材料制备与加工
1 材料制备与加工实验指导书

材料制备与加工实验实验指导书目录实验1、铝合金时效硬化曲线的测定及其影响因素分析实验2、焊接工艺与焊缝组织检验实验4、热塑性塑料的挤出造粒和注射成型实验1、铝合金时效硬化曲线的测定及其影响因素分析一、实验目的1.掌握固溶淬火及时效处理的基本操作;2.了解时效温度和时效时间对时效强化效果的影响规律;3.了解固溶淬火工艺(淬火加热温度、保温时间及淬火速度等)对铝合金时效效果的影响;4.掌握金属材料最佳淬火温度的确定方法;5.加深对时效强化及其机制的理解。
二、实验原理从过饱和固溶体中析出第二相(沉淀相)或形成溶质原子聚集区以及亚稳定过渡相的过程称为脱溶或沉淀,它是一种扩散型相变。
发生这种转变的最基本条件是,合金在平衡状态图上有固溶度的变化,并且固溶度随温度降低而减少,如图2-1所示。
如果将C成分的合金自单相α固溶体状态缓慢冷却到固溶度线(MN)以下温度(如T3)保温时,β相将从α相固溶体中脱溶析出,α相的成分将沿固溶度线变化为平衡浓度C1,这种转变可表示为α(C)→α(C1)+β。
其中β为平衡相,它可以是端际固溶体,也可以是中间相,反应产物为(α+β)双相组织。
将这种双相组织加热到固溶度线以上某一温度(如T1)保温足够时间,β相将全部溶入α相中,然后再急冷到室温将获得单相过饱和的α固溶体。
这种处理称为固溶处理(淬火)。
图2-1 固溶处理与时效处理的工艺过程示意图然而过饱和的α相固溶体在室温下是亚稳定的,它在室温或较高温度下等温保持时,亦将发生脱溶。
但脱溶相往往不是状态图中的平衡相,而是亚稳相或溶质原子聚集区。
这种脱溶可显著提高合金的强度和硬度,称为时效硬(强)化或沉淀硬(强)化。
合金在脱溶过程中,其力学性能、物理性能和化学性能等均随之发生变化,这种现象称为时效。
室温下产生的时效称为自然时效,高于室温的时效称为人工时效。
若将过饱和固溶体在足够高的温度下进行时效,最终将沉淀析出平衡脱溶相。
但在平衡相出现之前,根据合金成分不同会出现若干个亚稳脱溶相或称为过渡相。
材料制备与加工工艺

材料制备与加工工艺对于材料的制备与加工工艺的研究,是现代科学技术领域的一项重要工作。
材料的选择、制备和加工工艺直接影响了产品的质量、性能和使用寿命。
本文将介绍一些常见的材料制备与加工工艺,并探讨其在不同领域中的应用。
一、金属材料制备与加工工艺金属材料是最常见的材料之一,广泛应用于机械、建筑、航空等各个领域。
金属材料的制备与加工工艺主要包括熔炼、铸造、锻造、热处理等。
熔炼是将金属原料加热至熔点,使其液化后借助重力或电磁力等方法进行分离和纯化的过程。
铸造是将液态金属倒入模具中,经过冷却凝固得到所需形状的工艺。
锻造是通过将金属材料置于锻机上,借助外力作用使其发生塑性变形得到所需形状。
热处理则是通过对金属材料进行加热、保温和冷却等过程,改变其结构和性能。
二、陶瓷材料制备与加工工艺陶瓷材料具有优异的耐高温、耐腐蚀和绝缘性能,广泛应用于电子、化工、建筑等领域。
陶瓷材料的制备与加工工艺主要包括研磨、成型、烧结等步骤。
研磨是将原料进行细磨,使其粒度均匀。
成型是将研磨后的陶瓷原料进行压制或注塑等工艺,得到所需形状。
烧结是将成型后的陶瓷材料进行高温加热,使其颗粒间发生结合,形成致密的材料。
三、聚合物材料制备与加工工艺聚合物材料具有很好的可塑性和耐磨性,广泛应用于塑料、纺织、医药等领域。
聚合物材料的制备与加工工艺主要包括聚合、挤出、注塑、模压等。
聚合是将单体分子进行化学反应,形成高分子链的过程。
挤出则是将聚合物料塑化后通过模具挤出成型。
注塑是将塑化的聚合物料注入到模具中,通过冷却凝固得到所需形状。
模压则是将聚合物加热塑化后放入模具中压制,形成所需形状。
四、复合材料制备与加工工艺复合材料是由两种或多种不同材料组合而成的新材料,具有优异的特性和广泛的应用前景。
复合材料的制备与加工工艺主要包括预浸法、层叠法、注射法等。
预浸法是将纤维材料与树脂浸渍后固化,形成复合材料。
层叠法是将纤维和树脂分层叠加,经过压制和热处理形成复合材料。
金属材料制备与加工技术

金属材料制备与加工技术金属材料是工业生产中最广泛应用的材料之一,其特点是强度高、重量轻、导电性好、延展性强等。
金属材料的制备与加工技术是工业生产中不可或缺的重要环节。
本文将从金属原料的提取、金属材料的制备、金属材料的特性及加工技术等角度,展开论述金属材料制备与加工技术的相关知识。
一、金属原料的提取金属原料来自于矿石,矿石是地球上自然产生的含有金属元素的矿物石。
几乎所有矿石都需要经过熔炼、冶炼等一系列加工过程,才能将金属元素提取出来。
不同的金属矿石有不同的提取方法,如铁矿石通常采用高炉冶炼技术,铜、铅、锌等常见的有色金属,则采用闪速炉或氧气活性炉等技术。
二、金属材料的制备金属材料的制备通常包含提纯、合金化、制备成型三个主要步骤。
提纯是指通过各种方法,去除杂质,提高金属材料的纯度。
在高纯度金属制备过程中,物理化学方法是常用的手段。
合金是指在金属中加入一定的其他金属元素,以改变原有金属的性能、强度和其它特性。
合金化处理通常采用电解沉积、熔锅法、原位反应等多种方法。
制备成型是将经过提纯和合金化处理后的金属材料,通过成型处理,达到特定形状和尺寸的目的。
制备成型通常分为加热塑性成型和非加热塑性成型两种方法,加热塑性成型包括锻造、轧制、挤压、拉伸、深冲等;非加热塑性成型包括压铸、砂型铸造、金属模铸造等。
三、金属材料的特性金属材料的特性有很多,其中包括密度、热膨胀系数、导热系数、热传导率、电导率、热稳定性等。
