长青预硫化变换催化剂性能考核方案(1)
变换催化剂性能和控制工艺指标

QCS― 11 催化剂的技术性能介绍QCS― 11 是钴钼系一氧化碳耐硫变换催化剂,是我公司专门为高CO、高水气比研究开发的催化剂。
已经在两个壳牌气化工艺一变使用。
和QCS-03/QCS-01催化剂相比,耐热温度高、活性稳定性好、孔结构更加合理,另外,颗粒度均匀、装填效果好,能够有效的保证装填均匀、阻力减小。
镁-铝-钛三元尖晶石载体及特殊的加工制作工艺是确保QCS-11 催化剂具备上述特性的基础和必备条件。
目前高CO、高水气比工艺包括壳牌炉气化、航天炉气化、GSP 气化等,其中神华宁煤使用GSP是目前CO 和水气比最高的工艺,对催化剂的要求也最高。
我公司的QCS 系列催化剂采用镁- 铝-钛三元载体、稀土助剂,其活性稳定性、工况适应性是最好的,在与国外、国内催化剂对比使用过程中得到很多验证,获得中国、美国、德国、日本、印度、南非等国家的专利。
QCS― 11 钴钼系一氧化碳耐硫变换催化剂,适用于以重油、渣油部分氧化法或煤气化法造气的变换工艺,促进含硫气体的变换反应,是一种适应宽温(220℃~550℃)、宽硫(工艺气硫含量≥0.01% v/v )和高水气比(0.2~2.0)。
该催化剂具有机械强度高,结构稳定性好,脱氧能力强等特点,能有效地脱除与吸附原料气中的氧和焦油等杂质或毒物。
对高空速,高水气比的适应能力强,稳定性好,操作弹性较大。
具有稳定的变换活性,可延长一氧化碳耐硫变换催化剂的使用寿命。
新鲜催化剂活性组份钴、钼以氧化钴、氧化钼的形式存在,使用时应首先进行硫化,使金属氧化物转变为硫化物。
可以用含硫工艺气体硫化,也可用硫化剂单独硫化。
QCS― 11 耐硫变换催化剂不含对设备和人体有危害的物质,硫化时也只有少量的水生成并随工艺气排出,对设备无危害。
主要特点为:耐热温度高、活性稳定性好、孔结构更加合理。
颗粒度均匀、装填效果好,能够有效的保证装填均匀、阻力减小。
镁-铝-钛三元尖晶石载体及特殊的加工制作工艺是确保QCS-11 催化剂具备独特性能的基础和必备条件。
催化剂硫化方案2001
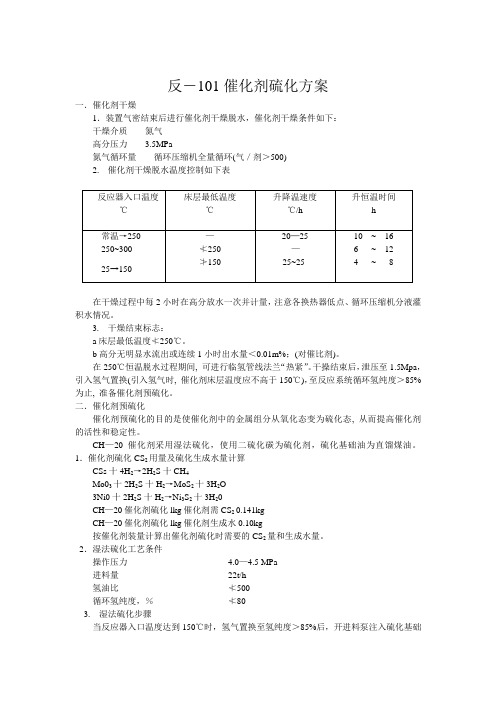
反-101催化剂硫化方案一.催化剂干燥1.装置气密结束后进行催化剂干燥脱水,催化剂干燥条件如下:干燥介质氮气高分压力 3.5MPa氮气循环量循环压缩机全量循环(气/剂>500)2. 催化剂干燥脱水温度控制如下表在干燥过程中每2小时在高分放水一次并计量,注意各换热器低点、循环压缩机分液灌积水情况。
3. 干燥结束标志:a床层最低温度≮250℃。
b高分无明显水流出或连续1小时出水量<0.01m%;(对催比剂)。
在250℃恒温脱水过程期间, 可进行临氢管线法兰“热紧”。
干操结束后,泄压至1.5Mpa,引入氢气置换(引入氢气时, 催化剂床层温度应不高于150℃),至反应系统循环氢纯度>85%为止, 准备催化剂预硫化。
二.催化剂预硫化催化剂预硫化的目的是使催化剂中的金属组分从氧化态变为硫化态, 从而提高催化剂的活性和稳定性。
CH—20催化剂采用湿法硫化,使用二硫化碳为硫化剂,硫化基础油为直馏煤油。
1.催化剂硫化CS2用量及硫化生成水量计算CSs十4H2→2H2S十CH4Mo03十2H2S十H2→MoS2十3H2O3Ni0十2H2S十H2→Ni3S2十3H20CH—20催化剂硫化lkg催化剂需CS2 0.141kgCH—20催化剂硫化lkg催化剂生成水0.10kg按催化剂装量计算出催化剂硫化时需要的CS2量和生成水量。
2.湿法硫化工艺条件操作压力 4.0—4.5 MPa进料量22t/h氢油比≮500循环氢纯度,%≮803. 湿法硫化步骤当反应器入口温度达到150℃时,氢气置换至氢纯度>85%后,开进料泵注入硫化基础油和CS 2(CS 2可根据总注入量及硫化时间确定,一般为1.5%左右)。
并在此温度下恒温润湿催化剂至高分建立液面,然后按10℃/h升温速度,将反应器入口温度升到230℃,恒温8—12小时,再按上述升温速度将反应器入口温度升到290℃.恒温6—8小时.再按上述升温速度将反应器入口温度升到310℃(催化剂床层最高温度≯320℃) 恒温4—6小时。
