定值时,电机正转。
当扭矩力达到一定值时,关闭电机。
当需要松螺丝时,闭合开关S1,打开电源。
单片机将控制电机一直反转,直到手动关闭电源。
图1 2)程序流程设计
3)程序软件设计
程序预定义如图3。
预先定义了有单片机封装库,ADS7825模数转换,电机,PWM,按键,扭矩力调节值。
图3
主程序如图4。
通电以后,首先初始化各个寄存器,调整各个寄存器工作状态。
然后读取张反转按键ZF的状态。
如果是正转状态,则控制电机以占空比60%正转,直到达到一定扭矩力才会停下来。
如果是反转状态,则控制电机以占空比70%反转,直到手动关闭电源。
图4
PWM定时器如图5.设置定时器T,定时129us中断一次。
以129us乘以100为一个PWM控制周期。
在电平转换点之前为高电平,之后为低电平。
图5
寄存器初始化如图6。
初始化定时器,启动模数转换。
图6
读取扭矩力如图7.单片机以一个超过25us的低脉冲对ADS7825的RC 引脚进行操作,控制BYTE采集16位的扭矩力数据。
图7
控制电机如图8。
单片机控制定时器的电平转换点来控制PWM的占空比和电机转向。
图8
三创新点总结:
1、此电动螺丝刀可以使用电池操作,抵消了以前的电动螺丝刀对电源线的依赖;
2、其巧妙利用齿轮的变速传动,转动主动轮,带动从动轮高倍转动,使被拧螺钉快速拧紧/松开,大大提高了工作效率;
3、还可以快速变换不同规格的螺丝刀头,适合对各种规格的螺丝操作。
;
4、其体积小巧、结构紧凑、携带方便,操作时只需单手就可以完成,高空作业的操作人员无须双手操作,大大提高了高空作业的安全系数;
5、结构简单、造价低廉,适合大众的需求。
四、应用前景:
现在市场上主要有普通手动螺丝刀和带电源线的电动螺丝刀这两种。
普通手动螺丝刀拧螺钉时,受到手转动角度的限制,其速度慢、效率低,工作消耗人的体力高,而且,当在高空仰头工作时,人容易劳累;而电动螺丝刀的工作效率虽高,但由于其购买价格也高,且受到用电的限制,只能在有电源供应的地方使用,其体积较大,携带不方便。
高效变速螺丝刀克服了上面两种螺丝刀的缺陷,其体积小巧,便于携带,工作时只需单手操作,传动比可达1:3.5甚至可以设计更高的传动比,工作方便快捷,省时省力,大大提高了工作效率;而且高效变速螺丝刀的生产流程相对简单,价格比较便宜,更适合大众需求。
附件:部分零件图
心得体会
1、从设计创意到完成作品的加工制作,我们经历了资料的检索、查询、整理与分析,数据处理能力得到提升;方案的不断修改与完善让我们学会设计与加工要统筹兼顾;在机构设计与产品加工中我们将专业知识充分运用到了实际产品开发。
在整个设计与制造过程中我们进一步掌握了机械设计与加工的步骤和要领,深刻体会到团队协作的重要性,同时团队成员综合素质和动手能力得到了很大的提高。
2、本次制作充分将所掌握的课本知识融入其中,比如把《机械原理》,计算机编程语言知识运用到机构的设计中,运用《工程力学》、《金属工艺学》和《数控加工技术》知识结合CAD、PROE软件对零件进行了合理的选材和设计加工制造。
3、从早期的设计构思到作品加工完成,我们深刻认识到现实与理论往往有较大差距,理论设想需要得到实验和实际产品的验证,机械设计与制造是一个不断循环反复完善的过程。
通过参与作品制作,我们学到了不少实用知识,真正体会到实践出真知的道理。
4、当我们耐心地解决一个又一个问题时,体会到机械设计是一项牵一发而动全身的工作。
因此在加工制造之前考虑整体机构各方面因素的时候要非常严谨和务求全面,在追求功能的实现的同时,必须充分地考虑到实际加工的困难、产品的性价比等。
总之,机械设计要“理论结合实际”。