不同的金属材料在这些特性方面的表现是不同的,而在材料的物理性质、化学性质等方面也有很大的不同。
钢铁是三维有序排列的铁原子和碳原子的合金,具有高强度和韧性,可以制成各种机械零件,用途广泛;铝和铜等有色金属,密度轻、延展性强,广泛应用于航空航天、电子、建筑等领域;而铂、金等贵金属具有良好的耐腐蚀性,广泛用于化工、电子领域等。
四、金属材料的加工技术金属材料的加工技术是将金属材料变成成品的重要环节。
金属材料的加工技术种类繁多,依据不同的材料、产品、加工要求等,可以进行精密加工、焊接、切削加工、热处理等多种不同的加工方法。
先进材料的制备与加工技术研究

先进材料的制备与加工技术研究随着科技的不断进步,人们对更加高新材料的需求也越来越强烈。
先进材料作为一种高科技领域的重要组成部分,在科技、工业、航空航天、军事等领域的应用越来越广泛。
在这个大背景下,先进材料的制备与加工技术也日益成为了研究的热点之一。
先进材料的制备技术主要包括实验室溶剂法、气相沉积、电化学沉积、高能球磨法等,不同的方法适用于不同形态的材料。
例如,实验室溶剂法适用于制备高质量的纳米材料;气相沉积则适用于制备薄膜及其异质结构;电化学沉积适用于制备具有特殊功能的稀土材料;高能球磨法适用于制备金属、陶瓷等材料的粉末。
制备方法的选择除了考虑材料本身,还需要考虑成本、效率、资源消耗等方面的因素。
为了使得制备方法更加实用,许多研究者致力于制备技术的改进。
例如,在实验室溶剂法中,人们不仅关注材料本身所处环境(溶液温度、溶液浓度等等),还会探究如何利用超高压、超高温等极端条件下进行溶剂法制备,从而得到特殊材料。
在气相沉积技术方面,研究人员则关注多种条件下的沉积速率以及沉积层的成分、结构等问题。
除了制备技术的优化,先进材料的加工技术也是制约其应用的重要因素。
先进材料的加工技术发展得好坏,直接决定了实际应用的效果。
例如在飞机制造领域中,使用合金材料作为零件具有很多优点,例如强度、韧性等,不过,这些材料常常需要进行高精度的切削加工。
传统的切削机床处理起来十分困难,因此人们需要采用先进的加工技术,例如电火花加工、激光加工等。
近年来,随着高能激光技术、电子束曲面制造技术、3D打印技术等的发展,人们越来越注重先进材料的加工技术。
这些先进加工技术有着不同的优势,例如激光加工可以实现高精度的加工,电子束曲面制造技术可以制造出形状复杂的高质量等离子体刻度,3D打印技术则实现了材料精细的组合。
不过,这些先进技术同样需要人们进行不断的研究和改进。
例如在3D打印技术中,人们最关心的问题是材料的粘度、熔融温度、沉积速率等等因素对于材料的形态、稳定性等问题。
《材料制备与成型加工技术》课件——绪论

成型加工(Forming and processing)
02
料制品各种成型方法及操作,成型工艺特点,成型工艺的适应性,成型工艺流程,成型设备结构及作用原理,成型工艺条件及其控制,成型工艺在橡胶、塑料、纤维加工中的共性和特殊性,各种高分子材料制品的成型加工过程,成型加工新工艺和新方法。
高分子材料(macromolecule material
按照高聚物来源分类
结构高分子材料--利用它的强度、弹性等力学性能功能高分子材料--利用它的声、光、电、磁、热和生物等功能
按照材料学观点
天然高分子材料--天然高聚物(natural)合成高分子材料--合成高聚物(compound)
2、高分子材料的分类(Classification of Polymer Materials)
2、高分子材料加工(Polymer material processing)
通常是使固体状态(粉状或粒状)、糊状或溶液状态的高分子化合物熔融或变形,经过模具形成所需的形状,并保持其已经取得的形状,最终得到制品的工艺过程。制造过程如下:
(1)成型加工过程的四个阶段
00
原材料的准备
01
使原材料产生变形或流动,并成为所需的形状
工程塑料(Engineering plastic)
01
是指拉伸强度大于50MPa ,冲击强度大于6kJ/m2,长期耐热温度超过100℃的、刚性好、蠕变小、自润滑、电绝缘、耐腐蚀性能等优良的、可替代金属用作结构件的塑料。
02
No.1
(3)橡 胶(rubber)
No.2
橡胶是室温下具有粘弹性的高分子化合物,在适当配合剂存在下,在一定温度和压力下硫化(适度交联)而制得的弹性体材料(橡胶制品)。按用途和性能可将橡胶分为通用橡胶和特种橡胶。
第一篇 金属材料的制备与加工工艺

一、生铁冶炼
2、高炉设备及工艺过程
一、生铁冶炼
2、高炉设备及工艺过程
图 5-4 高炉内型示意图
炼 铁 高 炉 的 结 构
炼铁工业设备图
炼铁工业设备图
一、生铁冶炼
铁 矿 石 熔 剂 焦 炭
2、高炉设备及工艺过程
上料机
喷吹 燃料罐
燃料 高炉
热风 热风炉
冷风 鼓风机
空气
炉渣
生铁
煤气
水 渣
渣 棉
矿石中的磷主要以(CaO)3P2O5[Ca3(PO4)2]的形 式存在,磷酸钙在1200~1500℃以固体碳为还原剂 发生直接还原反应,反应为: (CaO)3P2O5+5C=3CaO+2P+5CO 而SiO2存在,又能与磷酸钙中的CaO相结合, 使P2O5游离出来,从而加速磷酸钙的还原,反应为: 2(3CaO· 2O5)+3SiO2=3(2CaO· 2)+2P2O5 P SiO 2P2O5+10C=4P+10CO 被还原出来的磷除小部分挥发外都溶入铁中, 还原出来的磷与铁结合生成Fe2P或Fe3P并溶于生铁 中,因此控制生铁含磷量的唯一方法是控制炉料的 含磷量。
一、生铁冶炼
1、炼铁的原料