KC-103S型预硫化耐硫变换催化剂在甲醇合成装置的应用

KC-103S型预硫化耐硫变换催化剂在甲醇合成装置的应用李腾山;霍波【期刊名称】《煤化工》【年(卷),期】2017(45)3【摘要】针对榆林甲醇厂60万t/a甲醇装置合成气变换炉原催化剂活性严重衰退导致床层压降过大,进行了催化剂更换.介绍了KC-103S型预硫化耐硫变换催化剂的装填情况及开工导气的过程和应急措施,分析了更换该催化剂后的经济效益.运行结果表明,采用KC-103S型催化剂后,开车过程催化剂无粉碎现象、强度稳定性好,变换炉入口、出口、床层温度未发生明显变化,可缩短开工时间约40h,经济性良好.%With reference to the severe deactivation of the catalyst applied to the synthesis gas shift converter of 600 kt/a methanol synthesis unit in Yulin Methanol Plant,resulting in too much bed pressure drop,the catalyst was replaced.The loading of the KC-103S type presulfurization sulfur tolerant shift catalyst,the process of startup gas guiding and its emergency measure were introduced.The economic benefit after the replacement was analyzed.And the operation result showed that the catalyst had no grinding phenomenon in the startup process and the strength stability was good when adopting the KC-103S type catalyst.The inlet,outlet and bed temperature of the shift convener did not change,and the startup time could be shortened by 40 h,with good economic benefit.【总页数】4页(P44-46,50)【作者】李腾山;霍波【作者单位】兖州煤业榆林能化有限公司甲醇厂,陕西榆林719000;兖州煤业榆林能化有限公司甲醇厂,陕西榆林719000【正文语种】中文【中图分类】O643.36;TQ223.12+1【相关文献】1.KC-103S型预硫化耐硫变换催化剂在轴径向炉上的工业应用 [J], 毛成龙;刘杰2.清洁型KC-103S预硫化耐硫变换催化剂在GE水煤浆加压气化合成氨装置上的应用 [J], 郝元国;马燕;孙淼元3.预硫化型耐硫变换催化剂在合成甲醇项目上的应用与分析 [J], 韩舜才;李倩;殷智4.预硫化型低水气比耐硫变换催化剂在航天炉煤气化制甲醇项目中的应用 [J], 弋朝山;董新颖;屈伟舜5.KC-103S型预硫化耐硫变换催化剂在轴径向炉的装填和升温导气 [J], 李国方因版权原因,仅展示原文概要,查看原文内容请购买。
加氢催化剂预硫化方案

1. 引言加氢催化剂是广泛应用于石化工业领域的关键催化剂之一。
为了提高加氢催化剂的活性和稳定性,预硫化技术被广泛应用。
本文将从预硫化的原理、影响因素以及常见的预硫化方案等方面进行探讨。
2. 预硫化的原理预硫化是指在加氢催化剂使用之前,使用硫化物溶液进行处理,使其表面形成一层硫化物膜。
这一膜可以防止催化剂表面被氧化物或其他不活性物质占据,从而提高催化剂的活性和稳定性。
预硫化的原理可以归结为两个方面:•活性金属硫化物的形成:活性金属如镍、钼等能够与硫化物反应形成硫化物,这种硫化物能够促进加氢反应的进行,提高催化剂的反应活性。
•表面硫化膜的形成:硫化物膜可以阻隔外界氧气和不活性物质的侵蚀,减少催化剂的表面被氧化的机会,提高催化剂的稳定性。
3. 预硫化的影响因素预硫化的效果受到多种因素的影响,下面列举了一些主要的影响因素:3.1 硫化剂的选择预硫化过程中使用的硫化剂对催化剂的性能起着至关重要的作用。
常用的硫化剂包括硫化氢(H2S)、二硫化碳(CS2)等。
不同的硫化剂在反应中会产生不同的硫化物,并对催化剂表面的化学状态产生影响。
3.2 预硫化温度和时间预硫化温度和时间是影响预硫化效果的关键因素。
一般来说,高温和长时间的预硫化会使硫化剂更充分地与催化剂发生反应,生成更完善的硫化物膜。
然而,过高的温度可能会导致催化剂的部分活性成分被分解或损失,因此需要根据具体情况选择合适的预硫化温度和时间。
3.3 氛围条件预硫化过程中的气氛条件也会对催化剂的预硫化效果产生影响。
一般情况下,加氢环境中的氢气浓度越高,硫化剂与催化剂的反应速度越快,硫化物膜形成的效果也越好。
4. 常见的预硫化方案4.1 H2S气体预硫化H2S气体预硫化是一种常用的预硫化方式。
预硫化过程中,将催化剂放入加热炉中,通入含有H2S气体的加硫气体。
通过控制炉内温度和气氛浓度,使硫化剂与催化剂表面反应生成硫化物。
4.2 溶液浸泡预硫化溶液浸泡预硫化是另一种常见的预硫化方式。
催化剂预硫化操作简版

1.1.催化剂预硫化1.1.1.预硫化的准备工作1)变换催化剂升温脱水已完成,变换炉床层温度达200~220℃。
2)硫化剂已拉至现场(35t),考虑到催化剂硫化过程中损失等因素,硫化剂的准备量应为理论耗量的1.5倍。
3)21V009硫化剂罐已储存硫化剂;预硫化过程中当界位低于30%时应及时补充硫化剂。
4)联系调度引开工氢气至装置界区前备用。
开工氢气规格:压力≦1.0MPa(G),不含烯烃,氧气含量小于0.05%(V);开工氢气采样分析合格。
5)检查确认21E005、21E008、21E009已建立正常液位。
6)按岗位操作法投用工艺凝液汽提系统,工艺凝液汽提系统具备接收预硫化产生的含硫污水。
1.1.2.预硫化的注意事项1)预硫化过程中,严格按硫化曲线操作,控制好硫化温度、循环气中硫化氢及氢气浓度。
2)硫化氢未穿透催化剂床层时,催化剂床层任意温度不能大于280℃。
3)若催化剂床层温升超过30℃,则停止升温或降低注硫量,并且保持变换炉进口温度不变直至温升降至小于30℃。
4)硫化剂的加入应采取连续少量的原则加入,防止超温。
5)硫化过程中,定期检测循环气中的硫化氢浓度。
6)预硫化过程中,视采样分析结果,调整开工氢气补入量,将循环系统氢含量维持在10%~25%(V),以控制20%(V)为宜。
预硫化期间要始终保持H2含量在10%(V)以上,保证硫化剂加入后能完全氢解。
7)催化剂硫化产生的污水应密闭排往工艺凝液汽提系统。
8)若电加热器故障长时间停运:应停配氢气、停止注硫、停21K001,系统保温保压,必要时引氮气置换以降低系统内氢气浓度。
故障排除后按岗位操作法启动21K001、21E001进行硫化。
9)若注硫泵21P003不上量:催化剂停止提温,停止配氢气,尽快处理好注硫系统的故障并向催化剂注硫,重新配氢气以维持循环氢中氢浓度在指标范围内。
若注硫无法恢复正常,应监控循环气中硫化氢浓度,提高氮气补入量,以降低循环气中氢气浓度。
净化装置变换催化剂硫化方案0904

目录1 概述 32 准备工作 33 催化剂的升温硫化 44 注意事项75 附录91概述1.1变换单元所用催化剂K8-11为新型耐硫变换触媒,含有特殊载体,具有良好的低温变换活性、宽温和宽硫特性,较强的抗毒性能,较高的选择性。
1.2钴钼系列耐硫变换催化剂使用前其活性组分呈氧化态,催化活性很低,需要经过硫化变成硫化态才具有良好的活性。
首次硫化过程对催化剂的性能、使用寿命都有直接影响,因此硫化操作至关重要。
1.3催化剂硫化原理1.3.1硫化时起作用的硫化剂为H2S,硫化过程的主要反应式如下:CoO+H2S CoS+H2O ΔH0298= ―13.4kJ/mol (方程式1.3.1-1)MoO3+2H2S+H2MoS2+3H2O ΔH0298= ―48.1kJ/mol (方程式1.3.1-2)1.3.2考虑到安全因素,一般不采取直接引H2S气体进行催化剂的硫化。
H2S的制备可通过CS2和COS等与氢或水的反应得到。