(2)熔剂
作用:
降低脉石熔点,生成熔渣; 去硫
种类:
通常用碱性熔剂石灰石
要求:
碱性氧化物高(CaO+MgO)>50%,酸性氧化物低(SiO2+Al2O3) ≤3.5% P、S低,强度高,粒度均匀,一般25~75mm,最好与矿石粒度一 致
一、生铁冶炼
1、炼铁的原料
一、生铁冶炼
(2) 高炉渣
材料制备与加工课程设计

材料制备与加工课程设计一、课程目标知识目标:1. 学生能理解材料制备与加工的基本概念、原理和方法。
2. 学生能掌握不同材料的性质、制备工艺及加工技术。
3. 学生能了解材料制备与加工在工程、生活和科技领域中的应用。
技能目标:1. 学生能运用所学知识,设计简单的材料制备与加工实验方案。
2. 学生能运用实验仪器和设备,进行基本的材料制备与加工操作。
3. 学生能分析实验结果,评价材料性能,并提出改进措施。
情感态度价值观目标:1. 学生能培养对材料科学的兴趣,提高探究欲望。
2. 学生能认识到材料制备与加工在可持续发展、环境保护等方面的重要性,树立社会责任感。
3. 学生能在团队合作中,学会尊重、倾听、协作,培养良好的沟通能力和团队精神。
课程性质:本课程为高中年级的选修课程,旨在让学生了解材料科学的基本知识,掌握材料制备与加工的基本技能,培养学生的实践操作能力和科学素养。
学生特点:高中年级的学生具备一定的物理、化学基础,思维活跃,好奇心强,具备一定的实验操作能力。
教学要求:结合学生特点,注重理论与实践相结合,强调实验操作和观察分析,引导学生主动探究,培养学生的创新能力和实践能力。
通过分解课程目标为具体的学习成果,为教学设计和评估提供明确的方向。
二、教学内容1. 材料基本性质:密度、硬度、韧性、导电性等物理性质,以及化学反应、氧化还原等化学性质。
2. 常见材料分类:金属、陶瓷、塑料、复合材料等,及其特点和应用。
3. 材料制备方法:熔炼、烧结、化学合成、物理气相沉积等。
4. 材料加工技术:铸造、塑性加工、热处理、表面处理等。
5. 材料制备与加工工艺优化:探讨不同工艺参数对材料性能的影响。
6. 材料应用案例分析:分析不同材料在汽车、航空、电子、医疗等领域的应用。
教学大纲安排:第一周:材料基本性质及分类第二周:材料制备方法(一)第三周:材料制备方法(二)第四周:材料加工技术(一)第五周:材料加工技术(二)第六周:材料制备与加工工艺优化第七周:材料应用案例分析及实验操作第八周:课程总结与评价教学内容与教材关联性:本教学内容与教材《材料科学基础》相关章节紧密关联,涵盖第二章材料的基本性质、第三章材料分类、第四章材料制备方法和第五章材料加工技术等内容。
材料制备与加工工艺
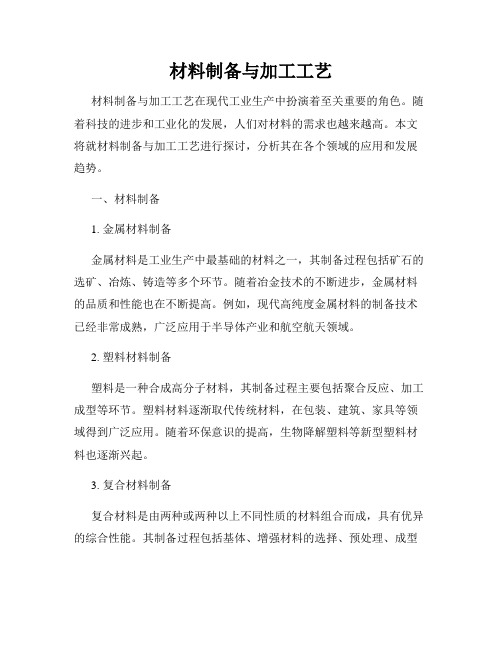
材料制备与加工工艺材料制备与加工工艺在现代工业生产中扮演着至关重要的角色。
随着科技的进步和工业化的发展,人们对材料的需求也越来越高。
本文将就材料制备与加工工艺进行探讨,分析其在各个领域的应用和发展趋势。
一、材料制备1. 金属材料制备金属材料是工业生产中最基础的材料之一,其制备过程包括矿石的选矿、冶炼、铸造等多个环节。
随着冶金技术的不断进步,金属材料的品质和性能也在不断提高。
例如,现代高纯度金属材料的制备技术已经非常成熟,广泛应用于半导体产业和航空航天领域。
2. 塑料材料制备塑料是一种合成高分子材料,其制备过程主要包括聚合反应、加工成型等环节。
塑料材料逐渐取代传统材料,在包装、建筑、家具等领域得到广泛应用。
随着环保意识的提高,生物降解塑料等新型塑料材料也逐渐兴起。
3. 复合材料制备复合材料是由两种或两种以上不同性质的材料组合而成,具有优异的综合性能。
其制备过程包括基体、增强材料的选择、预处理、成型等环节。
复合材料在汽车、航空航天、体育器材等领域有着广泛的应用前景。
二、加工工艺1. 金属加工工艺金属加工是将金属材料进行成型、切削、焊接等加工过程,以满足不同形状和尺寸的要求。
常见的金属加工工艺包括冷拔、热轧、冷冲、焊接等。
现代数控加工技术的发展,使得金属加工更加精确高效。
2. 塑料加工工艺塑料加工是将塑料材料进行挤压、注塑、吹塑等加工过程,制备成各种形状的制品。
塑料加工工艺简单易行,适用于大规模生产。
注塑成型技术被广泛应用于电子、家电、汽车等行业。
3. 复合材料加工工艺复合材料加工是将复合材料进行成型、固化、表面处理等加工过程,以获得具有特定性能的制品。
常见的复合材料加工工艺包括手工层叠、自动化复合、热压成型等。
随着复合材料应用领域的不断拓展,其加工工艺也在不断创新和完善。
结语材料制备与加工工艺是现代工业发展的重要支撑,其发展水平直接影响着产品的质量和性能。
随着科技的不断进步和需求的不断变化,材料制备与加工工艺也在不断创新和发展。
材料制备与加工技术-挤压

75MN单动卧式铝挤压机
挤压加工的特点:
1) 提高金属的变形能力 (三向压应力状态) 2) 制品综合质量高,组织细小,力性好,尺寸精度高,表
面质量高。 3) 产品范围广。 管、棒、线、材(大至1000mm;小至
几mm以下) 4) 生产灵活性大,更换模具即可 5) 制备组织不均匀,因为流变不均匀 6) 工模具损耗大 7) 效率低
• 挤压比:挤压压力、生产率及设备能力而定 • 挤压速度:与合金的可挤压性密切相关
2. 铜及铜合金的挤压 可以挤压管、棒、线材、型材、空心材。 (1)铜及铜合金挤压材料及其主要用途
(2)铜及铜合金挤压材料的可挤压性及挤压条件范围 与铝合金相比,挤压温度高、速度快。
3.钢铁材料挤压
钢铁材料挤压的两特点:
合
模
主