其主要反应式如下:CS2+4H2 2H2S+CH4ΔH0298= ―240.6kJ/mol (方程式1.3.2-1)COS+H2O CO2+ H2S ΔH0298= ―35.2kJ/mol (方程式1.3.2-2)1.3.3对耐硫变换催化剂而言,一般倾向于非在线预硫化。
但通常情况下,工厂没有外来氢源,则只能采取在线硫化(氢源来自上游气化装置)。
硫化时,一般要求系统内硫化氢含量≥1000ppm,为缩短硫化时间可通过补加硫化剂(如CS2)等方法来完成。
2准备工作2.1现场各安装项目完毕,触媒装填结束,系统气密试验合格,置换合格(O2<0.2%)。
2.2公用工程系统(水、电、气、汽等)正常。
2.3氮气循环风机试运正常,处于备用状态。
2.4上游气化装置至少一台气化炉运行稳定。
2.5二硫化碳槽已经充装7.6t CS2,并用氮气充压至0.7MPa(G)备用, 氮气压力维持稳定。
2.6开工加热器146E114正常备用。
预硫化变换催化剂使用情况
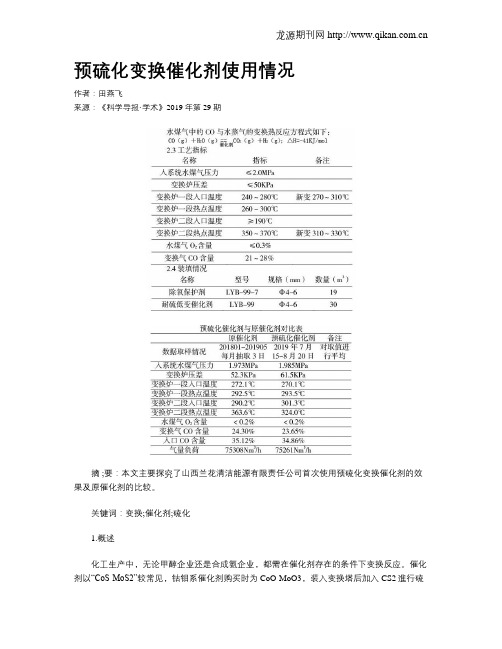
预硫化变换催化剂使用情况作者:田燕飞来源:《科学导报·学术》2019年第29期摘 ;要:本文主要探究了山西兰花清洁能源有限责任公司首次使用预硫化变换催化剂的效果及原催化剂的比较。
关键词:变换;催化剂;硫化1.概述化工生产中,无论甲醇企业还是合成氨企业,都需在催化剂存在的条件下变换反应。
催化剂以“CoS-MoS2”较常见,钴钼系催化剂购买时为CoO-MoO3,装入变换塔后加入CS2進行硫化方可有活性,同时生成大量H2S需要放空,近年来随着环保形势的严峻,一方面CS2难以购买,一方面要求“0”排放,所以我公司决定尝试使用预硫化好的催化剂进行装填及生产。
2.工艺简介2.1工艺流程水煤气经过压缩机加压至2.0MPa,进入两个并联的脱油器,脱除压缩机出口气体中夹带的油污和水,依次通过变换换热器、中间换热器的管程与变换气进行换热。
换热后由变换炉顶部与中压蒸汽一起进入变换炉一段,在硫化后的催化剂作用下进行反应。
通过增湿器(增湿器中利用脱盐水喷淋形成蒸汽,来调节变换炉二段入口温度,也可以节省一部分蒸汽)进入变换炉二段,在变换炉二段通过变换反应为合成岗位提供合格的原料气。
变换气进入中间换热器的壳程和水煤气换热进行降温,降温后进入中温水解炉,脱除变换气中部分有机硫,然后通过变换气换热器壳程再次换热降温,依次进入软水加热器和变换气冷却器降温结束送变脱系统。
2.2工艺反应经查阅数据2018年1月至2019年5月变更前催化剂(每月抽取5、15、25日数据)、2019年7月15日至8月20日的数据采集(全部数据采集),取样采取气量负荷基本一样的方案,对比上面指标进行采样,通过平均得出如上数据,从中我们看出,主要指标变换CO前后基本一样,可以保证生产稳定;二段热点温度较低体现其较好的活性;预硫化催化剂现压差较大需寻找原因,其余指标数据基本一致。
5.经济效益比较生产期间均具有稳定的变换作用,原催化剂在硫化期间取中间值,约需要31h,气量7500Nm3/h;预硫化催化剂硫化期间10.5h,气量4000Nm3/h。
变换催化剂性能和控制工艺指标

QCS―11催化剂的技术性能介绍QCS―11是钴钼系一氧化碳耐硫变换催化剂,是我公司专门为高CO、高水气比研究开发的催化剂。
已经在两个壳牌气化工艺一变使用。
和QCS-03/QCS-01催化剂相比,耐热温度高、活性稳定性好、孔结构更加合理,另外,颗粒度均匀、装填效果好,能够有效的保证装填均匀、阻力减小。
镁-铝-钛三元尖晶石载体及特殊的加工制作工艺是确保QCS-11催化剂具备上述特性的基础和必备条件。
目前高CO、高水气比工艺包括壳牌炉气化、航天炉气化、GSP气化等,其中神华宁煤使用GSP是目前CO和水气比最高的工艺,对催化剂的要求也最高。
我公司的QCS系列催化剂采用镁-铝-钛三元载体、稀土助剂,其活性稳定性、工况适应性是最好的,在与国外、国内催化剂对比使用过程中得到很多验证,获得中国、美国、德国、日本、印度、南非等国家的专利。