要
用
于
铝
和
软
铝
合
金的
空
心
型
材
生
产
各种实心模
注意: • 挤压温度高、强度大的合金用锥模。 • 模角α的取值 • 各种挤压模的定径带(各种挤压模通道上的园柱段)长度
空心模
3.3.4 挤压工艺案例 1. 铝及铝合金的挤压
铝及铝合金型材得到广泛应 用,其占挤压制品的70%以 上。典型的铝合金挤压型材 的断面形状见图5—56。
(1)各种铝合金挤压制品的性能及主要用途 美国铝业协会的变形铝合金牌号
▪ 第1位数字:主要合 金元素
▪ 第2位数字:对原始 合金的调整和对杂质 含量的限制
▪ 最后两位:在1XXX 系,代表铝的最低含 量;在2XXX和 8XXX系,进一步区 分合金
(2)各种铝合金的挤压条件范围
• 可挤压性指数是以6063的指数为100时的相对经验数值, 可挤压性指数越大,表示挤压加工越容易。
材料制备与加工实验20171023
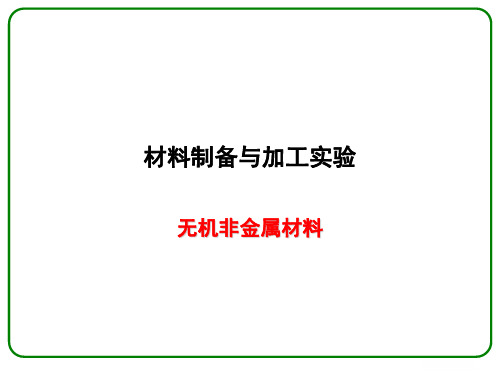
按下列公式计算泥浆的相对粘度:相对粘度=τ30s/τ水。 式中:τ30s为泥浆静止30s后,从粘度计中流出100ml所 需的时间,s;τ水为水从粘度计中流出100ml所需要的 时间,s。
③ 成形 先将做好的模具清理干净并捆扎好,然后将泥浆连 续不断地(注意保持垂直)注入模具内。 待泥浆在模具内壁吸附到一定厚度时,双手抱紧模 型,先将泥浆摇动,再把模具内多余的泥浆倒出,吸 附泥浆的厚薄就是坯体的厚薄。 坯体的厚薄要根据器皿的大小而定,大的器型可厚 些,小的器型可以薄些,一般注浆件在0.4至0.6毫米 左右。 最后,待模具内的坯体脱水到可以站立的强度时, 把模具打开,取出坯体。
加压方式:有单向加压和双向加压两种。
传统陶瓷材料中常含有粘土,粘土本身就是很好的 塑化剂。
而特种陶瓷的粉料一般为很细的瘠性物料,将对成 型产生不利的影响:
一是因流动性差和拱桥效应,影响对模腔的均匀填 充;
二是粉体越细、松装高度越大,压缩比大,因摩擦 而产生的力损失亦大,易使坯体密度不均匀;
三是孔隙中气体较难排出,易因弹性后效作用使坯 体产生层裂。
② 浆料粘度的测量 把涂-4粘度计内外容器洗净、擦干,置于不受振动 的平台上,调节粘度计三各支脚的螺丝,使之水平。 检查水平的方法与天平类似。在粘度计环形托架上有 一个水平器,当调节到水平时,液泡即在水平器的圆 圈内。
把搪瓷杯放在粘度计下面中央,粘度计的流出口对 准杯的中心。转动开关,把粘度计的流出口堵住,将 制备好的浆料借助玻璃棒慢慢地倒入粘度计的容器中, 至恰好装满容器(稍有溢出)为止,用玻璃棒仔细搅 拌一下,静置30秒钟,立即扒开开关,同时启动秒表, 眼睛平视容器的出口,待泥浆流断流时,立即关秒表, 记下时间。重复测定三次,取平均值。
新材料的制备与加工技术升级
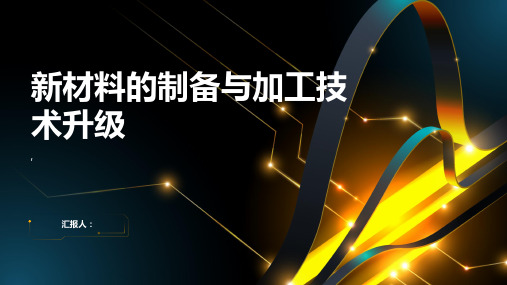
新材料制备与加工技术的结合,可以降低生产成本,提高生产效率,促进 产业升级。
新材料制备与加工的挑战
技术难度:新材料的制备和加工技术复杂,需要攻克多种技术难题
成本压力:新材料的制备和加工成本高,需要降低成本以提高竞争力
环保要求:新材料的制备和加工需要符合环保要求,减少对环境的影响 创新需求:新材料的制备和加工需要不断创新,以满足不断变化的市场 需求
耐磨损:新材料具有较低的 摩擦系数和较高的耐磨性, 能够长时间保持其表面光洁 度。
耐高温:新材料具有较高的熔 点、沸点和热导率,能够承受 较高的工作温度。
生物相容性:新材料具有良 好的生物相容性,能够与人 体组织相容,适用于生物医 学领域。
环保性:新材料具有较低的污 染性和毒性,符合环保要求, 适用于绿色制造领域。
Part Five
政策支持与市场前 景
国家政策支持情况
政府对新材料产业的术创新、促进产业升级等
添加标题
添加标题
添加标题
添加标题
政策扶持的具体措施,如资金支持、 税收优惠等
政策对市场前景的影响,如市场需 求、竞争格局等
市场需求情况
新材料在各行业的广泛应用 市场需求持续增长 政策支持推动行业发展 技术升级提高市场竞争力
建筑交通:高强度混凝土、复合材料、 智能材料
国防军工:隐身材料、防弹材料、智能 武器
Part Two
加工技术升级
传统加工技术
机械加工:包括车、铣、刨、磨、钻等 热处理:包括淬火、退火、正火、回火等 表面处理:包括电镀、喷涂、阳极氧化等 成型技术:包括铸造、锻造、冲压、注塑等
新型加工技术
材料工程专业就业方向

材料工程专业就业方向材料工程专业是一门以材料科学为基础,以工程技术为手段,研究材料的制备、性能、结构和应用的学科。
随着科技的不断发展和工业的不断进步,材料工程专业的就业前景也越来越广阔。
一、材料研发与设计方向材料研发与设计是材料工程专业的重要方向之一。
在这个方向上,毕业生可以从事新材料的研究与开发工作。
他们可以参与新材料的设计、制备和测试,为工业生产提供新材料方案。
这个方向需要具备扎实的材料基础知识和创新能力,因此对于研究院所、大型制造企业和科研机构来说,优秀的材料研发与设计人才是非常宝贵的。
二、材料制备与加工方向材料制备与加工是材料工程专业中的重要方向之一。
在这个方向上,毕业生可以从事材料的制备和加工工作。
他们可以通过改变材料的组成、结构和加工工艺,改善材料的性能,并满足不同工业领域对材料的需求。
这个方向需要具备深厚的材料工程知识和熟练的加工技术,因此对于制造业、航空航天等领域来说,掌握材料制备与加工技术的人才是非常重要的。
三、材料性能与测试方向材料性能与测试是材料工程专业中的重要方向之一。
在这个方向上,毕业生可以从事材料的性能测试和分析工作。
他们可以通过对材料的物理、化学、力学性能的测试和分析,评估材料的可靠性和适应性,并提供相应的技术支持。
这个方向需要具备扎实的材料基础知识和熟练的测试技术,因此对于材料生产、质量控制和技术服务等领域来说,具备材料性能与测试技术的人才是非常重要的。
四、材料应用与工程方向材料应用与工程是材料工程专业中的重要方向之一。
在这个方向上,毕业生可以从事材料的应用研究和工程应用工作。
他们可以根据不同工业领域的需求,将材料应用于产品的设计、制造和改进中,提高产品的性能和竞争力。
这个方向需要具备广泛的材料知识和工程应用能力,因此对于制造业、能源领域和环境保护等领域来说,具备材料应用与工程技术的人才是非常重要的。
五、材料管理与质量控制方向材料管理与质量控制是材料工程专业中的重要方向之一。
材料制备与加工工艺优化
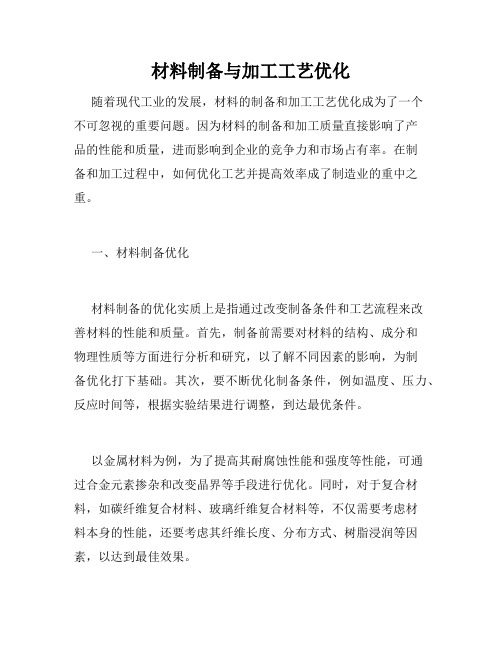
材料制备与加工工艺优化随着现代工业的发展,材料的制备和加工工艺优化成为了一个不可忽视的重要问题。
因为材料的制备和加工质量直接影响了产品的性能和质量,进而影响到企业的竞争力和市场占有率。
在制备和加工过程中,如何优化工艺并提高效率成了制造业的重中之重。
一、材料制备优化材料制备的优化实质上是指通过改变制备条件和工艺流程来改善材料的性能和质量。
首先,制备前需要对材料的结构、成分和物理性质等方面进行分析和研究,以了解不同因素的影响,为制备优化打下基础。
其次,要不断优化制备条件,例如温度、压力、反应时间等,根据实验结果进行调整,到达最优条件。
以金属材料为例,为了提高其耐腐蚀性能和强度等性能,可通过合金元素掺杂和改变晶界等手段进行优化。
同时,对于复合材料,如碳纤维复合材料、玻璃纤维复合材料等,不仅需要考虑材料本身的性能,还要考虑其纤维长度、分布方式、树脂浸润等因素,以达到最佳效果。
二、加工工艺优化材料制备优化是制造行业的一环,而生产制造中的关键环节——加工工艺优化,则直接关系到产品的质量和产量。
加工工艺的优化主要包括加工方式、加工参数、工具选择、研磨方式等方面。
具体来说,如何根据目标产品的需求来选择最优的加工工艺就是一个复杂的问题。
在生产制造过程中,需要考虑材料的性能、产品规格、加工精度等多方面因素,综合权衡,选择最优的加工工艺。
工具的选择也很重要,不同的工具材料和加工方式会对产品的成形、精度和表面质量产生影响。
研磨方式也应根据产品的具体要求来选择,例如外圆磨削、内圆磨削、平面磨削等方式。
三、工艺参数监控与优化工艺参数的监控和调整是加工过程优化的重要环节。
随着科技不断发展,监控和调整的手段也在不断更新,例如通过数据采集与分析系统、感应励磁传感器、高速摄像等技术手段来实时监控和控制加工过程中的多种参数变化。
另外,通过建立专门的质量检测体系和采用高精度的特殊检测工具,可以及时发现工艺偏差和问题,并采取必要措施予以解决。
新型材料制备和加工
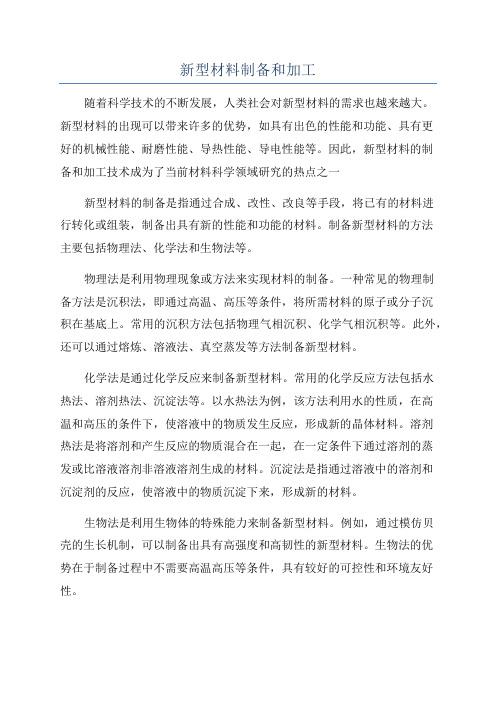
新型材料制备和加工随着科学技术的不断发展,人类社会对新型材料的需求也越来越大。
新型材料的出现可以带来许多的优势,如具有出色的性能和功能、具有更好的机械性能、耐磨性能、导热性能、导电性能等。
因此,新型材料的制备和加工技术成为了当前材料科学领域研究的热点之一新型材料的制备是指通过合成、改性、改良等手段,将已有的材料进行转化或组装,制备出具有新的性能和功能的材料。
制备新型材料的方法主要包括物理法、化学法和生物法等。
物理法是利用物理现象或方法来实现材料的制备。
一种常见的物理制备方法是沉积法,即通过高温、高压等条件,将所需材料的原子或分子沉积在基底上。
常用的沉积方法包括物理气相沉积、化学气相沉积等。
此外,还可以通过熔炼、溶液法、真空蒸发等方法制备新型材料。
化学法是通过化学反应来制备新型材料。
常用的化学反应方法包括水热法、溶剂热法、沉淀法等。
以水热法为例,该方法利用水的性质,在高温和高压的条件下,使溶液中的物质发生反应,形成新的晶体材料。
溶剂热法是将溶剂和产生反应的物质混合在一起,在一定条件下通过溶剂的蒸发或比溶液溶剂非溶液溶剂生成的材料。
沉淀法是指通过溶液中的溶剂和沉淀剂的反应,使溶液中的物质沉淀下来,形成新的材料。
生物法是利用生物体的特殊能力来制备新型材料。
例如,通过模仿贝壳的生长机制,可以制备出具有高强度和高韧性的新型材料。
生物法的优势在于制备过程中不需要高温高压等条件,具有较好的可控性和环境友好性。
制备新型材料的过程中,材料的性能往往与其微结构和组织有关。
因此,加工是制备新型材料的重要环节之一、常见的加工方法包括压制、烧结、热处理、喷涂、激光加工等。
压制与烧结是将材料粉末加工成块状材料的方法。
首先,将材料粉末放入模具中,然后通过加压使粉末成型。
最后,通过烧结处理,使材料颗粒结合成为坚固的结构。
热处理是通过控制材料的温度和时间,改变材料的组织和性能。
热处理常用的方法有退火、淬火和回火等。
通过合理的热处理工艺,可以提高材料的硬度、强度和韧性等性能。
纳米金属材料的制备与加工方法

纳米金属材料的制备与加工方法纳米材料是一种具有特殊性质和应用潜力的材料,其具有较大比表面积和尺寸效应,能够展现出与宏观金属材料不同的独特性能。
制备纳米金属材料是纳米科学和纳米技术的重要研究内容之一,本文将探讨纳米金属材料的制备和加工方法。
1. 物理方法物理方法是制备纳米金属材料的常用手段之一。
其中,溅射和蒸发是常见的物理方法。