QCS―11钴钼系一氧化碳耐硫变换催化剂,适用于以重油、渣油部分氧化法或煤气化法造气的变换工艺,促进含硫气体的变换反应,是一种适应宽温(220℃~550℃)、宽硫(工艺气硫含量≥0.01% v/v)和高水气比(0.2~2.0)。
该催化剂具有机械强度高,结构稳定性好,脱氧能力强等特点,能有效地脱除与吸附原料气中的氧和焦油等杂质或毒物。
对高空速,高水气比的适应能力强,稳定性好,操作弹性较大。
具有稳定的变换活性,可延长一氧化碳耐硫变换催化剂的使用寿命。
新鲜催化剂活性组份钴、钼以氧化钴、氧化钼的形式存在,使用时应首先进行硫化,使金属氧化物转变为硫化物。
可以用含硫工艺气体硫化,也可用硫化剂单独硫化。
QCS―11耐硫变换催化剂不含对设备和人体有危害的物质,硫化时也只有少量的水生成并随工艺气排出,对设备无危害。
主要特点为:●耐热温度高、活性稳定性好、孔结构更加合理。
●颗粒度均匀、装填效果好,能够有效的保证装填均匀、阻力减小。
●镁-铝-钛三元尖晶石载体及特殊的加工制作工艺是确保QCS-11催化剂具备独特性能的基础和必备条件。
催化剂预硫化

黑龙江安瑞佳石油化工学习资料〔催化剂预硫化方法〕气分车间2013年4月催化剂的预硫化催化剂的预硫化有两种方法:一是干法预硫化,亦称气相预硫化,即在循环氢或氢氮混合气或氢气与丙烷或氢气与丁烷混合气存在下注入硫化剂进行硫化;二是湿法预硫化,亦称液相预硫化,即在循环氢存在下以轻油等为硫化油携带硫化剂注入反应系统进行硫化。
催化剂硫化的基本原理催化剂硫化是基于硫化剂〔CS2或二甲基二硫DMDS〕临氢分解生成的H2S,将催化剂活性金属氧化态转化为相应的硫化态的反应。
干法硫化反应:用氢气作载体,硫化氢为硫化剂。
MoO3 + 2H2S + H2MoS2 + 3H2O9CoO + 8H2S + H2Co9S8 + 9H2O3NiO + 2H2S + H2Ni3S2 + 3H2O湿法硫化反应:用氢气作载体,CS2为硫化剂。
CS2 + 4H22H2S + CH4MoO3 + CS2 + 5H2MoS2 + 3H2O + CH4MoO3 + CS2 + 3H2 MoS2 + 3H2O + C9CoO + 4CS2 + 17H2Co9S8 + 9H2O + CH49CoO + 4CS2 + 9H2Co9S8 + 9H2O + 4C3NiO + 2CS2 + 5H2Ni3S2 + 3H2O + CH4基于上述硫化反应式和加氢催化剂的装量及相关金属含量可估算出催化剂硫化剂的理论需要量。
其硫化剂的备用量〔采购量〕一般按催化剂硫化理论需硫量的倍考虑即可。
硫化剂和硫化油的选择实际上催化剂硫化时是H2S在起作用,所以所选用的硫化剂在临氢和催化剂存在的条件下,能在较低反应温度下分解生成H2S,以有利于催化剂硫化的顺利进行,提高硫化效果,同时硫化剂中的硫含量应较高,以减少硫化剂的用量,防止其它元素对硫化过程的不利影响,另外硫化剂价格廉价、毒性小、使用安全。
常用硫化剂的理化性质见表4。
表4 常用硫化剂的理化性质催化剂湿法硫化时需要硫化油,硫化油一般采用含链烷烃的直馏煤油或轻柴油,其指标见表5。
预加氢催化剂预硫化方案

预加氢催化剂预硫化方案The document was finally revised on 2021中国石化九江分公司30×104t/a重整预加氢装置FH-40C催化剂原则开工方案中国石油化工股份有限公司抚顺石油化工研究院二○○九年四月一、催化剂干燥1、干燥前的准备工作(1)催化剂装填完毕,临氢系统进行氮气置换、气密合格。
催化剂干燥用氮气作介质。
(2)绘出催化剂干燥脱水升、恒温曲线。
(3)催化剂干燥前,各切水点排尽存水,并准备好计量水的器具。
2、干燥示意流程↓N2循环氢分液罐→循环压缩机→换热器→加热炉↑↓分离器←水冷←空冷←换热器←反应器↓放水3、催化剂干燥条件:高分压力:反应器入口温度:250℃循环氮气量:循环压缩机全量循环干燥温度要求见表2。
表2 催化剂干燥温度要求反应器入口温度℃床层温度℃升、降温速度℃/h升、恒温参考时间h常温→250- 10~15 15250~280 ≮200 - 至干燥结束250→<150≯150 20~25 4~54、干燥结束标准高分无明水放出。
5、干燥操作(1)在氮气压力下,循环压缩机全量循环,加热炉点火,以10~15℃/h的升温速度将反应器入口温度升至250℃,开始恒温脱水。