溅射是一种将金属材料沉积在基底上的方法。
通过在真空条件下将金属材料置于靶上,然后用高能粒子轰击靶材,从而将金属原子抛射到基底上形成纳米金属材料。
蒸发是通过将金属材料加热至蒸发温度,然后使其在真空条件下沉积到基底上形成纳米金属材料。
该方法适用于制备单一纯金属纳米材料。
2. 化学方法化学方法是制备纳米金属材料的另一种重要手段。
最常见的化学方法包括溶胶-凝胶法、水热合成法和沉积-析出法。
溶胶-凝胶法是通过将金属的溶胶转变为凝胶,然后经过干燥和热处理,最终得到纳米金属材料。
该方法可以获得较高纯度和较大比表面积的纳米金属材料。
水热合成法是利用水热反应合成纳米金属材料的方法。
通过在高温高压的环境中,将金属盐溶液和适当的还原剂进行反应,形成纳米金属材料。
该方法适用于制备多种金属的纳米材料。
沉积-析出法是将金属盐溶液中的金属沉积到基底上,然后经过适当的处理,使其析出形成纳米金属材料。
该方法相对简单易行,适用于大规模制备。
3. 机械方法机械方法是在已有金属材料的基础上,通过机械加工手段制备纳米金属材料。
常见的机械方法包括球磨法和机械合金化法。
球磨法是将金属粉末和球磨介质放入球磨罐中,在高速旋转的球磨罐内进行球磨,使金属粉末逐渐减小为纳米尺寸。
该方法适用于制备多种金属纳米材料。
机械合金化法是通过高能球磨设备对多种金属材料进行合金化,并形成纳米晶结构。
通过机械合金化,可以制备出具有优异力学性能的纳米金属材料。
4. 生物和生物合成方法生物和生物合成方法利用生物体和生物分子对金属离子进行还原和沉淀,从而制备纳米金属材料。
材料制备与加工 (应力)
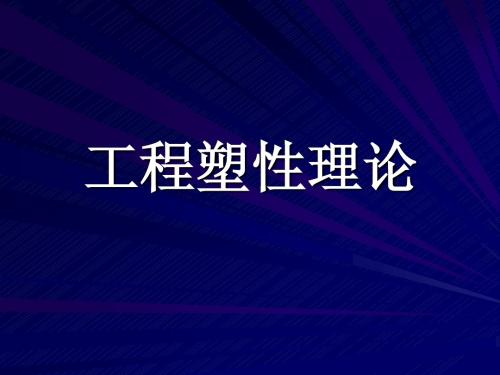
xy
yx
y
(b)x、y、z 平面上的全应力 (c)相互垂直三个平面上的九个应力分量 图 6-2 单元体的应力状态
x , xy , xz
切应力的第一个下标表示应力作用面法线的方向,第二个下 标表示该应力的作用方向。 用垂直于坐标轴的三个平面截取变形体某点,该点在三个截 面上有九个应力分量,
N S x l S y m Sz n
2 2 N S 2 N
2 2 S 2 S x S y Sz2
过一点垂直于坐标轴的三个截面上的九个 应力分量,称为该点的应力张量。
x xy xz ij yx y yz zx zy z
x , xy , xz y , yz , yx z , zx , zy
— 作用在y面上 (6-5) 过该点取一微小六面体(单元体),单元体足够小,可 2 以认为其各个面均过该点。 zz — 作用在z面上
2 yz
在单元体上标出各应力分量。
作用方向为 z 一组应力分量可以在六面体上相应的两个平行平面的任 意一个平面上标出。 作用方向为 y
考察ABC面与三个坐标面围成的四面体,四 面体足够小,可以认为ABC面过Q点。对于四
面体,由静力平衡条件, Fx Fy Fz 0
设ABC面上的全应 力为S,全应力S沿三个 坐标轴方向的分量分别 为Sx、Sy、Sz,
z
C
yx, xy
y
x
yz
A
Q
zy
xz zx
z
B
(3)变形体在外力作用下处于平衡状态
变形体处于平衡状态的充分和必要条件是, 作用于变形体的整体以及从整个变形体中分 离出来的每个单元体上的外力系的矢量和为零 ΣF=0, 外力系对任一点的总力矩也为零ΣM=0 。 利用平衡关系建立相应的方程
新型能源材料的制备与加工技术的研究
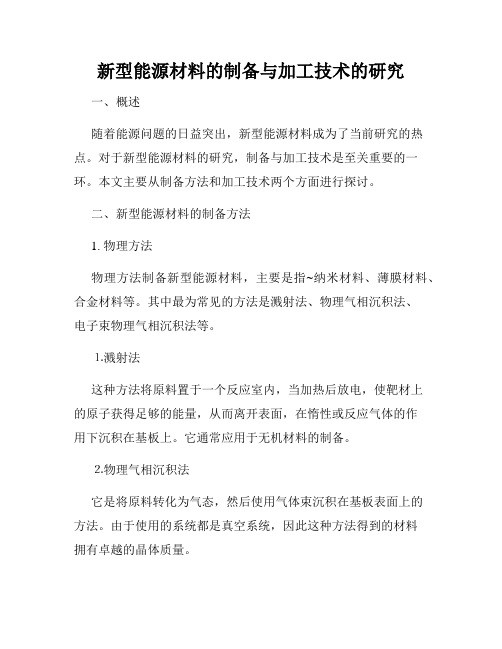
新型能源材料的制备与加工技术的研究一、概述随着能源问题的日益突出,新型能源材料成为了当前研究的热点。
对于新型能源材料的研究,制备与加工技术是至关重要的一环。
本文主要从制备方法和加工技术两个方面进行探讨。
二、新型能源材料的制备方法1. 物理方法物理方法制备新型能源材料,主要是指~纳米材料、薄膜材料、合金材料等。
其中最为常见的方法是溅射法、物理气相沉积法、电子束物理气相沉积法等。
⒈溅射法这种方法将原料置于一个反应室内,当加热后放电,使靶材上的原子获得足够的能量,从而离开表面,在惰性或反应气体的作用下沉积在基板上。
它通常应用于无机材料的制备。
⒉物理气相沉积法它是将原料转化为气态,然后使用气体束沉积在基板表面上的方法。
由于使用的系统都是真空系统,因此这种方法得到的材料拥有卓越的晶体质量。
2. 化学方法化学方法是通过化学反应制备新型能源材料的一种方法。
这种方法的优点是可以精确控制材料形成的位置和形态等性质。
其中,化学沉积法是制备新型能源材料的更好方法之一。
化学沉积是过程是将金属试剂、氧化物、硫化物以及其他化学物质加入溶液中,然后将其复合到合适的表面上。
因为这种方法不需要真空设备,因此制备成本相对较低,化学沉积法能够制备出形态多样的材料。
3. 生物合成法近年来,生物合成法作为一种新型的人工制备方法逐渐引起关注。
这种方法利用生物体内天然存在的代谢酶、微生物及其细胞等作为催化和模板作用,可以实现原子级别的组装,极为复杂的外型、大小和结构等纳米组织方法,加上制备的配方很少需要条件苛刻的高温高压系统,因此制备成本较低。
三、新型能源材料的加工技术1. 光刻在芯片加工过程中,光刻无疑是最常见和最重要的工艺之一。
其本质是通过光照和化学反应在光刻胶上产生图形,并通过显影清除不想要的图形,留下所需要的横向和垂直自然反转的图形。
光刻技术不仅适用于芯片制造,也可以应用于其他新型能源材料的加工过程中。
2. 扫描探针显微镜扫描探针显微镜技术作为高分辨率成像技术,能够实现对新型能源材料的微结构、表面形貌、力学性能等性能的观测和研究。
- 1、下载文档前请自行甄别文档内容的完整性,平台不提供额外的编辑、内容补充、找答案等附加服务。
- 2、"仅部分预览"的文档,不可在线预览部分如存在完整性等问题,可反馈申请退款(可完整预览的文档不适用该条件!)。
- 3、如文档侵犯您的权益,请联系客服反馈,我们会尽快为您处理(人工客服工作时间:9:00-18:30)。
、八、•刖言材料制备与加工(液态成形)材料科学与工程学院党惊知1)材料制备铸造材料的熔炼(化),处理等。
2)材料加工铸造方法、工艺、铸型、设备等。
1、材料制备1)铸铁普通灰口铸铁、球墨铸铁、蠕墨铸铁、特种铸铁等。
2)铸钢普通碳钢、低合金钢、特殊用钢等。
3)铸造有色合金铝合金、铜合金、锌合金、镁合金钛合金等。
材料的熔炼铸铁的熔炼铸钢的熔炼有色合金的熔炼熔炼设备铸铁——冲天炉,中频感应电炉等。
铸钢——电弧炉,中频感应电炉等。
有色合金——燃气、燃油炉,电阻炉,感应炉等。
熔炼工艺材料准备加料顺序熔炼温度化学成分处理工艺等液态合金的处理铸铁——孕育处理、球化处理、蠕化处理。
铸钢——净化处理。
有色合金——精炼处理、变质处理等。
2电磁泵低压铸造技术电磁泵系统是将电磁作用力直接作用于液态金属,驱动其定向移动,具有传输平稳、加压规范连续精确可调、炉体不需密封、生产过程稳定可靠等特点。
2. 1电磁泵低压铸造技术原理与过程电磁泵的工作参数是电磁铁磁隙间的磁感应强度和流过液态金属的电流密度。
它们与电磁泵的主要技术性能指标压头间存在如下关系:式中:厶p ――液态金属经过磁场作用区(长度为)后压强的增加量(即泵产生的理想压头)(N/m2);j ------- 在金属液中垂直于磁感应强度方向和金属液体流动方向上的电流密度(A/m2);B ----- 垂直于电流方向和金属液流动方向上的磁感应强度(T);L --------- 处于磁隙间的升液方向上的金属液体长度(m);2. 2电磁泵低压铸造工艺措施及参数选择1)铸型工艺参数的选择2)凝固方式的选择3)浇冒系统的选择2.3 浇注工艺参数的确定 低压铸造的浇注过程一般包括升液、充 型、结壳、增压、保压结晶、卸压等几个阶段。
加在密封坩埚内金属镁合金触变注射成形技术 近年来美国、日本和加拿大等国的 公司相4)铸型的排气充型模拟预测卷气、卷渣、冷隔等缺凝固过程模拟 -------- *•预测缩孔缩松 后处理设定初始条件及边界继成功开发出镁合金半固态触变注射成形机,其中主要有美国的Thixomat公司,日本的JSW公司等。
触变注射成形技术采用了一种所谓一体化”的成形方式,将压铸和注塑工艺合二为一,模具和成形材料与压铸工艺相似,工艺过程则接近于注塑成形,成形原理见图2-1镁合金触变注射成形原理在加热至部分熔化状态下,传统合金在液固两相区的初生 a 相以发 达枝晶形式存在,这种半固态合金具有很的很大的粘度, 不能够正常 充型。
若对这种半固态合金施加剪切, 可以得到球状初生a 晶,称之 为触变结构。
在一定温度下,具有触变结构的半固态合金在压力作用 下粘度大幅度降低,极易充填铸型。
两种半固态合金的组织见图 触变注射成形以半固态合金的触变行为为出发点, 具有触变结构的半 固态合金可以象热塑性材料一样流动,从而可以借助注塑原理成形。
触变注射成形的温度、压力以及涡杆转速远远高于注塑设备, 但成形 原理极为相似。
成形的加热系统采用了电阻和感应加热的复合工艺, 将合金加热至582士 2 C,固相体积分数高达60%,同时通入氩气进 行保护。
除镁合金和镁基复合材料外,铝合金、锌合金以及其复合材料均可 采用此种生产工艺。
采用这种工艺生产的零件除具备半固态成形的一 般特点外(例如零件内部致密、凝固收缩小和近终形成形) ,与普通压铸相比还有操作简单和安全、 效率高、切屑或碎片经碾研后回收率 近100% (可免除二次精炼过程)以及更加有利于环保等特点。
因此, 触变注射成形技术具有巨大的应用潜力,成为 21世纪的新一代金属 成形技术。
JS JSW 制造JLM850MG 触变注射成形设备触枝晶初生相组织的半固态合金搅拌获得的触变结构 需半固态合金变注射成形镁合金件触变注射成形技术的最新动向如下:1)热流道技术热流道技术是一种连续加热金属模具内流道,保持流道部位热熔液状态的方法。
热流道广泛应用于塑胶注塑成形,吹塑成形技术上。
为了把热流道技术应用于镁合金成形上,热流道部分的材料采用耐高温及耐熔损性的优质材料制作,并采用电磁感应加热方式,能进行迅速的升温、降温和精确的温度控制。
热流道技术具有以下特征:1)提高原料的利用率;2)缩短了成形周期;3)提高生产率(一模多个成形);4)由于缩短了熔液流动长度,而且实现成形机的小型化等。
如使用锁模力为220tf触变注射成形机生产手机外壳,虽然采用以往的冷流道方式可以一模成形二个产品;但是采用热流道方式,同样的成形机可实现一模4 个。
原料利用率也可以由20%左右提高至50%每个产品的成形周期为10秒以下。
2)铸造锻造法上的应用采用触变注射成形技术所成形的厚壁产品内部缺陷少(因具有高固相率),但固相率过高,会降低产品的机械性能。
一般厚壁产品,要求高强度时,采用锻造法来制造。
在这个锻造加工之前,如果铸造成形件是较近似成品形状的半成品(预制品)的话,就能将锻造工艺简化成精锻工艺。
这种方法成为铸造锻造法。
铸造锻造法的应用使锻造形状复杂的零件成为可能。
此外,也可以调整原材料的组织,使铸造性能不太好的原材料也可以无障碍地进行锻造加工。
采用触变注射成形技术制造半成品,随之快速锻造的方法逐渐引起人们的重视。