如果催化剂床层最低点温度达不到200℃,可适当提高反应器入口温度,但反应器入口温度≯280℃。
(2)在干燥过程中,每2小时在高分放水一次,并计量。
(3)画出催化剂脱水干燥的实际升、恒温曲线图。
(4)干燥达到结束标准后,以≯25℃/h的降温速度将反应器床层各点温度均降至<150℃,方可引入氢气进行高压气密,合格后进行催化剂预硫化。
二、催化剂预硫化催化剂预硫化是指催化剂在氢气存在下,硫化剂(如DMDS)分解生成H2S,H2S使催化剂金属组分由氧化态转化成相应的硫化态。
在预硫化过程中,关键问题是要避免金属氧化态在与H2S反应转化成硫化态之前被热氢还原。
所以,催化剂预硫化时,必须控制好预硫化温度与循环氢中H2S含量的关系,在H2S未穿透催化剂床层前,床层最高点温度不应超过230℃。
耐硫变换催化剂升温、硫化方案
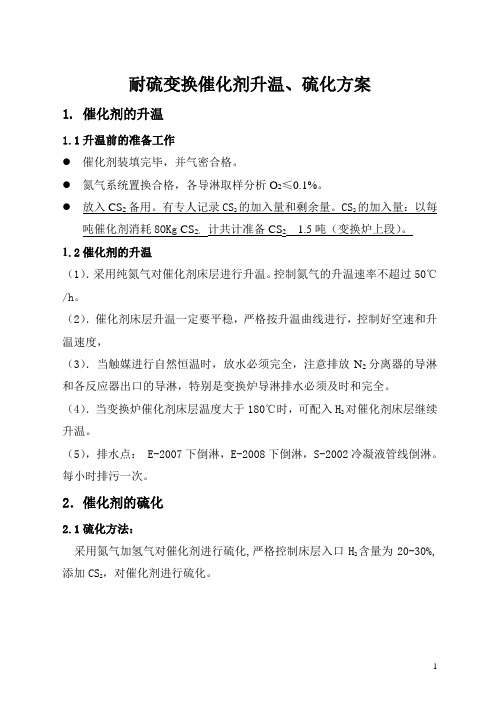
耐硫变换催化剂升温、硫化方案1. 催化剂的升温1.1升温前的准备工作●催化剂装填完毕,并气密合格。
●氮气系统置换合格,各导淋取样分析O2≤0.1%。
●放入CS2备用。
有专人记录CS2的加入量和剩余量。
CS2的加入量:以每吨催化剂消耗8OKg CS2,计共计准备CS2 1.5吨(变换炉上段)。
1.2催化剂的升温(1).采用纯氮气对催化剂床层进行升温。
控制氮气的升温速率不超过50℃/h。
(2).催化剂床层升温一定要平稳,严格按升温曲线进行,控制好空速和升温速度,(3).当触媒进行自然恒温时,放水必须完全,注意排放N2分离器的导淋和各反应器出口的导淋,特别是变换炉导淋排水必须及时和完全。
(4).当变换炉催化剂床层温度大于180℃时,可配入H对催化剂床层继续2升温。
(5),排水点: E-2007下倒淋,E-2008下倒淋,S-2002冷凝液管线倒淋。
每小时排污一次。
2.催化剂的硫化2.1硫化方法:含量为20-30%,采用氮气加氢气对催化剂进行硫化,严格控制床层入口H2,对催化剂进行硫化。
添加CS22.2催化剂硫化反应方程式CS2+4H2=2H2S+CH4+240.6KJ/molCoO+H2S=CoS+H2O+13.4KJ/molMoO3+2H2S+H2=MoS2+3H2O+48.1KJ/mol2.3催化剂的硫化●当变换炉层温度大于180℃,可配入氢气继续对催化剂床层进行升温度,氢气的配入量以H2浓度为准,使H2浓度达到20%左右。
●当触媒升温至230℃时,开始添加CS2对催化剂进行硫化,观察床层温升变化情况,控制CS2补入量稳定在20-40l/h。
同时适当提高触媒床层温度.●当床层温度达260-300℃时,保持CS2补入量,对催化剂进行硫化,同时要定时分析床层出口H2S和H2(每小时分析一次,维持床层出口H2在10--20%)。
●要保证在较低的床层温度(小于300℃)的条件下,使H2S穿透催化剂床层。
当床层出口有H2S穿透时,可加大CS2补入量继续对触媒进行硫化,CS2补入量可增加到80-150l/h,同时增加氢气的补入量,并加强H 2含量的分析,保证床层出口H2在10--20%。
关于催化剂的预硫化

关于催化剂的预硫化1.苯加氢装置所用催化剂为两种:预反应催化剂(M8-21,NiMo 4.90吨;NiO:4%, MoO3:14%)和主反应催化剂(M8-12,CoMo 11.9吨; CoO:3.3%, MoO3:14%),预计催化剂运转周期为3年,总寿命约为6年。
2.催化剂的作用●在预反应器内进行如下反应:⑴炔烃等不饱和物的加成转化反应:CnH2n-2+H2NiMo CnH2nC6H5C2H3+H2NiMo C6H5C2H5⑵含硫化合物的加氢脱硫反应:CS2+4H2NiMo CH4+2H2S●在主反应器进行如下反应:⑴烯烃的加成反应C n H2n+H2CoMo C n H2N+2⑵加氢脱硫反应C4H4S(噻吩)+4H2CoMo C4H10+H2S⑶加氢脱氮反应C6H7N+H2CoMo C6H14+NH3⑷加氢脱氧反应C6H6O+H2CoMo C6H6+H2O⑸副反应、芳香烃氢化反应C6H6+3H2CoMo C6H123.催化剂预硫化的目的本装置所用原始催化剂的主要成分为金属钴、镍、钼的氧化物,对粗苯中杂质的加氢并不具备催化作用,需将其变为硫化态,方具有活性。