对于那些由于要求高、价格等原因,而不能批量生产的汽车轮毂等安全保障类零部件、阀升程杆等发动机零部件,采用此铸造锻造工艺使其批量生产成为可能。
5. 镁合金压铸现在镁合金工程构件需求的98% 来自于高压铸造行业,其中的绝大多数应用于汽车和电子行业,因此镁合金的压铸工艺性能对其在工业中应用的发展起着决定性的作用。
事实证明,镁合金是一种非常适合于高压铸造的金属材料,既可以冷室压铸,又可以热室压铸。
其主要优点是产品质量好,生产效率高,加工成本低。
目前,仅有少数几个西方发达国家在镁合金生产成套及其关键技术等方面日趋成熟,实现了规模化生产。
而我国在此方面的工作才刚刚起步。
在大多数情况下,大型、厚壁、受力和有特殊要求的压铸件采用冷室压铸机生产,冷室压铸机原理见下图。
德国FRECH公司制造的镁合金冷室压铸机BUHLER 、德国FRECH 和美国PRINCE 等公司可以提供系列化的适用于镁合金的专用冷室压铸机,可以满足镁合金压铸生产的一般要求。
镁合金冷室压铸机的特点是:(1)快压射速度提高到8-12m/s ;(2)减少了增压过程的建压时间;(3)提高了压射速度和压射力;(4) 采用电磁自动定量给料装置给料,以避免镁合金浇注时氧化;(5) 如果采用特种压铸工艺时(如真空)设备必需配套等。
镁合金 热室压铸机是目前国外使用数量最多的镁合金压铸专用设备, 工作原 理见下图德国FRECH 公司制造的镁合金热室压铸机热室压铸机具有生 产效率咼、浇注温度低、铸型寿命长、易实现熔体保护等特点;缺点 是设备成本高、维修复杂且费用较高。
由于镁合金热室压铸机是针对镁合金的物化特性和压铸工艺®師塞二驾■帀込c3特点而设计的压铸机,因此在镁合金压铸生产中应用最广。
基于上述原因,国外主要压铸机制造商均向市场推出镁合金热室压铸机系列产品。
国外主要镁合金热室压铸机生产厂商如德国的FRECH公司,意大利IDRA公司,ITALPRESSE 公司、日本的TOYO、TOSHIBA公司、UBA公司、HISHINUMA公司等。
6. 挤压铸造挤压铸造的内涵挤压铸造(squeeze casting)也称液态模锻(liquid metal forging)。
挤压铸造将液态和固态金属成形原理有机结合起来,使液态金属以低速充型,在高压(50〜100MPa)下凝固,最终获得致密的可以热处理的铸件。
挤压铸造作为一种先进的加工工艺,它兼有铸造工艺简单、成本低,又有锻造产品性能好,质量可靠等优点。
挤压铸造工艺的主要用途:①实现接近净形化(near net shape)成形,生产高质量铸件,用于取代锻件。
②挤压铸造工艺被认为是一种理想的生产铝基复合材料的工艺。
挤压铸造基本特征:①挤压铸造设备必须要能提供低流速(0.05 —1.50m/s)、大流量填充铸型的能力,以便使金属液平稳的填充铸型和将铸型内气体赶出,而且要求在铸型被充满后挤压活塞能急速增压( 50—150ms 内),使充满铸型的金属液在较高压力( >50Mpa )下结晶。
②挤压铸造的内浇口一般开在铸件最肥厚部位,而且尺寸较大,其目的是让挤压活塞提供的压力有效的传递到铸型各部,使得金属液在高压下结晶,因此挤压铸件内浇口一般用机械加工的方法去除,不能像压铸件那样轻易敲断、去除。
③挤压铸造与压铸相比,它可以通过挤压活塞对铸件肥厚部分进行补缩。
而压铸件一般不能补缩,因此挤压铸造可以铸造n x 10mm厚度,壁厚不均的铸件,而压铸一般仅限于5—6mm 以下壁厚均匀铸件。
④挤压铸造与压铸一样只用脱模剂,所以挤压铸造凝固冷却速度与压铸一样可以达到金属型重力铸造冷却速度的3—5倍(约300—400 C /s)。
因此挤压铸件的力学性能,特别是延伸率高于其他铸造方法1—2 倍。
⑤挤压铸造由于只用脱模剂,不用保温涂料,铸件冷却速度快,且在高比压下结晶,液态金属紧贴铸型,故铸件尺寸精度(CT3-4级)、表面粗糙度(<Ra6.5 )等级都非常高,对于150mm 以下尺寸挤压件,在铸型上几乎可以不留缩尺。
(6)、挤压铸造铸件可以与金属型重力铸造铸件一样,进行固溶及时效热处理,以大幅提高合金机械性能。
6.1 直接挤压铸造工艺直接挤压铸造工艺的特点是无浇注系统,充型压力直接施加在型腔内的金属熔体上,充型金属液凝固速度快,所获得的铸件组织致密、晶粒细小,但浇注金属液需精确定量。
直接挤压铸造法适于生产形状简单的对称结构铸件,如活塞、卡钳、主汽缸等。
直接挤压铸造工艺6.2间接挤压铸造工艺间接挤压铸造工艺的特点是充型压力通过浇道传递给铸型型腔中的金属液。
与直接挤压铸造法相比,间接挤压铸造法较难在铸件凝固过程中保持较高压力,不利于生产凝固区间大的合金铸件,铸件的金属出品率也较低,但它十分容易控制铸件尺寸,不需要配置精确的定量浇注系统,生产柔性较好。
根据压射筒位置,间接挤压铸造设备分为水平式和垂直式两大类。
水平式间接挤压过程见图。
6.3挤压铸造工艺参数 ①比压比压的作用是使金属液在等静压的作用下,及时消除铸件气孔、缩孔和缩松等铸造缺陷。
并产生在压力下的结晶凝固机制,从而获得较 好的内部组织和较高的机械性能。
② 加压开始时间加压开始时间既为施压前金属液在型腔内的停留时间。
研究表明, 型腔中的金属液冷却到液相线温度以下时加压可获得最佳加压效果。
挤压铸造铝合金时,除薄壁件不必延时外,一般在合型和加压前需停 留10s- 20So ③加压速度加压速度是指冲头接触到金属液面以后的运动速度。
加压速度过 慢,液态金属自由结壳太厚而影响加压效果;过快(如过 0.8m/s ) 时则易使液态金属涡流形成而卷进气体, 增加液态金属的飞溅,促使 铸件形成披缝,甚至产生裂纹。