4.催化剂硫化的反应机理催化剂硫化所用硫化剂为DMDS(二甲基二硫),其在标准条件下为液体,恶臭,剧毒。
在催化剂硫化条件下,其被气化,并与氢气反应:CH3-S-S-CH3+ 3H2= 2 H2S + 2CH4反应生成的硫化氢再与金属钴、镍、钼的氧化物进行反应:H2S + CoO =Co S + H2OH2S + NiO =NiS + H2O2H2S + H2 + MoO3=MoS2 + 3H2O5.催化剂预硫化的过程⑴加氢系统的冷循环和升温加氢系统气密试验合格后,通过点燃H6101提高R6102的温度,通过循环,提到整个加氢系统的温度并应达到以下条件:V-6103 PIC-6171 2.4MPaR6101 TI-6151 159℃TI-6153 149℃H6101 TI-6161 145℃TI-6162A 244℃PICA-6167 开度16%R6102 TICA-6164 242℃TI-6167A 235℃E6104A TI-6145 65℃E TI-6144 63℃⑵B.T(总硫<1.0ppm)加入以上条件以达到主反应器预硫化的条件,但预反的温度比较低,不利于所需加入的DMDS的气化,为此必须提高与反应器的温度。
变换炉改造及催化剂应用
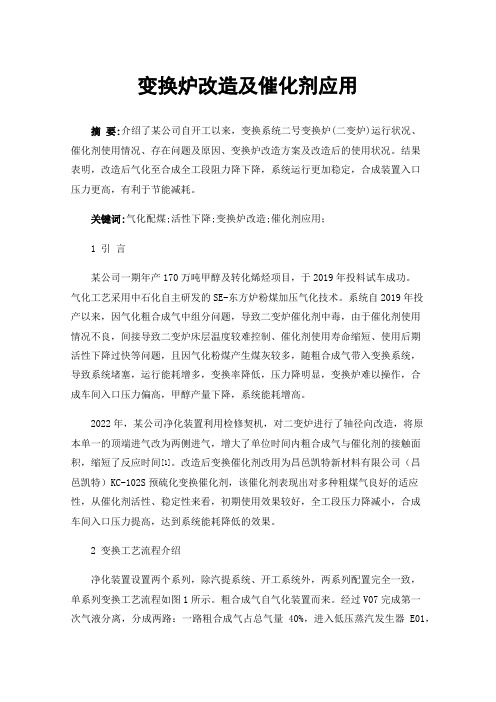
变换炉改造及催化剂应用摘要:介绍了某公司自开工以来,变换系统二号变换炉(二变炉)运行状况、催化剂使用情况、存在问题及原因、变换炉改造方案及改造后的使用状况。
结果表明,改造后气化至合成全工段阻力降下降,系统运行更加稳定,合成装置入口压力更高,有利于节能减耗。
关键词:气化配煤;活性下降;变换炉改造;催化剂应用;1 引言某公司一期年产170万吨甲醇及转化烯烃项目,于2019年投料试车成功。
气化工艺采用中石化自主研发的SE-东方炉粉煤加压气化技术。
系统自2019年投产以来,因气化粗合成气中组分问题,导致二变炉催化剂中毒,由于催化剂使用情况不良,间接导致二变炉床层温度较难控制、催化剂使用寿命缩短、使用后期活性下降过快等问题,且因气化粉煤产生煤灰较多,随粗合成气带入变换系统,导致系统堵塞,运行能耗增多,变换率降低,压力降明显,变换炉难以操作,合成车间入口压力偏高,甲醇产量下降,系统能耗增高。
2022年,某公司净化装置利用检修契机,对二变炉进行了轴径向改造,将原本单一的顶端进气改为两侧进气,增大了单位时间内粗合成气与催化剂的接触面积,缩短了反应时间[1]。
改造后变换催化剂改用为昌邑凯特新材料有限公司(昌邑凯特)KC-102S预硫化变换催化剂,该催化剂表现出对多种粗煤气良好的适应性,从催化剂活性、稳定性来看,初期使用效果较好,全工段压力降减小,合成车间入口压力提高,达到系统能耗降低的效果。
2 变换工艺流程介绍净化装置设置两个系列,除汽提系统、开工系统外,两系列配置完全一致,单系列变换工艺流程如图1所示。
粗合成气自气化装置而来。
经过V07完成第一次气液分离,分成两路:一路粗合成气占总气量40%,进入低压蒸汽发生器E01,通过调整,水气比降至0.3左右,将多余水分进行第二次气液分离,在通过预热,1#脱毒槽除灰、净化,送入1#变换炉,进行变换反应。
离开1#变换炉后,变换气经1#高压蒸汽E03发生器冷却,与另一路总气量60%的粗合成气混合,通过2#脱毒槽除灰、净化,进入2#变换炉再次发生变换反应,两次变换反应结束后,送出CO含量为20%左右的变换气,再经E04、E05、E17等设备进行余热回收,通过第三、第四次气液分离及洗涤,送至低温甲醇洗单元脱硫、脱碳,供合成装置生产甲醇使用。
耐硫变换催化剂装填及硫化方案
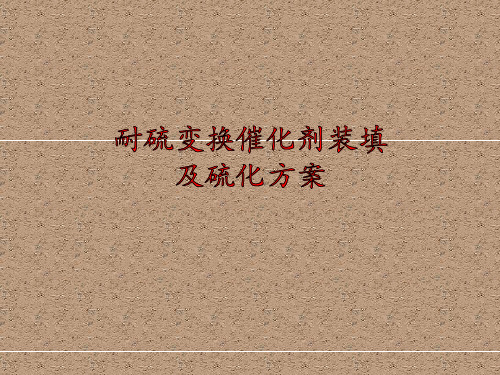
3.1.2把帆布袋接在装催化剂漏斗下面,炉内 作业人员拉住布袋出口,避免瓷球直接落到 下面摔坏。
3.1.3将瓷球铺平,确认达到所规定的高度。 注意先装50瓷球,后装25瓷球。
3.1.4催化剂卸出管也要装填上瓷球。
3.1.5将预制好的金属丝网正确地铺在瓷球上, 留出催化剂卸出管口。
3.2催化剂装填
3.2.1将催化剂装入吊斗
铺上木板,防止破损,在作业完成后,必须 把使用过的木板拿出炉外。
2.5 装填作业中,如果下雨、下雪要立即停 止作业,保护催化剂/过滤剂不被淋
湿。
2.6 在热偶套管周围充填时,注意不要造成 架空。
2.7 作业时,不要将异物带入炉内(铁片、 纸、烟头、泥土等)
2.8 应做好装填记录,包括物料的规格,型
3.2.6达到了规定的高度后,把催化剂表面推 平,把预制好的金属丝网铺在催化剂上面。 再装上300mm的瓷球。
4、四孔柱状过滤剂的装填
4.1按设计要求在所规定的位置上设置三层丝 网。
4.2 画出过滤剂装填的高度,用粉笔作上标 记。
4.3装填过滤剂至规定位置并推平。
4.4在过滤剂上设置一层丝网。再装上300mm
(3)CS2罐冲压,当罐内压力大于系统压力后, 稍开CS2罐入变换系统阀门,将CS2压入系 统,注意严禁CS2罐压力超过罐的设计压力。
(4)CS2和工艺气量的控制:在入口取样,控 制H2S+CS2含量3—5g/NM3,控制H2含量 在10%左右。
(5)控制床层温升T<20C/h,若床层温度上 升较快,应立即减少或停止加CS2量,同时 适当减少工艺气(或H2)量或增加N2量。
(6)注意随时分析出口H2S的含量,当出口
(6)注意随时分析出口H2S的含量,当出口 出现H2S时,可以适当提高入口温度。当 入口温度达到250--260C时,至少保持2h, 出口有H2S时,再慢慢提高入口温度,达 到300C,同时将入口总硫量提高到8--10 g/NM3。当出口气体中H2S含量维持在 4000-5000ppm时,可以认为硫化已结束。
- 1、下载文档前请自行甄别文档内容的完整性,平台不提供额外的编辑、内容补充、找答案等附加服务。
- 2、"仅部分预览"的文档,不可在线预览部分如存在完整性等问题,可反馈申请退款(可完整预览的文档不适用该条件!)。
- 3、如文档侵犯您的权益,请联系客服反馈,我们会尽快为您处理(人工客服工作时间:9:00-18:30)。
陕西长青能源化工有限公司
预硫化耐硫变换催化剂性能考核方案
编制:
审核:
审定:
批准:
编制单位:山东齐鲁科力化工研究院有限公司
一、概况
QCS-01S预硫化耐硫变换催化剂是含有新型组份和特殊助剂的新一代钴钼系一氧化碳耐硫变换催化剂,适用于以重油、渣油、沥青、煤渣、煤为原料造气的含硫气体的变换工艺,是一种宽温(200~500℃)、宽硫(工艺气硫化氢含量≥200ppm(干基))和宽水气比(0.8~2.0)的钴钼系CO耐硫变换催化剂。
我公司提供的67m3QCS-01S预硫化耐硫变换催化剂于2017年5月底装填就位并投入生产,投运以来一直运行状况良好,现申请对该炉催化剂进行性能考核。
二、考核依据
陕西长青能源化工有限公司与山东齐鲁科力化工研究院有限公司签订的预硫化耐硫变换催化剂合同及合同技术附件。
三、考核要求及说明
1、变化催化剂在技术协议约定的正常工况下运行。
正常工况:进变换工段气量(干基)为25.6-28.4万 Nm3/h,压力5.7-5.9Mpa,入变换炉CO 36-49%,水气比:0.8-1.1。
由于气化碳洗塔出口流量计指示不准,认可气化满负荷运行工况气量为正常工况气量。
2、性能考核期间每6小时取样分析一次变换炉进出口气样,由长青能化质检中心负责采样及数据分析。
3、变换炉进出口压差及变换炉出口温度以DCS显示PDIA2104/TI2107示值为准,每2小时记录一次数据,变换炉出口CO含量以质检中心手动分析数据为准,取考核期间数据的平均值。
4、考核相关仪表需准确、可靠,校验日期在有效期以内。
5、性能考核期间,操作人员应按规程和批准发布的考核方案进行操作,尽量维持工况稳定,要保持上下游负荷的一致性。
6、如因特殊原因导致性能考核无法按计划进行下去,经双方商定,另行选定时间重新进行考核。
四、考核主要指标
1、变换炉进出口压差≤0.06MPa;
2、变换炉出口CO≤6.0%;
3、变换炉出口温度≤470℃。
五、性能考核时间
2018年 5 月日至2018年 5 月日(72小时)
预硫化耐硫变换催化剂性能考核汇总表
厂方签字:
催化剂厂家签字:
变换催化剂性能考核数据采集表。